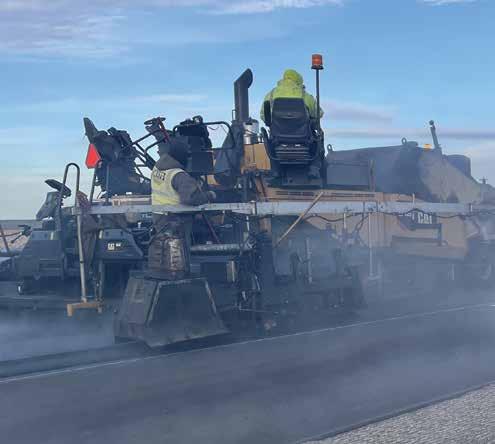
2 minute read
PROJECT MANAGEMENT
“We had a really good couple weeks where we were doing 25,000-30,000 tons a week in paving along with 10,000-20,000 tons of gravel placed in a week,” Wuori said. “It was the end of September when everything was clicking good.”
“The Mayo team did an amazing job from project management to field operations,” Christianson said. “It was a team effort that shows what kind of success we can produce as a company when we all work together and put our minds together on a common goal.”
In the Trenches
Portions of the existing system had what Wuori described as “really bad rutting.” Before the team could execute profile milling and paving of those sections, the rutted pavement had to be solved. Using a 12-foot mill in the driving lanes, they milled down 4 inches, basically creating a 12-foot-wide trench. They cleaned and tacked this trench, following the cleaning operation immediately with a paver, placing 2-2.5 inches of FAA 45. Behind that operation, the full width profile milling and paving came along.
“These two operations had to stay in coordination very well because we had to have back in everything that was milled in the day’s operations,” Wuori explained.
Caring Culture
The Mayo Construction website spells out a commitment to its workers, stating its quality of work is only as good as the expertise of its employees. The company offers a variety of insurances for workers and states, “We’re dedicated to ensuring all our employees are properly trained and feel confident in their abilities to successfully, and most important, safely complete their job duties.”
When Wuori integrated the Pavewise platform with best practices as a project manager on the Hwy. 52 project, this combination of tools gave him the opportunity to monitor the health of a handful of flaggers and pilot car drivers during the arduous project. This proved advantageous when a few workers were experiencing burnout and conflicts with other employees and needed assistance.
“I had the responsibility of managing up to 20 flaggers and pilot cars daily on this project and was able to use the software as a tool to help manage what teams worked well together and who was struggling with the team they were currently on. The software also assisted with managing the locations of where the flaggers and pilot cars needed to work on a dayto-day basis as construction operations changed daily.
“Having a digital platform that keeps you connected to employees' daily ener- gy and health is very important and makes the project much more efficient and safer for everyone. These are the people with the boots on the ground making the project a reality and they are more important than anything else on these projects.”
Christianson echoed the importance of the workers for this project’s final success, saying it was “a combination of a highly skilled milling team, paving team and rolling team that follow best paving practices and understand the importance of consistency in the field.”
Learn More
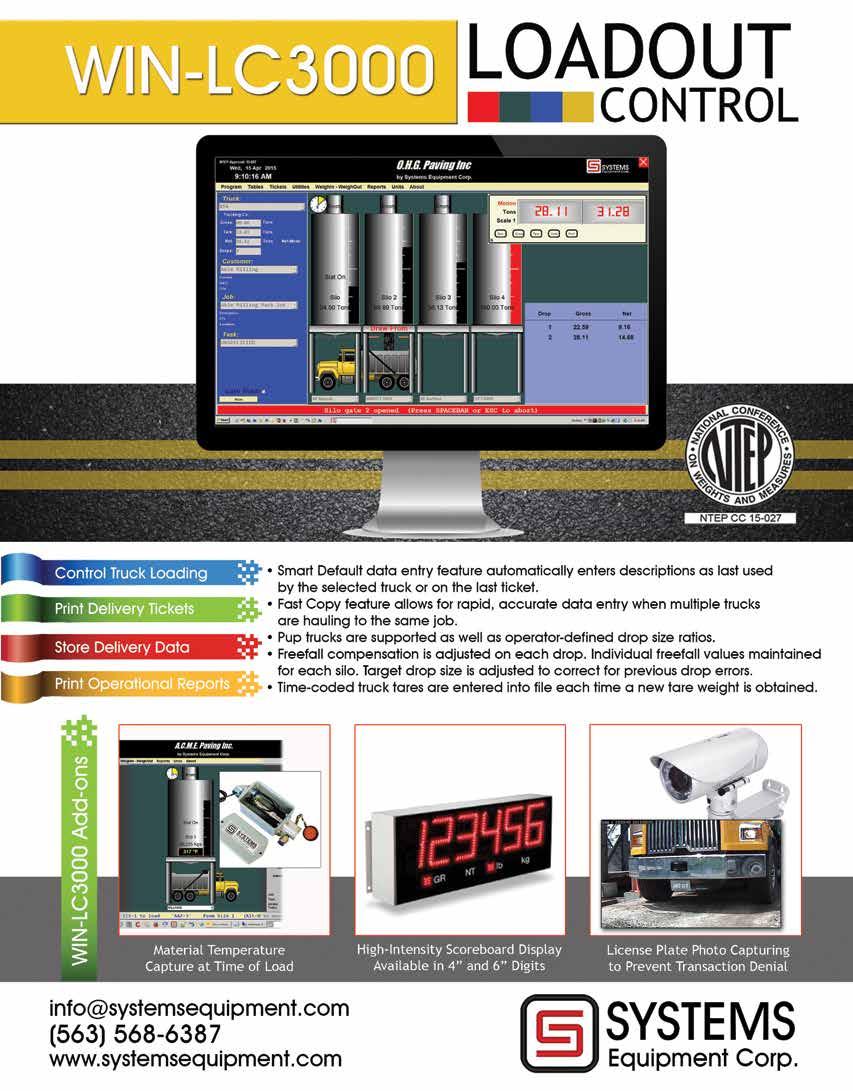