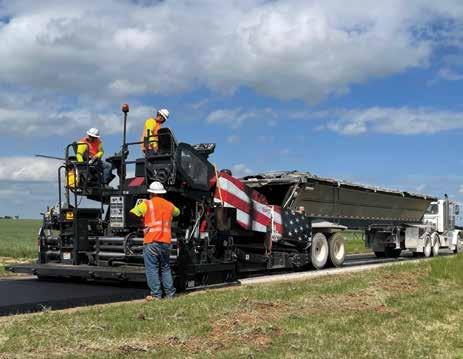
2 minute read
DYNAPAC NORTH AMERICA
Founded: 1934
Mission Statement: Your partner on the road ahead
Categories:
• Paving and/or compaction equipment/automation
Forward-Thinking Technology
Dynapac has a commitment to quality that dates back to the late ’70s with Continuous Compaction Control (CCC) or Intelligent Compaction. But it doesn’t end there as Dynapac is always ensuring quality control is met, measured and executed successfully.
Dynapac offers on rollers a documentation system, DYN@LYZER, that records stiffness of the compacted layer in real-time as well as temperature and number of passes, which eliminates guesswork and improves accuracy.
On our pavers we have introduced a system called Mat Manager to quantify and track the asphalt production rate and total operation control at the job site.
On the MF2500CS mobile feeder, the heart of the machines is the I-MIX system which lessens the probability of material segregation on the jobsite by moving the outer section of material into the middle of the material flow. This unique arrangement equalizes temperatures within the mix and blends large and small stones. The result is consistent and long-lasting road quality.
Sustainability with Asphalt
Dynapac equipment and technologies are well-positioned to pave the way towards innovation and implementation of net zero carbon emission solutions. Dynapac has consistently worked to create products that help contractors work more efficiently using less resources, lowering their impact on the environment.
The proven ECO-Mode system can be seen across the company’s portfolio of equipment and was recently added to their new line of Highway Class Pavers. The intuitive design of these machines, coupled with ECOMode, allows operation of the paver at the lowest possible engine RPM, resulting in increased fuel savings.
Screed heating is also possible with ECO-Zonal heating which consumes less power and fuel. The multizone heat control with fail-safe heating design keeps the screed heated at the right time, and the right temperature, saving time and energy consumption.
Dynapac is excited for the opportunity to forge a sustainable future for customers and our planet.
WE ARE A UL-142, ASME SECTION VIII AND API APPROVED TANK MANUFACTURER. Our facility is quality control inspected by Underwriter’s Laboratories four times per year.
WE ARE A LICENSED MANUFACTURER FOR THE STEEL TANK INSTITUTE (STI). We are the recipient of STI’s Quality Award 16 consecutive years and inspected two times annually.
ALL ASPHALT TANKS ARE BUILT TO THE UL-142 CONSTRUCTION CODE. We keep records of the steel purchases, welding practices, pressure tests and other quality control measures.
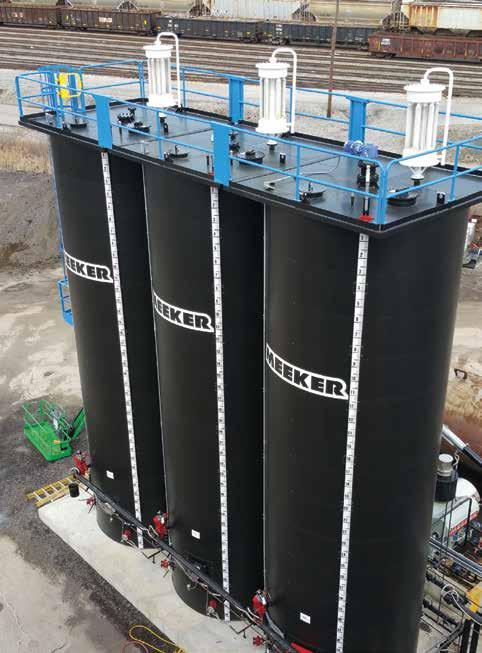
WE USE 6” INSULATION ON TOP AND SIDEWALLS OF OUR TANKS. The bottom of our tanks are insulated with foam glass block.
ALL OF OUR SHELL JOINTS ARE DOUBLE BUTT WELDED AND NOZZLE JOINTS SEAL WELDED INSIDE AND OUT. 100% Welded - The strongest union of two pieces of steel possible.
WE ARE CONSTANTLY IMPROVING OUR TANK DESIGNS. The only way to keep our tanks better than any other tank on the market!