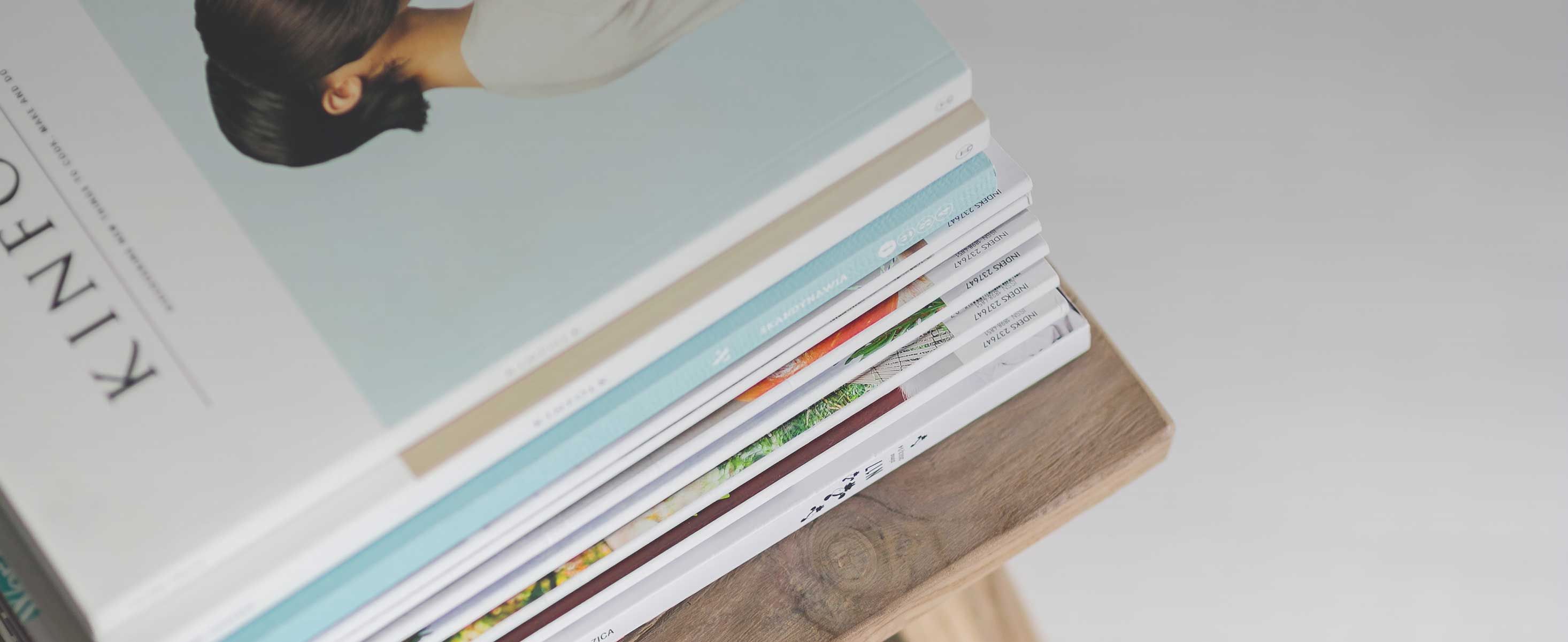
5 minute read
Ohio Trials Low Volume Ideas
P“Pavement resurfacing for low volume roads with extensive cracking is an issue faced by many local public agencies, including those in Ohio,” said Ala Abbas, a professor of civil engineering specializing in infrastructure, materials and pavement at the University of Akron. He and a research team has been investigating asphalt mix overlay alternatives for low volume roads—those with around 500 vehicles per day.
Existing options in Ohio range from chip sealing to full-depth reclamation (FDR). Abbas shared that Ohio Department of Transportation (ODOT) research have shown chip seal treatments are generally not effective if used on a pavement surface in poor condition and FDR is prohibitively expensive for most local public agencies (LPAs).
Motor paving, which ODOT defines as a cold-mix asphalt covered by a chip seal, is another option. “The advantage of this option is that it provides a resilient mix that conforms to the surface of the existing pavement,” Abbas said. However, this option isn’t widely used in Ohio because the equipment is not widely available in Ohio.
“There was an interest in producing a hot-mix asphalt [HMA] comparable to motor paving mix that can be produced at a traditional asphalt plant and placed using traditional paving equipment,” Abbas said. To do so, the research team reviewed existing resources and surveyed current practices for common resurfacing options on low volume roads. Then, they proposed and tested several asphalt mix designs in the lab and in the field.
The team discovered that LPAs use methods that aim to reduce cost in a variety of ways, including use of larger aggregates that require less binder, smaller aggregates at thinner applications, and high amounts of recycled asphalt product (RAP) between 30 and 100 percent to reduce use of virgin materials.
In its survey of 28 state and 100 local agency representatives, the team identified two types of asphalt mixes that seemed to be common for roadways with cracking. One used larger stone with a recipe mix design and the other was based on the 404LV (low volume) spec, “but that one tends not to be very useful on roadways with cracking,” Abbas added.
They began investigating an option with larger stone, based on Medina County Specification 402, which uses 90 percent No. 57 limestone and 10 percent natural sand, with 4.3 percent PG 58-28. “This is comparable to the cold-mix asphalt used in motor paving,” Abbas said, except motor paving uses an emulsion versus a binder. Additionally, the mix is constructed in a similar way to motor paving, by placing a 2-inch asphalt layer and then chip sealing it.
“We wanted to optimize the composition of the Medina County spec,” Abbas said, adding that the county reported good performance but issues with drying over time. “That was something we wanted to look at.”
They developed a variety of mix designs using PG64-22, PG58-28 and PG52-28 binders at 4.3 percent and then at different binder contents. They also adjusted the aggregate gradation, as well as the use of natural and crushed gravel in addition to limestone; tried a hydrolene asphalt extender at different percentages; and looked at the effect of RAP on performance.
LABORATORY & FIELD TESTING
The team used an IDEAL-CT screening test to narrow down potential mix designs, before evaluating the top eight more thoroughly using AASHTO T 283, Texas Asphalt Overlay Tester, Asphalt Concrete Cracking Device (ACCD), Semi Circular Bending Test (SCB or I-FIT), and Asphalt Pavement Analyzer (APA). They also used AASHTO T 305 to test for draindown.
Based on lab test results, the team selected five mix designs for field testing at two test sites, in Medina and Franklin counties: • 80% No. 57 limestone, 20% natural sand, with 4.8% PG58-28 • 80% No. 57 limestone, 20% natural sand, with 5.3% PG58-28 • 80% No. 57 limestone, 20% natural sand, with 4.3% PG58-28 with 4% hydrolene • 80% No. 57 limestone, 20% natural sand, with 4.3% PG 58-28 with 6% hydrolene • 80% No. 57 crushed gravel, 20% natural sand, with 4.8% PG58-28
The option with crushed gravel was not used in Medina County, because crushed gravel is not available in that county. The field tests—five sections in Franklin and four in Medina—were constructed in July and August 2020, respectively.
The team drew several conclusions from the field tests. “One of the recommendations is to make the asphalt mixture finer,” Abbas said. Although limestone and crushed gravel both performed well, Abbas recommended using aggregate with absorption below 3 percent, “otherwise you will need more asphalt content.”
They will continue to use PG58-28, and recommended a higher asphalt binder content between 4.3 and 5.3 percent. Abbas warned, “if you go too high, you’ll experience draindown issues.” They also recommended requiring an asphalt draindown test as part of the mix design.
Regarding the use of hydrolene, Abbas said the team needs to continue its evaluation of the test sections before drawing conclusions. Further field testing will also be conducted to learn more about each section’s long-term performance.
Construction recommendations included placing the lift at 2 inches thick, after pavement repair and milling, to ensure the lift is around twice the aggregate size (No. 57). Any thinner risks crushing the aggregate during compaction. They also suggest producing the mix at 275 to 280 degrees Fahrenheit to avoid damaging the binder, and ensuring the temperature is a minimum of 250 degrees when delivered to the paver.
The ambient temperature should be 50 degrees and rising, with no imminent rain. The team recommended using tandem steel wheel rollers weighing 6-10 tons and taking care not to over compact or crush the aggregate. Immediately following initial rolling, choke the pavement with No. 9 at a rate of 10 pounds per square yard. “Aggregate choking will help fill the void between larger aggregates ahead of the chip seal,” Abbas said. Then, apply the chip seal or asphalt overlay.
Other than using HMA, the only difference between motor paving and the new process outlined by Abbas’ team is the application of tack ahead of paving, which may be optional depending on binder content.
The result of their efforts combines the best parts of motor paving and HMA for Ohio’s low volume roads.
– BY SARAH REDOHL