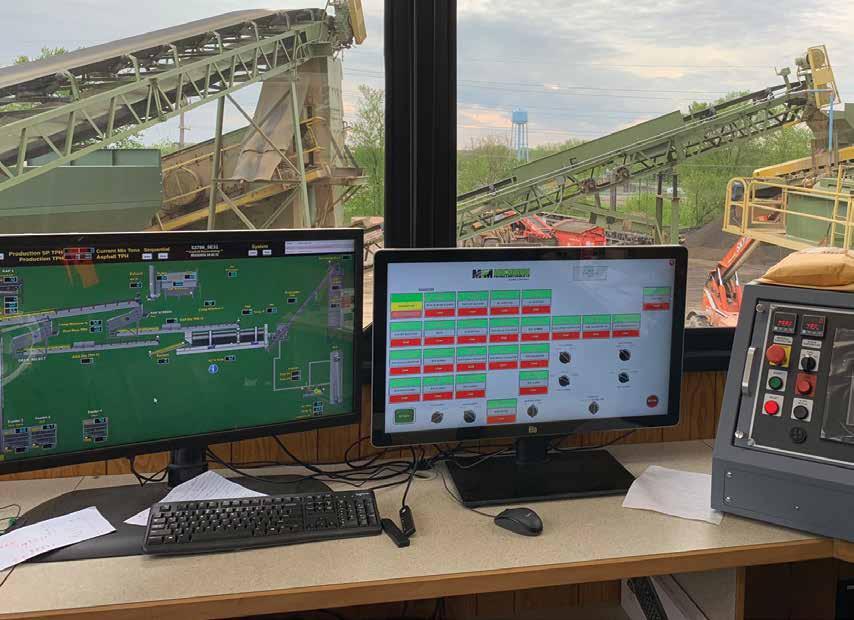
3 minute read
5 Ways to Improve Asphalt Plant Control
BY JEFF MITCHELL
HHot-mix asphalt (HMA) producers can improve the control of mix quality by implementing a handful of best practices. A robust blending and plant process control system could assist by automating these steps. Such steps should be integrated on a schedule that alerts you when it’s time to give them attention. Most producers also need the ability to add to and modify the system as the operation and market grows, and as specifications change.
Here are five ideas to optimize your plant controls. 1. Look at the changing technology. As developments to procedures and material designs advance, there will be more demand for additional ingredients, whether it be hydrated lime, liquid anti-strip, foaming chemistries, rejuvenators, modifiers, recycled asphalt product (RAP), and others. If your existing control system is a relic of the past or lacks support, it might prevent you from incorporating elements and integrating equipment correctly. It may also require a large upfront cost from the manufacturer—you—to make the modification. You certainly don’t want to cut corners to install components in a cobbled-up manner that introduces maintenance problems, or quality and efficiency complications.
2. Also consider your blending technology.
Have you ever had to wait for the extraction and gradation tests to “tweak” your liquid asphalt cement (AC) percentage? If your operations are like many plants, production cannot begin with confidence—particularly on federally funded jobs—until the first run of mix is checked for AC content and gradation. In some cases, people are adjusting the mix every day or certainly every week. If you can avoid this with reliable, real-time data from your blending controls, you can begin each production day with assurance. A comprehensive blending computer control can help your facility produce mix designs that are on target.

LEFT: The Accu-Track™ Advantage control system is designed to monitor hundreds of points on the plant multiple times per second, providing an alarm when there’s an upset or sequentially shutting the plant down if the problem is critical to operations and mix integrity. ABOVE: Producers should set the common “problematic” conditions for automatic alerting. RIGHT: Guess which one is the RAP pile and which is the pulldown (or waste) pile. You may have guessed incorrectly, because, before this plant had more robust process controls, the pulldown pile was 10 times the size of the RAP pile. Photos courtesy of Stansteel
3. Regarding start-up times, consider the start-up and shutdown mix going to the
waste pile at your plant. It’s not unusual for many contractors to report 100 tons or more a week in “pulldown piles.” This turns into real waste because the AC extractions are all over the place, meaning it can’t easily be metered back in as recycle. If you can minimize hot stops and starts with precise production and accurate silo inventories, you can reduce the waste going to the pulldown pile.
4. As previously mentioned, some of these conditions should be set for automatic
alerting. For example, not all producers remember to calibrate their belt scales on a regular basis. This is something that needs to be done more than once a year. A system like the Accu-Track™ Advantage from Stansteel has a built-in calibration deviation alert that notifies the plant operator when a belt scale or liquid AC metering deviates from setpoint.
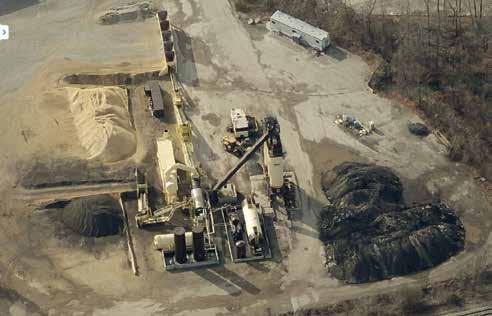
5. A modern way to “alarm” your plant in the event of a feeder no-flow, a fines or dustplug situation, an empty AC tank, a high-lev-
el alert in a silo, and so on is crucial. With a general industry condition of fewer plant operators and grounds people, personnel have many tasks to take care of in a day. It has become extremely challenging to watch and monitor plant operations in addition to managing truck traffic, loader functions and communication expectations. With the advanced and sophisticated controls available, like the Accu-Track Advantage, the systems monitor hundreds of points on the plant multiple times per second. Any upset will either provide an alarm or sequentially shut the plant down, depending on how critical it is to the operation and integrity of the mix.
Jeff Mitchell is the director, Stansteel Asphalt Plant Products. For more information, contact Stansteel at (800) 826-0223.