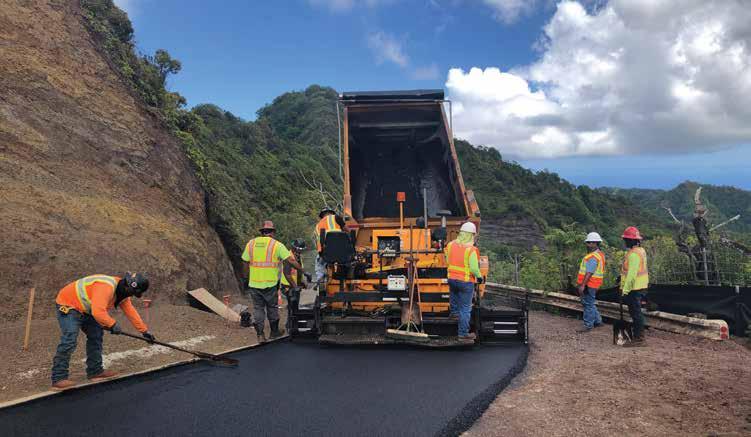
10 minute read
Meticulous Equipment Staging Leads to Pavement Preservation Success Story
You can see the face of the mountain in this picture. When the compaction team used the vibratory setting on the rollers, small rocks would dislodge and come rolling down the mountain onto the mat. A laborer followed the roller to brush the rocks away before the roller changed directions to prevent the rocks from being pressed into the mat. Photos courtesy of Road Builders Corporation
Road Builders of Hawaii executes a narrow mill and fill MATOC project with good planning, skilled teamwork
MMt. Ka’ala Road on Oahu is approximately 8 miles long, starting from Farrington Highway and ending at the Mount Ka’ala Air Force Station. During summer 2020, Road Builders Corporation, based in Honolulu, took part in a project that included pavement repairs to a 5-mile stretch in the middle of the roadway. The repairs consisted of 2 3/8-inch-thick cold milling and paving State V AC mix. Six reconstruction locations required 14 inches of cold milling, hard plastic root barrier, 10-inch aggregate base course and 4-inch paving of State V AC mix. In addition, the top 7 miles of the roadway received thermoplastic pavement striping.
That might sound like a typical pavement preservation project, but the team faced the unique challenges of high-altitude weather interruptions and a narrow road width that prevented easy movement of equipment. Here’s how Road Builders put good planning and best practices in motion to get the job done for owner/agency U.S. Army Corps of Engineers and General Contractor Elite Pacific Construction Inc.
ALL THE MOVES
In the typical open work area, backhoes, skid steers, work trucks, water trucks and service trucks can perform activities in front of and behind the milling operation and paving train. However, this road is only 10 to 13 feet wide with no shoulder area for most of the length of the road. That meant the movement of equipment throughout the day was restricted.
Shoulder areas large enough for trucks to pull over or turn around were sparsely
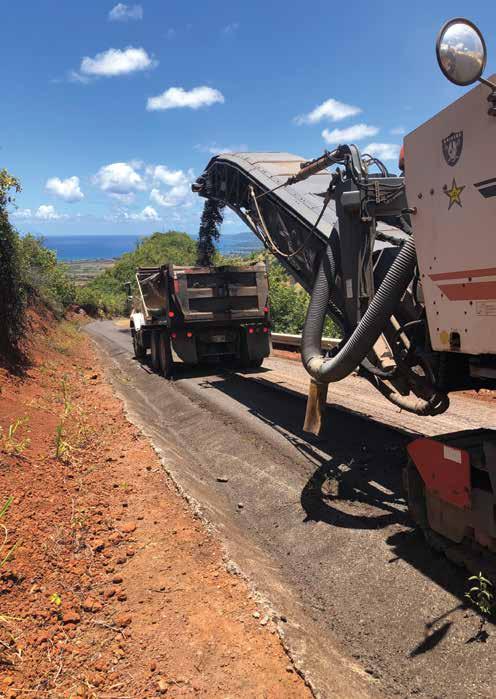
available, approximately half a mile apart. Combined with the many blind turns, it made traversing the mountain road dangerous. To provide for safer conditions, up to five dedicated radio personnel were stationed strategically at the staging area, at the work area, and at multiple locations along the haul road to control the construction vehicle traffic to prevent head-on collisions. This staging also allowed the radio personnel to inform the trucks the location of the nearest shoulder area where they could turn around to minimize the distance they would need to reverse up the mountain to back into position for the cold planer or paver equipment.
At the start of each cold planing day, a skid steer, sweeper, and a flatbed truck with water tote were positioned behind the cold planer for the entire day and all other equipment was positioned in front. The skid steer was able to remove any remaining pavement that was missed by the cold planer, the sweeper was able to clean the road surface, and the flatbed with water tote was able to refill all the equipment including the cold planer. During the paving operations, the rollers and a flatbed truck were positioned behind the paver for the entire day and all other equipment was positioned in front. Throughout the day, no equipment was able to pass to the other side of the cold planer or paving equipment. The flatbed with water tote was able to refill the roller throughout the day.
During cold milling days, there were also flaggers at the cold planer and at the stockpile area. With the first truck of the day driving up to the furthest shoulder area before the cold planer, it used that area to turn around and reversed uphill until it reached the cold planer.
There was an area near the bottom of the mountain that the Army Corps of Engineering designated as a stockpile area for which they wanted to take possession of some of the cold milled material. Once that area was filled up, the crew hauled the remaining cold milled material for the project to the Ala Imua hot-mix asphalt plant to be reclaimed.
The trucks were partially filled with the cold milled material because a fully-loaded truck might not be able to control its weight as it maneuvered back down the mountain. Sections of road with skid marks as well as deformed guard rails indicated the troubles previous trucks have encountered in the past. As the first truck passed the lower shoulder areas, the second truck could reverse and move into position in front of the cold planer and the other trucks could each move up to the next closest shoulder area.
During paving days, there were also flaggers at the paver and at the shuttle buggy, positioned at the base of the mountain. For paving operations, a shuttle buggy was positioned near the bottom of the mountain. Haul trucks took about 45 minutes to reach the shuttle buggy from the hot mix asphalt plant. The trucks were re-loaded with the hot mix, but only about half-full. It took about 30 minutes to drive to the highest point of the
project, not counting waiting times at the shoulder areas.
Another challenge was the grade of the road in certain areas. The roller had to travel at slow speeds to prevent “shoving” of the material, especially when changing directions. Also, the vibrations of the roller caused small rocks to come rolling down the face of the mountain and onto the mat. A ground person needed to follow the roller to remove the rocks before the roller changed directions to prevent the rocks from being pressed into the mat.
WATCHING THE WEATHER
Prior to the start of the project, Road Builders observed many areas of damaged guard rails and skid marks extending into the dirt embankments, which warned of the troubles and difficulties previous trucks had encountered when maneuvering on this road. Due to the steep grades of the road, trucks with heavy loads had difficulty traversing up and down the mountain. Tandem haul trucks were used to haul the cold mill material down the mountain and haul base course and AC mix up the mountain. However, the trucks could only be loaded to half of their normal capacity to make the climb up and to be able to control themselves coming down. Water trucks could only be partially filled for the same reasons.
In addition, due to the already dangerous driving conditions, any adverse weather conditions would make working on the project unsafe. Not only rain, but also low clouds limiting sight would mean the project couldn’t proceed that day. Because the project is in the mountains, the weather can be much different onsite than the conditions at the bottom or in the adjacent town. Therefore, the foreman or superintendent would arrive early, around 6 a.m., at the job site to observe the weather conditions—checking for rain and/ or limited visibility due to low clouds—and decide if work could be performed each day.
The highest altitude of the project was approximately 2,650 feet above sea level and the road to access the project was at sea level. The shuttle buggy was positioned near the bottom of the paving limits, around 240 feet above sea level. The AC mix temperature coming from the 225-TPH ADM Model EX8842 was above 300°F when it arrived at the shuttle buggy and was usually between 280°F and 300°F at the paver.
They didn’t notice a big effect on the temperature due to the altitudes; the temperature was mostly affected by the haul time to the shuttle buggy and the waiting times along the road shoulders. There was around a 10-minute duration from when an empty truck left the paver and the next truck could reverse up the mountain and arrive at the paver. And again, the trucks were only partially loaded by the shuttle buggy so that each could make the climb up some steep gradients of the road, the steepest being a concrete section of road between 15 and 20% slope.
Approximately 4,200 tons of AC mix (State V) was installed.
THE KEY PERSONNEL FOR THIS PROJECT WERE:
• Derek Samson, foreman, 17 years with
Road Builders (25 years of construction experience) • Maurino Batangan, foreman, 35 years with Road Builders (37 years of construction experience) • Mike Park, superintendent, 6 years with
Road Builders (44 years of construction experience) • Pana Widemann, quality control manager, 16 years with Road Builders (16 years of construction experience) • Lewis Boucher, safety director, 8 years with Road Builders (23 years of construction experience) • Keola Goo, operations manager/project manager, 6 years with Road Builders (23 years of construction experience) The strength of this team was to effectively access the challenges of the project and devise a plan to provide maximum production. Some key points of the plan were: • The first day of the project was spent reviewing the plans and going through all cold milling and paving operation scenarios with the crew. Not only was this beneficial to all crew members, but there was time to do this because it took an entire day to walk the cold planer and paver up to the beginning of the project area near the top of the mountain. • To provide up to five flaggers even though the road was already closed in order to get the trucks to and from the cold planer and paver as fast as possible while elimi-
nating the possibility of vehicle head-on situations on a mountainous road with hairpin turns. • To continually modify the flagging locations as the work progressed further down the mountain as truck cycle times decreased and spacing of shoulders areas changed. • A goal to always look at the estimated production rate and challenge the crew to beat that rate while still maintaining quality.
The repaired road now provides a safer travel way to the Air Force Station located at the top of Mt. Ka’ala. More importantly, infrastructure is improved for the men and women who put their lives on the line to defend our country as well as their military families and civilian employees who work on military installations. AsphaltPro Magazine is proud to share this worthy and top quality project with the industry.
– BY KEOLA GOO AND SANDY LENDER
MATOC COMPONENTS
The FY19 Mt. Ka’ala Road Pavement Repair, Site 3 to 4/5 project is part of a U.S. Army Multiple Award Task Order Contract (MATOC) that was awarded to companies that have an 8A small business designation. SBA (8A) is an ownership/ diversity certification sponsored by the Small Business Association (SBA) of the U.S. government. The SBA (8A) program is a nine-year business development program that provides business training, counseling, marketing, and technical assistance to small businesses that have been certified.
The first four years of the program are the developmental stage and the last five years are the transition stage. The goal of the program is to have 8A firms graduate and thrive in a competitive business environment. Elite Pacific Construction Inc. Is one of several companies that were awarded the MATOC contract and was the company that was awarded the task order to perform the Mt. Ka’ala road repairs. Road Builders Corporation was subcontracted to perform the cold milling and paving.
The project started June 1, 2020, and was completed Aug. 28, 2020, to repair the steep and winding road containing 14 hairpin turns rising 2,650 feet above sea level.

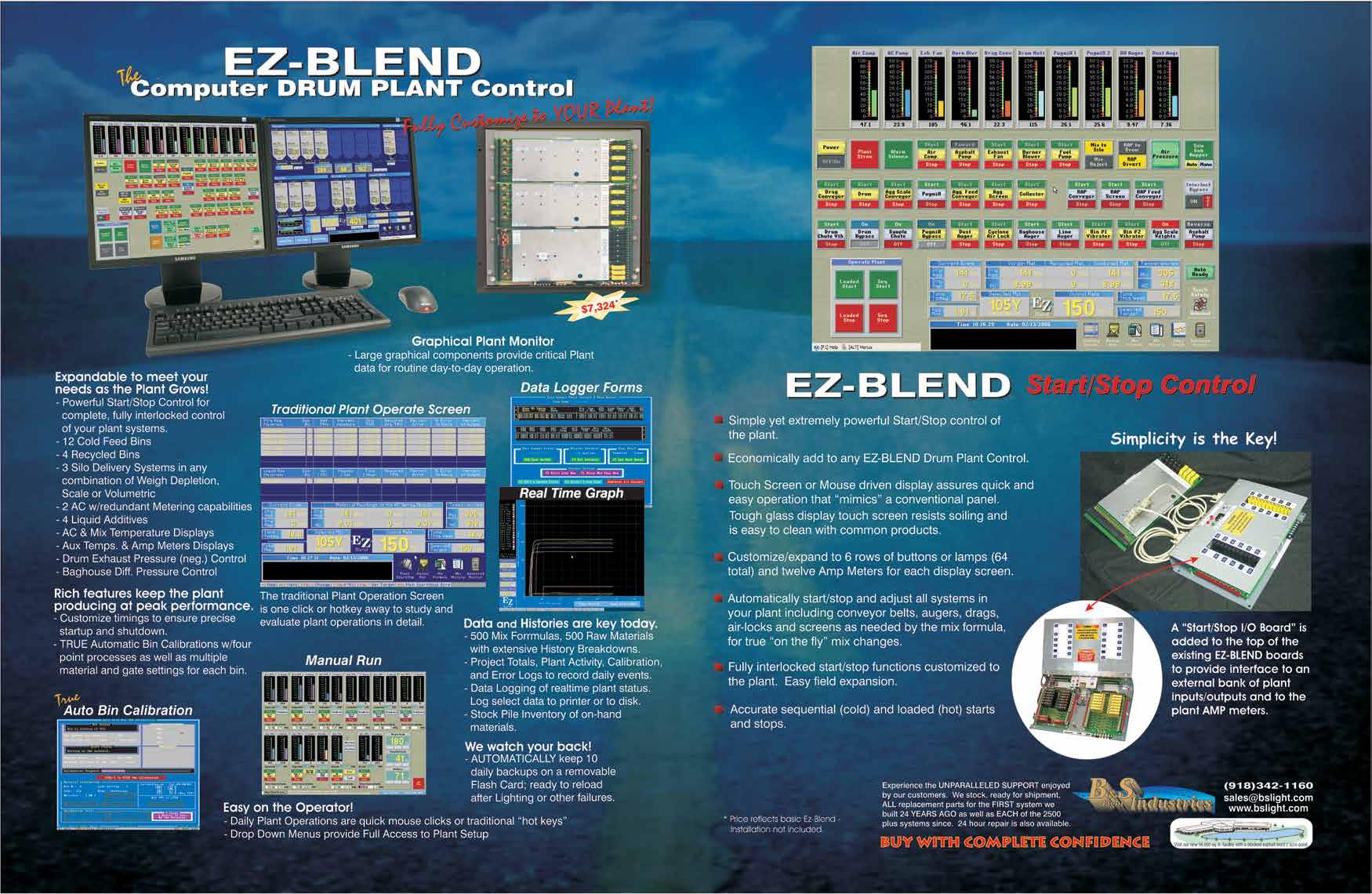
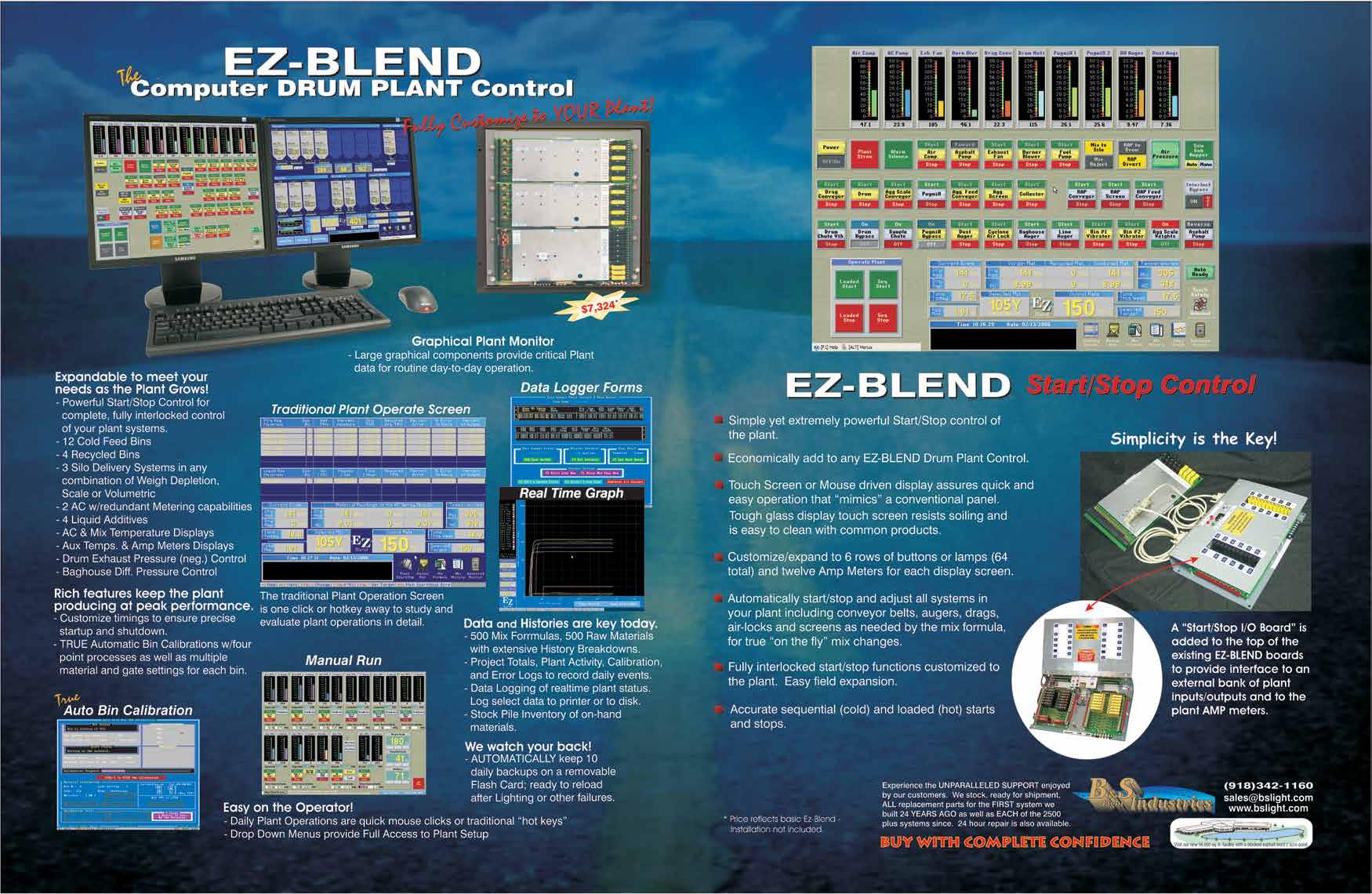