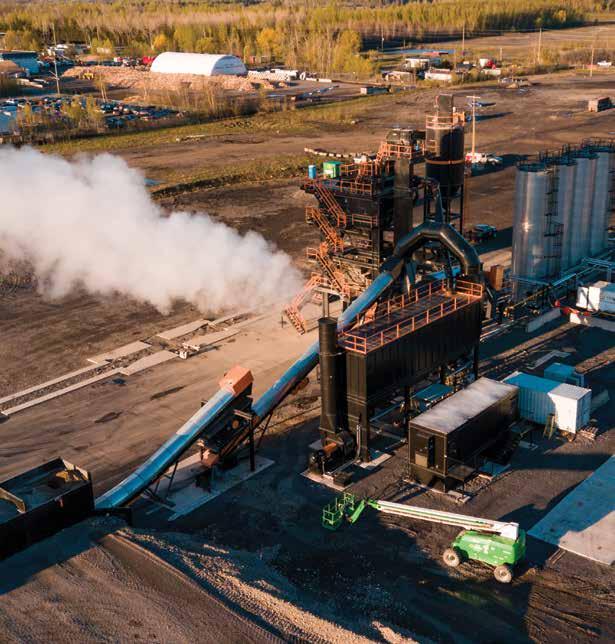
9 minute read
Hybrid Plant Increases D-Squared Growth
According to the Astec Industries website, the Astec Batch Tower (ABT) is offered in the full range of sizes with varying volumes of hot bin storage. In this picture, you can see the foundations in place for D-Squared's planned growth—hot-mix storage silos, QC/QA lab and RAP bins, among other elements to keep business moving forward.
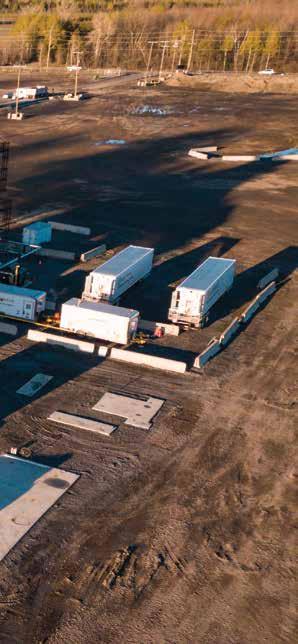
LLeadership at D-Squared Construction Limited, headquartered in Greely, Ontario, decided in November 2019 it was time to produce its own mix for its asphalt crews and customers. It took a lot of effort, but management writing letters to Parliament and finding the best zoned property on Boundary Road succeeded in achieving Ministry of the Environment (MOE) approvals for a hot-mix asphalt (HMA) plant from Astec Industries, Chattanooga, Tennessee. By December 2020, D-Squared Asphalt had permits to begin installation near Highway 417 in Ottawa and meet the goal of self-sufficiency.
Dave Meikle, the vice president of business development and acquisition for D-Squared Construction, spoke of the experience. “The environmental permitting process is a long, bureaucratic process, not for the faint at heart. Astec assisted whenever needed and was helpful during the process. Boundary Road offered the zoning required to permit the asphalt plant and is the perfect location due to proximity to the 417 to service a larger area.”
QUALITY GOALS
The team knows what it takes to see a goal from inception to completion. In 2006, Domenic Franco Madonna, a mere 19 years old, and partner Charles DePonte founded D-Squared Construction. They had a backhoe and dump truck at the time. They’ve since expanded their fleet, grown to more than 300 employees and opened a 120-acre quarry just east of Ottawa in Moose Creek.
By 2017, the company was able to complete a handful of multi-million-dollar contracts for Ottawa’s transit system, including three busy intersections along St. Laurent Boulevard. Taking on multiple large projects simultaneously meant relying on large producers for a timely supply of materials.
“It is a situation where on larger projects the suppliers dictate the pricing, this keeps you from competing in ‘their’ space,” Meikle explained. “We knew the growth of the company depended on being self-sufficient be it asphalt or quarry and pit supply.”
By November 2019, the leadership team knew they were going to pursue funding for a D-Squared asphalt plant. Management selected a hybrid plant from Astec Industries to suit their needs. The plant has a rating of 300 tons per hour (TPH), six cold feed bins, four liquid asphalt cement (AC) tanks, a lime silo with auger conveyor, and room for growth in recycled asphalt pavement (RAP) use.
“Our plant is a hybrid batch/continuous mix plant,” Meikle shared. “It has a double barrel dryer which will allow us to continuously mix
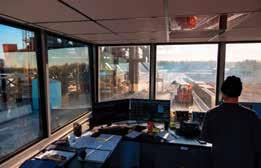
Dave Meikle, the vice president of business development and acquisition for D-Squared Construction, said Plant Operator Brady McDonald is second to none.
D-Squared provided its own mix via live-bottom trailers into a Shuttle Buggy on the Heron Road project this season.

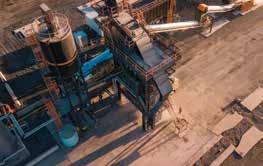
As part of their environmental stewardship, D-Squared Construction works with farmers in the area to distribute the lime product from its dust silo for use in their fields. Dave Meikle explained the lime product assists the farmers with the Phosphorous levels in their soil and, ultimately, reduces the amount of this product that would otherwise be wasted.
with the addition of a drag conveyor and silos, phase two of our plan, which we hope to complete over the winter. Phase two will also add the RAP cold feeds for running recycled material in our mixes.”
At this time, D-Squared relies on GEMTEC Consulting Engineers and Scientists Limited, headquartered in Fredericton, New Brunswick, for its quality control testing, but they’re planning on having their own lab set up during the 2022 construction season. In fact, they brought on Quality Control Manager Harrison Smith spring 2021 to increase efficiency in processes, reduce waste, improve on the use of time and resources, and serve as the liaison between D-Squared and GEMTEC.
“Harrison is a resourceful manager,” Meikle shared. “He’s successful at building and maintaining open communication between project team members and clients. He’s quality driven and proactive with advanced understanding of contract management, contractor oversight and construction administration.
“During the past 21 years, Harrison has worked in several roles within the quality control and civil construction/engineering field. He has effectively supervised and managed materials testing and laboratory operations on a variety of commercial, residential and heavy civil construction projects. Over the course of his career, he has provided laboratory testing and field inspection services of hot and warm-mix asphalt, cold in-place expanded asphalt mix (CIREAM), cold in-place recycling (CIR), aggregates [and more].”
Meikle explained that Smith’s role will be more than overseeing the quality control/quality assurance (QC/QA) of mix design for D-Squared.
“The QC manager’s role in our operation is essential to building a successful business that produces and delivers products to meet or exceed our clients’ expectations. He oversees construction activities and the manufacture of various construction materials at our asphalt plant, gravel pits and quarries to ensure that products, procedures and services are consistent and of the highest quality.”
Smith shared the company’s view of QC/QA going forward.
“At D-Squared we understand the importance of quality control and quality assurance procedures. To enhance client satisfaction during the construction project, the contractor must supply compliant materials to market and meet the expected quality requirements as outlined in the contract documents. By establishing a quality control team and a testing facility, we will better position ourselves to implement and maintain acceptable quality standards and best work practices allowing us to take on larger scopes of work over time. In addition, this will enable us to identify and eliminate any insufficient practices that may occur within our operations.”
For much of the new plant operation, D-Squared could hire from within, and that’s good news in today’s challenging workforce environment.
“We were able to pull from our current workforce the best candidates for the positions available with the plant manager,” Meikle shared. “Our plant operator/plant manager, Brady McDonald, is second to none, working endless hours to get us where are today. At D-Squared we have our own in-house recruiter who has his hands full to fill all of D-Squared’s staffing requirements.”
Through reciprocal relationships with vendors and contractors, and with an eye to mergers and smart growth, the team at D-Squared is expanding externally and internally. President Jessica O’Reilly told the Ottawa Business Journal in 2018 of their workforce development challenges, saying, “As we continue to grow, finding additional skilled

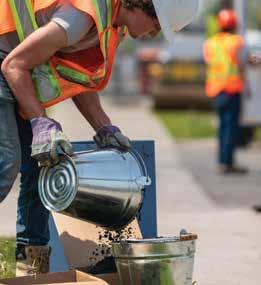
LEFT: For a Heron Road paving project, the D-Squared crew used a Hamm roller in the breakdown position. They had a smaller BOMAG roller on hand for finish rolling. RIGHT: Management plans to have its own working lab running during the 2022 construction season, but Quality Control Manager Harrison Smith already has the team performing proper sampling and testing for QC/QA, which is performed in concert with GEMTEC.
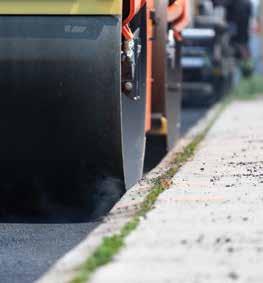
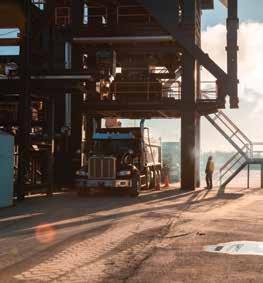
LEFT: A D-Squared equipment operator shows attention to detail on the Heron Road project. RIGHT: The D-Squared team was excited to produce its first mix April 23, 2021.
workers in our industry becomes increasingly difficult. We are always looking for new talent with which to build our team.”
One method of building the team is internal training, which management set up a program to accomplish. Phil Adams, is the human resources and recruiting manager.
TIMELINE FOR EXCELLENCE
Once the team at D-Squared had decided on its plant, the first load of components arrived Dec. 20, 2020, in time for the harsh weather of winter in Ottawa.
“The plant was erected during the coldest months of the year through all weather,” Meikle explained. “D-Squared completed the installation with the help of one Astec representative. This was a team effort from beginning to end. From bad soil conditions to letters to members of Parliament, from freezing cold labor in terrible conditions to incredible planning and engineers, it took an entire village to put this in motion. We appreciate everything from everyone who was involved in this process.”
The process included taking the extra precautions to safeguard the environment, a hallmark of the asphalt industry. For D-Squared, that meant taking a close look at dust control.
“Our state-of-the-art baghouse removes the dust and sends it to our dust silo, which has a slurry auger, which adds water to the dust when unloading to mitigate dust around the plant. We were sure to include the slurry auger when ordering the plant as this cuts down the dust at the plant by 80%.”
Another aspect of being a good neighbor is sharing the dust. Sounds counterintuitive, right? But there’s a brilliant method to the madness.
“One such project is to work with farmers in the area to distribute the lime product that comes from the dust silo for use in their fields.” Meikle further explained the lime product assists the farmers with the Phosphorous levels in their soil and, ultimately, reduces the amount of this product that would otherwise be wasted.
They produced their first batch of HMA April 23, 2021.
“We wouldn’t change a thing but admittedly the funding, city approvals, zoning and MOE approvals are a daunting task and not for the faint at heart. We were over the moon on April 23rd when we made our first batch!”
Since that first batch dropped in April, the plant and paving crews have been hard at work, making management proud to be producers.
“We have already produced City of Ottawa Friction Coarse high-grade asphalt and laid it on city roads and transit ways. In the tens of thousands of tonnes. Our plant and paving crews have performed flawlessly. The material is being made and laid on spec repeatedly. My hat’s off to every single one of them.”
– BY SANDY LENDER
Make your RAP piles pay for themselves.
Use ReLIXER™ to maximize RAP content while meeting project specifications.
Engineered, high-performance rejuvenator for High RAP & RAS mixes
Rapidly penetrates and rejuvenates. Reduces the virgin asphalt requirements in the mix. Allows increased RAP & RAS content while aiding compaction Improves low temperature performance, fracture toughness, aging & fatigue 100% RAP mixes with no virgin AC added are viable with outstanding performance