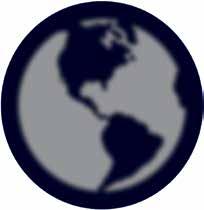
12 minute read
Latest Pavement Technologies Can Save Lives
TThe National Highway Traffic Safety Administration (NHTSA) reports that the economic cost of the car accidents claiming more than 90 U.S. lives per day is approximately $230.6 billion, and states most of these crashes can be avoided if preventive measures are taken at the road’s surface.
While many factors contribute to vehicular accidents, roadway infrastructure causes can be mitigated with proper pavement surface condition. The Little Book of Tire Pavement Friction uses a study conducted in Texas in 2009 to illustrate fewer car crashes happen along a road that has high friction than a road with lower friction. We also know that pavement distress results in a reduction in surface friction. Therefore, it is essential to monitor the pavement surface condition and improve surface friction if needed, both to save lives and money.
According to P.G. Roe and R. Sinhal in their 1988 “The Polished Stone Value of Aggregates and In-service Skidding Resistance,” skid resistance on wet surfaces decreases as speed increases, but surfaces with greater macrotexture have better friction at a higher speed and the same low-speed friction. The Little Book teaches us the difference between peak and sliding friction on dry and wet roads depends on both tire properties and characteristics of road surfaces. Therefore, we must maintain the macrotexture of the roads to ensure an appropriate amount of friction between tires and surface. Degradation of this macrotexture is considered distress.
As time goes on, even the best asphalt pavement can get distressed. Readers know there are many types of distress such as cracking, distortion, disintegration, skidding hazards and surface treatment distresses, and one kind of distress can lead to another. Hence, it’s important to invest not only in new infrastructure but also in the technology that detects and treats the distresses to achieve optimal friction between tires and road surfaces.
DETECT DISTRESS
Detecting and treating different distresses is a complex endeavor. While many countries use manual visual inspection, this method is not the most efficient. Hence, researchers recommend using an automated inspection system.
Automated distress detectors reduce the subjectivity of visual measurements, as detailed in Tom B.J. Coenen and Amir Golroo’s “A review on automated pavement distress detection methods” from 2017. Each type of distress is different, requiring unique detection and treatment strategies. For example, if automated technologies are being used, then detecting cracking that has a larger depth will require a different imaging technique and resolutions than when detecting rutting, which is shallow in depth. There are many technological options available to detect these distresses.
Use of poor technology to detect and treat pavement distresses brings unsatisfactory and sometimes counterproductive results. Researchers around the world are trying to use innovative, economically viable and efficient technology to detect asphalt pavement distress. The pavement management system (PMS) works efficiently when high-quality data is being input, as explained by Laura Inzerillo et.al., in the “Image-based 3D reconstruction using traditional and UAV datasets for analysis of road pavement distress” in 2018. Reports like “A Review of Three-Dimensional Imaging Technologies for Pavement Distress Detection and Measurements” from S. Mathavan et al. show studies involving 3D imaging technology to detect and prevent pavement distress have gained attention because of the high accuracy and fast results. Then reports like that from G. Loprencipe et al. in 2017 show the automated distress detection system may be highly accurate and less time-consuming, but it is expensive and not sustainable. The recent development in 3D technology and its effectiveness makes it a worthwhile technology, and researchers are trying to make this technology an economically sustainable option.
In 1997, the first 3D technology was used to detect cracks and rutting using a double-sided mirror system that could project a laser on the affected surface and collect reflected light. This system reported a vertical accuracy of 0.5 millimeters, according to a J. Laurent et al., presentation to the International Conference on Recent Advances in 3-D Digital Imaging and Modeling in 1997.
A more recent study conducted by R. Gui et al., took this 3D technology a step further. They proposed a 3D pavement components decomposition model (3D-PCDM) that can break down 3D pavement profiles into separate components and extract specific information about pavement distress. This technology showcases an efficiency of 92.75%, according to their abstract at https://doi.org/10.3390/s18072294
This technology follows three main steps. 1. In the first step, the frequency characteristics of pavement distress and performance indicators are analyzed using 3D pavement profiles. 2. During the second step, high pass filter separates low-frequency components (f) from the profile data. 3. In the last step, total variation of de-noising technique separates sparse component (x) and vibration component (t), and a pavement performance indicator is used to verify the validity of these components.
The data collection system contains a sensor head and controller. The sensor head collects data using a 3D camera and line laser, where the 3D camera is installed at an angle of 6-8 degrees to the laser so that it can obtain the profile. Whereas the sensor controller receives and pre-processes the profile data and uploads it to the host computer. This technology can provide accurate measurement of length, width and elevation of marked asphalt surfaces. When compared with real measured data, the difference is always between 1 mm, profiles obtained from decomposed sparse components are more stable and comprehensive than the actual measured data, mostly due to the unpredictable impact of pavement texture depth.
Potholes may be the most well-known type of pavement distress. For this discussion, we can turn to B. Kang and S. Choi’s presentation to the 2017 Ninth International Conference on Ubiquitous and Future Networks (ICUFN) in Milan. Believe it or not, classification of pot-
holes seems an unreachable goal because of the lack of accuracy of the existing detection system.
Existing automated detection systems for potholes fall into three main categories: 1. vibration-based, which is unreliable because it can’t detect potholes in the center of roads due to the lack of hits by vehicles; 2. 3D reconstruction using laser scanning, which is efficient but costly; and 3. 3D reconstruction using RGB color space image segmentation, which E. Buza et al., presented as 81% less accurate than 3D laser scanning—with potential for improvement—but economically sustainable for commercial use to the International Conference on Information Technology and Computer Networks.
A study conducted by J. Simon et al. and published in the International Journal of Recent Technology and Engineering proposed a unique solution to pothole detection. The researchers developed a system using an ultrasonic sensor and a force-sensing resistor connected to an Arduino Uno (open-source microcontroller). The ultrasonic sensor sends high-frequency sound waves and receives the echo while the time taken is being measured (used to measure distance) and marks the speed breakers. The force-sensing resistor then measures the pressure value when a vehicle faces a speed breaker or pothole.
Both ultrasonic and pressure sensor data are compared to determine the position of potholes in the pavement surface. If both ultrasonic sensor and pressure sensor show a higher value than the threshold, then it’s determined to be a speed breaker, but if only the pressure sensor demonstrates a higher value than the threshold while the ultrasonic sensor shows a stable value, then a pothole is detected. These data can be plotted to generate an accurate location of potholes.
Although this proposed technology is cost-effective, it has yet to realize commercial implementation. Studies like those performed by Coenen and Golroo have shown both the ultrasonic and pressure sensors are needed for the system to work accurately, but it has the potential to be mainstream. A similar study was conducted by Wang et al. to detect potholes, but they did not incorporate the ultrasonic sensor. But it failed to detect the potholes’ locations accurately because of the lack of precision of data, and it was concluded that just like accelerometers, pressure sensors are meant to be a complementary tool to detect distress in asphalt surface. The study conducted by Simon et al. accomplishes this task by successfully incorporating ultrasonic and pressure sensors to make the data more accurate.
In today’s world, the most commercially used laser-oriented distress detection technology, known as laser crack management system (LCMS), uses two high-performance lasers, which are attached to a camera, to measure road profile and road slope with a resolution of 1 mm. The system generates a 3D profile of the road using 2D intensity data and 3D texture data, as discussed in J. Laurent et al. 2012’s “Using 3D Laser Profiling Sensors for the Automated Measurement of Road Surface Conditions.”
Although it is a good approach, Coenen and Golroo reminded us quality issues due to lighting must be overcome for this system to I would recommend Tarmac for any Asphalt or Industrial Drying project. Their talented and knowledgeable staff provides swift exceptional service. From Parts, Equipment Sales, and Engineering Department, Tarmac gets the job done.
James Keene
Fred Weber, Inc. General Manager Asphalt Operations
(FRED WEBER has been a valued customer for over 22 years)
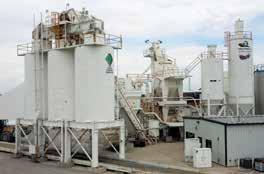
www.tarmacinc.com
ASPHALT PLANTS, COMPONENTS & PARTS CALL: 816-220-0700 OR email: INFO@TARMACINC.COM
become mainstream. However, due to technological advancements in recent years, structure from motion (SFM) technology has gained the interest of scientists. The use of SFM will enable road agencies to make a 3D model from any photo data set, and its potential to verify its ability to help in pavement distress applications will reduce cost. A study conducted by C. Santagati et al. proposed the use of the SFM technique. During this process, a camera takes pictures of the distressed sites, ensuring the angle between 5 and 10 degrees. This data is then imported into SFM software, and the 3D model is created. Every profile curve created by this technology can estimate the depth and width of specific distresses, which will then be used to determine the maintenance strategy.
DEVELOP SOLUTIONS
According to the American Society of Civil Engineers (ASCE), American infrastructure is deteriorating rapidly, and in the coming decade, the economy will lose $4.5 trillion to repair the damage. To prevent this large economic loss, we must concentrate on improving the quality and durability of the asphalt mix.
Maintaining surface roughness is an important part of any road management system because it provides necessary friction for vehicles. To improve an asphalt surface’s roughness, a study by S. Oleksandra et al. published in Science Direct suggests using a mix of cement, sand and reinforcing fiber. The introduction of this mix is supposed to improve the crack resistance, tensile strength and abrasion resistance.
As a new solution to asphalt surface distresses, researchers have suggested using self-healing technology for asphalt pavement to reduce maintenance costs, decrease carbon dioxide emissions and increase road safety. Nanoparticles, induction heating and rejuvenation are the three main self-healing technologies available for asphalt pavement design. According to J. Qiu et al., self-healing technology depends on time (rest period) and temperature. A more extended rest period and higher temperature lead to better healing.
A study shows that nano-clay in the asphalt pavement improves mechanical properties, and when driven by the surface energy, nano-clay moves to the tips of cracks to repair them. Nano-rubbers can also be used to improve the healing properties. A study conducted by J. Qiu et al. shows that a mix of nano-rubbers increases recovery up to 90%. Nano-rubber can be used to increase the durability of the asphalt mix and also work as a self-healing modifier. Different studies mention the use of a nano-rubber modifier; however, they didn’t mention any exact composition of the modifier. Hence, the exact healing mechanisms could not be determined. But the research in this area is still in its infancy.
Another study from Quantao Liu et al. has found that the use of conductive steel and wool fibers in the asphalt mix enables self-healing properties when heated. This system works by generating electromagnetic fields when the asphalt mix is placed through a coil. This process is repeatable, and damage control is easier. The researchers found the incorporation of steel fiber into the asphalt mix helps to achieve a

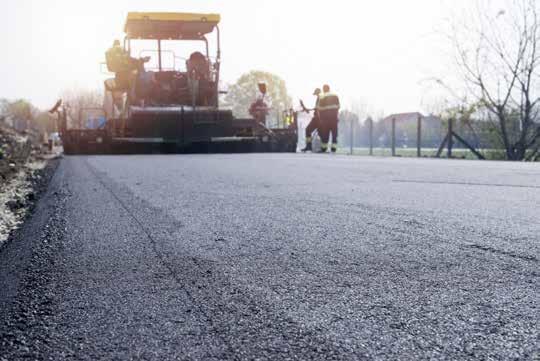
SIL3 PLe CAT3 PLd
greater bond between large aggregate (stones) and induces the self-healing mechanisms. Liu et al. wrote in the following year’s report, “Induction heating of electrically conductive porous asphalt concrete,” that steel wool type 000 is a better conductor than steel fiber. A. Garcia warned in the 2012 “Self-healing of open cracks in asphalt mastic,” if the surface gets overheated, it will affect the mechanical properties of bitumen; therefore, researchers have concluded the optimal heating temperature of the mixture is 85°C, and by introducing a resting period, the adverse impact can be avoided.
One of the reasons behind an asphalt pavement’s distress is the oxidation of the bitumen’s volatile content. Some reports, such as “Natural Solution Restores High RAP Performance” in this publication suggest the use of a rejuvenator, which can restore the properties of oxidized asphalt binders and extend the asphalt’s pavement life.
Studies discussed in Jun-Feng Su et al., 2014, suggest that 10 μm or smaller microcapsules are unsuitable for the self-healing process because they don’t contain enough rejuvenators to treat the asphalt binders. To control microcapsules’ size, the regulation of the core/shell ratio is important by modifying the prepolymers and emulsion stirring rates.
Although the self-healing process is an innovative and unique solution to a century-old problem, the research is still elementary. Therefore, its use isn’t going to be mainstream, but it holds the potential to save billions of dollars every year on road maintenance.
Safe and maintained roadway infrastructure is a key factor in reducing car accidents. To do that, we must detect and treat pavement distresses. Considering all the new research and technological advancements, it can be said that the future of asphalt technology is promising. To see fast improvements, it’s important to invest in the new technology.
– BY DR. RAJ SHAH, DR. FAN GU, MRINALENI DAS
Dr. Raj Shah is a director at Koehler Instrument Company in New York, where he has worked for the last 25 years. A Ph.D. in chemical engineering from The Penn State University and a Fellow from The Chartered Management Institute, London, Shah is also a Chartered Scientist with the Science Council, a Chartered Petroleum Engineer with the Energy Institute and a Chartered Engineer with the Engineering council, UK.
Dr. Fan Gu is an assistant research professor at the National Center for Asphalt Technology at Auburn University. He earned his Ph.D. from Texas A&M University, specializing in asphalt pavement design and asphalt materials characterization. He is a registered professional engineer in the state of Texas.
Mrinaleni Das is a student of chemical engineering at State University of New York, Stony Brook.
The authors would also like to especially thank Ms. Gabrielle Massoud for reviewing the article.