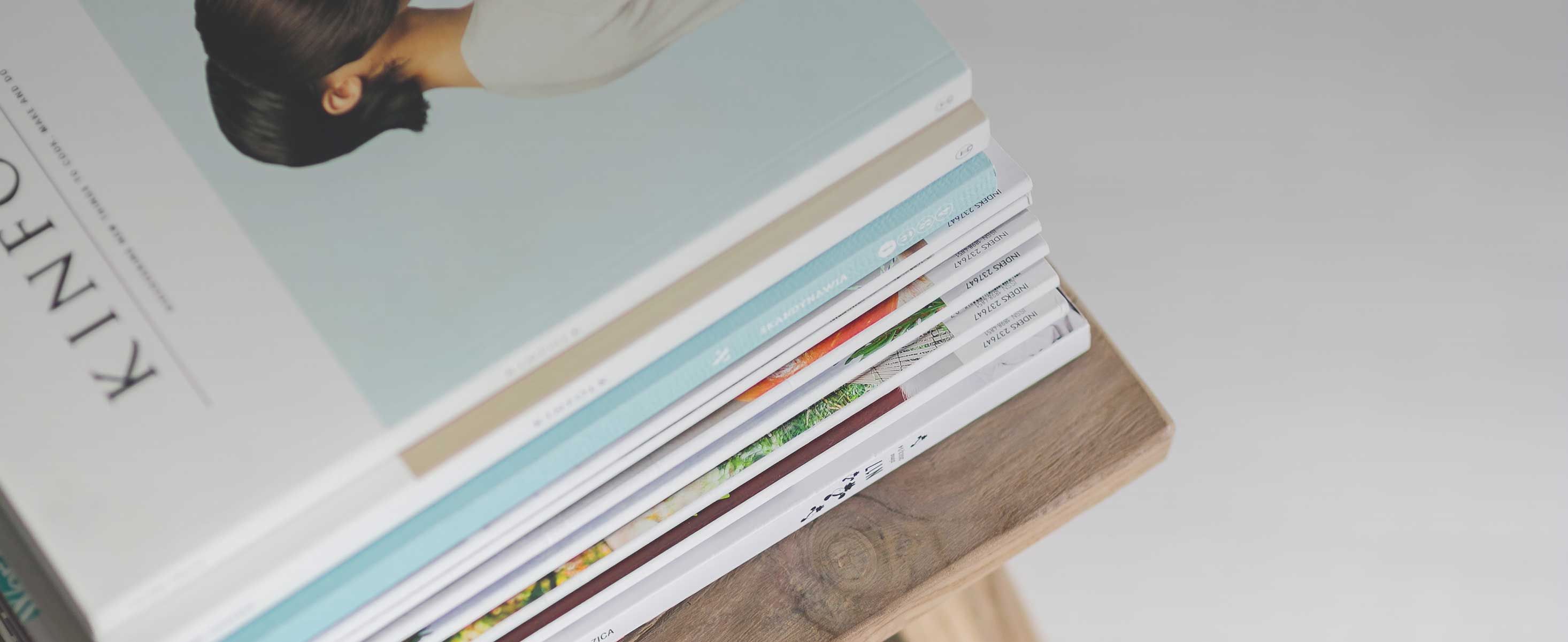
3 minute read
Calculate the Cost of Occupational Injuries & Illnesses
BY ASPHALTPRO STAFF
From increased productivity to simply being the right thing to do, there are many reasons to prioritize safety on the paving train or at the asphalt plant. But reducing workplace injury and illness is also a matter of profitability.
The Occupational Safety and Health Administration (OSHA) aims to make it easy for companies to estimate the cost of workplace injuries with its Safety Pays online calculator. This includes both direct and indirect costs, as well as the estimated sales a company might need to make to recover these costs.
According to OSHA, Safety Pays does not set a new standard or regulation, creates no new legal obligations, and information entered into the tools or calculated by the tools is not captured by OSHA. “[The tool] is intended to help raise employers’ awareness of the impact of occupational injuries and illnesses on profitability,” the Administration writes. More privacy information is available in the Department of Labor’s Privacy and Security Statement.
How Does the Safety Pays Calculator Work?
Employers can use the Safety Pays tool in several ways, depending on the information they have available, though OSHA says the tool will be most useful if the user has a recent record of their company’s workplace safety performance. For example, if you fill out OSHA Form 300A, you can enter the rate/100 of injury and illness cases per year. If that information is unavailable, the user can either enter the number of injury and illness cases per year or use the industry average for businesses in their North American Industry Classification System (NAICS) code.
Then, the user inputs how many of these cases included days away from work, work restriction or job transfer, either the rate/100 from OSHA Form 300A, the number of lost-time cases per year, or the industry average based on NAICS code.
Employers can further customize the data they input with their profit margin, type of workers’ compensation insurance, deductible amount, actual workers’ compensation costs per year, and actual indirect costs per injury. Then, Safety Pays will calculate both direct and indirect costs of workplace injuries and illnesses.
For users who don’t have company-specific data available, the tool can still be useful to learn about a company’s potential burden based on the likelihood of an injury occurring in your industry for a company of your size and to explore the potential costs of a typical injury in your industry.
For example, a company with 100 employees in the construction industry has an expected annual cost of $197,000 ($110,000 indirect costs and $87,000 workers’ compensation claims/direct costs). Top performers in the construction industry experience annual costs of $22,000 in direct and indirect costs.
According to OSHA, indirect costs are often inversely related to the seriousness of the injury. “The less serious the injury the higher the ratio of indirect costs to direct costs,” the Administration says. “While they may account for the majority of the true costs of an accident, indirect costs are usually uninsured and therefore, unrecoverable.”
Indirect costs might range from wages paid to injured workers for absences not covered by workers' compensation and training costs for a replacement worker to administrative time spent on that injury or even repair of damaged materials or machinery, to name only a few. The estimated indirect costs do not include potential OSHA fines, third-party liability and legal costs, worker pain and suffering, and/or the cost of related bad publicity.
What is OSHA’s Individual Injury Estimator?
Within OSHA’s Safety Pays toolkit is a second calculator that can be used to estimate how much a specific injury could cost a business and its impact on a company’s profitability.
To use the individual injury estimator, the user chooses an injury type from a drop-down menu of 40 injuries or enters their workers’ compensation costs, the company’s profit margin and the number of instances of that injury.
From that information, the tool uses the average direct and indirect costs of a given injury or illness, along with the company’s profit margin and an indirect cost multiplier, to project the total costs of the injury as well as the amount of sales a company would need to cover those costs.
For example, a single burn injury for a company with a profit margin of 3% results in a direct cost of $47,192, an indirect cost of $51,911, and requires an additional $3.3 million in total sales (given the 3% profit margin). An instance of hearing loss (occupational disease or cumulative injury) has a direct cost of $18,828, an indirect cost of $20,710, and requires $1.3 million in total additional sales.
“This tool can support you in fulfilling your responsibility to your workers’ safety and health,” OSHA writes. “You can also use the Safety Pays tool to explore the value of implementing workplace safety and health practices that keep your employees safe while lowering costs due to work-related injuries and illnesses.”
Safety Pays uses data on workplace injury costs compiled by the National Council on Compensation Insurance Inc. (NCCI), which manages the nation’s largest database of workers compensation insurance information. Indirect cost estimates are from the Business Roundtable publication, Improving Construction Safety Performance. For additional information on how the calculators work, see Background of the Cost Estimates available within each calculator.
Additional Resources
OSHA also highlights two additional tools to help calculate injury costs. This includes the Center for Construction Research and Training (CPWR) online ROI Calculator (www.safecalc.org), which allows contractors to input cost data to estimate their potential return on investment from implementing a safer work practice, material or tool. There’s also the ASSE Business of Safety Committee works, which aims to show how safety, health and environment investments can impact an organization’s profitability.