WORKING SMART
EMBRACING BEST PRACTICE & THE OPPORTUNITIES
NEW TECHNOLOGIES BRING
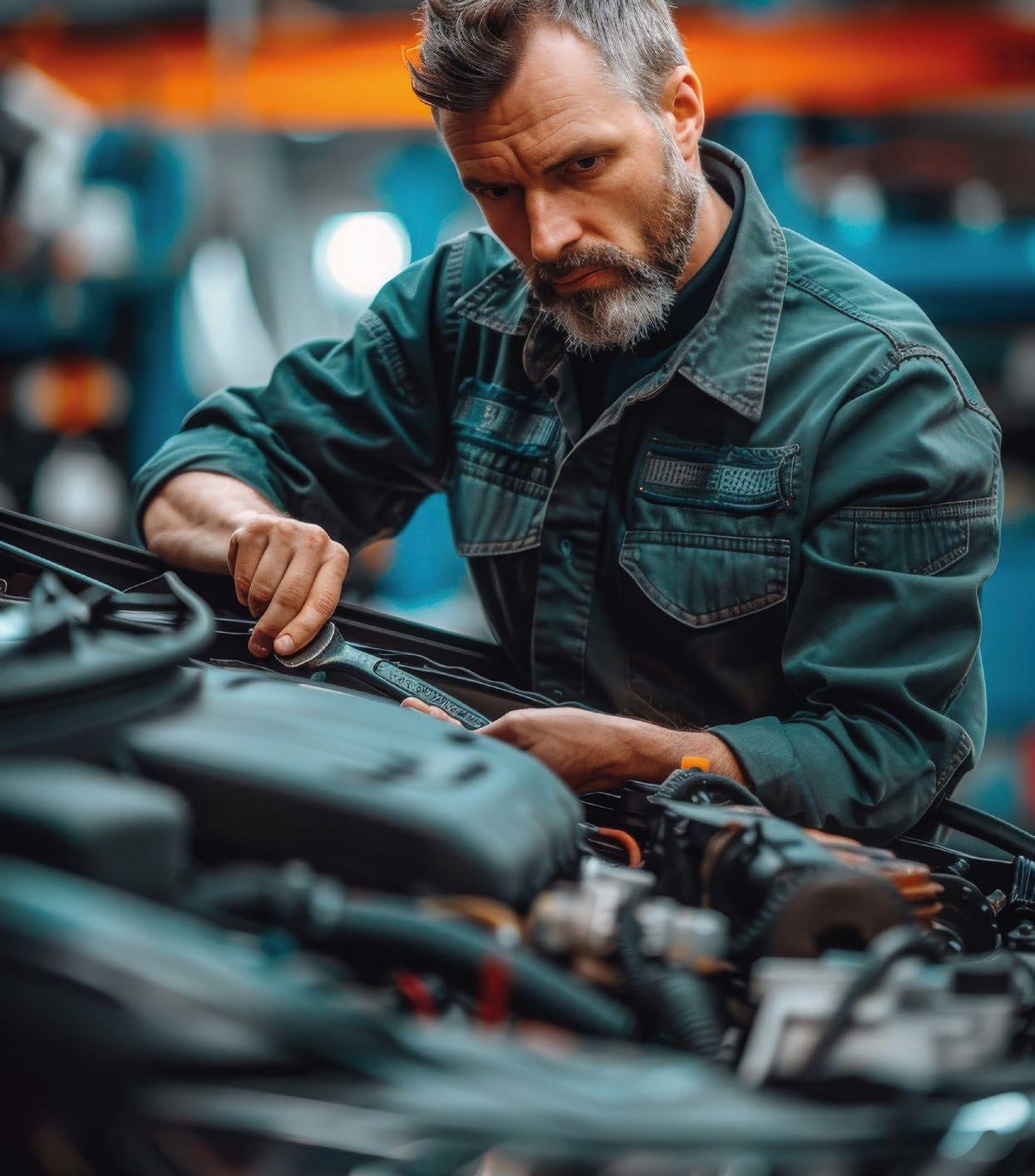
Includes: Clutches, Chassis repairs, Lighting, Batteries & Chargers & more
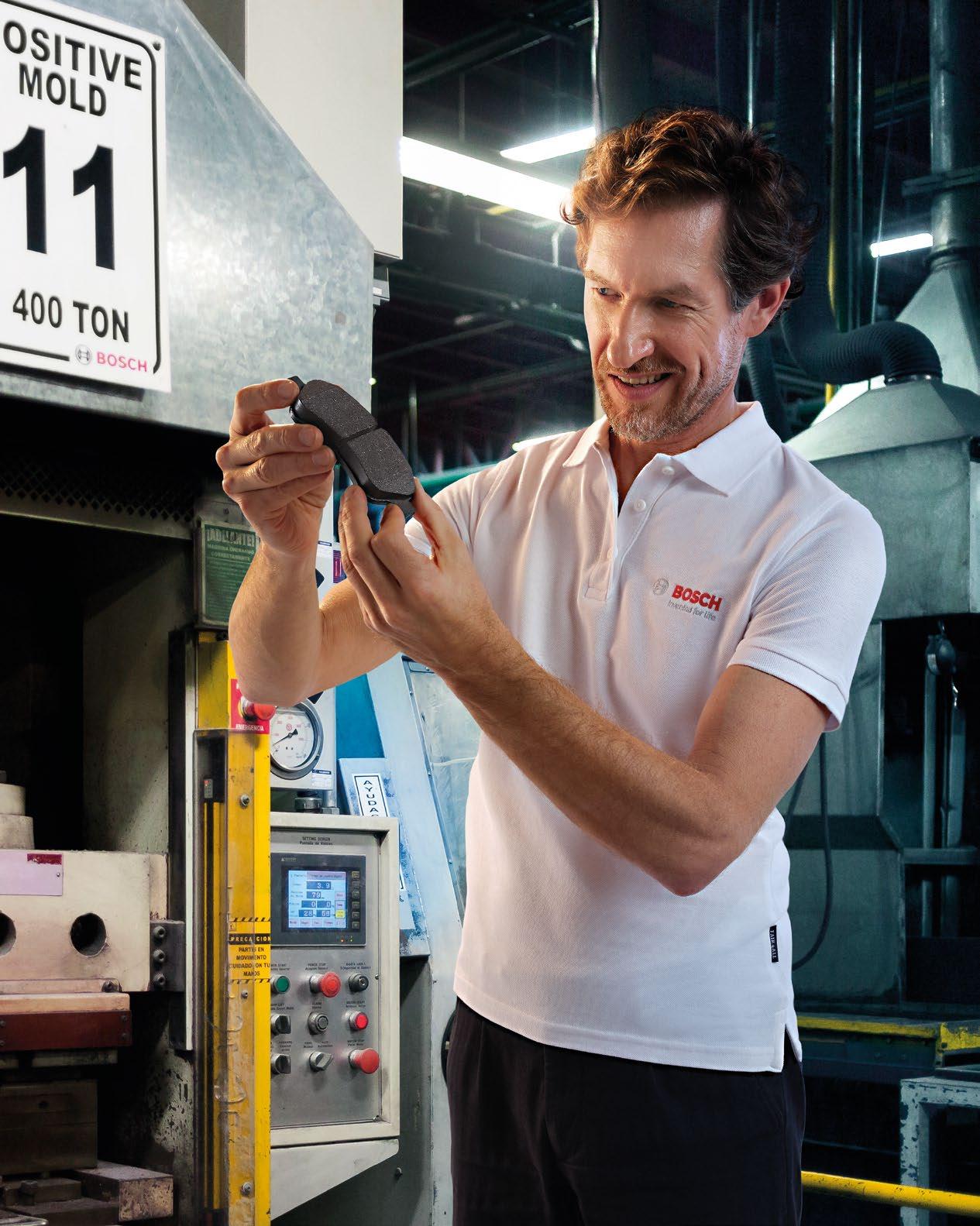


EMBRACING BEST PRACTICE & THE OPPORTUNITIES
NEW TECHNOLOGIES BRING
Includes: Clutches, Chassis repairs, Lighting, Batteries & Chargers & more
In our first issue of 2025, we focus our attention on working smart and embracing new technologies and the opportunities they bring in the areas of clutch replacement, chassis repairs, lighting and batteries.
We talk to AJ Fleetcare in Leeds about how they went the extra mile in their customer service, resulting in winning the National Garage Star Award and the Motor Ombudsman shares insights from its annual workshop survey, providing a snapshot on what garage owners believe the year ahead holds for their businesses.
We kick off the new year with a case study from our new contributor Neil Currie, who emphasises the importance of adding an extra step in the diagnostic process.
The printed March issue will focus on filters, oils & additives, exhausts & cats, and braking – if you have any repair tips to share, please get in touch!
Wishing you a prosperous 2025!
Nicola St Clair Editor Nicola@autotechnician.co.uk
* View and download previous digital issues at: www.autotechnician.co.uk
instagram.com/autotechnician_magazine youtube.com/@AutotechnicianMagazine facebook.com/Autotechmagazine bsky.app/profile/autotechnician.bsky.social
After 11 years of service, the Original Equipment Suppliers Aftermarket Association ceased operations at the end of 2024. OESAA launched in 2013 to highlight disparities in the quality of replacement parts and evolved to support independent workshop owners and technicians with training initiatives.
The body curated the series of AutoInform events, hosting several weekend events at the GTG training centres in Wolverhampton and Glasgow, providing insights on best practice, diagnostics and new technology.
OESAA Chairman, Nigel Morgan, who spearheaded the creation of the organisation, says: “We are immensely proud of the part OESAA played in elevating the standards of the industry, raising awareness about the benefits of OE-quality parts, and strengthening trust between suppliers, distributors and technicians.
“While OESAA will close, my hope is that our members will continue to independently advocate for premium solutions, support their customers and work in partnership with the next generation of automotive stars to ensure the aftermarket has a prosperous future."
IGA follows up call for review of MOT fee cap
The Independent Garage Association has continued its lobbying efforts, highlighting the significant financial strain caused by the stagnant MOT fee cap, which has remained unchanged for over 14 years.
Read the article here
Castrol will hold its first-ever conference for its Castrol Service workshops on 21 March 2025 at the Celtic Manor in Newport, Wales, bringing over 260 UK and Ireland-based workshops together to learn about its latest offers.
Sessions will cover digital marketing and how best to manage fleet business. Exhibitors will include Garage Hive and SAMOA Workshop Equipment.
The conference will conclude with a gala dinner with a range of entertainment, including the presentation of the new ‘Forever Forward Awards’, which recognise the achievements of businesses within the Castrol Service network. The awards will be in five categories including social media, building community and customer experience. The Forever Forwards Garage Award will also recognise a workshop that excels in all aspects of business, while the Castrol Spirit Award will reward a workshop that puts Castrol’s vision and values at the heart of their operations. Attendees will have the chance to nominate their own businesses across the five categories.
To learn more about the Castrol Service Network, how you can be a part of it, and to come along to the event, click here
If you’re already a Castrol Service workshop and would like to attend, register here
AT talks to Jeanette Landale, co-owner of AJ Fleetcare in Leeds (above centre right), to find out about the customer nomination that resulted in their National Garage Star Award and what this win means to their family business
In December, The Motor Ombudsman announced that AJ Fleetcare, an independent garage in Leeds, had been crowned the 2024 winner of the National Garage Star Award – the top prize in the Ombudsman’s annual competition. Now in their fifth year, the competition allows consumers to put businesses accredited to one or more of The Motor Ombudsman’s four Codes of Practice, or individual staff members, into the spotlight, for going the extra mile to deliver an exceptional level of service.
The family-owned business in Yorkshire was amongst the 3,262 online nominations that were submitted by motorists throughout the UK. These are short accounts from consumers, who put their ‘stars’ forward following acts of kindness and generosity and highlight gestures that went beyond what would normally be expected of staff, and which ultimately made a significant difference.
AJ Fleetcare emerged triumphant, with judges commending the business for their caring and altruistic support of a customer who was facing challenging circumstances looking after a relative, which saw the garage fix their customer’s vehicle at very short notice, whilst they also paid for a taxi fare to minimise inconvenience and keep the customer mobile. This was coupled with a thoughtful gift on the handover of the repaired vehicle, alongside words of reassurance.
AJ Fleetcare joined the Motor Ombudsman four years ago, drawn to the industry advice they provide and the benefit or their arbitration service, which steps in when a workshop and customer cannot find a solution when a dispute occurs, something they hope they never have to use, but is something that gives their customers’ confidence and co-owner Jeanette believes confirms their status as a reputable garage.
Read the full article here.
GSF Car Parts' National Distribution Centre is the most obvious step made to enhance customer convenience. 96% of all parts will be supplied through the NDC, exhausts being notable exceptions.
Realising that not evolving kills businesses but charging ahead like a whirlwind can prompt upset customers to switch their spending allegiances, Rob Marshall visits GSF Car Parts' National Distribution Centre, to see if its new owners are delivering the right kind of change
Determined to arrest years of underinvestment, the new management team has injected £101m this year to 'supercharge' GSF. This has funded a 500,000 sq.ft National Distribution Centre in Wolverhampton, West Midlands, employing over 400 people, supplying over 100,000 parts, feeding over 190 (and growing) nationwide branches, with a further 3,000 staff. Also new is more accurate OE-data-based parts cataloguing (Master Cat with WhatApp for Business) and a Trade Hub App. Investment on the ground has delivered younger and more reliable vans and flexible delivery means, including motorcycles and e-bikes.
Beyond figures
It all sounds very impressive and it is. Yet, figures mean nothing, if they do not deliver benefits. The aim is to make customers' lives easier but GSF's strategy has not sacrificed traditional values. In today’s AI-driven world, holding many millions of pounds in stock is not just costly but also unfashionable. Yet, GSF has done just that, reasoning that workshops prioritise delivery reliability and accuracy of delivery above gimmicks and even price. Crucially, people remain in charge, not bots. Instead, technology is employed judicially to bring benefits for customers, including live parcel tracking, Electronic Proof of Delivery and immediate account credits on returns. GSF Car Parts also shuns the modern practice of centralisation (such as that epitomised by the banking industry), by growing its regional branches, giving them autonomy, while supporting them with tools they need to maintain decent stock levels, including daily overnight deliveries that take away returns and even unwanted packaging for recycling.
GSF Car Parts feels that its latest transformations will provide the right people and systems that will deliver easier parts procurement for workshops. With over 20% growth recorded thus far during 2024, the changes appear to be delivering.
92% of GSF's sales are made to the motor trade, with a focus on independent workshops
While GSF Car Parts has invested in technology, it has not lost its people focus. The National Distribution Centre might not be automated but the firm reasons that its methodology provides maximum parts availability and accuracy.
For over 20 years ACTRONICS has been at the forefront of our industry developing sustainable remanufacturing solutions for you.
Our solutions are a cost effective, environmentally friendly alternative to replacement parts. Our Plug & Play solutions ensure a top-quality service backed by a 2-year warranty
Leadership extends beyond management and the aftermarket must move forward together were just two messages from the well-attended IAAF Annual Conference
Did you not manage to make the IAAF Conference and dinner? Well, cool it! Rob Marshall was present, notebook in hand, to give you the latest advice on how to be an everyday leader
Raising standards might sound like a cliché but it benefits not just your workshop but also the wider industry. The IAAF reasons that you can achieve this by being an 'Everyday Leader' and its speakers provided rays of inspiration to a packed conference room in Milton Keynes on a damp December Thursday.
GiPA's Quentin Le Hetet kick-started proceedings with key insights about why the Right 2 Repair campaign is so important. He revealed that, while cars on UK roads are becoming older, the rate will slow from 2026. GiPA foresees rapid growth in the proportion of cars aged under five years from 2026 onwards.
The subsequent panel discussion saw Neil Pattemore (IAAF) highlighting the UK aftermarket as comprising 60% of the whole UK automotive sector, worth £56 billion. Mark Field (IAAF) reasoned, therefore, that the aftermarket must work together to be effective and not fragmented groups.
Thankfully, this is happening, proven by Motorvate's launch. Comprising a not-for-profit automotive careers, skills and recruitment initiative, Motorvate is being planned and organised by the Automechanika Birmingham team. It will also focus on fun and social-type events that, as part of its partnership with World Skills UK, will look also at the future of the motor industry. For more information, click here
Looking into the future was a major theme of James Poulter's analogising of AI. With brains (knowledge), gut (instinct about whether something is correct, or not) and hands/feet (human touch), he implored garage AI users not to let the technology overtake the personal element.
Nigel Owens, MBE, the 2015 Rugby World Cup Final referee, gave a passionate speech after lunch, reminiscing about the struggles of being a young homosexual adolescent in a remote Welsh town. He attributes his career success to becoming more comfortable with himself, after attempting suicide. His message to garages was clear – people work best, when they feel comfortable and are accepted. Interestingly, he rejected workplace quotas, highlighting that recruiters should prioritise the best person for the job. IMI Diversity Task Force: take note.
Following Mr Owen's emotional roller-coaster was the plea for help from the Intellectual Property Office over counterfeit parts. The IPO called for aftermarket professionals to show leadership, by raising the profile and creating leads for the authority to investigate, as part of its ‘Fake Always Breaks’ campaign. You can do so, by reporting instances to local Trading Standards, or to enforcement@ipo.gov.uk. Further information can be found here.
From the UK to the EU, FIGIEFA followed, by Álvaro de la Cruz outlining its work by renewing and mandating the Motor Vehicle Block Exemption Regulations. Danny Tregaskes, from The Motor Ombudsman, followed. He advised garages how to show leadership, when tackling customer complaints. Interestingly, out of £15m of claims, only £3m were paid out, indicating that consumer demands can be unreasonable. It was unfortunate that these final two presentations were rushed, allowing the conference to finish on time, which numbed their effectiveness. Even so, this did not detract from a highly worthwhile event.
Results from the Motor Ombudsman’s latest annual survey or workshops highlight rising operational costs, taxes and utility bills to pose the biggest challenge for 89% of repairers, 14% higher than last year’s predictions.
The research found that over half of repairers (56%) are expecting motorists to cut back on essential repairs in a bid to save money, with 48% forecasting vehicle owners will forgo ad hoc and routine maintenance, such as servicing, to cut running costs in the shorter term.
With this set to add to the pressure on customer footfall and the bottom lines of workshops, the impact of rising costs will likely be felt further with the price of parts also on course for an increase, according to just over half (52%) of those polled, due to factors including ongoing component shortages and inflation. Around four in ten (42%) of those questioned said they will try to avoid passing on these heightened expenses to consumers in 2025 as the cost of living remains front of mind for many.
Close to half of repairers that were surveyed (48%) said that recruiting personnel would be a hurdle this year and when questioned specifically in relation to staff challenges, the majority (55%), said that they had to raise pay cheques in 2024 to both attract and retain existing employees.
The Ombudsman highlights that adverse trading environments can often bring new opportunities, and despite a backdrop of rising costs and skills shortages, just under half of respondents (42%) explained that they still plan to invest in the refurbishment of premises, with a slightly smaller proportion (39%) stating an intention to grow their workforce. In addition, during 2025, nearly a third (29%) of respondents explained that they are looking to review their opening hours to offer an improved work-life balance to staff, whilst around a quarter (24%) said that they plan to grow their pool of key suppliers to help drive down possible delays to the repair of customer vehicles.
Bill Fennell, Chief Ombudsman and Managing Director of The Motor Ombudsman, said: “Our latest survey of businesses in the service and repair sector shows an interesting juxtaposition of rising costs to operate on the one hand, and less revenue due to consumers delaying repairs and maintenance on the other, thereby setting the scene for a more challenging trading environment. This, of course, may be amplified by continued difficulties recruiting qualified staff to meet customer demand, meaning some significant headwinds persist this year for the nation’s garages and workshops.” Bill added: “However, amongst the possible hurdles set to be faced by businesses this year, there are positives to take away from the study in that there is still an appetite to invest to provide an even better customer experience."
Autotechnician magazine has teamed up with leading independent Electric Vehicle training provider Pro-Moto to offer a group of 20 technicians hands-on fault-finding experience on electric vehicles within its workshop, located in Ash Vale, Surrey.
The day is suitable for those with minimal or no experience working on EV’s, as well as those who have attained Level 3 or 4 and would like guidance on battery and charging faults and more complex EV-specific tasks not yet experienced within their own workshop.
When will it take place?
9.30am to 3.30pm, 29th March 2025
Where?
Pro-Moto, Unit 4 LDL Business Centre, Station Road West, Ash Vale, Surrey, GU12 5RT
What to expect on the day:
Hands-on experience
Review of common faults
Battery and charging faults
Parking, lunch and refreshments included.
Spend the day with us and immerse yourself in EV Technology! Just 20 places are available. Early bird rate of £138 inc. VAT if booked before 25th January 2025, £174 inc. VAT thereafter.
Head to https://autotechnician.co.uk/training/ to book your place now!
By Neil Currie AMIMI
Firstly, I’d like to introduce myself to those who don’t know me. My name is Neil Currie and I am a technician from Southwest Scotland. Some of my achievements include becoming an IMI-accredited Master Technician, a Level 4 EV Technician, and winning Top Technician in 2019. I’m excited to contribute articles to autotechnician and hope to meet some of you at an event in the future.
This article highlights a possibility that now needs to be considered and added as a step in your diagnostic process when addressing a drivability fault or when things may not quite add up. What is it, I hear you ask? Well, I am not going to spill the beans just yet, so read on to find out what I am referring to…
The vehicle in question for this article was a Land Rover Discovery Sport with the 2.0 Ingenium diesel engine. The vehicle had been booked in from another garage with the complaint of the engine management light randomly illuminating on the dashboard. When they plugged in their scan tool, it showed an EGR valve fault. This vehicle has a Euro 6 engine fitted with both low and high pressure EGR valves, and they were unsure what the fault referred to and wanted me to take a look. The garage explained that the fault would clear and the vehicle would then drive fine for days, sometimes weeks, before the light appeared again. There seemed to be no rhyme or reason to it. They suspected a faulty EGR valve but were not confident, so they opted to book it in rather than replace parts based on a guess.
The vehicle was brought in with the light illuminated and the fault code stored in the memory. Carrying out my own checks to confirm the complaint did indeed find a fault for an EGR valve, however it did not say which one. Checking the DTC number against Land Rover's information portal Topix, showed the fault referred to the high-pressure valve. I then decided to look at some live data to see what was going on. Bringing up EGR data showed a discrepancy right away. Upon starting a modern diesel engine at idle, we should see a command from the engine ECU to open the EGR valve. It won’t be fully open, as this would choke the engine, but a small percentage to start recycling exhaust gases to reduce the dreaded nitrogen oxides (NOX). However, on my vehicle, there was no command from the ECU at idle, at any point. I then took the vehicle for a road test and found it was not activated at any stage, which is clearly wrong.
This EGR valve also uses a position sensor for feedback to the ECU to show that it has indeed moved to the position it was told to move to. Previously, the ECU just presumed it opened after checking air mass, but with ever-increasing tighter emission limits, everything related to emissions must be monitored to ensure it has actually done what it was told to do. It may have opened, but has it opened at the correct percentage it was told to? Checking the EGR valve position in live data showed that the valve did not move, proving there was both no command from the engine ECU to tell it to do so and no movement from the valve itself. Where do we go from here? Is this an engine ECU fault? It cannot be a broken wire, as the output would still be sent, which we would be able to see in the data PIDs, it would just not make it to the valve. It could be a shorted wire, but the fault code did not indicate a short, high or low. I noted the fault code and cleared it to see if it returned immediately, as anything critical to emissions should, but it did not. I now had no stored fault codes and no warning lights illuminated, even after taking the vehicle for a road test – this matched part of the customer complaint. The garage also mentioned that the warning light would sometimes clear itself after cycling the key, which was interesting.
I decided the next step was to unplug the valve itself and see if the ECU then logged an open circuit code to show that it was capable of seeing a change in state. However, upon unplugging the valve and rechecking for faults, no fault codes appeared as before. This is clearly wrong, as the ECU monitors the circuit closely and will always log a fault code when the connector is disconnected, as that is how the circuit is designed to operate. This now brings me back to my introduction and that extra step to consider adding to your process: checking for a remap and the possibility of components being "mapped out" with tuning software. I now had proof to warrant updating the software to rule this out, as there is no point in continuing with the diagnosis if the vehicle is not standard. I say "update," as if there is an update available and it is loaded into the ECU, it will wipe the "map" and return the vehicle to standard specification. This depends on the manufacturer though, as some will not allow this if the software is already at the latest version. In that scenario, a stock file would need to be loaded onto the ECU via other means and tooling.
I contacted the garage to advise them of my findings and to ask permission to update the software and recheck the system for correct operation. They authorised the update and to recheck afterward. In the case of Land Rover, on certain control units, they allow you to load software into the control unit, even if it is the same version already installed and no newer version is available, which can be handy in certain scenarios. This applies to older vehicles using the factory scan tool SDD, I cannot comment at this moment whether this is still the case using their new platform, Topix Cloud. The vehicle had a newer software version available anyway, so I loaded the software in, cleared all the codes set from programming, then started the vehicle to be met with a shiny management light on. Reading the fault codes showed two codes stored (Figure 1).
This proved, without a doubt, that the software had been modified, as the second code showed unauthorised software had been detected even though it was now back to standard software. Additionally, the EGR code had changed and now showed a circuit low code. After a short while, the found code that was logged when I first checked for trouble codes was also logged, so I could now move forward with diagnosing the problem.
Rechecking live data now showed the ECU commanding the EGR to move, however, after a short period of idling, the position did not move as expected. The ECU then started increasing the percentage higher and higher until, finally, after not seeing a change at all after demanding 100 percent, it logged a fault code and shut off the EGR valve command. The reason the control unit does this is that it presumes the valve is partially stuck, normally due to carbon deposits stuck to it. The ECU then increases the opening command value gradually to attempt to move it and free the valve. However, if no valve position change is noted after commanding it fully open, it shuts off the command and logs a fault as something is not right with the operation. Some manufacturers will even "shake" the valve on engine shutdown to attempt to clean the carbon off, Ford springs to mind immediately, and it’s common to hear the EGR valve cycling fully open, then fully closed, then open again multiple times when the key is turned off.
So now I had to find out why the ECU was not happy with the EGR valve. Next, I decided to test the valve itself and the control signals from the ECU due to no change in position when commanded. Firstly, I checked the EGR valve motor resistance; if this was incorrect, the valve would not move regardless of being commanded to do so. Upon connecting my meter across the two motor pins, it read over 100 Ohms. For a motor like this, I would expect only a couple of ohms, so the valve itself was faulty and required replacement. I then informed the garage that it required an EGR valve and moved onto my next job, as it was a busy day with lots to do, I decided not to test the control signals since I had found an issue—something I would later regret!
Unfortunately, the valve was only available from Land Rover and was on backorder, so the vehicle then sat for several weeks awaiting the new valve. After it finally arrived, I fitted the new valve, cleared the faults and started the engine, confident all would be well. Imagine my dismay when the engine management light popped back on, and upon reading the codes, it still showed an error for the EGR valve I had just replaced.
Recovering my steps, the new valve showed 2.5 Ohms of motor resistance, which was as it should be; however, the ECU was still not happy. I then hooked up an oscilloscope and checked the incoming control signals to the motor, and it was not as expected. On the two control wires, one showed a command from the ECU as expected, but on the other, I had nothing whatsoever. In hindsight, I really should have checked the signals from the ECU after condemning the faulty EGR valve like I planned to do in the previous paragraph for a full diagnosis. However, having found an issue and being busy in the workshop, I was happy this needed rectification and believed this was why the component had been "mapped out." Maybe that is just me being too self-critical, but the valve was indeed faulty, so it had not been replaced for nothing. It is not that common, in my experience, to have two faults on the same component, but you can never say never!
I then stripped some panels to access the engine ECU, as now we had command. The only cause could be a wiring issue, and I needed to check the wire end to end. This meant accessing the necessary engine control unit multi-plug and testing from it to the EGR valve connector. Upon testing the wire with my meter for continuity, I had a reading of OL, which proved it to be an open circuit.
3-5 June 2025
NEC Birmingham
Only 15% of stands remaining
The event presents a unique opportunity to showcase your brand, products and services to over 15,000 automotive professionals. Attendees include garages, motor factors, body shops, retailers, dealerships, and detailers—all at the UK’s largest automotive aftermarket trade exhibition.
Book your stand today!
Following the loom visually, I found it went down and around the battery tray and air box from the EGR valve, so both were removed for a better look. Upon gaining better access and having a good visual inspection first, I found the loom had rubbed on something (Figure 2).
Upon moving some cables around, I found the cause (Figure 3): a bolt had not been tightened fully, making it sit higher from a previous repair. The vehicle had not been reassembled correctly, either, with the main harness not clipped into the top of this bolt to hold it securely. Upon carefully opening the loom at this point, I found a broken wire that matched the colour of the wire I had been testing. Checking from this break showed continuity to each connector, proving it to be my wire. I then proceeded to repair this wire and a couple of others that had also been damaged and insulated them. I tightened the bolt in question and re-secured the loom correctly to prevent a recurrence. I then reassembled the battery tray, air box, and ECU, and rechecked my EGR operation after clearing the stored fault codes. Viewing live data now showed what I wanted to see: upon being commanded, the EGR position now increased and decreased as told, and no warning lights were displayed on the dashboard. Taking the vehicle for a thorough road test showed it performed as expected, with demanded and actual positions matching perfectly.
One thing to add is that the unauthorised software fault would not clear, however, no warning lights or messages were displayed. Upon reading the setting criteria from Land Rover, it explained that when logged, the fault cannot be erased as it is a permanent trouble code set in the EPROM for traceability only. I can only presume this is for when the vehicle is under warranty, allowing the manufacturer to see if the vehicle has been modified, which would then obviously void the warranty.
Figure
I have been advised since repairing the vehicle that tuning companies can now remove this fault code, which again proves why you should add checking for modified software to your process. Without this code set and the strange behaviour I experienced from the control unit, it could be very easy to go down a path and make a misdiagnosis. Fitting a new ECU in this case would have fixed that part of the fault but with ever-increasing costs and chip shortages/backorders affecting the trade, I feel the need for accurate and correct diagnosis is now more important than ever.
Improve your clutch replacement abilities, by taking advantage of the support offered by quality brands and suppliers
Some workshops view manual transmission clutch work as elementary and yet, many technicians do not take advantage of the support available to them. Rob Marshall, therefore, asks major clutch brands how they help you with this laborious job.
As important as keeping abreast of new technologies is, try not to neglect bread-and-butter tasks. ZF Aftermarket told us that, while clutches are viewed as 'sunset' components by some workshops, its technical support team remains extremely busy, helping stuck technicians. While it is true that the clutch's core function remains unchanged, the technology behind today's components continues to evolve behind the scenes. Alliance Automotive reminds us that the basic principles of mechanical parts can be taken for granted, especially regarding clutch failure diagnosis. It joins ZF, by advocating clutch 'refresher' training courses as highly valuable and any wise technician should not dismiss such opportunities. Valeo is an even greater supporter of technician clutch training, not only because clutch repairs will continue to be in demand but also because the firm will be introducing Pendulum DMFs, E-Clutches and Torque Limiters into its range later this year.
With reports indicating a bleak outlook for the UK economy, customers are likely to continue their march to squeeze costs to a bare minimum. While the aftermarket offers superior value propositions than franchised workshops, even we must consider when things go too far and present a risk to your business. The bilstein group reasons that, because parts cost can be a deciding factor, it can be tempting to fit cheaper clutch kits to suppress costs. It asks workshops to consider that quality parts are integral to a quality repair solution, meaning that selecting low-cost, low-grade parts is an ill-thought-out false economy move, due to the hours of labour involved with a typical clutch change. ZF highlights that, should the customer not be aware that you are selecting a budget part
Are you missing out on a valuable profit opportunity by sending semi-automatic gearbox work to a ‘specialist’? Do you know that the latest semi-automatic vehicles are equipped with easily repairable double clutch systems?
LuK double clutch transmission systems can be found in an ever-growing number of popular vehicles, in both wet and dry versions. They can be serviced and repaired with just a little bit of know-how from us, along with the correct tools and a LuK 2CT repair solution from your local parts distributor.
We also offer an advanced 2-day IMI certified training course so you can add double clutch repairs to your service menu and stop turning money away!
www.repxpert.co.uk | https://vls.schaeffler.co.uk |
at the quotation stage, you risk difficult conversations later, should a problem develop. While this may not mean total failure, poor driving experience (such as judder, excessive slip and/or a weighty pedal) may spark a customer complaint and, potentially, a demand that you change the clutch at your cost.
Many workshops realise this but it is easy to be tempted away from established brands. Do so at your peril. As an example, Valeo says that its OE-quality clutch kits employ advanced friction materials, assembled with precision, so that technicians can deliver a quality repair and uphold their reputation. Sachs clutches, sold in the aftermarket, benefit from ZF's OE expertise and possess an unlimited-mileage two-year guarantee. Alliance Automotive says that strict auditing of its suppliers' manufacturing and testing procedures ensures that it can claim confidently that its 'NAPA'-branded clutches perform at least as well as the original part. Its self-assurance is reinforced by a 3-year/36,000-mile guarantee. Naturally, such features come at a cost and it would be impossible to provide all of these advantages, using the cheapest materials, with as much cost cut as possible from the manufacturing process.
Alternatively, a customer might try to shave a few quid and provide a clutch for you to install and it is interesting to canvass opinions from the clutch brands, rather than retailers. Blue Print advises that this situation is risky for workshops: should there be a fault with the part supplied, the onus is on the installer to rectify the situation, a problem about which some garages are unaware. Valeo says that, aside from the quality threat, customer-supplied parts can void warranties, leaving garages liable for failures that are not of their doing. Of course, it is also possible that the customer supplies a clutch that does not fit, leaving you further in the lurch, with an immovable car occupying a ramp, until the correct part arrives. ZF recommends strongly that technicians install parts that have been supplied by an authorised retailer, because counterfeit and poor-quality car parts are rife and represent a genuine safety concern, especially if they have been obtained through an unregulated source, such as an online marketplace. Alliance Automotive agrees but highlights exceptions, such as when the customer has sourced a premium upgrade clutch from a performance specialist, such as UniClutch. Some classic car clutches are also hard to find, although the First Line brand, Borg & Beck, reports that this is a growing part of its portfolio.
Common clutch replacement errors are common with technicians, unfortunately.
Whichever brand you choose, research the support available. Blue Print has a YouTube channel for its replacement clutches and 'Smartfit' conversion kits. These are in addition to its 'Protips' advice, available on the bilstein group's partsfinder website.
White-box parts can also be a false economy, due to the absence of an adequate after-sales back-up. ZF highlights its free-to-join [pro]Tech start network, which includes technical bulletins and OEM campaign information, not forgetting the Sachs technical support team, mentioned earlier. Blue Print highlights its in-depth clutch replacement technical articles, while Alliance Automotive focuses on TechMate as its technical partner. Valeo, too, offers strong aftersales support but emphasises its efficient parts supply that minimises workshop downtime and TechAcademy as evidence of its strong investment in training, which covers all types of clutches and transmissions.
While decent parts, from trusted, well-established brands, supplied by quality suppliers, go a long way towards a successful repair, even they cannot do everything. Alliance Automotive, Schaeffler and ZF agree that you should prepare well in advance, have a tidy workspace with the correct tools ready, and all the major parts present. Borg & Beck highlights the importance of cleanliness, too. Valeo reminds technicians not to overlook the health and safety protocols, especially as an average gearbox can weigh 65kgs. This includes reacquainting yourself with proper lifting techniques and that all lifting/support/safety gear is present and working. Do not neglect surrounding components, either. While the brands, within this feature, pride themselves on supplying all of the parts you need to ensure a satisfactory repair, they cannot consider everything, such as crankshaft seals. Therefore, be wary that you may have to order these parts separately, should you find them to be worn. Finally, as the average clutch replacement takes almost six hours, stay cool, allocate sufficient time and do not rush.
Schaeffler reports that the aftermarket is seeing hybrid vehicles (mainly PHEVs) requiring clutch changes. These clutches relate not just to the main transmission but also the secondary clutch that disconnects the engine from the e-motor. This clutch switches the drive power between the ICE and electric motor. In some cases, it can look like a standard diaphragm spring clutch, operated by a conventional concentric slave cylinder, and controlled by an electronic hydraulic actuator. Schaeffler reasons that training in this area should complement training on EVs and hybrids, because these types of power units do not employ 'traditional' clutches. Should you not be aware of these systems, consider adding clutch training to your 2025 New Year resolution list.
It is not just older cars, like this Volkswagen Scirocco, which require steering and suspension parts
While it is hard to predict the future, at least chassis repairs will remain a major source of workshop income, leading Rob Marshall to query leading suppliers about how they make your life easier
It is quite difficult to appreciate the engineering that goes into bolt-on consumable parts. After all, many chassis components, be they related to the steering, or suspension systems, are designed to be renewed. Understandably, it is difficult for most of us to identify an OE-quality track rod end, or drop link, from an inferior one by a curiosity glance. Indeed, a poor-quality part might even fit with no problems but you are sacrificing your reputation and risk having to repeat the task under warranty, when the part wears out prematurely, due to design and/or materials that prioritise manufacturing costs over longevity. This is where the major brands have your back covered. LKQ Euro Car Parts is one such distributor that stocks a range of components to suit differing price points but without allowing OE standards to slip. This range varies from brands that are made by original equipment suppliers, such as ZF's Lemförder, to the Starline aftermarket brand, for which LKQ is the largest European distributor. The bilstein group elaborates that, should you buy unknown parts from an unfamiliar source, you not only can have zero trust in its quality but consider also that you may have no support for warranty or compensation claims, should those parts fail. It states this is not the case with its Blue Print and febi components, which are guaranteed for three years. Alliance Automotive's brands possess the same warranty period and the company highlights its rigorous and regular audits of its manufacturing partners that enable it to do so.
LKQ Euro Car Parts advises that technicians forget to clear fault codes, before installing a replacement steering rack. By not doing so, the code cannot be cleared, meaning that the technician will have to install a replacement rack. Another common mistake involves not flushing contaminated hydraulic fluid from the system, causing the new rack to fail prematurely.
With Motaquip commencing its second decade as part of Comline, its maker told us that the brand's focus on OE performance remains not just unchanged but also refined, due to extra enhancements, such as an electrostatic painting process for extra corrosion resistance. DRiV reassures technicians about the comprehensive engineering processes and multiple durability tests behind those components bearing the 'MOOG' logo. Like Comline, it also has a cataphoresis painting programme but its beyondOE quality refinements include patented part design improvements and enhanced materials, backed with a warranty lasting five years.
Moog says that it supports technicians from the start of the repair process, by making the parts selection process as easy and as accurate as possible. TechDoc is the chosen platform for both Moog and Alliance Automotive's steering & suspension brands (specifically, 'NAPA' and Apec) and both suppliers highlight their expert technical support, both in-person and through a raft of installation guides, designed to answer the most common questions and provide the latest technical advice. Moog says that this information is also accessed via QR codes on its packaging and recommends that technicians consult its Garage Gurus programme for extra tips. ZF Aftermarket directs you to the free ZF [pro]Tech portal, which supports its Lemförder, and TRW brands.
Yet, all of this information should not replace formal training. Due to the safety-critical nature of the chassis systems, First Line recommends that all of its products be fitted by a trained installer, with access to the correct fitting tools. Motaquip agrees, saying that appropriate training prevents common installation errors that can lead to premature part failure. LKQ Euro Car Parts reminds us of its expanding LKQ Academy, through which technicians can access 87 IMI-approved courses to develop either new skills, or facilitate continuous professional development. Moog says that its Garage Guru training provides technicians with the knowledge to make accurate diagnoses of wear patterns in suspension systems, how to avoid common errors and updates on the latest innovations.
Quality brands are also helping technicians, by introducing new chassis parts that assist the aftermarket to compete with main dealers. With not just new electrified models but also a plethora of new brands arriving, those firms are doing an admirable job of keeping up.
New Range - febi is introducing a new line of shock absorbers for Light Commercial Vehicles featuring more than 120 products for popular makes and models. This new range covers more than 18,000 applications and over 90% of the current demand for LCV Shock Absorbers in the Aftermarket.
Fast to Market - Our range is dynamic and constantly expanding to meet the evolving demands of the Automotive Aftermarket. Using direct OE data, we link existing articles into our range to ensure the earliest product availability in the market.
Highest Quality - Every febi shock absorber is engineered to meet OE performance and design specifications, ensuring perfect fit and optimal functionality. Furthermore, all shock absorbers undergo rigorous inspections to guarantee they meet the high-quality standards set by the bilstein group.
One-Stop Shop - In addition to a vast selection of shock absorbers for LCVs, febi offers an extensive range of over 11,000 replacement parts for vans of all sizes and pick-ups. This makes febi the ultimate onestop shop for all your LCV repair needs.
Your No. 1 for Light Commercial Vehicle Shock Absorbers
Scan the QR code to watch the febi Shock Absorber technical video and animation or visit : youtube.com/ ferdinandbilstein
LKQ Euro Car Parts reports that many of its new-torange parts cover both Hybrid and BEVs. Its recent decision to stock upgraded 'MEYLE HD' parts is in response to some carmakers using the same suspension components in both its ICE and heavier electrified vehicles.
Blue Print has also been hard at work, adding an impressive 300 new steering and suspension to its febi range last year; First Line introduced a similar quantity, highlighting strong demand for MG BEVs, for which it caters. More information is available in its online catalogue
Moog has focussed its recent designs on addressing BEV's requirements for stronger but lightweight components. It reports that Hyundai's Ioniq 5, Volkswagen's ID.5, and the Skoda Enyaq have been added to its fold. Alliance Automotive reports that it also has concentrated on newer vehicles, due to increased demand for chassis parts that it attributes mainly to poor UK road conditions. The firm highlights that it will be the first aftermarket provider to provide OE-quality wishbones, stabiliser links, steering rack ends and track rod ends for the relatively low-cost Chinese-built Dacia Spring BEV, which was introduced in the UK last year.
MEYLE advises that seemingly minor oversights can affect quality bush replacements. Should bushes be pressed at the wrong angle, tensions result that deform the rubber, causing it to stick and weaken the bond. Prolonged mechanical stress can not only reduce bush life but also cause driver discomfort and can risk safety.
KYB is a specialist springs and dampers manufacturer that supplies OEMs and the aftermarket. It supports independent technicians, by providing data that is so accurate that TecDoc awarded it 'Premier Data Supplier' status. In addition, it helps you to work smart, by supplying over 130 vehiclespecific fitting videos on its YouTube channel. In addition, it produces frequent technical bulletins and QR codes on the packaging will take you to a dedicated portal of fitting tips and instructions. These tools will be supported by the KYB Suspension Solutions App, which will be launched later this year.
Yet, Meyle highlights that rear beam axles are especially vulnerable, owing to them being exposed to high forces. Correct installation requires accurate alignment and even pressure distribution. Without the right tools, Meyle reasons that it is difficult to achieve this precision but it can help.
In response, it develops special tools to make aftermarket bush installation easier. For instance, the firm can supply the pictured rear axle bushing tool (part number 32-14 710 0010) for certain Mitsubishi, Citroën and Peugeot models. Not only can Meyle supply the tool but also instructions, consumables and also bushes that either meet, or exceed, OE quality. First Line, too, reassures workshops with its focus on matching OE quality, at the very least, but emphasises its sheer portfolio size, which stretches to over 9,200 part numbers, comprising suspension arms, tie rod ends, rack ends, stabiliser links, engine mounts, top strut mounts and rubber-to-metal bushes.
Arnott supplies not just air suspension parts but also redesigns them. Owners are happy, because it remedies weaknesses in the OE part, but technicians benefit, too. Arnott reports that it engineers certain changes to make your life easier. A typical example of this is the pictured rear air spring on the W211 Mercedes-Benz E-Class. As the OE contains an external air reservoir, you have to disassemble and lower the subframe just to access the reservoir bolts. As Arnott eliminated the reservoir and integrated the functionality in their design, this saves you a whopping seven hours of labour time.
With over 100 years of expertise within the automotive industry, KYB is now expanding their product range to provide the complete suspension solution. Alongside shock absorbers, coil springs, mounting kits and protection kits, KYB’s range now includes control arms, stabiliser links, tie rod ends, rack ends and ball joints.
Just as drivers can develop bad habits over time, so too can technicians. Alliance Automotive, the firm behind the Apec and 'NAPA' brands, advises against developing shortcuts to save a few minutes. Tightening fixings with an air gun, while the vehicle is on a ramp, introduces torsional stress into bushes. Best practice dictates that fastenings should then be tightened to the correct torque, supporting the vehicle's weight. ZF Aftermarket advises of specific tools that are available to the aftermarket, which 'load' the suspension before fixings are tightened to the manufacturer's specification. An example of this is the wheel hub support, under part number T10149.
Comline/Motaquip's warranty department emphasises the importance of applying the correct torque, rather than opting for arbitrary air-gun tightness. It advises that the correct clamping force is vital for safety, because it avoids stripping threads, deforming components and reduces stress to preserve optimum suspension geometry and predictable handling.
Despite the fact that wheel bearing replacement is a relatively common task within the workshop, there is still some confusion among technicians between the different wheel bearing technologies and the fitting procedures that need to be followed to install them correctly.
To assist in this task, Dayco has produced a step-by-step guide to correctly install the front and rear wheel bearings on the popular 2018 VW Golf Mark VII.
We highlight best practice when it comes to bulb replacement, upselling opportunities and available training and resource on evolving lighting technologies
Lighting specialist OSRAM, highlights poor practices when it comes to bulb fitment
Headlights are safety critical components and should therefore be treated the same as other safety critical components, such as brakes, wiper blades and tyres.
Aligning headlights after bulb replacement ensures that the beam pattern is set in the correct place and is hitting the right points on the road. If a replacement bulb is not fitted correctly, it will not work correctly with the headlamp reflectors as intended and light can be scattered to oncoming traffic. While every technician knows they should be aligning bulbs after their fitment, it’s still not common practice.
It also presents a revenue opportunity for the workshop – just as wheel tracking and alignment is billable, so is bulb alignment. By charging a small amount for this service, the customer can be reassured their bulbs are giving them the best possible visibility and the workshop can earn extra income for a job that takes a small amount of time.
Fitment charges
Similar to the alignment issue, workshops should be charging for all jobs they undertake and the products being used. As a workshop usually has a large stock of bulbs, OSRAM has found that many do not charge for a replacement bulb, let alone for the fitment. This creates another revenue stream for the workshop, and while it’s a low price, adds up throughout the year. It also pays to think about upgrading to performance bulbs that offer even more profit margins than standard bulbs.
If you are changing one bulb, you may as well change both. From a business point of view, replacing in pairs means double the revenue but replacing bulbs in pairs is good practice as both bulbs will have the same light output. It also stands to reason that if one bulb blows, the other is likely to follow soon after.
Finally, poor quality bulbs tend to result in less visibility on the road for the driver and a bulb failure sooner rather than later. Some can even cause glare to oncoming road users, this could be as a result of the bulbs producing over the maximum lumen output or incorrect geometry of the filament, meaning the light is not reflected on the road as intended. A premium quality product will have been manufactured with precision engineering, and will give the best light output, last longer and subsequently result in a happier customer.
www.osram.co.uk/am
Since the dawn of the motor vehicle, Lucas has lit our journeys around the planet. Today we deliver our most advanced upgrade bulb line up for that 'extra' boost!
Whether you’re looking for more light on the road ahead, or you want that premium whiter look, Lucas has you covered. Blast off with up to 200%* more light or a stellar 5000/6000K white output† for out of this world style and performance. Light Booster and White Booster upgrades are e-marked and 100% road legal. For the adventurous looking to go off-road; Lucas LED Booster and Rally Booster provide our most extreme performance.
SCAN HERE TO MAKE FIRST CONTACT AND BOOST SALES
This year, ELTA Automotive will unveil a state-of-the-art light testing facility, one of just a handful of light measurement and photometry test facilities in the UK and Europe.
The facility will ensure light is directly precisely where it is needed while avoiding beam cut-off areas that cause glare and compromise safety. “All Elta bulbs are manufactured to meet regulation R37 standards and achieve e-mark status,” explains Marketing Manager, Tim Brotherton. “Key aspects of R37 compliance, such as geometry, photometry, and performance metrics like wattage, luminous flux, and kelvin temperature, are rigorously tested by our manufacturing partners throughout manufacture and beyond. At our new facility, we can now test bulb performance in headlamps to ensure compliance with Regulation 112, verifying optimal light output and precise beam patterns.”
A new generation of Lucas bulbs, available through Elta, provides a simple way to upsell to customers requiring replacement headlights, offering a choice of brighter or whiter? If the preference is brighter, the Lucas LightBooster offers 100%, 150% and 200% more light on the road with halogen or HID, while staying roadlegal. The Lucas WhiteBooster filters out yellow light at the brightest points of the filament, delivering a 5000K white light for halogen bulbs and up to 6000K for road-legal HID – providing a crisp, white modern appearance.
https://eltaeurope.com/ automotive-bulbs
Valeo offers a 15-minute training module on the evolution of vehicle lighting through its recently launched Valeo Tech Academy.
Nighttime driving poses significant challenges, with 72% of fatal road accidents taking place in low visibility conditions according to Valeo. “This means garages need to make sure their technicians are up to date with the latest lighting systems,” said Andy Swann, Managing Director at Valeo Service UK.
As more modern vehicles enter independent workshops, technicians find themselves dealing with the latest lighting systems, taking in halogen xenon and LED technology. “These differ fundamentally from more traditional headlights using filament bulbs,“ said Andy, “and technicians will benefit from learning about these systems through our training module.”
The training module, covers the basics of vehicle lighting systems, looking at the evolution from halogen to xenon and LED technology. It also discusses the future of lighting systems and provides guidance on using REGLOSCOPE PRO, Valeo’s equipment for measuring and adjusting lighting. Register or login to access the module here
HELLA released several new OE quality light units into the aftermarket throughout 2024; significant releases covered models from BMW, Tesla and Volkswagen.
Inner and outer sections of Tesla’s Model 3 and the LED rear light of the Model Y are available. Hella also supplies a standard LED headlight unti as well as the matrix headlight upgrade for the BMW 3 Series, which allows for adaptive functions such as ‘cornering light’ and ‘BMW Selective Beam’
“These lights are produced in series with their OE counterparts at the same factory,” said Product Manager Dave Clark, “which means you’re replacing like-for-like without compromise on quality or ease of fitment.”
A range of rear lights for the Volkswagen ID.Buzz was also made available, comprising six individual part numbers, with five LED tail light assemblies including stop lights and tail lights for the left side, centre and right side, as well as a tail gate cover.
Consider light alignment
“Headlamp beams travel a long way and need to be precisely set,” said Dave. “Even small variances will lead to dazzle, and these can be caused by other factors like suspension, vehicle load and even tyre pressures, meaning good general vehicle maintenance is important.”
Headlamp aim measurement within the MOT was amended by the DVSA in 2016 to ensure ‘correct alignment’ and avoid excess light in the dazzle zone. In 2024, ‘Lamps, reflectors and electrical equipment’ continued to be the most common cause of MOT failure, with a 25.28% failure rate, and headlamp aim was a significant contributor to this.
Hella provides information about xenon headlights, how they work, what causes xenon ballasts to fail, how faults can be rectified and why it is dangerous to retrofit illegal xenon headlights here
– How does your current supplier clarify their bulb quality?
– Do their bulbs comply with all the ECE regulations?
– Don’t compromise the safety of other road users! With OSRAM bulbs, you can be sure you are buying and fitting quality assured bulbs that meet all the necessary regulations.
Bulb checklist
Don’t compromise the safety of your customers and the reputation of your business. Buy and fit quality bulbs this lighting season!
Aftermarket suppliers discuss battery trends to highlight opportunities and replacement parts available to those looking to take on more ambitious EV repairs
Ecobat Battery discuss the trends of battery replacement and advise on how to address the needs of customers as they bring their vehicles in for service or repair
Although the vehicle manufacturers’ commitment to start/stop systems prompted a change in the technology provided by battery manufacturers, who moved away from SLI and over to AGM (absorbent glass mat) and then EFB (enhanced flooded battery), this change wasn’t reflected in the replacement market for several years. In 2016, just 2% of Ecobat Battery’s sales were AGM/EFB, whereas by 2022 it was nearly one quarter, with a comparable decline in SLI sales.
Two years on and the migration to AGM/ EFB batteries has continued, as start/stop technology is now fitted to almost every vehicle still incorporating a combustion engine. Ecobat Battery sales data confirms the reality of this trend as the present split between SLI and AGM/EFB is now 64%/36% and, when combined with vehicle application data, the migration rate looks to be accelerating. As a result, it is likely that the battery sales will be split 50/50, possibly as early as the end of 2025.
This shift in technology has significantly affected the life expectancy of these batteries, which are considerably more robust than their SLI cousins. In addition, the smart charging systems constantly monitor the condition of the battery and regulate the alternator to ensure it always receives the most appropriate level of charge. As a result, they are lasting 30 to 50% longer than a traditional SLI battery.
Its research highlights the importance of fitting the correct technology when replacement is required and rather than the traditional offering to customers of a good, better, best model option, providing the appropriate technology – SLI, EFB or AGM model.
Where’s the opportunity for workshops?
Battery testing for each vehicle that visits the workshop allows workshops to assess and share battery condition with their customers, building credibility, customer loyalty and battery sales. This is particularly important as the trends highlighted earlier demonstrate a reduction in the number of battery sales, so rather than losing those higher value sales to one of the national breakdown agencies when the battery fails by the roadside, they can be won by the independent workshop that actively carries out a battery testing regime.
These vehicle manufacturers made the right choice, you can too:
Scan here to visit the YouTube channel.
www.varta-automotive.com
It all starts with
Audi Bentley BMW Bugatti Chevrolet Chrysler Citroën Ferrari Fiat Ford GMC Honda Hyundai Jaguar Kia Lamborghini Land Rover Maserati Mercedes-Benz Nissan Peugeot Porsche Renault Seat Škoda Tesla Toyota Vauxhall Volkswagen Volvo
Banner has added to its existing range of start boosters, test and battery service products with the launch of its new Accucharger 15A and 25A.
“They offer a multi-stage charging programme that ensures that the optimum performance and longevity of both starter and vehicle electrical system batteries isn’t compromised,” says Country Manager, Lee Quinney. “Moreover, with seven charging stages, a 16V boost programme and a maximum charging current of 15A or 25A, they guarantee unrivalled performance.”
Features include a supply mode that prevents the loss of vehicle data when batteries are replaced and protection against splash water and overcharging.
The new Accuchargers are suitable for charging all batteries with 12V and 24V technologies, including lithium.
Email Banner to gain further information on its range of battery accessories.
“Battery testing for each vehicle that visits the workshop allows workshops to assess and share battery condition with their customers, building credibility, customer loyalty and battery sales”
Valeo is supporting workshops looking to take on more ambitious and profitable EV and hybrid jobs by introducing a range of chillers, used to help keep Lithium-ion batteries cool in many EV/hybrid thermal management systems.
EV and hybrid thermal management systems play a crucial role in maintaining batteries, ultimately preventing thermal runaway, which can destroy the battery and the whole vehicle. The chiller regulates the coolant temperature before it enters the battery, preventing heat damage. However, coolant can oxidise if left in the system for too long, corroding the chiller and requiring replacement. Debris can also block the chiller, which reduces its performance.
“EV and hybrid battery repairs will be among the main growth areas for garages over the next few years,” says Andy Swann, Managing Director at Valeo Service. “Technicians within independent workshops are learning new skills to take on this burgeoning opportunity, but they need access to components too, such as the chiller. Valeo is listening to what garages are telling us and making sure they have the parts they need as the market evolves.”
The first part, available now, is an OE reference produced by Valeo for the Volkswagen ID3. This will be followed in the next few months by another four references. These will cover further VAG vehicles, as well as Hyundai and KIA. Two of the references are also OE from Valeo, and will cater for Hyundai’s Tucson Plug-in Prime, and the KIA Niro EV EX Premium.
www.valeoservice.co.uk
New products, fitting tips & technical advice to ease fault-finding and installation
The opportunity to learn and win big!
The closing date for DENSO’s League of True Mechanics, LOTM, which provides technicians with training, prizes and the opportunity to take the European title and 2,000 euro prize, has been extended to the end of February.
“By extending the competition period until the end of February 2025, means that not only do more professionals have the opportunity to win the title, but a greater number will also be raising their skillset and work related abilities, which is invaluable, and the icing on the cake is that there is no enrolment fee or charge for the training modules, or technical information held on the DENSO E-learning site,” says Marketing Manager, Fatiha Laauich.
All courses marked with the ‘podium’ icon are included in the competition – once entrants have completed the courses and passed the final exam, they are credited with points and automatically enter the LOTM ranking. The current ranking is available after registration in the ‘Ranking’ section. Courses without this icon are still open and accessible, but they will not be included in the points system.
UK entrants can also gain IMI accreditation that these courses come with and the top prize is a Formula 1 British Grand Prix experience for two.
Is there any point servicing the aircon in winter?
WAECO answers with a firm yes! The air con system can be used over winter to keep humidity low within the vehicle and prevent windows from misting up. It is also important to use the system regularly to allow the refrigerant oil to circulate and operate correctly.
It is also worth checking under the bonnet for leaves that can block the air intake. If odours develop, the evaporator needs cleaning. A vaporising device such as the Refresho-mat from Waeco, which nebulises a chemical liquid, or an ozone generator, can be used for this purpose. But be careful with leather upholstery in the interior – it is better not to use ozone here.
NAPA Auto Parts 360 is a new eCommerce order platform designed specifically for workshops, who can search using any parts identifier, such as VRM, VIN, Part Number, OE Number, or even product name.
Live stock can be viewed across the entire NAPA Auto Parts network and wider Alliance Automotive Group, along with accurate delivery times. Repair time estimates can also be accessed via the platform. Find out more and register here.
With advancing technologies and an increasing average vehicle age, undertaking maintenance and repairs efficiently is even more important – Snap-on’s Apollo+ diagnostic tool has been created to help provide guidance and confidence for every task, from routine repair to the more challenging diagnostic tasks.
Fast-Track troubleshooting provides filtered information specific to the code and vehicle you have in front of you and its Intelligent Diagnostics provides a logical diagnostic workflow. You can save time with access to common procedures, specs and service interval resets as well as Smart Data, which provides code-based data lists that flag parameters out of range.
Detailed functional tests and OEM-specific scanner coverage for over 40 makes and more than 100 vehicle systems can be access via the 10” colour touchscreen display.
Click here to watch an overview video of APOLLO+.
A complete range of professional additives and tools from JLM for reducing emissions and improving performance in diesel, petrol and hybrid engines.
The ALLDATA Repair Centre experts help with an issue on a 2019 MY Peugeot 3008 1.2i
Alldata Repair provides independent workshops with instant access to genuine repair and maintenance instructions from 41 vehicle manufacturers and comprises over 90 million articles, millions of technical drawings and wiring diagrams with electrical connector views. Users who are struggling to find specifici information not yet uploaded to the portal, needing tailored service and maintenance schedules and unfamiliar with VM repair instructions can get support from its Repair Info Centre Service experts. Here, they help with an issue on a Peugeot 3008.
A motorist noticed an engine management light illuminated on the dash of their 2019 MY Peugeot 3008 1.2i, but the car was behaving normally. In the interest of safety, the driver booked it into their local independent workshop for inspection. The fault code P0137 downstream oxygen sensor was noted, the sensor was replaced, wiring checked, but the issue remained.
Solution
The ALLDATA Repair Info Centre Service experts had observed this issue before – the wiring wasn’t the problem; the issue was the ECU software.
To clear the engine management light, technicians must confirm, via the vehicle’s VIN number, that a correct oxygen sensor has been fitted and apply the modified software from the manufacturer.
For more information about ALLDATA Repair or sign-up to a trial, visit www.alldata.com/eu/en/repair-europe.
Double points for ‘Drive Cool’ promotion Workshops fitting any INA FEAD part or thermal management module throughout January and February can collect double REPXPERT points within the ‘Drive Cool’ promotion. FEAD products accruing double points during the campaign include INA FEAD KIT, INA Overrunning Alternator Pulley, INA Crankshaft Vibration Dampers and Decouplers and the INA FEAD Belt.
“Thermal management has become increasingly important within modern vehicles,” said Sales and Marketing Director Matt Selby. “As the car parc electrifies, this trend can only continue. At Schaeffler, we want to make sure that garages are being rewarded for all the hard work they perform in keeping cars running properly for their customers.”
Workshops that complete an INA survey taking place alongside the campaign will also be in with a chance of winning a Laser Tools cordless wrench kit.
To access the promotion, scan the QR code on the INA product box using the REPXPERT app. Once scanned, double points will be automatically added to your account. You can take part in the INA survey by visiting: www. repxpert.co.uk/drive_cool.