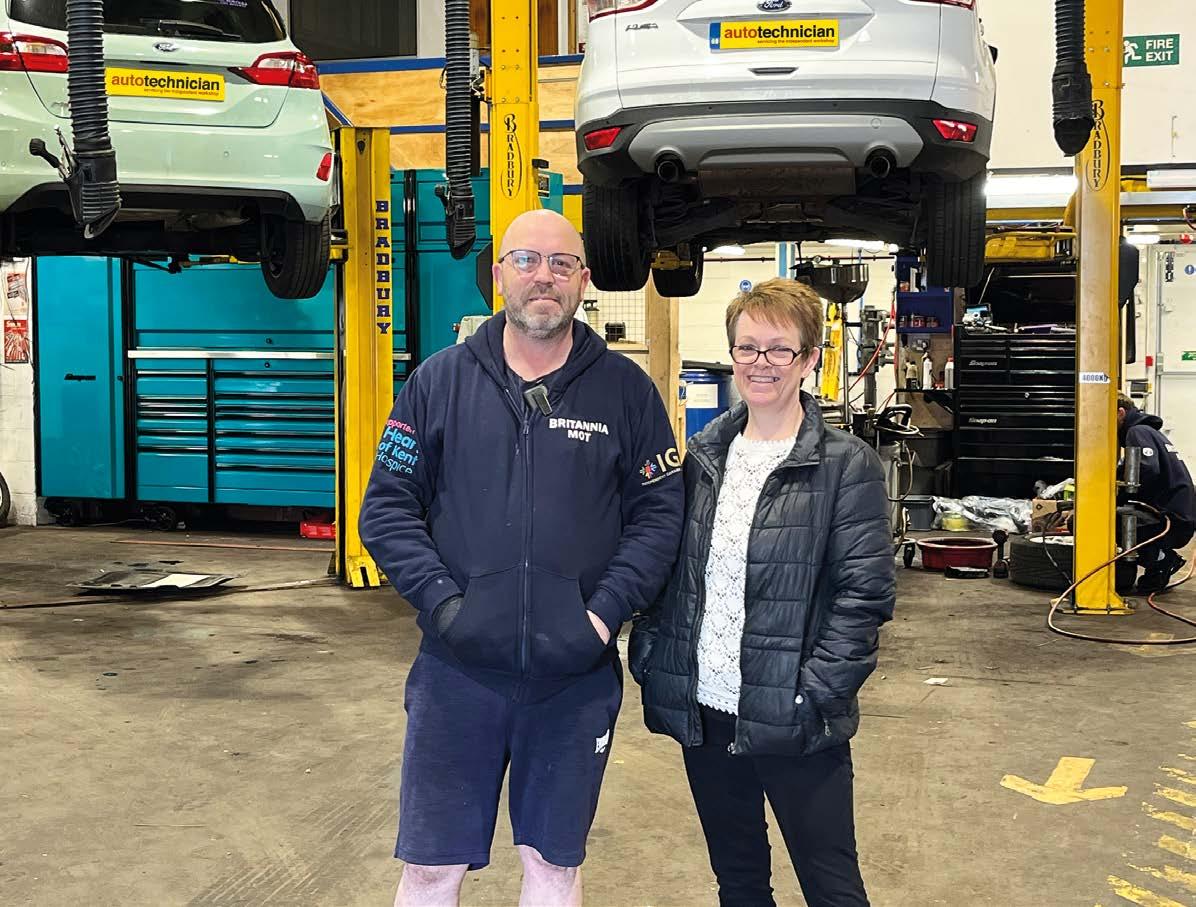
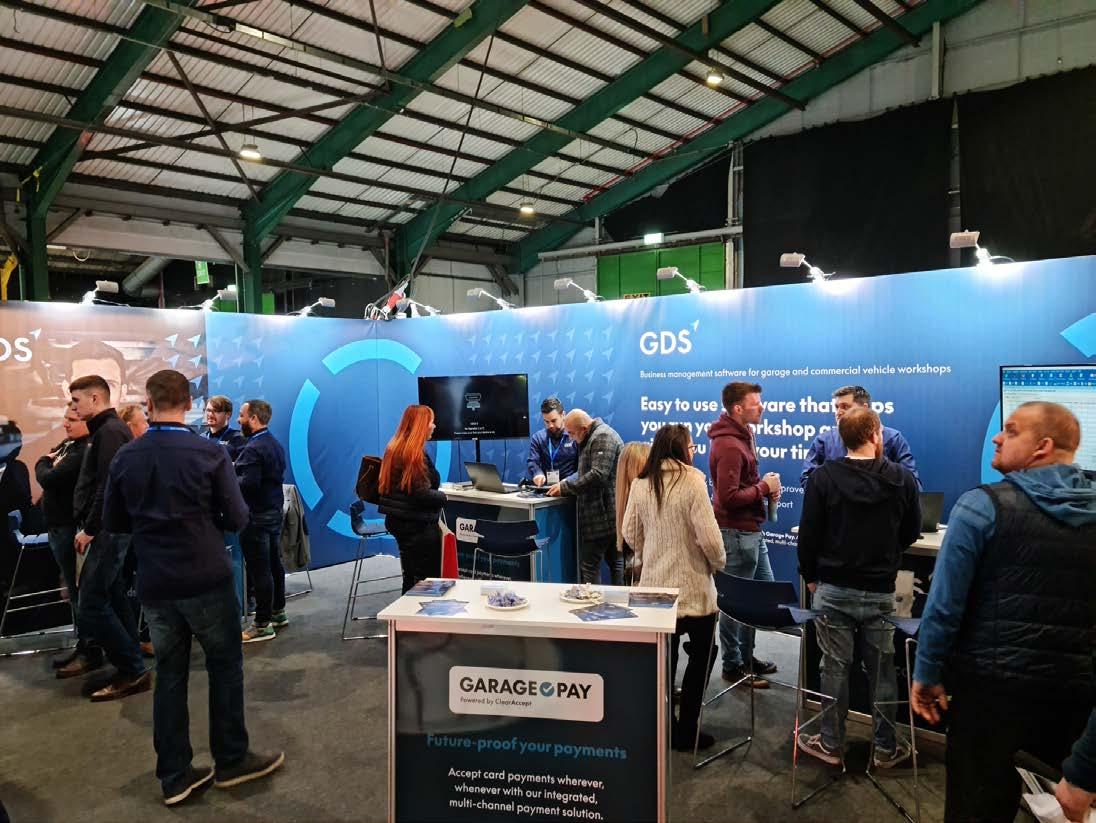
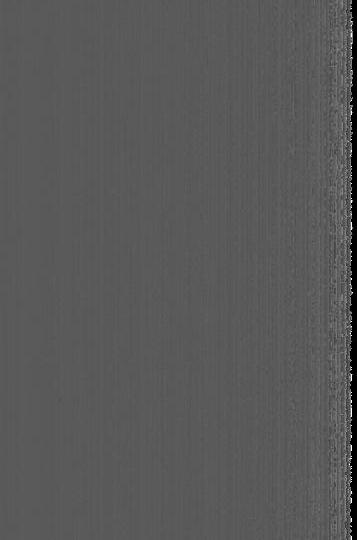
The Bosch FILTER+pro works effectively against viruses, bacteria, mold, fine dust and neutralizes allergens as well as harmful gases.
boschaftermarket.co.uk
JUNE 2023
P4 Industry news
P8 Countdown to Autotech Live
P10 Reframing people’s perceptions
P13 Gasoline Direct Injection issues
P16 KTS Diagnostics made ESI
P18 Voltage drop circuit testing – Part One
P24 Live and online training news
P32 Business support
P44 Technical data: The fight for survival
P51 Parts, Tools & Tips
P56 Support from Ben
NICOLA ST CLAIR, EDITORIAL DIRECTOR
Nicola@autotechnician.co.uk
07904 521 923
PAUL DEARING, COMMERCIAL DIRECTOR Paul@autotechnician.co.uk 07808 077 611
ROB MARSHALL, TECHNICAL EDITOR
NATHAN WISE, DIGITAL BRAND MANAGER Nathan@autotechnician.co.uk
MIKE SMITH, EDITORIAL ASSISTANT admin@autotechnician.co.uk
CONTRIBUTORS:
Andy Crook, Des Davies
To ensure you continue to receive the magazine, register here: https://autotechnician.co.uk/subscribe
As we prepare for a busy month ahead, heading to the eagerly awaited Automechanika Birmingham and our own workshop takeover in Cheltenham on 24 June, we have pulled together a jam-packed issue – full of practical advice, guides, case studies and industry news and views. We focus on training, business support and the issues surrounding technical data and visit IAAF Garage Award finalist Britannia MOT & Repair Centre to learn about the various support systems that have proved invaluable over the past few years.
We hope to see you in Birmingham 6-8 June, (free tickets are available at https://bit.ly/AutomechTickets) or at our one-day training event on Saturday 24th June at Cleevely EV – see page 8 for details, at time of going to press, you can still secure a ticket at https://autotechnician.co.uk/ training
The July/August issue will be mailed out on July 14 and will include technical tips and advice on Clutches, Steering & Suspension, and Batteries & Chargers – as ever, if you’d like to share your views, please get in touch. Have a great month.
Nicola@autotechnician.co.uk
facebook.com/Autotechmagazine twitter.com/autotech_mag
* View and download previous digital issues at: www.autotechnician.co.uk
Subscription to the magazine is free to those who fulfil the publisher’s criteria. UK independent workshops can subscribe at www.autotechnician.co.uk/subscribe Nine issues will be published throughout 2023 and will be mailed out free of charge to qualifying readers - you must work in a UK independent workshop, have buying responsibility and reside in the UK. Those who do not meet the qualifying criteria can request to receive a link to the digital issue free of charge or can opt to pay £25 for an annual subscription to receive an issue in the post.
All material, unless otherwise stated, is the copyright of Aftermarket Media Solutions Ltd and reproduction in whole or in part of any text, photograph or illustration, without prior written permission of the publishers, is prohibited. While all due care is taken to ensure the content of Autotechnician is accurate, the publishers cannot accept liability for omissions or errors. Any written material or pictures supplied by contributors are published in good faith and on the understanding they are free from any copyright or other restrictions.
Published by: Aftermarket Media Solutions Ltd, The Joiners Shop, Historic Dockyard Chatham, Kent ME4 4TZ
The Independent Garage Association (IGA) has submitted a response on behalf of members to the latest round of consultation on the UK replacement for the Motor Vehicle Block Exemption Regulation (MVBER), which expired on 31 May.
Stuart James, IGA Chief Executive comments: “The MVBER is a hugely important piece of legislation, both to our members and to the motoring public. It protects consumer choice and promotes open and fair competition in the service, repair and maintenance sector.
“As the voice of the independent garage sector, we have actively engaged with the government to help shape the UK legislation which will take its place – the Motor Vehicle Block Exemption Order (MVBEO), and we are pleased to see that consideration has been given to our previous comments and suggestions.
“There is a great deal to welcome in the new order. We are reassured that the MVBEO is, by and large, aligned to the needs of the British consumer and the UK motor vehicle sector.
The new legislation will include greater clarity for consumers around warranty restrictions and protect their freedom of choice in terms of vehicle service, maintenance and repair during the vehicle manufacturers’ warranty period. The Order also gives guidance on parts and supplier agreements which will protect the ability of independent garages to offer a quality service to the customer.
“We would have liked to have seen more clarity and reach within the CMA guidance document on the topics of access to in-vehicle data and access for independent operators to connected vehicle communications. These have the potential to mislead motorists into thinking they must take their vehicle into the authorised repair network, an important issue which we would like to see given further attention.
“Given the pace of technological advancements of motor vehicles in recent years, we are also urging the government to commit to an interim review of the MVBEO after three years, to ensure that the terminologies remain relevant and the MVBEO is operating as anticipated.”
eBay has relaunched its Certified Recycled programme, which sells recycled vehicle parts from 81 certified sellers and reports that UK motorists saved £99 million in 2022 by opting for used parts and accessories instead of brand-new replacements.
The online marketplace says Certified Recycled parts can be up to 70% cheaper compared to OEM parts RRP – all parts are checked and certified by the Vehicle Recyclers Association and warrantied – body parts feature a 12-month warranty while mechanical parts come with three months of protection – and are only supplied from end-of-life vehicles from approved sellers.
Additionally, they also come with a reduced environmental footprint. Last year, eBay UK shoppers buying used car parts and accessories saved more than 16,000 tonnes of CO2 and prevented 3,000,000kg of waste from ending up in landfills. This saving resulted from the millions of used parts sold across the eBay site last year, including almost one million exterior parts and accessories (including items such as mirrors, bumpers and door handles), over 400,000 lighting parts, and over 130,000 engine-related parts.
REPXPERT’s first Bonus Point Millionaire has been drawn from the huge list of members that scanned LuK boxes during the months of February, March and April – congratulations to Markhams Garage in Kingsland.
“To celebrate the 10th anniversary of the REPXPERT garage programme in the UK, another two other garages will be rewarded with a million bonus points over the course of the year, which they can spend on absolutely anything in the REPXPERT Bonus Shop,” said Marketing Communications Manager, Jeff Earl. “So, the message from Schaeffler is to follow Markhams’ lead and keep scanning those boxes and collecting your bonus points!”
www.repxpert.co.uk/millionaire
AUTOMECHANIKA BIRMINGHAM LAUNCHES DEDICATED STUDENT PROGRAMME
Automechanika Birmingham will welcome the next generation of aftermarket professionals with open arms on 8th June, providing a dedicated student programme in partnership with Autotech Academy.
many opportunities available to them. And we’re delighted to offer our student programme with Autotech Academy to give them a helping hand for a successful career in the sector.”
Gavin White, CEO, Autotech Group comments: “It is vital that we, as an industry, collaborate to demonstrate the full breadth of opportunities a career within the automotive sector can yield to the next generation. “Technology has transformed mobility, and the progress of the industry, and the potential careers within it, needs to be conveyed and amplified, as the competition to attract and retain talent is fierce. It is incredibly disconcerting to hear that young potential talent – students who have recently achieved an automotive qualification – are finding work in other industries, including retail and hospitality, because they are struggling to secure an automotive position.”
A complimentary ticket can be claimed at: https:// automechanika-2023.reg.buzz/autotechnician
“This year we are encouraging first-year, second-year and thirdyear students to attend our event in June and embrace the
IMI WILL REPRESENT THE INDUSTRY IN ALL-PARTY PARLIAMENT GROUP
The Institute of the Motor Industry (IMI) has been appointed as an Advisory Board member to the AllParty Parliamentary Group (APPG) on the Future of Employability, to discuss how to encourage people to work in the essential sectors that help drive the UK economy, including the motor industry.
“Like many sectors, we are facing a huge skills challenge and recruitment crisis against headwinds of an aging population and economic instability”, explained Hayley Pells, Policy Manager at the IMI. “It shouldn’t, therefore, be underestimated how significant our appointment to the APPG is. It is an important development enabling the IMI to represent the automotive sector with direct access to cross house, cross-party high-level discussion on all aspects impacting employability in the future.”
future of employability, from creating the right framework for retraining and upskilling, to the impact of technology on the way people work.
“The demographics of our workforce are changing”, concluded Hayley Pells. “Many motor industry professionals are retiring and, together with decreased immigration and reduced training budgets, this means a shortfall in workers. The EV revolution also means that conventional roles like vehicle technicians need to evolve with additional training to work on technologies such as ADAS and electric. And this means our industry should now be viewed through the lens of a technology sector. With this in mind we look forward to influencing further education strategies and investment to support the sector, including attracting older age groups to these vital new sectors, as well as appealing to a more diverse workforce.”
IS www.gea.co.uk GEA ACCREDITED ENGINEER Name Company Discipline Exp Date ID Number
Ask your XX123456 XX123456 XX123456 XX123456 XX123456
For peace of mind always use a Garage Equipment Association member.
his
TMD Friction’s training team recently visited service charity, Mission Motorsport, to carry out its professional technical training programme, Mintex Masterclass, to students.
The programme is carried out in accordance with Institute of the Motor Industry (IMI) criteria, with the team providing learners who are studying to achieve a Light Vehicle Level 3 qualification, with detailed braking best practice tips. TMD has confirmed that it will also conduct other training sessions throughout the year to further support the charity.
Launched in 2012, Mission Motorsport aids in the recovery and rehabilitation of those affected by military operations
Club Ricambi is merging with the Distrigo network, which will begin offering Genuine Alfa Romeo, Fiat, Fiat Professional, Jeep and Abarth parts throughout its 80+ UK outlets. These parts will be added to its existing programme of Genuine Vauxhall, Peugeot, Citroën and DS Automobiles parts, Eurorepar all-makes and wide range of brands such as Mahle, Delphi, Bosch, Ferodo, Nissens, Gates, Moog, and Monroe.
Distrigo has also expanded its PERKS reward scheme across the full range – customers earn points for purchases that can be used to save on future purchases or gain vouchers for Amazon or Snap-on.
by providing opportunities through motorsport and the motorsport industry. As part of the MoD's Career Transition Partnership, the charity helps those leaving the military to find employment in the automotive industry. An IMI training provider, Mission Motorsport's training wing delivers a range of qualifications up to, and including, Level 3 Diploma courses and full apprenticeships, enabling service leavers to bridge the gap between military service and second careers as civilians. The charity issued 158 qualifications last year to more than 40 veterans and service leavers. www.missionmotorsport.org
The finalists have been announced for the Automechanika Birmingham 2023 Garage Awards, hosted by IAAF, celebrating the very best of the garage industry. The winners will be announced at the awards evening on Wednesday 7 June at Hilton Metropole, NEC.
There are eight award categories including: Garage of the Year, Best Independent Garage (Single-Site) and ‘Auto-Mechanik’ of the year, Best Independent Garage (Multi-Site), Best Community initiative, Best Marketing Award, Best Customer Service Awards and the Lifetime Achievement Award.
The finalists for the Garage of the Year, are Coles Automotive, Hillclimb Garage, Jackson & Phillips Automotive Services, Lindleys Autocentres, Oldfields Garage Services, Plantexpand & Uckfield Motor Services.
Mark Field, IAAF Chief Executive, comments: These new awards will highlight our brilliant garage sector and the businesses and individuals working in it. We have a growing garage membership and we’ll be working hard to raise the profile of independent garages to motorists in the coming months.”
A full list of finalists is available at https://bit.ly/IAAFGarageAwards
Are you ready for autotechnician’s workshop takeover? We are counting down the days until we get together with readers and trainers once more at Autotech Live – our first official Workshop Takeover!
Trust us, you cannot afford to miss this…
What is it? A full day of diagnostic troubleshooting side-byside with a great bunch of technician trainers within Matt Cleevely’s impressive workshop
When? From 9.30 to 4.30 on Saturday 24th June
Where? Cleevely EV, Cheltenham GL51 8PS
What’s the format? Small groups of technician/workshop owners will rotate around three workshop bays, focussing on diesel, petrol and EV/hybrid faults. There are no presentations,
just hands-on faultfinding with justin-time learning thrown in by each guide trainer as and when required
How much will it cost me? Tickets are just £99+VAT
What! Why is it so cheap? Thanks to ACtronics, Alldata, Bosch Aftermarket and JLM Lubricants who support the campaign, we are able to offer cost-price tickets to ensure that everyone who is committed to upping their game can afford to do so.
Sign me up! At time of writing, you can purchase the last remaining subsidised tickets to the one-day event at www. autotechnician.co.uk/training
Andy will be challenging technicians to stick to the process while ensuring the business has the systems in place to benefit from diagnostics. If the business wants to be effective and the technician wants to be efficient, you need systems and processes. Andy will challenge you to diagnose the fault(s) efficiently and deal with the customer effectively. Are your systems and processes robust enough? Come and find out….
"I’m delighted to be involved in another autotechnician event where we get to meet like-minded industry professionals. This year the format is heading back to its roots and I’m looking forward to setting a broken car task for technicians and business owners to get their teeth into. As a small group, we’ll look at the real-world faults that have been presented, with some added customer twists and turns for good measure, and use a variety of dealer and aftermarket tools in combination
with shared knowledge and decision-making on how to attack the faults, from fault to fix. We’ll cover all the meat and potatoes of the technical task, with opportunities for questions and pitstops for learning and development throughout the task. Above all we’ll have some fun while learning about the serious business of troubleshooting faults within the workshop. I look forward to seeing you all there!"
Host Matt Cleevely and Eliot Smith of Pro-moto will lead a team of techs through EV faults
Matt says delegates will learn how to gain confidence repairing and diagnosing High Voltage circuits. Get a good understanding of what is required from a HV ready workshop and be inspired by working on EV’s within the busiest EV specialist workshop in the country.
Eliot will be tackling charging faults, so you can confidently attain whether you’re facing a faulty charger, charge lead or vehicle system. Learn how to diagnose common, and not so common, EV faults and get ahead of your competition.
In association with: Media Partner:
Tickets to this event are limited to ensure a hands-on, valuable learning experience. A number of subsidised tickets to the one-day event are currently available at www. autotechnician.co.uk/training. Email Nicola@ autotechnician.co.uk if you have any booking queries.
ACtronics are pleased to be continuing its sponsorship with Autotech for 2023
“As the market leaders in remanufacturing electronic automotive components, not only do we offer a first-class solution for garages, but we also support first-class training and technical support for the automotive trade. It’s more important than ever for technicians to have access to world-class training and ACtronics are very happy to work alongside autotech to provide this. It’s important that we all work together to futureproof garages ready for the changes ahead.”
“ALLDATA Europe is delighted to announce its partnership with autotech, a workshop training initiative that complements the OEM repair data provider’s strategy of supplying managers and technicians with accurate and up-to-date repair information.
With 89,000 make, model, engine and year vehicle combinations available on ALLDATA Repair, converting to 95% of vehicles on the road today, autotech participants can capitalise on this abundance of data while fixing faults in the Autotech Live workshop arena. Consequently, they can boost their first-time fix rate when returning to the real-world garage environment.”
Bosch Aftermarket UK & Ireland are delighted to sponsor Autotech Live 2023 – an event where technicians work together and solve live vehicle faults
“Autotech Live gives workshops the opportunity to highlight any skill or knowledge gaps and provides the right tools and training to support them. The event on June 24th gives technicians the chance to work on both ICE vehicles and EVs.
To support workshops, Bosch’s training centre delivers a full range of technical training courses for all levels and roles in modern workshops, accredited by the IMI.
Bosch is a well-known supplier of workshop solutions, offering a range of diagnostic testers such as the KTS series, and ESI[tronic] 2.0 Online software with ADAS Calibration, Air Conditioning, Emissions Testers, and Vehicle Systems Analysers, all EV compatible.”
JLM Lubricants UK are proud sponsors of Autotech
“The range of high quality JLM diesel and petrol additives is perfectly suited to the professional technician, including those who will be attending the Workshop Takeover. Attendees will receive an exclusive JLM goody pack including comprehensive information on the JLM product range. More and more professional technicians are choosing JLM products for their workshop because they realise that JLM produces top quality additives for both diesel and petrol engines that deliver excellent results, every time.”
Find out more at www.jlmlubricants.com
The latest autotech test joins the evolving bank of free knowledge assessments on www.autotechnician. co.uk/registration/ and looks at troubleshooting fundamentals and best methods to tackle the real-world fault assessments within your workshop.
This test has been created by VAG specialist, Gareth Davies, and presents the real data and investigation of faults on an Audi A3 within a multiple-choice format.
All you need to do is enter a few details at https:// autotechnician.co.uk/registration/ click an automated email reply and you get instant, free access to the multiple choice tests focussing on various topics and scenarios, including: Energy requirements of similar vehicles; Case Study – P0303; The SCR system; Hybrid & EV; Common sensors used in spark ignition engine management systems; Oscilloscope Quiz; Testing electrical components; Electrical Test; LIN Bus; CAN-Bus; Diesel case study & Ignition case study!
In the previous article in this series, Andy suggested having systems in place could help reframe people’s perceptions so that everyone has the same frame of reference. Here, Andy explains the difference between a process and a system using a diagnostic assessment as an example.
Processes are the steps required to complete a task. Processes, improve efficiency.
Systems are the interface between the person, the technology used, and the process. There must be a bridge. Systems improve effectiveness.
The process outlines how it's done and the system's interface between the various technologies used to do it.
It is a subtle difference, but what they have in common is a need for optimisation. You should always be seeking to improve both your systems and your processes.
What is the difference between effectiveness and efficiency?
Most people think they are one and the same. Efficiency is doing things right. Effectiveness is doing the right things.
Very subtle, but ever so slightly different. You can be efficient, without being effective. For example, if you have just changed the two rear tyres in record time, you were mega efficient. But, if that car needed its front tyres changed, you weren't very effective.
The system, remember this is the interface, between the person the technology and the task, should have identified which tyres to change. The process was changing the tyres. Now you can see how a person can be really efficient but not very effective, simply because they changed the wrong tyres.
The same logic can be applied to any member of staff when they discuss the work to be carried out on a customer's vehicle. Is there a bridge between the people involved, the technology used and the process? The process in this case is taking a booking. The systems identify the customer request,
communicate the offer, agree or not to proceed, take the booking and take payment. The technology could be a garage management system, the telephone, a card payment terminal etc.
Figure 1 on page 10 shows a simple system for dealing with prospective customers, having a template to record the customer request results in the correct offer being communicated (or the correct tyres being replaced).
In this case, a warning light is illuminated, and the colour, shape and method of illumination have been established. The template asks a series of questions that will help the technician. They form part of the Primary Data capture. Having established that a diagnostic assessment is required, the garage can present its offer.
Using the 4 C’s of the offer system
1. The Contract is clear
The customer is made aware of the work to be carried out in plain English.
2. Communication
The methods and frequency of communication between the garage and the customer are agreed upon and recorded.
3. Count
Both the time required, and the cost are agreed upon.
4. Consensus
Both the customer and the garage must see the offer as a winwin situation.
Using a system to present your offer results in a consistent approach to dealing with customers, see Figure 2
garage agrees to call during the customer's lunch break with an update.
6. Count
The assessment will be carried out before 12 pm and the cost is £100.
7. Consensus
Both the customer and the garage see this offer as a fair exchange, (win-win) this is a bit like the TV show deal or no deal, both parties must agree it is in their interest to proceed. As a final check, the garage asks the customer to outline the offer.
They ‘expect to know more via a phone call at lunchtime and hope it doesn’t cost much more than the £100 they have already paid’. This ensures there is no confusion, and acts as a final check that everything is crystal clear and recorded.
With agreement on what work will be carried out, when and how long it will take, the channels of communication established, and the price agreed. The final step is taking payment. Some garages find this much more difficult than others, but the assessment may be in two weeks' time, the best way to ensure that the customer turns up is to take payment now.
When the customer arrives, go over the diagnostic template with them, and ask if there is anything else they can add. Or if anything has changed since they spoke. Confirm they are clear with what work you are about to undertake and when and how you will contact them.
The technician will use a diagnostic process, similar to the one shown in Figure 3. The use of systems and processes will make sure the garage is both effective and efficient.
1. The Contract is clear
The customer is told using language an 8-year could understand (no jargon) that a series of tests will be carried out to prove what is or is not wrong with the vehicle. After which, the garage will report its findings (and make another offer).
5. Communication
The customer prefers to be contacted by telephone, although they are not able to answer their phone at work, they are on lunch between 12 and 1 pm and finish work at 4.30 pm. The
Next time, Andy closes the diagnostic process loop by evaluating performance.
For more ideas, advice and free training why not join the Garage Owners Network Facebook group? www.facebook. com/groups/garageownersnetwork
www.atomicsuccess.co.uk
Vehicle owners, workshops and vehicle manufacturers are seeing issues with Gasoline Direct Injected engines that cannot be put down to one fault. What’s behind the problems and what are the consequences? More importantly, what’s the solution? GDI specialist Phil Ellisdon of ASNU delivers his findings within a three-part series. In this second article, Phil highlights the importance of injector testing
All manufacturers producing vehicles with a combustion engine have one thing in common, they must all `meet with emission regulations’ and this is why there is a push towards electric vehicles. Although there is a requirement to stop producing vehicles with combustion engines by 2035, already some countries and some vehicle manufacturers are claiming the switch to all-electric cannot work as the infrastructure will never be available to cope if every car on the road was. Already GM has said it is investing $918 million in four U.S. plants with most of the money going towards new internal combustion engine production.
The current production of gasoline combustion engines is Direct Injection, GDI/FSI and are the most powerful and economical Gasoline engine ever produced and still able to meet current emission standards. The injector used in these GDI engines has the finest tolerance of any mechanical components on the car. The pintle ball and seat has a 1-micron tolerance, this is required to ensure correct delivery of the specific amount of fuel that the engine requires. The injector is fitted with a 30-micron filter to capture any debris getting past the main filter and protect the ball and seat from leaks and any disruption to the injectors fuel flow.
These injectors are required to operate in milli seconds, delivering the specified amount of fuel the engine requires in a determined spray pattern with a specific droplet size. All these functions are required in the harshest of environments, the combustion chamber.
If we look at any of the vehicle manufacturer’s service schedules, we can see during the service life of the vehicle we are required to change air filters, oil filter, fuel filters, pollen filters and many other components on the vehicle to ensure it maintains its reliability, performance, economy and most importantly, its exhaust emission levels. Nowhere during the life of any petrol engine does the VM recommend testing or servicing the injectors, yet its performance is critical in all aspects of the correct running of the engine.
Emissions are caused by unburnt fuel in the combustion chamber being expelled on the exhaust stroke. It is the responsibility of the injector to deliver the fuel in a combustible format so it will burn correctly. Failure on the injectors part to do this correctly will create un-burnt fuel and an increase in exhaust emissions, but it will also have additional consequences.
Failure to atomise the fuel correctly can lead to additional problems and long-term damage to the engine, possibly costing thousands to put right. Unfortunately, most of the problems we are seeing are of the VM’s own making. A poor atomising injector can create carbon build-up in the combustion chamber where additional un-burnt fuel will end up lying around the edge of the piston, washing away the lubricating oil, causing bore wash, wear on the piston rings and scoring the bores. Fuel can then emulsify the oil in the sump and cause wear in the bearings.
Unburnt fuel is also expelled on the exhaust stroke and drawn into the exhaust gas recycling system. This un-burnt fuel is then fed into the EGR valve, causing it to respond slowly or even fail completely. These fuel emissions are fed into the air track, where it leaves carbon deposits on the inlet valves.
The carbon on the valve can damage the valve stem guides and prevent the valve from seating correctly, causing poor running of the engine. With the growth of GDI/FSI injection, there is a need to maintain good performance drivability, fuel economy and maintain minimum exhaust emissions. Now is the time for workshops to ensure injectors are working correctly and performing as they were originally designed to –as in ‘AS NEW’ (ASNU) condition.
The HDEV1 injector was used in the first generation of VW/ Audi GDI/FSI engines. This is now coming to end of life production which means that once production of this injector stops there will not be any new injectors available for replacement. At present, there will not be an upgrade version available either, so the need to ensure the existing injectors are tested and serviced to maintain their performance and prolong their life has now become maybe one of the most important components on the engine that does not have a recommended service option.
As their trusted garage where they take their pride and joy for service and repairs, its only right that you should advise them of this situation and recommend that their injectors are serviced at a recommended interval to maintain their performance and save them money in the long-term.
As you are aware, poor-performing injectors can have a detrimental effect on the performance of the vehicle and can cause consequential problems, failure to maintain the performance of the injectors can cause long-term damage to the engine, resulting in expensive repairs – servicing them will ensure they maintain their performance.
The ASNU programme is now used by many of your wellknown fellow VW/Audi specialists, who are addressing the problem by joining our programme and ensuring their customers best interests and cars are looked after in the best possible way.
As you are your customer’s choice of workshop, it becomes your responsibility to make sure they do not end up with a vehicle where they have an injector related problem and then find out there are no replacement HDEV1 injectors available or if they are, only available at a premium price.
ASNU are world leaders in the field of testing and servicing Gasoline injectors with over 33 years' experience. Approved, recommended and used by Robert Bosch worldwide, ASNU can be found in most vehicle manufacturers Technical Support Centres. The ASNU ‘Low-Pressure Testing’ programme for GDI injectors is safe and easy to use by anyone in the workshop without special training and with over 10,000 ASNU systems in operation worldwide, the ‘ASNU Injector Diagnostics’ programme is the standard that everyone now works with.
The ASNU can test and service every gasoline injector ever produced, so no matter what the vehicle in your workshop, if its Gasoline, ASNU has it covered. ASNU is a cost-effective programme that not only saves your customers money in the long term, but will also save you time and money on trying to diagnose and fix combustion-related problems you can’t find, and will earn you money providing the injector service they need.
ASNU offer the best quality, the best service support and technical support that is second-to-none in this market, all very important when you are making a choice on buying your diagnostic equipment.
We can assure you that a combustion-related problem CANNOT be fixed unless the combustion chamber is working correctly and efficiently, the days of fitting new injectors is expensive, especially when basically there is nothing wrong
with them as such, just in need of a top-quality service carried out by professionals, using professional equipment.
As for flushing aggressive, harmful chemicals through the system to remove carbon, is this really the answer? We think not, we have seen so many injectors destroyed by these aggressive chemicals, the damage they can cause to the injectors’ filter baskets can be irreparable and costly, we prefer to describe it to customers as like putting a plaster on a bad cut that really needs stitching.
Don’t get stitched up, get your injectors professionally tested and serviced at one of our hundreds of ASNU Injector Service Centres around the country www.asnu.com/servicecentres
The ASNU Low-Pressure Testing programme for GDI injectors is safe and easy to use by anyone in the workshop without special training
Welcome to the third bitesize guide in our series of useful tips to help your workshop maximise the potential of your Bosch ESI[tronic] 2.0 software
In our previous issue we took a closer look at how technicians can quickly and easily run a complete vehicle diagnostic check with the ‘System Overview’ tool. Allowing them to identify intermittent issues, pending technical problems or difficulties that the driver or customer may not be aware of – at the touch of a button.
In this short guide, we will take the next logical step with the ‘Service Tasks’ tool. By putting all the tasks you need to complete a service for a specific vehicle right at your fingertips – in seconds – ‘Service Tasks’ is one of the most easy- to-use time-saving features your Bosch ESI[tronic] 2.0 software has to offer. Here is how it works...
The ‘Service Tasks’ tool on the ESI[tronic] 2.0 will guide you to precisely the right ECU for the chosen function – with no need for extensive searches or any prior knowledge about the make or model of the vehicle they are working on.
This is a great time-saver for quickly identifying and executing the most common tasks, from maintenance resets and tyre changes to brake fluid and pad replacements.
STEP 2
By selecting ‘Service Tasks’ you will be presented with a list of possible service tasks for the selected vehicle, see Figure 1
STEP 3
Simply double click the service task you want to execute and the ESI[tronic] 2.0 will take you straight to the correct function in the corresponding ECU, see Figure 2
STEP 1
Once you have selected the vehicle (see lesson 2) open the Diagnosis menu and click on the Service Tasks button, see
Figure 1
Or alternatively, the service task that is required can also be entered by selecting it with one click, and then by pressing ‘Start’ in the bottom righthand corner.
STEP 4
Users can also search for specific or desired tasks in the search bar, see Figure 3.
The ESI[tronic] 2.0 will let you easily search for any kind of available task and precisely tell which ECU to use – with no need for extensive research or any prior knowledge about the make or model of the vehicle they are working on.
Remember, ESI[tronic] 2.0 will also indicate if a specific service task does not require programming on the vehicle in question
to make sure you do not waste time with any unnecessary searches or undertaking more work than needed, see Figure 4
The ‘Mileage Function’ is another useful time-saving tool. By reading and consolidating all of the mileage data across the vehicle’s various control units – you can leverage this functionality to retrieve an accurate and efficient overview of all the mileage information stored in the vehicle. All in a single click, see Figure 5.
Remember, making sure your KTS/ ESI[tronic] 2.0 are running the very latest software updates is crucial for maximising the capabilities of the tools at your disposal.
When using our newest software, you can rest assured that any online software updates will be downloaded by the Diagnostic Download Manager automatically in the background, see Figure 6.
This is particularly useful for understanding whether a vehicle’s mileage has been changed when carrying out work on behalf of insurance companies, experts and appraisers looking to prepare a valuation report, when returning cars to leasing companies or to give an accurate picture to car dealerships trading-in used cars.
With reduced maximum download sizes, it has never been easier to make sure you always have the very latest functional diagnostic coverage and are kept up to date with any enhancements to existing diagnostic systems.
However, to ensure you benefit from these online updates, you will need to manually apply any local system software updates and confirm the installation of the downloaded software updates.
If these updates are overlooked, you may end up with reduced functionality and incomplete or outdated information. To make sure you do not miss out, simply click once on the ‘Install now’ button and the DDM will do the rest – installing every available update on your computer, see Figure 7
In the next issue, discover how the ‘Known Fixes’ feature could turn hours of Googling into seconds of searching.
www.bosch-training-solutions.com
If updates are overlooked, you may end up with reduced functionality and incomplete or outdated information. To make sure you do not miss out, simply click once on the 'Install now' button and the DDM will do the rest
Testing electrical circuits and components can be difficult to comprehend but it's like everything we learn on the vehicle, understanding the basics of electrical circuits can only help us to test and locate problems within these systems. It’s not easy and can be time-consuming; most technicians I have worked with would rather repair mechanical problems than delve into electrical diagnostics. You cannot blame them, it can take hours or even days to locate a fault in the electrical system, whereas mechanical problems tend to be, but not always, easier to diagnose. Here, I’ve tried to explain the fundamentals as simply as possible. To test and diagnose electrical circuits, you will need:
• Access to the manufacturer’s schematic diagrams and technical information are essential
• When testing vehicle circuit faults and components you need a good digital multimeter to diagnose and test faulty circuits and components
• Do not use an old analogue voltmeter as these will draw too much current when working on modern cars, especially with systems using electronics and computers, they will fry them!
• The multimeter is your best friend when diagnosing electrical circuit faults, you do not need to purchase fancy or expensive lab scopes or meters, a good quality basic multimeter with 10MΩ of resistance is all that is required. If you need to test electric/hybrid vehicles as well, you need a higher spec Cat III 600V for safety.
When voltage testing you must always connect the black meter lead to the common port connection, which is the earth/ground lead on your multimeter, and the red lead to the Volts/Ohms ports. For these tests we are going to use the 20V range scale on the multimeter, because there is no 12V scale available on most meters.
The circuit must be on or loaded e.g., if you’re testing the horn circuit press the horn switch, if you’re testing the brake switch press the brake pedal to check the circuit. If possible, always connect the multimeter black lead to the battery earth/ground minus terminal for a good ground connection, for accuracy. Sometimes this will be difficult as the battery location could
be in the boot area or another awkward location. If there is no positive connection under the bonnet area, make up some extension leads to connect to the battery if it is located away from the area you are testing.
Check your ground lead with a known good feed circuit e.g., battery positive, the OBD pin 16 connector when testing inside the vehicle, or fuse box live connector. When testing an electrical circuit with the engine running, remember that now the power source is the alternator/generator and not the battery voltage which is 12.6V, and this generated voltage can be between 13.6V to around 15V or more, depending on manufacturer specifications.
It's essential we understand the fundamentals and the relationship between Voltage, Current and Resistance:
Volts = Current multiplied by Resistance V = I * R
Current (I) = Volts divided by Resistance I = V / R
Resistance = Volts divided by Current R = V / I
We also need a good understanding of Ohm’s law (current in a circuit is equal to the potential difference divided by the resistance of the circuit).
Rule 1: A digital voltmeter displays the difference in voltage between where you place the black probe and to where you place the red probe.
Rule 2: The voltage after the last resistance in a circuit will always be zero (providing current can flow)
Rule 3: Volt drop will only occur across a resistance if current can flow.
Rule 4: The Volt drop across a resistance in a series circuit is in direct proportion to the comparative resistance values. Voltage drop across all the resistors in that circuit must add up to the source voltage. If you measure a 12V drop across the
Autotechnician’s team of trainers and top-notch technicians will be taking over Cleevely Motors in Cheltenham on Saturday 24th June and invite you to join them to tackle live faults together. Guests can expect various vehicles, including petrol, diesel and EV, and receive ‘just in time’ learning to get to the root of the problem with minimum fuss.
Andy Crook, Matt Cleevely, Gareth Davies, and Eliot Smith of Pro-moto will be on-hand to guide guests through the fault- nding process and potentially join in with some head-scratching! All faults will be live jobs and should make for an interesting challenge for all.
3 groups will get hands-on with petrol, diesel & EV faults Andy will challenge you to diagnose the fault(s) e ciently and deal with the customer e ectively.
Are your systems and processes robust enough? Come and nd out…
Don’t miss out on what will be an enjoyable day with a great bunch of people who are all committed to improving their rst-time x rate.
Tickets to the event are priced £99.99 plus VAT and include parking, refreshments, and lunch.
“As a small group, we’ll look at the real-world faults that have been presented, with some added customer twists and turns for good measure and we’ll use a variety of dealer and aftermarket tools”
“Delegates can learn how to gain con dence on repairing and diagnosing HV circuits”
A limited number of tickets are now available at https://autotechnician.co.uk/training/
In association with: Media Partner:
3YEAR W arranty
Schaeffler is renowned as a supplier of high-tech precision components and systems to leading vehicle manufacturers around the world, and we deliver these same parts to the independent aftermarket as LuK, INA and FAG complete repair solutions.
Our FAG WheelSet hub repair kits come with every genuine OE quality component you need to carry out a professional repair, right down to the last nut, bolt and washer - so no shopping around for missing parts. Every single part in the FAG steering & suspension range has been designed to OE specifications, before being produced using the very latest Schaeffler material and manufacturing quality standards. We are absolutely confident in the performance, reliability and durability of our FAG chassis products, so are able to offer a comprehensive 3-year unlimited mileage warranty and unrivalled free technical support.
battery terminals, the 1 or more resistors in that circuit should all individually add up to the 12V system voltage. So, within a 3-resistor circuit, if they have all equal resistance then the voltage drop across the individual resistors will be 4V each, adding up to 12V system voltage. This is Ohm’s law.
* If the supply voltage is the same voltage to the component as the battery voltage, for example, both are displaying 12.6V on the multimeter, then you have an open circuit, no voltage drop and therefore no current flow.
* If current is flowing in the circuit then there must be a voltage drop across the resistors/components
* If the current is flowing in the circuit then it must be taking something out of the power source or battery, therefore the voltage must drop in the circuit. It cannot be the same voltage as the battery supply, if it is, no current is flowing in that circuit and it will not operate correctly
* If the voltage reading on the ground/earth connector of a wire is around 0V and fluctuating up and down you may have an open circuit, or you are not connected to that wire or part of the circuit you are testing. Shake the leads of the multimeter until you get a stable reading, this then indicates that you are now connected to a good source or point of that circuit, a good ground.
What does a voltmeter do? The voltmeter checks the reading at the negative point where you place the black meter lead in a circuit, and the positive point where you place the other second red meter lead in the circuit. The meter will display a voltage reading if there is a difference in that circuit between the red lead and the black leads. Think of the ground/ earth circuit as a low-pressure circuit and the live/power circuit as a high-pressure circuit, so when you check between these circuits with a meter/gauge you will get a difference in pressure between the low pressure and high pressure. If there is a difference in pressure it will display a reading on your meter/gauge.
So now back to the voltmeter readings, in between the two multimeter leads that we have placed is the part of the circuit we are testing for anomalies or faults. If I place my meter leads across the battery it will read a battery voltage of say 12V, because I am probing one side which is 0V (low pressure) ground/earth/negative post, and the other side of the battery which is 12V (high pressure) positive post/live, this is because there is a difference between 12V and 0V, hence the display of 12V on my multimeter.
Therefore, as an example, if I place the red lead on the battery positive terminal and the negative lead at the component live side or input, then I am checking for a fault between the battery live side and the component input. If there is no difference in the reading, to where we placed the leads in that circuit between the red and the black leads, then that part of the circuit must be good and the multimeter will display 0V.
If there is a problem in the circuit a difference in readings of where we have placed the two leads of the multimeter, it will display a voltage reading and this means that this part of the circuit has a problem (if the reading is above 0.5V on a 12V system).
If we test this circuit and have a reading on the multimeter, for example a 3V voltage drop, then we need to back track, towards the battery post/power source with our negative black lead and probe the cable back along the circuit until we get a reading of 0V (0.5V max), and the fault will lie between these two readings in that circuit (poor connection, corrosion or damaged cable, spread pins etc.)
In summary:
When we probe the circuit with the negative lead (black), to where we probe the positive lead (red) in the same circuit, in between these two probed leads is the part of the circuit that we are testing. If there is no difference in that part of the circuit, we should have 0V (max0.5V) on the multimeter, which indicates that that part of the circuit is good, if there is a reading on the multimeter e.g., 2V, then there is a difference, and that part of the circuit has the fault, and we need to investigate further.
"Think of the ground/ earth circuit as a lowpressure circuit and the live/power circuit as a high-pressure circuit"
Every connection in the electrical circuit you are testing will have around 0.1V drop, this should be the maximum voltage drop allowed, if more than this we need to investigate. If you have 10 connections in that circuit it will produce a voltage drop of 1V (10 X 0.1V), so instead of providing 12V to that component it is now only supplying 11V, this circuit will now not operate to its full potential and needs to be checked for a fault.
An example for a typical 12V circuit is, 2 battery connections live and ground, 2 switch connections an input and output, 2 fuse connections an input and output, 2 component connections a live and ground and 2 relay connections 30 and 87 = 10 connections on this circuit, VD = voltage drop = 1V.
This is important. Wherever the power comes from – the battery, generator, capacitor, or other source – it must return to that power source to make a circuit to operate correctly, this is why the ground/earth part of the circuit is important).
A word of caution. Don't get confused with the test that goes across one side of the circuit only, with either end of the positive/live side or the negative /ground side of the circuit to test for a voltage drop, and the tests that we apply using the multimeter with the black lead permanently connected to the negative ground battery terminal, and using the red lead to go probing around the circuit to check the voltages in the circuit. The lead connections are different, and the readings will also be different!
Always test the power source first to check for the correct voltage, if the voltage is incorrect you need to replace the battery or recharge the battery back up to the required system voltage. If the power source readings are incorrect then your circuit/component readings will also be incorrect, giving you false readings with your test equipment, which may lead to incorrect diagnosis of the system and replacement parts that are not required.
The circuit in Figure 2 displays 12.3V, checking the positive or live side of the circuit using the multimeter; with the negative or black lead connected to the negative terminal of the battery and the positive or red lead connected to the live side of the resistor/component. This indicates a good positive or live side of the circuit to that resistor/component.
The circuit in Figure 3 displays 0.3V(maximum 0.5V), checking the negative or ground/earth side of the circuit using the multimeter with the negative or black lead connected to the negative terminal of the battery and the positive or red lead connected to the ground side of the resistor/component. This indicates a good negative or ground circuit to that resistor/ component.
If we now add up the previous live side reading with the ground side reading they should add up to system voltage, 12.3V live or power side and 0.3V on the ground/earth side, they add up to 12.6V – this is the battery or source voltage and indicates a good working electrical circuit. The Voltage drop reading of any circuit resistors/components should equal the battery/source voltage if the circuit and its component are operating correctly.
Meter 1 (M1) in Figure 4 displays 0.3V indicating a good ground/earth, but M2 displays 10.3V indicating a fault in this part of the circuit, so now we need to test the positive or live side of the circuit to locate the fault
If the resistors/components do not equal the battery/source voltage, then you have another resistance in that circuit not allowing the component to operate efficiently at the required voltage, we will now need to locate that extra resistance.
These are a few examples of problems that you may come across when testing live vehicle circuits. These methods can be used on any 12V circuits on the vehicle e.g., Starting, lighting, wiper/washer, engine management sensors and ABS. Having the correct knowledge of how the circuits operate correctly is essential, in addition to a reliable source of technical information (manufacturer data and circuit diagrams) to help you diagnose electrical faults and fix the vehicle.
Part Two on voltage drop testing will feature in the next issue.
The Independent Garage Association has added an EV Practical Fault-Finding course to its suite of skills training. The one-day course, delivered at various RMI training locations, focuses on frequent real-world faults that have been identified by its members. The Hybrid and Electric Vehicle Repair Alliance (HEVRA) has supported the development of the course with specialist knowledge and expertise.
The course will cover common faults in the following vehicle systems: Inverters, interlock circuits, DC – DC Convertors, charging circuits & contactor issues.
“Members have said that even with a Level 3 qualification, their technicians often don’t feel confident to move into diagnostics of the high voltage EV systems, says Stuart James, IGA Chief Executive. “We are delighted to be providing a solution to meet the needs of our members and the wider independent sector.”
Technicians will need to be qualified to a minimum of HEV Level 3 prior to attending. The course is open to nonmembers, but IGA members benefit from a preferential rate.
https://independentgarageassociation.co.uk
As technologies evolve, and repairs become more complex, professionals need continuous training. To make this as straight forward as possible, Valeo offers free access to its online training webinars, available live or on demand.
More than 70 sessions are available on the Valeo Tech@ssist training platform. Valeo Technical Trainers present at least one webinar a week throughout 2023, updating attendees on the latest products, technologies, and best fitment practices.
You can participate in live online webinars every Wednesday morning at 10am, and gain access to free downloadable technical literature, links to related content and Q&A’s with the technical trainers. All webinars are then published online and IMI members receive CPD points.
www.valeoservice.co.uk/en-uk
New data from the LKQ Academy training platform has revealed the areas where technicians’ knowledge and skills might benefit from a top-up.
LKQ Academy at LKQ Euro Car Parts, has analysed inbound calls to its Technical Helpline since the start of the year. It receives more than 1,000 calls per month and the data has revealed there are common trends that lead technicians to call in or use the online support system.
Diesel system repairs are the most common reason for technicians using the service, making up 35 per cent of all enquiries, followed by petrol and electrical issues both accounting for around 15 per cent. This data is consistent with the technicians’ scores in the LKQ Academy Skills Assessment – free to anyone looking to assess how they fare against their peers. Diesel and petrol test scores were the lowest overall in the first quarter of the year, with technicians achieving an average result of 32%. The test also highlighted that many need to top up their skills on
electrical systems, as results in the category were only slightly higher at 47%.
Bob Wiffen, Workshop Solutions Director at LKQ Euro Car Parts said: “Workshops have been evolving and adapting over recent years to keep up with changing regulations and new technologies. While it’s right that upskilling in diagnostics, ADAS and hybrid/EV is a focus, it’s important not to overlook the basics. Petrol and diesel engines will be commonplace on our roads for a long time yet, and it’s important technicians can complete every job on them effectively and efficiently.”
LKQ Academy provides IMI approved courses for all levels and cover everything from technical skills to business support and management. Individual and workshop-level memberships are available as a cost-effective means of buying multiple in-person and online training days across a 12-month period.
The Technical Helpline and Technical Troubleshooting Database are added benefits available to members.
www.lkqacademy.co.uk
We highlight upcoming live training dates and new content added to online training hubs to boost your skills and preview the Bosch ADAS course
• Business peaks, annual leave, training days and sickness cover
• Fully qualified and vetted vehicle technicians and MOT testers
• Contracts lasting from one day to six months at a time
• UK-wide network of over 450 contractors
• Flexible work patterns: early, late, night & weekend shifts SHORT-STAFFED?
WE PROVIDE RELIABLE TEMPORARY COVER FOR ABSENT TECHNICIANS AND MOT TESTERS IN YOUR WORKSHOP.
Contact us today to book your contractor!
Tel: 01234 432988
Email: hello@autotechrecruit.co.uk
Web: autotechrecruit.co.uk
NEED FRESH TALENT FOR YOUR WORKSHOP?
TAKE OUR INTERN TO CHECK THEIR POTENTIAL AS A PERMANENT EMPLOYEE.
• 6 to 12-month paid internships are a new, risk-free way of bringing new talent to your workshop
• Vetted candidates with a recent IMI Level 3 automotive qualification, equipped with a starter toolkit, basic safety workwear and uniform
• Assess your intern’s skills and work ethic before commiting to bringing them on as a permanent employee
• Over 200 candidates ready for an immediate start
We have interns ready to fill roles. Get in touch today!
Tel: 01234 432988
Email: hello@autotechacademy.co.uk
Web: autotechacademy.co.uk
Incentivised by high Euro NCAP ratings, car manufacturers are equipping even their most basic models with high levels of ADAS equipment
With motorcars evolving at a faster pace than ever, technicians need to keep up to date with upcoming technology types and current repair techniques, leading Rob Marshall to focus on Bosch's 2023 ADAS training offerings
It is quite easy for some garages to exist within a bubble. With rising interest rates, burgeoning inflation, unpredictable used vehicle values and restricted new car supplies, private motorists and fleets are keeping hold of their cars for longer. The result is that aftermarket technicians especially are being kept very busy, keeping these older vehicles safe.
Even so, this situation can isolate technicians from not just the latest technology but also the most recent repair techniques. With garages having such busy days, it is a brave move to take valuable time out for training. Yet, it is crucial to your survival.
Take ADAS as an example. While the technology is evolving rapidly from driver assistance to part autonomous systems, many of the hardware components have been fitted to cars for at least a decade. It seems crazy that, despite their rampant digital sophistication, virtually no ADAS system can calibrate itself without any technician input.
Therefore, manual calibration is essential to complete a safe repair. This may bring you in conflict with a customer, who may need persuading that the extra expense is essential to ensure that the vehicle's driver assistance systems work with and not against the driver. While it is true that an uncalibrated system is unlikely to flag a dashboard warning message, it can generate fault codes, or even cause the car to brake/accelerate suddenly for no apparent reason.
operations, which it covers under
Bosch is one such specialist that can help you. While it has a variety of online and in-person training events scheduled throughout 2023, Bosch is hosting a trio of ADAS offerings,
dependent on technicians' needs, all of which offer IMI qualifications and count towards your Continuous Professional Development.
Course VSB40 will be held on the 1st of September as a single-day face-to-face introduction to ADAS. It includes an overview of the various technologies, such as adaptive cruise control, traffic sign and speed sign recognition and blind spot monitoring. It explains the functions of RADAR, LiDAR, cameras and ultrasonic sensors that are necessary to enable such features to be effective. Some practical exercises are included, including calibration procedures with Bosch's DAS 3000 ADAS equipment and Bosch's KTS tools for diagnostic interrogations.
Due to vagaries in the IMI qualifications, the one-day VSB40 introduction is an IMI Level 3 course, whereas the two dayslong VSB41 provides you with an IMI Level 2 ADAS calibration award. You have a choice of either taking time away on the 5th and 6th of October, or taking the course in a trio of two-hour online modules within a virtual classroom, plus a half-day assessment.
The first day of physical training includes both ADAS theory and practical exercises that you conduct under the guidance of a tutor. It also encourages familiarity with the procedures and test procedures, again, using Bosch's DAS 3000. Day Two comprises the assessment, carried out unaided. This includes not just a practical assessment but also a multiple-choice paper.
The online blended learning alternative is split into four modules. The first one looks at how to set up the workshop correctly and details the importance of wheel alignment. Module Two includes an ADAS Code of Practice and how to use Bosch KTS and ESi diagnostics, plus the ADAS setup and the relevant software programs. The third module is dedicated entirely to practical exercises with the DAS 3000. The final practical assessment must be conducted in person, although you can complete the multiple-choice assessment online.
also learn where the various sensors are positioned and how to diagnose and even replace them - such as this RADAR and camera
Technicians that need more advanced ADAS diagnostic skills are catered for by Bosch's VSB47. You will need to have completed VSB40 and VSB41 beforehand, because VSB47 builds upon the knowledge gained from those courses. While offering an IMI Level 3 award, the theory lies firmly in IMI Level 4 territory and discusses the route that is being taken towards autonomy. It also includes information about sensor fusion, which brings together multiple inputs from different hardware, plus RADAR functions. The two-day course comprises a single day of training, with another half day of practical assessments, after which time you will be proficient in identifying and knowing how all of the ADAS system components work. Furthermore, you will be equipped to conduct advanced diagnostic test routines on not just the whole system but also individual components and use all of the available data to identify faults, as well as identifying, testing repairing and replacing any faulty parts found.
To begin, start by swapping over the inlet camshaft sensor with the exhaust camshaft sensor – they are the exact same part so this is often a very quick task. The fault migrates to the exhaust camshaft then replace the sensor, see Figure 2
If the fault stays on the inlet camshaft sensor then proceed to check the wiring. You will need a 5v feed, ground and an intact signal wire between the inlet camshaft sensor and the DME to prove the 5v supply and earth is being provided by the DME, see Figure 3
The fault presents with the engine management warning light illuminated and fault code 2968 stored in the Digital Motor Electronics (DME) from the inlet camshaft sensor. This fault can have many possible sensor-related causes – a faulty part, an incorrect part being fitted, faulty wiring, as well as sensor corrosion or damage. It may also indicate a DME internal fault or an inoperative inlet VANOS unit.
The valve gear on the N12 engine is equipped with variable camshaft timing control for the inlet and exhaust camshafts (also known as double VANOS). Both camshaft sensors record camshaft adjustment, via a sensor wheel fixed to the camshaft. The camshaft sensor works according to the Hall effect. Voltage is supplied to the sensor by the DME with 5 Volts and ground. The sensor then returns a digital signal via the signal line back to the DME, see Figure 1
Next, check the signal pattern with an oscilloscope. A signal indicates that the sensor is working, whilst scoping at the DME end will also check the integrity of the signal line. The signals, shown in Figure 4, are correct from a verified N12 running engine. Both the intake and exhaust camshaft sensors should have an identical scope pattern, just at different positions on the screen.
The Opus IVS 360 live support team has seen cases where nonOE or used camshafts have been fitted. When doing so, you must make sure the camshaft is an exact match for the part removed. Figure 5 shows the scope trace from an N12 where an incorrect inlet camshaft was fitted. We can see that with this alternative aftermarket part fitted, the inlet camshaft sensor
Opus IVS, who provide diagnostics solutions backed by OE master technicians, explain a problem documented for the N12 engine used on 2006 to 2013 second generation MinisFigure 1 Figure 2 Figure 3 Figure 4
signal has four phases compared to the image on the known good engine with only three.
By scoping the inlet camshaft sensor and exhaust camshaft sensor, along with the crankshaft sensor, the timing of the engine can be checked non-intrusively too using phase rulers and graph rulers as shown, see Figure 6a & 6b below
The Opus IVS DrivePro Elite diagnostic tablet offers a remote services VCI and coverage for 64 brands. It also comes with IVS 360 live support included, from a team of brand-specific OE master technicians. Opus IVS says this example is just one from within a library of hundreds of documented processes which the team can call upon to support customers with live repair guidance.
For even more in-depth solutions, garages can rely upon the pay-as-you-go appointment-based Remote Assist Program (RAP). This brings independent garages enhanced capability to complete a huge range of complex programming and coding jobs on-demand. www.opusivs.com
Autotech Training is an IMI approved training provider, delivering MOT, Electric/Hybrid vehicle and technical training services to workshops from its training hub in Milton Keynes and also at customer workshops.
Upcoming courses at its training hub include: A 2-day IMI LEVEL 3 Award in Automotive Air Con servicing and maintenance starting 21 June; 2-day Level 3 Award in EV/Hybrid system repair and replacement on 26 June; Level 3 in refrigerant handling on 30 June and 2-day Level 3 MOT Manager Training beginning on 3 July.
For more information and plenty more dates, visit https://autotechtraining.co.uk.
This example is just one from within a library of hundreds of documented processess which the team can call upon to support customers with live repair guidance
Delphi Technologies has released a Tesla e-learning module on Delphi Academy, the first in a new series of brand-specific online training courses.
Coinciding with the new release of Tesla Model S and Model X coverage on Delphi’s BlueTech VCI diagnostic tool, the ten-part course covers vehicle identification, data, and parts ordering before moving onto diagnostic hardware, connection, and common jobs.
“Everything is a little bit different when it comes to Tesla,” said Philip Mitchell, European Workshop Solutions Manager at Delphi. “But garages needn’t turn away these cars, they just need to understand how they’re different – that’s why we’ve released this new Tesla module.”
Tesla’s browser-based diagnostic tool requires technicians to correctly configure a laptop or PC for vehicle connection. Further difficulties arise after successful connection as Tesla’s distinctive IT-based jargon used within the tool can be problematic. The new e-learning course includes step-bystep video guidance, walking technicians through what can otherwise be a frustrating and time-consuming diagnostic process.
“The first stumbling block workshops face is knowing exactly which model they’ve got,” said Philip. “Knowing if it’s a Model S or Model X isn’t enough because they all use different processors, and the method of vehicle connection will depend on which processor it has.
“And then you’ll have to get through a layer of Microsoft security if you want to use Tesla’s browser-based diagnostic tool. Unless you correctly configure your computer beforehand, all vehicle communication will be blocked, and you won’t be able to connect to the car.”
Those achieving a 70 per cent pass mark or higher in the exam at the end of the module gain a Delphi certificate and IMI Continuing Professional Development (CPD) credit.
Delphi Academy hosts more than 200 learning modules with multi-media learning methods including interactive technical articles, videos and simulators for all levels of ability. New content is added on a monthly basis. The next brand-specific training course, due to be released in the summer, will cover PSA Group diagnostics.
Further information about Delphi Academy can be found at: https://academyuk.delphiautoparts.com/#/publicdashboard
Flintshire garage completes record e-learning hours
Hillcrest Motor Services in Flintshire, Wales has been recognised for completing a ‘record number’ of e-learning hours on the Delphi Academy online learning platform, completing more than 33 hours of training in less than four months, averaging half an hour a day.
Delphi presented garage owner Ivo Civicchioni with a Certificate of Outstanding Achievement and a voucher for further training. “We’re getting a few electric and hybrid cars coming in for MOTs now and being able to recognise the components and understand the fundamentals gives us that confidence to have them in the workshop,” said Ivo.
“I've been to lots of classroom courses over the years but, the trouble is, they can be quite expensive. That’s why digital training has been such a revelation for us.
“You’ve just got to be dedicated, make the time and effort to complete the courses. I've clocked up a lot of hours because when I get going, I really do find it interesting. I can sit down thinking I'll do an hour and sometimes I end up doing five.”
Tesla's browser-based diagnostic tool requires technicians to correctly configure a laptop or PC for vehicle connection
Nissens offers education in various forms, from live onsite sessions, through online self-learning courses, to technical marketing materials in print and digital formats. It has expanded its Training Concept – offering material on air conditioning, engine cooling, efficiency, and emissions, with a series of free live webinars conducted by product specialists. Nissens also offers free online training through its portal at https://ntc.nissens.com/. You can also watch recordings of past events on www.facebook.com/nissensautomotive
Recordings will be made available on the Nissens Experts portal – an internet platform with a library of more than 100 technical assets, including technical stories, tips, bulletins, and tools dedicated to technicians.
Upcoming events include ‘New refrigerants: Why use R1234yf and CO2 instead of R134a? Why are so many other refrigerants
With over 1,900 Control Arms covering over 90% of popular vehicle types, febi is your No.1 for Steering & Suspension parts manufactured in OE-Matching Quality.
The febi Quality Confidence
Due to the forces occurring when accelerating, braking and cornering febi Control Arms are manufactured using highgrade materials and use high-quality ball joints and bearings with the correct rubber hardness.
Provide the complete repair solution with febi ProKits which include all the necessary mounting parts for quick and efficient repairs.
Your No. 1 for Steering & Suspension
BY YOU
being tested and approved?’ on 16 June and ‘Oil, why can’t we just use a universal one?’ on 29 June.
It has also added a couple of modules to its online training programme, explaining how air conditioning (AC) service and repair should be conducted on popular PHEV models. Training Manager Michael Ingvardsen explains: “We see an increased demand for training in modern HVAC systems. The recent months have been extremely busy for us in terms of educating our customers in live and webinar-based training seminars. The many courses that have been held in Europe and the US have given us a clear idea of what technicians need, to become even better at understanding and servicing HVAC and heat pump systems in hybrid and electric vehicles, and what we’ve learnt, we now make available for everyone in the aftermarket.”
www.nissens.com/ntc
www.febi.com
autotechnician visits Britannia MOT & Repair Centre in Aylesford who make full use of the trade’s business support to overcome challenges and take on new opportunities, while the husband-and-wife team pass on their support to its staff, customers and local hospice
I pull up to Britannia, which sits in the heart of an industrial estate in Aylesford, North Kent. The workshop has a prime position, surrounded by car dealers and retail units, and judging by the number of cars in the workshop, my first impressions are that business is good.
Husband and wife team Mick and Roz Bentley oversee the technical and operational side, respectively. Mick moved around independents straight out of school and came to Britannia in 2002. “The garage had been open 14 months when I started here, an elderly couple had opened it later in life. I worked for them for about a year then started running it. As they got into health problems about twelve years ago, I bought in and eventually bought the rest of it. We have five technicians, across four bays and an MOT bay. We don’t specialise, we’re
a general repair garage – there’s very little we turn away. We service all makes, up to time and chain replacements, engine replacements, anything.”
Rather than being a threat to the local dealers they have become part of their support network, and they’re getting busier all the time. Their diagnostic armoury includes Snapon equipment, Delphi tooling and a Bosch KTS. They often use Opus for its technical support, when performing software downloads and using its remote service (IVS 360) for more complex tasks. “Where Opus are good,” explains Mick, “if it's something that's not on their system, they've still been able to access it remotely and get to the bottom of it for us. They’re quick coming back to us too. The younger ones like it down there as they can contact them via an app on the tablet.” There’s not one piece of kit that will do everything, so they are looking to invest in a new piece of diagnostic equipment – one of the reasons they are heading to Automechanika Birmingham, 6-8 June.
Mick and Roz place a high priority on training. “Everyone apart from Cam, who's only just recently joined us, is now Level Three mechanical, Level Three hybrid & EV. We did the Hybrid/EV through the IGA, they offer members a discount on those. We've just signed up with Euro Car Parts (LKQ Training Academy) for another 20 training days and 20 online courses as well.”
Roz is set to do some mental health courses with the St John Ambulance so they can better support their staff – a requirement that was realised following the pandemic lockdown, which they both found tough. Roz explains: “It was like through no fault of our own, business was failing around us. Every job rung up and cancelled, the phone didn't ring, the diary was empty…” But they’ve come back stronger: “We came back
with the best year we've ever had the year after that and now we're on course to beat that, not by a terrific amount, but with the cost of living, we're still grateful for that.”
They’ve introduced Pay Assist to help customers spread the cost of unexpected bills and provide discounts through a loyalty scheme, which is proving popular and has really helped some people. “It’s better that someone gets the work done and can spread the cost rather than having a car that's dangerous and really needs the work.”
The couple have accessed the support available from automotive charity Ben, to help a previous employee who was struggling. “He had some sessions, ultimately it didn't resolve it but it was nice to be able to offer that,” commented Roz. “We know our staff really well, we are a little family, but everyone has got their own lives, partners, kids, their family problems. You can't help bringing them with you to work at times. So, it's just trying to manage that.”
They are signed up to The Motor Ombudsman, which provides an arbitration service between customers and garages when complaints escalate but have not had use this to date. Mick says: “We should never get to the point of having customer complaints that accelerate that badly. We should be able to deal with it.”
“We have a lot of dealings with the IGA, they have been absolutely amazing,” says Roz. "In addition to the training, they were really useful during COVID, they helped us get a reduction on our rates which we didn't know we were entitled to. We fell into this bracket where we didn't get much support and without furlough, I'm not sure what we'd have done. But they were really helpful."
Mick is keen to highlight the service and support provided by Garage Services Online. “They’re fantastic. We've been online since ’94 but we’ve had a lot of problems with websites.” Roz says the original site was enormous and resembled the Yellow Pages with far too much content. Mick found two or three garage websites he liked that had been built by Garage Services Online and got in contact with them. “We had a lot of involvement on how we wanted it – what the tabs should be, how we wanted it to look. The relationship with them is fantastic.” “They're really intuitive because it's what they specialise in, rather than the people we've been with in the past who hosted websites for hairdressers, building firms…” adds Roz. Following their guidance and How-To guides, Roz can make amendments to the site, which is something she’s not been able to do before and rather enjoys. “With previous hosts, if we just wanted to put, say, five pounds on a price of the service and MOT offer, it would take them a month to alter and they'd charge us for it; with Garage Services it's the same day or next day and it's done.”
Since the new searchable site was launched one year ago, they have noticed an influx of new customers that are in their late 20’s, early 30’s – a group more comfortable with sourcing services online.
“There's been a bit of a domestic down in the workshop,” Mick chuckles. “Becky’s been with us a couple of years and we've just taken her boyfriend on! We’ve got to keep staff numbers up because of the amount we're doing here but finding staff in this trade now is impossible.”
As a world-renowned manufacturer of the highest-quality motor oils, additives, vehicle care products, chemical repair aids as well as service products, adhesives and sealants, we offer you the full range for the technical and visual preservation of vehicle value. A unique variety of products that you can only find at LIQUI MOLY.
With us, you get everything from a single source. This saves you a lot of time and money. A strong argument for retailers, workshops and consumers alike. Benefit from this added value, and take advantage of our product range and product expertise!
They poached Cam from another garage, but he was clearly ready to leave. Mick explains, “He’d been there since he did his apprenticeship. There's a fear of leaving your first garage because you think all the skills you've got are because of the people around you but he’d been neglected, and he had only done his Level Two and was being paid minimum wage. He did the first part of his MOT training last week here, which has given him the Level Three access. He kept telling Becky he had massive boss envy. We do look after them, but we appreciate what they do for us”. The team regularly go out socially together with their partners, to get a change of scenery and touch base with everyone outside of work.
Their landlord retired last year and gave them first refusal, they didn’t particularly want the additional stress of buying the premises but had a great relationship with him and didn’t want another landlord coming onboard so took the leap. The ‘straightforward sale’ took seven months but with hindsight has worked out well. “The plus side is now we can make workshop plans; there’s a new mezzanine going in. There seems to be this conception with EVs that they should be looked after somewhere akin to an operating room. So, we're going to change the whole look of the workshop, spread all the ramps down one side, get the floor painted, have fitted toolboxes in each bay, EV chargers, we're going to go for it!”
“I went through the period where the first electronics come out on cars and so many people just didn't want to know, so they shut down. Then it happened again with the MOT computerization, and I can see we're heading into another period where people can't be bothered to keep up with the training, when EVs start getting more problems.” But they have begun the training and are getting EV customers from miles around.
“A lot of that is coming through HEVRA – they’re really good people to deal with, a real passion to them as well, which is nice. Rather than wait until everyone's trying to make their daily money out of EVs, it’s better for us to get in beforehand and learn it at a slower rate.”.
Through the LKQ Academy they want to remain a touch ahead of the game and get the staff trained up to Level Four Hybrid/EV, and to gain advanced diagnosis skills.
They try to update customers a couple of times a week on Facebook, sharing cautionary horror stories, an unusual car or classic that comes through the shutter doors. I suggest that a lot of people would also appreciate the way they look after their staff and if people must spend money on their vehicle, they’d rather give it to an independent, family business who are doing business in a good way. Mick enjoyed seeing a recent recommendation for them on the Aylesford Facebook page. “Someone new to the area was looking for a local garage. A competitor responded with, ‘What do you want done, mate?’ One of our customers went on there and said ‘Use Britannia. They're awesome and they support local charities’. Having our own customers promoting us like that, that’s gold.”
I had researched feedback on the business and could see many longstanding customers whose entire family’s fleet of vehicles had been looked after them for years, praising their honest, transparent and friendly nature. One recommendation came from a regular customer who sent his daughter who had just
passed her test along to them alone, because they knew that she’d get treated properly there. “I’ve always found that a really nice comment – a lot of women are paranoid to go into garages, let alone at that age.
“Women are easier to deal with on the counter because you get past the 'men know about cars' nonsense, says Mick. “Women will actually just explain far easier what the problems are, where a man will stand and tell you, ‘Oh, I know what this is’. That's why Becky is such a good mechanic. She's got a very different view to it. She’s more methodical, puts a lot more thought into it. She's also more academic than the rest of us down there, she's straight into the technical documents – when we sent her on her EV course, she beat every bloke in the room hands down, which was expected.”
Silver lining
“This could well be a three-year degree course now and you would still come out wanting.” I agree, mentioning that the best technicians I have ever met have said they are learning every day. “That's what I'm enjoying more now, when the problem with my hand started, I was not happy I'd come off the tools at all, but with hindsight, it's worked better, because when we got them three down there at that age, I can now spend my day mentoring, guiding, passing skills on, which is nice.”
This shift in focus has also instigated a relationship with their local Heart of Kent Hospice. They have a not-for-profit agreement on their fleet of eight vehicles – they do not charge labour, for MOTs, or parts; getting these at cost-price from Euro Car Parts, GSF and Motor Parts Direct.
The Hospice helped Roz’s father when he was very unwell, and the team are happy about the role they play to ease one of the hospice’s burdens. Roz explains: “It's not part of the NHS; they have some funding but nowhere near what they need to run it. It's an incredible place”. David, the Hospices’ Corporate Partnership Manager, has said: 'Partnering with local businesses is so valuable to the hospice. The support we receive from Britannia helps to keep our fleet on the road while saving money. There's an obvious caring ethos among the whole team at the garage who all willingly seek out proactive ways to continue their support. It's this generous community support which helps us to be there for patients and their families that need our care.’
“With garages, there's such a reputation of everyone getting ripped off and it's nice to try and change it a little bit. It’s been a real eye-opener with the hospice. It was a shock to me how many customers were coming in and saying thank you for doing it, as they’ve helped with relatives.”
The garage is an IAAF finalist this year for ‘Best single site garage’ and ‘Community Support Award’. We wish them the very best and will no doubt be hearing more about their incredible journey in the future.
https://garage-services-online.co.uk
https://lkqacademy.co.uk
www.hospiceintheweald.org.uk
The Bosch Car Service (BCS) concept is designed to boost a workshop’s performance, sales, and marketing, providing the network with technician training, business support and access to its technical helpline. Garages must meet set criteria to join the network – some of the boxes that garages must have ticked include professional designated working areas and reception, the use of BCS signage and branding, and the ability to provide bumper-to-bumper all-makes servicing/MOT/diagnostics & electrical/mechanical repairs with a minimum of three ramps, staffed by three or more full-time technicians. All garages commit to a strict Code of Practice that is recognised by the Chartered Trading Standards Institute.
Bosch Car Service has just welcomed the largest independent garage group into the fold. The additional 16 branches of Elite Garages extends the network to more than 350 locations across the UK and Ireland.
David Lomas, the head of Bosch Car Service at Bosch UK & Ireland, said: “Everyone at Bosch Car Service is looking forward to working with our new partners at Elite Garages. Like all the partners in our network, Elite Garages provide expert advice, repairs and service and they have a long history of running a successful company. We have more than 350 Bosch Car Service locations across the UK and Ireland, and we’re excited to expand that to include Elite Garages’ network across southern and southeast England.”
The Independent Garage Association (IGA) says that its members are increasingly turning to them for guidance on how to reduce costs and manage their suppliers as business costs continue to rise.
Frank Harvey, Head of Member Services for the IGA explains: “With the cost of living and business overheads at an all-time high, getting the best price for outgoing bills is imperative. UK Garages are relying on the best rates, guidance and offers to help control their costs”.
Frank continues; “IGA members can drive down costs by utilising IGA’s bespoke Invoice Checker service, in association with Spiral Utilities. This is just one of the benefits of being part of the IGA member community. Our members can ensure that they aren’t getting caught on ‘roll over’ or expensive utility contracts.”
IGA’s Invoice Checker service helps garages to minimise
Elite’s management became interested in the Bosch workshop concept at the UK Garage and Bodyshop event in 2022. Elite’s Kelsie Whittemore said: “We wanted to partner with a premium brand like Bosch who have the trust, confidence, training, and equipment expertise to support our business. And we also wanted to have ability to use the Bosch corporate training programmes to support with staff recruitment and retention. The other key focus areas within Bosch are their expertise in Electric and Hybrid vehicles and also the Advanced Driver Assistance Systems (ADAS).”
For more information about Bosch Car Service, please visit www.boschcarservice.com/gb/en
time and the cost for these essential utilities by searching out the best deals in the market, and handling all aspects of the renewal process, with no charge to the member.
IGA members have access to a host of member benefits, along with exclusive offers from automotive industry businesses, including: A member helpline, technical training, MOT QC and Health & Safety schemes, online technical forum and helpline, exclusive commercial service offers for technical data and diagnostic tools, legal and HR advice, preferential training rates at RMI Academy of Automotive Skills sites, ability to join the CTSI-approved consumer code scheme, Trust My Garage (audit permitting).
To find out more about IGA membership, please visit: https://independentgarageassociation.co.uk/ membership-packages-pr/
If you are looking to boost efficiency, customer reach or profit from new revenues, or looking to save cash on your workshop bills, read on!
Castrol has launched a new app, Castrol Fastscan, that rewards workshops every time they purchase qualifying Castrol branded products and provides access to guidance, training, and technical support materials.
Workshop owners using Castrol Fastscan accumulate points for the purchase of Castrol EDGE, MAGNATEC, GTX, TRANSMAX and motorcycle branded products and can redeem those points against consumer electronics and home appliances. The first 200 workshops to sign up for the new app will receive 1,000 ‘free’ welcome points.
Castrol SERVICE workshops which participate in Castrol Fastscan will automatically have access to additional exclusive rewards. Over 220 independent workshops in the UK are already part of this network, allowing them to use ‘Castrol SERVICE’ branding. Participating businesses receive a range of benefits including a Castrol guarantee for the oil used in customers’ vehicles, operation quality certification, branded technician clothing, along with marketing support and training.
The Fastscan app also allows users to access an all-new knowledge hub containing technical support, ‘How To’ videos, and articles focused on vehicle service and maintenance topics. To join, workshops just need to source Castrol products from distributor The Race Group. To find out more, visit: www.castrol.co.uk/fastscan
Castrol is introducing a new independent certification provided by the TÜV Rheinland Group for its Castrol SERVICE workshops to help optimise operational standards and further build customer trust.
To become certified, participating workshops will receive information on what is required, and after a positive selfassessment, they can apply for an audit. TÜV Rheinland will then assess operational procedures in the workshop across business organisation, workshop appearance, process and transparency, technical and equipment, health, safety, and environment. After a successful audit, workshops receive a Castrol Certified Partner certificate and a certification shield for display at the workshop. A range of online assets are also available to use.
Eden Tyres & Servicing has become the first Castrol SERVICE workshop in the UK to obtain independent certification. Jim Nicholls, Eden’s Retail Director, said: “We’ve always been passionate about providing our customers with the very best levels of service. By becoming independently certified by TÜV Rheinland, our customers can be further reassured that they will receive a transparent, high-quality experience. It’s great to have become the first Castrol SERVICE workshop in the UK to receive this certification, a distinction that I’m sure will benefit our business.”
A ‘Google My Business’ service, offered as part of the Castrol SERVICE network, includes creation of a Google profile for the participating workshop, highlighting the location, opening hours, contact details and current offers available to customers. Participating workshops will also receive a monthly update from Google Business Insights, helping them track website traffic and activity.
Find out more about becoming a Castrol branded workshop at: https://bit.ly/Castrolbranding
LKQ Euro Car Parts, MPM Oil, Pagid, Schaeffler, Shell, Valeo, Varta, and ZF Aftermarket have launched a new garage concept to help navigate the ever-changing automotive landscape and provides independent workshops with the tools, training, and business support they need to grow.
1TEC Auto Hub delivers the latest technical and diagnostic data to facilitate a first-time fix, marketing support and materials, business support to help unlock further revenue streams, training including access to LKQ Euro Car Parts’ LKQ Academy, and a rewards platform.
Kevan Wooden, chief commercial officer, LKQ Euro Car Parts, said: “Collaboration is key in these times of rapid technological and regulatory change in our sector, while access to the latest tools, training and technical data is vital to garages working on modern vehicles.
Garage management system, TechMan, has made it to the finals of the IGA (Independent Garage Association)
BIG Awards which takes place at Leicester City Football Club on 22 September.
TechMan was born in 2015, to enable workshops to gain a tighter grip on the day-to-day running of the business. Owner, Terry Dorney, and the TechMan team has built the system from the ground up, using their real-time frustrations and knowledge to identify gaps in the market and create suitable solutions to assist technicians.
“This is why, through 1TEC Auto Hub, we’re seeking to create a network that supports a professional community of independent workshops and empowers them to futureproof their businesses.”
Members are required to meet a set of criteria to ensure consistently high standards of service.
Kevan Wooden continued: “In a market where poor service can have such tangible implications, we recognise the importance of developing trust with customers. Our ambition is to develop 1TEC Auto Hub into a brand that consumers actively seek out for best-in-class customer service and efficient, effective service maintenance and repair work.”
www.1tec.co.uk
Through its research and development on the needs of workshop owners, it continues to add new features to automate and reduce daily admin tasks to help independent garages and technicians boost efficiency, improve customer service, increase productivity and grow profitability.
For more visit information, or to arrange a demonstration, visit www.techmangms.com, or call 01604 666 720
Running a workshop can indeed be a challenging yet fulfilling endeavour. Among these challenges, three key words stand out: Technology, money, and planning. The rapid advancements in technology require workshop owners to constantly adapt and integrate new tools and systems to stay competitive. Financial management is crucial for ensuring a healthy cash flow, managing expenses, and making strategic investments. Additionally, effective planning is essential for setting goals, establishing a roadmap, and responding to market dynamics.
However, one more critical factor that workshop owners often face is staffing, or the lack thereof. Independent workshops frequently struggle with finding and retaining skilled staff members, leading to increased workloads, compromised service quality, and hindered growth. The shortage of qualified technicians and administrative staff poses a significant challenge to the success and sustainability of workshops.
The good news is that, despite these challenges, there are simple yet powerful steps that workshop owners can take
to guarantee the future success of their businesses. By implementing strategic measures, workshop owners can overcome these obstacles and thrive.
Our goal is to help garages stay in business and become more profitable. With over 15 years’ experience in helping businesses of all shapes and sizes, ActionCOACH understands the importance of business coaching, and through working with us at Maverick Diagnostics, they have gained a good understanding of the automotive aftermarket. Together, we have created the following ten fundamental steps as a guide to help you guarantee the future success of your workshop:
Business coaching offers numerous benefits that can positively impact your workshop. It provides you with an external perspective, allowing you to see your business through fresh eyes and gain valuable insights. A business coach can help you identify strengths, weaknesses, and opportunities for growth, enabling you to make informed decisions and implement effective strategies to drive success. Additionally, business coaching can assist in overcoming any obstacles that may be hindering your workshop's progress, ultimately leading to improved performance and profitability.
Planning is the foundation of a successful business. It is crucial to develop a comprehensive plan that goes beyond day-today operations and encompasses your long-term vision. By setting clear goals, creating actionable strategies, and defining measurable objectives, you can ensure that your workshop remains focused and aligned with your desired outcomes. A well-crafted plan also enables you to adapt to market changes, identify growth opportunities, and make proactive decisions to future-proof your business.
Running a workshop often requires making tough decisions that impact the direction and growth of your business. This could involve evaluating your staffing needs and making necessary adjustments, such as hiring, training, or restructuring your team. It may also involve investing in new technology or upgrading existing systems to improve efficiency and stay competitive. While these decisions can be challenging, they are essential for the long-term success of your workshop. Embrace change and be willing to make difficult choices that will ultimately drive positive outcomes.
Knowing when and what to invest in for is crucial for the success of your workshop. However, it's important to approach these investments strategically. Assess your specific needs, consider market trends and customer demands, and research the latest advancements in the aftermarket. By identifying the tools that will enhance productivity, deliver superior results, and provide a competitive edge, you can make informed investment decisions that yield a significant return on investment in the long run.
Understanding your finances is vital for making sound business decisions. Track and analyse key financial metrics such as revenue, expenses, profit margins, and cash flow regularly. This information empowers you to identify areas for improvement, optimise your pricing strategies, control costs, and make informed financial projections. By staying on top of your numbers, you can make strategic decisions that ensure the financial health and stability of your workshop.
Effective business planning extends beyond creating a plan on paper. It involves translating your strategies into actionable steps and implementing them in real-world scenarios. Break down your long-term goals into smaller milestones and create a timeline to track your progress. Regularly review and adjust your plans based on market trends, customer feedback, and internal performance indicators. Real-life business planning involves actively monitoring and refining your strategies to ensure they align with your evolving business environment.
Pricing your services appropriately is a delicate balancing act. It's important to set prices that are competitive within your market while adequately covering your costs and generating a reasonable profit. Conduct market research to understand the pricing landscape, analyse your value proposition, and consider factors such as labour, materials, overhead expenses,
and desired profit margins. Transparently communicate the value you provide to customers and be prepared to adjust your pricing strategy as needed to maintain a healthy balance between profitability and customer satisfaction.
Exceptional customer service is a cornerstone of a successful workshop. Managing your customers' expectations is crucial for building trust and loyalty. Clearly communicate your services, set realistic timelines, and provide regular updates throughout the process. Be transparent about any limitations or constraints that may affect the delivery of your services. Honesty and reliability are key in managing customer expectations. Ensure that you have clear communication channels in place to address any concerns or questions promptly. By consistently meeting or exceeding customer expectations, you can build a strong reputation and foster long-lasting relationships with your clients.
A deep understanding of your local market is essential for the sustained success of your workshop. Stay updated on industry trends, watch your competitors, and identify any gaps or opportunities within your market. Conduct market research to understand the needs and preferences of your target audience and tailor your services and marketing efforts accordingly. By staying informed and proactive, you can position your workshop as a leader in your local market and capitalise on emerging trends and customer demands.
Staffing is a critical aspect of workshop management. Analyse your business needs, including the volume of work, skill requirements, and customer demands, to determine the optimal number of staff members. Understaffing can lead to overwhelmed employees, compromised service quality, and customer dissatisfaction. On the other hand, overstaffing can result in excess labour costs and inefficiencies. Strive to find the right balance by forecasting workload, conducting skills assessments, and scheduling staff accordingly. Regularly evaluate and adjust your staffing levels to maximise productivity, maintain service quality, and drive profitability.
By following these ten fundamental steps, you can lay a solid foundation for the future success of your workshop. Overall, running a successful workshop requires a holistic approach that encompasses technological adaptation, sound financial management, effective planning, and strategic staffing. By proactively addressing these challenges, and following the proven steps to success, workshop owners can position their businesses for a prosperous future in the dynamic automotive industry.
Remember that running a workshop is an ongoing journey, and continuous improvement and adaptation are crucial.
The Motor Ombudsman, and its predecessor Motor Codes, have been supporting businesses in the service and repair sector for the past 15 years as part of their accreditation to its comprehensive Motor Industry Code of Practice for Service and Repair. The Code was launched to the motor trade in May 2008 to drive up the standard of work and service during the maintenance and repair of customer vehicles, and to reduce the occurrence of customer complaints.
More than 7,000 independent garages, vehicle manufacturer authorised repairers, and body repair centres across the UK abide by the 50 guidelines laid down by the Code. It was recently announced that mobile mechanics, tyre fitters, and smart repairers are now eligible to apply for accreditation.
The Motor Ombudsman’s in-house automotive dispute resolution service handles more than 100,000 contacts and 20,000 cases every year in relation to disputes across its four Codes of Practice. Demand from consumers for help with motoring-related complaints has been steadily rising this year, against a backdrop of increased financial pressures on households. In the first quarter of 2023, they saw a 25% increase in the number of contacts received from consumers (compared to the same period in 2022), with the number of cases accepted for adjudication rising by 30% compared to the same three months the year before.
In order to sustain high levels of service, and the swift delivery of case decisions to accredited businesses and consumers, The Motor Ombudsman has continued to invest in back office systems and expand the number of people working within its dispute resolution team.
As part of their accreditation, workshops have automotive experts to call on should they need independent and impartial guidance and information at any stage of a service and repair complaint made by a consumer. This is coupled with the ability to signpost customers to The Motor Ombudsman to help conclude disputes swiftly and fairly if it has not been possible to do this directly with a customer in the first instance.
Accreditation to The Motor Ombudsman grants exclusive use of the body’s widely recognised logo, and that of the Approved Code from the Chartered Trading Standards Institute (CTSI). Both are visual endorsements and important signs of reassurance to vehicle owners that a business is looking to go the extra mile and do everything they can to ensure customer satisfaction.
Promotional opportunities for businesses, as well as potential customer leads, are provided through a bespoke profile and booking contact details on the body’s online Garage Finder, which can also be populated with the latest promotional offers and services.
Businesses are also eligible to be nominated by their customers for a regional Garage Star Award, an opportunity for them and their staff members to be recognised for going above and beyond to assist consumers.
The Motor Ombudsman issues regular communications on industry trends and invites members to online webinars and events with expert speakers throughout the year.
Costing from less than £21+VAT per month, garages and mobile mechanics can apply for accreditation to The Motor Ombudsman’s Motor Industry Code of Practice for Service and Repair by visiting www.TheMotorOmbudsman.org/ garages/tmo-accreditation
Meet the team at Automechanika Birmingham, 6th to 8th June, on Stand F117 in Hall 20.
We cannot say that we were not warned. Five years ago, Wendy Williamson, former Chief Executive of the Independent Automotive Aftermarket Federation (IAAF), told us that the luxury of unimpeded access to the OBD port was under threat. She highlighted that the then new Fiat 500 had its OBD port closed off and that the Volkswagen Group and BMW were following suit with their newer models. The aftermarket, therefore, had to ready itself for battle with the vehicle manufacturers (VMs) to ensure that repair information remains accessible and available. The fight was on.
Fast forward five years and the situation has become more entrenched. The connected vehicle is becoming commonplace and is an "IT system on wheels", as Mark Field the IAAF's new Chief Executive, states. The problem with the connected vehicle is that the technology's premise is very difficult to oppose. As reported in the 4Focus section of this magazine in prior issues of AT, many manufacturers have vehicles that send
data not only to and from each other but also to and from the cloud. This information is used to enhance road safety, by, for instance, sending, receiving and comparing weather, road and traffic conditions. Even if all else fails and a crash occurs, eCall SOS (another legal requirement for all new cars) will contact the emergency services automatically, in case the occupants are incapacitated. Digital technology can also mitigate driver errors and prevent the law from being broken, such as using speed sign alerts to remind the driver of the limits.
Legislation that protects against unfair competition is being overhauled. While primary legislation exists (including that related to block exemption), the devil is also in the detail, which is provided by secondary legislation that is being revised in Europe, currently. In the UK, the Competition and Markets Authority (CMA) completed its consultation on the 16th of May and we look forward to bringing you its conclusions.
For more information on the government response to the Block Exemption Order, visit the government website here.
With traditional vehicle manufacturing looking increasingly unprofitable, manufacturers are looking to data as fresh revenue sources. Rob Marshall looksManufacturers communicate many messages about data and automotive autonomy to drivers but they tend not to mention that it can be used to restrict service and repair choices
The amount of data received and transmitted by modern vehicles is staggering. Carmakers emphasise the importance of cybersecurity but mounting evidence suggests strongly that this is used as an excuse not to act in the spirit of anti-competitive legislation.
Yet, such systems have facilitated governments to impose certain technologies onto drivers, including the mandatory intelligent speed limiters and data loggers that became legal requirements for all new cars sold within Europe and the UK from last year. No wonder the authorities are in favour of automotive digital tech!
Related but similar
Naturally, advanced driver assistance systems (ADAS) feature within the Venn diagram of autonomous driving, even though autonomous driving is not an everyday reality, despite the exaggerated and incorrect claims made by certain carmakers and politicians. Yet, developments continue, aimed towards a future driverless car. The big question has to be 'why'? BMW explains succinctly that automated driving can only serve one purpose: to make driving safer and more comfortable (which is actually two) even though they may be other reasons in the background...
With autonomous driving being promoted as an ultimate force for good, it is especially hard for anybody, including spineless politicians, to argue against technology that promises to improve road safety and save lives. While BMW scooped most attention at April's Shanghai Motor Show with its ice cream public relations disaster, you might have missed BYD (China's reported largest EV manufacturer) stating that it thinks fully automated driving systems are unachievable and that businesses are investing a lot of money in the technology, which "will prove it leads nowhere." Time will tell who is right.
Even so, carmakers are quite adept at persuading legislators that having significant quantities of digital information floating around is a good thing, while using the technology as a vital revenue source. Elon Musk is so convinced about digital revenue that he claims that Teslas could be sold for zero profit and the business would still thrive. Yet, not everyone is happy,
"Naturally, ADAS feature within the Venn diagram of autonomous driving, even though this is not an everyday reality, despite the exaggerated and incorrect claims by certain carmakers and politicians"
VMs also have to consider the security of data received by car owners, such as telematics. This means that extra permissions and security features are needed to allow workshops to access this information. Even so, this should not be used as an excuse to engage in anticompetitive activities.
not least car customers. BMW faced a backlash last year, when it introduced charges to activate certain features, such as heated seats (£15 per month), heated steering wheel (£15 per month) and Driving Assistant Plus active cruise control (£35 per month). While independent workshops are getting used to paying for manufacturer permissions, it seems that the general public is not quite so willing...
Another problem is security. While governments can see the advantages of digital technology, they are scared of either mischief-makers, or those with more sinister motivations, such as hacking into cars to steal, or use them as weapons. Naturally, VMs have the perfect solution: security. By creating a seemingly impenetrable fortress, hackers can be prevented from inflicting misery onto the public, from activating air conditioning to driving the vehicle remotely. Of course, a further advantage for carmakers is that they can obtain the legal right to deny what they think are illegitimate access requests to their security gateways, thus creating an unfair competitive advantage in the repair market.
Thankfully, the aftermarket repair industry has spotted that car manufacturers (unintentionally or otherwise) can create a very cosy position for themselves, by locking out the independent repairer. While the IAAF and the UK Alliance for the Freedom of Car Repair (UK AFCAR) appreciate the need for cyber-secure vehicles, they insist that legislation is needed to ensure that vehicle manufacturers do not impose a monopoly to control all aspects of automotive diagnosis, service and repair. They also report significant and increasing evidence of car-makers abusing their dominant position, by restricting access to the vehicles and associated data.
UK AFCAR continues to gather anecdotal evidence from independent workshops that they are facing increasingly restricted access to data and repair information. One garage reports that it could not complete a fuel additive 'Eolys' tank replacement on a Peugeot Partner without taking it to a main dealership, because it could not programme the part to the vehicle. Another workshop reported issues with a Mercedes A-Class ADAS system, caused by a faulty radar control unit that it could not configure, because it could not access the
Worryingly, problems are not limited to repair tasks. Routine maintenance operations are affected, too. A technician reported to UK AFCAR that he could not access Hyundai’s online service record, meaning that the garage could not record the maintenance work that it had completed. Other independents reported similar issues with Citroen and Mazda's digital service records, too.
UK AFCAR says that it is unsurprised by reports of independent garages being locked out of repair and maintenance activities by some VMs. The organisation stresses the importance of the independent aftermarket working on a level playing field, as detailed in legislation, to provide car owners with an effective choice of where they take their vehicle to be repaired or serviced.
If you are experiencing issues with manufacturers refusing you access to their gateways, contact the IAAF via www.iaaf.co.uk
AT reader, Les Dufty, is unhappy. Yet, he loves his work. After leaving a 20-year career with Rolls-Royce engineering, he chose to venture solo and become an Alfa Romeo independent repairer. Much of this decision was based on his experiences as a customer. A catalogue of problems with his brand-new 1981 Giulietta 2.0-litre saloon led him to conclude that garages were to blame, rather than the car. He recalls apathetic main dealers, coupled with aftermarket garages' distrust of anything more technically-exotic than a Morris Ital, all of which resulted in him starting a successful one-man business that is approaching almost forty years of continuous trading.
While his view of Alfa's main dealers remains unchanged, virtually everything else has done. Independent workshops are now much more open about technical innovation than ever before, especially as the pace of automotive development has accelerated so markedly. Despite his continued prowess with older models, many current-generation Alfa Romeos enter his workshop, such as the stunning but surprisingly slow-selling Giulia saloon and Stelvio SUV. Naturally, restricted information via the OBD socket led him to encounter the Alfa/Fiat Secure Vehicle Gateway (SVG), access problems with which saw him invest in a new Snap-on Zeus. Unfortunately, despite the best efforts of Snap-on's technical support, he still cannot gain gateway access.
"Fiat's reason for not granting me access is because I am not VAT registered," Les explains,
"Yet, my accountant has forwarded evidence that my business, Automeo, is a legitimate trading business but we have not received any further communication since Christmas. I have been in limbo since then."
You are not alone...
Les is not the only one experiencing problems. Adrian Shilling from WAD Wolverhampton describes Fiat's server-based WiTech 2.0 as such a nightmare that he accesses the manufacturer's SVG through his SnapOn Triton D-8, an aftermarket tool that he bought
originally for its scoping features. Unlike Les, however, WAD Wolverhampton has a Fiat technical account and, therefore, permission to access Alfa Romeo data. While he reports that remote support is available, should you wish to do something fairly simple, such as changing an account password, nobody within the technical department at Fiat tends to respond with answers to more involved problems. Adrian tells AT that he is not alone with this finding and that he speaks to a lot of other Italian motorcar brand specialists, who also cannot receive help from the manufacturer regarding gateway access.
Snap-on told us that it has been granted permission to access the gateway for Fiat, Chrysler and Alfa vehicles using Snap-on Diagnostic tools if the user has registered with FCA directly. Unfortunately, this is an FCA/Stellantis requirement. Should registration be successful, you will be provided with credentials that must be inputted into Snap-on’s Profile Manager (FREE). You will then have gateway access.
Snap-on elaborates that OEMs choose how they allow access. Unfortunately, diagnostic manufacturers/ software providers are informed of the decision and how the process works by the VM concerned and have no influence over it. The procedure may vary between manufacturers but Snap-on reports that it strives to make the process as easy as possible.
Snap-on says that it has a good relationship with former FCA brands, thanks to its contacts with AutoAuth in North America, which is the automaker's chosen provider. This relationship has proven beneficial for the aftermarket, because Snap-on is adding Nissan to its secure gateway portfolio this spring.
To find out who is to blame in this case, AT telephoned Mopar, the spare parts arm of Fiat/Alfa Romeo, which took us straight to a representative in Italy, who promised that the appropriate person would get in touch. At the time of going to press, our questions have not been answered, indicating that criticisms of the FCA/Stellantis's support for the aftermarket have merit.
You are not mistaken in thinking that Autotech is more about recruitment than digital services. Both topics are related, because Autotech sees digital technology as vital to the next generation of motor industry talent. This is one reason why it launched its new brand, Autotech Connect in April, at the site of Millbrook Proving Ground, just opposite the track where James Bond rolled his Aston Martin spectacularly in Casino Royale, (www.youtube.com/watch?v=HhbYK7WzeBw).
The future is now
Digital technology is encroaching across virtually every aspect of our lives. For vehicle manufacturers (VMs), who are spending millions on transforming how cars are propelled, data has become a crucial new revenue stream. Autotech Connect is all too aware of this and reminds us that tomorrow's vehicles are here. While seen as futuristic tech, data flows to and from not just current cars but also the VMs. The issue of whether these companies should be trusted to act fairly towards the aftermarket may be a pertinent topic currently, but this is not the issue on which Autotech Connect focusses.
Instead, it looks more closely at the importance of digital technology within automotive businesses. It is fair to presume that most independent workshops use some kind of digital technology. These vary from a straightforward website, with a contact form and e-mail address, to more complex digital booking services and advanced workshop and customer management systems. Yet, while this technology should make the business more efficient, while making technician lives easier, it also introduced fresh risks. One issue is that technicians and garage owners speak a very different language
from IT professionals, meaning we have a communication problem that makes conversations between Basil Fawlty and Mrs Richards look like picture-perfect clarity.
Many technicians will be aware of stories, where hackers have compromised car technology to either amuse themselves, or commit a crime. The problem is that these situations are coming closer to home. Virtually every modern car is connected to a network, even through the eCall SoS button, which became mandatory for new models from 2018. Such systems have created vulnerabilities that can be exploited. For instance, since hackers learnt how to access the CAN bus system via the headlight wiring, Toyota RAV4 thefts leapt by between 20 and 30% in Glasgow.
While car thieves have swapped crowbars for laptops, to steal customer cars from your premises, they can also hack your online systems to either demand a ransom fee, or steal data that you hold. The latter issue could be more serious than you might think. Not only can you be fined severely for data
1. Set up a guest Wi-Fi account on your premises.
2. Integrate two-factor (2FA)/Multi-factor authentication on everything.
3. Create a cyber attack plan and print it out (see https://www.ncsc.gov.uk/cyberaware/actionplan)
4. Protect all phones, computers and tablets from being accessed, including having password screen locks.
5. Download and install https://www.sophos.com/enus/products/mobile-control/intercept-x to protect your phone.
With thanks to Francis West of Westteck.
breaches but you risk being sued by your customers, if you have not protected their information adequately. The hack can either paralyse your systems, expose sensitive data to cause embarrassment, or destroy hard-won customer relationships.
Speaking at Autotech Connect's launch, Laurence Abbott highlighted Arnold Clark's cyber-attack last year plus a similar situation affecting Ferrari, who, to date, is refusing to accede to the fraudsters' demands.
So, why should this affect you? The issue is that hackers tend not to focus on the corporation size but the degree of
By the time this issue goes to press, the Competition and Markets Authority (CMA) would have completed its consultation on the draft guidance to accompany the Motor Vehicle Block Exemption Order (MV-BEOpreviously the MV-BER).
The IAAF argues that, without robust and detailed legislation to define the technical requirements, it will simply allow the VMs to dominate and control the market. While legislation, including the MV-BEO, exists to protect the aftermarket, the devil is in the detail and secondary legislation is necessary to clarify the VMs' obligations.
As modern vehicles receive and transmit data, the IAAF and UK AFCAR support the need to make them cyber-secure, providing that this is not used by the car makers to impose a monopoly on service, diagnosis and repair operations. The IAAF argues that evidence exists of VMs abusing a dominant position, which must be addressed.
Naturally, autotechnician will update readers as this important story develops.
• 75% of all fraud in the UK is cyber-based
• Businesses are nine times more likely to experience a cyber attack than property damage
• Only 2-5% of UK companies report cybercrime
• 94% of cyber attacks enter businesses via e-mail
• Four new cyber threats appear every second.
vulnerability. These are becoming so sophisticated that most businesses do not know until over 230 days after the attack happened.
With digital security, act as though you are in a lion's chase. You need not be the quickest, just faster than the person behind you. Should you be a garage owner, looking further into security is a prudent idea. If you rely on an IT provider, consider that it is unlikely to be a security expert. It is also alleged that well-known anti-virus software brands are not the best at keeping up to date with the latest threats. When researching the topic, you may also wish to investigate cyber insurance, such as that offered to the motor trade by the broker, Hamilton Leigh.
Even so, consider that garage staff, including technicians, can pose the biggest security risk. Even apparently innocent actions, such as inserting dongles from home into work computers risk spreading viruses from machine to machine. Leaving unattended computer screens unlocked and computers accessible in areas where the public has access creates a data vulnerability, too.
Therefore, technicians, when thinking about cyber security, don't allow yourselves to be the weakest link.
Three new wheel aligners have been added to the Hofmann Megaplan range, which now comprises five machines. The supplier says the new machines are the result of considerable customer research, use the latest technology, while unnecessary ‘vanity’ features have been removed, so that the price can be kept as low as possible. In some cases, the improved models are cheaper than their predecessors.
All feature Italian-engineered 3-point clamps, which they highlight are lighter to carry and arguably faster to set-up than any other clamp of similar design on the market.
The megaline 88 Pro is a mid-range CCD aligner featuring Automatic Charging (the heads automatically charge when docked onto the cabinet), Haynes Pro Software which eliminates the need for Number Plate Recognition or manual data entry and a more powerful, compact mini-PC.
The megaline Logik 6-2 is an advanced CCD wheel alignment system, successor to the Logik 6. It features a 27” ‘anti-glare’ monitor, ‘one-piece heads’ that save hassle and a free App that enables remote control operation.
The megaline 3D 3500HD, an advanced 3D aligner, heads up the range.
For more information, or to discuss options, visit: http://bit.ly/3ICNhPi
MOOG steering and suspension components now include a new engineering feature that helps installers deliver longerlasting repairs. Dust boots, manufactured from an advanced thermoplastic polyurethane (TPU) elastomer, significantly outlast conventional chloroprene rubber material used in many competing parts.
The new TPU boot material – used with MOOG ball joints, link stabilisers, tie rod ends and assemblies, and track control arms – offers up to 180% greater resistance to common forms of mechanical degradation and 30% greater resistance to high temperatures and is also far more resistant to wear.
Durability of MOOG parts are also extended using metal sealing rings that hold the boot firmly in place, to better retain grease and lock out dirt, water and other contaminants. The combination of the new TPU boots and metal sealing rings help protect the articulating joints of MOOG parts up to two times longer than competing designs.
“Professional installers are looking for parts that enhance their reputations and strengthen their customer relationships through longer service life and outstanding performance,” said Robbie De Moor, Steering and Suspension Director, DRiV Motorparts. “That’s why MOOG introduces innovative, roadtested technologies that go the extra mile. Initially this new feature will cover our most popular part numbers and will be applied to a wider range in future”.
www.moogparts.eu
There are over 12,000 products inside the new Tool Catalogue from Sealey, including 1,100 new tools. New products and extended ranges include the SV20 One-Battery Series, its professional 20V range of power tools. The AP556CSHV storage system combines all the features of the Superline Pro rollcabs with the added benefit of a three-drawer utility seat and fits together in a compact, space-saving design. The new 2180LE Low Profile 2 Tonne Trolley Jack is fitted with a 180° turning handle, allowing use even in tight spaces.
A digital version can be viewed at www.sealey.co.uk
Braking specialist TMD Friction UK has introduced nine new brake pad, disc, and drum references to its Mintex range for various popular passenger car applications.
In the brake pad product range, three new parts have been added, including MDB3491 for Fiat 500, 500e and Convertible, and Tipo Estate, Hatchback and Saloon models (2012-). New brake pad MDB4293 offers a replacement part for Audi A3 and Volkswagen Arteon, Golf, and Tiguan cars (all 2019-), and MDB3493 fits Genesis GV60, Hyundai Ioniq 5, Ioniq 6 and Tucson and KIA EV6 cars (2020-).
Three new brake disc references are introduced – MDC3070C for a wide range of Honda vehicles including the popular Accord, HR-V and Odyssey models (2004-),
MDC3091C fits a range of Ssangyong cars including the Kyron and Rexton (2002-), and MDC3163C provides replacement Mintex discs for Abarth 500, 595 and 695 cars (2008-).
Three new brake drums are available: MDB397 for KIA Picanto (2011-), MBD425 for Renault Clio and Clio vans (2012-), and MDB433 for Nissan Micra (2016-) cars. The new references are accessible via the brand’s online catalogue Brakebook, by entering the Mintex part number. The expert search function also allows searching by product criteria such as width, height, thickness, drum diameter and many other criteria. All new references have also been added to TecDoc and MAM cataloguing systems.
https://mintex.com/online-catalogue
Supertracker has unveiled a new explainer video that provides a step-by-step guide to using its cordless STR1 range of laser aligners, providing expert instruction and benefits of the alignment system.
The video, which is less than four minutes in length, shows how quickly the laser aligner can be set up on any four-post platform lift, platform scissor lift, on a level surface, over a pit or on 2-Post lifts using Supertracker alignment tables.
The STR1 laser aligner is a cordless system with hangers to fit wheels up to 24” and features rechargeable batteries that allow the measuring heads to be charged from the unit when not in use. It is available either as a trolley or a wall-hung half cab as a space-saving option.
Managing Director Andrew Bates said: “Thousands of workshops in the UK use and rely on Supertracker tools every day. Many franchise dealers, and fast fit operations use Supertracker in their workshops because they are cost-effective, robust, reliable, and quick and easy to use. We support our products with an onsite calibration and repair service. Spending tens of thousands of pounds on alignment equipment is not the only option for workshops. Supertracker alignment systems may be a gateway
product into wheel alignment, but for the user they offer impressive income for a relatively small investment.
The laser aligner video can be viewed here: https://youtu. be/Czp0JFdpBYs
We focus on Clutch, Steering & Suspension, Batteries & Chargers, and news from Automechanika Birmingham, as well as our usual features. If you would like to contribute your news or views, email Nicola@autotechnician.co.uk
Stabiliser bars have been installed in passenger cars for many decades and have remained practically unchanged in this time and although little known to many motorists, the component plays a significant role in ensuring a safe and comfortable journey.
In the event of failure or damage to the system, loud knocking noises frequently occur in the suspension when driving over bumps or potholes – mostly caused by worn bearings or defective ball joints on the stabiliser links. In the case of worn bearings, an unintended play arises between bearing and stabiliser bar, and the stabiliser bar begins to rattle in the bearings on deflection and rebound.
A frequently installed type of stabiliser link features ball joints that are protected by a rubber boot from spray water and external influences. They are also packed with grease to make the movement as frictionless as possible. Every now and then, the rubber boot or the associated seal is damaged, allowing
water to enter leading to too much play in the joints and the noises mentioned above.
Febi says that when replacing the stabiliser link, the correct torque must be applied, otherwise, the ball joint can be damaged, wear prematurely or even break off.
www.partsfinder.bilsteingroup.com
Snap-on has released the new ZEUS+ diagnostic tool with a fully detached wireless 4-channel scope, 12” colour touchscreen, 8-megapixel camera, as well as an integrated stylus with a flashlight built-in. It offers comprehensive verification and functionality testing, including advanced graphing features and OEM-level data, guided CTM/scope for verifying component failures and a fast one-touch full system code scan and clear.
Fast-Track Intelligent Diagnostics with SureTrack delivers verified parts replacement records and real fixes, along with Smart Data for relevant vehicle and code-specific PIDS, plus access to prefiltered functional tests and guided component tests to verify repairs.
Snap-on Customer Care comes as standard with ZEUS+, as well as 24/7 online training and support, flexible financing, and exclusive access to the Snap-on Cloud.
Click the link to watch an overview video on ZEUS+: https://bit.ly/3Nh59Di
The Philips Xperion 6000 range of professional work lamps are designed for any inspection task, even in tight spaces that are tricky to see and reach. Features include presence-sensing and magnetic and telescoping capabilities.
The latest addition is the Philips Xperion Under-Bonnet Light, seen here, which provides up to 1200 lumens of bright white light and has a rotary control that allows the brightness to be dimmed and adjusted to the ideal level. It can extend to two meters on either side so that the light can be properly positioned across an engine bay or any other area without having to change the lamp angle. It features a proximity sensor that detects activity within a 2.5-meter radius, allowing the light to automatically turn on or off for maximum battery-life. It has a battery status indicator and includes an Eco-mode in which the light can operate continuously for more than a full half-day.
The Philips Xperion 6000 range includes flood lights – one of
which even allows you to listen to music from your phone –wands, hand-helds, slim-lights, and flexi-lights, as well as two smart accessories – a charging station and find-my-light system.
www.philips.com/Xperion-6000
We’re currently living through challenging times and, at Ben, we’re seeing more and more of our automotive family turning to us for support.
Employees who are struggling with their mental health may not feel comfortable opening up to their line manager or employer, so it isn’t always obvious who needs support. This is why we’ve put together some of the warning signs that managers and employers can look out for so that relevant support can be provided:
Stress can sometimes cause normally mild-mannered individuals to begin snapping at their colleagues or an extrovert to suddenly retreat from social interaction. If someone seems more short-tempered, tearful, or quiet than usual, keep an eye on them and ask them if they want to talk.
A noticeable increase in sick days may be a sign that your employee is struggling. You may also notice someone taking longer lunch breaks or arriving to work late.
When someone is stressed or distracted by mental health issues, they may make uncharacteristic errors, miss deadlines, and find it hard to concentrate.
Significant changes in someone’s weight (rapid weight gain or loss) or different eating habits (eating significantly less or more) can indicate a mental health issue.
If you notice a colleague looks tired, lethargic or worn out on a regular basis, it could be a sign that they aren’t sleeping well, which could be down to stress and their mental health.
Appearance and personal hygiene
You may notice changes in appearance and personal hygiene e.g., body odour, looking unkempt, not looking after themselves and wearing the same clothes for longer periods.
Share our contact details & support
If you notice that an employee is struggling, you could take them aside and ask if they are OK. Let them know that Ben is here for the automotive industry community, day or night, 24/7. Our support is free & confidential.
Call – 08081 311 333
Email – supportservices@ben.org.uk
Chat online – www.ben.org.uk
To find out more about the services we provide, visit: www.ben.org.uk/gethelp
Ben also operates an out-of-hours text support service. To access this service, text BEN to 85258.
Online mental health support is available at www.ben.org.uk/mentalhealth
We also provide health & wellbeing tips via email: www.ben.org.uk/signup
To find out more about how Ben can support your organisation and the health and wellbeing of your employees, contact Rachel Clift, Health & Wellbeing Director at Ben: Rachel.Clift@ben.org.uk