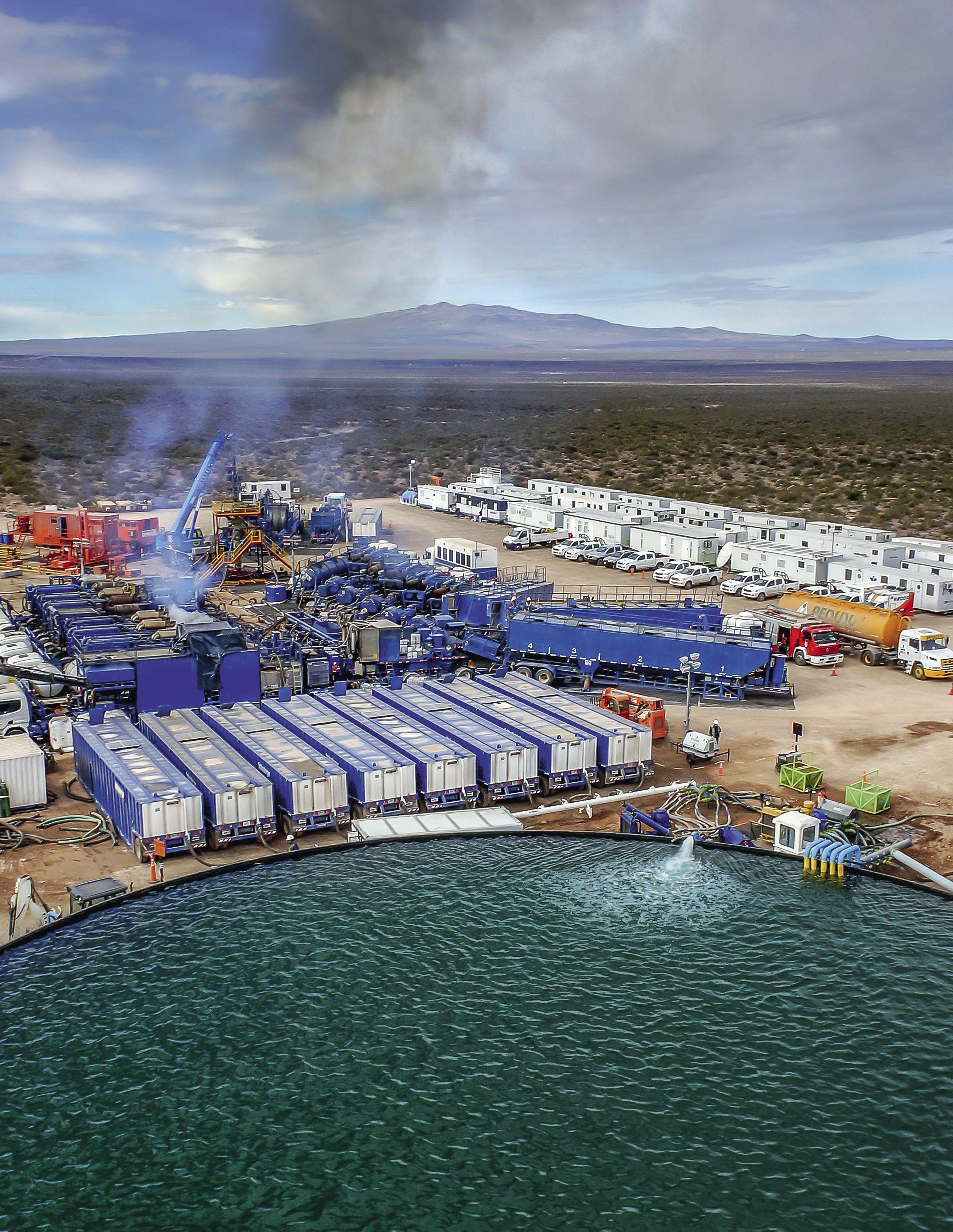
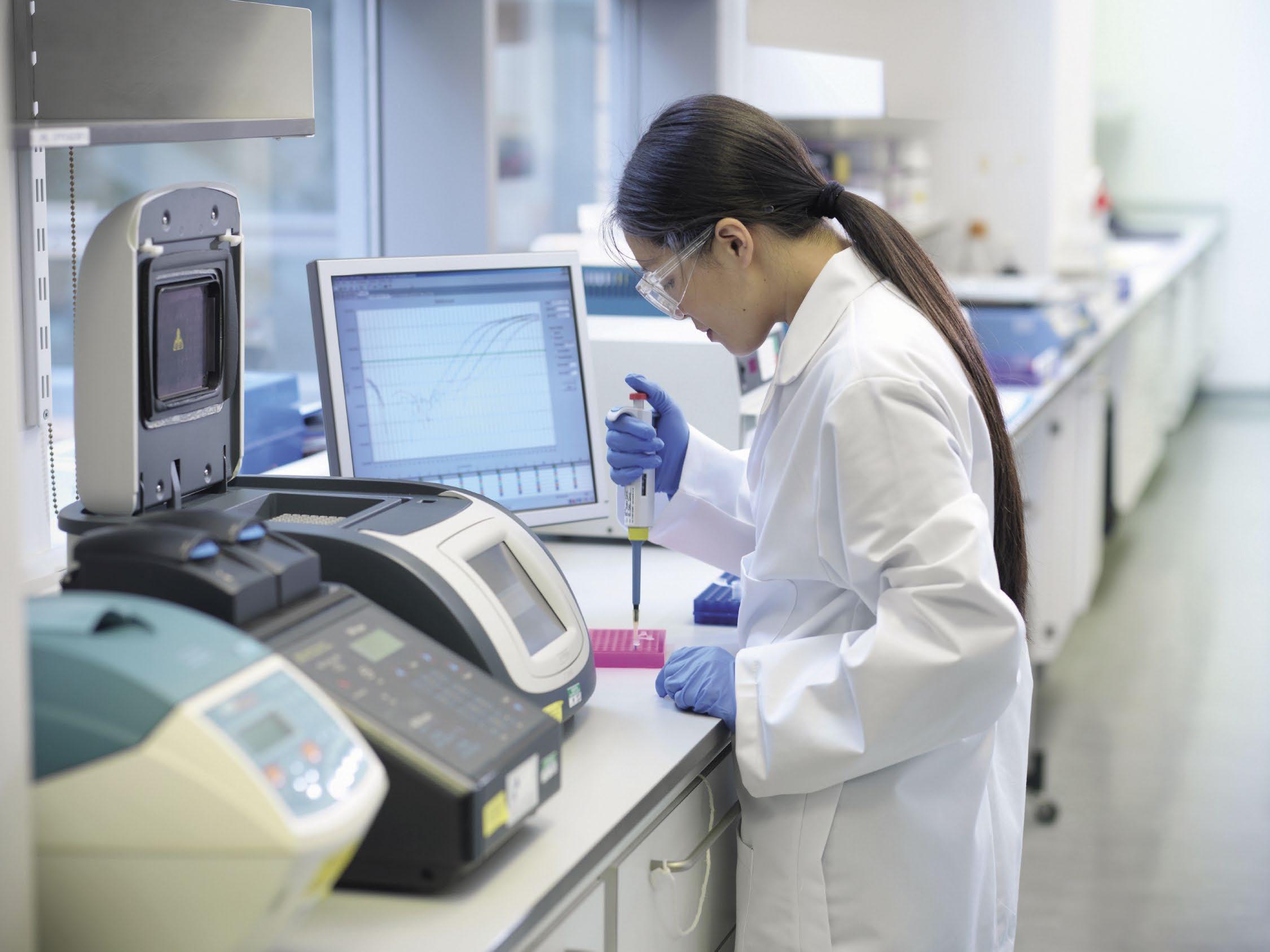
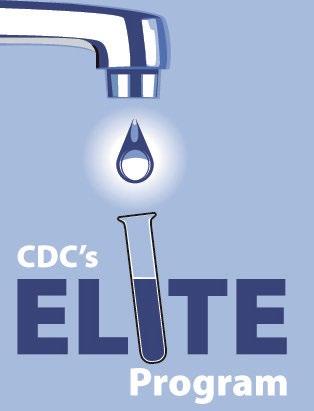
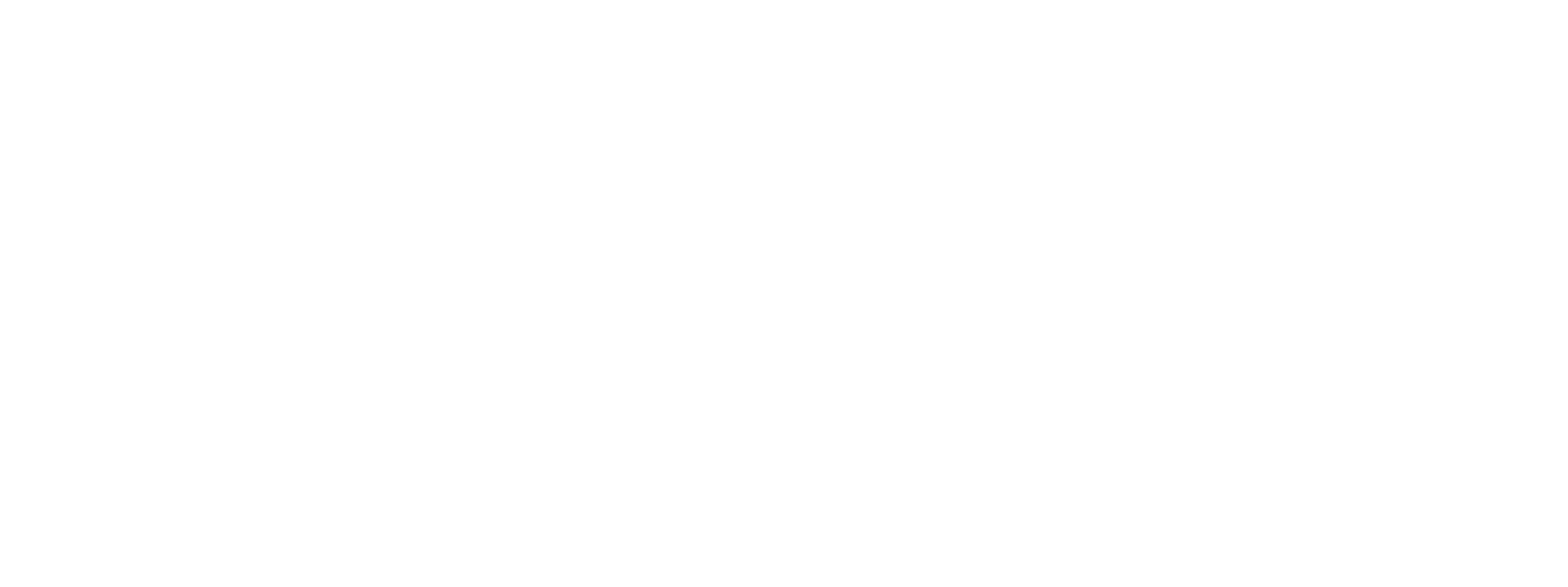
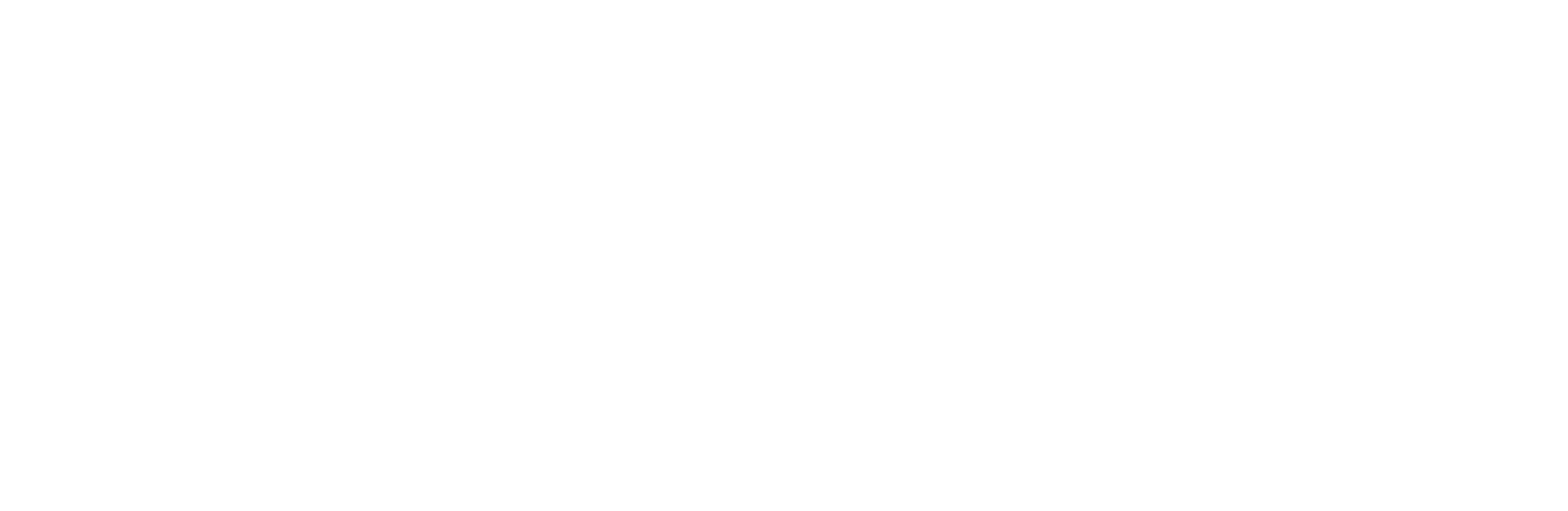
Colin Frayne, CSci, CChem, CEnv, FRSC, CWT, Aquassurance, Inc; and Barry B. Ekstrand, P.E., Finoric LLC
This two-part article series was originally developed by the authors as a white paper in collaboration with the oil and gas performance chemicals and services company Finoric LLC of Beasley, Texas. Part 1 primarily looked back at historical practices up to the current day, where less thought was given to the scaling tendencies of reinjected (and usually diluted) recycled brines, and the focus was (and currently still is) mostly on new well completion and frac’ fluid chemistries. This article primarily looks forward to an expansion of remedial stimulation of existing producing wells, and a future focus on the expansion of production brines and production chemistry work.
Brad Buecker (Buecker & Associates) and Denton Slovacek, Jean Holz, and Xavier LeBlanc (Hach)
A century of steam generation for power production and industrial process heating has demonstrated the necessity for proper condensate, feedwater, and boiler water pH monitoring and control. Yet, pH monitoring methods are often not well understood by plant personnel and engineers who design new plants. This article examines the importance of pH control in steam generating systems, including modern heat recovery steam generators (HRSGs) and co-generation units, and it outlines the technology to obtain correct readings.
Loraine A. Huchler, P.E., CMC®, FIMC
In boiler systems, the term "passivation" has been applied to a wide variety of situations, ranging from the strict electrochemist's definition of potentials to the boiler operator's measurement of soluble and insoluble iron in the boiler system. Other definitions include conditions of minimum iron solubility (i.e., minimum corrosion) or the existence of a tight, adherent iron oxide film. Although the descriptions may vary widely, the objectives are identical: to create conditions that minimize the corrosion of iron. This article series will examine the chemistry of iron oxides found in boiler systems, postulated corrosion mechanisms, the thermodynamic and kinetic conditions that control iron oxide formation in boiler systems, the effects of dissolved oxygen and chemical oxygen scavengers on these system conditions, and some passivation/corrosion measurement techniques.
Alexandra Peters and Averie Palovcak, Arkema Inc.
In the world of food sanitation, several important factors need to be considered to properly clean the equipment used in processed foods. Homeowners are aware of how integral it is to sanitize food contact surfaces. It is commonplace to regularly scrub counters, sinks, and refrigerators. On a larger scale, food manufacturers must also do the same. The objective must be to safely remove leftover food and kill bacteria that can spread disease if left untreated. Of a wide array of methods used to control this bacteria growth, ozone (O3) is one of the most effective.
1300 Piccard Drive, Suite LL 14
Rockville, MD 20850
(301) 740-1421 • (301) 990-9771 (fax) www.awt.org
President
Stephen C. Hallier, CWT
President-Elect
Noah Baskin
Secretary
John D. Caloritis, CWT
Treasurer
Kyle Rossi, CWT
Immediate Past President
Fred Shurtz
Craig Bodenmiller, CWT
Michael Bourgeois, CWT
Tammy Faber, MBA Michelle Lunn
Jack Altschuler
John Baum, CWT
R. Trace Blackmore, CWT, LEED AP
Michael Bourgeois, CWT
D.C. “Chuck” Brandvold, CWT
Thomas Brandvold, CWT
Brent W. Chettle, CWT
Dennis Clayton
Bernadette Combs, CWT, LEED AP
Matt Copthorne, CWT
James R. Datesh
John E. Davies, CWT
Jay Farmerie, CWT
Gary Glenna
Charles D. Hamrick Jr., CWT
Joseph M. Hannigan Jr., CWT
Staff
Executive Director
Denise Jackson
Deputy Executive Director
Sara L. Wood, MBA, CAE
Member Services Director
Angela Pike
Vice President, Meetings
Tina Schneider
Meetings Specialist
Caroline Bentley
Meetings Planner
Tim Foley
Matt Jensen, CWT Mark R. Juhl
Brian Jutzi, CWT
Bruce T. Ketrick Jr., CWT
Bruce T. Ketrick Sr., CWT
Ron Knestaut
Robert D. Lee, CWT
Mark T. Lewis, CWT
Steven MacCarthy, CWT Anthony J. McNamara, CWT James Mulloy Alfred Nickels
Scott W. Olson, CWT
William E. Pearson II, CWT
William C. Smith
Marc Vermeulen, CWT
David Wagenfuhr
Casey Walton, B.Ch.E, CWT Larry A. Webb
2023 Technical Training Seminars (West)
February 21–24, 2023
Doubletree Mission Valley San Diego, California
2023 Technical Training Seminars (East)
March 29–April 1, 2023
Omni Pittsburgh Hotel Pittsburgh, Pennsylvania
2023 Business Owners Meeting
October 3, 2023
Amway Grand Hotel Grand Rapids, Michigan
2023 Annual Convention & Exposition
October 4–6, 2023
DeVos Place Convention Center and Amway Grand Hotel Grand Rapids, Michigan
Also, please note that the following AWT committees meet on a monthly basis. All times shown are Eastern Time. To become active in one of these committees, please contact us at (301) 740-1421.
Second Tuesday of each month, 11:00 am—Legislative/Regulatory Committee
Second Tuesday of each month, 2:30 pm—Convention Committee
Second Wednesday of each month, 11:00 am—Business Resources Committee
Second Friday of each month, 2:00 pm—Pretreatment Subcommittee
Second Friday of each month, 10:00 am—Special Projects Subcommittee
Second Friday of each month, 11:00 am—Cooling Subcommittee
Third Monday of each month, 9:00 am—Certification Committee
Third Monday of each month, 3:30 pm—Young Professionals Task Force
Third Tuesday of each month, 3:00 pm—Education Committee
Third Friday of each month, 9:00 am—Boiler Subcommittee
Third Friday of each month, 10:00 am—Technical Committee Quarterly (call for meeting dates), 11:00 am—Wastewater Subcommittee
American Water Summit, January 24–26, 2023, Los Angeles, California
Cooling Technology Institute January 29–February 3, 2023, Memphis, Tennessee
ACS, Spring National Meeting & Expo, March 26–30, 2023, Indianapolis, Indiana
WQA, Convention and Expo, April 18–20, 2023, Las Vegas, Nevada
Exhibits and Sponsorships Manager
Brandon Lawrence
Senior Director, Creative Services/Marketing
Jennifer Olivares
Marketing Manager
Mary Claire Gordon
Managing Editor
Lynne Agoston
Production Manager
Tiffany Ward
Director of Accounting Services
Dawn Rosenfeld
Publisher
Denise Jackson
Managing Editor
Lynne Agoston
Production Manager
Tiffany Ward
Technical Editor
Michael Henley, mdhenleywater@gmail.com , (303) 324-9507
Advertising Sales Manager
Carol Nettles, carol@adboomadvertising.com
ASHRAE Winter Conference and AHR Expo February 4–8, 2023, Atlanta, Georgia
Membrane Technology Conference (sponsored by AMTA and AWWA), February 20–23, 2023, Knoxville, Tennessee
38th Annual WateReuse Symposium, March 5–8, 2023, Atlanta, Georgia
NACE, Corrosion Risk Management Conference, March 19–23, 2023, Denver, Colorado
Electric Utility Chemistry Workshop, June 6–8, 2023, Champaign, Illinois
AWWA, Annual Conference & Expo, June 11–14, 2023, Toronto, Ontario, Canada
ACS, Fall National Meeting & Expo, August 13–17, 2023, San Francisco, California
WEFTEC, Annual Technical Exhibition and Conference, September 30–October 4, Chicago, Illinois
RETA, Annual Convention, November 13–16, 2023, Jacksonville, Florida
The Analyst is published quarterly as the official publication of the Association of Water Technologies. ©2022 Association of Water Technologies. Materials may not be reproduced without written permission. The articles, studies, and reports in this publication are the works of the respective authors. AWT expressly disclaims any duty to investigate any article, study, report, conclusion, product, service process, procedure, design, or similar offering contained herein. AWT does not warrant that the information in this publication is free from error and does not necessarily agree with the statements or opinions contained herein. The appearance of any technical data, editorial material, or advertisement in this publication does not constitute an endorsement, warranty, or guarantee by AWT. This publication is not a substitute for the competent counsel of a water treatment professional, plumbing professional, mechanical official, or attorney. The user assumes any and all risks of relying on the information in this publication. Authors are responsible for ensuring that the articles are properly released for classification and proprietary information. All advertising will be subject to publisher’s approval, and advertisers will agree to indemnify and relieve publisher of loss or claims resulting from advertising contents. Editorial material in the Analyst may be reproduced in whole or part with prior written permission. Request permission by writing to: Managing Editor, the Analyst, 1300 Piccard Drive, Suite LL 14, Rockville, MD 20850, USA. Annual subscription rate is $100 per year in the United States (4 issues). Please add $25 for Canada and Mexico. International subscriptions are $200 in U.S. funds.
It is exciting to start my presiden tial year following the Annual Convention in Vancouver. What a great meeting! Thank you to all of you who participated and made it such a positive meeting.
And thank you for everyone who participated in the Annual Membership Meeting and bylaws vote. The vote on the two proposed bylaw measures passed, meaning AWT has added an Individual member category and has changed the definition of a water treatment company to 500 employees in a water treatment division.
Every year, the AWT Training Seminars improve based on the communications and feedback we gather from attendees. The programs are revised each year to ensure that the material is current and relevant. It can be difficult to justify the increasingly high cost of travel when budgets are tight, but the ROI you’ll receive from these meetings is phenomenal. In just three short days, you’ll learn or refresh on all aspects of water treatment. Attendees will be able to better communicate and high light their skills to customers.
AWT also offers a three-day Service Technician Training program. This seminar is designed for those new to the field. The program begins with the basics—an overview of the role of a service technician and why we use water. It continues with sessions on safety issues, feed equipment training, time and relationship management, filtration and pretreatment, boiler types and treatment programs, testing, cooling tower design and treatment programs, and writing service reports. This is a great introduction for those new to the water treatment industry as well as a way to further expand the knowledge and skills of those already employed as service and account management representatives.
In addition, AWT will also offer RO training and sales training and an ASSE training to prepare attendees to become ASSE certified.
I encourage all of you to become active in AWT. Attend the training seminars, work toward getting your CWT if you haven’t already, join a committee, and use the tools on the AWT website to get the most of your member ship. Taking advantage of all AWT has to offer will provide you with a sizeable return in knowledge, success, and, ultimately, reward. I welcome your feedback and can be reached at president@awt.org.
We’ve started planning for the 2023 Annual Convention & Exposition, which will take place October 4–6, 2023, in Grand Rapids, Michigan.
We’re excited to be going back to Grand Rapids! When we were last there, in 2017, we had a very successful meeting. If you haven’t had the chance to visit Grand Rapids, you’ll be pleasantly surprised. Known as the Craft Beverage Capital of the United States, Grand Rapids is a city that will constantly delight you with authentic and unforgettable world-class experiences made easy, affordable, and friendly.
Get ready to be wowed—Grand Rapids never fails to surprise visitors with its huge variety of things to see and do: world-renowned art museums and historic sites for cultural vacationers; world-class golf, recreation, and beaches for nature lovers; incredible farm-to-table restaurants for foodies; and wholesome "playcation" fun for families. And if you come early to Grand Rapids, you’ll get to experience ArtPrize, an international art competition decided by public vote and expert jury that takes place each fall in Grand Rapids.
It's all topped off by the most vibrant downtown between Chicago and Cleveland—delivering all the benefits of a big city with none of the hassle. You’ll be surprised by all that Grand Rapids has to offer.
The Amway Grand Plaza, a modernized 1920s historic riverfront hotel with a soaring glass tower, is a fourminute walk across the Grand River bridge to the Gerald R. Ford Museum and a nine-minute drive from the Frederik Meijer Gardens & Sculpture Park.
Rooms (with river or downtown views) come with free Wi-Fi and 24-hour room service. Assorted upgrades include seating, kitchen amenities, and free breakfast and cocktail hour.
Choose from five on-property restaurants, ranging from a coffee shop to an upscale steakhouse. You also won’t want to miss the spa, a sky-lit fitness center with a pool and two hot tubs, and plenty of boutique shopping.
We’re currently accepting abstracts for the 2023 conven tion. If you have a presentation that would be of interest to the membership, submit an abstract to be part of the program. We’re also researching keynote speakers, and while we haven’t selected one yet, we are considering some great people to inspire and motivate you in your work.
Mark your calendars now for the 2023 convention!
As we plan and prepare for Grand Rapids, I welcome your input and feedback. I can be reached at nbaskin@ towerwater.com. Thank you for the opportunity, and I look forward to serving you!
Great Products, Great People
Commitment, to our customers - We got your back.
Experience, Our sales team averages over 20 years of industry experience. Knowledge, of the equipment we offer and how to apply it.
- Accessibility, A real live caring person answers the phone, not a machine. Brands, We work with some of the best manufacturers in the industry.
- Stock, 1000’s of items in our Naperville, IL warehouse.
Editor’s note: This two-part article series was originally developed by the authors as a white paper in collaboration with the oil and gas performance chemicals and services company Finoric LLC of Beasley, Texas. Part 1 (Summer 2022 issue) primarily looked back at historical practices up to the current day, where less thought was given to the scaling tendencies of reinjected (and usually diluted) recycled brines, and the focus was (and currently still is) mostly on new well completion and frac’ fluid chemistries. This article primarily looks forward to an expansion of remedial stimulation of existing producing wells, and a future focus on the expansion of production brines and production chemistry work.
The subject of this article series examines hydraulic frac turing in oilfields in order to achieve higher yields of oil and natural gas. There can be different views on the spelling of the shortened term for “fracturing and fracture.” The generally accepted abbreviation for “hydraulic fracture” or “fracturing” is “frac.” Fracturing can be abbreviated as “frac’ing” or “fracing.” However, sometimes this term is referred to as “frack” or “fracking.” That said, generally those in the oil and gas industry will use the first spellings when referring to this practice because “frac” is short for fracture. For the purposes of these articles, we will use the spellings of “frac” and “fracing” to refer to fracturing.
Where produced water (PW) treatment is required, process equipment options for treating PW and other wastewater (WW) are commonly available in the market, from the most basic, low-cost “standard treat ments” to sophisticated, high-cost technologies that may include zero liquid discharge (ZLD). However, with the use of an effective and optimal treatment process, PW disposal volumes as WW may be reduced by perhaps 80% to 90%. Some service companies offer fully inte grated mobile WW treatment system trains, incorpo rating large reaction or frac tanks and other equipment that can treat perhaps 50,000 barrels per day (bbl/day) of formation/flowback water. These systems typically use conventional separation technologies, such as American Petroleum Institute separators and dissolved air flota tion (DAF) to demulsify and separate oil, grit, and sludges from water. Also, coagulation and flocculation techniques with a clarifier are required for the removal of most or all total suspended solids (TSS). The hope is that these systems also will provide some targeted
precipitation of minerals such as iron salts, which form part of the total dissolved solids (TDS).
Examples of “standard” WW process treatments are aimed primarily at TSS reduction or removal, but some treatments are offered specifically for oil and oily sludge removal and TDS reduction (or total elimination as in ZLD) as well as disinfection, destruction of volatile organic carbons (VOCs) and other types of organics, and removal of disinfection byproducts.
1. Sedimentation and clarification: A basic technology that relies on some particulates in water eventually settling out naturally or being aided by the use of inorganic chemical combinations (typically iron or aluminum based) and organic coagulation and flocculation chemistries—mainly alums and polyacrylamide. These chemistries can reduce the settlement time and provide an improved settled sludge with enhanced clarification of the supernatant fluid (i.e., less TSS).
2. Filtration: Systems may use back-washable multimedia, sand, disc, or bag/sock filters. Where the fluid contains organics, a granular activated carbon (GAC) filter may be preferable/required after the media filter, to remove VOCs or other organics.
3. Chemical precipitation: With the correct precipitant and pH (usually determined by field trials), this separation technology can be used to precipitate either specific metals and minerals or a range of contaminants. Clarification or filtration is required to remove the resulting precipitates.
4. Electrocoagulation (EC): EC is an electrokinetic technique with over a 100-year history, most often used in mineral mining operations and WW treat ments, including oily waters and metal-plating waste. EC typically has iron (Fe) or aluminum (Al) alloy electrodes, which, under the influence of a DC electric current, create metal salts that act as precipitants, coagulants, and flocculants that are used to remove transition/heavy metals, and/or other polluting chem istries, such as chromium (Cr), arsenic (As), selenium (Se), and pesticides. EC is a form of electrophoretic deposition (i.e., deposition of charged particles in a fluid or gel under the influence of an electric field).
5. Dissolved air flotation (DAF): Treatment equipment systems may also include variants such as dissolved gas flotation using nitrogen or induced air flotation. The objective is to separate oil or particulates, which rise and can be skimmed off from clean water. DAF may be preceded by American Petroleum Institute tanks or lamella systems!
6. Evaporation and thermal distillation systems: Several technologies can potentially be employed, including single and multi-effect or multi-stage thermal or mechanical evaporators. These separation technologies are very effective in producing a low TDS, clean, and purified water, but often at significant cost. An example is the mechanical vapor recompression distillation process, which can typically recover in excess of 90% of inflow without the need for pretreatment to remove alkaline earth and transition metals that may be present. Such systems may also incorporate a steam stripper to remove light-end hydrocarbons. Other evaporative technologies include MSF and MEV.
7. ZLD technologies: ZLD involves a combination of technologies that ultimately result in a zero liquid waste discharge. Equipment employed is commonly a combination of a brine concentrator, evaporator, and crystallizer. Pretreatment is almost always required to first remove oil, TSS, and some scale-forming contrib utors to TDS. Ultimately, solid salt crystals/powder and high-purity water are the only outputs, but these outputs come at a high capital and thermal heating cost.
8. Advanced oxidation processes (AOP): Sometimes known as super-oxidation, various types of systems are on the market, and these are now commonly employed as a tertiary treatment in drinking water processes to breakdown pesticides, volatiles, and other complex organics in water, and to also reduce chlorine disinfection byproducts. The most common process uses a combination of UV light and H₂O₂ (hydrogen peroxide) or O₃ (ozone) to generate highly reactive, oxidative hydroxyl radicals. In the frac/PW market, vendors provide this type of technology mounted on mobile systems for direct site treatments. These systems incorporate a series of steps that may also include providing ozone, acoustic and hydrodynamic cavitation, and electrochemical processes.
The oil and gas (O&G) industry uses a lot of water, and operators may work with production fluids having a high water cut in the oil, gas, and formation fluid mixture. Therefore, understanding the quality, consistency, and overall composition of the various waters and mixtures involved is important. Regarding the chemistry and physics of water, note that a water molecule is dipolar, with a distorted or bent shape, and these polar forces draw water molecules together (cohesion), such that the oxygen in each water molecule forms a bond with hydrogen atoms from other molecules. This is an electrostatic attractive force, termed a hydrogen bond.
The oil and gas (O&G) industry uses a lot of water, and operators may work with production fluids having a high water cut in the oil, gas, and formation fluid mixture. Therefore, understanding the quality, consistency, and overall composition of the various waters and mixtures involved is important.
This type of molecular bond holds the liquid water molecules together. Within the water mole cules’ tetrahedral shape, we find that each water molecule is hydrogen bonded to four other water molecules, with lots of empty space within the liquid water three-di mensional structure. This allows for the solvent water to accept a wide range and quantity of dissolved solute ions and is the reason why water is an excellent solvent.
Water’s capability of solvating and housing many different solute molecules is evident in treating hydraulic fluids and PW and evidenced by the high concentra tion of salts present in the PW. While water may not technically be a universal solvent, it does dissolve more substances than any other liquid. Note that this solu bilizing effect can lead to problems, such as unwanted reactions, the incorporation of biological material, salts with reverse solubility (that quickly precipitate on
heating), and strongly ionizable salts that can only be removed by reverse osmosis (RO), distillation, or expen sive evaporative processes.
The rationale for discussing concepts of self-ionization of water; its solvation; and its amphoteric, amphiprotic, and acid-base behavior, among other characteristics, is that the properties of water give rise to the fact that water is perhaps the most common solvent for precipitation, oxidation/reduction (redox), and acid-base reactions. Note that some of these reactions commonly occur in dynamic industrial waters, such as cooling water, process water, WW, reuse, hydraulic frac fluids, and PW, and these results may be difficult to control.
In view of water’s chemistry and an anticipated need to aim for reuse of PW where possible, to reduce freshwater requirements, it is probably necessary to first consider what types of WW treatment and options described earlier are offered by equipment OEMs and O&G service companies. Here are some questions to consider:
What treatment processes can work for us and match our needs?
Can any of the various standard equipment processes eliminate the need for chemistries (such as biocides, iron and sulfur precipitants, and scale/corrosion inhibitors), at least on a temporary basis?
Are the chemistries critical primary additives or only needed as water quality “polishers”?
Depending on any specific water under consideration, other factors will determine whether some of these equipment processes will prove useful and cost-effec tive. For example, thermal distillation, ZLD, or AOP processes are typically used for producing high-purity water and may be too expensive. Some equipment technologies offered to the water-reuse market sector may seem to be “overkill” and are probably not required, especially if we have a light-brine PW that simply needs TSS and some oil removed to produce a clean brine that can be easily blended into a hydraulic fluid base.
Similarly, membrane technologies such as RO or elec trochemical deionization are not likely required for most recovered brines, unless ultimately reused for cooling water makeup, irrigation water, purple pipes, or toilet flushing. Even so, it may be more useful to use
microfiltration and/or ultrafiltration with damage-re sistant polyvinylidene fluoride or polyether sulfone membranes.
These may prove to be extremely useful “cleanup” processes in guaranteeing the removal of all TSS. Note that ultrafiltration has the added benefit of removing all bacteria and viruses, thus providing an alternative disinfection route.
Consider that one or more of these physical processes, supported by “polishing” chemical treatments, only becomes necessary if the future reuse of a water source under consideration demands it. Thus, what treatment steps are really required, and what is a reasonable quality standard for a clean brine?
To consider what treatment steps are required, note that common salts used in the preparation of simple brine systems include sodium chloride, calcium chloride, and potassium chloride. More complex brine systems may contain zinc, bromide, silica, or iodine salts. These complex brines are generally corrosive and more costly to treat in terms of fluid chemistry components and the upfront need to anticipate potential operational problems (such as various forms of pitting corrosion). Brines often have complex chemistries with wide variabilities and constituent ion concentrations. What is their chemistry? What concerns do we have? Concerns may include mineral and biological contaminant residence times and crystal induction times. Also, we need to consider common ion association models and hydrate formation nucleation kinetics. What actions are required by water treatment practitioners when confronted with more complex brine water chemistries?
As noted, many gaseous and mineral impurities commonly found in production brines and other brine sources are generally corrosive. Salts typically present include inorganics, such as magnesium chloride, calcium chloride, and sodium chloride, and, at higher tempera tures, will hydrolyze to some degree, forming oxides and hydrogen chloride, an acid gas that condenses in water to form hydrochloric acid and can be extremely corrosive to common steels and other metals. (Note that sodium chloride is more resistant to hydrolysis at lower temperatures.) Desalting processes, plus the use of corrosion inhibitors, can be used to neutralize corrosion.
This combination can form weak corrosive acids that can form corrosion products like siderite (FeCO₃).
Sulfur compounds, in the form of corrosive sulfides (e.g., hydrogen sulfide [H 2S]), sulfates, and mercaptans, are almost always present to some degree. Effective control of sulfur chemistry corrosion processes and corroded metal cleanup (or at least its minimization) may be affected by using high-chrome steels in critical process areas, or by using inhibitor chemistries such as tetrakis(hydroxymethyl)phosphonium sulfate (THPS) or 2-(decylthio)ethanamine hydrochloride (DETA). Note that both THPS and DETA chemistries can also be used as biodispersants for control of biofilm forma tion. In their EPA-registered form, THPS and DETA are both extremely effective microbiocides for control of sulfate-reducing bacteria and other sessile and planktonic microorganisms contributing to problems of microbial induced/influenced corrosion.
Note also that scaling risks are compounded by rapid nucleation rates and the degree of dissolved mineral super saturation. Both of these factors are variables with nega tive effects linked to longer residence times, inverse salt solubilities, and higher temperatures. Thus, we sometimes see a decrease in solubility of undesirable ionic precipitates over time, and these may develop at some point beyond supersaturation concentrations. When they are produced, it is commonly by the addition to the solution of a soluble compound (from another ingredient) having an ion in common with the supersaturated precipitate (i.e., the common ion effect). This solubility change leads to an increase in actual precipitation and deposition, and beyond localized nucleation times, severe mineral salt scaling may occur (i.e., salts of Ca, Mg, Sr, Ba, and others).
Thus, in considering potential scale and corrosion control chemistries (and also antifoulants and dispersants), we have to consider among other factors, the degree of risk of scaling as indicated by saturation index (SI) calculations (e.g., Langelier, Ryznar, Puckorius, Stiff & Davis, and others). Typically, oilfield water treatment software is much more useful in providing accurate and comprehensive diagnoses and advice as compared to these simple SI formulae. For an example of what can be modeled to examine scaling and corrosion risks, see examples of 3-D modeling graphs from French Creek Software in Figures 1 and 2.
Figure 1: A model for calcite saturation levels. (Note: Red blocks represent unacceptable conditions, such that an increasing pH and an increasing temperature both present higher risks of supersaturation and scaling.)
Figure 2: Projected corrosion rate for carbon dioxide (CO₂) and H₂S. (Note: CO₂–H₂S corrosion rates peak with decreasing pH and also with increasing temperature.)
Until fairly recently, there has been limited PW recycling in some shale plays; however, as treatment technologies have improved and the scale of operations have grown, it now can be more cost-effective to recycle PW than to dispose of it in saltwater disposal wells. The financial rationale for the recycling of PW as makeup water for fracturing fluids will continue to improve because, at present in some plays, PW volumes are 200% to 400% in excess of the annual completion source-water demand, thus offering significant opportunities for water reuse.
This brings us back to the question of what a reasonable quality standard is for a clean brine. A useful minimum specification table for reusing clean brine as recycled PW is shown below as Table A. The table has been devised by a team from New Mexico State College of Engineering, with support from NGL Water Solutions, a water midstream treatment business unit of NGL Energy Partners.
Salinity
Reported after treatment
pH 6.0 to 8.0
Oxidation reduction potential > 350 mV
Turbidity
< 5 mg/L (approx. 25 NTU)
Oil < 30 ppm—no sheen
Hydrogen sulfide
Particle size
Nondetectable
Filter, < 25 micron
Rules of thumb tell us that several primary functional organic chemical groups act as scale and corrosion control additives (and more) in aqueous environments. Today, the focus on key functional group chemistries is often based on phosphonates/aminophosphonates, maleates/succinates, or homo/co/ter-acrylate polymers. Other chemistries exist, however, such as iso- and polyiso-propenylphosphonic acid, which are reaction products of both polymer and phosphonate, and various acrylate/maleic/phosphonate/sulfonate polymer combi nations. Also, there are chelants, green chemistries, azoles, imidazolines, long-chain fatty acid amines, surfactants, esters, and vapor-phase corrosion inhibitors. Formulations for any specific range of problems generally require a combination of additives drawn from two or more of these functional categories.
Rules of thumb also advise that each individual well-for mulated chemistry program selected will typically not be used in any moving body of water under examination (such as recirculating cooling water or drilling water) in concentrations exceeding 3 to 5 milligrams per liter (mg/L) total “actives” concentration, depending on the degree of supersaturation, the scaling species induction time, and/or nucleation rates. There will likely be a mix of chemicals employed under these conditions, and the total “actives” concentration of all chemistries will
seldom exceed 15 to 20 mg/L but more typically will be present in the body of water at a concentration of 10 to 15 mg/L in order to meet both technical and financial considerations.
Note: Induction time is the period between the moment a constant supersaturation is created, and scale-forming crys tals are detected, whereas nucleation rate describes how many scaling crystal nuclei of critical size form on a substrate per unit area and unit time. Induction time and nucleation rate are important criteria for chemistry application rates, and rates for these various additives will vary based on the specifics of any of a wide variety of industrial water treatment, oilfield, and refinery applications. For example, such an additives mix may be used in industrial water systems at, say, 12 to 15 mg/L total actives. However, the same mix can be used as an RO antiscalant/dispersant program at only 3 to 4 mg/L total actives. Additionally, the same mix may be successfully used as a scale inhibitor/dispersant for powerplant condenser cooling, but at only 100 to 150 parts per billion. Such a low concentra tion is possible because exposure to the hot condenser unit may be required for only 6 to 7 seconds, whereas the scaling crystal nucleation time available may be 10 to 12 seconds.
The primary types of chemistries employed are shown in Table B, and the relative properties of phosphonates are shown in Table C.
• Carboxylates (acrylates, maleates)
• Sulfonates (AMPS, sulfonated styrene, other specialty)
• Non-ionic (acrylamide and derivatives, hydrophobes)
• Provide general purpose functionality
• Typical backbone
• Good for dispersion (CaCO3, CaSO 4)
Sulfonates
• Typically for stabilization of phosphate, iron, and zinc
• Add electrolyte stability
Non-Ionics
• Extend functionality to include a broader range of solids
• Can change polymer configuration properties
• Can be effective for stabilization similar to sulfonates
Some basic properties of various phosphonates are as follows:
Sequestration and chelation
Threshold effect and scale inhibition
Deflocculation and dispersion
Good hydrolytic stability
Corrosion inhibition and/or synergism with other corrosion inhibitors
Formulation compatibility with most or all other additives in the formulator’s mix
More complex brine systems may contain zinc, bromide, silica, or iodine salts. These complex brines are generally corrosive and more costly to treat in terms of fluid chemistry components and the upfront need to anticipate potential operational problems (such as various forms of pitting corrosion).
Some commonly used scale and control additive chemistries are listed below:
1. AA/AMPS polymer (e.g., Acumer 2000)
2. AA/AMPS/PHOS polymer (e.g., Unichem 134)
3. AA/AMPS/TBA terpolymer (e.g., Acumer 3100)
4. ATMP phosphonate (e.g., Dequest 2000)
5. HEDP phosphonate (e.g., Dequest 2010)
6. HPA phosphonate corrosion inhibitor (e.g., Belcor 575)
7. PAA acrylate (e.g., AR-900A)
8. PAP amino phosphonate (e.g., Multicor 400)
9. PBTC phosphonate (e.g., Phos 9)
10. PCA polymeric dispersant (e.g., Unisperse 124)
11. PMA maleic scale inhibitor (e.g., Belclene 200)
12. TTTATH: triazine based corrosion inhibitor (e.g., Belcor 590)
13. N-tallow, 1,3,diaminopropane, corrosion inhibitor (e.g., Duomeen T)
Some commonly used chelants chemistries are listed below:
1. Amine carboxylate (EDTA type)
2. EDTA (ethylenediaminetetraacetic acid)
3. NTA (nitrioltriacetic acid)
4. DETPA (diethylenetriaminepentaacetic acid)
5. HEDTA (N-hydroxyethylethylenediaminetriacetic acid)
6. Natural types (low strength/low cost)
7. Citric acid
8. Gluconates
9. Polyphosphates—not hydrolyticaly stable
10. Triethylamine (TEA) —for specific applications
11. Silicate—not a true chelant
Some commonly used supporting microbiocide chemistries include:
1. NaOCl, 12.5% (aka bleach)
2. Stabilized chlorine, 1.5% (e.g., Justeq 07)
3. NaBr, 40% (e.g., Bromide Plus)
4. Stabilized HOBr, 10.1% (e.g., BromMax)
5. BCDMH 32% Br/Cl (e.g., Halogene T30)
6. BCDMH/trichloroisocyanuric acid (TCCA) (e.g., Bromoblend 99)
7. Isothiazolin, 1.5% (e.g., Kathon WT)
8. Gluteraldehyde, 15% (e.g., Aquacar 515)
9. DBNPA, 20% (e.g., BioBrom C-103L)
10. Polyquat, 60% (e.g., WSCP)
11. TBZ, 4% (e.g., Bellacide 325 Italmatch/BWA)
12. THPS, 25% (e.g., Tollcide PS)
13. Ethylene oxide/propylene oxide (EO/PO) BCP biodispersant (e.g., as manufactured by Italmatch/ WST, BASF, DOW/DuPont)
14. Quat ammonium chloride (e.g., Conlen Surfactant CST 8195) (Lamberti Group)
Some commonly used additional supporting chemistries include the following:
1. TTA copper corrosion inhibitor (e.g., Wintrol T-50Na)
2. Na nitrite (corrosion inhibitor)
3. Na silicate (corrosion inhibitor)
4. Na borate (pH buffer)
5. Tannin/lignin mixes (scale/corrosion inhibitors, and dispersants)
6. Zinc (Zn) acid, and Bayhibit AM is a brand of PBTC. HEDP and PBTC have become the de facto multifunctional inhibitor standards for calcium carbonate, iron, and silt, although, as stated elsewhere in this article, HEDP has very poor calcium tolerance. “Calcium tolerance” describes the ability of a chemical to resist complexation with calcium, so to avoid the risk of calcium phosphonate precipitation, it needs to be fed directly into a main flow line using a quill. Note that the poor calcium tolerance of the phosphonates can be suppressed by the addition of an AA/SA copolymer, thus keeping the phosphonate totally active in solution.
Because each of the phosphonates exhibits subtle (or sometimes not so subtle) changes in effectiveness for different contaminants, under different waterside conditions, it is common to blend them. For example, HEDP/ATMP is a very decent scale and corrosion inhibitor blend. HEDP and PBTC also function as useful corrosion inhibitors, by forming calcium carbonate/phosphonate complexes at the metal water interface, although amino phosphonates (such as ATMP) typically perform better as corrosion inhibitors. ATMP is a decent, low-cost, general-purpose scale and corrosion inhibitor but can be uneconomic in the presence of significant iron. Standard phosphonates perform well up to 100x calcite saturation levels, and under these circumstances appear to be more efficient for calcium carbonate than are most regular AA polymers. Additional notes are presented as bullet points here:
Examples of calcium tolerance are as follows: A scale of calcium tolerance was shown to be #9 for polyacrylate through #17 for HEDP, #2 for AMP, #75 for #HPA, #100 for PBTC, #530 for PMA, and #1,640 for the SA/ AA copolymer. It is likely that the calcium tolerance value for terpolymers is much greater—probably about #5,000! HPA is a very good steel corrosion inhibitor and functions by a self-limiting corrosion process, so it is good for soft water (where calcium is limited). But it may need higher feed rates (i.e., > 5 ppm actives). It is not halogen stable, but this negative can be ameliorated by use of monoethanolamine (MEA) in the formulation.
applications scale inhibitor. It is useful as a corrosion inhibitor for Al. Also, it has a high sequestration value, making it valuable for chelating Fe, Mn, and copper (Cu). It exhibits good thermal tolerance ability, and excellent hydrolytic and thermal stability.
PAPEMP is a good example of a multifunctional phosphonate, exhibiting excellent scale-control perfor mance at very high calcite saturation levels. It is also good for iron stabilization, sulfates, silica, and silicate deposit control. Also, being an aminophosphonate, it is an effective corrosion inhibitor.
HPA, because of its excellent solubility, stability, and corrosion inhibition, should also be present across the treating spectrum.
HPA has scale-control properties and is a good solubi lizer for Fe and manganese (Mn). DETA phosphonate (aka acid—diethylenetriaminepenta[methylene phos phonic acid]) is a good, general-purpose oil and gas
For Ba/Sr in O&G, we may need to use Bis(hexamethylene triamine penta(methylene phosphonic acid) (BHMTPMP or BHMT) or hexa-methylene diamine tetra methylene phospho nate (HMDTMP or HDTMPA). These are highly efficient chelating agents and have a good effect on calcium carbonate and barium sulfate (barite) scales. They are usually available as partly neutralized salts.
Note that barite solubility increases with temperature (as opposed to the inverse temperature solubility of calcium carbonate). Also, barite solubility is relatively pH inde pendent and lower than that of calcium carbonate.
Celestite (SrSO₄) is relatively pH dependent. Its solubility is higher than calcium carbonate and decreases with temperature. Most barite scales will contain some strontium within the crystal lattice, and barite and celestite are typically associated with other types of oilfield scales.
Polyaminophosphonates (PAP) are a developing group of blended phosphonates that offer even more multifunctionality than PAPEMP.
The merits of PAPEMP for calcium carbonate dispersion under stress indicate that the strong (negative) correlation with calcium carbonate saturation is due, at least in part, to the generation of a (thin) protective film of calcium carbonate. Good corrosion rates are obtained with PAPEMP at saturations as low as 50 times calcium carbonate, while excellent corrosion rates are obtained above 100 times calcium carbonate (CaCO₃) saturation.
Examples include Lubrizol K752, which is a brand name for a 2,000-MW polyacrylic acid, and Lubrizol K732, which is a 5,000-MW PAA.
Note that the 2,000 to 2,600-MW homopolymers are decent scale-control agents for heating, ventilation, air conditioning systems and RO. They can also be used in sugar evaporators, especially if blended with PMA (poly maleic acid—sometimes termed hydro lyzed PMA—or HPMA) or HEDP. 4,500-MW homoacrylate polymers are good dispersants for CaCO₃, silt, and iron under normal lower stress condi tions, as the backbone molecule tends to “curl” at high temperatures. Blending a 2,000-MW and 4,500-MW PAA provides for synergy and increased scope of application. (A 2,000-MW polyacrylic acid/acrylate is a good scale inhibitor for light duty.) A 4,500- to 5,500-MW PAA is a good dispersant and blending the two provides a wider range of application.
The financial rationale for the recycling of PW as makeup water for fracturing fluids will continue to improve because, at present in some plays, PW volumes are 200% to 400% in excess of the annual completion sourcewater demand, thus offering significant opportunities for water reuse.
Polyacrylic acids (PAA), polyacrylates, and polymeth acrylates (PMA—not to be confused with polymaleic acid chemistries, which are often also termed PMAs) are widely employed as dispersants and scale inhibitors in cooling water, RO systems, and many other applica tions. These chemicals can be employed either on their own as lower cost chemistries, as components of more complex chemical reaction blends to produce a multi tude of various co- and terpolymers, or in formulations as physical blends—often as a low-cost backup support to a more complex, selective, and expensive formulated chemistry. The most popular PAAs and PMAs are those with molecular weights ranging from 2,000 to 10,000.
HPMA and its salts are low-molecular weight, solvent-based polymerides with an average molecular weight of perhaps 500 to 900, depending on the produc tion method. This chemistry is soluble in water and has high chemical and thermal stability (the decomposition temperature is above 330 ℃). HPMA has a significant scaling threshold effect at high temperatures and pH and is suitable for use in high-alkalinity water systems or built with other chemis tries. HPMA has good scale inhibition against carbonate and phosphate scales under high temperatures with effective contact time as long as 80 to 100 hours. Due to its good scale inhibition and high-temperature tolerance properties, PMA chemistries are widely used in thermal desalination plants, low-and medium-pressure boilers, crude oil evaporation, pipelines, and industrial circu lating cool water systems. HPMA has a good corrosion inhibition effect when used together with a zinc salt. Its limitation is the low molecular weight aspect of its char acter, as this means that, while the chemical is a superb scale inhibitor, it is a very poor dispersant and usually needs the addition of a suitable dispersant, such as a
PAA (for lower stress situations) or phosphinocarboxyl ates (PCA) (for higher stress conditions.)
Note that PMA is typically more cost-effective for calcium carbonate scale control than the best of the more common polyacrylic acid-based products—by a high factor. The charge density at the maleic anhydride group is more intense than PAA, allowing for better crystal distortion. This blending approach is matched by evidence that most multifunctional formulas are versatile and forgiving, with various ingredi ents able to cover for one another. Additional comments regarding poly maleic acid and maleates, including PMA, AA/ MA, and SS/MA, note that they are excellent scale control additives but tend to be limited in their dispersive effect. For example, Belclene 200 is a brand of PMA, and Belclene 283 is a maleic terpolymer, which offers much better dispersion, when used with 4,500-MW PAA. Finally, the author has successfully used PMA as an antiscalant for MSF evaporators in the Middle East, hardness stabilization for water-storage tanks in the African Kalahari Desert, and sugar evaporators in Central America. It is a great antiscalant but lacks good dispersive powers due to a low MW. Additional notes are presented as bullet points here:
AMPS based copolymers (e.g., AA/SA) and terpolymers have high calcium tolerances, and their presence in a formula often causes a major improvement in the calcium tolerance of any phosphonates present, and also of homo-polymers such as polyacrylate and polymaleate. It has been found that a terpolymer typically inhibits precipitation of calcium HEDP much more effectively than do copolymers. This superiority extends to other copolymers and phosphonates and persists as temperature, pH, and hardness increase. The homo-polymers have no proven appreciable influence on phosphonate stability.
AMPS copolymers have been found to be excellent dispersants for calcium phosphate when no iron is present. We might then ask under what conditions the higher priced terpolymers are justified? As an example of this, experiments have shown 10 mg/L of the copolymer AA/SA-25 is required to achieve 90% inhibition of phosphate precipitation (when no contaminants were present), while only 7.5 mg/L of the terpolymer AA/SA/ SS is required (i.e., a 25% reduction in product usage).
Where iron content is low, the copolymers perform just about as well as the terpolymers for calcium phosphate. One report has found terpolymers to be almost twice as effective as the copolymers in the presence of 1.0 mg/L of iron. These tests showed more significant change when iron was increased to 2.5 mg/L, the terpolymer then becoming three times as effective. Copolymers have been found to be superior to the homo-polymer (polyacrylate).
Terpolymers are more expensive but are highly effective for dispersing phosphate and phosphonate complexes, as well as larger concentrations of iron, zinc, and silt.
While phosphonates inhibit the formation of crystals (via threshold and chelation mechanisms), polymers distort them (by crystal modification), preventing their further growth, and then disperse them. The homopolymers are excellent lower-cost control agents for calcium carbonate, silt, and iron under “normal” conditions, and their recommended dosage is less than that of copolymers or terpolymers. When raw material prices are factored in, this difference becomes even greater. There is, however, evidence that the dispersive advantage for homopolymers does not extend to calcium phosphate, or to large quantities of iron.
Copolymers and terpolymers include SS/MA, AA/AM, AA/SA, AA/COPS, AA/HPA, AA/ AMPS, AA/SA/NI, AA/SA/SS, and PBS/AM. For example, Betz Dianodic polymer is an acrylic acid/hydroxypropylacrylate, Versa TL4 is a sodium SS/MA, Calgon TRC 233 is a 60/40 AA/AMPS; Acumer 3100 is a strong brand for AA/SA/NI; and Alco Versaflex ONE is a copolymer. This group of polymers has a range of properties too wide for blanket recommendations, and individual polymer performance strongly depends upon specific polymer architectures.
Formulations for any specific range of problems generally require a combination of additives drawn from two or three, or more of these functional categories.
Polymeric acrylic acid/sulfonic acid copolymer (AA/ SA) or AA/AMPS extend the calcium tolerance of phosphonates, especially HEDP.
AA/HPA was the original dispersant for the Betz Dianodic stabilized phosphate programs. Note: Globally, stabilized phosphate/sulfuric acid and alkaline phosphate/dispersant programs are still the first choice of cooling water treatment in developing countries.
Azoles protect nonferrous metals and also prevent metallic contamination. Examples include TTA, BTA, and NaMBT, which are selected for corrosion control of copper and brasses. For example, Wintrol B-40Na is a 40% sodium BTA solution.
AA/SA/SS (ionic) terpolymer performs significantly better at preventing calcium phosphate precipitation than copolymers such as (neutral) AA/AM.
AA/SA/SS also exhibits better tolerance to metal ions (e.g., Fe, Mn, Al, Cu, Zn) than AA/SA (even though AA/SA is a good iron oxide dispersant because it is not affected by the presence of calcium, unlike PAA homopolymer).
Carboxylates, PCA, and phosphoncarboxylates (POCA) are BWA chemistries. For example, Belclene 494 is a POCA; Belclene 161 and Unisperse 124 are both brands of PCA; and Bricorr 288 is a phosphonated oligomer.
PCA is regarded as an excellent, thermally stable dispersant for use in steam boilers, but it is also a decent calcium carbonate scale inhibitor.
Bricorr 288 is a phosphonate reaction product corrosion inhibitor and alternative to HPA, but our experience is that it often performs better in closed loops than in open systems, and thus, it is a good alternative to Belclene 590 (which is itself, an organic replacement for nitrite.)
Nalco’s phosphonosuccinate oligomer is an alternative to Bricorr 288. Succinates are similar to maleates.
(Editor’s note: Within this section, specialty chemical treatments are mentioned with the names of the original manufacturers. Examples include Alco, Betz, and Calgon. These companies all are now part of other companies active in the water business. Their names were left in the text since those active in water treatment tend to remember some key chemistries by the original company names assigned at the time.)
TTA is normally the first choice, but it is not very soluble, necessitating incorporation in, mostly, strongly alkaline inhibitor blended formulations.
BTA is more soluble, but price and overall effectiveness may be a deterrent.
NaMBT is more suitable for closed loops. Products are typically employed to provide from 1.0 to 2.5 mg/L active azole in the water system—sometimes a little more. Higher concentrations—up to 25 to 30 mg/L actives are good inhibitors for multi-metal systems and provide disinfection.
Silica can also represent a problem area. Acumer 5000 and Versaflex Si are standard inhibitors. Polyetheramines are also used (e.g., Huntsman Jeffamine M-2070) as silica colloid stabilizers with Carbosperse K752 or K798 (as dispersants for the stabilized silica).
Zinc, having strong cathodic functionality and synergism with other inhibitors, is a welcome addition in highly corrosive settings.
Phosphates are well established components for corrosion inhibition but have serious solubility limits at high pH levels.
Some experts suggest that all formulas should, ideally, contain PBTC, HPA, azole, and terpolymer because of their individual effectiveness, versatility, and overall synergism.
This two-part article has looked at common historical O&G fracing practices involving high volumes of water and associated performance chemistries, and forward to an expansion of oilfield activities and more treated water reuse, to achieve higher yields of oil and natural gas. However, apart from global pollution issues, the United States faces an urgent water supply–demand
imbalance that must be resolved in part by a very signif icant increase in water recycling. For the O&G industry, this will likely mean an increased role for modern water separation technology equipment systems out there in the marketplace, and a reduced usage of performance chemistries, such that they are relegated to a “polishing” duty only.
Part 2 is mostly original work drawn on the authors’ experience and comments. Exceptions are Figures 1 and 2, which are reproduced with the kind permission of Rob Ferguson, and the second half of the section titled “A Guide to Scale and Corrosion Additives for More Complex Brine Water Chemistries.” This latter section is compiled largely of random extracts drawn from various published technical papers written by several collab orative authors, including Colin Frayne, (Consultant, Aquassurance, Inc.), Robert R. Cavano (deceased) (Scranton & Associates), Mahdi Sobhan (Cairo, Egypt), Dr. Zahid Amjad (Lubrizol Advanced Materials), and Rob Ferguson (French Creek). Key sources are as follows:
1. Amjad, Z.; Landgraf, R.T.; Penn, J.L. (2014). “Calcium Sulfate Dehydrate (Gypsum) Scale Inhibition by PAA, PAPEMP, and PAA/PAPEMP Blend,” International Journal of Corrosion
2. Cavano, R. (2002). “Phosphonates as Calcium Carbonate Control Agents,” the Analyst.
3. Cavano, R. (April 2005). “Inhibitor Choice and Dosage (For Scale Control in Cooling Towers),” Paper No. 05063, Corrosion 2005, Houston, Texas.
4. Cavano, R. (2008). “Developing Cooling Water Treatments—Parts 1, 2, 3,” the Analyst.
5. Frayne, C. (1999). Cooling Water Treatment: Principles and Practice Handbook, Chemical Publishing Co., New York, New York.
6. Ferguson, R. (Fall 2010). “The Chemistry of Strontium and Barium Scales,” AWT Annual Convention & Expo, Reno, Nevada.
7. Frayne, C. (2009). “Organic Water Treatment Inhibitors: Expansion of Current Guidelines, Parts 1 and 2,” the Analyst.
8. Frayne, C. (December 2010). “Control of Corrosion by Environmental Modification for Cooling, Heating, and Potable Water Systems,” Elsevier Reference Collection in Materials Science and Materials Engineering, Shriers Corrosion, pp. 2930-2970, ISBN: 9780444527875, DOI:10.1016/ B978-044452787-5.00161-X.
9. Sobnan, M. (2012). “Organic Phosphonates,” PowerPoint presentation, Egypt.
10. Sobnan, M. (2012). “Water Treatment Polymers,” PowerPoint presentation, Egypt.
11. Zuhl, R.; Amjad, Z. (2010). The Science and Technology of Industrial Water Treatment, CRC Press, Boca Raton, Florida.
Colin Frayne is British, now a U.S. citizen, and a leading industry consultant in water treatment, environmental science, and industrial process chemistries. At 16, he started full-time work as a trainee power plant chemist at Ford
Motor Co., UK, and studied part-time at the NE London Polytechnic (later the University of East London), Since those early days, Mr. Frayne has lived and worked on every continent (except Antarctica), with long spells in Africa, Europe, Asia and the Americas, working in industries of every description, including deep mining, steel plants, nuclear fuel, oil and gas, petrochemical, global data centers, F&B, and healthcare. He also worked on many environmental projects, including the Amazon basin, Welsh mountains, and Belgian canals. Today, he is a Fellow of the Royal Society of Chemistry, a Fellow of the Institution of Corrosion Technology, and a Fellow of the UK Water Management Society. He is also a European Chartered Scientist, a Chartered Chemist, and a Chartered Environmentalist. In 2004, AWT honored him with the Ray Baum Memorial Water Technologist of the Year Award, and in 2010, he received CWT Program Recognition of the Exam Writing Task Force. During his career, Mr. Frayne has also managed several businesses around the world and authored several published textbooks and peer-reviewed publications. He may be reached at (561) 267-4381.
With more than 40 years of experience, Barry Ekstrand is regarded as an accom plished executive leader of energy services and supply businesses, having served in senior executive leadership roles at both large integrated energy service companies and small/startup oilfield service and supply businesses. Mr. Ekstrand spent 22 years at Halliburton Energy Services in a variety of operations, sales, and technical management roles in the United States and Asia, with an emphasis in hydraulic fracturing, chemical stimulation, cementing, coiled tubing, and well testing businesses. He led Weatherford International’s organic startup of its hydraulic fracturing and pressure pumping business lines and then grew it from a zero capability/zero revenue concept to a top-tier global business. Mr. Ekstrand also led the startup of a high-quality frac sand and proppant manufacturing business, and he has worked with small energy service and supply companies to assist them with technology, commercialization, and management of growth. He currently serves as president and COO at Finoric LLC, a manufacturer of specialty chemical products for the oil and gas industry. Mr. Ekstrand received his BSc in chemical engineering from California State Polytechnic University at Pomona and his MBA from California State University at Bakersfield. He is a registered Professional Petroleum Engineer, and he holds eight patents. Mr. Ekstrand can be contacted at (713) 417-7745.
26.
27.
DTPMP: diethylenetriamine penta(methylene phosphonic acid)
EC: electrocoagulation
28. HPA: hydroxyphosphonic acid 29. HPMA: hydrolyzed polymaleic acid 30. MEA: monoethanolamine 31. Mg: magnesium 32. Mo: molybdenum 33. NTA: nitrioltriacetic acid 34. NTU: Nephelometric turbidity units 35. O₃: ozone 36. O&G: oil and gas industry 37. PAA: polyacrylic acid 38. PAP: polyaminophosphonates 39. PAPEMP: polyamino polyether methylene phosphonic acid 40. PBTC: 2-phosphonobutane 1,2,4-tricarboxylic acid 41. PCA/AMPS: phosphinocarbox ylic acid/2-acrylamido-2-methyl propane sulfonic acid
42. PMA: polymethacrylates 43. PMA: polymaleic acid 44. PW: produced water 45. RO: reverse osmosis 46. Se: selenium 47. SI: saturation index 48. SrSO₄: celestite 49. TBZ: thiabendazole 50. TCCA: trichloroisocyanuric acid 51. TDS: total dissolved solids 52. TEA: triethylamine 53. THPS: tetrakis(hydroxymethyl) phosphonium sulfate 54. TSS: total suspended solids 55. UV: ultraviolet 56. VOC: volatile organic carbons 57. WW: Wastewater 58. ZLD: zero liquid discharge
A century of steam generation for power production and industrial process heating has demonstrated the necessity for proper condensate, feedwater, and boiler water pH monitoring and control. Yet, as the authors can verify from direct experience, pH monitoring methods are often not well understood by plant personnel and engineers who design new plants. To begin with, instrumentation is often under- or overspecified. More importantly, many engineers do not realize that direct pH monitoring of high-purity water can be difficult and give imprecise data. This article examines the importance of pH control in steam generating systems, including modern heat recovery steam generators (HRSGs) and co-generation units, and it outlines the technology to obtain correct readings.
The primary component of most steam generators is mild carbon steel, with higher-grade steel alloys for super heaters and turbine blades/rotors. (Some industrial units or older power-generating boilers may contain copper alloys, which we will touch upon a bit later.) Modern online analytical chemistry instrumentation is a critical tool for protecting these systems from corrosion and deposit formation (1, 2). A key parameter is pH, whose importance regarding carbon steel corrosion is outlined in one of the most famous power industry corrosion charts, the Sturla diagram, which is shown in Figure 1.
The graphs in Figure 1 clearly show the influence of pH and temperature on carbon steel corrosion in conden sate/feedwater systems, and that corrosion dramatically decreases with a pH increase from 8.75 to 9.6. Note that these results were based on pH adjustment with aqueous ammonia (NH₄OH), which has been the common feed water pH-conditioning chemical for most high-pressure units. Samples were measured at 25 ºC. Ammonia raises the pH, as illustrated in Reaction 1.
The importance of the Figure 1 data became much clearer following the discovery of flow-accelerated corrosion (FAC) nearly four decades ago. A brief review of FAC fundamentals will be helpful.
During the evolution of large power plant construction and operation in the last century, researchers and power station chemists concluded that dissolved oxygen (DO)
ingress into condensate/feed water during normal operation was a prime factor for carbon steel corrosion, and, unargu ably, copper alloy corrosion. (Oxygen can cause severe corrosion during boiler shut downs. Look for an article on this subject in a future issue of the Analyst.)
Consequently, both mechanical deaeration and chemical methods (i.e., oxygen scavenger feed) were routinely employed to reduce feedwater DO concentrations to near zero. Oxygen scavenger (the better term is reducing agent) treatment combined with ammonia (or an alkalizing amine) came to be known as all-volatile treatment reducing [AVT(R)]. The chemistry induces the formation of a gray-black magnetite (Fe₃O₄) layer on carbon steel surfaces.
As suggested, a well-designed sample panel will cool all samples to 25 ºC, ±½ ºC. This enhances the accuracy of all instruments, not just pH.
Figure 1: Feedwater carbon steel dissolution as a function of pH and temperature.
In 1986, the foundations of this chemistry received a severe jolt, as “On December 9 of that year, an elbow in the condensate system ruptured at the Surry Nuclear Power Station (near Rushmere, Virginia). The failure caused four fatalities and tens of millions of dollars in repair costs and lost revenues” (3). Researchers learned from that accident, and others since, that the reducing environment produced by oxygen scavengers, coupled with the pH and temperature effects shown in Figure 1, is the prime ingredient for single-phase FAC of carbon steel. The attack occurs at flow disturbances such as elbows in feedwater piping and economizers; feedwater heater drains; locations downstream of valves and reducing fittings; attemperator piping; and, most notably for combined-cycle HRSGs, low-pressure (LP) evaporators, where the waterwall tubes (aka harps) have many short-radius elbows. In fact, FAC is still, globally, the leading waterside corrosion mechanism in fossil-fired power units (4).
Figure 2 shows photos of FAC-induced pipe failures (left) and heat exchanger walls that released high-pres sure water and steam.
FAC-induced failures at other plants have, in some cases, caused added fatalities. However, per the tech nique of oxygenated treatment (OT) implemented in Europe in the early 1970s, the Electric Power Research Institute (EPRI) developed a program to replace AVT(R) for utility drum units. It is known as all-vol atile treatment oxidizing [AVT(O)]. If the condensate/ feedwater system contains no copper alloys, which is true for virtually all HRSGs, then AVT(O) is recom mended instead of AVT(R). Oxygen scavenger feed is eliminated with AVT(O); rather, a small residual DO concentration (5 to 30 parts per billion [ppb], which is an adjustment from the previous 5 to 10 ppb guidelines) is maintained at the economizer inlet (4). Ammonia or perhaps an ammonia/alkalizing-amine blend is still used for pH control. High-purity conden sate (cation conductivity ≤0.2 microsiemens per centi meter [µS/cm]) is a requirement for AVT(O), but when proper conditions are established, magnetite becomes overlaid and interspersed with a tighter-bonding oxide, known variously as α-hematite or ferric oxide hydrate. It is noticeable for its distinct red color. Figure 3 shows passivated surfaces in a power plant using AVT(O) chemistry.
So, in most HRSGs, a pH range of 9.6 to 10.0 is recommended for the feedwater and LP evaporator circuit to minimize FAC. The high pH in the LP evap orator is encouraged to also minimize two-phase FAC. Briefly, this mechanism occurs in locations that have a joint water/steam phase, such as HRSG-LP drums, as oxygen and ammonia will flash off with steam, leaving behind rapidly moving water droplets of lower pH, which induce FAC.
As the above discussion emphasizes, pH monitoring is critical for reliable and safe plant operation. However, correct measurement and control can be a challenging task.
The fundamental definition of pH is the negative loga rithm of the hydrogen ion concentration. (Technically, it is the hydrogen ion “activity,” but for this discussion, concentration is sufficient.)
A very important property of water is auto-ionization. Apart from the influence of other constituents, a small fraction of water molecules dissociates into hydrogen ions and hydroxyl ions, as illustrated in Equation 1.
H₂O ⇌ H+ + OH Eq. 1
Hydrogen ions do not exist by themselves in solution, and Equation 1 is better represented by Equation 2.
2H₂O ⇌ H₃O+ + OH Eq. 2
However, Equation 1 will serve moving forward, as it sufficiently represents the following discussion.
Experiments have shown that in pure water, the concen tration of hydrogen ions and hydroxyl ions is 1 x 10 -7 moles per liter at 25 ºC. By convention, the equilibrium constant for this reaction is given as shown in Equation 3.
K eq = Kw= [H+] x [OH ] = (1x10-7) x (1x10-7) = 1x10-14 Eq. 3
Any increase in H+ ions will decrease the OH concen tration and vice versa. This leads to the subjects of acids, bases, and the pH scale. For aqueous chemistry, an acid is a substance that increases the hydrogen ion concentration, as represented by the reaction of the common compound hydrochloric acid with water (illustrated in Equation 4).
HCl + H₂O → H₃O+ + Cl Eq. 4
Hydrochloric acid is a strong acid that almost completely dissociates in standard aqueous solutions.
A base has the opposite effect and increases the hydroxyl ion concentration. Sodium hydroxide (caustic) is arguably the most well-known base (Equation 5).
+ H₂O → OH + H₂O + Na+ Eq. 5
Per Equation 3, pure water at 25 ºC contains 1 x 10 -7 moles per liter of hydrogen ions. The negative logarithm, and thus the pH, is 7.0. A pH of 7 is the definition of a neutral solution, albeit this pH can be established in solutions with dissolved ions that have buffering effects. The carbon dioxide/bicarbonate/carbonate series found in most surface supplies is the best-known example of buffered waters.
Consider the addition of enough acid to increase the hydrogen ion concentration to 1 x 10 -6 moles per liter (mol/L) (and, since [OH ] = Kw/[H+], decrease the hydroxyl ion concentration to 1 x 10 -8 mol/L). The nega tive logarithm of the hydrogen ion concentration is now 6.0, which is the pH of the slightly acidified solution. A solution with a hydrogen ion concentration of 1 x 10 -5 mol/L has a pH of 5.0, and so forth. Each change in pH unit represents a tenfold change in hydrogen and hydroxyl ion concentrations.
A fundamental pH probe and instrument schematic is shown in Figures 4 and 5.
“The pH measurement principle is based on the ionic exchange in the gel layer of the glass membrane” (5). Very accurate readings are possible in natural waters and solutions of sufficient ionic strength, but in the high-purity waters for steam generators, accuracy is often greatly diminished. Inaccurate measurements can give a mistaken assumption that chemical feed is satisfactory and FAC is minimized, when in fact they may not be. (To improve water quality measurement accuracy, iron monitoring, as discussed in References 1 through 3 and 6 through 8, is now commonly recommended as part of a comprehensive boiler water sampling program.)
Several methods are available for correctly checking and controlling pH in steam generator systems. For starters, high-purity feedwater pH can be directly correlated to specific conductivity established by the ammonia concentration, as shown in Table A.
Figure 4: The active tip of a pH probe.
Illustration courtesy of Hach.
Figure 5: Basic schematic of a pH and reference electrode.
A semi-log plot of conductivity versus pH produces a linear curve, which makes automatically controlled ammonia feed from online specific conductivity measurements very straightforward. This technique has become common. It should be noted that impurity ingress (including carbon dioxide) to conden sate and feedwater will influence conductivity and pH readings. This issue must be considered when eval uating chemical feed and control systems. For units in which an ammonia/neutral izing amine or amine-only feedwater treatment is utilized, algorithms can be designed to account for the difference in chemistry from straight ammonia treatment.
During the evolution of large power plant construction and operation in the last century, researchers and power station
chemists concluded that dissolved oxygen ingress into condensate/ feedwater during normal operation was a prime factor for carbon steel corrosion, and, unarguably, copper alloy corrosion.
Illustration courtesy of Hach.
Table A: Relationship of pH, Specific Conductivity (S.C.), and Ammonia in Pure Water (Readings at 25 ºC)
pH S.C. (µS/cm) Ammonia Conc. (ppm)
8.0 0.280 0.018
8.2 0.442 0.030
8.4 0.698 0.050
8.6 1.105 0.085
8.8 1.751 0.149
9.0 2.775 0.274
9.2 4.398 0.527 9.4 6.970 1.070
9.6 11.047 3.399 9.8 17.507 5.105
10.0 27.747 11.812
(Data Extracted from Reference 7).
Another chemistry issue that Table A clearly highlights is the significant increase in ammonia concentration as pH approaches 10. This is a function of the equilibrium reaction shown in Equation 1, which limits ammonia dissociation at high concen trations. This effect can be somewhat problematic when trying to achieve the neces sary pH to minimize two-phase FAC in the LP circuits of many HRSGs. A blend of ammonia with a lesser amount of a neutralizing amine may be more effective, but that is a subject for another article.
Conductivity can be used to accurately calculate pH in normal feedwater conditions, per Equation 6 (7).
pH = 8.55 + log(SC – CC/4) + 0.032(T – 25) Eq. 6
CC represents the cation conductivity of the sample, or as it is commonly called now, conductivity-after-cat ion-exchange (CACE). For samples properly conditioned to 25 ºC, the last term drops out. This method has become common for reliable pH calculations, and instru ments A are available to provide such data.
Direct high-purity pH measurement techniques have also advanced. It is common knowledge that pH and other measurements should come from on-line analyzers (as opposed to grab sample only). InstrumentsB are available that protects the integrity of the samples from outside interference, and provides continuous data to plant operators, chemists, and technical personnel, which in turn allows a rapid response to abnormal conditions.
Probe and data acquisition technology have been improved to provide more accurate and reliable readings. A general trend in this regard comes during sample panel fabrication, with primary and secondary coolers designed to produce samples at 25 ºC, ±½ ºC. Other key points (5) include the following:
Precisely controlled sample flow rate to eliminate errors caused by changes in flow.
A nonflowing reference electrode to eliminate salt leakage into ultrapure samples.
A sealed reference half-cell to eliminate electrolyte replenishment that can otherwise influence reading variability.
A conductive flow cell, connected to ground, to decrease static electrical charge induced by the flowing sample.
During downtimes, properly storing pH probes to ensure continued reliability and accuracy. In-situ storage methods are emerging to facilitate this process.
Reference 5 also highlights the importance of correctly accounting for temperature influence on pH measure ments and calibration. As suggested, a well-designed sample panel will cool all samples to 25 ºC, ±½ ºC. This enhances the accuracy of all instruments, not just pH. However, in many cases, sample temperatures may be well away from 25 ºC. Probes have been developed with precise temperature compensation devices to accurately calculate pH via the Nernst equation, as illustrated in Figure 6.
Temperature effects must also be considered when calibrating probes with standard solutions of different temperature than the sample. It may be necessary to disable the temperature compensation function of the probe to ensure that the probe and calibration standards match from a temperature aspect.
Figure 6: Representation of the influence on pH by temperature per the Nernst equation. -mV +mV
E = E0+ log aH+ R T nF ∆ slope ~ 0.2 mV/°C
While pH is a critical measurement for steam generator condensate, feedwater, and boiler systems, over-spec ification of the instrumentation is quite common. For several years, author Buecker reviewed bid documents for water treatment and water/steam sampling systems at numerous combined-cycle power plant projects. Invariably, the project designers would select pH instru ments for every steam sample. Steam is normally so pure that pH provides very little valuable data, and in fact may offer misleading information. Thus, the plant owner could save money by minimizing pH analyses of steam samples. Sodium, silica, and CACE typically provide the best data for steam purity monitoring (7, 8).
Accurate pH sampling and analyses of steam generator circuits are critical for reliable operation of the units. This article primarily focused on condensate/feedwater analyses, but boiler water monitoring is important too. However, for the many drum units that still use phos phate or caustic chemistry for boiler water treatment, pH is a straightforward measurement. It is the high-pu rity feedwater that presents challenges. Several reliable techniques are available to accurately measure or calculate pH, and from there, to automatically control chemical feed. While aqueous ammonia remains the typical condi tioning agent, more use is being made of ammonia/alka lizing-amine blends, particularly as a method to mini mize two-phase FAC in the LP drums of HRSGs.
1. Buecker, B. (September 2019). “Monitoring of Water and Steam Chemistry for Steam Generators,” Chemical Engineering
2. Buecker, B.; Powalisz, J. (July 2022). “HRSG Water/Steam Sampling: Do it Right or Face Potential Consequences,” Hydrocarbon Processing.
3. EPRI (2017). Guidelines for Control of Flow-Accelerated Corrosion in Fossil and Combined-Cycle Power Plants, EPRI Technical Report 3002011569, the Electric Power Research Institute, Palo Alto, California. Note: While EPRI typically charges a substantial fee for reports to non-EPRI members, this document is available at no charge due to the importance of FAC understanding and control. Visit https://www.epri.com for more details.
4. Shulder, S. (June 7–9, 2022). Technical data provided by Steve Shulder, retired, formerly EPRI water/steam chemistry program manager) during the 40th Annual Electric Utility Chemistry Workshop, June 7–9, 2022, Champaign, Illinois.
5. Hach (n.d.). “Ultra-Pure Water Measurements: pH • Conductivity,” Hach Technical Bulletin, Hach, Loveland, Colorado.
6. Buecker, B.; Kuruc, K.; Johnson, L. (January 2019). “The Integral Benefits of Iron Monitoring for Steam Generation Chemistry Control,” Power Engineering.
7. EPRI (2013). Comprehensive Cycle Chemistry Guidelines for Combined Cycle/Heat Recovery Steam Generators (HRSGs), EPRI Technical Report 2002001381, Electric Power Research Institute, Palo Alto, California.
8. International Association for the Properties of Water and Steam (2015). “Technical Guidance Document: Instrumentation for Monitoring and Control of Cycle Chemistry for the Steam Water Circuits of Fossil-Fired and Combined Cycle Power Plants.”
A Instruments are available that can provide specific and cationic conductiv ity or calculate pH. One example is the Hach 9523 instrument that measures specific and cationic conductivity and calculates pH.
B Instruments are available that protect high-purity water samples from outside contamination, while also providing continuous data to plant operators and other technical personnel. One example is the Hach 8362 pH monitoring system and sensors.
Brad Buecker is president of Buecker & Associates, LLC, which supplies consulting and technical writing/ marketing services. Most recently he served as senior technical publicist with ChemTreat, Inc. He has more than four decades of experience in or supporting the power industry, much of it in steam generation chemistry, water treatment, air quality control, and results engineering positions with City Water, Light & Power (Springfield, Illinois) and Kansas City Power & Light Co.’s (now Evergy) La Cygne, Kansas, station. His work also included 11 years with two engineering firms: Burns & McDonnell and Kiewit. He also spent two years as acting water/wastewater supervisor at a chemical plant. Mr. Buecker has a B.S. in chemistry from Iowa State University with additional course work in fluid mechanics, energy and materials balances, and advanced inorganic chemistry. He has authored or co-authored more than 250 articles for various technical trade magazines, including the Analyst, Industrial Water
Treatment, and Ultrapure Water Journal. Mr. Buecker has also written three books on power plant chemistry and air pollution control. He is a member of ACS, AIChE, AIST, ASME, NACE (now AMPP), and the Electric Utility Chemistry Workshop planning committee. He may be reached at beakertoo@aol.com
Denton Slovacek grew up farming and ranching in the Texas and Oklahoma Panhandle. His undergraduate degree was from Friends University in Wichita, Kansas, and he received his master’s degree from Oklahoma State University. Mr. Slovacek served on the faculty at Northeastern Junior College for 13 years as an instructor in chemistry and the soil sciences. In 1989, Clifford Hach hired Mr. Slovacek to collaborate with him on product development. During his 30+ year tenure at Hach, Mr. Slovacek has managed the Hach Technical Training Center, Customer Support, and Technical Support. Since 2011, he has worked directly with customers and Hach sales as an application development manager within the Industrial Markets segment. Mr. Slovacek also works closely with the firm’s R&D group. He can be reached at dslovace@hach.com .
Jean Holz has a bachelor’s degree in mechanical engineering from the University of Wisconsin–Madison. She has been with Hach for 28 years, working primarily in the Power Generation Industry segment. Her roles have included regional sales manager, inside sales manager, and applications development manager. In her current role, Ms. Holz’ responsibilities involve working closely with key industry accounts and Hach’s field sales team. She also works closely with Hach’s product development efforts for the power generation, and pulp and paper Industries. Ms. Holz can be reached at jholz@hach.com
Xavier Leblanc obtained a bachelor’s degree in chemistry in France and has spent the past 30 years in different functions as application chemist, training manager, and technical support specialist for the HachLange-Polymetron product range. As a specialist of pure and ultrapure water applications, he is now working for Hach as a product application manager and subject matter expert for ultrapure water applications. Mr. Leblanc can be reached at xavier.leblanc@hach.com
(Editor’s note: This article is the first of a two-part series.)
In boiler systems, the term "passivation" has been applied to a wide variety of situations, ranging from the strict electrochemist's definition of potentials to the boiler operator's measurement of soluble and insoluble iron in the boiler system. Other definitions include conditions of minimum iron solubility (i.e., minimum corrosion) or the existence of a tight, adherent iron oxide film.
Although the descriptions may vary widely, the objec tives are identical: to create conditions that minimize the corrosion of iron. This article series will examine the chemistry of iron oxides found in boiler systems, postu lated corrosion mechanisms, the thermodynamic and kinetic conditions that control iron oxide formation in boiler systems, the effects of dissolved oxygen and chem ical oxygen scavengers on these system conditions, and some passivation/corrosion measurement techniques.
Part 1 provides a tutorial about the chemistry of iron and iron oxides and commonly accepted hypotheses about mechanisms of corrosion and magnetite formation. Part 2 focuses on more practical aspects of passivation: the effect of system conditions and reducing agents and measurements of corrosion and passivation phenomena.
Some researchers have defined passivation as the creation of a barrier to additional oxidation; others have defined passivation as the absence of corrosion, with no reference to the nature of the metal surface. If the definition of passivation is the conversion of an oxide to magnetite, then a reduction reaction must have occurred. If the definition of passivation is the creation of a tight adherent oxide film from the substrate metal, then an oxidation reaction must have occurred. Corrosion is also defined as an oxidation reaction; by the second definition, passivation is the result of a controlled corrosion reaction. These two different defini tions raise the important question: How do we understand passivation—is it an oxidation or a reduction reaction?
Explaining the current and sometimes contradictory information about corrosion and passivation in steam generating systems requires a review of the chemistry of iron oxides in boiler systems, postulated corrosion
mechanisms, the thermodynamic and kinetic conditions that control iron oxide formation, the effects of dissolved oxygen and chemical oxygen scavengers, and some passivation/corrosion measurement techniques.
In boiler systems, the most common form of iron is carbon steel. Stainless steel alloys are also common in boiler systems for some process applications, such as ammonia or methanol production. The formation of iron oxides is a spontaneous process that occurs continuously on carbon steel surfaces. Oxides will convert from one form to another based on environmental conditions. Table A shows the four forms of iron oxides that exist in boiler water systems (1, 2).
Ferrous hydroxide (Fe(OH)2) is fairly soluble; however, it may exist as a gel-like material adhering to filters. Ferrous hydroxide has a yellowish color and forms at temperatures below 50 °C (122 °F). Above 50 °C (122 °F), ferrous hydroxide may convert to magnetite if system conditions are favorable.
All forms of FeO(OH), including goethite and lepido crocite, are insoluble in water and exist as a very porous, unstable oxide layer that is easily disrupted by mechanical or chemical processes. In systems where lepidocrocite exists, particulates trapped on a submicron filter (e.g., a Millipore® filter < l) will have a yelloworange coloration. Under certain conditions, lepidocrocite can convert to magnetite.
Oxide Crystal Form Mineral Name Thermal Behavior
Fe(OH)2
Ferrous hydroxide Above 50–100 °C, decom poses to Fe3O4 and H2; with trace (O2) transforms to Lepidocrocite.
FeO(OH)
Alpha Goethite Above 200 °C, dehydrates to Hematite.
Beta Above 230 °C, dehydrates to Hematite.
Gamma Above 200 °C, dehydrates to Hematite.
Fe2O3
Alpha Hematite Above 1,300–1,457 °C, decomposes to Magnetite.
Gamma Maghemite Above 250 °C, dehydrates to Hematite.
Fe3O 4 Magnetite
Millipore is a registered trademark of MilliporeSigma (a unit of Merck), Burlington, Massachusetts.
Hematite is insoluble in water and forms an oxide layer that may be porous and easily disrupted, or adherent and relatively stable, depending on the environmental condi tions of the system. In systems where hematite exists, particulates trapped on a submicron filter will show a brick red coloration.
Magnetite is an insoluble material. Like hematite, magnetite may form a porous oxide layer or a stable, protective oxide layer based on the environmental condi tions. However, unlike hematite, magnetite forms a very dense matrix that closely matches the lattice structure of the underlying steel surface, minimizing the mechanical stresses at the interface.
The formation of a continuous, adherent layer of magne tite is the most desirable form of iron oxide in boiler systems because it protects against corrosion. In systems where magnetite exists, a submicron filter will show a black coloration. The conditions that favor the conver sion of these oxides to magnetite are discussed in the "Magnetite Formation" section of this article.
All iron or carbon steel surfaces have a surface layer comprising a single oxide or a mixture of oxides. A widely accepted description of this oxide layer is a crystalline structure that is permeable to ionic transport (3–6).
One model describes the oxide layer as comprising two distinct layers: a thin, adherent, homogeneous inner layer and a less dense, less adherent, heterogeneous or homo geneous outer layer (7–9). Another model postulates a polymeric hydrated oxide in which water acts as a binder between the polymeric oxide chains to create an amor phous, single-layer structure (10). The conditions that favor the formation of these oxide layers are discussed in Part 2 in the section "The Effects of System Conditions." These oxide layers may or may not be protective, depending on the physical conditions of the system during and after formation of the oxide layer.
Most definitions of corrosion include the concept of the dissolution of a metallic material by chemical or elec trochemical reaction with its environment. Corrosion is considered an electrochemical reaction because electrical currents can be measured in the areas where dissolu tion is occurring. Electrochemical reactions result in a
network of localized short-circuited electrolytic cells on the metal surface. At the anode area of the iron surface, the following half-reaction occurs (Equation 1) (11).
Fe Fe2+ + 2e Eq. 1
At the cathode, one or both half-reactions (Equations 2 and 3) occur based on the pH and the presence or absence of dissolved oxygen.
H+ ½H 2 - e Eq. 2
2H+ ½O2 - 2e Eq. 3
Each half-reaction has an electrochemical or oxidation/ reduction (redox) potential. These redox potentials are related to the change in the free energy (i.e., the thermodynamics) of the system and are temperature dependent. The larger the difference between the redox potentials, the higher the reaction rate. Thermodynamic principles dictate that all reactions will proceed spontaneously (automatically) toward a state of the lowest free energy or equilibrium. As Fontana states (12), "Corrosion will not occur unless the spontaneous direction of the reaction indicates metal oxidation."
Combining these half-reactions, reaction equations (4) through (7) define the corrosion process in boiler systems that have an alkaline aqueous environment and operate at saturation temperatures. Corrosion is an electrochemical reaction because water and dissolved oxygen or acid salts, such as chlorides and sulfates, form electrolytes that cause corrosion reactions to occur (13). All these reaction rates increase with increasing temperature. These are illustrated in equations 4 through 7.
3Fe + 4H 2O 3Fe3O4 + 4H 2 Eq. 4
2Fe3O4 + H 2O 3Fe2O3 + H 2 Eq. 5
2Fe + 2H 2O + O2 2Fe(OH)2 Eq. 6
2Fe3O4 + ½O2 + H 2O 6FeO(OH) Eq. 7
With respect to passivation, the corrosion reaction in Equation 4 is favorable because newly formed magnetite may be protective. The corrosion reaction in Equation 5 may be unfavorable because hematite is often less
protective than magnetite. In the presence of dissolved oxygen and/or acid salts, these corrosion reactions may occur in a very localized manner, forming stable corrosion sites known as pits. An oxide layer forms above the pit (Figure 1); this oxide layer isolates the solution inside the pit from the bulk water. The corrosion process inside the pit is self-sustaining and will proceed until the removal of the oxide cap. Another type of corrosion, stress corrosion cracking (SCC), may occur across and along grain boundaries of elements or at locations where impurities substitute for the expected constituents in the crystalline lattice structure (13).
The commonly accepted mechanism for corrosion is a two-stage process: initiation of stable corrosion sites and progression of these microscopic pits into larger and deeper pits (4). There are several models that describe the mechanism of corrosion (14–19). Typically, corrosion is considered a heterogeneous (i.e., two-phase) electrochemical process involving charge transfer and mass transport (20–23). The corrosion mechanism starts with charge transfer (Equations 8 and 9): electrons moving through the solid metal substrate and the oxide layer(s) and then into the aqueous layer.
Fe + OH FeOH + e
Eq. 8
FeOH FeOH+ + e Eq. 9
Figure 1: Corrosion pit schematic.
The corrosion mechanism proceeds with mass transfer (Equation 10). As the corrosion process progresses, the iron ions diffuse into the aqueous media to form an iron oxide layer.
FeOH+ Fe2+ + OH Eq. 10
Depending on the system, rate-controlling reaction for pitting corrosion or stress corrosion cracking (SCC) might be the charge transfer step or the mass transfer step. For example, in a system that limits mass transfer (on a microscopic scale) and has residual manufacturing stresses or environmentally induced stresses, SCC or crevice corrosion may occur.
SCC is a very complex phenomenon with many postu lates about the mechanisms of crack initiation and prop agation. There is little consensus regarding the role of oxide films in minimizing SSC. Some scientists propose that magnetite will reduce crack propagation, while others assert that magnetite will prevent crack initiation. In the presence of a magnetite film, the alloy composi tion correlates with the risk of SCC. In the absence of a magnetite film, other factors, such as the presence of chlorides or residual stresses, have a larger role in the formation of SCC (13).
In most areas of the boiler system, the charge transfer is the limiting factor for the corrosion rate because the mass transfer rate is high. Consequently, the recir culating boiler water removes the corrosion reaction product—ferrous hydroxide—from the surface. As the concentration of the corrosion products decreases at the corrosion site, the thermodynamic forces re-establish equilibrium concentrations of the reactants, driving reaction (10) to the right and increasing the corrosion rate (21).
This type of corrosion is known as erosion-corrosion or flow-assisted corrosion. The corrosion rate or kinetics of erosion-corrosion depends on the flow velocity, water chemistry, temperature, and chemical composition of steel (24). Not surprisingly, the corrosion rate also depends on the magnetite film thickness (13). Various investigators have postulated mechanisms describing the method of dissolution and diffusion between the iron substrate, inner layer, outer layer, and aqueous phase (25–29).
To illustrate the principles of thermodynamics as they apply to corrosion phenomena, Dr. M. Pourbaix (30) created electrochemical potential-pH plots. These plots, known as Pourbaix diagrams, show the oxidation states and oxide compositions that are thermodynamically stable, (i.e., have the lowest free energy) as a function of pH, electrochemical potential, and temperature. Figure 2 shows the equilibrium iron-water system at 200 °C (414 °F). These Pourbaix diagrams enable predictions of the spontaneous direction of chemical reactions and an estimate of the composition of reaction products. These diagrams also enable prediction of environmental changes (e.g., pH) that impact the direction of the reac tions (i.e., the creation or dissolution of the metal and metal oxides).
These Pourbaix diagrams do not predict the integrity of the oxide film or the kinetics (reaction rate) (12). As will be described in Part 2 in the section "The Effects of Reducing Agents," system conditions such as pH and dissolved oxygen concentration influence the integrity of the film and the kinetics. For example, the rate of reaction (2) will increase with decreasing pH (pH = -log[H+]). Likewise, the rate of the cathodic Equation 3 will increase as the concentration of dissolved oxygen increases. However, these diagrams do not contain any information about the severity of the corrosion (i.e., pitting or SCC or any information about corrosion mechanisms).
Researchers have investigated various mechanisms to describe the formation of magnetite. There are two categories of mechanisms: in situ conversion of the existing substrate to magnetite versus oxide transport and conversion to magnetite. System thermodynamics control the probability of formation of magnetite; kinetics control the rate of formation of magnetite. Optimizing system conditions such as temperature, pH, concentration of reactants, and dissolved oxygen will improve both the thermodynamics and kinetics and the probability and rate of magnetite formation.
Under thermodynamically favorable conditions, magnetite formation is spontaneous through the oxidation of the iron surface, as described by Equation 11. "Spontaneous"
formation does not necessarily imply a fast process; the kinetics will control the rate of the reaction.
3Fe + 4H 2O Fe3O4 + 4H 2 Eq. 11
There are several different mechanisms proposed for the formation of magnetite from iron or other oxides. The best-known mechanism for the reduction of ferrous hydroxide to magnetite above 100 °C is the Schikkor Reaction (Equation 12) (31).
3Fe(OH)2 Fe3O4 + 2H 2O + H 2 Eq. 12
Investigators at the Naval Research Laboratory (32) have proposed a mechanism for the formation of ferrous hydroxide through the corrosion of iron metal (Equation 13).
Fe Fe2+ Fe(OH)+ Fe(OH)2 Eq. 13
The conversion of hematite or maghemite to magnetite can occur through slow heating, with minimal or no oxygen present (Equation 14) (2).
Fe2O3 heat Fe3O4 Eq. 14
This in situ conversion of the existing substrate to magnetite occurs under thermodynamically favorable conditions. Electrochemical potential describes the conditions that thermodynamically favor the formation and maintenance of magnetite. Pourbaix graphically illustrated all reactions that are theoretically possible and impossible for various electrode potentials and pH condi tions for iron and iron oxides (Figure 2).
Although Pourbaix's diagram shows all the reactions that are thermodynamically possible, not all reactions will necessarily occur due to a large "over-potential" or electro chemical energy barrier. Even if the system conditions (i.e., electrochemical potentials) are favorable to the formation of magnetite, the degree of protection against corrosion depends on the kinetics of the reactions and on the physical nature of the magnetite layer (e.g. density, oxide integrity, thickness). As Pourbaix (30) stated: "passivation thus does not necessarily imply the absence of corrosion."
In boiler systems, oxides such as ferrous hydroxide and hematite may precipitate onto a surface; under favorable
system conditions, these oxides may convert to magne tite (33). Several Russian researchers (34, 35) have suggested a mechanism for epitaxial growth of a protec tive oxide film at temperatures above 250 ° C (482 °F). The decomposition of a specific chelant forms "secondary compounds" or oxides of iron, followed by a protective two-layer oxide film on the surface of pearlitic steels. The inner layer of magnetite forms by contact between the decomposing chelate and steel. The outer layer forms by contact of the iron chelate with the inner layer.
Predictably, one of the pre-conditions for the formation and maintenance of a dense magnetite layer is that the solubility of magnetite is at a minimum at system condi tions. Congruent or coordinated pH/phosphate control for high purity boiler water is a practical application of this concept of magnetite solubility. The specification ranges for pH on the coordinated pH/phosphate control chart are consistent with the minimum solubility of magnetite in water at the temperatures defined by the saturated pressure. Similarly, the specification ranges for dissolved oxygen and pH of feedwater, condensate, and boiler water defined by Electric Power Research Institute (EPRI) guidelines are also consistent with those condi tions of minimum solubility of magnetite.
The second part of this article series will focus on more practical aspects of passivation: the effect of system conditions and reducing agents and measurements of corrosion and passivation phenomena.
1. Bloom, M.C.; Smith Jr., S.H. (April 1, 1969). "The Corrosion Products of Iron and Their Relation to Corrosion in Steam-Generating Equipment," Naval Research Lab, Project SF 51-542–601.
2. Troy, M. (May 1978). "Study of Magnetic Filtration Applications to the Primary and Secondary Systems of PWR Plants," Electric Power Research Institute, Palo Alto, California, Study 76–665.
3. Mario, G.; Ferreira, S.; Alda, M.; Simoes, P. (1991). Electrochemical and Optical Techniques for the Study and Monitoring of Metallic Corrosion, Kluwer Academic Publishers, New York, New York, p. 485.
4. Tjong, S.C.; Yeger, E. (1981 Journal of the Electrochemical Society, 128, p. 2251.
5. Bloom, M.C.; Goldenberg, L.(1965). Corrosion Science, 5, p. 623.
6. Foley, C.; Kruger, J.; Bechtoldt, C. (1967). Journal of Electrochemical Society, 114, p. 994.
7. Potter, E.C.; Mann, G.M.W. (1961). Proceedings of the First International Congress on Metallic Corrosion, London, U.K., p. 417.
8. Wagner, C.; Bunsenges, B. (1973). Physical Chemistry, 77, p. 1090.
9. Nagayama, M.; Cohen, M. (1962). Journal of the Electrochemical Society, 109, p. 781.
10. Okamoto, G. (1973). Corrosion Science, 13, p. 471.
11. Uhlig, H.H. (1948). The Corrosion Handbook, Wiley & Sons Inc. New
York, New York, pp. 4-6,
12. Mars G.; Greene, F. Greene, N.D. (1978). Corrosion Engineering, McGraw-Hill Co., New York, New York, p. 12.
13. Flis, J. (1991). Corrosion of Metals and Hydrogen-Related Phenomena, Selected Topics, Elsevier, New York, New York, p. 15.
14. Nishimura, R.; Kudo, K. (1981). Proceedings of the 8th International Congress on Metallic Corrosion, Mainz, Germany, 1, p. 6.
15. Rozenfeld, I.L.; Marshakov, I.K. (1964). Corrosion, 20, p. 1151.
16. Heine, M.A.; Keir, D.S.; Pryor, M.S. (1965). Journal of the Electrochemical Society, 112, p. 24.
17. Hoar, T.P. (1967). Corrosion Science, 7, p. 335.
18. Sato, N. (1971). Electrochimica Acta, 16, p. 1683.
19. Sato, N. (1982). Journal of the Electrochemical Society, 129, p. 255.
20. Field, E.F.; Holmes, D.R. (1965). Corrosion Science, 5, p. 361.
21. Castle, J.E.; Masterson, H.G. (1966). Corrosion Science, 6, p. 93.
22. Castle, J.E.; Masterson, H.G. (1966). Corrosion Science, 6, p. 253.
23. Marsh, T.F. (1966). Journal of The Electrochemical Society, 113, p. 313.
24. Huijbregts, W.M.M. (April 1984). “Erosion-Corrosion of Carbon Steel in Wet Steam," CORROSION 1984, New Orleans, Louisiana, (NACE, Houston, Texas), p. 39.
25. Bessone, J.; Karkaya, L.; Lorbeer, P.; Lorenz, W.J. (1975). Electrochimica Acta, 20, p. 273.
26. Bech-Nielsen, G. (1976). Electrochimica Acta, 21, p. 627.
27. Engell, H.J. (1977). Electrochimica Acta, 22, (1977) p. 987.
28. Bonhoeffer, F.K. (1953). Zeitschrift für Metallkunde (International Journal of Materials Research), 44, p. 77.
29. Weil, K.G.; Bonhoeffer, F.K. (1955). Zeitschrift für Physikalische Chemie (International Journal of Research in Physical Chemistry and Chemical Physics), 4, p. 175.
30. Pourbaix, M. (1966). Atlas of Electrochemical Equilibria in Aqueous Solutions, Pergamon Press: New York, New York, p. 71.
31. Schikorr, G. (1933). Zeitschrift für anorganische und allgemeine Chemie. 212, p. 33.
32. Linnenbom, V.J.; Hoover, J.F.; Dreyer, H.S. (Sept. 25, 1956). “Solubility and the Products of Reaction Between Iron and Water at 26 °C and 300 °C," Naval Research Laboratory Report 4824.
33. Hoar, T.P. (1949). Journal of the Chemical Society, Faraday Transactions. 45, p. 683.
34. Margulova, T.Kh.; Moskvin, L.N.; Efimov, A.A.; Vainman, A.B.; Kalinina, A.G. (1983). Thermal Engineering, 30, 8(1983) p. 467.
35. Moskvin, L.N.; Efimov, A.A.; Zhuravleva, E.yu (1989). Thennal Engineering, 36, 7(1989), p. 393.
Loraine Huchler is the founder and president of MarTech Systems, Inc., a firm that assesses and manages risk in water-re lated utility systems. Her work includes optimizing the performance of the water treatment service provider and the assets in water circuits in hot water/steam and chilled/condenser water in large-scale corporate and university campuses and manufac turing facilities. She also provides technology feasibility studies, water conservation and water reuse studies, technical training, and service as an expert witness in patent infringement and equipment failure litigation. Ms. Huchler has a B.S. in chemical engineering from the University of Rochester (New York), is licensed as a Professional Engineer, and has earned the accreditation of Certified Management Consultant®. Ms. Huchler can be contacted at huchler@martechsystems.com .
In the world of food sanitation, several important factors need to be considered to properly clean the equipment used in processed foods. Homeowners are aware of how integral it is to sanitize food contact surfaces. It is commonplace to regularly scrub counters, sinks, and refrigerators. On a larger scale, food manufacturers must also do the same. The objective must be to safely remove leftover food and kill bacteria that can spread disease if left untreated. Of a wide array of methods used to control this bacteria growth, ozone (O3) is one of the most effective.
Ozone is a recognized antimicrobial agent and strong disinfectant commonly used in the food sanitation industry. The U.S. Food and Drug Administration (FDA) formally approved ozone to be used as an antimicrobial agent for treatment, storage, and processing of foods in gas and aqueous phases in 2001. It has a proven history of avoiding and controlling biological growth on food products in both liquid and gaseous form. As a gas dissolves in water, ozone is used to disinfect water, fruits, vegetables, poultry, fish, and process systems used in food manufacturing; however, its unique ability to be used in gaseous form also expands its range of use. This versatility also allows it to be used as a long-term preservative for products during their storage and significantly extends their shelf life. The use of ozone allows a large variety of fruits to be able to be kept on the shelf at grocery stores year-round.
Ozone equipment manufacturers can provide full systems for ozone used in various applications, including seafood, cold storage for fruits and vegetables, and even bottled water. These ozone systems generate the ozone on site using ambient air and filtration to generate pure oxygen gas (O2) that is then excited using a small amount of electricity to change O2 into O3. The O3 gas is then injected into cold water to form what is termed as ozone water. This is illustrated in Equations 1 and 2.
What makes ozone particularly effective as a disinfectant is the aggressive tendency of the O3 molecule to be highly reactive with bacteria, virus organisms, fungus, mold, pathogens, and aquatic plant life. Understanding this, it is not surprising that ozone can be aggressive to materials of construction. Systems used to distribute ozone must be able to withstand continuous exposure to this substance without breaking down. For ozone gener ating systems, additional requirements beyond the chemical resistance to ozone exist. Temperature stability and durability are required of the material of construction for these components. Furthermore, since the ozone generation system could poten tially be exposed to sunlight with several applications, UV resistance is also required.
When choosing materials of construction for a chemical service, several engineering criteria need to be considered. Table A addresses the many factors a supplier would evaluate before deciding on the material of choice. Ozone is commonly handled by several materials listed in the table, but each material has different costs and performance across a wide range of design concerns. Without question, a material cannot be considered if it is immediately attacked by the chemicals it is exposed to. The degree of chemical resistance needed is weighed against the expected lifetime and the inconvenience and cost of having to periodically replace it. The material must work for the desired period of expected service within the range of temperature and mechanical performance that would keep a component from losing its utility by changing shape or cracking.
When fabrication is involved, such as welding or mechan ical joining along with all of the other considerations, a material that is easier to work with can be preferred over others. Often, when material welding is necessary, a mate rial that is offered as a stiff homopolymer version or as a flexible copolymer version that can be easily fused, can be a great advantage to keep performance of a tubing, nozzle, and fitting all of the same expectation. Finally, should special considerations such as abrasion, sunlight exposure, and/or flame resistance ever need to be considered, each material would have a different set of properties measured against these concerns. Table A offers a comparison of the properties of different materials.
As a gas dissolves in water, ozone is used to disinfect water, fruits, vegetables, poultry, fish, and process systems used in food manufacturing.
PVC CPVC PE PVDF/PVDF Copolymer FEP/ PFA 304/316 Steel Comments
Chemical Compatibility + ++ + +++ +++ ++ +++ Means no concerns for chemical compatibility Temperature Range + ++ + +++ +++ +++ +++ Means no issues even at boiling point of water Mechanical with Temperature ++ ++ + +++ + +++ +++ Means no creeping over time Processing and Joining ++ ++ +++ +++ + +++ +++ Means easy to produce in factory Rusting/Rouging +++ +++ +++ +++ +++ + +++ Plastics do not have issue with rust residue
Available Rigid or Flexible +++ + ++ +++ o o +++ Only PVC and PVDF are known to be both rigid and flexible, and PVC is limited in rigidity above 60 ° C
Upfront Cost very low low very low medium high low to medium Cost here is only related to product cost and does not include higher maintenance for materials with shorter life
Intangibles + ++ + +++ ++ + Outdoor weathering, abrasion resistance, longterm stability, other cleaning agents, and other material factors
Table A Key:
o - material has limited or marginal capability + - material can be considered but is not considered as the optimum for the property when compared with other options ++ - material is satisfactory for this property +++ - material is very desirable when this property is considered important
PVC CPVC PE PVDF/PVDF Copolymer FEP/ PFA 304/316 Steel
Chlorine Dioxide ++ ++ ++ +++ +++ o
Chlorine + + + +++ +++ o Chloramine + + o +++ +++ + Iodophors* o + + +++ +++ o Ozone + ++ + +++ +++ ++
Soaps and Surfactants + + +++ +++ +++ +++
Sodium Hypochlorite (Bleach) ++ ++ + +++ +++ o Steam (up to 30 psi) o o o +++ +++ +++ Peracetic Acid o o o +++ +++ ++
Key for Table B:
o – material has limited or marginal capability
+ - material can be considered but is not considered as the optimum for the chemical when compared with other options ++ - material is satisfactory for this chemical +++ - material is very desirable when this chemical is considered important *Note: Iodophors are a mixture of iodine with a solubilizing agent.
Table A displays the differences in commonly used mate rials based on their chemical compatibility, temperature range, mechanical properties with temperature, ease of processing and joining, rusting and rouging properties, range of flexibility, upfront cost, and other intangibles. When choosing a material, several considerations are involved, and for each application, these considerations may be of different importance to the end-user. Some materials are good in every category and others are more specific to performing to just a few properties. It is important to consider additional factors outside of chemicals when designing systems. It is recommended to consult water system manufacturers or designers for material advice.
In food sanitation, ozone may be used in conjunction with other cleaning agents. The most common of these agents are chlorine, chlorine dioxide, chloramine, iodine solutions, soaps, sodium hypochlorite, steam, and peracetic acid. When designing a system using ozone, it is important to be aware that the downstream materials of construction may be contacted by any of these chem istries. Table B gives a deeper dive into general chem ical resistance performance of materials that are often considered for water systems. The corrosion resistance of plastics in water treatment facilities has been discussed in other publications (1).
Commonwealth Chemical Specialties, LLC Leisa Corbett-DeMartino
27 Apple Street
A multitude of potential cleaning agents exist for water delivery systems. Ozone is a highly reliable cleaning agent but is sometimes used in combination with other tech nologies. Table B lists common disinfectant methods and a general chemical resistance rating for each material of construction.
Tinton Falls, NJ 07724 (781) 421-3038
lcorbett@commonwealthchem.com www.commonwealthchem.com
Commonwealth Chemical Specialties, LLC is a supplier of specialty water treatment products. We are a distributor of top specialty water treatment products manufactured by leading water treatment chemical manufacturers. We strive to provide high-quality water treatment products and knowledge/training to water treatment service companies.
Numerous studies support the resistance of polyvi nylidene fluoride (PVDF) to ozone (2, 3). PVDF is available in rigid homopolymer form (ASTM D3222) for high-strength, low-creep injection molded compo nents (4). In addition to this, it is also available in varied flexible copolymer form (ASTM D5575) for bendable products such as tubing (5). Both forms of PVDF are FDA compliant and USP Class VI compliant. They have also both been used in a wide variety of food processing applications (6, 7).
Eastern Technologies, Inc. Gary Reggiani
103 New York Avenue, Suite 105 Sinking Spring, PA 19608 (610) 780-2080
gary.reggiani@go2eti.com www.go2eti.com
After more than 55 years of product development, a wide range of PVDF and PVDF copolymer components are commercially available to design complete systems for any chemical processing application. The systems used by major suppliers of ozone generating systems often include parts ranging from ¼-inch tube fittings to 3-inch control valves. However, PVDF is not limited to these system sizes.
ETI is a provider of troubleshooting and application expertise to independent water treatment professionals. ETI supports only service companies with a full portfolio of water treatment additives and does not support or sell directly to the end-user. In other words, ETI does not compete with our customers, as our business goal is to support the success of water treatment professionals and their organizations. In fact, our desire to help our customers succeed is a central part of our business strategy and continuous improvement focus.
One example is Ozone International, which is based in Bainbridge Island, Washington, and has been a supplier of ozone-based sanitizing equipment since 2003. Ozone International discovered that using the traditional stream of low-pressure ozone-infused water in conjunction with a separate stream of high-pressure water enables ozone to not only sanitize but also clean. This technology has become essential in water and food processing industries. It has the ability to extend shelf life of food products
by more than 60% by controlling pathogens, which increases production by tens of millions of pounds per year and reduces sanitation time and labor. When asked in personal communication about the essential compo nents to the system, the production manager at the company, D. Nabors, explained that the PVDF injection withstands the ozone remarkably well, especially given the volume that it sees (8).
Figures 1 and 2 show examples of PVDF tubing used in the ozone generator. Experience has shown that polyolefins and polyvinyl chloride (PVC) polymers can be compro mised over time, depending on the concentration of ozone in the water. PVDF, on the other hand, is not significantly affected in equipment used for over a decade of service.
The vast majority of bottled drinking water is treated with ozone at some point in the process, and growing amounts of municipal water systems are now utilizing ozone to treat public drinking water. Applications for ozone are abundant in a wide variety of applications. This also includes a large increase of applications for cold storage. Cold storage rooms thrive on ozone injection in order to maintain bacteria-free environments. Figure 3 displays ozonation systems in use. These systems contin uously apply low-pressure, ozone-infused cold water to food products, conveyor belts, or other equipment, killing bacteria and other organisms. The low-pressure ozone-in fused water breaks the molecular bond between fat and hard, which ensures the maintenance of clean surfaces.
When choosing a material of construction, many prop erties and costs need to be considered. Depending on the application, a different material or a combination of mate rials may be the best design option. For ozone systems, fluoropolymers would offer the widest range of perfor mance. Regarding cost performance, PVDF is largely the material of choice for ozone delivery systems. Ozone tech nology has seen tremendous growth in the last decade. The versatility and comprehensive abilities of ozone to sanitize water systems make it a top option for designers.
The authors would like to acknowledge contributors who were either interviewed or sent written information to help with generating information: Dave Nabors, produc tion manager at Ozone International, and Robert Roe, creative director at Ozone International.
1. Peters, A.; Seiler, D.; Palovcak, A. (Summer 2021). “Using Plastic Piping to Carry Wastewater Chemicals," The Analyst 28(3), pp. 36–44.
2. Pate, K.T. (March 1991). “FILTERS: Ozone Exposure of DI Water Filters and Their Efficiency," Ultrapure Water®, pp. 32–38.
3. Robinson, D.N. (Feb. 12, 1993). “Kynar® 720 Pipe Resistance to Ozone," ELF ATOCHEM USER & APPLICATION REPORT, pp. 1–3.
4. ASTM Standard D3222 (2018). "Standard Specification for Unmodified Poly(Vinylidene Fluoride) (PVDF) Molding Extrusion and Coating Materials," ASTM International, West Conshohocken, Pennsylvania, 2003, DOI: 10.1520/D3222-18A, www.astm.org
5. ASTM Standard D5575 (2018). "Standard Classification System for Copolymers of Vinylidene Fluoride (VDF) with Other Fluorinated Monomers," ASTM International, West Conshohocken, Pennsylvania, 2003, DOI: 10.1520/D5575-18, www.astm.org
6. Peters, A.; Mutton, S. (July 2021). “PVDF Pipeline for Fructose Transportation, Processing Magazine, pp. 30–33.
7. Palovcak, A.; Pomonte, J. (November 2018). “Belting Breakdown?” Processing Magazine, pp. 32–34.
8. Nabors, D. (Summer 2022). Ozone International, Bainbridge Island, Washington, personal communications with A. Peters, article author.
Alexandra Peters works for Arkema Inc. as marketing and end-use applications engineer for the High-Performance Polymers business. She received her B.S. in chemical engineering from Villanova University. At Arkema, her focuses are in Kynar® PVDF end-use applications and standards. She is also a member of ASTM and the ASME B31.3 committee. Ms. Peters may be contacted at alexandra.peters@arkema.com
Averie Palovcak works as the market and applications engineering manager for Arkema. She received a B.S. and an M.S. in biomedical engineering from Drexel University and an MBA from Villanova University. Ms. Palovcak is an active member of various industry standards committees, including ASTM, ASME, ASPE, and AMPP. She has been working with engineers and end-users for more than six years, providing her engineering and plastics expertise for designing upgraded fluid-handling systems using fluoropolymers. Ms. Palovak can be reached at averie.palovcak@arkema.com
Spread plate methods are notoriously inaccurate, with up to tenfold variability in results for the same sample.1 Multiple peer-reviewed studies have confirmed that the Legiolert Test provides more accurate and consistent results.2–5
Sign Up to Receive Emails From AWT.
Did you know you can manage the notices you receive from AWT? It’s the best way to ensure you learn about all AWT benefits in a timely manner.
Sign in to the AWT website to select your communication choices and complete your profile today.
If you have trouble signing in or have any further questions, please contact:
Angela Pike
Senior Member Services Manager
(240) 404-6477 apike@awt.org
Cortec Corp. announced the expansion of its EcoCortec plant in Croatia. EcoCortec manufactures vapor-phase corrosion inhibitor films and bags.
EcoCortec purchased an approximately 10,700 ft2 (1,000 m2) polymer processing facility that includes reprocessing equipment for the recycling of waste into new materials. The facility, which will open in November 2022, is expected to help the company minimize the disposal of potentially useful materials and reduce the consumption of fresh raw materials and energy usage. It will be divided between two production facilities within the Croatia plant with warehouses of raw materials and finished goods.
For more information, visit www.cortec.com.
Danaher Announces Intention to Separate Environmental & Applied Solutions Segment to Create an Independent, Publicly Traded Company
Danaher Corp. plans to separate its Environmental & Applied Solutions segment to create an indepen dent, publicly traded company. The new company will include Danaher's Water Quality and Product Identification businesses and will be referred to as "EAS" until it is named at a later date. The transac tion is intended to be tax-free to Danaher shareholders and expected to be completed in the fourth quarter of 2023. "With today's announcement, Danaher will become a more focused science and technology leader committed to innovation and making a profound impact on human health," said Rainer M. Blair, president and CEO. "We believe that EAS will be advantaged as a standalone company with greater opportunities to pursue high impact organic and inorganic investments," Mr. Blair continued. "The combination of a resilient business model—with more than 50% recurring revenue—and a talented team with a foundation built on the Danaher Business System will position EAS to continue delivering the same outstanding results it has as part of Danaher." Mr. Blair concluded, "This is an important milestone for both Danaher and EAS and demonstrates our commitment to maximizing long-term value for all of our stakeholders."
Jennifer L. Honeycutt will become president and chief executive officer of EAS upon completion of the trans action. Ms. Honeycutt joined Danaher in 1999 via the acquisition of Hach, and she currently serves as a Danaher executive vice president with responsibility for the Environmental & Applied Solutions segment.
Netherlands-based Nouryon has been granted a U.S. patent for its LumaTreat tagged polymer products, which enable customers to measure available deposit-control agents in water treatment systems and reduce polymer and water usage during treatment.
Many essential processes at production and manufacturing sites rely on the continuous operation of water treatment systems, cooling towers, and boilers. The accumulation of scale deposits degrades the overall efficiency and lifespan of these systems, potentially causing failures or shutdowns detrimental to operations in industrial facilities.
LumaTreat tagged polymers incorporate fluorescent monomers that “smart tag” the deposit-control polymers used in water treatment and prevent the buildup of calcium phosphate, calcium carbonate, and other minerals that produce scale deposits. These fluorescent tagged polymers enhance system troubleshooting for water treatment professionals through remote and accurate monitoring of polymer consumption, decreasing the risk of estimation errors. They can also be used in conjunction with or as an alternative to pyrenetetrasulfonic acid in water treatment formulations to indicate real-time consumption rates of the active polymer. A tagged polymer that enables more precise measurements can aid in reducing polymer dosage and water usage, while remote monitoring can eliminate the need to travel to sites.
U.S. Patent No. 11,208,408, “Method of Controlling Scale in Aqueous Systems,” covers LumaTreat tagged polymer products and the fluorescent monomers used in their creation.
2024 Technical Training Seminar (East) April 17–20, 2024
Cleveland Marriott Downtown at Key Tower Cleveland, Ohio
2024 Annual Convention & Exposition September 10–13, 2024
Louisville Convention Center and Omni Louisville Louisville, Kentucky
2025 Technical Training Seminars (West) February 25–28, 2025
Doubletree Mission Valley San Diego, California
2025 Annual Convention & Exposition November 12–15, 2025
The Broadmoor Hotel Colorado Spring, Colorado
2026 Annual Convention & Exposition September 16–19, 2026
Oklahoma Convention Center and Omni Hotel Oklahoma City, Oklahoma
2027 Annual Convention & Exposition September 8–11, 2027
Cleveland Convention Center Cleveland, Ohio
355 Indiana Avenue, Suite 200
Indianapolis, IN 46204 (317) 275-1606 Website: www.mcgowaninsgrp.com
McGowan Insurance Group was founded in 1930 by William K. McGowan. Today, well into our third gener ation of the McGowan legacy, we remain an independent firm located in Indianapolis, partnering with more than 100 insurance companies. Since the beginning of our involve ment in the water treatment business over 20 years ago, our approach to the industry has been education. We ensure that our partner insurance organizations understand all verticals and facets of the water treatment business to minimize the ebbs and flows of the normal insurance marketplace.
McGowan provides risk-advisory services as well as commercial insurance products to all verticals in the water treatment industry. We propose lines of coverage such as general liability, pollution and professional liability, excess/ umbrella insurance, equipment and property insurance, automobile or fleet insurance, management liability, workers’ compensation, and other kinds of policies. Through this division, our firm also designs and deploys custom-risk management programs in the areas of DOT compliance, OSHA training and compliance, and safety services.
In addition, our Bonding and Surety Unit and Prestige Personal Insurance Unit provide those products and services to the businesses and families with whom we work. McGowan Benefits Group works with clients to develop appropriate health insurance programs. We service both employer groups and individuals in all areas of benefit need, including health, life, disability, and more. The benefits unit also provides technology solu tions and educational programs designed to address both compliance and employee participation.
McGowan Compliance Group is an advisory service offering a mix of technology solutions and other resources in support of our clients’ internal adminis tration needs (e.g., human resource compliance, benefit administration compliance, safety services).
The firm’s headquarters are in Indianapolis, and there are several satellite offices throughout Indiana for the 140 team members. McGowan serves clients all over the country as well as internationally.
We have been AWT members since 2004.
McGowan was named the 2017 AWT Supplier of the Year.
Michael Highum, CPCU–Partner, Risk Advisory; Clayton Highum, CIC–Risk Advisory; Josh Estelle, CIC–Partner, Benefits Group.
Walchem, IWAKI America Inc.
5 Boynton Road, Hopping Brook Park Holliston, MA 01746
(508) 429-1110
Website: www.walchem.com
Founded in 1974 as a manufacturer of analytic water treatment equipment and a distributor of chemical injection pumps, Walchem has grown to become a global provider of state-of-the-art water treatment controllers, sensors, and metering pumps. Iwaki began distribu tion of its products in North America in 1980 through Walchem Corp. By 1991, Iwaki and Walchem formed a joint venture company, Iwaki Walchem Inc., and manu facturing operations in the United States expanded. The merged businesses are known today as Iwaki America Inc.
Current Business
Acquired by Iwaki Co. Ltd. in 2008, Walchem is now a brand of Iwaki America and is sold in more than 100 countries worldwide. Walchem manufactures online analytical instruments and electronic metering pumps and provides solutions by integrating our instruments, sensors, fluid handling, and extensive remote data communications technologies. Iwaki America is respon sible for the company’s operations in the Americas and for developing and selling Walchem products worldwide. The Holliston, Massachusetts-based company, has oper ations in the United States, Argentina, and Brazil; sales offices throughout the Americas; and more than 100 sales channel partners.
In addition to Walchem, our subsidiaries include:
Iwaki Pumps—Magnetic-drive pumps for chemical processing and other critical applications. Iwaki Air—Air-operated double diaphragm pumps. Iwaki Aquatic—Aquatic housing systems for laboratory medical and toxicology research. Iwaki Sanwa—Pumps with 316 stainless steel construction for both high and low temperature applications.
Business Locations/Geographic Areas Served
Walchem products are designed and manufactured in Holliston and supported in more than 100 counties.
AWT Membership
Walchem has been a member of AWT for over 30 years.
Walchem, Iwaki America Inc. was recognized as the 2020 AWT Supplier of the Year.
John Miersma, Chairman, President, and CEO; Tom Marcone, Corporate VP Marketing; Jeff Hadley, Senior VP Walchem Sales and Business Development; Jeremy Brown, CPA, CFO; and Mark Pantazes, VP Walchem Technology.
AMSA, Inc.
4714 S. Garfield Road Auburn, MI 48611 (989) 662-0377 Website: www.amsainc.com
AMSA, Inc., was founded in 1996 in Midland, Michigan, by Dr. Attila Relenyi, following his resigna tion from Dow after 16 years, and Janice Shawl, upon seeing an opportunity to market decylthioethylamine (DTEA*) to small and medium-sized companies.
*DTEA is generic for this chemical composition name, which, in today’s internet, can be confused, but the chemical name is specific and exact.
The decylthioethylamine initial discovery and develop ment in the mid-1980s, led by Dr. Relenyi, was based on finding key molecule features using pattern recognition on over 180,000 compositions with test data relevant to our industry. AMSA has 18 current patents in biofilm control; algaecide control; and/or control of both biotic and abiotic sulfur deposit formation, including process of use, process of manufacture, and select compositions, both liquid and solid.
AMSA, Inc. is a specialty chemical manufacturer of custom chemistries that clean organic deposits in indus trial cooling water systems. AMSA BCP® chemistry is based on “designed molecules” that provide enhanced performance rather than simply blending raw materials into formulations. AMSA serves both the traditional cooling water market and the cooling water market in renewable geothermal power plants.
AMSA has two campuses: Auburn (headquarters) and Bay City, Michigan.
Reactions (chemical reactors) are run in quarterly campaigns in a facility a few hours from AMSA head quarters using all USA-sourced chemicals, with back integration and multiple sourcing overseas, if required.
AMSA exports to Southeast Asia, including Singapore, China, Taiwan, and the Philippines (power industry); the Middle East (Saudi Arabia); the European Union; the Americas; and Brazil; Mexico; Canada; and New Zealand and Australia.
AWT Involvement
AMSA has been a member of AWT since 1996 and is a long-time exhibitor. Our staff serve on the Business Resources and Cooling Committees.
AWT Awards
AMSA was named AWT’s 2009 Supplier of the Year.
Attila G. Relenyi, Ph.D., CEO and CTO; Janice K. Shawl, President and CFO; and Cindy Wallick, Controller.
Omya,
Inc. Cincinnati, OhioWhat prompted you to start volunteering with AWT?
When I started in the industry, I wanted to gain more expo sure to the major trends and evolutions within the industry as well as meet people who had a more established presence. With most of my career dedicated specifically to waste water treatment, Angela Pike suggested the Wastewater Subcommittee as a good opportunity to serve.
What has been the most rewarding thing about volunteering?
Making contributions that others can benefit from. When I reflect on all the helpful resources I use on a daily basis that other people spent time and effort creating, I feel like I am partially returning the favor by creating some resources for the industry myself.
How has volunteering improved your professional career?
By working more closely with others in the industry, I began to learn who had particularly strong expertise or connections in certain areas, which allowed me to broaden my resources within the industry. It also allowed me to showcase my strengths and become a resource to others in the community where I may be able to offer support.
Why would you encourage others to become a volunteer?
It is always hard to find time for tasks outside of our job responsibilities, but the routine and accountability associated with being part of a committee make it easier to allocate the time necessary to make meaningful contributions to the industry, and having the support of the organization and fellow committee members amplifies the efforts you put in.
Tell us about a current project you or your committee are working on?
One of the goals of the wastewater subcommittee was to increase the presence of wastewater-related articles in the Analyst. With my background in technical writing, I felt comfortable running with this initiative and have since submitted multiple articles for publication.
I’ve also recently been appointed to be AWT’s RTO liaison to the Water Environment Federation (WEF). The organization primarily consists of members in the North American munic ipal wastewater treatment market, but they show clear signs of wanting to continue to strengthen their presence in industrial wastewater as well as expand into other topics, including ones that overlap with AWT. On the contrary, AWT has a primary focus on heating and cooling but desires a strengthened position as a resource in industrial wastewater treatment as well. The expanding scopes of both AWT and WEF are leading to more overlap between the two organizations than ever before, creating a quality opportunity to collaborate, particularly in the indus trial wastewater space. The goals of this partnership are to unify efforts and resources surrounding industrial wastewater, increase AWT’s transparency into policy developments affecting the wastewater treatment industry, and foster increased awareness and engagement among the members of both organizations.
What is a past project that your committee produced that you feel has had the greatest impact on AWT and why?
I think the development of the wastewater treatment calcu lations tab in the AWT Calculations app has proven to be a great resource for improving the accuracy and efficiency of jar testing activities. I also think the updates to the Wastewater Treatment section of the Technical Reference and Training Manual more properly reflect the current status of the waste water treatment industry and allow for its continued utility as an excellent resource for wastewater treatment information.
What prompted you to obtain your CWT and when did you begin the process by taking the test?
Growing up in the industry working for my dad, I knew he had his CWT, which set the bar for me from the very begin ning. I started studying in earnest once the pandemic lock down hit our area and I had two things in abundance: time and the Technical Reference & Training Manual (TR&TM).
What advice would you give those thinking about taking the exam?
Start to go through the TR&TM well in advance of when you intend to take the exam. It will deeply inform your day-to-day work in the field and give you time to experi ence the information rather than just memorizing it.
What was the most difficult aspect of the exam?
The length of the exam is a true marathon event, and I run marathons, so the comparison is not one I make lightly.
How did you prepare for the test?
The TR&TM held 85% of the information I felt I needed to pass the exam. The rest came from holes uncovered by the practice exam.
Why do you feel this credential was important to have?
It's a way to demonstrate a high level of technical compe tence and expertise to your customers, your company, your peers, and even yourself.
How have you been able to utilize the expanded business connections you’ve made while volunteering?
What are the advantages of having the CWT designation?
Having passed the exam and earned my CWT, I feel like I can keep my chin up around my peers within the AWT community and at the same time I have a greater appreciation for just how much more there is to know.
How has your CWT improved your professional career?
Besides feeding a hunger for knowledge, it's given me confidence that I know more than a little what I'm talking about. I can take that confidence and make an impact with/for our customers.
What has been your greatest professional accomplishment?
It's not been the most financially rewarding part of our business, but I consider the operational improvements we've made with municipal customers to be a huge personal win.
What do you think are the most prominent issues facing the water industry today?
I think there's a lot of buzz around efficiency, but not enough of it directed well enough to make an impact. We have the tools to show our customers how to run efficiently, how to measure that efficiency, and track it for them if they don't do it themselves.
Certainly, a more expansive network delivers benefits on the business side, but almost more importantly, it makes being a part of our industry more fun. Being able to work with, serve with, and regularly interact with people you consider friends makes what we do more enjoyable.
The Pipeline and Hazardous Materials Safety Administration (PHMSA) under the Department of Transportation (DOT) has issued a final rule that amends the Hazardous Materials Regulations (HMR) to maintain alignment with international regulations and standards by adopting various amendments, including changes to proper shipping names, hazard classes, packing groups, special provisions, and packaging autho rizations. Additionally, PHMSA is amending the HMR to allow for better alignment with Transport Canada’s Transportation of Dangerous Goods Regulations. This rule became effective on August 25, 2022.
PHMSA expects that the adoption of the regulatory amendments in this final rule will facilitate transporta tion efficiency while maintaining the high safety stan dards currently achieved under the HMR. The admin istration also notes that the harmonization of the HMR with international consensus standards could reduce delays and interruptions of hazardous materials during transportation.
The following are some of the changes:
Hazardous Materials Table (HMT):
PHMSA is adding, revising, and/or removing certain proper shipping names, hazard classes, packing groups, special provisions, packaging authorizations, and bulk packaging.
PHMSA is removing the metal wall thickness require ments for certain metal intermediate bulk containers (IBCs) that have a capacity of 1,500 liters or less. Metal IBCs are currently the only type of IBCs for which there are minimum wall thickness requirements. This revision harmonizes the minimum wall thickness requirements for IBCs with the 21st revised edition of the UN Model Regulations.
PHMSA is extending the periodic inspection from five to 10 years for cylinders that are filled with hazardous materials described as “chemicals under pressure.”
PHMSA is amending the regulations to clarify that the exception permitting reduced size marking require ments are applicable to packages with either 5 L or less capacity, or those with a 5 kilogram or less net mass. The current HMR text states that the exception is applicable to packages with a maximum capacity of 5 kg or 5 L or less, rather than the maximum net mass, which is the more appropriate measure.
To read the final rule in its entirety, visit https://www. govinfo.gov/content/pkg/FR-2022-07-26/pdf/202215358.pdf.
Janet Kopenhaver is president of Eye on Washington and serves as the AWT Washington representative. She can be reached at (703) 528-6674 or janetk@eyeonwashington.com .
Traveling back from working in Australia on water treatment issues for the mining industry, I had a not-so-preferred seat in the middle of a wide body jet. Getting prepared for what I anticipated would be a very long 14-hour flight, I met my passenger to the left. He was an American traveling around Australia to play concerts with his rock band, but his greater success was writing and performing 62 songs used in television show episodes or as commercial jingles. To my right was a college-aged Irish women who was six months into backpacking around the world on her own.
As soon as we leveled out, the stories began passing through me from the left and right from two really fun people. The American talked about song lyrics he had written and TV show personalities he had met; the young Irish woman talked about sites she had seen and strangers she had befriended. In all, there were enough experiences had for a lifetime. After they had told some of their stories, I suggested, “Hey, I am an experienced, well-traveled water treater. Would you like to hear some good water treatment stories?” From my left I heard, “No.” From my right I heard, “No, not really.”
So, this episode of “Tales from the Waterside” is my chance to tell some of the stories that were omitted one day at 30,000 feet. The most fun ones, though, will be spoken, not written.
For me, as my years of water treatment experience start to add up, I realize that what I have seen, done, and heard—basically “been there, done that”— has had a much more lasting impact than reading the AWT Technical Reference and Training Manual (TR&TM) or the old Betz Handbook of Industrial Water Conditioning.
I tend to look at water treatment now as not repeating the mistakes that I have made in the past, comparing how water treatment systems are to how they should be, and evaluating all risks involved for successful outcomes based upon water quality and variability, operation and control, and equipment and design. I look to design for the 95% “most-of-the-time” scenario but anticipate and prepare for the 5% “out-of-control-time” when things have changed, are upset, or have basically gone south.
So, some of these are stories and memories that resulted due to failures on my part, immaturity, laziness, eager ness, or because I just had not yet been there or done that. They are in no particular order of value or impor tance, humor or concern, or interest.
Here are some stories I might have shared if my fellow passengers had expressed interest.
Early in my career, I had read about boiler inspections but had never participated in one to experience the confinement, heat, dirt, and knee-knocking movements. I was told to make sure the entry is safe, all blowdown lines blocked out, and that people were around. (The confined entry requirements now are much better than when I tried to kill myself on several occasions.) My boss and I entered a large field-erected coal-fired boiler for inspection. The other two boilers were still online. When someone performed a manual blowdown on one of the operating boilers and hot steam and water entered our mud drum, it was a race to see how fast we could crawl and escape through a very small hole.
Not learning as quickly as I should have, I once got stuck trying to get out of a large steam drum of a competitor’s
account when no one was in the boiler room. I eventually lost enough weight and was able to maneuver my way out. Never told anyone. Never got the account.
Hot process softeners were common in my early career, and they were often followed by hot zeolite softeners. I was young and thin, so there was no problem going into one to inspect the internals, even though it was still hot and steamy. But it was hard to climb out with the rope ladder laying against the side and you are exhausted from the heat. Helping hands dragged me out from that poor decision.
A customer’s facility manager once told me of a Lassie TV episode where Timmy was stuck in a drainage culvert with a big thunderstorm approaching, and Timmy yelled to Lassie to go get help. My customer was extremely claustrophobic and even had a hard time watching me inside a boiler. When I got stuck in a very tight steam drum, he screamed, “Run, Lassie, run!”
At the request of a client, I made a visit to a large chemical plant operating a new demineralizer system for its high-pressure boilers. The purpose was to deter mine why its new $1.5-million demineralizers were not producing water to the designed total dissolved solids (TDS). My boss was busy working on it, but all of this was quite new to me, being freshly out of college. While they were out in the water plant troubleshooting, I was reading the manual. I noticed that the specs called for water quality to be expressed in parts per million (ppm) TDS as sodium chloride (NaCl). Turns out, the company had won the bid because it (yes, I remember who it was) pulled a fast one by expressing TDS as sodium (Na) instead of NaCl. There was no problem in performance when we converted the water TDS of the effluent to NaCl. Lesson learned? Know your chemistry, conversions, conventions, and sneaks in the industry.
I was cleaning a slimed-up cooling tower containing lots of sludge at 5:00 am with a new client of mine. (Don’t ask what personal protective equipment [PPE] we used.) As we cleaned, he turned off his high-pres sure hose and said to me, I have four years of college. I replied, I have seven. “Just wondering out loud,” he said. Then we got back at it.
Feeding sulfuric acid into cooling towers for pH control is not uncommon, but it used to be much more common
than it is today. A colleague of mine working at a client site was working on the acid metering pump and the client asked me if he knew what he was doing. I said, “oh yeah, he does this all the time.” Just then, while still pressurized, the discharge tubing popped. His face showed the acid pot marks pretty much immediately, and his nice wind breaker jacket began showing the insulation inside.
My worst acid experience was when the acid line above me had come loose and was spilling down right onto me. I saw my smoking wet shoes not knowing why they were wet, and then looked up to catch acid in my face. I made it to the eyewash stand and washed for about 15 minutes, but then my clothes and shoes were pretty worthless, except my belt apparently, which someone stole while I was changing into some overalls.
I had business at some rendering plants or meat packers that also rendered. That smell is not so pleasant and tends to adhere quite well to a person. When I would come home to my apartment, my wife would “suggest” I change outside before coming indoors. For basket ball league, one time I had to go directly there. It was my best scoring night ever. No one wanted to guard a sweaty man who smelled like dead pig.
How fast does corrosion occur? A prospect was operating his boiler room with a hot water tank instead of a having a properly operating deaerator. This almost never works well, at least without a passivator or filming treatment chemistry. I put a coupon into the bottom of the tank using a retractable coupon holder, but then needed to pull it out to make sure I had it positioned correctly. Even with sulfite and a residual in the tank, the coupon showed significant corrosion after only 30 minutes.
A new client called me at home late one night. He could not keep his boilers from tripping off whenever they went onto high fire, and of course he blamed the chemicals. This time, the customer was right. Late at night, I learned that if you overdose polymer (in this case in the 300 ppm range), it becomes very surface active, causing the boiler water to prime with the site glass, filling and then emptying as the water line inverted. This is not the only place I have seen that happen.
On another bad night for me, a client called around midnight for a similar reason. All of the process and
heating boilers were foaming and carrying over. They had retubed a low-pressure heating boiler, and I provided boil-out chemical and procedures. Unfortunately, they did not close the steam isolation valve of the low-pressure boiler; it got cold that night; and it went into high fire and sent foaming boiler water out into the entire plant, contaminating all the steam and condensate system. I spent all night with boiler contractors draining and refilling. At 6:30 am, I had a very special meeting with the VP where I took some very large lumps. Luckily, later that day, my main contact at the plant stood up for me and said that I had told them that they needed to isolate the boiler when they did the boil-out. For all future boilouts anywhere, I made sure procedures and consequences were very clearly understood and agreed to.
Always know your water sources and chemical feed points. Do not rely on anyone without confirming on your own. Things can change. For a very large oppor tunity but very difficult water, lots of clarification jar studying was required to come up with a workable program. After three long days, I had a program that worked well. Then, I learned that my buckets of water samples contained a certain competitor’s coagulant. Can you say, wasted time?
I have always been a little suspicious that water company big brother is watching and has his spy network out there. When working for a water treatment company, I was sent a Sean Connery lookalike young water treater to work with me and gain some experience. I had a sales call set up one morning for 11:00 am, when I learned an emergency had come up and the prospect needed to change the meeting to after lunch. I asked “Sean” if he had any ideas for what we could do until the meeting. He responded, “Bowling?” So, I took him for lunch at a bowling alley. After our first round, when I looked over at him tucked away from me, he was talking into his pen, and said, “Open Channel D please, … you won’t believe what we’re doing now.” By the way, he left water treat ment shortly after that, but years later, I am still at it.
When a new client does not yet trust you or is just plain ornery, some people try to make them their friend, but some try to push them over the edge. With a very large RO install to use reclaimed water for boiler makeup, I experienced for the first time that aluminum in the water can cause very rapid loss of flux without much affecting
the differential pressures of any stage. As we were trying to determine the problem, aggressive and frequent RO clean-in-place (CIP) was required by us while the plant manager hovered with some unloving verbose. I knew that angrily and quickly dumping that entire bag of meta bisulfite by my colleague into the hot water of the CIP tank would clear the room, and soon the plant manager’s flight and choking cough had landed the intent.
Cooling towers and their sumps can be quite large and intriguing to effectively treat and monitor, often alluring some rather perilous perches. One day, when a board broke above a large sump at a client’s site, with one of my colleagues making a splash, a sign the next day had been strategically hung: “No Swimming Allowed.” Safe practices are kept front and center much more nowadays, as they should be.
I had a customer who was a really good basketball player, so we would play at lunchtime at a nearby college on my service days. He then suggested tennis, where I had the edge. The first time back after soundly beating him at two sets, he called me into his office, sat me down, and passed me a cartoon. It was two golfers walking off a course with the client saying to the supplier, “Well, that’s the hole, the match, and the account.” He was joking, but years later, I found out a big boss of mine was not so accepting after I beat him 6-0, 6-0, and my immediate boss asked me how stupid I was. Should the customer or boss always be right and always win?
These are some of my stories, but the best are still reserved for non-water treaters and airplane flights.
Dave Christophersen is owner of Dave Christophersen Consulting LLC and a senior consultant to AP TECH, based out of West Chester, Ohio. He has 45 years of experience in the water treatment industry, including managing water treatment programs for industrial sites for boilers, cooling systems, wastewater systems, and membranes. Having worked at Olin, Betz, Crown Solutions, and Veolia, Mr. Christophersen’s water treatment experience includes technologies for wastewater treatment, boiler water treatment and pretreatment, cooling water, and membrane technologies. He provides training, business, marketing, and technical support to the water treatment industry. Mr. Christophersen may be reached at christophersendave@gmail.com.
Many surprises can come up when overseeing care for a friend or loved one. One of the unexpected issues involves paying for the care a loved one might need and covering other expenses incurred when serving as a trustee or Power of Attorney (POA).
No matter the form of care that is needed, it is not cheap. According to the American Council on Aging (ACOA) (1), the national private-pay average for indi vidual nursing home rooms was $108,405/year, or $297/ day. A shared room was $94,900/year or $260/day. But those figures are not set in stone. ForbesHealth (2) reports an even higher range of $280 to $550/day, or $9,000 to $15,000/month. However, the Forbes article does reference the ACOA data as a worthwhile resource, and it should be noted that the ACOA presents cost figures
Statewide Averages*
State Private Room Daily Cost Yearly Cost
in regions of several states that exceed the average prices listed earlier. Table A provides a sample of statewide nursing home care price estimates based on ACOA data. Not all states are listed in the table. The aim of Table A is to show representative examples of costs in states in different parts of the of the nation. It is important to note that location, private or shared room, and type of care needed impact pricing. Also, within states, nursing home costs can vary based on location (e.g., urban, rural).
Assisted Living Assisted living is less expensive but can still cost tens of thousands per year. For example, data from AssistedLiving. com (3) for California shows a cost of more than $144,000/ year ($12,020/month) at the high end, and around $10,400 ($873/month) at the low end. The monthly cost for this form of care falls anywhere between these two extremes.
Shared Room Daily Cost Yearly Cost
Alabama $231 $84,315 $220 $80,118
Arkansas $220 $80,300 $200 $73,000
California $400 $146,000 $322 $117,530
Colorado $320 $116,709 $282 $102,810
Florida $317 $115,523 $285 $103,843
Illinois $235 $85,866 $206 $75,190
Kansas $224 $81,760 $207 $75,555
Louisiana $199 $72,719 $189 $69,113
Maryland $400 $146,000 $340 $124,100
Massachusetts $445 $162,425 $415 $151,475
Minnesota $430 $156,859 $381 $139,211
New York $435 $158,797 $420 $153,300
Ohio $270 $98,550 $240 $87,600
Texas $233 $85,107 $169 $61,503
Washington $344 $125,597 $310 $113,150
United States $297 $108,405 $260 $94,900
Source: Based on sample data from table at https://www.medicaidplanningassistance.org/. The full table includes data for different regions and urban areas within each state.
Assisted living can be anything from small cottages in a community or small apartments, to group homes in converted single-family homes. A common theme is that these facilities provide services (e.g., meals, assistance in toileting and bathing) for those not needing long-term care. The cost is affected by the types of services. In the previous paragraph, the high-end cost would be the price one might pay when receiving several services (e.g., bathing, dressing, toileting, dispensing of medicines, mobility assistance, etc.). In contrast, the low-end cost might represent a facility where the primary services are some meals and housekeeping.
When a loved one’s health precludes independent living, a third option is to bring the help to the residence where he/she lives. At the simple end, this can involve someone to help with cooking, cleaning, companionship, shop ping, and transportation to medical appointments. More involved care in the home could involve assistance with bathing and dressing. For those in greater need, care providers may be hired for a daytime shift, or even 24/7 care. The initial cost for assistance with the simple tasks can be around $25/hour. From there, the cost rises, based on the type of care providers and their training. For example, a registered nurse would be much more per hour.
In the case of home care, one would likely work with an agency that would place the caregivers. The value agencies provide is pre-screening of caregivers and the simplicity of being a one-stop service for the different care needs. However, there can be multiple business models within this approach. For example, when helping with my mom, we discovered a firm that would provide caregivers, but in this case, one would pay a placement fee to the agency, for example $20 for a three-hour shift, and then an hourly rate paid directly to the caregiver. In other cases, the care givers are direct employees of the agency.
Paying
Above, we have listed yearly costs in the six figures, which over time will diminish a life’s savings, and even tually take it all—even in the case of the careful saver. For the above types of care, private paying is expected. Of course, there are long-term care insurance policies that will help cover these costs, but with restrictions, based on the policy. The bottom line is that for many
families, they will eventually reach the point where the loved-one’s savings are gone and it is necessary to enter a government-run program called Medicaid, which will help qualified individuals to pay for their long-term care.
Much more could be written about the topics covered in the introduction of this article, but for the duration, Elizabeth Anderson, a Denver-area based attorney whose legal practice includes elder law, has graciously agreed to answer some questions from the Analyst about this important topic. Her answers follow.
The Analyst: What is Medicaid?
Elizabeth: Medicaid is a needs-based program. It is a joint state and federal program that will, in essence, “cover the rent” at an assisted living or skilled nursing facility. Medicaid can also pay for in-home health aides or community-based care.
The Analyst: How does one qualify to be on Medicaid and what are the requirements (financial and otherwise)? Is the application process simple, or is an outside professional needed?
Elizabeth: There are many types of Medicaid programs, and each program has its own requirement process. Qualifying for Medicaid Long-Term Care, the type of Medicaid that covers the cost of the care facility or in-home care for the elderly, can be a little difficult. To qualify for Medicaid Long-Term Care, a threepart test must be met. First, the applicant must have a medical need. If the applicant is over 65 and having difficulty with at least two activities of daily living, such as bathing, toileting, dressing, eating, transferring, and mobility, the person will likely qualify. Second, the applicant’s income must fall below a certain limit. Each of the 50 states has its own criteria, and these figures change each year. Medicaid uniformly, however, includes the same streams of income in this calculation: income from pensions, Social Security, and retirement accounts. Third, the applicant’s assets must fall below a certain limit. A single (unmarried) applicant can only own $2,000 of assets. If a married couple is applying, they can have combined assets of only $3,000. If only one spouse is applying for Medicaid, the applicant spouse can have $2,000 of assets and the healthy spouse can have $137,400. These figures are based on the 2022 figures for
the state of Colorado. Certain assets, such as a primary home, one vehicle, and prepaid cremation or funeral plans, are considered exempt assets.
The Analyst: If one is on Medicaid, what does Medicaid pay for? What will it not pay for? For example, if a nursing home costs $10,000/month, how much of that $10,000 is paid by Medicaid and how much by the patient?
Elizabeth: For nursing home Medicaid participants, nearly all of a participant's monthly income will be paid toward the cost of the nursing home care, and Medicaid will generally pick up the balance. Each state allows the Medicaid participant to retain approximately $30–$200 a month as a personal needs allowance.
The Analyst: Does someone on Medicaid have to requalify yearly?
Elizabeth: Yes. Medicaid eligibility does not automat ically get renewed. Each year, a renewal form must be completed with the required supporting documentation for proof of income and assets.
The Analyst: Is Medicaid only designed for older people in nursing homes or assisted living facilities? Or do they have programs for younger people as well?
Elizabeth: There are actually dozens of different types of Medicaid programs. For instance, there are special programs for children, adults under age 65, parents and caretaker relatives, pregnant women, SSI-eligible persons, seniors, and individuals with intellectual or developmental disabilities. Each program has different qualification requirements. While generally, the strictest qualification process is for assistance through the Medicaid Long-Term Care program, it is important to find out eligibility for the specific program you are enrolling in.
The Analyst: Will Medicaid pay for in-home care, or must one live in a care facility?
Elizabeth: Medicaid can pay for in-home care services, but there is typically a cap on how many hours of services or the number of visits a Medicaid participant is allowed each week. Once the level of care exceeds these limits, then a transition to a care facility may be necessitated.
The Analyst: What is the 5-year look-back rule?
Elizabeth: We typically encounter the 5-year look back rule when someone is trying to qualify for Medicaid Long-Term Care. Since this program has a resource limit as part of the eligibility criteria, Medicaid wants to ensure that Medicaid applicants are not simply giving their assets away in order to qualify. With this in mind, the applicant must disclose to Medicaid any gifts they have made in the past five years. Gifting includes assets that were sold under fair market value and assets that were transferred without fair consideration. If a gift was given in the past five years, a penalty may be applied. A penalty is simply a period of time that the applicant is ineligible. This means that, even though a person may qualify for Medicaid, Medicaid will not pay for care during the period of ineligibility, so the applicant or the applicant’s family must find the means to privately pay for care during the time period of ineligibility. This rule may appear harsh, but had those assets not been gifted, Medicaid would not have needed to pay for care.”
The Analyst: What is “spend down” and what does it affect?
Elizabeth: Generally, when we talk about spend down, this means that the individual is spending down all of their available assets in order to become eligible for Medicaid. For a single person, this may mean they are spending down their nonexempt assets to $2,000. If you are a couple applying for Medicaid, then they would need to spend down their nonexempt assets to $3,000.
The Analyst: How does it work? For example, if I gave my son $75,000 three years ago, and then needed to go into an assisted living facility or a nursing home and ran out of my own private pay money a year later, would that $75,000 gift impact my qualifying for Medicaid?
Elizabeth: Definitely. Since the gift was within the 5-year Medicaid lookback period, Medicaid would determine there is a period of ineligibility. This period of ineligibility is based on where you live and the average cost of care for your particular county. For instance, let’s say the average monthly cost of care in your area is $8,776 a month. Medicaid will state the penalty is $75,000 divided by $8,776, which is 8.55 months in which they would not pay for care. Your son would need
to “cure” this gift, i.e., he would need to pay the money back, to eliminate the penalty, or the applicant will need to find another means to pay for care during this period of ineligibility.
The Analyst: Are there “spousal protection” rules in the event one spouse is healthy but the other one must be admitted into a nursing home?
Elizabeth: Medicaid will look at both spouses’ assets to determine eligibility, but Medicaid does allow the non-applicant spouse, better known as the “community spouse,” to keep up to $137,400 in available resources. A portion of the applicant spouse’s income may be shifted to the community spouse in order to prevent spousal impoverishment. The community spouse is also entitled to any exempt assets, such as their primary home, one car, a prepaid cremation/funeral plan, and $1,500 cash value life insurance.
The Analyst: Can one still own a house and be on Medicaid?
Elizabeth: Yes, a home is generally considered an exempt asset, but the Medicaid applicant must live in the home or have an “intent to return,” and the home’s equity interest must be less than $636,000. If a commu nity spouse lives in the home, these criteria do not apply, and the home is considered exempt. Real estate can be tricky, though. If the community spouse sells the home, moves into a care facility, or dies, the home could become subject to estate recovery after the Medicaid participant dies.
The Analyst: After someone dies, can Medicaid make a claim to all remaining assets, or do they follow a formula? If there is real estate or, for example, valuable collectibles (e.g., coins, antiques), could Medicaid claim part or all of it?
Elizabeth: Medicaid allows for estate recovery. Medicaid is sort of like a loan. If the Medicaid recipient has the means to pay back Medicaid, then Medicaid has the right to collect. Generally, when an individual is on Medicaid, they have spent down their assets. The only asset left to collect from is usually the home. If the home is no longer considered exempt, Medicaid can place a lien on the property in order to be paid back. Medicaid can only recoup what it spent, so if there is a balance
remaining after Medicaid is paid back, those excess funds will pass to the next of kin.
The Analyst: The bottom line is that I want to be able to leave some type of inheritance to my family. How can I do so legally and avoid Medicaid’s requirements of a maximum of $2,000 in assets?
Elizabeth: There are a few tools we use in estate plan ning to shield assets from long-term care. Those tools work best when we have the luxury of time. We can gift money or place funds into various types of irrevocable trusts if we can wait more than five years to apply for Medicaid. As long as the asset is gifted or placed in an asset protected trust outside of the five-year lookback period, the person who created the trust will not be penalized for those gifts. If a client cannot wait five years to apply for assistance, then we may need to look at other tools, such as life care agreements, Medicaid exempt annuities, and irrevocable funeral/cremation accounts.
The Analyst: What happens if someone on Medicaid inherits money or real estate? Do they get kicked off Medicaid?
Elizabeth: They can definitely get kicked off if those inherited funds are not spent down below the Medicaid threshold by the end of the month the funds were received. This is why an appropriate estate plan is so important. If you want to leave an inheritance to anyone who is currently eligible for Medicaid or is likely to become eligible and is under the age of 65, it is imper ative that they do not inherit these funds outright. Through the use of a Supplemental (Special) Needs Trust, an individual can inherit and remain eligible for their government assistance programs. If a Supplemental Needs Trust is not created, then, typically, the Medicaid participant is kicked off of their benefits, and they will be forced to spend down.
The Analyst: Are there any useful websites or books about Medicaid that you would recommend?
Elizabeth: Unfortunately, most websites are too general to provide specific guidance and, as the Medicaid thresholds change yearly, many resource books become quickly outdated. With this in mind, I recommend you
go directly to the source. Check out your state’s local Medicaid website. They are full of helpful information.
The Analyst: Thank you for your time. Is there anything you would like to add to our conversation?
Elizabeth: Don’t be afraid to ask for help. Medicaid is complicated, and there are many rules to consider. This is especially true if you are contemplating protecting assets from long-term care. Consult a local Medicaid eligibility specialist or attorney who specializes in this field.”
1. ACOA (accessed June 2022). “2021 Nursing Home Costs by State and Region,” American Council on Aging, www.medicaidplanningassistance.org.
2. Wigand, M. (June 24, 2022). “How Much Do Nursing Homes Cost?” ForbesHealth, www.forbes.com/health/healthy-aging/how-much-do-nurs ing-homes-cost/#scrollto_nursing_home_costs_and_expenses_section
3. AssistedLiving.com (accessed June 2022). “What Is the Cost of Assisted Living?” A Place for Mom Inc., New York, New York.
The content of this article is based on the authors’ personal experiences and/or professional training. It is not intended to be legal advice. Readers with questions should seek the advice of a licensed attorney to address their specific situation.
Beyond Water… is a new column for the Analyst to address issues that members of AWT face in addition to their important work in the water treatment business. If you have an idea for an article, please feel free to send your suggestion to Mike Henley at mdhenleywater@gmail.com. We welcome your input.
Elizabeth A. Anderson, Esq., is an attorney specializing in estate planning, business planning, special needs planning, and elder law. She is a partner of the Law Network, P.C., a trusts, estates, and business planning law firm in Metro Denver. Ms. Anderson started her legal career working for the New York State Appellate Court. While there, she represented individuals with mental illness, intellectual and developmental disabilities, and the elderly in a variety of court proceedings, including Guardianships and Conservatorships. When she is not working or volunteering, she enjoys time with her husband and their two young sons. Her family loves adventure, and you will often find them hiking, skiing, or travelling. Ms. Anderson may be contacted at elizabeth@coloradoestateplanners.com .
Mike Henley provides consulting services through MD Henley & Associates and serves as technical editor of the Analyst. He formerly was editor of Ultrapure Water Journal for 27 years and has been active in several aspects of water treatment and the associated businesses for more than 30 years. Mr. Henley’s background includes helping with the organization of the technical programs at more than 60 UPW conferences, including Water Executive Forums.
©2022, Elizabeth A. Anderson, The Law Network, P.C. ©2022, MD Henley & Associates.
The purpose of this article is to review methods for monitoring corrosion in industrial water systems. The emphasis is on higher purity water systems such as are used in process water in microelectronics, pharmaceu ticals, and medical devices. These are important appli cations for middle market situations. The requirements for these and related manufacturing are very stringent. Consequently, the importance of ever more sensitive analytical methods increases. Wet chemistry and many instrumental techniques are simply not up to the task of ensuring water quality of the necessary purity.
Most of the methods discussed in this review are more advanced than wet chemistry and coupons, or even continuous corrosion rate meters. Technology has brought the cost of these methods down so that they are within reach of small water treatment companies, and expert systems software has made their execution and interpretation accessible to the typical water treat ment technologist. In addition, where it is impractical to acquire these capabilities, contract laboratories often can provide the capability and expertise to support the water treater’s needs.
While most of the methods discussed are primarily intended for high-purity waters, two methods (EIS and FTIR-ATR, defined below) are applicable to all water treatment situations, from cooling and boiler water to high-purity process water. Each method is briefly described, including what it does, what information it provides, comparisons of sensitivity and dynamic range, and pros and cons of its use. Industrial cooling systems are so full of contaminants that extremely high sensitivity is superfluous; parts per million (ppm) levels are usually sufficient. But in pharmaceutical systems, medical devices, and chip manufacture, these methods are indispensable. For example, as line widths in inte grated circuits get smaller and smaller, contaminants in the low-parts per billion (ppb) or mid-parts per trillion
(ppt) range become important. Methods described here are ion chromatography (IC), Fourier transform infra red-attenuated total reflectance (FTIR-ATR), X-ray fluorescence (XRF), X-ray diffraction (XRD), electro chemical impedance spectroscopy (EIS), and anodic stripping voltammetry (ASV). Older, more familiar methods, such as linear polarization or Tafel polariza tion, have been extensively covered for many years, so they are not included here.
The detailed discussion of each of these methods will be the subject of future articles where a more in-depth understanding will aid in method selection by the technologist. The methods are classified as liquid and surface, and each classification is divided as analytical or mechanistic.
These methods include IC, EIS, and ASV. Only EIS is mechanistic.
This method is for ultra-low concentrations of metal ions and is applicable mainly to microelectronics and medical device manufacturing. It has a sensitivity in the low-ppt range and is applicable to metal ions of atomic number greater than sodium. The equipment for this technique is available as a turnkey system and at a cost of around $25,000.
In this technique, a measured volume of the analyte is introduced into a cell where the anode is a mercury pool. The solution is vigorously stirred while maintaining a cathodic potential where all the metal ions of interest are reduced to the metallic state. The metal atoms dissolve in the mercury but remain at the surface, as diffusion into the mercury bulk is very slow. After the metal ions are exhaustively reduced, the voltage is scanned in the anodic direction using a ramp signal. As the voltage
reaches the potential of oxidation for a given species, there will be a current transient, and the area under the curve will correspond to the total amount of that species. The integrated current is the total charge, the total charge is related by moles of metal = Q/F, and Q=∫idT. The concentration can be calculated as shown in Equation 1.
∫idT x at. Wt. /F/volume of analyte = Concentration Eq. 1
Where:
F is the Faraday constant = 96,485 coulombs per mole.
The potential of the transient corresponds to the revers ible potential for that metal when corrected for the reference potential.
Figure 1 shows a typical ASV trace for multi metals.
Electrochemical Impedance Spectroscopy
EIS involves passing a low amplitude AC current through the cell at various frequencies, from less than 1 Hertz (Hz) to more than 10,000 Hz. The output will be an attenuated voltage but also a phase shift. The input signal is sinusoidal as is the output, but there will gener ally be a phase shift between the input and output. For example, when the input signal is at 90 degrees (i.e., a maximum), the output signal may be at 0 degrees, or 45 degrees or any value from 0 to 360 degrees. Accordingly, a phase lock detector is needed for the instrumentation.
-1.3
Ca+2 deposition potential from -1.2 to 2.4 V potential V vs Ag/AgCl
Anions and cations are analyzed separately on different columns containing either anion or cation exchange resins. The sample is injected into a port, and the ions are eluted with an appropriate electrolyte optimized to provide separation of ions. The detector is based on conductivity. Separation is achieved due to the relative affinity of each ion for the resin in that eluent.
Here is the basis for mechanistic interpretation. Imagine a box containing a circuit composed of resistors, capacitor,s and inductors in various serial and parallel configurations. If you pass a DC current through the box, all you will be able to measure is the equivalent resistance of the circuit. But, if an AC current is passed through the box with amplitude and phase shift measurement, and the signal frequency is scanned over some range, you can in principle determine the circuit architecture and the value of each component and its resistance, capacitance, and inductance. Some contributors to corroding surface behavior will involve diffusional elements. This too can be measured, and the frequency (i.e., the corrosion rate) where diffusion takes over as the rate-determining step can be observed.
A corroding interface is analogous to a circuit with resistive, capacitive, inductive, and diffusional compo nents. For example, a surface film of calcium carbonate is equivalent to a capacitor in parallel with a resistance (Rp,), which is the polarization resistance. The thicker the film, in general, the lower the capacitance. By measuring film capacitance over time, one can tell if the film is stable or is degrading or growing too thick. It is easy to see that this is a powerful tool.
Instrumentation and expert system software for exam ination are readily available in the $25,000 range.
However, interpretation of experimental results requires skills above a layman’s capabilities. Figure 2 illustrates a Randles cell of a corroding interface, and its imped ance behavior—both in phase (real) and out-of-phase (imaginary) components. The Randles cell is simply the electronic equivalent of the simplest example of a corroding interface. It comprises a solution resistance in series with a parallel polarization resistance and a film capacitance. It reflects the fact that the current has two pathways: corrosion current and capacitive film charging.
[CaCO₃]), which has the following crystal structures (calcite and aragonite), as shown in Figure 3.
model
plot
Figure 2: Randles cell of a corroding interface (a) impedance plot, imaginary (out of phase) component versus real (in-phase) component at various frequencies (b). 0 50 100 150 100
Here, solution resistance is in series with a parallel polar ization resistance and double layer capacitance. This is the simplest corrosion cell. Note that the corrosion rate is determined by measuring Rp and applying the Stern-Geary Equation for linear polarization. Note also that solution resistance (Rs) is directly measured and can be factored out. Typical corrosion rate meters do not compensate for solution resistance, so in low-conductivity waters, a linear polariza tion corrosion rate meter will measure the solution resistance primarily, and badly underestimate the actual corrosion rate. If Rs >>> Rp, then the measured resistance is Rs + Rp ~ Rs .
XRD and XRF are analytical, while FTIR-ATR is primarily mechanistic.
This technique involves identification of ionic solids by means of X-ray diffraction. Each crystalline solid has a regular spacing of ions (e.g., calcium carbonate
Ghkl
Θ Β Θ Β
Figure 3: Aragonite and calcite crystal structures. A O B
Incident plane wave Scattered plane wave dhkl (hkl) lattice planes
Θ Β Θ Β Θ Β Θ Β
Source: Figure in Practical Electron Microscopy and Database, an online book (https://www.globalsino.com/EM/).
If you have ever driven past a corn field, you will see that regularly spaced rows can be observed from different angles and that the spacing between the rows at different angles is different also. The spacing between the rows of atomic crystals is on the order of the wavelength of X-rays. The following diagram shows how monochromatic X-rays behave when the angle that the beam makes with the crystal leads to constructive interference (Figure 4).
Figure 4: Monochromatic X-ray behavior that occurs when a crystal interferes constructively.
Aragonite (a) (c) (b) (d)
Calcite
Source: Soldati, A.; Dorrit, J.; Glatzel, P.; Swarbrick, J.C.; Geck, L. (2016), www.esrf.eu/home/news/spotlight/content-news/spotlight/spotlight263.html.
The d-spacing between successive parallel planes of the crystal is calculated as n λ =2dsin(θ), where λ is the wave length of the X-ray beam, n is an integer, and θ is the angle between the plane and the normal to the plane, as shown in the diagram.
The distance AOB is the difference in the path length of X-rays scattering off two adjacent rows. If that path length, =2d sin(θ), is equal to an integral number of wavelengths, then the scattering is constructive; any other angle results in destructive interference. The angle θ, which coherently scatters the X-ray to give an image, is known as the Bragg angle. Every ionic species has a “fingerprint” of Bragg angles and intensities, and there are catalogs of Bragg angles and intensities for thou sands of ionic crystals (this one is free: http://www. crystallography.net/cod/ ). In this way, the species can be identified. Mixtures can also be identified by deter mining the fingerprint of the dominant species from the pattern; what is left is due to the other species.
Imagine two corn farmers whose seeding machines have different spacings. The resulting corn fields will look different from any angle. By measuring the spacings between rows at different angles, one can tell if the field belongs to Farmer Jones or to Old MacDonald!
This is a nondestructive method for determining atomic species (elemental analysis as opposed to molecular species). The principle of XRF is that high-energy X-rays can eject inner shell electrons from an atom, as opposed to valence shell electrons, which are ejected by lower energy excitations, such as heat in visible atomic absorp tion/emission. Ejecting an inner shell electron leaves a “hole” in the atomic electron configuration, and that hole is then filled by an electron from a lower energy shell “falling” into that hole with the emission of an X-ray photon. That photon will have energy (hν) equal to the difference between the hole energy level and the electron energy of the relaxing electron shell. Characteristically, that relaxation is delayed, leading to an extended emission process, hence fluorescence. Also, the emitted photon is necessarily of lower energy (longer wavelength) than the excitation photon.
The emission lines are characteristic of each atomic species. However, the spectra can be complex due to the presence of other elements.
Previously, the technique required complex equipment that was only found in laboratory contexts. But today XRF “guns” are readily available in the $30,000 range. These units can be used in the field on a wide variety
of samples without sample preparation. They provide a real-time output of the atomic composition of a sample by type and atomic percentage.
In principle, one of these devices can be used in a plant to determine alloy composition of materials, chemical analysis of liquids, contamination of dirt or fuel, coupon films, etc. For example, heavy metal composition of coal or fuel oil, extent and distribution of toxic elements from an emitter such as a smokestack, verification of alloy composition. The possibilities are endless. Even a small local water treater can afford to own one of these devices, and they are powerful tools for monitoring and surveying.
This is a somewhat exotic technique combining two different processes and is applicable to the study of surface films, such as gamma-iron oxide versus magnetite; cupric oxide; organic surfactants; or deposited films such as iron phosphate, calcium phosphate, or calcium carbonate.
Chemical bonds (not ionic bonds, however) vibrate at characteristic frequencies that typically lie in the infrared portion of the electromagnetic spectrum (300 Gigahertz [GHz] to 400 Terahertz [THz]), and so can absorb that radiation. If a beam of infrared radiation is passed through a sample, some of that radiation will be absorbed at char acteristic frequencies (equivalent to wavelengths, λ , and wavenumbers, cm-1). The resulting spectra can be inter preted as arising from certain characteristic bonds such as C-H, N-H, C-N, C=C, C=O, C=N, etc.
A complex waveform can be decomposed to a superpo sition of sine waves of varying amplitude, frequency, and phase. Figure 5 shows an example of this superposition. The Fourier transform transforms the signal from the time domain (x-axis on the left) to the frequency domain (x-axis on the right). An associated transform transforms the signal from the time domain to the phase domain (not shown below).
Using this technique, a pulsed signal can be repeat edly passed through a sample to yield an output that is summed. The signal-to-noise ratio increases with the square root of the number of scans so that after 100 scans,
the signal-to-noise ratio is 10 times greater than for a single scan (100 0.5 = 10); after 100,000 scans, the signalto-noise ratio is 100,000 0.5 = 316. The summed signal, which is in the time domain, is then decomposed to the frequency domain using the Fourier transform mathe matics. Pulses are typically less than one second so that thousands of spectra can be accumulated in a short period of time. Very weak single scan spectra can thus be ampli fied to very strong spectra. Hence, the spectra of very thin films of some substances can be obtained at good signalto-noise using this technique.
In this technique, a special crystal plate is clamped tightly to a surface, for example a corrosion coupon, The crystal transmits infrared radiation with minimal attenuation. The geometry of the crystal allows multiple passes of the beam through the sample. Each internal reflection leads to partial absorption of the infrared signal by the surface film on the sample. The penetration of the infrared beam into the sample is small so that only surface films are sampled, not bulk material.
In Figure 6, the angle of incidence (normal to the beveled edge of the ATR crystal) and the crystal thick ness and length produces 6 beam absorptions per side for each Infrared pulse. So, after 100,000 pulses the signalto-noise is equal to 1,200,000 0.5 = 1,095. However, even more importantly, only the film at the surface is being analyzed to the exclusion of other contaminants.
Consider trying to investigate the behavior of a tolyltri azole film on copper under various water chemistries. The FTIR-ATR method is ideal for this type of study. And, when combined with EIS studies, a detailed picture of the inhibition of copper corrosion by tolyltri azole can be elucidated.
2.2.8 Prohibited Organization. Any Water Treatment Company (WTC) that has, in the aggregate, more than one hundred fifty (150) full-time employees in the water treatment division or annual gross revenues from a primary water treatment operation that is greater than $30M US. Sustaining Members are exempt from this provision.
3. Chairing any AWT committee
These techniques are not commonly considered by typical water treaters and contribute little to ordinary industrial water treatment business. But increasingly, some industrial water applications require very sophisti cated monitoring and investigational techniques. This is especially true of microelectronics, medical devices, and medical appliance production industries. Also, hospitals and clinics can require the application of sophisticated techniques for critical systems.
Rationale
AWT small business owners would gain access to a wider network both domestically and abroad. New participants and their participation would enrich the value of the AWT community. There are many talented individuals who could contribute to the talent pool, and thereby increase our collective intellectual capital. Individual membership would help AWT gain a greater international footprint.
Even if the water treatment company does not possess the means or the technical capability to utilize these techniques, it should be aware of the various investi gational techniques because they can be subbed out to various commercial laboratory suppliers if the need arises. After all, the primary responsibility of a water treatment provider is to supply whatever expertise may be needed to support the service program at a given end-user.
This category would be restricted from:
1. Voting in AWT elections.
2. Sitting on the board of directors
Uniphos 2020.pdf 1 4/23/2020 3:57:49 PM
4. Participating in all “business owner only” functions, including the business resources section of the website.
They would get:
Orin Hollander, Ph.D., has a B.A. in chemistry from Northwestern University and a doctorate in chemistry from The Ohio State University. He worked for 16 years in the water treatment industry and for 26 years as president of Holland Technologies, a consulting and engineering firm serving water treatment companies and end-users.
1. Access to member educational resources
2. Member pricing for all events 3. Ability to participate in committees, but not chair
4. Greater connection to our community, but not any decision-making control
To view all FAQs on these ballot measures as well as learn more about the voting process, please visit https:// www.awt.org/members-section/amplify-awt.
A US-based company helping North American water treatment chemical companies, blenders, and distributors. Our technical representatives have more than 25 years experience in water treatment chemicals.
Uniphos, Inc. 1011 West Lake Street Suite 210 Oak Park, IL 60301
Phone: 708 445-1294 • Fax: 708 445-1394 • Email: gcollias.uniphos@sbcglobal.net
Note: The following discussions come from the Industrial Water Treatment interest group on LinkedIn.
Question of the Week What's in your toolbox or test kit that some people may not think about including in theirs?
Steve: A thumb drive. To extract data from a controller that is not connected to the internet.
Dennis: Most don't have a magnetic stirrer.
Steve: Camphor. I have always used camphor shavings to look for oil in condensate, boiler water or leaking heat exchangers. In clean water, camphor shavings will actually spin on the surface, with the slightest amount of oil it will stop spinning immediately. It is fun to show a client a beaker with clean water, put shavings in and see them dance around, then put your finger in (skin oil) and watch the shavings stop. I have identified many, many process leaks this way.
Seth: Scratch paper so you can map out systems at customer sites. The more I knew about an individual system, the easier it was to service it.
Jeff: A nice, bright head lamp. I have one on my hard hat and it really helps in those luxurious boiler rooms we all spend our time in. Also, may be obvious, but tubing, foot valves, weights and injection quills. Nothing kills productivity more than having to stop back at a custom er's facility to fix a leaking pump. Much more efficient to fix while onsite the first time and drive value to your customer by being able to react quickly.
Allen: A 47-mm filter holder and luer syringe "pump" with test filter circles from 0.45 to 30-micrometers (µm) to test for filtration requirement. Also carry an ultra filtration (UF) test module and deionized (DI) water dispenser to create sample dilutions.
Todd: I thought that everyone was only given a vice grips, strap wrench, duct tape and an extra-long Philips screwdriver for tools to use. Jokes aside, I always carried a crossover cable for connecting the laptop to PLCs. A small storage container that had odds and ends that one always forgets such as batteries for instruments or for memory backup, hose clamps, O-rings, shark bites, extra coupon holders, Teflon tape, fuses. Another container with various sized tube fitting. Lab equipment included a rubber policeman, a lab spatula, and 40-milliliter (mL) sample vials. Almost forgot the Fluke multimeter and a signal generator.
Narayanan: Toolbox: Feeler gauge to check clearance of nozzle/strainer inside a filter.
William: Water pressure gauge with fittings! How many times have you struggled with an intermittent issue only to discover nobody actually checked the incoming water pressure on the 20th floor and the real issue was the buildings booster pump.
Maxim: From now on, chewing gum will follow me on softener repair day! This trick saved me a lot of frustra tion while repairing a softener head! Long story short, the chewing gum is being use to hold the screw in the socket of a ratchet!
Question of the Week: Should the dechlorination point be before or after a reverse osmosis prefilter?
Todd: That is an “it depends” type of question. I have seen both. Some people say that it will help with chem ical mixing if it is before. I have also seen it after because the lack of chlorine in the water allowed for bio growth downstream of the sulfite-injection point.
Abilash: Would prefer after the prefilters as a bit of chlo rine prevents microbial growth on the filter elements. However, it should be before antiscalant dosing.
Tom: After the prefilter, before with a static mixer before the RO Main pump. I also like a constant feed chem pump (like the Blue White CD1 dual diaphragm or peristaltic) versus a pulsed pump.
The reason I like the feed after the prefilter is that we are only knocking down "surviving chemistry.” Prefilters are bug farms over time, with tons of nutrients. They will help consume the excess chlorine (effectively whacking bio growth), leaving less to treat on the RO feed side.
That said, always have ORP (oxygen reduction potential) on the RO feed with an alarm/system shut down when it goes above acceptable levels. Rule of thumb is we get 1,000 total ppm (parts per million) hours of chlorine exposure before the membranes are complete toast....so don't waste it on bad feeds.
Narayanan: Dear Mr. James, Good evening. Dechlorination done after prefilters (ultrafilters or sand filters or automatic self-cleaning filters) to prevent microbial fouling, increases the life of filters and sends the desired quality of feed water to the RO membrane. But, before a micron cartridge filter (5 µm), dechlori nation chemicals like SBS (sodium bisulfite), SMBS (sodium meta bi-sulfite) and the dosing tank contains some undissolved fine silts and fine particles that have to be filtered by a 5-µm filter (MCF) before the RO membrane to prevent fouling of RO membrane. Activated carbon filters are also used to dechlorinate chlorine, which is usually installed after sand filters.
Is "Everything looks good!" an appropriate summary on a Field Service Report? Why or why not?
Brian: Absolutely not. That’s the definition of complacency.
Mark: A shark also “looks” good behind the glass. Look versus Test …run the numbers and show me the data!
Robert: Use of subjective adjectives in any technical report is generally frowned upon. "The application is promising" is not something you put in a risk report when you ask for a $10-MM investment, right?
Jon: Screams drive by water treatment!
Daniel: If your customer, let's say a beverage plant, for instance, goes through an audit that will get flagged.
Laith: Possibly the pinnacle of account management if the statement is true.
John: This comment drove me crazy as a division manager! When I saw it, I scheduled an audit the next scheduled service visit and would typically give the rep a new review, finding many opportunities for improvement!
Michael: Hard to say. I've never used it. Is this account in a mythical paradise?
Des: Good morning, James. Must always be qualified “at the time of sampling”. Murphy is alive and well and his law on water sampling still applies. “Upsets occur after sampling— never before or during.”
Kevin: Yes! And please also tell me any of the locations where you find that lol. Easy pickings. Laziness is so shocking to me in this industry at times. Favorite thing to see on a competitor's report!
How long does the oxygen scavenger have to be turned off before conducting dissolved oxygen testing on boiler feedwater to determine deaerator performance?
Patrick: Calculate the hold time in the feedwater tank; based on capacity and the BFW pump. You then turn off the pump and wait the time for the tank to completely “turn over.” From there, I suggest using the Holy Trinity rule: Rinse three times— 3 x for sample rinse, 3 x for drum rinse outs… For example, the tank takes 20 minutes to completely turn over. Turn off the sulfite and in 20 minutes, you should mostly clear. Then wait 3 x 20 min more. If you wait too long, you risk accelerated oxygen attack.
How often should various components of your test kit be calibrated (e.g., conductivity meter, pH meter, colorimeter)?
Chris: I think an important addition to this discussion is that two-point calibrations should always be used and that for best practices, the standards should “bracket” the actual measure ments. pH meters measuring cooling waters from, say, 7.5 to 9.2 should use 7 and 10 stan dards. Conductivity meters measuring pure waters and using a single 3,000 micromhos standard are probably not going to give good results at these low levels. Handheld PTSA and fluorescein meters should be calibrated daily; continuous analyzers should be checked monthly, using DI water and a calibration stan dard above set point.
Frank: The smart aleck answer is “RTFM,” (Read the Free Manual). The owner’s manu al(s) usually states at least daily for pH and less often necessary for conductivity. Most of the folks at the AWT training tell me they calibrate pH daily or weekly and conductivity weekly or monthly. Checks against known standards on all testing meters and kits is a great idea. Especially if you notice any inconsistent results. Great topic.
Catherine: It depends on usage and specifications of the meter, but in general, colorimeters should have a cali bration check once a year. For traditional pH meters and conductivity meters, they should be calibrated as often as is practical but definitely before big changes in measure ment ranges. For digital probes, the length of time between calibration can be increased but users should be mindful of the waters they are testing, particularly taking into account residues that could "contaminate the probe" and like traditional meters, jumping between systems with very different ranges can effect calibration.
Moderator James McDonald, PE, CWT, is a director of technology & marketing with Chem-Aqua. He holds an M.S. in chemical engineering and is a Ray Baum Memorial Water Technologist of the Year award winner (2013). Mr. McDonald also chairs the Association of Water Technologies (AWT) Technical Committee. Mr. McDonald can be reached at James.McDonald@chemaqua.com .
Wastewater Treatment: DAF Innovation
The T²-Max® DAF Thickener handles high mixed solids flows without sacrificing separation performance.
The HD²XLRator® DAF design encompasses the full array of newly advanced technological innovations.
The Nx²JEM® DAF utilizes key hydraulic flow and laminar engineering principals to achieve high volume separation.
9268 www.pewe
As an early-career leader, one of the challenges you’ll inevitably face is the moment you realize that someone on your team is struggling to do something you’ve asked. Some may be willing to acknowledge their need for help and readily ask for it. Others may not, instead frantically searching the internet for articles or videos for guidance on how to approach the task.
It’s common for newer leaders to make assumptions about what their team can do, giving assignments without fully vetting whether someone has the skill, knowledge, or experience to succeed. Rather than leaving things to chance, effective leaders learn to be good teachers in moments when team members have the confidence and humility to ask, “Can you show me how?”
If you want to be an inspired teacher to the up-andcoming professionals you’re charged with leading, here’s what you can do.
Not everyone learns the same way. Some people need extensive knowledge and preparation to build their confidence before tackling a new task, while others prefer to dive in right away and learn through trial and error. Some people learn well in groups, while others prefer the privacy to learn on their own. There’s no right way to learn, but if you know what your team members prefer, you can tailor your approach to each individual when it’s time to offer guidance.
Great teachers know that learning is not a consequence of teaching; it’s a consequence of thinking. As you step into the role of actively teaching, begin by asking openended questions to draw out the specific challenge the person is facing. Are there aspects of the task where they can apply relevant experience? What skills have they previously developed that they can use right now? Help them make those connections to build up their confidence.
Some people may be hesitant to tackle a task due to a fear of failure. If you sense this is the case, rather than offering reassurance, ask questions to draw out their deeper angst. Help them discover that the nightmare scenario playing out in their head is highly unlikely. Use probing questions to help them reason their own way through a learning challenge, such as: “What’s the worst-case scenario? What’s the best-case scenario?”
Letting someone know that you struggled to learn the skill you’re now teaching them can sometimes be comforting. It eases the pressure people may feel to “look good” in front of the boss. But remember to stay empathic with your comparison — keep in mind that your struggles are in the past while theirs are current. Be sure that your comparison doesn’t inadvertently dismiss the real pressure someone is feeling.
You can approach a situation compassionately by saying something like, “I know this is hard, and the fact that I’m here probably makes it harder. Would it help to hear an experience I had struggling to learn something similar, and how I got through it?”
By asking permission to share your story, you demon strate care, and allow them to hear you in a way that suits their situation. You can finish by saying something like, “My intent isn’t to make an erroneous comparison of my experience to yours or imply that my example is worth following. You need to find a way through this that works best for you. I just wanted you to know that you aren’t alone in the challenge, and having struggled with this myself, I’m especially sympathetic to what you’re going through. I’d like to support you in a way that you’d find useful.”
Sometimes it’s helpful to demonstrate for learners how something is done. Always check in with your learner first by asking, “Would it be helpful for me to demon strate this for you?”
Be sure that you’re not conveying: “You should do this exactly the way I do it.” Demonstrations of a new skill should enable the learner to bolster their own approach, not simply mimic the demonstrator.
After you offer a demonstration, ask your learner: “What did you see that was helpful?” This gives them a chance to focus on specific things they can incorporate into their approach.
Once you’ve given someone “a lesson,” they may be more sensitive to your scrutiny as they practice mastering their new skill or task. Rather than letting their hypervigilance run amok, set expectations about how and when your next observation of their performance will happen. For example, if someone is working on their presentation skills, you don’t want them thinking that every time they present, they’ll be evaluated. Ask your learner, “Why don’t you let me know when you’re ready for me to assess your progress,” so they feel more in control of their ongoing learning.
Then, having observed them, begin your conversation with their reflections. Ask: “How did you feel that went? What did you feel went well? What would you do differ ently?” These questions will give you insight into how self-aware they are as a learner, and whether they tend to be overly harsh or overly lenient with themselves.
Finally, note one or two things you felt were particularly effective, and one area where you have specific ideas on how they can get even better. Always close by affirming their commitment and progress as a learner, noting clear evidence of progress.
If the task you’re asking someone to take on has a partic ular sense of urgency, you’ll understandably feel a sense of impatience, even frustration, as your learner works to learn and apply new skills in real time.
It’s essential that you have realistic expectations and that you don’t signal disappointment or frustration, as this risks arresting your learner’s progress and confidence. They will likely be even harder on themselves, and your unrealistic expectations may intensify their self-doubt.
Acquiring any new skill is a process of “three steps forward, two steps back,” especially in the early weeks and months of learning. Depending on the complexity of the skill, sometimes mastery can come quickly. But for many new skills, even basic levels of competence can take months to reach. Agree with your learner on regular check-in intervals to monitor progress.
The chance to lead a younger professional is a unique privilege. You’re impact on their self-perception and their desire to advance will be significant. By learning to be an inspiring teacher, you may just set someone on course to discover potential that might have otherwise remained hidden.
Ron Carucci is co-founder and managing partner at Navalent, working with CEOs and executives pursuing transformational change. ©2022 Harvard Business School Publishing Corp.