Key of
Benefits
What Is the Relationship Between Legionella Water Systems?
Modern qPCR and Why It Is Better Than the Culture Method for Legionella Testing
in Non-Potable
AWT—Your Voice
Our Legacy
1:
Published by Volume 29 Number 3 1300 Piccard Drive, Suite LL 14 • Rockville, MD 20850 Summer 2022ANALYSTthe IndustryTreatmentWatertheofVoiceTheVolume29Number3 2022Summer
Amoeba and
Amplify Honors
Water Sustainability Impact Oil
How Can the IoT (Internet of Things) Support Industrial Water Treatment?
Treatment?
Part How Does and Gas Water
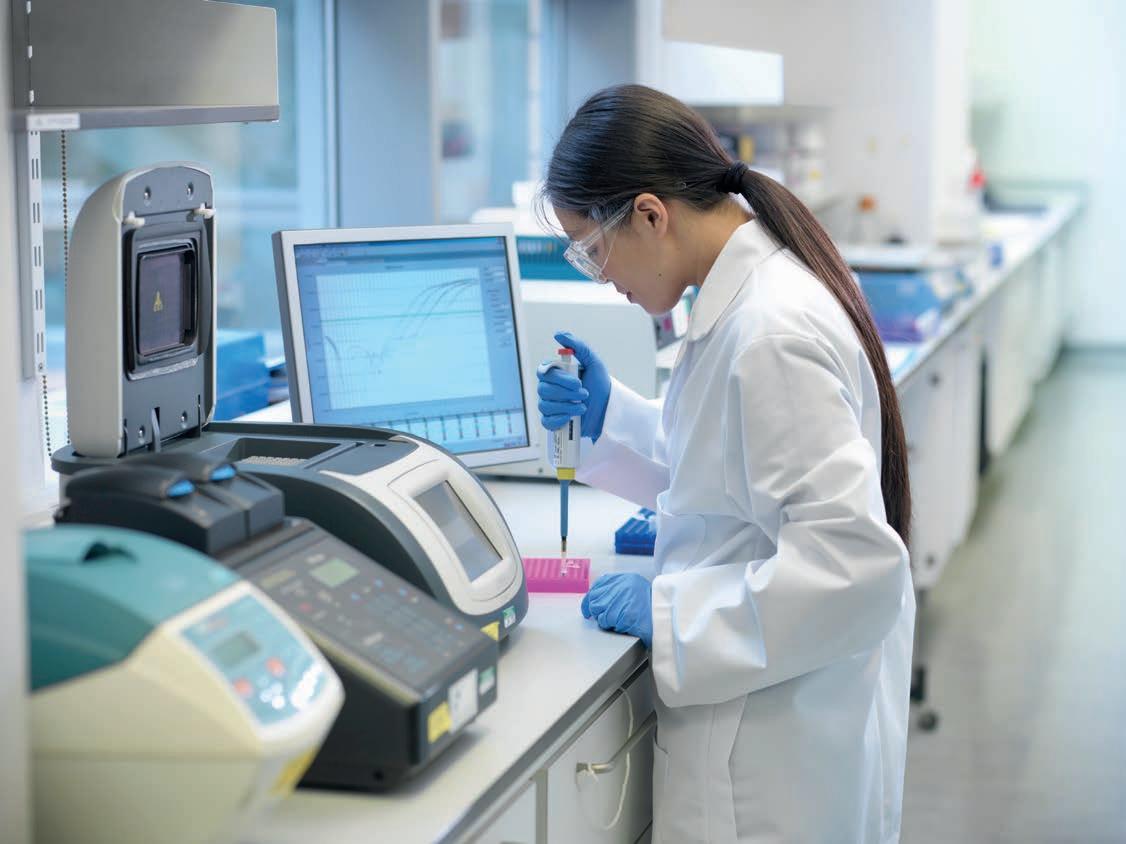
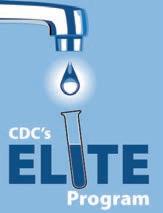
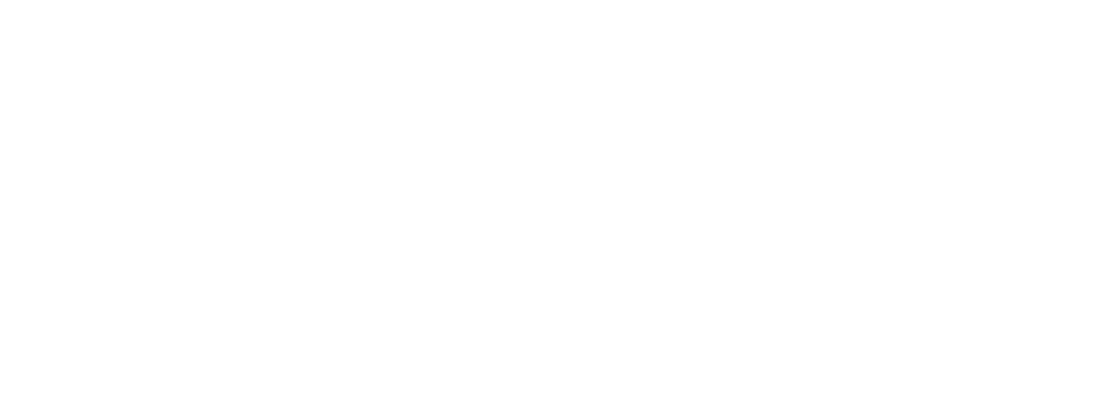
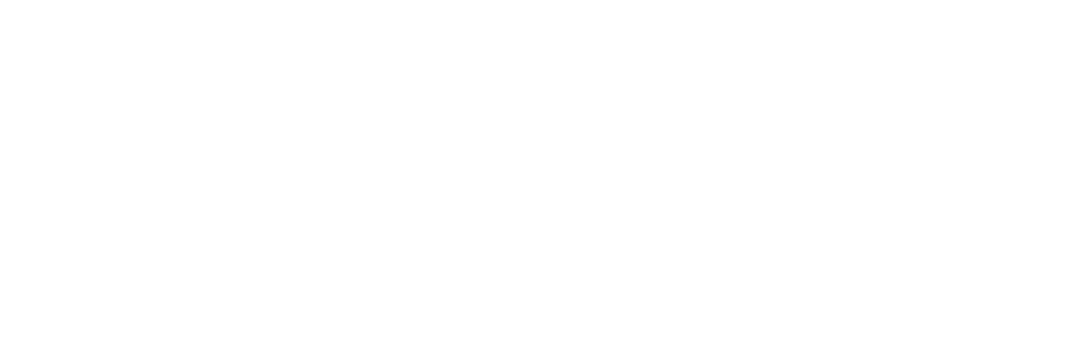
In 2019, the board established a governance task force of members to evaluate options for addressing concerns regarding the sustainability and health of the association. Ongoing mergers and acquisitions as well as a lack of time from member volunteers means that for AWT to remain relevant, we need to evaluate our current structure.
Since the discovery of Legionella bacteria during the 1976 outbreak that occurred in Philadelphia at the Bellevue Stratford Hotel, the culture method has been used to identify the presence of Legionella in water. The culture method was not intended to effectively quantify the bacteria and has many deficiencies and subjectivity in the method itself. However, the culture test is the predominant method now in use by laboratories. Polymerase chain reaction (PCR) methods have become more established and have supplemented or replaced culture methods in many industries and for many types of bacteria.
A dynamic and evolving landscape of connected technology presents a daunting opportunity to revolutionize the way we manage water treatment. With current technology, it is possible to know immediately when there is a system upset. This wave of connected devices presents a future where online visibility to all your system parameters is at your fingertips. This article will analyze the current state of conventional water treatment methods, highlight some existing Internet of Things (IoT) augmented water treatment methods, and project theoretical use cases and future IoT water treatment models, leveraging connected devices to either optimize workflow or heighten quality control.
14 Key Benefits of Modern qPCR and Why It Is Better Than the Culture Method for Legionella Testing
Colin Frayne, CSci, CChem, CEnv, FRSC, CWT, Aquassurance, Inc.; and Barry B. Ekstrand, P.E., Finoric LLC
Shivi Selvafratnam, Ph.D., Weas Engineering Inc.
54 How Can the IoT (Internet of Things) Support Industrial Water Treatment?
Dave Christophersen, CWT, Dave Christopherson Consulting LLC
As a result of global population growth and an increased demand for energy and good quality water, the demand and supply positions for vital resources (especially water) varies considerably from country to country; but globally, freshwater withdrawals have increased six-fold over the last 100 years, and we all face an uncertain future due to critical worldwide water shortages and quality problems. In view of this crisis, this article series focuses on the oil and gas industry and its relatively large usage of water (e.g., for hydraulic fracturing fluids). It provides an overview on the types of standard water treatment separation processes available to implement the three Rs (i.e., Reuse, Recycle, and Reclaim) and aims to further reduce water consumption.
Legionella is an opportunistic waterborne pathogen that exists as a free-living organism and an intracellular parasite in which several amoeba species serve as the host organism. The life cycle of Legionella is thought to be dependent on the existence of an amoeboid host that is present in a complex biofilm community. Whether this host–parasite relationship is a necessary or an opportunistic relationship is not well understood. In this article, we examine non-potable water systems for the presence of Legionella spp. and free-living amoeba (FLA).
Laith Charles, Watermark LLC
8 Amplify AWT—Your Voice Honors Our Legacy
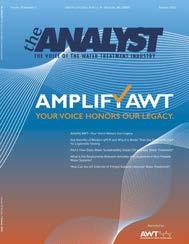
3 the ANALYST Volume 29 Number 3 Cover Amplify AWT— Your Voice Honors Our KerryCoverLegacygraphics:Bankert 4 C alendar of Events 5 President’s Message 6 Message From the President-Elect 61 Membership Benefits 62 Industry Notes 64 Discovering AWT 67 C WT Spotlight 68 Making a Splash 69 C apital Eyes 71 Tales From the Waterside 73 T.U.T.O.R. 77 What’s (Water) on Your Mind? 80 Business Notes 82 Advertising Index Summer 2022 Volume 29 Number 3
26 Part 1: How Does Water Sustainability Impact Oil and Gas Water Treatment?
44 What Is the Relationship Between Amoeba and Legionella in NonPotable Water Systems?
Treasurer
Third Monday of each month, 9:00 am—Certification Committee
Second Friday of each month, 2:00 pm—Pretreatment Subcommittee
Calendar of Events
Association Events
Third Monday of each month, 3:30 pm—Young Professionals Task Force
John E. Davies, CWT
Matt Copthorne, CWT
Publisher, Heidi J. Zimmerman, CAE
Second Wednesday of each month, 11:00 am—Business Resources Committee
2022 AWT Board of Directors
2023 Annual Convention & Exposition
Second Tuesday of each month, 2:30 pm—Convention Committee
Brian Jutzi, CWT
Casey Walton, B.Ch.E, CWT
Managing Editor
Fred Shurtz
Third Friday of each month, 9:00 am—Boiler Subcommittee
Devos Place and Amway Grand Hotel Grand Rapids, Michigan
John Baum, CWT
Pam Simmons
Mark R. Juhl
Matt Jensen, CWT
Sara L. Wood, MBA, CAE
Lynne Agoston
Michael Bourgeois, CWT
Directors
4 the ANALYST Volume 29 Number 3
Second Friday of each month, 10:00 am—Special Projects Subcommittee
William E. Pearson II, CWT
Third Tuesday of each month, 3:00 pm—Education Committee
Michael Henley, mdhenleywater@gmail.com, (303) 324-9507
Jennifer Olivares
Rockville, MD 20850
September 20, 2022
Also, please note that the following AWT committees meet on a monthly basis. All times shown are Eastern Time. To become active in one of these committees, please contact us at (301) 740-1421.
Production Manager, Tiffany Ward
Joseph M. Hannigan Jr., CWT
October 4–7, 2023
2022 Business Owners Meeting
Mark T. Lewis, CWT
Vancouver Convention Centre Vancouver, Canada
Pan Pacific Vancouver Hotel Vancouver, Canada
Marketing Coordinator
Marc Vermeulen, CWT
Tim Foley
John D. Caloritis, CWT
Second Friday of each month, 11:00 am—Cooling Subcommittee
President
Stephen C. Hallier, CWT
The Analyst Staff
Jack Altschuler
Scott W. Olson, CWT
Tammy Faber, MBA
Angela Pike
Michael Bourgeois, CWT
Third Friday of each month, 10:00 am—Technical Committee
1300 Piccard Drive, Suite LL 14
Director of Accounting Services
Meetings Planner
President-Elect
Advertising Sales Manager
William C. Smith
Ron RobertKnestautD.Lee, CWT
Dennis BernadetteClaytonCombs, CWT, LEED AP
Managing Editor, Lynne Agoston
Noah Baskin
James Mulloy Alfred Nickels
Immediate Past President
The Analyst is published quarterly as the official publication of the Association of Water Technologies. ©2022 Association of Water Technologies. Materials may not be reproduced without written permission. The articles, studies, and reports in this publication are the works of the respective authors. AWT expressly disclaims any duty to investigate any article, study, report, conclusion, product, service process, procedure, design, or similar offering contained herein. AWT does not warrant that the information in this publication is free from error and does not necessarily agree with the statements or opinions contained herein. The appearance of any technical data, editorial material, or advertisement in this publication does not constitute an endorsement, warranty, or guarantee by AWT. This publication is not a substitute for the competent counsel of a water treatment professional, plumbing professional, mechanical official, or attorney. The user assumes any and all risks of relying on the information in this publication. Authors are responsible for ensuring that the articles are properly released for classification and proprietary information. All advertising will be subject to publisher’s approval, and advertisers will agree to indemnify and relieve publisher of loss or claims resulting from advertising contents. Editorial material in the Analyst may be reproduced in whole or part with prior written permission.
Larry A. Webb
Kyle Rossi, CWT
ACS, Fall National Meeting & Expo, August 21–25, 2022, Chicago, Illinois
Past Presidents
Senior Director, Creative Services/Marketing
Bruce T. Ketrick Sr., CWT
2022 Annual Convention & Exposition
Caroline Bentley
Meetings Coordinator
Mark Coldren, CWT
Grace L. Jan, CMP, CAE
R. Trace Blackmore, CWT, LEED AP
Deputy Executive Director
Dawn Rosenfeld
Steven MacCarthy, CWT
Heidi J. Zimmerman, CAE
Ex-Officio Supplier Representative
Vice President, Meetings
Carol Nettles, carol@adboomadvertising.com
Brent W. Chettle, CWT
StaffExecutive Director
David Wagenfuhr
Jay Farmerie, CWT
Secretary
Tiffany Ward
Quarterly (call for meeting dates), 11:00 am—Wastewater Subcommittee
RETA, Annual Convention, November 7–10, 2022, Reno, Nevada
Member Services Director
Request permission by writing to: Managing Editor, the Analyst, 1300 Piccard Drive, Suite LL 14, Rockville, MD 20850, USA. Annual subscription rate is $100 per year in the United States (4 issues). Please add $25 for Canada and Mexico. International subscriptions are $200 in U.S. funds.
Mary Claire Gordon
Production Manager
www.awt.org
James R. Datesh
Exhibits and Sponsorship Manager
Brandon Lawrence
Other Industry Events
D.C. “Chuck” Brandvold, CWT
Technical Editor
Gary CharlesGlennaD.Hamrick Jr., CWT
Bruce T. Ketrick Jr., CWT
Second Tuesday of each month, 11:00 am—Legislative/Regulatory Committee
Ultrapure Micro, In-person meeting, September 28–30, 2022, Glendale (Phoenix), Arizona WEFTEC, Annual Technical Exhibition and Conference, October 8–12, 2022, New Orleans, Louisiana IWC, Annual Conference, November 6–10, 2022, Orlando, Florida
Thomas Brandvold, CWT
Anthony J. McNamara, CWT
September 21–24, 2022
(301) 740-1421 • (301) 990-9771 (fax)
At the conclusion of the convention, I end my term as AWT’s president. I’ve learned a lot during this time and have found it incredibly rewarding to serve AWT. This is an exciting time to be part of this great organization!
I also can’t wait to honor the winners of the Ray Baum Memorial Water Treater of the Year, Supplier of the Year, and Rising Star awards. It’s such a privilege to be able to present these awards to our exceptional recipients. I’m humbled to have the honor.
5 the ANALYST Volume 29 Number 3
We have a great program planned with outstanding educational sessions. The exhibit hall provides the opportunity to learn about the latest from our suppliers. And once again this year, you may be able to leave the convention with equipment or services you’re in need of, all while supporting our charity partner, Pure Water for the World, through our silent auction.
Volunteer With AWT
While I’m thankful to be able to interact with peers at a moment’s notice, it also strikes me how important in-person meetings are. During conferences and events, I always find those impromptu meetings in the hallway to be some of the most valuable interactions I have. I’m able to find solutions to problems and gain insights that might not have happened otherwise. The conversations are more robust when we’re face to face.
AWT Bylaws and the Amplify Campaign
If you aren’t already, I hope you consider getting involved with AWT by volunteering for a project or committee. When I started out in the industry and began coming to AWT events, serving on a committee expanded my network and knowledge. It was a great way to quickly develop a trusted group of peers with which to exchange ideas. I’ve been able to bring great resources and mate rial back to my company, making us stronger for it. Volunteering can be as simple as reviewing a paper for the Annual Convention or helping with a long-term project. We have many opportunities to suit your avail ability. If you’re interested, please reach out to AWT staff at (240) 404-6477, and they can set you up on the right path. That’s how I got started—one quick conversa tion with staff.
Our water treatment company members should have received a copy of the proposed bylaws that will be discussed during the Annual Membership Meeting.
That’s why I’m looking forward to the AWT Annual Convention & Exposition in Vancouver in September. It’s a great time to learn, talk with peers in the industry, and get revitalized and refreshed about what we do every day.
President’s Message
As I write this, there has recently been a flurry of activity on the AWT Exchange, with people reaching out seeking input to challenges they’re facing. I read the Exchange daily and continue to learn from all he great water treatment professionals in our industry.

Thank you for the opportunity to serve. I can be reached at president@awt.org
To ensure maximum participation in the bylaws vote, we will be live-streaming the Annual Membership Meeting. Each water treatment company member is entitled to one vote. Our online system will allow electronic voting on the bylaws, so be sure to participate. Your vote matters!
By Matt Jensen, CWT
6 the ANALYST Volume 29 Number 3
the insights he has learned from his time running the leadership development program at the University of Toronto through his decade traveling the globe and increasing the leadership capacity of some of the world’s most dynamic organizations.
Drew will provide you with a custom roadmap to begin building more effective leadership as an individual or an organization. Regardless of where your employees or your organization are in their leadership journey, Drew and the Day One approach will take you to another level.
Drew’s Wall Street Journal bestselling book This Is Day One: A Practical Guide to Leadership That Matters shares
It’s almost here! The 2022 AWT Annual Convention & Exposition will take place September 21–24, 2022, in Vancouver, British Columbia, Canada.
Keynote Speaker
Currently, COVID restrictions continue to ease. All travelers into Canada will need to download and use the ArriveCan app to show proof of vaccination, but all testing requirements into and out of Canada have been lifted. As always, we will continue to monitor the situa tion and let everyone know as restrictions ease further.
At the conclusion of the Annual Convention, I will assume my role as AWT president. AWT has some great programs and services in the works for the coming year, and I look forward to developing them alongside our committed volunteers.
As I step into my new role, I welcome your input on the future direction of AWT. I can be reached at steve@ wetsolutionsinc.com. Thank you for the opportunity, and I look forward to serving you!
Message From the President-Elect
Our keynote speaker this year is Drew Dudley, who is on a mission to help people unlearn some dangerous lessons about leadership. As the founder and chief catalyst of Day One Leadership, he has helped top organizations around the world increase their leadership capacity.
By Steve Hallier, CWT
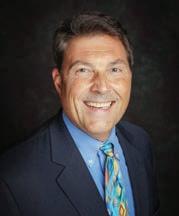
Your one stop shop for Metering Pumps 9001 Hanslik Ct. Naperville, IL 60564 | Tel: 630-355-3330 | info@quantrol.net | www.quantrol.com SCAN ME!
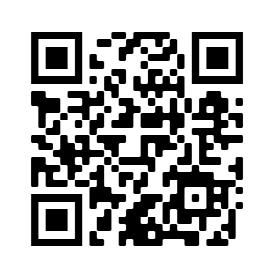
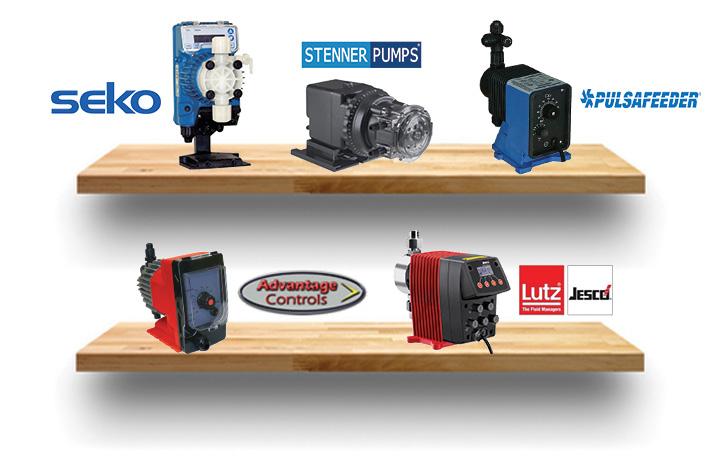
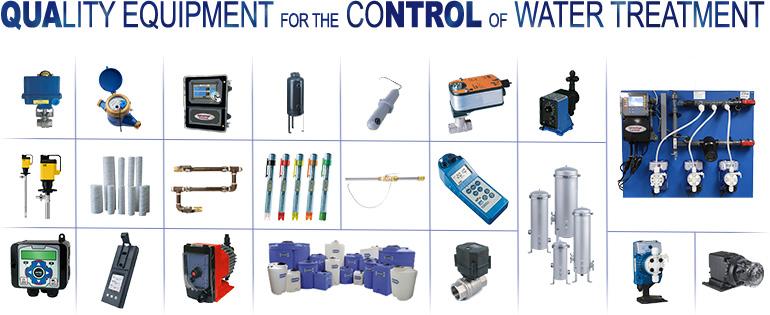
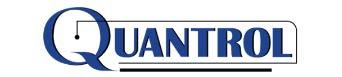
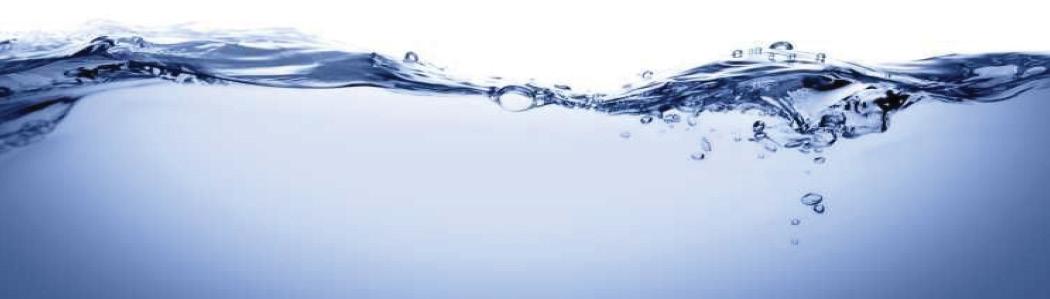
8 the ANALYST Volume 29 Number 3
Amplify AWT—Your Voice Honors Our Legacy
Introduction
AWT’s current bylaws are inhibiting growth that would lead to long-term sustainability. Water treatment company (WTC) members are limited to companies with less than $30 million in annual sales and fewer than 150 employees. These existing limits are prohib iting growth and engagement, leading to a decline in talent and intellectual capital for all members. If we continue to contract at this rate, AWT will have fewer than 450 companies by 2029.
of today bears very little resemblance to the fledgling organization of 1985. The diversity of the companies in the association is considerable in terms of size, scope of operations, geographic location, and other factors. The dynamic AWT of today provides high-level technical training, unparalleled networking opportunities, educational events, legislative monitoring, regulatory compliance assistance, and more to help your company succeed. The scope of programs offered by the association will continue to develop based on the shared and changing needs of its members.
4,500 individual employees receiving benefits from AWT. Today, mergers and acquisitions have reduced the number of companies AWT serves to about 560, yet the number of employees receiving AWT benefits has increased to almost 5,100.
Proposed Measure 1
In 2019, the board established a governance task force of members to evaluate options for addressing concerns regarding the sustainability and health of the association. Ongoing mergers and acquisitions as well as a lack of time from member volunteers means that for AWT to remain relevant, we need to evaluate our current struc ture. Recommendations from the task force, refined by input from the membership, leads us to two bylaws recommendations that will create a stronger AWT to continue as the leader in serving the water treatment industry.
9 the ANALYST Volume 29 Number 3
At this year’s Annual Business Meeting in September, the membership will be voting on two changes to the AWT bylaws that have been designed to help the organization grow well into the future. It is important to note that you do not need to be physically present in Vancouver to vote. The meeting will be livestreamed, and AWT has created a way for any eligible member to vote, regardless of their participation at the convention.
These founding members operated their businesses similarly: most of these companies blended their own products, they served the same market segments in their regions, and the owners of the firms all had similar backgrounds in terms of experience and education. These founding members came together to form, like most beginning trade organizations, a very homogeneous
Small Business Administration, a “small-business” is 500 employees or fewer, so it would follow an existing precedent. With the cap set at 500 employees, we serve our historical desire to remain small business focused.
Proposed Changes
To change the cap on WTC members by removing the dollar restriction and increasing the number of employees to 500 or fewer employees in a water treat ment
Thegroup.AWT
AWT was founded in 1985 by a handful of entrepre neurs who came together based on a common concern about the inability of water treatment firms to secure affordable product liability insurance. This was a major issue at the time, threatening the continued existence of water treatment businesses. Their solution was to create an insurance program based specifically on the smaller and medium-sized independent water treatment firms.
Accordingdivision.tothe
It has been almost two decades since the size restric tion has been modified, which has not allowed for inflation. By setting the increase higher than just the inflation rate, we can account for growth into the future. Members would not be punished/excluded for growing. Historically, excluding members that have grown has resulted in a loss of talent/intellectual capital/contri butions for the good of the members. Members who have had to leave committee participation because their company sized out would be able to return.
AWT History
Current Membership Structure
AWT is a trade association with over 560 member companies. From 2016–2019, AWT served over 600 member companies, and these companies had over
Proposed Bylaws
The task force also recommends that anyone with an interest in water treatment be allowed to join AWT as an individual member. This would allow AWT companies to gain access to a wider network both domestically and abroad. This would also open the talent pool to AWT, allowing for greater engagement in our community. While members in this category would have access to water treatment resources and AWT pricing and be able to serve on committees, they would be restricted from voting in AWT elections, sitting on the board of directors, chairing a committee, or participating in the Business Owners Meeting and website.
Companies whose primary customer is the water treatment end-user (80% of sales to end-user). The company is limited to annual gross sales of $100M US from water treatment operations. This category can include divisions and subsidiaries of larger companies only if the parent company is not involved in the sale of water treatment products or components. If two subsidiaries or divisions join, their combined total annual gross sales must be under $100M US from water treatment operations.
Current Bylaws
The addition of the following category and updated numbering of subsequent categories:
2.2.1. Water Treatment Company (WTC)
Section 2.2 of the AWT bylaws outlines the eligibility of all classes of membership as listed in section 2.1
Current Bylaws
Proposed Bylaws
2.2.8. Prohibited Organization. Any Water Treatment
A second section of the bylaws would also need to be modified to align with this change. For this addition, there is no change to existing language since it is new proposed language.
2.1. Classes. There shall be six classes of members: Water Treatment Company (WTC); Water Treatment Supplier Company (WTS); Honorary Emeritus; Sustaining; Individual; and Student.
Companies whose primary customer is the water treatment end-user (80% of sales to end-user). The company is limited no more than 500 full-time employees working in the water treatment division to qualify for this category. This category can include divisions and subsidiaries of larger companies only if the parent company is not involved in the sale of water treatment products or components. If two subsidiaries or divisions join, they shall not have more than 500 full-time employees.
2.2.8. Prohibited Organization. Any Water Treatment Company (WTC) that has, in the aggregate, more than one hundred fifty (150) full-time employees in the water treatment division or that is greater than $100M US. Sustaining members are exempt from this provision.
2.1. Classes. There shall be five classes of members: Water Treatment Company (WTC); Water Treatment Supplier Company (WTS); Honorary Emeritus; Sustaining; and Student.
Amplify AWT—Your Voice Honors Our Legacy continued
We would allow for growth and increase member engagement, all while remaining true to the spirit of helping small business owners.
2.2. Eligibility. The qualifications for each membership class shall be as follows:
Current Bylaws
2.2. Eligibility. The qualifications for each membership class shall be as follows:
Company (WTC) that has, in the aggregate, more than five hundred (500) full-time employees in the water treatment division. Sustaining members are exempt from this provision.
2.2.1. Water Treatment Company (WTC).
Students who qualify under the SEED
Proposed Measure 2
10 the ANALYST Volume 29 Number 3
Current Bylaws
2.2.5. Individual. Anyone with an interest in water 2.2.6.treatment.Student.
Proposed Bylaws
A second section of the bylaws would also need to be modified to align with this change:
Proposed Bylaws
West 866.798.1089Coastwww.EMSL.comEastCoast800.220.3675 WATER TESTINGINDUSTRYSERVICESCorrosionTestingLegionellaTestingMicrobiologyTestingChemicalAnalysisParticulateIdentificationMicroscopicIdentificationPFASTestingFiltrationStudiesMetalsTestingMicroplasticsTestingBacteriaTesting

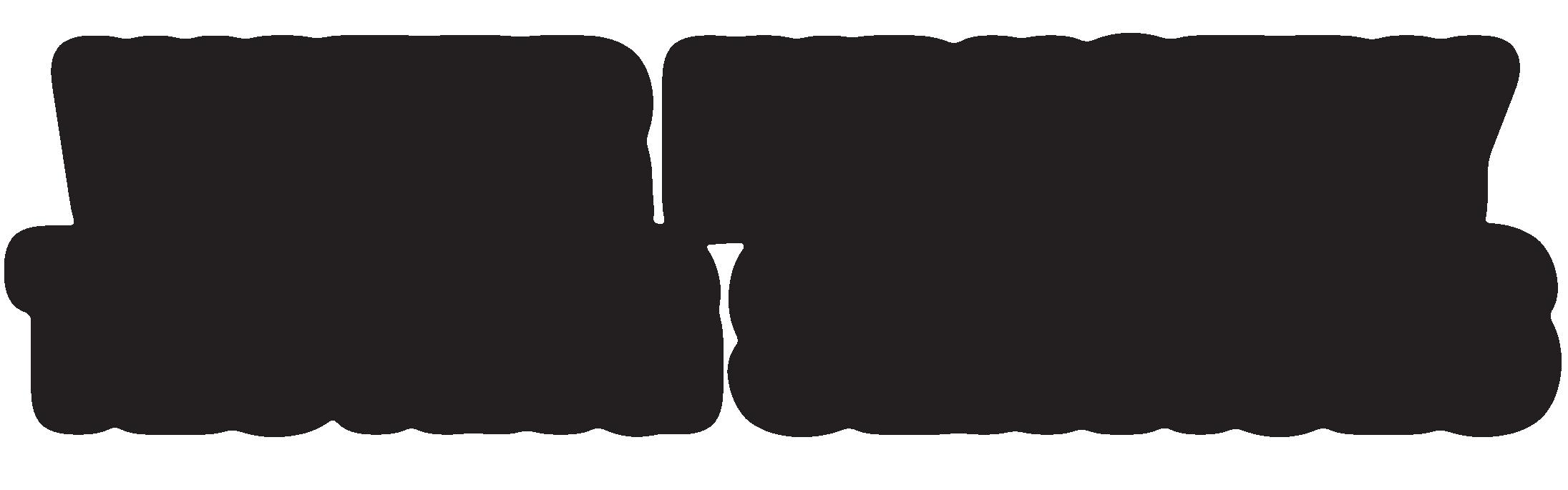


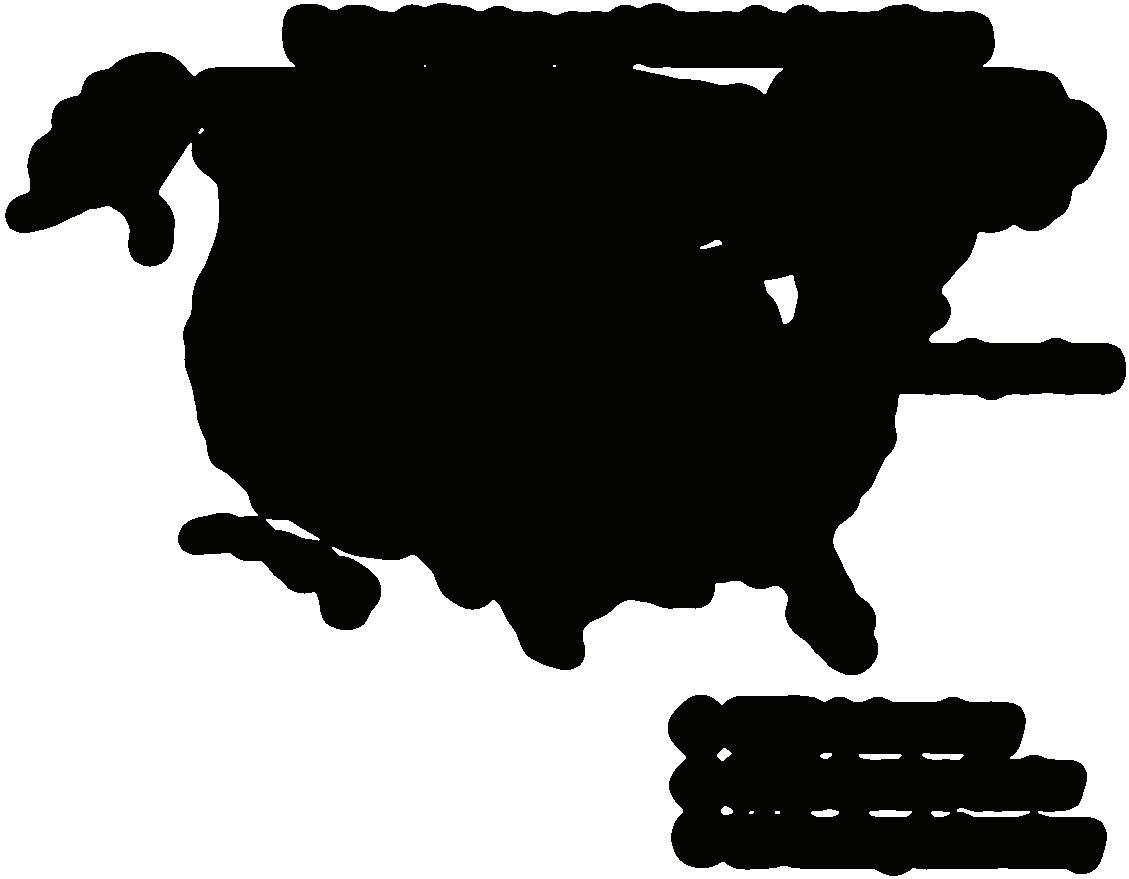
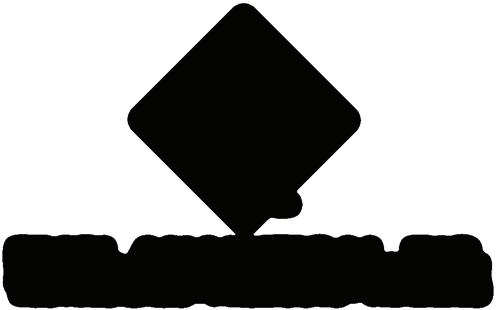
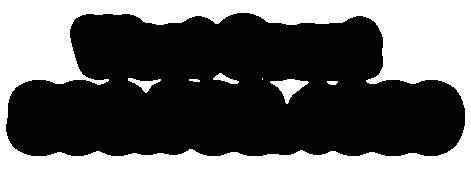
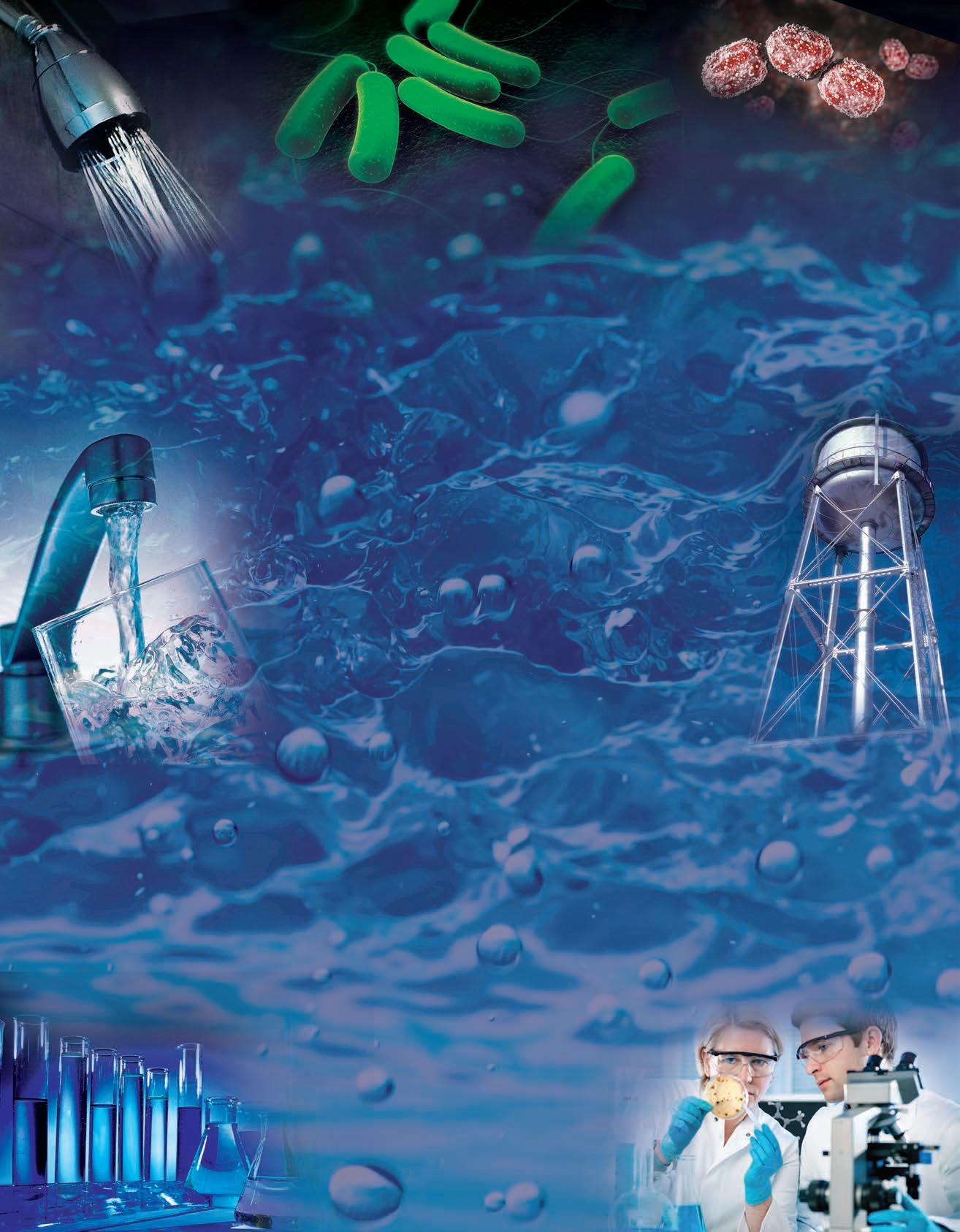
3) You may submit your vote one of three ways in accordance with AWT bylaws:
program description as prescribed by the policies and procedures as set by the board of directors.
c. Vote by proxy. For each measure, a voting member will be assigned to cast all proxy votes in favor, another for against, and a third for abstain. Upon the conclusion of the meeting, the proxy voters will supervise the casting of all votes for their designated option. This option is recommended ONLY for those who cannot attend in person or log in for remote participa tion. Anyone who submits a proxy vote ahead of time will NOT receive a voting link, even if they decide to attend the meeting. This is to ensure that only one vote is permitted per company.
Conclusion
Amplify AWT—Your Voice Honors Our Legacy continued
1) One vote is permitted per WTC company. Official voting notifications have been sent to eligible voting companies electronically as well as via mail.
2.2.7. Common Ownership. Any eligible member company with common ownership or control by a current AWT member company may elect to join AWT. If the eligible member companies share the same membership category, one of the companies would be required to sub-register under that membership cate gory. If the companies qualify for different categories, they would join at the WTC membership rates. If the companies are in the WTC category and still meet the criteria for a WTC, then the owner must designate which company will be the voting member. Member companies with common ownership or control may only have one representative elected to the board of directors at any given time.
12 the ANALYST Volume 29 Number 3
We are confident that these changes will allow us to stay true to our core values and members while embracing the excitement of the future. Be sure to participate in this important vote that will allow us to move forward to a stronger future.
It is important to emphasize that physical in-person attendance will not be required to participate in this vote. To ensure that as many eligible voting members have an opportunity to vote as possible, this year’s busi ness meeting will be livestreamed. Regardless of whether you are attending in person or online, please take a few moments to review the voting procedures below.
Make Your Voice Heard: Casting Your Vote
a. Attend the membership meeting in person. At the conclusion of the meeting, you will be sent a secure electronic voting link. This vote may be cast from your phone or at a voting station provided at registration using a login unique to you. Important: You must attend the meeting to vote.
the meeting, you will be sent a voting link to cast your vote, provided your attendance was recorded.
b. Attend the membership meeting remotely via Zoom. A Zoom link will be sent to those who selected remote participation prior to the meeting with instructions for how to enter your name. Important: You must attend the meeting to receive a voting link. Upon conclusion of
2) The proposed bylaws changes will be voted on as separate measures.
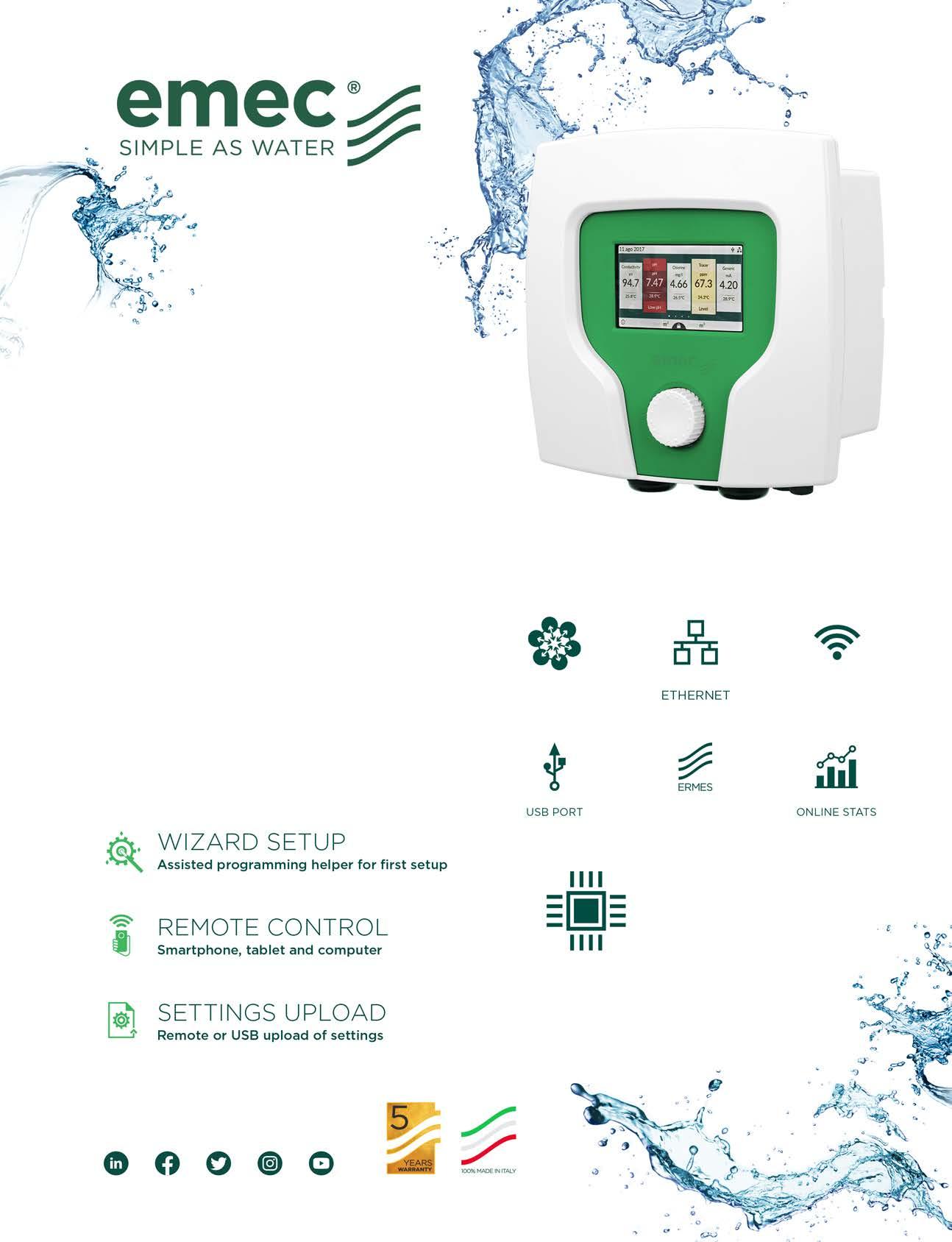
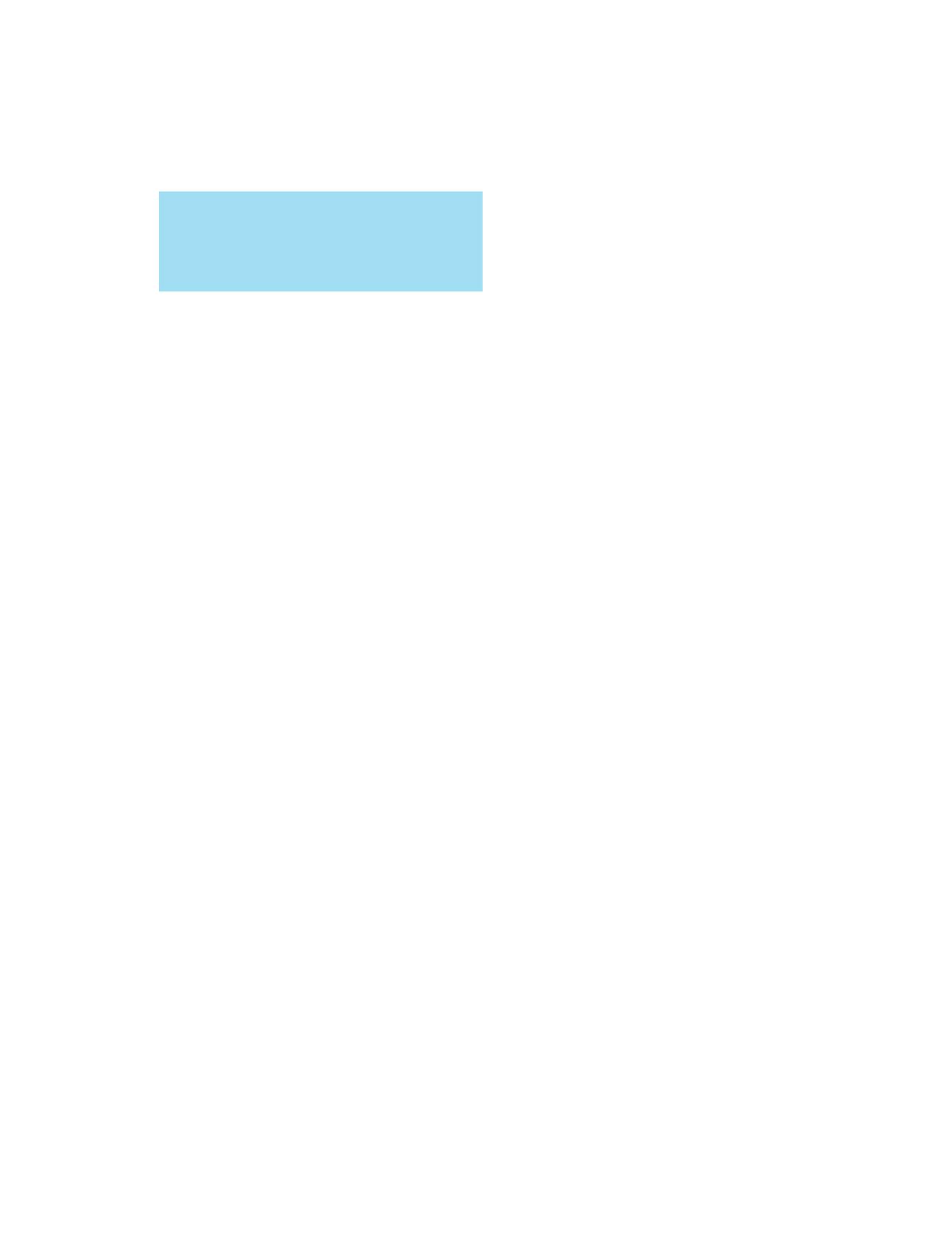
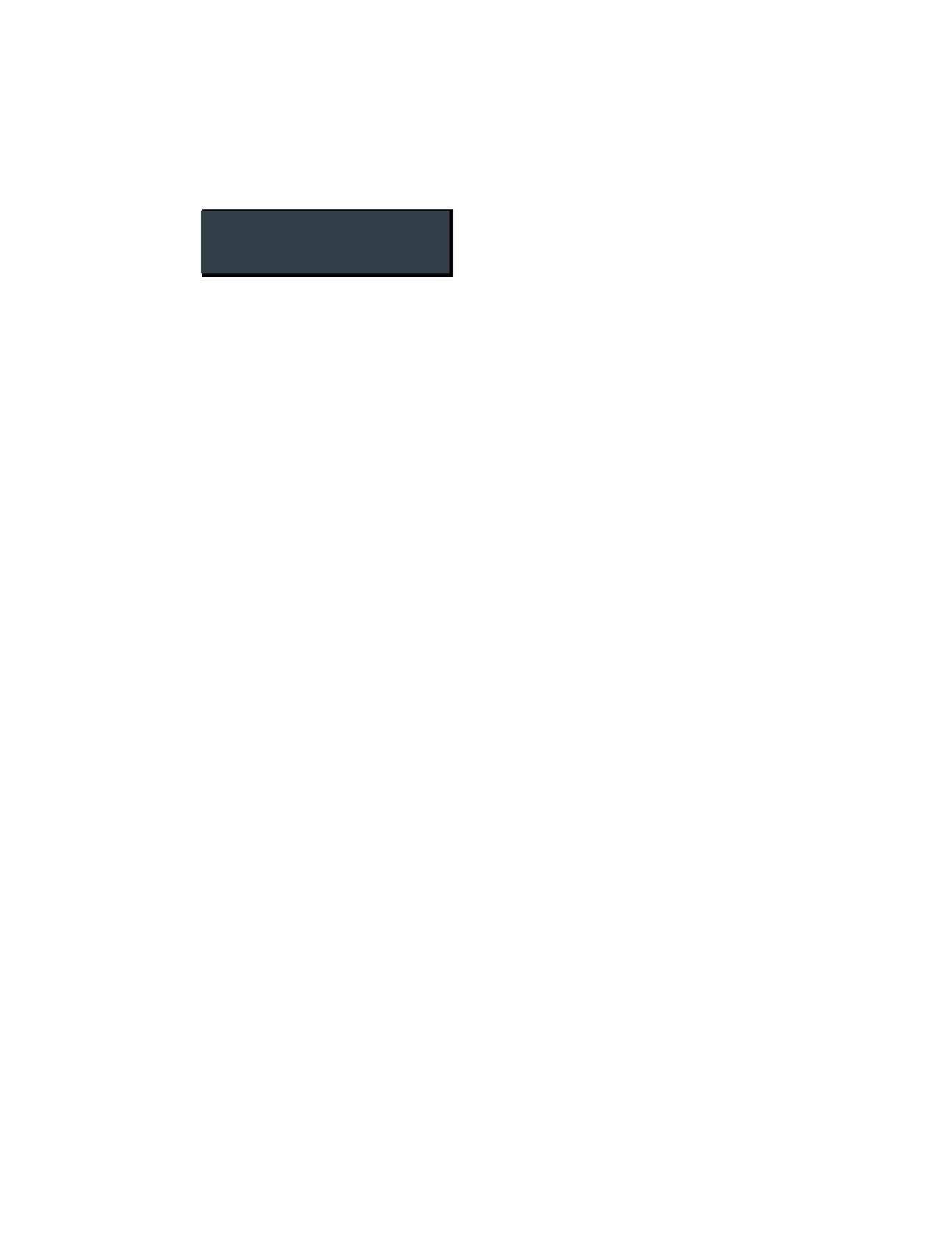
Dave Christophersen, CWT, Dave Christophersen Consulting LLC
Source: www.alchetron.com
Several test methods for Legionella are currently available on the market. Some are designed for field work, and others are typical for laboratory testing. Two lab methods are culture and PCR or qPCR.
Background
The culture method commonly used by CDC elite labs follows the procedure established by the International Organization for Standardization labeled ISO 11730 (1). There is some subjectivity in the procedure to remove interfering bacteria, with the goal of trying to get Legionella bacteria cells or groups of cells to grow on an agar plate over the course of days, creating colonies big
14 the ANALYST Volume 29 Number 3
Since the discovery of Legionella bacteria during the 1976 outbreak that occurred in Philadelphia at the Bellevue Stratford Hotel (pictured on left), the culture method has been used to identify the presence of Legionella in water.
A picture of the Stafford Hotel in Philadelphia, where the 1976 outbreak of Legionella occurred.
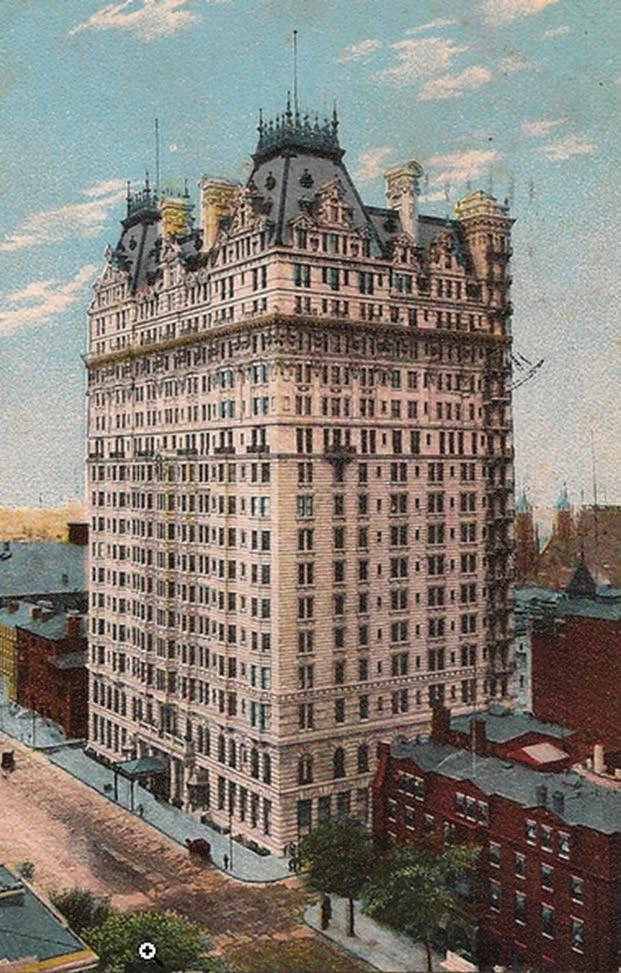
This article will discuss monitoring for the presence of Legionella and how the qPCR technology can improve biocontrol in cooling water and building water systems.
The culture method was not intended to effectively quan tify the bacteria and has many deficiencies and subjec tivity in the method itself. However, the culture test is the predominant method now in use by laboratories. Polymerase chain reaction (PCR) methods have become more established and have supplemented or replaced culture methods in many industries and for many types of bacteria. The Centers for Disease Control and Prevention (CDC) and other organizations recognize PCR as an approved method for Legionella analysis, but most people and organizations remain unaware of newer quantitative PCR (qPCR) methods and their ability to identify Legionella type and with much greater preci sion. Today, the modern qPCR method can have better usefulness than culture methods for routine monitoring and remediation work.
Key Benefits of Modern qPCR and Why It Is Better Than the Culture Method for Legionella Testing
Cooling Towers:
Building Potable Water Supplies:
enough to recognize and count as Legionella colonies. Each is recorded as colony-forming units (CFUs).
Figure 1: Charts from PCR amplification of genetic material.
Moving Forward With qPCR
If we had used qPCR methods that are available now, going back to 1976, we would not even discuss changing to the culture method for regular and remediation work.
Becauseguidelines.CFUlevels
Chart courtesy of BIOTECON Diagnostics Co.
• Action: 50 to 100 GU/mL
As data builds, we will more likely be able to establish better correlation data to Legionella GU level and the risk of Legionnaires’ disease and create better alert and action
are colonies on a plate and not necessarily actual cell numbers in the water, they may not provide very good alert or action control guidelines. Use of qPCR allows for a much better risk assessment and with more reliable data. The sooner we start using GU, the faster we will improve control and reduce risk.
Table A provides suggested guidelines for Legionella alert and action levels.
To help with getting qPCR accepted and used more, we need GU alert and action levels for building/potable waters and for cooling tower waters that are as safe as CFU guidelines but not set too low. Various studies suggest a one log increase or a little more compared to CFU as alert and action levels. To offer some higher safety, it may make sense to look at half that. This is open for discussion, and there is probably enough published data available to establish a guideline (2, 3).
Modern (Elite) qPCR Versus Culture Method
PCR is a molecular method that amplifies target genetic material with special enzymes, primers, and reagents and an instrument called a thermocycler to achieve high enough levels so that they can be detected. Newer, modern techniques can quantify the amount of the targeted genomic sequence and quantify them as number of genomic units (GU) or Legionella cells present in the water sample (qPCR), and even classify them as Legionella species, Legionella pneumophila, Sero Group 1, or Sero Group 2-15.
Since the two are very different, there is no good way to compare and contrast the two. Figure 1 shows data from PCR amplification of genetic material created from each cycle of amplification.
Many people familiar with PCR recognize it as a rapid results screening tool to see if Legionella are present. If so, they may then move onto further testing using the culture method. But modern qPCR, which we can even further categorize as elite qPCR methods, can do so much more. Test kits are available with the reagents basically prepared and freeze dried to increase ease and accuracy in the testing. Figure 2 shows PCR tube strips containing extracted DNA material along with neces sary primers and components to duplicate and amplify targeted DNA sequences. These tubes are placed into the rack of a thermocycler machine.
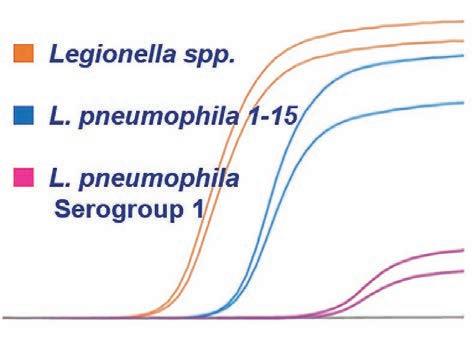
• Alert: 50 to 100 GU/mL
Table A: Suggested Guidelines
• Action: 500 to 1,000 GU/mL
• Alert: 5 to 10 GU per milliliter (GU/mL)
Today, the question should be, “Why and how to proceed with qPCR?”
15 the ANALYST Volume 29 Number 3
A GU is a specific section of the gene that is recognized with laboratory techniques such as PCR and can be quantified to associate with the amount of genetic mate rial coming from, in this case, a Legionella cell. A CFU is different in that it is a colony grown on an agar, containing perhaps millions of freshly grown bacteria cells.
on a given day, the complexity of the water matrix, and options available to the culture method that may influence how a particular lab runs the culture method. Figure 3 is a workflow chart taken from BIOTECON Diagnostics’ qPCR instructions manual.
16 the ANALYST Volume 29 Number 3
Key Benefits of Modern qPCR and Why It Is Better Than the Culture Method for Legionella Testing
Because GU and CFU are different units, there is no direct and consistent conversion from one to the other. There are statistical methods based upon compara tive testing results on large sample sizes that can yield some algorithm to make conversions, but it is best to understand what each method and unit are providing. The GU count is generally expected to be higher than CFU count for several reasons. Modern qPCR can be calculated to report results as GU, which is equivalent to one Legionella cell, while a CFU can develop from one or more cells. As an example, if the average isolate originates from groups of three cells, then 1 CFU would equal 3 GU. If each CFU originates from single Legionella cell, then 1 CFU = 1 GU. Also, qPCR detects most all Legionella in the sample (Limit of Detection [LoD] of 5), while the culture method can miss some or even most of Legionella present.
Figure 2: Tube strip for qPCR analysis.
The lab time required for qPCR can compare favorably to the culture method. It depends on several factors, such as how many Legionella tests are being performed

Figure 3: Example test procedure flow and time required for each stage.
continued
Photo courtesy of BIOTECON Diagnostics Co.
The efficiency or consistency of qPCR is very high, with some studies showing >90%, while the culture method is so low that arguments have been made that a difference in tested levels during a remediation or other actionable effort cannot statistically detect changes.
Image courtesy of BIOTECON Diagnostics Co.
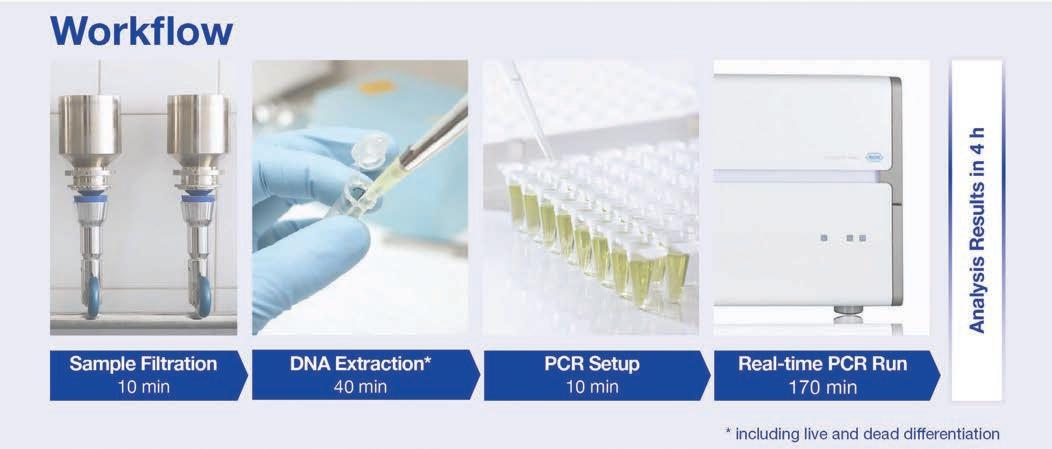
CLOGGED PUMPS? Tackle wipes and large debris with these solutions from USABlueBook! GET PRODUCT DETAILS usabluebook.com/NoMoreClogsAT 800.548.1234 • usabluebook.com OPERATOR DESIGNED FOR LARGE MUNICIPAL LIFT DemingSTATIONSDemersibleChopper Pumps • Slice the most troublesome solids into small pieces StationGuard Manual Bar Screens • Capture damaging wipes and debris FOR SMALLER APPLICATIONS AND LIFT STATIONS Goulds GFK and GFV Series Sewage Pumps • Non-clog impellers handle wipes and 2" solids FlowRake Rag Catchers • Catch and retain flushables OPERATOR DESIGNED EXCLUSIVE
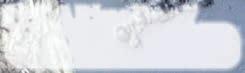

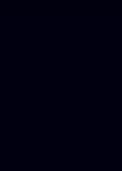
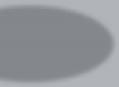
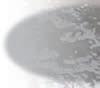



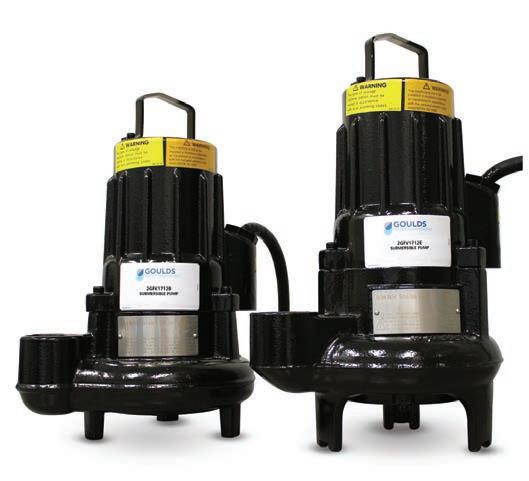
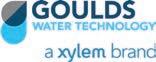
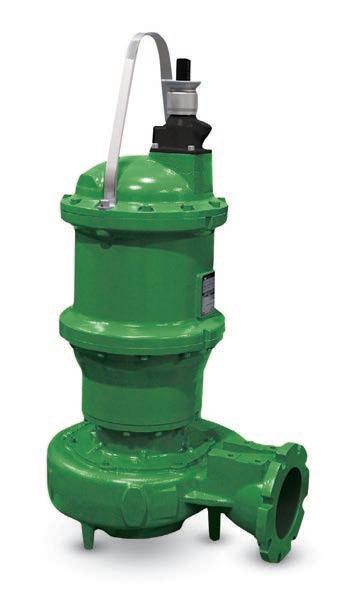
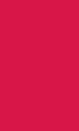


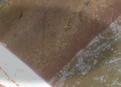
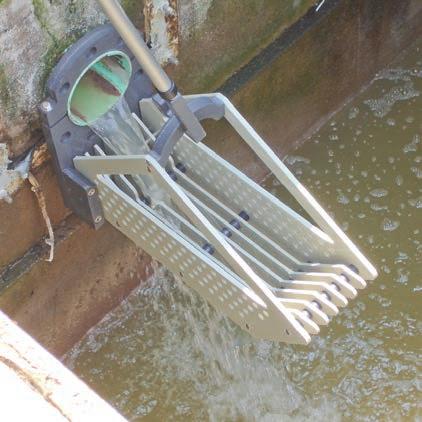
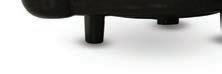


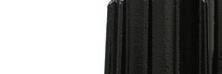
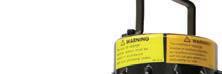
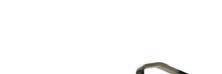


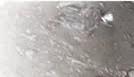
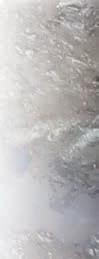
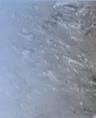
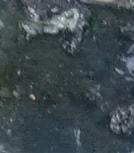
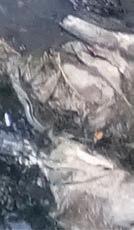
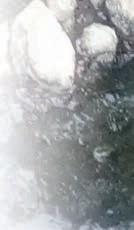

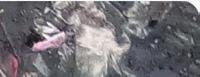
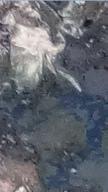


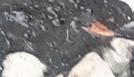


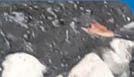
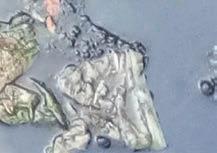
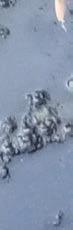
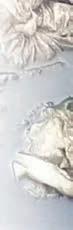


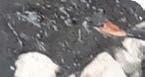
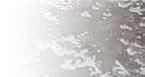
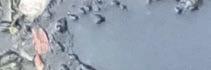
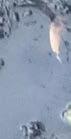
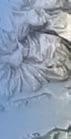
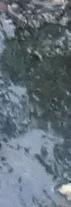
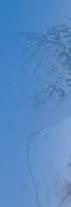
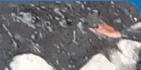
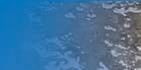
Because the culture method has been in use for so long, it has been accepted, and many who rely on it have not critically examined it or know the details of its procedure and its many inherent inaccuracies and problems. There are many liberties that can be taken by the laboratory technician. Waters can be plated directly or concentrated with filtration. The volume of water can be discretionary. It suggests one liter, but smaller volumes are acceptable.
Laboratory cost Similar to culture Similar to qPCR
Acid treatment to help remove non-Legionella bacteria before culturing may be necessary, but again, this is up to the lab to decide. Even the agar material, incubation process, and time varies from lab to lab. Actual identifi cation of Legionella- cultured isolates can be quite diffi cult. Some labs confirm Legionella by replating suspected isolates grown on the first plate, while other labs do not.
18 the ANALYST Volume 29 Number 3
Recovery of Legionella present High Low
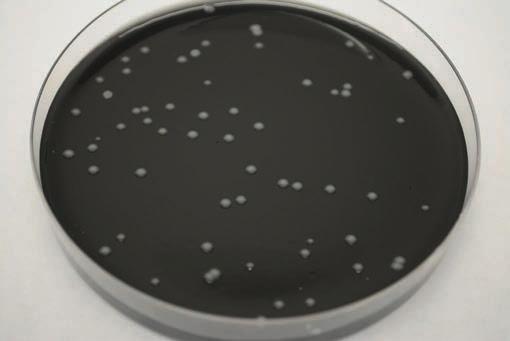
Process qPCR Culture
Total laboratory time Similar to culture Similar to qPCR
Can distinguish live from dead cells Yes Yes
So, even though the ISO 11731 standard method and the “CDC Laboratory Guidance for Processing Environmental Samples” (4) may be used, it is still a highly subjective procedure. Results take days to attain, (three days for tentative indications and up to 14 days for confirmations). Results are erratic and unreliable (e.g., poor sensitivity/recovery, poor efficiency).
Culture Method
How are results reported Genomic Units (GUs) CFUs
Repeatability of results Consistent Inconsistent
For the water treater and end-user, they will want guidelines based on GUs to be used in conjunction with CFU guidelines until CFU guidelines become outdated. As with any newer method, it usually requires key early Withadopters.understanding
Since the water treatment community (including water treatment companies and water management plan writers), relevant associations, healthcare facilities, government regulators, laboratories, and various other organizations may not be aware of modern qPCR capa bilities, we need to better publicize this needed change of best practice (5).
Table B highlights some of the major differences in the test methods and value differences between qPCR and culture.
The colonies are difficult to isolate, grow, and count. The culture method relies on cells to be viable and culturable. The organisms are typically alive but in a stressed state. As a result, only a portion, and likely a small portion of the organisms present, are actually cultured, even under the best of conditions. Figure 4 shows an example of cultures grown on the black Buffered Charcoal Yeast Extract (BCYE) plates.
Time for results 4 hours 7–14 days
Attempts to culture them may be suppressed by anywhere from 5 to 99% due to the selective nature of the medium required and isolation techniques used. Many cells can be in a state of metabolic dormancy, so they are Viable But Non-Culturable (VBNC), but they could perhaps resuscitate within a water system and pose a risk to human health.
Can be used to speciate types of Legionella Yes Yes
Actionable control response benefits High value Low or no value
Key Benefits of Modern qPCR and Why It Is Better Than the Culture Method for Legionella Testing continued
Figure 4: Example of cultures grown on a BCYE.
Comparison of reporting units Higher than CFU Lower than GU
Table B: Comparison of Test Methods
Culture plate courtesy of Q Laboratories, Cincinnati, Ohio.
Establishing qPCR as the New Gold Standard
of modern qPCR capabilities, a next step includes getting GUs written into guidelines and procedures.
Brenntag offers a complete line of inhibitors that can help optimize heat transfer processes. Our full line of Dispersants and Antiscalants keep scale at bay across a wide variety of industrial applications. heat transfer is compromised by scale formation, call your local Brenntag Water Specialist to help provide a solution. dispersants antiscalants formation, not
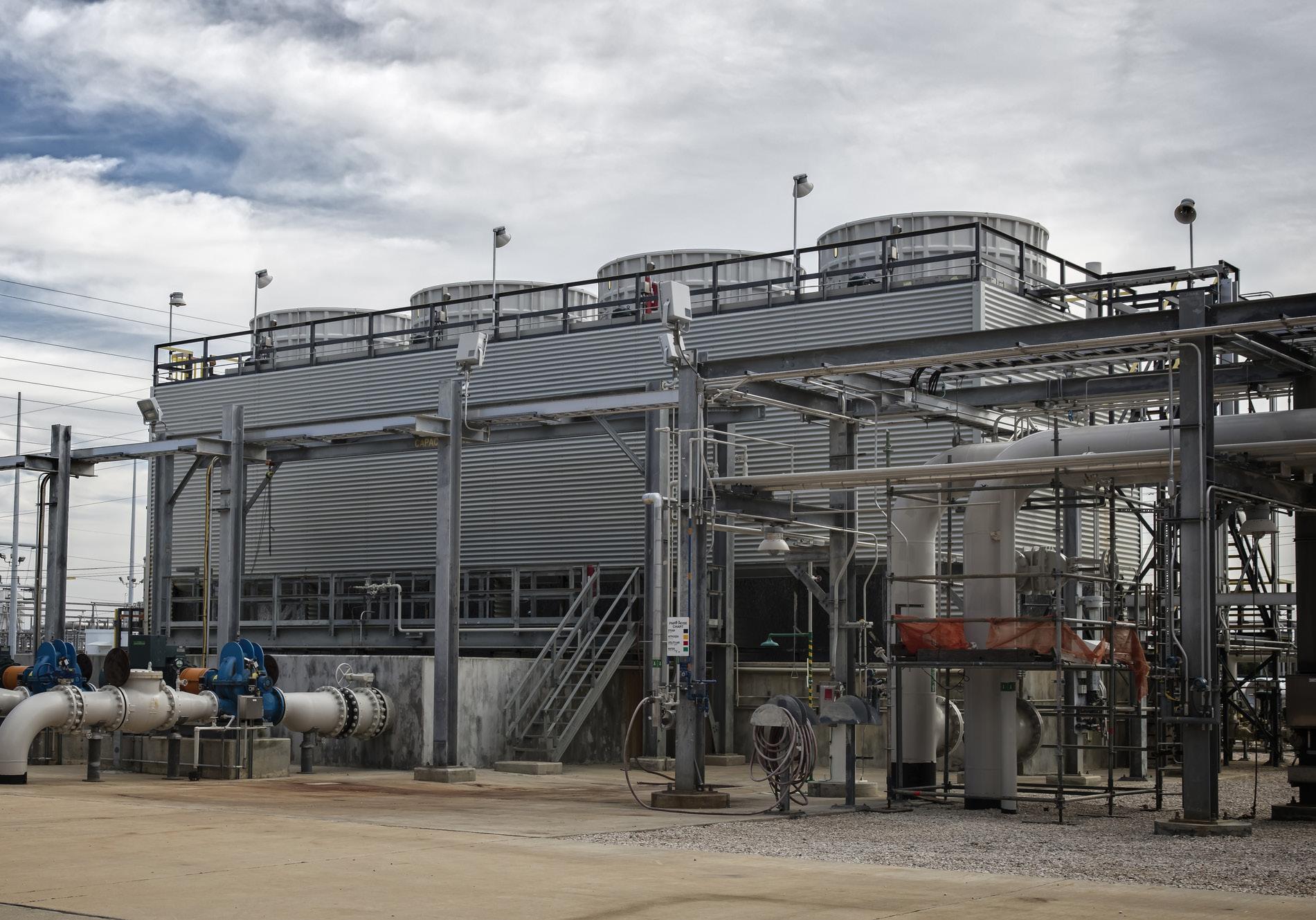
■ LumaTreat™ tagged polymers ■ Specialty homopolymers ■ Non-phosphorus containing polymers ■ Polyacrylates ■ Polymethacrylates ■ AA:AMPS Copolymers ■ AA:MA Copolymers ■ Terpolymers Scan to view the
and
If
process flow
contactus@brenntag.comwww.brenntag.comoffering. Inhibit scale
Figure 5 demonstrates how CFUs can vary due to the source of the Legionella cells while the quantification of genetic material is not influenced by the condition of the cells.
Figure 5: Genesis of CFU versus GU.
Legionella are associated with biofilm and mostly located within biofilm. Sloughing of biofilm is the major source of Legionella going into the water for most systems. If steady state is reached, the sloughing of biofilm can be thought to be more consistent while a certain biofilm thickness is maintained, but most likely there are events over the minutes, hours, days, and weeks that inconsis tently release biofilm. The concentration of Legionella that are contained in the water that is aerosolized into
Reasons that the culture method is still used:
PCR is a achievegeneticamplifiesmethodmolecularthattargetmaterialwithspecialenzymes,primers,andreagentsandaninstrumentcalledathermocyclertohighenoughlevelssothattheycanbedetected.
20 the ANALYST Volume 29 Number 3
Culture method is useful to trace origin of an outbreak by genetic analysis.
PCR microproof® Legionella – GU Reagent D

Plate Count – CFU X
Key Benefits of Modern qPCR and Why It Is Better Than the Culture Method for Legionella Testing continued

It takes time and effort to make changes to established procedures and guidelines.
The capabilities of the modern qPCR method are not yet well known.
single cells Live VBNC dead infected amoeba biofilm chunk other bacteria
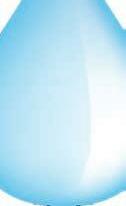
The CFU results are an established convention, and response actions have been provided within written procedures.
Drawing courtesy of BIOTECON Diagnostics Co.
Other Considerations for Legionella Testing and Control of Legionnaires’ Disease
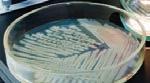
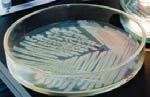

Almost universally, the culture method is recognized as a very poor and problematic procedure and is still ironically called the “gold standard” by some, but it is also recognized that the time delay for results adversely affects human health.
Where waters are more complex and a series of screenings are required and the plating of isolates are performed, the test can be labor Resultsintensive.arereported in CFUs, which can have very arbitrary value since the CFU is a million or more cells on the growth media, but it does not consider the genesis of the colony. Each colony could have grown from quite a different number of initiators of the colony. It could have grown from one single Legionella cell, a group of agglomerated cells, a large group of cells clinging to a suspended solid, one or many cells within an amoeba, or a portion of a detached biofilm containing perhaps thousands of cells.
Table C looks at some of the major contributions to disruptions to steady state and how that can influence bacteria levels.
Water changestreatment Biocides, surfactants, other chemical concentrations changes



Water variationssupply Bacteria concentrations or loading rate changes


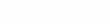


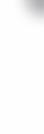
Nutrient loading Biofilm growth rate
Is the water sample point appropriate to the point where water is aerosolized and related to the risk of Legionella bacteria being contained in the water droplet?
21 the ANALYST Volume 29 Number 3
System Parameter Cause or Consequence to Steady State
Does the system have a steady state condition, or could there be major disruptions?
The value of testing in a water management plan is highly dependent on how good the plan is and how well it is implemented. If there is no water management plan for preventing Legionnaires’ disease, then there is little value for water testing. Where a good plan exists and is followed, and some level of steady state exists, the testing is more valuable for confirmation and prevention of Legionnaires’ disease.
Table C: Disruptions to Steady-State Conditions
Water hammer Pump or valve operation can rattle pipes and release biofilm
5-micron (µm) water droplets would vary considerably based on the specific dynamics, system designs, and retention times.
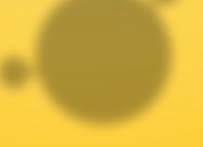
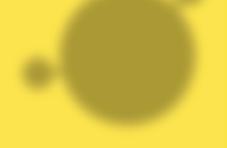
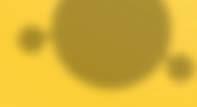
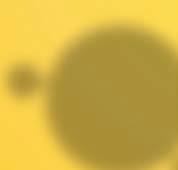
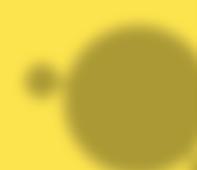

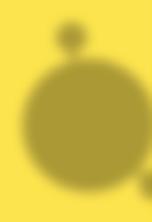
What if the Legionella source is contained in biofilm within the return header to the cooling tower and
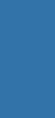


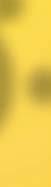


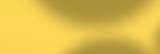



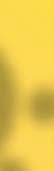

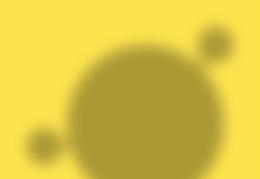





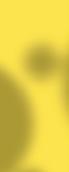
Flow rate changes Low flow—biofilm growth; High flow— biofilm releases
Temperature Affects growth rate of biofilm
Intermittent use of systems Allows stagnation, adding variability to total system
How valuable is any testing method if there is infrequent

testing, no consistent steady-state condition, a poor water management plan, and no effective critical control points? In non-steady-state systems (which is probably most systems), sampling and testing every hour or 24 hours would likely show high variability with both culture and qPCR methods.
Questions to Consider
Example 1
Key Benefits of Modern qPCR and Why It Is Better Than the Culture Method for Legionella Testing continued


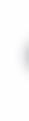
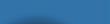

Is the probability of successfully culturing a single cell less likely than successfully culturing a larger group of cells? Or put another way, which approach could distort the total CFU number?
Should there be a correlation between risk of disease from the amount and form of Legionella bacteria inhaled?
How is facility liability and potential litigation affected? As a modern, elite qPCR method becomes more well-known and implemented, it is possible or even likely that those using an inferior method such as culture could be at greater liability risk in litigated cases of Legionnaires’ disease.
Pitchman: Well, no, not really. Legionella are very hard to grow, and there can be so many other types of bacteria there, so we need to do pretreatment steps that probably kill a lot of the Legionella or stress them so much that they will not grow on the agar. They are viable but not culturable.
Key Benefits of Modern qPCR and Why It Is Better Than the Culture Method for Legionella Testing continued
Is there a correlation between the ability to culture a single cell or small group of cells that could be contained in the aerosol and the most problematic form causing disease?
Pitchman: I have a new test method that I think would be useful for testing for Legionella bacteria and should be part of a plan to reduce the risk of Legionnaires’ disease.
Right now, there does not seem to be a correlation between CFU detected in a water supply and risk of disease. Considerations include:
Shark Tank Routine Pitching Culture
Committee: Are the viable but not culturable bacteria dangerous, and could they cause Legionnaires’ disease?
If the bacteria are grouped in the system water, do they get separated in the testing procedure? Alternatively, could some cells get grouped in the process? How would that affect risk correlation of CFU to risk of acquiring Legionnaires’ Disease?
Which Legionella cells are most likely to be contained in aerosolized 5 µm or less water droplets, and how does that relate to the CFU determined in the bulk water sample that was tested?
What if qPCR Was Established and Culture Was the New Method?
22 the ANALYST Volume 29 Number 3
Example 2
Does the sample point relate consistently to the point where the water is aerosolized?
Committee: How does it work?
To implement change, sometimes it makes sense to poke fun at the existing condition and turn the table upside down. In an attempt to do that, it appears absurd to think that we would implement culture as the best available technology for Legionella testing if modern qPCR had been in use since 1977 instead of the culture method. The absurdity may be recognized where someone tries to pitch culture as a new proposed method in an effort to try to get funding or acceptance. To illus trate, here is a sample what such a discussion might be like on the well-known Shark Tank TV program.
Pitchman: Well, you take a sample of water, filter it to concentrate the bacteria, resuspend what was filtered, plate it on a culture media and grow the bacteria, and then count the colony forming units.
How does the procedure of filtering the sample onto 0.45-µm paper and then resuspending the sample into a buffer solution affect the grouping of bacteria and resul tant CFU?
Does an aerosol most likely contain one or several Legionella cells that are 1 µm in diameter and up to 20 µm long, and are these harder to culture than larger groups or biofilm fragments.
sampling is done from the cold well sump or to supply water after filtration and treatment?
Committee: So, one Legionella bacteria in the water will create one colony-forming unit—right?
Pitchman: Well not exactly. A colony-forming unit can be created by one cell, or two, or three, or 10, or 100, or even 1,000. A colony-forming unit could be created by a fragment of biofilm that may have even thousands of Legionella bacteria cells contained in it.
Committee: Oh, I see. But at least it does detect all the Legionella in the water sample?
Committee: Hmm, this sounds like you might have to spend quite a bit of time to finally get an answer?
Committee: So, let me get this straight, cells that can be exposed to the culture material and still are viable to grow, will show up as a colony-forming unit on the plate and can be recognized and counted as a Legionella bacteria?
support growth. That way we can confirm that it really was Legionella.
The test can find Legionella in the water but may miss many or even most.
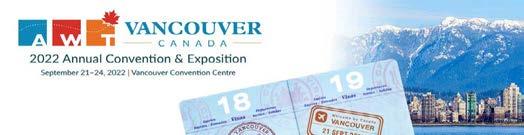
23 the ANALYST Volume 29 Number 3 SANIKILL and SaniWare Treatment and control The patented SANIKILL technology now combined with SaniWare water quality monitoring Expandpanels! OPPORTUNITIES!your Visit www.sanipur.com - sales@sanipur.com - 484-351-8702 COME VISIT US AT BOOTH #152
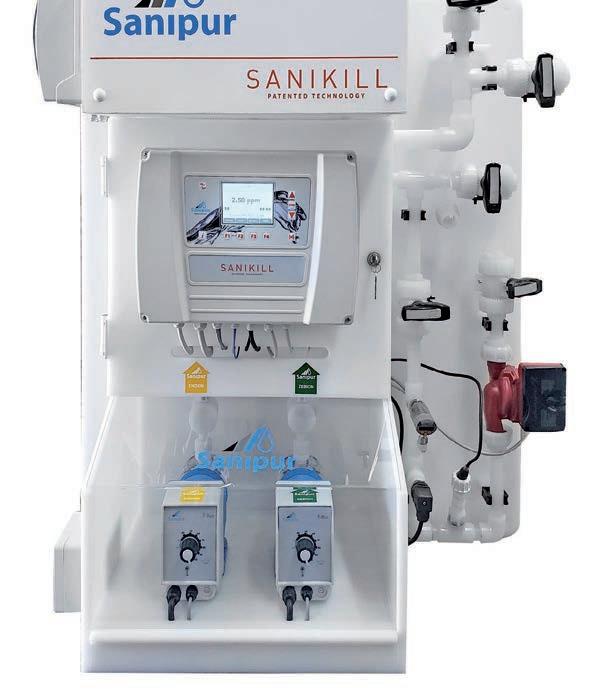

Pitchman: Yes, but it is really dependent on the water sample and the matrix of that water. We often might have preliminary indication after three to seven days, but some samples will take 14 days or longer.
Key Benefits of Modern qPCR and Why It Is Better Than the Culture Method for Legionella Testing continued
Pitchman: Oh no. There are other steps to try to find the specific species.
Pitchman: Well, I guess so. Yes, probably. That is a concern.
Committee: Are you kidding? I’d have to wait up to 14 days compared to 4 hours? You can probably recognize the different species of bacteria that are growing as colo nies though, right?
Committee: So, the method grows all the Legionella in the water except those that we kill or inhibit from growing?
Pitchman: Well, not quite. Often, bacteria that are contained within amoeba do not culture either, but maybe they do if they make it out of the amoeba, and in that case could grow.
Pitchman: Sort of, but not exactly. In the end, I must admit that the recovery rate can be quite low, and also inconsistent. It takes a certain skill to recognize a Legionella colony and to distinguish it from non-Legio nella colonies, so we take an isolate sample from a repre sentative amount of the colonies that grew and replate on two different types of other plates. One plate type can grow the Legionella and the other typically will not
Committee: So, let me understand this so far:
It takes seven to 14 days to get an answer.
2. Lee, J.L.; Lai, S.; Exner, M.; Lenz, J.; Gala, V.; Casati, S.; Hartemann, P.; Lück, C.; Pangon, B.; Ricci, M.L.; Scaturro, M.; Fontana, S.; Sabria, M.; Sanchez, I.; Assaf, S.; Surman-Lee, S. (2011). “An International Trial of Quantitative PCR for Monitoring Legionella in Artificial Water Systems,” Journal of Applied Microbiology, pp. 1032-1044.
• Provides results in 4 hours of lab work
Key Benefits of Modern qPCR and Why It Is Better Than the Culture Method for Legionella Testing continued
Conclusion
• Consistent
An important step for acceptance and greater awareness would be for the AOAC International (Association of Official Analytic Chemists) to approve the qPCR method through their development process. On its website, it states that “approved methods undergo rigorous, systematic, scientific scrutiny to ensure they are
And it is not really useful in quantifying or giving consistent results.
highly credible and defensible—and can be used with confidence by industry, regulatory agencies, research organizations, testing laboratories, and academic insti tutions.” This would allow agencies, organizations, and end-users to have confidence in the method and results.
Dave Christophersen is owner of Dave Christopherson Consulting LLC and a senior consultant to AP TECH, based out of West Chester, Ohio. He has 45 years of experience in the water treatment industry, including managing water treatment programs for industrial sites for boilers, cooling systems, wastewater systems, and membranes. Having worked at Olin, Betz, Crown Solutions, and Veolia, Mr. Christophersen’s water treatment experience includes technolo gies for wastewater treatment, boiler water treatment and pretreatment, cooling water, and membrane technologies. He provides training, business, marketing, and technical support to the water treatment industry. Mr. Christophersen may be reached at christophersendave@gmail.com .
The Legionella are extremely difficult to separate from background flora and are hard to culture and grow and then identify, so it can be quite dependent on a laboratory’s skill and experience.
4. CDC (January 2005). “CDC Laboratory Guidance for Processing Environmental Samples,” National Center for Immunization and Respira tory Diseases, Pneumonia Response and Surveillance Laboratory, U.S. Department of Health and Human Services, Centers for Disease Control and Prevention, Atlanta, Georgia.
References
• May be more useful in linking bacteria concentration to risk of Legionnaires’ disease
• Is cost effective
Since the discovery of Legionella bacteria, the culture method has been used. Even with improvements, it remains a very difficult culture test for capturing, growing, and identifying Legionella bacteria in a water sample. A rather high level of experience is required to make some of the subjective decisions described in standard procedures, it is imprecise, does not accurately quantify, and takes days for results.
Increased awareness of modern qPCR capabilities should lead to it becoming the preferred laboratory test method for Legionella bacteria. For most regular monitoring of water systems, Legionella action and alert efforts, or remediation processes, modern qPCR testing should improve water safety.
3. Collins, S.; Stevenson, D.; Walker, J.; Bennett, A. (2017). “Evaluation of Legionella Real-Time PCR against Traditional Culture for Routine and Public Health Testing of Water Samples,” Journal of Applied Microbiology, pp. 1692-1703.
The colony-forming unit is a colony that results from the genesis of many possible combinations of Legionella groupings, so it doesn’t represent any consistent amount of Legionella.
• Precise
Statements made in publications such as AWT’s 2019 Legionella: A Position Statement and Guidance Document, and the 2020 publication Management of Legionella in Water Systems, from the National Academies of Sciences, Engineering, and Medicine, all need to be updated to recognize the full capabilities of today’s qPCR method and that qPCR could replace culture for most moni toring and mediation work.
• Does not require much lab training
• Can identify Legionella species, Legionella pneumophila , SG-1,and SG-15 all in one step
1. ISO (May 2017). “Water Quality—Enumeration of Legionella,” 2nd ed., International Standard Organization (ISO) 11731, Geneva, Switzerland.
5. Lowenstein, M.; Benzinger, J. (September 2021). “Comparative Evaluation of Three Modern PCR Methods for Quantitative and Qualitative Analysis of Legionella spp. for Routine Monitoring of Premise Water System Samples,” presentation at AWT Annual Convention & Exposition, Providence, Rhode Island.
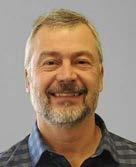
24 the ANALYST Volume 29 Number 3
qPCR on the other hand is:
Pitchman: That about sums it up, but we think calling culture the Gold Standard could help get it better accepted.
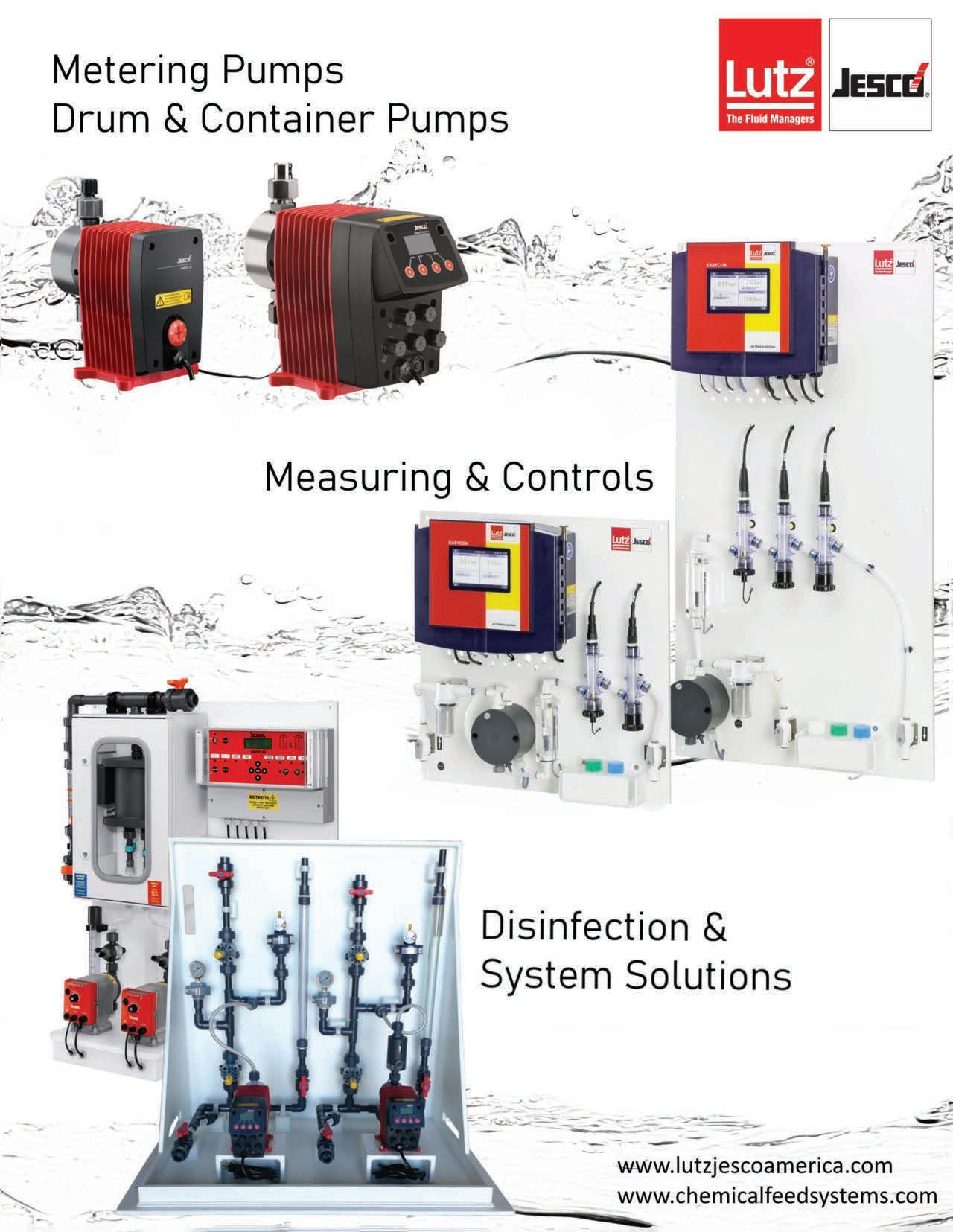
Part 1: How Does Water Sustainability Impact Oil and Gas Water Treatment?
Colin Frayne, CSci, CChem, CEnv, FRSC, CWT, Aquassurance, Inc.; and Barry B. Ekstrand, P.E., Finoric LLC
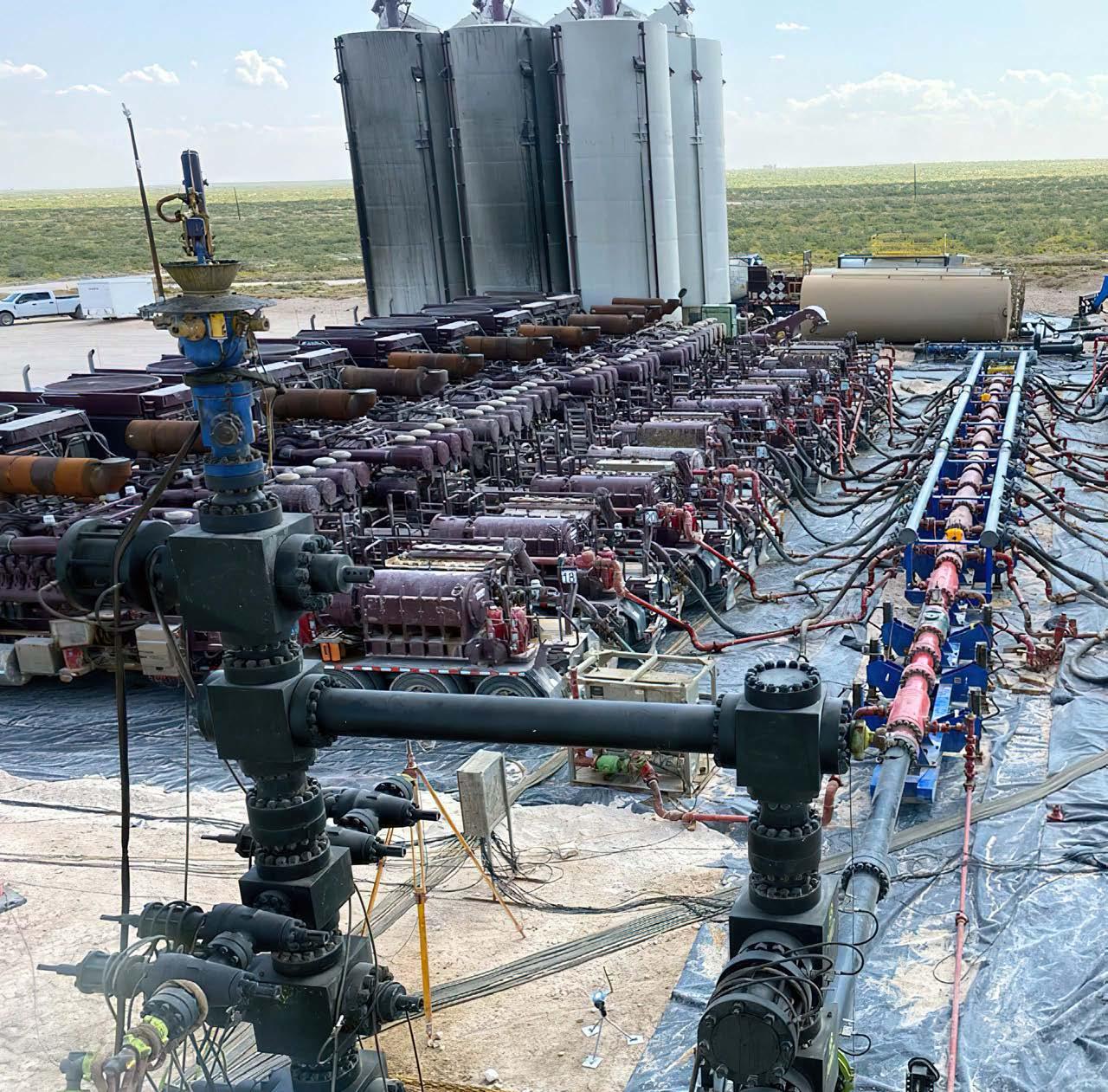
27 the ANALYST Volume 29 Number 3
Editor’s note: The authors originally developed this two-part article series as a white paper in collaboration with the oil and gas performance chemicals and services company Finoric LLC of Beasley, Texas. Part 1 primarily looks back from historical practices to the current day, where less thought was given to the scaling tendencies of reinjected (and usually diluted) recycled brines, and the focus was (and currently still is) mostly on new well completion and fracture fluid chem istries. Part 2 primarily looks forward to an expansion of remedial stimulation of existing producing wells, and a future focus on the expansion of production brines and production chemistry work.
This article series examines hydraulic fracturing in oilfields for achieving higher yields of oil and natural gas. There can be different views on the spelling of the shortened term for “fracturing and fracture.” The generally accepted abbre viation for “hydraulic fracture” or “fracturing” is “frac.” Fracturing can be abbreviated as “frac’ing” or “fracing.” However, sometimes this term is referred to as “frack” or “fracking.” That said, generally those in the oil and gas industry will use the first spellings when referring to this practice because “frac” is short for fracture. For the purposes of these articles, we will use the spellings of “frac” and “frac’ing” to refer to “fracturing.”
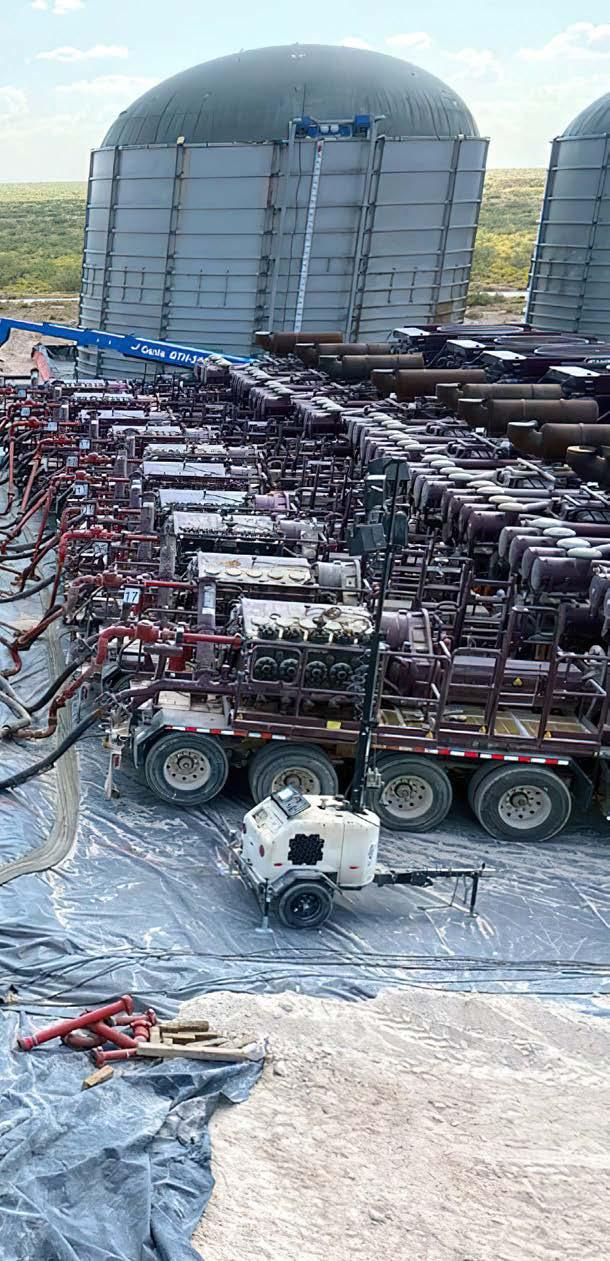
Abstract
As a result of global population growth and an increased demand for energy and good quality water, the demand and supply positions for vital resources (especially water) varies considerably from country to country; but globally, freshwater withdrawals have increased six-fold over the last 100 years, and we all face an uncertain future due to critical worldwide water shortages and quality prob lems. In view of this crisis, this article series focuses on the oil and gas industry and its relatively large usage of water (e.g., for hydraulic fracturing fluids). It provides an overview on the types of standard water treatment separation processes available to implement the three Rs (i.e., Reuse, Recycle, and Reclaim) and aims to further reduce water consumption. Additionally, these articles provide some guidance notes on the benefits, limitations, and application of phosphonates, polymers, and other waterside chemical inhibitors and performance addi tives for selection by water treatment practitioners when confronted with more complex brine water chemistry.
Increased Demand for Energy and Good Quality Water
Hydraulic fracturing treatments aim to stimulate (increase the productivity) of low-permeability oil and gas wells by creating a propped fracture (a crack in the reservoir rock) extending deep into the reservoir from the wellbore. The fracture is created by pumping a hydraulic fluid at high pressures that cause the reservoir rock to fail, creating the fracture at the wellbore and then extending it into the reservoir. Sand or other prop ping agents are pumped into the fracture during the frac treatment, which holds the fracture slightly open after the frac job is completed. The resulting propped fracture is highly conductive, which allows reservoir fluids to flow into the wellbore at much higher rates than those of nonstimulated wells.
year (nb: 1 cubic meter = 264.172 U.S .gallons). However, it is clear that most conventional renewable water resources are declining in both output and quality in many countries as a result of population increases. Today, water shortages are affecting more than 3 billion people, and the amount of fresh water available per person has plunged by a fifth over the last two decades (4).
In spite of the politics of climate change and activist calls for a reduction in the world’s dependence on fossil fuels—in favor of nuclear energy, solar and wind power, and other sustainable energy sources—global demand for crude oil (including biofuels) has in recent years been continuously climbing by approximately 10% per year. In 2006, daily global crude oil demand was 85.3 million barrels per day (MMB/D). At the time of the writing of this article in mid-2022, daily global crude oil demand was estimated to be 96.5 MMB/D, and the estimate for 2026 is 104.1 MMB/D. The only decrease in demand in recent history was in 2020, when usage dropped to 91 MMBD due to the economic and mobility impacts of widespread shutdowns across the world due to the COVID-19 pandemic (2). Specific to the United States, the Energy Information Administration (EIA) estimates that about 2.70 billion barrels of crude oil were produced directly from shale (tight) oil resources in 2020. This is equivalent to about 7.37 MMB/D and equal to about 65% of the total U.S. crude oil production, which shows how important unconventional resource development of shale oil (and gas) production is to the total annual output of U.S. hydrocarbon production (3).
Part 1: How Does Water Sustainability Impact Oil and Gas Water Treatment? continued
Relationship Between Hydraulic Fracturing and Water
28 the ANALYST Volume 29 Number 3
In the United States, water use in 2015 was estimated to be about 322 billion gallons per day (Bgal/d), which was 9% less than in 2010. The 2015 estimates put total withdrawals at the lowest level since before 1970, following the same overall trend of decreasing total withdrawals observed from 2005 to 2010 (5). This lower (i.e., improved) water withdrawal position is likely due to significant changes in agricultural and horticultural irrigation practices, including use of surface-and subsur face drip irrigation techniques.
Demographics tell us the number of people in the world increased more than four-fold during the 20th century, and so we may wonder what humanity’s future will look like (1). Unfortunately, beyond trends on future popu lation growth, it remains extremely difficult to predict with much certainty the future of the world’s inhabi tants. However, it is clear that the threads of mankind are closely intertwined with our impact on the natural environment; pandemics and other catastrophic events; fertility rates; and access to space, food, health services, education, and other resources. Therefore, it seems very unlikely that mankind’s demand for energy and good quality water will ever diminish.
Additionally, to reduce demands on the fresh water use, we see water/wastewater recovery, recycling, reinjection, purple pipes, and other water reuse techniques being increasingly practiced by municipalities and industries of all types. We are also seeing an increase in the commer cial application of a wide range of modern water and wastewater treatment technologies that barely existed 30 or 40 years ago—particularly those processes that incorporate polymeric membranes, such as wastewater membrane bioreactors (MBR), seawater reverse osmosis (SWRO), and electrochemical deionization (EDI).
The demand and supply positions for vital water resources vary considerably from country to country, but globally, freshwater withdrawals for agriculture, industry, and domestic/municipal use have increased six-fold over the last 100 years or so, with a sharp rise from the 1950s onward. However, since 2000, the annual increase in global water withdrawals appears to be plateauing, or at least decelerating, at around 4 trillion cubic meters per

30 the ANALYST Volume 29 Number 3
By the mid-2000s, oil and gas shale drilling was growing rapidly. Shale frac designs deviated from the historic frac design approach in several significant ways:
The cost of disposing of these large volumes of water
Today, shale frac job sizes have grown, along with wellbore lengths and number of frac stages per well, such that tens of millions of gallons of water may be used for the completion of the wells on a single drilling pad. As the demand for larger and larger volumes of water grew, a number of issues became problematic and critical:
The cost of sourcing these large volumes of fresh water became significantly large.
There are a larger variety of available chemical additives that allow for easier adjustment of the waterbased frac fluid physical properties.
Part 1: How Does Water Sustainability Impact Oil and Gas Water Treatment? continued
For many years, each frac job was designed with the specific well, formation rock properties, and other reservoir parameters in mind. This effort, along with a continual focus on maximizing the commercial value of
The viscosity of the base fluid would not be raised, so no viscosifiers/gelling agents were added.
Correlations were seen between larger frac job sizes and higher well productivity, leading to another large uptick in treatment volumes.
the frac treatments, led to treatment volumes growing significantly over time. By 1980, frac jobs using more than 100,000 gallons were common, and very large treatments of ~1 million gallons were sometimes occur ring. Treatment volumes continued to grow throughout the 1980s and 1990s and into the early 2000s, with most frac designs incorporating relatively expensive high-vis cosity fluid systems. These fluid systems were designed to suspend the frac sand as it was being pumped so that it would not settle out, but rather, would be carried far into the fracture so that the fracture would be propped open deep into the reservoir.
Because viscosity was low, enhanced sand suspension was lost. As a result, the frac jobs needed to be pumped in high turbulent flow (i.e., at much higher pumping flow rates). Use of polyacrylamide-based friction reducers (FR) to reduce the treating pressures of the frac jobs grew exponentially.
In some areas, access to the necessary volumes for the frac jobs became increasingly difficult to find.
Well completions increasingly moved into a “manufacturing mode” where the same frac design was pumped on each job. Operational efficiency (amount of time to pump each frac job) became a primary focus.
Water is a great solvent that can carry multiple desired chemistries into the reservoir.
Water is benign and much safer to work with. Water is generally far more plentiful and available. Water usually has a much lower cost.
The first frac job was pumped in 1947, and the early frac jobs were just a few hundred gallons in volume—a miniscule size by today’s standards. Just about every fluid imaginable has been used as the base fluid for a frac job, with napalm (gelled gasoline) being used on the first job, and also including crude oil, gelled oils, inorganic and organic acids, acid/water/oil emulsions, and foams, but the vast majority of frac jobs have used water—both fresh and brine, and both gelled and ungelled—as the base fluid. Not surprisingly, water brings a number of benefits over the other alternatives:
A fundamental design concern for frac treatments is compatibility between the frac fluid and the reservoir rock mineralogy and reservoir fluids. For example, in the presence of fresh (non-brine) water, smectite and mixedlayer clays will swell, while illite and kaolinite clays will break apart and migrate. The result in each of these cases can be a significant reduction in reservoir permeability due to plugging of pore throats in the rock caused by these physical changes in clay structure. Creating an artificial brine by adding an appropriate amount of a compatible salt (such as potassium chloride or a “KCl substitute,” such as choline chloride) to the fresh water will reduce or eliminate these effects. Other potential concerns include dissolution and re-precipitation of iron compounds, precipitation of asphaltic sludge from the oil, deposition of paraffin (wax) from the oil, creation of emulsions with the oil, and creation of water blocks in the reservoir. Suffice it to say that ensuring compatibility between the water-based frac fluid and the reservoir is critical. Intuitively, the ideal frac fluid would be made with a base fluid that is from (or mimics the composition of) the native reservoir water.
The size of the frac sand being pumped became smaller due to lower terminal settling velocity and ability to carry it farther into the fracture before settling out.
31 the ANALYST Volume 29 Number 3
Given that the process of unconventional development, including hydraulic fracturing of shale for oil and gas production in the United States, is equal to about 65% of total U.S. output, there is no doubt that we are in a golden age for shale plays. The rise of North American shale oil and gas production has brought game changing predictions about supply and demand, and with it, key players with technologies and expertise to unlock previ ously inaccessible shale resources (6). The Independent Petroleum Association of America (IPAA) indicates that hydraulic fracturing has been safely used in the United States since 1947 and that more than 1.7 million U.S. wells have been completed using the frac’ing process. Indeed, the U.S. Environmental Protection Agency (EPA) has stated that unconventional oil and natural gas plays a key role in our nation’s clean energy future (7). for Legiolert and more results
The number and size of frac jobs pumped annually is expected to continue to grow in the coming years, which means that the water volumes required to make up the frac fluid will continue to increase. Effective treatment and cleaning of recycled frac and produced water for reuse in frac treatments will not only remain a critical
Rising TDS levels resulting from recycling may cause a reduction in efficacy of certain frac fluid components, such as FR. In some cases, dilution with additional fresh water to reduce the TDS below a particular threshold may solve the issue, while in other cases a change in FR chemistry may be required.
accurate Legionella
during flowback after the frac job—always a concern in the past—now became extremely high.
1.ReferencesLucasCE, Taylor TH Jr, Fields BS. Accuracy and precision of Legionella isolation by US laboratories in the ELITE program pilot study. Water Res 2011;45(15):4428–4436. doi:10.1016/j.watres.2011.05.030 2. Petrisek R, Hall J. Evaluation of a most probable number method for the enumeration of Legionella pneumophila from North American potable and nonpotable water samples. J Water Health. 2018;16(1):25–33. doi:10.2166/wh.2017.118 3 Spies K, Pleischl S, Lange B, et al. Comparison of the Legiolert/Quanti-Tray MPN test for the enumeration of Legionella pneumophila from potable water samples with the German regulatory requirements methods ISO 11731-2 and ISO 11731. Int J Hyg Environ Health 2018;221(7):1047–1053.doi:10.1016/j.ijheh.2018.07.006 4. Sartory DP, Spies K, Lange B, Schneider S, Langer B. Evaluation of a most probable number method for the enumeration of Legionella pneumophila from potable and related water samples. Lett Appl Microbiol. 2017;64(4):271–275. doi:10.1111/lam.12719 5. Barrette I. Comparison of Legiolert and a conventional culture method for detection of Legionella pneumophila from cooling towers in Québec. J AOAC Int 2019;102(4):1235–1240. doi:10.5740/jaoacint.18-0245 © 2021 IDEXX Laboratories, Inc. All rights reserved. • 2485785-01 • All ®/TM marks are owned by IDEXX Laboratories, Inc. or its affiliates in the United States and/or other countries. The IDEXX Privacy Policy is available at idexx.com. See the difference the Legiolert Test can make atidexx.com/legiolertdifferenceTheLegiolert ® Test is a more accurate culture test for Legionella pneumophila Spread plate methods are notoriously inaccurate, with up to tenfold variability in results for the same sample.1 Multiple peer-reviewed studies have confirmed that the Legiolert Test provides more accurate and consistent results.2–5 Ask
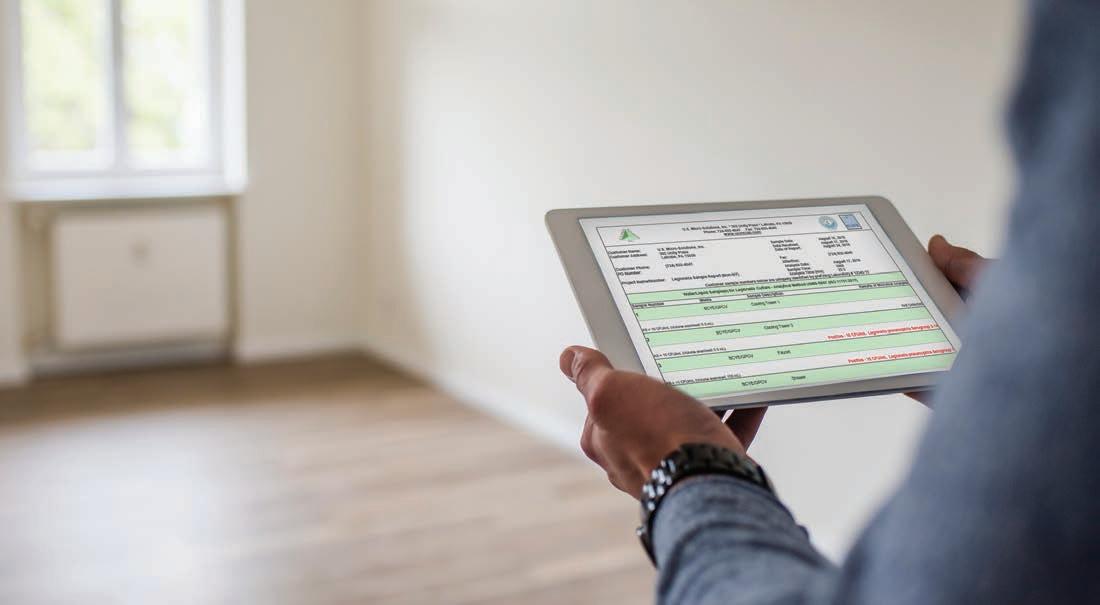
deliver
2485785-01 AWT Summer 2021.indd 1 6/6/21 9:24 PM Part 1: How Does Water Sustainability Impact Oil and Gas Water Treatment? continued
As a result, recycling and reuse of the previously used frac water and produced water became a necessity.
aspect of the frac job execution for years to come, but it will be a necessity and required enabler for economic and social viability of the drilling and completion of new oil and gas wells.
Wastewater Recycling
Recycling and reusing frac water and produced water ultimately means dealing with all of the challenges of effective water treatment: the need to clean up brine water containing high TDS and high TSS, at times along with dissolved iron, residual oil, residual chemicals, and/or contamination with bacteria.
This water reuse, recycle, reclaim focus is of significant business interest to both large and small service compa nies in the oil and gas and water treatment chemical/ equipment fields. These firms tend to operate in several specialist niche sectors and geographies within the global oil and gas support services market and may offer sepa ration processes, such as oil/water separation, evapora tive water recovery, or wastewater clarification. Specific performance chemical “packages” may be required, to perhaps include demulsifier s (treaters, droppers, and hybrids, etc. to destabilize/ break/ flocculate/ coalesce water-in-oil emulsions), reverse demulsifiers (to break oil-in-water emulsions), reverse emulsion breakers (REB) (to break complex water-in-oil-in-water [W/O/W] emulsions), as well as gas hydrate inhibitors, surfactants, antifoams, coagulants, flocculants, precipitants, piping corro sion inhibitors, and antiscalents
32 the ANALYST Volume 29 Number 3
However, oil and gas production obtained from shale plays uses a lot of water! Depending on the play, a well may require from 2 to 5 million gallons or more before comple tion, of which 80 to 90% is used for fracturing and only 10 to 20% will be typically required for drilling and other purposes (8). That is a lot of frac wastewater for poten tial disposal, and although the EPA advises us there are approximately 144,000 underground injection (disposal) wells for produced water (PW) disposal, some practices can possibly create problems. If injection volumes into disposal wells result in injection pressures that exceed the frac gradient of the injection formation, microfractures can be created that grow vertically into other formations that lie above or below the injection zone.
Additionally, note that during the sequential oil or gas recovery process, PW emerges as an associated byproduct, containing mainly formation water (FW) and a small portion of frac fluids as flowback. As an example, in the Permian Basin, the PW-to-oil ratio (PWOR) of shale wells is around three, and for all U.S. plays on average, more than 90% of the PW is naturally occur ring FW and connate/interstitial water. That is a lot of frac wastewater for potential disposal, and although the EPA advises us there are approximately 180,000 under ground injection wells for PW injection, some practices can possibly create problems.
Previously, chemistries for slick water generation, proppant support, and some limited water treatment for scale, corrosion, microbiological, and/or general fouling
Part 1: How Does Water Sustainability Impact Oil and Gas Water Treatment? continued
The Three R’s of Water: Reuse, Recycle, Reclaim
Currently, the preferred method for disposal of PW is through permitted Class II water injection wells, of which 20% are saltwater disposal wells and 80% are wells that are enhanced oil recovery (EOR) injection wells. These EOR injection wells include waterflood injection wells (i.e., injection of water to drive oil in the reservoir to producing wells), steam-injection wells (to
“Water, Water, Everywhere, Nor Any Drop to Drink”
For shallow injection wells, this could include forma tions that contain potable groundwater, resulting in risks of contamination to shallow groundwater aquifers. Another potential effect of overinjection is the creation of localized micro earthquakes being felt at the surface. With these potential negative impacts, it is clear that effective management of produced wastewater is criti cally important to ensure positive environmental, social, and governance (ESG) impacts result instead. Adequate numbers of local injection wells must exist and be avail able to ensure that wastewater disposal injection pres sures stay well below formation frac gradients.
to disposal of frac fluids is wastewater capture, treatment, and reuse—for new frac jobs, irrigation, cooling water, or other purposes. This recy cling practice has been growing year over year in output volumes. However, in view of the continuing global importance of oil and gas, produced by both conven tional and unconventional means, and the need to move closer to a water-secure and net-zero world, it is important during new well development and production to aim to use even less fresh water and associated chem istries. Thus, in the oil and gas industry, it is also neces sary to recover, treat, and reuse as much PW, FW, and flowback frac fluids and blends as possible.
–Rime of the Ancient Mariner, by Coleridge
thermally thin and drive viscous oils), and water alter nating gas (WAG) injection wells or simultaneous water and gas (SWAG) injections wells (both are techniques to improve the sweep efficiency of waterfloods or gas Thefloods).alternative
The Blender Matters
Private Label Blending Coast to Coast
QualiChem offers nationwide blending for private label products, supplied from our plants located in Salem, Virginia and Verdi, Nevada. We are now better positioned to provide our customers with industry-recognized benefits and services coast to coast.
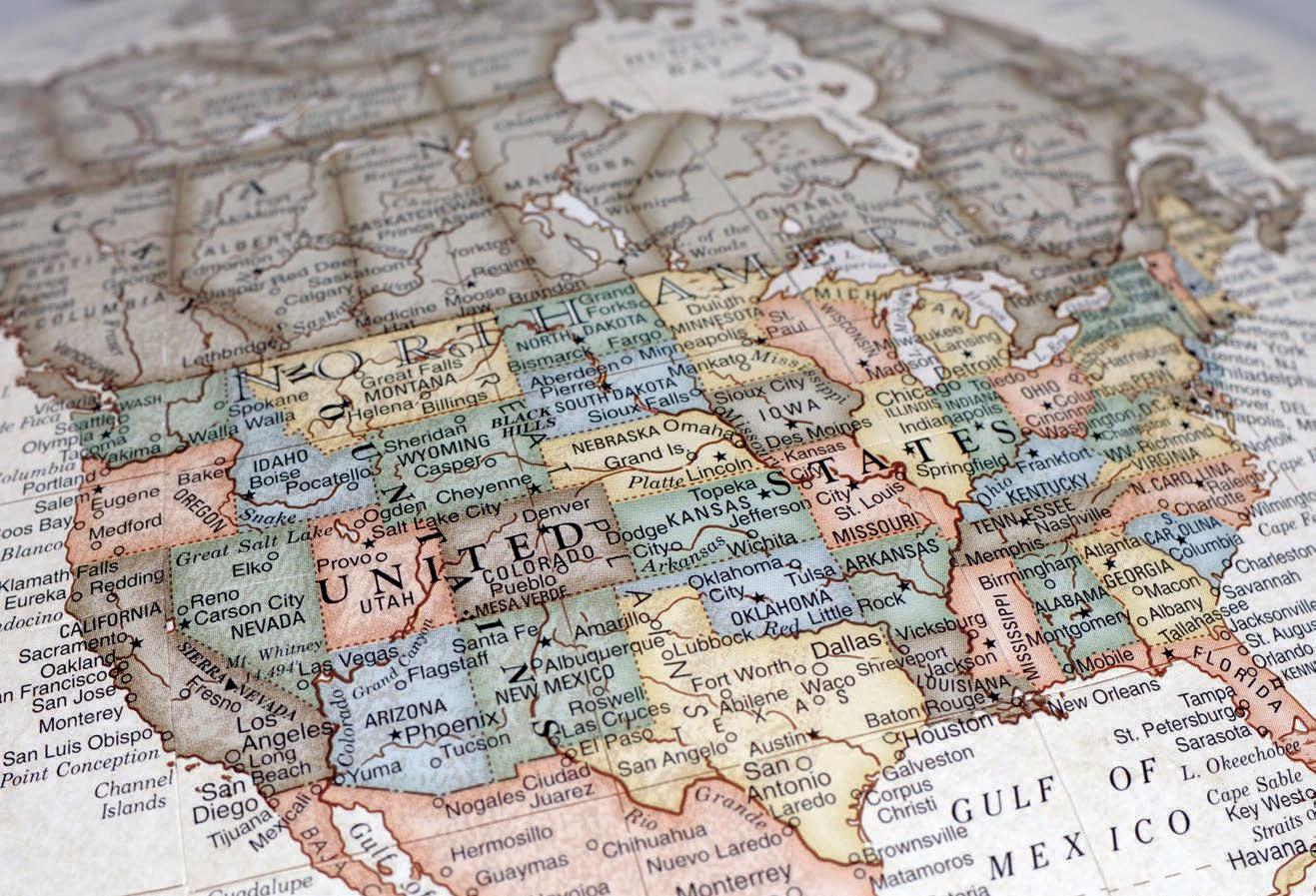
Just one more way we are demonstrating how…
AN
Please visit us at the AWT 2022 Annual Convention & Exposition – Booth #439. | www.qualichem.com ISO 9001:2015 COMPANY
No Direct Sales Precision LabelsCustomApplicationFormulatoryManufacturingExpertiseSupportGHS-CompliantandSDSs 800.296.9102
SUPPLIER OF THE YEAR
Nearly everything injected into a well is foreign to it, so there is a need to fully understand the likely impact of fluid constituents on the rock and its associated envi ronment. This means that a comprehensive analysis of all fluid interactions with the formation rock and its environment is the first need. It is well understood that produced water quality varies from play to play, and no single technology exists that is best for treating all produced waters in all operating areas, such that it can be recovered for blending or direct reuse. Additionally, operators understand that to produce a laboratory anal ysis of water quality and contaminants is not particularly difficult, but its interpretation and what this ultimately means in terms of slick water and other frac fluid chem istries can be challenging. Here are some considerations:
What is the best way to implement any specific frac job using fresh or recycled water?
3. Gelling agent cross-linker: Typically, zirconium, titanium, or borate-based. These create or improve the polymer network and system viscosity. Uncrosslinked guar-based polymers (commonly called “linear gels”) may become thinner with an increase in temperature, so a cross-linker can aid viscosity stabilization.n* For example, 0.2 to 2.0% of potassium chloride (KCl) or substitute in the base water; 5 to 15% or so of fracturing acid employed (usually hydrochloric acid [HCl]); and the many tons of varying size, shape, and strength of crystalline silica sands or ceramic proppant (of typically, 0.1 to 0.2 mm diameter).
4. Slick water friction-reducer (FR): Fracturing fluids need sufficient viscosity to create and open a fracture but must also have a low friction coefficient. Linear
How can the answers to these questions help to implement the concepts of Reuse, Recycle, and Reclaim?
What types of processes may eventually be required to treat the large volumes of produced water?
34 the ANALYST Volume 29 Number 3
What chemicals are present in the frac fluid? Frac fluids potentially contain a wide range of additive chemistry
Service companies offer expertise in working with their arsenals of complex (and now usually more eco-friendly) chemistries and formulations in order to modify produced brines for reuse as frac fluid bases. Some service firms may also be active with remedial stimula tion of existing producing wells, which traditionally has been a smaller focus for business development opportu nities but is expected to grow in the future. Similarly, growth is also expected for novel or “green” produc tion chemistries, and their application in optimizing repurposed brines and other industrial waters for reuse. However, consideration of the formation rock surfaces and mineralogy is very important when formulating new chemical treatment products.
products that vary in composition from play to play, such that each additive is itself a formulation of performance chemistries, collectively providing a task-specific compo nent of an overall fracturing fluid program. Beyond the addition of primary ingredients,* the total formulated performance additive packs may comprise perhaps 0.3 to 0.75% by volume (3,000 to 7,500 milligrams per liter [mg/L], or ppm) of the base frac fluid.
inhibition were typically primarily focused on treating a wide range of fresh waters, with perhaps less emphasis being given to treating the scaling tendencies of rein jected (and usually diluted) recycled brines. This focus is changing, and more applications expertise is often now available for managing the native reservoir brines that will be produced in the future.
Chemistry additive components for hydraulic fracturing fluids may include some or all of the following materials:
1. Surfactant: Used to reduce oil/water surface tension. Example: a poly(ethylene glycol) methyl ether (PEG methyl ether) or similar.
2. Gelling agent: Typically, guar gum or a derivatized guar-based polymer such as hydroxypropyl guar (HPG) or carboxymethyl hydroxypropyl guar (CMHPG). Other polymers that may be used include hydroxyethyl cellulose (HEC) and xanthan gum. In all of these cases, the purpose of the gelling agent is to increase the frac fluid viscosity and help support and carry the proppant. Nonderivatized guar gum is used in the vast majority of water-based frac jobs requiring significant viscosity. Other types of gelling agents include those for oil-based frac fluids, such as phosphate ester surfactants (e.g., dialkyl phosphoric ester) or phosphorus-free gelling agents, and may be used to recover or enhance production output.
Part 1: How Does Water Sustainability Impact Oil and Gas Water Treatment? continued
35 the ANALYST Volume 29 Number 3
7. Corrosion inhibitor: Typically, long-chain ethoxylated fatty acid alkylamine film formers are used to reduce the corrosion resulting from acids being pumped down steel casing and tubing (pipes) that make up oil and gas wells.
Since it is desirable to achieve a higher propped frac length (that is, to pump the frac sand grains farther into the fracture from the wellbore before settling out), the frac fluid pumping rate must be very high (typically 80 to 140 U.S. barrels per minute [bpm]) on shale frac jobs in order to achieve adequate propped frac length. At these pumping rates, friction pressure becomes high, and friction reducers are necessary to lower the frac job pumping pressure. In some cases, a lightly gelled linear guar is used, but FR and HVFR are generally preferred because they are able to lower the friction pressure to a greater degree at a lower cost. FR and HVFR can lower the friction pressure by 60 to 80%, depending on the water salinity and other chemical presence. FR and HVFR chemistry are typically based on polyacrylamide (PAM) or PAM/AM copolymers.
US Patents #8431022 & #9962631

5. Live breaker: Ammonium persulfate [(NH4)2 S2O8] and other oxidizers break the polymer network and reduce the viscosity of a fracturing fluid (ideally) following the end of each frac stage to help flow the well back. The breaker oxidation reaction speeds up significantly with increased temperature and increased breaker concentrations, so designing an optimized breaker schedule for the specifics of each frac job is desirable.
The T²-Max® DAF Thickener handles high mixed solids flows without sacrificing separation performance.

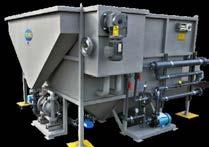
The Nx²JEM® DAF utilizes key hydraulic flow and laminar engineering principals to achieve high volume separation.
The HD²XLRator® DAF design encompasses the full array of newly advancedinnovations.technological
Contact PEWE at: 360-798-9268 www.pewe-usa.com
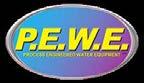
gels typically generate 12 to 18 centipoises (cPs) of viscosity, where crosslinked gels can generate viscosities of 500 to 4,000 cPs or more. However, for many unconventional shale formations, low viscosities of only 1 to 5 cPs may be all that is required and desired, although in some cases a high-viscosity friction reducer (HVFR) may be used to generate viscosities in the 8 to 13cPs range. In either case, FR or HVFR yield relatively low frac fluid viscosities. Because shale frac designs show a preference for low viscosities, the terminal settling velocity of the frac sand particles is relatively high and results in the frac sand settling out quickly in the typical shale frac design.
6. Encapsulated breaker: To ensure that the breaker does not reduce frac fluid viscosity too early, an encapsulated breaker can be used. An encapsulated breaker consists of a time-release coating or encapsulation of ammonium persulfate
9. Iron inhibitor: Perhaps control here might also be served by the scale inhibitor/dispersant, or via a watersoluble ethylenediaminetetraacetic acid (EDTA), gluconate, terpolymer, or alternatively, by imidazoline film adsorption. In combination with pH control
Part 1: How Does Water Sustainability Impact Oil and Gas Water Treatment? continued
WastewaterDAFTreatment:Innovation
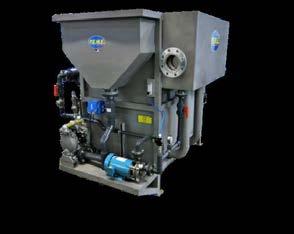
[(NH4)2S2O8] that results in a slower release of the oxidizing breaker. This allows the designed concentration of oxidizer to reach the tip of the fracture at full strength before releasing, so the entire fracture sees a uniform viscosity degradation after completion of the frac job.
8. Scale inhibitor: Typically, a copolymer and/ or a standard phosphonate, or perhaps a diethylenetriamine (DETA) phosphonate, are deemed suitable for management of alkaline earth salts and scales such as calcium carbonate, barium sulfate, and others.
As discussed earlier, following frac jobs, produced water containing both formation water and flowback water is most seen, with the proportion of formation water increasing over time. It is common to find the amount of frac fluid volume recovered to be very low, with a significant amount of the injected volume being “lost” to uptake/absorption forms of inhibition and/or other mechanisms in the formation.
12. Demulsifier: Perhaps an EO block copolymer, ethoxylated alkylphenol, or di-epoxide (all of appropriate hydrophilic-lipophilic balance, HLB), in, for example, a methanol or a heavy aromatic naphtha (HAN) solvent.
(keeping the solution pH at less than 5), a viable approach can be to use iron inhibitors to prevent oxidation of ferrous iron (Fe+2) to its ferric (Fe+3) form. Ferrous iron does not precipitate below a pH of 8.5, but ferric iron forms precipitates at pH of 3.5 or above.
Table A is an example of typical analytical ranges of some commonly found parameters in raw produced water samples. Table B also shows a produced water analysis, but this time with a review of analytical constituents and key saturation parameters, as calculated using French Creek ion association modeling software. Results are indicative of which contaminants, dissolved minerals, and potential down stream problems may need to be reviewed when treated
Part 1: How Does Water Sustainability Impact Oil and Gas Water Treatment? continued
11. Biocide: Used to kill bacteria that is present or can grow in a surface tank and systems, or downhole in producing wells. Typically, a non-oxidizer gluteraldehyde, quat, or isothiazoline blend.
We know that produced formation waters are highly variable within and between shale formations. We also understand that sometimes, sampling problems and limitations of some analytical test methods can occur, which adds to problems to be solved.
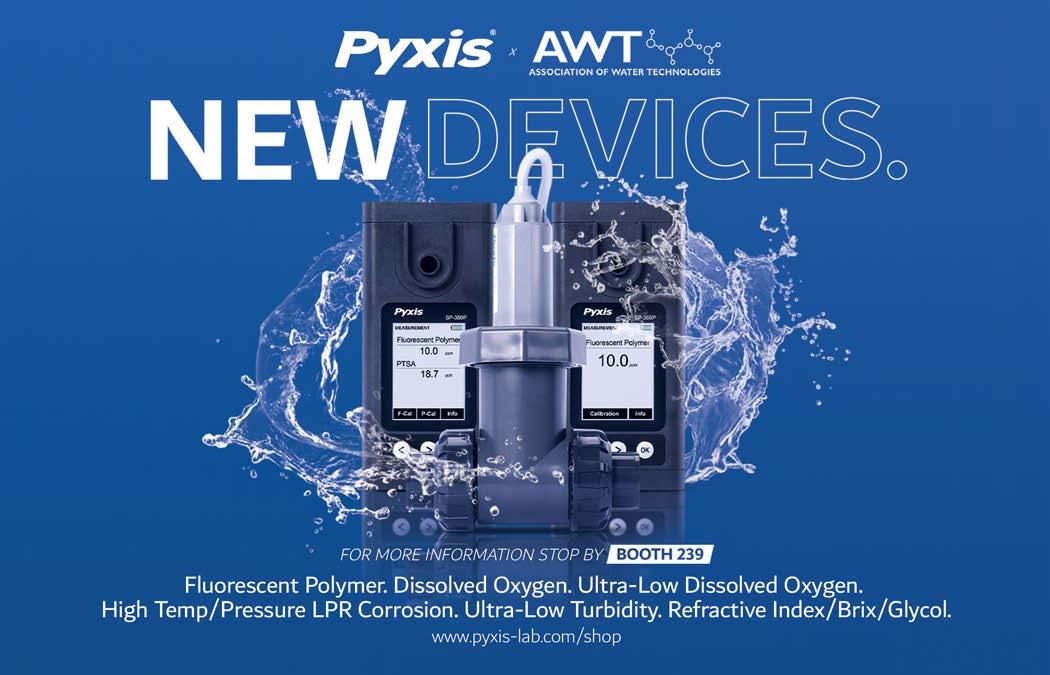
Water Sources
10. pH buffer: Used to control the pH of a solution. Perhaps a simple chemistry such as hydronium ion/ conjugate base (e.g., a citric acid-phosphate mix), or perhaps the use of a methane/ethane sulfonic acid chemistry.
36 the ANALYST Volume 29 Number 3
INITIA® 585 Radical Polymers is here to help with technical support and WaterCycle® modeling. Contact us at info@radicalpolymers.com or 423.316.9877 Patented Non-Phosphorus Technology for Stressed Calcium Carbonate Control
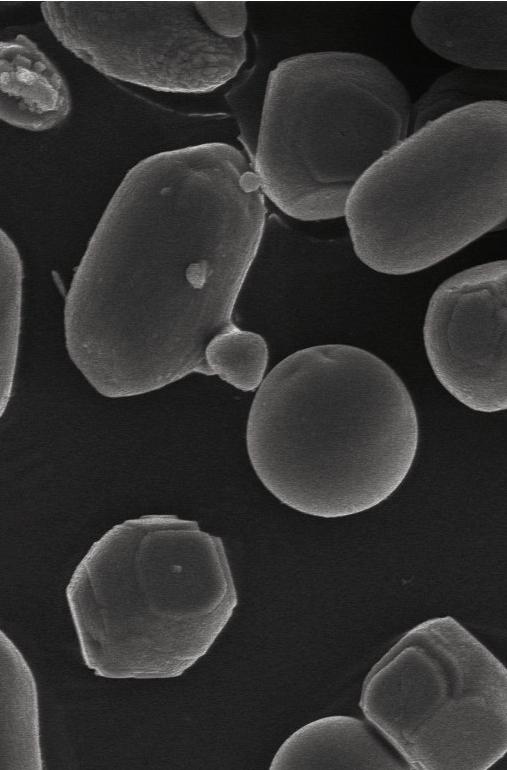
1. Ten years ago, ExxonMobil affiliate XTO Energy teamed up with a major oilfield services company to test the feasibility of reusing produced water for new frac’ing operations. Real-world tests confirmed that with minimal treatment, the fluid used in these wells could successfully fracture the rock and carry sand into the fractures to hold them open, even when based on 100% produced water, saving fresh water, money, and wasted truck trips (10).
Few volatile organic compounds (VOCs) and semivolatile organic compounds (SVOCs) are regularly detected in produced formation waters. However, when they are seen, benzene, toluene, and xylenes (BTX) are the most common VOCs found, and phenols and pyridene are the most common SVOCs.
Raw Produced Water Samples, Reflecting Typical Analytical Ranges of Some Commonly Found Parameters
Strontium Mg/L Sr 60–2,400
Zinc mg/Zn 0–5
Sodium (Na) mg/L Na 22,000–70,000
Calcium mg/L Ca 500–35,000
Table A: Example of Typical Analytical Ranges for Constituents of Produced Water Across Plays
Concentrations of barium and strontium salts tend to rise and fall but generally correlate with total dissolved solids (TDS) results. Chloride represents the most abundant anion.
pH 4.0–7.0
Boron mg/L Bo 20–30
Figure 1 (12) is an example of a produced water analyt ical constituents review. Note that the figure includes both graphs and tabular data.
Turbidity NTU 80–250
2. According to the Texas Water Development Board, in areas of Texas where fresh water is scarce, the waterintensive nature of hydraulic fracturing could be a cause for concern. Some frac wells require 10 million gallons of water or more. Isn’t there a way to recycle and reuse this water? Frac fluids combine water with proprietary mixes of chemicals and are unsuitable for reuse without treatment. “There are chemicals, oil droplets, rock fragments, polymers and a bunch of gunk you need to get rid of,” noted Dr. Jean-Philippe Nicot, senior research scientist with the Bureau of Economic Geology at the University of Texas at Austin. “Also, you may have collected chemicals that might not be compatible with the chemicals injected into the water for your frac operation, and therefore it might not work.” And because of its potential toxicity to waterborne organisms, frac water cannot simply be disposed of in surface waters (11).
Barium mg/L 1–7
38 the ANALYST Volume 29 Number 3
Electrical conductivity µS/cm Not possible due to oil
Chloride mg/L Cl 20,000–165,000
Potassium mg/L K 1,250–1,700
Iron mg/L Fe 0.5–35
produced waters are reused as a frac fluid, or for other purposes, such as drilling, cooling, or irrigation water.
Some useful related comments extracted from cited papers in this article and reports on this subject are provided in this section:
Concentrations of these various analytical parameters appear to increase with time following hydraulic fracturing activities and remain at high concentrations in the produced formation water from operating wells in each shale formation (9).
Part 1: How Does Water Sustainability Impact Oil and Gas Water Treatment? continued
Magnesium mg/L Mg 500–4,500
Note that inorganic and wet chemistry tests on produced waters can be affected by very high solids content and other shale matrix complexities.
Total suspended solids (TSS) Mg/L TSS 1,000–12,000
Treatment Considerations in Water Recycling
Considering the current water recycling position, most recent research work, technical reports, and promotional documents essentially say the same thing: recycling oil and gas produced water for reuse in new frac opera tions or other water uses (e.g., irrigation, purple pipes,
Total dissolved solids (TDS) mg/L 45,000–275,000
Parameter Units Range of Results
toilet flushing, drinking/potable) is a viable process and usefully saves fresh water, transport costs, and waste! The question then becomes one of identifying future uses of treated reclaimed water, and then adjusting one or more standard equipment treatment technologies or process trains (and selective water treatment chemistries) to precisely match needs. Going forward, a better under standing of the variabilities in production brines and matching them with appropriate performance chemis tries will likely be a bigger focus.
PARAMETERS
Iron(as Fe) 0.600Phosphate(as PO4) 0.00
Ammonia(as NH3) 0.00H2S (as S) 0.00
Figure 1: Example of a produced water analytical constituents review.
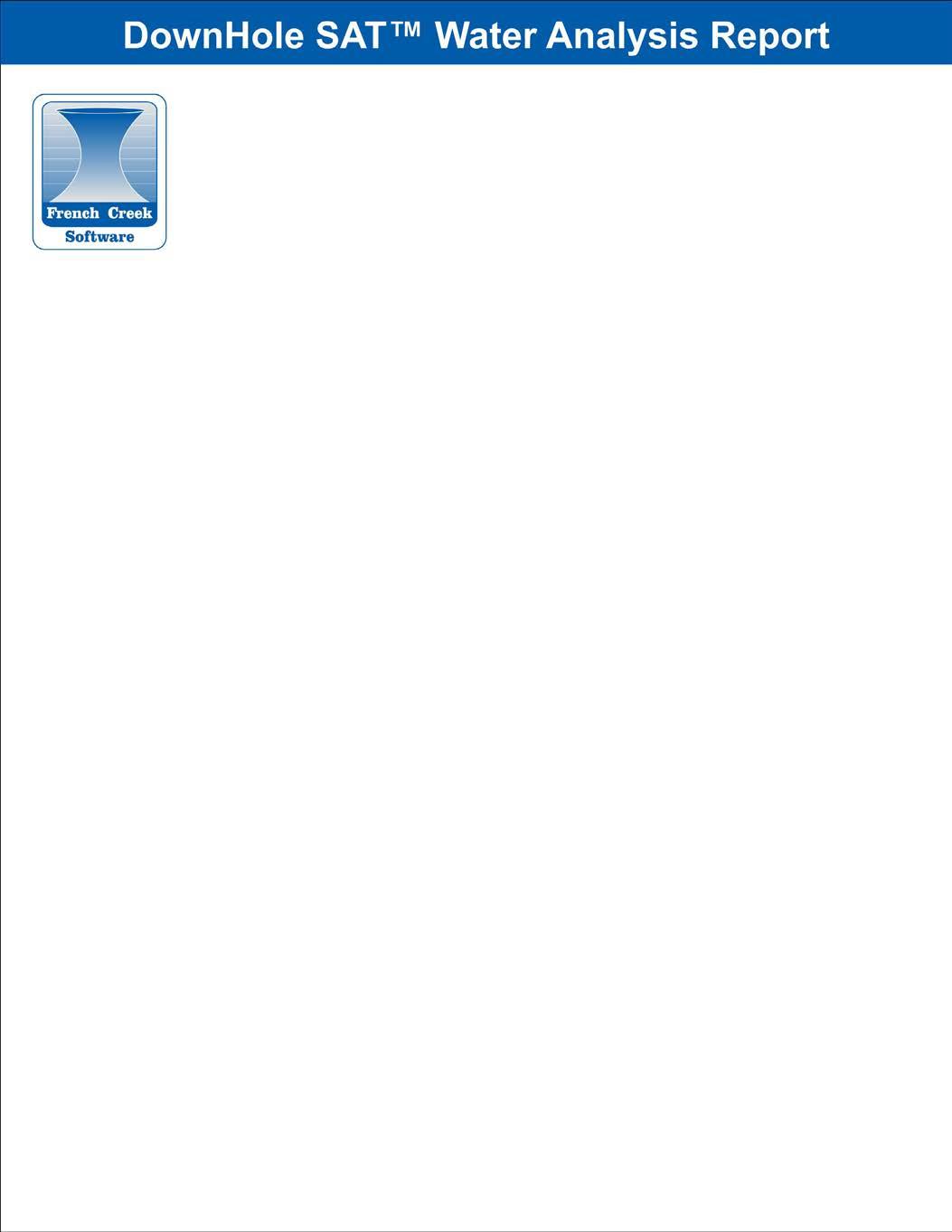
Strontium(as Sr) 67.30Acidity(as CaCO3) 49.78 Sodium(as Na) 22000"M" Alkalinity(as CaCO3) 795.00 Potassium(as K) 1370"P" Alkalinity(as CaCO3) 0.00
Aluminum(as Al) 0.00Fluoride(as F) 0.00 Manganese(as Mn) 0.700Nitrate(as NO3) 0.00 Zinc(as Zn) 0.00Boron(as B) 0.00 Lead(as Pb) 0.00
Sample Date: 03-20-2014 at 1436
Temperature(oC) 20.00Sample pH 7.45
Calcium(as Ca) 6230Chloride(as Cl) 45800 Magnesium(as Mg) 474.00Sulfate(as SO4) 1860 Barium(as Ba) 0.00Bromine(as Br) 0.00
Lithium(as Li) 0.00Silica(as Si) 0.00
39 the ANALYST Volume 29 Number 3
Report Date: 03-20-2014
Field Tech: Joseph Bear
Resistivity(megohm-cm)1.31e-5T.D.S.(mg/L) 77962
Conductivity(umhos/cm) 76048Sp.Gr.(g/mL) 1.000
Magnesite Saturation Ratio Temperature °C 21.0 29.9 38.8 47.7 56.6 65.5 74.4 83.3 92.2 101 110 110 7.006.005.004.003.002.001.000RatioSaturation Anhydrite Saturation Ratio Temperature °C 21.0 29.9 38.8 47.7 56.6 65.5 74.4 83.3 92.2 101 110 110 7.006.005.004.003.002.001.00RatioSaturation Calcite Saturation Ratio Temperature °C 21.0 29.9 38.8 47.7 56.6 65.5 74.4 83.3 92.2 101 110 110 35.030.025.020.015.010.05.00RatioSaturation Gypsum Saturation Ratio Temperature °C 21.0 29.9 38.8 47.7 56.6 65.5 74.4 83.3 92.2 101 110 110 2.402.202.001.801.601.401.20RatioSaturation Source: Figure courtesy of French Creek Software, Reference 9. Part 1: How Does Water Sustainability Impact Oil and Gas Water Treatment? continued
ANIONS(mg/L)
SYSTEM IDENTIFICATION
SCALE AND CORROSION POTENTIAL
Sample 1
Temp. Calcite Anhydrite Gypsum Barite Celestite Siderite Mackinawite (oC) CaCO3 CaSO4 CaSO4*2H2O BaSO4 SrSO4 FeCO3 FeS 21.00 3.80 0.0622 1.01 3.54 1.58 150.53 0.00-0.0434 0.587 -29.94 0.422-0.0901 0.00 -0.710 29.90 5.40 0.0875 1.01 4.40 1.46 124.45 0.00-0.0646 0.572 -31.66 0.674-0.0413 0.00 -0.721 38.80 7.22 0.112 1.07 22.52 1.38 104.64 0.00-0.0908 0.573 -31.38 1.000.00197 0.00 -0.733 47.70 9.27 0.136 1.19 52.38 1.49 122.97 0.00 -0.123 0.579 -30.54 1.43 0.0413 0.00 -0.746 56.60 11.68 0.163 1.38 88.29 1.62 140.26 0.00 -0.165 0.582 -30.09 1.98 0.0796 0.00 -0.760 65.50 14.47 0.192 1.66 125.63 1.75 153.84 0.00 -0.218 0.582 -29.98 2.69 0.118 0.00 -0.775 74.40 17.67 0.225 2.06 161.12 1.87 164.72 0.00 -0.287 0.579 -30.19 3.58 0.156 0.00 -0.792 83.30 21.25 0.261 2.64 192.77 1.99 173.64 0.00 -0.373 0.574 -30.70 4.67 0.193 0.00 -0.810 92.20 25.21 0.301 3.47 219.78 2.09 181.17 0.00 -0.481 0.567 -31.51 5.97 0.230 0.00 -0.830 101.10 29.03 0.349 4.60 245.39 2.16 188.81 0.00 -0.624 0.550 -33.66 7.39 0.265 0.00 -0.860 110.00 33.49 0.399 6.30 264.52 2.25 194.85 0.00 -0.796 0.538 -35.25 9.08 0.295 0.00 -0.884 110.00 33.49 0.399 6.30 264.52 2.25 194.85 0.00 -0.796 0.538 -35.25 9.08 0.295 0.00 -0.884 Lbs per Lbs perLbs per Lbs per Lbs per Lbs per Lbs per 1000 1000 1000 1000 1000 1000 1000xSAT xSAT xSAT xSAT xSAT xSAT xSAT Barrels Barrels Barrels Barrels Barrels Barrels Barrels Saturation Ratios (xSAT) are the ratio of ion activity to solubility, e.g. {Ca}{CO3}/Ksp. pCO2 (atm) is the partial pressure of CO2 in the gas phase. Lbs/1000 Barrels scale is the quantity of precipitation (or dissolution) required to instantaneously bring the water to equilibrium.
Sample ID#:669 ID 04201998
WATER CATIONS(mg/L)CHEMISTRY
Lab Tech: Ernest Jack
Part 1: How Does Water Sustainability Impact Oil and Gas Water Treatment? continued
5. Why does the oil industry continue to operate on the assumption that water with high levels of TDS is unsuitable for frac’ing? The perceived understanding has always been that salty water prevents the proper hydration of the crosslink-gel and friction reducers, but as this study indicates, salt is clearly not the issue. Is there something else that would prevent a proper hydration of guar gum in the water? The real reason that the oil industry prefers to use fresh water for frac’ing is simply because it is cheap and clean, completely justifiable when trying to run a business. In essence, it is the low count of total suspended solids (TSS) in aquifer water that makes the gelling hydration possible, not the absence of salt. The fact is that TSS in the form of colloidal particles are very small in size (0.001 to 1 micrometers [µm]) yet very large in surface area. This structure makes colloids abrasive to friction inducers, negatively impacting the rheology of crosslinked gels. Where the oil industry has long operated on the notion that TDS is the bottleneck in widespread frac water reuse, the study shows that TSS is the real culprit. The study recounts that at 99% TSS removal, the produced water was successfully blended into a crosslinked-gel-based frac fluid suitable for hydraulic fracturing (13).
Novel, high viscosity STFR chemistries (HVFR) are now offered by any number of service companies that can tolerate in excess of 200,000 mg/L brine TDS. Chemistries tend to be based on new types of very high molecular weight (2 to 30 m molecular weight molecular weight [MW]), multivalent surfactant co/ter-polymers, in anionic, non-ionic, and cationic forms. An example is a reaction product formed from a cationic monomer (e.g., [3-(methacryloylamino propyl]trimethylammonium chloride) with a non-ionic monomer (e.g., N-vinyl formamide) and a carboxylic monomer (e.g., maleic acid metal salt) (14).
40 the ANALYST Volume 29 Number 3
Additionally, what must be considered is the role of additive chemistries to inhibit potential scale, corrosion, and deposition problems that are initiated by alkaline earth metals (i.e., calcium [Ca], magnesium [Mg], strontium [Sr], barium [Ba], radium [Ra]) and/ or some of the transition metals (i.e., copper [Cu], iron [Fe], vanadium [V], cobalt [Co], manganese [Mn], nickel [Ni], chromium [Cr], titanium [Ti], among others).
Third-party opinions on treatments, as stated above, tend to focus on TSS and its removal being the key requirement, and while the authors of this article are in agreement that total TSS removal is a good first step, the need to separate oil, oily sludges, and hydrocarbons from
Removal of Oil and Sludges
Also, in some regions and exploration areas, it is necessary to control sulfur compounds (as, say, with geothermal brines).
4. The study shows that brine water possesses all the characteristics required for effective frac’ing: easy preparation, rapid hydration, low fluid loss, good proppant transport capacity, low pipe friction, and effective recovery from the reservoir. Unlike fresh water, salt water does not restrict oil flow because of an osmotic imbalance that results in clay swelling. Simply put, salt water is good for frac’ing and any statements otherwise are unfounded (13).
Consider the following WW treatment notes to support our view:
High silica, in either colloidal or reactive forms, can present additional problems, depending on brine pH, temperature, magnesium content, and other factors. How do we treat for silica control?
For some plays, produced water quality may be such that 100% can be directly reused without further treatment (i.e., those with lower salt content, minimal TSS, and low hydrocarbon content), except, perhaps, for adding a biocide and changing out the FR in the “slick water package,” for a more expensive but salt-tolerant friction reducer (STFR) chemistry. Under these conditions, there is no expectation for a reduction in well performance.
water is also required in order to produce clean brine s. If wastewater (WW) treatment is restricted to TSS alone, the PW is likely to be undertreated!
3. In 2014, Apache Corp.(Texas) treated and recycled more than 10 million barrels of produced water, which was then used in the company’s hydraulic fracturing operations. These efforts reduced the company’s road use by more than 80,000 truck trips (11).
Hydrocarbons in produced water will cause issues with salt-tolerant FR chemistries.
10. ExxonMobil and U.S. Chamber of Commerce Foundation (2012). “Recycling Water in Hydraulic Fracturing,”, accessible at uschamberfoundation.org/recycling-water-hydraulic-fracturinghttps://www.
8. Mantell, M. (2013). “Recycling and Reuse of Produced Water to Reduce Freshwater Use in Hydraulic Fracturing Operations,” 2013 EPA Hydraulic Fracturing Study Water Acquisition Workshop, U.S. Environmental Protec tion Agency, Washington, D.C., www.epa.gov
1. Roser, M. (November 2019). “Future Population Growth,” Our World in Data, accessible at https://ourworldindata.org/future-population-growth
9. Coleman, N.P. (2011). “Produced Formation Water Sample Results from Shale Plays,” EPA Workshop, U.S. Environmental Protection Agency, Washington, D.C., accessible at ing_in_thailand.pdfhttps://ie.unc.edu/wp-content/uploads/sites/277/2016/03/hydraulicfracturdocuments/producedformationwatersampleresultsfromshaleplays.pdfhttps://www.epa.gov/sites/default/files/;or
13. Gruber, E. (2021). “Recycling – Produced and Flowback Wastewater for Fracking,” Ecologix Environmental Systems, Alpharetta, Georgia, accessible at Recycling-Flowback-and-Produced-Water-for-Fracking.pdfhttps://www.ecologixsystems.com/wp-content/uploads/2021/05/
2. Statista.com (accessed Dec. 4, 2021). “Daily Demand for Crude Oil in Million Barrels per Day,” EIA Oil Market Report, accessed at statista.com/statistics/271823/daily-global-crude-oil-demand-since-2006/https://www.
“Salt Tolerant Friction Reducer,” U.S. Patent No. 10,385,253 B2.
References
7. EPA (accessed April 26, 2022). “Unconventional Oil and Natural Gas Development,” Energy and the Environment,” accessed at fracturing%20technologiesplay%20a%20key%20role%20in,drilling%20and%20hydraulic%20gov/uog#:~:text=Unconventional%20oil%20and%20natural%20gas%20https://www.epa.
11. Benton, J. (2015). “Fiscal Notes: Recycling Fracking Water. Drillers Reuse, Repeat,” accessible at cal-notes/2015/october/fracking.phphttps://comptroller.texas.gov/economy/fis
Colin Frayne is British, now a U.S. citizen, and a leading industry consultant in water treatment, environmental science, and industrial process chemistries.
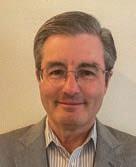

5. Ritchie, H.; Roser, M. (2017). Water Use and Stress, published online at: OurWorldInData.org Retrieved from: https://ourworldindata.org/ water-use-stress
At 16, he started full-time work as a trainee power plant chemist at Ford
Motor Co., UK, and studied part time at the NE London Polytechnic (later the University of East London), Since those early days, Mr. Frayne has lived and worked on every continent (except Antarctica), with long spells in Africa, Europe, Asia, and the Americas, working in industries of every description, including deep mining, steel plants, nuclear fuel, oil and gas, petrochemical, global data centers, F&B, and healthcare. He also worked on many environmental projects, including the Amazon basin, Welsh mountains, and Belgian canals. Today, he is a Fellow of the Royal Society of Chemistry, a Fellow of the Institution of Corrosion Technology, and a Fellow of the UK Water Management Society. He is also a European Chartered Scientist, a Chartered Chemist, and a Chartered Environmentalist. In 2004, AWT honored him with the Ray Baum Memorial Water Technologist of the Year Award, and in 2010, he received CWT Program Recognition of the Exam Writing Task Force. During his career, Mr. Frayne has also managed several businesses around the world and authored several published textbooks and peer-reviewed publications. He may be reached at (561)
Part 2
14. Frederick K.,W.; Chen, S.-R.; Loeffler, R.J.; Sawant, K. (Aug. 20, 2019).
With267-4381.morethan
40 years of experience, Barry Ekstrand is regarded as an accom plished executive leader of energy services and supply businesses, having served in senior executive leadership roles at both large integrated energy service companies and small/startup oilfield service and supply businesses. Mr. Ekstrand spent 22 years at Halliburton Energy Services in a variety of operations, sales, and technical management roles in the United States and Asia, with an emphasis in hydraulic fracturing, chemical stimulation, cementing, coiled tubing, and well testing businesses. He led Weatherford International’s organic startup of its hydraulic fracturing and pressure pumping business lines and then grew it from a zero capability/zero revenue concept to a top-tier global business. Mr. Ekstrand also led the startup of a high-quality frac sand and proppant manufacturing business, and he has worked with small energy service and supply companies to assist them with technology, commercialization, and management of growth. He currently serves as president and COO at Finoric LLC, a manufacturer of specialty chemical products for the oil and gas industry. Mr. Ekstrand received his BSc in chemical engineering from California State Polytechnic University at Pomona and his MBA from California State University at Bakersfield. He is a registered Professional Petroleum Engineer, and he holds eight patents. Mr. Ekstrand can be contacted at (713) 417-7745.
41 the ANALYST Volume 29 Number 3
6. Gilleland, K.; Selle, L. (2013). “Golden Age for Shale Plays,” Hydraulic Fracturing Techbook, Hart Energy, Houston, Texas, p. 58.
4. Earth.org (March 2022). “More than 3 Billion People Are Affected by Water Shortages,” report available at https://earth.org/3-billion-peopleare-affected-by-water-shortages
12. Ferguson, R. (2011). “Downhole SAT User Manual,” French Creek Software, Valley Forge, Pennsylvania, www.frenchcreeksoftware.com
Part 1: How Does Water Sustainability Impact Oil and Gas Water Treatment? continued
In the second part of this technical article series, we will look at an expansion of remedial stimulation of existing wells, and a future look at the expansion of produc tion brines and production chemistries. Topics to be addressed in Part 2 will include treatment technologies, water chemistry, and treatments for concerns such as corrosion.
3. U.S. Energy Information Administration (EIA) (accessed March 7, 2022). FAQS: “How Much Shale (Tight) Oil Is Produced in the U.S.?” accessed at https://www.eia.gov/tools/faqs/faq.php?id=847&t=6
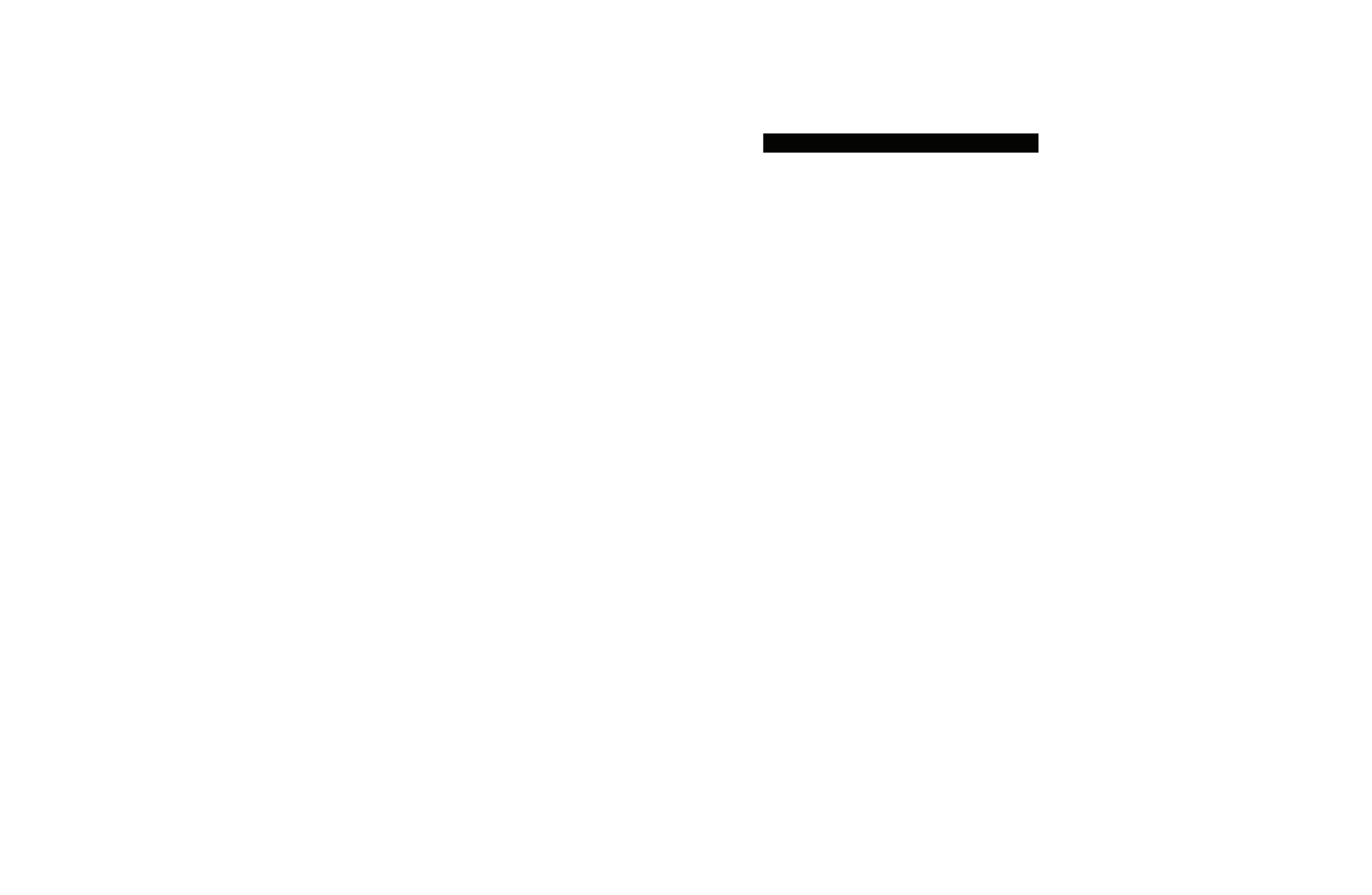
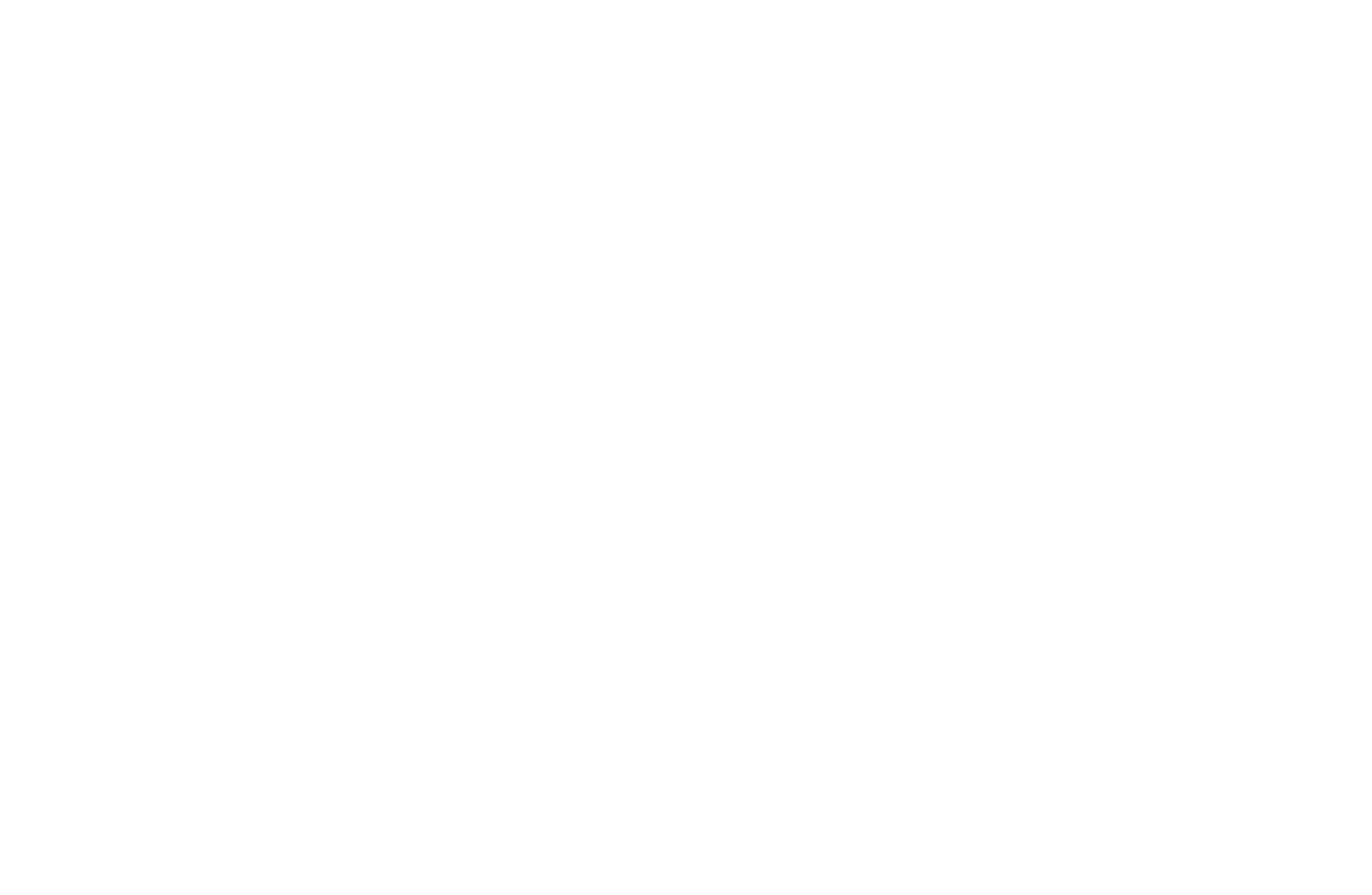
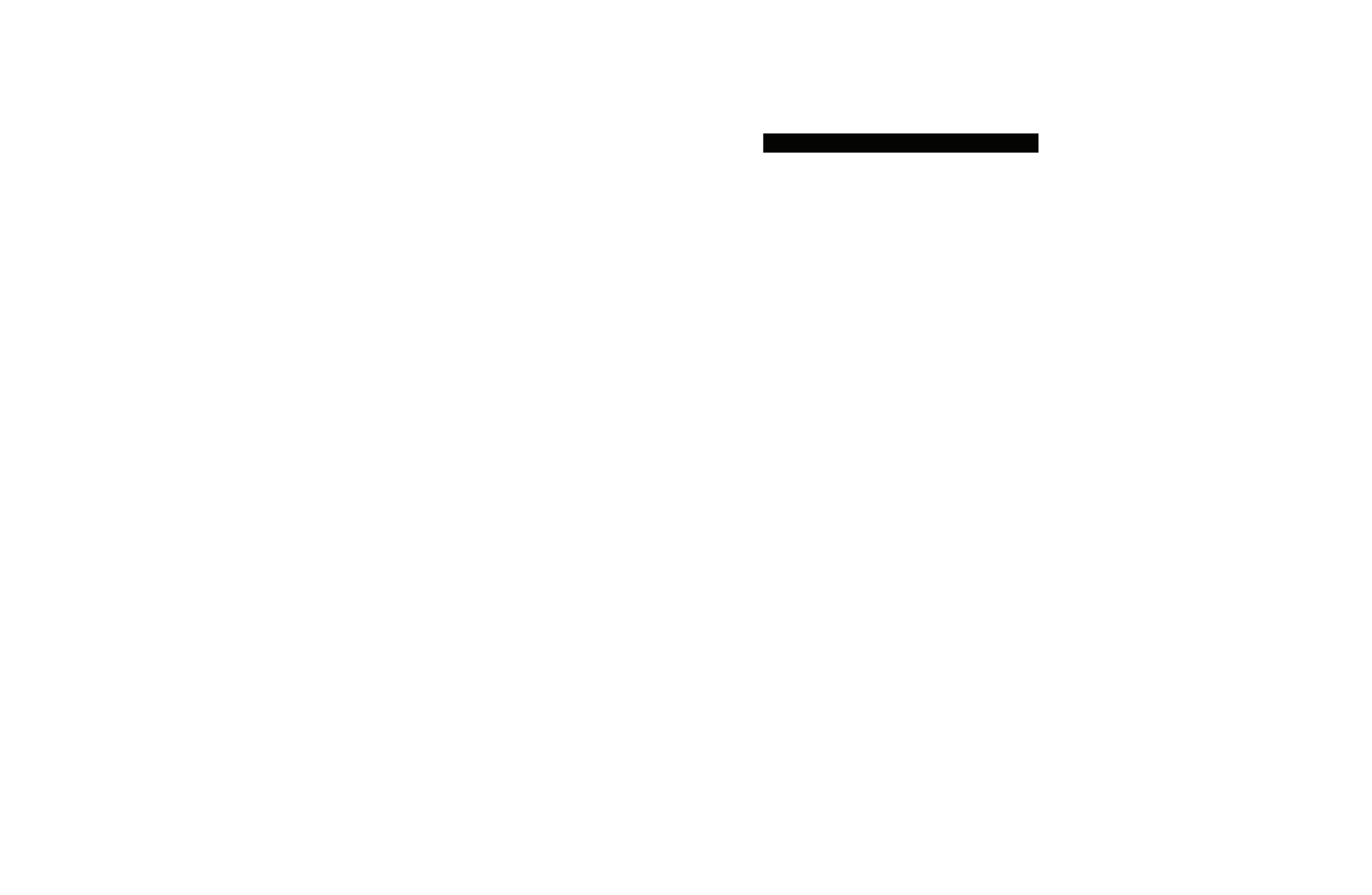
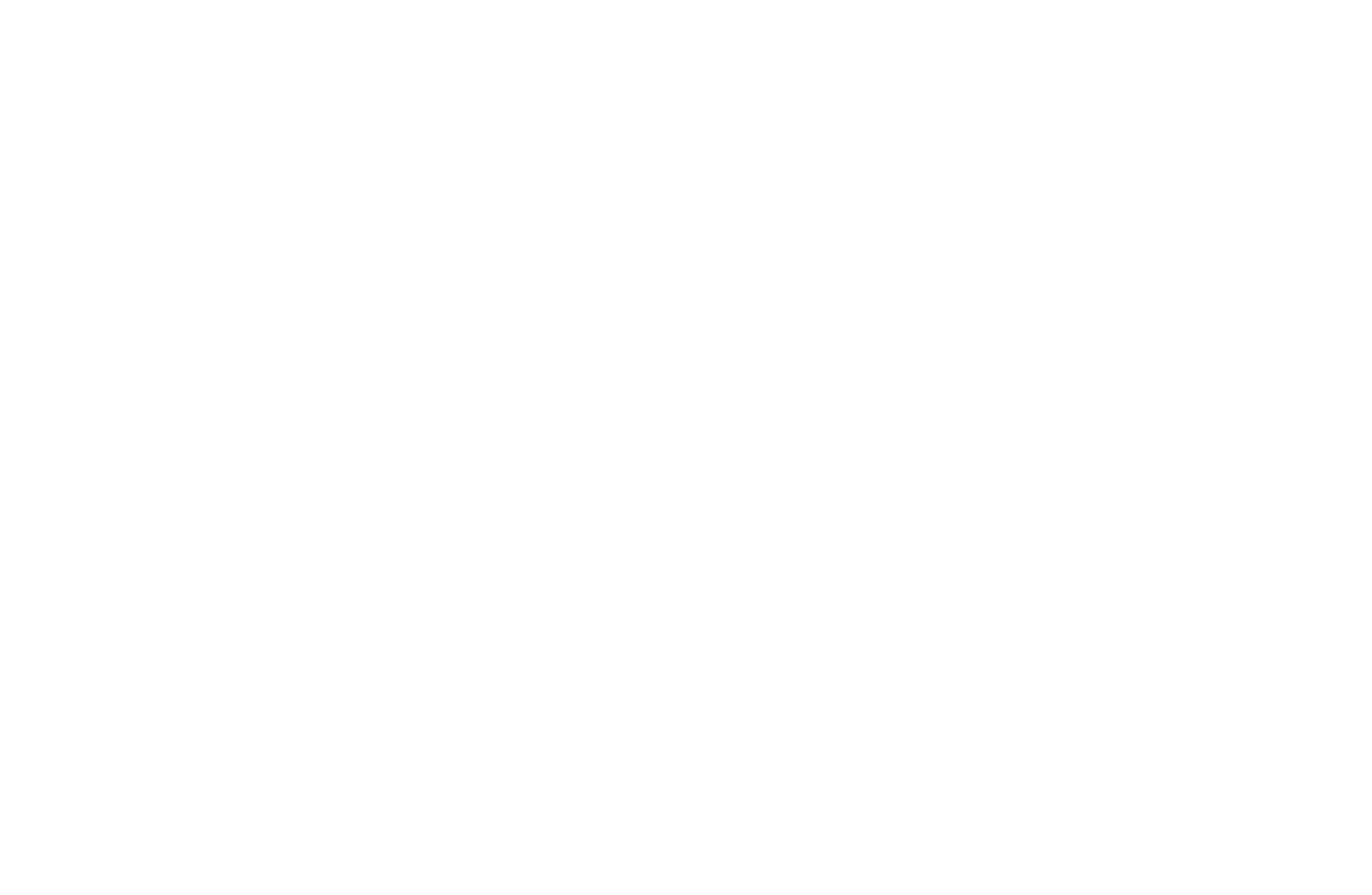
What Is the Relationship Between Amoeba and Legionella in Non-Potable Water Systems?
Shivi Selvaratnam, Ph.D., Weas Engineering, Inc.
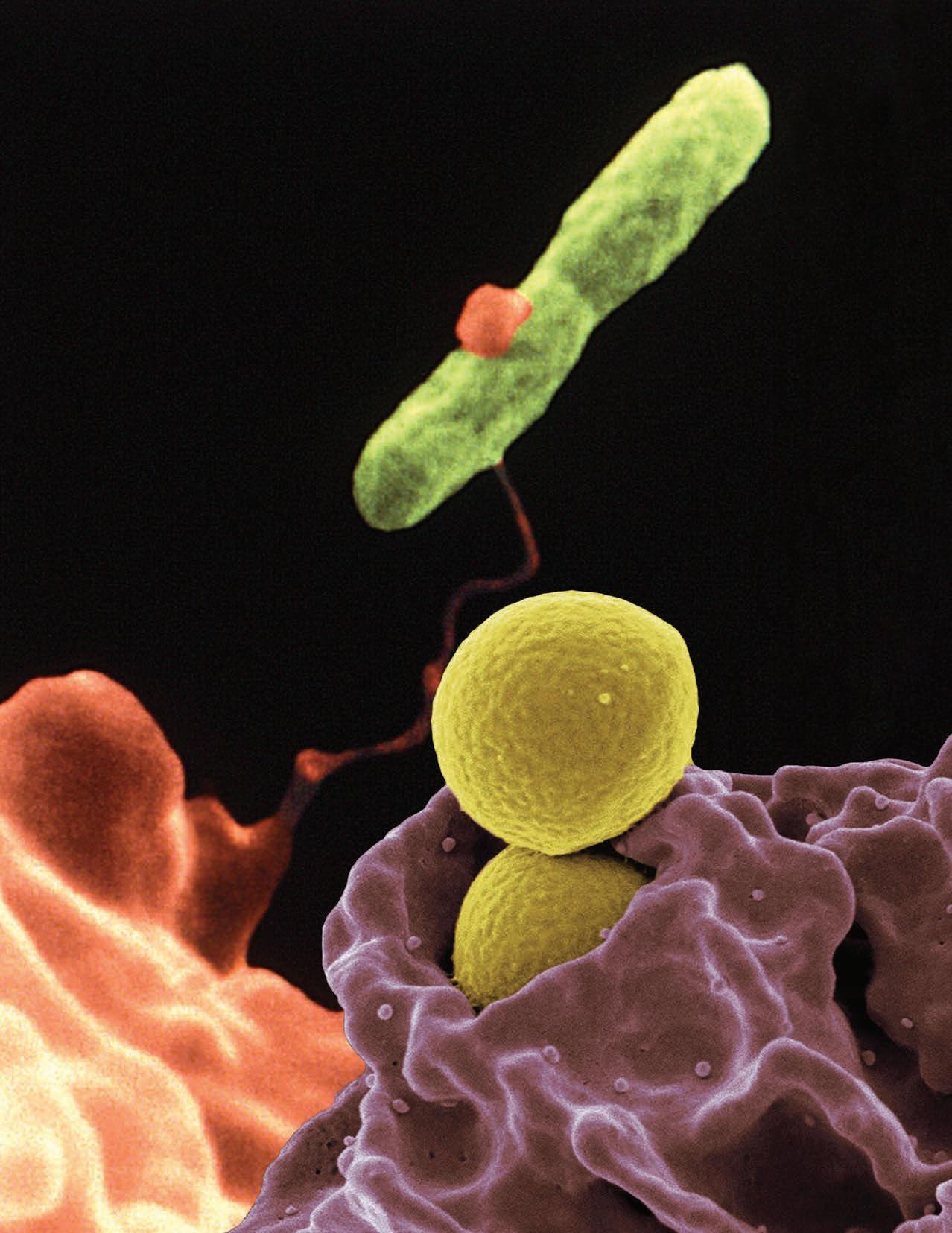
Results from our previous study on the efficacy of chlorine, chlorine dioxide, and monochloramine on the growth of amoeba in potable water suggest that chlorine dioxide may effectively mitigate a contaminated system with as little as a single dose of 4.0 ppm in 24 hours, though this would be an offline use (7).
Materials and Methods
Abstract
Examination of Legionella From Non-Potable Water Samples
A selective procedure was used to reduce the numbers of non-Legionella bacteria before culturing since water samples may contain high concentrations these bacteria (8). Samples were either heat or acid treated prior to Forplating.heat
Non-Potable Water Sample Collection 100 milliliters (mL) of non-potable water samples were collected in sterile wide-mouth screw cap polypropylene plastic bottle containing 100 milligrams (mg) sodium thiosulfate preservative.
The two modes of existence for Legionella also point to two modes of growth suppression. That is, control of growth within a biofilm and indirect control of growth by curtailing the growth of amoeba. Within the context of potable water, disinfectant mechanisms to control microorganisms include chlorine dioxide, chlorine and monochloramine. Almost all amoebicidal data on these disinfectants is derived from studies done to remediate drinking water that has been contaminated with amoeba that are pathogenic (e.g., Giardia spp.) (6).
45 the ANALYST Volume 29 Number 3
Legionella is an opportunistic waterborne pathogen that exists as a free-living organism and an intracellular parasite in which several amoeba species serve as the host organism. The life cycle of Legionella is thought to be dependent on the existence of an amoeboid host that is present in a complex biofilm community. Whether this host–parasite relationship is a necessary or an opportu nistic relationship is not well understood. In this article, we examine non-potable water systems for the presence of Legionella spp. and free-living amoeba (FLA). We use conventional culture techniques to determine the presence of and quantify Legionella spp and a LIVE/ DEAD ® stain to determine the presence of and quantify live and dead amoeba. The LIVE/DEAD stain uses the dyes SYTO ®9 and propidium iodide to render viable amoeba green and dead amoeba red, respectively, using epifluorescence microscopy. This technique has been used on other eukaryotic cells but not on amoeba We successfully used this technique when examining the relationship between Legionella and amoeba in potable water, as reported in our Summer 2020 Analyst article.
The natural environment in which Legionella thrive is complex and therefore not well understood. On one hand, there is a school of thought that the preferred state of existence for Legionella is that of an intracel lular parasite residing within several host protozoan species, including free-living amoeba (FLA) (3). FLA are widespread in the environment. Indeed, Legionella is well adapted to this parasitic “lifestyle” and possesses several gene-based regulatory mechanisms to ensure its long-term survival (4). Nevertheless, Legionella has also been found as a resident of biofilms present in potable and non-potable water systems, independent of a para sitic existence (5). The requirement for L-cysteine and an unusually high demand for soluble iron to support its growth is indicative that in the absence of a parasitic relationship, Legionella may require a communal envi ronment to provide these exogenous growth factors.
The purpose of this investigation was to determine if there was an association between amoeba and Legionella in non-potable water and how this association compares to our previous work with potable water.
Processing of Non-Potable Water Samples for Legionella Isolation
For acid treatment, 0.1 mL of sample was added to 0.9 mL of buffer pH 2.0. The suspension was then incubated for 5 min at room temperature.
Introduction
treatment, a 500 microliter (µ L) of sample was incubated in a water bath at (50 ± 1) °C for (30 ± 2) minutes (min).
Legionella spp are the most common cause of waterborne infections in the United States (1). Although Legionella are considered to be fastidious environmental organisms, they are readily cultivated in an aerobic environment on heterotrophic media, such as Buffered Charcoal Yeast Extract (BCYE) (2).
Amoeba were concentrated from an active culture by centrifugation at 1,500 revolutions per minute (rpm) for 1 min. The supernatant was decanted, and the pellet was
Amoeba Culture Used in Disinfectant Experiment
Plating of Samples
Axenic cultures of Acanthamoeba sp. were maintained by subculturing them in PYG (proteose-peptone-yeast extract-glucose) medium every few weeks.
Visualization of Live and Dead Amoeba From Non-Potable Water Samples
The LIVE/DEAD FungaLight™ Yeast Viability Kit was used to visualize live/dead amoeba. The kit contains solu tions of SYTO ® 9 green fluorescent nucleic acid stain and the red-fluorescent nucleic acid stain propidium iodide. These stains differ both in their spectral characteristics and in their ability to penetrate healthy amoeba cells. When used alone, the SYTO ® 9 stain generally labels all amoeba in a population—those with intact membranes and those with damaged membranes. In contrast, propidium iodide penetrates only amoeba cells with damaged membranes, causing a reduc tion in the SYTO ® 9 stain fluorescence by fluorescence resonance energy transfer (FRET) when both dyes are present. Thus, with an appropriate mixture of the SYTO ® 9 and propidium iodide stains, amoeba with intact cell membranes stain fluorescent green, whereas amoeba with damaged membranes stain fluorescent red.
Examination of Amoeba From Non-Potable Water Samples
Even when no detectable Legionella or TPC were respectively.anddetectedamoebaeobserved,werein8324samples, Amoeba and Legionella
Stained amoeba slides were viewed under an epifluorescence microscope using a fluorescein long-pass filter. Fluorescence from both live (green fluorescent) and dead (red fluorescent) amoeba was viewed simultane ously, and respective counts were recorded.
Preparation of Amoeba Samples
BCYE agar containing 0.1% alpha-ketoglutarate was used as the base medium for the recovery of Legionella. Two types of selective BCYE agar were used in the processing of the samples. The first was designated BCYE complete with antibiotics (purchased from Hardy Diagnostics); the second was designated BCYE complete without antibiotics.
Media for Legionella Growth and Isolation
46 the ANALYST Volume 29 Number 3
Filtration of Samples for Amoeba Isolation 50 mL of non-potable water samples used for Legionella analysis (from above) were filter-concentrated using a 47-millimeter (mm) filter funnel assembly disinfected with 80% isopropyl alcohol between uses and containing a sterile 3.0 micrometer (µ m) black polycarbonate filter. 3 mL of Tris buffer containing SYTO ® 9 and propidium iodide (from LIVE/DEAD FungaLight™ Yeast kit) were added to the membranes and incubated at room temperature for 15 min. Liquid from the membranes were removed by filtration, and the membranes were transferred to a large microscope slide. A few drops of deionized water were added to each membrane and covered with a large cover slip. The slides were incubated at 36 °C for 15 min prior to microscopy.
Efficacy of Disinfectants on Survival of Amoeba
Plates were examined after 72 to 96 hours of incubation for Legionella. Suspect Legionella colonies were streaked onto BCYE agar plate without L-cysteine and antibiotics, and a positive control BCYE agar plate without antibiotics. The plates were incubated for 24 to 48 hours. Colonies that grew on BCYE agar, but not BCYE agar without L- cysteine, were considered to be presumptive Legionella species and later sero typed using the Dry Spot ™agglutination test (Oxoid, Dardilly, France) or direct fluorescent antibody (MTech).
What Is the Relationship Between
Examination of Cultures for Legionella
The number of live and dead amoeba were determined for each of the nine squares on the hemocytometer and used in computing live and dead amoeba/mL. The average number of live and dead amoeba for the nine squares, the surface area of the field of view, and the volume of water filtered were used in the final calculation to determine the number of amoebae per mL.
Plates (described above) were inoculated with 0.2 mL of either acid-treated or non-acid-treated suspension and distributed over the agar surface with a plastic spreader. They were then incubated at 36 °C in a humidified incubator for 14 days at a minimum humidity of 95%.
in Non-Potable Water Systems? continued
2022 Annual Convention & Exposition
September 21–24, 2022 | Vancouver Convention Centre CANADA

Scan the QR-code or go to https://bit.ly/3wEVuft to learn how to prepare to travel to Canada.
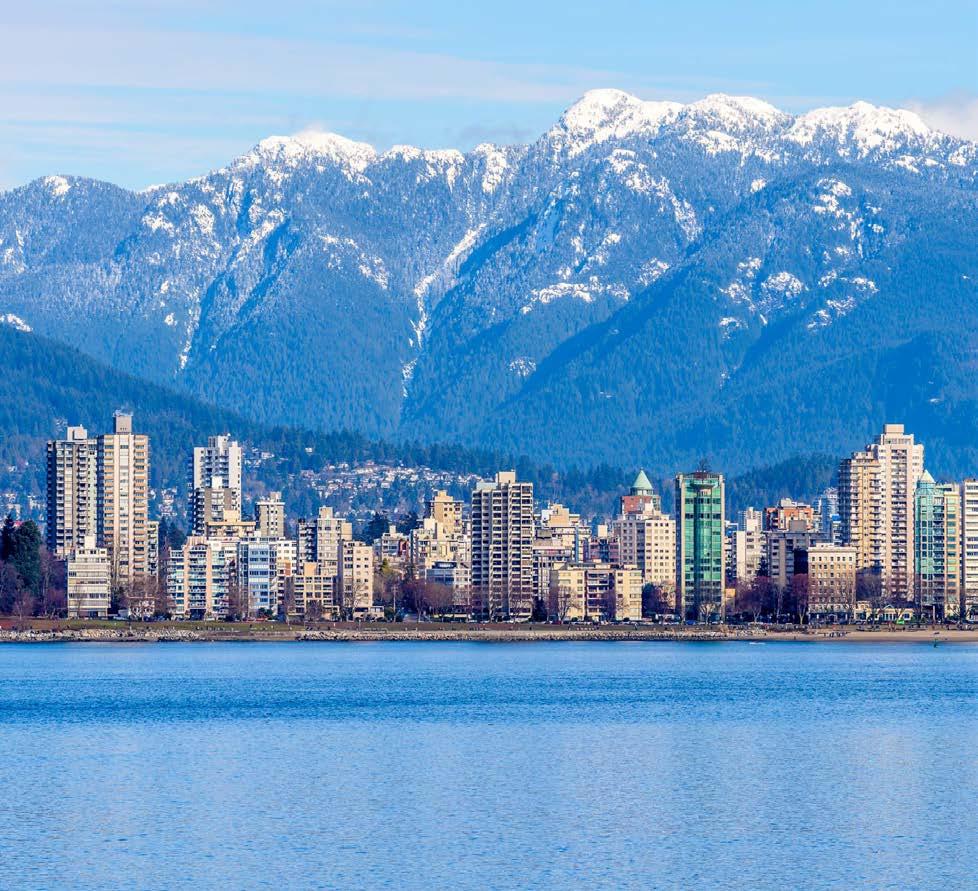
Preparation of Amoeba Samples for Disinfectant Assays
TPC 1-99 55 42 36
All disinfectant assays were performed in saline buffer at room temperature. Amoeba were concentrated from an active culture by centrifugation at 1,500 rpm for 1 minute. The supernatant was decanted, and the pellet was resuspended in 1 mL of saline buffer. The suspension was recentrifuged at 1,500 rpm, followed by decantation of supernatant and resuspension of pellet in 6 mL of saline buffer.
Legionella All ranges 171 120
TPC 100-999 49 38 256
TPC >100,000 9 4 275,000
non-potable water samples were analyzed for the presence of Legionella and TPC bacteria. These were subsequently examined for the presence of amoeba to determine if there was a relationship between these Withp and Without Amoeba 0 NA 22 0.281 550 0.002 0 1,600 NA 25 44 0.211 0 0 NA 45 0.165 358 0.048 2,833 3,400 0.290 22,000 0.301 268,000 0.467 10,235 28,853 0.044
TPC 0 36 24
TPC 10,000-100,000 11 6 16,666
Results and Discussion
25 ppm of BARDAC® 2250 R was used to determine if the methodology used in these assays is effective against amoeba. This is a twin-chain dimethyl ammonium chloride, which is effective against a broad spectrum of microbial organisms, including algae. Times tested were 0, 15, 30, 45, and 60 min.
Chlorine (1, 5, and 10 parts per million [ppm]) and a microbiocide (isothiazalone; 35 and 219 ppm) were tested for efficacy against amoeba. For the chlorine
TPC All ranges 171 120
Legionella 1,000–9,999 1 0
Legionella 100–999 13 12 185
Table A: Association of Amoeba With Legionella and TPC in Non-Potable Water Samples CFU/mL No. of Samples PositiveAmoebaSamples Average With CFU/mLAmoeba Average Without CFU/mLAmoeba
Legionella 1–99 30 25 30
Legionella 0 127 83 0
Table A shows data on the association of amoeba with Legionella and total plate count (TPC) in non-potable water
Determination of Disinfectant Efficacy on Survival of Amoeba
P = Statistical probability What Is the Relationship Between Amoeba and Legionella in Non-Potable Water Systems? continued
Experimental Protocol
48 the ANALYST Volume 29 Number 2
experiments, at the end of each incubation period and before the addition of the staining dye, any remaining free chlorine was quenched by the addition of sodium thiosulfate. Times tested for all disinfectants were 0, 15, 30, 45, and 60 min, and 24 hours.
Previously,samples.171
TPC 1,000-9,999 11 6
For each disinfectant assay, the 6 mL of suspension in saline buffer was divided into two 3 mL centrifuge tubes. One centrifuge tube was used as the untreated control, while the other was used for the treatment. 500 µ L from each centrifuge tube was withdrawn at the various tested times for determination of disinfectant efficacy.
At the end of each assay time, 0.5 mL each of propidium iodide and SYTO 9 were added to the assay microcentri fuge tube and incubated at room temperature for 15 min. The tubes were then incubated at 36 °C for 15 minutes. 10 mL of stained sample was loaded into the injection area of a C-Chip hemocytometer, ensuring that the chamber fills by capillary action.
resuspended in 1 mL of Tris buffer. The suspension was recentrifuged at 1,500 rpm, followed by decantation of supernatant and resuspension of pellet in 1 mL of Tris buffer. 500 microliter (µ L) (500 µ L) of the prepared culture was used for the positive control. For the nega tive control, 500 µ L of prepared culture was treated with 1 mL of 70% isopropyl alcohol and incubated at room temperature for two minutes. The suspension was vortexed prior to use.
Data Management Software for Water Treatment eSR and Aliquot® Pro make it easy to connect, communicate, manage and analyze your client data. BuildReportsCustom DataCentralizedStorage GraphTrendand Connect to Controllers Users have access to a variety of features including user-entered reports, data storage from external devices, graphing and trending features, inventory management and document storage. All the features included in eSR are designed to enhance the consulting aspects of service-oriented companies.
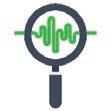
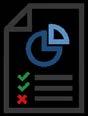
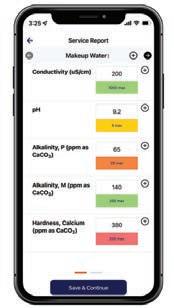

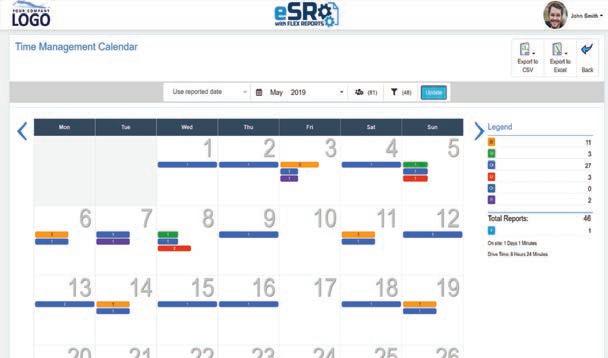
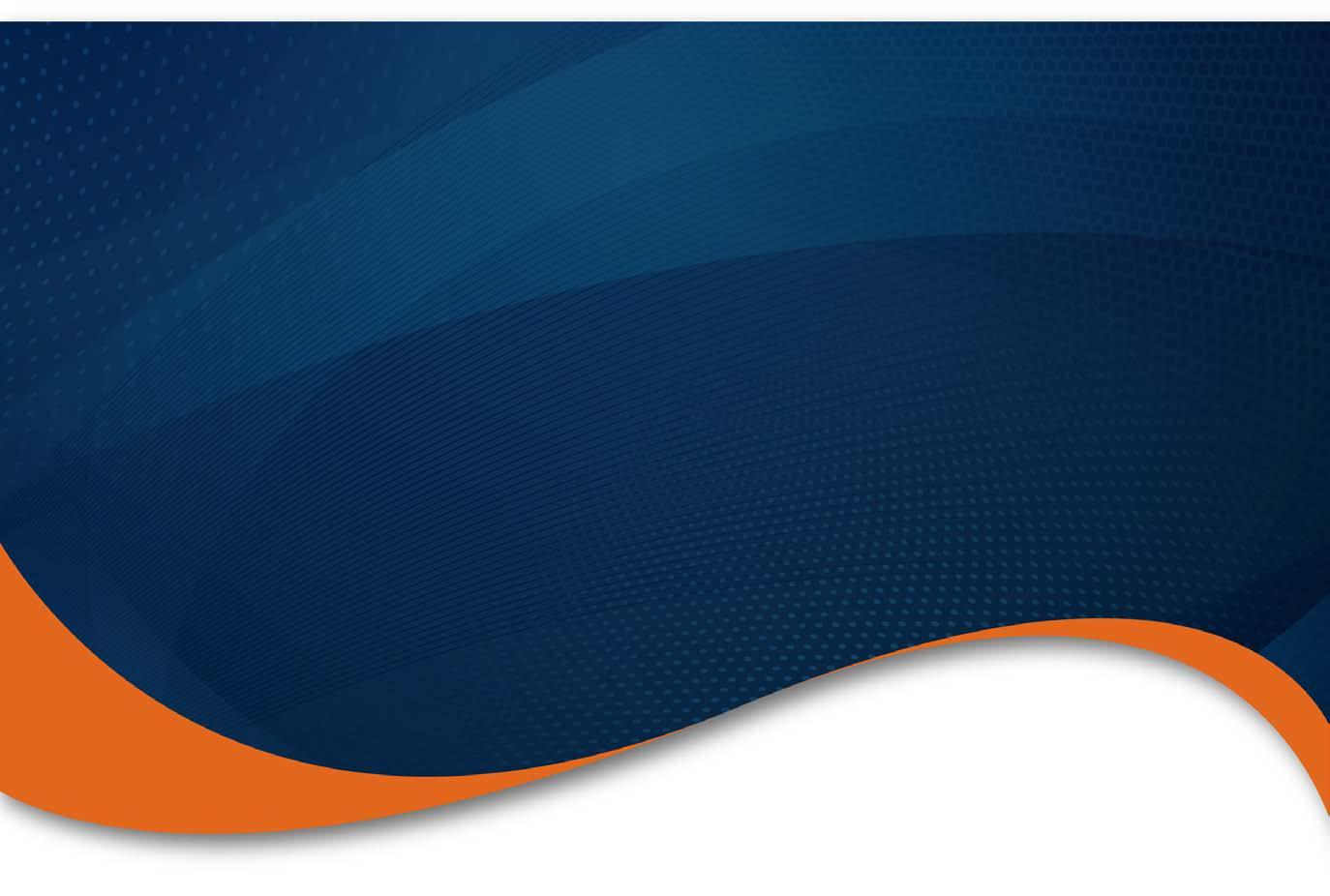
What Is the Relationship Between Amoeba and Legionella in Non-Potable Water Systems? continued
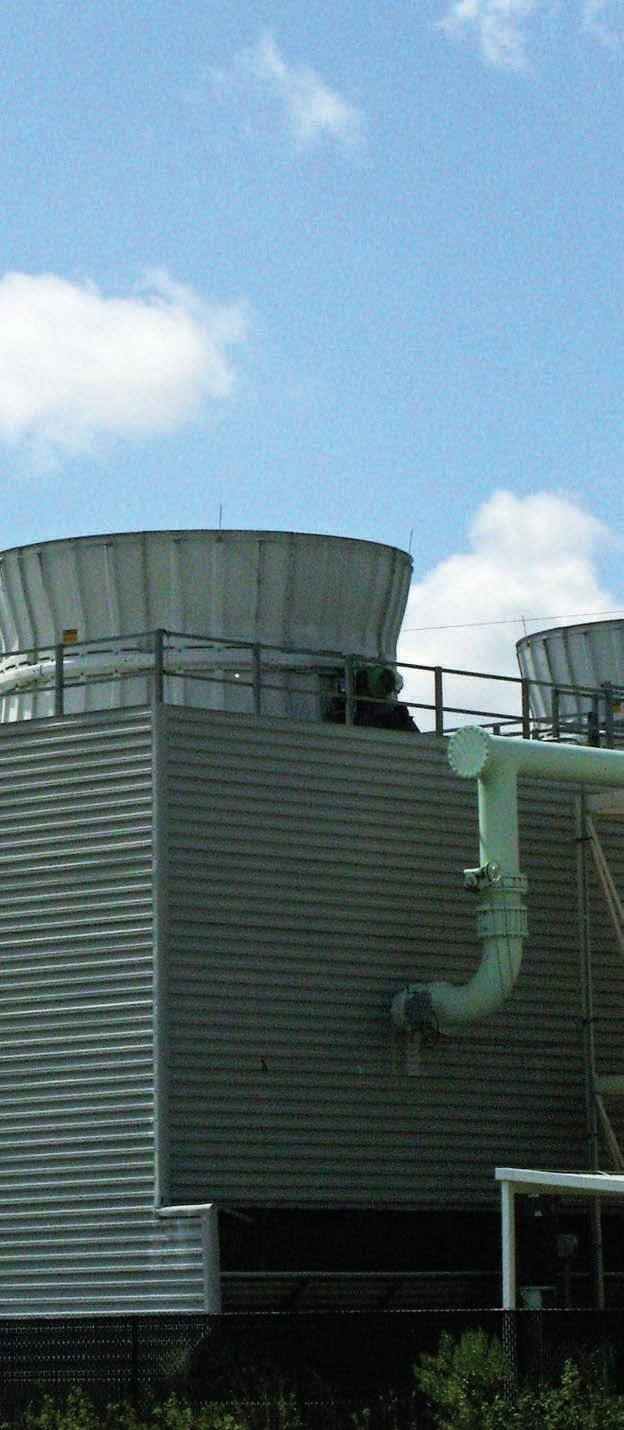
Table
microorganisms in non-potable water. All samples were selected randomly.
As can be observed from the data in Table A, amoebae were present in all identified ranges, including when Legionella and TPC were absent. Though Legionella and TPC were absent in these samples (n=127 and 36, respec tively), amoeba occurrence in these samples is not unex pected since FLA feed on fungi and algae in addition to bacteria. These results were in contrast to a previous investigation with potable water where amoebae were present in all the identified ranges, with the exception of samples with no Legionella and TPC concentrations of less than 10 colony-forming units per mL (CFU/mL).
Table B shows that when water samples tested positive for amoeba, these samples contained almost equal numbers of viable (n=95) and nonviable (n=96) amoebae. This could be an indication that between the times of collec tion and processing, there is some die-off of amoeba.
The probability that TPC and Legionella concentrations had anything to do with the presence of amoeba is not demonstrated by t-test probabilities done for all available concentration ranges except for Legionella and TPC in the range of 100 to 999 CFU/mL. At this range, the p value with and without amoeba was 0.002 for Legionella and 0.048 for TPC, indicating that the relationship between Legionella and amoeba and TPC and amoeba is statistically significant. Even when no detectable Legionella or TPC were observed, amoebae were detected in 83 and 24 samples, respectively. These results are in contrast to our previous observations in potable water, where amoebae were present in all ranges except for samples with no Legionella and TPC concentrations of less than 10 CFU/mL (8).
50 the ANALYST Volume 29 Number 3
B: Numbers of Legionella, TPC, and Amoeba for Positive-Testing Field Samples in Non-Potable Water Legionella TPC AmoebaLive AmoebaDead Maximum cells/ mL 430 500,000 123,708 477,158 cells/mLMode 10 10 13,254 4418 cells/mLAverage 78 10,931 25,977 33,744 Number of samples 171 171 95 96
TPC versus Total Amoeba -0.04
hours for the three tested concentrations. After 1,440 minutes of contact time at all three concentrations, 0 ppm of chlorine remained in solution.
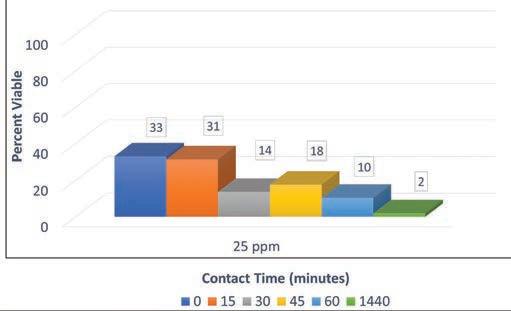
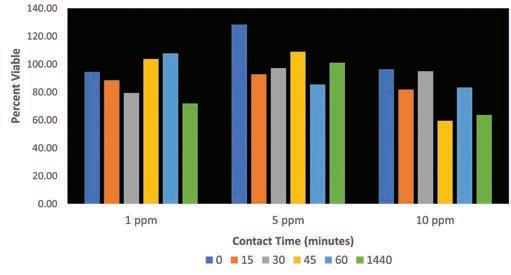
Table C: Correlations Between Microorganisms in NonPotable Water
Correlation (r)
The presence of total number of amoeba (dead + alive) is weakly negatively correlated with the presence of either Legionella (r = -0.014) or TPC (r = -0.04), indicating that as one variable increases, there is a decrease in the other. There is a weak positive correlation (r = 0.25) between the concentration of live and dead amoeba, which is unexpected. There is also a weak positive correla tion between Legionella and TPC (n = 0.37), which is different from the results obtained in potable water (8). This data is shown in Table C.
Figure 2: Effect of Isothiazalone on survival of amoeba.
In Figure 2, data indicate that the two concentrations of isothiazalone tested are unable to exert a significant amoebicidal effect and that there is no linear relationship between concentration and time tested. The two concen trations tested were the minimum (35 ppm) and maximum (219 ppm) doses suggested by the manufac turer as maintenance concentrations when microbial control is evident in a system. Even after a 24-hour isothiazalone treatment with 219 ppm, the percent viability remained high at 76%, suggesting that this microbiocide is not an effective amoebicide at the concentrations tested.
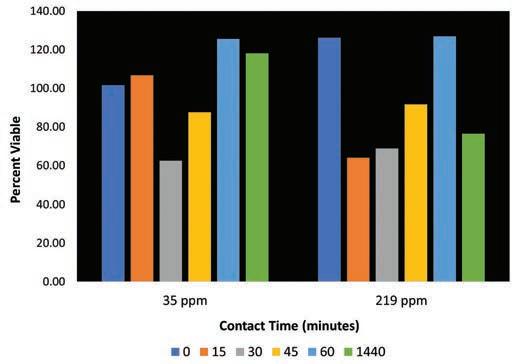
Modes for field samples tested positive for live/dead amoeba well above the minimum detectable concen tration of 3 cells/mL. In our previous research, potable water samples were more likely to contain viable rather than nonviable amoebae, indicating that between the times of collection and processing, most of the amoebae remained viable (7). The numbers of Legionella and TPC were typical of previously reported values (7, 9).
**Live versus Dead Amoeba 0.25
A quaternary ammonium compound (dodecyl dimethyl ammonium chloride [DDAC]) served as the positive control. In previous experiments, this compound affected a complete kill of amoeba (8) though in the current
Cells/mL
The data in Figure 1 indicate that a typical (1.0 ppm) and maximum allowable concentration (10.0 ppm) of free chlorine for non-potable water treatment are unable to exert a significant amoebicidal effect. There appears to be no linear relationship between contact time and percent viable amoeba at any of the tested concentrations, though there is a small decrease in viability by the end of 24
What Is the Relationship Between Amoeba and Legionella in Non-Potable Water Systems? continued
Figure 3: Effect of DDAC on survival of amoeba.
*Excluding Legionella samples pre-selected as having no detectable Legionella (<0.05 **ExcludingCFU/mL).samples that had no detectable amoeba.
Figure 1: Effect of free chlorine on survival of amoeba in non-potable water.
Legionella versus TPC 0.37
51 the ANALYST Volume 29 Number 3
*Legionella versus Total Amoeba -0.014
The two concentrations of isothiazalone tested were unable to exert significant amoebicidal effect.
What Is the Relationship Between Amoeba and Legionella in Non-Potable Water Systems? continued
Based on this research, the author has the following observations about the relationship between amoeba and Legionella in non-potable water systems:
52 the ANALYST Volume 29 Number 3
The author would like to thank Carmel Holliday for her help with data collection, the U.S. Environmental Protection Agency’s Office and Research and Development for the amoeba cultures, and Weas Engineering for its continued support of our research projects.
6. National Research Council (US) Safe Drinking Water Committee (1987). Drinking Water and Health: Disinfectants and Disinfectant By-Products, vol. 7, National Academies Press, Washington, D.C.
7. Selvaratnam, S.; Coughlin, M.; Holliday, C. (2020). “Association of Amoeba and Legionella in Potable Water Systems,” AWT Symposium, Association of Water Technologies, Rockville, Maryland.
Amoeba and TPC concentrations appear to be correlated positively in the ranges of 100 to 999 CFU/ mL TPC and when all ranges are compared.
References
LIVE/DEAD® fungal/yeast stain can be used effectively to determine the presence of and quantify amoeba in non-potable water.
1. CDC (November 2017). “Surveillance for Waterborne Disease Outbreaks Associated with Drinking Water—United States, 2013–2014, Morbidity and Mortality Weekly Report 66(44), Centers for Disease Control and Prevention, pp. 1216–1221.
2. Edelstein, P.H.; Edelstein, M.A. (1991). “Comparison of Different Agars Used in the Formulation of Buffered Charcoal Yeast Extract Medium,” Journal of Clinical Microbiology, 29, pp. 90–191.
8. CDC (2005). “Procedures for the Recovery of Legionella from the Environment,” U.S. Department of Health and Human Services, Public Health Service, Atlanta, Georgia.
Amoeba were present in all identified CFU/mL ranges, including when Legionella and TPC were absent.
4. Oliva, G.; Sahr, T.; Buchrieser, C. (2018). “The Life Cycle of L. pneumophila: Cellular Differentiation Is Linked to Virulence and Metabolism,” Frontiers in Cellular and Infection Microbiology, 8, p. 3.
This paper was presented at the 2021 AWT Annual Convention & Exposition, which was conducted September 22–25, 2021, in Providence, Rhode Island.
Acknowledgements
3. Boamah, D.K.; Ghou, Z.; Ensminger, A.W.; O’Connor, T.J. (2017). “From Many Hosts, One Accidental Pathogen: The Diverse Protozoan Hosts of Legionella,” Frontiers in Cellular and Infection Microbiology, 7, p. 477.
9. Selvaratnam, S.; Coughlin, M.; Sotkiewicz, E.; Holliday, C. (2018). “Practical Recommendations for Meeting the Objectives of the CMS Memorandum,” AWT Symposium, Association of Water Technologies, Rockville, Maryland.
Summary
TPC and Legionella concentrations are not correlated to amoeba concentrations in non-potable water except in the 100 to 999 CFU/mL range.
Shivi Selvaratnam, Ph.D., joined Weas Engineering in 2016 as the senior microbiologist and currently serves as the director of the chemistry and microbiology labs at Weas. Dr. Selvaratnam received her doctorate in microbiology from Drexel University and subsequently completed her post-doctorate at the University of Notre Dame. She worked in academia for seven years as an assistant professor of biology, teaching courses in microbiology and conducting research on the effects of pollutants on microbial communities in freshwater ecosystems. Prior to joining Weas Engineering, Dr. Selvaratnam worked as a technical environmental specialist at the Indiana Department of Environmental Management. She may be reached at shivi.selvaratnam@ weasengineering.com
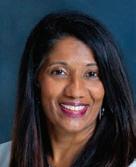
5. Abdel-Nour, M. Duncan, C.; Low, D.E.; Guyard. C. (2013). “Biofilms: The Stronghold of Legionella pneumophila,” International Journal of Molecu lar Sciences, 14, pp. 21660–21675.
There was no linear relationship between contact time and percent viable amoeba at any of the tested concentrations of free chlorine.
investigation, viability of amoeba was 2% at the end of the experiment (1,440 minutes). Though DDAC did not affect complete kill, the significant reduction in viability of amoeba suggests that targeting the membrane of these organisms may be a more effective disinfection strategy rather than oxidation and/or chlorination of a reactive moiety such as primary and secondary amines. Figure 3 shows the effect of DDAC on amoeba survival.
With increased biocide costs on top of increased inhibitor costs, plus supply issues… ‘Tis not the time to run afoul with fouled systems! Clean it Up & Keep it Clean® ® Use BCP ® Products* for Cooling Water System Cleanup and MaintenanceBCP®Products (DTEA II® / DTEA II® Plus) are a phone call away! AMSA, Inc.® 4714 S. Garfield Rd Auburn, Michigan, USA • 48611 Tel: (989) sales@amsainc.com662-0377 www.amsainc.com • Concentrated doses 50-150 ppm of BCP ® 1015 or BCP ® 2175 • Clean and remove organic deposits via blowdown & filtration Fast Off-Line Cleaning Controlled On-line Cleaning Two Ways to Clean it Up • Slightly elevated slug doses with BCP ® 1015 or BCP ® 2175 are monitored over time until system metrics meet ‘target level of cleanliness’ Slug Dose Maintenance Cleaning Programs Two Ways to Keep it Clean • Maintenance doses 25-65 ppm of BCP ® 1015 or BCP ® 2175 Continuous Dose Maintenance Cleaning Program • 50-150 ppm continuous dose of BCP ® 6010 based on blowdown *DTEA II® / DTEA II® Plus
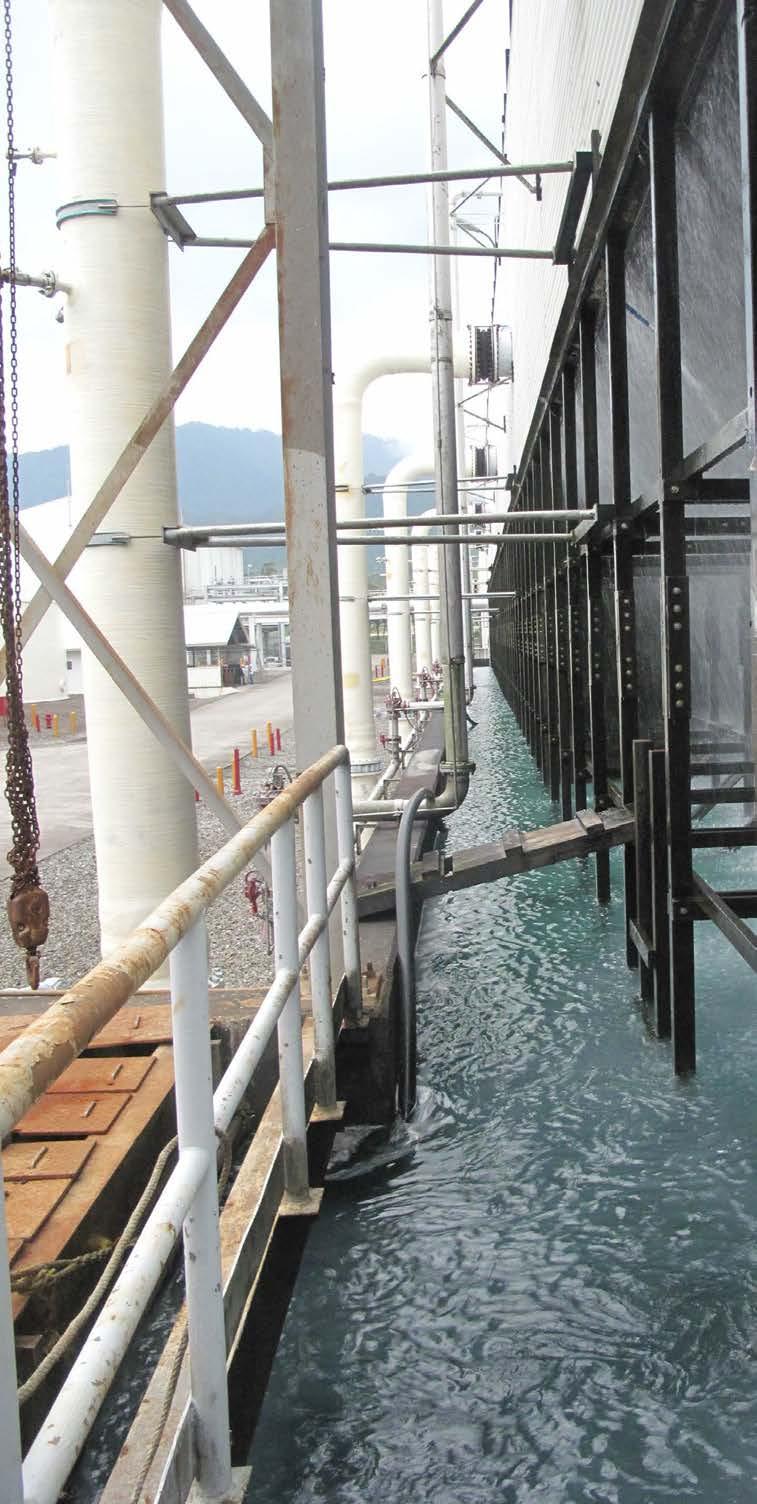
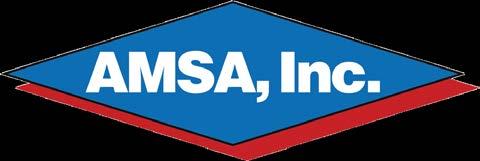
How Can the IoT (Internet of Things) Support Industrial Water Treatment?
Laith Charles, Watermark LLC
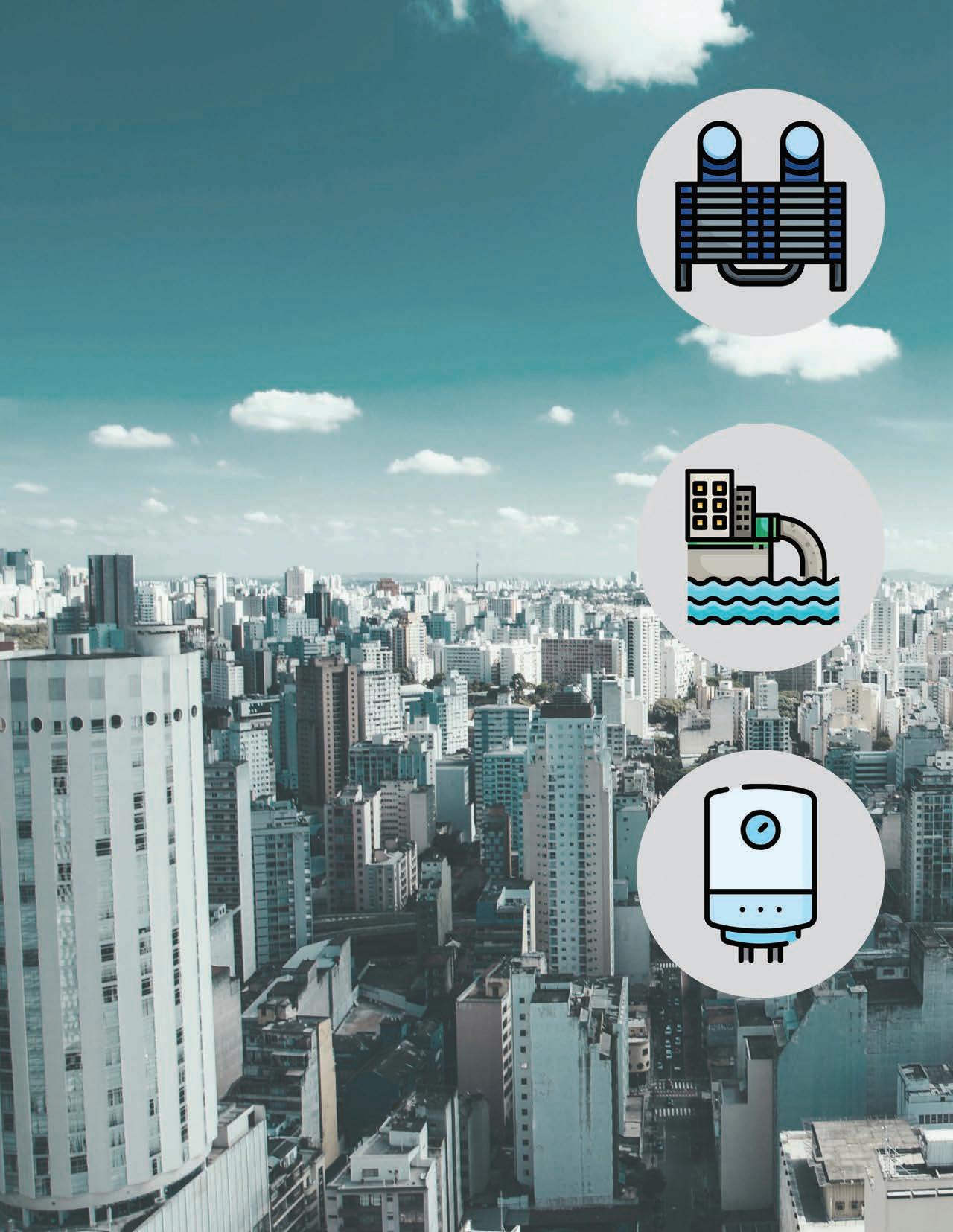
A dynamic and evolving landscape of connected tech nology presents a daunting opportunity to revolutionize the way we manage water treatment. With current tech nology, it is possible to know immediately when there is a system upset. Most new treatment equipment is either equipped with a connectivity standard or has an optional
Interconnected controllers predate to the 1990s. For example, Pulsafeeder’s MCT210 system was established in 1991. It came with the Layer 2 Connection (L2 option) and was capable of interfacing with a networked computer through an analog modem. Also, a software suite called PULSAworks allowed users to access realtime system values by remotely changing operating parameters, viewing historical data, and even receiving a callout in the event of alarm conditions.
Current State of Networked Devices
Origin of Networked IWT Controllers
Most middle market industrial water treatment control lers are still not actively networked. Much of the existing installed infrastructure is simply incapable of managing a network stack and connecting to the internet. Newer middle market controllers in the last 10 years can handle all these protocols and more: Modbus, Building Automation Control Network (BACnet), and the full Transmission Control Protocol/Internet Protocol (TCP/ IP) stack to get on the internet. Depending on the equipment and the manufacturer, systems can either interconnect with an optional communications card or remain standard with the base controller.
Currently, there are several technophilic companies choosing to standardize on remote communications. These companies leverage cloud connectivity and the added value of online tools as part of their business
Current State of IoT
55 the ANALYST Volume 29 Number 3
Additionally, cellular modems can get process control lers online without relying on the customer’s ethernet connection. The price point of online-capable devices has decreased, and the value proposition of the online capabilities has improved along with the demand for connectivity options. Depending on how you define middle market industrial water treatment, only about 40% of new controllers sold in 2020 are equipped out-the-door with networking functionality, and a much smaller percentage of these devices are ever networked. Approximately 4 to 5% of current state middle market process controllers are networked; however, several market conditions are forcing water treatment to leverage online connectivity. Some of the factors driving connected options include competition, regulation, resource management, and customers.
Thisupgrade.wave
of connected devices presents a future where online visibility to all your system parameters is at your fingertips. The price point of connected equipment is decreasing, and the number of available connected options is increasing. Meanwhile, the cost of labor is going up, and the supply of labor is scarce. This article will analyze the current state of conventional water treatment methods, highlight some existing Internet of Things (IoT) augmented water treatment methods, and project theoretical use cases and future IoT water treatment models, leveraging connected devices to either optimize workflow or heighten quality control.
The percentage of controllers sold with connectivity in the early 1990s was around 5% due to the large costs associated with getting equipment networked as well as the added cost of modems and need for a clean analog line. The equipment sales were simply pre-purchasing the communications functionality for future connectivity of which was rarely leveraged. Over the years, these previously premium and costly functions became more cost competitive. For example, analog-wired connections became reliable digital connections that could either be wired or wireless. Less reliable one-way protocols were even replaced with complete communication stacks; however, these initial improvements led to lackluster market adoption and diminished the value sell proposi tion of the platform.
First generation networked controllers were also pointto-point communications with limited access to a single controller at a time. Building out multiple processes at a specific location was often time-consuming and extremely cumbersome. These were groundbreaking features in this market, but it was still not enough. The introduction of first-generation interconnected control lers did not exhibit any noticeable market push on water treatment. The reliability, scalability, capability, and overall installed cost all needed to significantly improve to drive adoption rates.
application for leveraging IoT devices to augment water treatment is a passivation treatment developed by EVAPCO that allows end-users to put an immediate heat load on a newly installed cooling system. The process involves two steps: 1. A factory applied pretreatment, and 2. A tightly monitored and controlled in-field passivation process. The in-field portion of the passivation requires site-specific chemistry, a local service provider, help from the installing contractor, and the cooling tower maker’s feed and control panels. Remote monitoring of this process through an online
model. To do this, they either build in the price of connectivity in their service contracts or apply it as a fixed overhead expense as an integral part of their opera tions. Some companies, either by choice or to stay within regulatory compliance, are forced to lean on connec tivity. Largely as a response to heightened visibility to Legionella , some regulations allow for lesser testing inter vals when treatment is supported with online controllers. Markets are also pushing to migrate to a connected equipment package due to competitive pressure, upselling services, or compliance reasons. To remain in compliance, the market share of connected devices has been growing steadily, and within the next few years, the majority of sold controllers will have connectivity options standard, with around 25% of new controllers expected to be capable of 24/7 online service.
Anotherorganization.real-world
How Can the IoT (Internet of Things) Support Industrial Water Treatment? continued
In the last five years, regulatory entities have increased their supervision of evaporative cooling systems. The presence and risk associated with Legionella has been a driving factor for more legislated oversight. This is leading companies to find creative ways to meet the heightened testing and reporting requirements. New York City is the most stringent area in North America for keeping open-loop cooling systems compliant. For example, New York City Chapter 8, Title 24 requires performing routine manual water-quality moni toring of temperature, pH, conductivity, and biocide
Since these installs depend on connectivity, Mr. Baskin has invested in several internal resources to develop failsafes and procedures to detect if a modem or controller were to go offline and stop reporting so that they can quickly troubleshoot and keep their customers compliant with reporting requirements. He is constantly looking for smarter tools that work with his company and solve problems versus creating different problems. When everything is functioning as it should, these tools help remove burden and unnecessary busy work from the working day so that they can focus on other aspects of their
56 the ANALYST Volume 29 Number 3
monitoring must occur at least three times per week with no more than two days between monitoring. This manual process is required unless it is automated. To replace the need for manual testing, reports from IoT-augmented water treatment equipment can be used to stay in compliance instead. Without online visibility, facilities personnel would need to perform the testing, the number of required service visits would need to skyrocket, and the cost of a service contract would increase to counterbalance labor elements. In this instance, many accounts simply upgraded all the water treatment equipment to online as well as having a dedicated online controller. This option was much easier than tripling your workforce overnight or reducing the capacity of the current staff.
However, R. Baskin (1) reported in a technical paper from the 2018 AWT Annual Convention that this is easier said than done. “Several setup steps have now been added to our standard start-up procedure,” he stated at the conference. Mr. Baskin reported on the need to bring controllers in house for configuration prior to deploying on the field. Additionally, the pain point of establishing a cell modem connection and maintaining it reliably over time is one more thing to manage, as it commonly complicates installs. “Initial connectivity can require changing which cellular carrier the modem connects to or feeding long antenna wires up a few floors where there is a better cell signal,” he said.
Toconcentration.remaincompliant,
While leveraging online connectivity and reporting is great in theory for automating an otherwise very manual
process, reliability of this solution is paramount. In the real world, there are still some hurdles to overcome. If we shift our mentality to require online connectivity as an integral part of our business to manage our evaporative cooling systems, which is common in New York City to maintain regulatory compliance, then reliability becomes vital. We want technology and connectivity to synergize and augment our business as usual and automate what would otherwise be manual processes.
control equipment were online and reliably networked, could we fundamentally shift our service model? With complete transparency to all probe measurements, tank levels, water meters, and more, it is simple to mine infor mation from accounts prior to rubber hitting the road.
In another reaction scenario, when we check our high-conductivity alarm, we might see that the bleed relay has been energized for hours. Despite the contin uously energized bleed valve, the conductivity in the
57 the ANALYST Volume 29 Number 3
portal A allows for 24/7 visibility to critical system parameters during the infield passivation process to help identify potential issues before they become problems.
Figure 1: Example of controller probe and relay data.
For instance, an online controller goes into a high conductivity alarm. The water system supervisors get notified at 9:23 am of the system upset. There are at least two distinctly different reaction scenarios. First, we confirm the controller status online and check some basic program parameters: the controller programming, presence of flow, and relay HOA (hands-off operation) status. After observing the controller’s information online, we notice the conductivity is indeed high and the controller has entered an alarm state as a result; however, the bleed relay is not currently energized. In a matter of seconds, we can deduce the bleed relay is in a lockout status and we have just fed one of our biocide timers. The controller is fully functional, but seasonal demand has changed, and the tower is cycling up faster than normal.
Depending on the equipment and controller.withstandardcardcommunicationswithinterconnectcansystemsmanufacturer,theeitheranoptionalorremainthebase How Can the IoT (Internet of Things) Support Industrial Water Treatment? continued
Theoretical Uses of IoT
Continuous innovation of industrial water treatment equipment presents vast possibilities. Today’s largest water treatment issues can be largely solved by some future technology, and some of this technology already exists in either an adjacent market or at a higher price point. With current technology, it is possible to connect a cooling tower controller to the internet and receive routine graphical reports of key system parameters (see Figure Additionally,1). an immediate notification can be sent to a smartphone, or as an email, about any system upsets, such as high conductivity. While simple knowledge is powerful, knowing that key parameters stay within desired ranges allows us to validate quality of service for self-verification, company quality control, and a high service level to the customer. How else can we leverage data today? What are some improved workflows using technology in today’s state that allow for efficient use of all our resources? For a little bit of theoretics, if all our
The partners work with J. Downie (2), a startup and commissioning specialist at EVAPCO Water Systems, to set up site-specific reports and alarms. In personal communication with the author, Mr. Downie observed that “the response from our partners is that they like getting the daily reports to see how the passivation numbers are trending. The ability to see real time data reduces site visits and improves the passivation outcomes for our customers.” This technology use-case adds a level of quality control to the critical passivation process and ensures, should any system upsets occur, that swift corrective actions can be implemented prior to any system damage.
As a solution, we can remotely make some adjustments to the program to compensate for this seasonal swing by making minor tweaks to the pre-bleed and lockout settings on our biocide timer. One hour after the lockout period has expired, the bleed relay can open again, our conductivity goes back within range, and we get notified that the alarm has cleared. We now have a more refined program and did not need to adjust our schedule to accommodate an emergency visit.
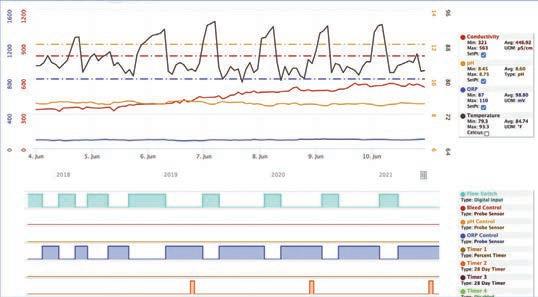
How Can the IoT (Internet of Things) Support Industrial Water Treatment? continued
On the other hand, many of the benefits of optimizing the controller programming are based on historical performance, and the cost impact of response time to the end-user is Simulationastronomical.of
Table A: Sample Water Characteristics for Simulated Model Parameter Value
process continues to rise. When the probe measurements do not match our control measures, we know there is something wrong, and we would like to notify onsite personnel and schedule an impromptu service visit to remedy the issue. Knowing the exact failure mode being troubleshot and seeing the controller online prior to going onsite can ensure that you bring the correct components to fix the issue the first time. With the right spare parts kit, you can pull in the timeline to remedy the issue and reduce burden involved. This accelerated responsiveness will help reduce company attrition rate, improve the percentage of time your chemistry is within desired control ranges, and fix most issues during the initial visit as opposed to making multiple trips.
All these measures impact a company’s internal operations, such as account reten tion and human resource management. Keeping accounts and freeing up time are invaluable for having companies operate at their best. Nevertheless, these benefits still amount to customer hesitation. The upfront burden of modem costs, setup fees, and the recurring data fees frequently seem difficult to justify. Additionally, the learning curve of figuring out a process and training your team to support connectivity can seem intimidating. These factors have stacked up to push a lackluster market adoption.
Makeup conductivity 150 S/cm Makeup total alkalinity 120 ppm Makeup calcium hardness 40 ppm System tonnage 500 Drift rate 0.05%
the operation of a water treatment system is important because it will show an end-user the likely opportunity cost when a process control system is used. To be consistent, let us take the high-conductivity example and run a simulation where we compare effi ciency loss in a chiller as a function of response time. Statistically, without customer intervention, we will catch process issues at 50% of our service interval. Conversely, if we are notified of high conductivity online, then we should be able to remedy the system within 24 hours of receiving the alarm. Table A shows the system parame ters of a computed simulated failure mode.
Cost of power 15 c/kWh
The cost of operating a chiller with these parameters (as featured in Table A) for a year at 6,500 hours and a 70% average load during operation is approximately $220,000 per year. The difference in responding in 24 hours to system upsets versus 15 days is exorbitant for scale deposition. Deposited scale will indef initely add to chiller inefficiency until removed, which typically involves some level of system shutdown. Responding within one day leads to less than 1 mil of deposition in our simulated example, and conversely, responding in 15 days to this upset leads to over 1/64th of an inch of scale deposition (see Figure 2). This would cause a site’s chiller to be 16.2% less efficient and likely lead to other issues within the evaporative cooling system. Within the 15-day span alone, the end-user would spend ~$1,200 more in energy. Should the scale stay on the chiller tube over the course of a whole year, it would cost an extra $35,640 per year to run that 500-ton chiller.
The interesting aspect of this simulation is that scale does not deposit immediately. The Langelier Saturation Index (LSI) needs to be in a scaling state for some time before the point of nucleation begins; then, scale will ramp up the speed of deposition until the flow of the water in the chiller starts breaking off the deposits. The rate of deposition drops off asymptotically. The key difference is response time. A detailed view of the math used to power this tool can be found at: https://ewater mark.net/murphys-law-of-scaling-up/ This is a great example of a value-add service, as online visibility can remove burden from customers and empower them with
58 the ANALYST Volume 29 Number 3
Frequency of service 30 days Cycle of concentration setpoint 3.5
On the other hand, many of the benefits of responseimpactandperformance,onareprogrammingtheoptimizingcontrollerbasedhistoricalthecostoftime to the end-user is astronomical.
11335 Lewis Braselton Blvd. Braselton, GA 30517 (Fax)770-978-1443770-978-4165 www.biosourceinc.cominfo@biosourceinc.com 2021 Supplier of the Year • Biocides (oxidizing & non-oxidizing) • Polymers, azoles, phosphonates, sod. molybdate • Repacking (all drum sizes and pails available) • Regulatory and technical assistance Having LetAvailabilityProductIssues?ushelpyoupieceitalltogether. IN BUSINESS SINCE 1991.

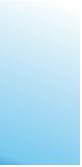


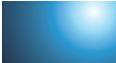
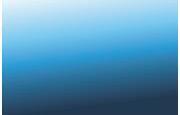
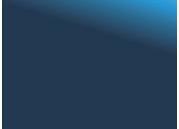
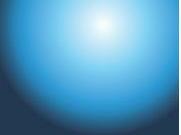
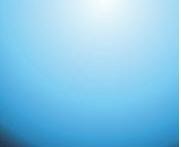
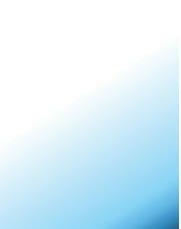
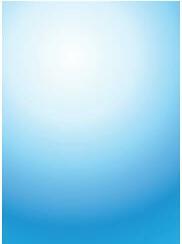
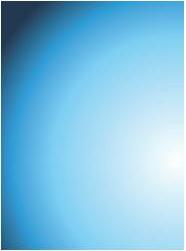
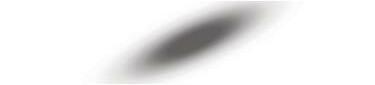















60 the ANALYST Volume 29 Number 3
3. O’Reilly, V. (Spring 2021). The Metro Group, Boston, Massachusetts, personal communication with L. Charles, article author.
The current state of water treatment control technology is just the tip of the iceberg. While there is a lot we can do today, several innovations will need to follow suit to improve this platform. The Metro Group on the Eastern Seaboard have been working with online controllers for over six years. For The Metro Group to comply with state and local regulations in New York, online visibility and reporting is convenient and has even become necessary for some clients. Although of course, the equipment is only as good as its ability to measure important species in water.
While some probes like a toroidal conductivity probe are extremely robust where measurements do not drift over time, industry standard pH and oxidation reduc tion potential (ORP) probes degrade and require even tual replacement. V. O’Reilly (3) of The Metro Group believes sensor electronics still have a way to go to meet the market needs, as current probes are either relatively cheap and require more frequent calibration and replace ment or they cost too much for the market to bear. When you need to make water treatment decisions based on your online controllers’ capabilities, you must be able to trust that your probe readings are accurate.
A The online portal mentioned in the text is through Pulsafeeder’s Pulsalink.
Laith Charles is president of Watermark, a manufacturers’ representative of water treatment equipment, and CTO of Dosinfection, an OEM/distributor of hydronic solutions. He is the first recipient of AWT’s Rising Star Award and a degreed electrical engineer, who is focused on improving sustainable-use and resource management of aquatic systems. Mr. Charles can be contacted at laith@ewatermark.net
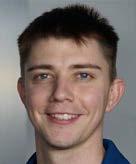
This paper was presented at the 2021 AWT Annual Convention & Exposition, which was conducted September 22–25, 2021, in Providence, Rhode Island.
The amount of energy and water we are responsible for as an industry is astronomical, and it is a moral obligation to police the efficient use of them. Who knows what exactly the future looks like? We might have predictive failure analysis for systems performed on the cloud side, merging of data between a chiller and its efficiencies and the water treatment program, a simplification of connectivity process and more and more smart devices managing processes. These advancements will compound all the time and raise the bar of industrial water treat ment and expose opportunities in the marketplace. We are at a critical time in water treatment. Enforced regula tions are trending toward becoming more stringent. Our labor pool shortage and rising cost of talent will either force an increase in the cost of services or force innova tion to efficiently use what resources we have.
How Can the IoT (Internet of Things) Support Industrial Water Treatment? continued
Future Market Needs
As the technology price continues to drop and connec tivity becomes more affordable and streamlined, the opportunity for upselling services and removing complexity from the current status quo will be inter esting to watch unfold. Whatever the future looks like or becomes, IoT will play an integral role in the next evolution of water treatment.
References
Figure 2: Graph of simulation example.
The power of future state process data on a large scale specific to water treatment systems is exciting. Today, technology can lead to incremental process improve ments and optimizations that will spread over all the accounts we manage. Water and energy are both valuable resources. As water treatment professionals, equipment manufacturers, and chemical blenders, we can make a massive difference to the use of these resources.

1. Baskin, R. (September 2018). “Legionella from a Water Treater’s Perspective,” presentation at AWT Annual Convention & Exposition, Orlando, Florida.
2. Downie, J. (Spring 2021). Evapco Water Systems, Manchester, Maryland, personal communication with L. Charles, article author.
visibility to the process to ensure better quality control of the water treatment program.
Endnote
Conclusion
If you have trouble signing in or have any further questions, please contact:
Did you know you can manage the notices you receive from AWT?
Be Sure You’re Taking Advantage of Your AWT
Emails From AWT.
Sign in to the AWT website and select your communication choices and complete your profile today.
Membership Benefits
It’s the best way to ensure you learn about all AWT benefits in a timely manner.
61 the ANALYST Volume 29 Number 3
Angela Pike
Senior Member Services Manager (240) apike@awt.org404-6477
SignBenefits:UptoReceive
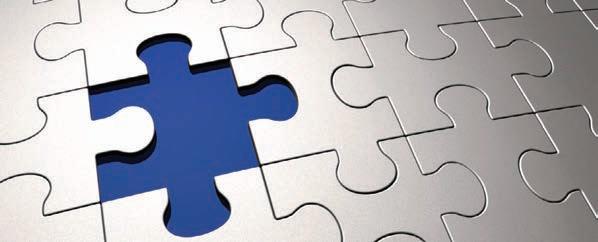
Cortec’s VpCI®-641 Hydrotest Corrosion Inhibitor Earns USDA Certified Biobased Product Label
Cortec® Corporation is pleased to announce that VpCI®-641 and VpCI®-641 PTSA corrosion inhibitors for hydrotesting and fresh water cooling systems have earned the USDA
H2O 62 the ANALYST Volume 29 Number 3 H2O
Certified Biobased Product label. These products repre sent Cortec’s commitment to developing technologies that use biodegradable and renewable materials where possible, allowing industries to fight corrosion in an environmentally responsible manner. VpCI®-641 offers an economical, “greener” alternative to other hydro testing products on the market that are not biobased and must be used at a higher dosage.
Aliquot Pro is avail able for download on the iOS app store and Google Play. For more information, visit aquaphoenixsci.comScientific,aboutForaliquotproesrflexreports.com/www..moreinformationAquaPhoenixvisitwww..

CommentsVoice-to-Text–dictate commentsreportusing voice to text
View Last Three Results – See recent test history when writing reports (online mode)
Industry
“We applaud Cortec® Corporation for earning the USDA Certified Biobased Product label,” said Vernell Thompson, USDA BioPreferred® Program. “Products
Turnkey Report Entry – Automatically sync data directly to your eSR site
VpCI®-641 is a water-based blend of contact and vaporphase corrosion inhibitors for protection of ferrous and non-ferrous metals (including copper, aluminum, and brass) in industrial waters. VpCI®-641 contains 69% USDA-certified biobased content and can be used at fairly low concentration levels for greater economy and lower conductivity. VpCI®-641 provides corrosion protection during hydrostatic testing and in some cases can be used in closed-loop cooling systems filled with fresh water. VpCI®-641 PTSA includes a PTSA tracer option that makes it easier to monitor proper concentra tion for ongoing effectiveness in closed loops and reused hydrotest water. When it comes time for wastewater disposal, VpCI®-641 makes the process easier as a biode gradable water treatment product that does not contain nitrite or phosphate inhibitors.
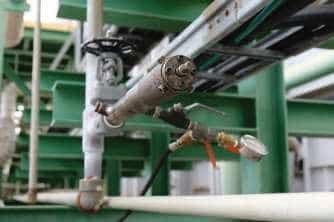
Aliquot Pro, a Free Mobile Companion App for eSR AquaPhoenix announces the launch of Aliquot Pro, a free mobile companion app for eSR that is included with every company’s subscription. Aliquot Pro is designed to give you and your customers the ability to manage data from any location and device.
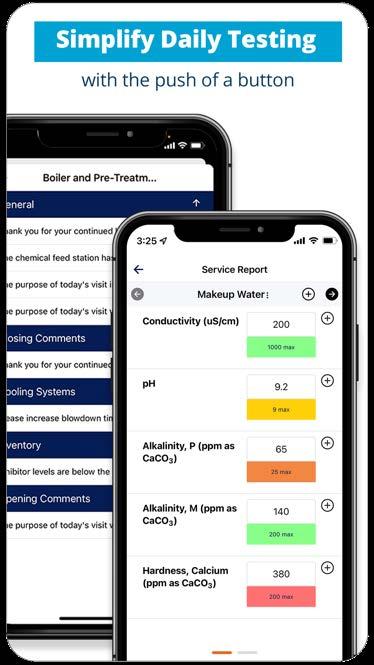
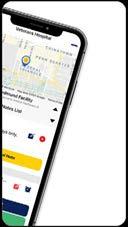
ConnectivityController – View recent data history and connect to your compatible controller
Quickly
AquaPhoenixNotesLaunches
When used together, eSR and Aliquot Pro allow you to create a centralized location for data entry, data storage, and analysis. Key features of the app include:
FAS-DPD is a method for testing sanitizers that uses drop-wise titration instead of color matching.
French Creek Software Awarded Innovation Award
Why Choose FAS-DPD?
The Innovation Award was created to recognize the innovative application of technical expertise or experience with industrial process heating and cooling equipment and projects or efforts to reduce costs, improve thermal processing efficiency, and increase safety. In Robert’s honor, a $1,000 scholarship was made in his name at the University of Minnesota, College of Biological Sciences, AXE Professional Chemistry Fraternity.
No color matching needed. Even a user with color vision deficiency can see the color change at the endpoint of the titration from pink to colorless.
There is no wait time for full color development. This method is accurate and repeatable, no matter what the lighting is in your facility. No electronic meter is needed to read the results.
Read chlorine as low as 0.2 ppm and as high as 20 ppm without reagent bleaching.
FAS-DPD Testing for Sanitizers From Taylor Technologies
In addition to creating an opportunity for industries to demonstrate their commitment to sustainability by the voluntary use of biobased products, the USDA BioPreferred® Program also includes a mandatory federal purchasing initiative for federal agencies and their contractors, with special biobased purchasing requirements for products in 139 identified categories. VpCI®-641/VpCI®-641 PTSA surpasses minimum biobased content requirements under the Corrosion Preventatives category (53% minimum biobased content). By using these products, federal agencies and contractors can comply with federal purchasing preferences in their everyday product acquisition. For more information, visit https://www.cortecwatertreatment.com/contact-us/
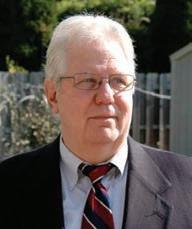
Testing for chlorine and other sanitizers is essential for protecting food safety. Many facilities rely on colormatching tests to determine chlorine levels, which can result in human error when comparing the pink color created (especially in fluorescent lighting). For a complete listing of our water-testing products, visit www. taylortechnologies.com
At the end of June, hundreds of industrial process heating and cooling equipment professionals gath ered at the Donald E. Stephens Convention Center in Rosemont, Illinois, for the inaugural Process Heating & Cooling Show
The inaugural Innovation Award was presented to Robert J. Ferguson for French Creek Software, the industry-standard modeling program for cooling water systems. “Rob developed the first easily understood method for interpreting scaling indices that is widely used and accepted. He also has developed and implemented the concept of 3D graphs of operating profiles that indicate scale potential and the associated inhibitor dosage and failure points,” noted Michael Bourgeois of Chemco Products, one of several to nominate Robert for the award. French Creek Software was founded by Robert and his wife, Janet, in 1989. In accepting the award, Ferguson credited his wife, who played integral roles in the company while the couple raised their family. “Rob and Janet’s contributions to those involved in water cooling cannot be overstated,” said Linda Becker. “Their modeling software provides the foundation for numerous programs still in use today to optimize cooling water treatment selection, troubleshooting and evaluation.”
from Cortec® Corporation are contributing to an ever expanding marketplace that adds value to renewable agriculture commodities, creates jobs in rural communi ties, and decreases our reliance on petroleum.”
63 the ANALYST Volume 29 Number 3 Industry Notes continued
7838 N. Faulkner Road Milwaukee, WI 53224
AWT Membership
Founded in 1973 in Compton, California, Lakewood Instruments was among the first companies that manu factured water treatment controllers. When expan sion was needed, founder Bob Doenges moved the company to Glendale, California. In 1994, Lakewood was purchased by Osmonics and moved to Glendale, Arizona. In 2000, Osmonics was bought by GE and became part of GE Water. In 2003, GE moved the oper ations to Glendale, Wisconsin, and then in 2005, Bill Brink purchased Lakewood. Mr. Brink also owns ETI, the manufacturer of the printed circuit board compo nents used in Lakewood products, and he moved the operation to Milwaukee, Wisconsin.
64 the ANALYST Volume 29 Number 3
Phone: (414) 355-2807 (800) Website:csd@lakewoodinstruments.com228-0839www.lakewoodinstruments.com
Lakewood Instruments
AWT Awards
Bill Brink, President/Owner; Donald Wiseman, Director of Operations and Marketing; Paul Peacock, Regional Sales Manager.
Lakewood Instruments currently serves all parts of North America from its Wisconsin location.
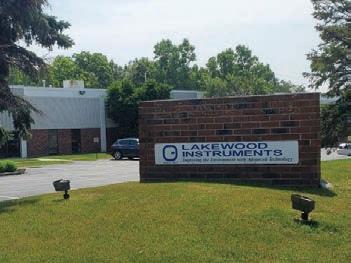
Top Executives
Current Business
Lakewood Instruments offices in Milwaukee.
Discovering AWT
Lakewood Instruments was honored with the AWT Supplier of the Year Award in 2011.
Lakewood Instruments designs, manufactures, and sells cooling tower and boiler conductivity and chemical feed controllers for the water treatment industry. Other parameters, such as pH and ORP, can be controlled using numerous user-configurable feed schemes inherent in the company’s controllers. In addition, Lakewood provides drum switches, various transmitters and pre-amplifiers, plumbing accessories, water meters, and process sensors. The company’s goal is to work with water treatment service, and chemical providers, by meeting and exceeding their facility water treatment equipment needs.
Company History
Lakewood Instruments has been a member of AWT since the early 1990s.
Geographic Areas Served by the Company
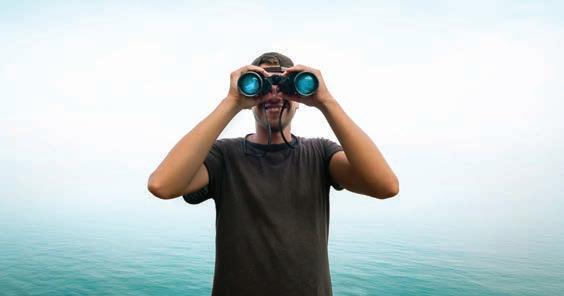
4138 South Creek Road Chattanooga, TN 37406 (423) 316 www.radicalpolymers.com9877
AWT Awards
Radical Polymers received the 2018 AWT Supplier of the Year Award.
Company History
Current Business
Radical Polymers, LLC
AWT Membership/Involvement
Top Executives
Company partner Mike Standish became an AWT member in 1990. Radical Polymers joined AWT in 2014. Radical Polymers has presented papers at AWT conferences, of which two have been published in the Analyst. Mr. Standish has served as a supplier representa tive on AWT’s Board of Directors.
Mike Standish, Vice President–Water Additives; Leslie Standish, Co-Founder; Chelsea Farmer, Product Manager; Paul Turgeon, CEO–MFG Chemical.
Radical Polymers was founded by Mike and Leslie Standish in 2014 with the purpose of serving indepen dent water treatment companies with differentiated products backed by extensive comparative technical data. Radical Polymers launched its business at the 2014 AWT convention in Dallas, Texas. In 2016, Radical Polymers purchased its current facility in Chattanooga, Tennessee, where the company has extensive lab and pilot testing facilities. MFG Chemical purchased Radical Polymers on July 1, 2022. MFG, led by Paul Turgeon, is headquartered in Chattanooga and has extensive manufacturing capabilities for polymers and other water additives at its North Georgia manufac turing facilities.
Skid for testing treatment chemical performance inside company plant.
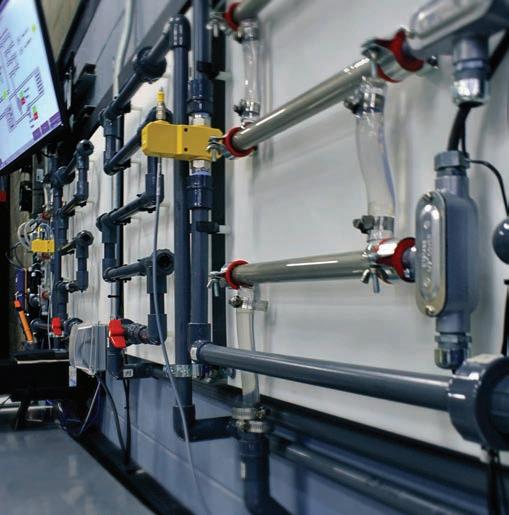
Geographic Areas Served by the Company
The company serves clients in North America, Europe, the Middle East, and Asia.
65 the ANALYST Volume 29 Number 3 Discovering AWT continued
Currently, Radical Polymers offers a wide range of polymer technologies for mineral scale and deposit control. The range of applications for the products include cooling towers, boilers, mining, geothermal, and other process water applications. Within the current range, several of the company’s polymers and blends are also NSF 60 registered for use in RO drinking water applications. Radical Polymers dedicates a large portion of its resources to product development and technical service. This has led the company to develop an extensive data package for each of its products and recent granting of a U.S. patent for the use of INITIA® 585 and related maleic technologies.
17647 Foltz www.scrantonassociates.com(440)Strongsville,ParkwayOH44149572-2277
Current Business
66 the ANALYST Volume 29 Number 3 Discovering AWT continued
From its Strongsville, Ohio, location, Scranton Associates serves clients in North America and the Caribbean.
Geographic Areas Served by the Company
Top Executives
In 1919, Leo A. Lux began to manufacture water treat ment chemicals in downtown Cleveland, Ohio. In 2008, Scranton Associates moved to our current facility in Strongsville, Ohio, about 20 minutes south of Cleveland. Scranton Associates is a family-owned business, cele brating 100+ years and four generations.
Scranton Associates manufactures (or blends, combines, dilutes, neutralizes, repackages) high-quality water treatment products to your specifications on a privatelabel basis only. Scranton Associates is an EPA-approved establishment; we are able to formulate, repackage, and re-label biocides. predominantly for the industrial water segment. Our formulations include cooling tower products, boiler products, condensate treatment prod ucts, closed-loop treatment products, glycol inhibitors, cleaners, and wastewater products, among others. We do not sell to end-users, so as never to compete with our customers. We maintain the confidentiality of customer formulas and lists. Our services include technical and regulatory support, expert assistance in developing and improving customer formulas, and SDS/label services. We offer both liquid and powder blending capabilities.
Company History
Scranton Associates Company headquarters in Strongsville, Ohio.
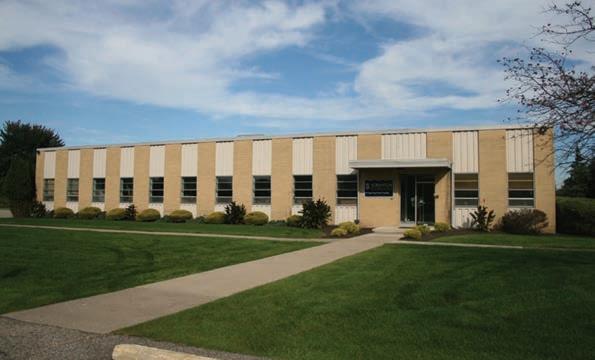
AWT Awards
Jill Cavano, President; Lee Cavano, Technical Director.
Scranton Associates, Inc.
Scranton Associates was awarded the Supplier of the Year award in 2015. Robert (Bob) Cavano received the Ray Baum Memorial Award in 1992.
AWT Membership
Scranton Associates has been an AWT member from the start. Bob Cavano has written many papers over the years, as well as the Raw Materials Specifications Manuel. Lee Cavano and Jill Cavano have both taken active volunteer roles within AWT. Lee continues to be active on the Legislative and Regulatory Committee; he was a former “Leg/Reg” Committee chair. Jill serves on the Young Professionals Task Force and is currently the chair of the AWT Business Resources Committee.
Why do you feel this credential was important to have?
I was also prompted after going to the AWT technical training seminar for the first time and seeing the amount of knowledge and experience the members had and were willing to share. During these seminars, I could begin to see just how much there is to learn (and how much I did not know). After that, I made it a goal to focus on the technical aspects of the industry and work toward obtaining the CWT certification.
There are many advantages to having the CWT designa tion. The CWT is well known within our industry and has aided me in starting new relationships with others in the water treatment field and provided me with oppor tunities to build even more. This ability to network is
I would have the say that my greatest professional accomplishment has been building strong, long-term relationships with my customers. It is very rewarding to be thought of as a resource and partner when it comes to troubleshooting complex issues or helping to conserve resources.
What are the advantages of having the CWT designation?


What has been your greatest professional accomplishment?
Having my CWT has also improved my career by helping set myself and my company apart. Being able to provide the extra value that comes with the CWT to our customers is very helpful in building and maintaining relationships.
Guardian CSC Bedford, PA
vital to staying up to date and providing the best possible services to our customers.
Turnbull, CWT
How has your CWT improved your professional career?
Also, the CWT designation is a conversation starter. Many times, prospective customers have asked about the designation and it has given me the chance to discuss the advantages of working with a CWT. In turn, our current and prospective customers can see an objective measure to our level of competence and the dedication that we have to our profession.
The CWT credential is the gold standard for our industry. It demonstrates that we as water treatment specialists take our profession seriously and are willing to invest the extra time to gain the knowledge and experi ence needed to acquire this credential. The importance in having a group of well-educated and ethical individuals goes a long way to gaining respect for the entire industry. To be part of this group is a great honor.
What prompted you to obtain your CWT, and when did you begin the process by taking the test?
The CWT designation has improved my professional career by building my confidence in my ability and knowledge of water treatment systems. The continuing education requirements also help me stay up to date on the different technologies, both chemical and equipment, that are out there.
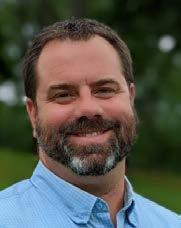
Guardian CSC has always been focused on technical training for their employees, so very shortly after I entered the water treatment industry, I was told about the CWT. The encouragement and support from the other CWT’s within the company was also a great influ ence in my pursuit of the CWT.
67 the ANALYST Volume 29 Number 3 CWT SpotlightChris
Being able to invest in and hopefully inspire the upcoming generation of water treatment professionals. I joke that I never thought in a million years I would still be in water treatment after 20 years! The water treatment industry has provided more than a job for me—it has become a career and helped develop parts of my profes sional character and expertise I didn’t know I could achieve.
What has been the most rewarding thing about volunteering?
68 the ANALYST Volume 29 Number 3
Many of the leading vendors who provide chemistries, testing, and/or equipment also attend many of the AWT events and trainings. Several times, we have met the right people at the right time to help with current needs or projects during AWT events, either at lunch or after a presentation—or right at the bar!
In the world of mentorship, you should always have someone you’re learning from in order to grow. You should also always pour into others to pass on that knowledge. Volunteering with AWT has given me both opportunities at once.
I’ve been honored to take on the role of teaching the chemistry portion of the Water Treatment Training seminar. We are working on creating a module that will help solidify the basic chemistry knowledge needed for professional water treaters and help tie that knowledge to the other aspects of the water treatment industry.
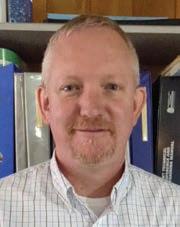
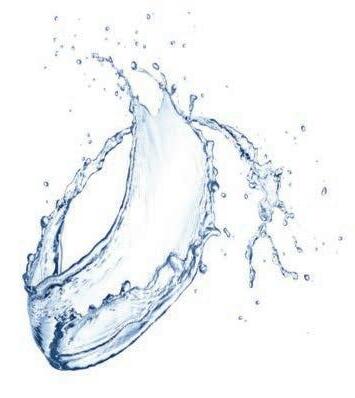
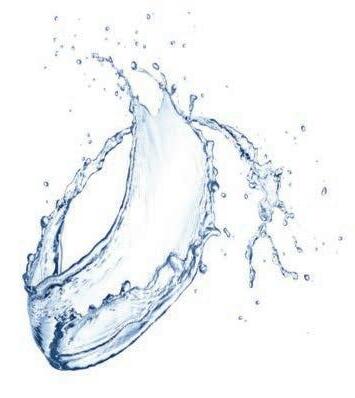
I also helped in the beginning stages of the online course Introduction to Water Treatment. This course has been a great help to our own company’s initial training for new hires to give them a solid understanding of the basics of water treatment.
What prompted you to start volunteering with AWT? I got started in the water treatment industry in February 2002 in Albuquerque, New Mexico, with Industrial Water Engineering. Two months later I was sent to my first AWT Technical Training seminar in Atlanta—talk about drinking from a fire hose! I had previously been a high school science and math teacher, so at least some of the math made sense! I was impressed by the depth and quality of the presentations, the professionalism of the instructors, and the genuine desire of AWT to provide some of the industry’s best-quality training. I have always had a desire to train and teach, so when the opportunity came up to help as an instructor, I was truly honored. I never imagined back then that someday I would have the opportunity to become part of the same training!
How has volunteering improved your professional career?
Why would you encourage others to become a volunteer?
Tell us about a current project you or your committee is working on?
Making a SplashDaniel
How have you been able to utilize the expanded business connections you’ve made while volunteering?
Merritt, CWT CH2O, Olympia,IncorporatedWashington
It has linked me with a family of professionals that I can reach out to and expect to receive honest and indus try-leading advice. It has also given a competitive edge when prospecting new business or handling challenges with current customers when they know that you are part of a professional group, such as AWT.
What is a past project that your committee produced that you feel has had the greatest impact on AWT and why?
New Hampshire: Sen. Maggie Hassan (D) won by just over 1,000 votes in 2016, and in a year that so far is trending in Republicans’ favor, she will be vulnerable in November.
The 2022 midterm elections are fast approaching and both Democrats and Republicans have a lot on the line, including control of both the House of Representatives and the Senate. Midterm elections are almost always a referendum on the incumbent president, and generally the most closely watched indicator in a midterm elec tion is the president’s approval rating. President Biden’s approval rating average is in the low 40s, pointing to serious losses for the Democrats.
Current thinking is that Democrat.upsseatsRepublican-heldcontrast,Republican.upsconsideredheldDemocratic-26seatsaretoss-orleaningByonlyninearetoss-orleaning
Pennsylvania: This state has quickly become a battle ground, ever since the Republican incumbent, Patrick Toomey, announced his retirement.
Here is a summary of the most vulnerable Senate and House seats, and governorships this November.
Arizona: The state is in the spotlight as Sen. Mark Kelly (D) hopes to win his first full term in the Senate. With
The WhatElections—MidtermtoWatch For
Senate:
Nevada: Of all the compet itive races with Democratic incumbents, Republicans are most bullish about Nevada. The GOP has been hammering Democrats for prolonging COVID restric tions that hurt Las Vegas’ tourism-based economy.
Currently the Senate is evenly split between the two parties. Therefore, a pick-up of only one seat for either party means they will control the Senate. Of the 35 seats up for reelection this year, 14 are held by Democrats. Republicans will be defending 21 seats. These seats are the ones to watch.
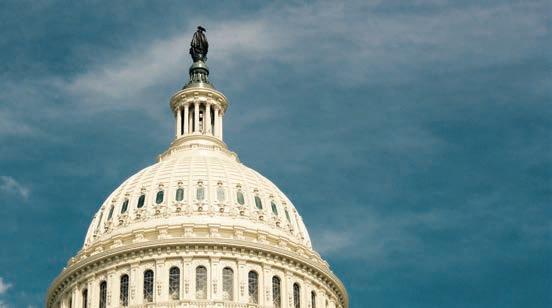
House:
Georgia: An especially competitive race is shaping up in Georgia, where incumbent Sen. Raphael Warnock (D) will face former NFL running back Herschel Walker. The Republican has high name recognition but is untested as a candidate and faces allegations of domestic abuse.
Republicans need a net gain of just five seats to retake the House majority. Current thinking is that 26 Democratic-held seats are considered toss-ups or leaning Republican. By contrast, only nine Republican-held seats are toss-ups or leaning Democrat.
Capital Eyes
69 the ANALYST Volume 29 Number 3
voters giving Democrats low marks on the economy and immigration—two defining issues for Arizonans— Kelly’s challenger is sure to be competitive.
Wisconsin: The most vulner able Republican this year is Ron Johnson, whose job approval rating is lower than Biden’s.
Additionally, in the past three decades, both parties have suffered major midterm losses in the House two years after capturing the White House. Democrats lost 54 House seats under Bill Clinton in 1994 and 63 seats under Barack Obama in 2010. Republicans lost 42 seats under Donald Trump in 2018.
Ukraine: The war in Ukraine is a wild-card issue. So far, Ukraine has not become a dominant political issue, in part because of support for Ukraine and advocacy of U.S. assistance by both parties.
The Issues:
In total, Republicans are targeting about 70 Democratic seats. They include seats in Arizona, Maine, Ohio, Iowa, and New Jersey.
Several issues remain at the forefront of voters’ minds this year, including:
Inflation and the economy: Inflation is a constant pres ence on the minds of voters when buying groceries, filling their gas tanks, or paying their home heating bills. Unless there is a considerable easing in the next few months, it will continue as one of the top issues of concern. The most recent polls show that nearly 7 in 10 Americans disapprove of the way President Biden has handled inflation. Fifty percent say they trust Republicans to handle the issue, compared with 31 percent who say they trust Democrats more.
70 the ANALYST Volume 29 Number 3 Capital Eyes continued
In 2020, Republicans flipped 15 Democratic-held seats, and they are hoping to replicate that success this year by focusing on inflation and pointing to the rise in crime across the United States as evidence that Democrats cannot handle law and order. House Democrats are arguing that they are trying to counter inflation by pushing for tax cuts, providing child-care options, lowering prescription drugs costs, and fixing the supply chain.

Crime: Crime is another hot issue as many major cities are suffering from rising homicide rates and increases in other types of crime.
Janet Kopenhaver is president of Eye on Washington and serves as the AWT Washington representative. She can be reached at (703) 528-6674 or janetk@eyeonwashington.com
There are 30 gubernatorial races this year. Democratic losses in Michigan, Pennsylvania, or Wisconsin would give Republicans full control of the government in those states. The three most competitive races are in Georgia, where Gov. Brian Kemp will be in a rematch with Democrat Stacey Abrams; Wisconsin, where Gov. Tony Evers (D) will have a tough battle for reelection; and Nevada, where Gov. Steve Sisolak (D) is concerned about possible erosion among Latino voters, long a prime constituency for their candidates.
Governors:
The border: The surge of undocumented immigrants along the U.S.-Mexico border continues to be a problem that the Biden administration has yet to bring under control.
Jerry Angelilli, Consultant
An Innovative Way to Attack Biofilm and Fouling
Biofilm, biofouling, and corrosion can be serious prob lems in water systems. In this article, we will examine a creative solution that worked when we faced this issue at an end-user that made plastic bottles.
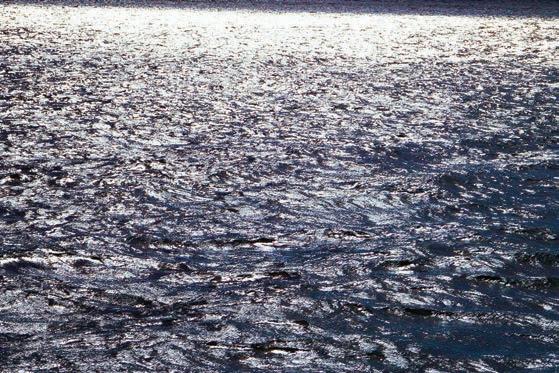
Background
Situation
As part of the problem audit team, I participated as a representative of our engineering department for the existing water treatment chemical supplier. After a complete survey of the equipment, we compiled data on existing corrosion rates and microbiological dip slides,
71 the ANALYST Volume 29 Number 3
Employing different approaches to the traditional methods using chlorine dioxide, I have addressed biofilm and organism growth in a variety of water systems. I had successfully applied this chemistry to a once-through river water cooling system to eliminate biological fouling in a cement production facility with a former employer. In this application, a separate building was erected to house the generator and precursor chemicals. This particular method employed sodium chlorite, sodium hypochlorite, and hydrochloric acid. The customer requested a turnkey operation, so the entire process was kept under lock and key. I alone attended and serviced the generator and changed chemical drums.
My approach was selected over the competitive proposals of applying a typical organic biocide or using chlorine. Both of these methods required that that the chemicals be completely neutralized before discharging the water back into the river. These methods required additional chemicals and testing to prove no residual remained. With the low level of chlorine dioxide of 0.5 parts per million (ppm) applied, no testable levels of chlorine were seen at the discharge point with no neutralization process needed. The result of the application of chlorine dioxide was completely successful in treating the cooling water and remediating all microbiological fouling of cooling water channels.
documenting the attempts to correct the situation with traditional chemical agents. This history included corrosion coupon results on carbon steel, a stainless-steel grade, copper, and an aluminum alloy to reflect various metallurgies in the system.
Tales From the Waterside
Biofilm and microbiological fouling were found in small-diameter channels of changeable molds in a large Eastern plastic bottle manufacturing facility. The molds are composed of various materials, but mostly propri etary grades of either stainless steel or aluminum alloys. To complicate matters, small fittings or other compo nents like valves can also have copper-bearing alloys.
The Problem
This problem caused increasing downtime and falling production efficiency by decreasing the service-run length of molds before they had to be changed for cleaning. A variety of microbiocide products were applied under the direction of a water treatment consulting firm with little to no effect on correcting the problem. These molds are supplied by a semi-closed chilled water recirculating system. The system water is chilled by heat exchangers, sent to the process equip ment, and then returned to tanks that are open to the atmosphere, which allows airborne contamination to enter the system.
Engineering Audit
As part of a team working with a large Southern univer sity hospital system, I assisted in developing a unique process that was tried and proven to reduce water usage. Air-conditioner condensate is relatively pure water and is usually sent to drain. A system was devised and installed to collect this water from three different chiller plants with a connected chilled water loop. The biggest issue was to prevent biological fouling without complex biocide applications. Our recommendation was to feed chlorine dioxide at each recovery tank and pump the free conden sate into the chilled water loop to overcome the water losses that were previously replaced with costly city water. By adjusting the treatment chemistry in the chilled water loop, we successfully kept corrosion minimized while saving the customer considerable operational
Within hours, we could observe dramatic changes in the clarity of the pond water. Disinfection was verified using serial dilution bottles prepared with specific agar for a variety of organisms, like total heterotrophic bacteria (aerobic) and sulfate-reducing bacteria (anaerobic.) After this simplified concept was validated, the team received approval for purchasing a trailer and generating equipment to control this application for use on a hydraulic fracturing site. This successful trial led to the development of a new subsidiary company; the purchase and erection of a manufacturing facility; the development of an application stan dard for the chemical residual necessary for these applications, and production of several state-of-the-art portable treatment and control trailers for use on hydraulic fracturing of oil and gas exploration sites in Arkansas, Oklahoma, Texas, Pennsylvania, and West Virginia.
72 the ANALYST Volume 29 Number 3 Tales From the Waterside continued
where a co-worker and I procured a rental trailer with a chlorine dioxide generator and had precursor chemical delivered to the site along with sections of hoses and a large pump to bring water into the generator trailer. There, the chemical could be applied and then returned by a discharge hose to the opposite side of the pond.
Problem-Solution Approach
After completing the audit and data compilation, I suggested a two-fold approach to the problem at the plastic bottle molding plant. The first step would be to disinfect the system and remove existing biofilm by applying chlorine dioxide in a premade solution product of 3,000 ppm strength to prove the concept. Once the concept was validated, we would move to the second step, which would be to propose a permanent chlorine dioxide generator to the plant management for maintaining a low, continuous residual in the
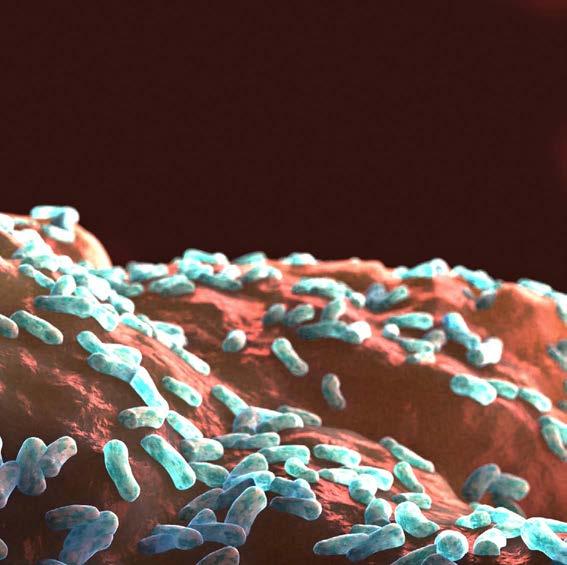
Additionally,costs.Iserved on a team to effectively use this technology to disin fect complete building water systems that were infected with Legionella bacteria. The first successful application was in a VA nursing home in the Midwest. After a total evacuation of patients and personnel, our team applied chlorine dioxide in a solution to the entire domestic water system to develop and maintain a 5 to 10 ppm residual for a period of 1 to 2 hours. Every tap in the building was tested to ensure a positive residual was held for the desired holding time. After the disinfection, the entire system was flushed with fresh water and every tap was retested to confirm that all chemical was gone. This similar procedure was applied in various other loca tions, including a large Gulf of Mexico coastal hospital whose water system was fouled by the storm surge after a Ashurricane.amember
continued on page 79
of a company task force, I also worked on applying chlorine dioxide in various oil field water system disinfection processes, which resulted in two patents for treatments in that area. This process was first applied to water impoundments in rural Arkansas,
Source: https://blog.ansi.org/2018/09/ansi-ashrae-standard-188-2018-legionnaires/
Monitor water parameters, like disinfectant residual and pH, on a regular basis. Measurement frequency should be based on performance of the water management program or Legionella performance indicators for control. Adjust frequency according to the stability of perfor mance indicator values. For example, the measurement frequency should be increased if there is a high degree of measurement variability.
Test Strips
WaysT.U.T.O.R.to Make Field Testing for Chlorine Compounds Simpler
i. monitoring method and schedule for temperature measurements in the hot water and cold water systems.
ii. monitoring method and schedule for measuring the chemical disinfectant residual or physical parameters in the hot water and cold water system.
Introduction
Colorimeter/Photometer/Spectrophotometer
Test strips (Figure 1) can measure free chlorine and total chlorine. These can be good for quick chlorine checks, but they are generally not sensitive enough to measure the lower chlorine levels found in cooling tower waters. Test strips can come in various ranges, and the ones we would use for cooling towers would have an upper limit of 10 parts per million (ppm) as chlorine (Cl 2).
iv. procedures and schedule for maintaining water treatment system disinfectants, and
Source: pointInowner’stheirnotofTestinging-Towers.pdfhttps://www.cdc.gov/legionella/downloads/Control-Toolkit-Coolforthebiocideresidualshouldbeanintegralpartanyriskmanagementprogram.Thistestingshouldbereservedforthewatertreatmentsupplierandperiodicvisitsbutshouldalsobepartofthesystemregularresponsibilities.thisarticle,wewilldiscussseveraltestingoptionsandouttheiradvantagesanddisadvantages.
The following methods are available for testing chlorine and its related compounds:
Test Strips
Titration
iii. procedures to address water supply interruptions or breaks in water supply piping.
ANSI-ASHRAE Standard 188 (2018):
Technical Updates, Tips, or Reviews
Color Matching
Regular testing for oxidizing biocides in water is more important than ever in the times of Legionella and diseases like COVID-19. Industrial water systems are frequently targeted as the source of illness, especially Legionella. It is the responsibility of professional water treaters to design, recommend, and implement programs that protect water systems and prevent outbreaks.
Testing Options
3. Water treatment. The legionellosis risk management plan documents shall include:
73 the ANALYST Volume 29 Number 3
v. water treatment products, the procedures for their application, and configuration that the products comply with applicable regulations.
Chris Golden, CWT, Taylor Technologies, Inc.
Oxidizing biocides have been widely used to maintain control against bacteria in water systems. Chlorine has been fed to municipal drinking water systems for years. In this article, we will focus on cooling tower waters. Chlorine and bromine products are a part of every open cooling water system’s treatment program, especially since the ANSI/ASHRAE Standard 188-2018 was published and the CDC issued the Legionella Control Toolkit. Details about each are noted below:
From the CDC Cooling Towers Toolkit:
The midget and slide comparators use a liquid-to-liquid match where the water sample created matches against a liquid standard. This is preferable to the liquid-toprint, as in the color cards and color disks. Precision is increased with this method, but the comparators are somewhat more fragile and susceptible to freezing.
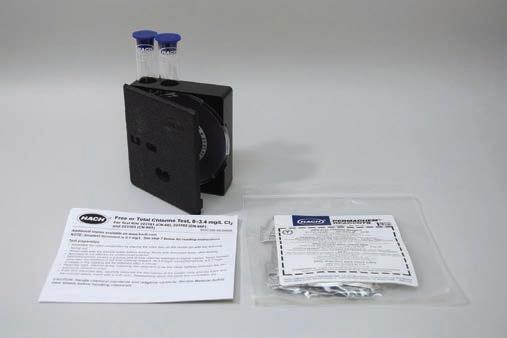
Figure 4: Midget (top) and slide (bottom) color standards.
Source: LaMotte Co.
Color Cards
Figure 3: Color disk.
Figure 1: Example of test strips.
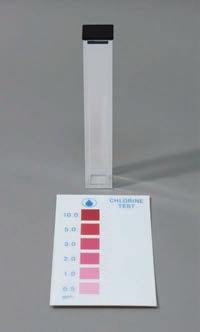
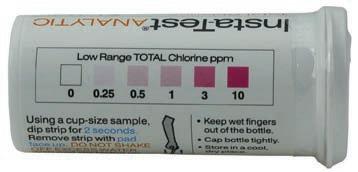
Source: Hach Co.
Liquid Color Standards (Midgets and Slides)
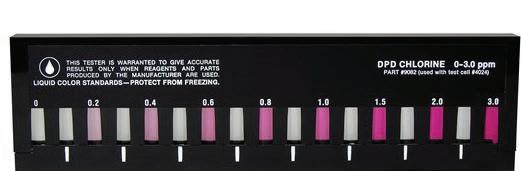
on the wheel. This method is better than the color card because it allows for any color or turbidity in the sample water to be accounted for in the color measurement. This method also allows for better sensitivity in reporting chlorine levels.
Color matching involves adding an indicator to a prop erly measured sample and allowing a color to develop. This color is usually in proportion to the amount of analyte in the water. The color is manually measured against color standards. For chlorine, the indicator is usually DPD* (N,N diethyl-p-phenylene diamine), and a pink color develops in proportion to the chlorine level in the sample. Color-matching methods are shown in Figures 2 through 5. *Note: OTO (orthotolidine) is also used as an indicator for chlorine testing, but it only tests total chlorine.
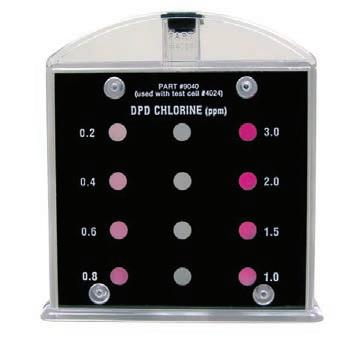
Color Matching
Color Disks
Color disks (Figure 3) are printed with colors on a circular disk. The procedure is similar to the color card being a liquid-toprint color match, except that a blank with no reagent is used for the color comparison against the prepared sample. The tester then looks across the sample from the side and matches the color in the water to the colors
Color cards (Figure 2) are printed with colors corre sponding to the various levels of chlorine, both free and total. The proper volume of sample is added to the sample cell, and then the appropriate volume of indicator is added to the sample cell. The tester then looks down through the sample from the top and matches the color in the water to the colors on the printed card. The color intensity of pink increases with the higher levels. Again, as with test strips, they generally do not have the sensi tivity we look for in cooling towers.
74 the ANALYST Volume 29 Number 3 T.U.T.O.R. continued
Figure 2: Color card printed for chlorine test
These electronic devices are excellent for determining free and combined chlorine in the typical ranges for cooling tower waters. They are accurate and precise, and they increase in accuracy and precision as you move up the scale in cost. Every professional water treater should have a colorimeter/photometer. The reason is for the
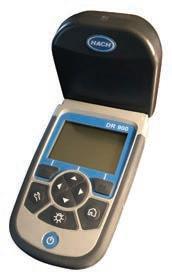

Asking a water tech, especially one who may be color-impaired, to do this testing may not be the best choice for determining chlorine levels, particularly for free chlorine at the lower levels prescribed.
Titration
Ampoules
Figure 7: A titration kit used for water testing.
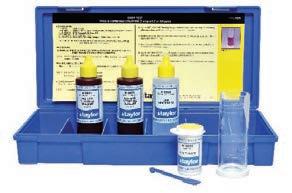
In the author’s opinion, for manually measuring chlo rine, the slides and midgets are preferred. They provide good precision, as they are read in 0.2 parts per million (ppm) increments at the levels that typically concern us for cooling towers. (The ampoules using the photometer will be discussed in the next section.)
Source: CHEMetrics.
The ampoules (Figure 5) have the reagent predis pensed in the test ampoule. This saves the user from measuring reagent and sample size. This method uses a liquid-to-liquid color match, but it could also use a photometer, improving the accuracy over manually read colors. Precision is increased with this method, but the ampoules and comparators are somewhat fragile.
75 the ANALYST Volume 29 Number 3 T.U.T.O.R. continued
Colorimeter/Photometer/Spectrophotometer
Sources: Taylor Technologies (left) and Hach Co. (right)
The industry seems to not know enough about the chlorine titration method FAS DPD. Asking a water tech, especially one who may be color-impaired, to do this test method may be the best choice for determining chlorine levels, partic ularly for free chlorine at the lower levels prescribed. It is generally inexpensive, and, therefore, excellent for customer contract accounts where profits need to be protected. Figure 7 shows an example of a titration kit.
This is the method that the author would like to empha size for testing chlorine compounds, including bromine. It has the following qualities, which are beneficial for field testers and customers alike:
Figure 6: Examples of colorimeters/fluorometers.
But are these the right devices if you are to arm your customers with daily chlorine test kits to meet risk management objectives?
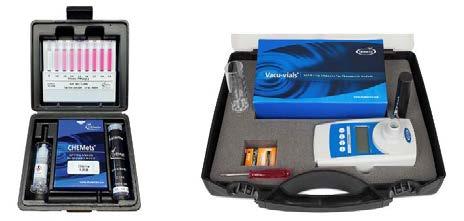
other critical tests they do, like metals, scale inhibitors, and corrosion inhibitors. The drawbacks to these devices can be initial cost and maintenance They are electronic devices and need to be handled with more care than our other work tools. Be sure to choose a colorimeter with a robust warranty period. Figure 6 shows two examples of a colorimeter/fluorometer.
Figure 5: Ampoules.
These color-matching methods, however, require human eyes to determine the color and the corresponding chlorine concentration. DPD is the preferred option for this method and creates a pink shade of color. This color may be difficult to distinguish at the low levels in cooling water. Want to know your color IQ? Click (https://www. xrite.com/hue-test) to take a quick test to determine your color vision acuity.
Low cost
Midgets, slides, and ampoules
Takes human error out of interpreting colors
Easy to use
Higher upper limit
Improved sensitivity with more Improvedstandardsprecision comparing a liquid to a liquid
RelativelyMaintenancefragile
print)CardsColor-Matching(liquid-to- Ease of use Limited sensitivity Cost Human Comparingerrora liquid to a printed color is not optimum Color (liquid-to-print)Wheels Ease of use Limited sensitivity Cost Human Comparingerrora liquid to a printed color is not optimum
FAS-DPD Cost
Reliable results
Reagent shelf life around 12 months
Limited sensitivity Cost Human error
trophotometertometers/Colorimeters/PhoSpec
Ease of use
Test Strips Ease of use
Chris Golden has been involved in the water treatment and chemical industries since 1989. For more than 16 years, he worked as a field consultant for industrial facilities’ water systems. These facilities included steel mills, paper mills, power plants, manufac turing, and food processing. Mr. Golden joined Taylor Technologies in 2007 and currently serves as the director of sales. In 2007, he also became involved with the Association of Water Technologies and went on to earn his Certified Water Technologist (CWT) in 2007. Mr. Golden holds a degree in chemical engineering from Lehigh University. He can be contacted at cgolden@taylortechnologies.com
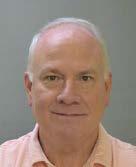
This paper was presented at the 2021 AWT Annual Convention & Exposition, which was conducted September 22–25, 2021, in Providence, Rhode Island.
Relatively fragile Cost Human error
Improved repeatability over color-match Less sensitivity than photometercolorimeter/methods
Closing Thought
Accurate
76 the ANALYST Volume 29 Number 3 T.U.T.O.R. continued
Table A: Overview of Chlorine Testing Choices Chlorine Testing Options Advantages Disadvantages
For those who are interested in learning more, here is a link to a video of this method: 0.2isTheThecom/watch?v=4ugRC3bDsaI&t=184shttps://www.youtube..colorchangeattheendpointiseffortlesstodiscern.dropequivalencyfora25-milliliter(mL)sample0.2ppmasCl2,soitcoversagoodportionoftheppmto2.0ppmasCl2rangeweshouldwant.Theprocedureiseasytouseandrepeatablewhilebeingrelativelylowcost.Anaddedbenefitisthismethodwillnot“bleachout”likeotherDPDmethodswhenchlorineisabove10ppm—thismethodcanmeasureupto20ppmasCl2andcantestbromineaswell.
High upper limit
Best sensitivity and precision Cost
The FAS DPD method fits both the field representatives’ and customers’ test ranges and abilities. Fast, econom ical, and easy to use, it is the test method that could be at every cooling water application.
Finally, with chlorine product pricing being high this year (as of 2022), you want to not only protect your low end of the spec range but also the high end. Overfeeding, especially in contract accounts, could prove to be very costly. Maintaining a tighter control on chlo rine and bromine levels will improve your bottom-line profits. Asking customers to participate in testing and control is another good idea. Table A provides an over view of chlorine testing options for cooling tower water.
Compiled by James McDonald, PE, CWT, Chem-Aqua, Inc.
Question of the Week
What Dangers Are Faced When Treating Water?
Dennis: I had an account about 35 years ago, where a truck driver was killed delivering caustic to a bulk storage tank. The tank vent had corroded closed and allowed the tank to pressurize during delivery (or at least, so it appeared). The driver was within the tank containment when the opposite end blew off, projecting the tank onto the driver. Be careful out there!
What’s (Water) on Your Mind?
Matthew: I’ve seen an 8-inch hose explode. It shot right near me and several union plumbers. It sounded like a howitzer going off. This could have been tragic. We’re
Editor’s note: This is a new column in the Analyst that contains discussions from the Industrial Water Treatment interest group on LinkedIn about different subjects rele vant to water treatment. Each column will contain excerpts from “Questions of the Week” posed by James McDonald on LinkedIn.
77 the ANALYST Volume 29 Number 3
Robert: Driving. This is the most dangerous thing you will do in this career, and there is no way to avoid it, unfortunately.
lockout/tagout nor proper communication had been conducted. Lessons were learned quickly very early in my career.
James: When I was brand new in industrial water treatment and being trained on boiler inspection, my manager and I were just about to enter the mud drum of a water tube boiler when steam started coming out of the manhole. My manager and the plant manager looked at each other a little white in the face. An oper ator had blowdown one of the nearby boilers, and steam had backed up into the one we were literally just about to Neitherenter.
Peter: Some real cases: 1. Operators working around got legionellosis and died; 2. A technician fell into a waste water anaerobic tank and suffocated; 3. A boiler operator got severely burned by leaked high-pressure steam.
To illustrate the importance of safety awareness, what are examples of “100 Ways to Die” in industrial water treat ment? What are the dangers we may face every day that pose a risk to life?
talking a 200-pound hose traveling hundreds of miles per hour. I hugged my wife and kids later that afternoon. The cause was one of two things: Either a pocket of air that compressed too fast or a bad hydraulic crimp on the hose.
Daniel: I lost a co-worker several years ago who went into a new vessel to check a header prior to loading media while he was there to commission a UPW system. The vessel was only about 5 feet from the manway to the header. It was full of argon due to a purge line connected to a system a contractor was working on downstream. Had he done a proper confined space entry, he would still be with us.
Group Discussion
Question of the Week: What do you LOVE about your job?
3. Positive efforts to save natural resources and maintaining the integrity of critical equipment.
Nellie: New technology, new solutions, transfer of knowledge … I just love water, the impact it has on industries, environment, and society, and most of all, our dependence on water, the bloodline for survival.
Muhammad: Here’s my list:
5. Searching of new chemistries.
Chris: What’s not to love?
7. Abstract and case studies writing.
Last but not least: Whenever our company is having any issue, we have brainstorming discussions with the utility and plant operation team.
Angela: Everything!
Craig: Solving problems, working in the lab. Precision chemistry work. Bucket chemistry.
Ghaith: No day is similar to the other one.
Lisa: Every day is different.
Steven: Taking business off competitors (one in particular).
1. Continuous learning aptitude.
Ali: Troubleshooting and customer service.
2. Knowledge about multiple industries.
Patrick: I love everything about it. Dealing with different systems, working with a team to help problem solve, and not being behind a desk all day, every day. My absolute favorite thing is seeing behind the scenes what others probably will never be able to see.”
Allen: “Making a difference and bringing value to my customers. In addition to learning new technologies.”
Adam: The people and places. I’ve met some awesome friends through this industry. And I get to travel around
Tammy: The people and that it’s different every day.
Miguel: Amazing new challenges with each passing day, allowing for a constant growth of knowledge.
Justin: Building friendships that carry on outside of work. Seeing my customers being successful.
78 the ANALYST Volume 29 Number 3 What's (Water) on Your Mind continued
Phil: I’d say the same: the people I work with, the customers, and always learning something new!
Francis: I agree. Problem-solving is at the heart of what we do every day! Without such challenges, life would be boring!
4. Inspection of critical equipment, troubleshooting/ report writing.
Damilola: Meeting people all the time, and of course, solving problems for customers.
Gian: I love that there’s always something new to learn and new people to connect with, all for the benefit of society and the environment.
Des: Probably the people in the water business.
Michael: “Making customers happy, because they are the true purpose of all our collective actions.”
Muhammad: Continuously thinking about solutions.
6. Training engineers.
Brian: Making friends and constantly learning new things.
John: The really great people I have met and worked with!
Mark: Everything!!!!!!!!! ��
Joshua: I love seeing all the different processes and how
Steven: Problem-solving. I truly enjoy being presented with a water treatment problem and finding a solution. Sometimes, the problem isn’t water related, but I can still assist the customer in finding the right solution. Being more than a chemical person and more of a solution provider is what I love about my job.
my territory and feel involved with many different communities.
Group Discussion
79 the ANALYST Volume 29 Number 3 What's (Water) on Your Mind continued Tales from the Waterside continued from page 72
Safety Concern Issue
Paul: When chemical treatment regarding biolog ical and corrosion rate is ok, a maximum of 10% is acceptable. Everything, such as corrosion rate, temperatures, level of chemical treatment, and biological counts, should be monitored.
Question of the Week
Tony: I would say no more than 5 to 10% to cover routine maintenance, strainer cleaning, flushing and replacement of filters, and blowdown of Spirovents. Anything over 10% should really be investigated as a leak. Also, having a water meter on the pres surization unit will help monitor whether the loss is consistent (potential leak) or can be attributed to once off maintenance events.
Jerry Angelilli retired as engineering manager at Chem-Aqua Inc. in 2020. He began his career in water treatment with Betz Entec in 1978 as a sales representa tive. After serving as a staff engineer with that company, Mr. Angelilli developed technical knowledge and skills that led him to other positions in both sales and technical roles with other industry-related companies. He began his last affiliation with Chem-Aqua in 2007 as a senior engineer and was promoted to manager of oxidative technology in 2010, and eventually to engineering manager until his retirement. Mr. Angelilli has served on the AWT Technical Committee since 2008 and currently chairs the Boiler Subcommittee.
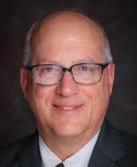
Normally, chlorine dioxide generators require at least a solution of sodium chlorite or (chlorate form) and some method of acidifying the component using a strong inor ganic acid, like hydrochloric or sulfuric. Some methods actually use chlorine gas or sodium hypochlorite (bleach) in the process. Since this facility has a strong corpo rate safety department, they ruled out any potentially hazardous materials like these.
The plant management personnel agreed to our approach, and within a few months, we documented success by improved corrosion rates and minimized microbiological issues. These treatment steps resulted in improved plant efficiency and fewer mold changes.
Conclusion
How do you determine what an acceptable baseline annual water loss is for a closed loop?”
From my research and experience with a variety of chlo rine dioxide generation methods, I had already placed a type of generator that used a mild (less than 6% as sodium chlorite) product described as stabilized chlo rine dioxide. The solution is made of chlorine dioxide that is pH-adjusted with caustic. In this form, it can be activated using any acidic material. In this case, we suggested citric acid, which is used safely a food additive.
Vinod: It should not be more than 5%—maximum 7%. If it is more, then check your system for a leak. Truly closed cooling systems should have maximum of 1% loss per month.”
system to prevent accumulation of future biofilm and bacterial fouling.
Group Discussion
James McDonald, PE, CWT, is a director of technology & marketing with Chem-Aqua. He holds a master of engineering degree in chemical engineering and is a Ray Baum Memorial Water Technologist of the Year award winner (2013). Mr. McDonald also chairs AWT’s Technical Committee. He can be reached at James.McDonald@chemaqua.com

“stuff” is made. I love the smell of cereal, Combos, and soda. Some I could do without.
Our Solution
Acknowledge Your Emotions
You’ve got a direct report struggling with time manage ment. As a manager, it can be challenging to know how to address the issue. On the one hand, you need them to get things done, and your natural tendency might be to respond in obvious annoyance at the lack of followthrough or even to consider writing them up. On the other hand, you want to develop your team members. You may have truly brilliant individuals whom you know have the potential to be exceptional contributors if they could only figure out how to use their time effectively.
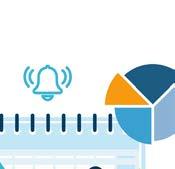
This process helps you to release pent up negative emotions before you give feedback so that you’re not overly harsh with your direct report and do more harm than good.
If you’re a manager unsure of how to help, here are some practical steps you can take to improve the situation.
Process what you’re feeling on your own or with a trusted person, and honestly assess why you’re so upset. Is it a lack of control? Fear? Embarrassment? Stress?
Assess Your Part
If you’ve been managing this person for a long time, you’ve likely experienced a broad range of emotions, ranging from mild irritation to outright infuriation. Your feelings will vary depending on how severe the issues have been, the stakes involved, your personality, your expectations, and your stress levels.
Your direct report may very well have poor time manage ment. But you might want to consider whether you also have poor time-management skills and in which ways, if any, you’re contributing to the problem.
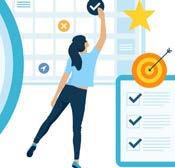
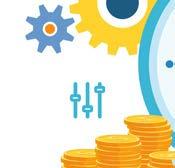

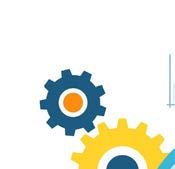
Before you give feedback to your employee, acknowl edge your emotions. Write out anything you might be thinking or feeling in a free-flowing manner. Do not share your raw thoughts (via email or otherwise) with your colleague. This exercise is so you can become aware of your own internal state.
How to Help an Employee Who Struggles With Time Management
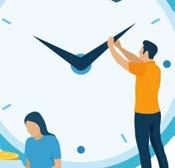
The telltale signs are there: Tasks done at the last minute, completed late, or even forgotten. Tardiness at meetings. No response to emails or replies at weird times, like 2 am. And more explanation of why items aren’t done than action to finish them.
80 the ANALYST Volume 29 Number 3 Business Notes
Pinpoint the Stress


Earlier this year, I had a situation I found very stressful with an outside contractor. There was a large project that I needed them to complete, and they were very delayed. One day as I was thinking about it, I realized that within the larger project, there were just a couple of distinct
If you send over assignments last minute, don’t give clear direction, refuse to set priorities, have no follow-up system or forget to give feedback, then your actions could be playing a role in the situation. If you also expect your employees to be constantly available through email, chat, or other channels, which prevents them from setting boundaries to complete focused work, you’re also partially at fault for the struggles they face.
Elizabeth Grace Saunders Real Life E-Time Coaching & Speaking
By identifying these issues in advance of the feedback conversation, you can go in acknowledging where you could also have done better.
report likely knows they have really bad time management and may feel worse about it than you do. Laying into them is counterproductive; increased negative emotions about their work usually causes more delay, not less. Remember that you’re on the same team. Instead of tearing them down, build them up each step of the way.
Communicate What You Need
Appreciate Progress
Structuring the situation so that they can get and keep momentum can make a world of difference.
Take the time to think through exactly what’s causing issues for you with your direct report’s lack of time management: Do you not have what you need for important update meetings or presentations? Are you experiencing stress from them asking you to review things last minute? Are their actions costing you time or money? Do you feel anxious when there isn’t good communication on status? Once you know this, it will help focus your feedback discussions.
To get your direct report started, consider taking these actions with them:
Work with them to prioritize the work. Brainstorm the direction to take. Talk through the smaller parts. Set up intermediate milestones. Do some of the work with them in a meeting. Team them up with colleagues. Request daily updates on what they planned to do and what they’ve accomplished.
items that mattered most. Once those were done, my stress would dramatically decrease, and the other parts could take more time.
In some situations, simply giving feedback about what you need or want can improve the situation. But in others, you’ll need to do more to help things move forward.
Sometimes you’re too close to a situation. No matter how hard you try, you can’t provide objective, calm feedback. Or your direct report may not be able to be honest with you about what’s truly going on, such as wasting hours each day scrolling on their phone or a situation at home that may be distracting them.
By clarifying my most important needs, I felt less stressed and could communicate what I needed to get back most urgently, even if the whole project wasn’t done.
Elizabeth Grace Saunders is a time management coach and the founder of Real Life E Time Coaching & Speaking. 2022 Harvard Business School Publishing Corp.
In these situations, it can be helpful to connect your employee with outside resources, such as time-management training, an internal coach, or an external coach who can help them to develop these skills. Someone with experience in helping people overcome these challenges and who is more emotionally distant from the situation can often be more effective than someone with a history of frustration.
Youroutcomes.direct
Get Outside Support
Help at the Start
When you start noticing movement in the right direc tion, show appreciation for each step forward. You may feel concerned that giving positive feedback too quickly when they haven’t done everything yet will cause them to slack off. But the opposite is usually true. Positive feedback helps to build their confidence, positivity, and motivation and can propel them toward better and better
As a manager, you can’t force anyone to improve their time management. But your communication and actions can make a huge difference in your direct report’s ability to overcome their struggles and increase their produc tivity.
81 the ANALYST Volume 29 Number 3 Business Notes continued
Although you may feel tempted to unload all of your frustration on your direct report about the stress they’ve caused you and the issues they’ve had, a harsh approach will typically backfire. They’ll be so overwhelmed by your anger and shut down or become defensive and stonewall. Take deep breaths, and try to remember that they likely mean well but simply struggle in this area.
Once you know exactly what’s bothering you, calmly communicate exactly what you need, when you need it, and why you need it. You can also ask them what they need from you to help them be successful.
82 the ANALYST Volume 29 Number 3 Advertising Index 53 A MSA, Inc. 49 AquaPhoenix Scientific 59 Bio-Source, Inc. 19 Brenntag North America 82 CHEMetrics 13 EMEC 11 EMSL Analytical Inc. 2 Environmental Safety Technologies 31 IDEXX 25 Lutz-Jesco America Corp. 42 M yron L Company 35 Process Engineered Water Equipment 29 Pulsafeeder, Inc. 36 P yxis Lab, Inc. 33 Q ualiChem, Inc. 7 Q uantrol, Inc. 37 Radical Polymers 23 Sanipur US LLC 21 Scranton Associates Inc. 84 Special Pathogens Laboratory 17 USABlueBook 83 Walchem, IWAKI America Inc. WATER TESTING SHOULD BE SIMPLE That’s why our self-filling ampoules are PREMIXED, PREMEASURED and PRECISE We provide test kits for Low Range Dissolved Oxygen, Ammonia, Chlorine, DEHA, Filming Amines, Hardness, Hydrazine, Iron, Molybdate, Ozone, PAA, Phenol, Phosphate, Sulfide and more. +1.540.788.9026 | www.chemetrics.com
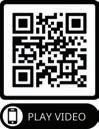

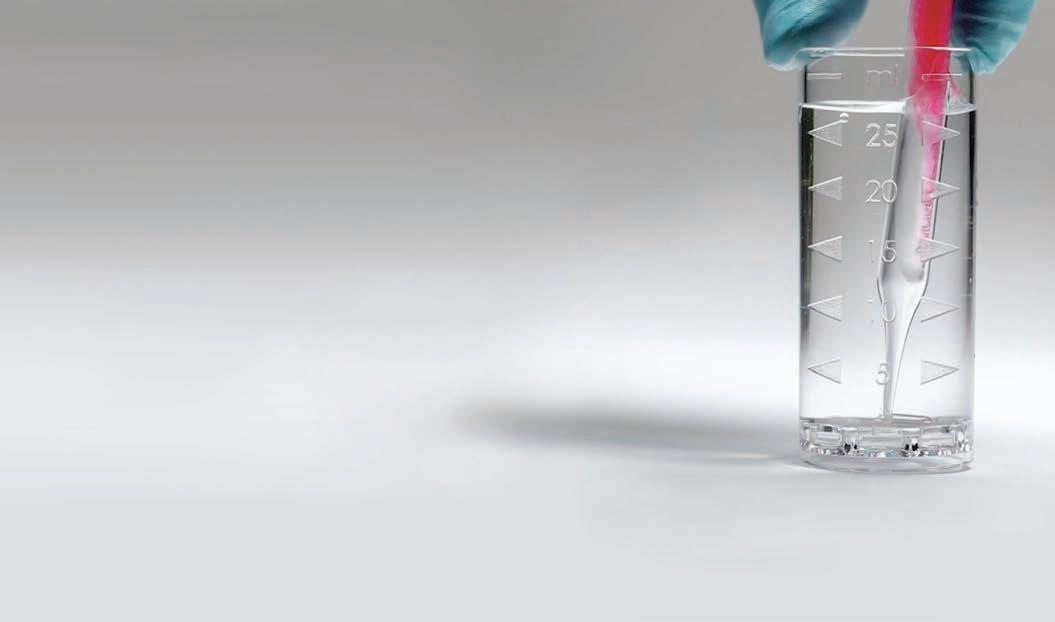
W600...
INTRODUCING

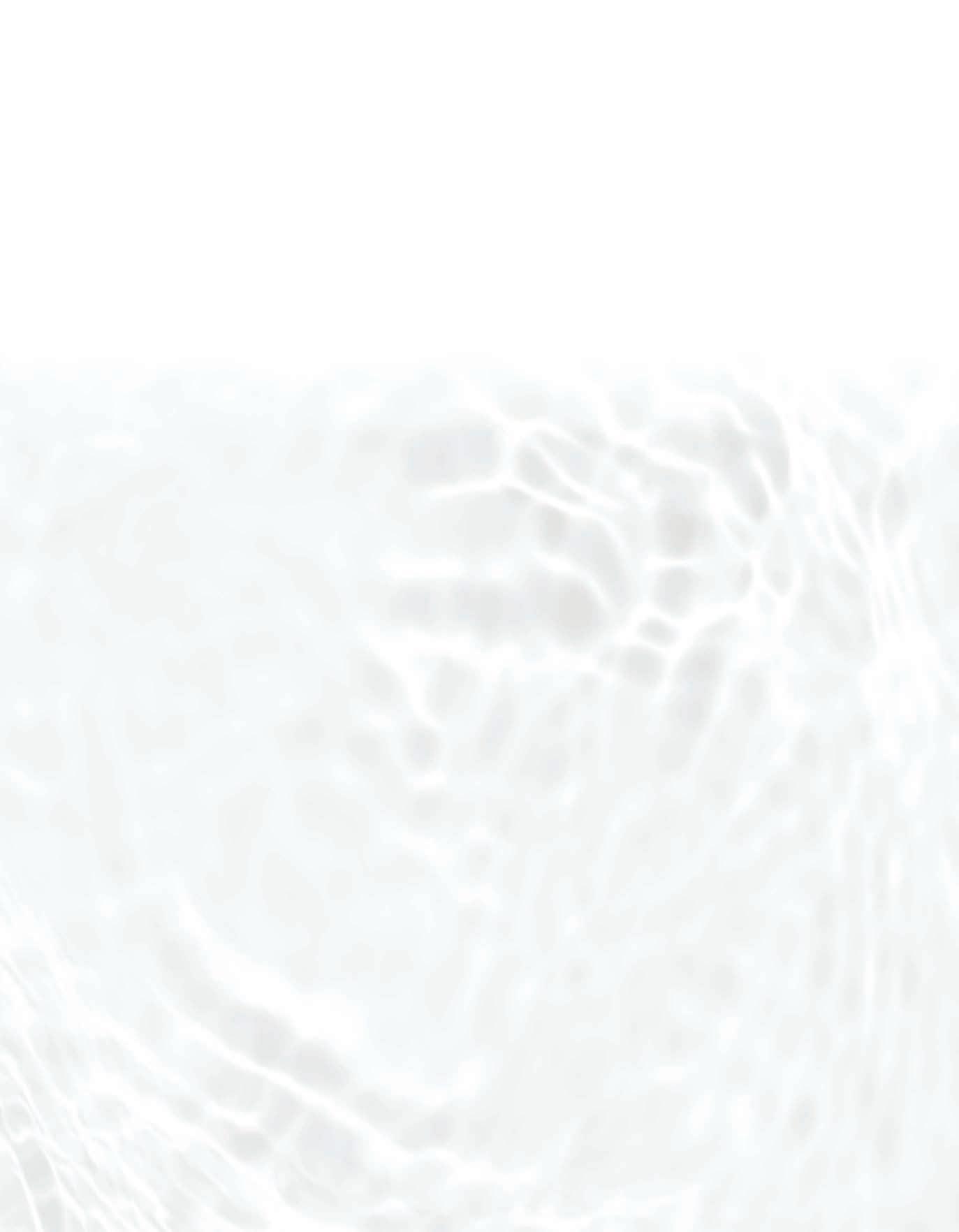
The only better
LEARN MORE! WALCHEM.COM Visit us at AWT BOOTH 252

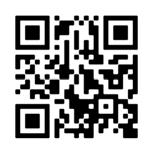
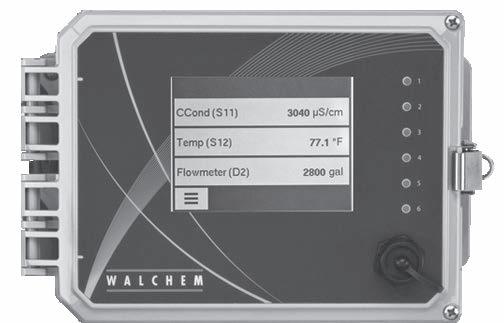
Get the
tools and

Special Pathogens Laboratory gives you the Legionella expertise required to protect your clients’ water systems through total Legionella control—testing, water management, education, and certification training to become a professional Legionella Water Safety and Management Specialist. Legionella resources, support need from
you
laboratory services to ASSE certification in one place: • Legionella and waterborne pathogens testing • Outbreak response • Legionella consulting services • LegiDoc water management plans • ASSE 12080 certification training • Guidebook: Puzzled by Legionella: A Guide to Understanding Detection, Prevention, and Water Management AWT Members Special O er $200 discount on the next ASSE 12080 certification training. Use discount code: AWT-Discount 20% discount Puzzled by Legionella guidebook. Use discount code: LearnAWT-Discountmore specialpathogenslab.com/asse-12080-certification
END THE LEGIONELLA info@specialpathogenslab.comSpecialPathogensLab.com | 877-775-7284 THE LEGIONELLA EXPERTS ®
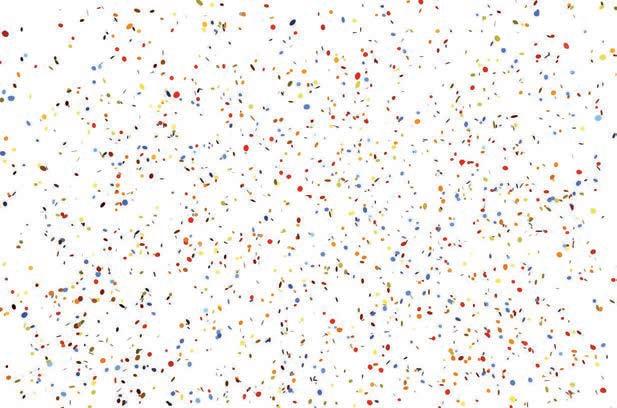
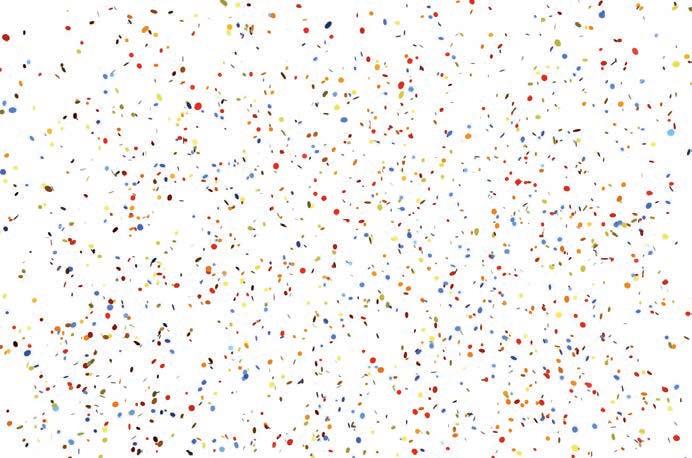