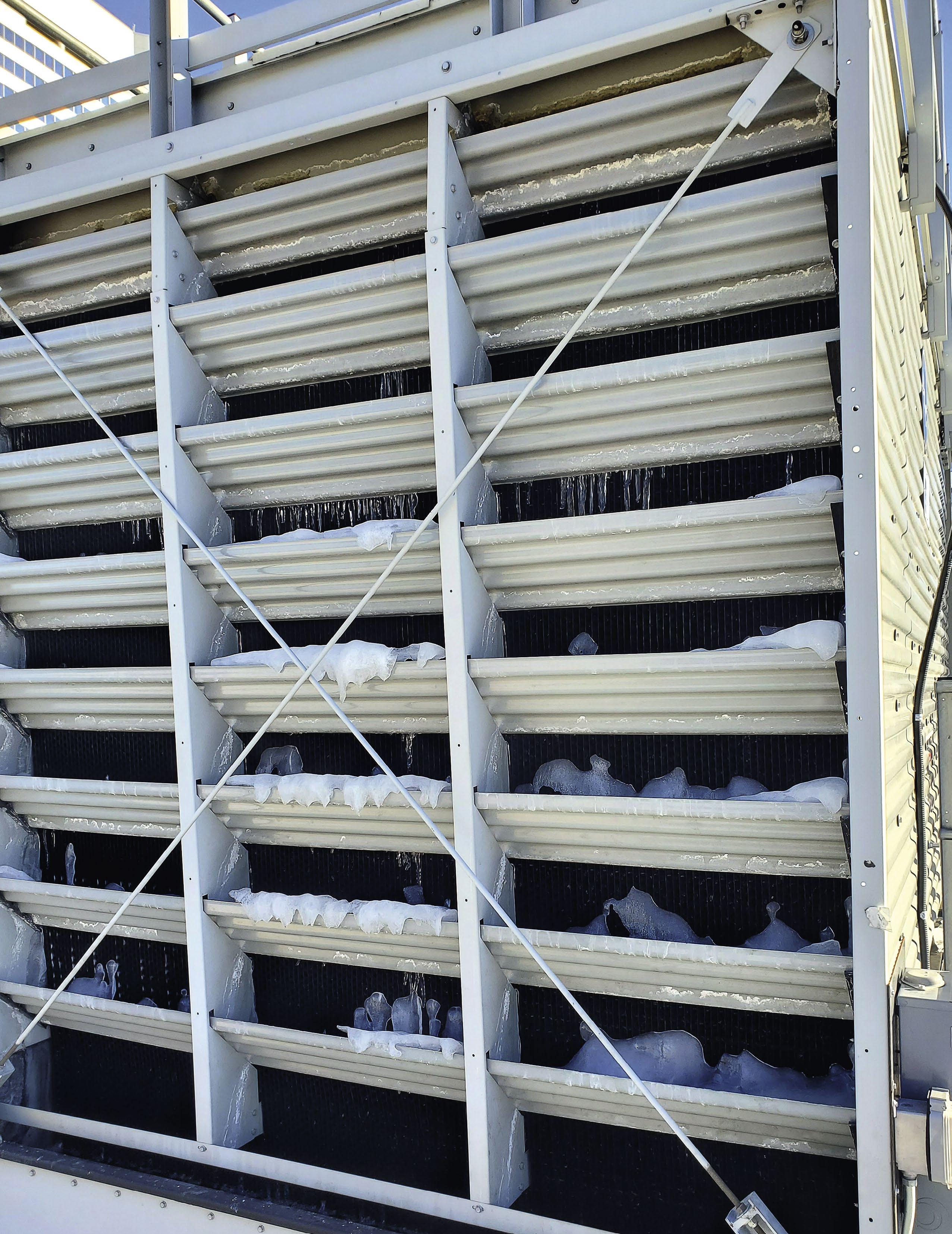
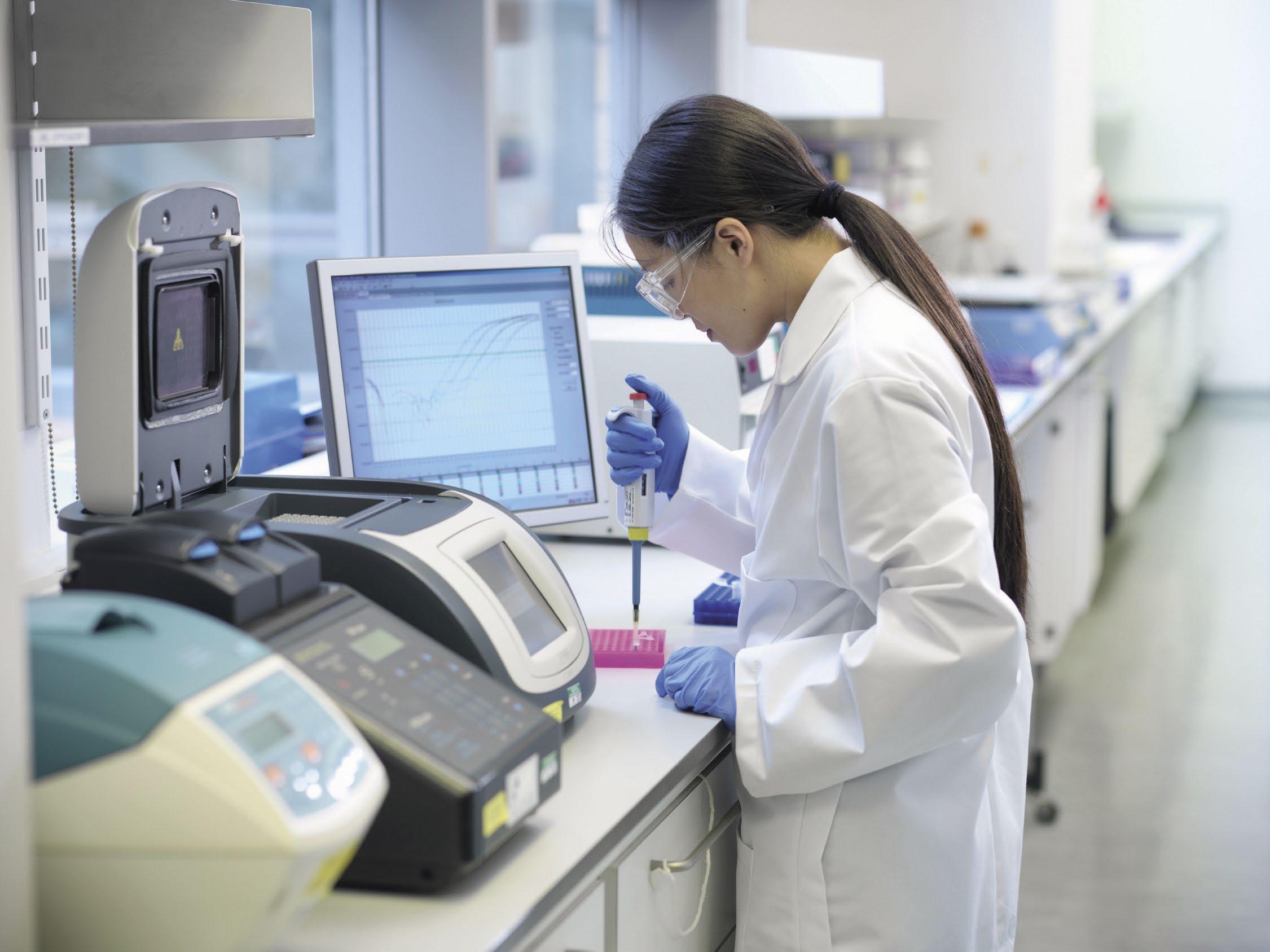
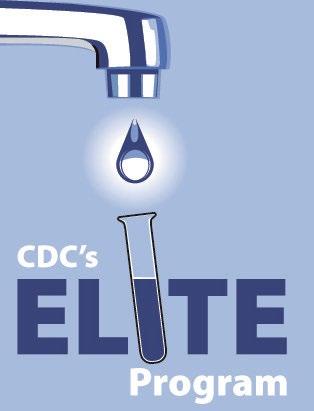
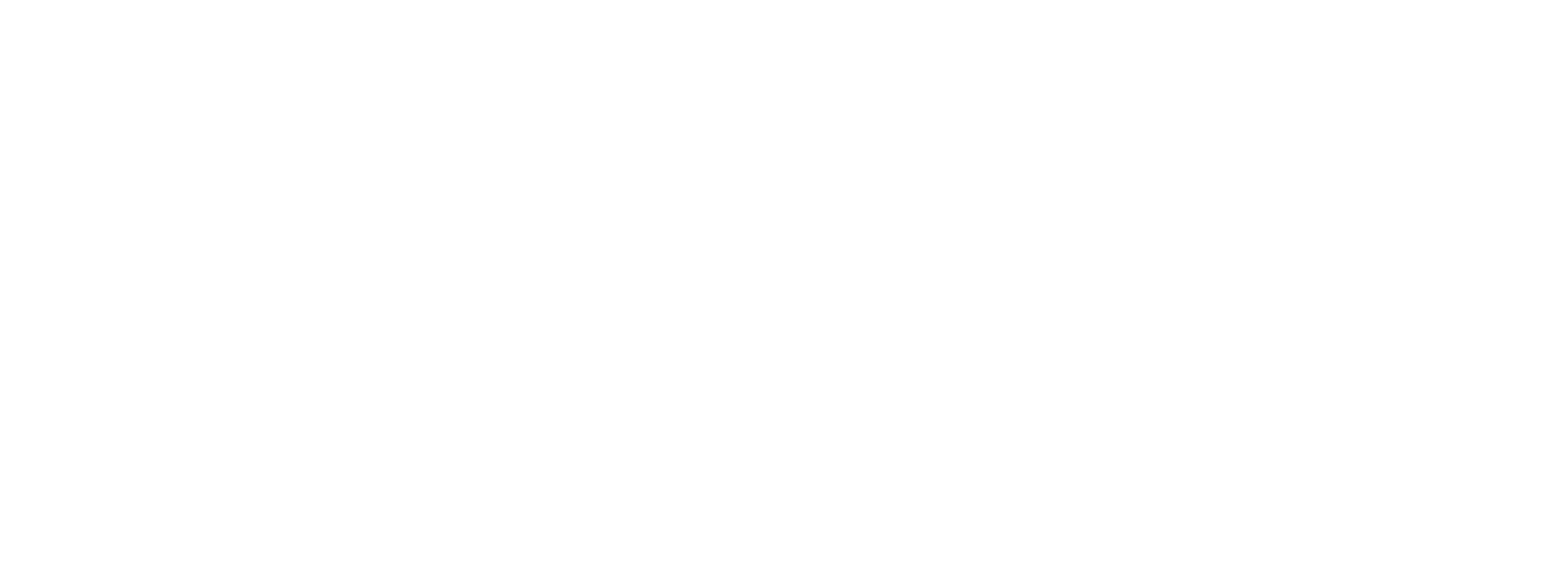
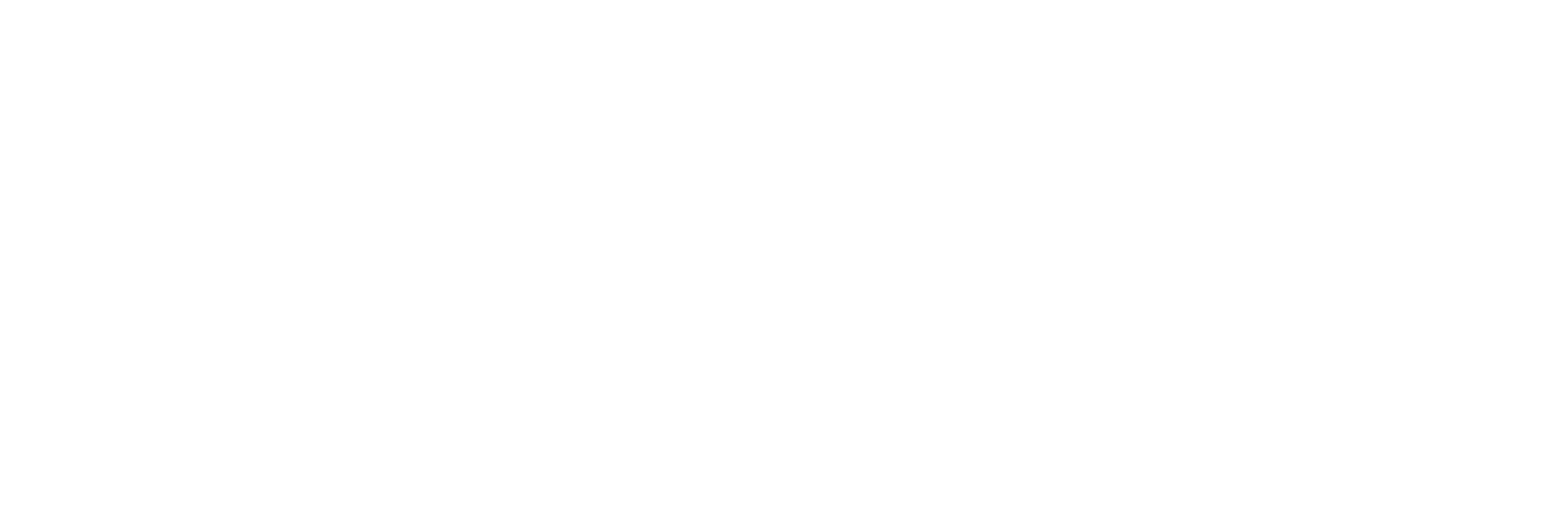
This article presents a new guidance document issued by the Cooling Water Subcommittee. Subcommittee members involved with writing the document are Derrick Vandenberg, Vance D. Fiegel, Robert Downey, and Thomas Mercer. The aim of this work by the Cooling Water Subcommittee is to offer SOPs for cleaning and disinfecting cooling towers.
Catherine Allen, Tintometer Inc.
Microbes, as with all lifeforms, have optimal conditions in which they thrive. Unfortunately, for water treatment specialists, these conditions are just what we find in open and closed water recirculating systems. Microbes are especially abundant in open recirculating systems due to the concentration of nutrients through the cycling of dissolved solids by evaporation as well as suspended solids being blown in. This article will investigate the methods in which a large microbiological population in cooling water systems is undesirable and why regular monitoring can minimize the detrimental effects on the system.
Swati Sharma, Ph.D., Water Engineering Inc.
An important method for improving a facility’s energy efficiency is to increase the condensate return to the boiler. Depending on the system, magnetite (also known as black iron oxide) can potentially contribute to the reduction of condensate return into the boiler feedwater system. In the absence of a condensate return, the steam system must compensate for the loss with makeup water, thereby increasing operational costs. Most of the systems suffer from black iron oxide contamination, creating thick sludge deposits. These deposits resulting from corrosion, along with water hardness scales and other unwanted contaminants, can lead to system failure. A design using magnetic dirt filtration technology was studied for the removal of magnetite in the condensate return. The study showed that the filtration technology removed more than 80% of the magnetite from the system, resulting in low iron levels.
Robert J. Ferguson, French Creek Software, Inc., and John F. Zibrida, Zibex, Inc.
Laboratory testing of water treatment programs for scale and corrosion control are run and used for several purposes. Testing results should correlate well to field results under the same or similar conditions. This article discusses parameter selection and test experimental design. The goal is to avoid laboratory simulations that predict stellar results in a beaker but result in abject failure when applied in actual end user water systems.
1300 Piccard Drive, Suite LL 14
Rockville, MD 20850
(301) 740-1421 • (301) 990-9771 (fax) www.awt.org
President
Stephen C. Hallier, CWT
President-Elect
Noah Baskin
Secretary
John D. Caloritis, CWT
Treasurer
Kyle Rossi, CWT
Immediate Past President Fred Shurtz
Craig Bodenmiller, CWT
Michael Bourgeois, CWT
Tammy Faber, MBA Michelle Lunn
Jack Altschuler
John Baum, CWT
R. Trace Blackmore, CWT, LEED AP
Michael Bourgeois, CWT
D.C. “Chuck” Brandvold, CWT
Thomas Brandvold, CWT
Brent W. Chettle, CWT
Dennis Clayton
Bernadette Combs, CWT, LEED AP
Matt Copthorne, CWT
James R. Datesh
John E. Davies, CWT
Jay Farmerie, CWT
Gary Glenna
Charles D. Hamrick Jr., CWT
Joseph M. Hannigan Jr., CWT
Staff
Executive Director
Denise Jackson
Deputy Executive Director
Sara L. Wood, MBA, CAE
Matt Jensen, CWT Mark R. Juhl
Brian Jutzi, CWT
Bruce T. Ketrick Jr., CWT
Bruce T. Ketrick Sr., CWT
Ron Knestaut
Robert D. Lee, CWT
Mark T. Lewis, CWT
Steven MacCarthy, CWT
Anthony J. McNamara, CWT James Mulloy
Alfred Nickels
Scott W. Olson, CWT
William E. Pearson II, CWT
William C. Smith
Marc Vermeulen, CWT
David Wagenfuhr
Casey Walton, B.Ch.E, CWT Larry A. Webb
Senior Member Services Manager
Angela Pike
Vice President, Meetings
Tina Schneider
Meetings Specialist
Caroline Bentley
Tim Foley
Exhibits and Sponsorships Manager
Brandon Lawrence
Senior Director, Creative Services/Marketing
Jennifer Olivares
Marketing Manager
Mary Claire Gordon
Managing Editor
Lynne Agoston
Production Manager
Tiffany Ward
Director of Accounting Services
Dawn Rosenfeld
Publisher, Denise Jackson
Managing Editor, Lynne Agoston
Production Manager, Tiffany Ward
Technical Editor
Michael Henley, mdhenleywater@gmail.com, (303) 324-9507
Advertising Sales Manager
Carol Nettles, carol@adboomadvertising.com
The Analyst is published quarterly as the official publication of the Association of Water Technologies. Copyright 2022 by the Association of Water Technologies. Materials may not be reproduced without written permission. Contents of the articles are the sole opinions of the author and do not necessarily express the policies and opinions of the publisher, editor or AWT. Authors are responsible for ensuring that the articles are properly released for classification and proprietary information. All advertising will be subject to publisher’s approval, and advertisers will agree to indemnify and relieve publisher of loss or claims resulting from advertising contents. Editorial material in the Analyst may be reproduced in whole or part with prior written permission. Request permission by writing to: Managing Editor, the Analyst, 1300 Piccard Drive, Suite LL 14, Rockville, MD 20850, USA. Annual subscription rate is $100 per year in the U.S. (4 issues). Please add $25 for Canada and Mexico. International subscriptions are $200 in U.S. funds.
2023 Technical Training Seminars (West)
February 21–24, 2023
Doubletree Mission Valley San Diego, California
2023 Technical Training Seminars (East)
March 29–April 1, 2023
Omni Pittsburgh Hotel Pittsburgh, Pennsylvania
2023 Business Owners Meeting
October 3, 2023
Amway Grand Hotel Grand Rapids, Michigan
2023 Annual Convention & Exposition
October 4–6, 2023
DeVos Place Convention Center and Amway Grand Hotel Grand Rapids, Michigan
2024 Technical Training Seminar (East)
April 17–20, 2024
Cleveland Marriott Downtown at Key Tower Cleveland, Ohio
2024 Annual Convention & Exposition
September 10–13, 2024
Louisville Convention Center and Omni Louisville Louisville, Kentucky
2025 Technical Training Seminars (West)
February 25–28, 2025 Doubletree Mission Valley San Diego, California
2025 Annual Convention & Exposition
November 12–15, 2025
The Broadmoor Hotel Colorado Spring, Colorado
2026 Annual Convention & Exposition
September 16–19, 2026
Oklahoma Convention Center and Omni Hotel Oklahoma City, Oklahoma
2027 Annual Convention & Exposition
September 8–11, 2027
Cleveland Convention Center Cleveland, Ohio
Also, please note that the following AWT committees meet on a monthly basis. All times shown are Eastern Time. To become active in one of these committees, please contact us at (301) 740-1421.
Second Tuesday of each month, 11:00 am—Legislative/Regulatory Committee
Second Tuesday of each month, 2:30 pm—Convention Committee
Second Wednesday of each month, 11:00 am—Business Resources Committee
Second Friday of each month, 2:00 pm—Pretreatment Subcommittee
Second Friday of each month, 10:00 am—Special Projects Subcommittee
Second Friday of each month, 11:00 am—Cooling Subcommittee
Third Monday of each month, 9:00 am—Certification Committee
Third Monday of each month, 3:30 pm—Young Professionals Task Force
Third Tuesday of each month, 3:00 pm—Education Committee
Third Friday of each month, 9:00 am—Boiler Subcommittee
Third Friday of each month, 10:00 am—Technical Committee
Quarterly (call for meeting dates), 11:00 am—Wastewater Subcommittee
American Water Summit, January 24–26, 2023, Los Angeles, California
Cooling Technology Institute, January 29–February 3, 2023, Memphis, Tennessee
ASHRAE Winter Conference and AHR Expo, February 4–8, 2023, Atlanta, Georgia
Membrane Technology Conference (sponsored by AMTA and AWWA), February 20–23, 2023, Knoxville, Tennessee
38th Annual WateReuse Symposium, March 5–8, 2023, Atlanta, Georgia
NACE, Corrosion Risk Management Conference, March 19–23, 2023, Denver, Colorado
ACS, Spring National Meeting & Expo, March 26–30, 2023, Indianapolis, Indiana WQA, Convention and Expo, April 18–20, 2023, Las Vegas, Nevada
Electric Utility Chemistry Workshop, June 6–8, 2023, Champaign, Illinois AWWA, Annual Conference & Expo, June 11–14, 2023, Toronto, Ontario, Canada
ACS, Fall National Meeting & Expo, August 13–17, 2023, San Francisco, California
WEFTEC, Annual Technical Exhibition and Conference, September 30–October 4, Chicago, Illinois
RETA, Annual Convention, November 13–16, 2023, Jacksonville, Florida
As water technology professionals, we must continually be innovating. For us to do that, we must learn from each other. In this Technology Supplement to the Fall 2022 issue of the Analyst, we provide new AWT guidance on cooling tower cleaning and disinfection; we examine the optimal use of regular monitoring to mitigate microbial influenced corrosion from boiler condensate return; and we focus on whether and how lab testing results are—or are not—relevant to the daily operation of water treatment systems. We hope you find this Supplement both interesting and beneficial.
I welcome your comments and suggestions, so please do not hesitate to reach out to me at president@awt.org.
Pragmatic. It’s one of my favorite words because it means to look at life in a practical way without the distractions of philosophy and long, drawn-out intellectual discussions and debates. “If it makes sense, then let’s do it this way ” is a pragmatist’s guiding principle. Likewise, water treatment lends itself to reality and what will get the job done.
In this Technnology Supplement to the Fall 2022 issue of the Analyst, two of the articles look at utilitarian matters related to cooling tower operation. The third article focuses on iron removal from boiler condensate return, while the final article reviews whether lab testing results are relevant to the day-to-day operation of a water treatment system.
In the balance of this commentary, we will briefly examine each of these contributions.
The first article in The Supplement, “AWT Cooling Tower Cleaning and Disinfection Guidance,” presents a new guidance document issued by the Cooling Water Subcommittee. Subcommittee members involved with writing the document are Derrick Vandenberg, Vance D. Fiegel, Robert Downey, and Thomas Mercer. The aim of this work by the Cooling Water Subcommittee is to offer SOPs for cleaning and disinfecting cooling towers.
The article begins with a section that examines standard operating procedures (SOPs) for cooling towers. Subsections examine these areas:
• What is the purpose of cleaning and disinfection procedures?
By Mike Henley, MD Henley & Associates• Why is it important to clean and disinfect the cooling system?
• How can we protect workers?
The next section is titled “Cleaning and Disinfection Procedure.” Areas covered in this section include:
• Pre-cleaning disinfection.
• Cleaning the cooling tower.
• Cleaning of the cooling tower fill pack.
• Post-cleaning disinfection.
Author Catherine Allen (“How Can Regular Monitoring Mitigate Microbial Influenced Corrosion in Cooling Systems?”) examines corrosion caused by microorganisms, also commonly referred to as microbially influenced corrosion (MIC), which can be found in open and closed cooling systems. Biofouling creates an environment that facilitates corrosive conditions. Sessile microbials that settle on surfaces and form biofilms are the source of MIC formation.
Ms. Allen notes that it is important to understand that biofilms can form insulating layers that impact the performance of heat exchangers. Biofilm can also set up the conditions that lead to corrosion and prevent corrosion inhibitors from reaching the metal surfaces within a system.
Topics addressed by the article examine background on biofilms and detection and monitoring approaches. Subjects discussed in the article include:
•
• Biofilms
• Microbiological analysis of cooling water
• Common dipslide
• Sulfate-reducing bacteria
• Spot tests
The aim of microbial monitoring in cooling water systems is to detect biofouling early so steps can be taken to prevent MIC and related corrosion in a cooling system.
Dr. Swati Sharma’s article, “Technical Briefing: Using Magnetic Dirt Filtration for Magnetite Removal,” looks at an approach for removing magnetite, also known as black iron oxide, from the condensate return by using magnetic iron dirt filtration technology. Filtration is viewed as a way to eliminate magnetite, which can create sludge deposits that, in combination with water hardness and other contaminants, may contribute to boiler system failures. Another benefit of magnetite removal is the ability to reclaim water for reuse in a boiler.
Corrosion caused by magnetite can cause such boiler system problems as poor system circulation, blocked pipes, higher operating costs, and boiler breakdowns. To look for a solution to help solve this problem, Dr. Sharma reports on a study where iron-removal filters were tested for their efficacy in removing iron from the condensate system at a steam-generation plant.
In the final article of the Technical Supplement, authors Robert J. Ferguson and John F. Zibrida (“Are We Treating Beakers or Systems? The Pitfalls of Laboratory Simulation”) raise the very real question about whether or not lab-based studies that simulate water treatment provide accurate information that is applicable to the end user site. The authors suggest that a goal of lab work tied to water system simulations should be to generate findings that translate into successful water treatment in the field.
The authors note that laboratory simulations should be conducted under conditions matching those of an actual operational system as closely as possible. They also say that the use of pilot test units can help lab work to better duplicate an actual system because they may use the same water source.
For pilot tests, the article also reports that successful lab and pilot testing includes determining and matching parameters such as treatment product residence time, shear force against the tube wall, water temperature, and the number of active sites for growth on an existing substrate.
(Editor’s note: This article is based on new guidance procedures recently developed by the AWT Cooling Water Subcommittee.)
1. What is the purpose of cleaning and disinfection procedures?
a. Maintaining the cleanliness of the cooling tower system and the cooling water in it is critical for preventing or controlling the risk of exposure to Legionella. This paper provides proven, professional guidance on how to effectively and safely clean and disinfect a cooling tower system.
b. It is the job of the building owner and their responsible manager to make the decisions as to whether the cooling water system is clean enough for operation as well as the frequency and scope of inspection and the need for system cleaning. For such decisions, they may seek advice and help from specialist service providers for water treatment, risk assessment, cleaning, and disinfection.
c. In all cases, local conditions and local regulations must be considered and followed when designing the procedures for inspecting and cleaning the cooling system.
2. Why is it important to clean and disinfect the cooling system?
a. Legionella are more likely to proliferate in water systems that contain sediment, deposits, and biofilm, which can protect the organisms from water treatments that are used to control microbiological growth. Sediments and deposits also provide nutrients that accelerate growth and lead to multiplication of bacteria counts. Maintaining system cleanliness is crucial to reducing cooling tower hygiene risks.
b. Effective water treatment measures can reduce the rate at which a cooling system becomes fouled. However, an evaporative cooling system will inevitably accumulate airborne debris, dust, and other particulate matter from the atmosphere and may be subject to contamination originating from the process for which the system provides cooling. It is therefore necessary to take cooling systems out of service periodically for physical, and possibly chemical, cleaning to remove this fouling.
a. As a good practice to ensure worker safety, employers should provide appropriate personal protective equipment (PPE) and demand its use when workers perform any routine maintenance, cleaning, or disinfection activities on water systems that may be contaminated with Legionella. This includes work on hot and cold domestic water systems; cooling towers; and heating, ventilation, and air conditioning
“A cooling tower system cleaning operation will normally comprise a precleaning disinfection; a physical cleaning, and, if appropriate, chemical cleaning; and a postcleaning disinfection.”
(HVAC) equipment. If Legionella contamination is possible but a Legionellosis outbreak is not known or suspected, use respirators. The U.S. Occupational Safety and Health Administration (OSHA) prescribes the following criteria as found in the OSHA document Legionellosis (Legionnaires’ Disease and Pontiac Fever, which is available at https://www. osha.gov/legionnaires-disease/control-prevention):
• When inspecting a cooling tower or taking water samples (i.e., for a short time exposure to tower vapor), use a National Institute for Occupational Safety and Health-approved respirator at least as protective as an N95 respirator. N95 refers to particulate masks that have 95% efficiency in removing 0.3-micron (µm) particles.
• When working with biocides to clean and disinfect systems, use eye protection (chemical goggles or face shield with safety glasses), protective gloves, and suitable protective clothing, as recommended by the biocide manufacturer.
• Workers engaged in tower cleaning must wear, at a minimum, the PPE required for any chemicals being used, and a half-face air-purifying respirator equipped with an N100 cartridge.
• Ensure that the selection of respiratory protection considers the agents used for decontamination, and provide combination cartridge respirators where both particulate and chemical hazards may be present. If organic vapor cartridges are used, implement a cartridge change schedule.
• Tasks that involve an increase in moisture and spray, including cleaning and decontamination activities, may adversely affect N100 cartridge respirators. In such instances, consider providing a supplied-air respirator to improve worker protection. A loose-fitting powered air-purifying respirator or supplied-air respirator may also improve worker comfort when wearing respirators for long periods.
• Just as for worksites with mandatory use of respirators, employers who permit voluntary use of respirators
must implement a respiratory protection program that complies with the applicable provisions of OSHA’s Respiratory Protection standard (29 CFR 1910.134). This includes compliance with the standard’s requirements for obtaining medical clearance for wearing the respirator and for conducting fit testing prior to actual use of respirators and must comply with the provisions set forth in the standard’s Appendix D (Mandatory) – Information for Employees Using Respirators When Not Required Under the Standard.
• In the event of a known (i.e., identified) or suspected Legionellosis outbreak, workers who may be exposed to aerosolized Legionella must wear respirators. For most exposures, respirators should be equipped with N100 filters or a similar type of filter media capable of effectively collecting particles in the 1-micron size range. Examples of workers with potential exposure include those examining the affected water system, conducting disinfection activities on the system, or performing other essential tasks in areas near contaminated cooling towers or serviced by contaminated HVAC units.
• The employer should always conduct a hazard analysis to determine which workers are at risk of exposure and identify any additional hazards that may be present and the appropriate measures to control worker exposures.
• PPE provided to workers (including respirators and other clothing or gear) must be selected in accordance with OSHA’s PPE standards (29 CFR 1910 Subpart I).
• Hand protection (i.e., gloves) must be selected based on the material (e.g., nitrile, vinyl) compatible with any chemical exposure. Selection should also consider the other characteristics of the glove, such as fit, durability, and comfort. If necessary, use the vinyl or nitrile gloves under heavier (e.g., rubber, leather, heavy cotton) gloves for operations with potential for glove tearing or for protection against hand injury.
• Replace disposable gloves as soon as possible when contaminated, cracked, torn, or punctured and upon task completion.
• Remove gloves prior to leaving the work area and place them in areas specifically designated for storage, washing, decontamination, or, for disposable or damaged reusable gloves, disposal.
• Thoroughly wash hands with soap and water upon removing gloves, before eating, and when replacing torn or worn gloves.
• Required PPE, except for most protective footwear, must be provided at no cost to the worker, readily accessible to workers, and available in appropriate sizes.
A cooling tower system cleaning operation will normally comprise a precleaning disinfection; a physical cleaning, and, if appropriate, chemical cleaning; and a post-cleaning disinfection.
a. Before cleaning the system, the cooling water should be disinfected using an oxidizing biocide such as chlorine, bromine, or chlorine dioxide in conjunction with a suitable biodispersant. This is to minimize health risks to the cleaning staff and surrounding building occupants.
b. Based on product and dosage recommendations of the water treatment supplier or specialist service provider, the biodispersant should be added 30 minutes before the addition of the chosen disinfectant chemical. The biodispersant should be circulated throughout the cooling water system via normal cooling tower operation, to ensure that the bio dispersant reaches all wetted surfaces.
Caution: The dispersant must not be a surfactant because the cooling tower manufacturers have discovered that surfactants and certain wetting agents can impede the efficiency of highefficiency drift eliminators (where installed), thereby rendering them ineffective and causing the cooling tower fans (on mechanical draft cooling towers) to carry Legionella-containing droplets a significant distance away from the cooling towers.
c. The required concentration of the free disinfectant as recommended by the product manufacturer should be established and circulated throughout the cooling tower system. Manufacturer’s recommendations for the required time should be followed. If there are no instructions, then a continuous minimum residual of 5 milligrams per liter (mg/L) as free chlorine for a minimum of five hours should be maintained. If the time available to conduct the operation is limited, using a higher disinfectant concentration for a shorter time may be acceptable. This will, however, increase the risk of damage to the materials of construction of the cooling water system. Excessive disinfectant levels should be avoided.
d. The disinfecting solution is to be monitored periodically and maintained in the cooling tower system throughout the disinfection period by adding more disinfectant as required. The normal disinfectant level required depends on the minimum circulation period adopted. Table 1 provides the minimum contact times in disinfectant levels.
Minimum Circulation Time
Minimum Continuous Disinfectant Level (as free Cl2)
5 Hours 5 mg/L
2 Hours 25 mg/L
1 Hours 50 mg/L
*Health and Safety Executive (Great Britain) Page 35, Table 1.6 https://www.hse.gov.uk/pubns/priced/hsg274part1.pdf
e. The recommended disinfectant residual needs to be established throughout the whole system for the contact time and not simply the cooling tower sump. Systems with multiple sumps may require additional dosing to ensure good distribution of disinfectant.
f. Initially, the cooling tower fan(s) are switched off until the disinfectant is mixed throughout the system. Rotate offline equipment (e.g., offline chillers, plate-and-frame heat exchangers, condenser water pumps) so that the disinfectant reaches all parts of the associated condenser water system. Once this is achieved, the fan(s) should be switched on for the remainder of the process to ensure that the disinfectant reaches all internal surfaces that become wet during normal operation of the tower, and which potentially could be contaminated.
g. If chlorine is used as a disinfectant, its efficacy is reduced if the system pH value is greater than pH 8. To achieve the same disinfection effect, its residual needs to be increased 3 to 4 times (i.e., in place of 5 mg/L for five hours, 15 to 20 mg/L is required for the same period). Generally, this is not recommended, so if the system water is above pH 8, adopt one of the following procedures to compensate, without increasing the chlorine residual:
• Introduce a heavy bleed off for several hours to reduce both rthe pH of the system water and its chlorine demand before carrying out disinfection.
• Reduce system pH by adding an alkalinity reduction chemical.
• Augment the chlorine dosage with enough sodium bromide to change the disinfectant from chlorine to bromine.
h. If bromine or chlorine dioxide is used in systems where the pH is above 8, the reserves do not need to be increased and the pH does not need to be adjusted, as these disinfectants remain effective at higher pH levels.
i. Once the system has been predisinfected, the water should then be dechlorinated and drained. Dechlorination can be accomplished using a dechlorinating agent, such as sodium bisulfite.
a. After precleaning disinfection, manual cleaning operations can be carried out with all accessible areas of the tower being cleaned. Accessible areas of the system should be washed adequately, but cleaning methods that create excessive spray (e.g., high-pressure water jetting) should be avoided.
b. If considered necessary, high-pressure jetting should only be carried out when the buildings nearby are unoccupied or, in the case of permanently occupied nearby buildings, windows should be closed, air inlets blanked off, and the area that is being water jetted should be tented. The area should be isolated, and consideration of other occupied premises nearby, as well as people who may be nearby during cleaning, should be taken.
c. It is important to check with cooling tower manufacturer representatives, or the cooling tower Operations & Maintenance manual regarding recommended cooling tower cleaning procedures. For example, some cooling towers have specially designed fill packs and/or fill removal systems. Failure to properly follow guidance can result in damage to the fill pack or fill removal systems. This would lead to channeling of cooling water and subsequent reduced thermal performance. In addition, some cooling tower fill packs have limitations on the pressure of water jetting. Too high of a pressure can damage the fill pack and lead to water channeling, reduced thermal performance, and ultimately, premature failure of the fill pack, increasing customer maintenance costs.
d. Should it be determined prior to cleaning that the fill pack is in poor condition or cannot be cleaned physically, it is recommended that the old fill pack be replaced with new fill pack during this process. This needs to be planned in order to have sufficient time for the new fill pack to be ordered and placed onsite. Otherwise, time will be lost, and negative operational impact could result.
e. Cleaning staff that carry out water jetting or other operations that could create aerosols should wear suitable respiratory protective equipment (RPE) as described above, and the cleaning contractor in the method statement should specify this. Staff using this equipment should be adequately trained and the equipment properly maintained. Further guidance on why and when RPE should be used and how to select RPE that is adequate and suitable should be investigated by the cleaning staff and their managers.
f. In addition to the manual cleaning operations, enhanced chemical cleaning processes may be required to remove certain types of deposit. Table 2 gives guidance on cleaning processes that can be employed for different types of fouling. Once clean, the system should be drained and flushed with clean water until the water going to the drain is clear. Cleaning staff should be aware of local discharge requirements.
Silt, sediment, and airborne dust
Biofouling
Hardness scale
Corrosion products
Organic process contaminants
Physical removal with shovels, a wet vac, or similar method. Post-disinfect to ensure that any microbial fouling released is killed.
Strong oxidizing biocide combined with biodispersant and circulated with fans off and heavy purge. Shut system down and drain all sumps. Check cleanliness of strainers, heat exchangers, and fill pack.
Acid clean using appropriate acid and inhibitor. If cleaning proves to be ineffective, consideration should be given to replacing heavily scaled fill pack.
Acid clean using the appropriate acid and inhibitor or suitable chelant/dispersant.
Identify the contaminant and select an appropriate solvent/dispersant.
3. Cleaning the cooling tower fill pack
a. Maintaining the cleanliness of the cooling tower system and the water in it is critical for preventing or controlling the risk of exposure to Legionella ; it is therefore necessary to demonstrate the cleanliness of the system, including the fill pack, whether the fill pack is removed or not. The approach to cleaning the cooling tower fill pack will depend on several factors, including:
• The nature of the contamination
• The design of the cooling tower and practicalities of accessing and/or removing the fill pack
• The type of fill pack in use (i.e., block or sheet)
b. If the cooling system operates in a relatively clean environment with continuous effective water treatment, it is possible for a cooling tower fill pack to remain free from fouling for several years. However, a fill pack may appear clean from the visible surfaces but be fouled internally.
c. Removal of the cooling tower fill pack, where this can be done relatively easily and reinstated safely without damage, will improve the inspection and assessment and aid any potential cleaning.
d. Whether the fill pack is removed or not, evidence of its cleanliness should be demonstrated and assessment made using appropriate techniques, as detailed in Table 3, and the findings recorded. Photographic records of fill pack condition can help in the process and should be maintained.
e. Sheet fill pack can also be separated to allow silt or sediment to be washed off. Block-type fill pack cannot be cleaned effectively by jetting but may respond to flushing with high volumes of water or cleaning fluid. If a chemical process is
required to remove fouling, this may be done most conveniently in situ by circulating a concentrated cleaning solution through the pack. Application of a suitable cleaning solution may remove light deposits. Alternatively, the fill pack can be removed and immersed in a suitable cleaning solution. In some circumstances, it may be possible to remove certain deposits by removing the back, allowing it to dry out and then gently knocking or dropping it from a low height to shock the dry deposits off, taking care not to damage the fill pack itself.
f. When the fill pack or drift eliminators are heavily found and cleaning is not practical, consider replacing them. It may be prudent to hold sections of new pack and drift eliminators on site for use during system cleaning operations. It is important that replacement pack and drift eliminator match or have the same dimensions and performance as the original to maintain proper water/ air flow balance. Improper water/air flow balance can negatively impact cooling efficiency and increase the volume of drift and aerosol release from the system.
a. Upon completing the cleaning operation, the system should be refilled and disinfected using the method described under “pre-cleaning disinfection,” using an oxidizing biocide to maintain the minimum disinfectant levels and circulation times indicated in Table 1. The disinfectant levels should be monitored periodically and maintained to ensure that the minimum levels are present. The use of a bio dispersant will enhance the effectiveness of this disinfection. This should be done following the same process as outlined in prior Section 1b.
Caution: The dispersant must not be a surfactant because the cooling tower manufacturers have discovered that surfactants and certain wetting agents can impede the efficiency of highefficiency drift eliminators (where installed), thereby rendering them ineffective, thus causing the cooling tower fans (on mechanical draft cooling towers) to carry Legionella-containing droplets a significant distance away from the cooling towers.
b. If returning the system to immediate service, the disinfectant level can be allowed to decay over the first few hours of operation and a startup level of the normal water treatment chemicals added. If, however, the system is going to be left idle before restarting, dechlorinate the water, drain and flush the system, and leave it empty. On startup, the system should be refilled with fresh water, and the water treatment program should immediately be reinstated with a dosage of the appropriate startup level of treatment chemicals, including biocide.
c. Before water containing high residuals of chlorine, bromine, and chlorine dioxide is discharged to the drain, neutralize
the disinfectant. The usual procedure is to add sodium bisulfite as a neutralizer. The effluent from any disinfection and/or chemical cleaning process, neutralized or not, may require a “consent to discharge.” Therefore, permission to discharge may be required from the effluent receiver.
Derrick Vandenberg obtained his bachelor’s degree in chemistry in the late 1980s. In 2002, he joined Guardian Chemicals Inc. to sell to and serve the water treatment industry. He obtained his CWT 15 years ago. He now serves as technical director for Guardian Chemicals as well as managing a large customer territory in the Great White North.
Vance D. Fiegel is a cell and microbiologist, inventor, and entrepreneur. He began his career at the University of Minnesota, where he studied the basic biology of inflammation and wound healing. Leaving the university 30 years ago, he has co-founded numerous ventures and is currently the chief science & technology officer at Creative Water Solutions, LLC and Atlantic BioVentures, LLC. He has published more than 60 research articles and holds over 25 U.S. and foreign patents.
Robert Downey is a global water treatment specialist for Baltimore Aircoi (BAC)l. In the years prior to joining BAC, he worked at Phigenics, a water management and hygiene consultancy. Before Phigenics, Mr. Downey enjoyed a 22-year career at Nalco Water in various sales and sales management roles. In his current role at BAC, he helps customers with expertise and advice to help them manage their evaporative cooling needs, with particular focus on water quality, usage, treatment, and hygiene issues.
Thomas Mercer, CWT, has served on both the Cooling Water Technical Subcommittee and the Education Committee during his membership at AWT. He has been with DuBois Chemicals for his entire 38-year career. At DuBois, Mr. Mercer is currently the technical specialist for the eastern United States. He has held several roles at DuBois, including developing water treatment products for cleaning, treating, and descaling cooling towers, boilers, and closed loops. Mr. Mercer has also developed and presented water and wastewater training programs for both customers and DuBois personnel. In recent years, he was in the first class to be certified in the Certified Legionella Water Safety & Management Professional ASSE/IAPMO/ANSI 12080 program. Mr. Mercer’s work has also included training and presentations to outside organizations such as ASHRAE, Healthcare Engineers, and others.
Microbes, as with all lifeforms, have optimal conditions in which they thrive. Unfortunately, for water treatment specialists, these conditions are just what we find in open and closed water recirculating systems. Microbes are especially abundant in open recirculating systems due to the concentration of nutrients through the cycling of dissolved solids by evaporation as well as suspended solids being blown in.
In cooling water systems, the wet surfaces are prone to microbiological growth, which in turn can lead to the formation of a biofilm. If left untreated, the biofilm can result in biofouling, causing a reduction in plant life and plant efficiency.
Biofouling issues need to be controlled, although the methods of control vary depending on whether the microbes are in a planktonic or sessile state. Sessile microbes are responsible for biofilm formation. Once biofouling has occurred in a system, even mechanical cleaning cannot remove all traces of a biofilm. Previously fouled surfaces are more susceptible to colonization, as residual biofilm materials promote growth and reduce lag time between biofouling episodes.
While the effects of biofilm in a system are well known, it is important to keep the following in mind:
• Biofilms can act as an insulating layer, and the performance of the heat exchanger deteriorates in correlation to the thickness of the biofilm.
• Microbial influenced corrosion (MIC) occurs when the microbes act as catalysts for conventional corrosion.
· The presence of the microbes prevents corrosion inhibitors from reaching and passivating the systems metal surfaces.
Corrosion reactions are accelerated by microbiological interactions.
· Microbial metabolites can be corrosive to the metalwork.
· The most common category of MIC bacteria are sulfate-reducing bacteria (SRB).
In this article, we will investigate the methods in which a large microbiological population in cooling water systems is undesirable and why regular monitoring can minimize the detrimental effects on the system.
Corrosion, which is irreversible deterioration of a metal, is estimated to cost global industries a staggering $2.5 trillion annually (1). The latest figures estimate that 15 to 35% of that figure could be saved by the implementation of better corrosion controls.
Metal alloys used in the water systems of industrial processes and structures are susceptible to corrosion, and the rate and type of corrosion can be determined by a number of factors. These include:
• Microbiology
• Water chemistry
• Metallurgy
• Electrochemistry
For the purposes of this article, the author will concentrate on microbiology, but the reader should take note that to fully understand and mitigate against corrosion, all four of these elements need to be understood in complex water systems.
Natural waters contain a diverse mixture of microbes, some of which are ubiquitous, and when a metal surface is immersed in water, corrosion and biofilm formation both begin almost immediately. Corrosion that is caused, or influenced, by microbes is known as MIC, which can also be referred to as biocorrosion. In literature, it is shown that MIC is not caused by the direct interaction of microorganisms with the material but by the reaction of the medium in the area of the biofilm, and in particular, from the metabolites of the microbes in question (2).
MIC can be observed wherever and whenever an influx of organic substances occurs and suitable surfaces are available for the microorganisms that form biofilm to colonize. The temperatures of the media play more of a secondary role, as the relevant microorganisms are active within a temperature range of approximately -20 °C and 120 °C. The ideal temperature, however, is at 10 °C to 40 °C. Hence, the operational temperature of cooling water systems is within the ideal range that makes them prone to MIC (3).
“A 21-day SRB test is recommended for reference purposes, but shorter tests can provide equal confidence for routine management of the water system, provided sufficient numbers of samples are collected and analyzed.”
The microbial population in waters can be general divided into two populations:
1. Planktonic (free-floating)
2. Sessile (immobile)
The same species of microorganisms can be found in both populations. Table A shows some of the most common microbes found in cooling systems.
Part Effect
Sulfate Reducing Bacteria Heat exchangers, deck, basin Converts sulfate to H2S; causes corrosion
Shewanella Heat exchangers Dissolves Fe/MN oxide protective layer
Gallionella Heat exchangers, deck, basin Converts soluble iron salts into iron oxide; can form voluminous deposits
Lepththrix Heat exchangers, deck, basin Converts soluble iron salts into iron oxide; can form voluminous deposits
Thiobacillus Heat exchangers, wood Converts sulfur or sulfides to sulfuric acid
Pseudomanas Heat exchangers Produces exopolysaccrides that promote biofilm formation
Legionella Human being Produces pneumonia-like symptoms
Brown rot fungus Wooden structure Biodegradation of wood
White rot fungus Wooden structure Biodegradation of wood
Soft rot fungus Wooden structure Biodegradation of wood
Blue green algae Heat exchangers, deck, basin Reduces heat transfer in heat exchanges
Source: Reference 4—“Influence of Microbes in Cooling Tower: A Review,” Ranjana Tewari, S K Mehta, Pujan Vaishnav.
In addition to those listed in Table A (4), many other types of planktonic bacteria exist in a cooling water system. These planktonic forms come together to form a sessile aggregate that adheres to the inside of the system’s pipework. These sessile bacteria then produce a slime, an extracellular polymeric substance that forms a matrix of DNA, proteins, and polysaccharides. The result is a substance that forms a protective layer around the population of bacteria. Biofilm development is normally isolated into three distinct stages of development:
1. Attachment: Bacteria can adhere to surfaces in a number of ways. This includes variations in metallurgy allowing attachment sites on surfaces, chemical nutrients, or a lack of biocide. The primary method of adhesion is through weak Van der Waals forces and hydrophobic effects.
2. Growth: Once initial colonization has occurred, population size increases exponentially. Other bacterial species and inorganic components of the water system contribute to and constitute the complex biofilm layer.
3. Dispersal: Bacteria within the biofilm secrete enzymes and break free of the biofilm itself, becoming planktonic once again. This enables the biofilm to spread to other parts of the water system.
Once formed, these biofilms can generate aerobic and anaerobic conditions. The anaerobic conditions enable anaerobes such as SRBs to multiply, and a potential difference is established between different areas of the metal surface.
SRB, such as Desulfovibrio, reduce sulfur compounds like sulfate, sulfite, and thiosulfate to hydrogen sulfide. SRB are thought to be the most prolific contributor to MIC and a major cause of corrosion in open and closed water-cooling systems. SRB use several mechanisms of corrosion, including cathodic depolarization, anodic depolarization, production of corrosive iron sulfides, sulfide-induced stress corrosion cracking, and local corrosion.
The presence of SRB is normally indicated by a reddish or yellowish nodule on metal surfaces that, when broken, exhibits black corrosion byproduct. If hydrochloric acid is added to the black deposit, hydrogen sulfide will be released, giving off a “rotten egg” odor.
The presence of SRB can contribute to accelerated, localized pitting corrosion and eventual perforation of the pipe. Corrosion by SRB can cause significant damage to surfaces, particularly where pipework may have bends, uneven surfaces, abrasions, or joints and welds. In addition, the amount of nitrite, often used as an anodic corrosion inhibitor in cooling water systems, can be reduced by SRB and therefore in closed heating and chilled systems where nitrite is used, SRB must be controlled. In Figure 1 (5), the left photo shows a cleaned corrosion coupon with SRB growing on it, while the right photo shows a Type 304 stainless steel condenser tube with pits and dark spots.
While it is possible to control the MIC process, the corrosion programs that are used by water treatment companies are not always effective: inhibitor levels can drop, be used up and/or provide a source of food for bacteria and other organisms (e.g., nitrite-based corrosion inhibitors feeding nitrite-reducing bacteria). It is essential that water quality is monitored and that microbiological control be at the forefront of any water treatment program.
“Once biofouling has occurred in a system, even mechanical cleaning cannot remove all traces of a biofilm.”
Figure 1: The left photo shows a cleaned low-carbon steel corrosion coupon with SRB growing on it and producing concentric rings of corrosion. The right photo is a water washed Type 304 stainless steel 5/8-inch condenser tube that has pits and dark spots.
“Agar dipslides now form part of many legislative guidance papers in terms of routine microbiological monitoring.”
many countries. However, the plate count method requires the operator to have access to a laboratory, a filtration set up, and training for how to count the results. Because the lab test is cumbersome, an easier method was required for routine monitoring. This is why agar-based dipslides have become so popular.
Agar dipslides now form part of many legislative guidance papers in terms of routine microbiological monitoring. Figure 2 illustrates increasing bacteria contamination such as may be found on a dipslide. Many different types of agar dipslides are available for various species. Dipslides are great tools for monitoring for a number of key reasons:
• Relatively inexpensive.
• Easy to use—widely considered a “Do-It-Yourself” microbiology test.
There are several ways in which microbiological control can be achieved, including:
• Reducing or eliminating suspended solids
• Dosing biocides.
• Maintaining water movement throughout the system (e.g., eliminating dead legs).
• Monitoring and sampling the system on a regular basis
A 2016 report estimates that the Earth supports approximately 1 trillion species of microbes, with most of them yet to be discovered (6). When it comes to cooling water, hundreds of species may be present at any one time, with some being very difficult to measure.
It is considered best practice to use “indicator organisms” to gain a general overview of the microbiological condition of the water. This translates to: if the level of general bacteria is kept under control, one can assume your system will be kept microbiologically under control
Traditional methods for these tests have adopted standard agar plate count methods. These are still used in laboratories today, and their results are required to fulfil regulatory guidance in
• Full results are available within two to five days (application dependent). Because the user has access to the test, checking for early indication (e.g., after 24 hours) is possible.
• Allow for trend analysis.
Figure 2: A reading shows increasing contamination of bacteria on TTC dipslide, demonstrating how trends can be tracked and illustrated.
While there are a lot of advantages to dipslides, users should keep the following in mind:
• Dipslides will only measure the number of planktonic (culturable) aerobic bacteria in a sample.
• Dipslides will not measure:
· Bacteria that will not grow on the type of agar media being used.
· Bacteria which require a different incubation temperature.
Bacteria that are not actively growing at the time of sampling.
Bacteria with special growth requirements.
· Bacteria growing inside biofilms (sessile).
• The correct temperature for incubation forms an integral part of any microbiological test and it is a general misconception that “hotter is better” or “the hotter the incubator, the faster the results.” Neither of these statements are true, and, in fact, incorrect temperatures can result in misinterpretation of results.
Dipslides should be incubated to best replicate the system from which the sample was taken to provide a “true” picture of the general microbiological condition of that system. Given the correct conditions, bacteria can reproduce exponentially, doubling in number in as little as 20 minutes. To help encourage growth, we want to duplicate the environment in which they are currently surviving as much as possible.
To use humans as an analogy, we are incredibly good at self-regulating our body temperature to 98.6 °F (37 °C), but our environment can have a direct impact on our ability to maintain that ideal temperature. If a person is simply placed in a desert climate without proper supplies and protection, they will ultimately end up with heatstroke, which can cause death. Similarly, if you place someone in an arctic climate, hypothermia can set in and will lead to death. A person will not thrive in either condition because we are not able to regulate our body temperature to an optimum level. This applies to all organisms, including those we are trying to detect in a cooling system.
For example, samples taken from a cooling water sump will have come from an environment where that temperature is approximately 30 °C (86 °F). The test methods for testing bacteria from cooling water are therefore designed to be at the same temperature for optimum results.
The dipslides and agars described in the next section only demonstrate the capability of some of the more popular variants.
The most common type of dipslide is a dual-sided slide that allows convenient enumeration of aerobic microorganisms (in total viable count). The dipslide is prepared with nutrient TTC agar on both sides and is used for general-purpose cultivation of aerobic organisms, which can be obtained from surfaces, fluids, or the air. The TTC additive in the nutrient agar reacts with enzymes produced in aerobic respiration to produce a color change from white to red, allowing easy enumeration. This is illustrated in Figure 3.
Figure 3: Shows increasing contamination of bacteria on TTC dipslide.
The TTC/ROSE dipslide allows convenient enumeration of aerobic microorganisms (total viable count), including yeasts and molds in a single test. The dipslide is prepared with nutrient TTC agar on one side (responsive to aerobic microbes) and a Rose Bengal agar with chloramphenicol, which selects for yeasts and molds, typically used in the food industry.
Figure 4: Both sides of the TTC/Rose Bengal.
The Rose Bengal agar (Figure 4), as its name suggests, gives this side of the slide a distinctive pink coloration, making it easy for the user to identify which side is which. The TTC/ROSE dipslide is also ideal for use in the detection of hydrocarbon using microorganisms found in fuel storage. These microorganisms cause blockages to fuel filters, and the acidic metabolites can cause tank erosion. The TTC additive in the nutrient agar reacts with enzymes produced in aerobic respiration to produce a color change from white to red, allowing easy enumeration. The Rose Bengal agar will show growth as white, white/pink, or yellow/green spots, depending on the type of yeasts or molds present.
A 21-day SRB test is recommended for reference purposes, but shorter tests can provide equal confidence for routine management of the water system, provided sufficient numbers of samples are collected and analyzed. The standard method typically uses a modified Postgates broth or modified API RP-38 medium, which is inoculated with 1 milliliter (mL) of sample and incubated under anaerobic conditions at 30 °C for 21 days.
The shorter tests contain a straw-colored citrate medium, which reacts to the production of hydrogen sulfide to give a semiquantitative result after incubation at 35 °C for five days. The SRB test is used specifically to indicate the presence of bacteria, which, under the correct conditions, are able to produce hydrogen sulfide. Hydrogen sulfide is a colorless gas that is extremely corrosive to ferrous and nonferrous metals.
Results are determined by the spreading black precipitation from the inoculation point through the agar (Figure 5). When testing samples already high in sulfide, there may be a sudden blackening of the medium, in which case, contamination can be judged by the advancement of the blackening further into the medium. The results are semiquantitative.
Figure 5: SRB results.
Source: Reference 7.
The photos in Figure 6 show varying degrees of contamination from a closed-circuit water system.
This test is used to confirm the presence of SRB on a metal surface. This test is done on the spot of the corrosion site. A solution of this reagent is placed onto the metal surface for testing. Using a concentrated light and a magnifying lens, nitrogen bubbles are seen to evolve when sulfides are present. The rate of bubble evolution is indicative of the degree of sulfide contamination.
This test is primarily performed in a laboratory and using a microscope for easier visualization. Figure 7 (8) shows an example of an azide spot test.
Figure 7: High rate of nitrogen bubble evolution showing, indicating positive indication of SRB.
Special thanks to Curtis Williams, BSc., MSc. (Hons); Chris Shaw, BSc. (Hons), MWM Soc; Ian Penney, BSc. (Hons), FWMSoc; Kaylie Boland, and Karl Hodge for their input and specialist knowledge in writing this article.
1. Koch, G.; Varney, J. Thompson, N.; Moghissi, O.; Gould, M.; Payer, J. (2016). “International Measures of Prevention, Application, and Economics of Corrosion Technologies Study,” NACE International, Houston, Texas, accessible at http://impact.nace.org/documents/Nace-International-Report.pdf
2. Heitz, E. (1996). Microbially Influenced Corrosion of Materials Scientific and Engineering Aspects, with 56 Tables, 1st ed., Springer, Berlin, Germany.
3. Bartels, S.; Richter, T.; Nowak, E. (2009). “Microbially-Influenced Corrosion in Cooling Water Systems Development of a New Protection Concept for System Components Conveying Brackish Water,” VGB PowerTech 89(5), pp. 74–78.
4. Tewari, R., et al. (August 2019). “Influence of Microbes in Cooling Tower: A Review.” https://www.irjet.net/, International Research Journal of Engineering and Technology (IRJET), accessible at www.irjet.net/archives/V6/i8/IRJET-V6I864. pdf
5. Puckorius, P.R. (June 2018). “Understanding and Detecting MIC in Cooling Water Systems,” Water Purification and Conditioning, accessible at www. wcponline.com/2018/06/15/understanding-detecting-mic-cooling-water-systems/
6. Bakalar, N. (May 23, 2016). “Earth May Be Home to a Trillion Species of Microbes.” The New York Times, accessible at www.nytimes.com/2016/05/24/ science/one-trillion-microbes-on-earth.html#:~:text=According%20to%20a%20 new%20estimate,the%20number%20of%20insect%20species
7. Borenstein, S. (1996). Microbiologically Influenced Corrosion. 1st ed., Springer, Berlin, Germany.
8. Ibraheem, A.K. (September 2011). “Microbiologically Induced Corrosion,” Global Engineering Matters, AstraZeneca plc.
Cooling water systems can be ideal homes for waterborne microorganisms due to their materials of construction, operational temperature, operational pH, and a number of other factors. These waterborne organisms contribute to corrosion of the system in their accountability for MIC.
A number of measures can be put in place to control MIC, including regular flushing, eliminating dead legs, biocidal treatment, and inhibitors. These preventative actions should all be done in conjunction with regular and consistent monitoring.
Monitoring of indicator organisms is used to determine overall system health, and more specific testing can be done on species particularly associated with MIC, including SRBs. This monitoring is required at a frequency that, if interpreted correctly, can identify risks quickly, allowing remedial action to be taken to minimize any potential damage to the system integrity.
Catherine Allen is an application specialist and product manager at Tintometer Ltd. And focuses on products for use in industrial water treatment. Ms. Allen is a graduate of Newcastle University, having received a BSc hons degree in applied biology. After graduation, she immediately started work as a technical specialist for a test kit manufacturer, working in both laboratory and sales roles. Ms. Allen may be reached at Catherine.Allen@lovibond.uk
An important method for improving a facility’s energy efficiency is to increase the condensate return to the boiler. Depending on the system, magnetite (also known as black iron oxide) can potentially contribute to the reduction of condensate return into the boiler feedwater system. In the absence of a condensate return, the steam system must compensate for the loss with makeup water, thereby increasing operational costs. Most of the systems suffer from black iron oxide contamination, creating thick sludge deposits. These deposits resulting from corrosion, along with water hardness scales and other unwanted contaminants, can lead to system failure. A design using magnetic dirt filtration technology was studied for the removal of magnetite in the condensate return. The filters use individually removable neodymium magnetic rods, making it easy and safe to maintain. The study showed that the filtration technology removed more than 80% of the magnetite from the system, resulting in low iron levels. This article reviews some of the study findings.
The condensate system is an integral part of a boiler system. When steam is transferred to process application, it converts back to a liquid phase known as the condensate. Returning condensate to the boiler is an attractive option because the condensate not only contains water but also the boiler treatment chemicals and the energy needed for combustion. Returning condensate to the boiler is one of the highest returns on investment. Thus, the condensate needs to be of high quality.
Magnetite is one of the oxides of iron that is magnetic in nature (i.e., ferrimagnetic), and it may prevent condensate return. Old systems suffer from black iron oxide contamination, creating thick sludge deposits. These deposits resulting from corrosion, along with water hardness scales and other unwanted contaminants, can lead to system failure. Magnetite corrosion is a common problem in heating and cooling systems.
The oxide particles vary in size from large to sub-micron. The sub-micron-sized oxide particles can eventually leach to system water during operation. The presence of dissolved iron enhances the growth of iron bacteria, which forms dark-colored slime layers on the inner side of a system’s pipes. The slime is then released into the network through water flow fluctuations, leading to dirt buildup and damage to the system. Iron oxide, in combination with other debris or contaminants, could become mordant during circulation through the system, causing mechanical and operating failures (1–5).
Magnetic filtration techniques have been gaining recognition for their ability to remove iron oxide in hydronic heating systems. Yamamoto et al. (2) developed an iron oxide removal system utilizing a superconducting magnet from the boiler
feedwater in the thermal power plants. The study conducted by Okada et al., and Yamamoto et al. (2, 5) concluded that scale or iron oxide removal is efficient using a superconducting magnetic separation system. Another study by Mori et al. (1) developed a superconducting high-gradient magnetic separation (HGMS) system that could remove iron oxide in the boiler-feedwater system of thermal plants. The study simulated the hydronic heating system and conducted the HGMS experiments under a constant flow rate with a large pump in a large-scale system having a filter diameter of 300 millimeters (mm) (1).
In 2018, the innovation group at ADEY manufactured a magnetic filtration system designed with neodymium magnets to form bands of thicker and thinner magnetite collection. The filter canister is designed in a way that is large enough to capture the magnetite without affecting the flow of water but results in minimal pressure drop (3).
Keeping a condensate return system operating at peak performance is crucial. Customer expectations, operating budgets, and client comfort are all at stake. It is vital to protect against anything that might lead to hydronic system failure.
Magnetite corrosion can be potentially harmful to boiler and cooling components, even in small amounts. It can cause expensive damage to systems, leading to:
• Poor system circulation
• Erosion damage in turbulent areas
• Excessive system noise
• Blocked system pipes and heat emitters
• Increased operating costs
• Frequent breakdowns and costly repairs
The purpose of this study, in collaboration with ADEY, was to understand the efficiency of magnetic dirt filters A in removing black iron oxide sludge from a condensate system.
“The condensate system is an integral part of a boiler system. When steam is transferred to process application, it converts back to a liquid phase known as the condensate.”
Figure 1: Magnetic dirt filters.
A condensate system in a steam generation plant had a constant issue of high iron levels coming into the system,, which impacted the reusability of the condensate return into the boiler feedwater tank. Due to the old systems in place throughout the facility, a number of these existing systems consistently brought more than 20 parts per million (ppm) of iron back to the condensate receiver. As a result, the facility was not able to reuse the condensate and was also dealing with the expenses of makeup water.
To reduce the high levels of iron in the hydronics system, the author used the magnetic dirt filter range that removes damaging iron oxide sludge through magnetic filtration technology. Two 4-inch filters were installed in parallel at the facility to reduce the iron sludge from the condensate system before it entered the receiver tank and then he deaerator tank. The installed filters are shown in Figure 1.
“Due
systems
place throughout the facility, a number of these existing systems consistently brought more than 20 parts per million (ppm) of iron back to the condensate receiver.”
The system was installed and data were collected to test for iron levels before and after the filters. The data shown in Figure 2 show a decrease in iron levels from the condensate sample in a period of 60 days dated from August 2020 to October 2020. The initial concentration of iron in the beginning of filter installation was 9 ppm. Over the period of 60 days, the iron levels decreased to less than 1 ppm. Other data recorded from January 2020 until October 2020 and presented in Figure 3 show consistently high iron levels of more than 20 ppm until the installation of the filters and a gradual decrease in the iron levels post-installation.
to the old
in
Figure 3: Iron level trend over a period of 300 days.
The author wishes to thank Neil Watson, CFO of ADEY, for his help with this article.
1. Mori, T., et al. (2020). “Removal of Iron Oxide Scale from Feed-Water in Thermal Power Plant by High-Gradient Magnetic Separation: Scale-Up Effect,” IEEE Transactions on Magnetics, 56.12, pp. 1–8.
2. Yamamoto, J., et al. (2018). “Removal of Iron Scale from Feedwater in Thermal Power Plant by Magnetic Separation—Introduction to Chemical Cleaning Line,” Progress in Superconductivity and Cryogenics, 20.2, pp. 6–10.
3. Adey, C.; Downie, S. (Oct. 9, 2018).”Separator Device,” U.S. Patent No. 10,092,912.
4. Shibatani, S., et al. (2016). “Study on Magnetic Separation Device for Scale Removal from Feed-water in Thermal Power Plant,” IEEE Transactions on Applied Superconductivity, 26.4, pp. 1–4.
From the data presented above, it was evident that the iron present in the condensate sample was mainly magnetic in nature and therefore could be attracted by the magnets in the filter. The remaining nonmagnetic and dissolved iron levels were low in concentration and were treated by satellite feed of neutralizing amine. The filter that was used forces system water to pass through the central magnetic core, where iron oxide is drawn out by powerful magnetic rods.
The magnetic dirt filtration technology successfully removed more than 95% of the particulate magnetic iron oxide from the condensate return in a period of 60 days, which allowed the system to have lower iron levels and a low pressure drop.
5. Okada, H., et al. (2016). “Development of a Magnetic Separation System of Boiler Feedwater Scale in Thermal Power Plants,” IEEE Transactions on Applied Superconductivity, 26.3, pp. 1–5.
A The ADEY MagnaClean CommercialTM magnetic dirt filters were the filters referenced in the article.
Swati Sharma, Ph.D., completed her doctorate in environmental engineering from North Dakota State University, where she specialized in wastewater treatment and quality monitoring. Dr. Sharma has eight years of experience in industrial, municipal, and agricultural water/wastewater treatment using biological, physicochemical, and electrochemical methods. Currently working as research and analytics manager at Water Engineering Inc., Dr. Sharma is involved with in-house analytical laboratory management, chemical formulations, and technical consulting in industrial water and wastewater solutions. She may be contacted at ssharma@h2oeng.com
Laboratory testing of water treatment programs for scale and corrosion control are run and used for several purposes:
• To evaluate new inhibitors and treatments and predict field performance over a range of systems and operating parameters.
• To optimize treatments and determine the minimum effective dosage.
• To compare existing treatments to proposed treatments.
• To develop “technically accurate and appropriate” data for sales literature and promotion.
• To explore new areas, such as inhibitor interaction, with respect to synergy and antagonism.
Testing results should correlate well to field results under the same or similar conditions. This article discusses parameter selection and experimental test design. The goal is to avoid laboratory simulations that predict stellar results in a beaker but result in abject failure when applied in actual end user water systems.
On my (Robert Ferguson’s) first day at a new job with a major water treatment company in the early 1980s, a meeting was held to discuss discrepancies between minimum effective dosage in laboratory tests and dosages that actually worked in the field. The application under study was calcium carbonate scale control in high volume once-through condenser cooling systems. Dosages observed to prevent scale in the laboratory were approximately 3 to 10 times those found to work in the actual condenser cooling systems. A simple question resolved the dilemma:
Question: “What was the duration of the laboratory test, and what is the residence time where scale must be prevented in the condenser cooling systems?”
Answer: “Laboratory tests were run for 15 to 30 minutes, and the minimum dosage that prevented precipitation was noted. The condenser cooling system had a design residence time of 5.6 seconds.”
Developing and applying a “time” factor synchronized the dosages (1–3). The increase in dosage when time is increased from 6 seconds to 900 seconds has been found to be an increase of 240%. The increase from 6 seconds to 24 hours for the same inhibitor and conditions was calculated at 1,900%. Matching the residence time by which an inhibitor must prevent scale formation and growth is a critical parameter that can make or break correlations of laboratory dosages to those actually required in the field.
A popular test (4) for comparing inhibitor effectiveness against calcium carbonate scale is run at a high ionic strength from sodium chloride due to its origins as a test for oilfield brines. This test typically underestimates dosages for lower total dissolved solids (TDS) applications, such as cooling water.
This failure to correlate is due to the effect of ionic strength on scale potential, such as calcite saturation ratio, and on inhibitor effectiveness:
• As ionic strength increases, activity coefficients decrease, resulting in a decrease in driving forces for scale formation, such as calcite saturation ratio. The recommended dosage will decrease, typically as ionic strength increases, with all other parameters held constant (5). This effect is observed in the typical TDS range for commercial water treatment applications. At extreme TDS levels, activity coefficients actually increase as near effects gain control (6).
• As ionic strength increases, the dissociation constants for acid groups on inhibitors increase. This results in an increase in the percentage of an inhibitor in the active dissociated form. Lower dosages will then be recommended due to the higher percentage of active inhibitor under the higher TDS test condition than in the lower TDS field application (7).
In laboratory simulations, many tests start out in sparkling clean beakers or with new polished heat exchangers. Scale formation must then proceed in multi steps:
• Seed crystal formation
• Seed crystal attachment or growth and attachment
• Growth on the existing substrate
Each step is unique and requires a different inhibitor model (8).
The saturation ratio must exceed the “activation energy” to overcome the barrier between aqueous-phase clusters and the solid-phase crystals or amorphous solids.
Deposition: Once this barrier is crossed, seed crystals must grow to a size where they attach to the system, thus forming a substrate with active sites for growth on an existing substrate.
Growth: Precipitated scale serves as a substrate for growth by aqueous-scale-forming molecule clusters. A lower energy (saturation ratio driving force) is required for growth on an existing substrate.
These steps define the rule of thumb that “It is easier to keep a clean system clean than to keep a dirty system from getting dirtier.”
Laboratory simulations in clean beakers or equipment simulate the seed crystal formation stage. Some researchers jump over this step by adding seed crystals (9) or by adding steel wool to non-scale active sites.
Dosages from studies in “clean” beakers may recommend lower dosages than necessary for an operational “dirty” system.
Laboratory tests for corrosion inhibitors can be extremely misleading when run in clean, brand-new, shiny beakers with sandblasted coupons or pristine probes. The worst case of this phenomena as observed by the authors occurs with a neutral-to-slightly alkaline phosphate treatment with a new novel scale inhibitor thought to also have corrosion inhibitor properties. The combination provided superior results in the “sterile” laboratory environment.
Field results were disappointing for this approach. The effectiveness of this surface-active scale inhibitor was affected because it adsorbed on the system components, suspended solids, and other active sites. The inhibitor was also a nutritious “treat” for the field system microflora. Therefore, the fouled heat transfer surfaces required significantly higher inhibitor levels (phosphate) to inhibit corrosion under existing deposits.”
This failure to translate from beaker to operating system could have been prevented in many ways, one being an intermediate onsite pilot study.
Promotional literature and advertisements may include test results comparing an inhibitor to competitive products under conditions where no inhibitor works. For example, if inhibitors are known to fail at saturation ratios above 150, and inhibitors are compared at a saturation ratio of 300, none of them will typically ever provide adequate performance in an operational treatment program. Theis type of testing can also be misleading, but the results do not necessarily relate to the performance or limits to be expected in the operational system.
The degree of “failure” is represented in these tests as percent inhibition. Less than 100% inhibitions demonstrates less than complete control (Equation 1).
% Inhibition = 100% x (Ca initial – Ca final)/Ca initial Eq. 1
It is strongly recommended that tests of this type be avoided. Simulations should be conducted under conditions matching those of the actual operational system as closely as possible. Failure limits should be evaluated, and treatments not applied above their failure points (10, 11).
The pharmaceutical industry uses statistical models to extrapolate the equivalent of % inhibition to 100%. These, or similar algorithms, have been employed in an attempt to extrapolate dosages to 100%. This approach is not recommended, as it can result in extrapolations implying that scale control by an inhibitor is achievable above its failure point.
Pilot test units can come very close to duplicating an actual system. Onsite test units can use the same water source. In an ideal situation, laboratory tests might be run, and a preliminary dosage model developed (Step 1). In Step 2, dosages from the laboratory model will be evaluated on the pilot unit. Optimum dosage results will then be verified on the operating commercial system for Step 3. This sequence was used in the development and field verification of the first utility once-through cooling system ultra-low dosage models (2, 3, 12, 13).
Similar approaches and development sequences have proven successful in modeling open recirculating cooling water systems (14). The sequence for cooling tower systems might include laboratory screening tests and preliminary models, laboratory pilot units that vary from circulators to pilot cooling towers, pilot cooling systems in the field using the same makeup source, and verification through implementation on the operating system.
Care should be taken when shipping water to a laboratory pilot unit. The pH and carbonic equilibrium will shift. Microbial activity can further deteriorate and change the sample. Metals such as iron will not be reliable after shipping, and silica might become altered or adsorbed.
A key to successful laboratory and pilot testing is determining and matching critical parameters such as:
• Residence time.
• Shear force against the tube wall.
• Temperature, including low end if scale control follows normal solubility, like barite.
• Active sites for growth on an existing substrate.
It is important to evaluate obvious parameters and match those relevant to your application.
The ultimate test for treatment is performance in the operating system. Establishing criteria for success is paramount in the final evaluation. Many evaluations have a success criteria of clean heat transfer surfaces (and/or other system components) upon physical inspection. Others have a criteria of no following factor increase (or, in the case of utility surface condensers, decrease in cleanliness factor).during the field evaluation.
Systems that operate by necessity under conditions where no treatment will provide maintenance of cleanliness and/or heat transfer might have a success criteria of an extended run between cleanings. Success criteria might also include improved cleanliness, as was the case with the first successful field biodispersant trials.
Inhibitor synthesizers and water treatment service companies and formulators have long claimed (or at least alluded to) synergistic formulations, which include the following:
• Synergy would be demonstrated if a blend of inhibitors had a higher failure point than either inhibitor applied as the sole inhibitor.
• If a blend of inhibitors performed better when either inhibitor was applied as the sole inhibitor, this would be demonstrated if induction time extension by the blend was greater than that expected for either inhibitor at the dosage.
The antithesis of “formulating for synergy” is “formulating for antagonism.” Here are two examples:
• If a blend of inhibitors had a lower failure point than either inhibitor applied as the sole inhibitor, antagonism would be demonstrated.
• If a blend of inhibitors provided poorer performance when either inhibitor was applied as the sole inhibitor, antagonism would be present. This would be demonstrated if the induction time extension by the blend was less than that expected for either inhibitor at the dosage.
Synergy and antagonism, and test methods for determining their presence, are discussed in References 15 and 16.
Laboratory tests for selecting and optimizing treatments for field applications should incorporate test parameters as close to those of the field as possible. Results of laboratory simulations should be correlated and synchronized to actual field performance. If the parameter causing a poor correlation is not apparent, evaluate mechanisms (e.g., initial seed formation, growth on an existing substrate) and independent parameters (e.g., time) to determine the missing variable. The tests should be adapted to reflect the impact of the missing parameter.
Evaluations should incorporate laboratory simulations, pilot evaluations, and onsite verification where possible. Onsite pilot evaluations are preferred when feasible.
“A popular test for comparing inhibitor effectiveness against calcium carbonate scale is run at a high ionic strength from sodium chloride due to its origins as a test for oilfield brines.”
1. Ferguson, R.J. (November 1992). “Developing Scale Inhibitor Models,” presentation at WaterTech ’92, Houston, Texas.
2. Ferguson, B.W.; Ferguson, R.J. (1981). “Side Stream Evaluation of Fouling Factors in a Utility Surface Condenser,” Journal of the Cooling Tower Institute, 2, pp. 31‐39.
3. Ferguson, R.J. (2003). “30 Years of Ultra-Low Dosage Scale Control,” Corrosion 2003, San Diego, California.
4. NACE (2016). “ Laboratory Screening Tests to Determine the Ability of Scale Inhibitors to Prevent the Precipitation of Calcium Sulfate and Calcium Carbonate from Solution (for Oil and Gas Production Systems),” Test: NACE TM0374-2016-SG, National Association of Corrosion Engineers, Houston, Texas.
5. Ferguson, R.J. (Nov. 13–17, 2011). ”Mineral Scale Prediction and Control at Extreme TDS,” Paper No. IWC-11-77, International Water Conference, Orlando, Florida.
6. Ferguson, R.J. (November 2020). “Modelling Mineral Scale Precipitation Mass in Industrial Systems,” Paper No. IWC-20-73, International Water Conference, Virtual Annual Conference.
7. Ferguson, R.J. (Feb. 9–12, 2015). “The Impact of Inhibitor Speciation on Efficacy: pH, Ionic Strength and Temperature Impact,” Presented at the 2015 Cooling Technology Institute Annual Conference, New Orleans, Louisiana.
8. Ferguson, R.J. (2011). ”The Kinetics of Cooling Water Scale Formation and Control,” annual AWT Conference, Association of Water Technologies, Rockville, Maryland.
9. Gill, J.S.; Anderson, C.D.; Varsanik, R.G. (Oct. 24–26, 1983). “Mechanism of Scale Inhibition by Phosphonates,” Paper No. IWC 83-4, International Water Conference, Pittsburgh, Pennsylvania.
10. Ferguson, R.J.; Standish, C. (September 2017). “Developing Realistic Scale Inhibitor Test Procedures: Calcium Carbonate Scale Inhibitor Testing,” annual AWT Conference, Grand Rapids, Michigan, Association of Water Technologies, Rockville, Maryland.
11. Ferguson, R.J. (Aug. 18, 2020). “Interpreting Indices in Context and Setting Limits,” French Creek Software Lock-down Webinar Series, (https://vimeo. com/451309283).
12. Ferguson, R.J.; Smas, M.J. (Oct. 25–27, 1981). “Practical Application of Condenser System Performance Monitoring to Water Treatment Decision Making,” Paper No. IWC 81-25, International Water Conference, Pittsburgh, Pennsylvania.
13. Ferguson, R.J.; Codina, O.; Rule, W.; Baebel, R. (Oct. 24–26, 1988). “Real Time Control of Scale Inhibitor Feed Rate,” International Water Conference, Pittsburgh, Pennsylvania.
14. Bross, B.; Ferguson, R.J. (2012) “Pilot Cooling System Evaluation of Treatment Program Effectiveness in a Refinery Environment,” Paper No. 2012, CTI Annual Conference, Cooling Technology Institute, Houston, Texas.
15. Ferguson, R.J.; Standish, C. (2016). “Modeling Scale Inhibitor Blends: In Search of Synergy,” AWT Annual Convention & Exposition, San Diego, California, Association of Water Technologies, Rockville, Maryland.
16. Ferguson, R.J.; Standish, C. (September 2018). “Modeling Scale Inhibitor Upper Limits: In Search of Synergy,” AWT Annual Convention & Exposition, Association of Water Technologies.
Robert J. Ferguson is the president of French Creek Software, Inc., a company he co-founded in 1989. His professional career includes positions with Nalco, Apollo, Mogul, Calgon, Chemlink, and Baker. Mr. Ferguson began modeling mineral scale formation and its control in 1974. Software he has developed is used for modeling cooling water, reverse osmosis, and oilfield chemistry. He is proud to be a Ray Baum Water Technologist of the Year honoree, the first AWT Innovation Award honoree, the first Process Cooling Innovation Award recipient, and a Ben Franklin Technology Center Innovation award winner. Mr. Ferguson was educated at the U.S. Naval Academy and the University of Minnesota and received a B.S. in biochemistry and microbiology. Mr. Ferguson can be reached at robferguson@frenchcreeksoftware.com
John Zibrida is the president of ZIBEX, Inc. He has been a member of AWT for more than 30 years and has over 40 years of experience in the chemical and environmental industries. Mr. Zibrida has authored several papers at NACE International and AWT. He also chaired the water treatment committee of CTI and was AWT Boiler Subcommittee chair. He holds a bachelor’s degree in chemistry from Florida State University and an MBA from Emory University. Mr. Zibrida studied chemical engineering at the University of South Florida and the Colorado School of Mines. He can be contacted at jfzibrida@cs.com
This paper was presented at the AWT’s Annual Convention & Exposition, which was conducted September 22–25, 2021, in Providence, Rhode Island.