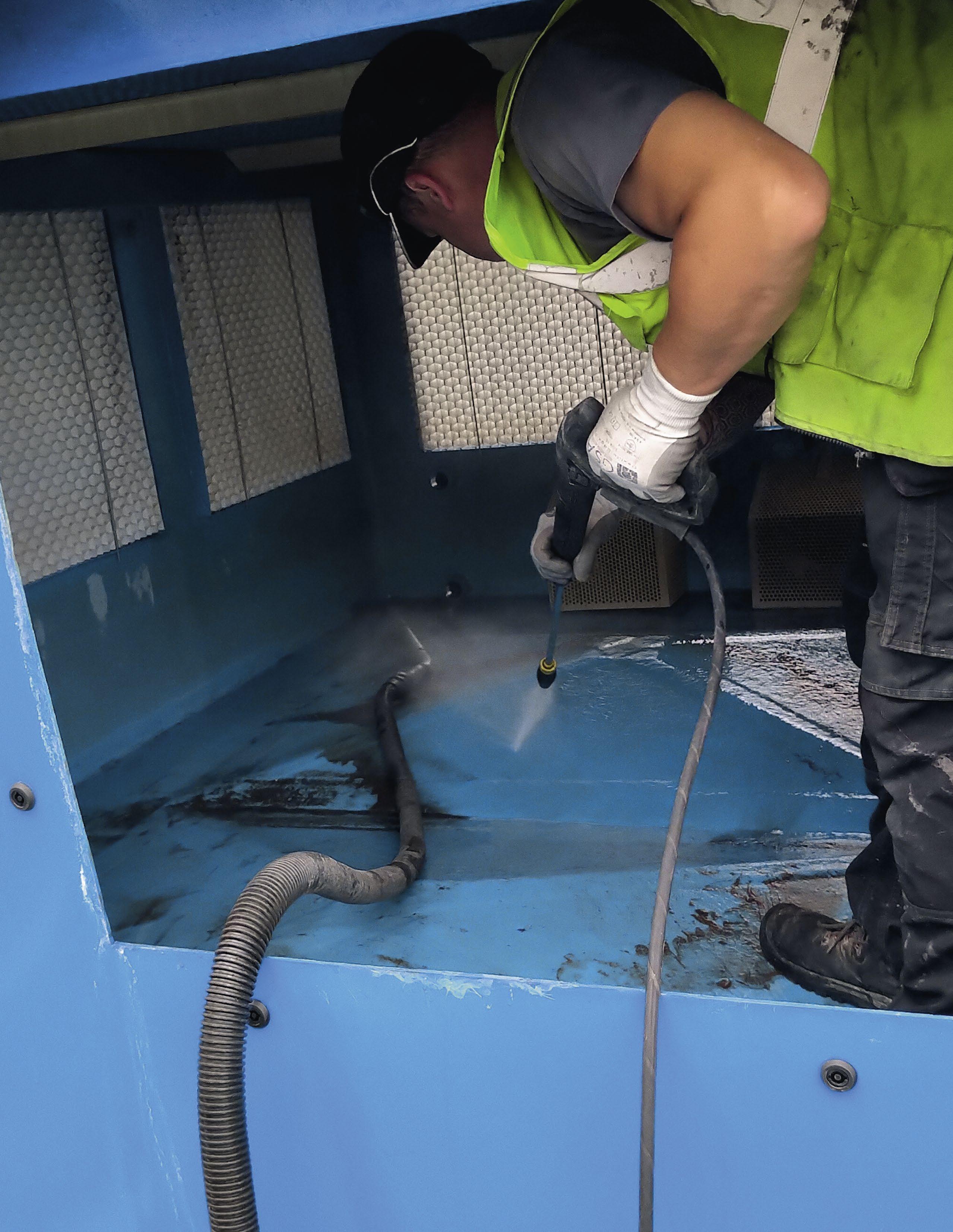
17 minute read
AWT Cooling Tower Cleaning and Disinfection Guidance
AWT Cooling Subcommittee
(Editor’s note: This article is based on new guidance procedures recently developed by the AWT Cooling Water Subcommittee.)
Standard Operating Procedures for Cleaning Cooling Towers
1. What is the purpose of cleaning and disinfection procedures? a. Maintaining the cleanliness of the cooling tower system and the cooling water in it is critical for preventing or controlling the risk of exposure to Legionella. This paper provides proven, professional guidance on how to effectively and safely clean and disinfect a cooling tower system.
b. It is the job of the building owner and their responsible manager to make the decisions as to whether the cooling water system is clean enough for operation as well as the frequency and scope of inspection and the need for system cleaning. For such decisions, they may seek advice and help from specialist service providers for water treatment, risk assessment, cleaning, and disinfection.
c. In all cases, local conditions and local regulations must be considered and followed when designing the procedures for inspecting and cleaning the cooling system.
2. Why is it important to clean and disinfect the cooling system? a. Legionella are more likely to proliferate in water systems that contain sediment, deposits, and biofilm, which can protect the organisms from water treatments that are used to control microbiological growth. Sediments and deposits also provide nutrients that accelerate growth and lead to multiplication of bacteria counts. Maintaining system cleanliness is crucial to reducing cooling tower hygiene risks.
b. Effective water treatment measures can reduce the rate at which a cooling system becomes fouled. However, an evaporative cooling system will inevitably accumulate airborne debris, dust, and other particulate matter from the atmosphere and may be subject to contamination originating from the process for which the system provides cooling. It is therefore necessary to take cooling systems out of service periodically for physical, and possibly chemical, cleaning to remove this fouling.
3. How can we protect workers? a. As a good practice to ensure worker safety, employers should provide appropriate personal protective equipment (PPE) and demand its use when workers perform any routine maintenance, cleaning, or disinfection activities on water systems that may be contaminated with Legionella. This includes work on hot and cold domestic water systems; cooling towers; and heating, ventilation, and air conditioning (HVAC) equipment. If Legionella contamination is possible but a Legionellosis outbreak is not known or suspected, use respirators. The U.S. Occupational Safety and Health Administration (OSHA) prescribes the following criteria as found in the OSHA document Legionellosis (Legionnaires’ Disease and Pontiac Fever, which is available at https://www. osha.gov/legionnaires-disease/control-prevention):
• When inspecting a cooling tower or taking water samples (i.e., for a short time exposure to tower vapor), use a National Institute for Occupational Safety and
Health-approved respirator at least as protective as an
N95 respirator. N95 refers to particulate masks that have 95% efficiency in removing 0.3-micron (µm) particles.
• When working with biocides to clean and disinfect systems, use eye protection (chemical goggles or face shield with safety glasses), protective gloves, and suitable protective clothing, as recommended by the biocide manufacturer.
• Workers engaged in tower cleaning must wear, at a minimum, the PPE required for any chemicals being used, and a half-face air-purifying respirator equipped with an N100 cartridge.
• Ensure that the selection of respiratory protection considers the agents used for decontamination, and provide combination cartridge respirators where both particulate and chemical hazards may be present.
If organic vapor cartridges are used, implement a cartridge change schedule.
• Tasks that involve an increase in moisture and spray, including cleaning and decontamination activities, may adversely affect N100 cartridge respirators. In such instances, consider providing a supplied-air respirator to improve worker protection. A loose-fitting powered air-purifying respirator or supplied-air respirator may also improve worker comfort when wearing respirators for long periods.
• Just as for worksites with mandatory use of respirators, employers who permit voluntary use of respirators
must implement a respiratory protection program that complies with the applicable provisions of OSHA’s Respiratory Protection standard (29 CFR 1910.134). This includes compliance with the standard’s requirements for obtaining medical clearance for wearing the respirator and for conducting fit testing prior to actual use of respirators and must comply with the provisions set forth in the standard’s Appendix D (Mandatory) – Information for Employees Using Respirators When Not Required Under the Standard.
b. During known or suspected outbreaks:
• In the event of a known (i.e., identified) or suspected
Legionellosis outbreak, workers who may be exposed to aerosolized Legionella must wear respirators. For most exposures, respirators should be equipped with N100 filters or a similar type of filter media capable of effectively collecting particles in the 1-micron size range.
Examples of workers with potential exposure include those examining the affected water system, conducting disinfection activities on the system, or performing other essential tasks in areas near contaminated cooling towers or serviced by contaminated HVAC units.
• The employer should always conduct a hazard analysis to determine which workers are at risk of exposure and identify any additional hazards that may be present and the appropriate measures to control worker exposures.
• PPE provided to workers (including respirators and other clothing or gear) must be selected in accordance with OSHA’s PPE standards (29 CFR 1910 Subpart I).
• Hand protection (i.e., gloves) must be selected based on the material (e.g., nitrile, vinyl) compatible with any chemical exposure. Selection should also consider the other characteristics of the glove, such as fit, durability, and comfort. If necessary, use the vinyl or nitrile gloves under heavier (e.g., rubber, leather, heavy cotton) gloves for operations with potential for glove tearing or for protection against hand injury.
• Replace disposable gloves as soon as possible when contaminated, cracked, torn, or punctured and upon task completion.
• Remove gloves prior to leaving the work area and place them in areas specifically designated for storage, washing, decontamination, or, for disposable or damaged reusable gloves, disposal.
• Thoroughly wash hands with soap and water upon removing gloves, before eating, and when replacing torn or worn gloves. • Required PPE, except for most protective footwear, must be provided at no cost to the worker, readily accessible to workers, and available in appropriate sizes.
Cleaning and Disinfection Procedure
A cooling tower system cleaning operation will normally comprise a precleaning disinfection; a physical cleaning, and, if appropriate, chemical cleaning; and a post-cleaning disinfection.
1. Precleaning disinfection a. Before cleaning the system, the cooling water should be disinfected using an oxidizing biocide such as chlorine, bromine, or chlorine dioxide in conjunction with a suitable biodispersant. This is to minimize health risks to the cleaning staff and surrounding building occupants.
b. Based on product and dosage recommendations of the water treatment supplier or specialist service provider, the biodispersant should be added 30 minutes before the addition of the chosen disinfectant chemical. The biodispersant should be circulated throughout the cooling water system via normal cooling tower operation, to ensure that the bio dispersant reaches all wetted surfaces.
Caution: The dispersant must not be a surfactant because the cooling tower manufacturers have discovered that surfactants and certain wetting agents can impede the efficiency of highefficiency drift eliminators (where installed), thereby rendering them ineffective and causing the cooling tower fans (on mechanical draft cooling towers) to carry Legionella-containing droplets a significant distance away from the cooling towers.
c. The required concentration of the free disinfectant as recommended by the product manufacturer should be established and circulated throughout the cooling tower system. Manufacturer’s recommendations for the required time should be followed. If there are no instructions, then a continuous minimum residual of 5 milligrams per liter (mg/L) as free chlorine for a minimum of five hours should be maintained. If the time available to conduct the operation is limited, using a higher disinfectant concentration for a shorter time may be acceptable. This will, however, increase the risk of damage to the materials of construction of the cooling water system. Excessive disinfectant levels should be avoided.
d. The disinfecting solution is to be monitored periodically and maintained in the cooling tower system throughout the disinfection period by adding more disinfectant as required.
The normal disinfectant level required depends on the minimum circulation period adopted. Table 1 provides the minimum contact times in disinfectant levels.

Table 1: Recommended Minimum Disinfectant Level for Different Circulation Times
Minimum Circulation Time
5 Hours
2 Hours
1 Hours
Minimum Continuous Disinfectant Level (as free Cl2)
5 mg/L 25 mg/L 50 mg/L
*Health and Safety Executive (Great Britain) Page 35, Table 1.6 https://www.hse.gov.uk/pubns/priced/hsg274part1.pdf
e. The recommended disinfectant residual needs to be established throughout the whole system for the contact time and not simply the cooling tower sump. Systems with multiple sumps may require additional dosing to ensure good distribution of disinfectant.
f. Initially, the cooling tower fan(s) are switched off until the disinfectant is mixed throughout the system. Rotate offline equipment (e.g., offline chillers, plate-and-frame heat exchangers, condenser water pumps) so that the disinfectant reaches all parts of the associated condenser water system. Once this is achieved, the fan(s) should be switched on for the remainder of the process to ensure that the disinfectant reaches all internal surfaces that become wet during normal operation of the tower, and which potentially could be contaminated. g. If chlorine is used as a disinfectant, its efficacy is reduced if the system pH value is greater than pH 8. To achieve the same disinfection effect, its residual needs to be increased 3 to 4 times (i.e., in place of 5 mg/L for five hours, 15 to 20 mg/L is required for the same period). Generally, this is not recommended, so if the system water is above pH 8, adopt one of the following procedures to compensate, without increasing the chlorine residual:
• Introduce a heavy bleed off for several hours to reduce both rthe pH of the system water and its chlorine demand before carrying out disinfection.
• Reduce system pH by adding an alkalinity reduction chemical.
• Augment the chlorine dosage with enough sodium bromide to change the disinfectant from chlorine to bromine.
h. If bromine or chlorine dioxide is used in systems where the pH is above 8, the reserves do not need to be increased and the pH does not need to be adjusted, as these disinfectants remain effective at higher pH levels.
i. Once the system has been predisinfected, the water should then be dechlorinated and drained. Dechlorination can be accomplished using a dechlorinating agent, such as sodium bisulfite.
2. Cleaning the сooling tower a. After precleaning disinfection, manual cleaning operations can be carried out with all accessible areas of the tower being cleaned. Accessible areas of the system should be washed adequately, but cleaning methods that create excessive spray (e.g., high-pressure water jetting) should be avoided.
b. If considered necessary, high-pressure jetting should only be carried out when the buildings nearby are unoccupied or, in the case of permanently occupied nearby buildings, windows should be closed, air inlets blanked off, and the area that is being water jetted should be tented. The area should be isolated, and consideration of other occupied premises nearby, as well as people who may be nearby during cleaning, should be taken.
c. It is important to check with cooling tower manufacturer representatives, or the cooling tower Operations & Maintenance manual regarding recommended cooling tower cleaning procedures. For example, some cooling towers have specially designed fill packs and/or fill removal systems. Failure to properly follow guidance can result in damage to the fill pack or fill removal systems. This would lead to channeling of cooling water and subsequent reduced thermal performance. In addition, some cooling tower fill packs have limitations on the pressure of water jetting. Too high of a pressure can damage the fill pack and lead to water channeling, reduced thermal performance, and ultimately, premature failure of the fill pack, increasing customer maintenance costs.
d. Should it be determined prior to cleaning that the fill pack is in poor condition or cannot be cleaned physically, it is recommended that the old fill pack be replaced with new fill pack during this process. This needs to be planned in order to have sufficient time for the new fill pack to be ordered and placed onsite. Otherwise, time will be lost, and negative operational impact could result.
e. Cleaning staff that carry out water jetting or other operations that could create aerosols should wear suitable respiratory protective equipment (RPE) as described above, and the cleaning contractor in the method statement should specify this. Staff using this equipment should be adequately trained and the equipment properly maintained.
Further guidance on why and when RPE should be used and how to select RPE that is adequate and suitable should be investigated by the cleaning staff and their managers.
f. In addition to the manual cleaning operations, enhanced chemical cleaning processes may be required to remove certain types of deposit. Table 2 gives guidance on cleaning processes that can be employed for different types of fouling. Once clean, the system should be drained and flushed with clean water until the water going to the drain is clear. Cleaning staff should be aware of local discharge requirements.

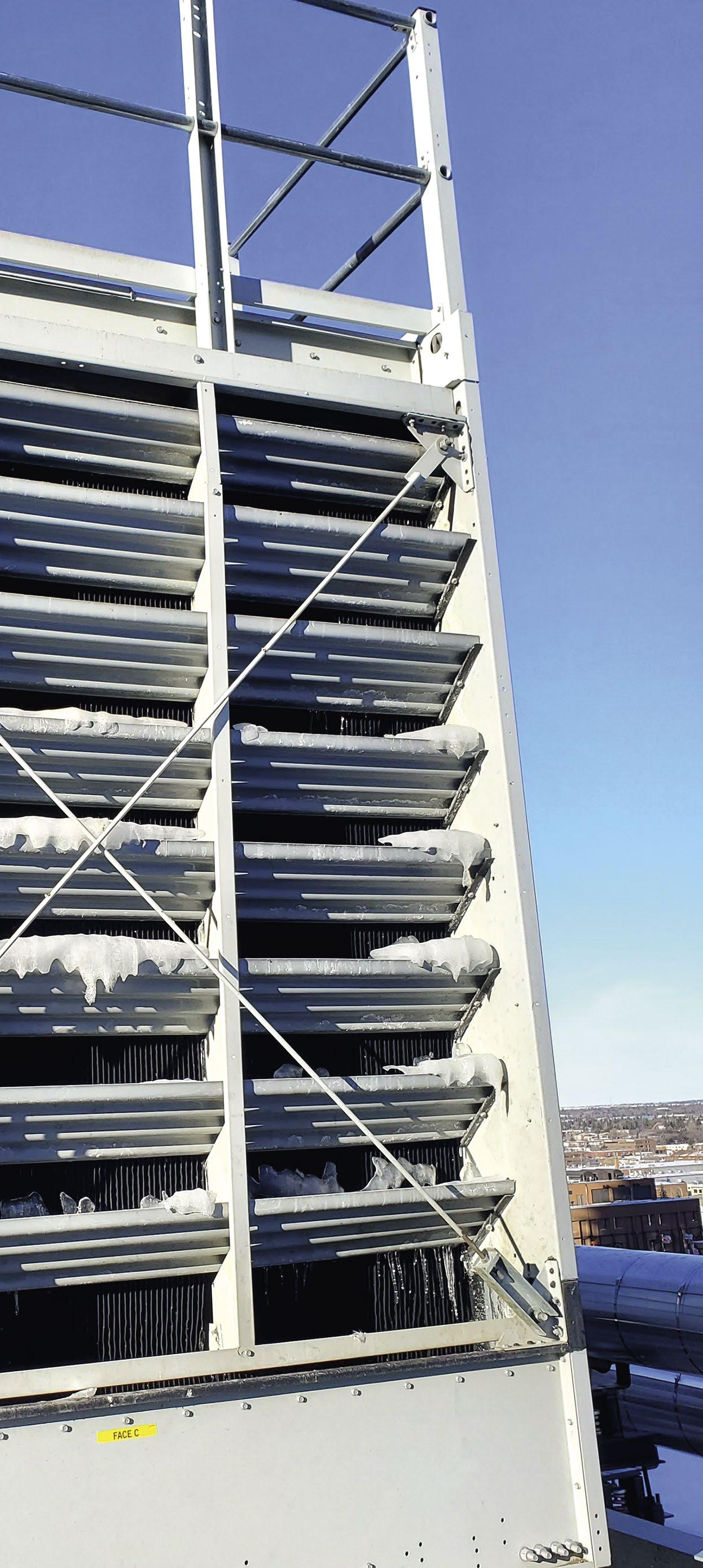
Table 2: Cleaning Processes for Different Types of Fouling
Type of Fouling
Silt, sediment, and airborne dust
Biofouling
Hardness scale
Corrosion products
Organic process contaminants
Cleaning Procedure
Physical removal with shovels, a wet vac, or similar method. Post-disinfect to ensure that any microbial fouling released is killed. Strong oxidizing biocide combined with biodispersant and circulated with fans off and heavy purge. Shut system down and drain all sumps. Check cleanliness of strainers, heat exchangers, and fill pack. Acid clean using appropriate acid and inhibitor. If cleaning proves to be ineffective, consideration should be given to replacing heavily scaled fill pack. Acid clean using the appropriate acid and inhibitor or suitable chelant/dispersant. Identify the contaminant and select an appropriate solvent/dispersant.
3. Cleaning the cooling tower fill pack a. Maintaining the cleanliness of the cooling tower system and the water in it is critical for preventing or controlling the risk of exposure to Legionella; it is therefore necessary to demonstrate the cleanliness of the system, including the fill pack, whether the fill pack is removed or not. The approach to cleaning the cooling tower fill pack will depend on several factors, including:
• The nature of the contamination
• The design of the cooling tower and practicalities of accessing and/or removing the fill pack
• The type of fill pack in use (i.e., block or sheet)
b. If the cooling system operates in a relatively clean environment with continuous effective water treatment, it is possible for a cooling tower fill pack to remain free from fouling for several years. However, a fill pack may appear clean from the visible surfaces but be fouled internally.
c. Removal of the cooling tower fill pack, where this can be done relatively easily and reinstated safely without damage, will improve the inspection and assessment and aid any potential cleaning.
d. Whether the fill pack is removed or not, evidence of its cleanliness should be demonstrated and assessment made using appropriate techniques, as detailed in Table 3, and the findings recorded. Photographic records of fill pack condition can help in the process and should be maintained.
e. Sheet fill pack can also be separated to allow silt or sediment to be washed off. Block-type fill pack cannot be cleaned effectively by jetting but may respond to flushing with high volumes of water or cleaning fluid. If a chemical process is
required to remove fouling, this may be done most conveniently in situ by circulating a concentrated cleaning solution through the pack. Application of a suitable cleaning solution may remove light deposits. Alternatively, the fill pack can be removed and immersed in a suitable cleaning solution. In some circumstances, it may be possible to remove certain deposits by removing the back, allowing it to dry out and then gently knocking or dropping it from a low height to shock the dry deposits off, taking care not to damage the fill pack itself.
f. When the fill pack or drift eliminators are heavily found and cleaning is not practical, consider replacing them.
It may be prudent to hold sections of new pack and drift eliminators on site for use during system cleaning operations. It is important that replacement pack and drift eliminator match or have the same dimensions and performance as the original to maintain proper water/ air flow balance. Improper water/air flow balance can negatively impact cooling efficiency and increase the volume of drift and aerosol release from the system.
4. Post-Cleaning Disinfection a. Upon completing the cleaning operation, the system should be refilled and disinfected using the method described under “pre-cleaning disinfection,” using an oxidizing biocide to maintain the minimum disinfectant levels and circulation times indicated in Table 1. The disinfectant levels should be monitored periodically and maintained to ensure that the minimum levels are present. The use of a bio dispersant will enhance the effectiveness of this disinfection. This should be done following the same process as outlined in prior Section 1b.
Caution: The dispersant must not be a surfactant because the cooling tower manufacturers have discovered that surfactants and certain wetting agents can impede the efficiency of highefficiency drift eliminators (where installed), thereby rendering them ineffective, thus causing the cooling tower fans (on mechanical draft cooling towers) to carry Legionella-containing droplets a significant distance away from the cooling towers.
b. If returning the system to immediate service, the disinfectant level can be allowed to decay over the first few hours of operation and a startup level of the normal water treatment chemicals added. If, however, the system is going to be left idle before restarting, dechlorinate the water, drain and flush the system, and leave it empty. On startup, the system should be refilled with fresh water, and the water treatment program should immediately be reinstated with a dosage of the appropriate startup level of treatment chemicals, including biocide.
c. Before water containing high residuals of chlorine, bromine, and chlorine dioxide is discharged to the drain, neutralize the disinfectant. The usual procedure is to add sodium bisulfite as a neutralizer. The effluent from any disinfection and/or chemical cleaning process, neutralized or not, may require a “consent to discharge.” Therefore, permission to discharge may be required from the effluent receiver.
Collaborating Authors of Guidance Document
Derrick Vandenberg obtained his bachelor’s degree in chemistry in the late 1980s. In 2002, he joined Guardian Chemicals Inc. to sell to and serve the water treatment industry. He obtained his CWT 15 years ago. He now serves as technical director for Guardian Chemicals as well as managing a large customer territory in the Great White North.
Vance D. Fiegel is a cell and microbiologist, inventor, and entrepreneur. He began his career at the University of Minnesota, where he studied the basic biology of inflammation and wound healing. Leaving the university 30 years ago, he has co-founded numerous ventures and is currently the chief science & technology officer at Creative Water Solutions, LLC and Atlantic BioVentures, LLC. He has published more than 60 research articles and holds over 25 U.S. and foreign patents.
Robert Downey is a global water treatment specialist for Baltimore Aircoi (BAC)l. In the years prior to joining BAC, he worked at Phigenics, a water management and hygiene consultancy. Before Phigenics, Mr. Downey enjoyed a 22-year career at Nalco Water in various sales and sales management roles. In his current role at BAC, he helps customers with expertise and advice to help them manage their evaporative cooling needs, with particular focus on water quality, usage, treatment, and hygiene issues.
Thomas Mercer, CWT, has served on both the Cooling Water Technical Subcommittee and the Education Committee during his membership at AWT. He has been with DuBois Chemicals for his entire 38-year career. At DuBois, Mr. Mercer is currently the technical specialist for the eastern United States. He has held several roles at DuBois, including developing water treatment products for cleaning, treating, and descaling cooling towers, boilers, and closed loops. Mr. Mercer has also developed and presented water and wastewater training programs for both customers and DuBois personnel. In recent years, he was in the first class to be certified in the Certified Legionella Water Safety & Management Professional ASSE/IAPMO/ANSI 12080 program. Mr. Mercer’s work has also included training and presentations to outside organizations such as ASHRAE, Healthcare Engineers, and others.