
7 minute read
INYECCIÓN
INCREMENTE SU PRODUCTIVIDAD
CON UN TORNILLO DE BARRERA
Un caso de éxito demuestra cómo reemplazar el tornillo de propósito general en inyección puede reducir el tiempo de ciclo.
POR AJA LANG, INGENIERA DE APLICACIONES, NORDSON XALOY
En el moldeo por inyección, la penalización por usar un tornillo de uso general en una aplicación que tiene requisitos especiales a menudo consiste en tiempos de ciclo más largos. Este es particularmente el caso en producción de embalajes y otras aplicaciones en las que es esencial un alto rendimiento, o en piezas de pared delgada.
Para un cliente de Nordson Corporation que produce piezas grandes de pared delgada, el cambio de un tornillo estándar a un tornillo Xaloy de diseño personalizado ha resuelto un problema de tiempo del ciclo, aumentando la productividad y la rentabilidad.
En una de sus fábricas de América del
Norte, este cliente estaba usando un tornillo de uso general para procesar polietileno de alta densidad (PEAD) 100 % reciclado en una máquina de Ube de 1.000 toneladas.
El gramaje de inyección era de 3.750 g. Su problema consistía en que la fase de recuperación del tornillo era demasiado larga.
Era un problema muy común en el moldeo por inyección, que a menudo implicaba el procesamiento de polipropileno (PP) o
PEAD virgen o reciclado.
El tiempo de recuperación es el tiempo que tarda el tornillo en girar nuevamente a su posición establecida. Se lleva a cabo durante la fase de enfriamiento. Una regla general común es que el tiempo de recuperación debe ser de 1 o 2 segundos menos que el tiempo de enfriamiento establecido.
Si el tiempo de recuperación excede este tiempo de enfriamiento, el ciclo general de la máquina aumenta.
Nordson diseña tornillos personalizados para ayudar con los problemas de recuperación. El tornillo de barrera Xaloy MeltPro, por ejemplo, funde de manera más eficiente que un tornillo de propósito general. Al tiempo que reduce el tiempo de recuperación, el tornillo MeltPro puede producir una temperatura de fundición más baja y reduce la necesidad de contrapresión.
El cliente informó mejoras significativas desde que usó el tornillo MeltPro. Se redujo el tiempo de recuperación, lo que permitió reducir el tiempo de enfriamiento y disminuir el tiempo del ciclo en un 12 %. Como resultado, el rendimiento aumentó en un 14 %, al pasar de 1.041 a 1.184 partes por día.
CÓMO FUNCIONA
Un tornillo estándar puede presentar dificultades en aplicaciones que requieren alto rendimiento, porque tiene una eficiencia de fusión limitada y puede generar altas temperaturas de fundido, lo que a su vez prolonga el tiempo de enfriamiento. En la zona de transición o compresión, la disminución en la profundidad del canal aumenta la velocidad de corte y agrega calor al polímero fundido. Posteriormente, la fusión eficiente de sólidos contra el barril calentado se detiene, y hay una ruptura en el fondo de sólidos en el canal del tornillo. Los materiales no fundidos
restantes se distribuyen por todo el canal del tornillo, como cubitos de hielo en agua. El resultado es un proceso de fusión menos eficiente. Además, el calentamiento de la masa fundida continúa en la sección de dosificación menos profunda del tornillo. El polímero que finalmente se inyecta en el molde desde un tornillo estándar puede contener gránulos no fundidos o presentar variaciones de temperatura o viscosidad. El resultado son propiedades y mezcla de colores deficientes. Es posible lograr una mayor mezcla utilizando un tornillo con una profundidad de canal reducida, pero esto se hace a expensas del sobrecalentamiento y un rendimiento reducido, ya que el volumen de resina transportado por revolución del tornillo es menor.
La razón principal para usar un tornillo de barrera en lugar de un tornillo estándar es evitar la ruptura del fondo de sólidos y proporcionar un proceso de fundición más eficiente. Hay varios diseños de tornillos de barrera disponibles. Para este cliente, Nordson recomendó el tornillo MeltPro ya que logra el mayor rendimiento en comparación con otros tornillos de barrera, al tiempo que exhibe baja temperatura de fundido y alta eficiencia de fusión, además de requerir una contrapresión mínima.
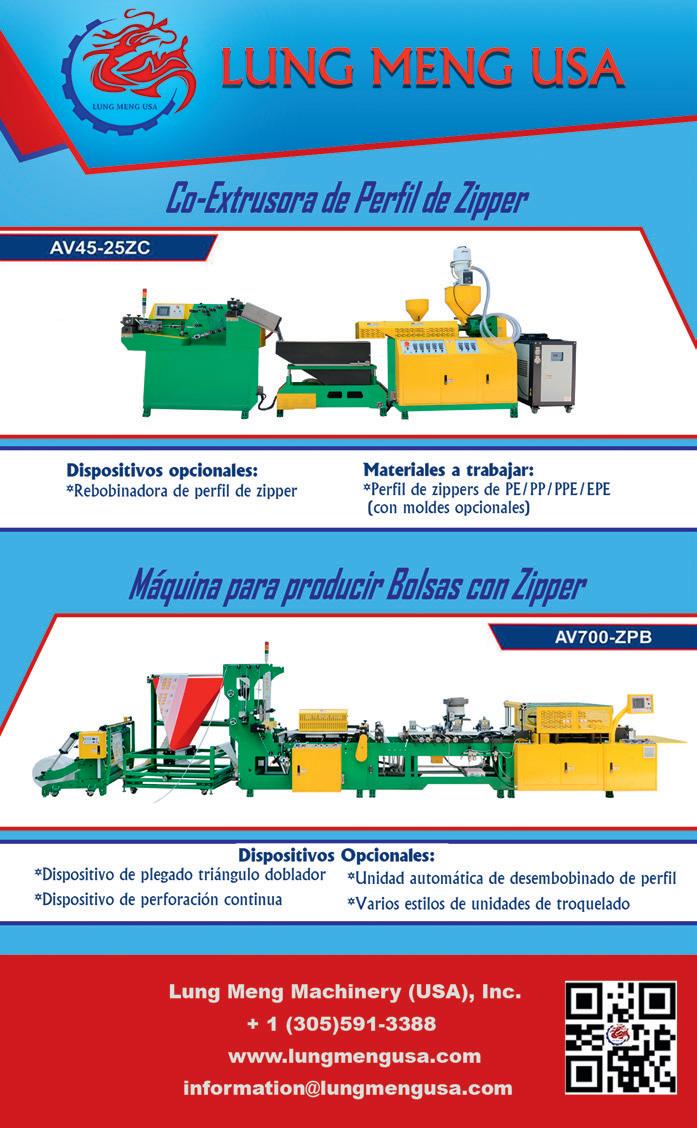
En un tornillo MeltPro, al comienzo de la zona de transición (compresión) se inicia un segundo tramo. Este tramo se llama barrera o tramo intermedio y separa el canal de sólidos del canal de fundido. A medida que el material avanza por la zona de transición, la fusión continúa. El tramo de barrera se mueve debajo de la película de fundido y la misma se recoge en el canal de fusión. De esta manera, los gránulos sólidos y el polímero fundido se separan y se realizan diferentes funciones en cada uno.
El diseño adecuado del tornillo es a menudo la clave para optimizar un proceso de inyección. Los tornillos estándar o de uso general proporcionan una plastificación adecuada en muchas aplicaciones. En aplicaciones más desafiantes, hay una amplia gama de diseños de barrera y tornillos de mezcla disponible para cumplir con los requisitos específicos de moldeo por inyección. TP
UNA EMPRESA DE INYECCIÓN FRENTE AL COVID-19
El fabricante Iprocom S.A. tuvo que parar durante el cierre industrial generado por la emergencia sanitaria y Juan Carlos Zuleta, fundador y presidente, nos comparte su experiencia.
JUAN CARLOS ZULETA
TECNOLOGÍA DEL PLÁSTICO: ¿Cómo se ha visto impactado Iprocom con la coyuntura del Covid-19? JUAN CARLOS ZULETA: Iprocom es un fabricante colombiano de componentes plásticos de alto desempeño para empresas que pertenecen a diferentes sectores y encadenamientos productivos, como ensambladores de motos, automóviles y electrodomésticos, empresas de la construcción, entre otros. Con las medidas de aislamiento obligatorio implementadas por el Gobierno para reducir la tasa de contagio del Covid-19, todos los sectores económicos se han visto afectados de alguna manera e Iprocom no ha sido la excepción, dado que nuestros productos no fueron catalogados como básicos y debimos suspender nuestras operaciones, al igual que nuestros clientes. Estamos haciendo un esfuerzo muy grande para proteger los puestos de trabajo porque, hoy más que nunca, tenemos que ser socialmente responsables, no sólo con nuestros colaboradores sino también con las familias que dependen de ellos. Tenemos claro que estamos ante una crisis sin precedentes para la que no estábamos

preparados y que los auxilios del Gobierno no son suficientes ni se van a mantener indefinidamente, y por esta razón es necesario que la economía se vaya reactivando de manera progresiva, al mismo tiempo que se cuida la salud de las personas.
TP: ¿Qué medidas está tomando Iprocom para implementar protocolos de bioseguridad y cómo están impactando esas medidas la productividad? JCZ: Hace unas semanas, el Gobierno acertadamente autorizó el reinicio de actividades de dos sectores muy importantes para la economía del país como la manufactura y la construcción, siempre y cuando las empresas implementen los estrictos protocolos de bioseguridad definidos por el Ministerio de Salud. En Iprocom pudimos reanudar operaciones hace pocas semanas gracias a la agilidad y a la disciplina con que implementamos los protocolos de bioseguridad, trabajando de la mano con las autoridades municipales y sus entidades de control, con nuestro equipo de brigadistas y con el compromiso de todos nuestros colaboradores. Dentro de las medidas adoptadas están el lavado frecuente de manos, el distanciamiento físico, el uso de tapabocas, la toma de temperatura al ingreso a la planta y la desinfección del calzado. La implementación de estas y otras medidas para poder operar de manera segura nos ha ocasionado una caída en la productividad cercana al 12% básicamente por el tiempo que demandan muchas de las actividades contenidas en el protocolo y que terminan impactando el ritmo de producción: la distancia entre procesos ha incrementado los tiempos de desplazamiento del personal, el ingreso a la empresa se hace a un ritmo más lento, hay más paros programados durante los turnos para lavarse las manos y los cambios de moldes y herramientas tardan un poco más.
TP: ¿Ve usted una oportunidad de sustitución de importaciones en la nueva coyuntura y con el precio del dólar? ¿Cómo pueden aprovechar las empresas esta oportunidad? JCZ: El nuevo escenario económico mundial plantea muchas oportunidades para sustituir importaciones y fortalecer la industria nacional, como respuesta al encarecimiento del dólar y a la alta dependencia de los productos hechos en China que ha resultado tan nociva para muchísimas empresas y sectores, no sólo por tratarse del país donde se originó esta pandemia que tiene en jaque al mundo entero sino también por lo frágiles que se pueden volver las cadenas de abastecimiento tan largas.
Hoy, más que nunca, los departamentos de integración nacional de las grandes empresas manufactureras -ensambladoras de motos, carros, electrodomésticos, entre otras- deben ser conscientes de que su función no consiste solamente en cumplir con un porcentaje de costo nacional para poder certificar el origen de sus productos, sino que son responsables, en gran medida, de la recuperación económica del país, abasteciéndose y generando empleo localmente. TP