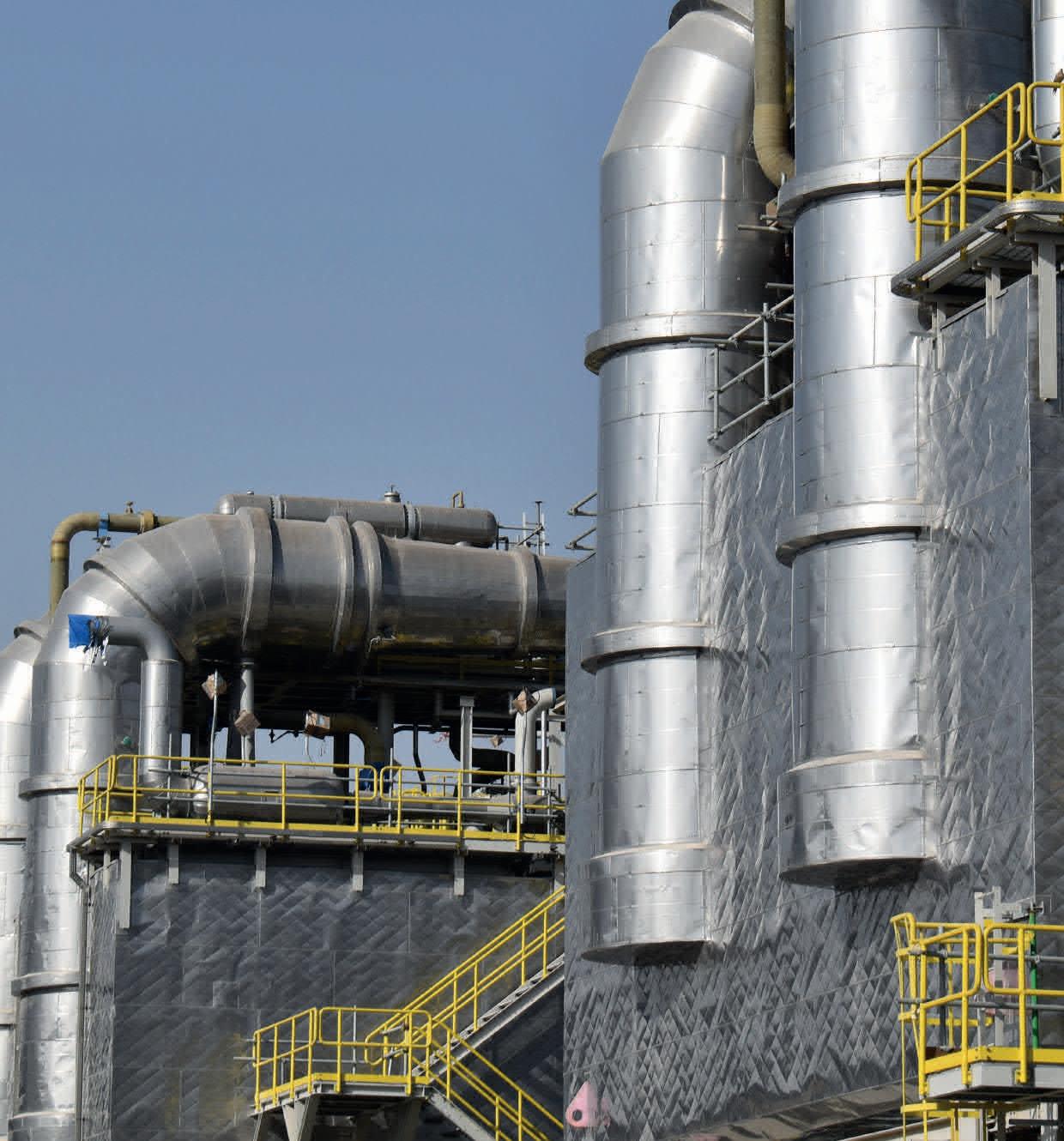
2 minute read
Asset Integrity
Asset integrity concerns prevention of equipment failure leading to hazardous events. The purpose of Asset Integrity is to prevent plant and equipment failure and safeguard asset availability. Asset Integrity supports sustainable development by reducing the risk of harm to personnel and the environment and has been identified as one of Bapco’s most important material topics.
G4 Disclosure Management Approach (DMA) Asset Integrity and Process Safety
The asset integrity management framework is documented in Bapco’s Mechanical Integrity Programme Overview Standard, which describes the programme scope and departmental responsibilities. We have a risk-based inspection standard for fixed assets, which provides Bapco-wide guidelines to ensure that the risk-based inspection processes are conducted consistently to the required standard. The basic premise of risk-based inspection is to prioritise assets whose failure leads to highest risk of loss of containment events.
Bapco has further specific standards for various sub-disciplines requiring asset integrity processes. These include standards for equipment scheduling and inspection, maintenance workflows for workshop activities, repair of relief valves and rotating equipment, and the provision of equipment and tools.
We conduct two types of maintenance for asset integrity:
• Preventive maintenance is conducted at a predetermined interval to address age related failures. Preventive maintenance includes lubrication, inspection of wearing parts and identification of damaged or poorly adjusted components. Repair work that is identified as being necessary during preventative maintenance can range from adjustment to complete overhaul of an asset that will normally be carried out within our workshops.
• Predictive maintenance is the application of measurement or testing techniques designed to detect likely future failures, to allow planned repairs before equipment failure. This provides information on the current condition of one item equipment or system to allow the timing and extent of preventive or corrective maintenance to be decided. We select predictive maintenance intervals based on engineering analysis of the probability of failure on-demand and likely time to failure.
Bapco undertakes regular active monitoring of maintenance activities to confirm performance standards, with any deviation from the standard rectified by actions assigned to relevant staff. Internal audits periodically monitor this process against the agreed risk based inspection and maintenance schedule.
Asset Integrity Defined Key Performance Indicators (KPI)
Bapco has defined KPIs for monitoring the effectiveness of its asset integrity program. KPI targets are reviewed periodically. The KPIs include the monitoring of safety device failures, mean time between failure of rotating equipment (pumps, compressors, etc.) and losses of containment. Each KPI has an annualised target and overall objective to achieve the required performance.
OG13 Number of process safety events by business activity
Bapco’s process safety metrics are based on accepted global industry practice such as American Petroleum Institute (API) 754 ‘Process Safety Performance Indicators for the Refining and Petrochemical Industries’. API proposes a range of indicators for loss of containment, generally designated as Tier 1 to Tier 4, with Tiers 1 and 2 representing the most severe indicators. The GRI G4 Standard requires Bapco to report the number of Tier 1 and Tier 2 process safety events that occurred during the reporting period. These are given in the table below.