
8 minute read
EQUIPMENT FOCUS: SOLUTIONS IN SIZE REDUCTION
SOLUTIONS IN SIZE REDUCTION
Multi-material compact shredders, whether mobile or stationary, single-shaft or fourshaft, slow-speed or high-torque, are an integral piece of equipment in the recycling equation. The profitable conversion of “waste” into usable commodities basically could not be done without accurate, efficient size reduction of material, whether it’s plastic, mixed waste, paper, e-waste, metals or organics. Following are some of the latest advancements from key manufacturers in the shredder sector.
LINDNER NEXT-GENERATION ATLAS TWIN-SHAFT PRESHREDDER NOW AVAILABLE IN NORTH AMERICA >>
At the beginning of October Lindner, the Austriabased specialist in shredding technology and system solutions for waste processing, invited recycling industry leaders and other guests to Lindner Atlas Day, held on the shores of Lake Wörthersee, Austria. At the event, Lindner pre sented their eponymous next generation twinshaft primary Atlas 5500 shredder for automated 24/7 operation (shown above).
Stefan Scheiflinger-Ehrenwerth, head of product management at Lindner Recyclingtech, explains that their design team focused on a shredding machine that would provide ideal output size and chunkiness for subsequent sorting processes, with high energy efficiency for 24/7 operation.
According to Scheiflinger-Ehrenwerth, in waste processing, the trend is clearly towards auto mation. When it comes to robots and separation technologies such as NIR sorting, processes now require uniformly flowing material – in terms of both flow rate and particle size – in order to be productive.
He explains: “Our tests have shown that materials shredded to the size of an A4 sheet and with a low fines content are ideal for preventing as many picking errors as possible in subsequent automatic sorting processes. The Atlas’ ripping cutting sys tem is simply tailor-made for that. Even collection bags for plastic waste can be ripped open easily without shredding the contents.”
Scheiflinger-Ehrenwerth continued, “Due to
Rotochopper entered into a new distribution partnership with Lindner in 2019. Shown is a model 75DK mobile shredder.

asynchronous shaft operation, where the shafts shred effectively in both directions of rotation, we additionally achieve a constant material out put of approximately 40 to 50 metric tons per hour. This means that the shredder continually delivers enough material to the conveyor belt to be perfect for productive sorting.”
The new Atlas 5500 shredder also features a new FX fast exchange system. For maintenance with minimum downtime, the entire cutting sys tem of the new Atlas 5500 can be completely exchanged in under an hour using this system. And thanks to a second cutting unit, made up of a shaft pair and cutting table, it’s possible to keep up production while, for example, welding work is carried out on the rippers.
EDGE INNOVATE TO LAUNCH TWO NEW HIGH-CAPACITY SHREDDERS AT CONEXPO 2020 >>
Ireland-based EDGE Innovate is set to debut two new highcapacity waste shredders at CONEXPO 2020, to be held in March in Las Vegas. The new VS420 and HS750 will take their place in EDGE’s ever-growing waste shredding product line and will be showcased this year with EDGE’s proven TRT622 tracked mounted trommel and newly designed TS100 track stacker.
According to EDGE, the new HS750 is a totally new concept to the shredder world. It offers operators a highcapacity, horizontal slow-speed shredder that combines high throughput, the ability to withstand difficult-to-shred materials and superior resistance to non-shreddables. The company says they have uniquely combined the benefits of a high-torque, slow-speed shredder with a horizontal positivefeed delivery system which also incorporates intelligent ma terial management and tramp metal protection.
The EDGE HS750 (shown right) is powered by a Tier 4 Final/Stage IV Caterpillar C18 engine providing 750 hp (560 Kw). These shredders also include two rotor modes, easy serviceability, an intuitive operating system, customizable
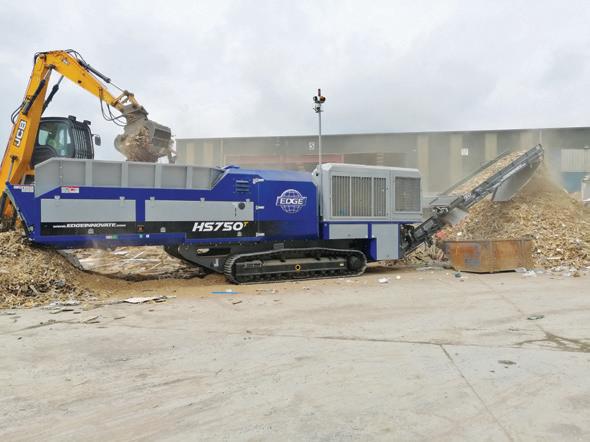
shredder programs and radio remote control, allowing operation by a single operator.
The new EDGE VS420 is a high-capacity, high-torque twin shaft shredder that can be used as either a primary or second ary unit. With 420 hp, this shredder is ideal for the processing of a large array of materials such as green waste, MSW, C&D, biomass and end-of-life tires. Key features of the VS420 include: intuitive controls, high resistance to contaminants, customizable twin shredder shafts, flexibility for chassis configuration and high fuel efficiency.

We Know Every Day is a Grind That’s why we make our granulators so tough
Size reduction is tough work that can really do a number on your equipment. At Herbold, we know that granulator performance and durability is critical to your success. That’s why we build our equipment to deliver maximum throughput and require minimal maintenance and downtime. Here’s how: • Double Cross Cutting Action – Reduces Jams and Material Fines • Adjustable Bed and Rotor Knives – Maintain Constant Cutting Circle • Safe, Easy Access to the Grinding Chamber – for Improved Maintenance, Screen Changes and Machine Cleanout • Replaceable Armor Plating Inside the Cutting Chamber • Faster and Safer Knife Changes – Adjustments are Made in Jig Outside of Granulator • Available Force Feeders – Increase Throughput by 50% - 80%, Reducing Power Consumption
200 TONS OF CONSTRUCTION DEBRIS
SHREDDED IN 3 HOURS
INDUSTRIAL SHREDDING EQUIPMENT

{ { wood waste | construction and demolition debris | pallets | railway ties cable reels | paper rolls | green waste | mattresses | tires | aluminum e-waste | white goods | food waste | domestic, industrial & bulky waste
EXCLUSIVE NORTH AMERICAN PARTNER OF HAAS RECYCLING SYSTEMS HAAS TYRON 2000 XL is the perfect tool for high volume waste reduction. With adjustable shaft speeds and independent shaft control in both forward and reverse, you can make quick work out of even the toughest materials.
Contact one of our experts today! 1.800.465.3214 | shred@shred-tech.com

TDS 825 SLOW-SPEED SHREDDER FROM TEREX ECOTEC IS A HIGH-CAPACITY, CUSTOMIZABLE MACHINE IDEAL FOR LARGE-SCALE OPERATIONS >>

Terex Ecotec has launched the TDS 825, a robust twin-shaft, slow-speed shredder. Ideal for large-scale operations, this highcapacity, customizable machine takes shredding to the next level and is suitable for all types of material including residential and commercial waste, bulky items, organics, waste wood, tree stumps and roots.
According to Ecotec, the TDS 825’s innovative hydrostatic drive offers protection against contamination and allows for bi-direc tional shredding, while independent gear boxes enable each shaft to be run separately, helping to reduce wrappage and improve shredding. Should a blockage occur, the shafts can be controlled via the radio remote control, allowing material to be repositioned before attempting to re-shred.
This double-shaft shredder has 2.5 m-long shafts made from solid steel, with a fully welded tooth configuration, providing extremely high production rates with excellent size reduction.

Located in the centre of the chamber, directly below the shred ding shafts, is a replaceable breaker bar, which controls the end product size. This is done by retaining material in the chamber to aid reduction, and it protects the transfer belt from damage caused by large pieces of contaminants. A number of breaker bar options are available, depending on the level of reduction required, and are easily replaceable due to the TDS 825’s side door chamber access.
High production, easy for operators The TDS 825 is powered by a 770-hp Scania V8 DC16 engine and has been designed to provide operators with unrivalled levels of service access. The unit’s high-volume tipping hopper increases the feed area, providing optimum material feed, and can be activat ed using the control panel or via remote. Tipping cycle times can be configured to suit the application and hydraulic folding hopper extensions allow for increased capacity, preventing infeed material from falling out, especially in bulky applications.
In addition, quick and easy set-up from ground level is guaranteed with the TDS 825, taking a matter of minutes with no tools or working-at-height required. The overband magnet is both height- and angle-adjustable hydraulically, and lifts up and away from the product conveyor when not in use. All con veyors are built to a modular design, allowing each one to be removed independently for ease of maintenance. A separate transfer conveyor with a high specification belt ensures material is effectively removed from below the shredding chamber. The product conveyor raises hydraulically and folds into mainten ance mode to allow removal of the transfer conveyor. The TDS 825 is maneuvered via a robust tracked undercarriage, making it a great solution for difficult terrain.
SSI recently announced two new patents for their PRI-MAX primary reducer. These high-volume, heavy-duty shredders are designed to process the most difficult materials and now include a cartridge cutting table designed to be easily removable without disconnecting the drive or hydraulic connecting NEW PATENTS FOR PRI-MAX AND INTRODUCTION OF TRI-SHEAR THREE-SHAFT INDUSTRIAL SHREDDERS LATEST FROM SSI >> hoses. The second new patent is for SSI’s stackable shafts which have slideon cutters and spacers, making the shaft reusable and configurable. (More on this news is online at recyclingproductnews. com. Search: Pri-Max.)
SSI has also launched the Tri-Shear line of shredders (above right). The Tri-Shear line of low-speed, high-torque, threeshaft, industrial rotary shear shredders are designed to efficiently process a var iety of difficult materials to a consistent particle size.
According to SSI, Tri-Shear shredders are multi-purpose machines designed to shred, liberate and reduce a wide range of materials (not including thick metals) in a single pass. The three shafts in the Tri-Shear shred and recirculate materials within the machine until they are a small enough size to pass through the remov able screen below the cutters. Three models are available ranging in power from 224 KW (300 hp) to 560 KW (750 hp) with hopper openings from 1,600 x 2,565 mm to 2,305 x 2,680 mm.
Tri-Shear series three-shaft shredders feature simple heavy-duty construction, shock protection, bulk feed capability, energy efficient operation, as well as low noise, dust, heat generation and mainten ance costs, with minimum footprint and foundation requirements. Units are also available with electric drive and Smart Drive configurations, removable screens, self-cleaning capability, application-specif ic feed hoppers and cutter configurations, seal and bearing protection, as well as a patented Advanced Cutter Locking Sys tem (ACLS).
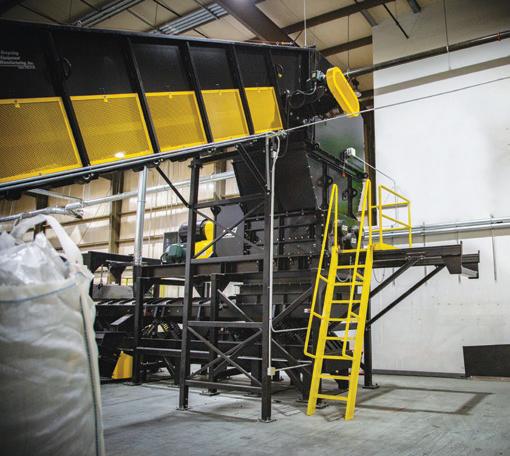
