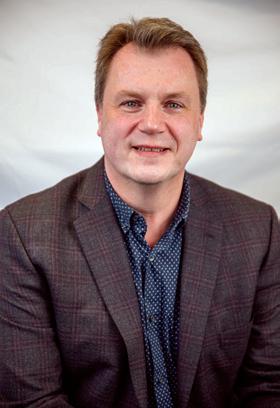
8 minute read
A FUTURE FOR EOL TIRES IN ONTARIO
A FUTURE FOR EOL TIRES
MAKING THE SHIFT TO A FREE MARKET MODEL FOR END-OF-LIFE TIRES IN ONTARIO
BY STEVE MELDRUM
In 1990, millions of stockpiled used tires burned for 17 days in Hagersville, Ontario, creating a serious environmental hazard. This laid the foundation for a sustainable tire recycling industry in Canada. The incident was a clarion call to the government that highlighted the need to establish an effective approach for management of used tires across the country. Since then, the tire recycling industry has made some major strides, with robust used tire recycling programs and industry bodies established across all Canadian provinces to manage sustainable and environment friendly recycling of end-of-life (EOL) tires.
EVOLUTION OF AN EOL TIRE
A tire is considered EOL when it can no longer be used on any vehicle (after having been re-treaded or re-grooved). While all tires eventually turn into EOL tires, the bulk of them come from passenger vehicles such as cars and trucks. The typical passenger tire contains 30 types of synthetic rubber, eight types of natural rubber, eight types of carbon black, steel cord, polyester, nylon, steel bead wire, silica and 40 different kinds of chemicals, waxes, oils and pigments.
Disposing of EOL tires in an environmentally friendly way has become the top priority across the tire ecosystem, requiring consistent collaboration among individual tire manufacturers, global governments and the tire industry. This is especially important considering that we generate an estimated one billion EOL tires globally, each year.
According to the World Business Council for Sustainable Development (WBCSD), EOL tire management approaches can fall under three broad frameworks: industry responsibility, government/community responsibility and a free market approach.
Industry tire responsibility puts the onus on tire distributors and manufacturers to collect EOL tires based on the number of units sold each year. This is usually managed by a separate not-for-profit organization. This model has become popular across Europe, Japan, Korea, Turkey, and now Ontario. Government/community responsibility typically involves a government body that becomes responsible for EOL tires, with an allocated budget set aside for this purpose. Lastly, the free market approach allows
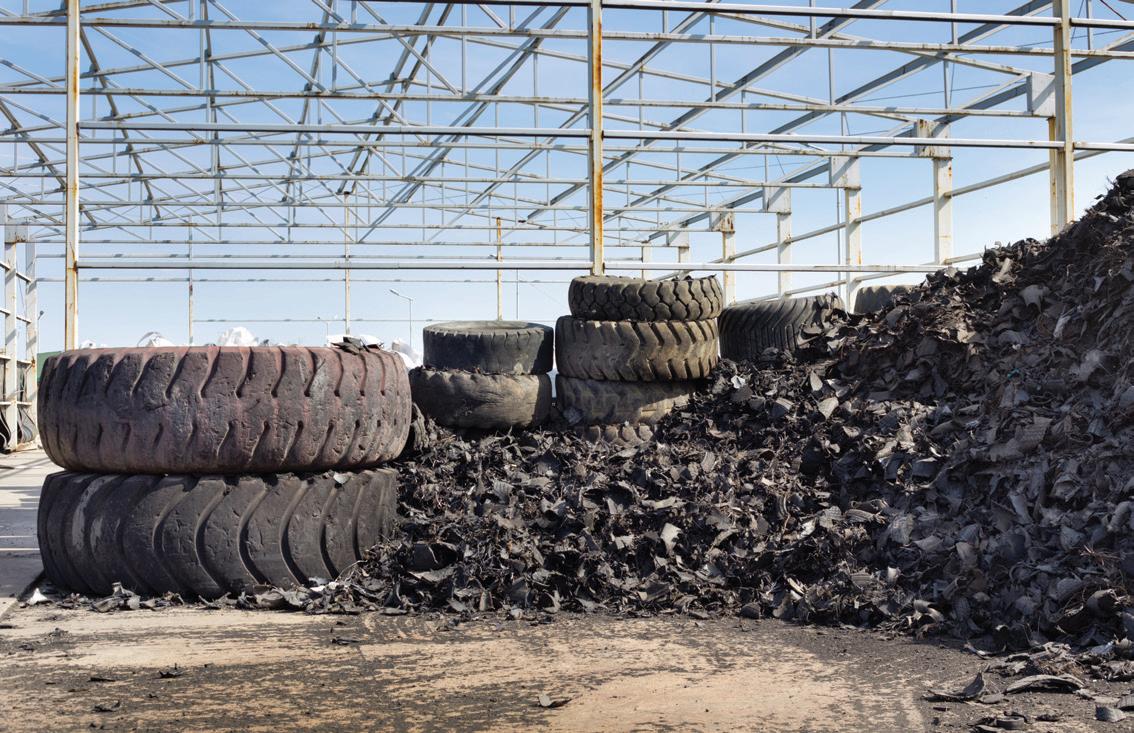
It is estimated that one billion end-of-life tires are generated globally each year.
YOU’RE BACK IN THE RACE. ONLY LINDNER CLIENTS CAN TRULY SAY:







’With the new Micromat cutting system, we were able to signifi cantly increase throughput even with tough materials.’

Jan-Hendrik Wilming CEO Lohner Kunststo Recycling GmbH Germany
In Vechta, Germany, Lohner Kunststo Recycling (LKR) knows exactly how to bring industrial plastic waste back to the starting blocks. Jointly owned by Remondis Group, the company has been recycling production waste and surplus since 1992. Today, LKR is a specialised full-service provider that transforms 45,000 metric tons of waste into valuable raw material every year for its customers worldwide. To shred this waste, the company relies on Lindner’s technology – like the Micromat with its new Multiplex rotor. Thanks to the cutting system’s new 3D stepped design, the shredder can produce up to 40% more output, even with tough input material. All the while maintaining Lindner’s signature high fl exibility and maximum productivity.

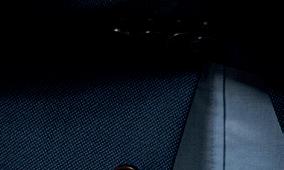
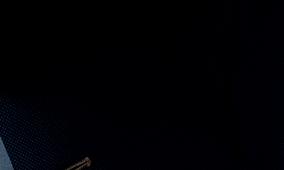
third party companies to operate independently to support the resource recovery process, which is how countries such as Austria, Germany, Ireland and the U.K. operate.
HOW IT ROLLS IN ONTARIO
Closer to home, there are over 12 million new tires sold each year in Ontario alone. But the province’s tire recycling industry witnessed a tectonic shift when it became the first in Canada to embrace the Individual Producer Responsibility (IPR) model, a legal regulation governing tire recycling (Regulation 225/18) which took effect on January 1, 2019. This regulation made tire manufacturers responsible for:
• Registering and working with the Resource Productivity and Regulatory Authority (RPRA) to keep records, submit timely and consistent reports to increase transparency, measure performance and ensure compliance;
• Providing a free, convenient tire collection network that provides a minimum number of collection sites across Ontario;
• Meeting resource recovery standards for the collection and management of tires;
• Educating consumers to increase public awareness and promote public participation in the resource recovery of tires. As a result of the IPR model, each producer now has to either make their own arrangements to collect and manage tires in order to meet their mandatory individual targets, or use Producer Responsibility Organizations (PROs) to help them meet their responsibility. A PRO enters into contractual relationships with service providers on the tire producer’s behalf and works to organize the collection and recovery of EOL tires. The PRO also participates in research and development activities for new recovery processes, liaises with local authorities, and helps producers comply with reporting obligations.
As the largest PRO in Ontario, eTracks manages over 80 percent of the collection and recovery obligations on behalf of tire producers in the province. It was incorporated by the Tire and Rubber Association of Canada (TRAC) to help tire manufacturers responsibly
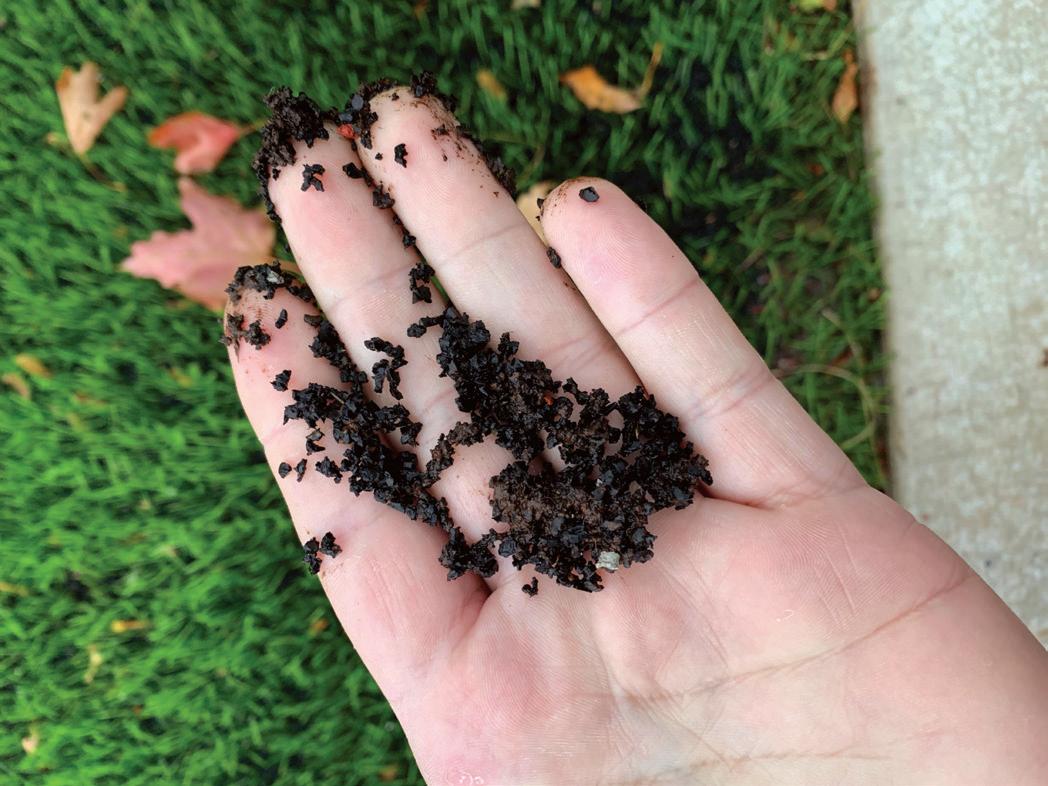
manage and dispose EOL tires in Ontario as required by the Ontario Resource Recovery and Circular Economy Act (RRCEA). eTracks is a not-forprofit company and is not motivated by gain but, rather, by outcome. With a breadth and depth of knowledge of product stewardship and supply chain management in Canada, eTracks is committed to building strong and productive relationships in the tire recycling industry through ethical and transparent business practices.
RESOURCE RECOVERY – EOL TIRE DERIVATIVES
A mindset shift has taken place with respect to EOL tires. They are now being viewed as a resource rather than waste, which has proportionately increased producer responsibility and the need for collaboration within the industry. EOL tires can be recycled into a number of items including crumb rubber, ground rubber, modified asphalt, gravel substitute, construction materials and wastewater treatment filters. These products can be used in a variety of ways. For example, crumb rubber can be used to make rubberized flooring for playgrounds, hockey arenas or athletics facilities. Recycled tires can be used in place of gravel in roadway sublayers, drainage ditch aggregate and highway embankments. Other uses include welcome mats, landscaping mulch additives, and as cost-effective asphalt cement, an alternative material for construction of road and highway systems.
Environmental issues continue to be a driving force behind EOL tire recycling. As the industry evolves, it is becoming clear that there can be significant benefits when collaboration between tire manufacturers, retailers and governments occurs. Now, in a huge range of industries, including at mines located in Northern Canada where there are hundreds of tonnes of tires stockpiled, what once may have been destined for the landfill is being diverted to facilities for recycling.
Today, most industry organizations in developed countries have tire recycling management programs in place to ensure that EOL tires are managed sustainably and safely. However, this progress should be seen as just the beginning. Continued efforts are imperative to help increase awareness about EOL tires as a resource, and to encourage innovation through research and development programs that find new, effective and environmentally sound uses for EOL tires.

SHREDDING EXCELLENCE for over 40 years!


ONE
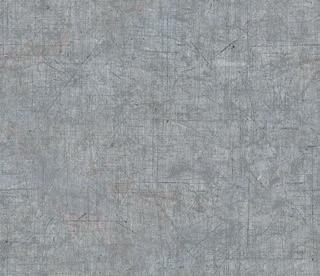
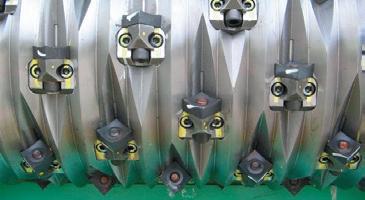
TWO
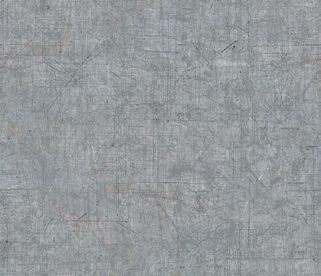
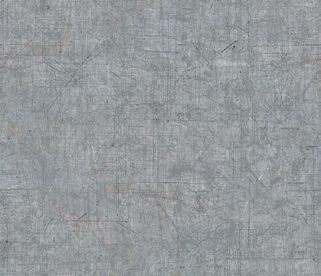


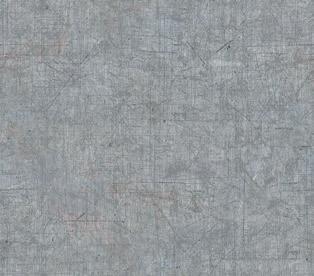
FOUR
YOUR THREE BEST OPTIONS FOR SIZE REDUCTION


Granulators, too!
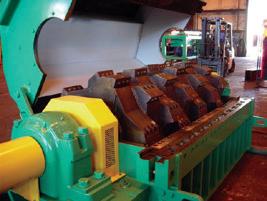


No matter what material size reduction requirements you have, we have the heavy-duty equipment and heavy-hitting engineers to address your needs. For more than four decades, we’ve been the durable, versatile shreddder ‘Brand of Choice’ for demanding applications all over the planet.
PET PP Fiberglas Epoxy ABS PVC HDPE LDPE
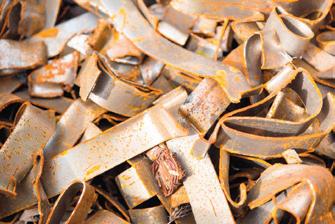









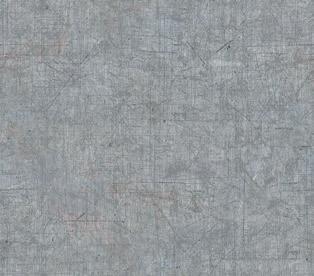
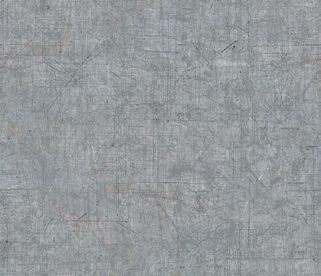
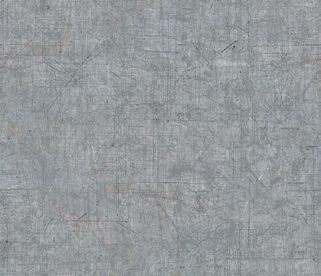
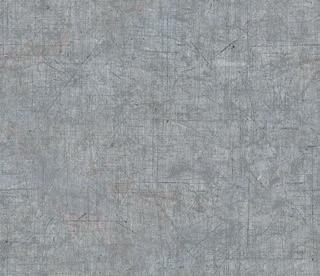