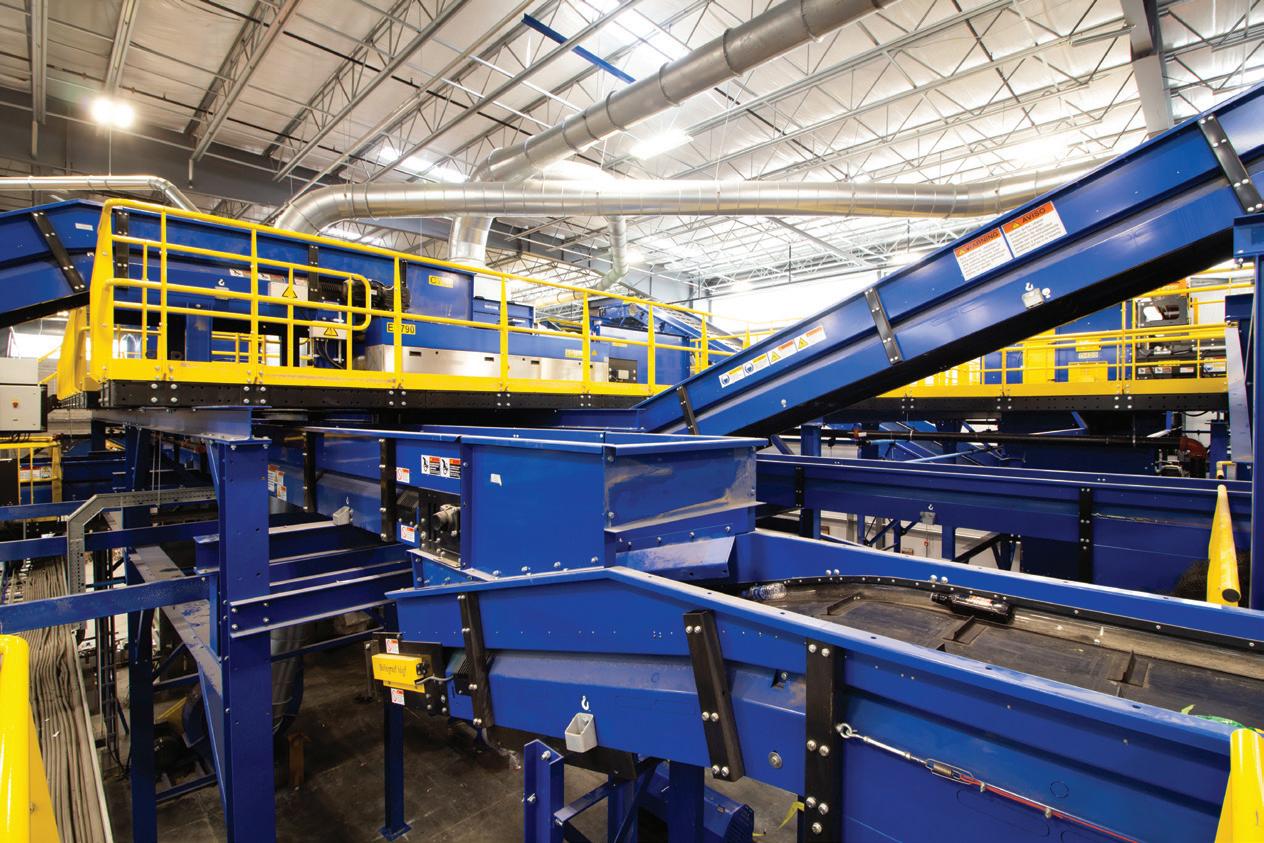
13 minute read
PREPARING MATERIAL FOR INTELLIGENT SORTING
Five steps to prepare material for intelligent sorting
BOOSTING HIGH-TECH SORTING PERFORMANCE AT THE MRF
Automation. Artificial intelligence. Robots. Whatever new technology a MRF may be in the market for, there are multiple factors to consider. At Van Dyk Recycling Solutions we visit MRF operations all over the U.S. and Canada. We see first-hand the challenges these sites face, such as highly-contaminated inbound material streams and inbound stream changes due to various factors, ranging from light-weighting, the Amazon effect, reduction of ONP, increase of film and trash, to high maintenance costs and increasing end product quality demands. There are also challenges with respect to maintaining a safe working environment and manual sorting labour issues – like finding willing candidates to show up every day and dedicate themselves to sorting through trash. Whatever technology is being considered – and there are some really cool systems out there (robots, optical sorters, material monitoring cameras) material needs to be properly prepared first for it to be properly recognized, BY MARK NEITZEY
sorted or monitored. Any separation device – a screen, an optical sorter or a robot – likes to be fed a steady diet of consistent material, on a single layer of the conveyor. If possible, material should be consistent by size with fines removed, and similar by shape, rigidity and density.
The following are five ways to help prepare material so that MRF operations can get the most out of their intelligent optical sorter or robot.
SCREEN FOR SIZE – WITHOUT GETTING WRAPPED UP
Mechanical screens remain an important piece of the puzzle at a MRF to help separate material into different fraction sizes, preparing material for further sorting or intelligent separation. Large fractions and fines can be removed and a target size can be directed to an intelligent separation device such as an optical sorter or robot. In the last few years screens have been greatly improved. Van Dyk and many other suppliers now offer non-wrapping screens that properly size material without allowing film bags to be wrapped around their shafts.
SEPARATE 2D FROM 3D – THE IMPORTANCE OF BALLISTIC OR ELLIPTICAL SEPARATORS
An elliptical or ballistic separator performs highly accurate separation of 2D and 3D materials. Paddles “walk” 2-dimensional objects (such as film bags and light sheet paper) over the screen. Items with rigidity (bottles, cans, 3D cardboard) bounce backward. Also, the paddles have true two-inch holes in them to allow the last bit of glass fines to fall through. With minimal maintenance and no star changing required, the elliptical separator has clearly become the best choice for final clean up at the MRF, whereas more traditionally a commingled or polishing screen would be used. With the ability to remove light sheet paper, film and fines, the elliptical screen is becoming a must have to properly prepare a container line for further processing (whether using optical sorters, robots or human pickers).
CONVEYOR BELTS – HOW THEY PLAY A PART
Conveyor belts and sequencing play a large role in the success of any intelligent separation device. This is because
asked for more innovation.

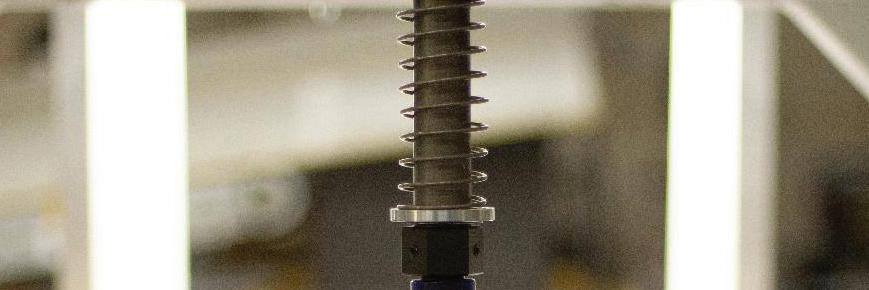
wasteexpo.com Register with code VP10 and save 25% on the conference program and get FREE Exhibit Hall admission. Recycling Product News readers save!
We’re delivering it. WasteExpo 2020. It’s all about you.
You’re always looking for a way to improve your business or department. Whether it’s more efficient processes, better equipment or the latest innovations to give you an edge. You want up to the minute information, the latest techniques and the know-how to maximize your profitability. WasteExpo has been the showcase for these types of innovations for 50+ years.
With 600+ exhibitors, 14, 500 of your colleagues, and the most comprehensive education program in the industry, you’ll find exactly what you need to succeed. WasteExpo 2020. You need to be here. Learn more. wasteexpo.com
the goal is to get material to a single layer to give the separation device a chance to succeed.
Here are some tactics to thin out material:
• Place two conveyors in succession and set them at different speeds;
• Whenever possible, feed subsequent conveyors in a straight line instead of at 90-degree angles; • Use wider transfer conveyors directly prior to the intelligent separation device;
• Use proper cleats on inclining conveyors that help space material and keep it from clumping together; • Have all conveyors on variable speed drives to give maximum flexibility to properly sequence the conveyors.
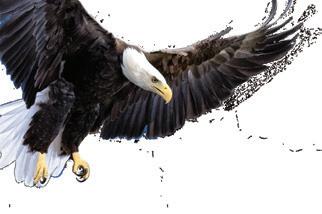
COM P A C T P O WER
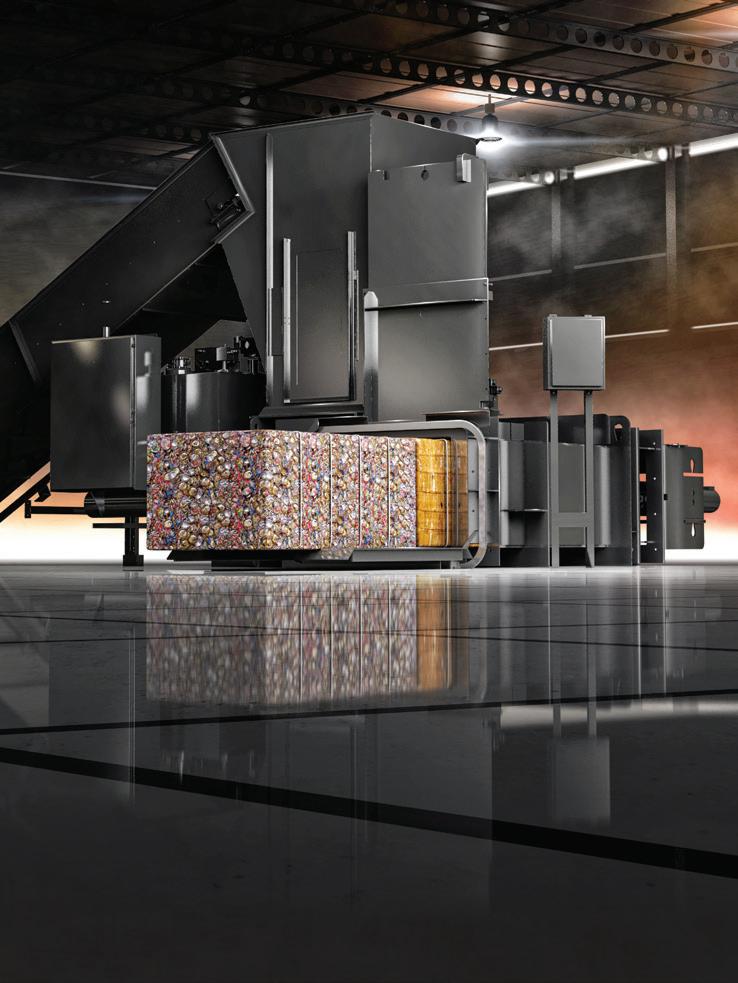
• TWO-RAM ON A HORIZONTAL BUDGET • VERTICAL BALE DOOR AVAILABLE • IDEAL FOR MULTI-MATERIAL FACILITIES
AMERICAN BALER TAKES PERFORMANCE TO NEW HEIGHTS!
I N T E G R I TY I Q U A L I TY I R E L I A B I L I TY I VA L U E
AN INTELLIGENT SORTER IS ONLY AS GOOD AS ITS MATERIAL FEED. “ “ MARK NEITZEY
These are all small details, but they all play a part in properly preparing material for intelligent separation.

SHAKE THINGS UP – WITH VIBRATORY FEEDERS AND DISC SPREADERS
If a sorting system has the extra height needed, a vibratory feeder or a disc spreader (shown below) can be the perfect tool to help spread material across a wide belt, for single layer coverage of material on its way to an intelligent separation device. If a customer is buying an eight-foot-wide optical sorter, but the incline conveyor that is feeding the eight-foot-wide acceleration conveyor is only four feet wide – this could cause a problem. The material will not get spread across those eight feet and only 50 percent of the optical sorter will be utilized. A vibratory feeder or disc spreader will help spread material as it drops onto the full width of the optical sorter’s acceleration conveyor.
KEEP THINGS STILL – WIND TUNNELS ELIMINATE FLOATING AND DRIFTING
The addition of a wind tunnel to an optical sorter’s acceleration conveyor is a good way to help process light materials at a higher throughput. Typically, light sheet paper and film starts to fly up and drift when a conveyor speed approaches 550 to 600 feet per minute. A wind tunnel added to an acceleration conveyor applies air flow at the same speed as the conveyor to stabilize the light floating materials and allow the acceleration conveyor to operate at higher rates of speed (upwards of 800 to 1,000 feet per minute). This allows more throughput to pass under an optical sorter and still be at a recognizable single layer. Recovery rates will rise while accuracy is maintained or even improved.
At Van Dyk Recycling Solutions we know how challenging it is to run a recycling operation. Operators are under constant pressure to meet goals in the face of changing end markets.
When it comes to using the latest robotic or optical sorting technology, recycling facility operators should simply keep in mind that it is really all about the way the system is fed.
Put simply: intelligent sorting technology is only as good as the quality of its material feed.
Mark Neitzey is director of sales, Van Dyk Recycling Solutions.


Wind tunnel technology helps keep lightweight paper and film on highspeed belts for higher throughput.

PO Box 29, Corning, Iowa • Fax (641) 322-3527 • sales10@brownbearcorp.com 641-316-7196 • www.BrownBearCorp.com • www.youtube.com/c/Brownbearcorp
C&D RECYCLING on-site CRUSHING IN THE CITY REUSING MATERIAL ON A CONFINED URBAN SITE ALL IN A DAY’S WORK FOR PRIESTLY DEMOLITION

BY KAITLYN TILL, MANAGING EDITOR P riestly Demolition was founded by Vic Priestly in 1971, originally as Vic Priestly Contracting Limited. The company remains family owned and operated, currently under the leadership of Ryan Priestly, and has built a reputation for tearing things up in Toronto.
Priestly Demolition has its own TV show, Salvage Kings, on the History Channel, as well as a popular YouTube channel, and was responsible for the demolition of an iconic landmark – the interior of Maple Leaf Gardens. They are also known for handling logistically challenging jobs, including the 401/404 interchange bridge demolition, along with urban demolition on restrictive downtown jobsites.
CUMBERLAND STREET DEMOLITION Priestly Demolition was recently hired to tear down a multi-storey parking garage on Cumberland Street in Toronto’s Yorkville neighbourhood. The site was a confined downtown property (90,000 square feet) and the parking garage consisted of 325,000 square feet of total building space. The job was completed in five months.
For the project Priestly Demolition used a Kobelco SK1000 demolition excavator, Komatsu PC600 and PC490 excavators, and Link-Belt 240 and 8000 excavators, in addition to a mobile crane, dozer, several compact loaders and an Extec (acquired by Sandvik in 2007) mobile concrete crusher and stacker.
According to Brian Priestly, VP of operations, when a structure is torn down, on-site crushing is the ideal solution to make disposal of material most efficient and cost-effective, whether it will be reused on site or hauled away.
For the Cumberland Street job, they operated a jaw crusher on site and used the material as backfill. Forty thousand tons of concrete was crushed to fourinch-minus for the backfilled space, which created a certified platform for drill rigs to work on to prepare the site for new construction.
Of course, on-site processing must satisfy the regulatory requirements of the region. According to Priestly, prudent equipment selection is important for reducing both dust and noise in urban environments.
“We try and use a lot of hydraulic crunchers or processors to diffuse the noise,” he said. “Hammers are needed sometimes, but in the preparation of the concrete and the processing of larger oversized concrete we’ll use a processor to break it down as well, as it’s a great tool to remove steel from the concrete, then recycle after the fact.”
On the Cumberland job, Priestly Demolition’s excavators were outfitted with primary processors to pre-crush concrete.
“We use the processors to pulverize the material to allow a more efficient crushing process,” he said, adding that “Sufficient water is required to ensure no risk of silica dust is present for workers or the public.”
Priestly added that when it isn’t feasible to crush on site, the destination of material depends on customer requirements. In these cases, they have the
Priestly Demolition’s equipment fleet, on site in downtown Toronto, included multiple excavators using primary processing attachments and an Extec mobile concrete crusher which reduced 40,000 tons of concrete to four-inch minus.

ability to take material to their yards for crushing; they can remove and recycle the steel, then crush the rest to salable aggregate. “We try and determine all the crushing requirements at the tendering process with the customers.”
He said demolished material is typically crushed to at least four-inch minus and some customers want two-inch minus for subbase and compaction ability. “We can/will crush to a customer’s specification,” continued Priestly. “Currently in Ontario there is a demand for recycled product. There is a surplus in crushed asphalt but concrete and/or stone is going out the door as quick as you can make it.” RPN
G A S • D I E S E L • E L E C T R I C D U S T & O D O R C O N T R O L E Q U I P M E N T DUST • 3 N O Z Z L E H E A D S / 3 X C O V E R A G E • 7 4 H P D I E S E L E N G I N E • N O G E N E R A T O R R E Q U I R E D T H E T R I D E N T B U F F A L O T U R B I N E B U F F A L O T U R B I N E . C O M



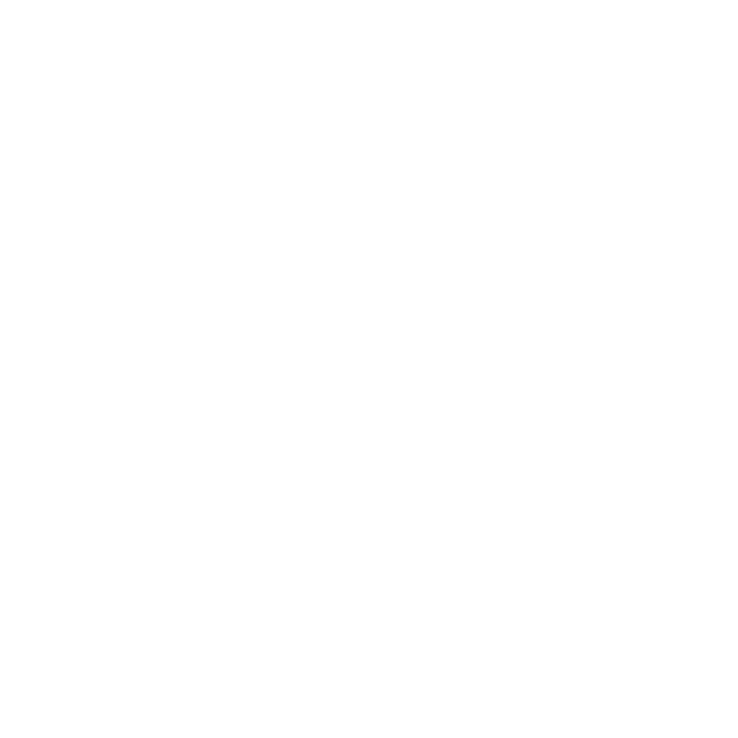


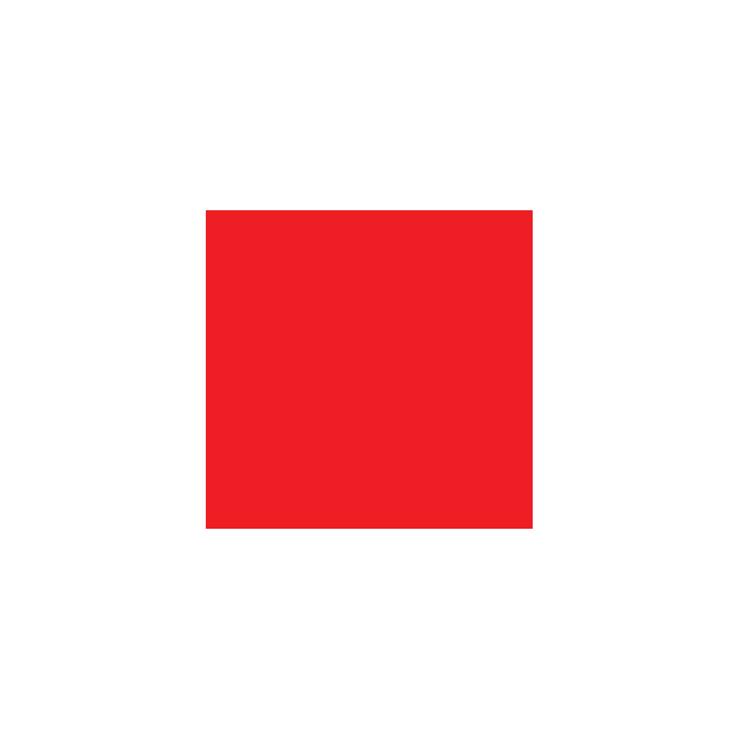
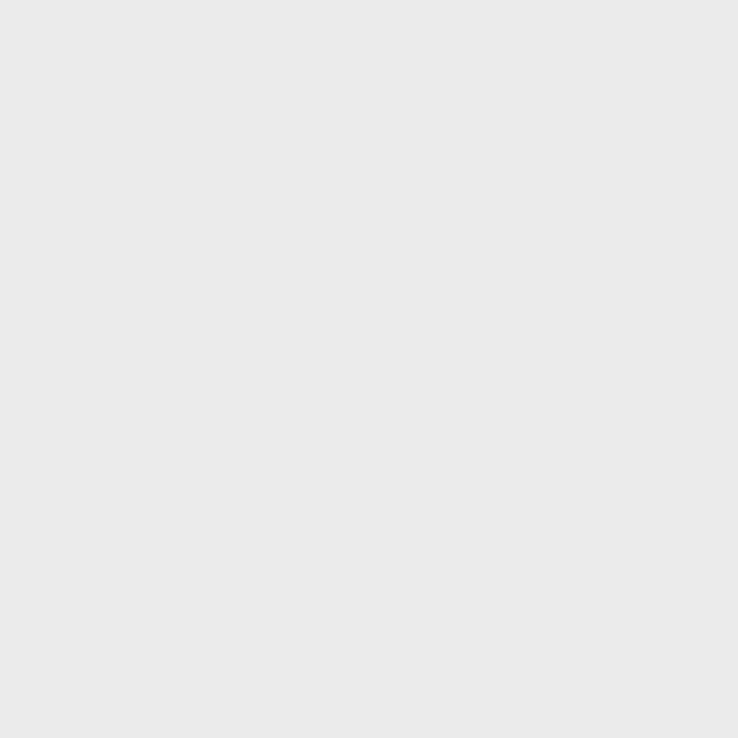
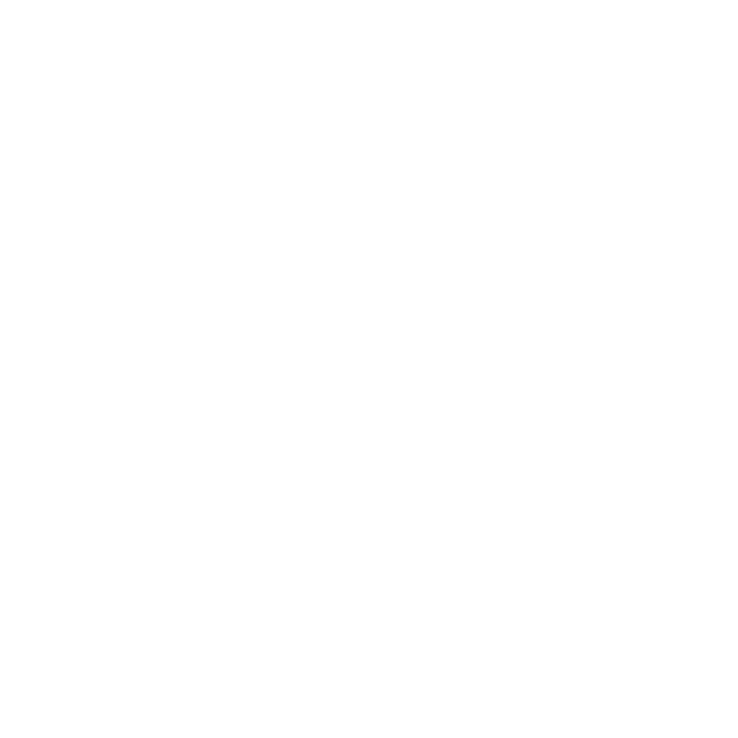


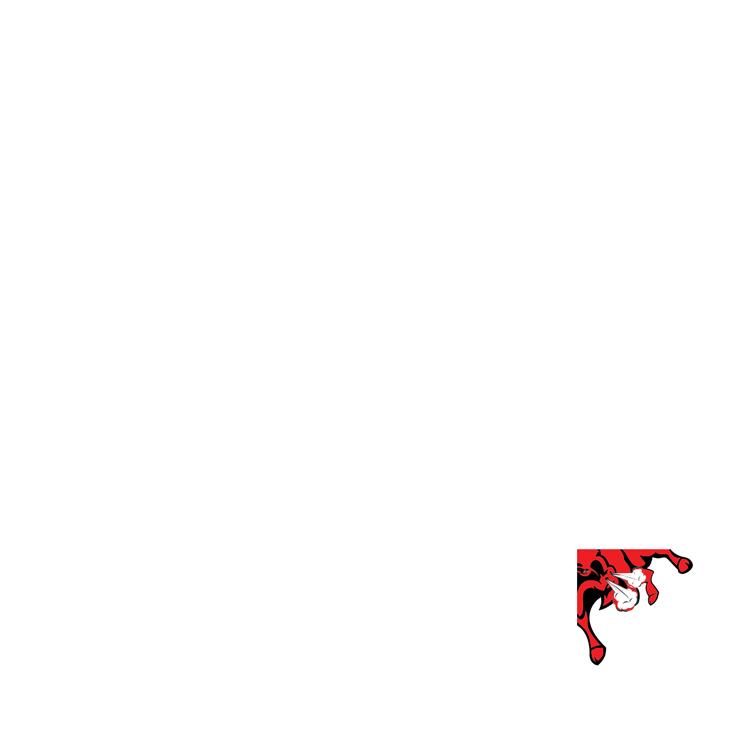



RecyclingProductNews.com HIGHLIGHTS FROM >>
INDUSTRY FORECAST CONNECT WITH US INDUSTRY EVENTS

Top trends to watch for at CONEXPO-CON/AGG 2020



TRAINING AND EDUCATION
Training Center is the heart of “uptime” strategy for Sennebogen in the Americas
SCREENING Recycled Material, Rubber, Glass, Wood and Metal




Superior Gyratory Screening Technology Higher speeds, larger strokes and greater capacity
A 100% Written Performance Guarantee Based on material, volume and eciency
3-Year Drive Warranty The best warranty in the Industry
800-663-0323 Phone: 604-539-1029

www.bmandm.com Email: sales@bmandm.com
E-WASTE

e-Stewards to extend Wisetek’s e-waste certification to all international sites
American Baler.........................................................40
Bateman Manufacturing...........................................45 BM&M Screening Solutions .....................................44 Brown Bear...............................................................41 Buffalo Turbine .........................................................43 Bunting Magnetics ...................................................15 CONEXPO-CON/AGG..............................................47
ELV Select ................................................................25 Gensco Equipment...................................................43 Granutech-Saturn Systems......................................29 Herbold USA ............................................................31 Industrial Netting ......................................................45
Kensal Carbide.........................................................17
Lindner Recyclingtech America................................27 Machinex....................................................................9 Mack Trucks .............................................................48 Michel’s Industries Ltd. ............................................21 OverBuilt Inc...............................................................7
Paradigm Software...................................................44
PMR Inc....................................................................13 R.M. Johnson ...........................................................23 Rotochopper Inc.......................................................37 Sennebogen LLC........................................................2 Shred Tech ......................................................... 32-33
STADLER America....................................................35
Van Dyk Recycling Solutions......................................3 Vermeer ......................................................................4 WasteExpo 2020 ......................................................39
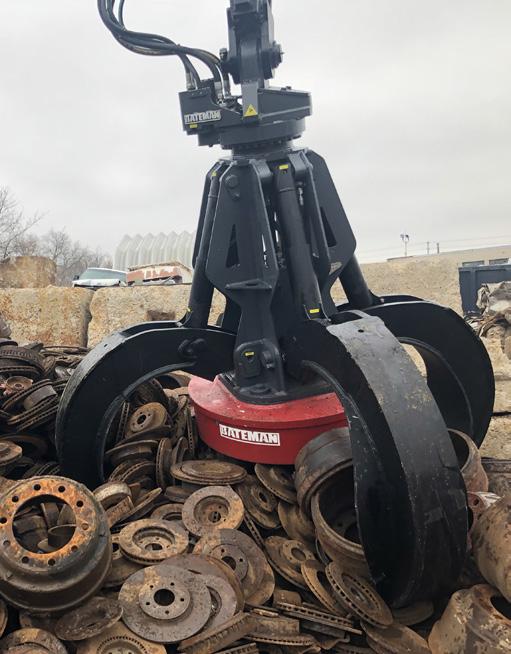
CALL TODAY 705-487-5020 www.batemanmanufacturing.com

Car-Go-Net “The preferred disposable” ®

•Fused joints won’t unravel • Easy to apply in a single pass • In stock for immediate shipment
RETRACTION In our November/December 2019 edition cover story, “Hope for Mattresses” erroneous information about recycling in the U.S. was included. According to Mike O’Donnell, Managing Director of the U.S. based Mattress Recycling Council (MRC), there are a total of 14 facilities recycling mattresses in the U.S., in three states (California, Rhode Island and Connecticut.) All three have currently established state programs, with funding coming from a fee at point of sale. Combined, programs in the U.S. are recycling over 1.5 million mattresses and box springs annually.
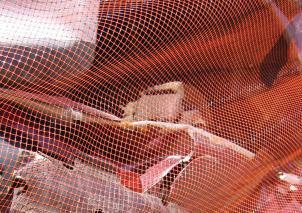
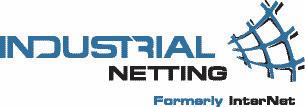