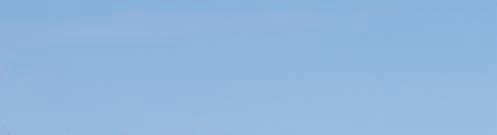

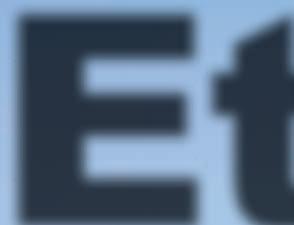

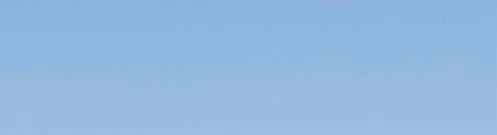
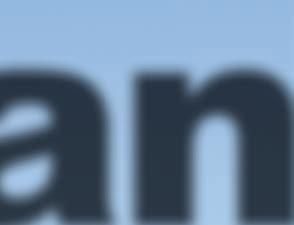
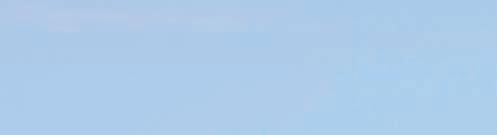
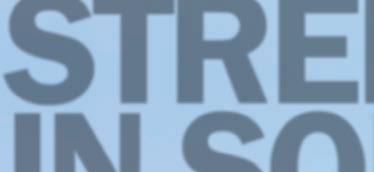
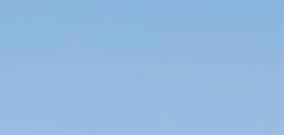
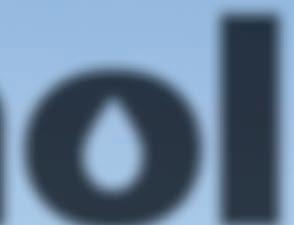
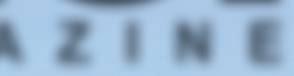
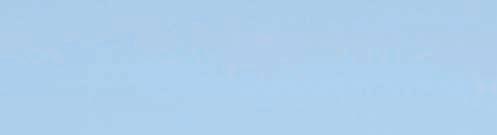
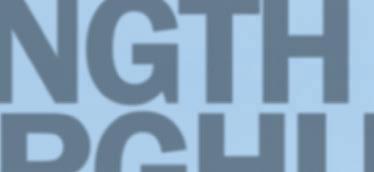
Producers, Farm Groups and Researchers Focus on Feedstock Potential

Producers, Farm Groups and Researchers Focus on Feedstock Potential
PAGE 14
PLUS Corn Oil Recovery Gets a Plant-Wide Approach
PAGE 20
EPA's New D3 Testing Prompts Surge in EP3 Approvals
PAGE 32
CTE Complete is uniquely innovative. Combining the strengths of our Technology Center with our Technical Services and Operational Support teams, we provide on-site expert guidance beyond our enzyme and yeast solutions. Ready to elevate your plant’s performance?
LED™ (Low Energy Distillation) allows facilities to expand production while lowering energy and carbon intensity per gallon. This patented Fluid Quip Technologies’ solution uses less energy than existing distillation designs, reduces downtime, and lowers CI scores. In fact, we’ve designed and engineered one of the lowest CI score ethanol plants in the world.
Expand your plant without expanding your CI. Talk to FQT today and start planning for tomorrow.
President & Editor Tom Bryan tbryan@bbiinternational.com
Online News Editor Erin Voegele evoegele@bbiinternational.com
Contributions Editor Katie Schroeder katie.schroeder@bbiinternational.com
Features Editor Lisa Gibson lisa.gibson@sageandstonestrategies.com
Vice President of Production & Design Jaci Satterlund jsatterlund@bbiinternational.com
Graphic Designer Raquel Boushee rboushee@bbiinternational.com
CEO Joe Bryan jbryan@bbiinternational.com
Chief Operating Officer John Nelson jnelson@bbiinternational.com
Director of Sales Chip Shereck cshereck@bbiinternational.com
Account Manager Bob Brown bbrown@bbiinternational.com
Circulation Manager Jessica Tiller jtiller@bbiinternational.com
Senior Marketing & Advertising Manager Marla DeFoe mdefoe@bbiinternational.com
Ringneck Energy Walter Wendland Commonwealth Agri-Energy Mick Henderson Western Plains Energy Derek Peine Front Range Energy Dan Sanders Jr.
June
Omaha, NE (866) 746-8385 | www.fuelethanolworkshop.com
Now in its 41st year, the FEW provides the ethanol industry with cutting-edge content and unparalleled networking opportunities in a dynamic business-to-business environment. As the largest, longest running ethanol conference in the world, the FEW is renowned for its superb programming—powered by Ethanol Producer Magazine —that maintains a strong focus on commercialscale ethanol production, new technology, and near-term research and development. The event draws more than 2,300 people from over 31 countries and from nearly every ethanol plant in the United States and Canada.
Omaha, NE (866) 746-8385 | www.sustainablefuelssummit.com
The Sustainable Fuels Summit: SAF, Renewable Diesel, and Biodiesel is a premier forum designed for producers of biodiesel, renewable diesel, and sustainable aviation fuel (SAF) to learn about cutting-edge process technologies, innovative techniques, and equipment to optimize existing production. Attendees will discover efficiencies that save money while increasing throughput and fuel quality. Produced by Biodiesel Magazine and SAF Magazine, this world-class event features premium content from technology providers, equipment vendors, consultants, engineers, and producers to advance discussions and foster an environment of collaboration and networking. Through engaging presentations, fruitful discussions, and compelling exhibitions, the summit aims to push the biomass-based diesel sector beyond its current limitations. Co-located with the International Fuel Ethanol Workshop & Expo, the Sustainable Fuels Summit conveniently harnesses the full potential of the integrated biofuels industries while providing a laser-like focus on processing methods that deliver tangible advantages to producers. Registration is free of charge for all employees of current biodiesel, renewable diesel, and SAF production facilities, from operators and maintenance personnel to board members and executives.
Customer Service Please call 1-866-746-8385 or email us at service@bbiinternational.com. Subscriptions Subscriptions to Ethanol Producer Magazine are free of charge to everyone with the exception of a shipping and handling charge for anyone outside the United States. To subscribe, visit www.EthanolProducer.com or you can send your mailing address and payment (checks made out to BBI International) to: Ethanol Producer Magazine Subscriptions, 308 Second Ave. N., Suite 304, Grand Forks, ND 58203. Back Issues, Reprints and Permissions Select back issues are available for $3.95 each, plus shipping. Article reprints are also available for a fee. For more information, contact us at 866-7468385 or service@bbiinternational.com. Advertising Ethanol Producer Magazine provides a specific topic delivered to a highly targeted audience. We are committed to editorial excellence and high-quality print production. To find out more about Ethanol Producer Magazine advertising opportunities, please contact us at 866-746-8385 or service@bbiinternational.com. Letters to the Editor We welcome letters to the editor. Send to Ethanol Producer Magazine Letters to the Editor, 308 2nd Ave. N., Suite 304, Grand Forks, ND 58203 or email to editor@bbiinternational.com. Please include your name, address and phone number. Letters may be edited for clarity and/or space. TM
Please recycle this magazine and remove inserts or samples before recycling
Minneapolis, Minnesota (866) 746-8385 | www.safconference.com
Serving the Global Sustainable Aviation Fuel Industry Taking place in September, the North American SAF Conference & Expo, produced by SAF Magazine, in collaboration with the Commercial Aviation Alternative Fuels Initiative (CAAFI) will showcase the latest strategies for aviation fuel decarbonization, solutions for key industry challenges, and highlight the current opportunities for airlines, corporations and fuel producers.
Threads of efficiency and value creation weave through this month’s feature lineup, which includes stories on maximizing distillers corn oil yield, making corn fiber ethanol viable, connecting with farmers on climate-smart ag data and, to kick things off, simply taking a moment to recognize grain sorghum’s importance. From the intersection of agriculture and biofuels, this issue focuses on the joint pursuit of higher value products in the context of lower carbon intensity production.
Our reporting starts with “Sorghum’s Staying Power,” on page 14, which reminds us that, while used by only a small percentage of U.S. ethanol producers, grain sorghum, or “milo,” gives ethanol plants in the central plains—from Texas to Nebraska to eastern Colorado—a good option when they need it. Sorghum is rather drought-tolerant and, depending on its availability, serves as a viable replacement, supplement or combination feedstock with corn. Beyond the gate, we look at research into different varieties of sorghum, and the work National Sorghum Producers is doing behind the scenes to further enhance the crop’s versatility and value.
Switching from inputs to outputs, we take a fresh look at the industry’s ongoing progress in extracting greater volumes of DCO per bushel of corn (and, yes, that sometimes includes sorghum). “Parallel Pathways,” on page 20, explains how ethanol producers are achieving previously impossible yields of 1.1, 1.2 or even 1.3 pounds of oil per bushel by deploying complementary strategies that layer together best-in-class mechanical, biological and chemical processes. As we report, however, the industry’s average DCO yield is nowhere near those high-end numbers—most plants are recovering 60% or less of their feedstock’s available oil—so there is tremendous room for growth and several ways to effectuate it.
Back to farming, we bring you a roundup of related but distinctly different platforms for agricultural MMRV—the measurement, monitoring, reporting and verification of climate-smart and regenerative farming. “Verifying Impact,” on page 28, looks at five such offerings now available to growers, retail agronomists and biofuels producers to track and validate low-CI practices, which are now an integral part of the low-CI ethanol equation. These platforms truly have it all covered, from scoring low-CI crops and standing up real-time ethanol plant CI data, to validating and quantifying low-CI ag and helping ethanol producers get optimal value for their upstream CI reduction efforts.
Finally, in “Modernized Measurement,” on page 32, we look at corn kernel fiber (CKF) ethanol production, which has been happening for years, but under inconsistent guidelines and value drivers. That is, until last year when the U.S. EPA clearly identified a methodology to measure and distinguish CKF ethanol from corn starch ethanol. The agency also tucked CKF ethanol into its Efficient Producer Petition Process, allowing EP3 plants to repetition for D3 RIN pathway approval, essentially clearing the way for producers to monetize CKF. A small surge in production has resulted and RINs associated with cellulosic/CKF ethanol have increased over the past year from 1.3 million to over 43 million. That growth appears to be carrying into 2025.
Right Combination for Maximum Oil Recovery
• Delivers up to 15% increased corn oil recovery
• Enables pathway to produce low-CI cellulosic gallons
• Dewaters corn kernel fiber for reduced natural gas consumption
• Maximizes plant operability
To learn more, contact your account manager.
Agriculture is part of the American Coalition for Ethanol’s DNA. That’s why the U.S. Department of Agriculture trusted us to lead a Regional Conservation Partnership Program (RCPP) project to help ethanol producers and farmers unlock new markets and profit opportunities through soil health practices—such as reductions in tillage, efficient fertilizer use and cover crops—applied to feedstock crops.
We’re gaining considerable ground thanks to our ethanol producer partners and USDA’s support.
Last year, select ethanol companies helped us engage nearly 1,000 farmers across 10 states who offered to enroll 500,000 acres of conservation practices in our RCPP. We expect farmers to begin adopting practices later this year. Once they have implemented the practices, land-grant scientists will collect soil samples and other field-level data about the resulting carbon benefits to pressure test models, such as GREET, which are used to calculate carbon credit values. Running the data through GREET and other models helps us target information gaps, which currently prevent farmers and ethanol producers from monetizing ag practices in regulated fuel markets.
The ACE RCPP also helped inspire USDA to publish technical guidelines this year to serve as a blueprint for how to monetize biofuel feedstocks like corn, soy and sorghum.
USDA’s guidelines feature a new Feedstock Carbon Intensity Calculator (FD-CIC) which generates carbon credits for no-till, reduced-till, cover crops and nutrient management as stand-alone farming practices. It calculates even better credit values for stacking or combining some of these ag practices. In other words, USDA responded to our disappointment with the all-or-none bundled ag practice requirement and artificial cap on credit values in the expired sustainable aviation fuel (SAF) tax credit and discarded that impractical approach.
Instead, USDA’s new guidelines represent the most significant acknowledgement to date by a government agency that practices already utilized by most farmers reduce the carbon intensity of biofuels.
Going forward, if California or a Midwest state apply the USDA guidelines to a clean fuel program, it will increase demand and return economic value for U.S. farmers and ethanol producers. Additionally, if Treasury incorporates the USDA guidelines into the 45Z Clean Fuel Production Credit, ethanol producers could have another pathway to be “in the money.”
The final 45Z regulation is yet to be determined, so there are no guarantees. But, the preliminary USDA feedstock calculations are meaningful. For example, no-till could reduce the carbon intensity of corn production in eastern South Dakota by nearly 12 points and potentially be worth more than $100 per acre if fully monetized through 45Z. The combination of no-till and a cover crop could subtract nearly 22 points from the same corn’s carbon intensity and potentially return more than $200 per acre if fully monetized through 45Z. What’s more, the Department of Energy has reduced ethanol’s induced land use change (ILUC) score by nearly four points, so the average dry mill corn ethanol score has improved significantly.
While these advancements are encouraging, ACE is convinced the practices many farmers are already using today should generate even greater carbon credit values, and we expect the RCPP field-level measurements from nearly 200 counties across the Corn Belt will prove us right when run through the FD-CIC and GREET model.
We are indeed gaining ground. Our work with USDA, ethanol company partners and farmers will ultimately empower ethanol producers and the farmers supplying them to maximize opportunities to sell new and valuable products, diversify their profit potential and earn premium prices in regulated clean fuel markets.
In recent months, the European Union has shifted its political focus to emphasize simplification, better regulation and the need to supercharge domestic industries.
Already the European Commission is working on new proposals for a Clean Industrial Deal, a strategy to strengthen the domestic supply of protein and measures to increase the competitiveness of EU agriculture.
In fact, ‘competitiveness’ and ‘strategic autonomy’ have rapidly become the new EU policy buzzwords. The question is whether policymakers will be willing to put words into actions with a more pragmatic approach when it comes to biofuels.
That’s certainly what other countries around the world have been doing—not just countries such as Brazil and the U.S., which have long seen the value of biofuels—but also Japan, Indonesia and India, which have all instituted policies making more effective use of sustainable biofuels in the effort to reduce emissions in transport.
In Japan, for example, Toyota is developing innovative technology for new internal combustion engines that run on green fuel, including renewable ethanol. India has ramped up its support for a domestic ethanol industry; Brazil and the U.S. have reconfirmed their consistent policies to support renewable ethanol industries.
In Europe, not so much. The EU is still placing all of it transport decarbonization bets on one technology—electrification—even though the European Court of Auditors has warned that this could leave the EU vulnerable to over-reliance on battery technology and raw materials whose supply is not guaranteed.
It’s not just a matter of finding the best way to achieve the ambitious targets the EU has set for itself in the fight against climate change; it’s also a matter of rising to the challenge of staying economically competitive.
This was underlined dramatically recently in a report to the Commission from Mario Draghi, who said the EU should take a more pragmatic, technology-open approach to achieving its Fit for 55 goals and unleash the potential of sustainable low-carbon alternative fuels such as renewable ethanol.
The Draghi report also notes that while the EU has been a world leader in developing renewable energy, thanks in part to the use of sustainable biofuels, its recent policy choices put it at a competitive disadvantage against the rest of the world going forward.
Opening up to the contribution of renewable fuels as early as possible will not only help broaden the range of solutions and preserve affordable mobility for all EU citizens, but also lead to faster emissions reduction instead of waiting for sales of battery electric vehicles to grow and the infrastructure they require to develop. To succeed, we need all solutions: this includes both electrification and renewable fuels.
In the coming months, as the EU moves to clarify its definition of CO2-neutral fuels, it should take this reality into consideration. It should also consider the major innovations in production that are already increasing the GHG-savings score of renewable ethanol, in some cases to more than 90% compared to fossil fuel. All renewable and carbon-neutral ethanol that is compliant with the Renewable Energy Directive (RED) should be included in the definition of CO2-neutral fuels.
Such a technology-open approach is essential, as Draghi pointed out. “The technological neutrality principle, which has been a guiding principle of EU legislation, has not always been applied in the automotive sector,” his report states. It notes the upcoming review of the CO2 for cars regulation “should follow a technologically neutral approach and should take stock of market and technological developments.”
So far, the talk has been promising. Now it’s time for action.
All included for one price
Capturing and storing carbon dioxide in underground wells has the potential to become the most consequential technological deployment in the history of the broader biofuels industry. The Carbon Capture & Storage Summit will offer attendees a comprehensive look at the economics of carbon capture and storage, the infrastructure required to make it possible, and the nancial and marketplace impacts to participating producers.
This premier Summit is designed for producers of biodiesel, renewable diesel, and sustainable aviation fuel (SAF) to learn about cutting-edge process technologies, innovative techniques, and equipment to optimize existing production. Attendees will discover e ciencies that save money while increasing throughput and fuel quality. This world-class event features premium content from technology providers, equipment vendors, consultants, engineers, and producers to advance discussions and foster an environment of collaboration and networking.
Knowing the Industry You Serve
Ethanol 101 will serve as a one day in-depth survey of the history, science, production and market basics of the ethanol industry. Populated by some of the industry’s most recognized professionals, this seminar will serve not only to bring you or your new employee up to speed on “must know” information about the ethanol industry, but will also provide a forum to meet respected industry representatives and network with them and their fellow seminar attendees.
“There were a variety of knowledgeable speakers. I found the tracks I attended to be extremely bene cial.”
– Erin Ferris, NCERC | SIUE
Network on the FairwayLimited Golfers
The Players Club offers one of the most unique gol ng experiences available in the Midwest. As one of the only Arnold Palmer signature golf course designs in the area, The Players Club is Nebraska's premier and only 27-hole private facility. Encompassing nearly 350 acres of Nebraska's farmland, the course is wonderfully incorporated into its natural environment. The aesthetic beauty of its rolling bent grass fairways, artfully sculptured bunkers and abundance of natural waterways and wetlands, contributes to a gol ng adventure unrivaled in the area.
“This was my second FEW and this experience was even better than the last. Well put together, great networking, and thought-provoking sessions.”
– Michael Borrie, Andersons Inc.
The FEW is the largest gathering of private and public sector ethanol professionals in the world. Your customers will be here seeking tailored solutions to the unique challenges they face. Attendees will include current and future producers of ethanol, industry vendors, technology providers, equipment manufacturers, project developers, investors and policymakers. Demonstrate your commitment to the future of the ethanol industry and plan to exhibit at this once-a-year opportunity.
“The conference was well organized and had great attendance.”
– Sally Y. Hart, CapCO2 Solutions
Start-ups with Capital
Do you have a new product or service in the ethanol, SAF, or carbon realm and are looking to further your business with funding? Consider applying for and submitting a pitch deck for Pitch Day at the Int’l Fuel Ethanol Workshop & Expo.
On Wednesday, June 11th, the Int’l Fuel Ethanol Workshop & Expo will be hosting two 90-minute pitch sessions for startups in the ethanol industry. All pitches will be open-door. Each nalist will receive 10 minutes to pitch, followed by a 10 minute Q&A session.
Blue Biofuels has announced the signing of an agreement to acquire 35.5 acres of land in Frostproof, Florida, marking a significant milestone in the company’s commercialization efforts. The site will house a cutting-edge production facility designed to produce an initial 3 million gallons of biofuel annually. The infrastructure and avail-
able land can support future expansion to 100 million gallons per year of cellulosic ethanol and 100 million gallons per year of sustainable aviation fuel (SAF).
The property, located in Polk County, one of the fastest-growing counties in Florida, is in the heart of central Florida’s agricultural region, offering access to an
Haffner Energy, an advanced solid biomass-to-clean fuels solutions provider, LanzaTech, a carbon management company providing a differentiated syngas-to-ethanol solution, and LanzaJet, an ethanol-to-jet technology company and fuels producer, have announced that they are working together to explore joint biomass-to-sustain-
able aviation fuel (SAF) projects covering the entire production value chain. The three companies are exploring SAF production opportunities, including the development of commercial plants, joint technology licenses, offtake opportunities as they become available, and funding support and/or investment in specific SAF projects.
Scoular is the new formalized supplier of grain and logistics to Mid America Agri Products - Wheatland ethanol plant in southwestern Nebraska. Scoular operates an extensive origination network in western Nebraska, including a grain elevator network in the vicinity of and across the road from the ethanol plant in Madrid. Scoular’s network of producer and commercial rela-
tionships in this geography, as well as logistics capabilities, will support the grain supply partnership with MAAPW. The ethanol facility grinds 16.5 million bushels of corn annually, producing 48 million gallons of ethanol, plus distillers grains and corn oil.
“We are excited to collaborate with Scoular, whose expertise and robust network align with our mission to drive sus-
abundant supply of biomass feedstock. It is also strategically located in the proximity of the Port of Tampa, which will facilitate efficient logistics by rail and road for biofuel transportation.
“The three companies together demonstrate the type of partnership and technology alignment this industry will need to be successful in meeting the global demands of aviation,” said LanzaJet CEO Jimmy Samartzis.
tainable innovation in agriculture and renewable energy. This partnership not only ensures a reliable grain supply for our ethanol production, but also strengthens our broader strategy of integrating cuttingedge carbon sequestration technology into our operations,” said MAAPW CEO Prestin Read.
Verity Holdings LLC, a subsidiary of Gevo Inc., and Landus announced a new agreement aimed at unlocking added value for farmers through sustainability premiums via export markets. This collaboration leverages Verity’s advanced platform to track and verify the attributes of agricultural products, enabling Landus to docu-
ment and assign value metrics for soybeans processed at its soybean facility in Ralston, Iowa.
This farmer-centric agreement reinforces Verity and Landus’ commitment to expanding opportunities in international markets for sustainably certified products, such as those derived from regeneratively
POET and Tallgrass announced they have entered into definitive agreements to connect POET’s Fairmont, Nebraska, bioprocessing facility to the Tallgrass Trailblazer carbon dioxide (CO2) pipeline. Under the arrangement, the POET facility will capture bioCO2 for transportation and permanent underground sequestration.
grown soybeans and corn. By streamlining the certification and data-verification process, the partnership aims to deliver measurable premiums to farmers meeting program requirements while incentivizing processors to adopt efficiency-enhancing systems that drive long-term sustainable outcomes.
Tallgrass is in the process of converting a natural gas pipeline that has safely operated for over a decade to transport CO2 to its sequestration site in Wyoming, minimizing the need for additional pipeline infrastructure. The Trailblazer project is under construction and expected to commence commercial operations in 2025,
Larson Engineering Inc. has completed its acquisition of Fagen Engineering LLC, the engineering arm of construction company Fagen Inc.
Larson Engineering is retaining all of Fagen Engineering’s employees and maintaining existing office leases in Granite Falls, Minnesota, within the Fagen Inc. headquarters, and Greenville, South Caro-
lina, ensuring continuity for current clients while expanding its national presence.
The acquisition stemmed from Larson’s more than 20-year working relationship with Fagen Engineering and Fagen Inc., as well as interest in the team’s specialized ethanol and biofuel plant and carbon capture expertise.
which will enable near-term connectivity of POET Bioprocessing - Fairmont.
Capturing and sequestering bioCO2 from the bioethanol production process lowers the carbon intensity of the final product, which will open new market opportunities that create value for Nebraska corn growers and bioethanol producers.
As the ethanol industry’s leading design builder, Fagen Inc. and Fagen Engineering have been involved in the development or installation of more than 90 facilities for original build, expansion or enhancement projects.
Certain ethanol producers rely on it, commodity organizations fight for it, and researchers tout its potential.
By Luke Geiver
Western Plains Energy has been running both corn and sorghum as feedstock at its Oakley, Kansas, ethanol plant for 21 years. Derek Peine, CEO, says his team has learned how to process and use both feedstocks together without much change to daily operations.
From ethanol yield to feedstock costs to market access, sorghum (also referred to as milo) has and will continue to present opportunities, Peine says. “I think running sorghum at our plant is a true advantage.”
WPE isn’t alone in its continued belief in sorghum. Policy influencers and sorghum experts, including National Sorghum Producers, are showing growers and ethanol producers how and why the crop, now more than ever, can be a prime player in the evolving biofuels landscape centered on lowering carbon intensity scores. Across the country, regionally and nationally focused research labs are releasing
new insights on topics ranging from better sorghum breeds to the crop’s suitability as a sustainable aviation fuel (SAF) feedstock.
The allure of using sorghum as a feedstock in ethanol production is directly linked to drought or low-moisture growing conditions. In arid regions like Kansas, sorghum is a consistent option for feedstock, and corn isn’t always available or economical—the feedstock mix varies considerably, depending on availability and price.
“The deciding factor is in the market conditions,” Peine says.
China sometimes has a strong influence on U.S. sorghum, which creates availability issues and price increases. During those times, Peine will use less sorghum, if possible. But other times, like this past year, sorghum is the only option. “This year, when the dryland corn burnt up, the sorghum bounced back,” he says.
Ultimately, WPE needs to be able to run both feedstocks at any given time. The feedstocks are commingled and not metered, with extra considerations for operation and enzymes.
Because the kernel size of sorghum is smaller than that of corn, the hammer mill screen must be tweaked. And although a basic enzyme package will work to break down the sorghum and corn mix, a more advanced cocktail option is preferred, Peine says.
With the proper considerations, the sorghum and corn mix doesn’t affect ethanol production yields. In the distillers grains market, the sorghum-based product is priced equally to a corn-based feed. WPE markets wet distillers grains to cattle feeders.
But sorghum must be handled differently than corn post-production, Peine says. Sorghum oil, unlike corn oil, will solidify at room temperature. So, once the sorghum oil goes through WPE’s evaporators, it enters heated oil tanks and heated storage tanks. Custom-
ers who utilize the sorghum oil understand the need for heat during transport, Peine says. Overall, sorghum oil yield is smaller than corn oil yield.
Sorghum isn’t valued equally in all markets or policy frameworks, Peine explains. Its CI-reduction value in California’s Low Carbon Fuel Standard, for example, is less than that of other feedstocks such as corn.
Through the 45Z tax credit configuration in place for 2025 to 2027, sorghum-based ethanol production through fermentation is on par with corn-based ethanol in its emission rate. Both will be granted the same tax credit value.
While Peine says his plant will always benefit from a more diverse feedstock mix, others running plants in areas with sorghum availability have differing viewpoints. Walt Wendland, president and CEO of Ringneck Energy near Onida, South Dakota, is certainly interested in
IN THE MIX: Ethanol producers in dry regions rely on sorghum in their feedstock mix. With the proper considerations for the corn/sorghum combination, a plant's daily operations remain largely unaffected.
policy and production-based advancements on the sorghum front, but he isn’t prioritizing adding the feedstock to his plant’s mix.
Because of the lower oil volumes available with sorghum-based ethanol production, combined with the uncertainty on sorghum as a recognized D3 RIN feedstock, Wendland says sorghum prices need to be at least 5% to 10% lower than corn to justify its use.
That doesn’t mean Wendland isn’t following sorghum. He’s particularly interested in ongoing research to test and prove ethanol production volumes from sorghum feedstock used in conjunction with second-generation ethanol or with new enzymes.
About a dozen U.S. ethanol plants use a corn/sorghum mix. There is potential for other plants to take advantage of sorghum, as 19 producers currently operate in Kansas, Colorado and Texas—states known for growing the drought-tolerant crop. In addition, some plants outside of the sorghum belt also run a corn/sorghum combination.
In the past two years, biofuel-based sorghum research has explored everything from genetically modifying growth of the plant to enhancing the oil accumulation ability of certain varieties.
A study by the University of Illinois at Urbana-Champaign released last year outlined the feasibility of region-specific feedstocks for SAF. The research aimed to clarify the best options for producing the necessary feedstock to meet the U.S. SAF Grand Challenge, a goal aimed at making 3 billion gallons of SAF by 2030 and 35 billion gallons by 2050.
After breaking down the U.S. into four feedstock producing areas based on rainfall— the Great Plains, Midwest, Northeast and Southeast—the researchers identified four main feedstock options that could be used to produce SAF: corn stover, miscanthus or switchgrass, and sorghum. In certain areas of
the Great Plains, the researchers said sorghum provided the best option.
The DOE’s 2023 Billion Ton report outlining the feedstock resources available for bioenergy production in the U.S. notes roughly 3.5 million tons of sorghum are produced annually. The report also shows that grain sorghum accounted for the production of 76.7 million gallons worth of D6 RINs as of 2022, made from 1.7 million tons of grain sorghum.
To date, most biofuel produced from the sorghum species is produced from the grain version. Specialty crops like sweet sorghum or energy sorghum are and can be grown specifically for bioenergy similar to miscanthus or switchgrass. The energy-specific varieties are being explored today.
Texas A&M AgriLife Research and the Texas A&M College of Agriculture and Life Sciences released research in 2024 looking
into a new bioenergy sorghum opportunity: wax. Sorghum used for bioenergy feedstock produces high volumes of wax, and in some cases, the researchers believe up to 180 pounds of wax per acre can be produced from bioenergy sorghum.
“Bioenergy sorghum spent 50 million years surviving in Africa, in a very hot, dry environment,” said John Mullet, university distinguished professor in agricultural biology at
Texas A&M. “To survive drought at high radiation levels, the sorghum adapted by secreting a lot of wax on the surfaces of leaves and stems.”
The research team is now looking at ways to characterize the production pathways of wax in sorghum and explore how it might be collected and later used as a value-added product.
At the U.S. Department of Energy’s Joint Bioenergy Institute, researchers are adding wheat genes into sorghum to improve its performance characteristics and further enhance its ability to tolerate conditions where precipitation is lower than annual evaporation levels.
A multi-organization research effort led by the Center for Advanced Bioenergy and Bioproducts Innovation lab—a DOE Bioenergy Research Center—is finding new ways to improve sorghum’s drought tolerance. Using tools to map out the full gene expression pathways in the plant, the CABBI research supports its theory that “plants are factories” and can deliver large amounts of lipids through
better breeding and a more robust understanding of how the plant produces grain or oils.
Even in California, Great Valley Energy LLC played a part in assessing the feasibility of producing advanced biofuels and value-added coproducts using sweet sorghum. Great Valley Energy joined a three-part field trial for the California Energy Commission, testing five varieties and a fractionation process originally designed for sugar cane.
Different configurations were used to examine the resulting biofuel, biofuel intermediates and value-added coproducts. The best configuration produced an internal rate of return at 25.4%. That configuration produced a 20% sugar solution for over-the-fence fuel ethanol production, livestock forage/feed blendstock and for extraction and upgrading of nutraceuticals.
After reviewing all the growing, production and processing methods for sweet sorghum in the region, Great Valley Energy concluded that “sweet sorghum is a viable crop that grows well in California and provides
reduced inputs and substantive sugar yields to have an advantageous carbon intensity compared to other crops for ethanol production,” adding that “several processing scenarios designed to add value to the rest of the sorghum stalk are technically feasible.”
Matt Durler, managing director of National Sorghum Producers, has big goals for sorghum as it relates to biofuels in 2025. At the heart of those aspirations is to highlight the environmental and economic benefits of sorghum farming and position the crop as an indispensable part of the biofuels industry.
“The NSP is focused on connecting resilient farming practices to producing lowcarbon ethanol,” Durler says. That involves helping growers and producers validate their unique farm-level carbon intensities and advancing efforts to monetize those practices at the global, federal, state and private fuel market level.
Durler and his team have made significant strides in the past year to advance the narrative and understanding of sorghum as an ethanol feedstock suitable for modern CI-driven policy frameworks, he says.
Multiple shipments of ISCC-certified sorghum ethanol have been exported worldwide, he says. International Sustainability and Carbon Certification is an independent, multistakeholder initiative created to support and certify fully traceable and sustainable supply chains.
The ISCC-certified shipments represent a significant milestone, Durler says, by demonstrating the ability of sorghum producers to meet rigorous farm data requirements. “Clearing this hurdle has opened the door for expanded domestic low-carbon fuel markets, adding value to the industry and ensuring sorghum’s relevance in ethanol production.”
The January release of 45Z Clean Fuel Production Credit guidance also presents a transformative opportunity for the sorghum industry, he says.
“By providing a framework to quantify and reward resilient farming practices, the rule has the potential to reshape how farmers document and adopt sustainable methods,” Durler says.
Amy France, NSP chair and a sorghum farmer from Scott City, Kansas, says the guidance is positive for sorghum, as it is a recognized feedstock in the program. “However, critical gaps remain, particularly regarding the specifics of the greenhouse gases, regulated emissions GREET model and USDA’s guidance on climate-smart agricultural practices,” she says.
The enhanced value proposition for sorghum’s inclusion in 45Z is expected to drive greater adoption of the crop as a biofuel feedstock and expand opportunities for farmers, Durler says.
NSP has helped ensure that sorghum plays a vital role in the future of sustainable agriculture and biofuels. Through work with the Partnerships for Climate-Smart Commodities Program administered through the
USDA, NSP is helping to advance farm data collection needed to validate metrics required by low-carbon fuel markets. For sorghum, like many other biofuel feedstocks, traceability is almost as important as what the feedstock is, the NSP says.
Through a $65 million project, NSP is working with sorghum producers in Colorado, Kansas, Nebraska, New Mexico, Oklahoma and Texas, in addition to tribal lands, to help expand markets for climate-smart sorghum. Part of the project’s purpose is to highlight climate-smart sorghum sold to ethanol companies for use in production and sale into the California fuel market. Archer Daniels Midland, Conestoga Energy Partners, Kansas Ethanol, Pratt Energy, Western Plains Energy and White Energy are all involved in the initiative. Enrolled sorghum producers have or will document their practices using a tracking and monitoring platform designed by Nestle and Danone. The list of climate-smart practices includes a variety of testing and monitoring methods deployed mainly by growers, ranging from soil health testing to irrigation water management.
Regardless of where, when or by whom sorghum is being used, NSP’s Durler sums up the organization’s stance: It will ensure “sorghum’s potential is recognized on a global stage.”
Author: Luke Geiver writer@bbiinternational.com
A new day is dawning for ethanol production. Our industry-leading lineup of yeasts and yeast nutrition, plus our newly added Spartec® enzymes, are pushing the limits of fermentation and reaching levels of performance never achieved before. Paired with our renowned educational programs and expert services, we’re setting a course for even greater yields and performance.
With LBDS, THE FUTURE OF FERMENTATION IS BRIGHT AND THE POSSIBILITIES ARE ENDLESS.
Corn oil optimization is now a plant-wide endeavor, with biological, chemical and mechanical processes working together to reach maximum availability and extraction.
By Lisa Gibson
In late 2024, IFF launched two high-performing enzyme solutions—trademarked OPTIMASH AX and OPTIMASH F200—as a corn oil-optimizing combination that reduces the amount of oil lost to the wet cake.
“Through our studies, we’ve found that a lot of ethanol producers are making ethanol close to theoretical yield,” says Marina Chow, research and development leader in grain processing for IFF. “But for oil recovery, what we’re finding is the majority of customers are recovering at 60%. That translates to a lot of theoretical yield and room for more oil recovery.”
And that, Chow says, means massive volumes of distillers corn oil (DCO) remain untapped and still available for mechanical solids separation—the hardware of extraction—and enzymes are vital to freeing up those latent yields. “We know we need mechanical and biological, and chemical can enhance the mechanical,” Chow says, adding that IFF immerses itself in all aspects of DCO extraction, collaborating as much as possible with leading equipment and technology providers in the space.
Producers leveraging today’s specialized enzymes in tandem with mechanical separation technologies often install additional yield-boosting solutions like syrup conditioning, downstream demulsifiers and associated dosing systems, deploying a full
suite of complementary tools for DCO maximization. Strategies vary, Chow says, but whole stillage is where it all starts.
Through its robust oil mapping technology, IFF measures the amount of DCO in every operational unit and process to understand where it is being lost. Consistently, IFF identified the largest area of DCO loss as the whole stillage separation stage, Chow says.
“We focused on the whole stillage separation stage to change the characteristics of the stillage,” she says. “By treating with enzymes early, it pushes oil and makes it so the wet cake holds on to less oil.”
SERVICING COSS-SL: A technician services Trucent’s COSS-SL (Corn Oil Separation System – Stokes’ Law) centrifuge system. It's one option on the market for mechanical extraction.
The paired OPTIMASH enzymes loosen the fiber and allow release of the DCO, Chow explains. Company data shows the enzymes boost corn oil yield by 15.7%, from 0.89 pounds per bushel to 1.03.
The market today is different from 10 years ago, when IFF started learning about how biological solutions could help increase corn oil availability, Chow says. “Ten years ago, adoption didn’t have the momentum it has now because oil prices were lower. They left that in wet cake so poultry feed, etc., had that fat content.”
But as DCO prices and demand have increased, more producers want to extract that oil instead of leaving it in feed coproducts.
With robust corn oil markets, the ethanol industry has embraced IFF’s paired OPTIMASH solution. “Reception has been very good because the results have been very good, even at high-yielding ethanol plants,” Chow says. “Customers seem to really appreciate the amount of support given when implementing, as well.”
Adding oil recovery enzymes can impact downstream processes, including fouling and changed process characteristics. So IFF carefully monitors all downstream processes for its customers. “We don’t just drop the solution in and leave,” Chow says. “We stay and we work with the customer.”
The solution also has the added benefit of lowering CI scores, in that the enzymes dewater, relieving pressure on the dryers. As the enzymes are cellulases, they will also work on corn kernel fiber. “Our customers find that by adding these enzymes to fermentation, they can get the benefit of qualifying for CARB, and also [generate] cellulosic credits,” Chow says.
Trucent’s TruDose system measures emulsion breaker needs in the feed and doses appropriately, says Bob Fesser, business development and sales manager for Tru-
cent. “Feed is constantly fluctuating so you can’t just program a dose,” he says. “TruDose measures and makes adjustments.”
Trucent has studied the stages of DCO loss in an ethanol plant and pinpointed about 250 factors that come into play. Fifty of those are significant, Fesser says, including viscosity, temperature and emulsion breakers.
While Trucent no longer offers an emulsion breaker to the ethanol industry, TruDose works with any emulsion breaker additive, Fesser says. “We developed a way to help plants optimize their dose rate and maintain that dose rate regardless of process fluctuations. We can show our customer where the industry is with regard to several key factors to optimize DCO yields, beyond just the extraction equipment.”
to thin stillage results in an exponential loss in free surface oil.
But Trucent also focuses on the mechanical side, offering its COSS-SL (Corn Oil Separation System – Stokes’ Law) centrifuge system. With its disc stack redesign, COSS-SL helps producers recover more DCO, particularly when paired with TruShield-SC, a syrup conditioning mesh screening step that further reduces particle size before the centrifuge stage.
“We know if there’s a pretreatment ahead of separation, by getting oil to coalesce into larger droplets and run in equipment longer, you’re going to get higher yields,” Fesser says. “We redesigned the disc stack based on those corn oil properties to have more surface area, which, in turn, increased efficiency 3% to 5% ... just by changing design of the disc stack.”
With COSS-SL and TruShield, producers might see up to 10% more extraction efficiency, Fesser says.
Upstream DCO recovery solutions are increasing interest in mechanical separation technologies, he adds. “They look promising to the point that plants are buying more extraction equipment from us because they know there is going to be more oil available.”
The evolution looks promising, he says. “As an industry, we’re always getting better.”
ICM’s FOT Oil Recovery technology also focuses on the wet cake. “FOT Oil Recovery is a mechanical solution that utilizes the existing whole stillage dewatering decanter stage with new design centrifuges that have improved capacity and efficiency that add the capability for a washing step,” says Adam Anderson, director of sales for ICM. “The mechanical ability to separate and wash the wet cake is the best solution a plant can have to control and minimize the oil that would otherwise go with the wet cake.”
ICM emphasizes a fully integrated approach to DCO recovery and makes its team of technology integration specialists available for customers who want to enhance their mechanical solutions with biological or chemical additives.
“We look at it as a holistic system,” says Alex Wayman, director of project development for ICM. “We do provide a mechanical solution, but if there’s a need or a want from a customer to bring in a chemical solution, we’re more than happy to sit down with a customer ... and be more of a consultant.”
“In the last decade, there have been significant developments with enzymes, yeasts and demulsifiers, as well as mechanical approaches and upgrades, all designed to make the oil available for recovery,” Anderson says. “A lot of plants have incorporated these, and it’s helped the industry evolve from the 0.5-pound-perbushel baseline yields that were common in the early years of oil recovery, to 1-plus pound per bushel that have become common today. This evolution led to impressive reductions in oil lost with
OK, so our IRmadillo™ may have a long nose and a funny look.
But that nose can sni out exactly what’s going on inside every one of your processes. Every single second of the day.
And if you know the precise chemical composition inside all your lines and tanks, there’s virtually nothing you can’t improve.
Filled with ground-breaking new technology, IRmadillo™ helps keep yeast happy, eliminates failed batches, reduces enzyme use, and much, much more.
So while you’re sitting around waiting for your next set of HPLC results, why not visit our website, and read up on the whole amazing IRmadillo™ story?
the syrup, but there is still opportunity with oil lost to the wet cake. And this is where we see the opportunity for the next great yield baseline to be set. It’s the missing lever that will allow plants to get as close as possible to the max percent recovery of their incoming oil. And stay there.”
Anderson adds, “It’s a wide range and we’ve got the bench of subject matter experts that understand the entire plant and the full integration of this technology and everything you need to bring along with it to maximize corn oil recovery.”
The system is also efficient with dewatering, lowering energy consumption of the dryers and, therefore, CI scores. The proprietary two-part separation process integrates post-distillation, optimizing the
feed to the evaporator and ensuring a drier cake. The resulting energy efficiency gains contribute to reduced operational costs and enhanced overall plant performance.
Elite Octane in Atlantic, Iowa, has installed FOT Oil Recovery and reported a DCO yield of 1.35 pounds per bushel in late 2024.
Wayman and Anderson point out that comparing corn oil yield in pounds per bushel is not apples to apples, given higher fat content in some corn feedstocks than others. “You don’t put oil into the process,” Wayman says. “What you’ve got comes as a feedstock.”
“It’s been fun to talk to the customers in different regions,” Anderson says. “So as we come to them with this message of,
‘Hey, not all corn feedstock is made the same,’ they appreciate that and can realize what is possible with the feedstock they have.”
Together, these biological, chemical and mechanical processes, and others like them, offer whole-plant pathways to optimized DCO recovery.
“It’s literally: Make it available, keep it available, recover it,” Anderson says.
Author: Lisa Gibson lisa.gibson@sageandstonestrategies.com
Leading ethanol producers recover only about 50% of available corn oil.
For tiva® and Fiberex ® solutions are designed to help you surpass this benchmark and optimize your plant’s efficiency. Extract more value from your corn feedstock with our comprehensive portfolio of tailored solutions -- potentially increasing corn oil recovery by up to 25% .
Connect with your Novonesis Account Manager to discover the optimal combination of solutions for your operations.
Various technology providers offer data solutions for farmers looking to implement low-CI practices as new monetary rewards incentivize their feedstocks.
By Katie Schroeder
Technology providers have been working for years to develop platforms with the capability to track and verify low carbonintensity (CI) farming practices. They are innovating to help connect farm data with ethanol producers, aggregating the intel needed to accurately estimate CI scores of crops and the fuels derived from them.
As 45Z comes into effect in 2025, offering ethanol producers monetary return for lowering their CI scores, there is an opportunity to pass that value on to farmers utilizing regenerative ag practices, a standout method of significantly reducing CI scores. However, to connect the dots between field and fuel, crop data must be accurately collected and compiled for verification and compliance.
Several options are already on the market for farmers looking for ways to track, verify and share their data with ethanol producers.
Preston Brown, president and founder of Incite.ag, was an Illinois farm kid, the inspiration behind his pursuit of agronomy. Now, his company helps biofuel producers understand their fuel scores and how to source low-CI feedstocks.
Brown explains that when the business was started four years ago, the technology was a harder sell for ethanol producers. “If you’re bringing a disruptive software solution to an ethanol plant, saying, ‘Hey, we can measure your fuel CI on a more realtime basis—we can give you dynamic feedstock scoring and leverage tools for that.’ There’s a lot of plants that would say ‘That’s interesting,’ but at the end of the day, you know, do they need it?” For pioneering early adopters, the answer was “yes,” but opportunities provided by the potential credits from 45Z have increased the number of interested biofuel producers—those who were waiting for a “clear value proposition.”
Brown says most ethanol producers have not yet had public, commercial-scale feedstock CI scoring conversations with their feedstock suppliers, and developing relationships while introducing a new conversation around data capture takes time. “There is a tremendous amount of education and enablement, trust building and process creation that needs to be implemented,” he says. “Refining these elements is critical to be able to capture the volume of data that you need for scoring and then ultimately compliance. When you execute all those steps effectively, you maximize the most important element of all: buy-in from all those individual corn suppliers.”
Incite.ag uses a “boots in the dirt” operating philosophy, collaborating with the ethanol plant’s origination team to help farmers input their data into Incite.ag’s program. That could include a straightforward sync of data between the farmer’s management software system and Incite.ag’s system, or a more manual approach. Incite.ag’s system can automatically connect with a farmer’s management software, extract and map the data, then generate a CI score.
The value proposition for Incite.ag’s software is its ability to automatically share farm data, capture ethanol plant information and share it with a third-party compliance organization, Brown explains.
“At the end of the day, we’re helping plants get ready,” he says. “We’re helping producers to get the education and enablement they need to be able to ramp up into CI scoring, because you just can’t flip the switch and start maximizing value. It takes a stair-step approach.”
Gevo developed Verity Tracking as a wholly owned subsidiary, designed to help validate and quantify the “intangible” benefits of low-CI fuels by tracking relevant data throughout the value chain, explains Ron Zink, chief operating officer with Verity.
“We’re creating the checkpoints along the system—using accounting documen-
tation and distributed ledger technology (DLT)—to memorialize and create an audit trail for the environmental attributes of both feedstock and fuels, including traceability to the farm as well as the CI of the distribution of the product, if desired,” Zink says.
When the feedstock leaves the farm gate, a sustainability declaration is created that outlines the attributes of the corn. Then, if it goes to an ethanol plant, the environmental impact from transportation can be added, as well as the CI data related to transforming that corn into ethanol and other coproducts, Zink explains.
Through a market-based approach, Verity is looking to help ethanol plants improve their profitability while enabling a premium price for farmers for their climate-smart approaches. This tracking plays a key role in building trust by laying out a detailed record that can prove the CI reduction impact. “We’re doing that end-toend because it’s a really nascent area, and it makes sense to say, ‘Let’s build out a system that everyone can use and trust,’” Zink says, emphasizing that Verity works with partners throughout all aspects of the supply chain.
In September 2024, Gevo acquired Cultivate AI, which is now part of Verity and contributes expertise on compiling and elucidating data at the field level. Jill Stanford, formerly the CEO of Cultivate AI, now works as the vice president of product with Verity. Combining Cultivate AI with Verity creates new opportunities to look at the data with the whole supply chain in mind, Stanford says. Cultivate AI’s platform serves farmers by collecting data generated from their equipment and consolidating it into an easily deciphered format. Now that the company is part of Verity, the Verity module can take relevant data from Cultivate AI—such as nitrogen fertilizer application—and generate a CI score.
“What we’re doing with this Verity module is enabling that data sharing for just the corn acres enrolled in a program,” she says. “One of the challenges I see in this sustainability attribute tracking area is making that complex data easy to exchange. By capturing data from equipment or [extrapolating corn acreage] from imagery, we can provide verified traceability to the field level.”
Minnesota-based CIBO Technologies leverages a combination of computer vision, carbon and crop modeling, and various data sciences to comprehend a variety of agricultural systems and calculate an estimated CI score using satellite data. The platform empowers farmers to explore potential financial benefits before sharing their data with the company. When a farmer decides to register for a program, they share data with CIBO to determine an exact score for their crops.
CIBO is able to codify any type of program, whether it be a Scope 3 solution offered by a food corporation or a tax credit offered by a government entity and brought to farmers by an agriculture retailer or crop consultant. The goal is to make these programs more accessible to farmers, helping them find stackable incentives, with the intention of promoting implementation of regenerative agricultural practices. The opportunity to help give these practices staying power motivates CEO Daniel Ryan and his team. Helping farmers maintain longterm profitability while implementing these practices is vital.
Our team of experts haveover 20 years of ethanol plant maintenance expertise. We o er full service and parts for all Fluid Quip equipment to ensure peak performance.
•OEM Parts Warehouse
•$2 million+ inventory on-hand
•Factory Trained & Certified Techs
•MZSA™ Screens
•Paddle Screens
•Grind Mills
•Centrifuges
•Gap Adjusters
“We like to try [to find] things that we can stack,” Ryan says. “For example, stacking a USDA program on top of a renewable fuel program, so they get more money per acre to do these practices. And so, that’s really the farmer side of the equation: Delivering an incentive optionality to them and they can pick what works best for the operation.”
CIBO Technologies’ platform offers farmers the tools needed to document and optimize practices such as no-till farming and cover cropping, he explains. The platform also uses AI-driven analytics and remote-sensing capabilities to give farmers high-resolution, real-time data to track the effectiveness of their carbon sequestration efforts, making it easier to comply with USDA guidelines.
Although the platform possesses a lot of complexity in the background, its user interface is straightforward. “We, behind the scenes, ... are able to run the whole emissions inventory, all that stuff without them seeing all that deep tech running,” Ryan says. “They just get a very nice user experience. But below the surface, there’s a lot of things that have to happen to generate an answer.”
A new update to a tested technology platform offers retail agronomists and farmers an opportunity to track their CI data and share it with ethanol producers. For Xarvio, a BASF brand, the core focus is on the agriculture retailer, explains Kyle King, U.S. commercial lead for Xarvio Field Manager. Xarvio Field Manager helps determine what crop variety would work best in which field, manage stress factors from weeds, pests and diseases, and more.
Now, Field Manager’s recent update will add a sustainability element and allow interconnectivity with Xarvio Bioenergy, which is dedicated to helping ethanol producers manage their CI scores. The platform has the ability to document tillage, cover crops and nitrogen practices—the key data points with CI impacts under the GREET model.
“What we’ve learned and what we’ve experienced is when it comes to agronomic recommendations on how to properly manage cover crops, how to properly manage nitrogen within a corn crop, retail is the go-to,” King says. “They’re the lead, and so that’s another key reason why we focus our energy with ag retail, because they’re the ones that are going to be making those recommendations to help those farmers drive their CI score down, which would be obviously a huge benefit to all parties involved.”
Jeremy Zidek, new business development manager with Xarvio, explains that the sustainability element has always been a part of the Field Manager program globally, but is now tailored to work in the unique environment in the U.S. “Biofuels and the Inflation Reduction Act is pretty unique to the U.S. and to North America, so we’ve focused on that market approach rather than the carbon offsets market, but sustainability has been a core focus of Xarvio since its earliest days,” he says.
Farmers can choose to give ethanol producers access to the CI-related data
stored in Field Manager, interconnecting with Xarvio Bioenergy. “The growers want to ensure their hard work is rewarded and that their data is only shared with people who are required to see it or who they choose to share it with,” Zidek says. “The ethanol plants simply want to ensure they’re able to source low-CI grain and meet their reporting requirements. Xarvio Bioenergy addresses both of these needs.”
Mitchell Hora, founder and CEO of Continuum Ag, started the company to serve as an agronomy consultant, but now it assists farmers in measurement, monitoring, reporting and verification (MMRV) of the feedstock CI they provide to various industries. Continuum Ag developed a software called TopSoil, which allows farmers to input basic information and get an estimated CI score derived from the GREET feedstock calculator, which is integrated into Continuum’s platform.
Farmers can enter data and calculate their base CI score, compare different fields and then contrast it with models simulating changed practices. “So, they [get] their scores for free, they can run scenarios, it’s all for free,” Hora says. If the farmer decides to move forward with verification of these estimates, Continuum charges a fee per acre.
Verifying the CI score entails gathering records of fertilizer usage, tillage, crop yields, field boundaries and more. At year-end, the farmer will sign an attestation, and a third-party auditor will audit
CI COMMUNICATION: Farmers are able to share their Feedstock Supplier CI Report with ethanol producers through Incite.ag.
PHOTO: INCITE.AG
the farmer. After the audit is complete, Continuum will issue a verification certificate. Currently, Continuum has scored more than 350 million bushels. Nationwide, 5.4 billion bushels of corn would be directly influenced under 45Z. Corn is not the only crop that qualifies as a feedstock under 45Z, explains Hora; sorghum and soybeans are also included.
“We’ve been proving concepts and trying to get ahead of this because of the nature of the credit and currently being only a three-year program, and farmers have a very critical role to play to be the solution,” he says. When guidance from the U.S. Department of Agriculture was released in mid-January, Hora said his team was ready to step into the framework when it is complete.
Ultimately, as a farmer, Hora values these practices “with or without tax credits” because of the positive impact they have on soil health and agriculture overall. “I see this as a tremendous opportunity to utilize this tax credit to incentivize the adoption of more regenerative systems and get a really positive environmental outcome.”
Stepping into 2025, MMRV service providers seek to be flexible, having already done the legwork to set themselves up to help farmers and ethanol producers take advantage of the tax credits offered by the IRA.
Author:
Katie Schroeder katie.schroeder@bbiinternational.com
A testing change adopted by EPA’s efficient producer pathway program is attracting producers with the means to generate D3 RINs from corn kernel fiber ethanol.
By Luke Geiver
Since March 2024, the number of approved U.S. Environmental Protection Agency EP3 petitions has skyrocketed. Going back to 2018, the most EP3 petitions accepted in a single year for corn-based ethanol was four. In 2022, only a single EP3 petition was approved. Since last March, however, EPA has approved 39 petitions.
EP3, which stands for Efficient Producer Petition Process or, informally, efficient producer pathway program), is part of a demonstration and compliance apparatus created more than a decade ago by EPA. The process enables producers to generate renewable identification numbers (RINs) for ethanol volumes above their original grandfathered capacities granted through the Renewable Fuel Standard. Producers petition the EPA and supply information including feedstock type, production processes and fuel type. The agency then assesses the combined information, assigns a greenhouse gas emission rate to the fuel produced and determines if additional RINs can be generated by the plant.
Without the approved efficient producer pathway recognition, any ethanol gallons produced and sold above the grandfathered numbers established before implementation of the RFS have to be sold without a RIN designation.
Ethanol Producer Magazine spoke with EPA about the impetus behind the increase in petitions and what the agency has learned about the ethanol industry since it began administering EP3. A deep dive into the numbers also shows how the industry has changed, along with new opportunities that might exist for producers that have already received an EP3 pathway.
According to an EPA spokesperson, the rapid increase in approved EP3 petitions starting in March 2024 is directly linked to the adoption of a new ASTM testing method, E3417, that finally enabled EPA to measure the cellulosic content of ethanol. EPA now has a clear option to allow ethanol producers coproducing corn starch ethanol and corn kernel fiber ethanol in-situ to be able to identify and generate both D6 and D3 RINs.
“In March 2024, the EPA announced an update to include facilities that coproduce D-code 6 corn starch ethanol and Dcode 3 corn kernel fiber (CKF) ethanol,” the spokesperson says. “This was related to the EPA’s acceptance of an ASTM test method for measuring volumes of ethanol produced from CKF.”
E3417 was developed by the ASTM International Committee on Bioenergy and Industrial Chemicals from Biomass. According to the committee, “this test method is intended for use in the measurement of the fermentable portion of cellulosic content in
pre- and post-fermentation corn biomass specifically for the apportionment of a percentage of the total ethanol produced in a fermentation as cellulosic.”
While the amount of cellulosic content—or D3 RIN gallons—is relatively small compared with the overall volume of D6 gallons produced annually, the value of D3 RINs is significantly higher than D6 gallons. Most years, the value of a cellulosic waiver credit is above $2. Typically, producers that may have used corn kernel fiber didn’t bother with generating D3 RINs because there was no accepted and efficient system for doing so. The adoption of test E3417 didn’t necessarily unlock new production options for the industry, but provided the necessary testing and recognition capability for producers to receive credit for current practices.
In its guidance announcement on the D6 and D3 generation possibility, EPA explained it was streamlining its EP3 petition process to allow previously awarded EP3 producers to re-petition in order to gain the D3 RIN production pathway possibility. Included in the recent surge of approved petitions are several producers that had previously been approved through the EP3 process.
“Based on these updates, many ethanol facilities that already had an EP3 approval for only D6 corn starch ethanol chose to submit a new petition that allows them to coproduce D3 CKF ethanol,” the EPA spokesperson says.
The spokesperson adds that in 2025 the agency will also look at ways to potentially incorporate coproduction of cellulosic grain sorghum fiber ethanol into the EP3.
“We are looking at options to make this as streamlined as possible. We are also evaluating other ways to reduce administrative burden related to the EP3 process.”
Weaver and Tidwell LLP, a tax advisory firm with an Energy Compliance Team that serves the ethanol industry, says producers hoping to fully leverage both the D6 and D3 RIN generation possibilities should consider creating an approved Quality Assurance Plan, as D3 RINs are commonly verified under a QAP.
Weaver’s Energy Compliance Team issued a specific notice to producers following the March 2024 E3417 announcement, reminding them of the requirements for the pathways, including engineering reviews. Engineering reviews are required when a facility produces a new renewable fuel like cellulosic ethanol. The reviews are also beneficial to producers looking to simply apply for EP3 petitions after performing de-bottleneck work or any other measure that has helped them exceed their D6 grandfathered RIN production.
Beyond EP3 pathways, Weaver’s team can also help producers looking to sell unde-
natured cellulosic ethanol into other production processes, such as alcohol-to-jet fuel for D7 RINs (cellulosic diesel).
Tony Miller, principal engineer on Weaver’s Energy Compliance team, says producers should identify a lab to conduct cellulosic testing if they want to generate D3 RINS.
EPA’s spokesperson says the agency has learned a lot about the ethanol industry since it first began EP3.
“Based on the data provided through the EP3 process, we have observed that dry mill ethanol plants have increased their efficiency over time in terms of increased gallons of ethanol produced per bushel of feedstock and reduced process energy use per gallon of fuel produced.”
To qualify for EP3, a producer has to show a GHG reduction of at least 20%. If a producer has a process that doesn’t fall in line with EP3 mandates, they can petition to show that their process does generate total emissions at 20% or less compared to gasoline.
The EP3 petitions always require producers to provide information related to upstream emissions, process emissions, downstream emissions and lifecycle emissions. All of those emission numbers are used to generate what the EPA believes to be the percentage reduction in GHGs. Of the EP3
petition awardees since March 2024, most show reductions in process and lifecycle emissions, with some producers also showing a reduction in upstream emissions.
Most baseline corn starch numbers used by EPA are still categorized in one of four possibilities. In the first, a plant petitioning for additional RIN generating capacity would need to deploy all of the following: dry mill process; powered by
natural gas, biomass or biogas; and at least two advanced technologies from the approved technology list. The basics of the approved technology list include some form of corn oil fractionation, membrane separation, raw starch hydrolysis or a combined heat and power (CHP) technology.
The second option to generate a D6 RIN includes a dry mill process; power from natural gas, biogas or biomass; at least one of the advanced technologies; and drying of no more than 65% of the DDGS annually.
The third option requires the same power requirements of the previous two options, none of the approved technologies, but drying of no more than 50% of the DDGS annually.
The fourth option is for wet mills and requires biomass or biogas for process energy.
To generate a D6 RIN from starches from crop residue and annual cover crops, producers must ferment using natural gas, biomass or biogas for process energy.
D3 RINS, unlike D6, can be processed in any fashion, as long as they convert cellulosic biomass to fuel.
Most of the recent EP3 awardees dating back to March 2024 have been granted the ability by EPA to update their compliance monitoring plan to include D6 and D3 RINs based on the grounds that they were, could potentially or might consider producing ethanol using both corn starch and corn kernel fiber feedstocks.
KAAPA Ethanol Holdings out of Nebraska for example, granted a petition in 2025, showed a GHG reduction of 22.9%. E Energy Adams, also granted a petition in 2025, came in at a GHG reduction of 25% and was granted the ability to produce D6 and D3 RINs. Hub City Energy, awarded as part of a large group of petitions dated November 2024, showed a 21.4% GHG reduction. Heron Lake Bioenergy, another November 2024 awardee, came in at almost 30% GHG reduction. Redfield Energy out of South Dakota showed a 27.9% GHG reduction. Hankinson Renewable Energy recorded a 30.3% reduction.
While there is a clear pattern of dry mill ethanol producers reducing their GHG emissions, any additional benefits to reducing CI scores won’t equate to changes in EPA’s administration of the RFS and RIN model, the agency says.
“Many modern dry mill ethanol plants can demonstrate they already meet the statutory 20% GHG reduction threshold for corn starch ethanol,” the EPA spokesperson says. “While the EPA supports process efficiency improvements for many reasons, due to the structure of the RFS statute, further CI improvements will not change the number or type of RINs these facilities can generate under the program.”
Miller says the new testing methods that allow producers the ability to unlock the cellulosic content from corn kernel fiber makes this an exciting time for the industry. “However, there are several RFS compliance nuances related to the LCFS program that all producers of D3 RINs from CKF should be aware of,” he says, reiterating the need for a QAP.
While the effects of streamlined CKF measurement and EP3 inclusion is just beginning to play out, a story of growth is unfolding. According to the EPA, more than 1.1 billion D3 RINs were generated in 2024, a tiny fraction (43.3 million) of which was for cellulosic/CKF ethanol; the balance was for renewable natural gas. But there were only 1.3 million D3 RINs generated for cellulosic/CKF ethanol in 2023. So, in fact, RIN generation in that category expanded by more than 3,000% year over year, which is consistent with the rise in EP3 approvals and the improved CKF methodology that unfolded in 2024. So far this year, data for January 2025 shows that 7.3 million D3 RINs were generated for cellulosic/CKF ethanol in that month alone, suggesting that a doubling of last year’s total is possible.
Author: Luke Geiver writer@bbiinternational.com
April 22 - 24, 2025
JW Marriott Minneapolis / Mall of America Bloomington, MN
• An evolution of the biofuels financial conference
• Network with like-minded agribusiness professionals
• Located at the famous Mall of America
• Hands-on training with industry leaders
Scan to registerforthe 2025 Beyond Innovation Conference. Limited seating available, so act now!
Trucent utilizes decades of experience and detail-oriented service to fix problems and find novel solutions.
By Katie Schroeder
Offering turnkey solutions for corn oil extraction, Trucent provides ethanol producers with innovative science and data-driven solutions to process problems. As one of the first companies to introduce corn oil extraction technology to the ethanol industry, Trucent continues to leverage internal data to refine existing technology, address emerging industry challenges and capture new opportunities, explains Chris Clausen, director of technology for Trucent’s Bioprocess Solutions. “We really focus on having science and data-driven designs and adapt to evolving customer needs as our industry shifts,” he says.
Beyond its flagship Corn Oil Separation System (COSS), Trucent has introduced a variety of products in response to feedback from producers and analysis of internal data, such as TruShield, a pretreatment and protection system that can be integrated in front of any separation system, protecting expensive equipment and increasing efficiency; and TruDose, an automated “smart” dosing system with real-time adjustment for chemical additions.
Clausen emphasized that Trucent innovation is driven by a robust analysis of internal performance metrics—from parts usage trends to service technician insights—
that fuel collaborative engineering sessions and drive new product developments. This data-driven approach ensures that every improvement is implemented to address real challenges.
The “why” driving Trucent’s product development team is that any new products or improvements help solve customer problems, reduce capital expenditures, enhance DCO quality and improve overall system reliability.
The Trucent Team
Decades of Innovation, Proven Results.
Precision Solutions
Research, advanced engineering, lab analysis, and custom solutions to optimize your system and process.
Experience-driven start-up, maintenance, and service to enhance system reliability, efficiency, and long-term operation.
Ongoing support tailored to your process, with Trucent certified technicians, over 25,000 in-stock parts, and an innovation team dedicated to making impactful improvements.
By CEM Corporation
In ethanol production, whether through wet or dry milling, one of the most crucial factors in optimizing output is the careful control of oil extraction. During the milling process, maximizing the oil extracted from the raw materials is vital, as incomplete extractions can leave valuable oil behind, resulting in inefficiencies and lost revenue. While dry milling is a more cost-effective approach, it comes with a higher risk of incomplete oil extraction. CEM Corporation offers a solution to this challenge with the ORACLETM system, designed to accurately analyze oil content thus ensuring more complete and efficient oil recovery.
The ORACLE system provides rapid and precise oil content analysis in just 30 seconds, without the need for calibrations. It can accurately analyze any sample from DDGs to DCO, stillage to syrup, and more, allowing
ethanol plants to assess oil content at various stages of the process. This fast, reliable analysis helps ensure that plants can make necessary adjustments to their milling processes to optimize recovery and prevent the waste of valuable oil. Additionally, the system eliminates the need for dangerous solvents and minimizes the risk of operator errors, making it both safer and more efficient than traditional methods.
Even high-yielding ethanol plants typically recover only about 50% of the available oil. The introduction of the ORACLE system provides plants with valuable insight into where and how much oil remains throughout the process. This rapid injection of information allows operators to adjust milling conditions, leading to more efficient operations and higher yields. The ability to test the corn product at every stage of the milling
process—whether in solid, liquid or slurry form—demonstrates the system’s versatility.
The ORACLE system is also more repeatable and reliable than conventional extraction techniques, such as Soxhlet, providing consistent results that plants can trust. This repeatability allows for more reliable outcomes, ensuring that production remains optimized across various processes and conditions.
To further enhance the value of coproducts, the ORACLE system can be paired with CEM’s SMART 6TM moisture/solids analyzer. This enables precise moisture analysis, improving the shelf life and quality of coproducts, like DDGs, and increasing their market value. By providing a complete solution for oil analysis, the ORACLE system helps ethanol plants achieve better results while maximizing their bottom line.
New technologies push DCO production to record highs.
By ICM
Since distillers corn oil (DCO) entered the ethanol industry as a high-value coproduct, producers and technology providers have worked long and hard to find ways to maximize the amount of DCO they could recover. Early on, DCO yields greater than 0.5 pounds per bushel were acceptable, and within a few short years, 0.75 pounds per bushel became a sustainable yield. Then, for years, yield trends crept higher, with whispers and rumors of some producers being able to achieve DCO yields of 1.0 pound per bushel or higher.
But recent press releases have been much louder than whispers, with numbers significantly higher than 1.0 pound per bushel blowing past previous industry standards. Ethanol producers are seeing breakthroughs, thanks to new technologies and an evolved focus on whole-plant optimization.
ICM’s FOT Oil RecoveryTM is setting a new standard for DCO recovery. It has helped plants achieve numbers that were once thought unattainable.
“Distillers corn oil is the most valuable product an ethanol plant sells on a per pound basis,” says Nick Bowdish, CEO of Elite Octane. “We were consistently extracting just more than 1.0 pound per bushel, but we try to challenge ourselves to not get complacent and instead stay focused on generating more value out of every bushel of corn we process. When ICM presented their FOT Oil Recovery technology to us, it just made sense that a new mechanical solution to recover the oil leaving the plant in our distillers grains solids would let us take
the next step. We have achieved an average extraction rate of 1.31 pounds per bushel in our Atlantic facility since the FOT Oil Recovery technology came online in April 2024.”
ICM is not only introducing a breakthrough technology but also challenging how the industry measures success in DCO recovery.
“Not every plant is starting with the same opportunity,” explains Chuck Gallop, director of innovation with ICM. “Distillers corn oil ‘production’ is a misleading statement, because there is nothing we are doing in the process to ‘produce’ the oil.”
By using percent recovery as a performance metric alongside yield, ICM provides a more comprehensive view of a plant’s potential. Percent recovery offers producers a better understanding of the theoretical maximum recovery, which depends on the crude fat percentage of the incoming corn. At the same time, reported yield is an essential metric for tracking improvements over time. Together, these metrics empower producers to better evaluate their performance and identify areas for optimization. The table above serves as a reference guide for what can be achieved with ICM’s FOT Oil Recovery technology, depending on all these variables.
James Broghammer, CEO of Pine Lake Corn Processors, agrees and expands on the challenges: “Potential is first and foremost
Continued on page 40
Continued from page 38
dependent on the amount of oil in the incoming corn, which changes every growing season and depends on the region. From there, it is on us to make it available, keep it available and recover it. That’s what ICM has helped us do. Their technology has allowed us to maximize recovery, ensuring we capture as much value as possible from every bushel.”
ICM’s FOT Oil Recovery system underwent extensive validation before being introduced to the market. To ensure its performance and adaptability, ICM conducted onsite trailer testing at more than 20 commercial facilities, collecting comprehensive data across a variety of operational conditions.
“Testing across multiple facilities allowed us to fine-tune the technology and gather the data to prove its value,” says Shaun Hubler, ICM’s director of technolo-
gy commercialization. “This process wasn’t just about validating performance; it was about earning the trust of our customers. We know FOT Oil Recovery works, and we have the results to back it up.”
ICM’s FOT Oil Recovery technology is part of a broader, whole-plant approach that evaluates every aspect of the ethanol production process. This comprehensive strategy includes fat mapping, a method to monitor fat migration throughout the entire plant. By tracking where and how fat moves within the system, ICM can identify opportunities to maximize recovery and address inefficiencies.
Recent projects using FOT Oil Recovery have achieved DCO yields exceeding 1.35 pounds per bushel (80% recovery) while significantly improving energy consumption. These numbers resonate with board members, investors and plant manag-
ers alike, showing the potential for greater profitability and long-term competitiveness.
With the ethanol industry setting new standards for DCO recovery, the race is on for producers to adopt the latest technologies. Board members and investors are beginning to ask their plant managers the critical questions: Are you doing enough to maximize the value of every bushel of corn? What steps are being taken to keep up with industry leaders?
ICM’s FOT Oil Recovery technology is not only exceeding expectations. It’s creating a shift in how the industry thinks about DCO performance. By embracing this whole-plant perspective, ethanol producers can confidently join the chase, secure in the knowledge that they are investing in a more profitable and sustainable future.
our future