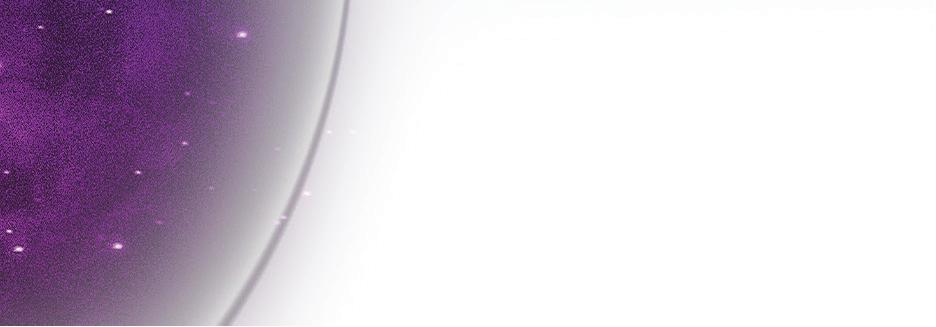
2 minute read
So Much More to Learn
It’s well known that ethanol plants are a great source of 99% pure, biogenic CO2. And not only is it ideal for sequestration, but for transforming into myriad biobased fuels and chemicals. A white-hot new segment of CO2 utilization is the pursuit of electrofuels, or e-fuels, and it’s showing up in our headlines often. Earlier this summer, for example, e-fuels developer Infinium and Navigator CO2, a carbon dioxide aggregator, announced a partnership to deliver 600,000 tons of CO2 per year from the latter company’s proposed pipeline system to a future Infinium biorefinery. When that news broke, we were already working on another story about e-fuels, albeit from the angle of public sector research.
In “CO2 Utilization: Biofuel from the Stack,” on page 12, we look at R&D aimed at commercializing e-fuels from ethanol plant fermentation CO2, ideally paired with renewable energy like wind power. We explain how the U.S. Department of Energy is working with labs across the country (NREL, Berkeley, Argonne, Lawrence Livermore and Oak Ridge) to elevate e-fuel pathways from the lab to commercial scale. The idea is that, through one of several possible conversion routes, an ethanol plant’s CO2 can be converted into ethanol or another intermediate, then upgraded to a drop-in fuel like SAF. It will be interesting to see if and how e-fuels reach commercialization at the intersection of public research and private sector investment.
Next, in “Growing A Knowledge Tree,” on page 20, we look at how multi-plant executive management can enhance opportunities for information and resource sharing between facilities. As the story explains, multi-plant executive management allows for production synergies, mistake avoidance, solutions sharing and the exchange of advice on any number of issues a facility might experience. The executives we talked to had like-minded beliefs—and similar hands-on approaches—geared toward fostering plant cultures that value communication, or as one CEO put it, a “learner mindset” to build trust between personnel working together at the same location or hundreds of miles apart.
Speaking of fostering a learner mindset, this year marks the 20th anniversary of a corn ethanol R&D hub that’s helped train hundreds of industry professionals while advancing innumerable production technologies—The National Corn-to-Ethanol Research Center at Southern Illinois University-Edwardsville. As we report in “NCERC’s 20 Years of Impact,” on page 28, the facility, under the leadership of John Caupert for the past 17 years, has been a dependable outlet for entities ranging from multinational corporations to small startups looking to test, validate or improve a component of the ethanol production process. Almost every ethanol plant in the U.S. is using at least one technology or product that has some connection to NCERC. But for all that Caupert and his team have previously accomplished, this milestone seems to be more about NCERC’s future than its past.
Finally, be sure to read “Taking A New Crack at the Cellulosic Code,” on page 36, which chronicles the vision of a Florida company chasing what others have struggled to accomplish at scale—the production of ethanol from cellulosic biomass. We explain how Blue Biofuels intends to convert 15-foot-tall king grass—managing the feedstock itself—into low-carbon biofuel. Making commercial quantities of ethanol (and lignin) from purpose-grown biomass has proven troublesome for other companies in the past, but true visionaries are rarely deterred by what others have failed to achieve.
MEET TODAY’S GOALS. ANSWER TOMORROW’S QUESTIONS.
SOLUTIONS, DESIGNED BY LBDS.
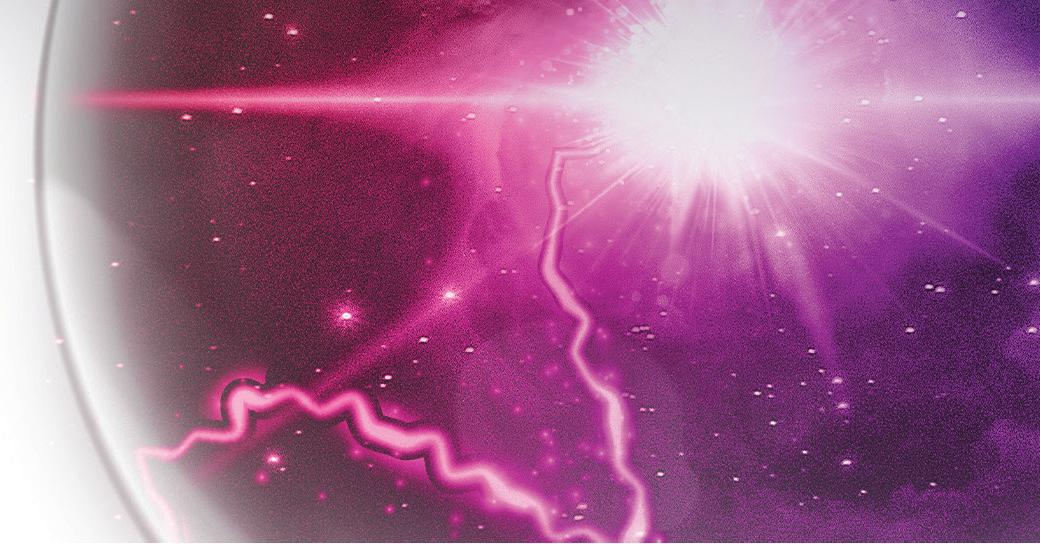
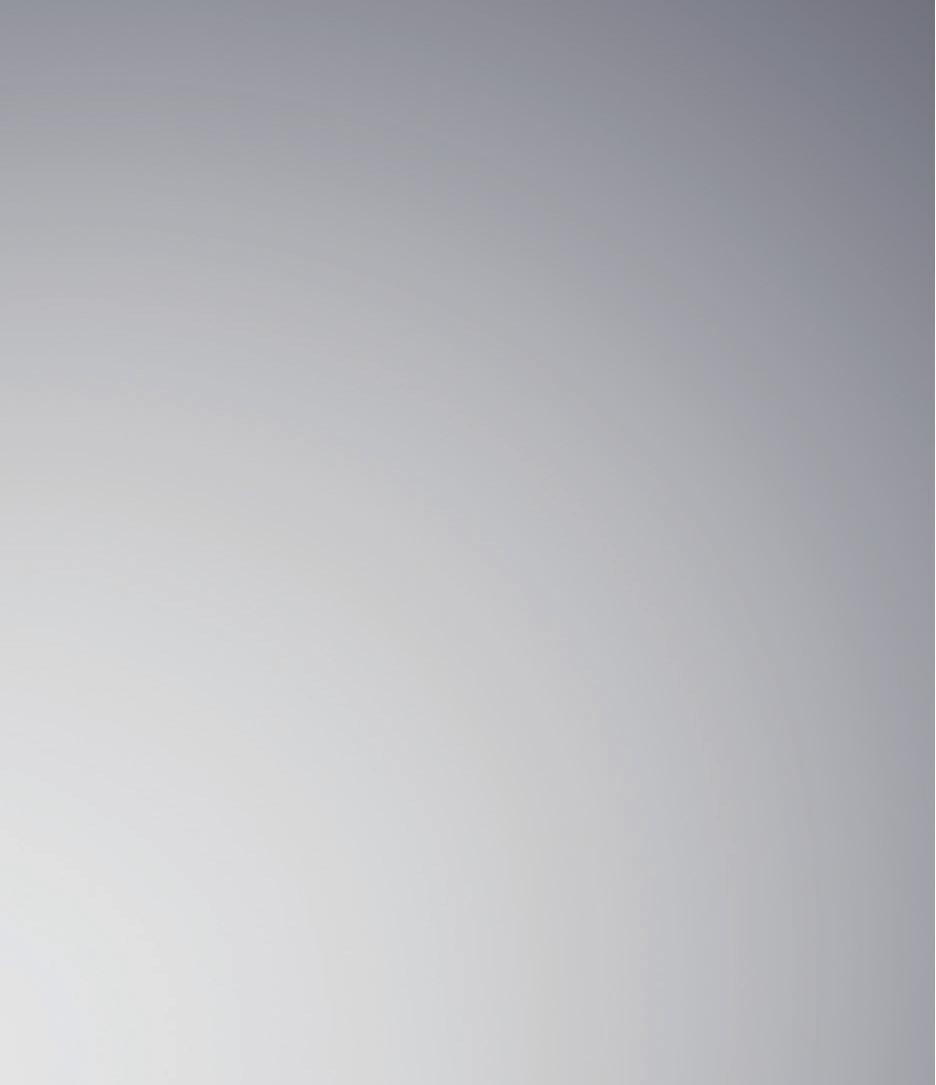
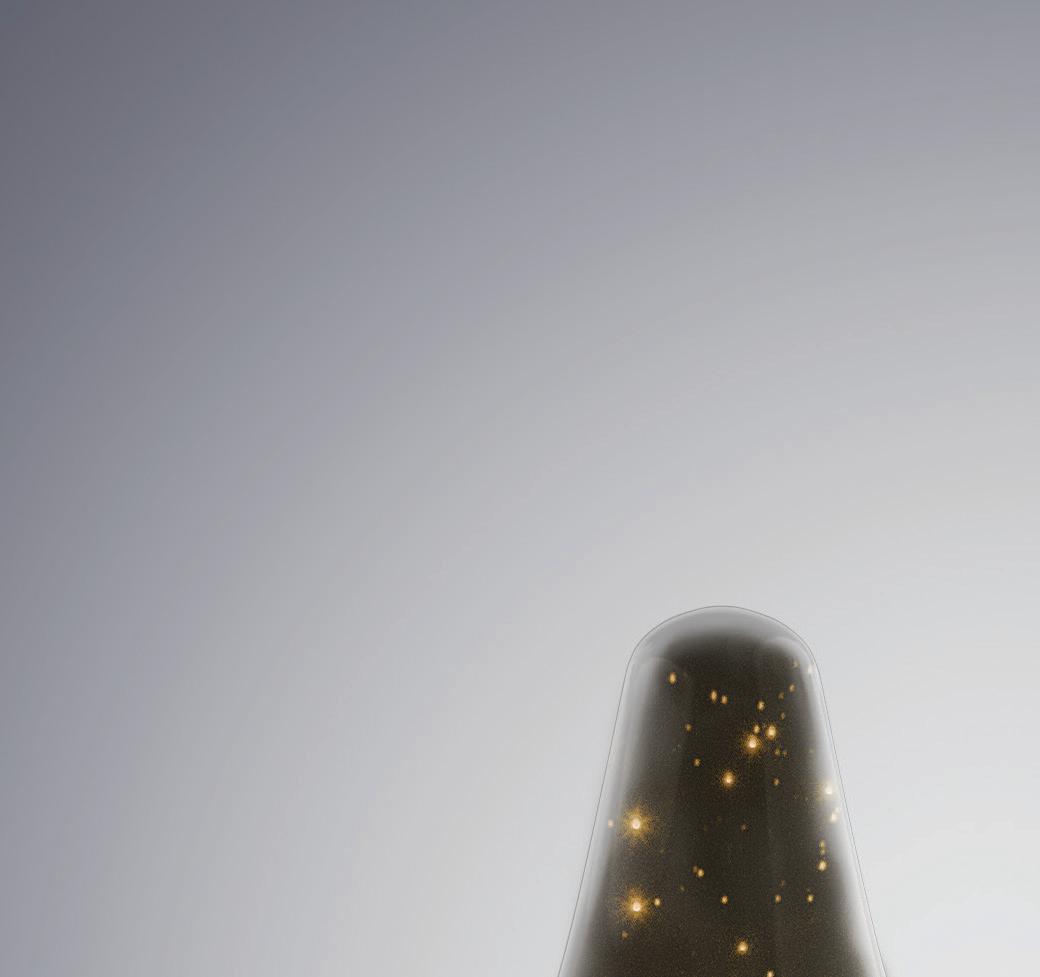
We put Fermentation First™. You get yeast, yeast nutrition, enzymes and antimicrobial products, alongside the industry leading expertise of our Technical Service Team and education resources. Find the right solution for your ethanol business at LBDS.com.
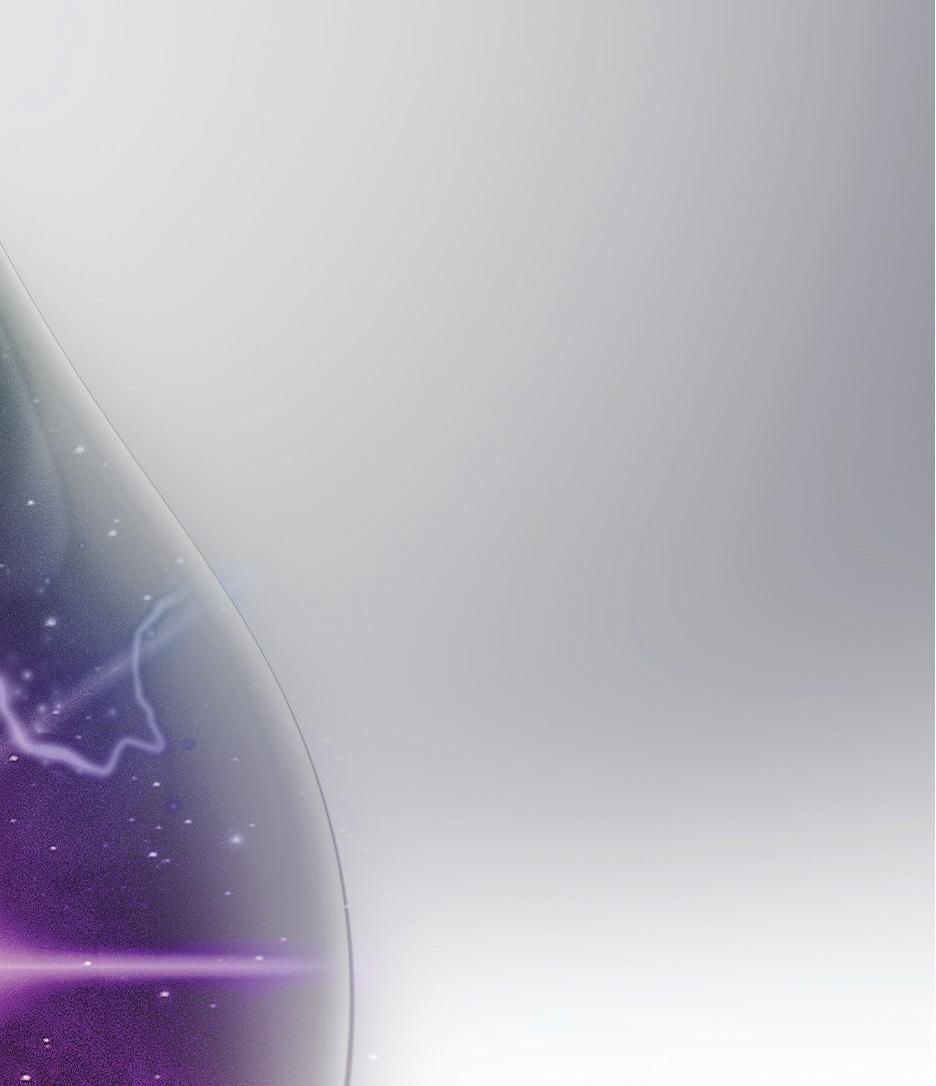
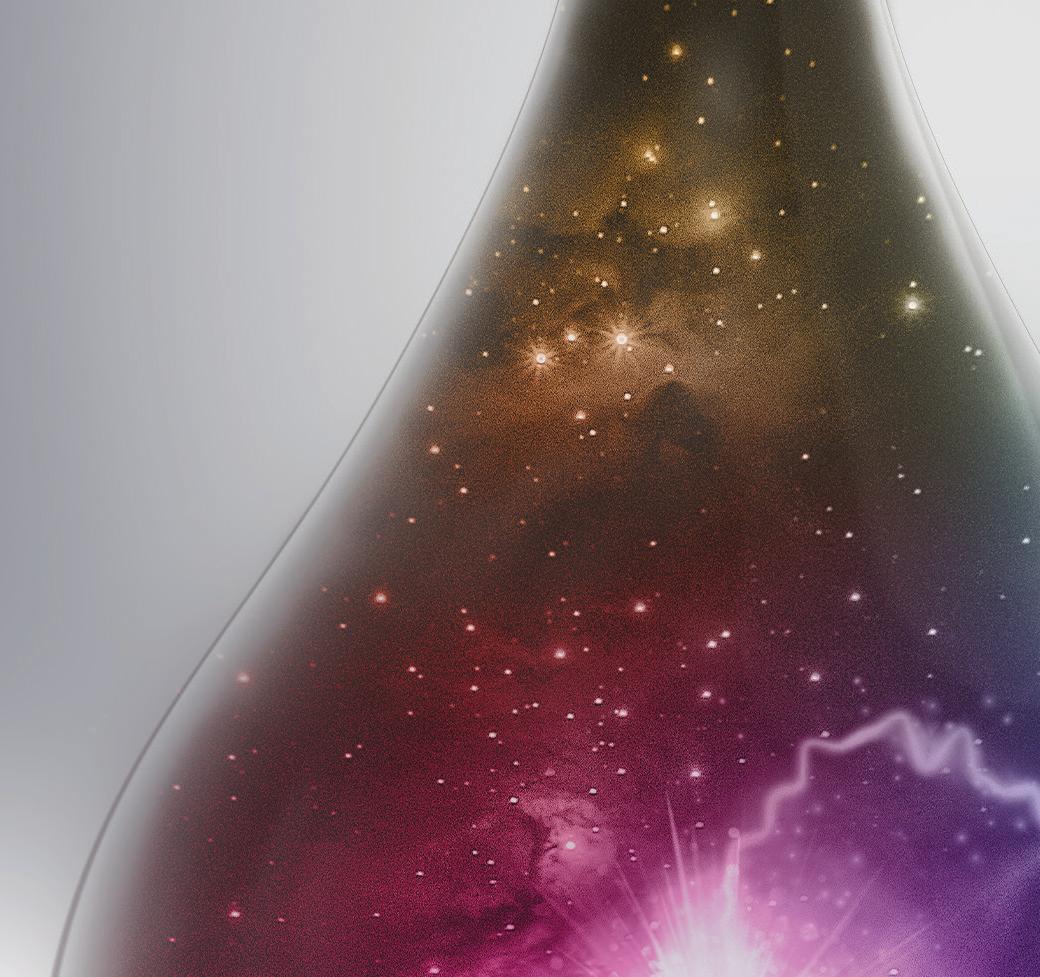
gcooper@ethanolrfa.org