
8 minute read
OUTLOOK
THE LONGVIEW: POET Founder and CEO Jeff Broin says his company will continue to diversify and innovate as it strives for major carbon reductions in the years ahead. POET is the largest biofuel producer in the world.
PHOTO: POET
SOLUTIONS AT THE SURFACE
POET Founder and CEO Jeff Broin reflects on the growth of his company, its pledge to explore new technologies, discover new products and lead the industry toward ultra-low carbon bioethanol. By Tom Bryan
When POET acquired six Flint Hills Resources bioethanol plants in June, it added 730 million gallons of annual capacity to its portfolio, lifting the company to 3 billion gallons, expanding its fleet of bioprocessing plants to 33 and reinforcing its status as the world’s largest biofuel producer—of any
kind. Those numbers are not lost on Founder and CEO Jeff Broin, but he frames the deal not in the context of new volume, but new people.
“We didn’t just acquire some great plants, but 370 new team members,” he says, explaining that POET, based in Sioux Falls, South Dakota, now has more than 2,200 personnel across eight states. “We are absolutely excited about what has been accomplished with the acquisition, and the expansion of our team is a big part of the story.”
The opportunity to acquire the FHR plants came at POET quickly, and Broin credits the company’s experienced management team for rapidly executing on the purchase and integrating the facilities into POET’s fleet over the summer. In addition to the six plants, the acquisition included two terminals and FHR’s high-protein feed business, NexPro, which POET is maintaining while assessing its position as a hi-pro feed supplier. The acquired facilities range from 100 MMgy to 130 MMgy, with five in Iowa and one in Nebraska. The six biorefineries produce 1.5 million tons of distillers grains and 170 million pounds of distillers corn oil (DCO) annually. Unlike POET’s other biorefineries, the acquired FHR plants do

TEAM BUILDING: When POET acquired six Flint Hills Resources bioethanol plants in mid-2021, it expanded its production volume by 730 million gallons and gained 370 skilled personnel, including the team members shown here at the company’s Fairmont, Nebraska, facility.
PHOTO: POET
not currently possess the company’s patented raw starch hydrolysis platform, BPX. “The former FHR plants are conventional,” Broin tells EPM. “It will take time to determine what changes might be made in the future.”
The impact of the deal, possibly the largest in ethanol industry history, is hard to overstate. In addition to its ability to produce nearly 3 billion gallons of ethanol annually utilizing 930 million bushels of corn—roughly 6% of the U.S. crop—POET now produces 14 billion pounds of distillers coproduct (in multiple forms), 975 million pounds of DCO, and 6 million tons of commercial CO2. Plus, two of the company’s plants produce purified alcohol, both grain neutral spirits (GNS) and USPgrade alcohol.
Perhaps the figure that matters most to Broin, however, is 40,000. That’s the number U.S. farmers that supply corn to POET’s bioprocessing plants. “For us, this has always been about agriculture and capturing more energy from the surface of the earth,” he says. “Our growers aren’t just delivering corn, but leading the way with regenerative, climate-friendly agricultural practices.”
Net-Zero Quest
Low-carbon agriculture, and pending market-based credits associated with it, will likely play a key role in POET’s ability to meet its ambitious carbon intensity reductions. In September, the company released its inaugural environmental, social and governance (ESG)
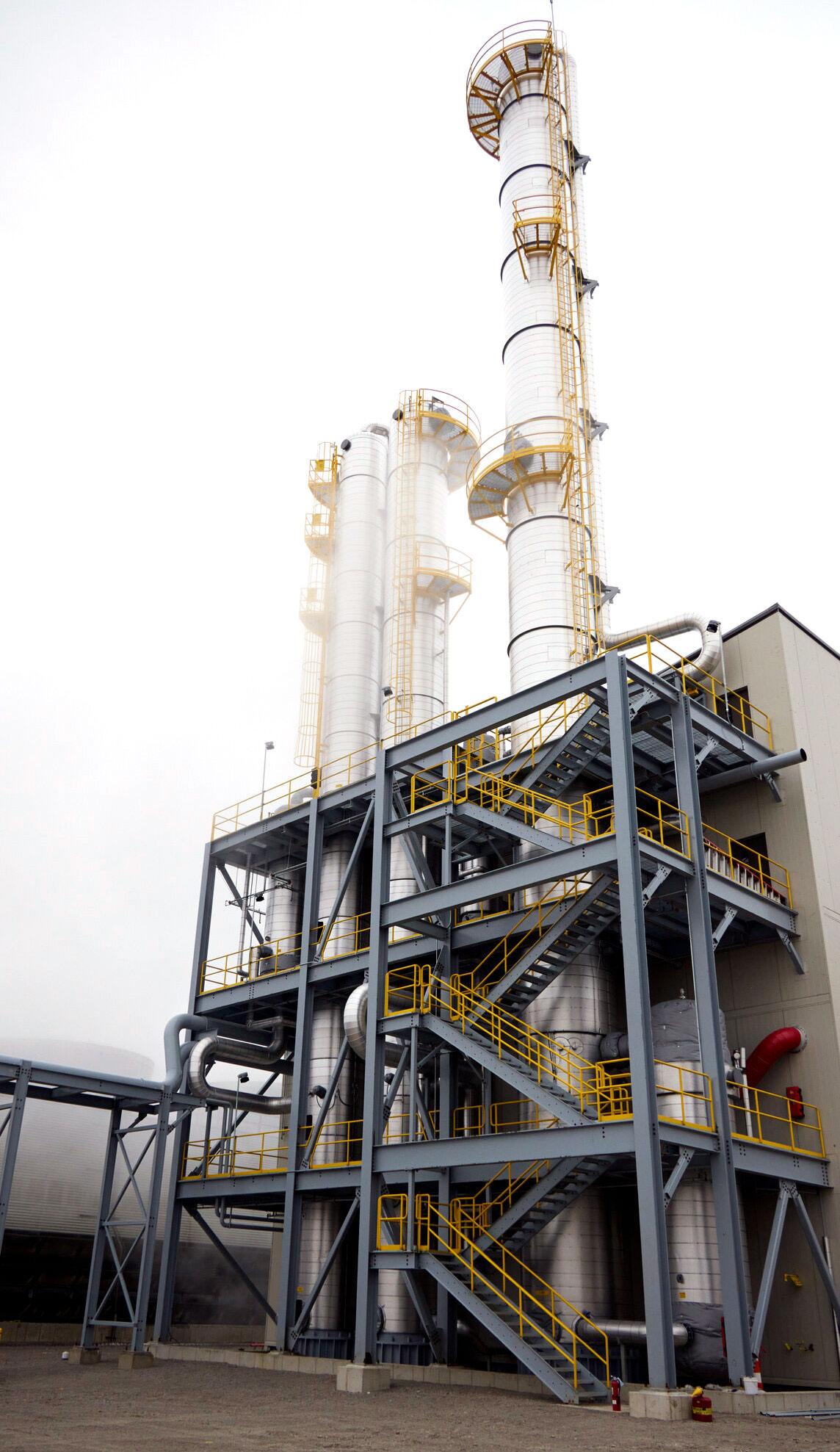
HIGHER LEVEL: With high-purity alcohol production now online at its bioprocessing facilities in Leipsic, Ohio (shown here), and Alexandria, Indiana, POET is producing both USP-grade alcohol and grain neutral spirits (GNS).
PHOTO: POET
report, titled The Sun, the Soil & the Seed, detailing POET’s 34-year journey as a pioneer in the renewable energy sector, along with its progress in developing biofuels and a growing suite of plant-based bioproducts while maintaining a tradition of environmental stewardship, technological innovation, and a renowned workplace culture. The report included POET’s target of achieving net-zero carbon emissions from its fleet of bioprocessing facilities by 2050 and a GHG emissions reduction of 70 percent compared to gasoline by 2030 (as compared to an industry-wide average of 46 percent less GHG emissions than gas today).
“Low-carbon farming can and will play a key role in this,” Broin says. “With the right incentives in place, we believe farmers will embrace opportunities to accelerate our industry’s drive toward net-zero with bioethanol made from low-carbon grain.”
The ethanol industry’s quest for ultralow carbon biofuel has been widely defined as a three-pronged approach: continued efficiency gains through technology adoption
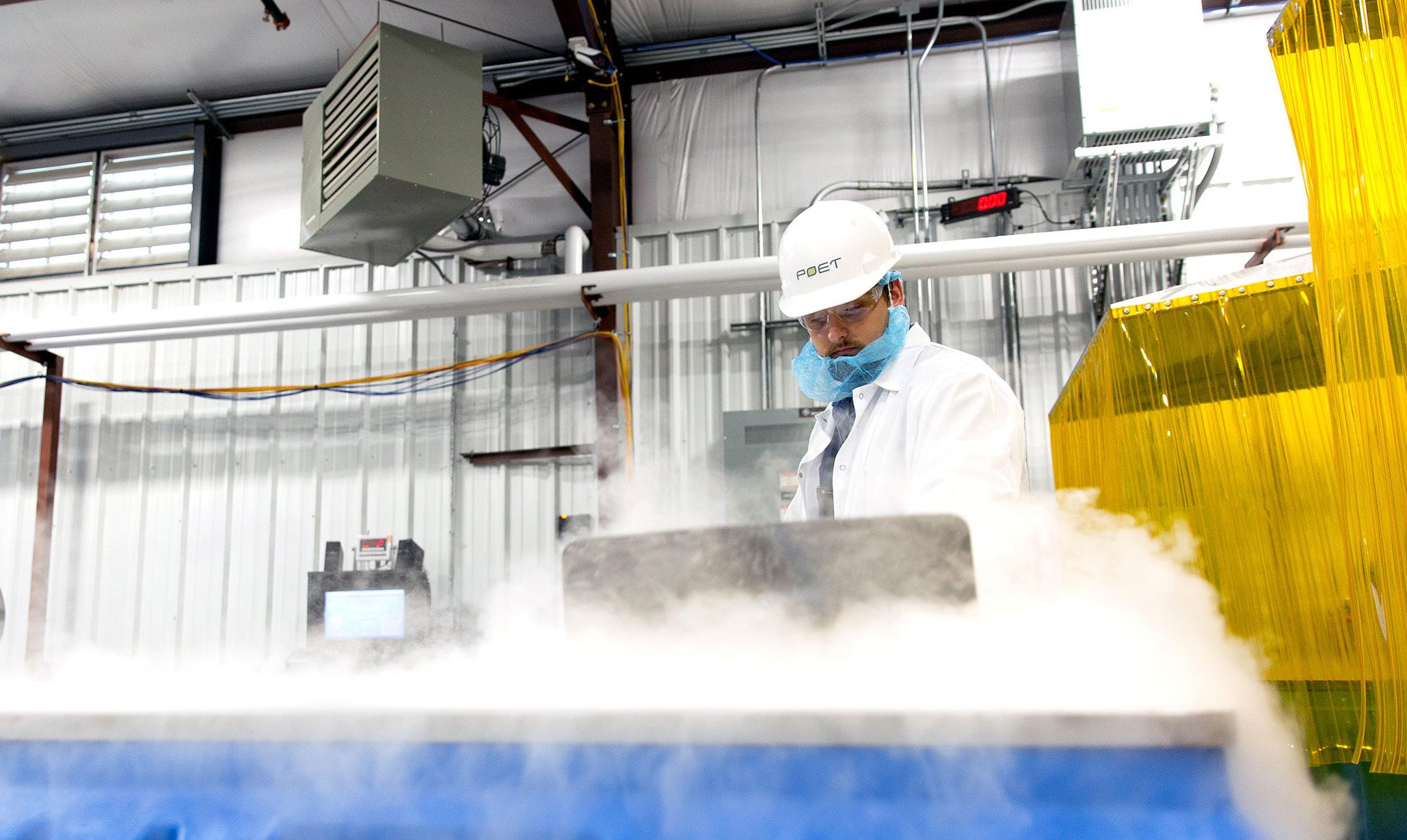
PURE PRODUCTS: POET currently produces 6 million tons of CO2 for commercial use and is one of the fastest-growing renewable CO2 distributors in the U.S., with over a dozen manufacturing facilities across the Midwest.
PHOTO: POET
and process innovation (a key pillar for POET); low-carbon farming (with the right carbon accounting and incentives in place); and, for many producers, carbon capture and sequestration (CCS). As of September, more than 50 U.S. ethanol plants had engaged in the early stages of CCS, many signing on to participate in CO2 aggregation via future pipelines, others independently exploring CCS through onsite test wells, regulatory approvals or feasibility analysis.
POET, however, with the largest commercial CO2 capture operation in the industry, seems to be forging its own path forward while maintaining keen interest in CCS. The company has a fully integrated renewable CO2 and dry ice branch, POET Pure, that supplies CO2 to customers in beverage carbonation, food processing and other industries nationwide. So, while other producers line up for CO2 sequestration, POET’s Carbon Strategy Team is studying carbon reduction from every possible angle while maintaining its role as an essential commercial CO2 provider.
“Carbon capture is exciting, but we think there are several technologies that can help the industry lower its carbon footprint,” Broin says. “We are evaluating several of those technologies and expect to make decisions soon in terms of what we might pursue. There are several ways to achieve reductions, and it will be critical to have state and federal policy support to help the industry reach these goals.”
It is vital, Broin says, for the ethanol industry, along with agriculture, to unite around opportunities for facility-level carbon reduction technologies such as combined heat and power (CHP). “If there are incentives to compress CO2 and inject it into the ground, there should be incentives for equivalent carbon avoidance at the plant level,” he says. “Carbon capture and storage is a great opportunity but using biomass for process heat is another proven way to lower carbon intensity, and it merits similar credit.”
Broin continues, “If you take a bioethanol plant and incorporate CHP from biomass— eliminating natural gas—that should get the same carbon intensity credit as injecting CO2 into the ground because you’re eliminating carbon in both scenarios. I’m a supporter of carbon sequestration. I think it’s fantastic, but the government needs to give us the opportunity to use biomass, biowaste, ag waste and process streams to displace fossil fuel use. At the end of the day, they’re just different strategies with the same objective: eliminating carbon emissions from fossil fuels.”
Embracing Change
Through continuous innovation, POET has reduced its annual energy use, on a per plant basis, by 18% since 2005, and lowered its water use by 20% since 2007, while increasing ethanol yield by 8%. The company’s Chancellor, South Dakota, bioprocessing plant uses steam generated from biomass combustion and methane gas pipelined from a landfill near Sioux Falls. Nearly half of all POET plants now utilize energy-efficient, steam-powered turbines that generate electrical energy from process steam. In October, the company completed the instal-
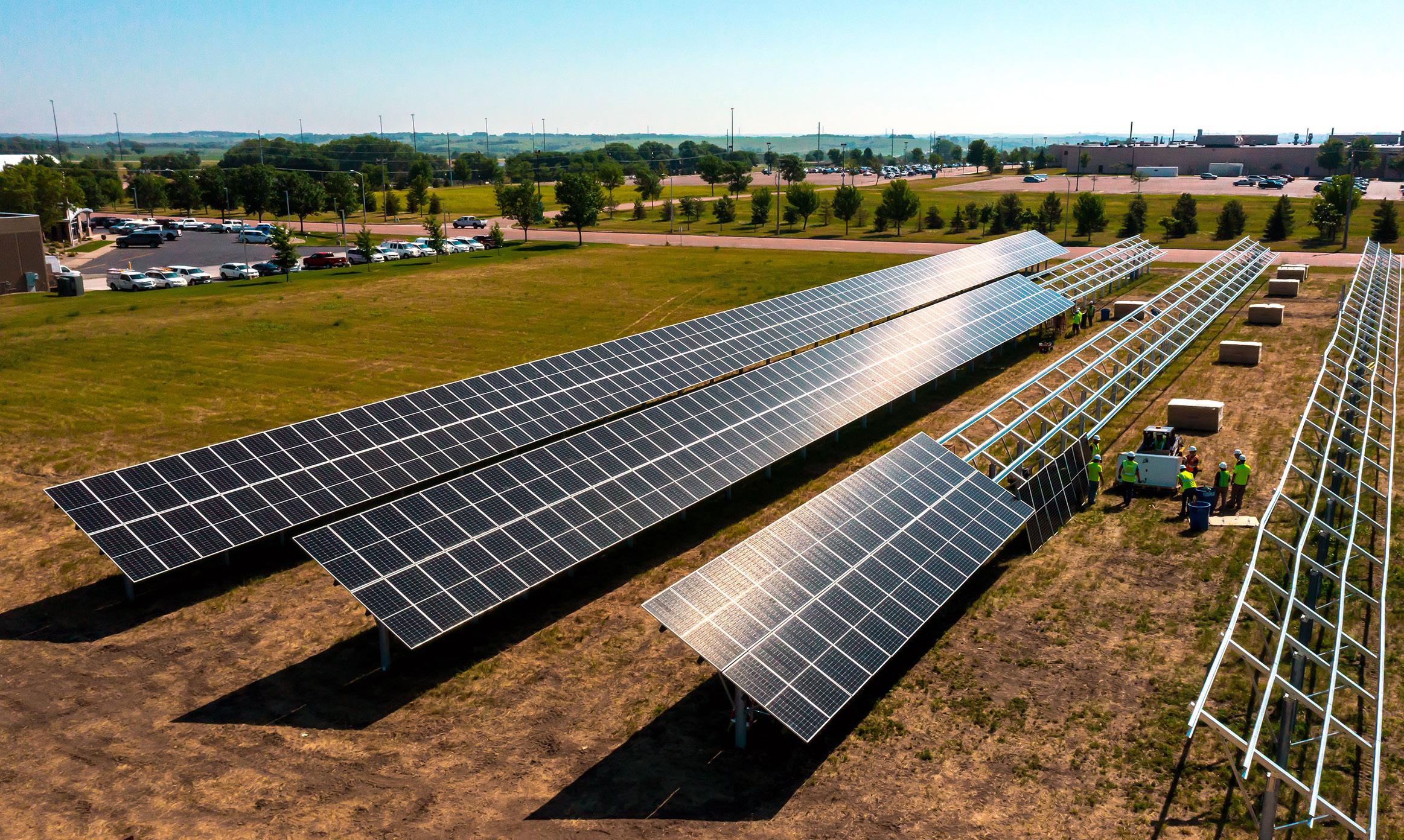
ENERGY ONSITE: In October, POET completed the installation of a 400 kW solar farm at its headquarters in Sioux Falls, South Dakota, which will power the company’s office building and send excess power to the local grid.
PHOTO: POET
lation of a 400-kW solar farm at its headquarters in Sioux Falls—the largest solar installation in the city—which will generate enough energy to power the POET office building and send any excess power to the local grid. POET is even evaluating the potential of solar energy at its bioprocessing plants.
The solar installation is just one more example of Broin’s embrace of renewables, rooted in his long-held belief that fossil fuels can be replaced by biobased energy—which is ultimately a derivative of solar energy—produced at the surface of the planet. “We are big believers that we need to return to the surface of the earth,” he says. “There are a multitude of products that can be derived from the sun, soil and seed,” he adds, pointing back to the company’s ESG report and its aspirations for carbon neutrality.
Paradoxically, climate change indifference does persist in both agriculture and biofuels, but Broin doesn’t struggle with it. “I think there is clear evidence that the planet is warming, and agriculture is seeing the effects of it,” he says. “You look at the changes in weather patterns, temperatures, the frequency of extreme storms, and I think we all see some change.”
But regardless of opinions on climate change, Broin says, embracing a clean energy future is an easy choice. “Why not do everything you can to leave the world as good or better than you found it?” he asks. “Again, I think that starts with a return to the surface of the earth and a move away from fossil-based energy. Why not do what we can?”
Author: Tom Bryan Contact: editor@bbiinternational.com
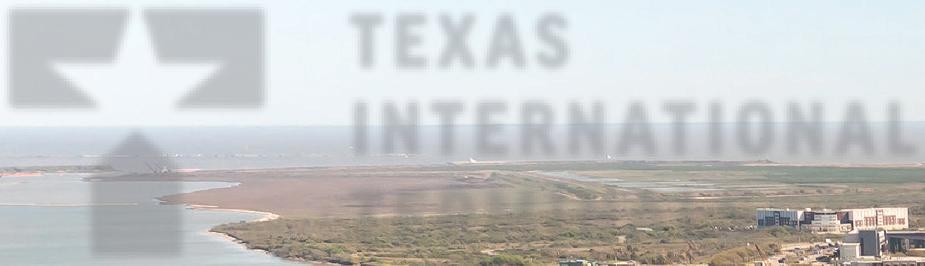
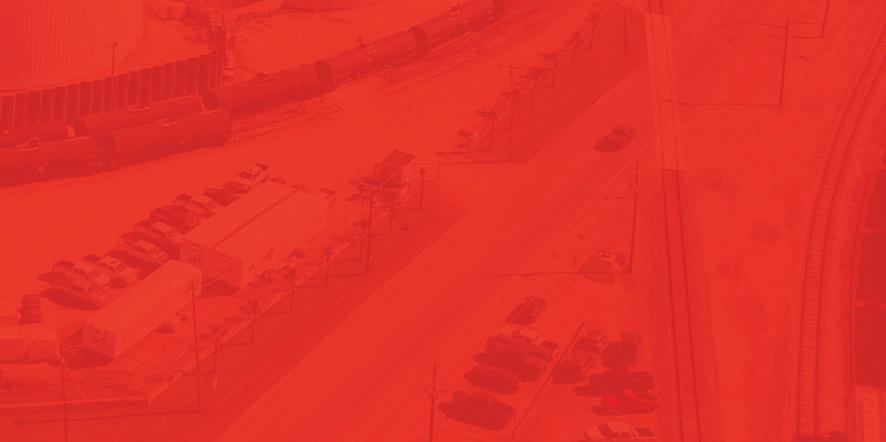

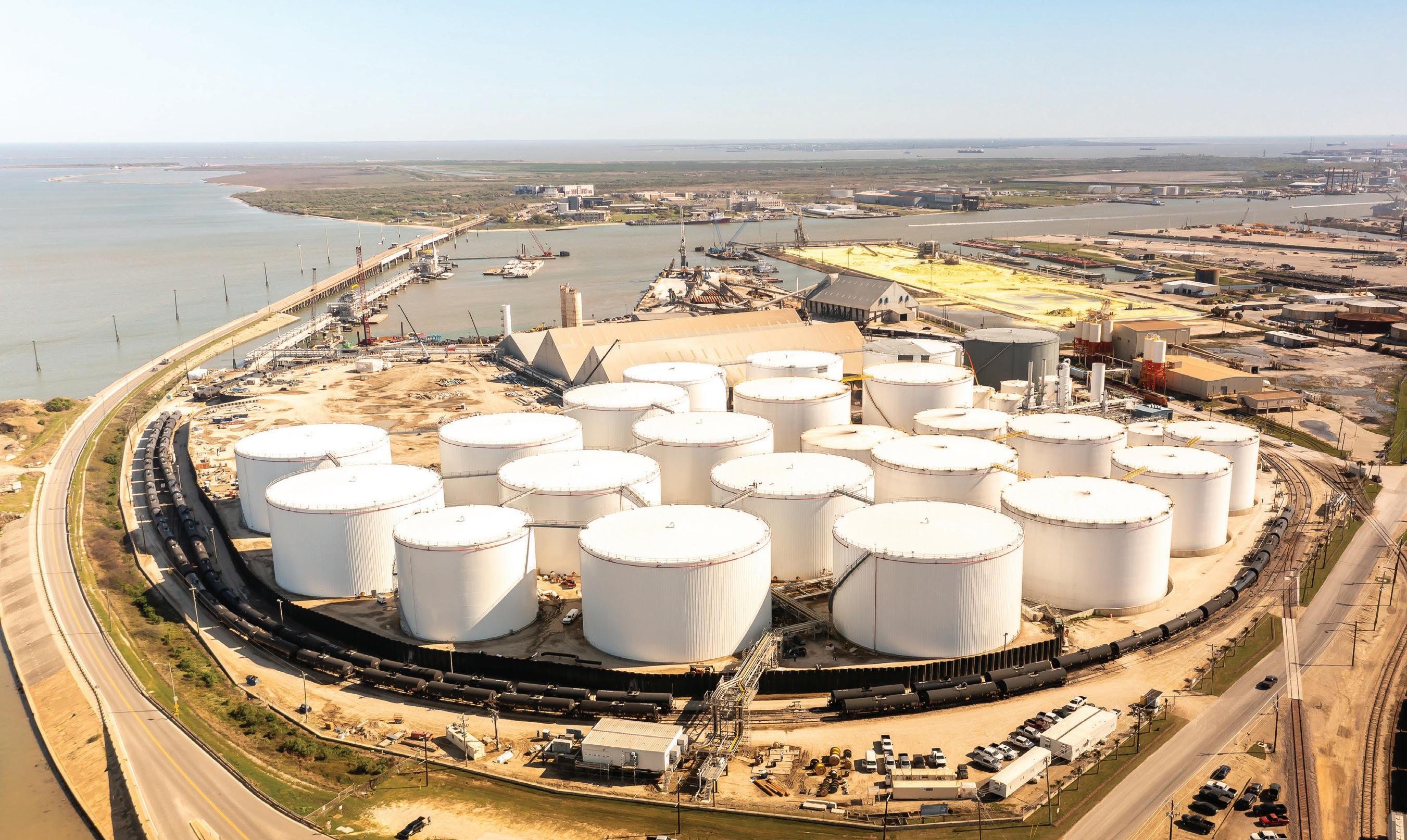
WE MOVE THE WORLD FORWARD.
RAIL, STORAGE AND MARINE CAPABILITIES
RAIL • UP and BNSF direct access • 160 railcar unloading spots, unload at 15,000 bph • Landing tracks capable of staging 4 unit trains • Unit train turn times of 24 hrs or less STORAGE • 2 million barrels of dedicated storage • Denaturant & bitrix blending • Foreign Trade Zone MARINE • 3 deep draft berths • Loading rate of 10,000 to 20,000 bph • 3 barge berths