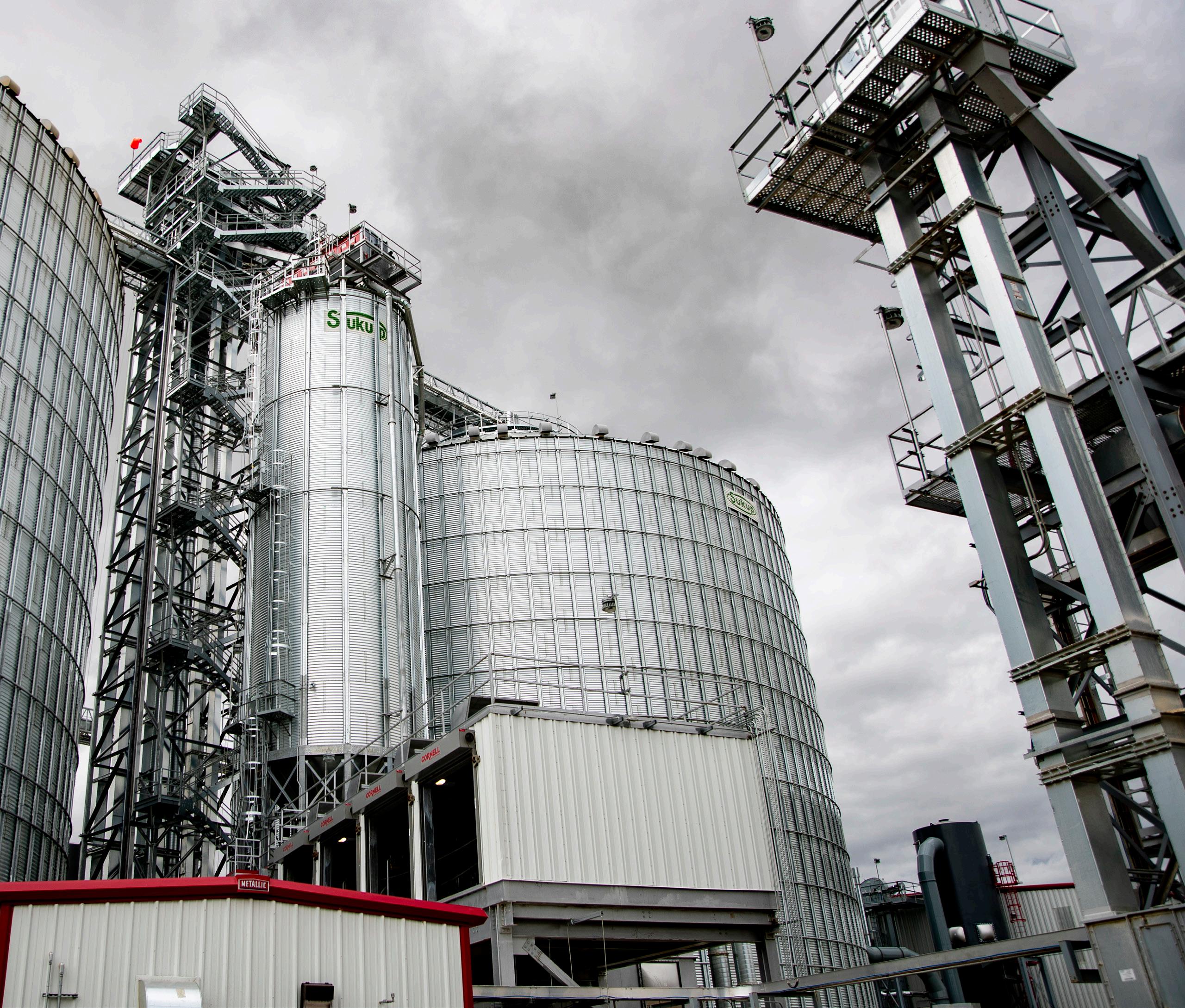
9 minute read
FEEDSTOCK
GRAIN STORAGE ON THE GROW
With a third of U.S. ethanol plants producing 100 MMgy or more, and most wanting at least 30 days of bin capacity, onsite grain storage has evolved. By Tom Bryan
With this year’s corn crop expected to top 15 billion bushels—the second largest harvest in history—and Iowa alone surpassing 2.5 billion bushels, another wave of grain storage expansion may be on the horizon in the Corn Belt, despite high steel prices and longer project wait times.
Such bumper crops amplify the need for more grain storage and, when prices are good, create an economic windfall that trickles over to on-farm and industrial improvements like grain storage. Farmers benefit from added grain storage by being able to hold onto their grain until prices are optimal. Likewise, ethanol plants upsize their storage for enhanced flexibility and control. “For ethanol producers, more storage is often an easy financial decision,” says Brent Hansen, commercial accounts manager at Iowa-based Sukup Manufacturing Co. “Grain bins are among the quickestpayback investments producers can make. If they can capture grain fresh out of the field near the end of the year, that’s about the best price they may see. Any volume you can get right away is going to typically help your margins.”
Hansen explains that producers also benefit from enhanced grain storage in the spring when growers are planting and unable to deliver their stored grain to the plant. “It’s not only about being able to accept that new grain in the fall,” he says, “but also having capacity to keep enough on hand to maintain control in the spring.”
When the majority of U.S. ethanol plants were built 10 to 15 years ago, most were 50 to 80 MMgy and sized their grain storage for 10 to 12 days of production. Anything above half a million bushels of storage was adequate. “Whether it was for cost reduction or other reasons, most ethanol plants were built with a minimum amount of grain storage on site,” Hansen says. “They just didn’t see the advantage of going real big. It’s a different story now.”
Today, ethanol plant grain storage varies widely, but most producers have, or want, at least 20 days of capacity. “A lot of them would like to be at 30 or even 60 days depending on location,” Hansen says. “The advantage they get with larger bins, whether it’s a 1-, 1.5-, 2- or 2.5-million-bushell bin, is getting substantially more storage on a smaller footprint than was previously possible.”
Space isn’t an issue for all producers, of course, but Hansen says even those with multi-acre sites can benefit from the scale and efficiency of an extra-large grain bin. “The ethanol industry is going bigger these days because they’re just turning so much grain,” Hansen says. “With the smaller etha-
SIZING UP: Two years ago, at Ringneck Energy in Onida, South Dakota, Sukup Manufacturing Co. completed what was then the largest single-site deployment of its equipment anywhere in the world. The Ringneck project included two 105-foot diameter grain storage bins and a 21-foot diameter hopper bin; several bucket elevators and conveyors; several catwalks and support towers—including one that is 60-feet tall—two zero-entry bin sweeps; and two large steel buildings.
PHOTO: SUKUP MANUFACTURING CO.
nol plants of the past, and the truck elevators, anything over 1 million bushels was considered pretty substantial because they didn’t always have the capability to monitor large amounts of incoming grain; it was risky.”
Now, with a third of U.S. ethanol plants over 100 MMgy, all having sophisticated procurement strategies, high-speed receiving and monitoring capabilities, grain storage strategies have changed. Sukup, which has delivered grain storage and receiving infrastructure to as many as 50 U.S. ethanol plants, made headlines earlier this year for building the world’s largest free-span grain bin. The container, built for Golden Grain Energy (GGE) in Mason City, Iowa, has a remarkable 165-foot diameter and a peak height of 144 feet. The massive bin, dubbed “Binzilla,” holds 2.2 million bushels of corn, and according to GGE CEO Chad Kuhlers, the system has increased the 127 MMgy plant’s grain storage from about 1.275 million bushels to almost 3.5 million bushels. Kuhlers said GGE went from about 10 days of storage to 30.
GGE grinds about 130,000 bushels of corn per day, or 42 million bushels annually. The added capacity has increased the plant’s efficiency and bolstered its corn-buying flexibility, allowing GGE to better bridge times when farmers and elevators aren't shipping corn, such as holidays or during bad weather. Notably, GGE increased its receiving capacity from 40,000 bushels per hour to 65,000 bushels per hour.
Other big Sukup projects in recent years include Homeland Energy in Lawler, Iowa, Elite Octane in Atlantic, Iowa, Ring-
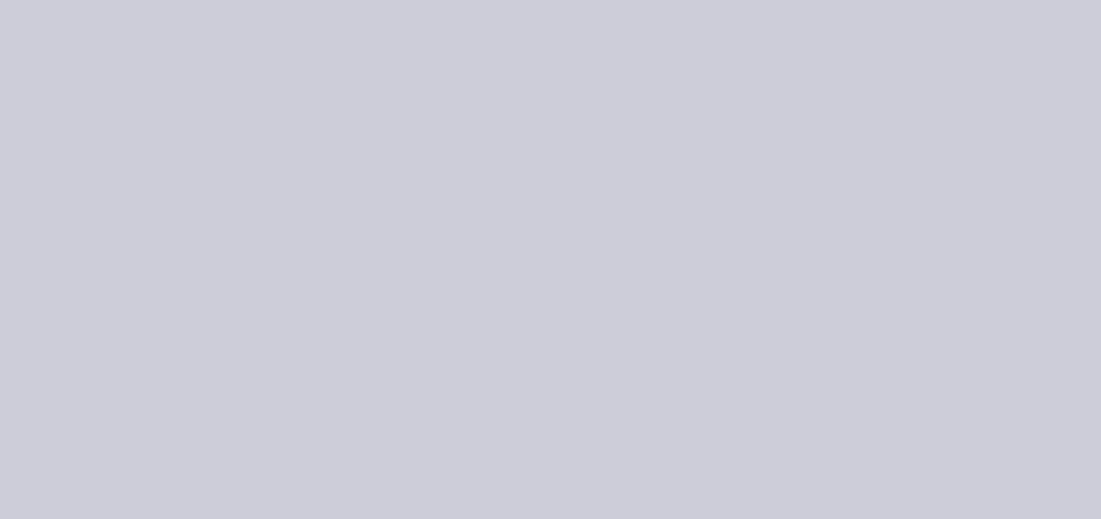
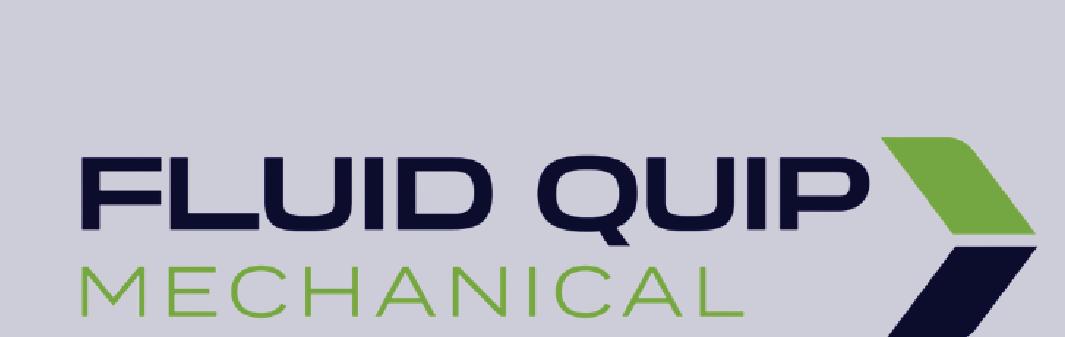




PLANT UPTIME IS IMPORTANT TO YOU, SO IT IS IMPORTANT TO US. Our full service team of experts have 20 years of ethanol plant maintenance reliability and uptime history. 24/7 support and ready access to a full inventory and all Fluid Quip equipment parts, ensures that you maintain your plant’s uptime status.
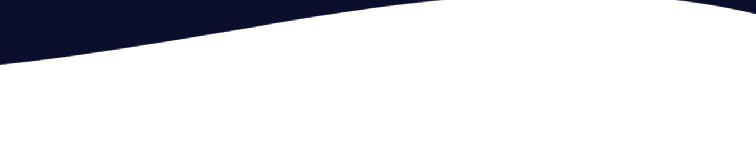
• OEM Parts Warehouse • $1 million+ on-hand inventory • Fully stocked trucks • Overnight/hot shot shipping
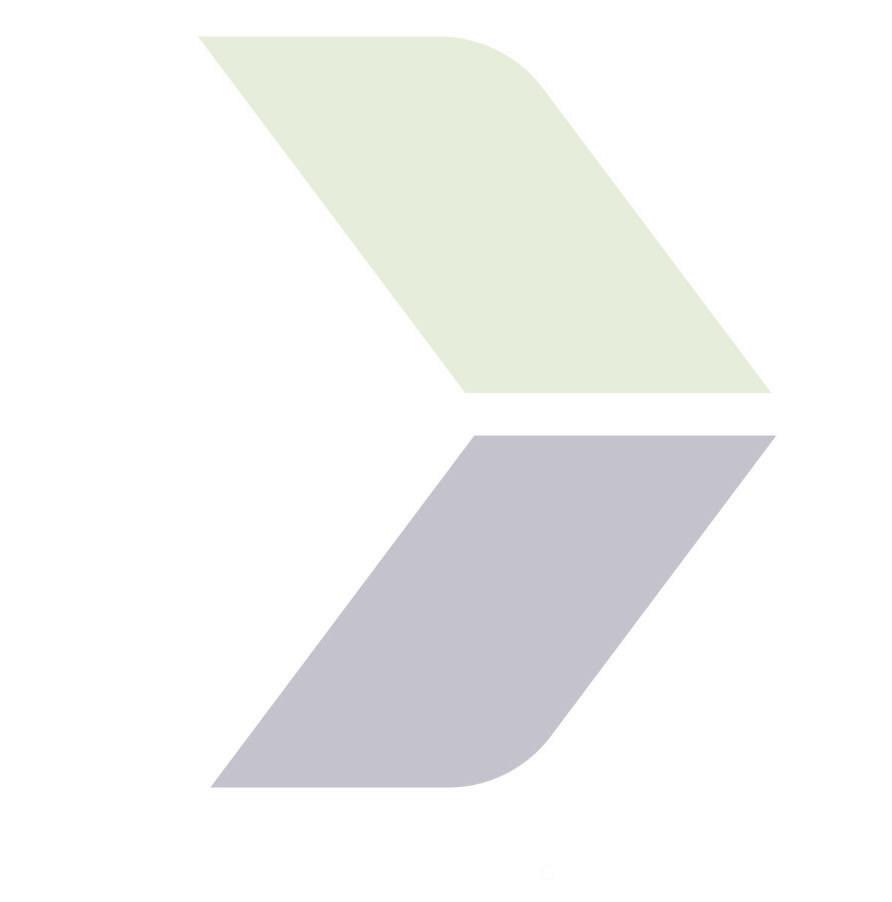
PARTS

EQUIPMENT SERVICE

• Factory Trained & Certified • MSC™ Systems • SGT™ Grind Systems • FBP™ Fiber By-Pass Systems • MZSA™ Screens • Paddle Screens • Grind Mills • • Centrifuges Centrifuges
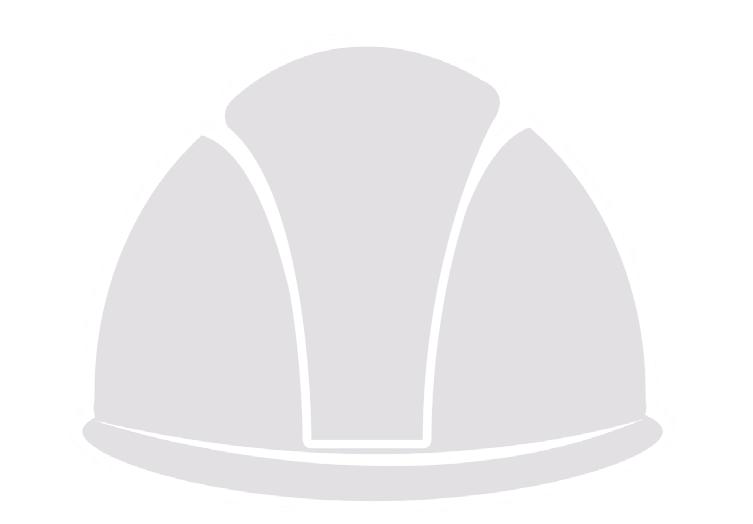

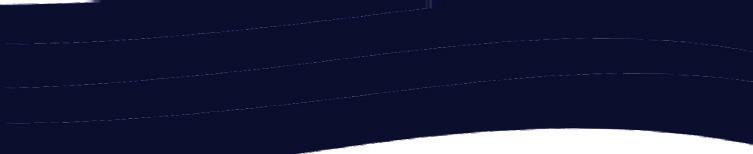
FluidQuipMechanical.com | 920-350-5823 | follow us on on Fluid Quip Mechanical is a division of Fluid Quip Technologies i . BINZILLA: Earlier this year, Sukup built the world’s largest free-span grain bin for Golden Grain Energy in Mason City, Iowa. The single container can hold 2.2 million bushels of corn.
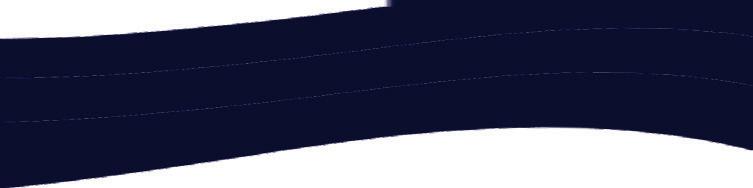

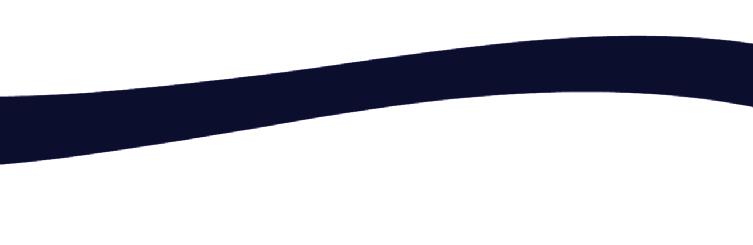
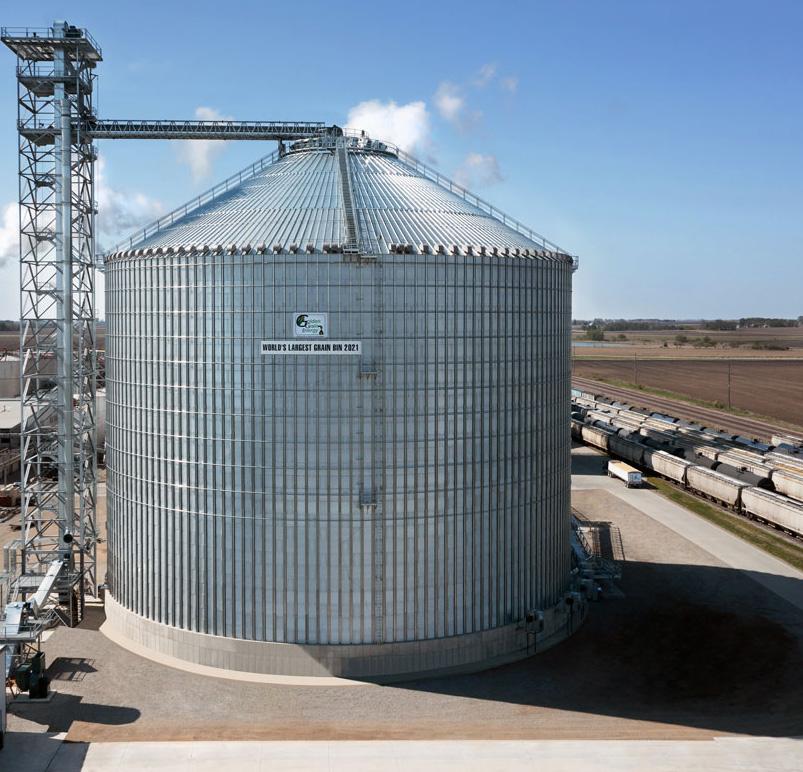
PHOTO: SUKUP MANUFACTURING CO.
neck Energy in Onida, South Dakota, and a former Flint Hills Resources plant in Menlo, Iowa, now owned by POET. Sukup manufactured massive bins at each location and, for Homeland, Ringneck and POET-Menlo provided its complete package including elevators, grain bins, buildings and conveyers, along with support structures.
Following completion of the Ringneck project, Steve Sukup, vice-president and chief financial officer of Sukup and a member of Ringneck’s board of directors, said the job was the largest single-site deployment of Sukup equipment in number of pieces and dollar value. “As a company we’ve been expanding our commercial-scale material handling equipment offerings for the past several years,” he said. “This project really pulls it all together in a way that shows we can equip big commercial projects with the grain storage and handling equipment they need.”
With its headquarters in Sheffield, Iowa, a steel coil facility 30 minutes to the north in Manly and manufacturing 15 minutes to south in Hampton, Sukup is the largest family-owned and operated grain bin manufacturer in the world. The components of its bins are manufactured in Iowa and constructed by a network of builderdistributors across the country. In fact, Sukup grain bins can be found all over the world.
The company was started in 1963 by Eugene Sukup and, like the ethanol industry, has continuously redefined itself through innovation. Sukup is known for innovations such as its patented double-ended stud bolt, which mitigates moisture problems. Sukup was also the first company to use bolts with a better coating to prevent rust, as well as sidewall splice plates that allow laminated sidewall sheets to be connected end-to-end instead of overlapped. The plates simplify construction and provide for a more watertight bin than using the traditional method of overlapping sheets. The company also offers wider bin decks for enhanced safety. Larger bins also require enhanced structural support and roof capacities. “We’re building the largest of them with 150,000-pound roof capacities” Hansen says.
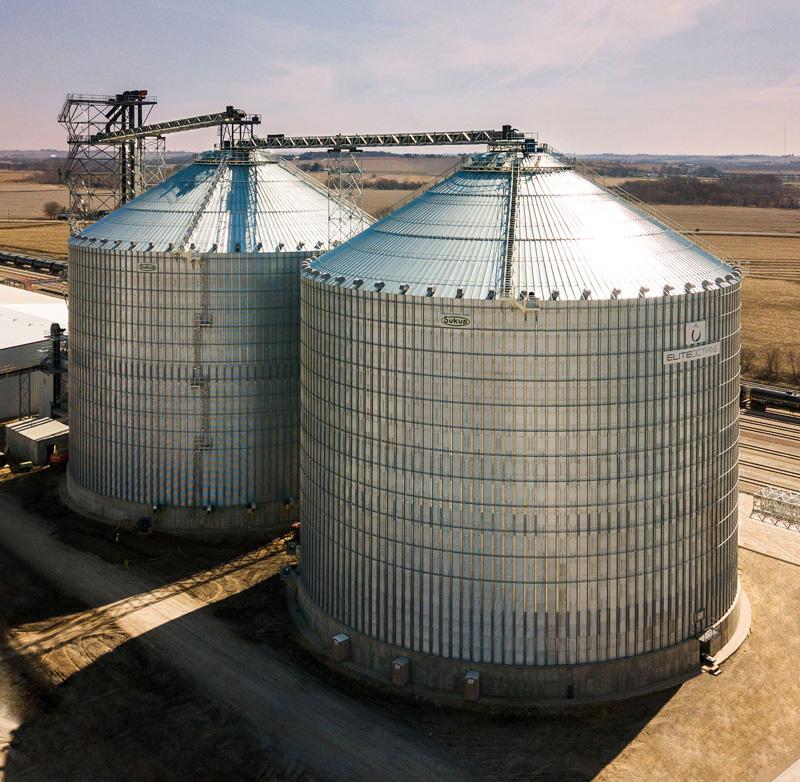
DOUBLING UP: In 2019, Sukup manufactured two massive grain bins for Elite Octane in Atlantic, Iowa, that hold nearly 2 million bushels of corn each.
PHOTO: SUKUP MANUFACTURING CO.
These and other innovations have kept Sukup busy with new projects in the ethanol industry, and Hansen expects an influx of new commercial orders in 2022, despite the high cost of steel.
With the price of sheet steel at nearly $2,000 a ton, two to three times its prepandemic price, the cost of corrugated steel grain bins has, in fact, risen. But Hansen says that hasn’t necessarily deterred ethanol producers from moving forward with projects.
“It does present challenges,” Hansen says. “You’re looking at double or even triple the cost with some steel. Whether its coiled or tube steel. The supply chain has also been tight at times, and we have done everything we can to keep things moving. Labor has also been an issue—everyone is looking for employees.”
While the steel industry is working to bring both existing and new capacity online, the price of steel—and everything made from it—is expected to remain high for some time. “We have a lot of interest for next year, but we’re not seeing all these issues being completely resolved by spring,” Hansen says. “Lead time is longer than normal. It’s been that kind of year for everyone. This situation is not unique to our company, our distributors, or the grain storage industry. Everyone is feeling these price and supply chain issues— whether you’re buying a couch, a truck or a grain bin—and it’s hard to say when it will ease up.”
Hansen adds, “Costs may be up, but ethanol production is in a good place. We support ethanol, we truly believe in it, and we remain ready to serve producers whenever they need us.”
Author: Tom Bryan Contact: editor@bbiinternational.com
More than a Check valve


www.checkall.com
Call us at 515-224-2301 or email us at sales@checkall.com
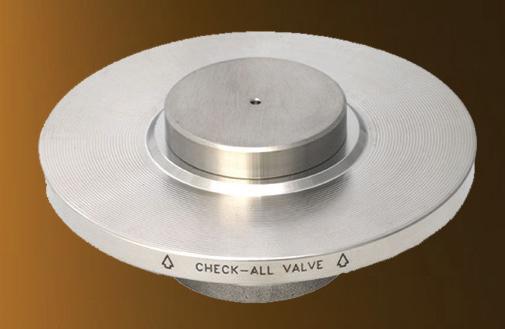