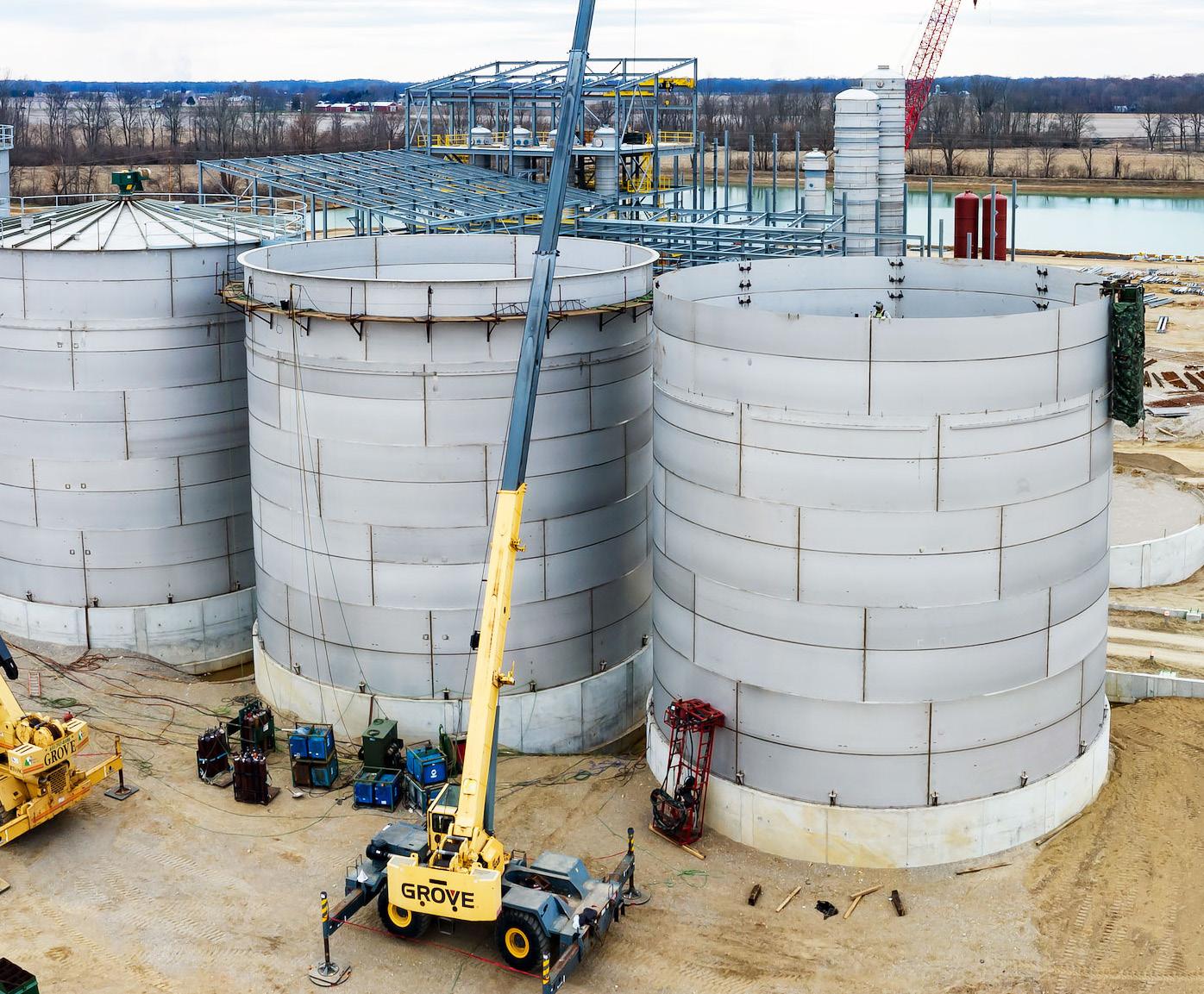
13 minute read
BUILD
STEEL STARTING WITH
Most ethanol plant upgrades require the installation of new tanks or vessels. The carbon and stainless steel they’re made from is super expensive right now, but fabricators are still getting orders. By Tom Bryan
While record-high steel prices and a strained supply chain are causing unprecedented challenges throughout manufacturing, few U.S. ethanol producers are deferring projects because of it. In fact,
despite higher costs and longer lead times for products made from flat, sheet and coiled steel, project activity is expected to rise in 2022 with ethanol output at its pre-pandemic level.
Ethanol plants are, of course, almost entirely made of steel—from their process machinery and piping to their metal buildings and structural supports—but the heavy-gauge steel that is “burned, beveled and rolled” to make tanks, vessels and columns is perhaps their most outward-facing characteristic. Ethanol Producer Magazine visited with two Midwest fabricators in late 2021, one that builds large tanks in pieces and assembles them on site, and another that delivers custom-manufactured shell and tube condensers. While the two companies make quite different products, both are dependent on steel and expect robust activity in 2022 despite the lingering high-cost environment.
Ethanol’s ‘Echo-Boom’
With a focus on field-erected tanks, Brown Tank LLC has been fabricating carbon and stainless steel storage and process tanks for U.S. ethanol producers for more than two decades. From massive 2-million-gallon ethanol storage tanks to large process tanks—fermenters, beer wells, liquefaction tanks and more— the St. Paul, Minnesota-based company is a full-service tank builder that not only understands the ethanol industry but supports it. “We’ve always been, and remain ready to serve ethanol plants,” says Scott Kraker, professional engineer and longtime sales manager at Brown Tank. “We’ve been working with producers since the early days, and through every stage of growth and evolution.”
With its experienced team of engineers, technicians and in-the-field fabrication personnel, Brown Tank is a one-stop shop that translates the design of a collaborating process engineer or EPC to construction-ready tank components. “Our professional engineering team produces the structural design plans for use in fabrication of the raw materials for the field construction of the tank on site,” Kraker says.
In a different realm of the steel vessel business, Decatur, Illinois-based Mason Manufacturing custom builds shell and tube evaporators for ethanol producers. Unlike the large tanks that Brown fabricates, however, Mason’s process vessels are entirely built in its shop and shipped out ready for installation. “That’s a large portion of our business, maybe twothirds of our volume,” says Doug Cox, vice president and engineering manager at Mason. “We also build pressure vessels—reactors and columns—and, to a lesser extent, tanks. But our bread-and-butter is shell and tube heat exchangers.”
For years, Mason has been providing the ethanol industry with 190-proof condensers, sieve vaporizers, cook water heaters and CIP heaters made with both carbon and stainless steel (304 and 316). “We were able to get in on the ground floor with the ethanol industry’s top EPCs early, so we’re in a lot of ethanol plants throughout the Corn Belt,” Cox says. “Having that decades-long presence has been good for us because people see our units in the plant. They’ve been in operation now for 10, 15, 20 years—with Mason Manufacturing nameplates on them—so if they need replace-
PROJECT LIFT: Brown Tank, which constructs both storage and process tanks for ethanol plants, supports its clients throughout the planning and design stages of project development and engineering by providing pricing and technical guidance on tank-related concepts prior to construction.
PHOTO: BROWN TANK
ment, parts or advice on upsizing, they know where to turn.”
Brown, too, serves many of the same ethanol clients it built tanks for in the early years. Working on ethanol projects, Kraker says, is a collaborative effort that pivots around project efficiency. “Ultimately, tank fabrication is about response time, cost and quality of service,” he says. “With our experience and in-house engineering and fabrication, we really have control of our business cycle. That enables us to come through for our customers in a manner they expect.”
Kraker says Brown Tank supports its clients throughout the planning and design stages of project development by providing pricing and technical guidance on tank-related concepts. “By doing this, our clients our able to understand their potential budget options for expansions and repairs,” he says. “The fact that we are heavily weighted with engineering knowledge gives us the ability on help our customers select economical designs that make best use of available materials to keep projects on budget.”
Stainless steel tanks don’t easily corrode and seldom require repair. Carbon steel, on the other hand, tends to corrode predictably, requiring new tank bottoms over time. “It’s just the reality of flat-bottom tanks, especially those made from carbon steel, that the underside of the floor in contact with the foundation tends to suffer corrosion due to moisture and other issues,” Kraker says. “There’s little you can do to prevent that, so there is often repair work at the 10- or 20-year interval to extend the longevity of the tank.”
Some of the new and repeat ethanol customers Mason serves also have issues with aging carbon steel-based components in their plant. “In the past, some of these shell and tube components were made with the most readily available and cost-effective material— carbon steel,” Cox says. “The major components like tubes and tube sheets were usually stainless, but some of the other components were carbon—especially in plants that raced to get completed back in the early-to-mid-2000s.”
But Cox says ethanol producers don’t just call Mason to replace aging carbon steel evaporator components, but to optimize, debottleneck or boost flow rates. “While the construction boom peaked over a decade ago, we’ve seen an ‘echoboom’ of work in ethanol,” he says, explaining that pushing an older 190-proof condenser to a higher-than-design flow rate can create problematic vibration, for example. “Replacing those aging condensers can be a key part of enabling a 100-million-gallon plant to operate at 120 or 130 million gallons per year.”
How It’s Made
All Brown Tank components are made at its 60,000-square-foot fabrication facility in St. Paul, where its shop personnel machine every piece with as much precision as possible. “We do everything we can to fabricate all the parts and pieces accurately to make it easier to assemble on site,” Kraker says. “On-site modifications to materials impact field productivity and schedules, so everything has to be ready to go.”
Ethanol storage tanks must comply with API standards—primarily API 650—while the vessels and columns made by Mason fall under ASME standards. The size and parameter of each tank design determines the gauge of steel used for the walls, floor and roof. Kraker says one-quarter to one-half inch steel is typical for storage tanks. The steel arrives in St. Paul in large flat sheets. “They typically arrive in eight-foot wide by 20- or 30-foot-long pieces,” he says.
Fabrication at the shop requires workers to cut to size, square up and prep the steel sheets with any machining necessary to support field welding. For curved wall pieces, shop technicians “burn, bevel and roll” the steel to the specifications of the tank’s circumference.
The steel used for the bottom and top of a tank, when complete, has a quilt-like appearance to form the round shape of the structure’s floor and roof. Structural steel supports are used inside tanks to hold up the roof and provide overall support. Aluminum floating roofs built by third-party contractors are assembled on site and installed inside the ethanol storage tanks before they are sealed shut.
Most storage tanks, and virtually all large process tanks, have concrete foundations; fermenter tanks sit on taller concrete pedestals to elevate the discharge piping to above-grade; storage tanks and other process tanks usually sit on a concrete slab or ring wall.
In Decatur, Mason’s fabrication process also begins with raw steel. “Everything we buy is
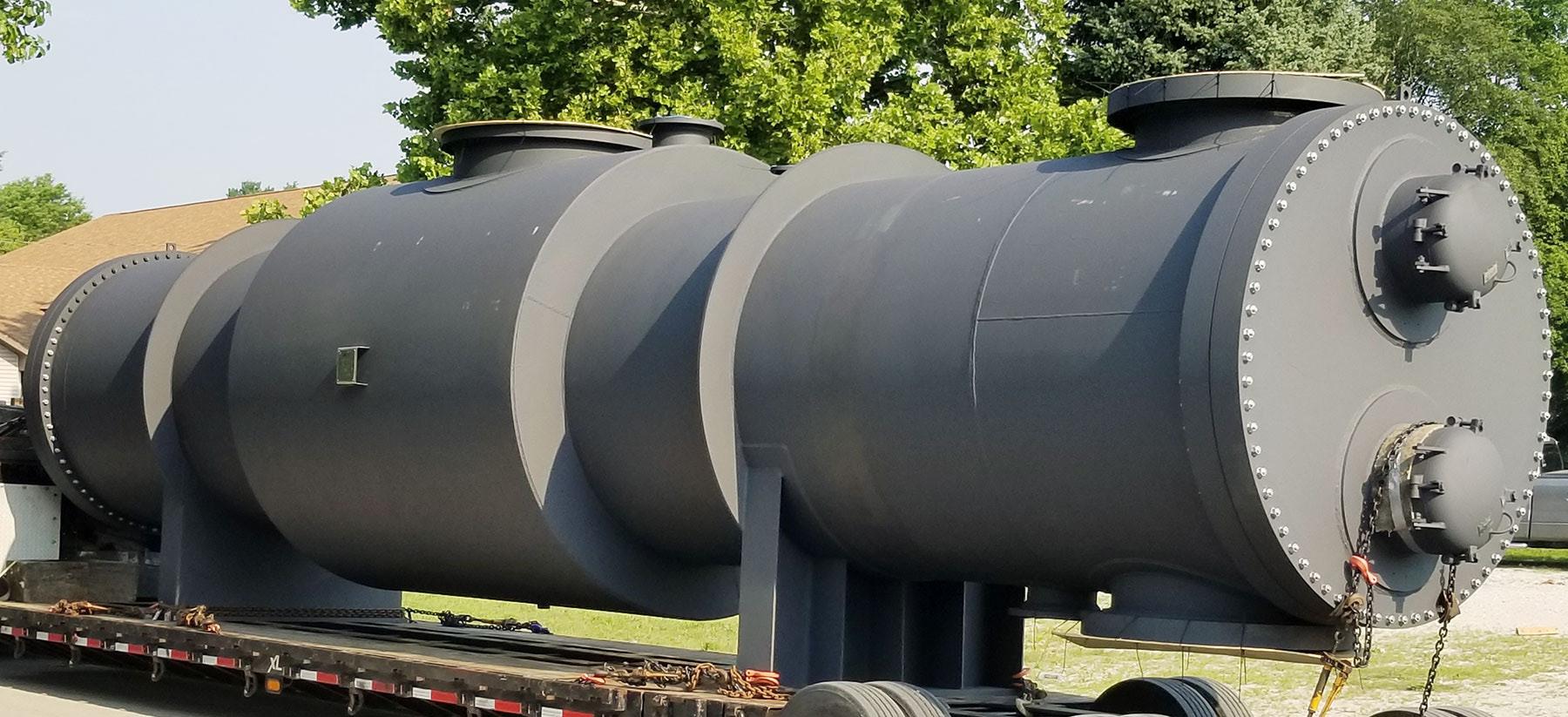
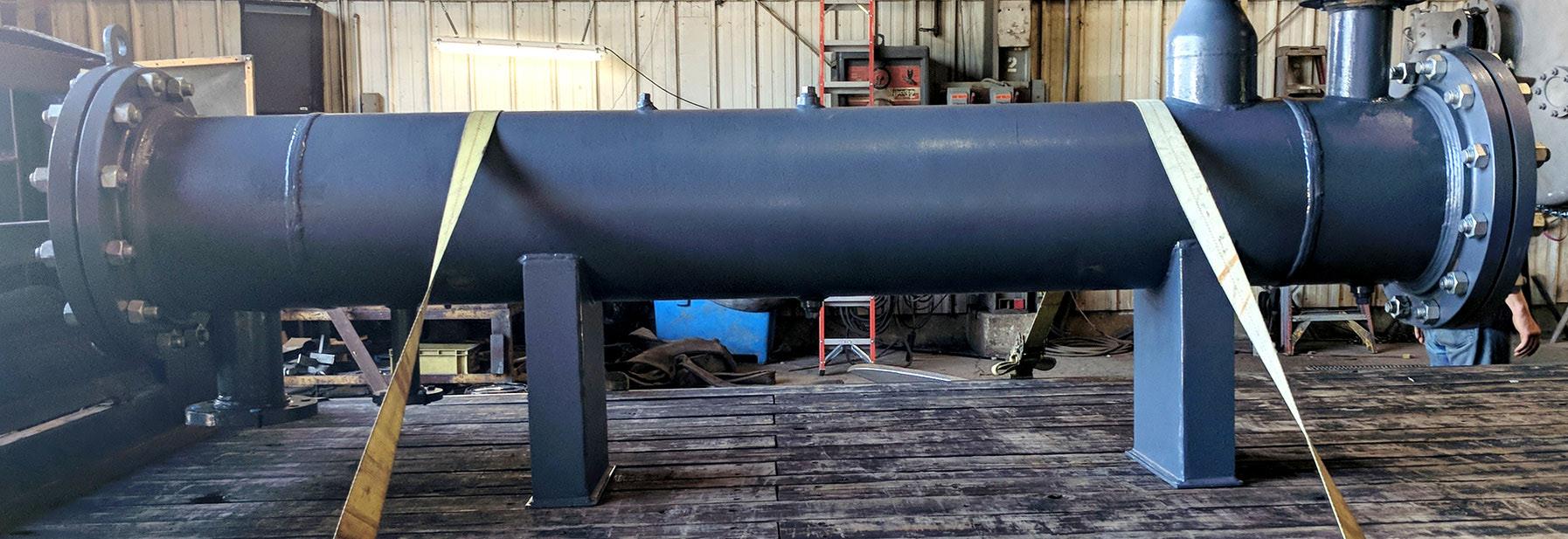
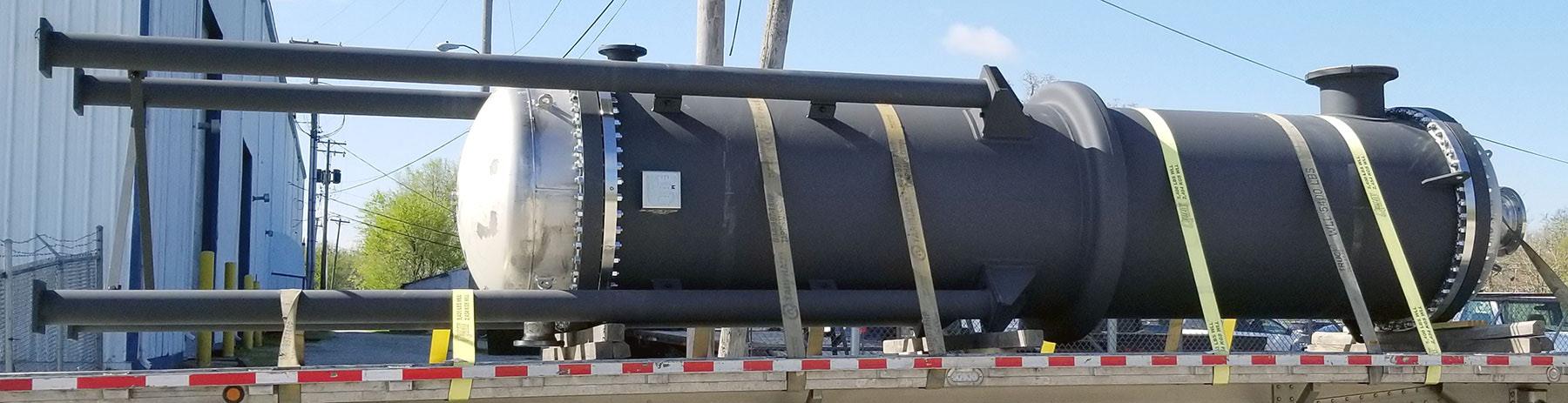
CUSTOM MADE: Mason Manufacturing provides the ethanol industry with 190-proof condensers, sieve vaporizers, cook water and CIP heaters. Despite high steel prices, the company is busy fulfilling projects the ethanol industry can no longer afford to defer.
PHOTO: MASON MFG.
custom to the job,” Cox says, explaining how a custom shell and tube evaporator is built.
With engineering details in hand, Mason creates a bill of materials for each project and identifies “long-lead” items while drawings are still being finalized. “Typically, that’s going to be your tubes and tube sheets, as well as form heads and machined items,” Cox says, explaining that long-lead items generally do not change in geometry or size in final design. “The tube quantity, length and thickness typically are not going to change.”
Pipes are cut to length and nozzle projections are made. Steel plates are cut to size, burned and beveled. “Then we roll the steel and weld it,” Cox explains. “After welding we typically re-roll everything for out-of-roundness tolerance, per ASME code.”
Numerous components are precisionmachined prior to fitting. When everything is ready, the components are moved to a “fitter station” where experienced personnel assemble the pieces of the shell and tube heat exchanger as welders work behind them to fuse everything together. When the shell is completed, but before the “bundle” is inserted, a third-party inspector is brought in to do an internal and external inspection of the welds,
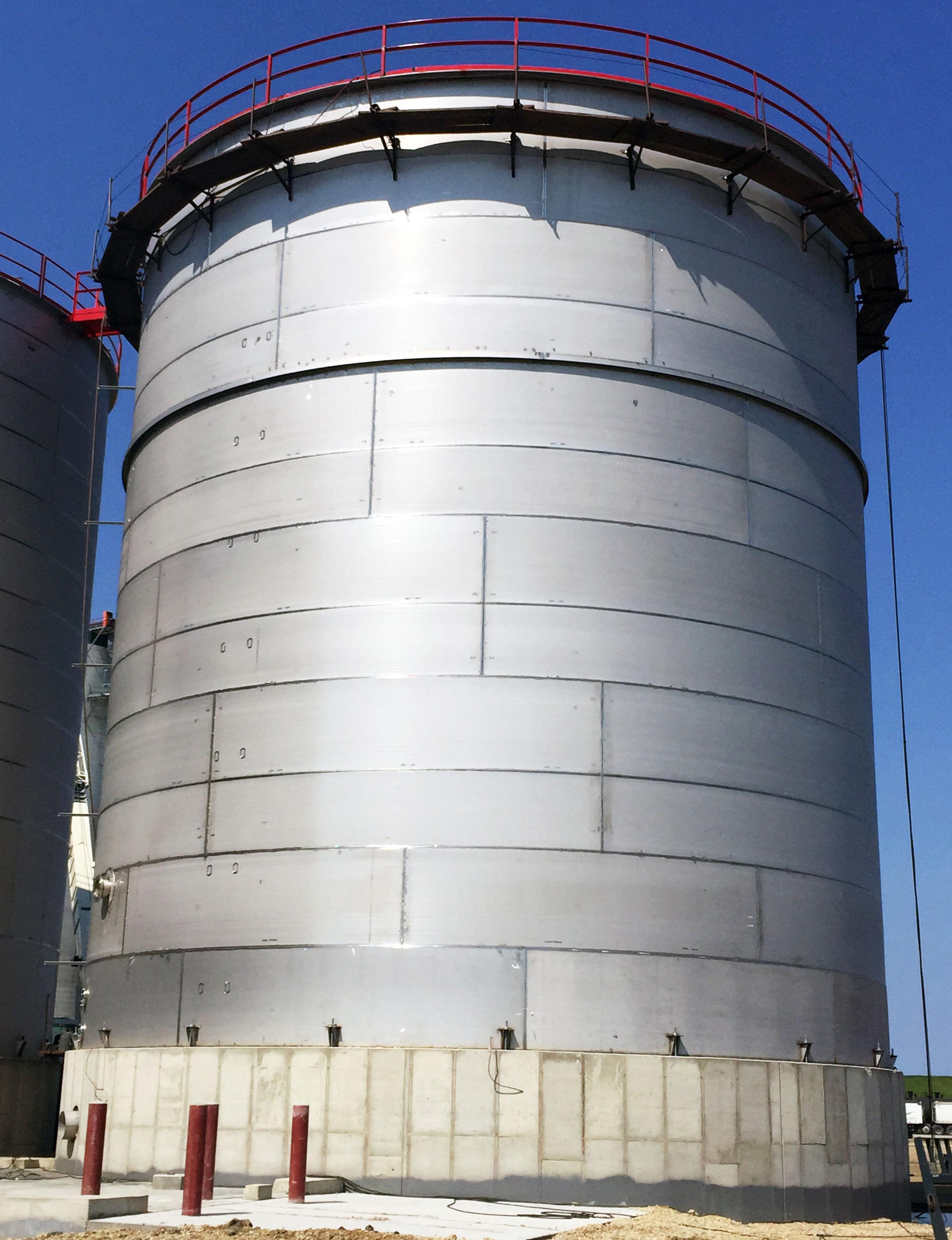
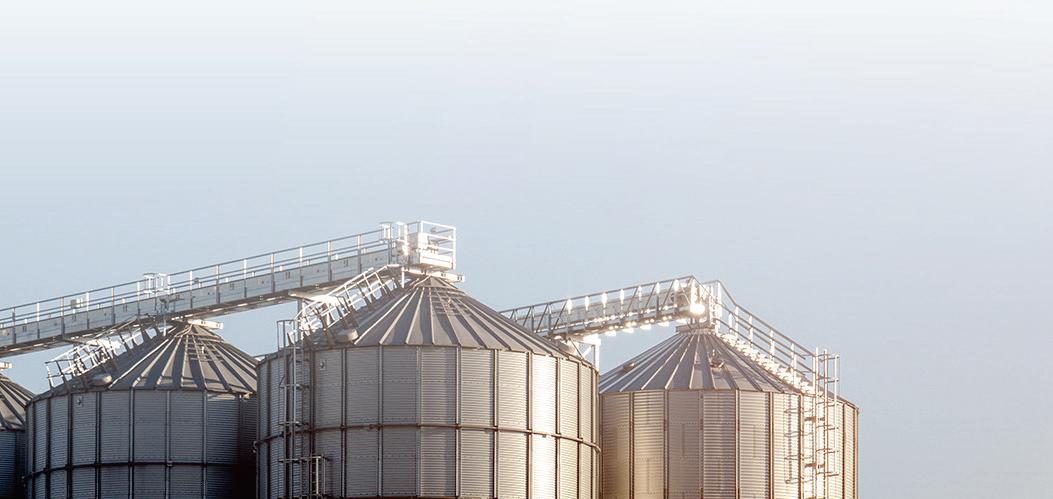
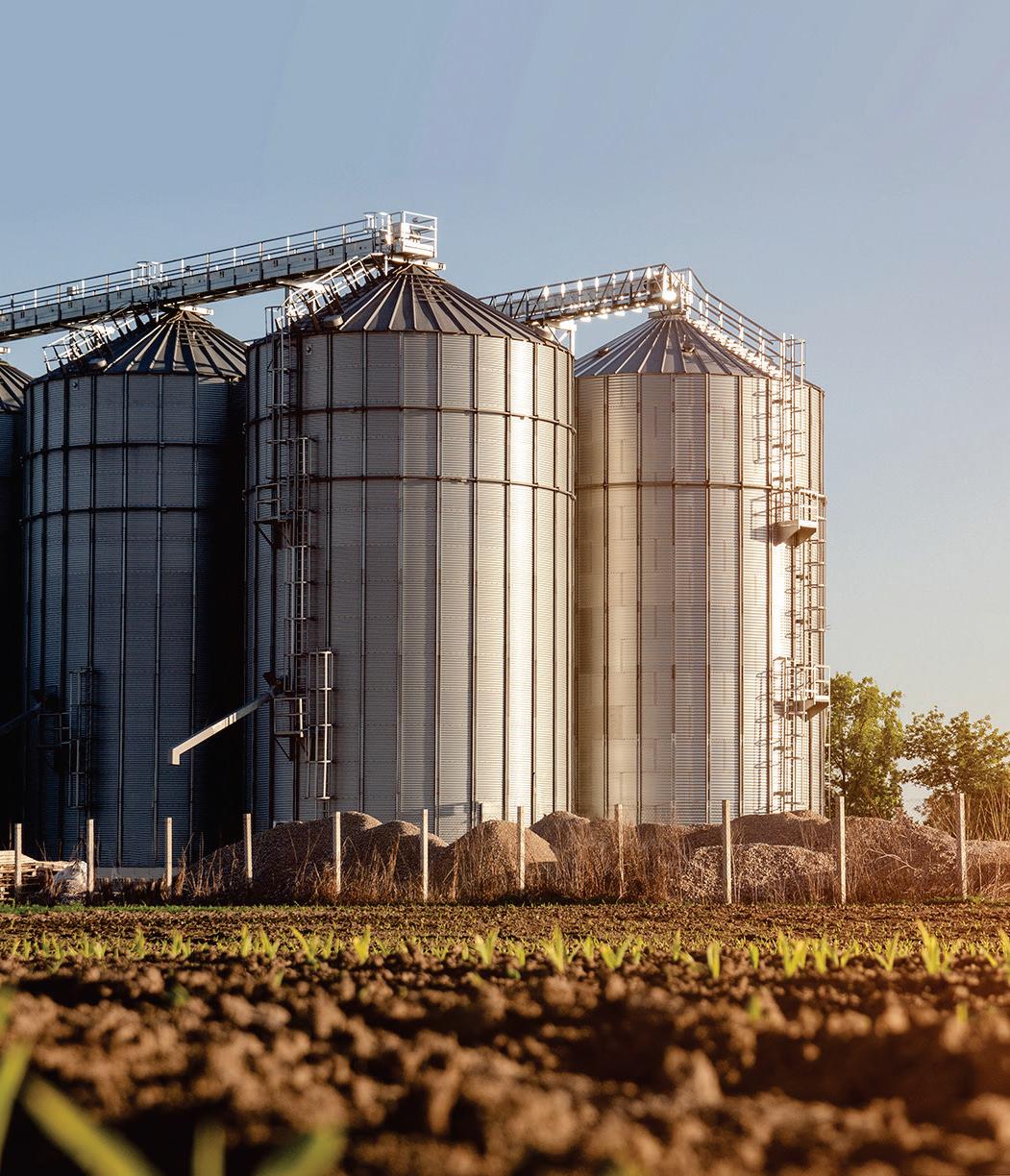
SOLID BASE: Most storage tanks, and virtually all large process tanks, have concrete foundations; fermenters sit on taller concrete pedestals to elevate the discharge piping to above-grade; storage tanks and other process tanks usually sit on a concrete slab or ring wall.
PHOTO: BROWN TANK
another ASME requirement. “We build the [tube] bundle externally and then push it into the unit before weld sealing those tubes into the sheets.” Final inspection and hydro-testing is completed prior to shipment.
High-End Alcohol Work
Today, all new ethanol process tanks are stainless steel, while fuel ethanol storage tanks are still built from more affordable carbon steel. However, high-grade alcohol—including United States Pharmacopeia (USP) grade alcohol and grain neutral spirits (GNS)— must be stored in stainless steel tanks, which are also equipped with floating roof systems. “We’ve been busy building USP-grade stainless steel storage tanks for ethanol producers since the pandemic started, and just recently finished projects in Michigan and Kansas,” Kraker says.
Kraker says the demand for stainless storage tanks has been relatively steady with the uptick in high-grade alcohol production during the pandemic that, for many producers, has morphed into a longer-term play.
Mason, too, has seen an increasing number of jobs in the ethanol industry related to producers pursuing high-grade alcohol. “We
WE CLEAN SILOS
Why is Mole•Master™ the ethanol industry’s rst choice for silo cleanout?
EXPERIENCE
#1 silo cleanout contractor, worldwide, for 35+ years.
TOTAL MATERIAL RECOVERY
Bulk storage and process vessels are restored to 100% of planned storage capacity with maximum ef ciency and minimum downtime.
RESTORED PRODUCTION
100% dry process, no mess, no mud and no expensive cleanup.
Mole•MasterTM crews are intensively trained to OSHA/MSHA standards and are ready to mobilize to your site, anywhere on earth.
are definitely seeing that activity, producers turning to a different filtration process and trying to get to a higher-grade alcohol for sanitizer or other high-end products,” Cox says. “We have been involved on the engineering and fabrication side of this with … the thermal design for fitting geometries to complete the necessary heat loads, as well as the filtration technologies.”
Steel Price, Supply
Current carbon steel prices—double or triple what they were pre-pandemic ($1,800$2,000 per ton verses $500-$700)—and protracted supply constraints have added budget and logistics complexities to the tank fabrication process. But Kraker says Brown Tank is doing what it can to keep its customers on budget and on schedule.
“We are all aware that there are extreme challenges throughout the supply chain, and this includes steel suppliers,” he says. “Pricing and availability continue to challenge customer budgets and construction schedules. Our team [provides customers with] timely information to make prompt decisions to mitigate these issues. Acting quickly in this market is the key to securing the resources necessary for successful projects.”
Kraker says high material pricing has impacted follow through on some projects, but ethanol producer margins, and the payback on new process technology and extra stor-
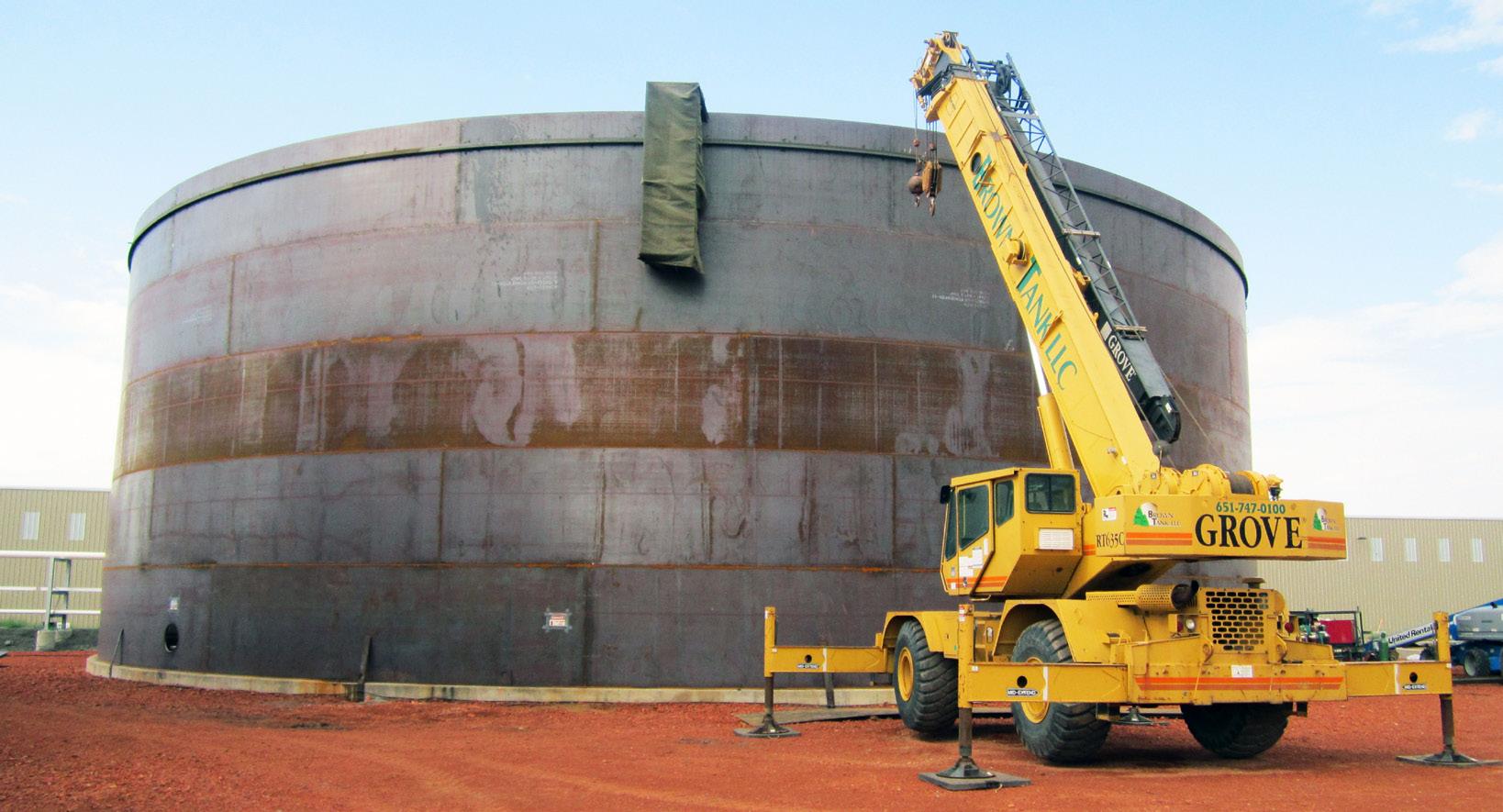
CARBON COSTS: The prices of the carbon steel used for fuel ethanol storage tanks has almost tripled over the past 18 months, matching the cost of stainless steel pre-pandemic.
PHOTO: BROWN TANK
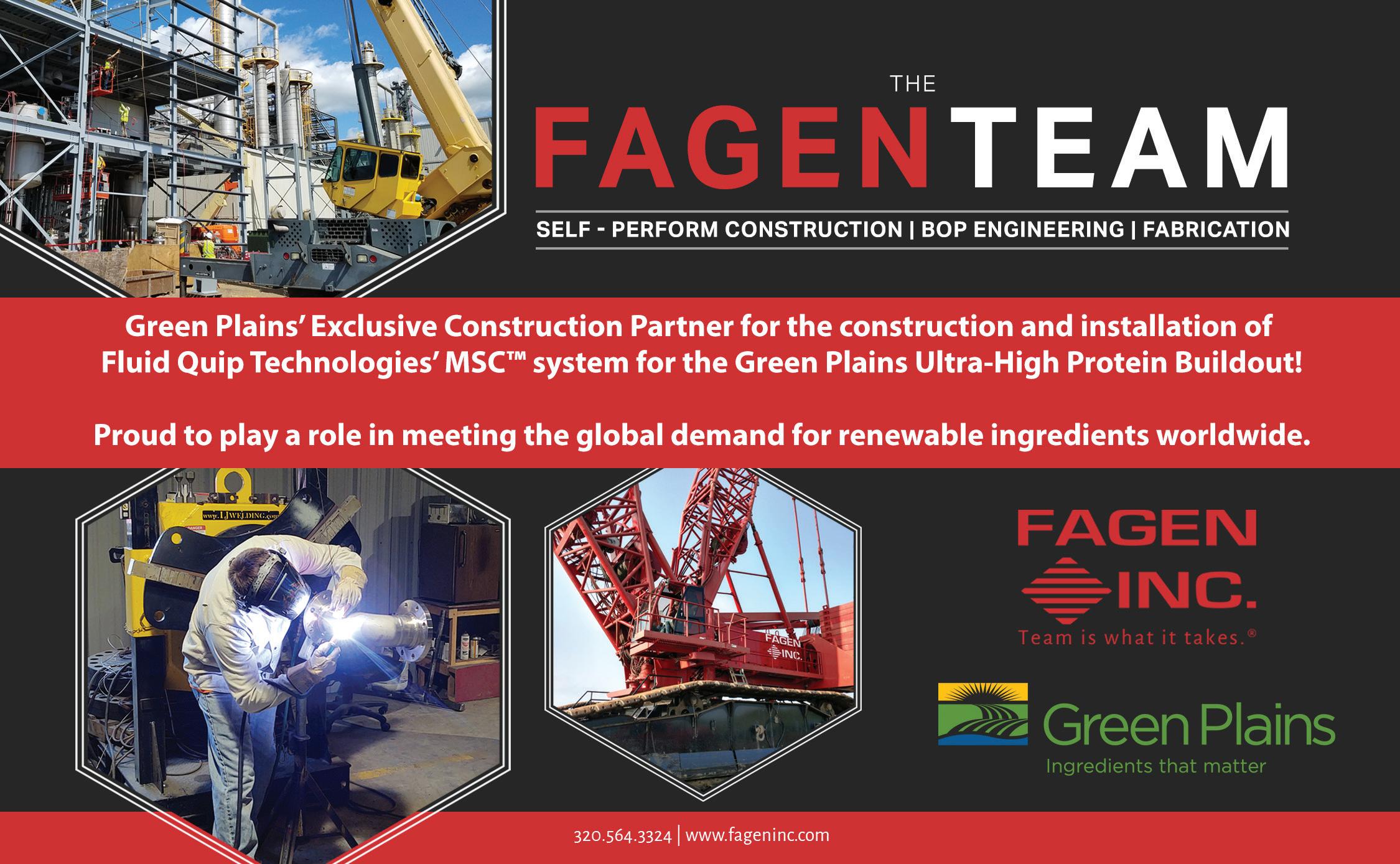
age capacity often overrides concerns about the current cost of steel. “We’re seeing that most producers are able to implement their plans, even in a high-cost market,” Kraker says. “Ethanol producers face challenges—we’re part of Growth Energy and we hear about the political challenges they’re up against—but they’re still finding ways to proceed with these projects. The market is hopeful, and producers are expressing a desire to proceed with plant improvements.”
Cox agrees, saying that higher prices for both carbon and stainless steel aren’t deterring ethanol producers from moving forward with necessary projects. “It doesn’t seem to be relaxing customer need,” he says. “No one seems to be backing off their plans because of cost. There is very high pent-up demand, customers have been needing to order things for the last year and a half, and I think they feel like they simple can’t put these projects off.”
The high price of stainless steel doesn’t shock Cox as much as the current price of carbon steel. “Stainless is typically more price volatile because of the elements in it, so we’re used to seeing price fluctuations with stainless,” Cox says. “But carbon steel is simple, so the fact that prices doubled or tripled in the past year is extraordinary. Carbon steel right now is priced comparable to stainless steel prepandemic.”
Kraker says high steel prices may persist for months or even years. “Last week, there was another notice of a stainless steel price increase, and I expect the same with carbon steel,” he says. “This pricing bubble is going to continue as long as they have disruptions on their end with labor issues and plant supply logistics.”
Kraker continues, “Communication with our clients on projects is key to ensuring that they secure materials early enough in the process to mitigate any delay issues that prevail into next year’s construction season. Everything we’re seeing—all the forecasts—are predicting that this is going to continue for some time.”
Supply issues have also affected project timelines for Mason. Cox says the lead time of steel components such as tubing has been lengthened over the past six to nine months as demand has increased while supply tightened. “There was a large sheet metal strike here in the U.S., with multiple plants down for a few months,” he says. “That strike, along with very high demand—with a lot of projects being released in 2021—has everyone playing catch up. It has created tubing lead times that are 18 to 22 weeks.” Cox says Mason has scrambled to find additional vendors, looking at both domestic and non-domestic tube suppliers, which are in turn dependent on their steel coil suppliers. The whole steel sector is simply lagging,” he says. “I think demand came back a lot quicker than people expected and the whole supply chain just hasn’t been able to catch up.”
Despite these price and lead-time challenges, Cox says, steel vessel fabrication work is steady. “Costs are obviously up but, again, I think people just can’t defer some of these projects any longer. The project orders keep coming in, and a lot of ethanol customers are already looking at spring.”
Author: Tom Bryan Contact: editor@bbiinternational.com



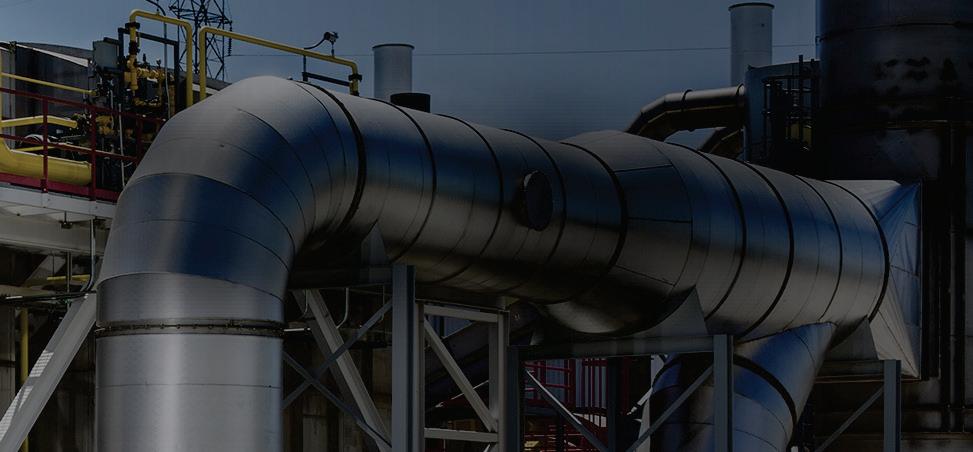
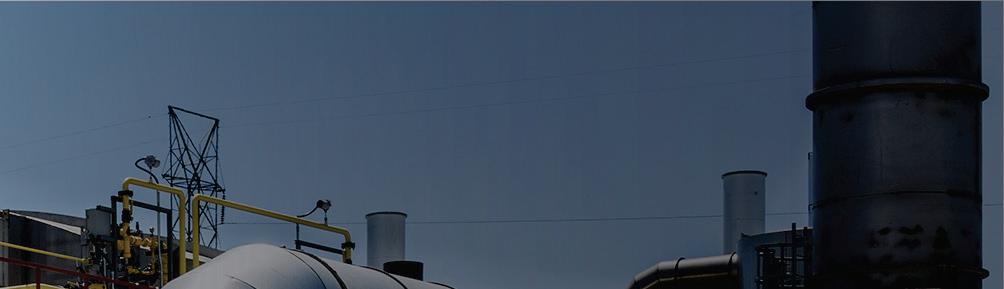
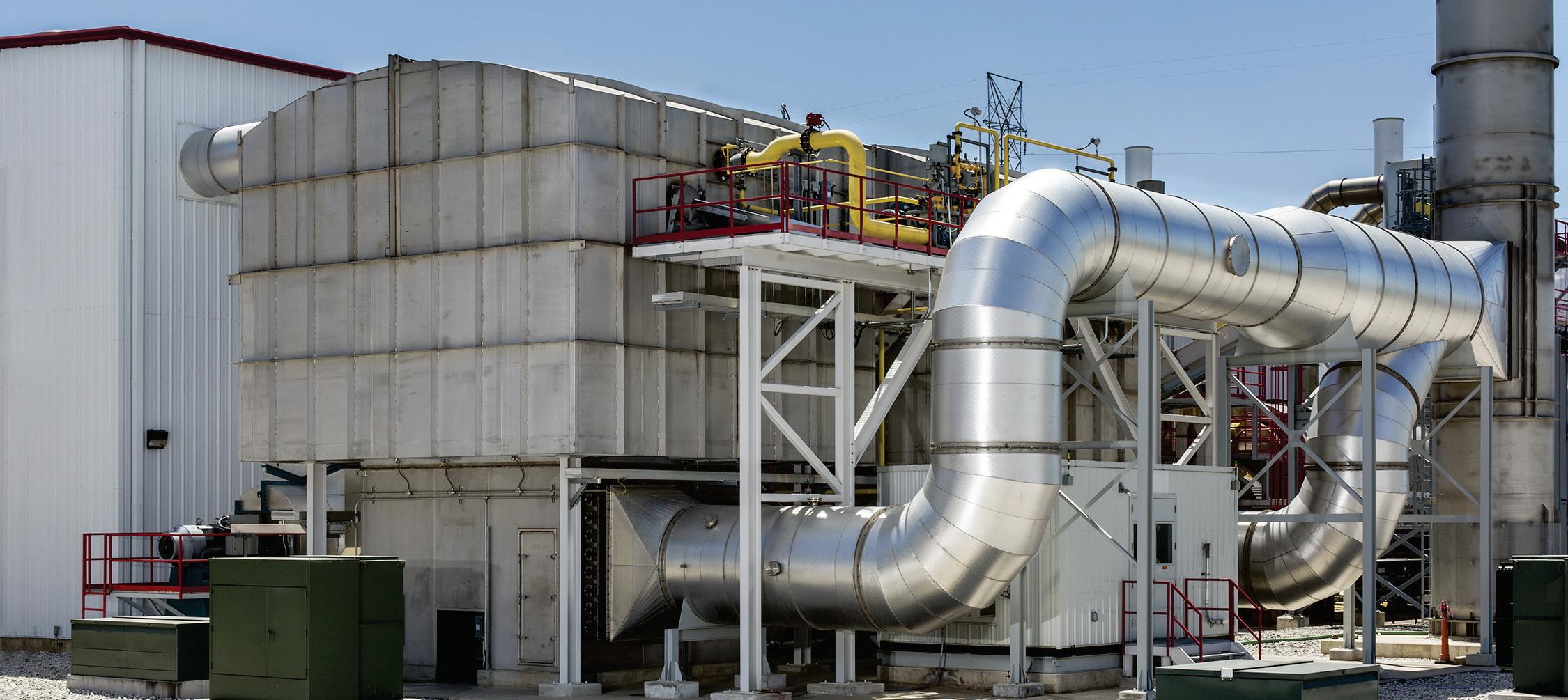

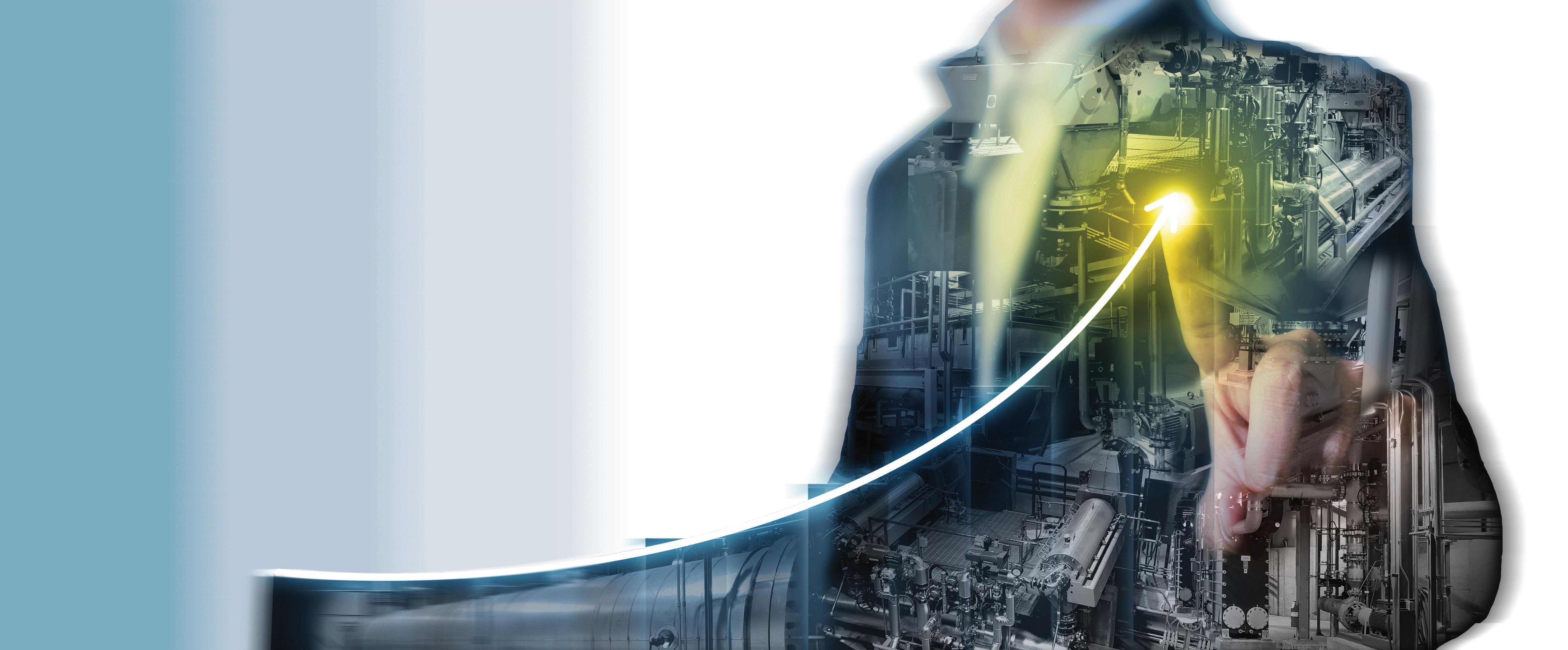