
11 minute read
EVENT
PHOTO: STOCK CRITICAL CONTENT The fi rst Plant Maintenance and Safety Summit, held virtually in December, featured crucial information on how to reduce injuries and fatalities, along with educational discussions on upkeep, optimization and more. By Lisa Gibson
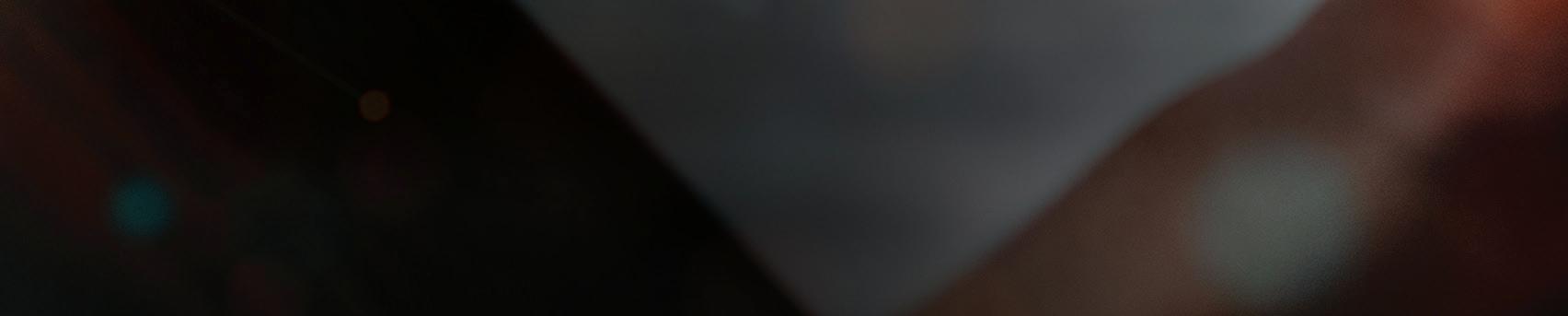

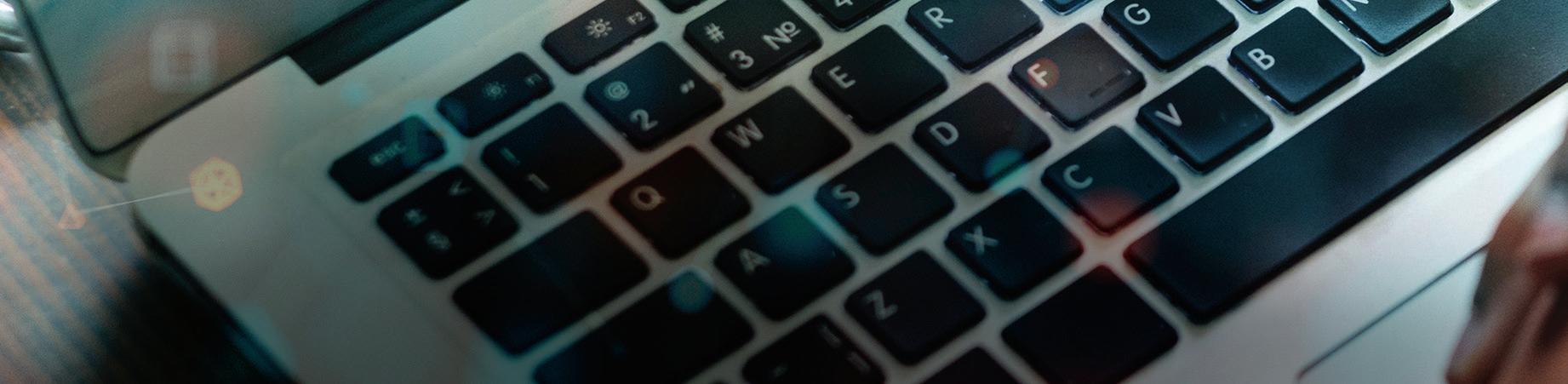
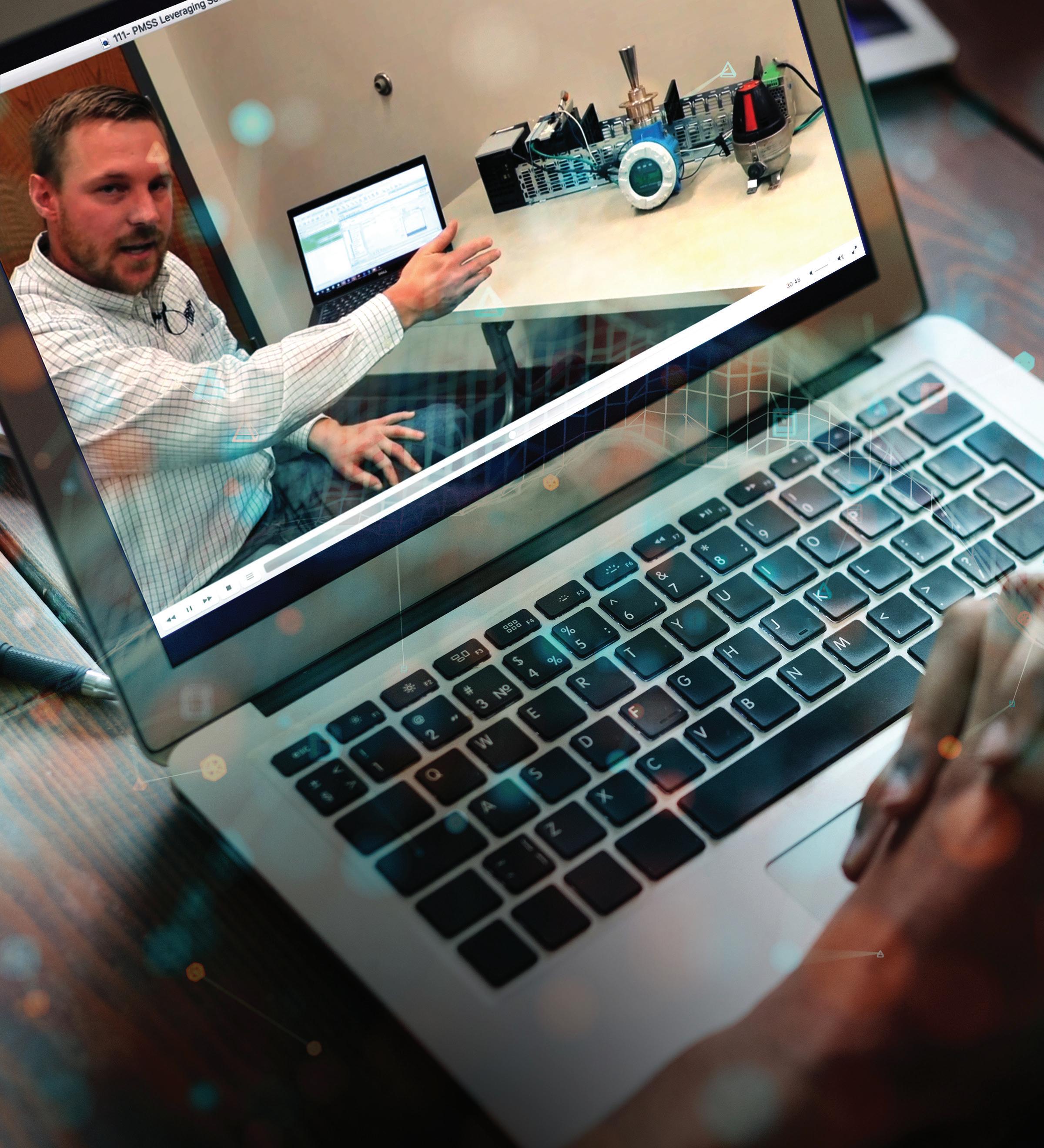
“Do your employees readily identify near misses, or does your site simply not have near misses?” Jacob Hencke, senior EHS consultant with ERI Solutions/PROtect, asked attendees during his presentation at the virtual Plant Maintenance and Safety Summit, Dec. 16-17.
“Do employees have near miss training?” he continued, imploring his audience to think critically about their SIF (serious injury, fatality) near misses. “Do managers support near miss reporting? If one is reported, is it addressed in a positive manner to encourage further near miss reporting?
“Near misses are a critical part of not just regular safety, but specifically incidents that have serious injury, fatality potential,” Hencke said.
He was one of 11 presenters at the Plant Maintenance and Safety Summit, the first of its kind organized by BBI International. Like September’s virtual Fuel Ethanol Workshop & Expo, the PMSS featured a virtual trade show and networking opportunities.
The event drew in 167 attendees, 86 of which were ethanol producers from 50 facilities.
“The feedback we received on the real-life, in-the-facility style presentations was extremely positive,” said John Nelson, vice president of operations, marketing and sales at BBI International. “The presenters did a tremendous job delivering real-life content and applications that can help production facilities operate efficiently and safely.”
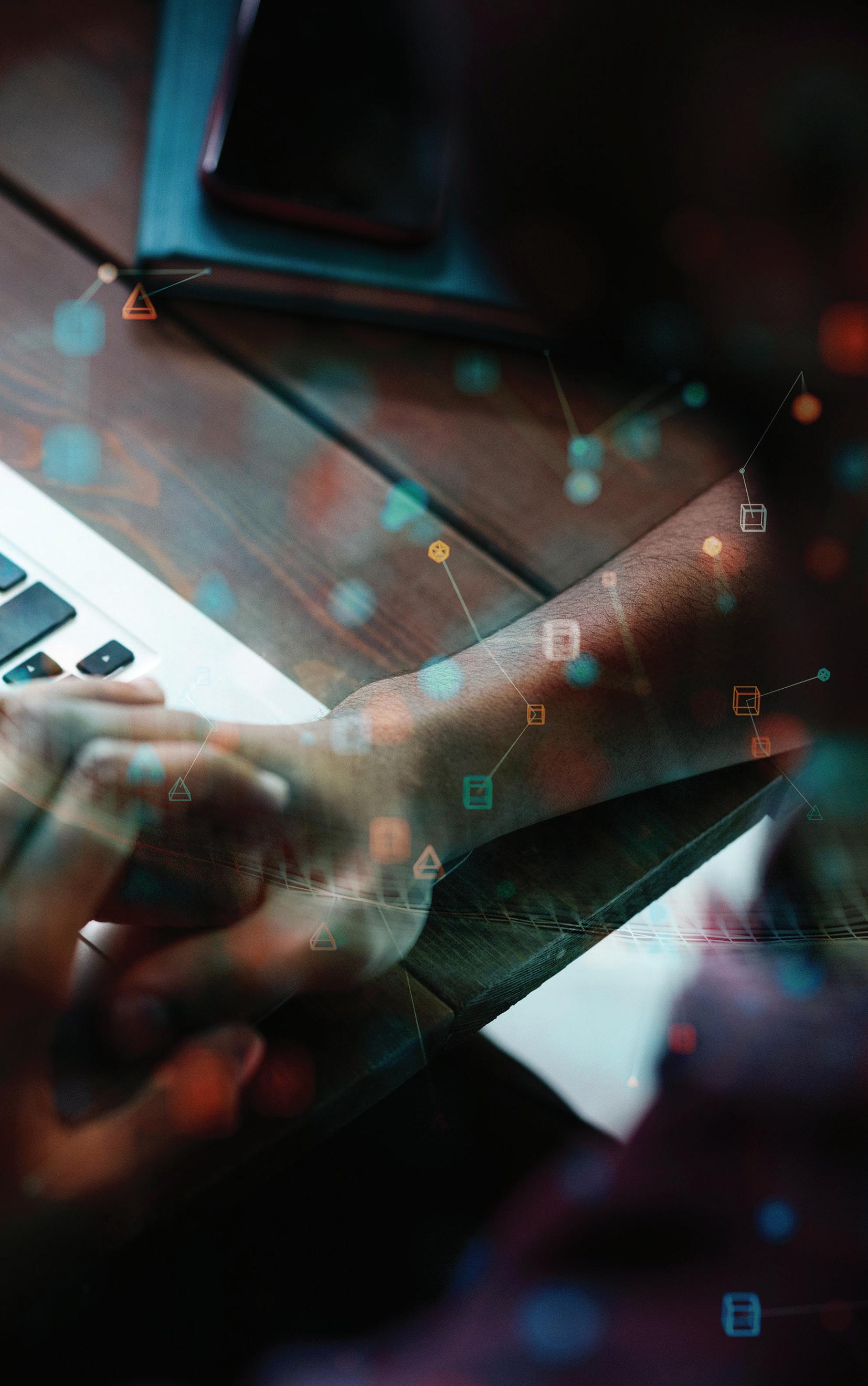
HEINRICH’S HELP: Jacob Hencke, senior EHS consultant with ERI Solutions/PROtect, presented during the virtual Plant Maintenance and Safety Summit, held Dec. 16-17. He focused his presentation on the significant impacts of reducing near misses in ethanol plants. PHOTO: JACOB HENCKE, ERI SOLUTIONS Near Miss Reporting
During his presentation, Hencke emphasized that documenting, communicating and resolving near misses in ethanol plants can help reduce incidents that cause serious injury or death. He presented during the PMSS panel “Your Most Valuable Asset: Deploying Safety Strategies Aimed at Eliminating Lost Time Injuries, Near Misses.”
“Your most valuable asset: your people,” he said.
Not all incidents have the same risk level, so they can’t all be evaluated through the same lens, Hencke said. A fall from an elevated platform is an SIF incident, whereas a fall on slippery ice on the ground is a non-SIF incident.
An SIF includes fatality, life-threatening injury or illness, and life-altering injury or illness. Life-threatening injuries are those that are likely to lead to death without immediate medical attention. Life-altering injuries could include injury that causes
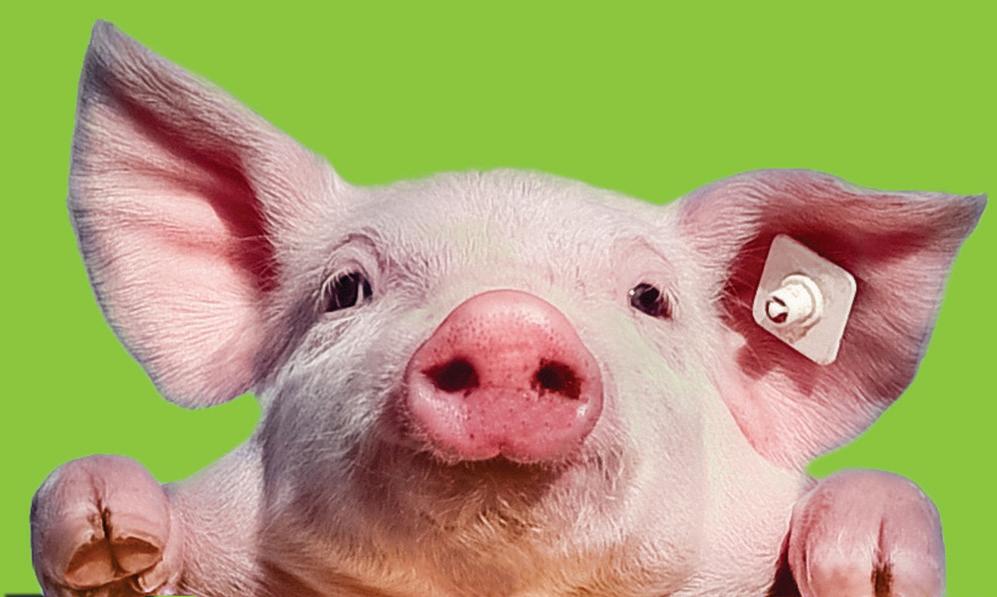


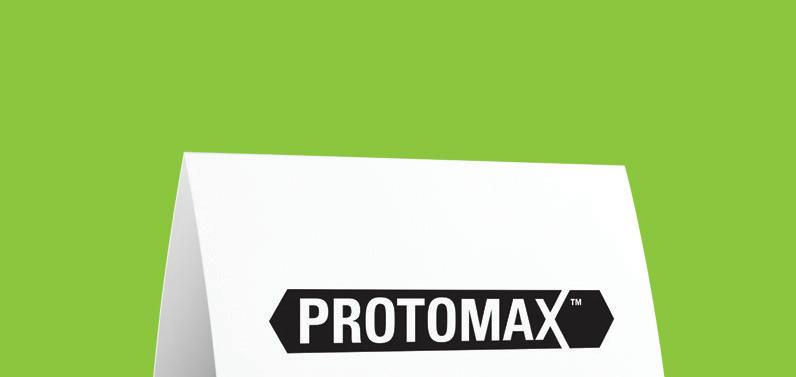




SIF DEFINED: Hencke outlined the definition of SIF: serious injury or fatality. PHOTO: JAY BECKEL, ERI SOLUTIONS
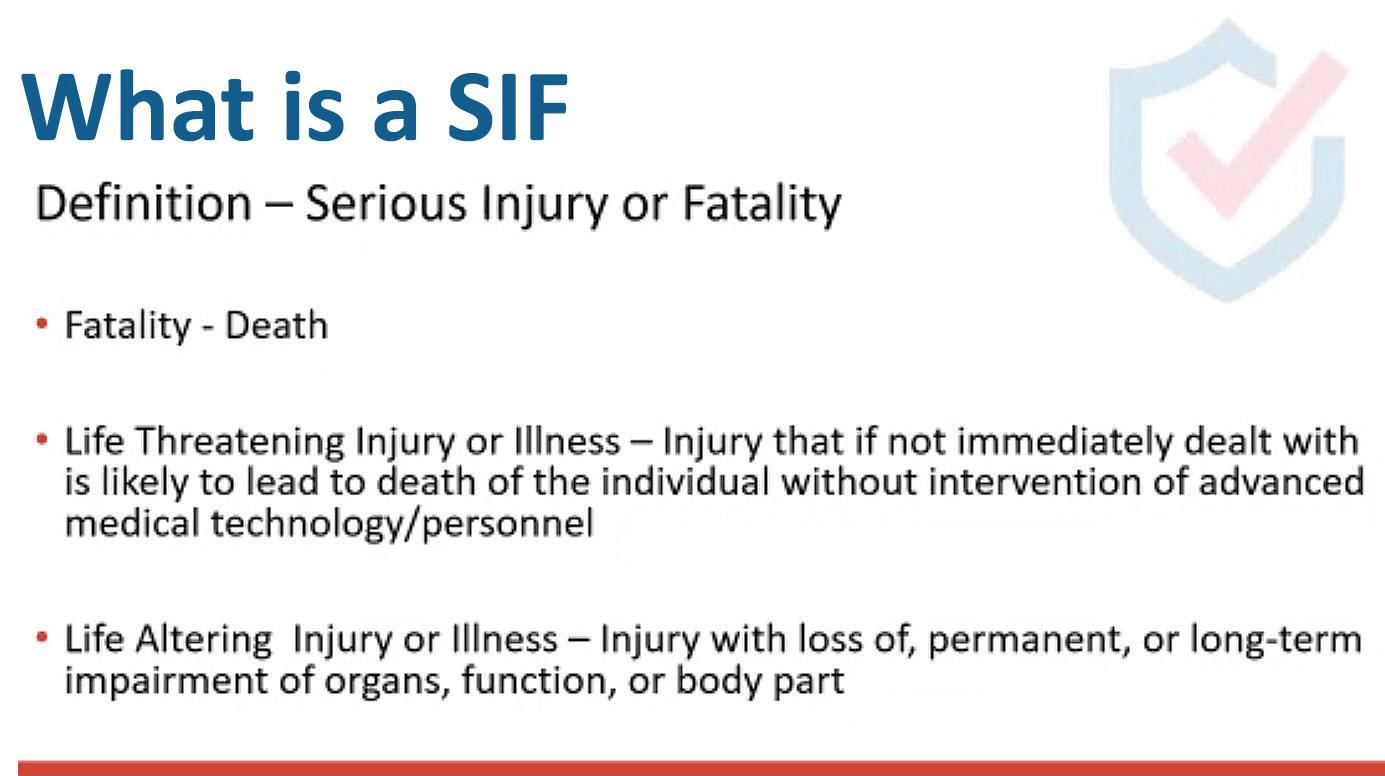
permanent or long-term impairment of organs, function, or a body part. Hencke cited burns as an example of a life-altering injury.
Hencke also shared a story about employees raking coal in a powerhouse. Staff knew that if too much coal piled up, it would release a fireball while raking. They told each other informally about this risk, but it was not reported or documented as a near miss. “Employees didn’t recognize this hazard, that it had serious injury potential and it should be dealt with,” Hencke said.
SIF precursors like this can go unnoticed because they’re missed entirely due to lack of reporting, recognition or knowledge about the reporting process. But SIF precursors can be eliminated before they have a chance to occur, Hencke said.
“Employee ‘tribal knowledge’ in the case of this incident concerning the need to step out of




Ethanol Handling, Handled.

AGI Tramco, a division of AGI manufactures the most complete line of chain and belt conveyors designed for safe and efficient handling of bulk materials for a variety of different industries. AGI Tramco Model GTM and Bulk FloTM are the premier bulk material conveying choices where dependable performance is needed in ethanol production environments. AGI Tramco is an ethanol industry leader and offers customizable, rugged conveying systems to producers across the globe. Contact us today for a quote: aggrowth.com/en-us/brands/tramco
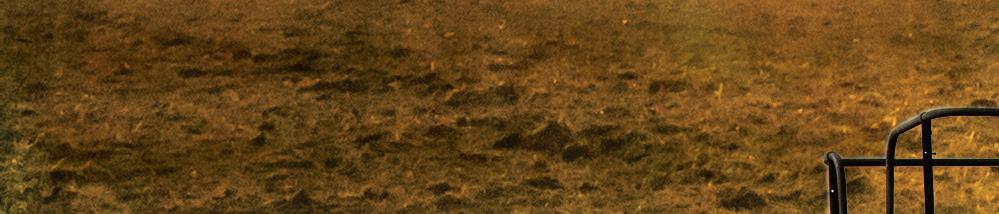
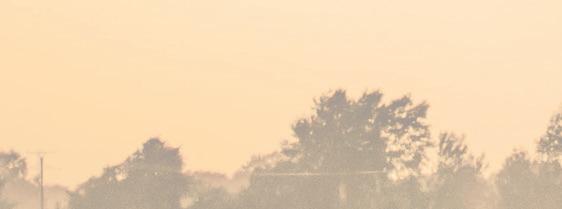
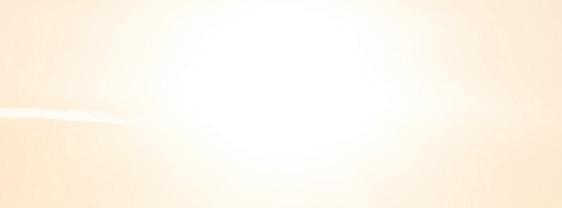

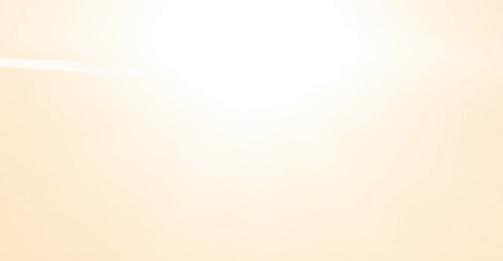
the line of fire of the flare up is great hazard recognition by employees,” Hencke told Ethanol Producer Magazine after his presentation. “This hazard was dealt with internally among operators through an informal procedure—step out of the opening when raking is performed or else you will be exposed to a burn hazard.” During writing of the SOP for this task, the potential flare up was not identified or addressed, he added. Because employees accepted this risk as a part of this particular job and didn’t communicate to management or their respective supervisor, the risk persisted until an employee injury was experienced.
“With recognition of the fire ball hazard and reporting it formally to management or the safety department, additional layers of protection could have been put in place to prevent the burn potential,” Henke said.
“Behavioral based safety (BBS) has played a crucial role in identifying risks similar to the one laid out in this incident. An example of a formidable BBS process involves peer-to-peer reviews through a formal document or observation card. The observation is the vehicle to drive informal conversations about safety between employees, rather than a member of management. Employees can observe each other completing job tasks and provide feedback on safe/unsafe behaviors or procedures. An observation of the particular task—raking coal bed boiler—would have identified this potential hazard or behavior to avoid the hazardous condition (flare up).”
SIF incidents can include mobile equipment operation, energy isolation, elevated work, suspended load, line break/ chemical exposures, confined space, and contractor activities. But not all carry the same SIF potential, Hencke said. In a recent evaluation, PROtect found that 80% of mobile equipment operation had SIF potential, while confined space work was at 100% SIF potential.
“You have to take a multipronged approach,” he said.
Robust near miss reporting would include incident investigation protocol with SIF precursor identification, and review for site-specific operations (hazardous operations, etc.).
Not all incidents are SIF, Hencke cautioned, so reducing SIFs doesn’t necessarily reduce all hazardous incidents. But, of course, they’re the most dangerous and developing a protocol will help protect a plant’s most valuable assets.




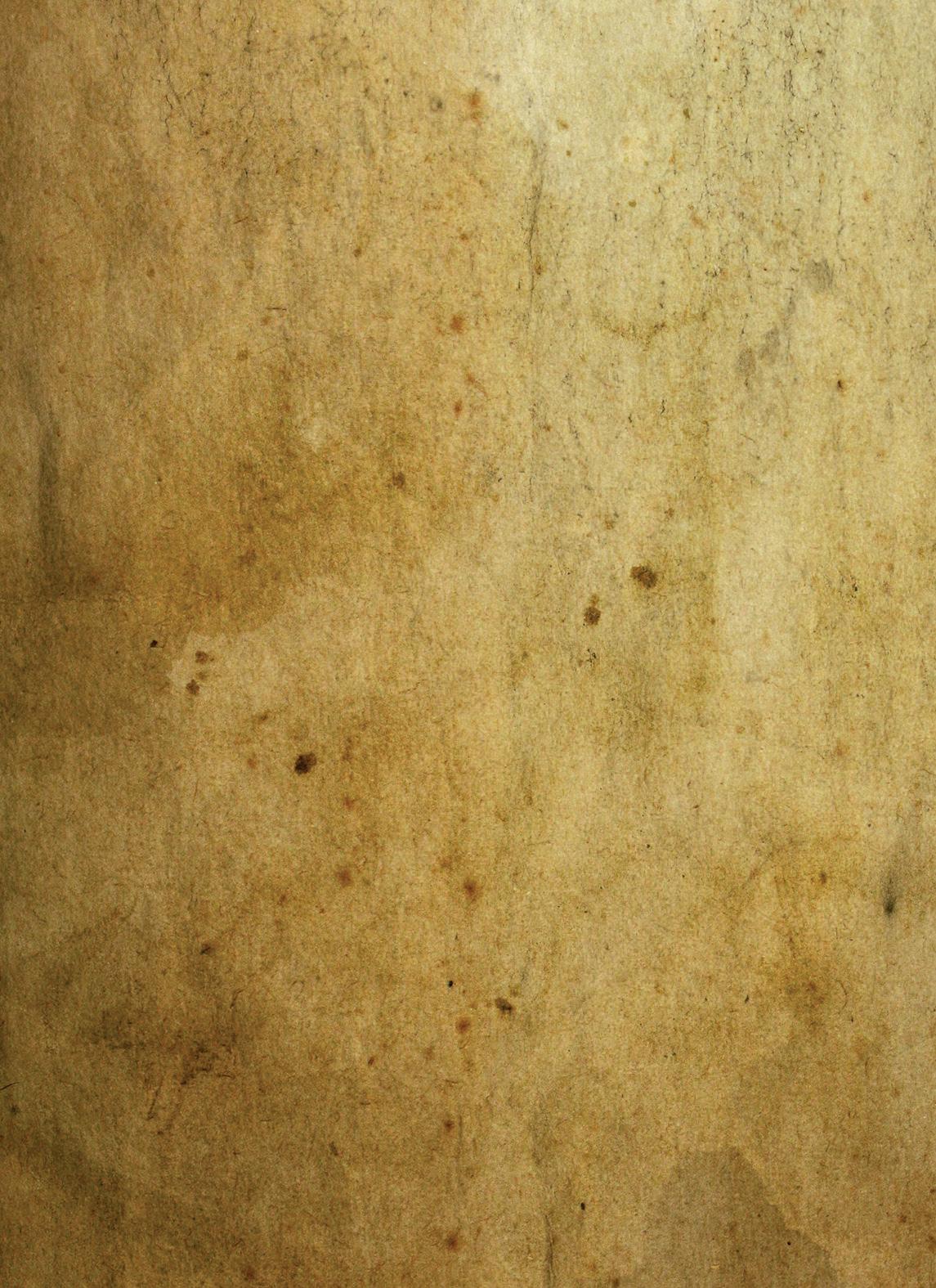
Beckel

PIPE PARAMATERS: During his presentation, Jay Beckel, senior vice president, risk and compliance services at ERI Solutions Inc./PROtect showed this slide about piping classification inspection requirements. PHOTO: JAY BECKEL, ERI SOLUTIONS
Miles of Pipe
Beyond SIF, safety can extend to equipment, as well. It’s important to be aware of different safety and inspection requirements for different piping classifications in an ethanol plant, according to Jay Beckel, senior vice president, risk and compliance services at ERI Solutions Inc./ PROtect. And don’t rely on your nondestructive testing (NDT) provider to keep track of it, he added.
In Beckel’s presentation during the panel, “Miles of Pipe: Assuring the Mechanical Integrity of Your Plant’s Piping Matrix,” he talked about classification, organization, documentation and more. “Process safety information can be very, very vast,” he said. “Today, we’ll focus only on [piping and instrumentation diagrams] P&IDs.”
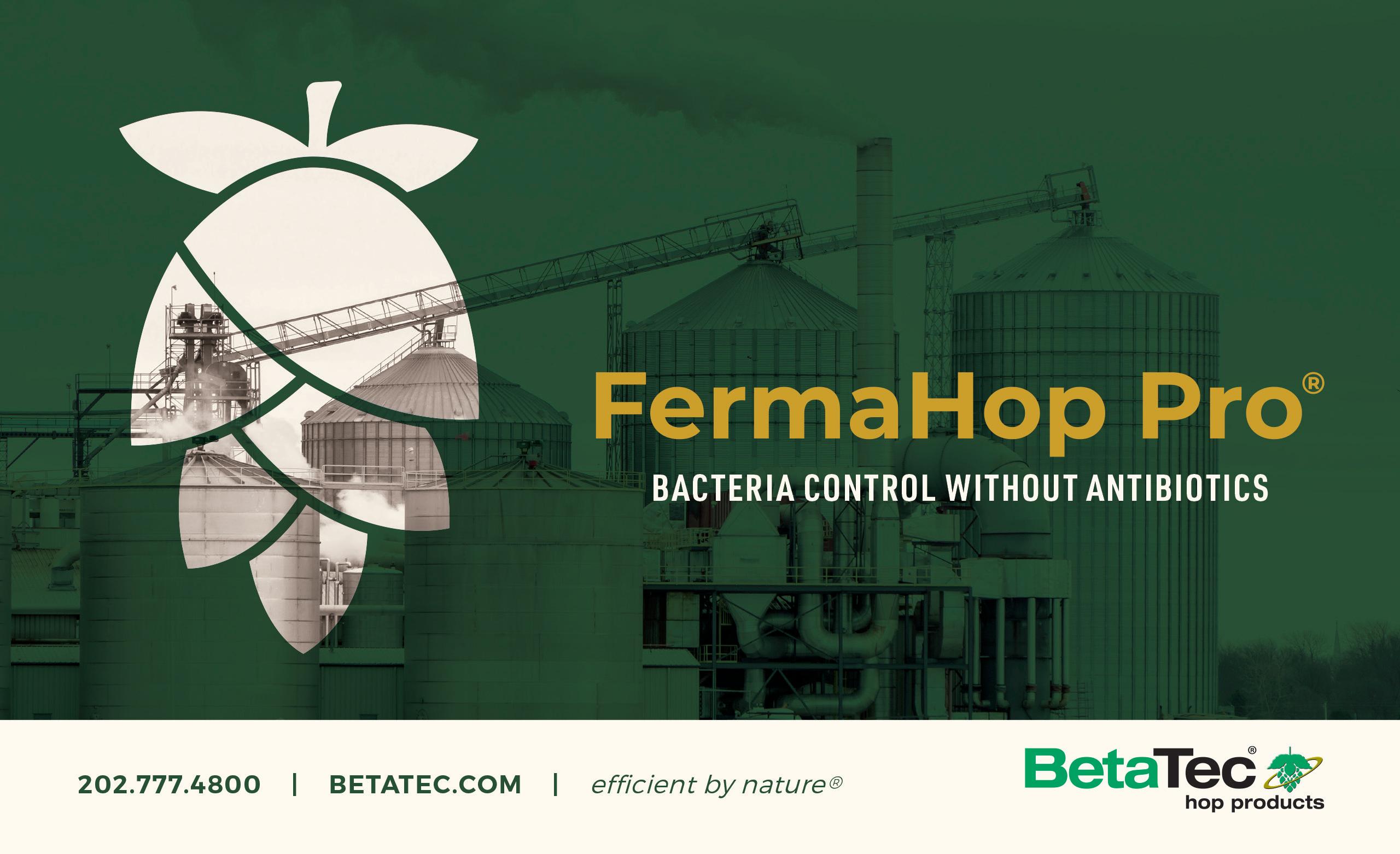
First, Beckel walked his audience through the four pipe classifications, including: • Class 1 – Piping with the highest potential for emergency issues. • Class 2 – Piping that is not otherwise classified. • Class 3 – Piping containing flammable materials but not likely to vaporize, or located in remote areas where no significant consequences are likely. • Class 4 – Piping containing nonflammable and nontoxic materials. “Much of your piping probably is class 4,” Beckel said.
Each classification has its own inspection requirements, timeframe thickness and timeframe visual. But there’s more to consider. “Did any of you know that there could be minimum thickness?”
Of utmost importance in a P&ID is an accurate legend, preferably just one, Beckel says. “With too many, it makes it hard to follow along.”
The legend should include at minimum: materials of construction; line size; pressure rating; whether the pipe is insulated; whether it’s heat traced; coating type; other piping details including classification, which should be on each line of the P&ID; and line numbers for all lines that follow the legend.
“It’s pretty straightforward, but you’d be amazed at the plants that don’t have something on each line for their P&IDs,” Beckel said.
“And you need a documented approach to tie all these things together,” he said, listing pressure vessels, piping and tanks, transmitters and pumps. “All the pieces of the puzzle you have in your

| continued on page 24 |

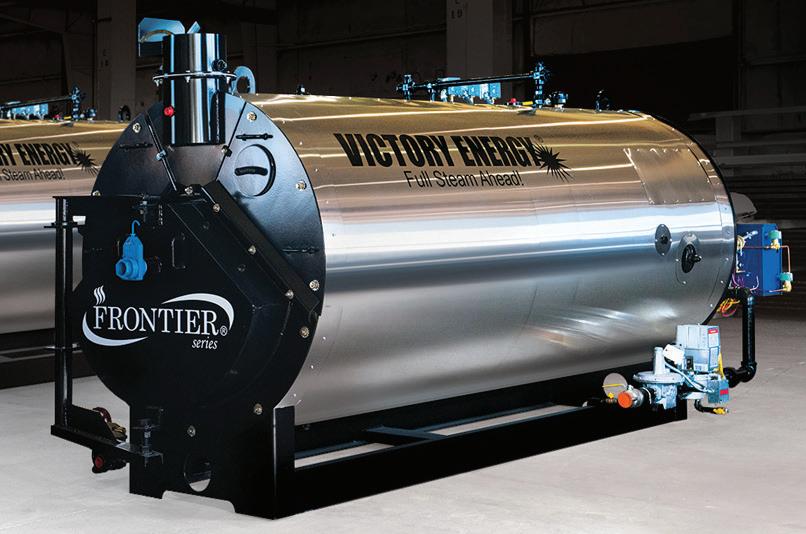
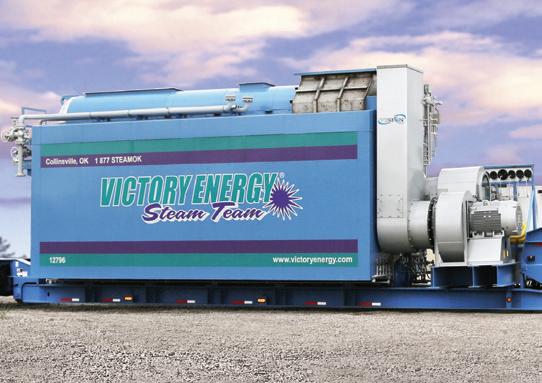

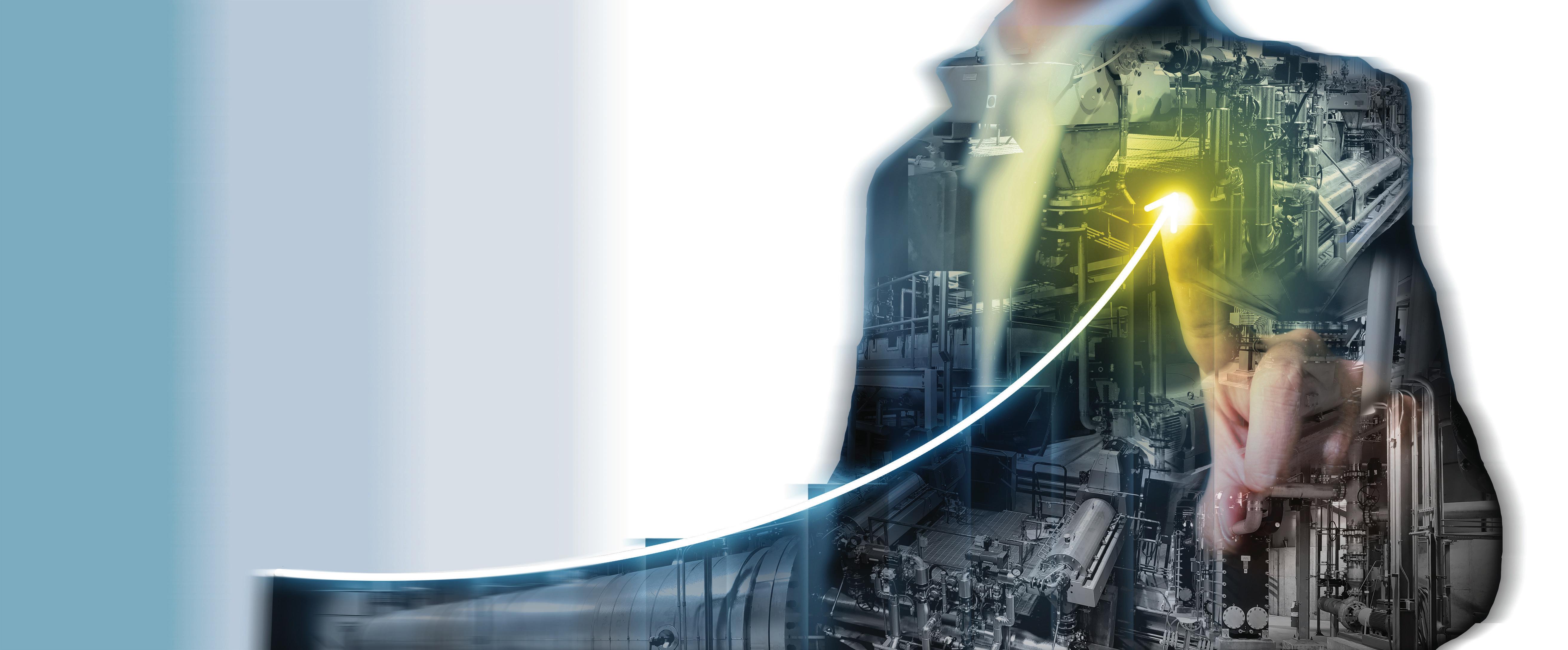

| continued from page 20 |

Through infallible standards, laboratory analytics and compliance solutions, Bion makes your work more-efficient, more-profitable and higher-performing.

To ensure you have the highest-quality data and most-efficient processes, we offer three customer-centric service lines: Axion, Soliton and Compli.
It’s important to be aware of different safety and inspection requirements for different piping classifications in an ethanol plant... And don’t rely on your nondestructive testing (NDT) provider to keep track of it.
plant, you should have in your written approach to pipeline integrity.”
It should be plant specific, not a prepared program, he added. “Hold your contractors and staff accountable.”
Traditional Vs. Advanced
NDT can be traditional or advanced, Beckel said. Traditional is a visual approach with thickness. Advanced can include magnetic flux leakage, automated ultrasound thickness mapping, guided wave technology and pulsed eddy current.
Of magnetic flux leakage, Beckel said, “The technology is super. It really helps to ID pitting and gradual wall loss.” But it only works on carbon steel, he added.
Automated ultrasound thickness mapping needs to be on an insulated
surface, he said, and can be used manually or in an automated fashion. “Automated UT mapping is pretty advanced. It’s a good system to have in place. It can really identify a lot of things you could miss.” The pipes must be clean for this method, he said.
Guided wave can inspect up to 1,150 feet of pipe from one location. “It’s a great technology for underground piping or other inaccessible piping,” he said, adding it has 100% coverage even with clamps or sleeves in place.
Pulsed eddy current is good for corrosion detection, as it can scan through thick insulation and even fireproofing, Beckel said. It can map and accurately identify remaining wall thickness without removing insulation.
Organization
The P&ID might have 150 to 300 different line numbers in a given section of the plant, Beckel told his audience. So, when spread out to the entire plant—the slurry tank all the way to loadout—the number grows exponentially. “It’ll take some organization, and spreadsheets might not be the best way,” he said.
Beckel strongly recommended an asset Integrity management platform that organizes by area or line number, has the capacity to compare with other facilities in the industry or corporation, easily identifies corrosion and erosion, and ties in with the incident management system.
Armed with all this information, Beckel cautioned his audience on one last item:
“Don’t fall into the trap of only regulatory requirements. This needs to be a risk-focused approach, not solely about regulations.
Author: Lisa Gibson Editor, Ethanol Producer Magazine 701.738.4920 lgibson@bbiinternational.com LEGEND ACCURACY: Beckel illustrated with this presentation slide what a P&ID legend should include. PHOTO: JAY BECKEL, ERI SOLUTIONS
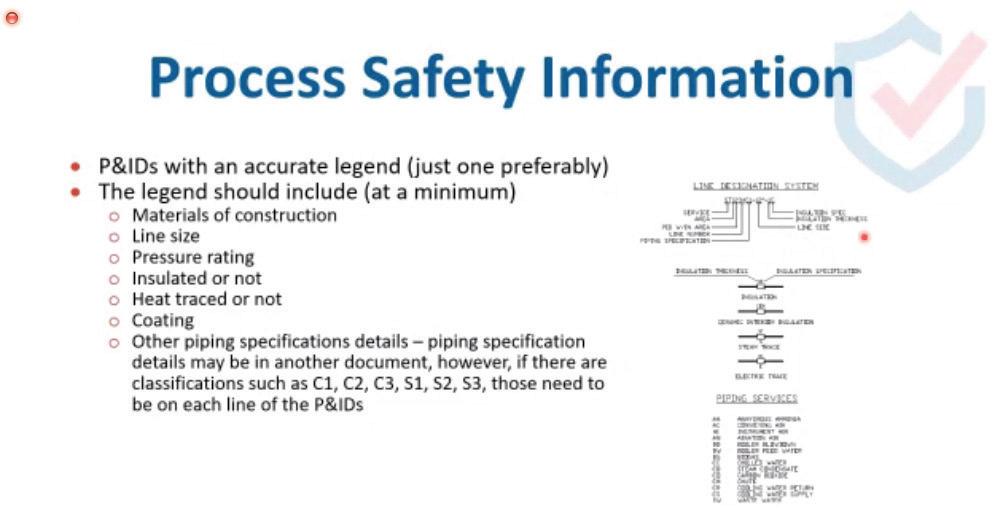
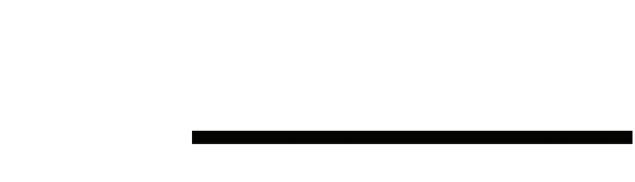
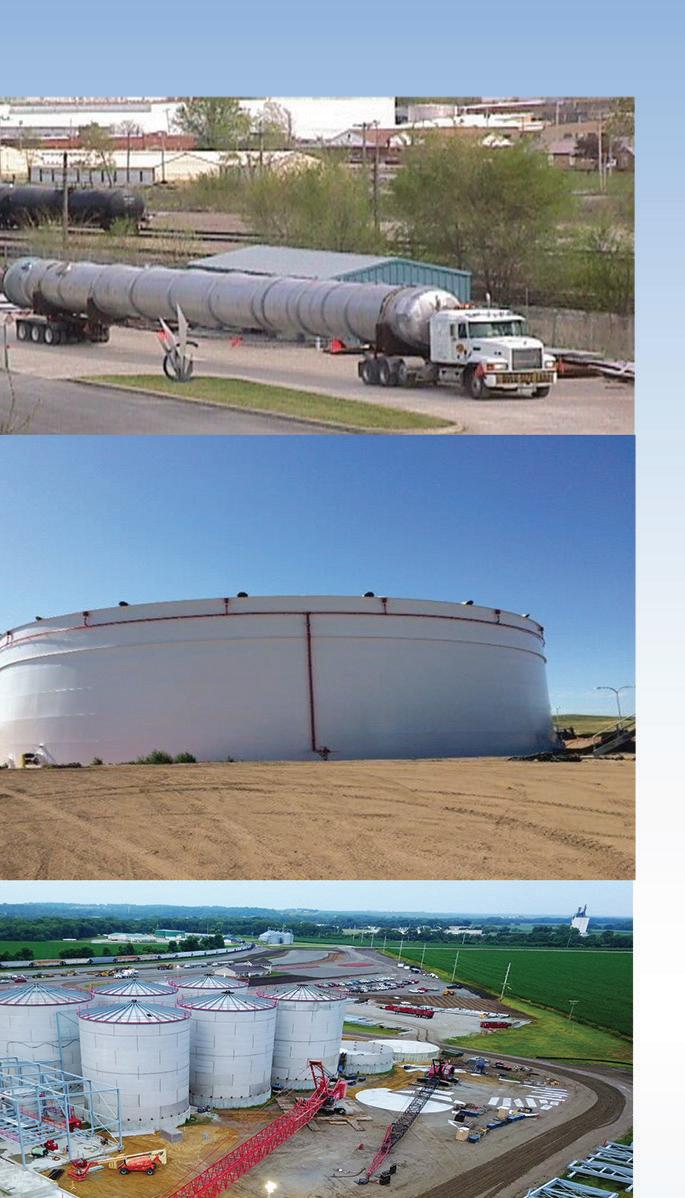
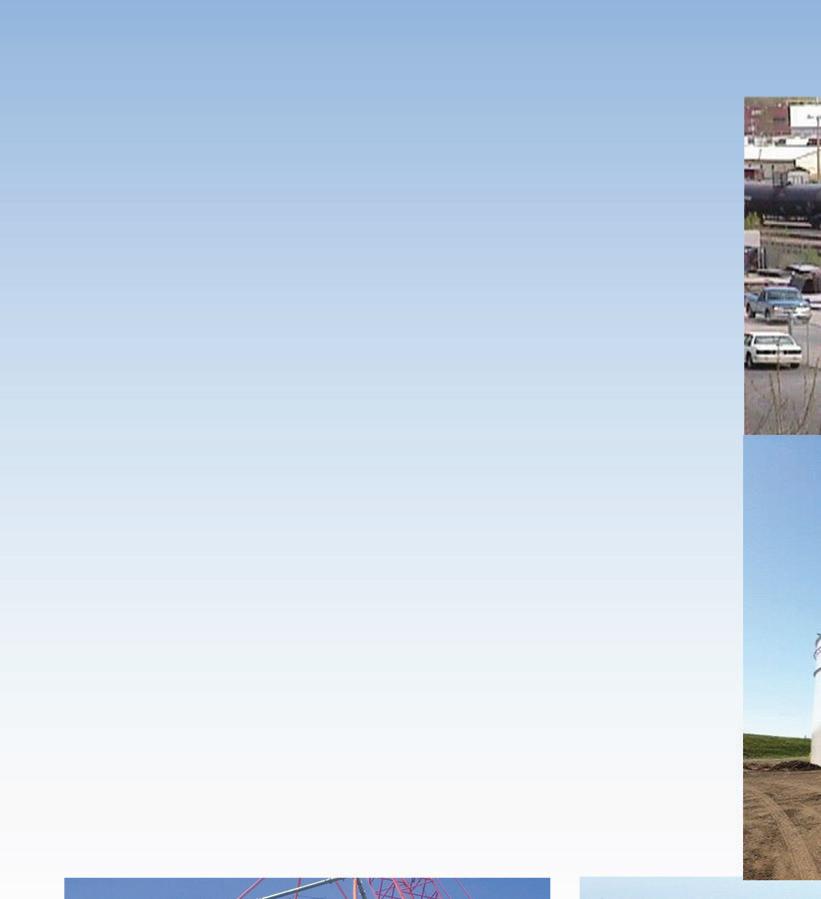


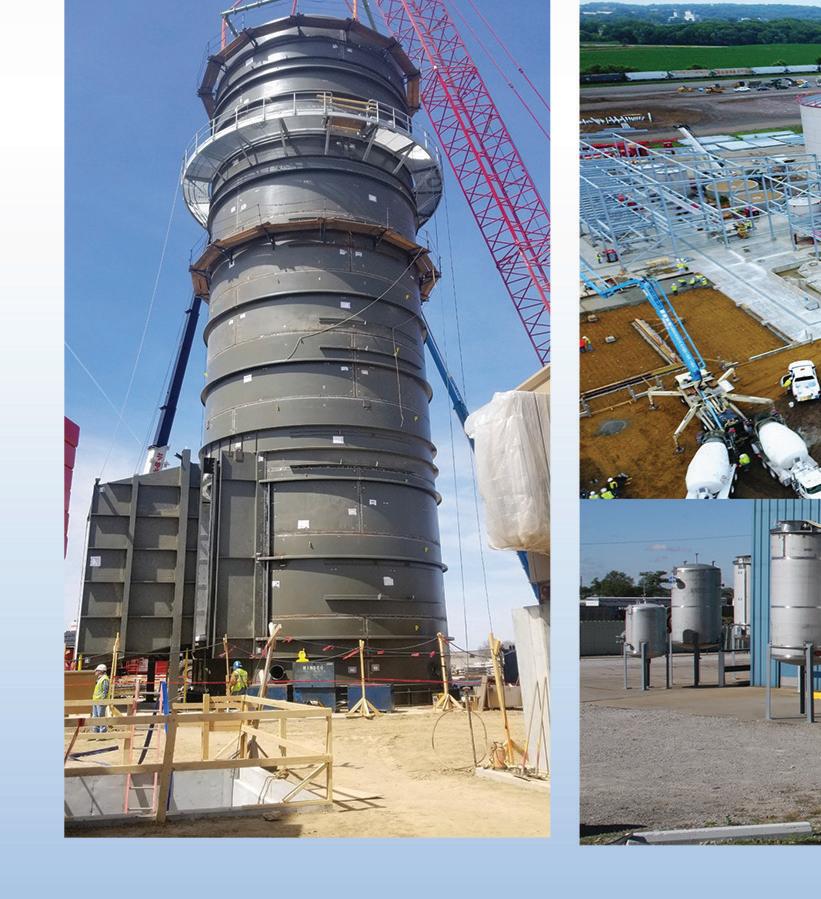