
10 minute read
DATA
to From Reactive Proactive
Data analysis for process improvements can range from simple to complex, low cost to high. In many plants, the keys to optimize maintenance, cleaning and overall performance remain unused. By Lisa Gibson
The data necessary for process control, predictive maintenance and even predictive cleaning is already being captured at ethanol plants. The next step is to figure out how to use it to boost efficiency.
Producers are starting to come around to digitalization of existing data to improve overall performance, says Don Mack, industry and automation alliance manager with Siemens. “We can come in and look at the overall situation and see where we see potential for improvement at a high level and identify low-hanging fruit.” Producers can “dip their toes” in digitalization with no large investments, he says.
“The sensors are already there, and they see an opportunity to improve the overall performance of their plants and produce as much ethanol as possible.”
Some do make investments in bettering their datadriven operations, including in automation and real-time analysis, says Ryan Magner, chemical engineer with Black & Veatch. Automation creates a data funnel, he says, reducing 1,500 data points into 15 or 20 anomalies to analyze.
DATA-DRIVEN OPERATION: The collection, proper analysis and application of data in an ethanol plant can boost efficiency, enhancing production and competitiveness in a tough market. PHOTO: BLACK & VEATCH
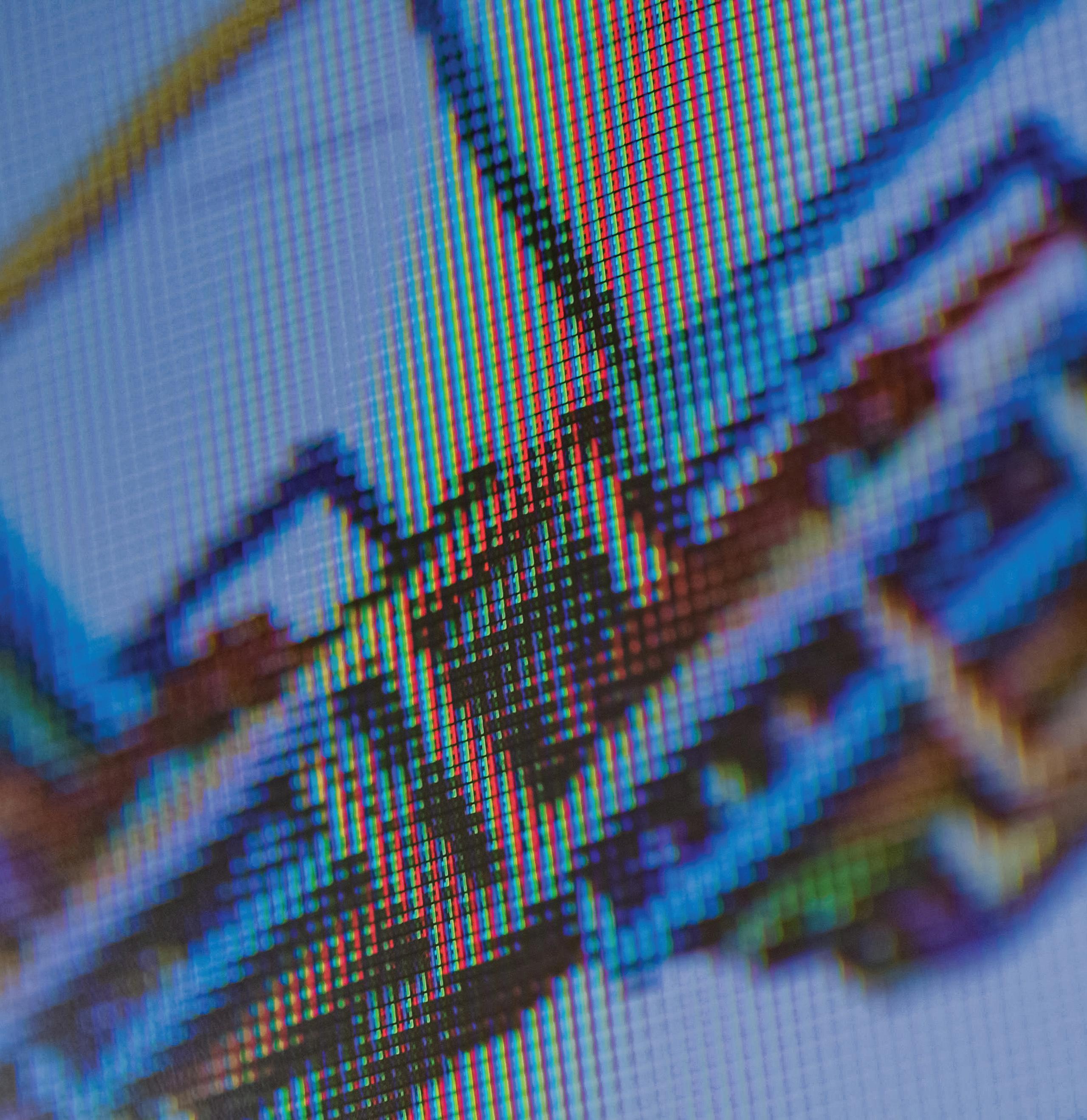
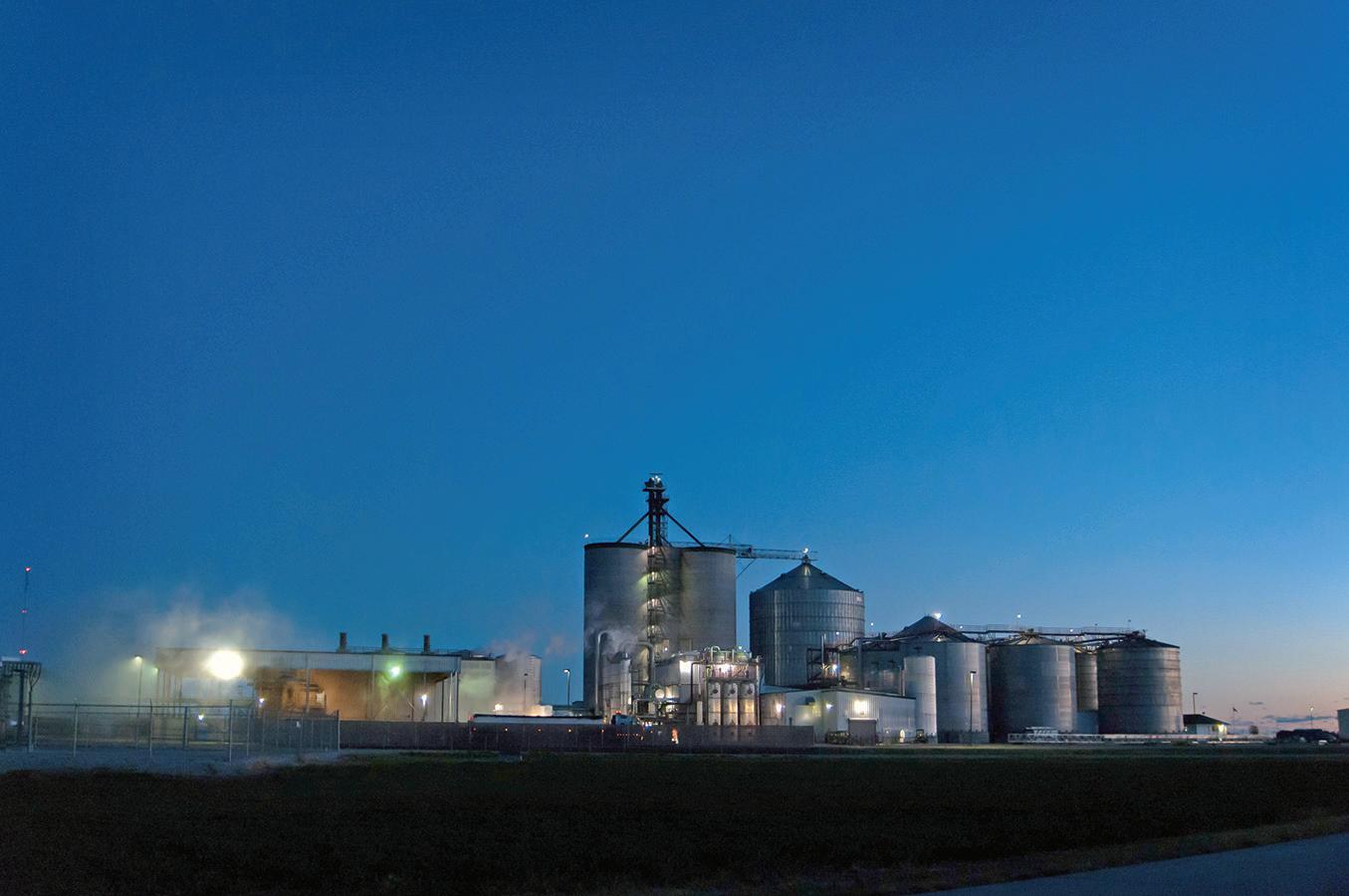
The Specialist in Biofuels Plant Appraisals
• Valuation for nancing • Establishing an asking price • Partial interest valuation
Few certi ed appraisers in the United States specialize in ethanol plant and related biofuels properties. Natwick Appraisals o ers more than 50 years of worldwide experience. Your appraisal will be completed by a certi ed general appraiser and conform to all state and federal appraisal standards. Our primary specialty in industrial appraisal work is with ethanol, biodiesel, and other types of biofuel facility appraisals, including cellulosic ethanol plants.
Call us for a free, no-obligation consultation today.
800-279-4757 701-793-2360 Natwick Appraisals 1205 4th Ave. S., Fargo, ND 58103 www.natwickappraisal.com natwick@integra.net
DATA DEMO: Data provide an edge in early detection of emerging issues. PHOTO: BLACK & VEATCH

And Anne Chronic, director, market analytics for Phibro, emphasizes the predictive cleaning benefits of data analysis.
Whether a producer’s interest in their data lies in maintenance, cleaning or process control, it all boils (or ferments) down to efficiency.
People, Processes and Tools
Magner says Black & Veatch has a few main focuses when it comes to data. “We think about it in three parts: people, processes and tools. I like to think you start with the tools: That’s the software.
“Best practices—you should have some type of software that’s doing data analysis in real time,” Magner says. “Some look at trends and manually analyze their data, and you’re going to miss a lot that way. You really have to have a piece of software that’s taking a holistic approach and looking at your entire facility and then detecting anomalies.”
Beyond software, the right processes and people are crucial. A system that sends emails about anomalies detected in the plant isn’t useful without the knowhow to evaluate and address them, Magner says. Hundreds of alerts could come in each day on a fleet of ethanol plants. “It’s important to have the right people involved and a good set of processes to provide actionable items to the site.”
That sheer volume of data provides a
Introducing the SYNERXIA ® Gem Collection


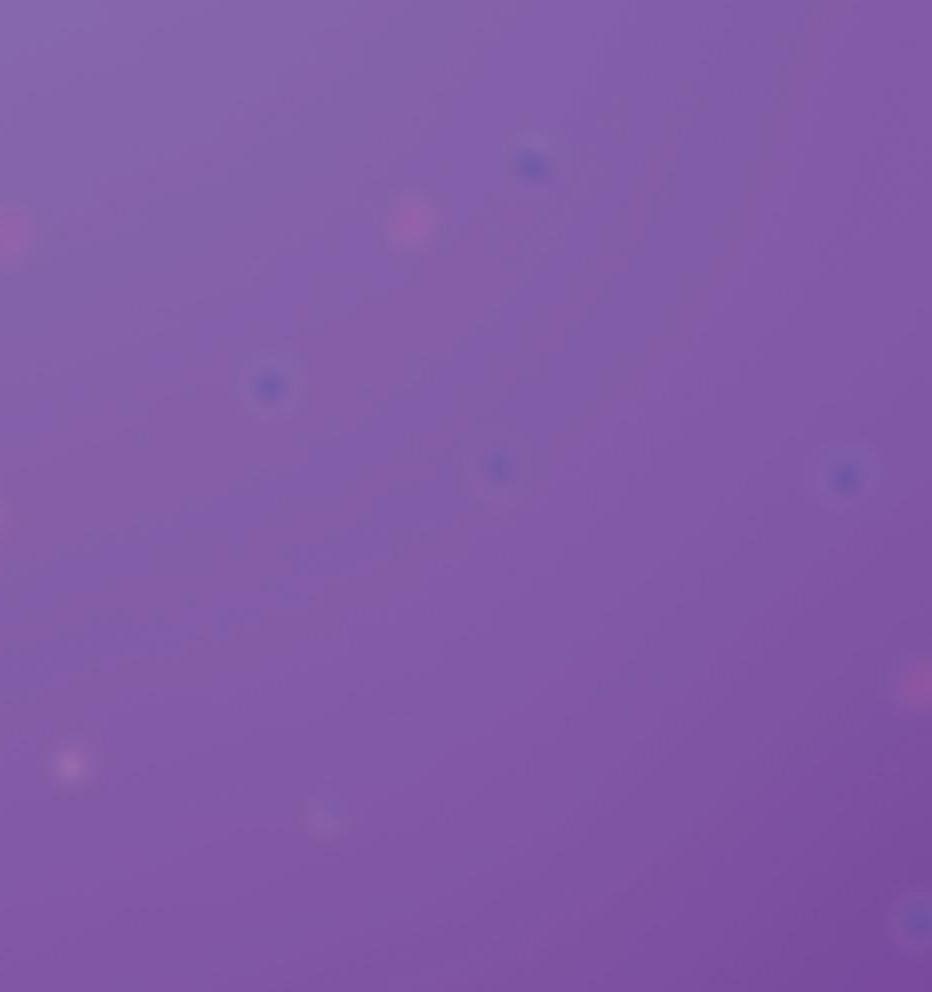
The next advancement in high-performance yeasts to make your plant shine.
www.xcelis.com

good reason to deploy automated and realtime software, Magner says. Looking at data and trends each morning from the night before illuminates 50 or 100 data points, when there are about 5,000 in an ethanol plant, he says. “Maybe 1,500 you realistically care about, but you’re only seeing 5, 10% of the total data you’re able to analyze, when you’re doing it in a manual way, not automated.
“That’s the first way you’re vulnerable there—just the scale. You’re just not able to cover all the of process variables that can cause failure.”
Relying on DCS alarms, for example, to detect bearing temperature and vibration is a reactive method that might come too late, he says. “Our software will look at best practices, look at all data continuously and detect that failure way before it gets on an alarm and before it gets into the engineer’s daily checks.”
An automated system also adds context that could generally be overlooked. Bearing temperature of 150 degrees during the summer months is good, but in the winter, with much lower outdoor temperatures, that same 150 degrees might be 10 or 20 degrees higher than it should be.
“You would never catch that on an alarm, but our software is going to know, at this ambient temp and load, this is getting too hot and it could fail when it gets warmer outside,” Magner says.

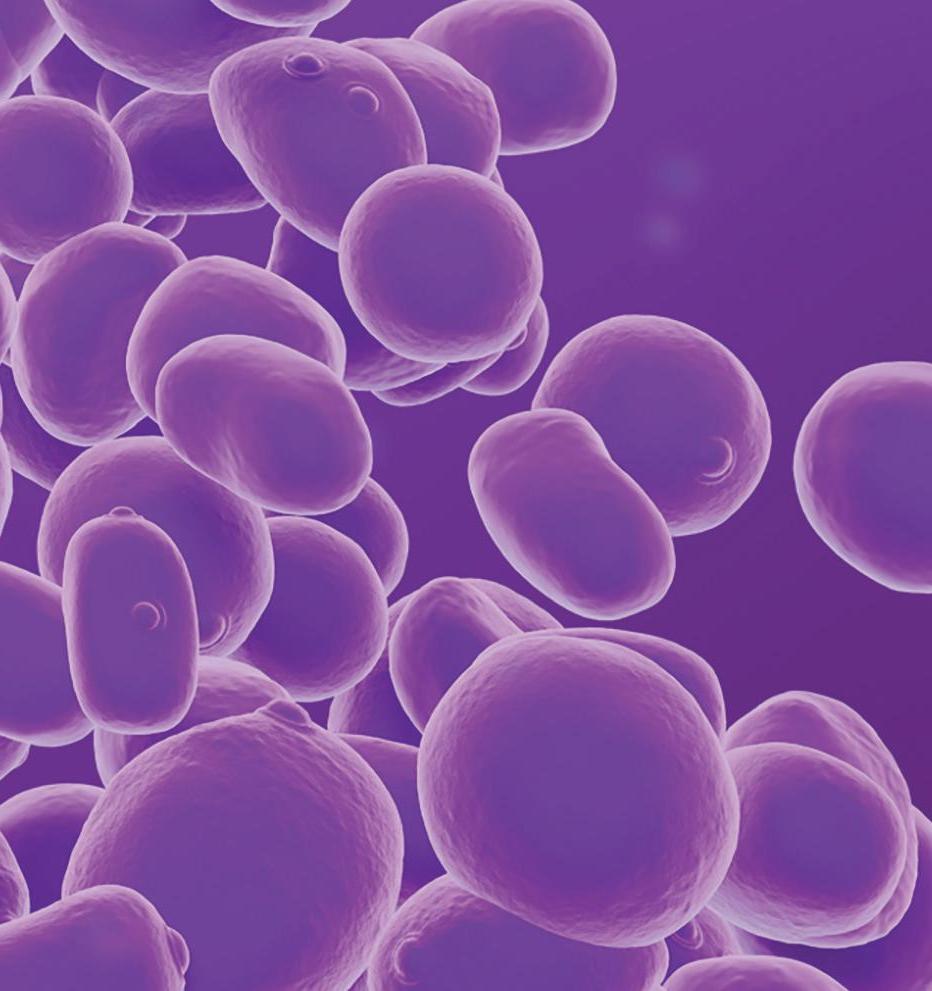

877-811-4073 www.agcountry.com Proudly serving customers across all facets of agriculture
Process Control, Predictive Maintenance
Mack says most of Siemens’ customers in process industries are aware of and quickly learning more about digitization techniques. “They know there are capabilities out there by applying data analytics that can improve operations, that can improve maintenance.”
Digitalization converts data into information that can help make actionable decisions to improve performance, Mack says, using valve monitoring and maintenance as an example.
“To maintain and avoid problems, they’ll apply preventative maintenance, establish a routine where once a month or so, they look at the control valve. Invariably, it’s ok and they don’t have to do anything, but they still spend that cost and that time. What we can do with a valve monitoring type of process is we collect information from a smart valve positioner that is attached to the valve.”
The positioner sends a signal to the valve to move it for desired flow. Besides making that adjustment, that valve positioner can collect useful information, such as how many times the valve was opened and closed, or the maximum temperature it reached.
Data Siemens collects is compared to known parameters to identify thresholds that indicate maintenance is needed. “Now you’re moving toward predictive maintenance instead of preventative, with monitoring,” Mack says. “There are actually tools now that can calculate a maintenance date based on that data that’s coming back.”
And apps can help now, too. “What’s kind of happening is that you’re developing a library of apps … that you can apply and it really is starting to follow what we’re doing in real life. If you need to address a specific problem, usually you can find an app out there.”
Siemens has tools for its customers to develop their own apps, too, if a more tailored approach is optimal. The company
DATA POINTERS: Engineers collaborate at the Black & Veatch Remote Monitoring & Diagnostics Center in Kansas. PHOTO: BLACK & VEATCH

can offer a digital twin, as well, a virtual version of a plant or process that can conduct research and development to analyze effects of process changes or improvements.
Full digitalization of data and its subsequent use is starting to take off in the ethanol industry, Mack says. “It’s still new and we’re still having costumers come to us to better understand where they can be using this. But we do find that most of our customers these days have some sort of digital initiative within their companies.
“The keys are that customers shouldn’t be afraid,” Mack says. “If it seems overwhelming, if it seems too expensive, it doesn’t have to be. The first step is understanding what you have—what data, what issues you’re encountering, and will data available be able to be analyzed to address issues?”
Calibrate for Cleaning
Chronic says Phibro has started applying data even to cleaning schedules in ethanol plants. She doesn’t hide her enthusiasm about the possibilities.
“We do look at fermentation data, and we look at that a lot, but what we’ve learned and started to do is leverage our fermentation data analytic knowledge and apply it in other areas of the plant. That’s where we’ve really found we can enhance the application of our processing aids.”
Heat exchangers, for example, often are cleaned routinely, without drawing on existing data to plan for optimal performance. “We can provide additional insight and knowledge,” Chronic says. Data can show the benefits of cleaning on certain timelines, allowing further improvements. “So really guiding customers on making a data-driven decision on when they clean things, rather than just an arbitrary schedule-type basis.
“In addition to the back end of the plant, benefits can also be seen in the front end of the plant via increased beer well feed temp, as a result of improved cleaning of beer/mash exchangers.”
Trends in the data can also detect whether a certain evaporator is taking the majority of the steam load. Data collected while that evaporator is being clean would show it was dominant, providing an opportunity to improve efficiency, Chronic says.
Many plants have transmitters that haven’t been maintained or used because producers don’t know that data can be useful, Chronic adds. “Usually, the equipment is there to monitor, but they might need to
XCELIS® Yeasts SYNERXIA® SAPPHIRE

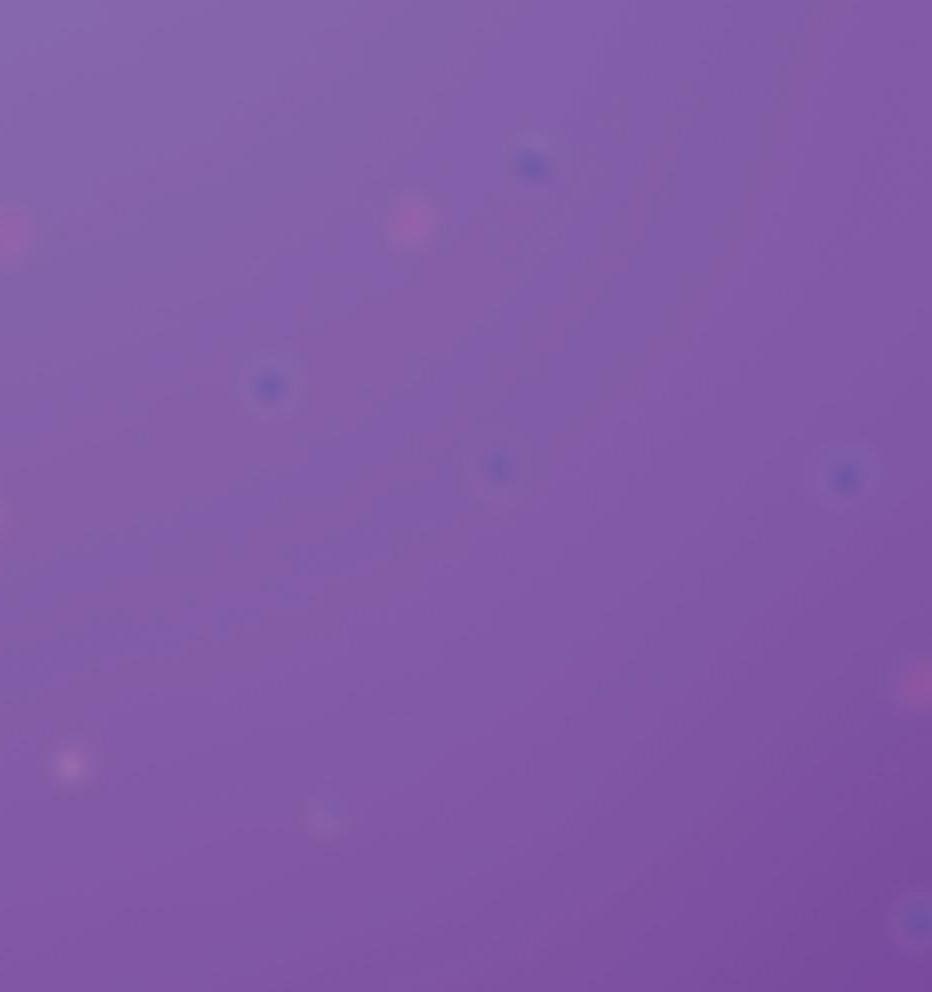
The most powerful combination of yield, robustness and enzyme expression in a yeast.
www.xcelis.com


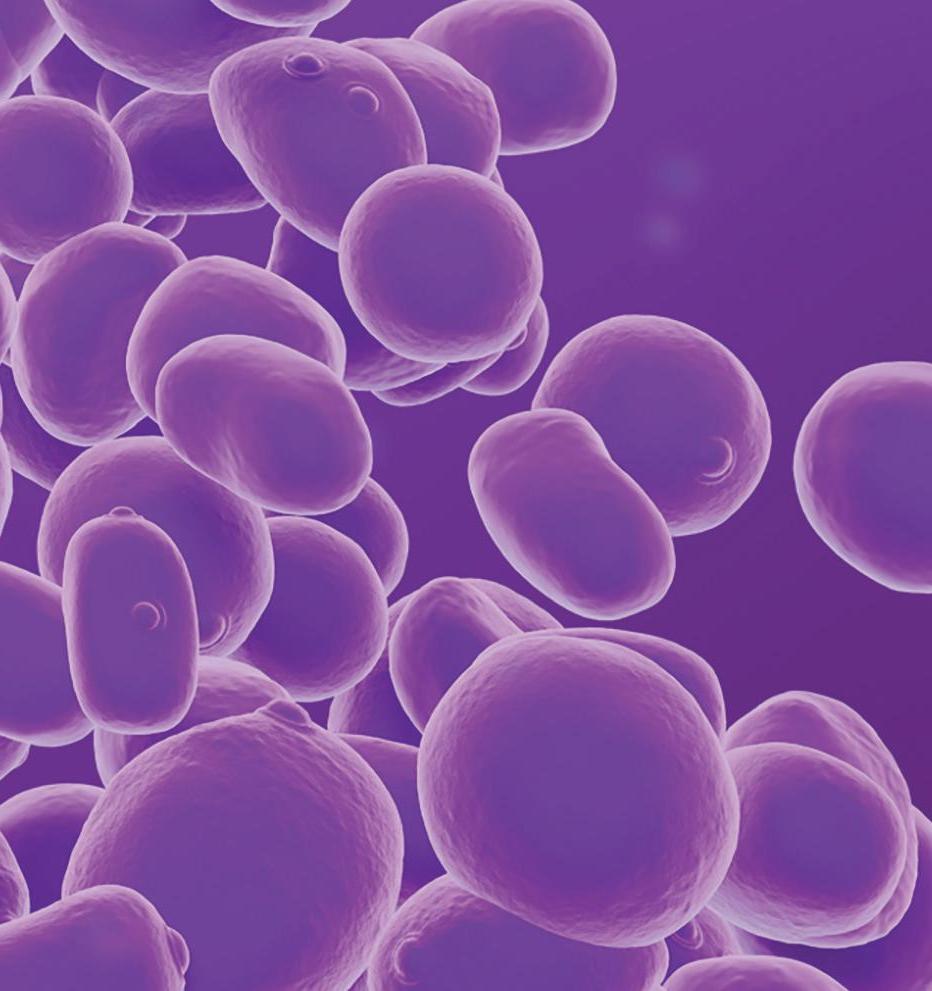

SOURCE: SIEMENS

calibrate or do a quick upgrade. All at once, that can really enhance the understanding of what’s happening and how effectively they’re doing things in the plant.
“We’ve had some really great feedback from customers. Many admit they haven’t approached things like this before.”
Beyond routine cleaning, plants working with Phibro have been able to extend time between hydroblasting. “Plants are making decisions that directly affect their performance,” Chronic says. “We’ve seen benefits in reduced steam usage, improved production consistency, better heat transfer, and optimization of cleaning product usage and effectiveness.”
Chronic says the data analysis supports Phibro’s new total cleaning program. “We see this as a way to help producers go to the next level.
“It’s an exciting area. I definitely am someone who has always been driven by data, so this is really exciting, partnering with plants.”
The Nuts and Bolts
One of the most common mistakes plants make in data collection, analysis and application? “Not doing it,” Magner laughs. “Not having real time analysis, not looking at the entire facility and seeing the whole picture. You have all this data available to you, but you’re just not using it.
“There’s a lot of nuts and bolts and things going on behind the scenes, and at the end of the day, the point of this software and what we’re trying to do is to prevent failures and improve operational efficiency.”
Mack and Magner emphasize that data-driven operation plays a crucial role in keeping ethanol plants competitive.
Magner says, “Maybe the plant down the road has this monitoring system and they’re preventing three, four, five downtimes a year, and you aren’t. We know how competitive the ethanol market is. Especially in the past year, we’ve seen how tight it’s gotten.”
To keep that competitive edge, to maintain and optimize efficiency, data can provide a meaningful boost. And it’s easy to start, Mack says.
“The first thing is just to look at it, whether they do it themselves or bring in companies such as Siemens or others to evaluate the situation. We think that’s the best way to get started.”
Author: Lisa Gibson Editor, Ethanol Producer Magazine 701.738.4920 lgibson@bbiinternational.com
XCELIS® Yeasts SYNERXIA® RUBY
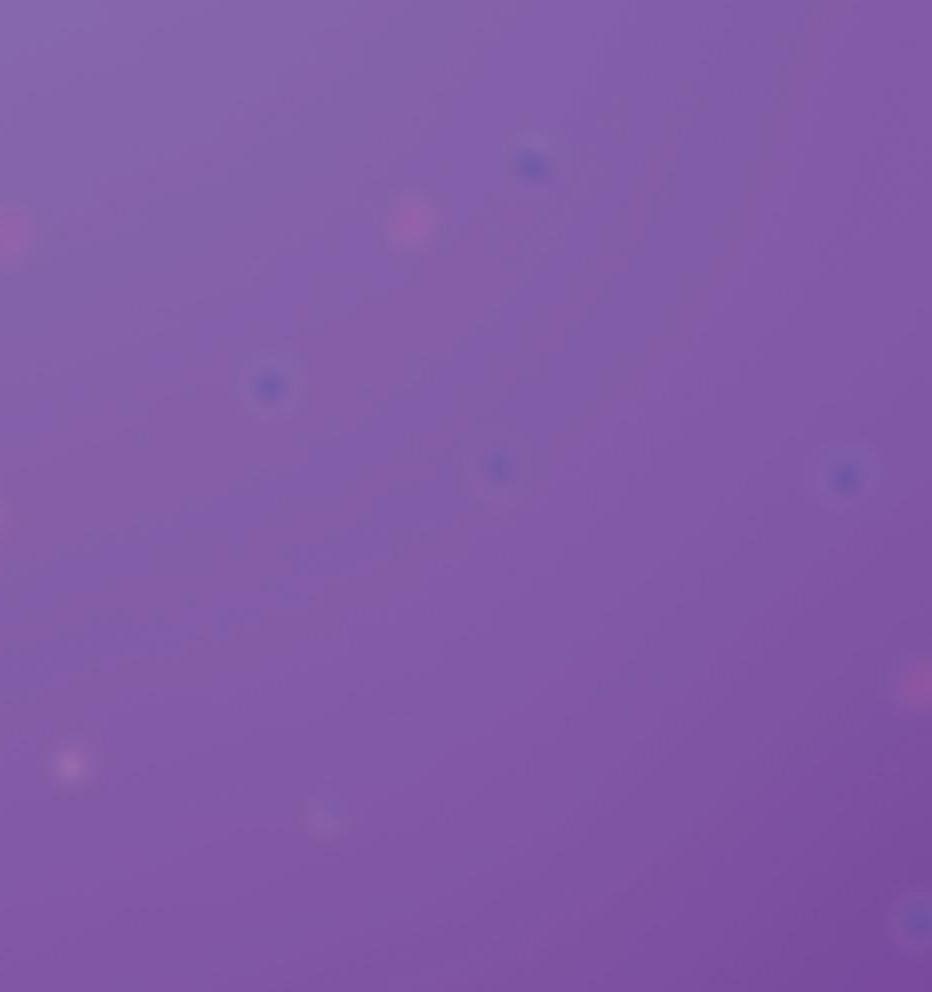
The new standard in high yield yeast driving plants to the peak of performance.
www.xcelis.com


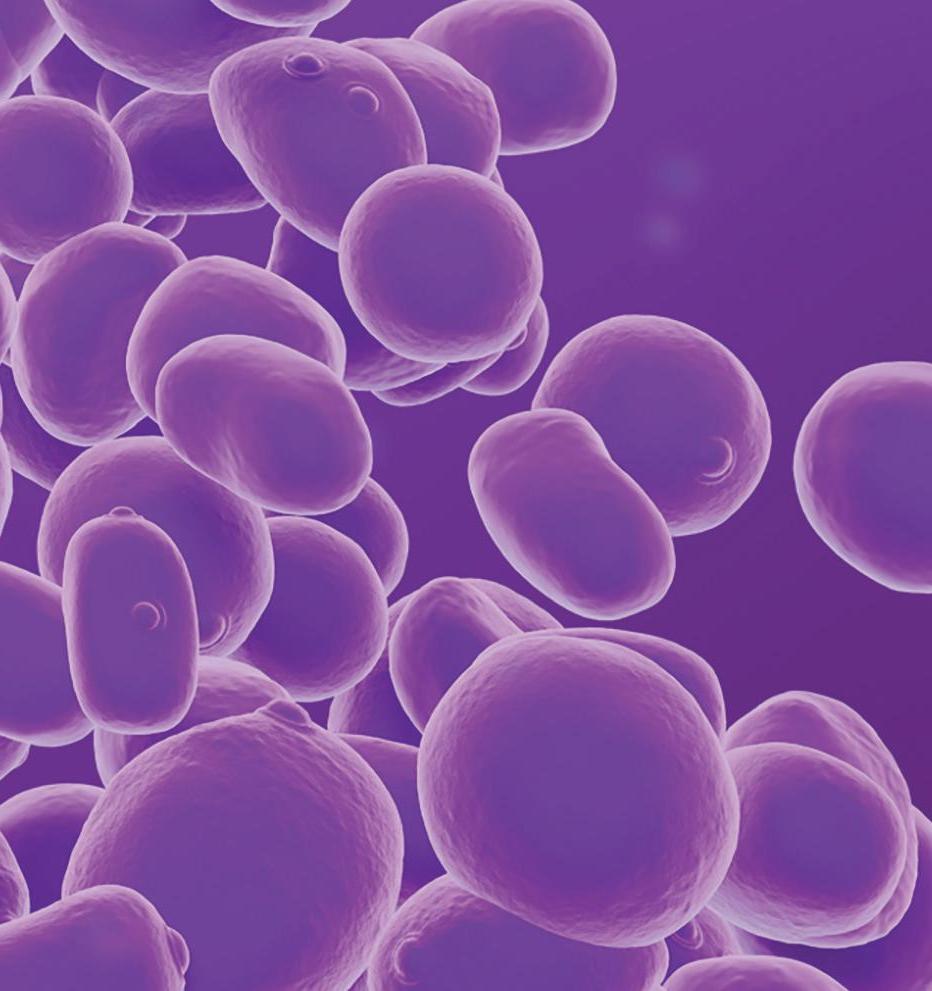