
10 minute read
MAINTENANCE
CMMS SCANNING EFFICIENCIES
Fully utilizing Computerized Maintenance Management Systems can tighten inventory, reduce overtime, and increase equipment life and plant uptime.
By Susanne Retka Schill
With the hundreds of systems and thousands of individual components needing regular maintenance in an ethanol plant, computerized maintenance managements systems (CMMS) have long been a tool to keep the plant humming along.
New methods such as scanning bar codes and using mobile devices have made things easier, but the basics haven’t changed since CMMS was first deployed, says Joel Tesdall, president of Mapcon Technologies Inc. “CMMS came out in the early ’80s. The base function of CMMS back then is the same as now: Tracking work orders and preventative maintenance.”
But while CMMS may be common across the industry, not all producers are using it to full capacity, Tesdall says. The initial step that most do is build equipment and parts lists and maintenance schedules—lubrication every so many days, bearing checks, etc. The software then generates preventative maintenance (PM) work orders on a daily or weekly basis. Maintenance technicians use the work orders to plan and record their work, keeping a record on each piece of equipment tracked in the system.
“From there, it depends on management and how detailed they want to get,” Tesdall says. Tracking inventory is most often next and it expands from there—purchasing, project management, human resources scheduling, troubleshooting, checklists and internet and bar code technologies.
Besides an increase in asset lifetime because of better maintenance, CMMS can become a powerful tool for improving productivity, Tesdall says. “Processing work orders, tracking efficiency, finding and processing parts—things that seem little, but they become huge when you implement them. For instance, you have a work procedure that comes up that needs five widgets. The tech has to find those widgets on the shelf in the stock room somewhere. If you’re not organized, it can literally take that guy an hour to find those parts. That’s that one day. How many times does he do that
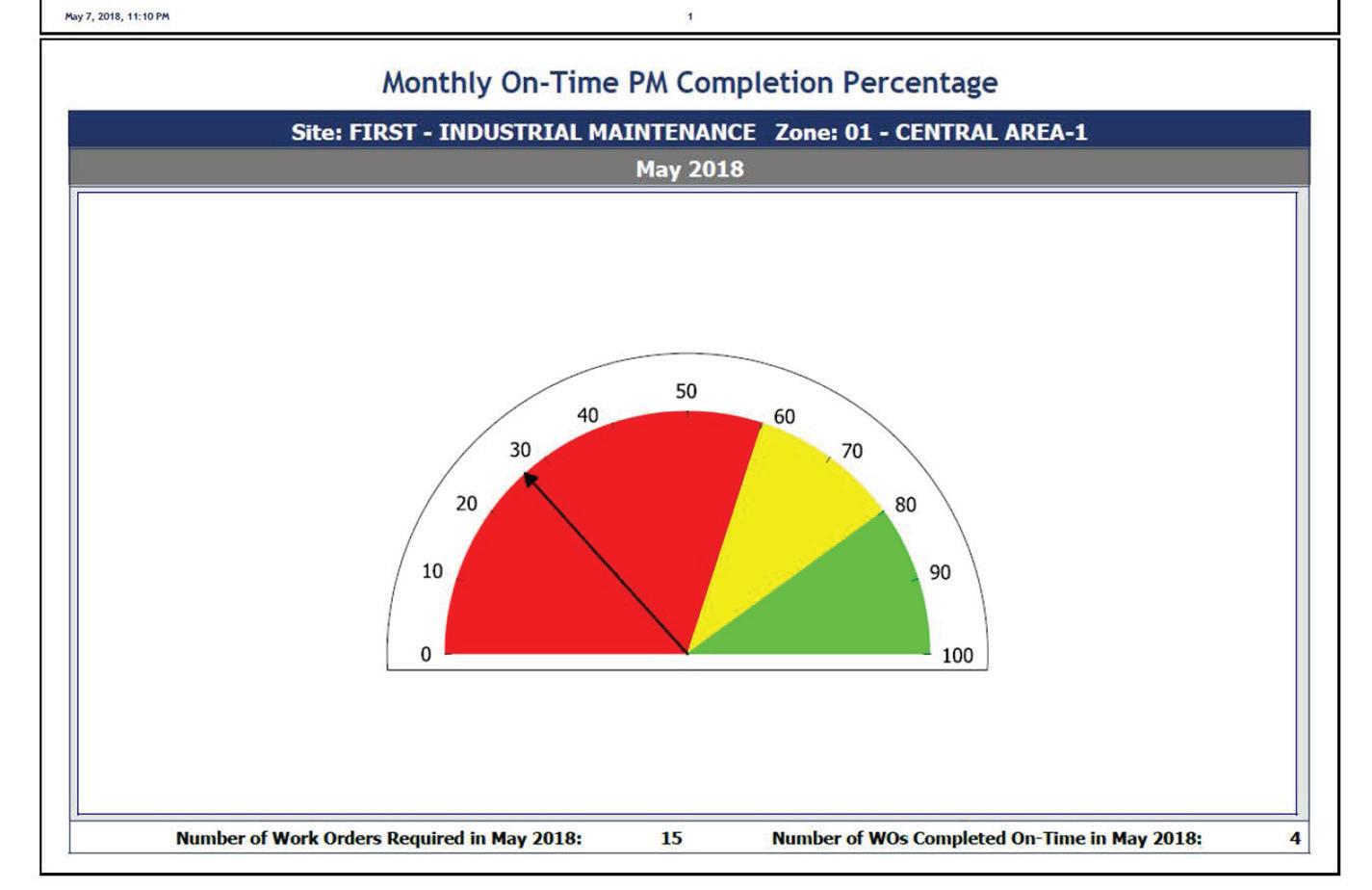
Example Report PHOTO: MAPCON

in a week? In a month? A year? Now assign a cost to that and multiply it out. That’s a big number, just for something as simple as that.”
A fully implemented inventory control knows of an upcoming PM requiring a bearing and a filter, makes sure they’re in stock, or generates a purchase order. “When the maintenance techs get that work order, it says the parts are in this store room, in this bin. They walk over and get it. Or maybe the storeroom clerk has it sitting on the table, because he was informed of it. Now they go out and work. You may have cut that time in finding parts by 80%. That’s productivity. Multiply that out by a year and how much a tech cost you. That’s a huge dollar.” He cites a plant that saved millions in a year. “The return on investment can be huge, if you aren’t efficient to start with.”
Using CMMS to tighten parts inventory also improves the bottom line, Tesdall says. With $1 million in spare parts, a common approximation of ethanol plant inventory, and the carrying cost estimated to be 15%, the potential savings are impressive. The software can help identify the critical parts that need to be on hand, and reduce inventory overhead on other parts that can be ordered as needed.
As plants become more successful in implementing the basic CMMS functions, many start looking for other ways to become more efficient, he adds. Using the human resources scheduling function to plan labor can help reduce overtime. And, the compiled data on how long tasks take and how much overtime is paid out can be used to justify hiring more people, if needed.
BOLSTERED BASICS: Upgrades to computerized maintenance management systems have included bar code scanning and mobile device pairing. Many plants might not be using their CMMS to full capacity. PHOTO: MAPCON





PLANT UPTIME IS IMPORTANT TO YOU, SO IT IS IMPORTANT TO US. Our full service team of experts have 20 years of ethanol plant maintenance reliability and uptime history. 24/7 support and ready access to a full inventory and all Fluid Quip equipment parts, ensures that you maintain your plant’s uptime status.


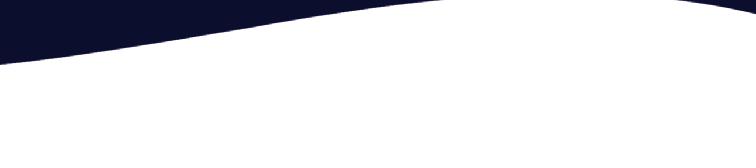

Example Report PHOTO: MAPCON


PARTS OEM Parts Warehouse $1 million+ on-hand inventory Fully stocked trucks Overnight/hot shot shipping

EQUIPMENT
SERVICE • Factory Trained & Certified • MSC™ Systems • SGT™ Grind Systems • FBP™ Fiber By-Pass Systems • MZSA™ Screens • Paddle Screens • Grind Mills • • Centrifuges Centrifuges

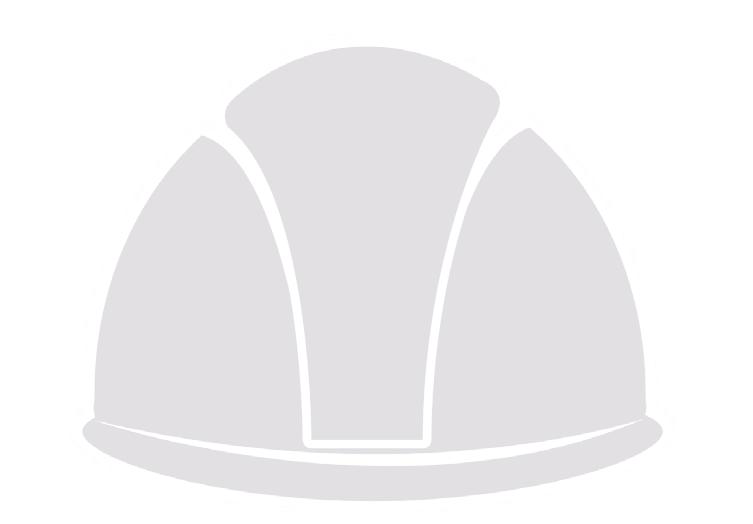
FluidQuipMechanical.com | 920-350-5823 | follow us on on Fluid Quip Mechanical is a division of Fluid Quip Technologies i . Mobile Efficiencies
Ethanol plants are now adding mobile capabilities that put work order details and reporting at the maintenance technician’s fingertips. The devices can also be used to scan bar codes on parts as they’re used, updating inventory in real time.
“Mobile access is desirable and makes [CMMS] more likely to be used, maybe not by the older generation, but the younger generation,” says Jay Beckel, senior vice president of risk and compliance services at ERI Solutions Inc./PROtect. “It makes for better data collection, too. It’s a lot easier to record that data in the field rather than come back to the maintenance shop and type it in based on memory.”
Beckel recommends plants add key performance indicators (KPIs) into their CMMS that apply to environmental health and safety requirements, following SMART ideology—making KPIs specific, measurable, achievable, relevant and time-framed. “They can be hard to follow sometimes, but when you set a new goal and determine new KPIs, following SMART will give you better results,” Beckel says.



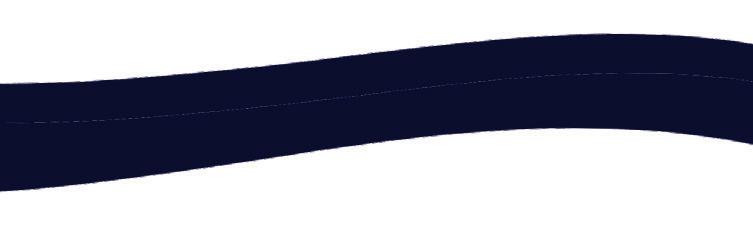
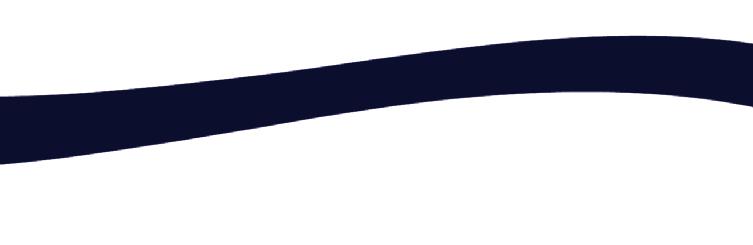
KPIs to consider adding to CMMS to track preventive maintenance
Percentage of critical equipment properly documented and justi ed. Percentage of assets with damage mechanism and expected remaining life span identi ed and justi ed. Percentage of assets with PMs. Percentage of PMs with written standard operating procedures (SOPs). Percentage of SOPs that clearly state consequences of deviation.
Percentage of technicians trained on/certi ed to perform those PMs exactly as outlined in SOPs. Percentage of PMs completed on time. Number of PMs past due.
Number of PMs more than 1 cycle past due.

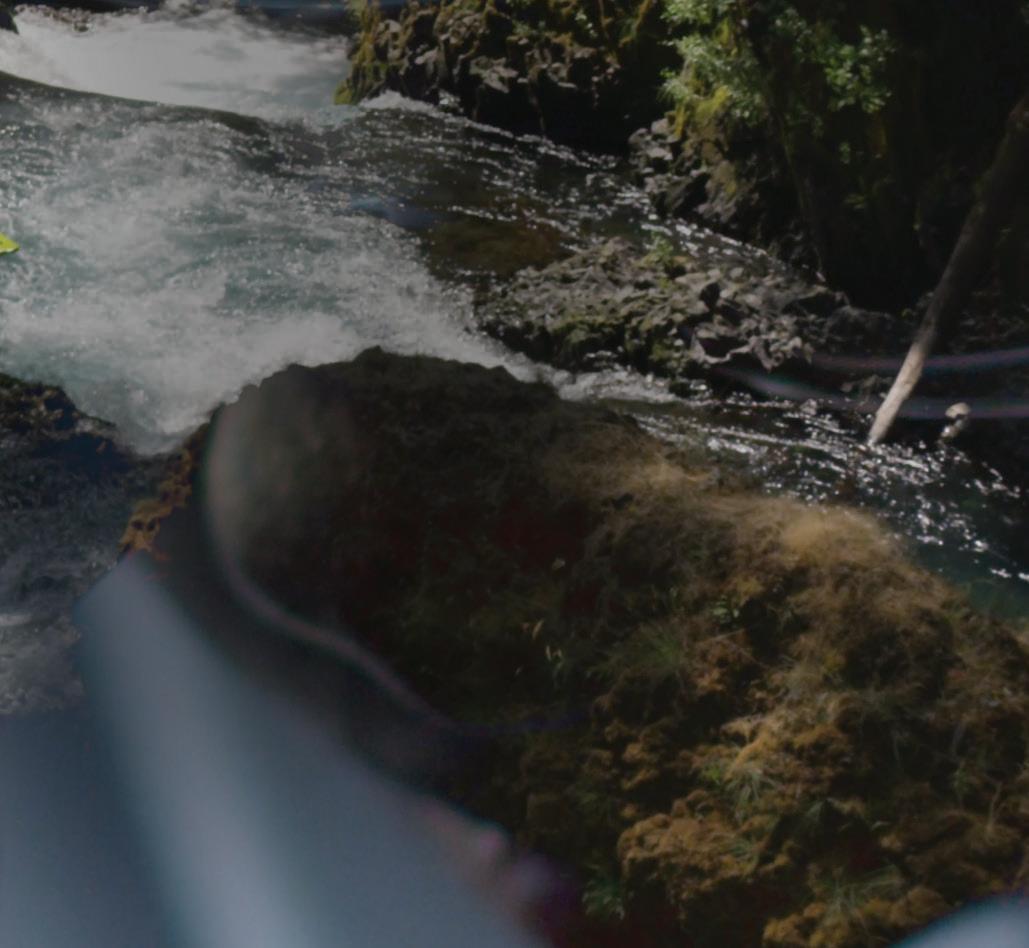


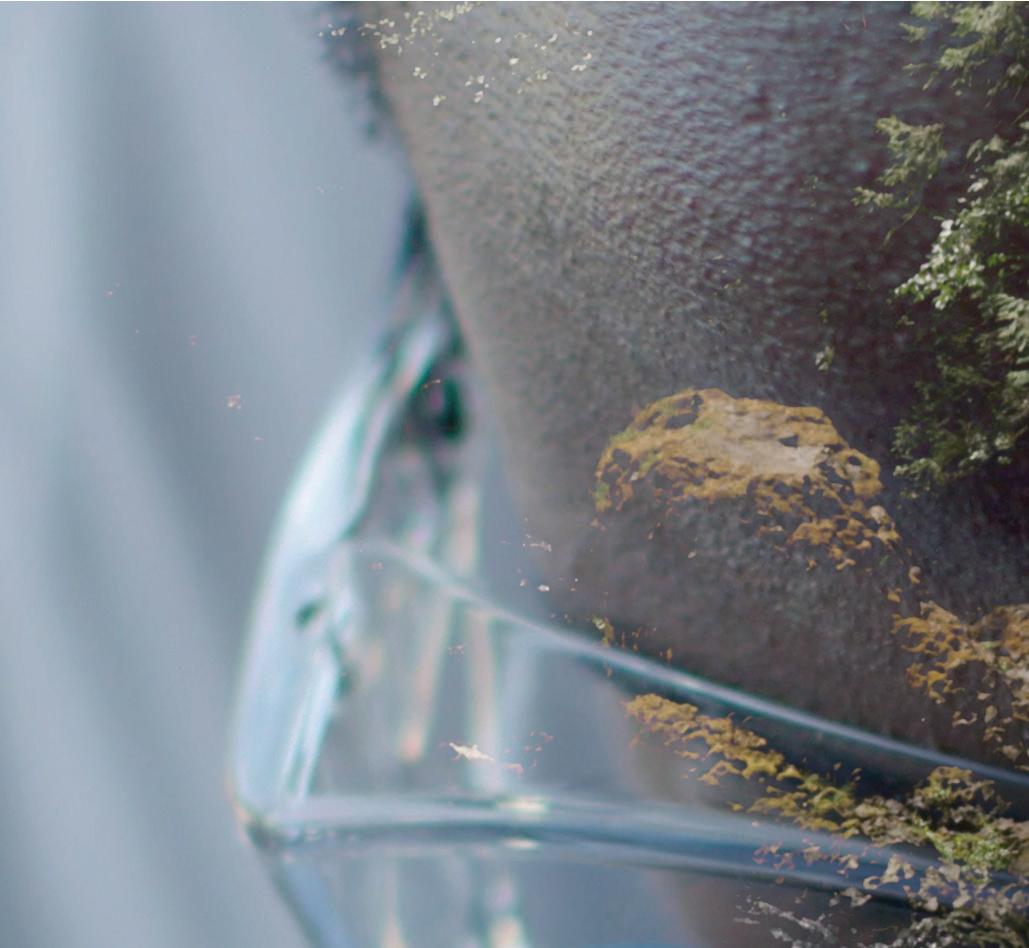

Example Report PHOTO: MAPCON
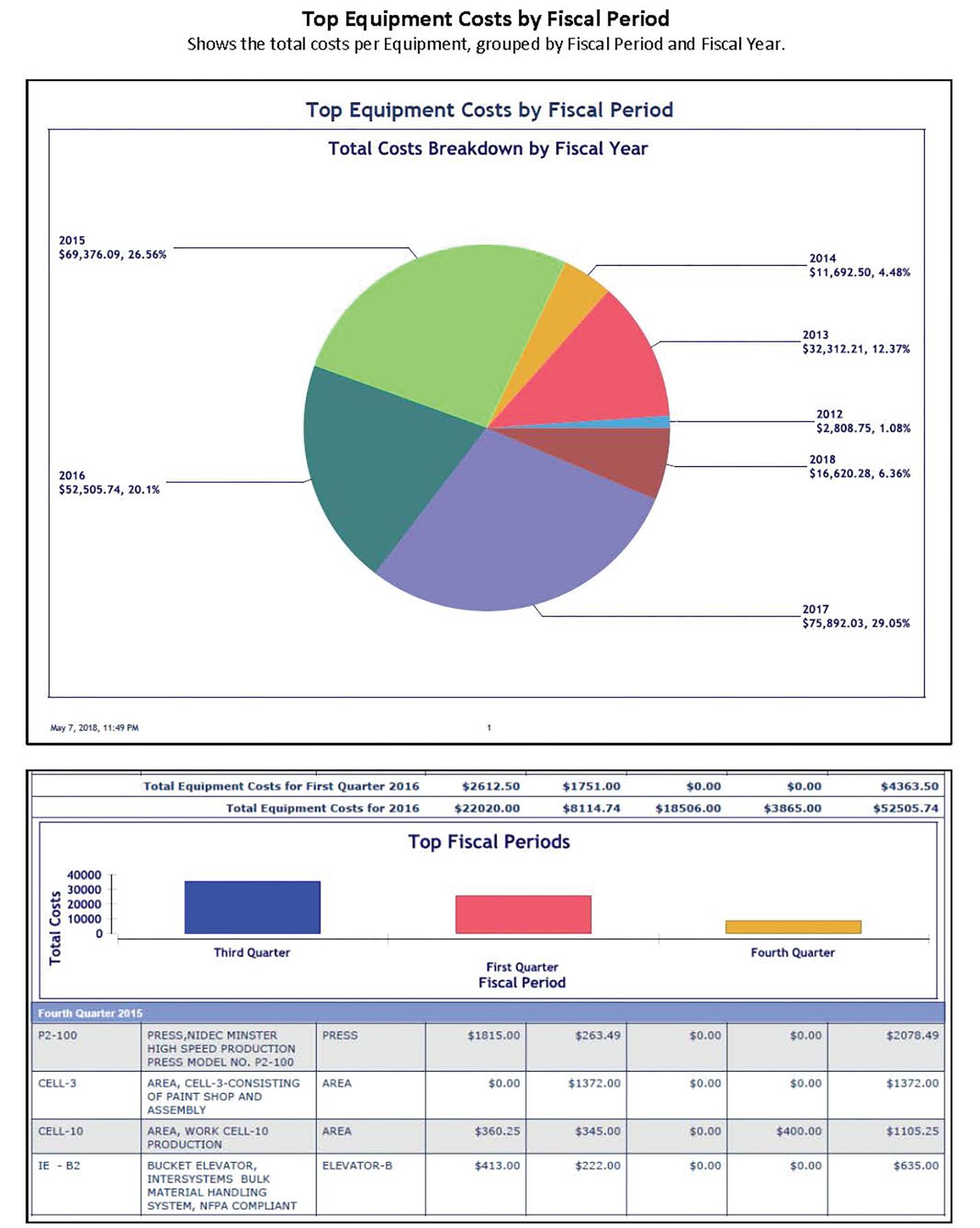
Beckel discussed the key performance indicators in CMMS at the Plant Maintenance and Safety Summit produced by Ethanol Producer Magazine and held virtually Dec. 16-17.
All equipment should be evaluated for its expected life span, Beckel recommends. “If you can, calculate remaining time left in your CMMS. Ask yourself what it’s based on, time of use or cycles, and which is best?”
The next step is to identify the damage mechanism, since each piece of equipment fails as a result of different factors. “You need to plan your analysis and preventive maintenance activities that are tracked in your CMMS accordingly,” he says. The life of a fermentation tank may be 50 years, but welds can crack and support structures for agitators can fail, he adds.
Tracking preventive maintenance on critical equipment should include documenting available spares, any specialty or custom requirements for one-of-a-kind equipment, installation needs and whether the plant’s maintenance staff can do the maintenance or a third-party vendor is needed. The software can also note required lead time and cost.
Other items to consider tracking in CMMS is whether the PM for every single piece of equipment in the plant is complete with work orders and written standard operating procedures (SOPs) specifying the main-

NEW INDUSTRY TOOL NOW AVAILABLE

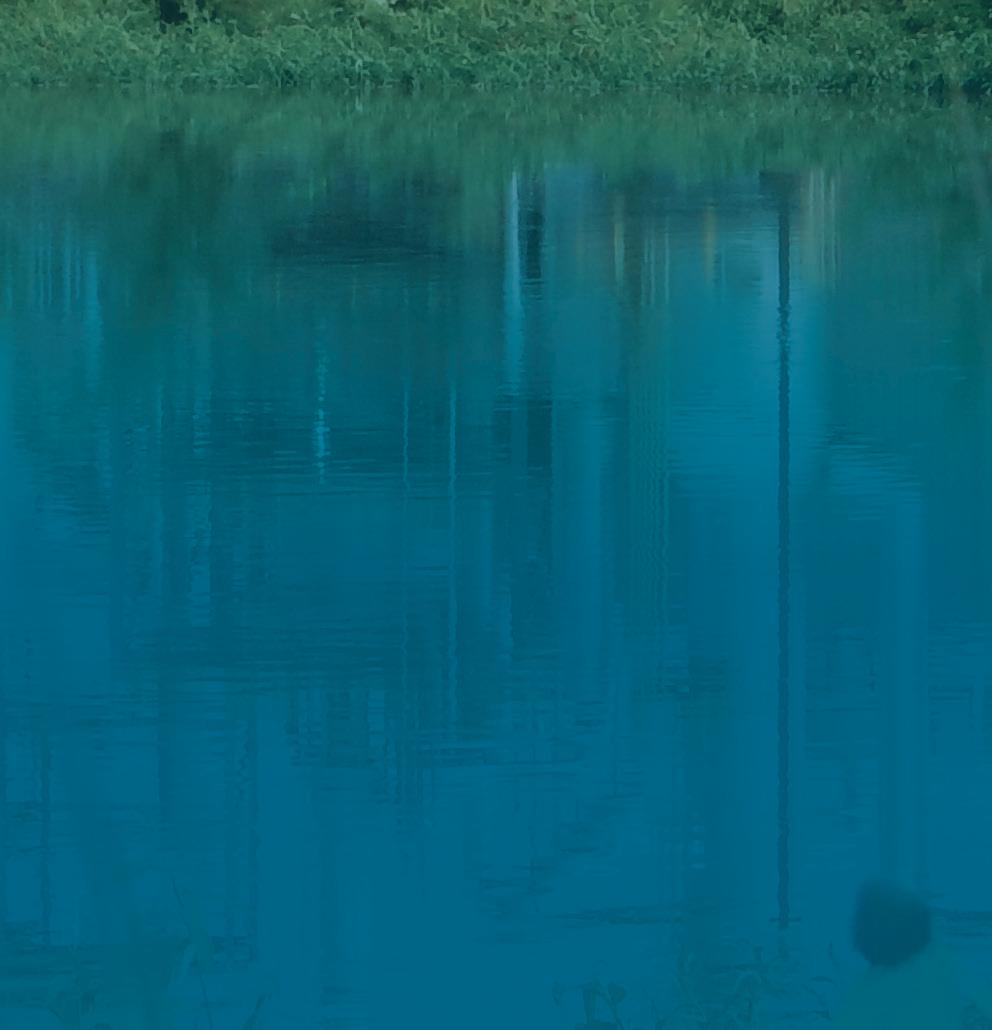
‘State of the Industry’ Ethanol Data Hub
Explore Growth Energy’s new data hub presenting the latest information on America’s biofuel industry, with user-friendly tools to track and visualize important trends — from ethanol production and exports to U.S. blending.
Learn more at
GrowthEnergy.org/datahub

Example Report PHOTO: MAPCON
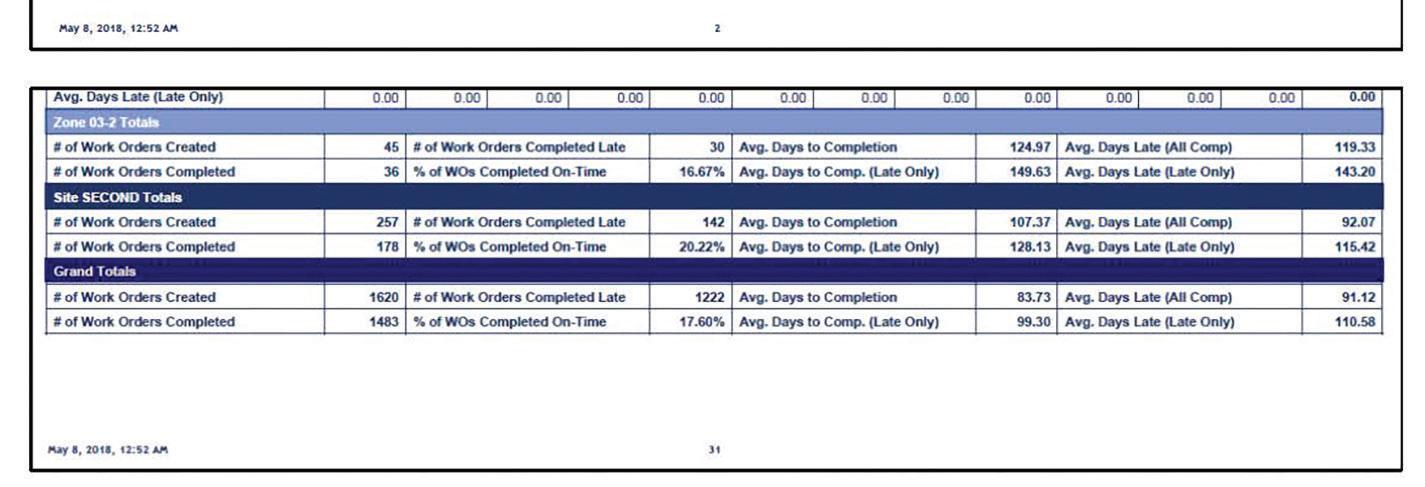
tenance procedure. “Consistency can add life,” Beckel says, adding that including the consequences of failure is helpful. “This can greatly increase technician buy-in if they understand what could happen if they don’t do their job properly or consistently.”
Tesdall recommends maintenance managers utilize checklists for procedures with specific orders, or if a maintenance record is required on certain pieces of equipment for compliance requirements. The technician can check off the steps on the checklist on a smart phone or tablet, which also keeps track of the time. Issues can be noted and red flagged.
Now, Software as a Service (SaaS) is becoming more popular, Tesdall says. Software is bought on a monthly basis and hosted on the internet, with access via a browser. For ethanol plants, switching to SaaS will depend upon their security model, Tesdall says. “In the ethanol industry, almost all our customers are self hosted, on their servers in their building. But, we have quite a few that have decided to host with us because there are cost savings. They don’t have to maintain the servers, the hardware, the network and it reduces the demand on their IT staff.”
A virus—and not the corona variety— prompted a couple of plants to move to SaaS, Tesdall adds. A virus got into the network and took down the CMMS. “For an ethanol plant not to have CMMS is a huge deal,” he says. The ability to connect to the internet keeps the CMMS and financial software running during a network crash. “We have a professional data center where that’s all they do,” Tesdall says. “They maintain the servers. They spend all day looking for threats.”
Using all these available methods and technologies to implement CMMS to the fullest improves maintenance efficiency and overall plant operations, Tesdall and Beckel agree.
Author: Susanne Retka Schill Freelance writer/editor retkaschill@yahoo.com
" ...Making time for the NEC proves to be a must year after year."
" ...The conference provides a platform for education and promotes growth and continued forward momentum of ethanol production, policy and the overall marketplace.”
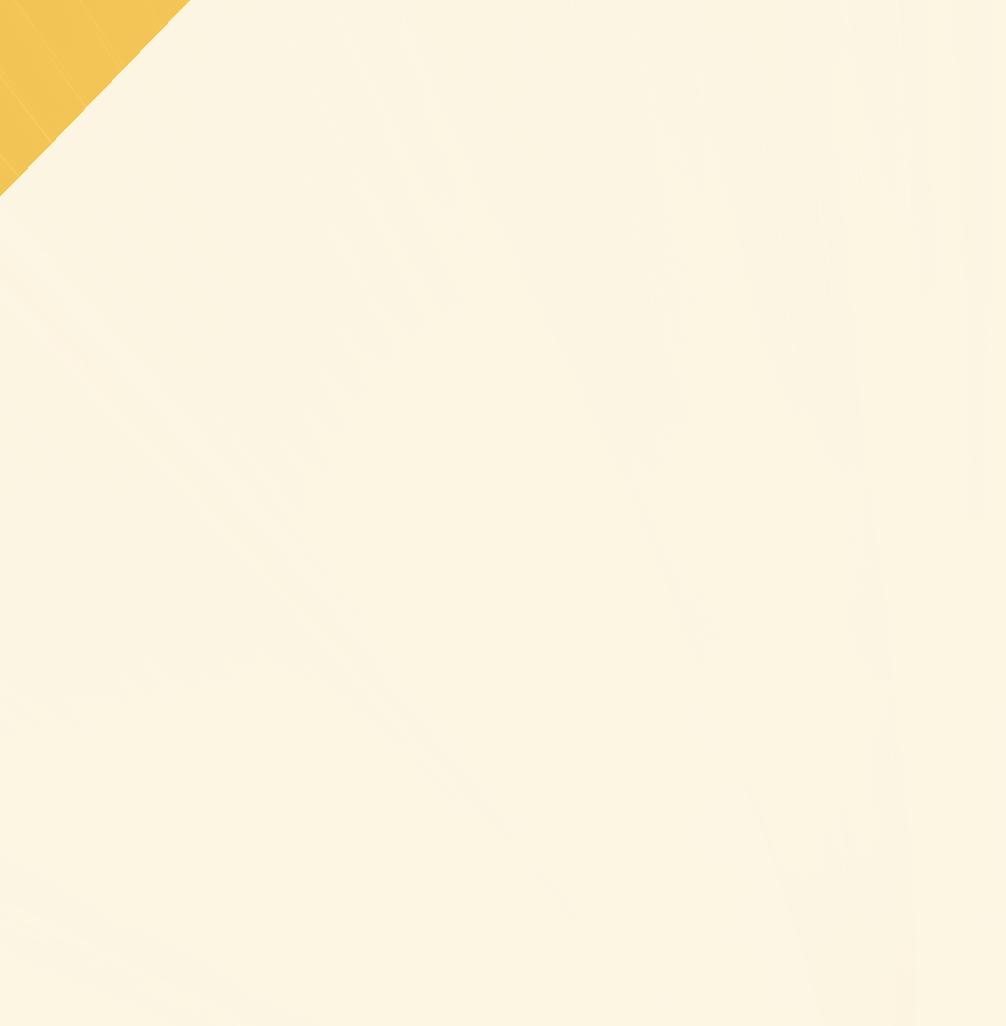
PRESENTS
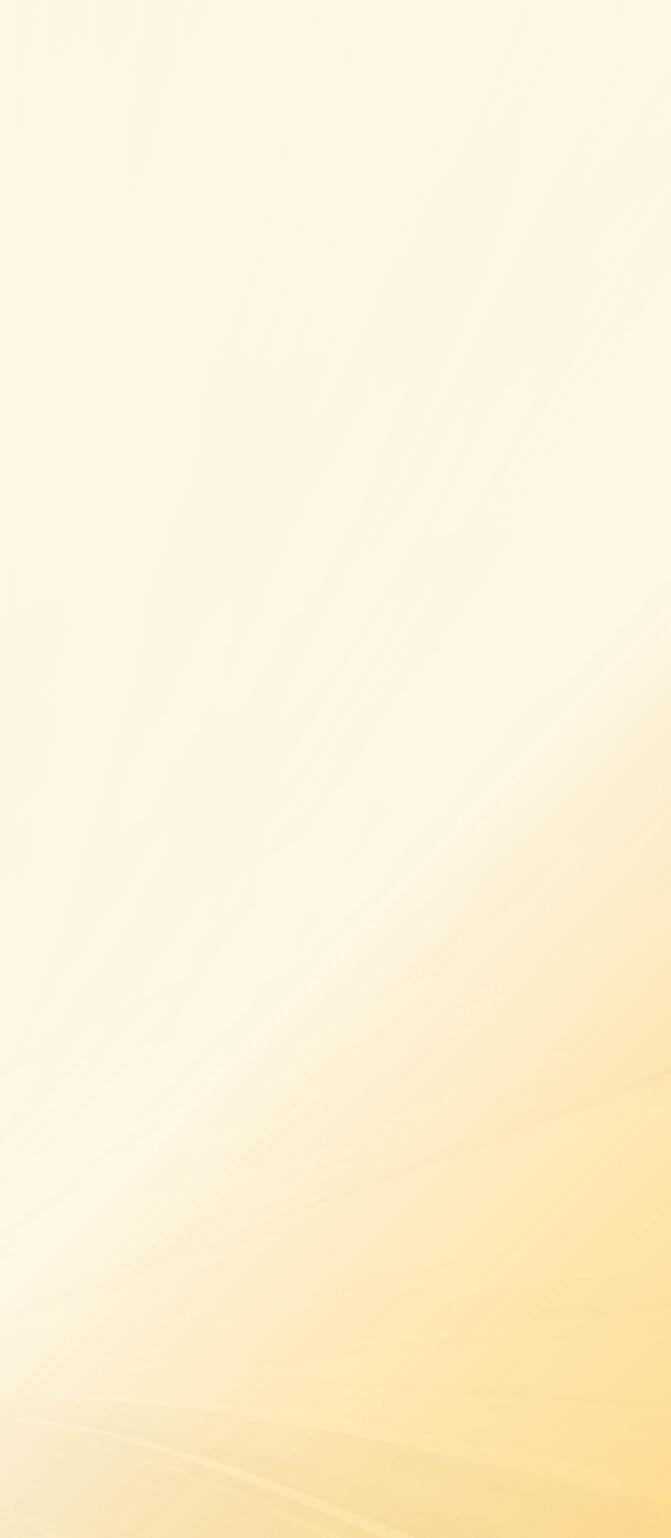

— REGISTRATION IS OPEN — for the all-digital 26th Annual National Ethanol Conference
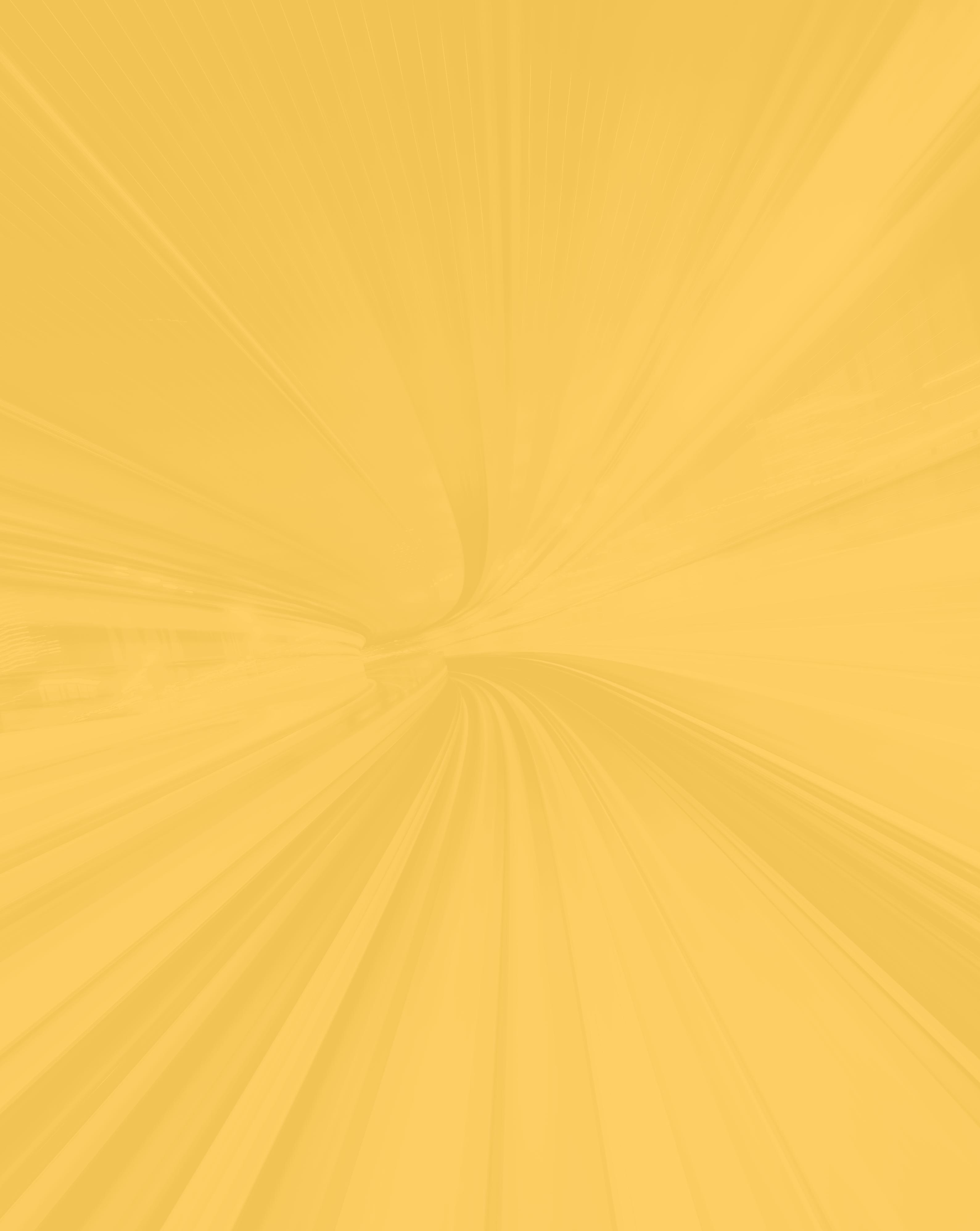
Don’t miss out on all the valuable intel, incomparable content and high-level networking. Grab your pass today for the leading global ethanol conference of the year.
