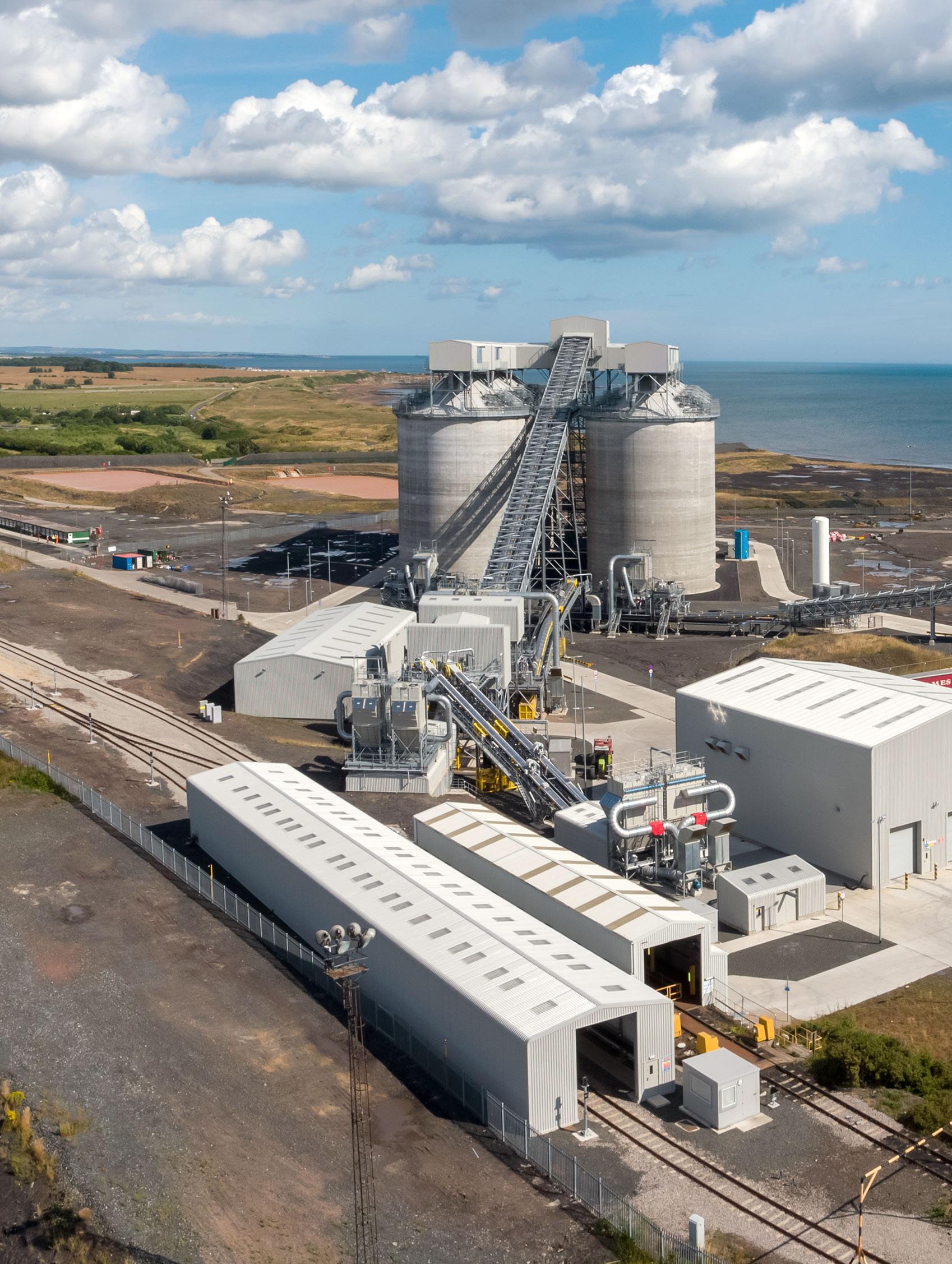
7 minute read
OPERATIONS
Now and Beyond 2027
Four years after its conversion from coal to wood pellets, Lynemouth Power Station is evaluating opportunities to extend operations long into the future. BY ANNA SIMET
The Lynemouth Power Station consumes roughly 1.5 million tons of wood pellets annually, which are primarily sourced from Canada and the U.S.
PHOTO: LYNEMOUTH POWER STATION
When it was first fired up in 1972, northeast England’s Lynemouth Power Station was designed to combust Northumberland coal—and it did, for its first 40 years of operation. During that time, most of the power generated at the 420-MW station was sent to a nearby aluminum factory, Lynemouth Smelter, which closed its doors in 2012. With the possibility of being converted to biomass already in the works, the plant changed hands a few times from then until now, with RWE npower taking over in 2013, and EPH acquiring the facility in 2016, a year after the plant ceased burning coal. When that happened, the biomass project began to gain momentum, says Jonathan Scott, commercial and fuel director at Lynemouth Power Station. “The government was looking at the asset base in the U.K. energy sector and opportunities to reduce emissions—Drax was another candidate— and at Lynemouth, this was done by modifying and replacing parts of the plant, from the coal handling system to the combustion process, with some substantial investments.”
The project aligned with the country’s ambitious CO2 reductions, and to aid in financials, the U.K. government granted Lynemouth a contract for difference (CfD), a mechanism designed to support low-carbon electricity generation by subsidizing the market price of power generated at the plant. As of now, the CfD extends to 2027. “It has been quite a successful project,” Scott says. “We’ve managed to reduce CO2 emissions substantially while maintaining output and efficiency levels similar to what we had with coal.”
Just a few years after reaching full operations on wood pellets, attention is on potential strategies to keep the plant operating long after the CfD ends, according to Scott. He says most recently, much of the focus has been on fuel and potential alternatives to wood pellets—alternatives that are compatible with the converted plant and will allow for maximization of conversion investments, which totaled about $400 million.
As for what those investments entailed, Scott begins with one of the major components of the project: its fuel receiving, handling and storage operation at the Port of Tyne.
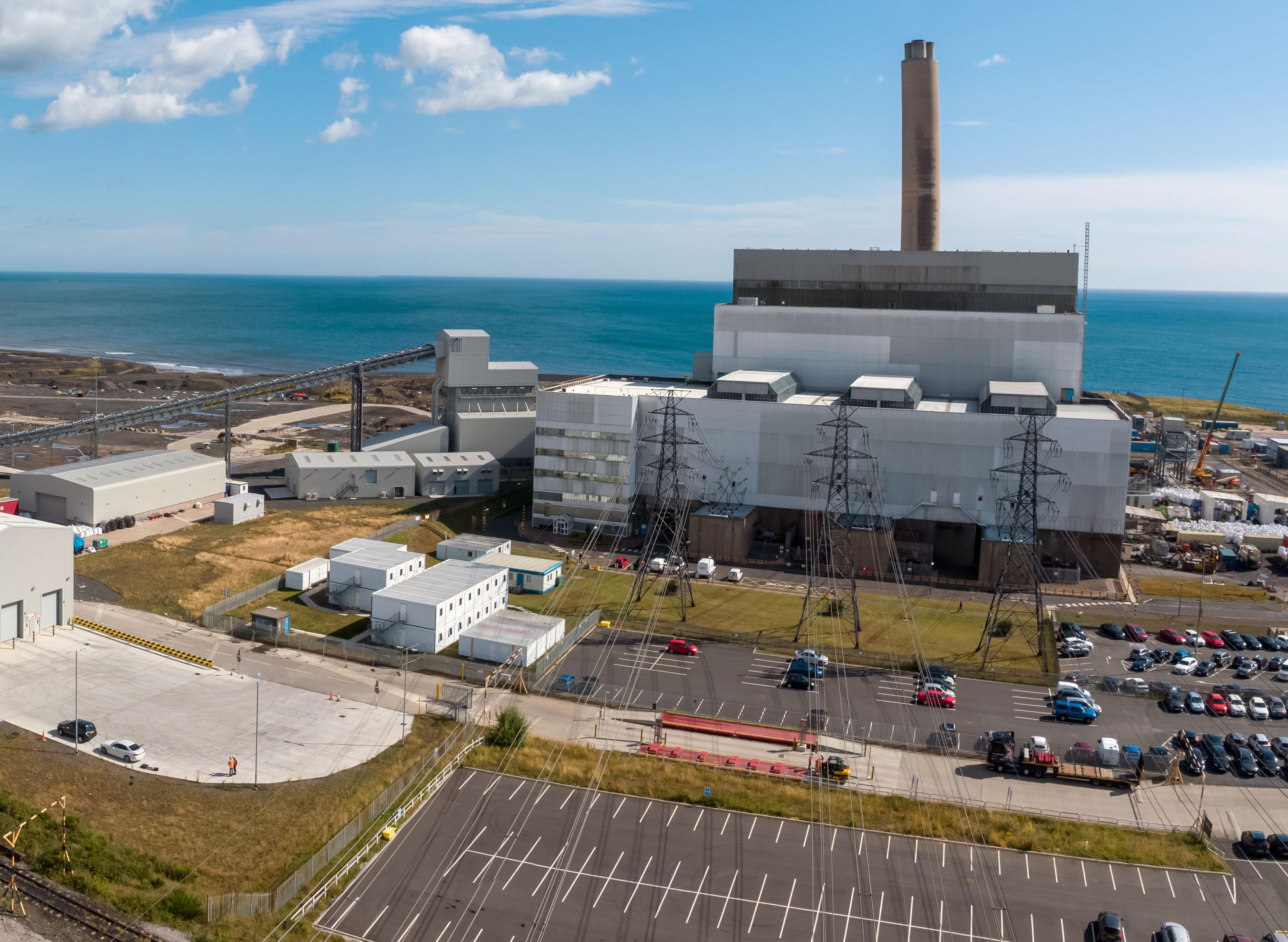
The Project
“Because of the type of storage and handling system needed, it required a substantial investment,” Scott says. “We identified some local ports that could meet the requirements, but because of the size of the investment required and the risks involved, it meant that we needed to go with just one port and directly invest in the material handling system on their land. So, we own and operate the facility.”
As part of the project, the port financed a 125-metre quay extension, rail infrastructure and two new ecohoppers, and it provides all marine services and equipment related to unloading vessels, Scott says. “There are conveyors, transfer towers, safety systems, screening for ferrous and nonferrous contaminants, and additional conveyor systems for three storage silos, each of which has a capacity of 25,000 tons of wood pellets.” The 45-meter diameter, 194-foot-high concrete slip-formed silos can discharge pellets at a rate of up to 1,700 metric tons per hour, according to Spencer Group, the principal contractor, via dual closed conveying systems running 1,364 meters (4,475 feet). From there, Scott says, the wood pellets are reclaimed to a rail-loading silo, which may dispatch from four to six 25-wagon trains to Lynemouth each day. “The rail wagons have been specifically designed for wood pellets,” Scott says. “It’s a nice system. The trains feed into our storage at Lynemouth, which is about 50,000 tons.”
While material handling was a significant part of the conversion, there was also significant work to prepare, replace and refurbish the combustion and emission control systems, which required major outages of all three 140-MW units. “There were four main packages with different EPC contractors for each—material handling onsite, material handling offsite, the combustion and emission modification, and the control system,” Scott says. “Tying the whole thing together was quite an investment. This meant going from operating with a full analog control system to a more modern, digital control system— imagine a coal power station that is 1970s vintage. The control system had to be modified quite substantially.”
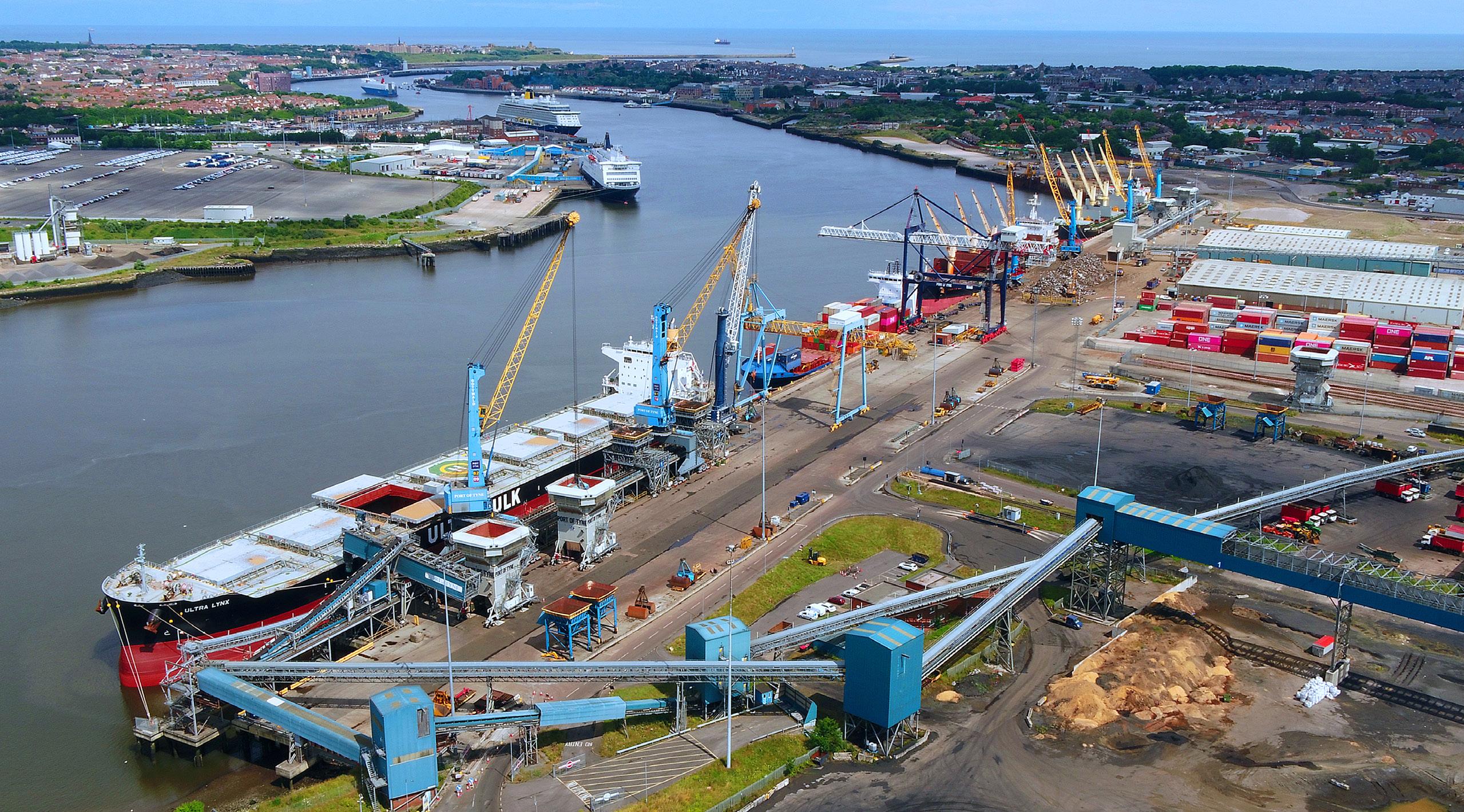
The Port of Tyne is the largest wood pellet handler in Europe and receives 100% of Lynemouth Power Station's fuel.
PHOTO: PORT OF TYNE
Also onsite at the power station is a warehouse facility that holds approximately 2,300 lines of specialized maintenance equipment, to avoid any downtime or issues related to sourcing spare parts. “With biomass, there are some specific dynamics behind this,” Scott says. “Much is to do with safety reasons, the material handling infrastructure and the various systems on the plant for handling wood pellets. There are many small, safety-critical systems in place after the biomass conversion, and if a system goes down, there is a safety risk and liability, so we need to carry more critical spares. Some are relatively unique and not available in manufactures’ warehouses, so we hold many spares. If we do lose any production time, it’s minimized.”
As for what aspects of the conversion were the most challenging, Scott says there were many, considering the project's massive caliber. “The timeframe was one—we were to complete the project quickly to get online—the expectation of the time scale was a challenge. It took a lot of effort from the EPC contractors and the experience of the Lynemouth team. Another [challenge] was getting to efficiency targets aligning with the plant’s safety and reliability plan.”
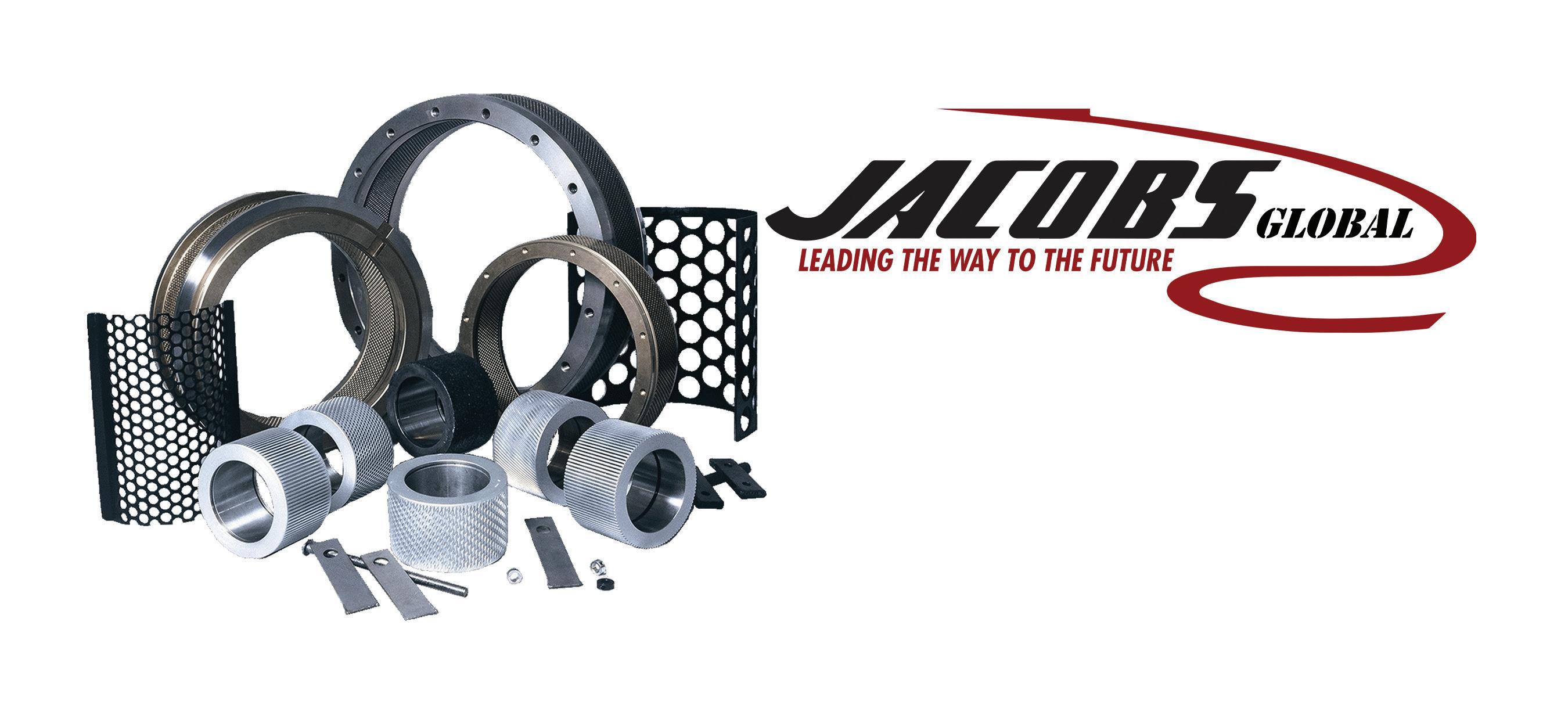
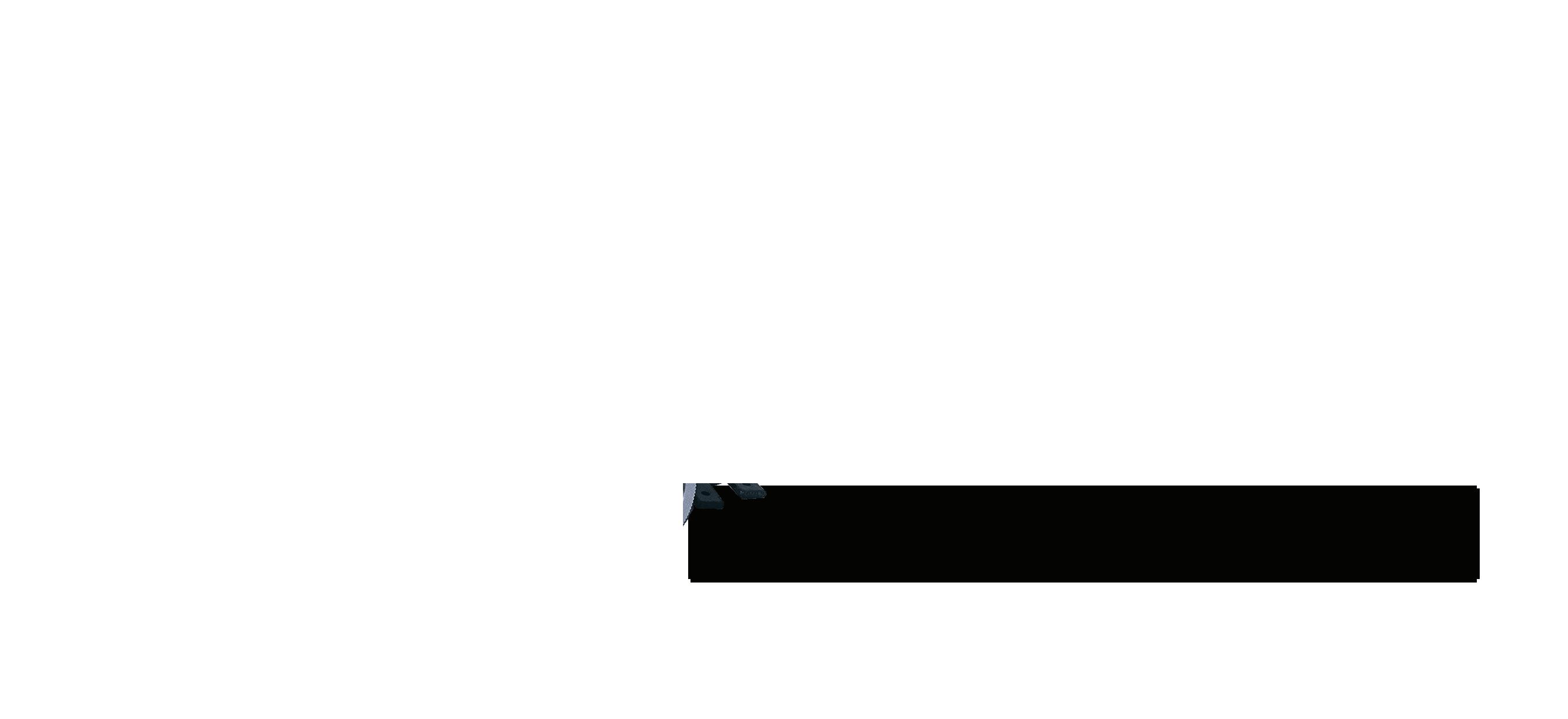
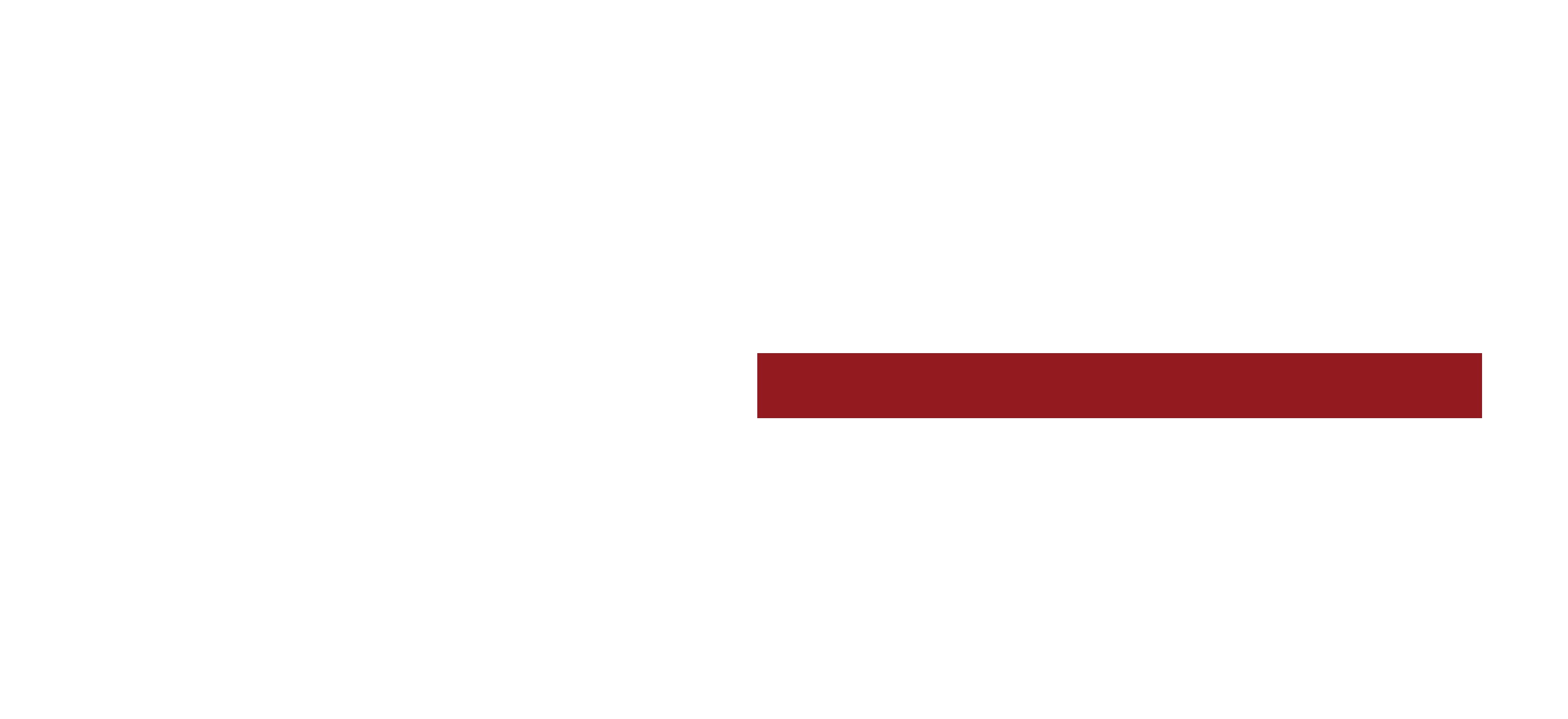


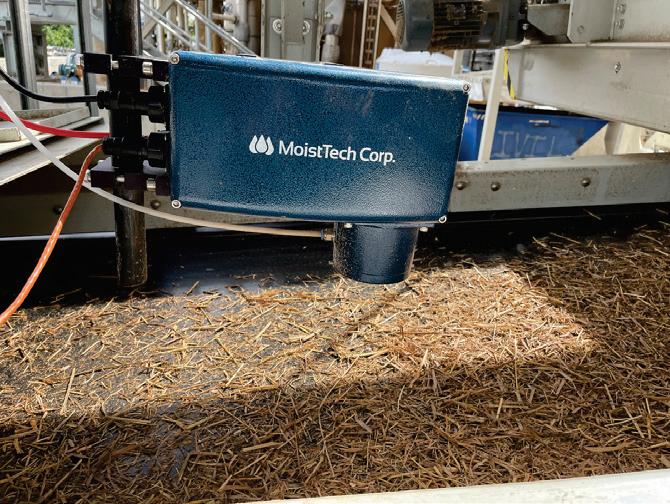
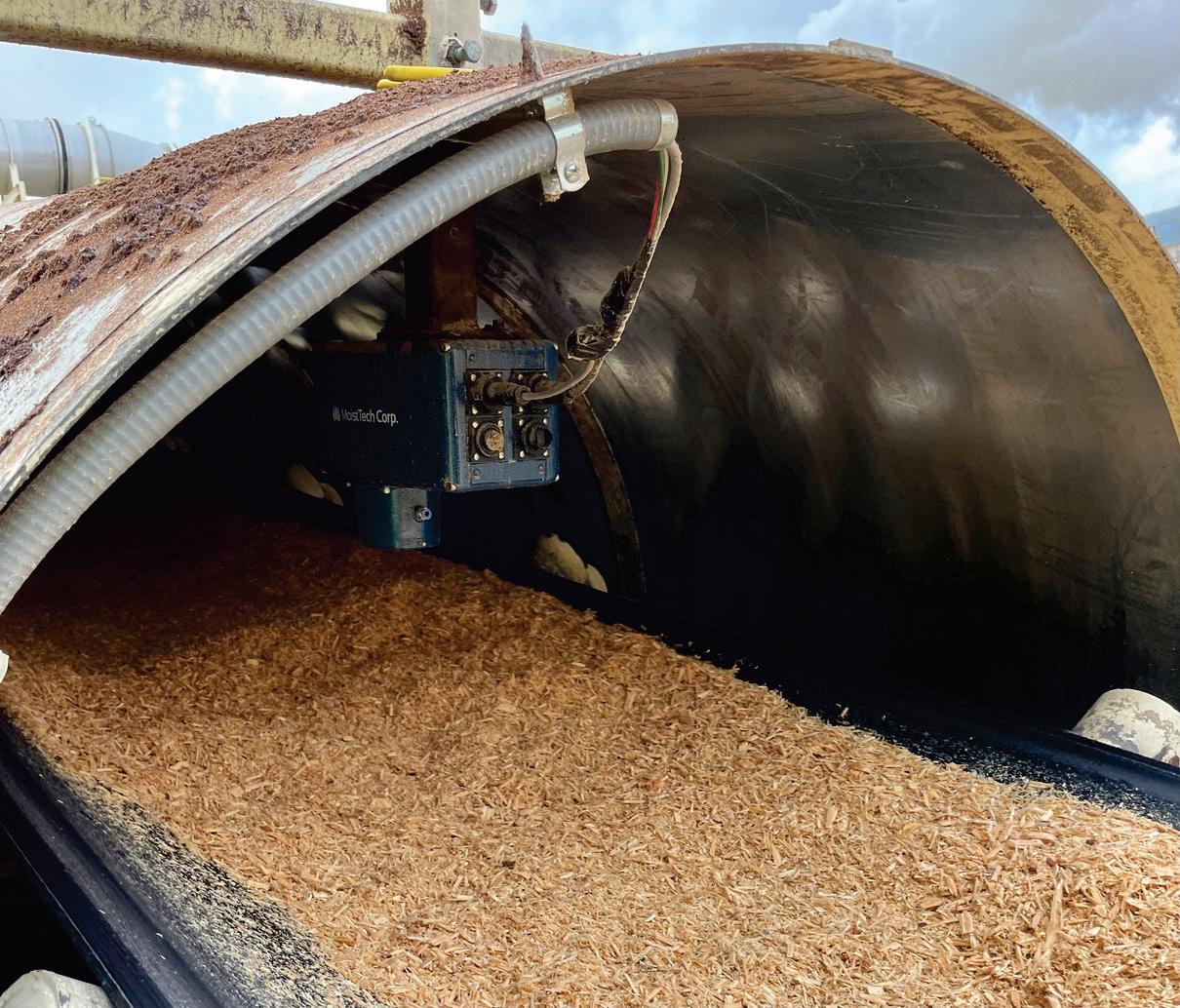
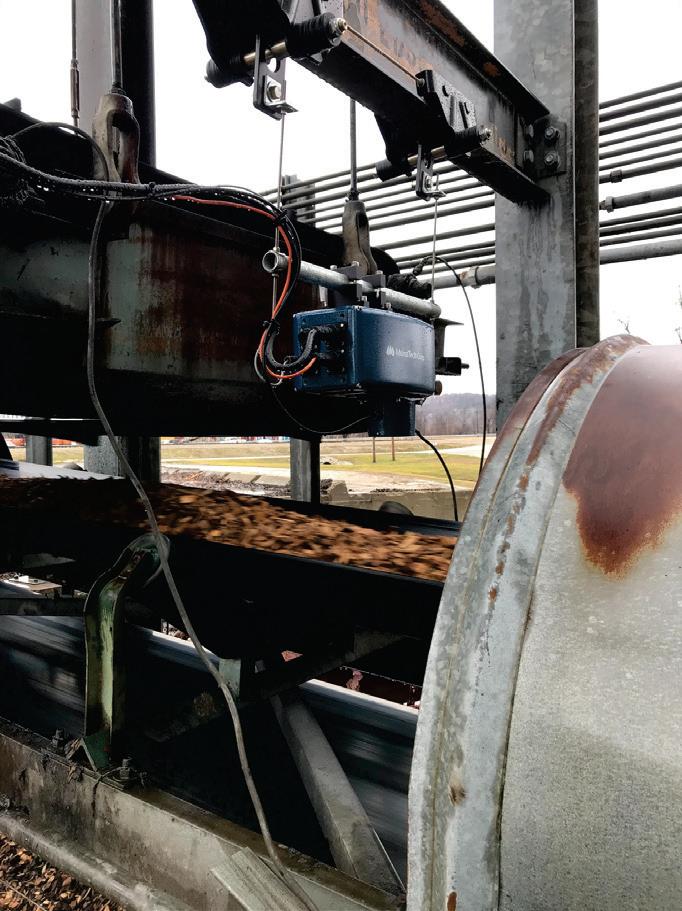
The Glasgow Declaration on Sustainable Bioenergy
Lynemouth Power Station has joined many other organizations from the global bioenergy industry in launching the Glasgow Declaration on Sustainable Bioenergy, a signed declaration that outlines the indispensable role that bioenergy will play in net zero ambitions agreed by the international community. It sets out a vision for the sustainable growth of the bioenergy sector to 2050. For Lynemouth, the goal is to complete a comprehensive review of options for the plant from 2027 onward when the current CfD ends. This includes potential for BECCS, how it could be applied to the site, how it would interface with existing operations, and the work required to extend the operating period of the existing plant.
While the innovation and emissions reductions achieved by converting from coal to wood pellets speaks for itself, the plant isn’t stopping there.
Innovation & Looking Ahead
In a bid to even further reduce its environmental footprint, Lynemouth is on the hunt to find an economical, beneficial use for combustion ash. “At the moment, it’s conditioned and sent into our ash bins onsite, but it could be used for various other beneficial purposes,” Scott says. “We have a couple of development trials taking place, centered around land remediation and whether the chemical composition of the ash can be helpful in remediating otherwise barren land. We are also having discussions with third parties in relation to its potential beneficial use in agriculture.”
These efforts considered, Scott points out that compared to coal, the ash content of wood pellets is significantly lower, so the amount being landfilled since the conversion has been substantially reduced.
And, as aforementioned, Lynemouth is in discussions with various U.K. government departments regarding different concepts for running the plant from 2027 and beyond. BECCS is at the forefront of options. “We’re looking at business models for continuing to operate this as a biomass station,” Scott says. “The basis for the conversation investment was having the CfD until 2027, but the plant has a much longer expected life cycle. We’re starting to determine what the potential costs would be to extend its operating life—we believe a lot of the existing infrastructure could be replaced or repaired, and some improvements made. We have looked at alternatives to wood pellets, how to improve our efficiency and to reduce our auxiliary power. We don’t see any major barriers so far, with the investment signals from the government. A BECCS project would support the U.K.’s Net Zero Strategy, and we could be operating well into the 2030s and ’40s, supporting those targets.”
In conclusion, Scott says, with plenty of steps yet to go, the work at Lynemouth Power Station isn’t yet done. He adds, “It’s never done.”
Author: Anna Simet Editor, Pellet Mill Magazine asimet@bbiinternational.com 701-738-4961
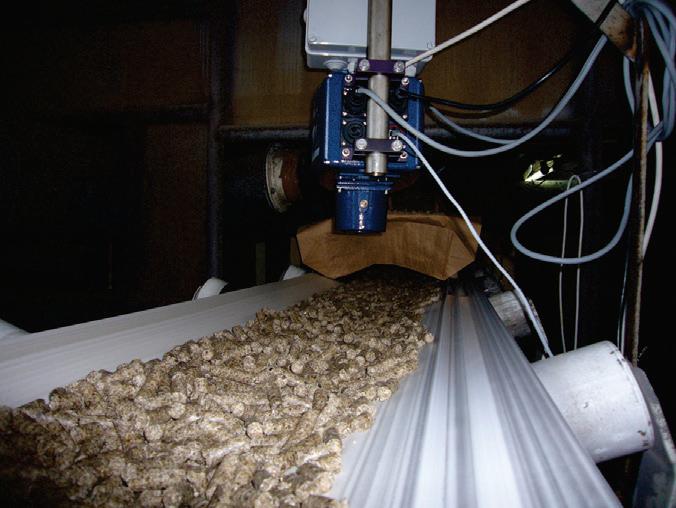
