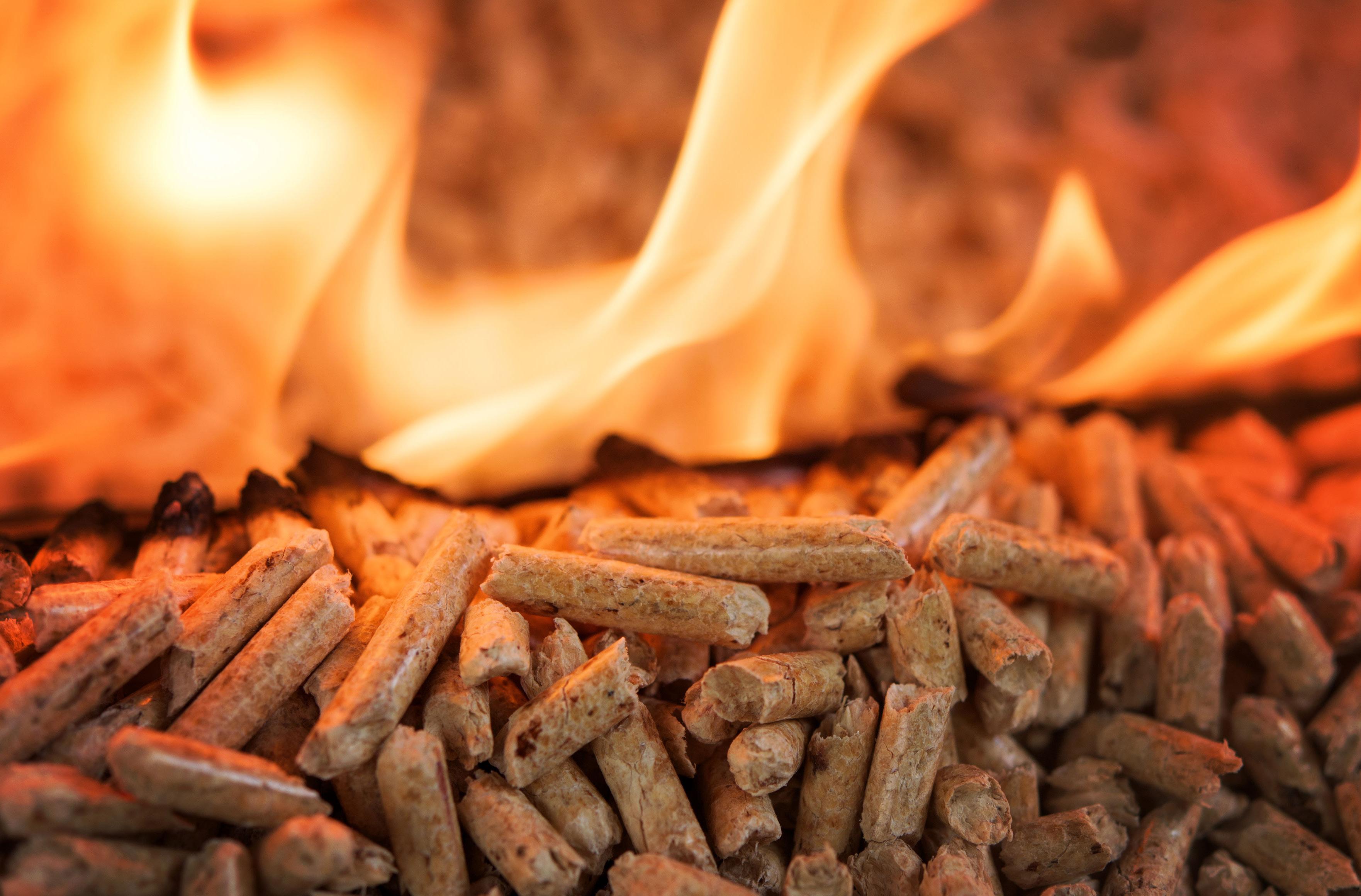
5 minute read
PRODUCT
Understanding Ash Fusibility (Clinkers)
BY CHRIS WIBERG
When it comes to the science of biomass combustion, no parameter is more complicated than ash fusion. When ash fusion characteristics are favorable, ash remains ash, and the only challenge is to remove it from the combustion system in such a way that it does not build up excessively. Conversely, when ash fusion characteristics are not favorable, strange things happen—ash can clump together and may need to be broken up, or even chiseled out of an ash pan. It can form a brick, look like a fused piece of glass, or even resemble a honeycomb. This unwanted ash behavior is referred to as fouling or slagging when it builds up in industrial burners, and is referred to as clinkers in smaller scale combustion appliances. No matter what you call it or how it looks, the process by which it forms is relatively simple, as it is just a function of melting point. However, troubleshooting it can be complex because there are many factors involved.
First, let’s start by qualifying that “clean” ash (free of dirt, rocks, unburned carbon, etc.) is primarily a combination of inorganic oxides. When biomass is burned, the organic material (essentially all the carbon, hydrogen, nitrogen and oxygen) is released, and inorganic minerals remain in the oxidized form that we see as ash. Through testing, we know that biomass ash is primarily composed of oxides of calcium, silica, aluminum, magnesium, potassium, manganese, sodium, iron, phosphorus and other minerals. Each of these oxidized minerals is present as a solid, and like any other solid, they have a melting point. The range of melting points for the various mineral oxides present can vary greatly, and the overall melting point of the collective ash is a function of all the mineral fractions and chemical interactions that occur at the elevated temperatures of the combustion system. As a result, ash generally melts over a range of temperatures, rather than a specific temperature. The range can be anywhere from a few degrees to 50 or even 100 degrees Celsius. That’s why when you see ash fusion test results, it is reported as
a range of temperatures (e.g., deformation temperature=1,310 C, hemispherical temperature=1,330 C, flow temperature= 1,350 C). In this example, the ash melted over a range of 40 degrees C.
Deformation temperature (DT) is considered the critical parameter in the ash fusion test because this is the temperature at which the ash first begins to melt and becomes “sticky.” Sticky ash will collect on essentially all surfaces within a combustion system, creating an insulating effect, which causes the temperature of the overall combustion system to increase. The increased temperature drives more melting. This process continues until the ash becomes fluid and essentially slags/fouls the system (shutdown time). Interestingly, the nature of the slag/clinker can tell you a few things. If the ash is clumpy but can still be broken by hand, then you know you were just above the DT. If you find actual glass, then the ash has fully melted. A brick is generally somewhere in between. The honeycomb effect occurs when settled ash (such as in an ash pan) melts on the top, and the melted droplets run down into the colder ash below.
The key to preventing ash fusion problems is to keep the temperature of the combustion system below the DT of the ash. Since most biomass combustion systems operate at or below 1,200 C, it is common practice to assess fuels by verifying DT is somewhere above this temperature. Fortunately, slagging/clinkering is generally not an issue with “clean” wood (no bark, sand, dirt or other debris). I am currently unaware of any species of North American tree that, by nature of its mineral uptake, has a DT below 1,200 C. Ash fusion with woody biomass is almost always related to some form of contamination getting into the feedstock material. The same can’t be said for other forms of biomass (nut shells, agricultural grasses, energy crops, etc.). These materials regularly have high ash content, driving up the chance for a low DT.
That said, higher ash alone is not a good predictor of whether a particular form of biomass will have problems with ash fusion. The nature of the mineral composition of the ash is the driving factor. If, for example, the ash is high in calcium, then ash fusion temperatures are generally high. If silica is high, then there is a much greater chance that there will be ash fusion problems, but not always. Silica is interesting in that if it is present as silicon dioxide, then the actual melting temperature is very high (1,710 C). However, like carbon, silica has four active electrons that can bond with other minerals, often resulting in complex silicates that have lower melting points. For this reason, nine times out of 10 when we see ash fusion problems, it is related to silica. There are other minerals can be problematic when elevated, so when struggling with ash fusion issues, a mineral breakdown of the ash is often helpful in finding the source.
There are many other factors that can complicate an ash fusion investigation. The combustion system can be oxygen-rich or oxygen-poor, changing melting point conditions. Biomass can be contaminated with obscure materials (e.g., fertilizer and salts), commonly through the use of unclean transport systems. Contaminants are often intermittent, so testing the next batch of fuel will not necessarily help you figure out what caused the ash fusion problem associated with the prior batch of fuel. All said, if you understand the principles above, you should have a better chance of determining what is causing the ash fusion problem you are dealing with.

Author: Chris Wiberg VP of Laboratories, Timber Products Inspection/Biomass Energy Lab cwiberg@tpinspection.com www.tpinspection.com
Feeding, Conveying and Elevating Solutions
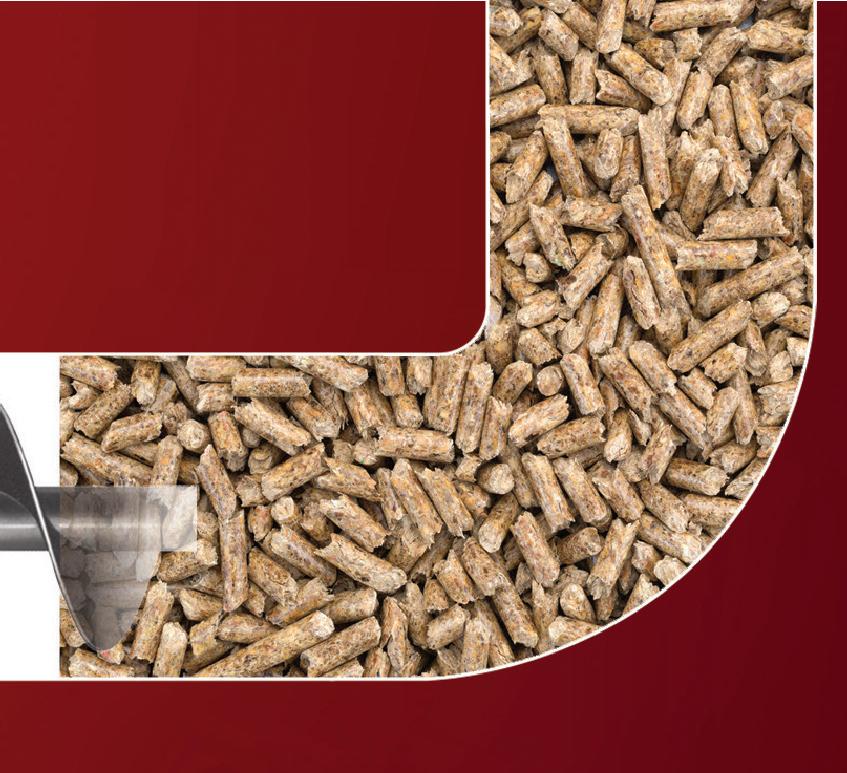
For the Wood Pellet Industry
Screw Conveyor Corporation has provided engineered material handling solutions since 1932. We focus on Screw Conveyors, Screw Feeders, Round and Flat Bottom Drag Conveyors, as well as Centrifugal and Continuous Bucket Elevators (both belt and chain). Visit screwconveyor.com to learn more about our capabilities. We look forward to working with you on your next engineered material handling solution!
700 Ho man St., Hammond, IN 46327-1894 Phone 219-931-1450
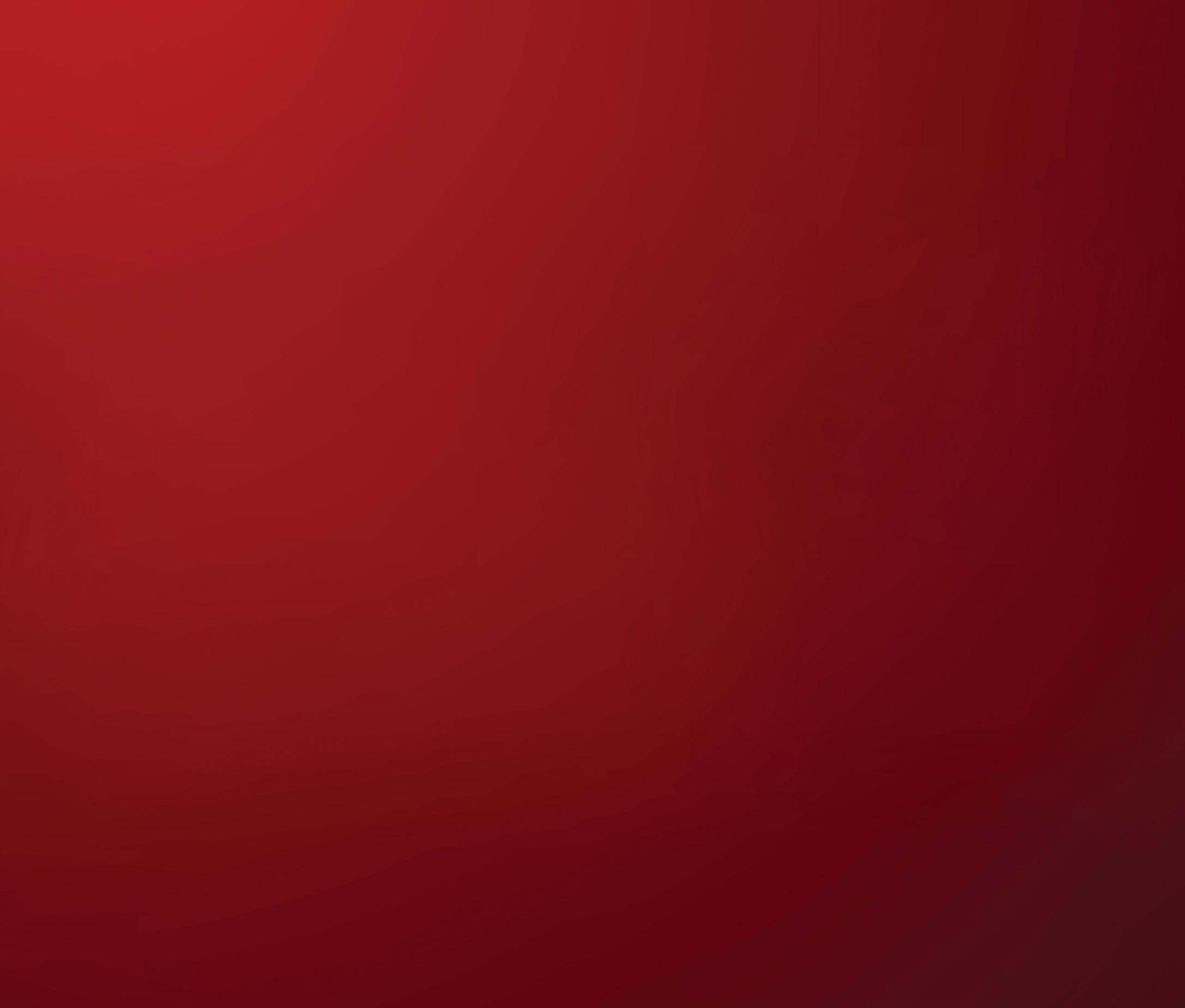