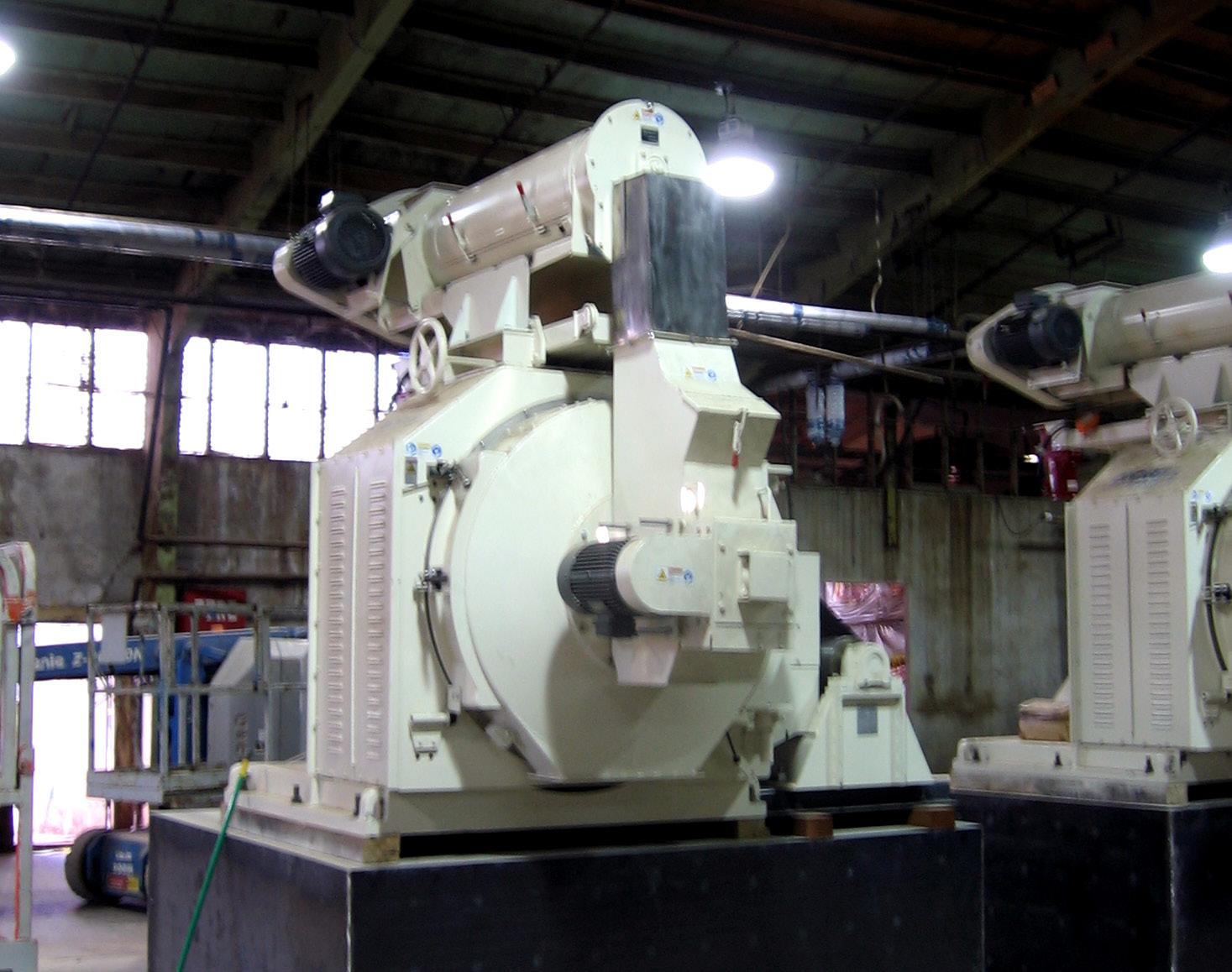
5 minute read
PROJECT DEVELOPMENT
PHOTO: EVERGREEN ENGINEERING
Project Management: Development, Execution and Critical Communication
In a recent pellet mill upgrade project, several challenges led the project to come in late and over budget.
BY JEFFREY TUMA
“The root of most problems is the solution of most problems: communication.”
The foundation for success of a large project is communication. Whether verbal or written conveyance of peoples’ roles and responsibilities, when and where things are happening, or the specific metrics for success, a shared understanding by stakeholders is key. Another component of this is the value of visual communication. In engineering projects, visual communication might include organizational charts, project schedules, budget tracking and drawings, all of which are instrumental in project execution. In the absence of these items, misunderstandings, costly overruns, frustrations between project members, project scope deviations and Tuma utter chaos can occur.
In the example of a recent pellet mill upgrade project, it initially had a clearly defined project scope and budget, which led to the belief that it would be a very manageable project, not requiring the rigor and project controls that one might typically see. The timeline was based merely on promised equipment deliveries, and installation would commence accordingly. Pretty straightforward, no schedule needed—so some believed. The project budget incorporated a solid contingency for the scope as planned, reserved for those items or circumstances that are generally described as “What we don’t know that we don’t know.” Thus, budgetary spending controls were not fully in place, nor expected to be utilized.
In some cases, when subject matter experts feel that a project is easy or a no-brainer, the tendency can be to “not sweat the details,” and to skimp on things like engineering drawings. With this project being a retrofit of a narrow scope, end points and connection points (where the old process meets the new process) were deemed simple and not needing the additional project diligence coming from the proper engineering cycle. Projects of a certain size and scope can be led and managed by a single person. But when projects are large, or small ones grow, it is usually best for a project team to work together toward success. With this project appearing to be straightforward, one person was expecting to manage the budget, scope and schedule, as well as serve as the technical expert for design, installation and commissioning. This considered, the following are some valuable lessons learned, and accompanying recommendations.
Communication: Open, Often and Visual
Set a project schedule. As the project progressed from initial groundbreaking, contractors mobilized and sought to begin installation planning based on equipment delivery dates. In the beginning, all appeared okay, with a few minor slips and setbacks, but then came notification of the larger delivery delays. Compounding these delays were items being delivered out of sequence and not in full, leaving the installation contractor figuring out how to put the puzzle together. Naturally, questions came about: "When is this arriving? When can that be completed? Do we have enough resources to complete it?” If a project schedule had been used to communicate the impact
of the delays to all stakeholders, better decisions could have been made to reduce the costly overruns when having too many resources with not enough work, and vice versa. Additionally, the impacts and alternate planning would have been beneficial when it became apparent the project deadline for completed commissioning would not be met.
Set a project budget. For this project, spending was fast and furious, as with most capital projects where high-dollar equipment requires larger initial payments. As the project progressed, the subject matter experts projected a large contingency for the initial scope, but did not want to miss out on the opportunity to include a few other items while the plant was down. At first, it was a few items here and there, but the list quickly lengthened—growing the scope of the project to encompass the entire plant site. With the current project spend not universally being known, the budget turned to managing the contingency drawdown to cover the added scope. When the unknowns became reality, the costs were unavoidable. With more delivery delays, cost overruns became inevitable. When the contingency was used early for added scope, the entire project ran over budget for the duration. Had the budget controls been in place, with visibility of current status and estimate to complete, different decisions may have led to the project coming in on budget.
Make the plan and work it. A good engineering drawing set is merely a tool for communicating what to do and how to do it. It can clearly define the plan, and in the preliminary stage, identify areas of concern that need more diligence. A good example of this was in the planning of setting new equipment and conveyors. Equipment locations were predetermined, but the setting of the infeed conveyors was simply left to the installation contractors to modify, relocate and set. Leaving this to contractors can lead to misalignment, wrong configurations and improper design modifications.
As the scope of the project increased, more areas of the plant were modified without proper drawing sets. This left the installation contractor to figure out more and more of the design themselves, leading to costly rework upon inspection and commissioning. Had the plan been set from the beginning and been adjusted accordingly— e.g., drawing sets approved, then revised and communicated—the plan would have worked to better align with the initial budget, and may have mitigated much of the frustration between stakeholders.
Share project execution. When managing small or simple projects, one can be of mind to handle all aspects alone. As projects grow, it is imperative to utilize a team to manage different parts of a project. A project manager or subject matter expert trying to manage everything will lead to missed details, miscommunications, frustrations among stakeholders, and ultimately, burnout. Having people take specific responsibilities within a project and communicate regularly on the status, past performance, and what’s ahead can mitigate the pitfalls common to projects that exceed initial project constraints. Specifically, when a group looks after the budget, scope, schedule and performance, collectively, they can make better, more informed decisions than one person can by themselves. As observed, this likely would have helped this project stay under control and finish on time and budget.
As we look to have good definition in all phases of pre-project planning, knowing and effectively communicating the plan is critical. When projects are approved for financial expenditure, stakeholders want to know what the risks are and how they are being mitigated. Having a good plan that can be communicated, whether it is written, verbal or visual, is key to mitigating risks and achieving project success.

Author: Jeffrey Tuma Senior Project Manager, Evergreen Engineering Inc. 541-484-4771 www.evergreenengineering.com