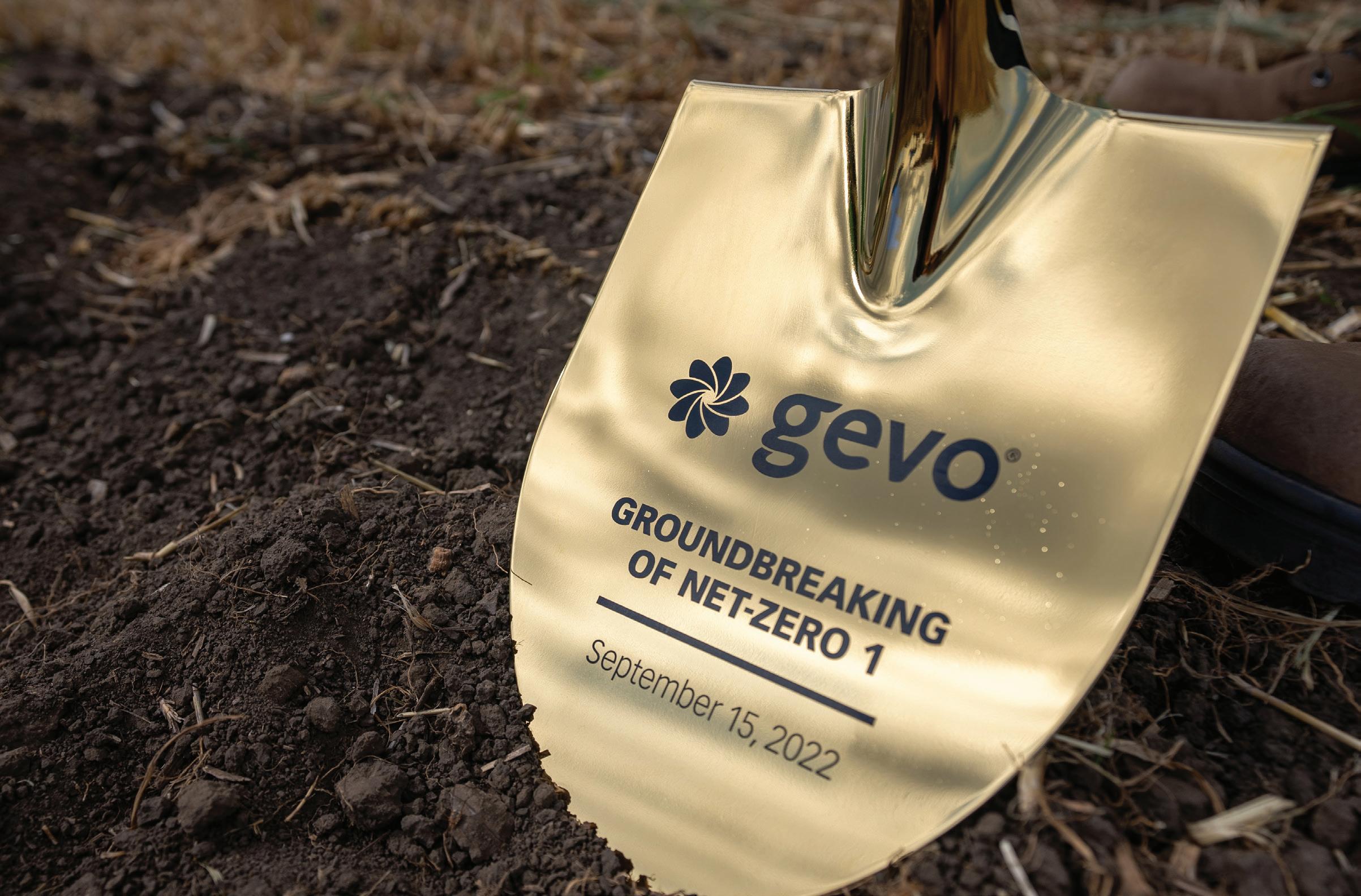
9 minute read
PROJECT
DIGGING INTO
DECARBONIZATION
Putting its deep knowledge of corn biorefining to work, Gevo has pivoted to blaze a new trail in sustainable aviation fuel.
By Katie Schroeder
Gevo Inc., an emerging key player in the sustainable aviation fuel (SAF) industry, is leveraging its unique experience in biofuel production to develop a platform for decarbonized biorefineries set up to potentially produce nega-
tive carbon SAF. Formed in 2005 with the goal of developing yeast to convert carbohydrates into methanol and isobutanol, Gevo has now entered the burgeoning biobased jet fuel space, signing offtake agreements with roughly a dozen airlines and setting a goal of producing 1 billion gallons of SAF by 2030. Its history of producing isobutanol, ethanol and renewable hydrocarbons puts the Coloradobased company in a strong position to help de-fossilize the aviation industry.
Ethanol and Isobutanol Ties
Over a decade ago, Gevo acquired an ethanol facility in Luverne, Minnesota, retooling the plant for the production of both isobutanol and ethanol, side by side. The effort took a few years to commission, but by mid-2014, Gevo had successfully demonstrated the joint production of the two biofuels. The company was drawn to isobutanol production due to its promising characteristics—its high energy content and potential as a valuable gasoline blendstock, explains Tim Cesarek, chief commercial officer at Gevo.
Isobutanol’s chemical structure gives it flexibility as a chemical intermediate for difficult-to-decarbonize parts of the chemical industry, according to Paul Bloom, Gevo’s chief carbon and innovation officer. Although ethanol and isobutanol are both produced by fermentation, isobutanol requires a more advanced process technology and runs at a lower concentration than ethanol.
Isobutanol also has the potential to be transformed into isobutylene, a component used by the petroleum industry to make plexiglass or polycarbonate, and it is also wellsuited for conversion into isooctane and, ultimately, SAF. Gevo pursued the isooctane path through its production of racing fuel and renewable gasoline. The company began production of renewable premium gasoline and biobased jet fuel in Silsbee, Texas, over a decade ago, early experience that enabled it to pursue SAF. “We were one of the first to secure a pathway from the FAA, which was the alcohol-to-jet pathway,” Cesarek says. “At that time, we utilized our isobutanol production in Luverne and took that alcohol to Silsbee where we produced isooctane for racing fuel and jet fuel that was used in multiple OEM engine sets.” Over a period of several years, Gevo secured ASTM certification for its SAF, getting approval in 2016. Now, the company is ready to take the next step, just as global demand for SAF is set to soar.
SAF Era Begins
Worldwide, SAF is in high demand because it is the only market-ready option for an aviation industry striving to decarbonize—and as a result of low-carbon fuel mandates, carbon reduction targets and the proliferation of government incentives for SAF globally. With hydrogen and battery power still still decades away from being realistic options for carriers, SAF is critical.
“Gevo’s ‘drop-in’ SAF, meaning it can just drop into existing engines and infrastructure, gives carriers the ability to reach those net-zero goals sooner, while not relying on
GETTING OFF THE GROUND: Gevo officially broke ground on its Net-Zero 1 SAF biorefinery in September, starting dirt work on the first of what might ultimately be three or more similar alcohol-to-jet fuel plants.
PHOTOS: GEVO INC.
technology that’s not ready for commercial scale,” explains Bloom. “We have always been focused on how we can use domestic, lowcarbon feedstocks to create alcohols and Cesarek carbohydrates to make fuel. Gevo is all about creating low-carbon fuels, while at the same time ensuring the American farmer is compensated appropriately for growing the low-carbon feedstock we will use. This helps the environment and rural American jobs."
The aviation industry has the goal of 3 billion gallons of cost-competitive SAF available by 2030, which is a 66,000 percent increase over 2021 production rates. “It's an exciting time to be working on solving the challenge of lowering greenhouse gas emissions in the aviation industry,” Cesarek says explaining how Gevo has had to prioritize its activities to pursue its new vision. Recently, both the Silsbee and Luverne plants have idled as Gevo shifts its focus to the completion of its highly anticipated Net-Zero 1 plant in South Dakota.
CarbonNegative SAF
To provide the millions of gallons of SAF it has contracted, Gevo intends to build and operate a series of decarbonized plants to produce SAF with extremely low carbon intensity, or CI. Its flagship project, Net-Zero 1, located in Lake Preston, South Dakota, broke ground in September and is expected to be operational in 2025. When complete, the plant will transform corn into sustainable aviation fuel with a low or potentially negative carbon intensity, and Gevo will guarantee the CI of its fuel utilizing a proprietary block chain tracking system called Verity Tracking, calculating CI from field to flight.
“We’re constantly mindful of how to mitigate the fossil CO2 emissions in our process, and we’re constantly mindful as to how we can capture that CO2 and sequester it,” Cesarek says.
The Net-Zero 1 plant will use wind energy, renewable natural gas (RNG) and carbon capture and sequestration (CCS) to attain a negative CI score for its fuel (-5 grams of
Bloom CO2 per megajoule of energy), as determined by Argonne National Laboratory’s GREET model (the ethanol industry's preferred model for its own product and SAF), explains Cesarek. Not only will wind energy be used to de-fossilize the biorefinery’s electric input, but it will also be used to make green hydrogen, which is needed in the process of hydrolysis. The facility’s need for thermal energy, which would normally be met through natural gas, will instead be met by RNG derived from the biomethane of surrounding dairies and potentially Gevo’s own northwest Iowa dairy.
The process flow of Net-Zero 1 will begin with low-carbon corn, which Gevo plans to procure from local farmers by incentivizing regenerative farming practices such as low- or no-till technology, lower amounts of artificial fertilizers and biological treatments to reduce nitrous oxide emissions, Bloom explains. The corn will then be converted into ethanol, DDGS and distillers corn oil, Cesarek says. The low-carbon ethanol will be converted into jet fuel using technology from Axens North America. “Axens not only provides
GREENFIELD VISION: While this rendering of Gevo's Net-Zero 1 SAF biorefinery under development in Preston, South Dakota, shows a solar array at the planned complex, the company has determined that wind power is better suited be the plant’s electricity source. Not only will the wind energy be used to de-fossilize the plant’s electric input, but it will also power green hydrogen production, which is needed in the process of hydrolysis, part of the SAF production process.
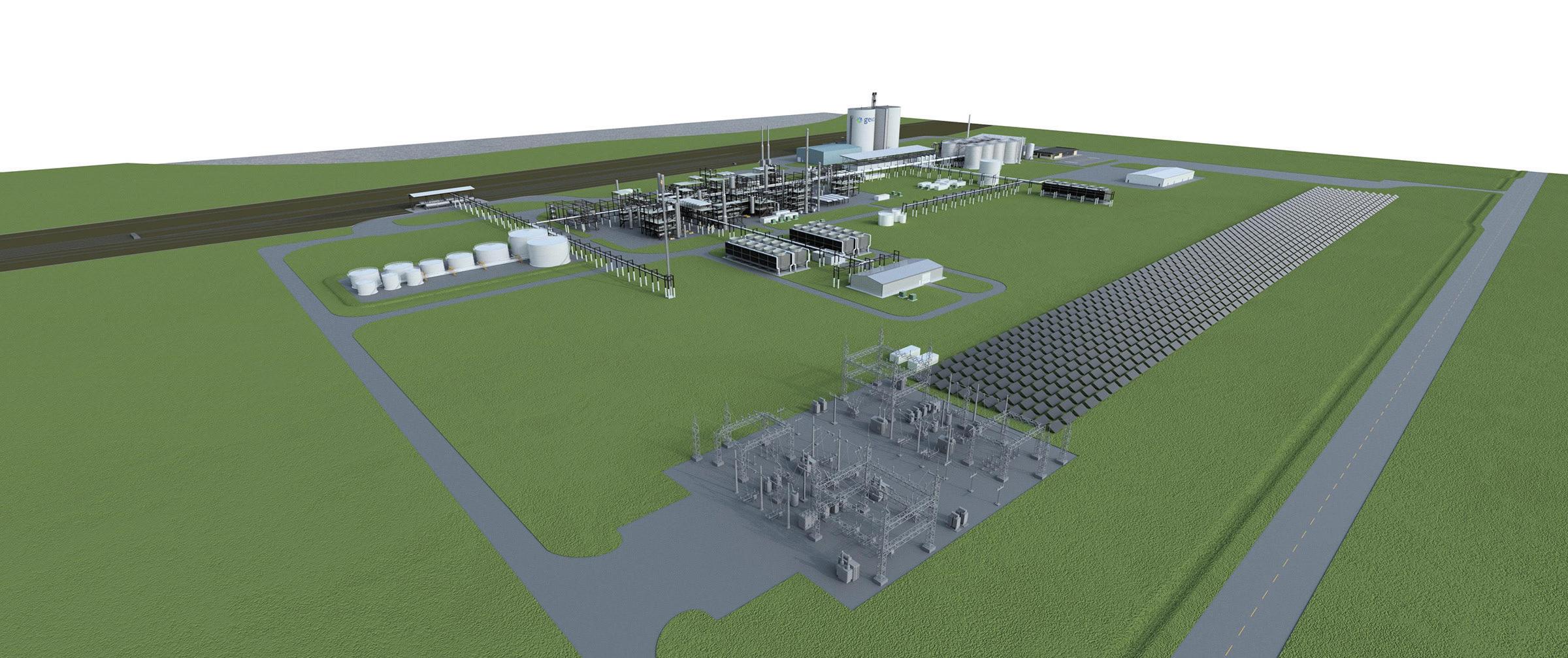
IMAGE: GEVO INC.
process guarantees, but their process technology and unit operations are also in use in the petroleum industry today,” Bloom says. Axens provides a complete range of solutions for the conversion of oil and biomass to cleaner fuels, the production and purification of major petrochemical intermediates, the chemical recycling of plastics, all-natural gas treatment and conversion options along with water treatment and carbon capture. “The combination of what they had already developed [for producing] ethanol-to-jet, combined with what we know about ethanol and our de-fossilization strategy ... is kind of the secret combination— the magic—that we brought together to make something that was executable in a time frame that could meet the demands of [our] customers.”
Net-Zero 1 is to be the first of several decarbonized greenfield and brownfield plants planned to provide Gevo's contracted 375 mil-
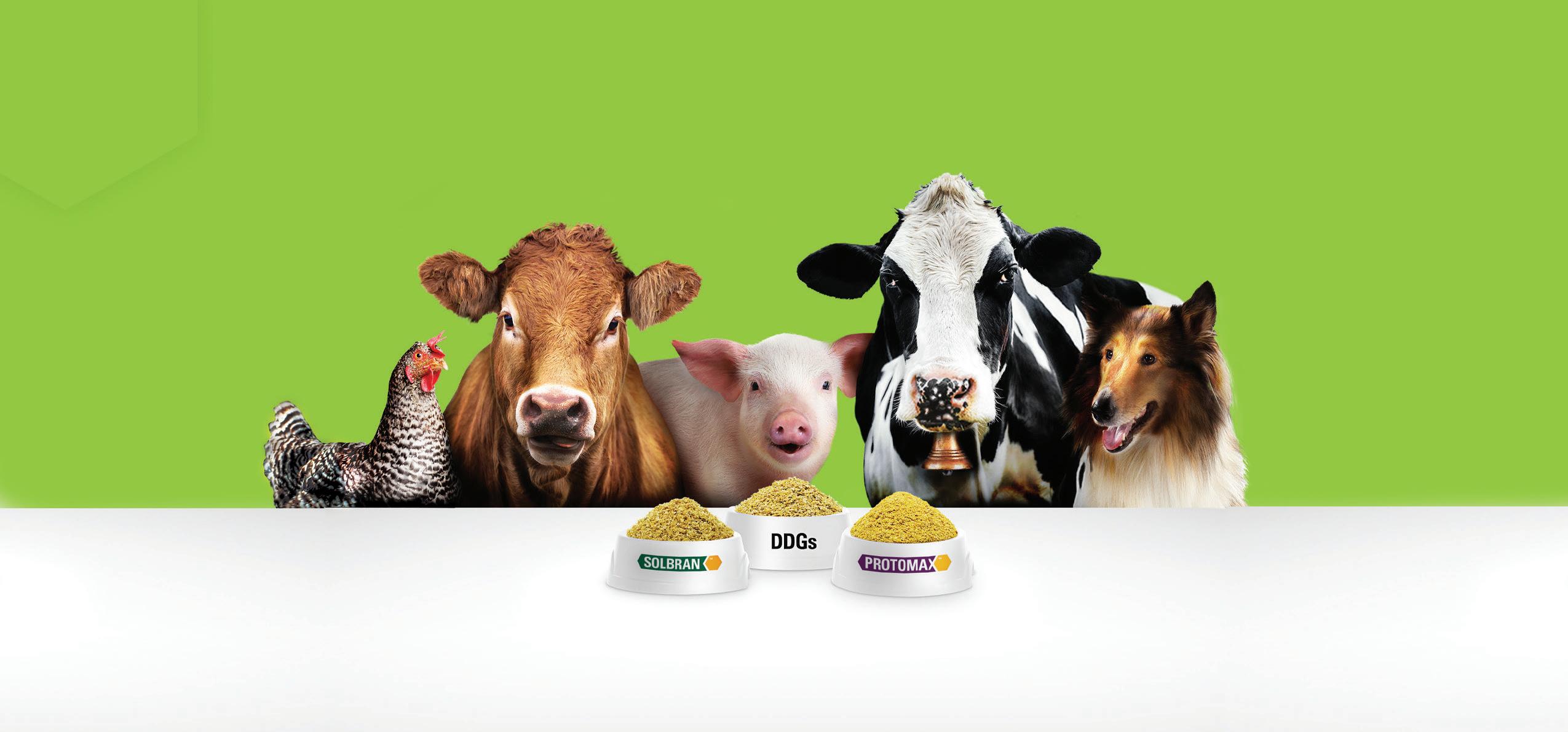

lion gallons of SAF. And with just two-plus years to stand up production on schedule, Cesarek says, the company is primarily competing against time.
“The cascading order of what it takes to build a plant, to put in place the necessary ecosystem, to demonstrably decarbonize, to build pipelines to capture CO2 and put it in the ground, and to build a wind farm, is our biggest challenge,” Cesarek says. “The market is here now, and they want the product now and ... a lot of it. So, it’s a matter of meeting and exceeding that demand."
Developing Verity Tracking
To guarantee that its SAF is low carbon, Gevo along with JV partner Blocksize Capital, is developing a block chain solution, or distributed ledger technology, called Verity Tracking. The technology will allow the tracking of carbon through the entire production process from farm to flight, explains Bloom. The system will allow Gevo to track carbon in the field and compensate farmers who are delivering low carbon feedstocks, accordingly. “Verity will enable us to verify the entire cycle of a carbon molecule, which means we can better compensate farmers growing low CI crops. The American farmer is the key to our entire business. Without farmers growing low CI corn, and what we are uniquely capable of doing with that corn, we’d be no different than any other company,” he says.
Gevo plans to make Verity Tracking available to any biofuels producers who want to verify and track carbon emissions from the field to the harvested bushel to the refined gallon.
One of its top near-term challenges is making sure the carbon reduction practices farmers put in place are rewarded by existing and future policy. For example, the California Low carbon Fuel Standard does not take into account the reduction of emissions in the feedstock when sustainable farming practices are used, but rather uses a flat number to calculate the CI score for every specific crop. Bloom says this needs to change in order to reward those delivering carbon benefits throughout the value chain.
Looking into the future, Gevo’s priority is the completion of financing for the NetZero 1 plant, and of course to get it built and operating. As those targets are met in South Dakota, the company intends to follow through on the engineering, design and development of Net-Zero 2, 3 and perhaps more plants at locations Gevo has already begun to identify, explains Cesarek. “The convergence of demand and availability of technology-ready processes within the context of the overall energy transition creates an immense opportunity for us. It’s exciting to think of what we’re going to do in the coming years and the entire team is working hard to make a difference,” he says.
Author: Katie Schroeder Contact: katie.schroeder@bbiinternational.com
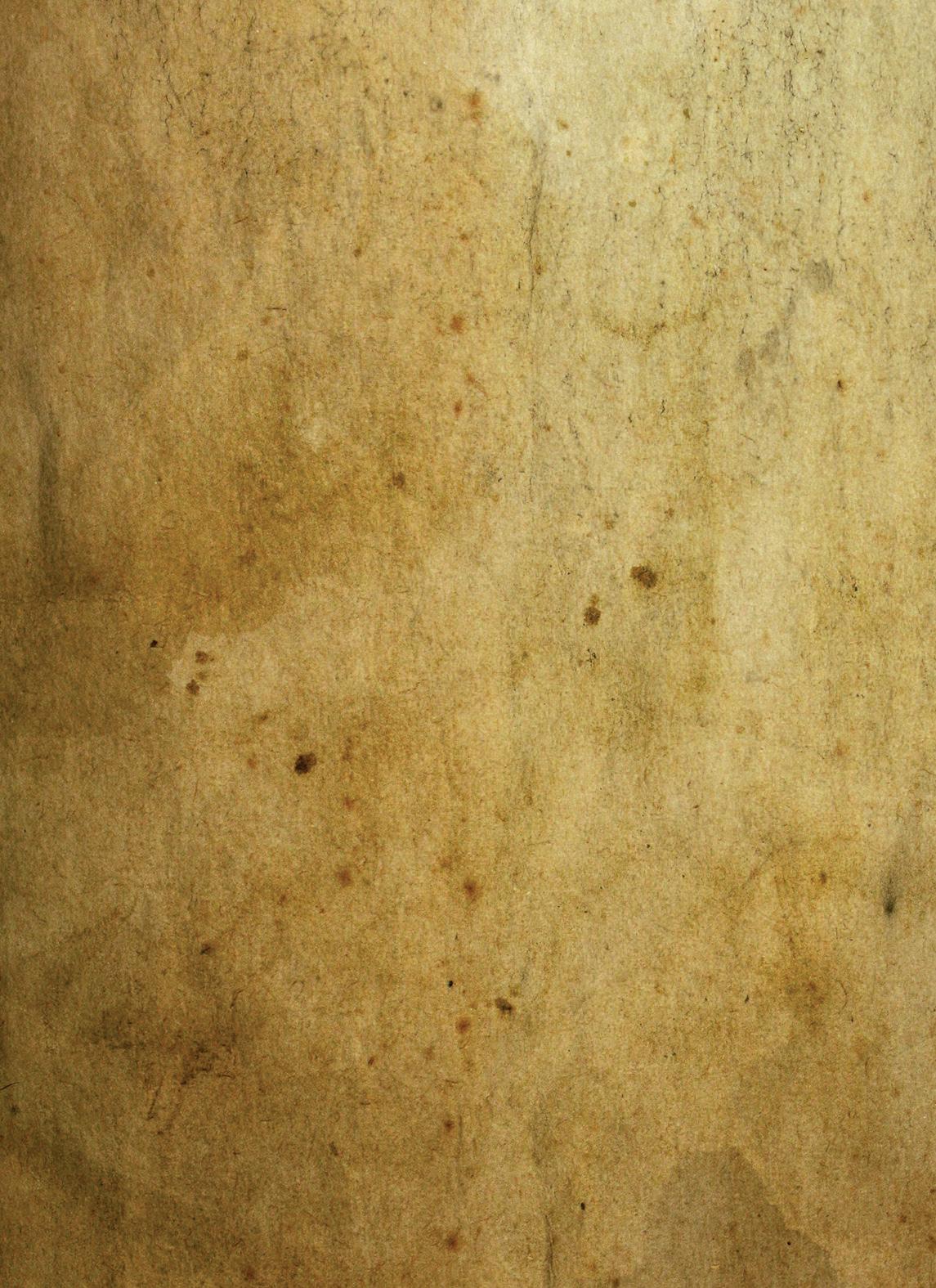
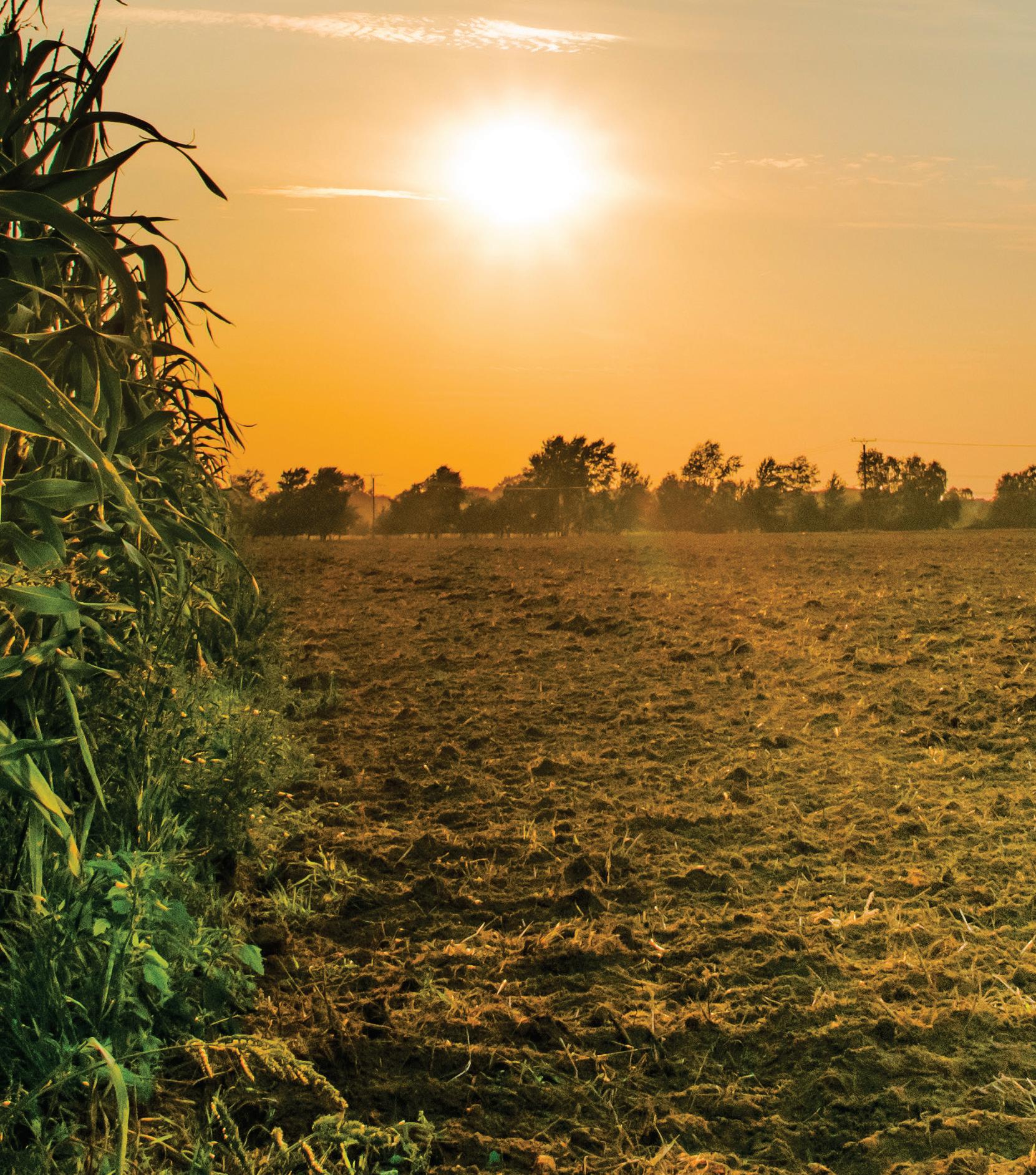
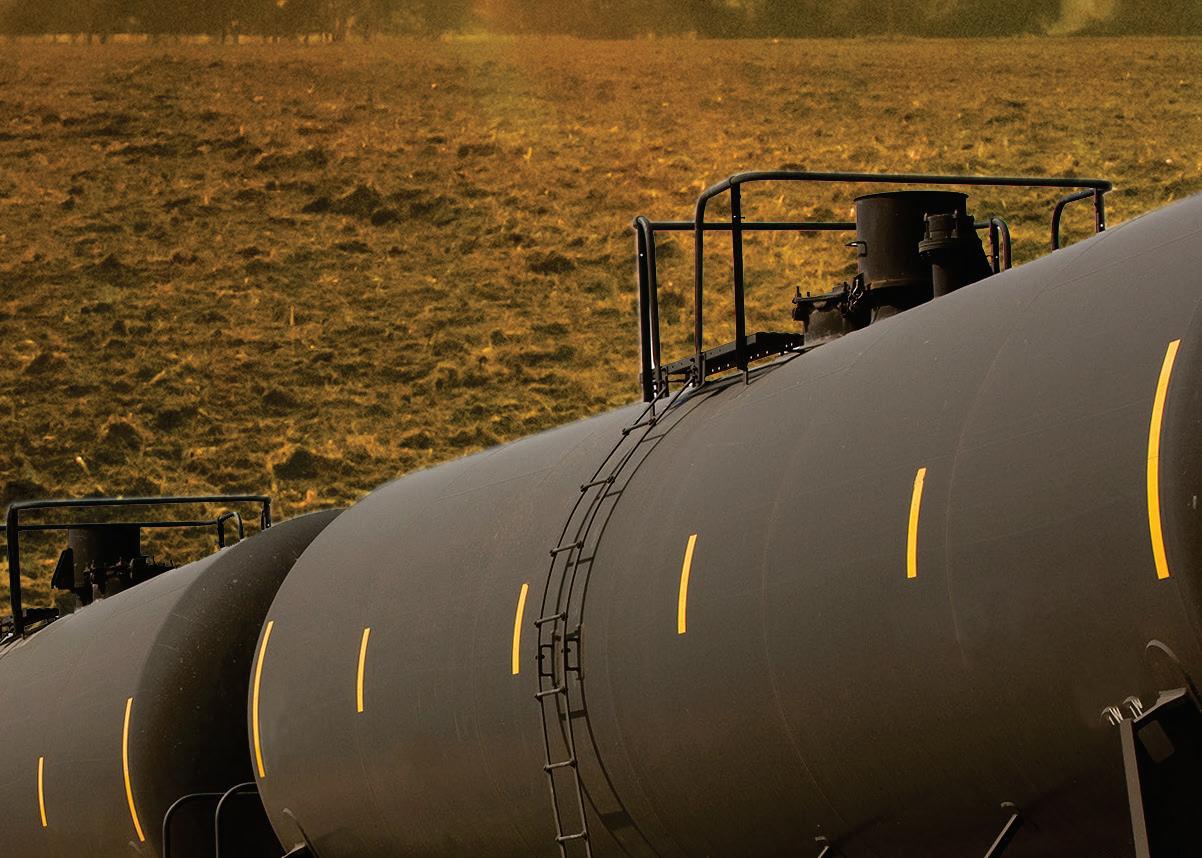
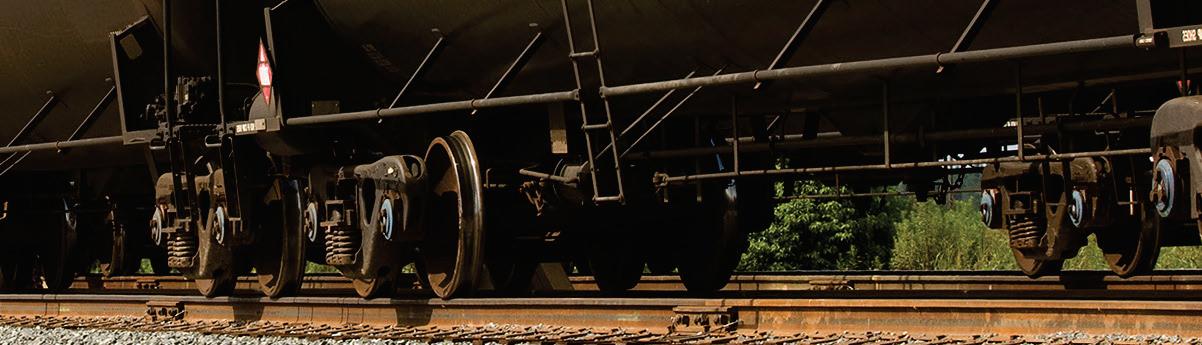

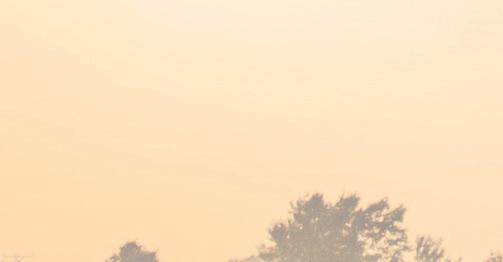
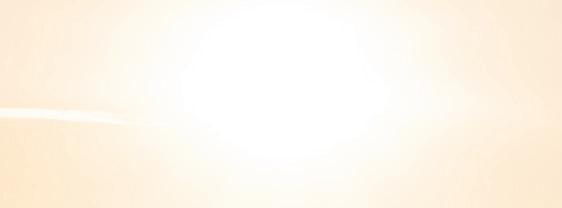
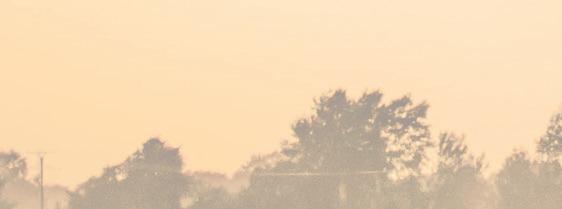
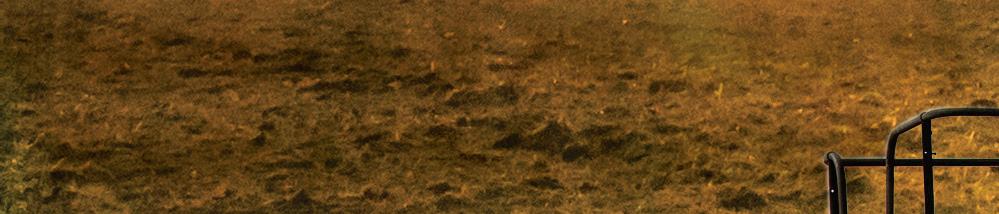