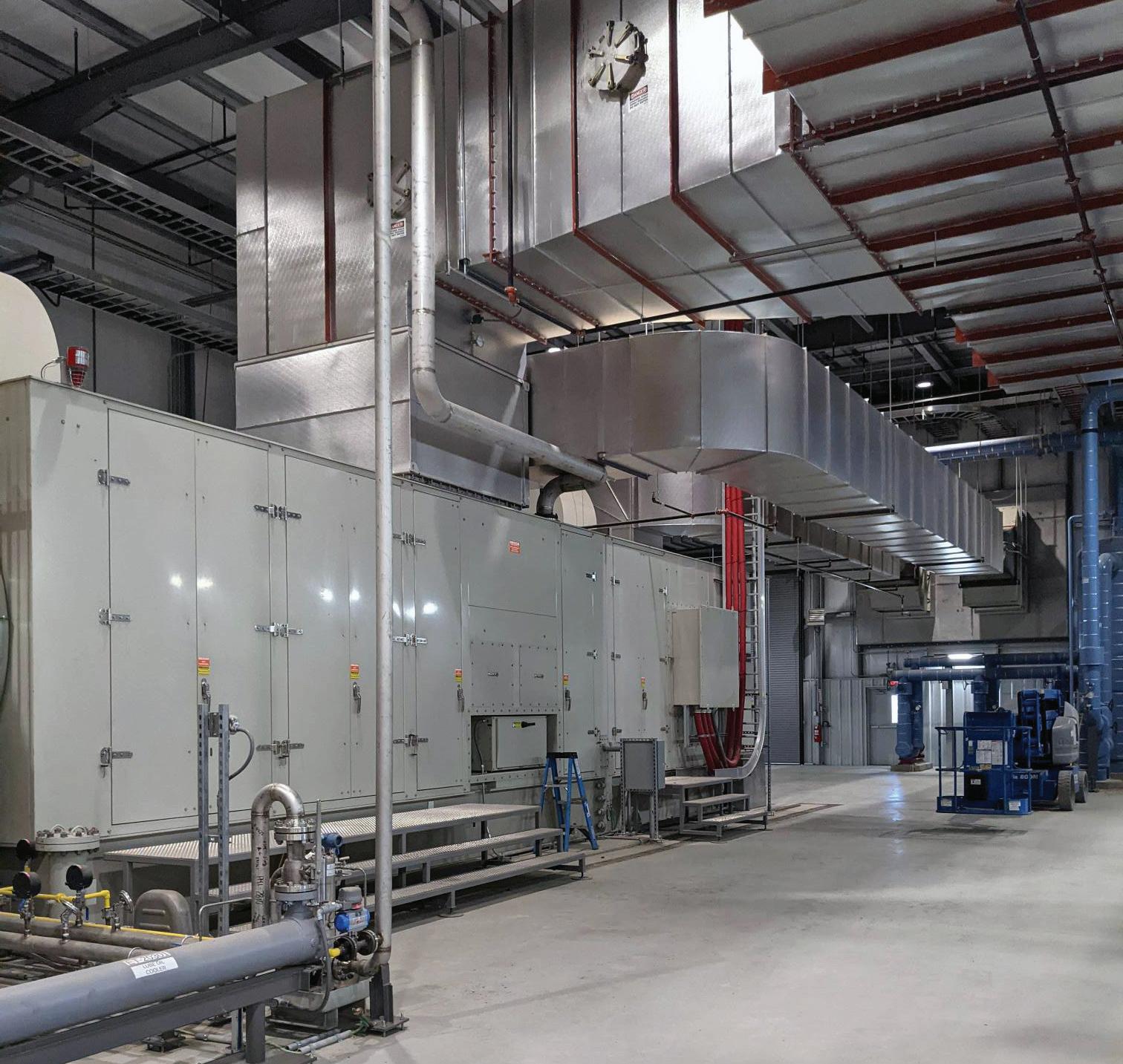
8 minute read
ENERGY
Stepping Up to CHP Platforms
While combined heat and power has been an enticing option for energy progressive ethanol plants for years, it’s now a front-andcenter play for producers on carbon reduction quests. By Luke Geiver
Combined heat and power (CHP) isn’t novel to ethanol production, but mounting enticements for low-carbon, on-site energy generation are giving it strong new appeal. The technology—
while large-scale and industrially robust—is simple, proven and effective. A turbine, combined with a generator along with a boiler on the backend, can produce electricity in a system that is more than 90 percent thermally efficient. Power produced from a modern CHP system can run in the 2 cent-per-kilowatt range, a big decrease from the 5-cent to 10-cent range common on the Midwest grid. Modern CHP designs are reliable and don’t go out when the grid goes down. They are tougher to hack from a remote locale. And, in an industry full of producers focused on lowering their carbon intensity (CI) scores, CHP systems can provide one of the largest CI score reduction offerings of any technology or strategy that doesn’t include the words “underground injection” or “pipeline.” For plants thinking about carbon reduction, the acronym CHP now seems almost synonymous with lower CI.
The State of CHP and Ethanol
Bernie Hoffman, vice president of P&E Solutions, an industrial contractor and service provider to entities evaluating CHP systems, has been in and around the ethanol industry for 22 years. Hoffman has watched the evolution of the industry, and right now, he’s busy helping several ethanol producers with CHP systems. “Everybody in the ethanol industry views their situation as this: upgrade, or get left behind,” Hoffman says.
For many facilities, CHP systems are proving to be the next big plant improvement. Blue Flint Ethanol LLC’s plant in Underwood, North Dakota, recently held a tour to show off some of its work and plant evolution. A major part of the tour was its CHP expansion. Hoffman’s team currently has three projects underway (and another eight to 10 producers talking with his team) that are bound by NDA’s, and whether it’s his company or another provider, Hoffman believes there will be several more projects on the way in the near-term.
CHP in the ethanol space is established, he adds. Adkins Energy in Lena, Illinois, has been running CHP for more than two decades, while others are relative newcomers to it, like Kansas Ethanol in Lyons, Kansas, which has been running CHP for roughly one-and-a-half years, according to Hoffman. More broadly, there are roughly 38 ethanol facilities currently in the U.S. Department of Energy’s CHP database.
The industry push to lower CI scores will now make CHP one-part wanted and one-part needed. California’s Low Carbon Fuel Standard has been a driver for ethanol plants “wanting” CHP for the past four years, Hoffman says. “Typically, a CHP installation will lower a plant’s carbon score by 10 to 12 percent.”
According to Hoffman, producers that have signed up for carbon capture pipelines or are building on-site injection wells have all realized that CHP is no longer just a want, but a need. “It takes a lot of electricity to put the CO2 in the ground or move it away via pipeline,” he says. “What we are finding is that the electricity demand for CO2 matches the total electricity demand for the ethanol plant.” For context, Hoffman provides the following example. For a 100 MMgy ethanol plant, the electrical demand of the entire facility will be roughly 6.8 MW. The electrical demand for
ENCLOSED ENERGY: This is an actual turbine, the Solar Titan 130. When installed, the unit is contained in the enclosure shown so the internals are not exposed or visible.
PHOTO: P&E SOLUTIONS STEAM MACHINE: The heat recovery steam generator shown here is a boiler attached to the turbine. The HRSG creates the steam needed for the entire ethanol plant process.

PHOTO: P&E SOLUTIONS
capturing and injecting, storing or sending it through a pipeline is estimated to be about 6 MW.
“They [the plants that have signed onto a carbon capture project] know there is an added electrical load that is coming,” Hoffman says. “If you are an ethanol producer doing carbon capture, you have an even more compelling story to install CHP.”
The Nuts and Bolts of CHP
A typical CHP installation costs roughly $25 million and is paid back in four to five years, according to Hoffman’s loose projections he shares with potential clients. That is installed, running and turnkey. Hoffman’s team guarantees a CHP project startup in 17 months. The heat recovery steam generator takes roughly 10 months to deliver and install, with the turbine and the boiler coming two months later. The major work components of the job include civil engineering for site prep and infrastructure integration, piping and pouring the big concrete pedestals. Tieins can be done during a regular maintenance outage that occurs during the project buildout, Hoffman says. One annual maintenance job is required for the CHP system, which can also be done during a regularly scheduled plant maintenance outage.
With the push by producers to start working on CCS projects or join a pipeline network, Hoffman urges producers to start looking at their own situation sooner than later, because the timeline for getting the HRSG may be pushed back by a few months. Some fiscal incentives for CCS require construction to commence in the next 36 months, so getting started sooner on an installation is more advantageous to the entire process, he says.
The results are positive. P&E has realworld information from a 118 MMgy facility that it installed a CHP system for. The plant power demand was 6.8 MW, plant steam load was 160,000 pounds/hr and the plant’s CO2 production came in at roughly 300,000 tons/ yr. After installing a One Solar Titan 130 PGM LoNOx gas turbine gen set (capable of making 14 MW); one Rentech HRSG (with a max team capacity output of 300,000 pounds/hr), the plant earned a direct energy savings of $7.2 million per year. The carbon reduction totals came in at 37 gm CO2 e/MJ—or an estimated monetary value of $26 million annually. All of the plant's electricity needs were created from the turbine and 100 percent of its required steam was provided by the HRSG.
With the P&E Solutions CHP offering, the design replaces grid electricity and steam from existing boilers once the project is complete. Grid power becomes backup only. The host plant can also shut down existing boilers and existing steam sources. “This can be important as many plants are aging and boilers need significant maintenance or replacement,” Hoffman says.
The Right Tech at The Right Time
Hoffman calls CHP and CI score reduction efforts a “marriage made in heaven.” He was part of a panel of speakers at the 2022 International Fuel Ethanol Workshop & Expo in Minneapolis, the world’s largest gathering of ethanol producers. The entire panel talked about the role of CHP in the ethanol space, specifically how it can help with carbon reduction efforts. “I think this is a perfect storm for the benefits of CHP right now,” Hoffman says.
The FEW panel on CHP also included Rondo Energy Inc., a renewable heat tech innovator that provides industrial decarbonization services. Rondo has already been
awarded major investment dollars, including funding from Bill Gates. Additionally, Kevin Jensen, power generation account manager at Solar Turbines Inc. (a division of the Caterpillar Co.) shared how CHP complements other low- or zero-carbon energy sources. And Brandon Emme, director of technology development at ICM Inc., offered insight on the use of CHP and other process optimizations for lowering CI scores at the plant.
Currently, gas turbines are the most common tech for CHP, with relatively low emissions and no cooling requirement. Gas turbines are widely used in CHP applications and have relatively low installed costs, according to the U.S. DOE.
Along with Hoffman, the others on the FEW panel noted the significant financial incentives under the Inflation Reduction Act, along with the LCFS, that can come from adding CHP. The other benefits include lower overall direct energy costs and higher ther-
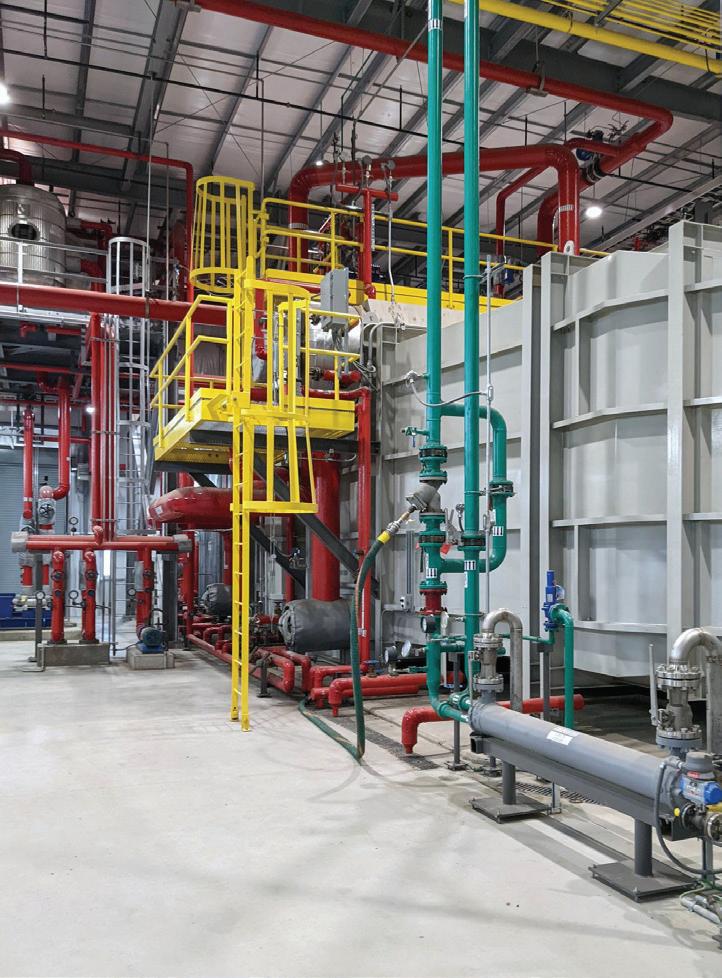
PIPES OF POWER: The steam line pipe, shown here, attaches to the HRSG and moves steam from the CHP system to anywhere in the ethanol plant. Most steam set-ups cover everything required at a plant.
PHOTO: P&E SOLUTIONS mal efficiency, making CHP attractive across a full spectrum of energy prices, mainly natural gas. Plants can find a renewable energy feedstock to fuel a CHP set-up, which in turn lowers the CI score even more. Depending on how efficient a plant is, P&E Solutions has done modeling (for roughly 30 plants) that shows energy savings using CHP can be between 30 percent to 58 percent per year.
“I like to think that CHP will become the new corn oil recovery in the ethanol industry,” Hoffman says. “When plants first installed centrifuges to recover corn oil it spread throughout the industry and, today, I think every plant in the U.S. is selling corn oil.”
Author: Luke Geiver Contact: editor@bbiinternational.com
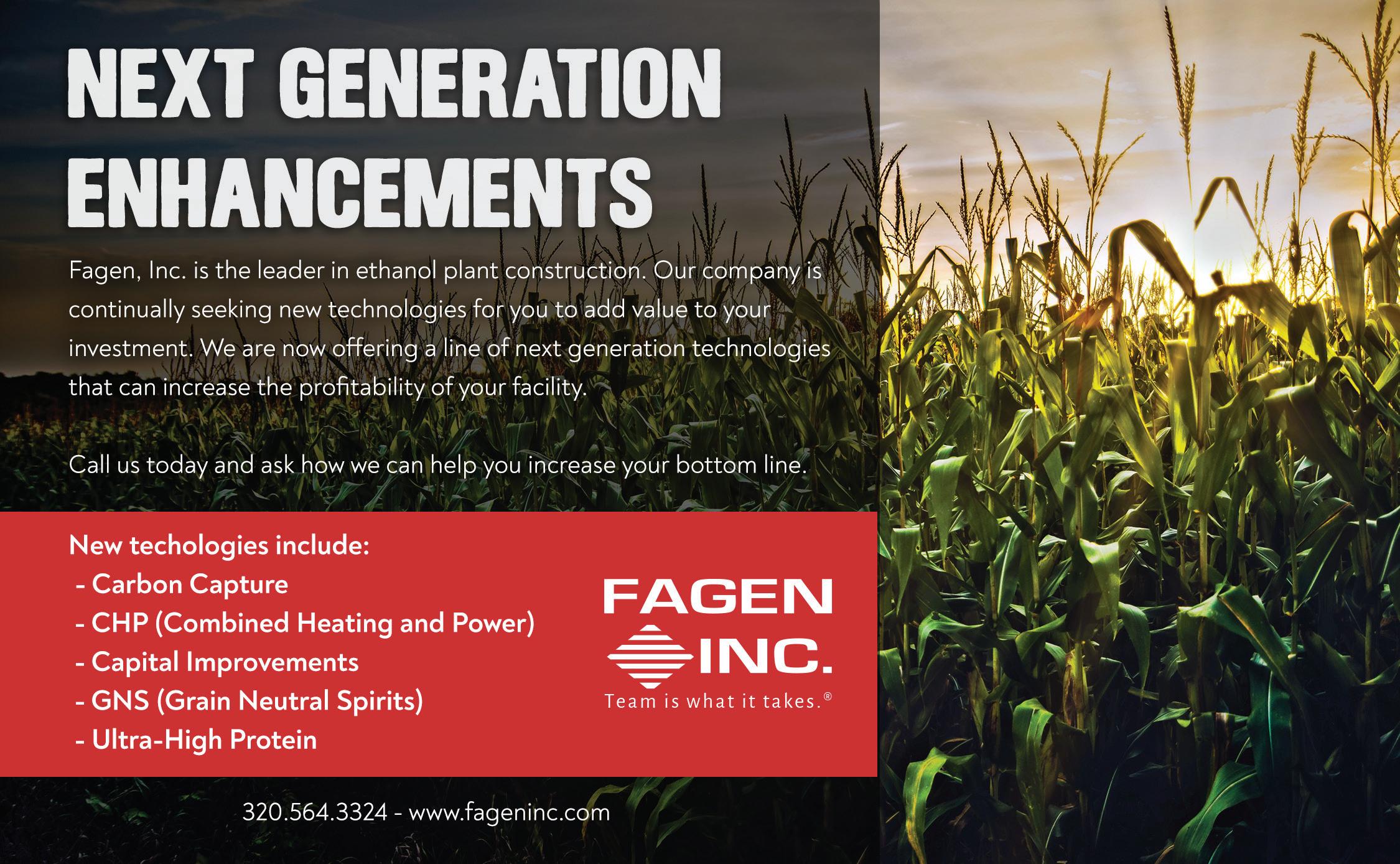
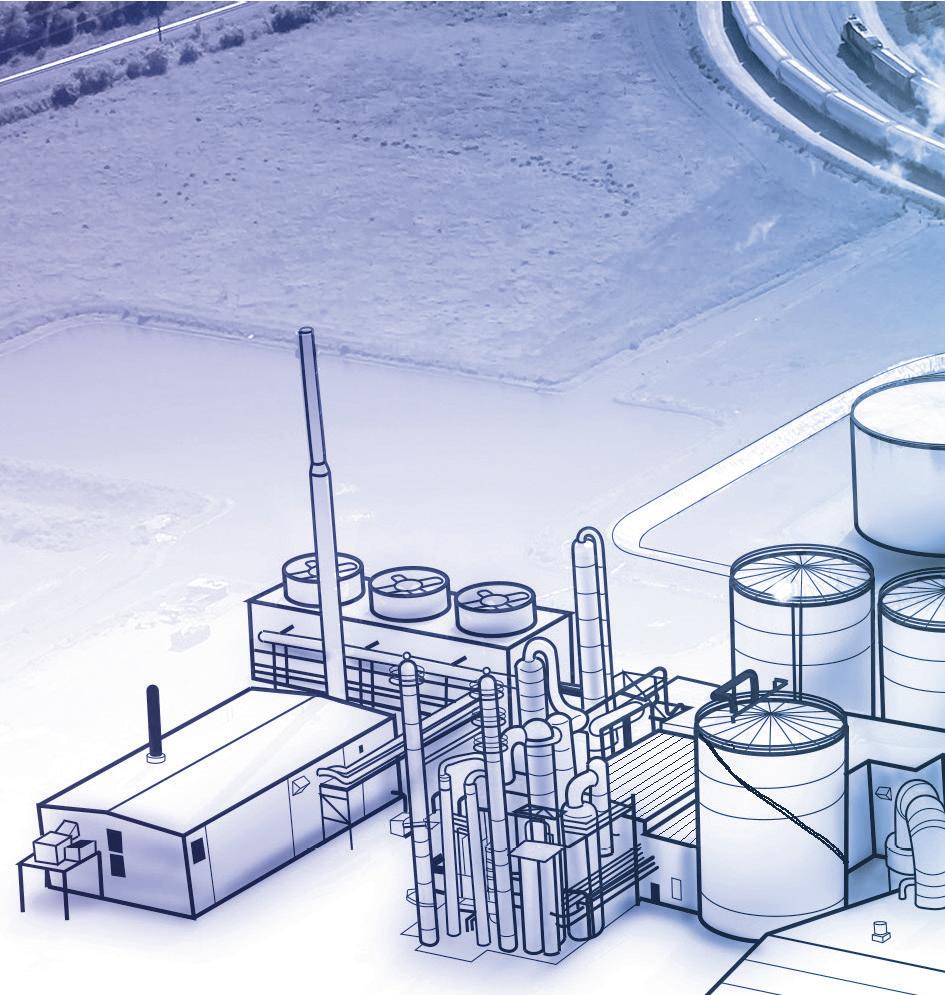
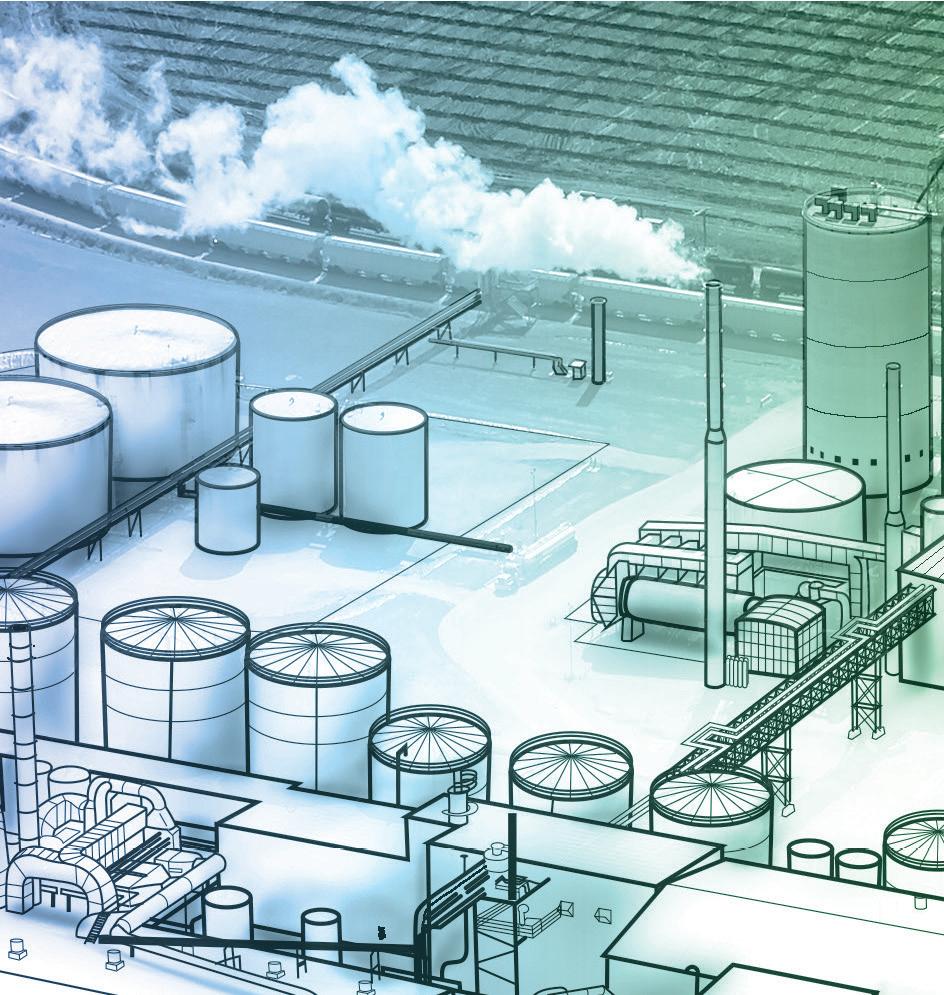
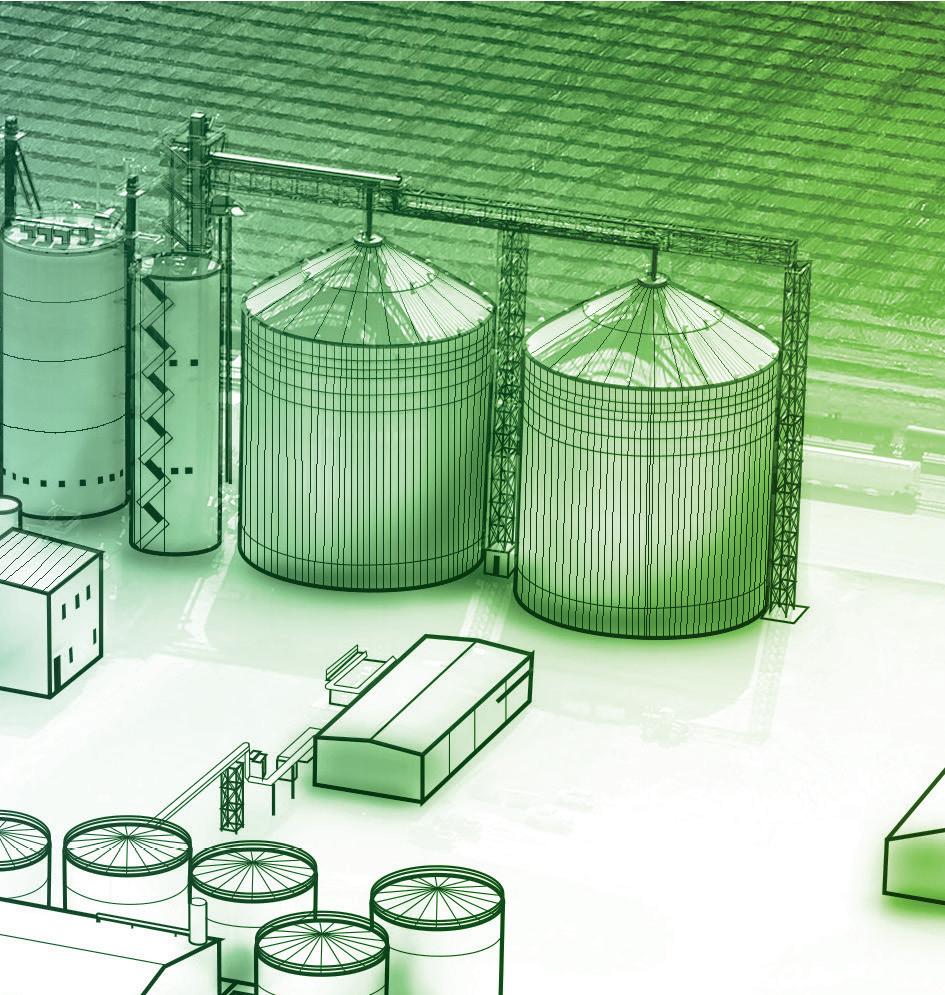
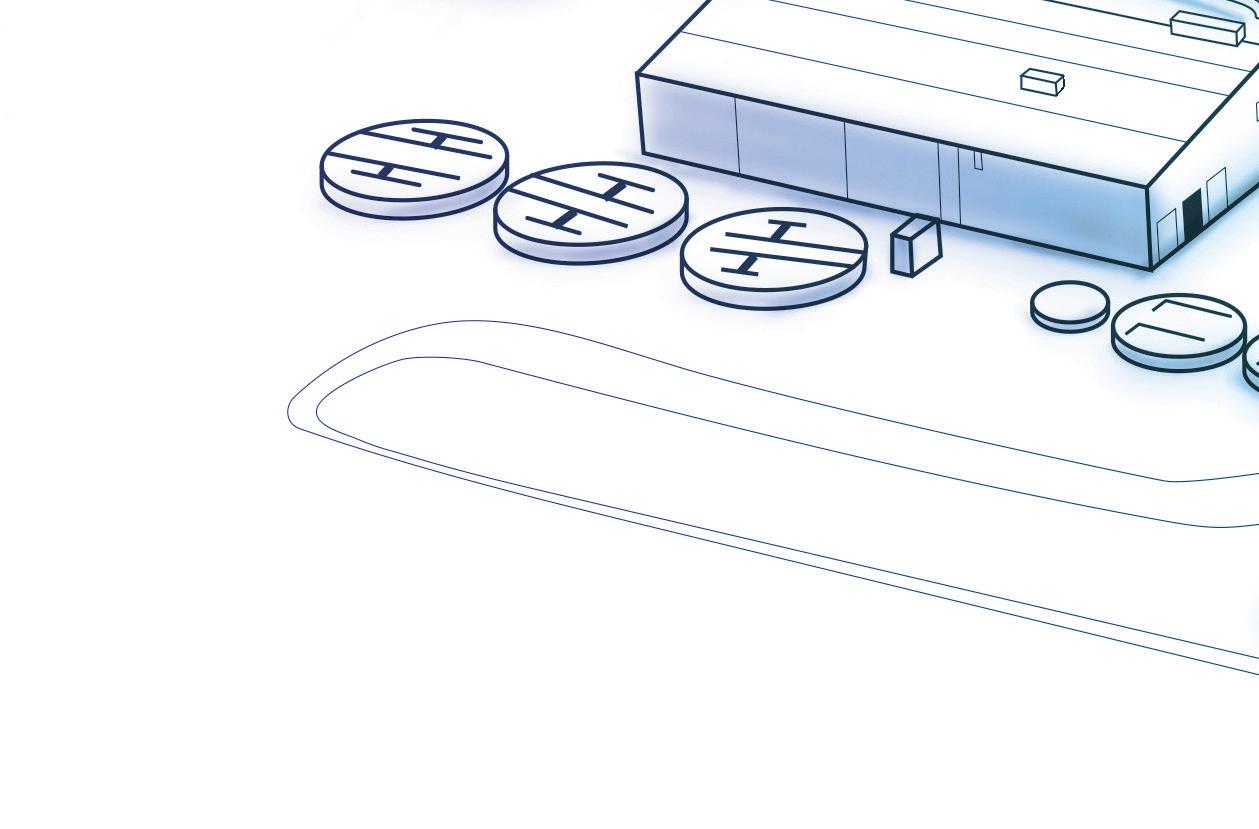
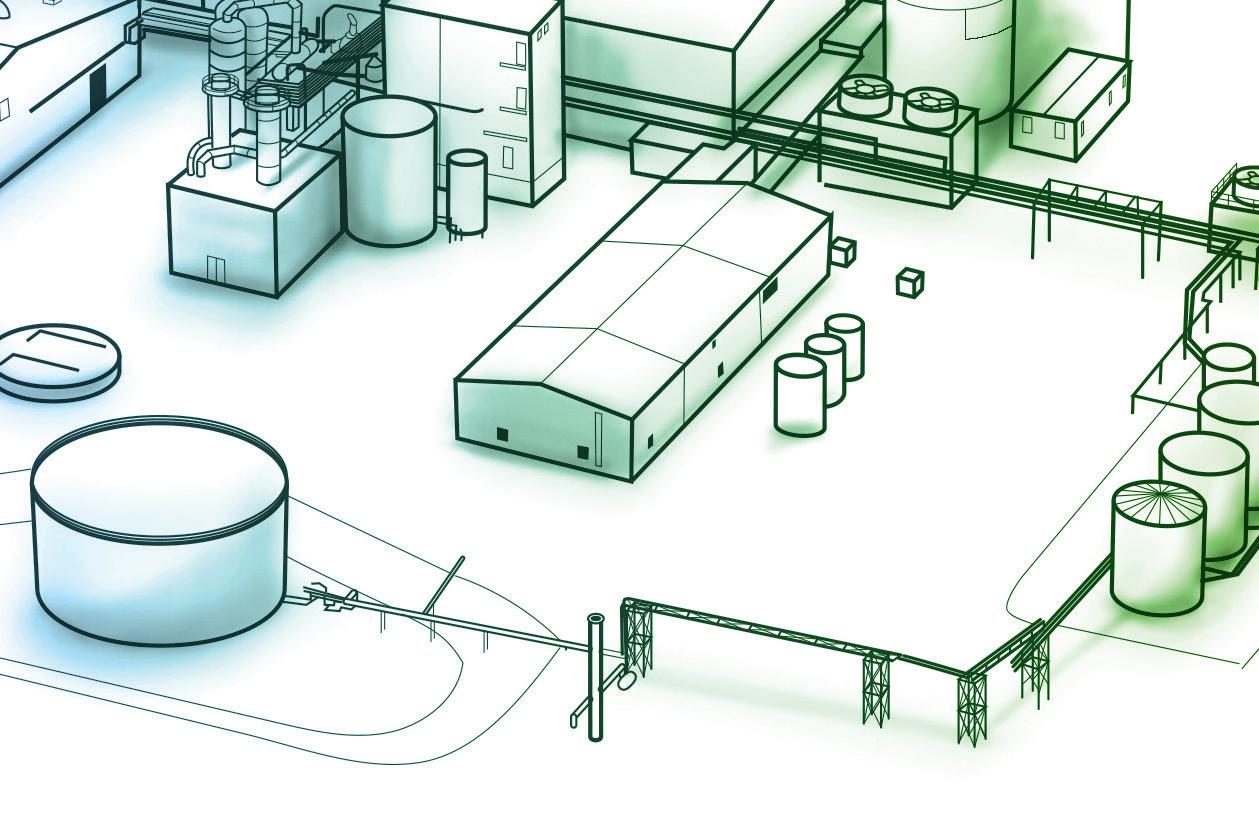
XCELIS® Yeasts
WELCOME TO THE SYNERXIA® GEMSTONE COLLECTION
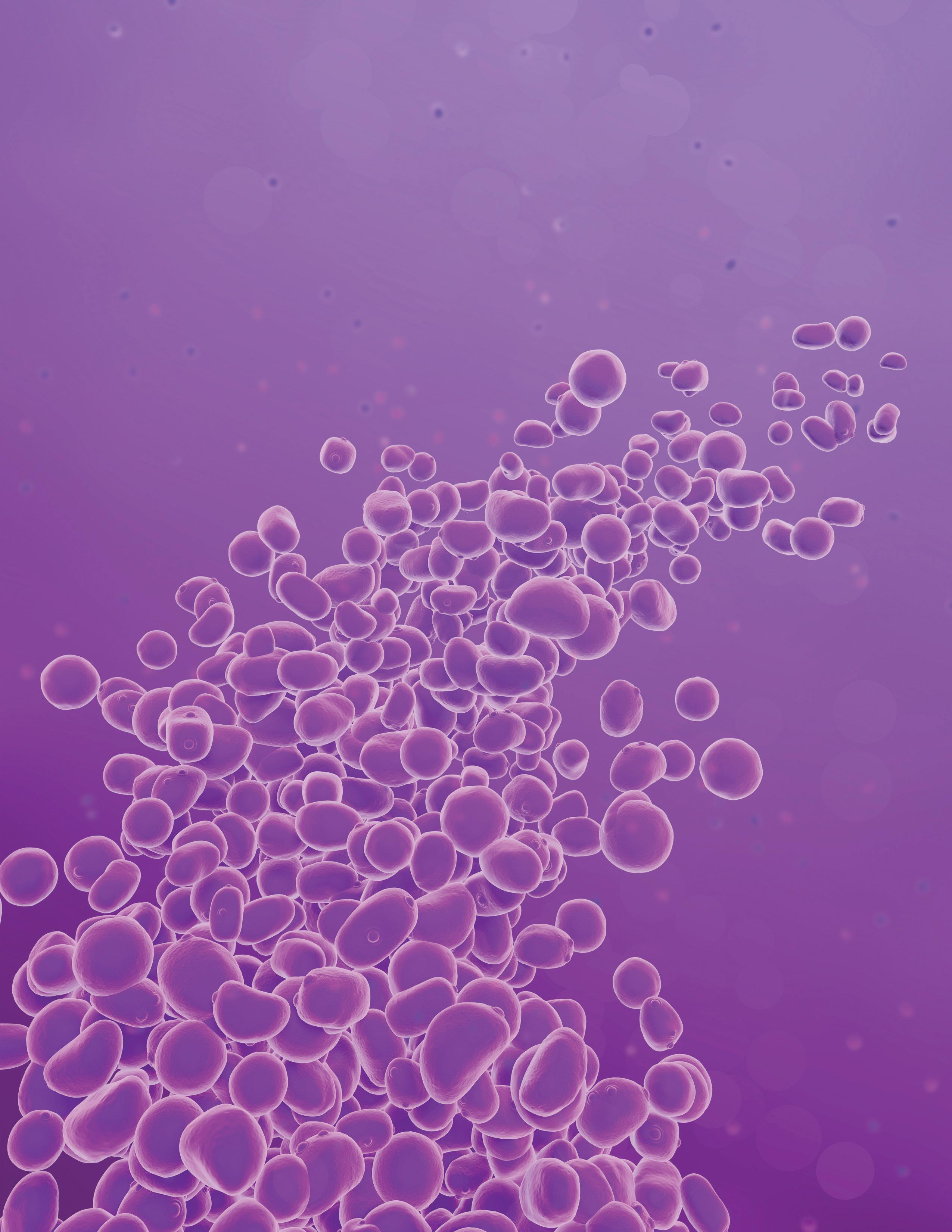
Three new high-yield yeasts engineered for your plant’s needs
SYNERXIA® SAPPHIRE – The most powerful combination of yield, robustness and enzyme expression in a yeast. SYNERXIA® RUBY – The new standard in high yield yeast driving plants to the peak of performance. SYNERXIA® EMERALD – The yield-enhancing yeast geared for maximum ethanol plant throughput.
308 2nd Ave. N., Suite 304 Grand Forks, ND 58203
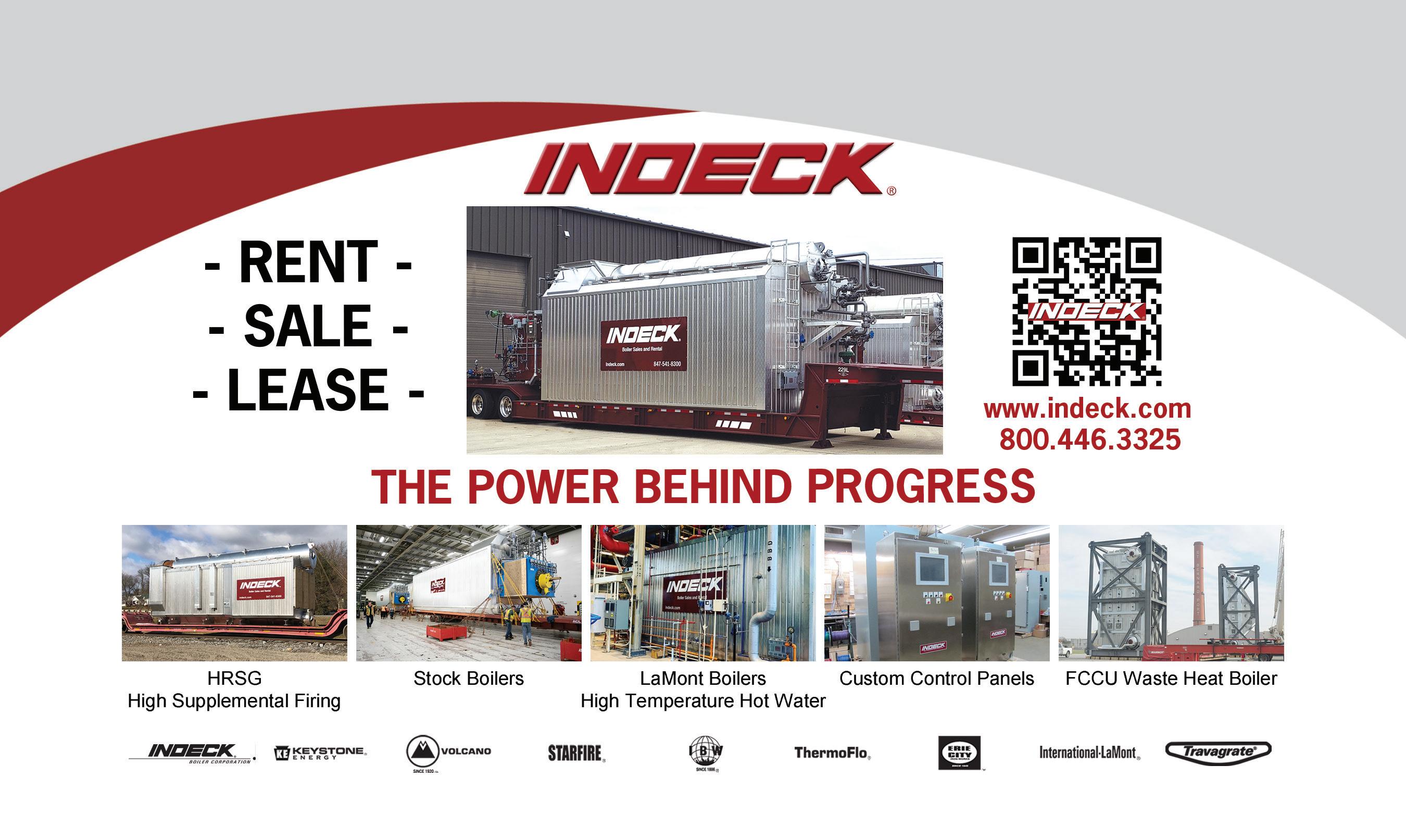