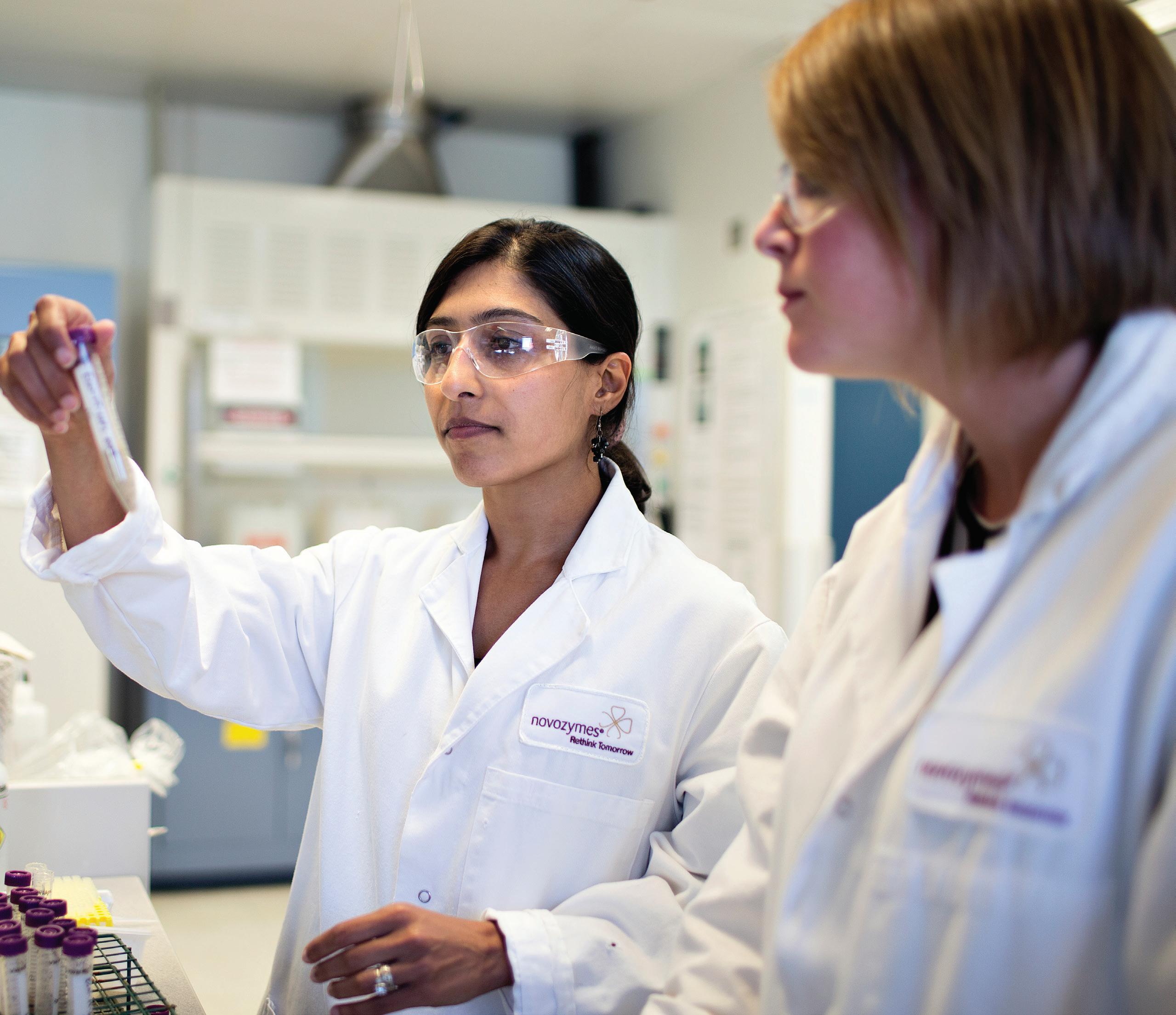
10 minute read
Enzymes
LIFTING UP PRODUCTION
With advanced enzyme solutions, ethanol producers are unlocking more value from corn and other feedstocks. These evolved cocktails are designed for greater heat tolerance, higher output—including DCO yield—and, of course, next-generation pursuits. By Katie Schroeder
In recent years, many ethanol producers have started migrating toward a more diversified biorefining model as they adapt to changing markets and changing
times. The enzymes industry has not only kept pace with this evolution, but helped create it, enabling producers to maximize output, boost distillers corn oil yield, tap into cellulosic ethanol and more.
Novozymes is a provider of yeast and enzymes for the ethanol industry, developing enzymes for liquefaction and saccharification, explains Robert Osborne, R&D manager and leader of the yeast application research and development team. For cellulosic ethanol release, Novozymes has primarily developed and offers cellulases and hemicellulases. Amanda Moser, Novozymes R&D manager, explains that when the company’s customers expressed interest in low-carbon fuel markets, starting years ago, Novozymes intensified its commitment to assist them.
Initially, Novozymes got into secondgeneration ethanol production with its involvement in a first-of-its-kind cellulosic ethanol plant in Crescentino, Italy. The company’s trademarked Cellic line of products included enzymatic pretreatment technologies that catalyze the degradation of plant waste.
Novozymes’ Cellic products help producers breakdown feedstocks such as woody biomass to produce second-generation ethanol. To liberate sugars needed to produce ethanol, the cellulose and hemicellulose found in biomass needs to be degraded. The structure of lignin makes accessing cellulose and hemicellulose difficult because it’s a complex, crosslinked polymer, which gives researchers a challenge in identifying the right combination of enzymes to attack and break down the components within the lignin matrix, explains Osborne. However, the Novozymes team was able to take advantage of its scientists’ expertise and knowledge, combined with a foundational understanding of the customer’s process, to develop technologies to break down biomass to “liberate fermentable sugars,” he explains.
“Novozymes has significant experience developing cellulases and hemicellulases, and we entered this industry initially to support 2G ethanol customers,” Osborne says. “That was really the original focus. We made an intentional market expansion as 2G has taken longer to come online than anticipated. About five years ago, Novozymes evaluated ... how [we could] ... leverage our technology and investment in developing fiber-degrading enzymes for 1G customers. We started looking at the corn fiber matrix to figure out how the fiber degrading—and the knowledge that we had gained and developed from years past—could create value for our 1G ethanol customers.”
In the last five years, Novozymes has been using the combined knowledge of yeast and enzyme development to determine the best combination of enzymes and yeast to help customers achieve their business targets, Osborne explains. The company’s Fiberex platform allows producers to release cellulosic ethanol from the corn fiber matrix to access low-carbon fuel markets, and increase ethanol and coproduct yield, Moser says.
Development of these enzymes starts with an understanding of the substrate, Moser and Osborne agree, a clear understanding of what the enzyme does to the substrate and how different enzymes can complement each other.
“Knowing the substrate and then also being able to test for those benefits. So, knowing that ‘Hey we’re going to get to see this much cellulosic ethanol, we’re going to get to see this much corn oil,’” Moser says. “So, being able to blend those two things is really important and a differentiator when it comes to those enzymes.”
The platform includes a combination of robust fiber-degrading enzymes enzymes, as well as enzyme-expressing yeast strains. The exciting part about cellulosic ethanol released from the corn fiber matrix is higher value ethanol for our customers, “Whether it’s delivered
EYING INNOVATION: Researchers at Novozymes' Franklinton, North Carolina, research center are continuously engaged in both enzyme and yeast R&D and product development targeted at both first and second-generation fuel ethanol production.
PHOTO: NOVOZYMES
as the enzyme itself or it’s expressed from a yeast to find the right combination that breaks down that fiber matrix,” he says.
Moser explains that Novozymes worked with the California Air ResourcMoser es Board to deliver the right technology. “The way we help our customers is to understand what is required for CARB pathway approval by working with our customers, the engineering firm and the fiber analytics providers to understand what technology is needed,” he says. “Then, with the fiber analytics, we can show that our Fiberex solutions deliver up to 3 percent more ethanol qualifying as cellulosic gallons.”
Novozymes R&D conducts full-scale application testing to ensure that the enzymes perform as promised without disrupting the producer’s established production process. After the top enzyme solutions are
identified, they will run them through a gambit of application-relevant testing to ensure that it works in a variety of processes and conditions. “It’s not just one size fits,” says Moser. “We want to be sure that our products can work for all of our customers to really enable them to hit those low carbon fuel markets.” Osborne They approach understanding the plant holistically, learning their customer’s goals and pain points. “We have dedicated scientists who lead full-scale application testing, working in close collaboration with our customers,” Moser explains. “We generate commercially relevant
data that show our solutions can help our customers achieve their goals. It’s not just a tiny test tube, it’s a full-scale fermenter.”
Consistency and Carbon Reduction
CTE Global is an enzyme and yeast provider that develops products that help producers increase yield of both ethanol and DCO, improve production consistency and reach low-carbon markets, explains Pedro Peña, R&D director with CTE Global. He explains that enzymes allow producers to open the corn kernel and get to the protein, fiber, starch and fats, breaking up the matrix in a way that mechanical grinding cannot do. “When we’re looking at innovations, one of the biggest things is putting together enzyme blends that are going to push the boundary of yield, whether that’s oil or whether that’s ethanol,” Peña says.
There are three enzyme blends that CTE Global has been developing as part of its line of next-gen alpha amylase blends, each of which will include different blends of alpha amylase, thermostable protease and thermostable xylanase. The thermostable xylanase component increases oil yield by breaking up the fiber matrix, releasing oil and freeing up more starch to increase ethanol yield, Peña explains. Thermostable protease also seeks to improve oil yields but has the added benefit of providing a blend of amino acids to support yeast health. These enzymes allow producers to release more corn oil, target the corn fiber and improve ethanol yield, all within liquefaction due to their ability to handle high temperatures. “In essence, it’s the combination of those three different enzyme activities coming together in a family of alpha blends that we feel is going to give us and our customers an ability to push yield to a new boundary than we had before,” he says.
The thermostability—ability to function in high temperatures—of these enzymes allows producers to “do more with less” and get better results utilizing the high temperatures of liquefaction, Peña explains. Specifically, the alpha amylase benefits the producer by getting more starch into the solution instead of going into the distillers grains. Thermostability allows the protease to open the corn matrix at a higher temperature, increasing the efficiency of the enPeña zyme, releasing more oil from the kernel and generating amino acids and peptides to improve yeast nutrition. The xylanase provides similar benefits, breaking down the kernel’s fiber matrix effectively at high temperatures.
Another innovation CTE Global has been pursuing is the use of cellulases and hemicellulases to turn corn fiber into low-carbon cellulosic ethanol. “Giving our customers an opportunity to tap into the low-carbon markets has been awesome, has been a lot of fun, and something we’re really passionate about,” Peña says. Although implementing these products necessitates operational shifts, he explains that the CTE Global team is committed to helping producers optimize operations to maintain conventional output while producing the most cellulosic ethanol possible, as producers take advantage of new opportunities in the low-carbon fuel sector. “I think as an industry we have an opportunity to play a big role in decarbonizing liquid fuels, and that is a huge opportunity. I think our industry is rising up to the challenge,” he says. “To us, it was a no-brainer to participate and do everything we can to make this into a reality,” he says.
Tailoring solutions to fit every customer is key to CTE Global’s customer relations. Peña explains that understanding the unique goals and situations of each customer is key to CTE’s process. Before implementing a product at a plant, CTE Global will typically do a trial scope at the facility to understand their process, needs, challenges and goals, in order to match them with the best product for their situation. “We execute a suite of analyses to look deeply into the processes, so we understand where the opportunities lie. Based on customer needs and capabilities and our Technology Center findings we're able to come out to the market with a new product that answers the bell,” Peña says.
Continuous Innovation
Qureshi
BASF, another leading supplier of enzymes for the ethanol industry, recently launched its Spartec brand, under which all of its bioenergy products are found, including the company’s latest innovative alpha amylase, Spartec AMY 110. Brian Hoskins, product manager for bioenergy at BASF, explains that the Spartec brand was developed from a combination of the word “Sparta,” implying courage, strength and discipline, and the word “tech” or “technology,” representing innovation and product performance.
Spartec AMY 110 is used in liquefaction to hydrolyze starch, explains Asfia Qureshi, BASF’s head of applications, innovation and quality control for bioenergy. The amylase reduces viscosity, enabling plants to have higher run rates, increased ethanol yields and increased corn oil recovery. Qureshi explains that Spartec AMY 110 also makes a substantial sustainability contribution in the value chain by increasing yields and production efficiency. “The lower viscosity is very important from a processing standpoint. It eases manufacturing by improving the flowability of the slurry. This places less burden on equipment and ultimately results in better economics overall,” Hoskins says.
In recent years, BASF has seen a shift in customer goals and priorities, Hoskins explains. With high corn oil prices and a greater focus on carbon reduction, ethanol producers are placing more emphasis on DCO yield and lowering CI scores. “We do also see some plants prioritizing protein. They can separate that and get higher value for it if it is in a higher concentration or a higher purity than just selling it as DDGS—which would be what is left over,” Hoskins says. “These coproducts have become increasingly important.”

PLANT UPTIME IS IMPORTANT TO EVERYONE
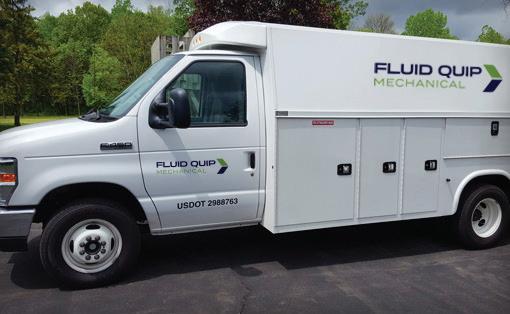
TECH TALK: Novozymes scientists discuss enzyme and yeast manufacturing testing protocols, an essential component of the company's new product research process.
PHOTO: NOVOZYMES
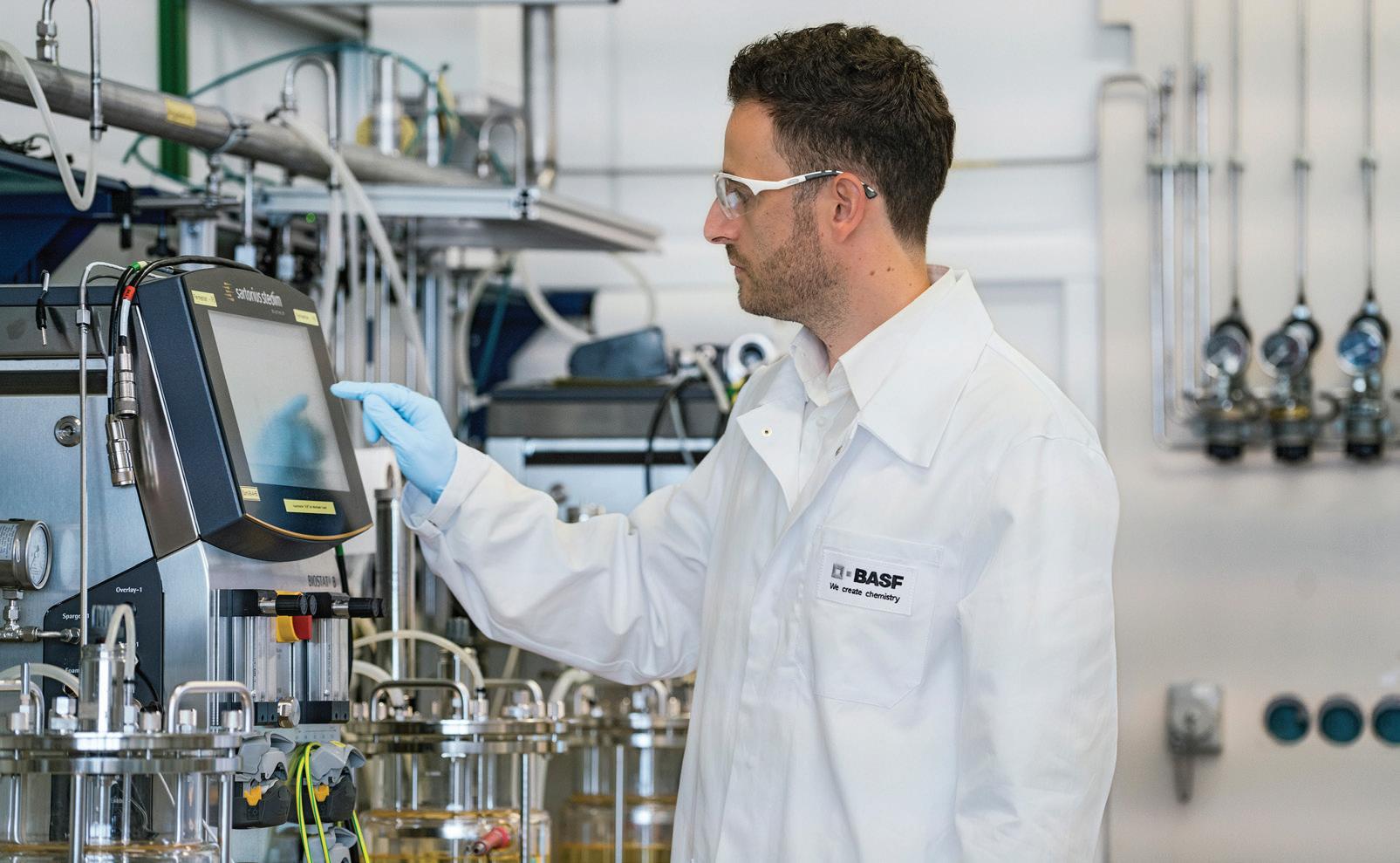
PUT TO THE TEST: A BASF technician checks on a pilot fermentation related to new biotechnological processes relying on advanced enzymes. Our full service team of experts have 20 years of ethanol plant maintenance reliability and uptime history. 24/7 support and ready access to a full inventory and all Fluid Quip equipment parts, ensures that you maintain your plant’s uptime status.
• OEM Parts Warehouse • $1 million+ on-hand inventory • Fully stocked trucks • Overnight/hot shot shipping
PARTS
PHOTO: BASF
One of BASF’s products helping producers capture more value from coproducts is Spartec CEL 100, a cellulase enzyme launched a few years ago that the company says helps increase oil production while reducing residual starch in DDGS. Qureshi explains that cellulases can also generate ethanol from corn kernel fiber. “We’re always looking at ways of working with biorefineries to develop sustainable solutions. Whether it’s improved feed products, alternative chemical pathways, biobased chemistries, these are all areas of interest for BASF,” she says.
As ethanol producers shift towards a biorefinery model that prioritizes coproducts such as corn oil, DDGs and protein alongside their ethanol, the enzyme industry is keeping in step with producers’ needs as each vendor innovates to develop the products that will help producers thrive.
Author: Katie Schroeder Contact: katie.schroeder@bbiinternational.com
EQUIPMENT SERVICE
• Factory Trained & Certified • MSC™ Systems • SGT™ Grind Systems • FBP™ Fiber By-Pass
Systems • MZSA™ Screens • Paddle Screens • Grind Mills • Centrifuges
