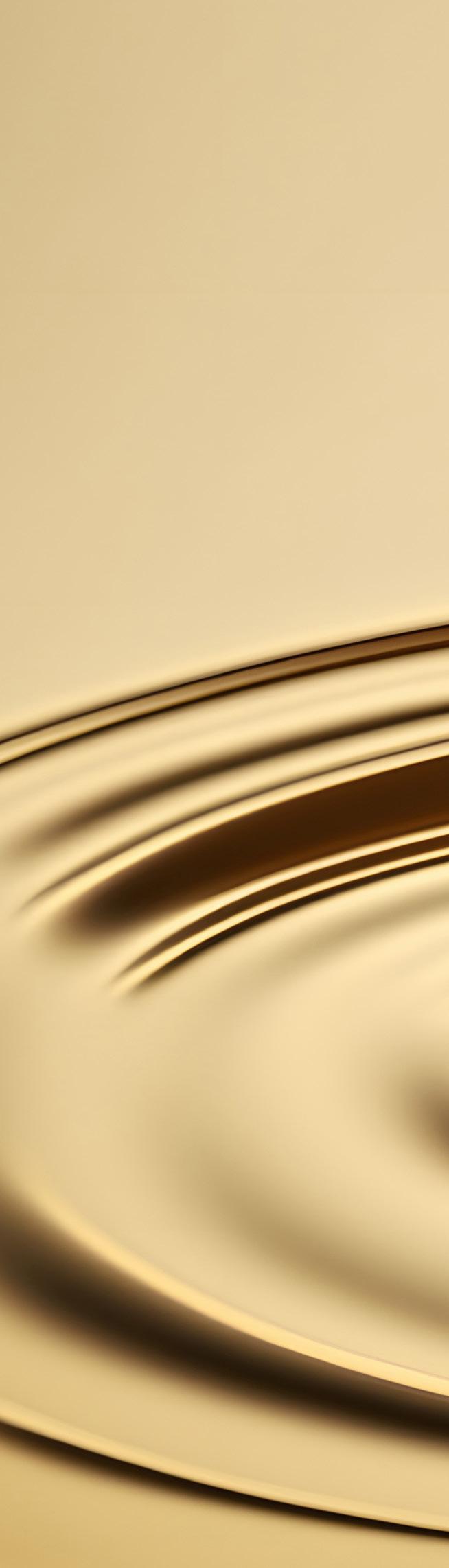
7 minute read
Getting the Drop On Purification
The rise of renewable diesel production—and what’s coming with SAF—is elevating demand for distillers corn oil. New technologies could push DCO values even further.
By Katie Schroeder
Technologies and products designed to maximize distillers corn oil (DCO) yield continue to capture the interest of ethanol producers as unprecedented demand for the coproduct continues to create sustained high value. Now, on the heels of last year’s passage of the Inflation Reduction Act amid a flood of sustainable aviation fuel project announcements and mounting renewable diesel volume growth, there is not only a heightened focus on producing more DCO, but doing so with fine-tuned purification technologies that yield RD/SAFready product that’s on-spec for upstream biorefining. This month, experts from ICM Inc. and Visionary Fiber Technologies speak with Ethanol Producer Magazine about DCO purification in the context of meeting customer expectations in the lucrative, high-growth RD/SAF market.
Scott Kohl, chief technology officer with Visionary Fiber Technologies of
Lockhart, Texas, explains that VFT is working with ICM to bring its microfluidic reactor, or fiber reactor, to the ethanol industry. The patented DCO refinement technology is a continuous flow process designed to extract significantly more impurities than traditional separation methods, resulting in a clean DCO that can be sold directly to renewable diesel refineries, bypassing or easing pretreatment at their site. The reactor features a small footprint, skid-mounted design. VFT believes the technology is well positioned for where the DCO market is headed.
The renewable diesel market is growing significantly, Kohl explains, and DCO is already considered to be a coveted feedstock for the industry. “DCO has an unusually low [CI] score, it’s renewable [and available] in large quantities,” he says. “If we clean it up, I see it as a natural fit into renewable diesel and sustainable aviation fuel in the next few years because demand is there.” According to projections based on data reported in Biodiesel Magazine in 2022 and 2023, Kohl believes that the renewable diesel market will need 5 billion gallons of vegetable oils by 2025 if current growth remains on track.

Chuck Gallop, director of innovation with ICM, explains that the CI score of DCO, as well as its moderate free fatty acids (FFA) content, make it an attractive feedstock for both renewable diesel and SAF. The ethanol coproduct’s CI score is roughly 20-25-points lower than refined bleached deodorized (RBD) soybean oil, explains Kohl. This score differential is key to lowering the CI score of the final product. Producers have seen value increases of 5 to 12 cents per pound for clean DCO, according to Gallop. In May, standard DCO (not purified to RD/SAF specs) was selling for 55 cents a pound in the Upper Midwest, so purification potentially gives producers a 10-20% premium.
The purity of incoming feedstock can be a challenge for renewable diesel produc- ers. “None of the triglycerides or feedstocks are equal in terms of quality,” Gallop says. “Also, the renewable diesel manufacturers, those plants aren’t standardized ... so each plant ... currently has its own oil quality standard we have to meet.”
Alcohol-based jet fuel is coming, but the most common variety of SAF production today utilizes plant and waste oils as feedstock; DCO may be among them if it can reach the necessary purity levels. Kohl explains that many renewable diesel plants are being set up to make RD and SAF simultaneously, although very few are currently doing so.
Feedstock Challenges
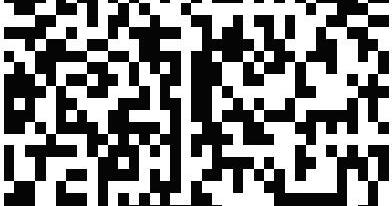
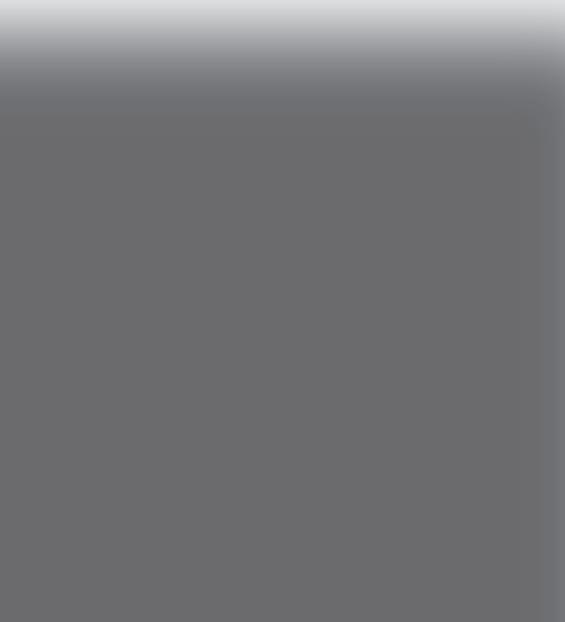
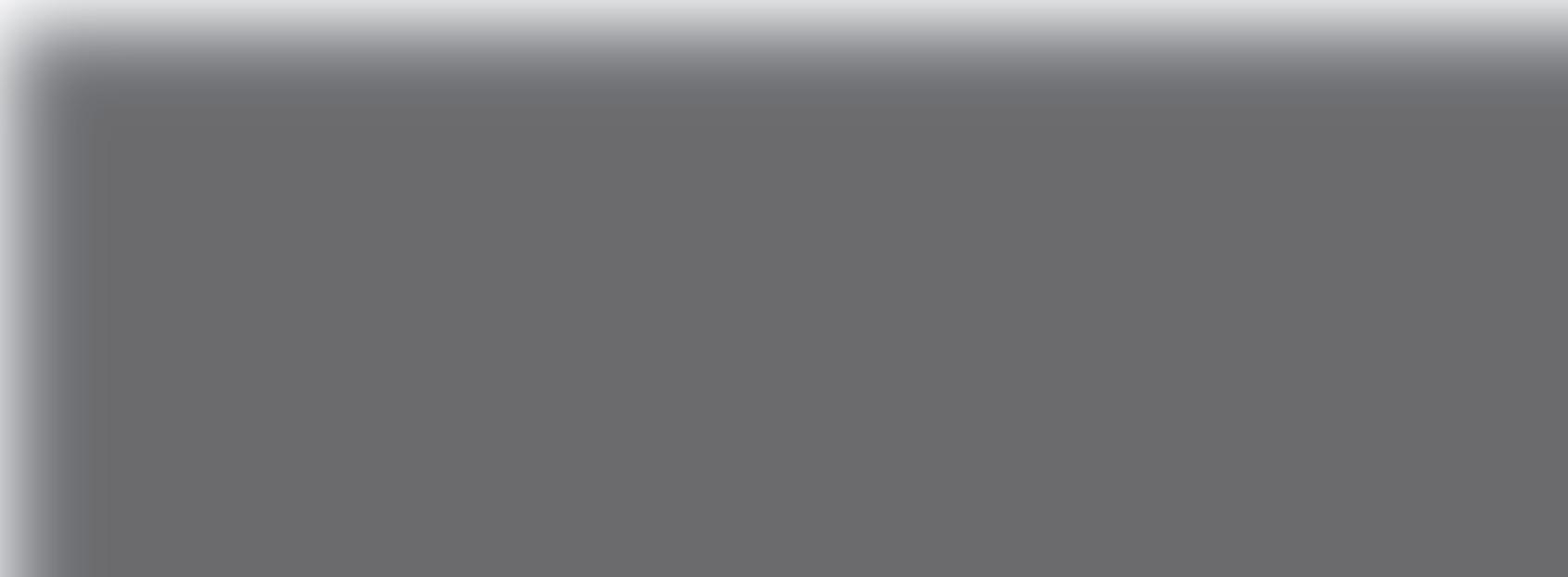
Most soybean oil used in making renewable diesel is food grade, cleaned using the RBD method. DCO also needs to be cleaned of contaminants before it can be used in a renewable diesel or SAF process.
“There are components inside that corn oil that could be considered a catalytic poison, meaning that these components could coat the catalyst and make it ineffective in the process,” says Gallop. Some of the contaminants include metals such as zinc, magnesium, potassium, sodium and calcium. Phosphorous, vanadium, silicone, acid and inorganic chlorides are other troublesome components that may be found in DCO before it is purified. Gallop explains that removal of inorganic chlorides is very important since the chemical can cause pitting in stainless steel. Some of these contaminants come from water used in the process, other contaminants such as iron may be introduced during transport to the renewable diesel plant. For example, the oil may be slightly acidic from the ethanol plant causing iron from the rail car to leach into the oil. FFA content in the DCO needs to be low as well.
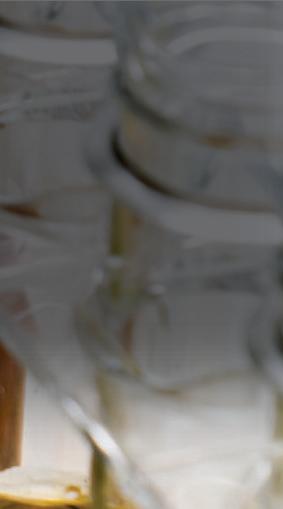
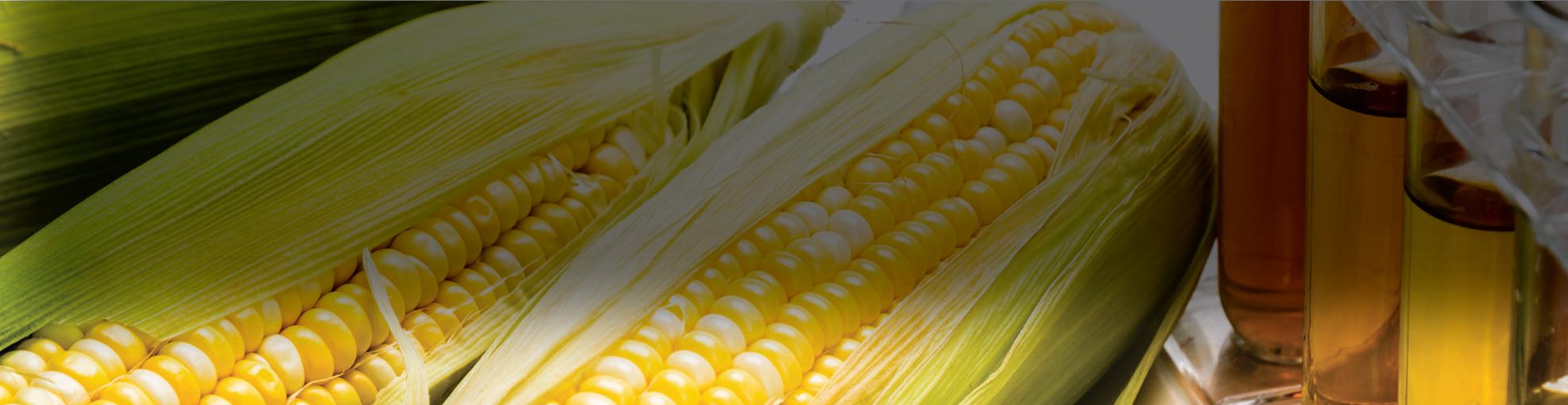
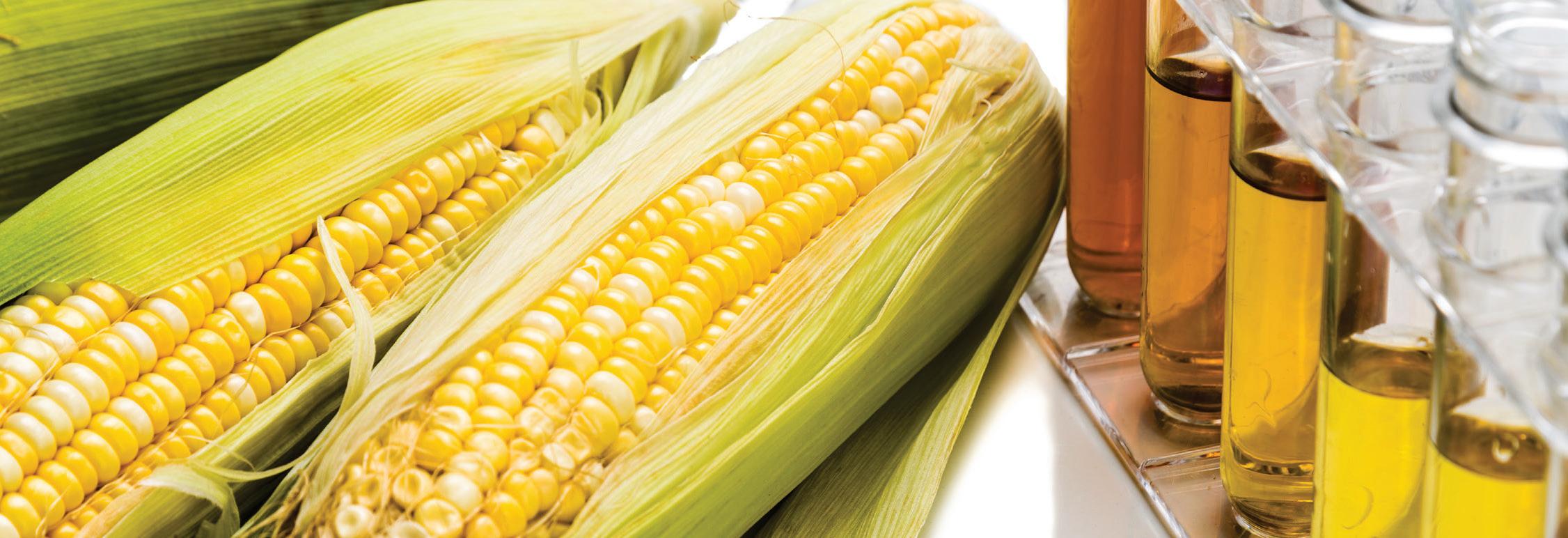
Removing these contaminants is paramount, and every renewable diesel or SAF plant has a pretreatment process used to get the oil up to spec. However, ICM’s team has designed a process using VFT’s microfluidic reactor that allows ethanol producers to clean the DCO to meet the renewable diesel producers’ purity standards onsite at the ethanol plant.
Purification Techniques
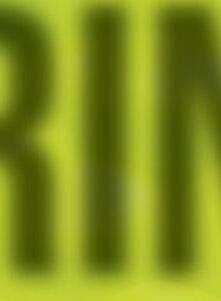
There are several purification techniques that have been used to clean vegetable oils over the years. Kohl outlines three different methods, the first of which uses solid adsorbents such as bleaching clay and silica to remove impurities. The adsorbents are used after a centrifuge and water are combined with some chemistry to degum the oil and get rid of the phosphorous.


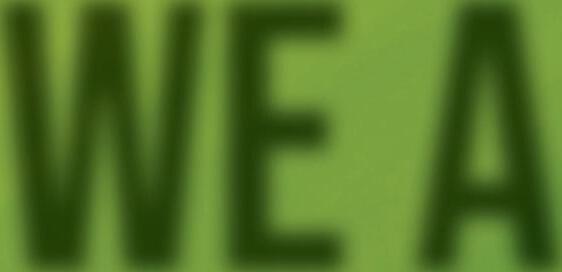

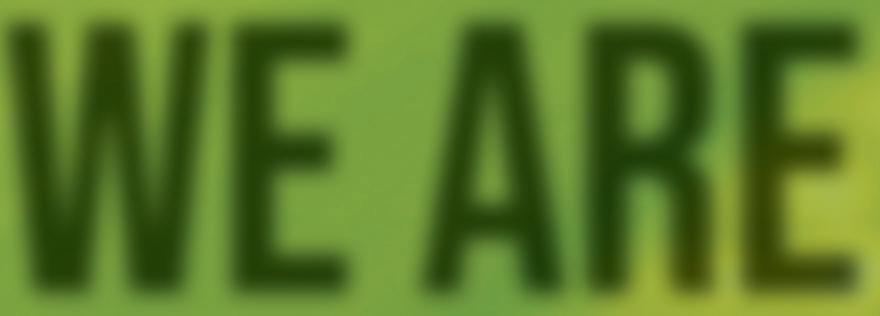
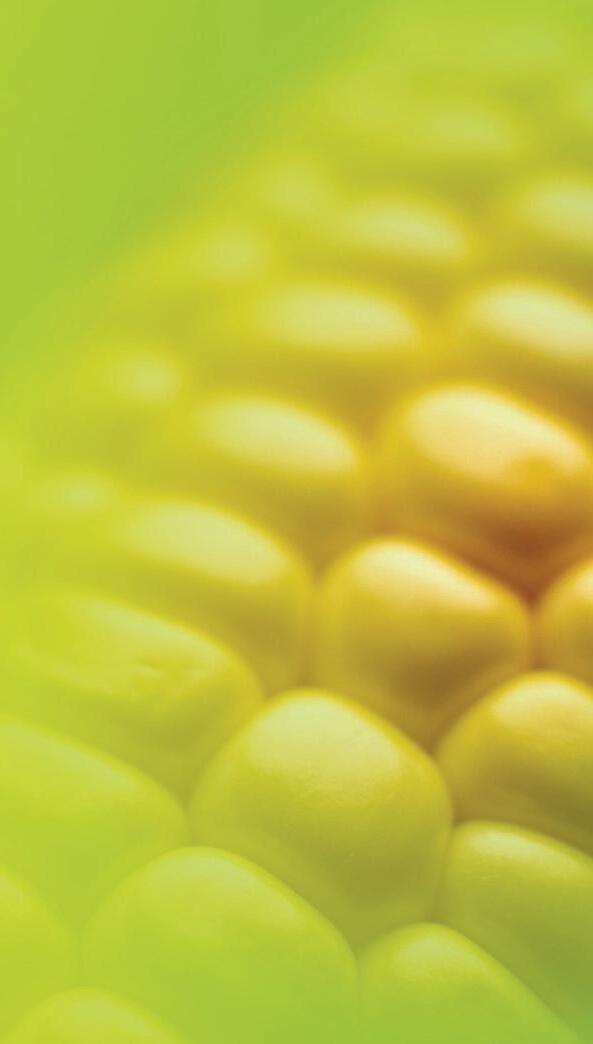
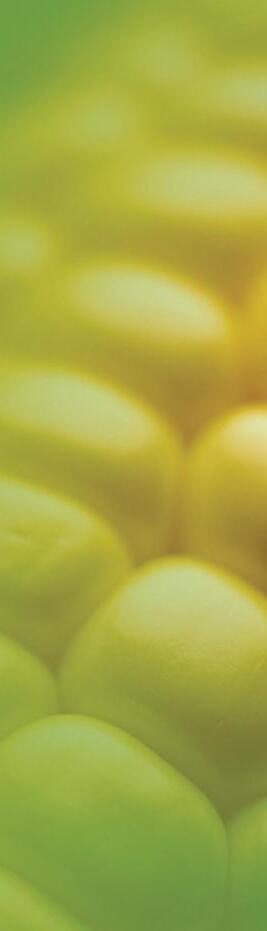
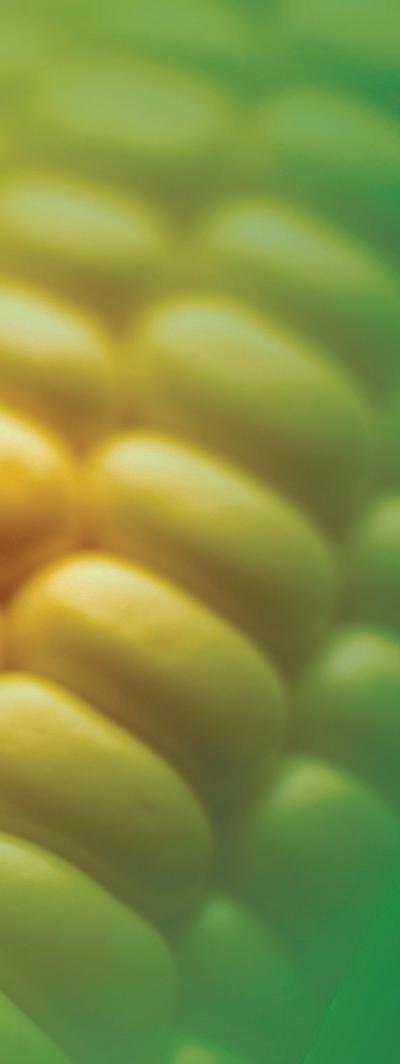
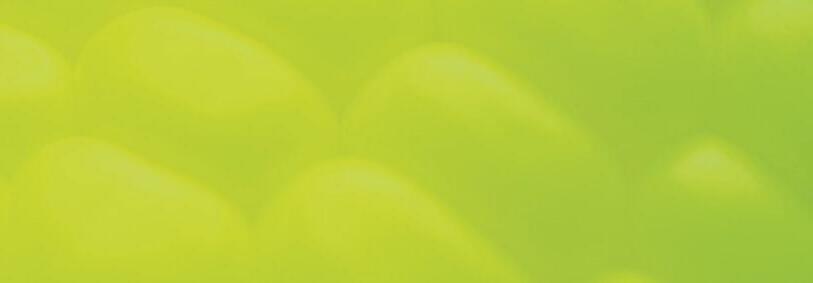
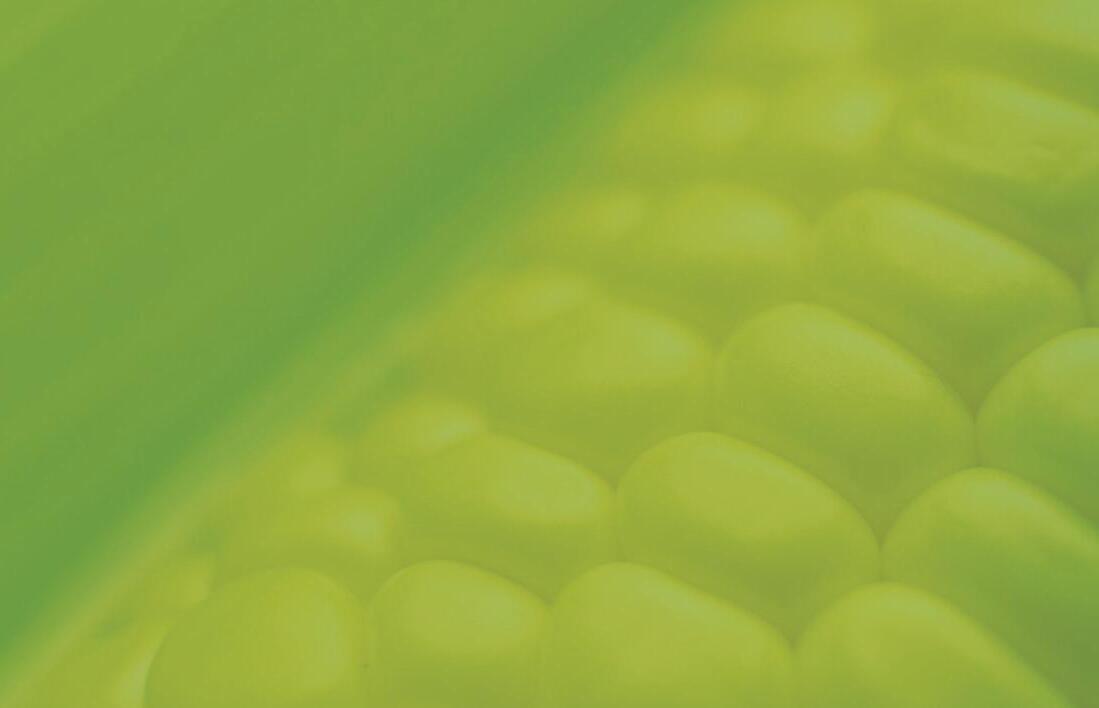
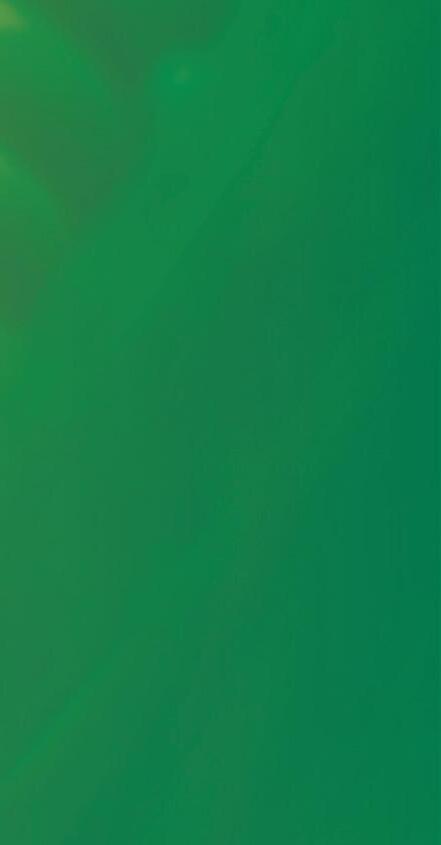
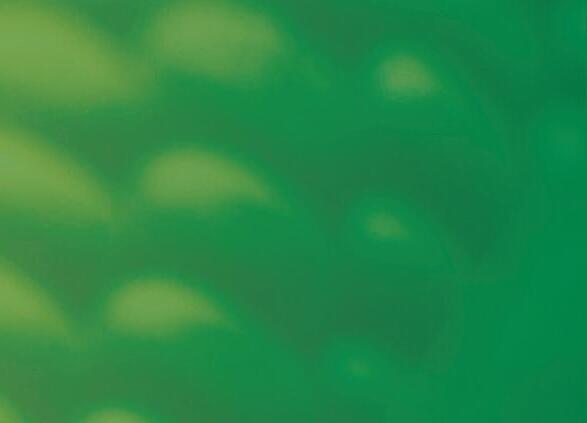
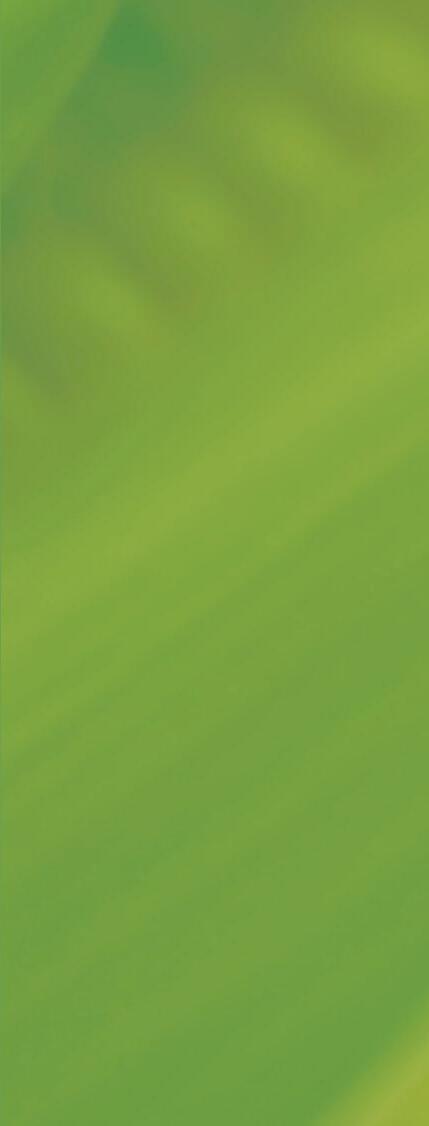
“The adsorbents are a powdery material that they use to adsorb these contaminants, and they want, they push the oil with the contaminants through the filters with this powdery material, and the material adsorbs the contaminants,” Kohl says. “And what comes out of there, all of the contaminants are removed and now that oil is clean enough to go to a diesel manufacturer or SAF.”
The downside to this process is that some of the oil is consumed by the adsor- bents and the bleaching clay can be difficult to dispose of because of its flammable properties.
A second method is the use of a centrifuge and water to dissolve the contaminants out of the oil. “And then you go to a centrifuge, and you centrifuge the water from the oil and ... dispose of the water that contains the contaminants. That separates it from the oil and now the oil should be clean enough to go into renewable diesel,”
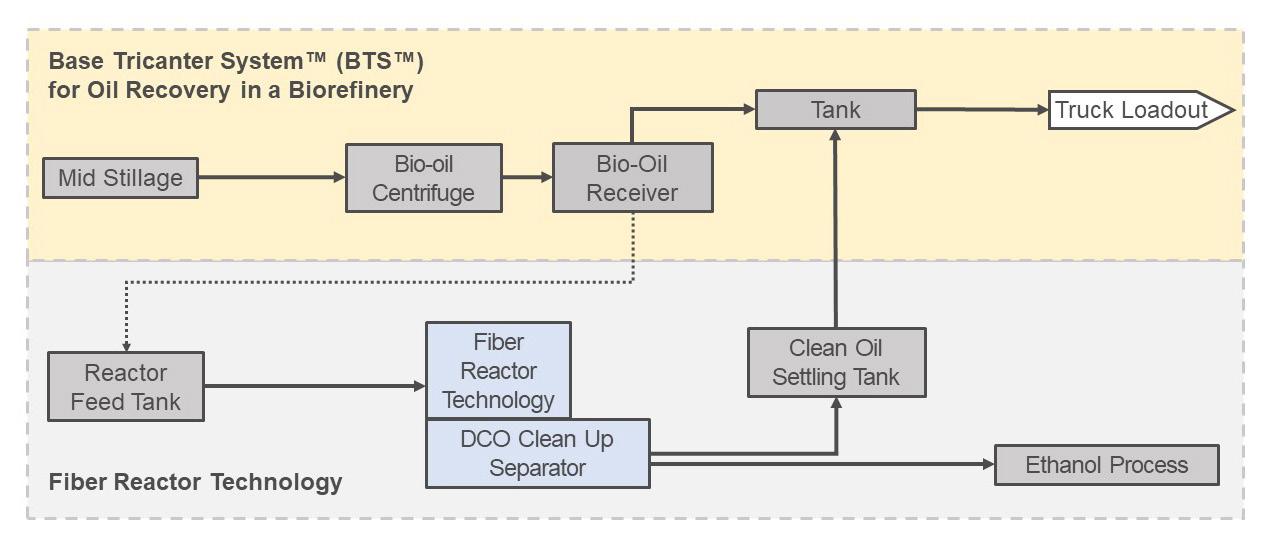
A third method is the use of a water wash, the method ICM uses with VFT’s microfluidic reactor to clean oil gently without creating an emulsion, which would bind the oil and water together.
Digging Into the Technology
ICM’s process is a deionized water wash that removes contaminants from the DCO without any added chemicals. Gallop explains that this technology is useful for both ethanol producers and renewable diesel producers. “Because the pollutants in there are water soluble, we use just deionized water to pull those out, however if we have harder-to-clean-up feedstocks, we can introduce chemistries to do that,” he says. “And that might be a pH adjustment, it might be a scavenger ... or a surfactant of some sort, but those things can be easily introduced to our process, if we’re looking to other components from the oil or process other feedstocks such as tallow, soybean oil or the like.”
The development of the microfluidic reactor, originally developed for the biodiesel industry, started back in 2018-2019 and was converted for use in the renewable diesel sphere a few years later, Kohl explains. In 2021, ICM signed an agreement with VFT to be the exclusive distributor and EPC contractor for the technology in the ethanol space.
The components of the process include a static microfluidic reactor and static liquid/liquid separator. The reactor is a vertical column filled with many fine stainlesssteel fibers, which efficiently mix the water and oil as they are pumped through the reactor. As they mix, the water captures the various water-soluble metals and contaminants. The only moving parts in the process are pumps and level or flow control valves, Gallop explains. After the existing corn oil recovery system takes the concentrated stillage off of the evaporators and through an oil recovery centrifuge, the oil is recovered from the oil receiver tank and goes into the feed tank at the start of the purification process.
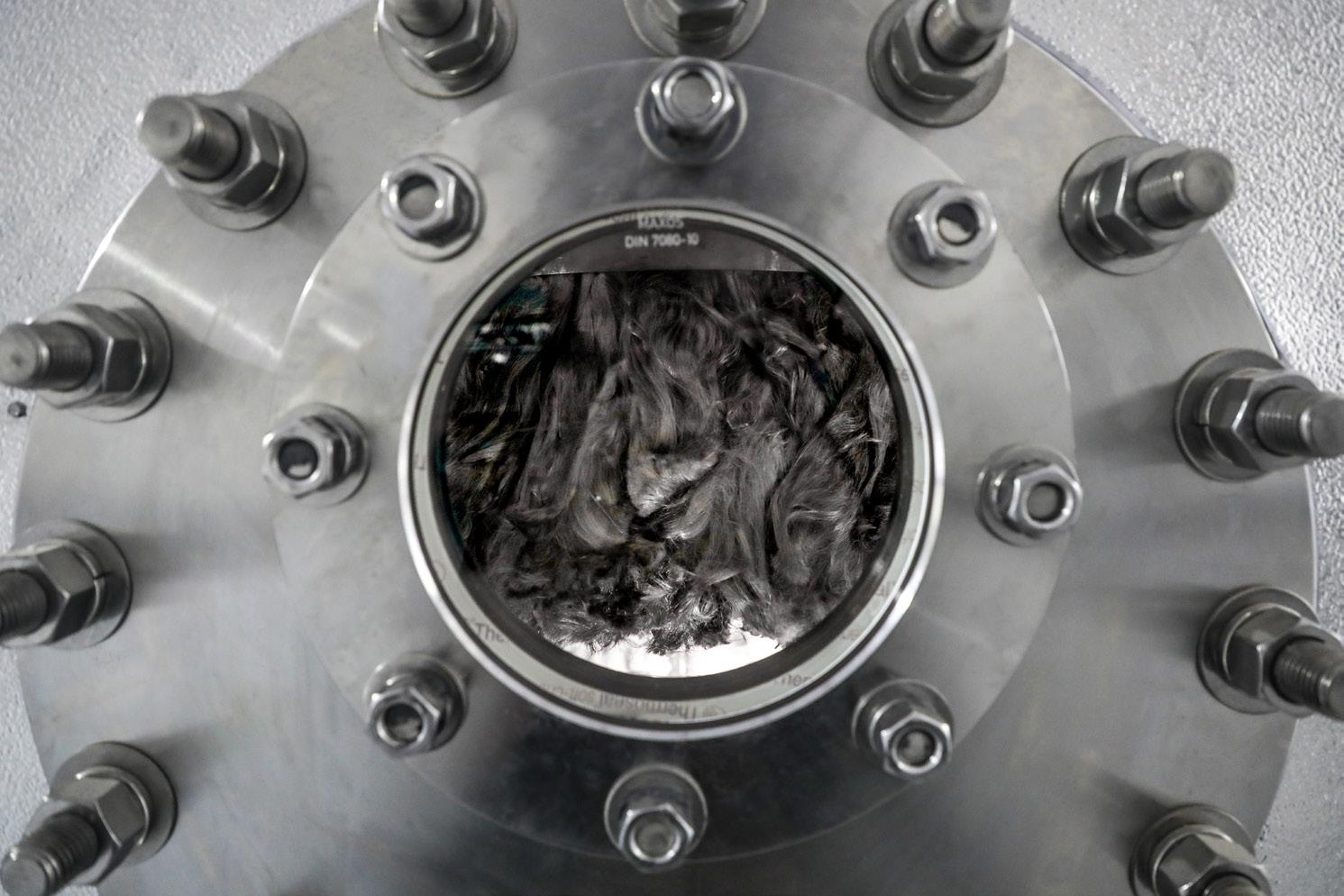
“[The feed tank] is just a holding tank to make sure we have enough volume before our reactor to ensure constant feed rate,” Gallop says. “We might do some temperature adjustment here as well. So, then we come into the top of our reactor, the oil [and] the solvent pass down through the reactor and into a separating tank where the oil will float to the surface and then be sent right back to the storage tanks. The aqueous solvent then settles out on the bottom and comes out of that separating tank and is recycled right back into the ethanol process.”
Because of how the system is designed, it integrates into the ethanol process most effectively, due to two factors that Gallop describes. First, all the water used to clean the oil can be cycled back through the ethanol process and does not need to be dealt with as wastewater. “You basically have eliminated a wastewater treatment process and that makes it highly attractive at a very low operating cost for an ethanol plant to get that done,” Kohl explains. Second, any neutral oil taken by the solvent will also be recycled back through the system and extracted when it comes back through, so none is lost. “It’s fully integrated into the ethanol process,” he says.
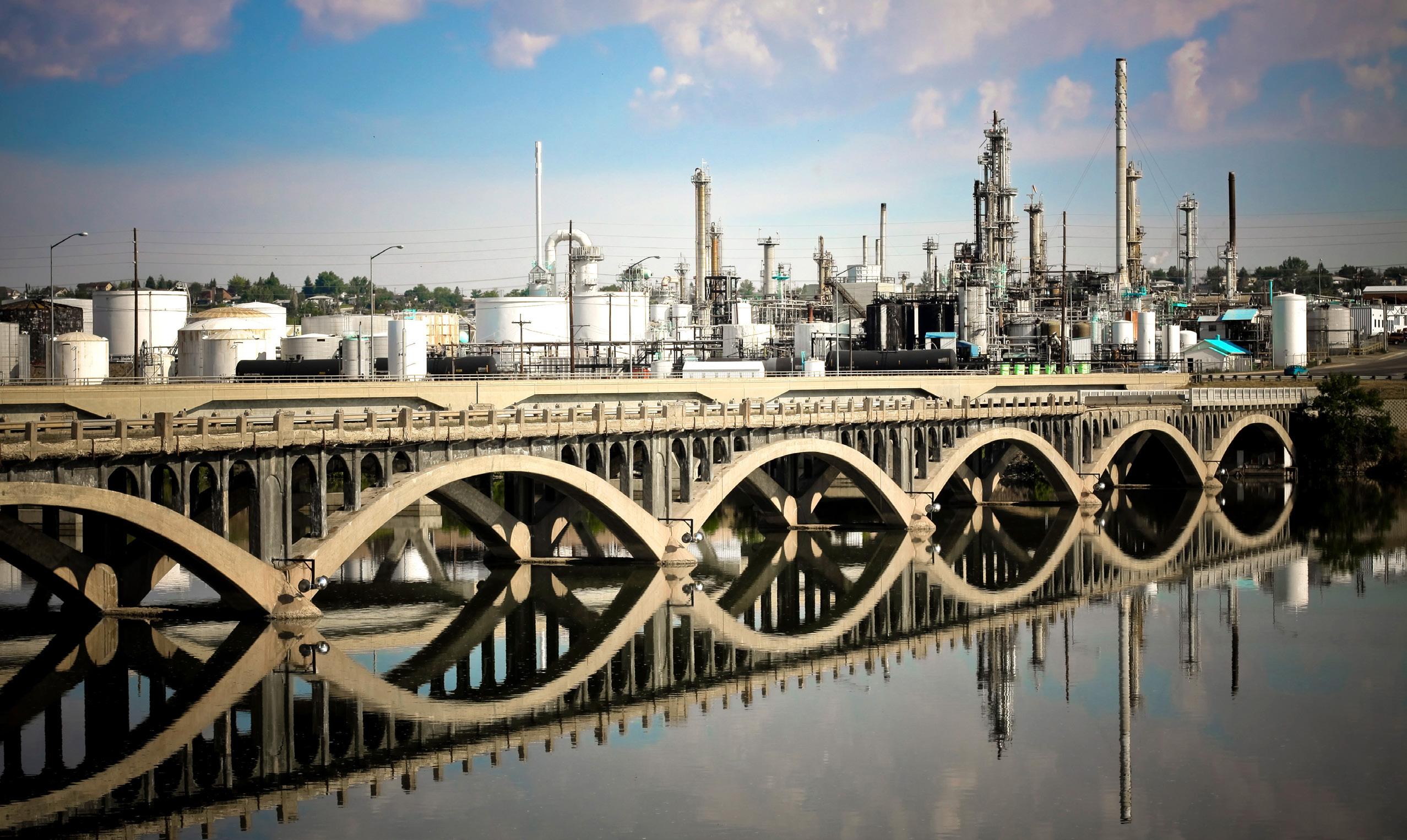
In plant trials, the technology was able to bring the phosphorous content of a producer’s DCO from 2 ppm down to 0.4 ppm, well below the renewable diesel producer’s threshold of 2 ppm. “It’s really important not to run right at the spec because everybody uses different third-party analytical labs to measure the oil quality, and the labs aren’t always spot on, meaning the results can vary,” Gallop says. “We don’t want to have rejected oil quality just because we’re right on the acceptable limit, so we want to overachieve oil quality.”
The inorganic chloride levels were also reduced to 0.3 ppm and 1.26 ppm, well below the required level of 10 ppm, with only the process and use of the aqueous solvent.
Because of how the system is designed, it has “negligible” impact on the CI score of the DCO, according to Kohl. “The CI score that already exists with the DCO will almost be identical, there will be almost no change,” he says.
Purification technology gives producers a way to expand their tradition of magnifying the value of the corn kernel. Kohl explains that implementation of this technology is simply another way to add value to the ethanol producer’s operation. “Your business is adding value to the raw material you’re buying, and that’s what you’ve been doing, that’s the whole reason you exist,” he says. “Here’s another opportunity to add additional value to the products you make.”
Author: Katie Schroeder
Contact: katie.schroeder@bbiinternational.com