
2 minute read
PUT DECADES OF EXPERIENCE TO WORK IN YOUR FACILITY.
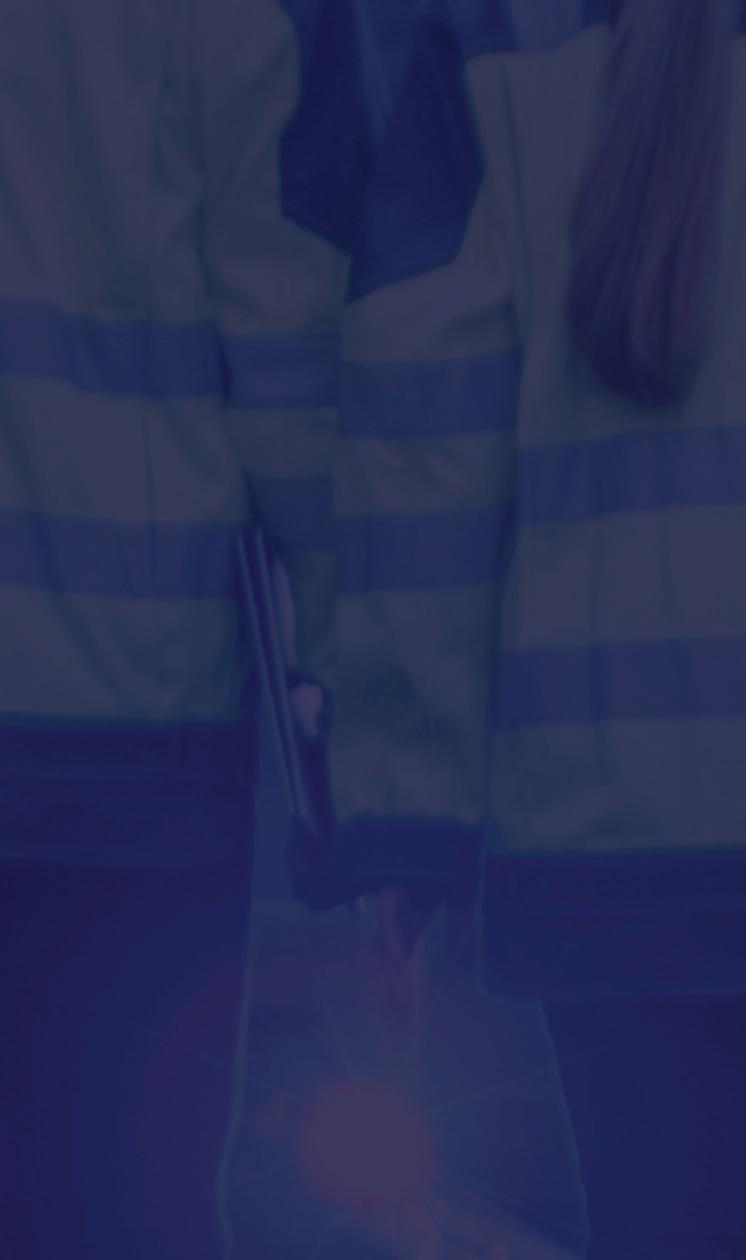

ing hydrogen production would be sold or sent to permanent storage, potentially generating tax incentives. Lastly, hydrogen fuel or designer options would be sold to customers.
The technology module is built off a system that relies on high-temperature thermals that create steam before converting that steam to hydrogen. Steam-methane reforming, the main method used today for producing hydrogen, typically relies on natural gas liquids—mainly methane—as a feedstock. Methane in the presence of steam at 3 to 25 bar pressure (1 bar equals 14.5 psi), along with a catalyst, produce hydrogen, carbon monoxide and a small amount of CO2. They call it the water-gas-shift reaction, according to the U.S. Department of Energy. In the final step of the reformation process, carbon dioxide and other impurities are removed from the stream, leaving pure hydrogen.
Feedstock gas for Proteum (in this case an ethanol beer cut) and low amounts of water are fed into the core technology platform where it first runs through standard auxiliary equipment before entering the proprietary steam non-methane reformer technology. The result is clean hydrogen fuel. Additional modular units can be added for CO2 separation, H2 separation, or synthetic natural gas.
If ethanol is used as the feedstock, it must be injected at 375 to 500 psig and be oxygenated. The base systems produce 19,000 kg/day. For utilities, the electrical needs are 480V three-phase wye, 60 Hz, less than 1.0 MVA. The water source amount can be a dilute-alcohol feed (e.g. 40 vol% ethanol) or fresh water at a rate of 10 gallons per minute. A 10 MB minimum connection is also required. The overall footprint of the base modular unit is roughly half an acre and they can be integrated with waste heat recovery systems.
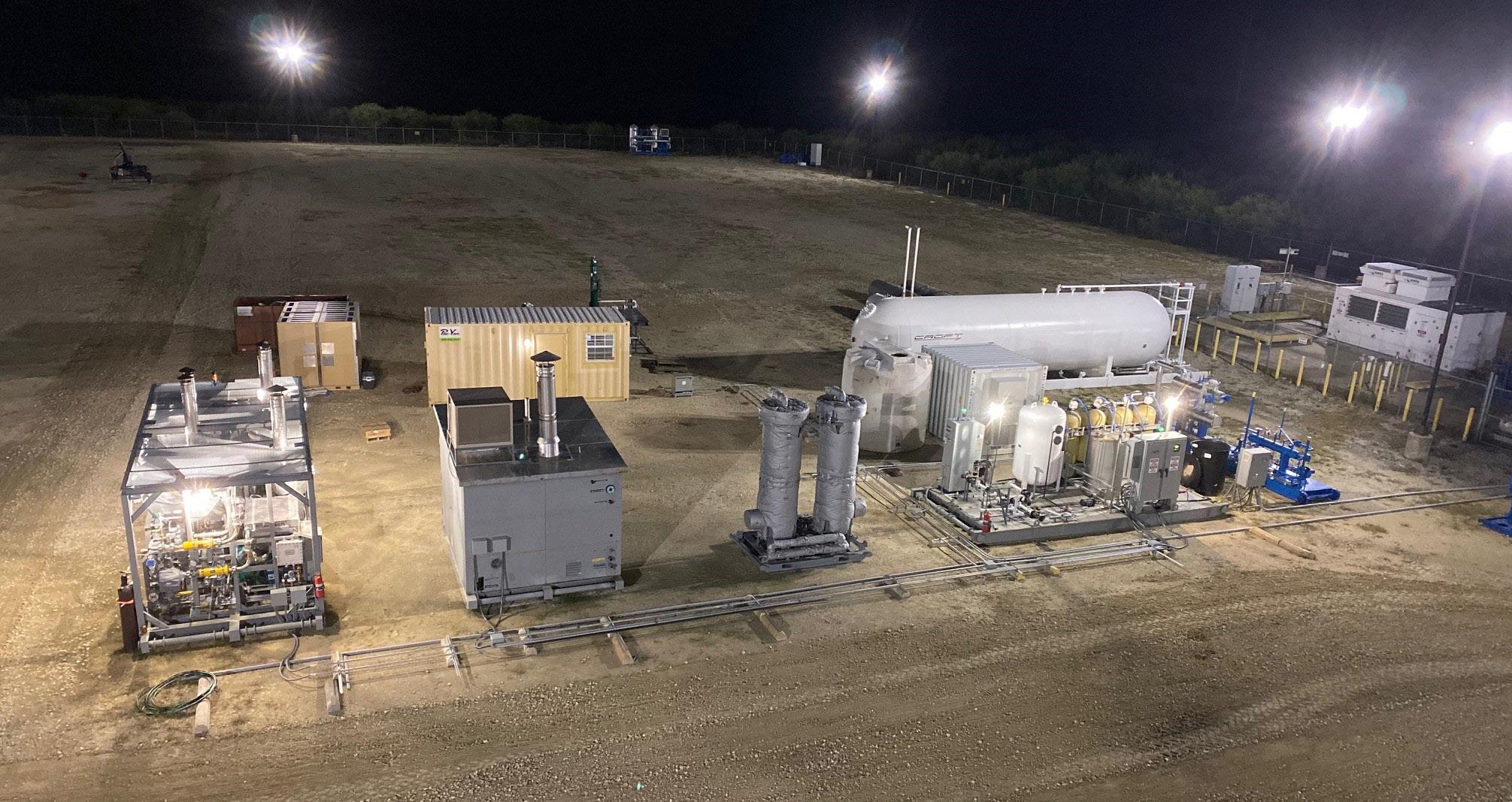
According to Tree, the Proteum business model relies on four things: feedstock, a hydrogen offtaker, a CCS project and land. With an ethanol partner providing the feedstock through a joint venture or through sale, Proteum already has offtakers ready for the hydrogen product. Working with an ethanol producer that is sequestering carbon, Proteum can send over roughly 500 tons of CO2 per day.
“We can also provide the ethanol producer with some waste heat and power to their facility,” he says.
More Than a Goal
Proteum is currently working on the buildout of a hydrogen production facility in California, according to Tree. But the team is also working to expand across the Midwest ethanol belt. Starting in 2014, the company had already racked up several important milestones. It all started as a technology proof of concept to better utilize flare gas produced during shale oil and gas production. A system was tested in the Bakken of North Dakota, along with shale plays in Texas. A commercial system was deployed in 2017, used by major exploration and production company Diamondback Energy in 2018 to help utilize flare gas; it received a statement of endorsement and technical qualification by global consulting and testing firm DNV GL in 2020; tested and proven for hydrogen production from NGLs in 2021; and turned fully commercial through term sheets in 2022.
Late last year, the company signed with Transitus Energy to produce hydrogen from hydrocarbons produced in the North Sea. The agreement included a letter of intent for opportunities in the U.K., Netherlands, Republic of Ireland and Norway to produce low-carbon hydrogen for European markets.


Now, Tree jokes that ethanol producers can get into the diesel business by producing clean hydrogen that could or will replace fossil-based diesel. He knows some aren’t sold on hydrogen or the idea of a new fuel type. But he also is quick to rattle off story after story of major trucking companies announcing moves into hydrogen fleet expansions. Or stories from California about diesel trucks being removed from the roads by 2035. And, to help illustrate the difference between electric heavy cargo trucks and hydrogen fueled alternatives, he points to weight and time. EVs are much heavier, and they also require much more time to recharge. A refill on a hydrogen-fueled truck takes about the same time as a fossil-based diesel option, he says, and that alone is attractive to OEMs looking at investing in hydrogen.
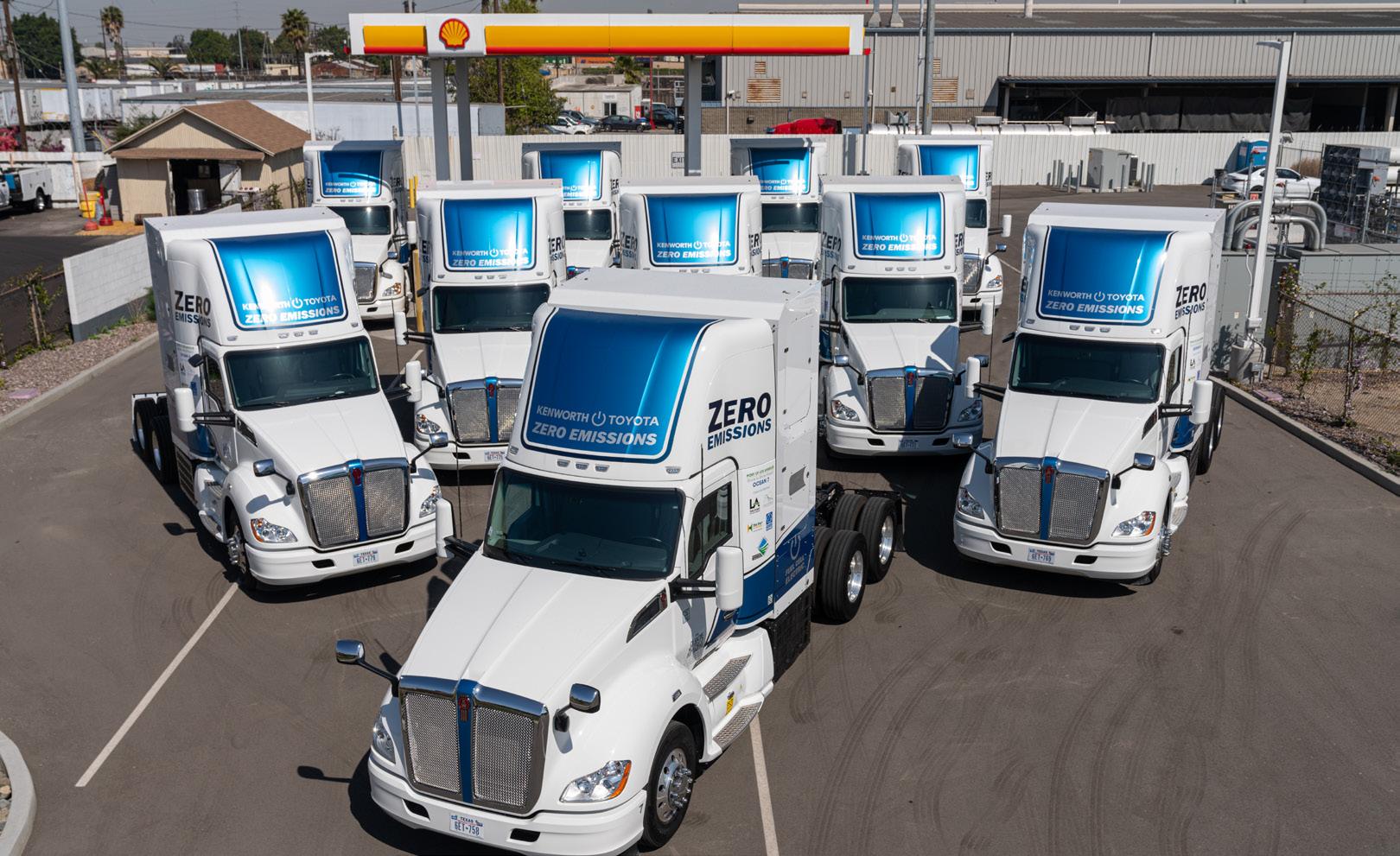
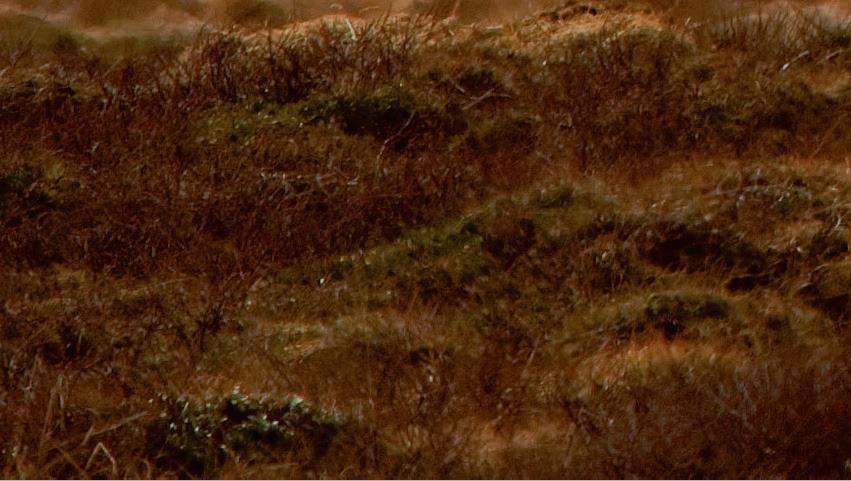