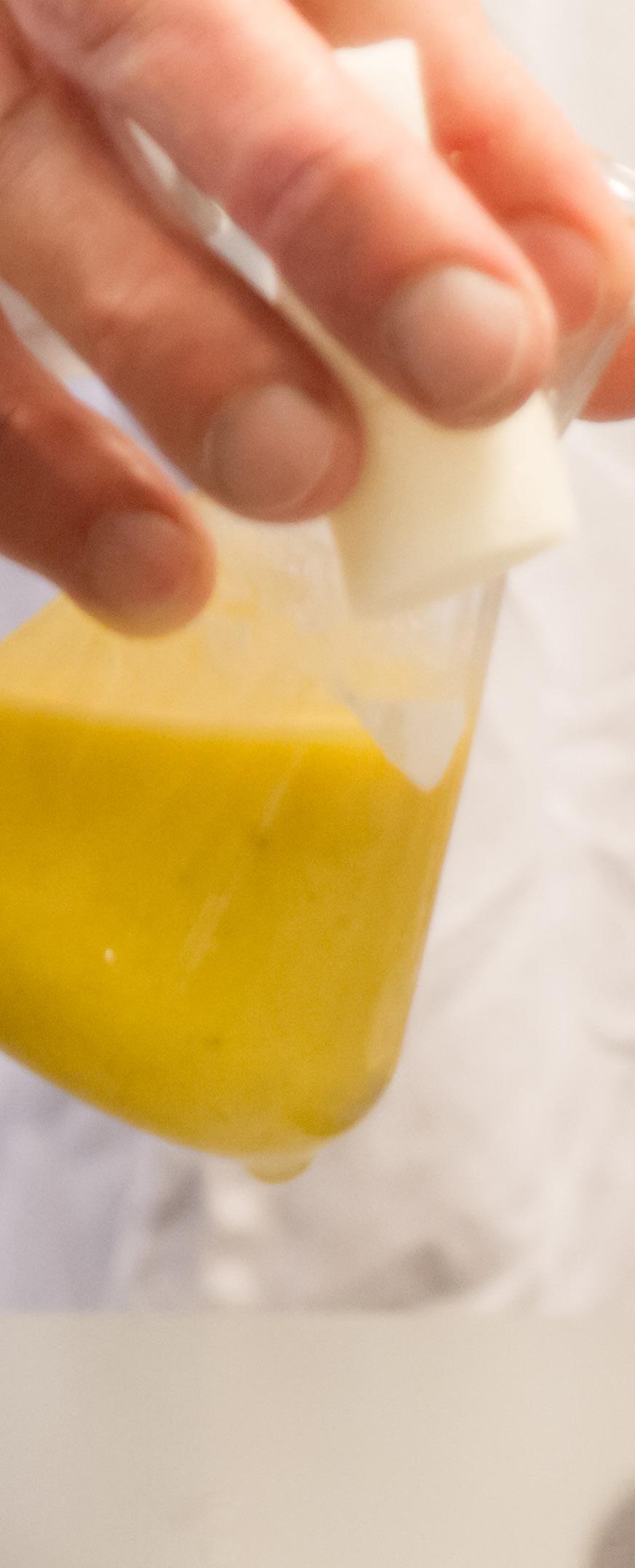
7 minute read
GRAIN Changers
IFF has established a next-gen ethanol modeling and services toolkit to go with its flexible portfolio of fermentation products.
By Luke Geiver
Is it the technical services team, or the yeast and enzyme products themselves, that have made IFF such an integral part of the ethanol industry’s ability to achieve greater success? While each producer working with IFF might simply say it’s both, we checked in with the company to be sure—to get the latest on its technical services team and how they’re moving the industry to a new level. IFF also shared updates on its advanced capabilities and products.
It Could Be the Tech Team
Griffin Ford, North America technical services leader for IFF, leads a roster of techs that has decades of combined ethanol production experience. “We have been in hundreds of plants,” Ford says, “and we have a lot of ethanol knowledge.”
Ford himself has spent more than 20 years in industrial fermentation working previously as an ethanol lab manager. His degree is in brewing and fermentation from Heriot-Watt University in Scotland. He’s fluent in all things ethanol and alcohol (he was a brewmaster before entering the industrial ethanol sector in 2008 and at one time was working to develop a specialty vinegar). Most of the current roster of tech experts working with Ford also come from the ethanol industry with a broad range of skills and backgrounds ranging from agriculture to engineering to food science.
Besides working to help producers find the best enzyme or yeast solution for their particular production needs, the team supports technical trials, trains ethanol staff, performs site visits, troubleshoots issues and, amongst other things, leverages artificial intelligence (AI) applications to help producers troubleshoot issues as well as choose the best products for optimum fermentation performance. Their work, Ford says, spans everything from the most basic to the most complex. “We take a very holistic approach to looking at the plants,” he says, “and we make sure we are using the right products at the right time.”
Onsite at the ethanol plant, Ford or members of his team can offer operational insight and evaluations. If a plant is having issues with a particular problem, the technical service team will help diagnose and solve it When a plant finds an infection, the team will perform a hygiene evaluation, including sampling and plating to pinpoint where the infection is. As Ford points out, the team has seen it all and is always thinking about ways to solve new issues. In addition to problem solving, the team visits plants throughout the year to perform custom workshops or training sessions on new products, processes or enzymes and yeast in general. They also host workshops and training sessions from the Applied Innovation Center, their state-of-the-art lab and testing facility in Cedar Rapids, Iowa.
The team tries to be an extension of every plant it works with. “One of the nice things with us is that we separate technical services from sales. We are really focused on optimizing the performance of our partners,” Ford explains.
Optimized Products and Tools by IFF
Although the IFF technical services team has years of experience between them, they are also leveraging and developing tools of the future. “We have moved into advanced analytics, machine learning, AI and predictive modeling with XCELIS® AI,” Ford says. They also have a great base of world-class tools already at their dispos- al. From yeasts to enzymes to accessories used in ethanol production, IFF has it. If it weren’t for the work being done by Ford and his team, it might be easy to say that it's the products that have made IFF such a staple in the industry.
For ethanol clients working with IFF, its development of predictive tools means that when it's time to make or just consider a change to a different IFF enzyme, yeast or yeast blend, Ford and his team can provide modeling.
“If a plant wanted to make a change, we could simulate that and see what that
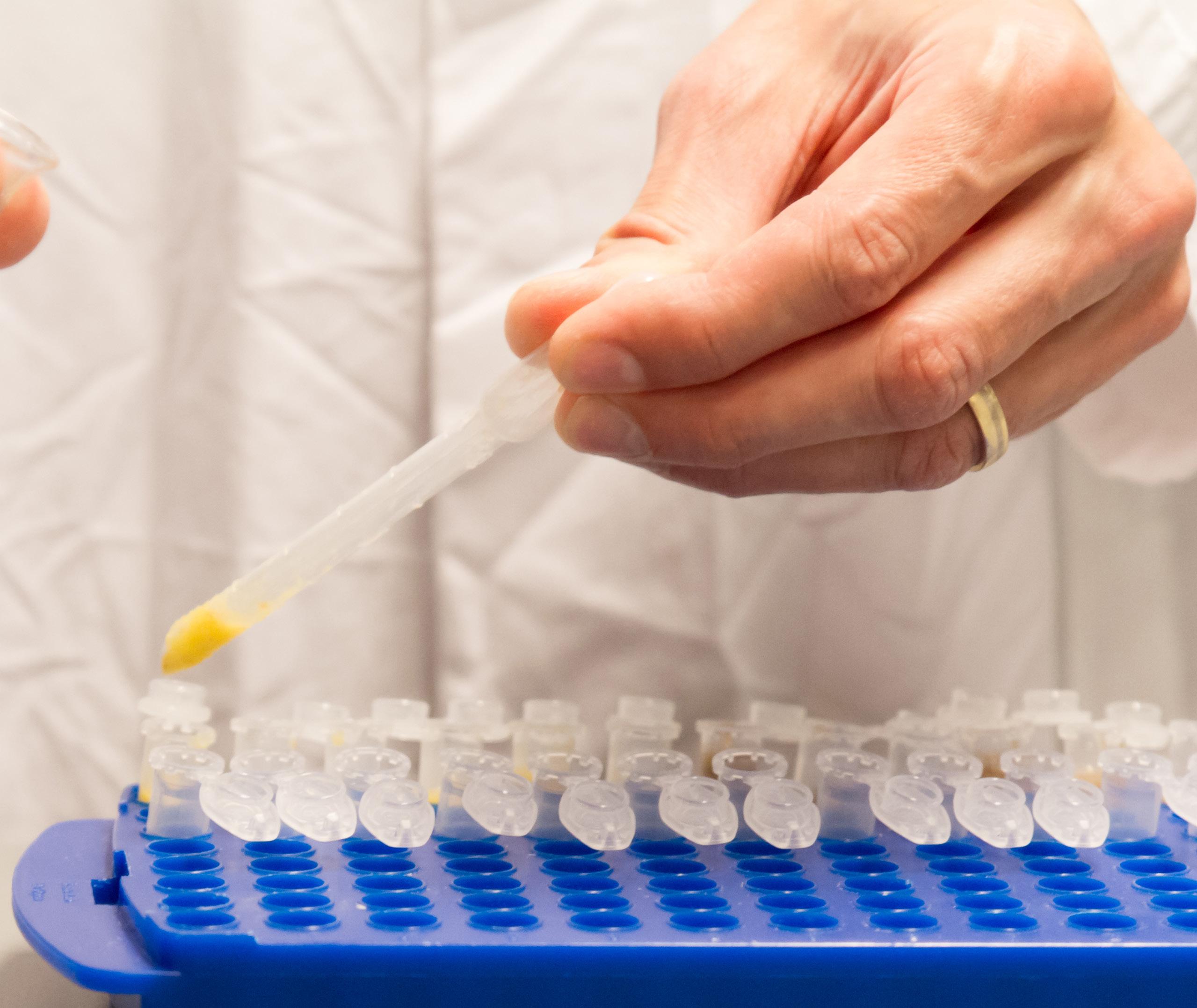
Production
would do to the plant,” he says. XCELIS can model various yeast strains, look at temperature settings, staging and other factors impacting fermentation.

IFF has been developing XCELIS to help producers realize the promise of AI. The platform provides data science services across a broad range of areas to deliver advanced insights from large datasets. IFF says XCELIS can reveal important patterns and insights in datasets that may not have otherwise been evident. Benefits include predictive monitoring to detect operational anomalies or achieving model-driven prescriptive decisions that result in improved process efficiency and higher yields.
Ford and his team specifically use data to help producers determine the best yeast or yeast blend for the desired outcome. While many producers have shifted to yeast strains enhanced by genetic modification to get higher yields and robustness, there have been tradeoffs, including considerations for nitrogen usage, antibiotic and GA inclusions, temperature ramping and solids control. IFF can use plant data to explore which yeast or yeast blend will work best given a plant's operating conditions.
Ford cites summer heat or planned shutdowns as an example of when a yeast strain choice becomes important. If a plant is approaching a shut-down, it may need a long-lasting yeast. If it's summer and the heat will be an issue with fermentation, a particular heat-tolerant strain could be used. In the past, when corn supply has been in question due to flooding along the Mississippi, producers have had to look at different yeast strains with reduced rates with longer fermentation times.
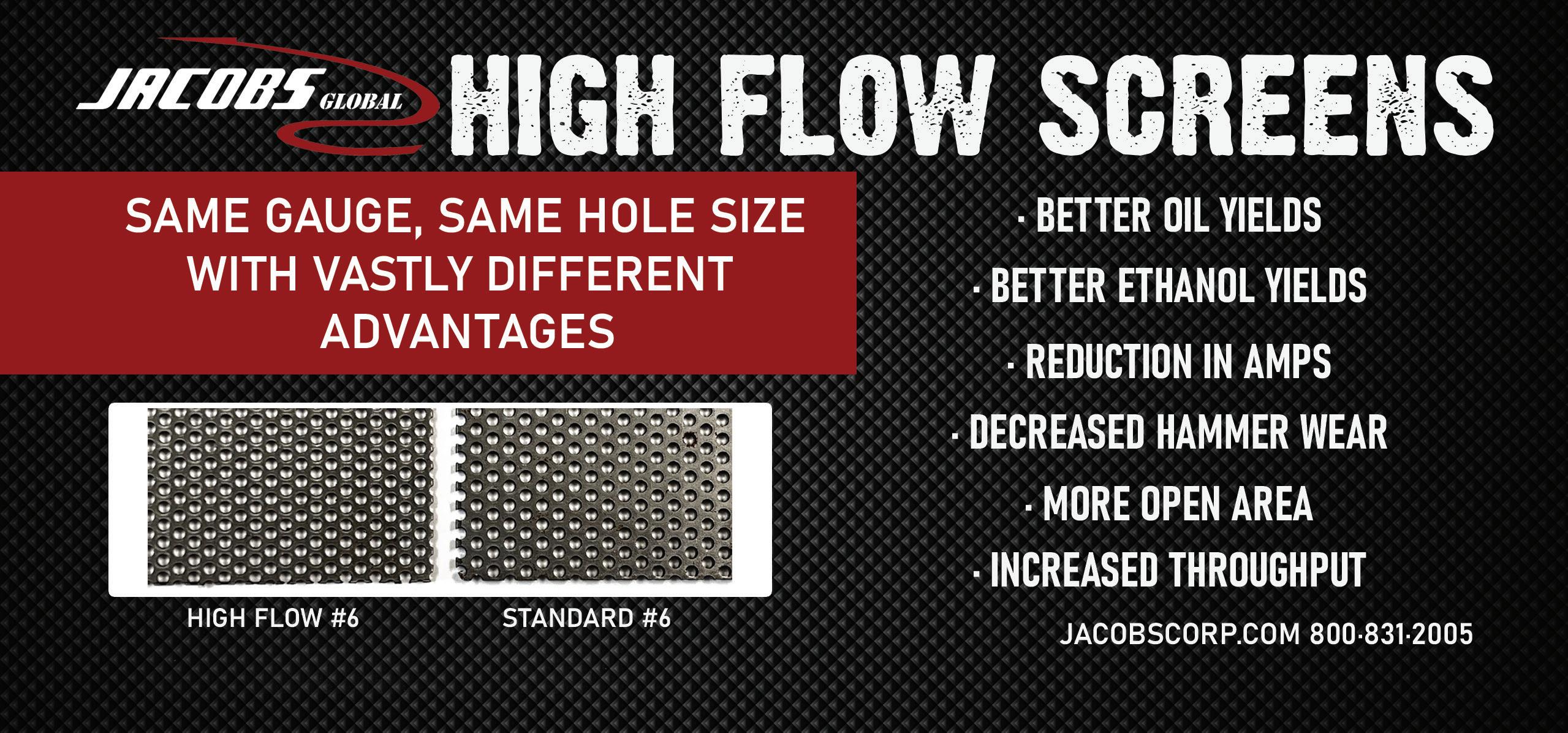
“Producers are always looking at higher yields but they are also looking for flexibility,” he says.
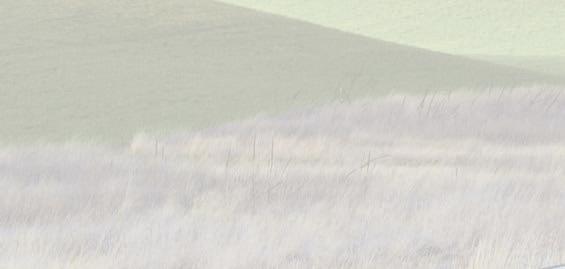
With IFF’s gemstone line of yeasts, producers can get flexible optionality and a consistent price across the board. IFF doesn’t charge different prices for different yeasts.

“The reason we have a collection and not just one is because we want the customer to be able to choose the yeast or yeast blend that is best for them,” Ford says.
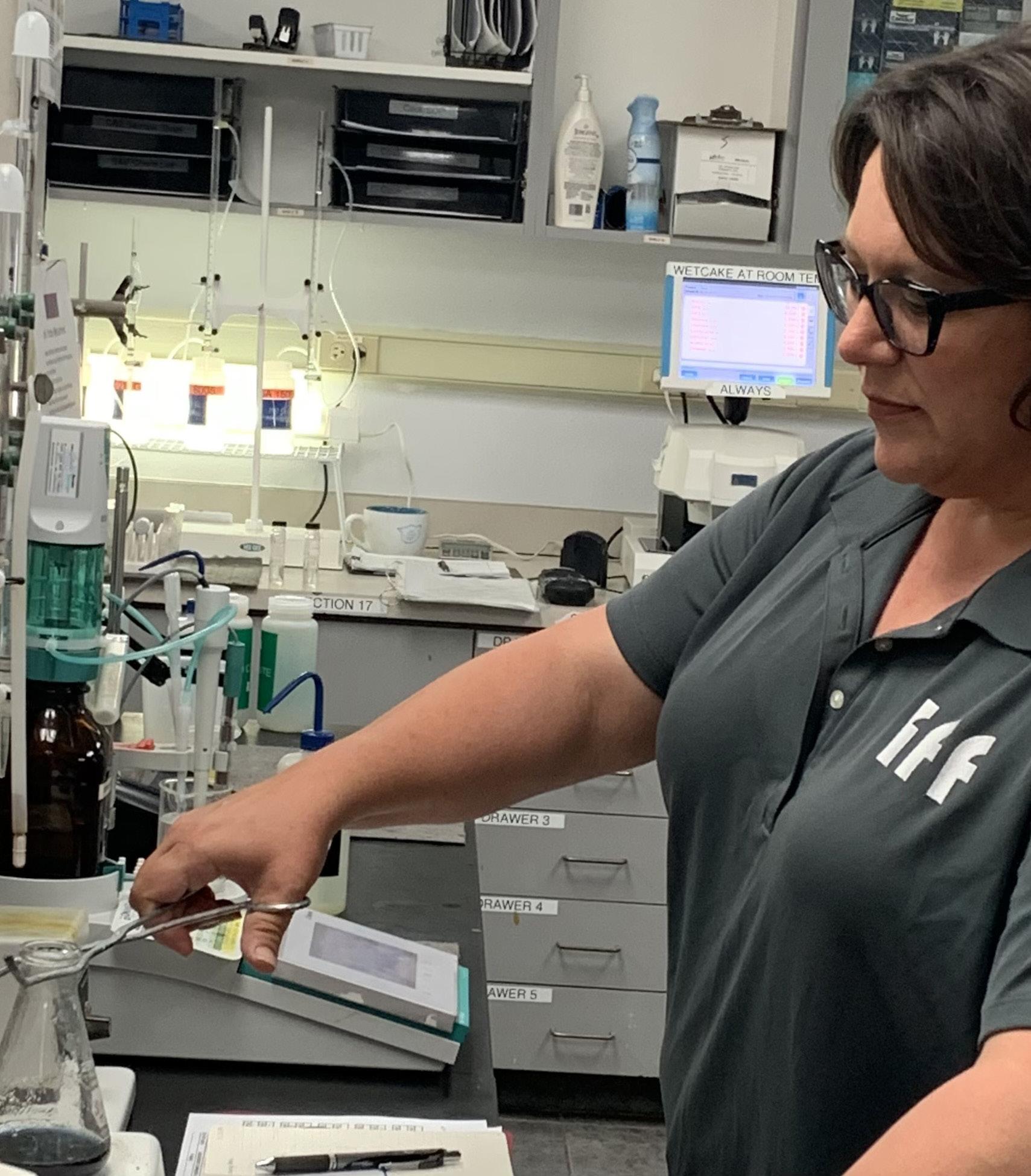

Producers can also get synergistic benefits from blending different yeast strains, all of which can be modeled using IFF technical services. And, as any longtime brewmaster would say, as Ford does, there is always an art to fermentation. That is where IFF’s years of experience adds to its capabilities, he says.
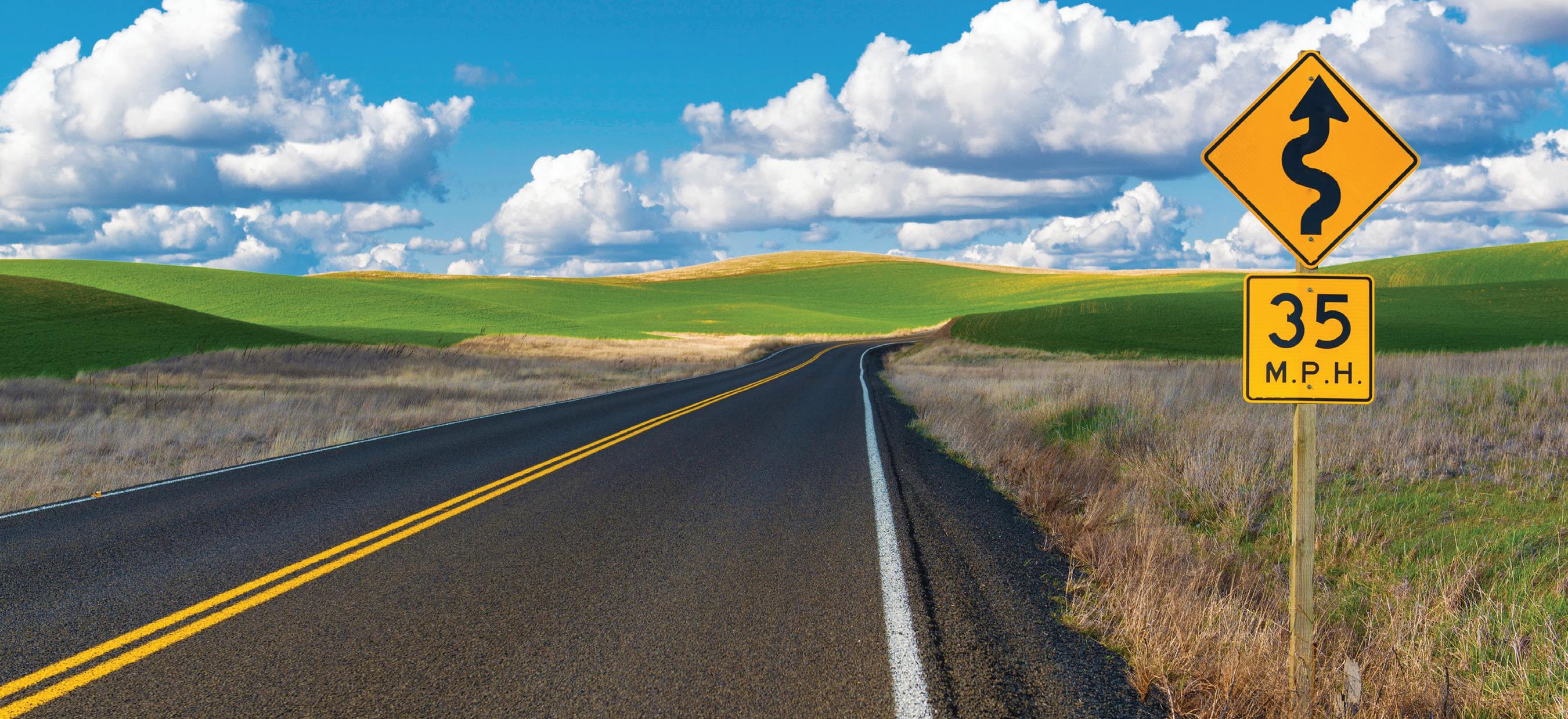
The IFF Yeast Collection
The SYNERXIA® Gemstone collection is backed by years of R&D and application work that constantly tests and improves the yeasts available from IFF. All of the yeast is available dry, so it can be mixed and matched depending on the desired outcome. There are three cornerstones to the trademarked Synerxia collection: SAPPHIRE (extreme robustness), RUBY (highest yield) and JADE (fastest).
The SAPPHIRE option delivers highyields finishing with ultra-low DP1, along with thermotolerance and infection robustness, expression of a glucoamylase with high affinity for residual starch and the ability to reduce glucoamylase doses by up to 80 percent. Ford says his team can go into much greater detail about each of their products, because, after all, he says, they love working with fermentation.

With its RUBY option, producers can get the highest yield of any yeast available, according to IFF. They can also reduce CO2 and glycerol. RUBY produces less acetic acid compared to other yeasts and enables up to 65 percent glucoamylase reduction.
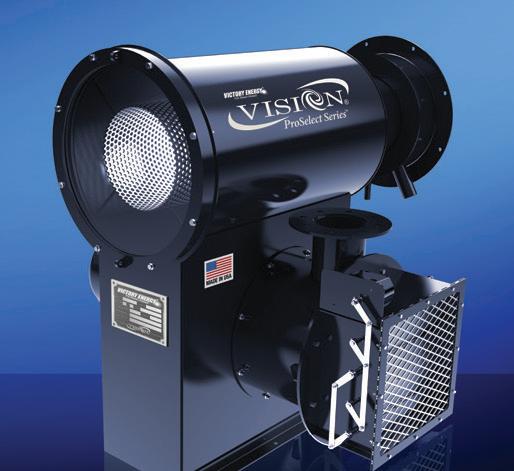
For maximum throughput and the fastest yeast, producers use JADE. It enhances ethanol yield, has what IFF calls “unmatched robustness,” all while increasing the rate of fermentation and replacing glucoamylase by up to 75 percent.
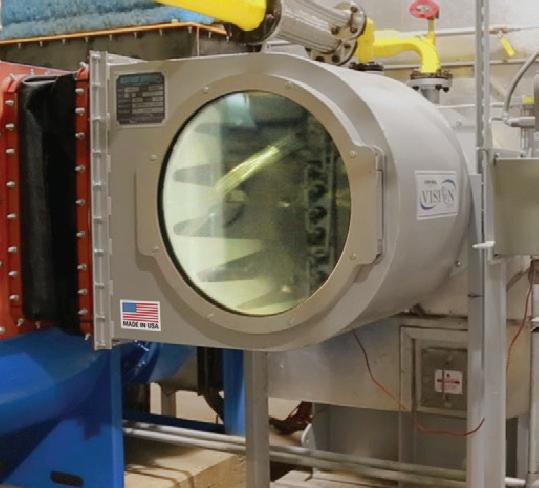


From Ford and his team’s perspective, the ability to blend yeasts allows customers to find the ideal combination of rate, yield and robustness. You never know when a plant process might fail, grain supply falls or environmental factors change enough to alter the fermentation process, he says. IFF and its technical team can ensure that no matter what happens and no matter what a producer wants to happen, they will be prepared and educated on what can happen.
“Producers need levers to maximize yield with different yeasts,” he says. With the GMOs, there is a push and pull, as a plant increases yield it might sacrifice other attributes.
Some yeasts might need very specific conditions. The technical team at IFF has found several ways to help producers look at those conditions, from onsite visits to deploying the latest XCELIS AI tool.
“We are really trying to partner with plants,” Ford says, adding that as cheesy as it sounds, the team enjoys the process of working with its plant partners.
“We can find out where their pain points are. We can find out how they want to run their plants,” and, Ford says with the type of excitement behind his voice that you only hear from someone that has a passion for what they do, “we have the tools to help them do it.”
Author: Luke Geiver Contact: editor@bbiinternational.com
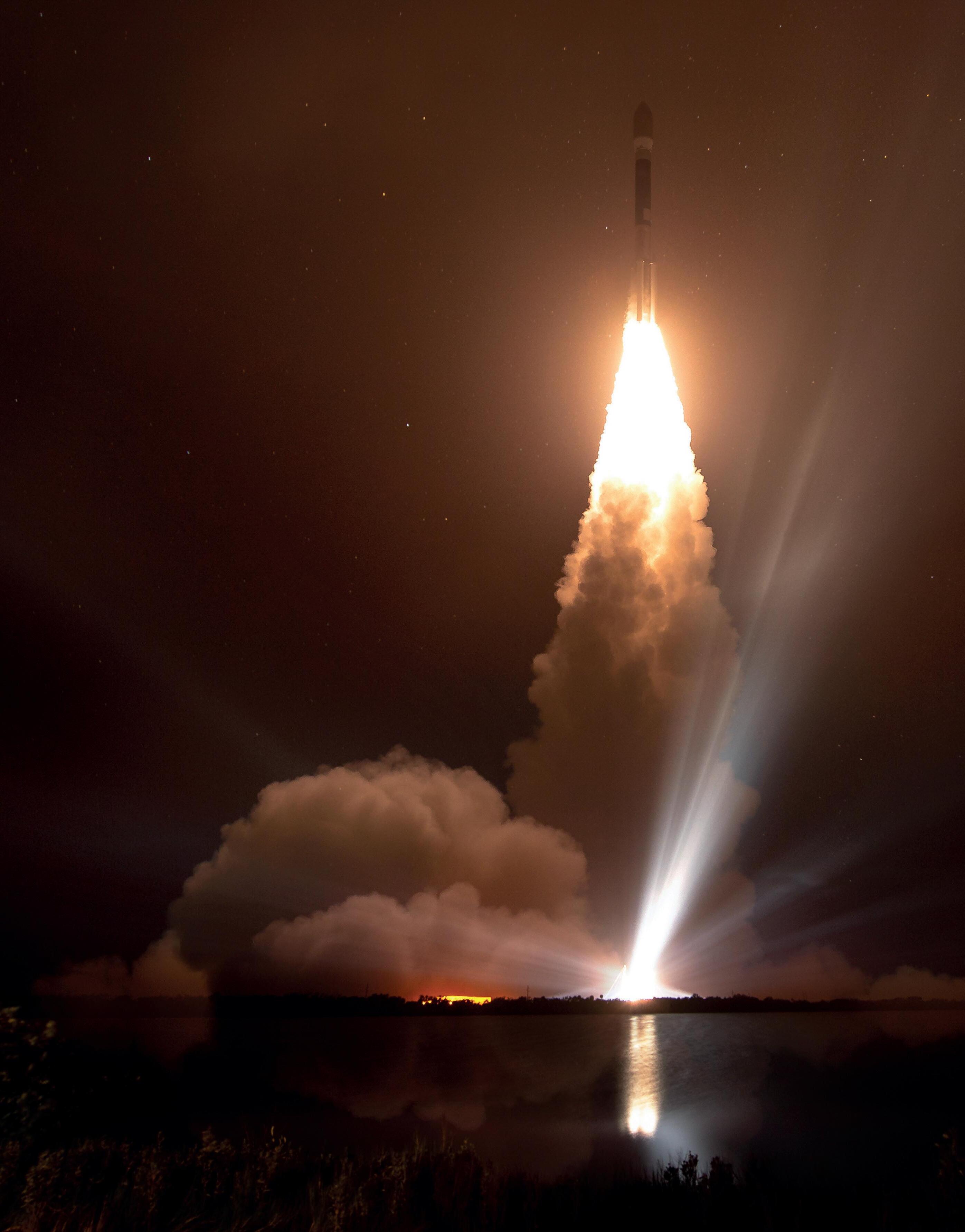
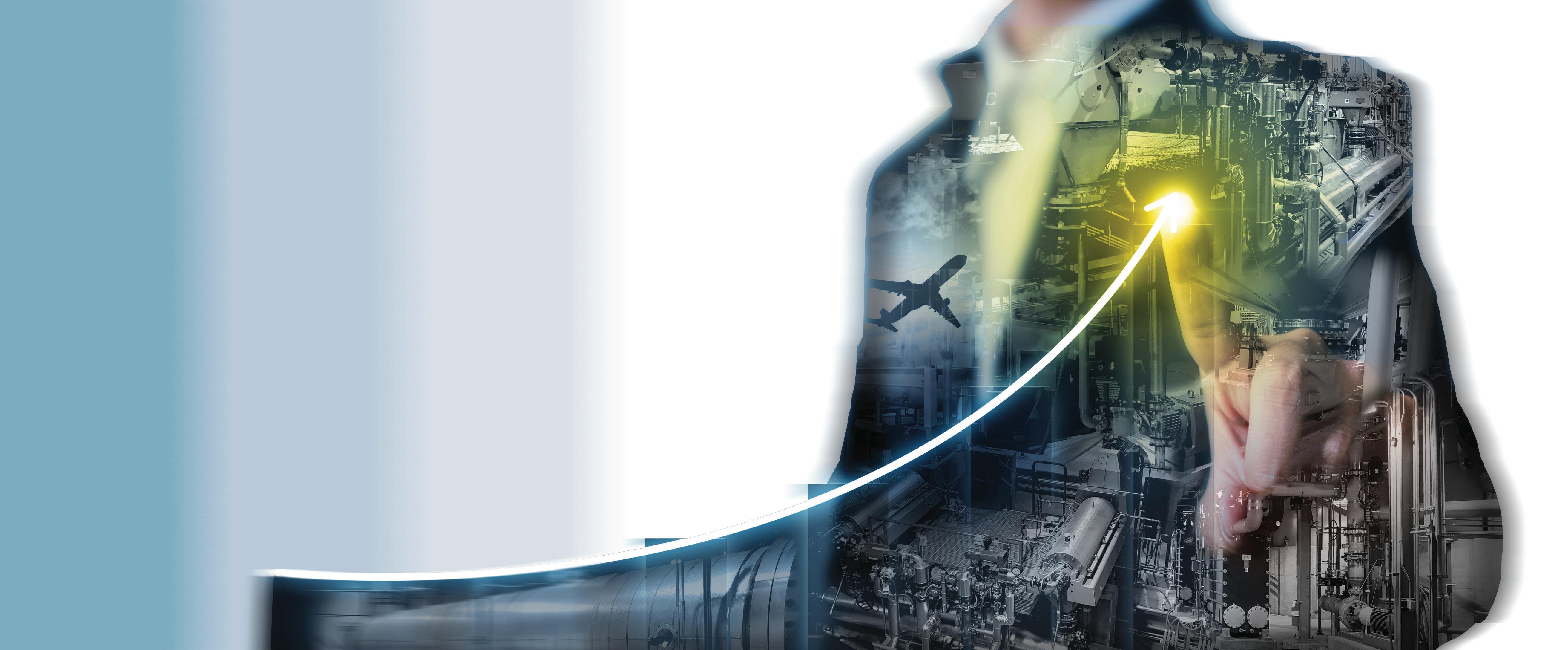
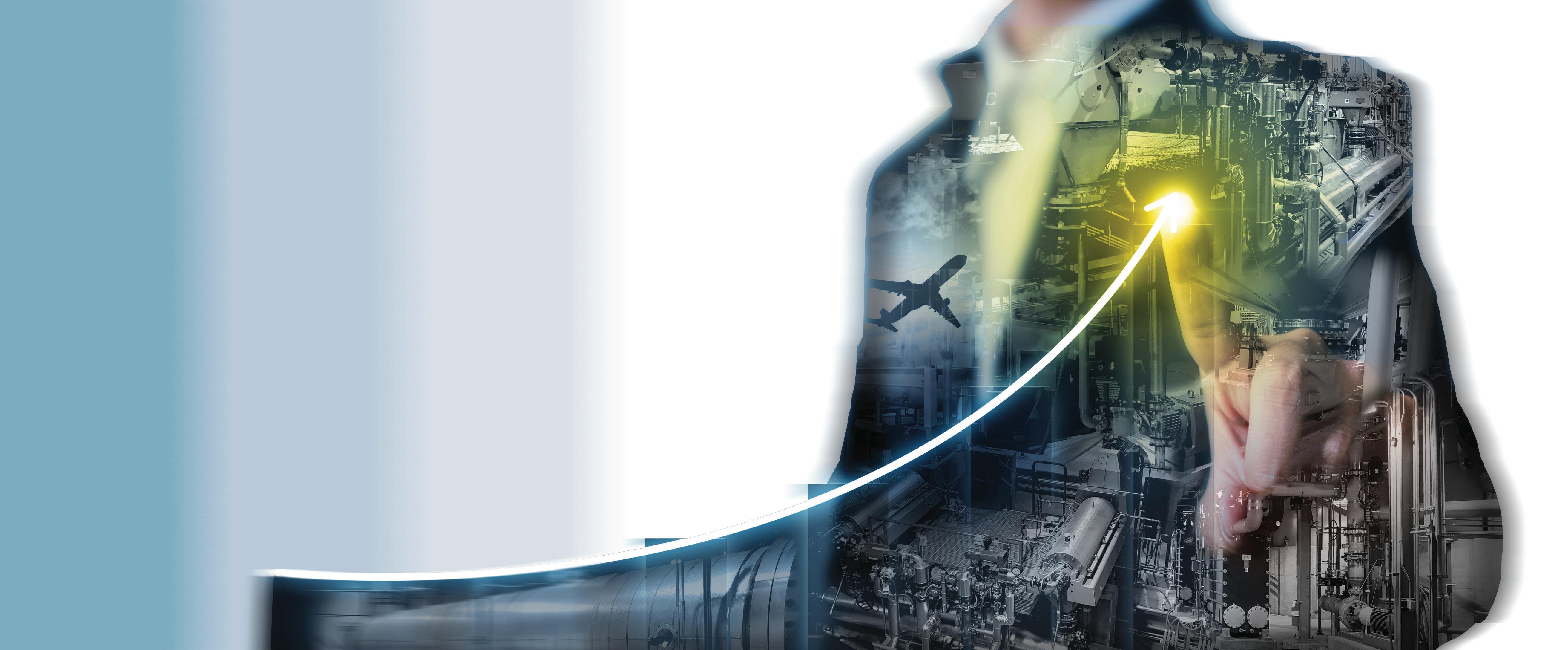
Proteum Energy wants to work with ethanol producers to turn ethanol into hydrogen. CEO Laurence Tree tells Ethanol Producer Magazine the company’s path to market—and Proteum’s end goal—seems both plausible and possible. The company has proven tech with more than 35 patents in multiple countries, including Saudi Arabia, the U.S., Canada and India. More than $65 million in investment by a team of engineers working on the process to turn ethanol into hydrogen—for nearly a decade—has gotten results. Researchers from the University of Regina have proven that the Proteum process of transforming natural gas liquids like ethane, or even simply ethanol, can produce a clean, renewable hydrogen. European energy firms are signing up to use it. California will likely be home a Protuem hydrogen production facility in the future. Hydrogen produced from the system, Tree explains, qualifies for the state’s Low Carbon Fuel Standard credits as well as 45Q tax credits. “When ethanol is used as a feedstock with our technology,” Tree says, “the end product’s carbon intensity score can actually be negative.”
And then there is the hydrogen market. Much like the electric vehicle market, the hy- drogen sector is an evolving mix of hopeful hype, practical resource opportunities and a technology application that seems to be always on the horizon. The fuel itself is used in a fuel cell and produces water as a byproduct. It can be produced from natural gas, nuclear power, biomass, solar, wind and ethanol. Big names that are widely recognizable on the interstate today are investing in or already using hydrogen as a fuel source; they include Toyota, Volvo Daimler, Kenworth, Cummins, Hyundai and more.
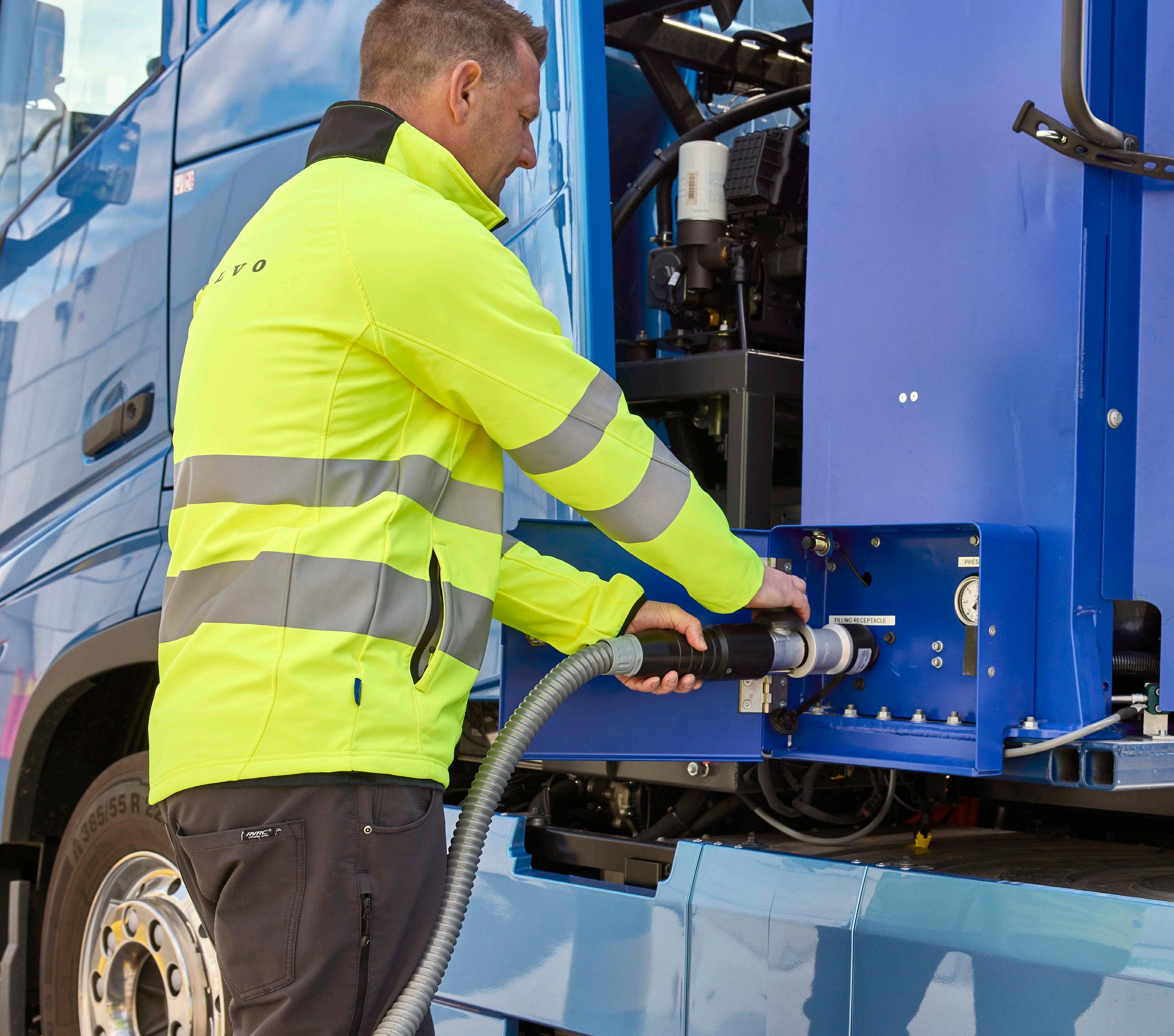
Daimler has already developed a range of prototypes that it has tested in Germany. The company calls hydrogen “a pillar” of its long-term strategy. Cummins, like Daimler, has also invested in prototypes and calls itself a major player in the future of hydrogenbased heavy-duty transportation.
“You see what is going on around the world and there is a clear push to change heavy-duty transportation,” Tree says. “Manufacturers are adopting the technology. They are going to hydrogen because they know it is coming.”
Proteum Energy sees the hydrogen market in the billions. Utilizing its engineering capability and hydrogen production tech, the company intends to enter the market through ethanol, and here’s how it might do it.
