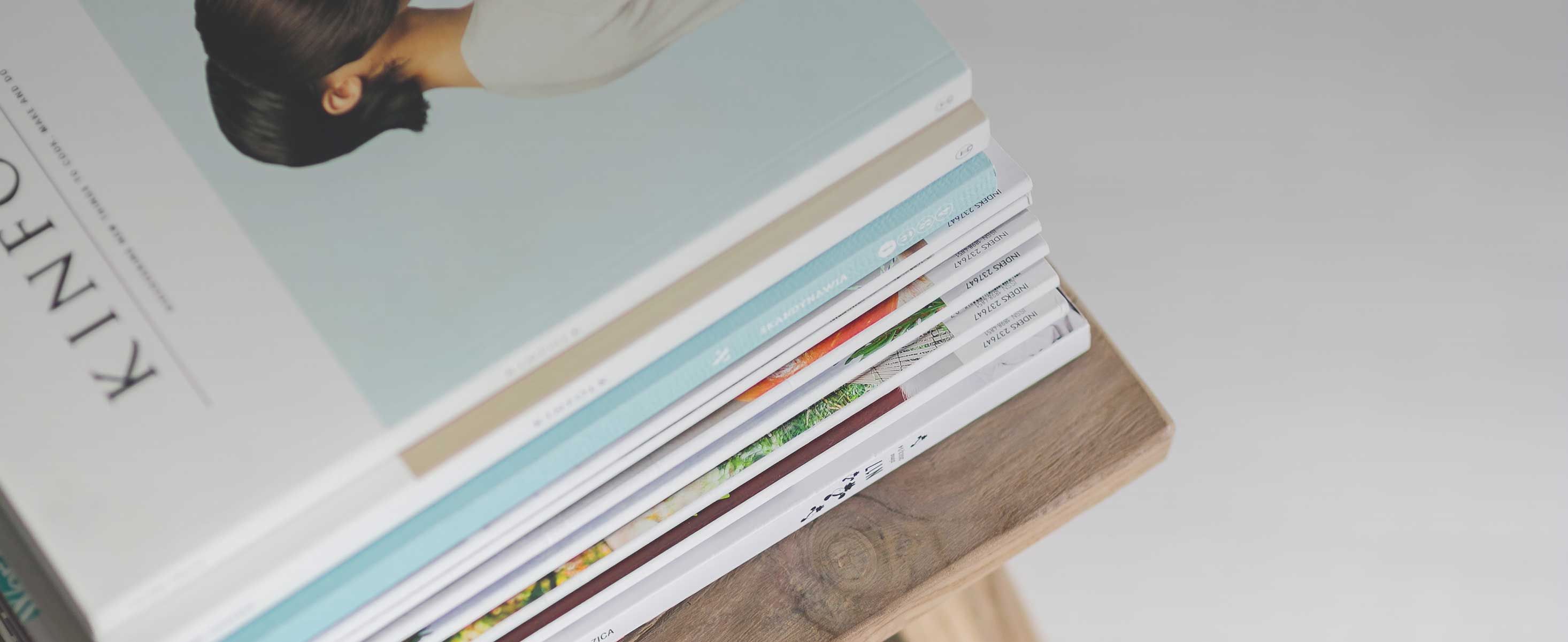
5 minute read
High Reliability Organisations – from concept to reality
from BBMC Yearbook 2021
by bbminingclub
Susan Johnston, Program Leader Governance and Leadership in Mining, Sustainable Minerals Institute, The University of Queensland
Over the past year many companies with operations in the Bowen Basin have been grappling with the question of how to use High Reliability Organisational (HRO) Principles to make their mines safer.
This follows a recommendation in the Queensland Governmentcommissioned Review of All Fatal Accidents in Queensland Mines and Quarries that the industry 'adopt the principles of HRO theory in order to reduce the rate of serious accidents and fatalities'; and subsequent endorsement of the value of HRO thinking in the Queensland Coal Mining Industry Board of Inquiry into the Serious Accident at the Grosvenor mine. External encouragement and companies' own commitments to ongoing safety improvement have driven a deep, and timely, reconsideration of the factors that need to change if we are to avoid further serious injuries and deaths in the sector. HRO theory and principles are not new. For 30 years, researchers have endeavoured to distil what separates those organisations who, day after day, year after year, reliably keep their people safe in very hazardous circumstances - from the rest. The best of this research identified that HROs were organisations who 'thought differently', who had a 'collective mind', and a 'shared sense of commitment to reliability' across units and levels.
As many industry leaders are now aware, these researchers also argued that HROs exhibited five core characteristics, often called 'Principles'. In summary, HROs were seen as: • Sensitive to Operations – meaning they were interested in how their organisation actually worked, not how the organisational chart, or senior executives said that it was supposed to operate. HROs focused on identifying organisational barriers to change, removing silos, and improving communications. • Reluctant to Simplify – HROs understood that some complex issues cannot safely be simplified. Where simplification was chosen, this was done very deliberately, and mindful of what could go wrong as a result. • Committed to Resilience – these organisations built the necessary capability to both prevent incidents and respond to them quickly when they occurred, to ensure impacts were minimised. • Deferring to Expertise – in HROs those with the most relevant knowledge were heard, and could have impact, regardless of where they sat in the organisational hierarchy. • Preoccupied with Failure – an essential component of being a HRO is to be continually aware of the potential for error. In these organisations, small failures were tracked, analysed, and responded to. It is worth noting that the researchers argued that all of these Principles were essential attributes of HROs. Being very good, even exceptional, in one area alone would not allow an organisation to become a HRO. For many Queensland mining companies wanting to follow through on the recommendations that HRO Principles be put into practice in the sector, the full package of HRO characteristics initially seemed too complex, and too vague, to implement. Perhaps unsurprisingly, some industry leaders have focused on what seems like the most familiar territory – enhancing efforts to report incidents; and learn from them. Introducing, or reinforcing, a genuine Preoccupation with Failure has become the priority. There is a danger, however, that a singleminded focus on reporting incidents, while very worthy in itself, will divert attention away from the wholesale, multifaceted effort that is required to achieve higher organisational reliability in safety, environmental management, social performance, or many other aspects of company operations. If, for example, poor internal relationships, excessive workloads, or conflicting priorities are not addressed – as they could be in an organisation Sensitive to Operations – incidents are very likely to continue to occur, even as we get better at reporting them. Truly adopting HRO Principles requires us to invest time in organisational improvement in multiple ways. As a first step we need to understand, before any initiative is introduced or change is made, exactly what the current state of play looks like. In effect, as some companies have recognised, there is a need for a HRO baseline assessment allowing both areas of strength, and weakness, to be identified. A reliable baseline assessment should answer some key questions. Understanding whether, for example, an organisation is Sensitive to Operations might involve ascertaining whether there are any silos, conflicting priorities, poor interpersonal relationships, or unreasonable expectations that, in real practical terms, make it unlikely that organisational aims will be achieved. Assessing whether a company exhibits Deference to Expertise might involve testing whether worker input is encouraged, welcomed, and acted upon, even when that input conflicts with a company's existing approach. Deciding whether an organisation is Reluctant to Simplify might require an examination of the extent to which simplification is seen as an end goal in itself; and of how often the potential consequences of simplification are thoroughly considered before change takes place. A comprehensive HRO baseline assessment can provide companies with a solid foundation for a tailored HRO improvement plan. One of the fallacies in current discussions on HRO Principles is the argument that there can be one, standardised, journey to higher reliability. In fact, as The University of Queensland's own engagement with Bowen Basin operators over the past year has affirmed, site and company needs will vary. For some, internal organisational issues of the sort the Principle of Sensitivity to Operations is designed to address are the most significant barriers to improvement. For others, inadequate attention to building capability, in line with Commitment to Resilience, is the core issue. Every company, and indeed, every site, is likely to have its own particular baseline and need its own particular improvement pathway. What is a constant is the need for a certain kind of leadership. The early researchers noted that leaders in HROs were not only (or even primarily) focused on the work that needed to be done; they were most interested in the individuals doing the work. Personalities, personal needs and interrelationships were factored into leaders' thinking about how a task could best be carried out. More recent research has recognised that unless leaders fully engage their teams; and unless a shared sense of what matters is developed; no amount of process change will succeed in facilitating the deep organisational shift the industry is seeking. As the great scientist and thinker Charles Darwin told us more than a century ago, 'in the long history of humankind, [it is] those who learned to collaborate most effectively who have prevailed'. Understood deeply, actioned thoughtfully, and approached holistically, High Reliability Organisational Principles provide us with a means to prevail in the collective aim of achieving a stepwise improvement in safety and health in the Bowen Basin mining industry.