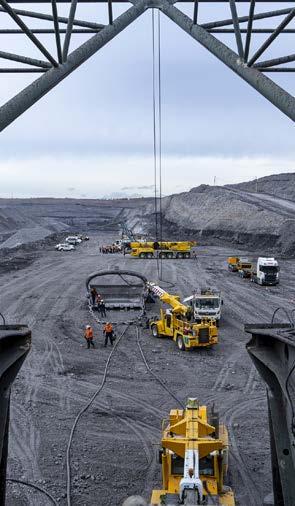
5 minute read
The critical role of interoperability in mining automation
from BBMC Yearbook 2021
by bbminingclub
Photo: Peter Turnbull
Jeff Sterling, Managing Director, Universal Field Robots
In Australia, the resources sector is a critical sector, responsible for an estimated 10% of our GDP and contributing to almost 35% of Australia’s
GDP growth in 2019.
The remoteness and vast distances between resources operating sites and difficulties related to technology connectivity and integration present considerable challenges for the industry. This has accelerated Australia’s push into robotics and automation, particularly over the last decade. Automation, digitisation, and integration initiatives are at the forefront of most mining companies’ technological roadmaps. Interoperability is a necessity for the success of these initiatives and can only be solved using collaboration and communication in order for the mining industry to build an interoperable future. According to the Global Mining Guidelines Group, interoperability is the ability of two or more systems, components, or processes to exchange contextualised information so that they can act on this information to achieve business and operational outcomes. Mining equipment and systems interoperability is a high priority for the international mining community. Universal Field Robots has been heavily involved in interoperability in mining automation, running robotic machines on the surface and underground, within different jurisdictions and diverse corporate cultures. This presents varied and unique challenges.
Given the numerous Original Equipment Manufacturers (OEMs) active across global mining operations, the ability to develop machine-agnostic autonomy solutions is critical to enable integration with numerous brands, such as Caterpillar, Komatsu, Bobcat and Kubota. Autonomy applications can be created by configuring a machine and attachment combination to complete specific tasks, such as loaders, mobile radio coverage and specialised handling activities. Interoperability is challenging, as it is required to exist on multiple levels. At the first level, integration with the machine to monitor health and capability such as battery voltage, fuel level and sending alerts to the operator is needed. A further level of integration involves various sensors that are required to deliver robotic functions, and a third level of integration is the robotic machine with the mine infrastructure for communications, security, GPS adjustment and data curation. A next level challenge is the interaction of multiple vehicles, robots, people, and systems. Collision Avoidance Systems (CAS) are pushed forward with a new ISO standard 21815 part 2 and are applicable for an operator in the seat but it is still early days as to how interoperability is achieved with robotic machines. Communications are very much at the core of interoperability. This is handled by different layers, protocols, and application software. A Pandora’s Box of possibilities exists, including CAN J1939, TCP/UDP, profisafe and websockets. The complexity is daunting, but the magic happens with the clever application and configuration of software realising surprising new capabilities and outcomes. We have recently been working on a project to deliver teleremote and autonomous capabilities for ancillary tasks in an underground mine block cave automation area. This involves autonomy being integrated into both a Bobcat S770 and Caterpillar 262 loader to provide options for mine operators. The loaders must be interoperable with the mine systems, such as traffic management and be controlled from a control station in a common surface control room. Functional safety is a key requirement, and it was necessary to implement safety critical communications over propriety systems and develop our own safety critical communications protocol. This better suits mobile equipment and interoperability and can be implemented more readily on mine sites. In more basic terms, this means that when the control room operator presses stop, the loader will stop as designed and will meet functional safety requirements. Autonomous mining equipment, such as drills, require constant communications. Given the remoteness and distributed nature of most mine sites, potential reduced or failed connectivity risks costly downtime. A new solution to this challenge is an autonomous teleremote tracked machine that acts as a radio point of presence. Robots can drive to a location on the mining bench to support autonomous drills. At the required location, the machine establishes a high bandwidth microwave data link with the mine network and extends a tall mast to rebroadcast radio coverage to the drills. When a blast is scheduled, the machine can drive from the control room to a safe place away from the blast. Safety surveillance is an additional potential use case for these robots, where machines are fitted with a pan tilt zoom camera on the mast, allowing remote control room operators to observe activity from a high vantage point and ensure the safety and security of their drilling machinery and operations. On a more future-facing horizon, developments will advance persistent autonomy. We have been collaborating with other METS companies and investigating digital twin simulation for earth movement, which will be used to create discrete commands to control robotics and scan, monitor, and map new mine surfaces. The intent is to compare the created work with the digital twin plan and use AI to update the planning settings. In this way, autonomous operations can be orchestrated reliably at a high level and achieve increased levels of consistency and independence of operation. This has the potential to become version 4.0 of fleet management. Future scenarios will be demonstrated with the aim of controlling all machine activities on the mine and minimise the need for operators to be in the loop to achieve persistent autonomy. The novelty of these challenges is absorbing much discussion with mining and robotics cross-functional teams. Seemingly simple things like symbols are potentially challenging, by needing to convey meaning to operators with different linguistic and cultural backgrounds. Introducing automation requires re-engineering processes and workflows and a high level of attention to human factors. We have created a granular development process to evaluate the new ways of doing things and to map human interaction with the system and the Graphical User Interface (GUI). Success will be determined when operations begin, and only minimal changes are requested. Advanced digital technologies are enhancing – and in many cases revolutionising – equipment, processes, planning and execution to enable more productive, safe, and cost-effective mines. Interoperability is a requirement for maximising the capabilities and benefits of mining automation, digitisation, operational integration, and data analytics initiatives and can be a huge innovation driver. It is the most critical component in achieving an industry 4.0 operating model. UFR is continuing to develop new applications to accelerate adoption and customer benefits, which have led to four product releases this year alone. Enhanced capabilities and new customer requests can be developed on one site and then rolled out to sites around the world to quickly spin up new benefits. What we are now seeing with digital transformation in mining is tremendous, with stranded value being unlocked that can be harvested by savvy and progressive organisations. As more mining companies pursue digital transformation initiatives, the need for industry-wide interoperability has become very urgent. It is, however, difficult to solve. Are you up for the challenge?