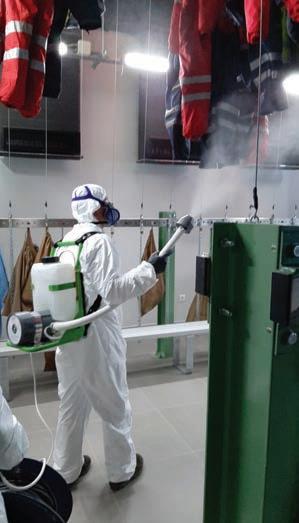
10 minute read
Miners develop best practices for operating during a pandemic
Mining sector develops best practices for a COVID-19 world
By Alisha Hiyate I n many jurisdictions around the world, mining has been classified as an essential service, allowing mines to continue to operate during the COVID19 pandemic.
For a sector that takes safety extremely seriously, how are practices being amended to deal with this new reality and to protect employees and communities?
From transport of personnel to site, maintenance tasks that require more than one person, and meal times, miners have had to rethink every aspect of operations to continue operating safely.
Some of their solutions – including physical distancing reminders in the form of marking out what 2 metres distance looks like in areas where employees congregate – will be familiar to anyone who’s visited a grocery store lately.
Even in jurisdictions where mines have been deemed “non-essential” businesses, operations must still maintain a minimum number of staff to maintain the site during care and maintenance. So physical distancing, new procedures around common areas, crew changes, etc., still need to be thought through and applied, with guidance from various health authorities.
We asked miner Eldorado Gold and contractor Redpath Mining to share their experiences coping with the pandemic in the multiple jurisdictions they operate within.
“We’ve utilized and followed guidance from Health Canada, the WHO, Centres for Disease Control and in some areas we’re relying on provincial and regional recommendations, and even in some cases local health units,” says Chris Betsill, manager of Health Safety and Environment with Redpath Mining.
Like others in the mining business, Redpath, a North Bay, Ont.- headquartered mining contractor works at sites around the world.
“I would say these sources of information refined our strategies and many of our clients also responded quite well and provided their guidance and controls to prevent or reduce the number of cases on their property.”
And that varies site by site and by client.
“You’ve got remote sites where everyone’s in a camp; we’ve also got projects that are located in a city where people go home back to their families, so each scenario poses different challenges.”
George Burns, president and CEO of Eldorado Gold, which has mines in Quebec, Turkey and Greece, says while the company has relied on guidance from multiple authorities, it’s been pretty
Far left: Disinfection at Eldorado Gold’s Efemcukuru gold mine in Turkey. Left: Physical distancing markers at Efemcukuru. Below: Practicing physical distancing during a meeting at Eldorado Gold’s Kisladag gold mine in Turkey CREDIT: ELDORADO GOLD

consistent on what measures need to be taken to stop the spread of the disease.
“The high-level guidance is fairly consistent,” Burns says. I think what’s different is how fast the virus is spreading in each jurisdiction and then what the government determines is the appropriate action to be taken.”
Eldorado’s mines have been affected differently by the crisis. While its mines in Turkey and Greece are still in full production, its Lamaque underground mine in Quebec had to be transitioned to care and maintenance after the Quebec government deemed mining a non-essential business in late March.
That transtion was achieved within 24 hours, with the number of workers onsite reduced from hundreds to 35 required for care and maintenance. Remote monitoring technology allowed management to
There’s a great deal of collaboration happening within the sector, and not just within Canada but internationally – the industry is sharing best practices and then each mining association in a particular jurisdiction is sharing what the industry is doing to reduce risk and helping governments make informed decisions.”
– GEORGE BURNS, PRESIDENT AND CEO OF ELDORADO GOLD.
continued to evolve: As of Apr. 15, the Quebec government is allowing mines to reopen with strict sanitation and physical distancing measures in place, as well as longer rotations for crews in fly-in operations and a reduction of flights in and out of sites.
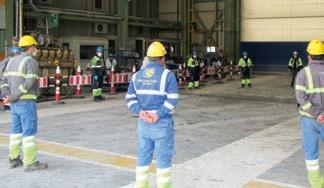
COVID-19 guidelines
Where operations have been able to remain open, guidelines and controls specific to COVID-19 have had to be developed, both to protect employees, clients, and communities, and to reduce the impact of the pandemic on the business. This has been aided by guidance from authorities, guidance from internal crisis management plans, and miners sharing best practices with each other directly and through local mining associations.
“There’s a great deal of collaboration happening within the sector, and not just within Canada but internationally – the industry is sharing best practices and then each mining association in a particular jurisdiction is sharing what the industry is doing to reduce risk and helping governments make informed decisions,” says Eldorado’s Burns. “I’ve been impressed with the amount of sharing – and it’s not new for our industry when it comes to safety and health, there is no competition between companies. That industry norm is just continuing through this pandemic.”
For mining operations, the physical distancing guidelines of 2 metres separation between people that have been
central to health authorities’ recommendations has provided some challenges.
At their offices, miners have been restricting non-essential travel and, since the pandemic started to spread more widely in March, employees who can work from home have been working remotely. Limiting the number of staff who come into the office, and in some cases, implementing one-way entrances and exits has also helped reduce risk where employees need to go in.
Companies are making use of relatively new technologies that were implemented pre-COVID-19 and now proving essential to business – for example the use of video and teleconferencing capabilities, and remote monitoring.
“We have, like many companies been investing in technology over the last couple of years, and in particular, our video teleconferencing capability has worked fabulously,” said Burns. “So we have all kinds of crisis teams that are managing safety, hygiene and business management, supply chains, customers – essentially where people can work remotely, we’re leveraging this technology and it’s working fabulously.”
At mine sites, stepped up sanitation, education around COVID-19 and health screening measures – including health questionnaires, and temperature screening – have been put in place to reduce the risk of bringing the virus in.
Whenever employees are normally gathered together, procedures have been implemented to allow distancing have been put in place. For example Eldorado Gold is managing transport of employees to its sites differently, says Joe Dick, the company’s chief operating officer.
“We don’t run any camp jobs, so we have transport. We have dispersed people so that we have physical distancing within transport. And in some locations, we’re doing a screening before you get on transport and in other locations, as you get off transport. Then, we also have deployed some staggered starts so that we don’t have those crowded areas at the beginning and end of shift.”
Dick says the company is also using personal protective equipment (PPE) – face shields – in transport.
“Most of our congregation points are in transport or at the start or end of shifts and through staggering and monitoring and screening, we’re doing quite well there.”
Dick says PPE is also being used for some maintenance tasks where two or more people are required to work closely.
“Then there are a couple of things that we discontinued until we figure them out, so in an underground application where we may be sanding steel sets or something like that where there’s close involvement between 2-3 workers at a time,” he added.
Entry into common eating areas at Eldorado’s locations in Greece and Turkey, is managed with a certain amount of people allowed in at a time, and staggered. And like grocery stores, the company has placed markers on the floor as a reminder for employees to keep 2 metres apart.
Eldorado has also installed thermal scanners at its Lamaque mine in Quebec, to prevent workers with an elevated temperature from entering the facilities.
As Eldorado has implemented its plans, its also tried to verify that the controls that have been put in place are working and are practical, through task observation. Dick says task observation, which also helps to improve controls, is a best practice that will survive the current crisis.
“From my perspective, the concept of task observation to make sure that what you’re doing is effective, and seeing management in the field observing is really good for the morale of the teams that are doing the work,” Dick says.
Underground considerations
Redpath specializes in underground mine contracting (construction and mining), where workers are often in close quarters.
The company has limited the number of workers in transport – whether it’s in cages, buckets or in light vehicles – and mandated the use of masks when physical distancing is not possible.
“Some examples would be riding cages down the shaft, bringing personnel into the mines in light vehicles – those are some specific situations that we’ve had where we’ve had to assess the risk and institute some unique controls to eliminate or reduce potential transmission of the virus,” says Betsill.
“As far as using mobile equipment or transporting people, we’ve implemented certain sanitization procedures in between shifts, periodically throughout the shifts, and like a lot of others, we’re also relying on PPE – gloves and respirators and in some cases face shields.”
While Redpath’s projects are international, much of its staff is not necessarily locally based. With projects in Canada, the U.S., South America, Indonesia, Mongolia, Africa and Australia, the company would normally have many employees moving back and forth on their regular rotations, or on scheduled site visits.
That’s not happening now because of international travel restrictions – and that means that some Redpath employees may be away from home until these restrictions ease.
“We’re quite grateful for all the loyal Redpath people who have decided to work extended rotations due to these travel restrictions and we also appreciate the sacrifice that their families are making during these uncertain times,” Betsill says.
PPE concerns
Betsill says Redpath has been able to transfer some PPE between projects in cases where one project has a surplus of materials. Redpath’s operations were able to donate 19,000 pairs of disposable gloves to the local North Bay Regional Health Centre at the end of March. But sourcing PPE at a time when it’s in extremely high demand is a concern.
“We’re working closely with our vendors and clients to source PPE to protect our workforce from the normal hazards inherent to our industry, as well as those related specifically to the COVID-19 crisis,” Betsill says. “As they should, frontline health care workers and emergency services are taking precedence for some specific equipment that we also require. In some cases, our suppliers of this equipment are focused strictly on health care and emergency services, which we support 100%. So it’s something we’re trying to navigate now and I think that will be an issue for the next couple of months.”
While the company wouldn’t normally require the N95 masks that the health care sector might use, it is considering PPE similar to that because of the potential to bring COVID-19 into a site and the need to protect workers.
In addition to PPE, other supplies – consumables and machine parts – are also a concern in the medium term.
Communication
Throughout the crisis, the importance of communication has become apparent.
“Communication – when you’re in a crisis – comes to a higher state of being,” said Eldorado’s Burns. “We’ve always been focused on safe behaviours and safety practices – not only at work but encouraging employees to take it (safety) home and have it become a habit at home. And I think with the virus, the same thing has happened.”
Burns adds that Eldorado employees have appreciated the company’s approach during the pandemic to reduce risk and at the same time, try to preserve the business and preserve their jobs.
“I think that’s highly appreciated by our workforce, and we’re trying hard to articulate that reality to governments so that as they make their tough decisions, they can make an informed decision.” CMJ
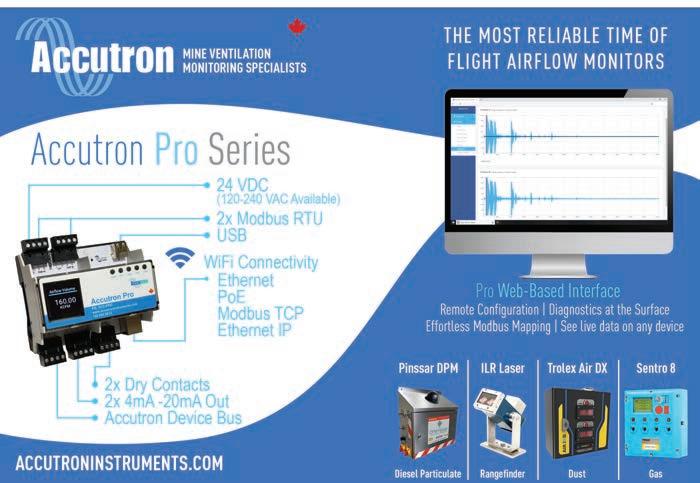
