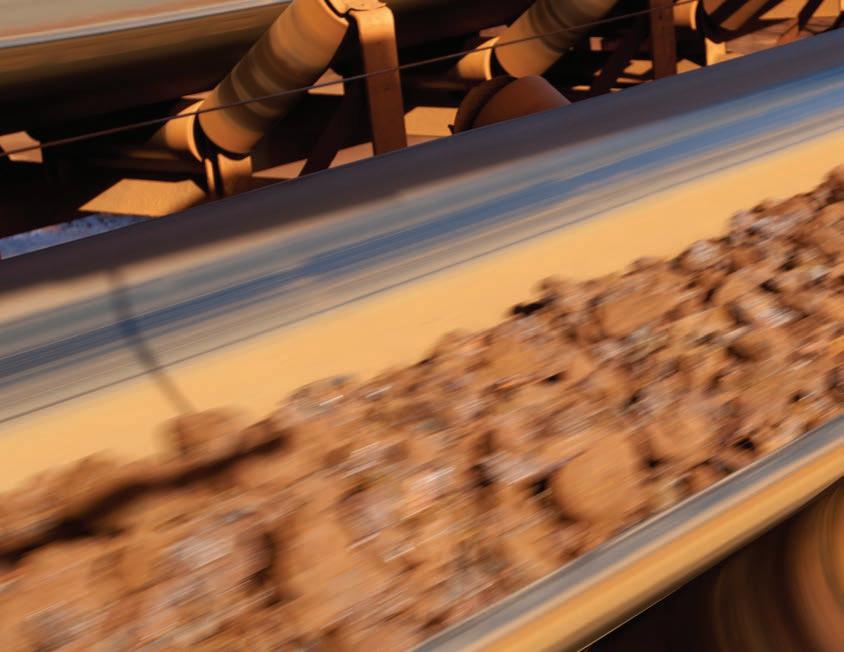
9 minute read
CostMine investigates how well “rules of thumb” used in mining really work, focusing on conveyor costs
Evaluating rules of thumb using conveyor costs CostMine analysts investigate 4 ‘rules’
By Sam Blakely and Scott Stebbins R ules of thumb are often used in the mining industry as methods of providing approximate answers for different portions of mining activities. But do these “rules” work? Are they outdated? To answer these questions, we decided to focus on conveyor costs and the associated rules of thumb widely used in underground mining.
We intend to show how Sherpa for Underground Mines, a software tool available from CostMine, can be used to bolster confidence in items like de la Vergne’s rules of thumb (or to make determinations in more project-specific problems) in a way not possible without Sherpa’s speed and engineering capabilities. We chose de la Vergne’s compilation of conveyor cost rules of thumb to assess using Sherpa for Underground Mines. The majority of these rules are echoed below:

mine production exceeds 5,000 tons. (Source: Al Fernie)
2 As a rule, a belt conveyor operation is more economical than truck haulage if the conveying distance exceeds 1 km (3,280 ft.). (Source: Heinz Altoff)
3 The ton-mile cost of transport by belt conveyor may be as low as one-tenth the cost by haul truck. (Source: Robert Schmidt)
4 The installed capital cost of a long belt conveyor system to be put underground is approximately equal to the cost of driving the heading in which it is to be placed. (Source: Jack de la Vergne)

Our modelling technique, and that of Sherpa for Underground Mines, consists of a whole-project cost approach. Costs associated with several tasks and processes not directly related to purchasing, operating, and maintaining the machines must also be considered to properly evaluate economic decisions.
In the case where primary transport options are compared it must be remembered that ventilation requirements differ for each approach, as are the cross-sectional areas of the faces of each of the respective openings through which the machines transport the ore. Shop facilities, and the nature of the service vehicles, are more extensive for truck transport than for the conveyors. Every such factor figures into the overall economics of each transport method and are incorpo
Modelling Assumptions
When a conveyor transports ore out of the mine, the mine-run is crushed before it’s loaded on the belt to minimize belt damage. The models used in this analysis replicate this procedure. Typically, mine-run ore is not crushed prior to truck transport, but is instead crushed after it is delivered to the mill. In both scenarios, the ore is crushed, but when a conveyor is specified for primary transport, the costs of this process are often attributed to the mine costs. For truck transport, they are included in the mineral processing costs. To effectively compare conveyor and truck transport, the costs of purchasing, installing, and operating an underground crusher have been subtracted from the conveyor transport scenario values below. Figure 1: Cut and Fill Haul Method, Production Rates and LOM Costs
CONTINUED ON PAGE 30 rated into the values below.
RULE OF THUMB #1: Production rate
To begin, typical deposits and matching mining projects which utilize cut and fill, sublevel longhole and room and pillar stoping methods were constructed in Sherpa for Underground Mines at various production rates. In accordance with rule of thumb No. 1, conveying distances were set to 1 km. The results of this analysis can be seen in Figure 1 and align with de la Vergne’s rule of thumb whereby a conveyor is economically advantageous as compared to rail or truck haulage when production rates exceed 5,000 t/d. The results of the sublevel longhole and room and pillar analyses showed similar overall trends. Though, relative to the cut and fill Sherpa models, the spread in costs above 5,000 t/d was greater in the sublevel stoping analysis and narrower in the room and pillar analysis.
RULE OF THUMB #2: Economic transport distance
Evaluators, and the preceding analysis, have assumed that conveyor haulage is economically advantageous when compared to truck haulage when material is to be transported a distance of more than about 1 km (3,280 ft.). To verify this assumption, we’ve constructed a series of production scenarios which examine a room and pillar mine operating through a variety of production rates and primary haul distances. For our work, only the deposit thickness (as opposed to the deposit width or length) was varied to provide the different resource tonnages (and subsequent production rates). This minimized the impact of the haulage costs from the face to the crusher station on the overall project costs.
SHERPA FOR UNDERGROUND MINES
CostMine offers several engineering-based mining cost estimating software tools and works continuously to improve these products. One such offering is Sherpa for Underground Mines, which is software that uses resource and mine production information to estimate labour, supplies and equipment requirements, which are in turn used to estimate the associated mine capital and operating costs. To do this, the application uses evaluator-supplied information to calculate over 800 engineering parameters. These parameters can be readily altered to more precisely reflect project conditions. In addition, help screens and a manual offer technical guidance for each parameter value.
One value of the Sherpa suite of software, which includes Sherpa for Underground Mines, is its ability to complete engineering-based mining cost estimates in a timely manner. This allows you to assess a multitude of what-if scenarios as you make planning, development or production decisions, a task not easily accomplished when time is of the essence or without such tools.
HARD ROCK MINER’S HANDBOOK
Another resource available to developers and professionals who must make such decisions are the precepts and rules of thumb found in literature, such as those in the well-known Hard Rock Miner’s Handbook, written by Jack de la Vergne (published by Stantec Consulting). These rules of thumb are the result of decades, if not centuries, of experience and are of great value to many. They give evaluators the opportunity to diligently draw upon the industry’s collective experience as they solve the problems of estimating costs.
The results of this evaluation (Figures 2-6) indicate that haul length is indeed a primary factor when truck haulage costs are compared to those of conveyor transport. Though, as indicated by rule of thumb No. 1 and Figures 2-6, production rates have an equally significant impact. As can be seen, above a certain production rate (somewhere near 5,000 t/d), overall project operating costs will be less when a conveyor transports the ore, once a specific haul distance is exceeded (in the scenarios which we examined). In each of the models with production rates greater than or equal to about 5,000 t/d, this distance was somewhere between 1,830 and 3,660 metres (6,000 and 12,000 ft.).
It is critical to note the minor variations from one data point to the next. The curves are typically neither smooth nor uniform. These variations represent a condition that manifests because of the finite availability of machine sizes. Put simply, in some instances a (theoretical) 27.5-inch-wide conveyor may have provided maximum utilization at a specific production rate. But because such a conveyor belt width does not exist, a 30-inch-wide conveyor is selected instead, which provides more than enough capacity. As a consequence, this machine will then be slightly underutilized (and subsequently more expensive in terms of cost per ton), unless the production rate is changed.
Modelling of this type points out the benefits of more detailed analysis. The suite of available sizes for any type of machine is a series of finite options. The conveyor width that the application selected for the 1,000 t/d scenario may provide more capacity than necessary, which is reflected in a higher overall cost. Alternately, it might have selected a truck size in which an additional hauler would be necessary but not fully utilized, thereby increasing the overall project per-ton cost associated with a truck transport scenario.
RULE OF THUMB #3: Cost per ton-mile
It is said that conveyor transport costs are typically about 10% of those attributable to truck transport. This statement is vague in that it does not go on to define which costs are included, and if this relationship is applicable to any specific distance. Our analyses tend to dispute this relationship.
On average, over all the scenarios we examined, total per-ton-mile operating costs for conveyor haulage were about 39% of those for truck transport. These costs include the diesel (US$2.65 per gallon) or electricity (US$0.087 per kWh) to propel the truck or the belt, maintenance and repair parts and labour, tires and an operator for the truck, and lubricants. All prices used in our analyses are in terms of 2020 U.S. dollars. If ownership costs are included, the total perton-mile operating costs for conveyor haulage averaged 72% of those for truck transport. For these analyses, ownership costs are simply the purchase price divided by the expected life of the machine prior to overhaul or replacement.
The lowest ratio of conveyor transport operating costs to truck transport operating costs (excluding ownership costs) was about 0.26:1 for a scenario in which 15,000 t/d are transported about 500 metres (1,650 ft.). This ratio did not vary much with respect to distance. For a similar scenario in which the material was transported 350 metres (11,400 ft.), the ratio of conveyor transport operating costs to truck transport operating costs (excluding ownership costs) was about 0.3:1. This ratio was as high as 1.19:1 for a case where only 1,000 t/d were transported 350 metres and ownership costs were included.
RULE OF THUMB #4: Adit development and installed conveyor costs
Rule of thumb No. 4 tells us that the cost of purchasing and installing a long conveyor is roughly equal to the cost of developing the opening through which it will operate. But the term “long” is not defined. For consistency, the authors chose to investigate this rule of thumb using an adit length of 1 km (3,280 ft.).
The results of this analysis indicate that this rule of thumb primarily applies to projects near in scale to 5,000 t/d ore production. At this rate, conveyor purchase and installation costs are roughly equal to the cost of driving an appropriately sized adit. However, at production rates below 5,000 t/d, the cost of the conveyor is near half the cost of driving the adit. Above 5,000 t/d, the scenario is just the opposite and the cost of developing an appropriate opening tends to be about half the installed cost of the conveyor. Cost differences do begin to narrow as the transport distance is increased; however, the cross over in costs (the point at which they are roughly equal) still seems to occur around 5,000 t/d.
Conclusion
Rules of thumb continue to be a viable source of information when evaluators estimate costs of proposed operations at their earliest stage. They bring a level of practical experience to the estimate that provides a tangible boost in confidence of the results, which is difficult to replicate. However, there are drawbacks. Such rules fail to account for variations in wages and the prices of fuel and electricity attributable to the passage of time and circumstance of location. And with the availability of more and more reliable sources of current (and continually updated) cost information in formats that can provide very timely results, the risks of relying entirely on rules of thumb are increasingly unjustified. CMJ
Sam Blakely is a cost analyst and geologist with CostMine (www.costmine.com), a division of Glacier Resource Innovation Group. He can be reached at sblakely@glacierrig.com. Scott Stebbins, P.E., is president of Aventurine Mine Cost Engineering, and designed the Sherpa sotfware suite. He can be reached at aventsherp@aol.com.