

MINING IN THE DIGITAL AGE
Artificial intelligence is making the unseen seen
DEEP SEA MINING AND THE GREEN TRANSITION
GRASSY MOUNTAIN COAL PROJECT IN ALBERTA
CRITICAL MINING IN BRITISH COLUMBIA

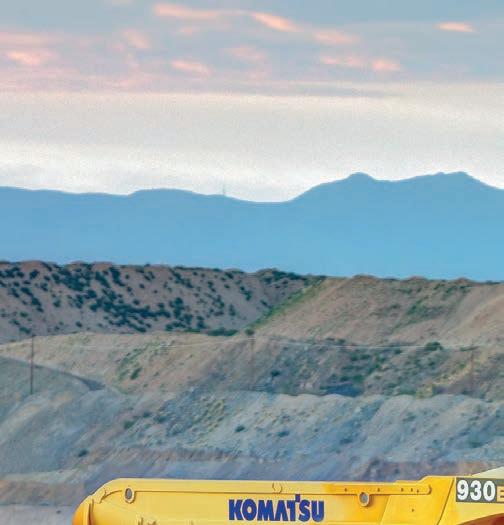
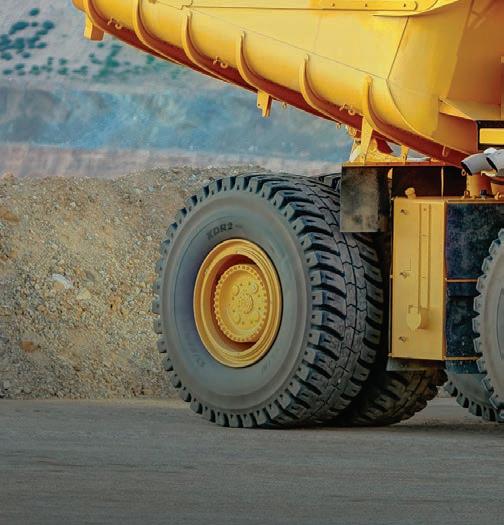


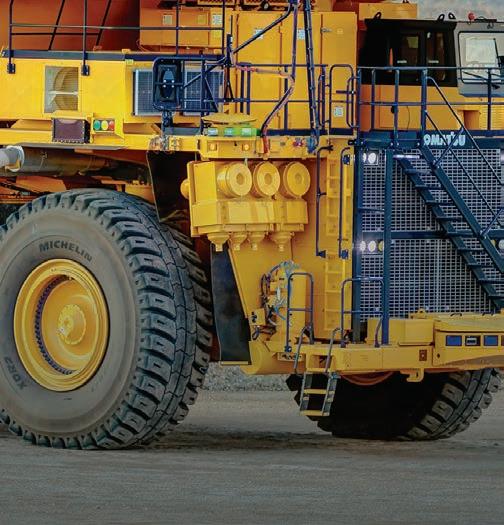
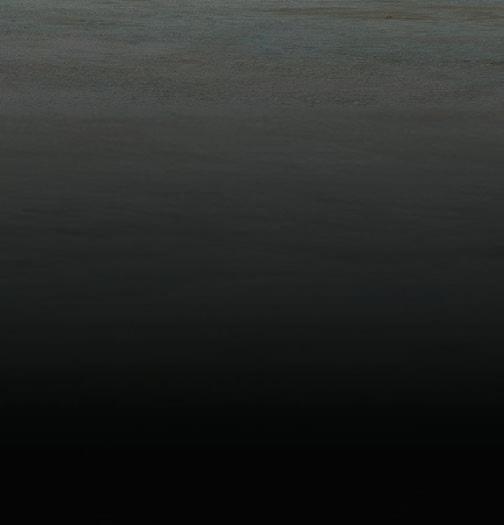

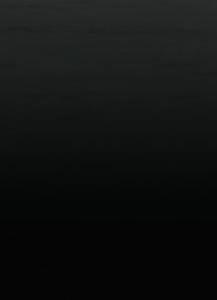
FEATURES
MINING IN THE DIGITAL AGE
8 Meeting the metals mining shortfall.
16 The role of mine electrification in a digital era.
18 Environmental technologies can help mining companies navigate the new GRI sustainability standard.
20 Making the unseen seen: Artificial intelligence provides real-time visual insights into mining operations.
24 Precision beyond the noise: Preparing for solar-triggered signal disruptions.
27 Embracing technology fusion and quantum sensing can accelerate mineral discovery.
31 Autonomous tire inspections and artificial intelligence can improve safety, uptime, and compliance.
33 Lack of tech talent holds mining innovation back.
MINING IN CANADA
35 Deep sea mining can provide metals for the green transition.
39 Benefits of the Grassy Mountain coal project in Alberta.
41 Critical mining in British Columbia: $36 Billion in critical minerals investment at stake.
INTERNATIONAL MINING
44 Argentina’s abundant copper and lithium.
MAINTENANCE AND AUTOMATION
46 Using automation to correct conveyor belt mis-tracking.
MINING WORKFORCE
49 What is the correlation between transformational leadership and the profitability of Arizona copper mining companies?
HISTORY OF MINING
51 Fire and the mining frontier.
DEPARTMENTS
4EDITORIAL | Artificial intelligence will revolutionize the mining industry.
6FAST NEWS | Updates from across the mining ecosystem.
10COSTMINE | Are rail transport costs really four times higher?
13MIN(E)D YOUR BUSINESS | Sustainable mining finances: Exploring costs and liabilities.
53ON THE MOVE | Tracking executive, management, and board changes in Canada’s mining sector.
www.canadianminingjournal.com
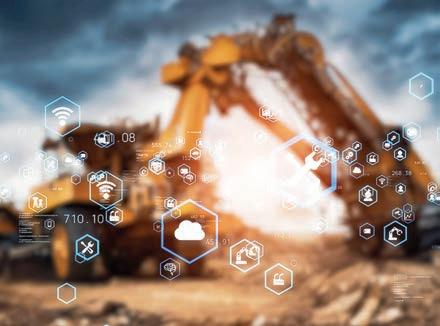
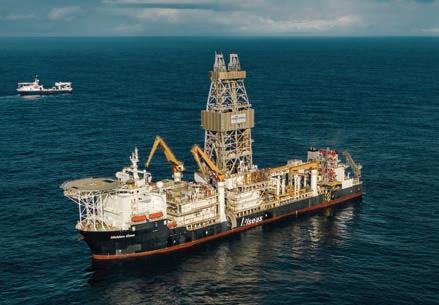
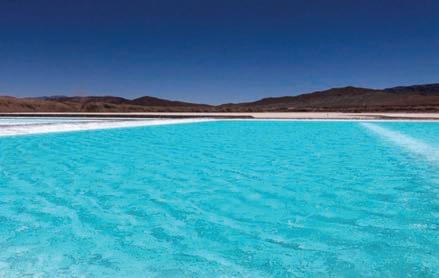
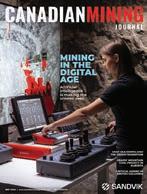
Coming in June/July 2024
Canadian Mining Journal’s June/July issue will report on water management, and we look at methods to improve the planning and results of mine closure, including a detailed look at tailings, with a special feature on pumps.
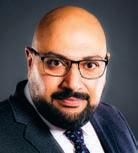
PArtificial intelligence will revolutionize the mining industry
rime Minister Trudeau announced earlier in the month of April that the federal government would be setting aside $2.4 billion in Budget 2024 to position the country in the forefront of artificial intelligent (AI) and secure Canada’s AI advantage. This announcement is important for the mining industry, especially with all the great work being done on AI in the technology sector in Canada and how that work is finding applications in mining. However, it is not yet clear whether or how the mining sector can directly benefit from this announcement.
According to a recent survey by Gartner, 80% of executives think automation can be applied to any business decision. The survey revealed how organizations are evolving their use of AIas part of their automation strategies.
In recent years, the adoption of AI has emerged as a gamechanger for mining, allowing for more efficient mineral exploration, maximizing extraction by improving drilling and blasting technologies, taking automation to new levels, and dramatically improving safety and environmental monitoring. Additionally, AI can also help in mining by optimizing predictive maintenance, processes, supply chain, and operational performance.
In this issue, we cover several topics related to “Mining in the Digital Age” on pages 8 and 16-34, with a special focus on AI. For example, on page 16, the article discusses the role of mine electrification in a digital era. On page 18, Rachel MadorHouse explains how new environmental technologies can help mining companies. Additionally, AI is making the unseen seen in the mining industry: alwaysAI is using AI to provide real-time visual insights into mining operations (see page 20). One of our regular contributors, Danny Parys, argues that the lack of tech talent holds mining innovation back on page 33.
In our “Mining in Canada” section, an interview with Craig Shesky, CFO of The Metals Company, sheds some light on how deep sea mining can provide metals for the green transition (see page 35). Flip to the interview on page 41 in which I discuss critical mining in British Columbia and how a recent independent study concluded that $36 billion in critical minerals investment could be at stake with Michael Goehring, president and CEO of the Mining Association of British Columbia (MABC).
If you are planning to be in Vancouver, B.C. between May 12 and 15, 2024, to attend CIM CONNECT 2024, please remember to collect a copy of this issue and visit The Northern Miner Group’s booth 707.
Finally, our June-July 2024 issue will report on water management, and we look at methods to improve the planning and results of mine closure, including a detailed look at tailings, with a special feature on pumps. CMJ
MAY 2024
Vol. 145 – No . 3
69 Yonge St., Ste. 200, Toronto, ON M5E 1K3 Tel. (416) 510-6789 Fax (416) 510-5138 www.canadianminingjournal.com
Editor in Chief Dr. Tamer Elbokl telbokl@canadianminingjournal.com
News Editor Marilyn Scales mscales@canadianminingjournal.com
Production Manager Jessica Jubb jjubb@northernminer.com
Advisory Board
David Brown (Golder Associates) Michael Fox (Indigenous Community Engagement) Scott Hayne (Redpath Canada) Gary Poxleitner (SRK)
Manager of Product Distribution Allison Mein 416-510-6789 ext 3 amein@northernminergroup.com
Publisher & Sales Robert Seagraves 416-510-6891 rseagraves@canadianminingjournal.com
Sales, Western Canada George Agelopoulos 416-510-5104 gagelopoulos@northernminer.com
Toll Free Canada & U.S.A.: 1-888-502-3456 ext 2 or 43734
Circulation Toll Free Canada & U.S.A.: 1-888-502-3456 ext 3
President, The Northern Miner Group Anthony Vaccaro
Established 1882
Canadian Mining Journal provides articles and information of practical use to those who work in the technical, administrative and supervisory aspects of exploration, mining and processing in the Canadian mineral exploration and mining industry. Canadian Mining Journal (ISSN 0008-4492) is published nine times a year by The Northern Miner Group. TNM is located at 69 Yonge St., Ste. 200, Toronto, ON M5E 1K3. Phone (416) 510-6891.
Legal deposit: National Library, Ottawa. Printed in Canada. All rights reserved. The contents of this magazine are protected by copyright and may be used only for your personal non-commercial purposes. All other rights are reserved and commercial use is prohibited. To make use of any of this material you must first obtain the permission of the owner of the copyright. For further information please contact Robert Seagraves at 416-510-6891.
Subscriptions – Canada: $51.95 per year; $81.50 for two years. USA: US$64.95 per year. Foreign: US$77.95 per year. Single copies: Canada $10; USA and foreign: US$10. Canadian subscribers must add HST and Provincial tax where necessary. HST registration # 809744071RT001.
From time to time we make our subscription list available to select companies and organizations whose product or service may interest you. If you do not wish your contact information to be made available, please contact us via one of the following methods: Phone: 1-888-502-3456 ext 3; E-mail: amein@northernminergroup.com
Mail to: Allison Mein, 69 Yonge St., Ste. 200, Toronto, ON M5E 1K3 We acknowledge the financial support of the Government of Canada.


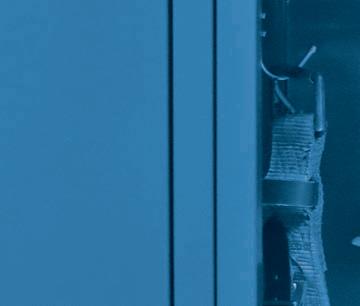

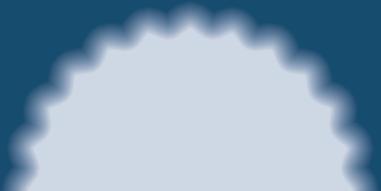

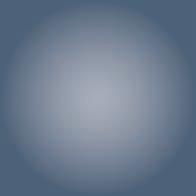



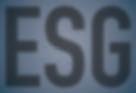
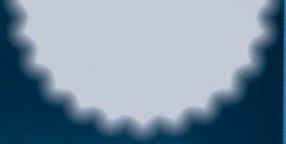
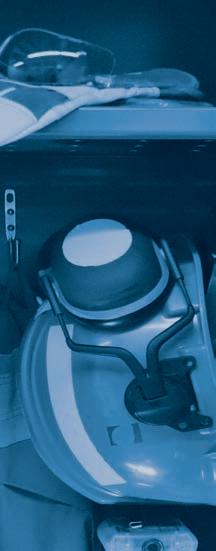
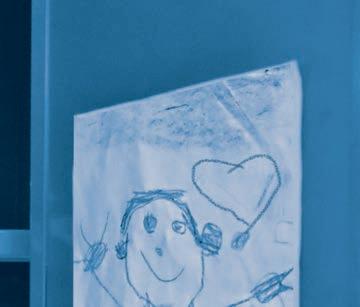
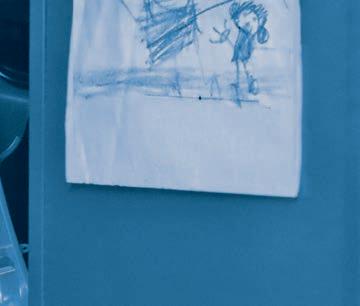
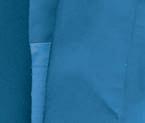

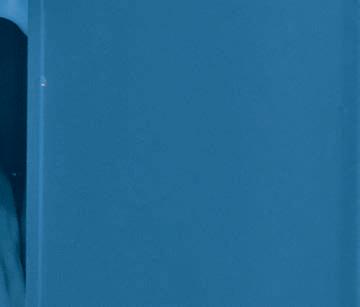


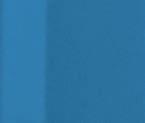
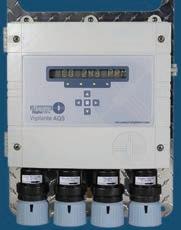
• MINE DEVELOPMENT | Canada Nickel starts work on Crawford FEED, eyes 2027 production
Canada Nickel Company has kicked off front end engineering design (FEED) at its flagship Crawford nickel project in northern Ontario, which it expects to bring into production in 2027.
Ausenco Engineering Canada, the engineering partner, will lead this development phase, which is to be finished by August. Data collected during the 2024 winter geotechnical program, which is nearing completion, will support FEED activities, Canada Nickel said.
“As we continue to successfully advance Crawford financing and permitting activities, we are confidently moving into this next phase of project development,” chief executive Mark Selby said, adding that the company is aiming for a mine construction decision by mid-2025,
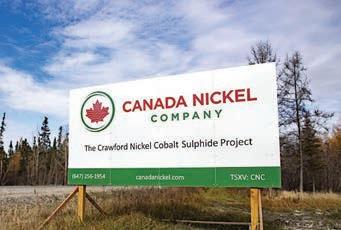
with first production by the end of 2027.
The proposed operation will consist of two open pits complemented by an on-site mill, to be completed in two phases to allow for throughput ramp-up. Total capital cost for the two phases is
• NEW MINE | Ascot begins milling at its Premier gold project in BC
Ascot Resources has begun ore processing at the Premier gold project 25 km from Stewart, B.C. Rock was introduced to the grinding circuit on March 31, and the first ore was fed on April 5, 2024.
The project is located on Nisga’a Nation Treaty Lands in the prolific Golden Triangle of northwestern British Columbia.
Commissioning activities continue on the gravity and leaching circuits, the carbon regenerations circuit, the elution circuit, cyanide destruction facility, and the gold room.
The tailings storage facility, new water treatment plant, tailings thickener, and pipeline systems are all ready for operation.
Currently, mining has begun from the Silver Coin and Big Missouri deposits to feed a refurbished 2,500 t/d
processing plant. Mining of the Red Mountain deposit will begin in year three, and then from the Premier deposit. Low-cost longhole stoping is planned for most of the mines, and ore will be trucked to the mill and waste will be returned underground as rockfill and cemented rockfill.
The refurbished processing plant uses conventional crushing, grinding, and gravity circuits followed by a standard carbon-in-leach (CIL) process to produce doré bar. An energy-efficient fine grinding ball mill and an additional preleach thickener to facilitate a finer grind of the hard ore. The tailings dam was also raised to increase capacity.
Total gold production from the Premier project will be 1.1 million oz. of gold and 3 million oz. of silver. CMJ
Make sure to send your press releases to: editor@canadianminingjournal.com
estimated at US$3.5 billion.
Over a 41-year project life, total metal production is calculated at 3.54 billion lb. of nickel, 52.9 million lb. of cobalt, 490,000 oz. of palladium and platinum, 58 million tonnes of iron, and 6.2 million lb. of chromium. First production is targeted for 2027.
Peak production at Crawford nickel mine is expected in year 11, when autonomous trucks and remotely operated shovels are fully integrated into the operation. Canada Nickel counts with the backing of top players in the mining and batteries market. The Toronto-based miner attracted the interest of Agnico Eagle Mines, Canada’s largest gold producer, which now owns 12% of Canada Nickel. CMJ
• TOLL MILLING | Talisker signs deal to toll Bralorne gold
ore a Nicola’s Merritt mill
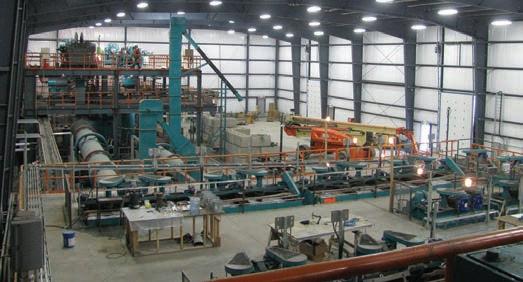
Nicola Mining and Talisker Resources have signed an agreement to toll ore from Talisker’s Bralorne gold project at Nicola’s Merritt mill, near the British Columbia town of the same name.
Nicola’s mill is the only processing plant permitted to accept third party gold and silver feed from throughout the province.
In February this year, Talisker drilled 86.5 g/t gold over 1.5 metres within a 9.6-metre section at 14.31 g/t at Bralorne project, where mining is to begin at the Mustang gold mine before the end of June.
Nicola’s flagship project is New Craigmont, a project including the former Craigmont copper mine adjacent to the mill. The mine ceased operation in 1979 and was dismantled in 1982. The property was consolidated, and Nicola gained 100% ownership in November 2015. Additional work is planned this year to increase both tonnage and grade at New Craigmont. CMJ
Greenstone

Equinox Gold says it is on track to produce first gold at the $1.2 billion Greenstone project in northern Ontario next month after starting ore processing this week.
The project, located 275 km northeast of Thunder Bay, Ont., is a 60:40 partnership with New York-based Orion Mine Finance Group. It aims to produce 400,000 oz. of gold per year and more than 5 million oz. over a 14-year mine life.
Equinox has stockpiled more than 1.5 million tonnes of ore at Greenstone and pre-crushed 70,000 tonnes of low-grade ore for early commissioning feed, it said. Progressively higher-grade ore is to be fed into the mill as production ramps up towards a planned throughput of 27,000 tonnes per day. Commercial production is targeted for this year’s third quarter.
• LITHIUM PLANT | Winsome reveals plan to repurpose Renard diamond plant for lithium

Perth-based Winsome Resources plans to buy the Renard diamond mine in Quebec and transform the plant to process lithium.
The company has paid $4 million for an option to buy the assets, which could help hasten development of its Adina lithium discovery in the Eeyou Istchee James Bay region.
Renard, developed and formerly operated by Stornoway Diamonds from 2016 until December last year, contains a permitted processing plant. Winsome says it may be possible to repurpose the plant to treat lithium ore.
The company can choose to exercise its option to acquire Renard any time after it is approved by the Quebec Court and before Sept. 30 for $52 million in cash or scrip. Extensions to the timeline are possible. Winsome would be bound to a specific payment schedule if it does exercise the option. CMJ
• MINE RESCUE | Norcat and partners unleash 5G underground with SafeSight’s winning technology
The Mining Technology Innovation Challenge, a collaboration betweenNorcat,Rogers,Dell Technologies, theOntario Vehicle Innovation Network(OVIN), and theMining Innovation Commercialization Accelerator(MICA), announced the successful conclusion of the Mining Technology Innovation Challenge, powered by Rogers 5G.
The challenge encouraged innovative start-ups and entrepreneurs from across Canada to develop underground mining technologies that utilize the capabilities of the Rogers 5G wireless private network at the Rogers Technology Centre of Excellence at the Norcat Underground Centre in Onaping, Ont. The solutions focused on underground safety, productivity, energy efficiency, and environmental impact and leveraged the ultra-low latency on the Rogers 5G network. SafeSight Exploration emerged as the challenge winner on May 30, 2024.
SafeSight’s 5G-enabled underground emergency response and mine rescue tool kit, DeepTraxx-5G and SafeScanner-5G, are illuminating a path towards a safer future for the entire industry. The winning technology received $100,000 worth of support, including $25,000 in funding for proof-of-concept development and testing at the Rogers Technology Centre of Excellence.
The integration of 5G technology in the mining sector holds great promise, offering high-speed connectivity and low-latency capabilities that can significantly enhance safety, communication, productivity, and operational efficiency in underground mines across the globe. CMJ
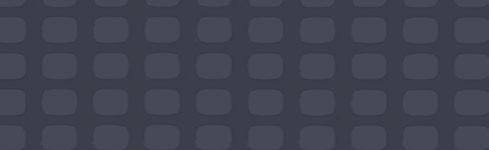
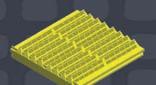


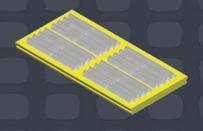

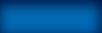

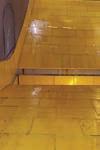


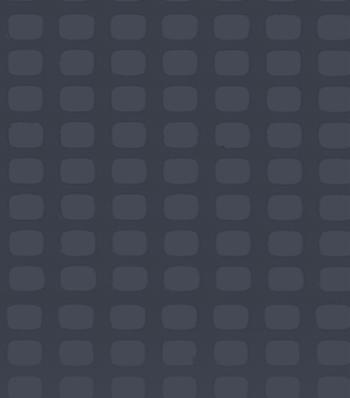
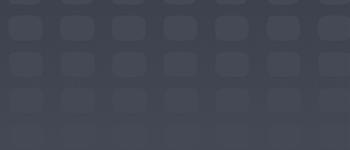
Meeting the metals mining shortfall
Moving away from fossil fuels to meet essential global carbon reduction targets means mining for metals and minerals will need to increase significantly over the coming years. Electric vehicles, wind turbines, solar panels, and overall electrification are all areas of increased demand, meaning metals like copper, iron, and zinc will be continuously required.
How the need for more metals will be met with our current infrastructure is uncertain. Taking copper as an example, production is predicted to reach a crisis point by 2030 with an annual deficit of five million tonnes. Stemming from a surge in demand driven by the exponential growth in electric vehicles and a myriad of other electrification applications, surpassing current production capacity, this is an alarming prognosis that would ultimately impede global sustainability goals.
Demand for refined copper to meet global decarbonization efforts is poised to nearly triple by 2050, compared to the 2020 production levels. This means the world is challenged with sustaining an annual increase in copper production of between 20% to 30% within the next seven years ― that is a capacity on par with the current outputs of major producers Chile and Peru combined.
Canada is viewed by the world as a frontrunner when it comes to the adoption of technologies for the energy transition. It has a healthy copper market, particularly in its province of British Columbia, highlighted by major projects, including one in which ABB provided electrification technologies and expertise with Copper Mountain Mining. The country regularly produces more than 500,000 tonnes of copper per year ― around 3% of the world’s production ― and its exports of the material are valued at approximately $10 billion per year.
Infrastructure investment: A ticking clock
New mining operations are an increasingly urgent necessity, and there are several industry projects awaiting decisions,
yet many investors are waiting until the price is right. With highly specialist equipment required and only a small number of industry players, the risk with this approach is a major bottleneck on the horizon.
On top of the challenge of timely investment, mining companies are processing ore grades that are increasingly low, with one tonne of copper in every 100 tonnes of rock at best. They typically do this with advanced and scalable grinding technology solutions. The industry workhorse for driving mills has been the gearless mill drive (GMD), which facilitates the extraction of copper from raw materials through grinding processes in the most efficient way.
ABB is the market leader of GMDs in the world and building these very large units takes time. This equipment challenge becomes two-fold when considering the forecasts of future ore grades being even lower than present, so much so that double the ore will need to be processed for the same amount of copper.
Increasing extraction and decreasing emissions
The integration of technology, alongside investments in new mining ventures, will be pivotal in ensuring that the world secures the essential metals required for the energy transition while maintaining cost-effectiveness and limiting the environmental impact of extraction.
The need to extract and process additional metals, while mitigating the already precarious and prominent issues associated with global warming this presents, is a formidable challenge for the sector. Mining currently contributes around 7% of total greenhouse gas (GHG) emissions globally, with diesel combustion in machinery alone responsible for half of this substantial environmental footprint.
Efforts by mining enterprises to reduce carbon encompass multiple initiatives to shift machinery from diesel to electric wherever feasible. Additionally, they are actively engaged in designing machinery fueled by alternative energy sources like
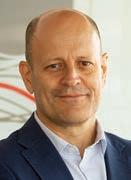
hydrogen and ammonia. This concerted endeavor aims to significantly curtail, if not eliminate, the reliance on fossil fuels in mining equipment such as trucks, loaders, and excavators.
Unlocking value with artificial intelligence (AI) and digital technology
The digital transformation of equipment, systems, and procedures, with the primary objective of optimizing operational efficiency within mining operations, is another crucial imperative for the sector. For instance, within the domain of GMDs, numerous predictive analysis systems have already been implemented to monitor equipment. These advanced systems enable companies to proactively address maintenance requirements, ensuring peak availability and efficiency for their machinery.
Artificial intelligence (AI) is ushering in a new era of innovation in mining equipment, empowering advanced performance and operational analyses. This transformative technology provides a more comprehensive range of insights, particularly in machine operation. This enables proactive measures to prevent issues and, importantly, facilitates indepth assessments of processed ore quality.
The shift towards digitalizing operations is imperative because of the heightened demand, prompting mining companies to prioritize maintenance procedures and preemptive failure mitigation. In this environment, even the slightest efficiency improvement holds significant value.
Embracing digital transformation becomes not just a necessity but a strategic advantage, enabling mining entities to proactively address challenges, optimize processes, and ultimately enhance overall operational performance. It is this evolution, alongside investments in novel mining ventures, that will help the world secure the essential metals required for the energy transition. CMJ
Wilson Monteiro is global business line manager for gearless mill drive at ABB.
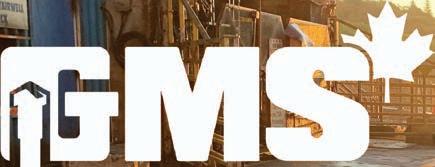

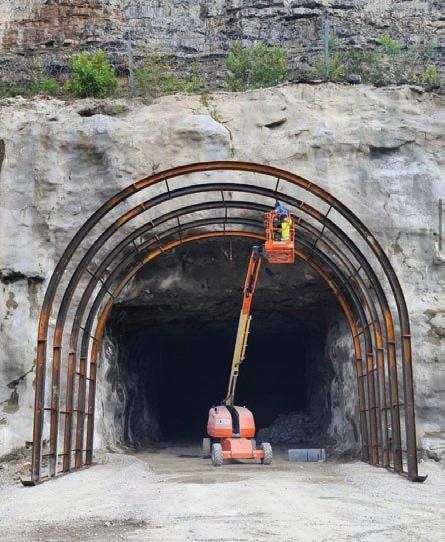
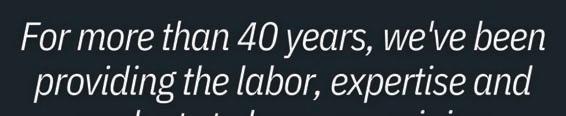
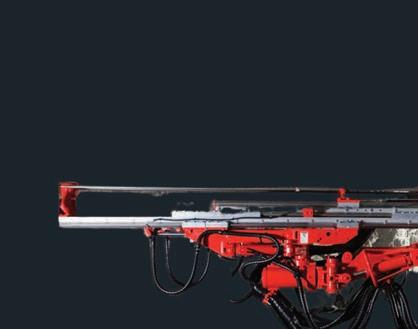

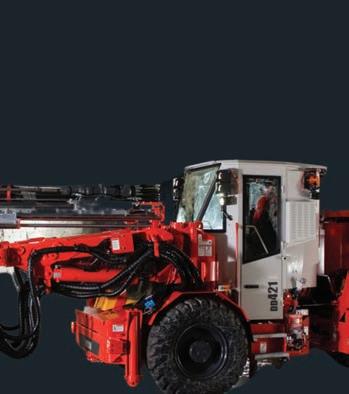
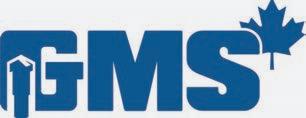
ARE RAIL TRANSPORT COSTS REALLY FOUR TIMES HIGHER?
Our analyst’s review for rail transport over the past decades notes the abnormally large increase in the cost to move rail freight continues and new rates now persist for a third year. The new cost regime in transportation appears a more permanent fixture since the initial impact of Covid-19 continues unchanged. What is happening or what might be a cause of the much-steepened upward increase in cost seen since 2020? Figure 1 (and accompanying table) compares rail transport cost for distances of 800 km and 1,600 km (in dollars per ton/mile) for the initial period 2004 to 2020, which then bends upward to 2023 in the recent period.
Initial period. From 2004 to 2020, the rise has been along a well-defined trend. The black curve for the 1,600-km distance helps to explain the rising trend. The average rate for 1,600-km cost trend from 2004 up to the time of Covid-19 rises at a smooth annual rate of US$0.0043 per tonne/mile each year (black dotted line depicts). Many unusual events coincided with Covid-19: schools and businesses shut down, and ocean freight was backlogged. The return to normal required about a year or two, but the rise in rail transport cost did not normalize, though it seems more permanent.
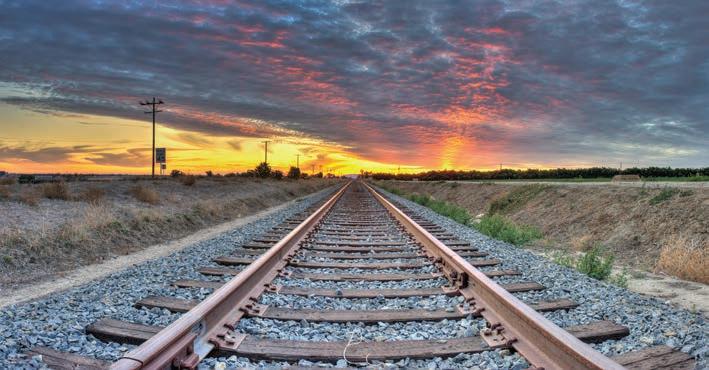
Recent period. After 2020, the initial trend no longer applies as the curve departs to a much steeper annual per tonnetonne/mile trend. What is unusual is the much steeper rise in the cost for each of the green and black curves after 2020 (black arrow), with cost climbing from US$0.107 per tonne/mile in 2020 to US$0.160 per tonne/mile in 2023. The year-over-year costs are increasing at a much faster rate per year in the recent period, with increases more than four times larger than the initial 2004-20 period because the year-over-year price trend climbed from US$0.0043 (the slope

of a best-fit dotted line) pre-2020 to US$0.0178 in the post-2020 period. This means the cost of transporting a tonne of freight by rail for a 1,600-km distance climbed from US$98 per tonne in 2018 to US$160 per tonne in 2023. Overall, this means that costs may double every two to three years rather than doubling each 10 to 15 years.
The rise in year-over-year trend is much larger for the shorter 800-km distance when comparing the recent period to the initial period. The annual rate of increase for the initial period was US$0.126 per tonne/mile in 2020 compared to US$0.196 per tonne/mile in 2023. This is a more than 5X year-over-year increase to move freight for the 800-km distance with costs rising from US$57 per tonne in 2018 to US$98 per tonne.
What factors might explain the sudden upward cost trajectory? Is other information available to support, deny or verify the increases in cost? The following four charts explore related data to find an explanation.
Data for line-haul railroads from U.S. Bureau of Labor Statistics below (Fig. 2) also confirms a change is underway as seen in observations discussed. The BLS producer price index for line-haul Railroads rises above the trend line after 2021 (black arrow) following the dip below trend during 2020-021. The pro-
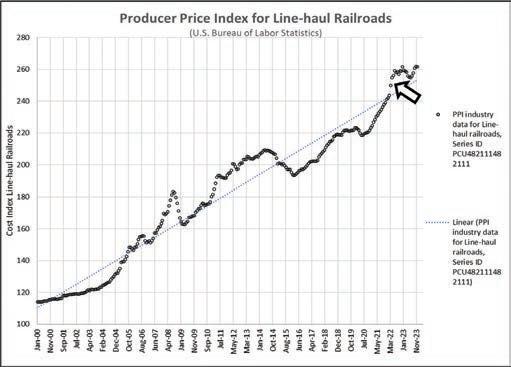
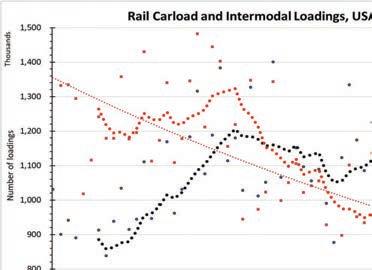

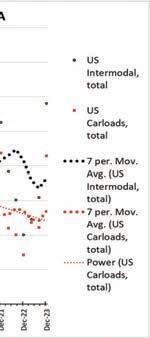
The largest railroad companies earn revenue margins of 15%, and returns on capital invested are in the order of 12% to 14%.
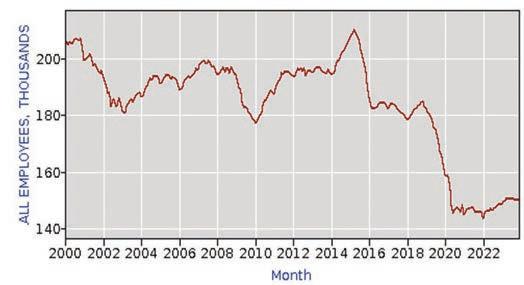
ducer price index indicates that business intensity has increased, by either price or volume but is not more specific as to a cause. Either one or both of these two explanations are possible; noticeable as first, an increase in volumes of business or second, an increase of rates per unit shipped. More detail is revealed from the examination of the monthly rate of
economic recovery underway in the recent period. This analysis also shows that business intensity in the 2020 postCovid recovery exceeded rates following the 2008-09 recession. Rail business accelerated at remarkably high rates from the beginning in June 2020 to a peak in January 2023 before returning to
Canada, and Mexico for rail by carloads and intermodal units. Loading data in Fig. 3 shows monthly loadings averaged by quarter year of rail cars and intermodal units (in thousands) at U.S. and Canadian railroads (Assoc. of American Railroads, by permission). The curves show the number of carload (bold red
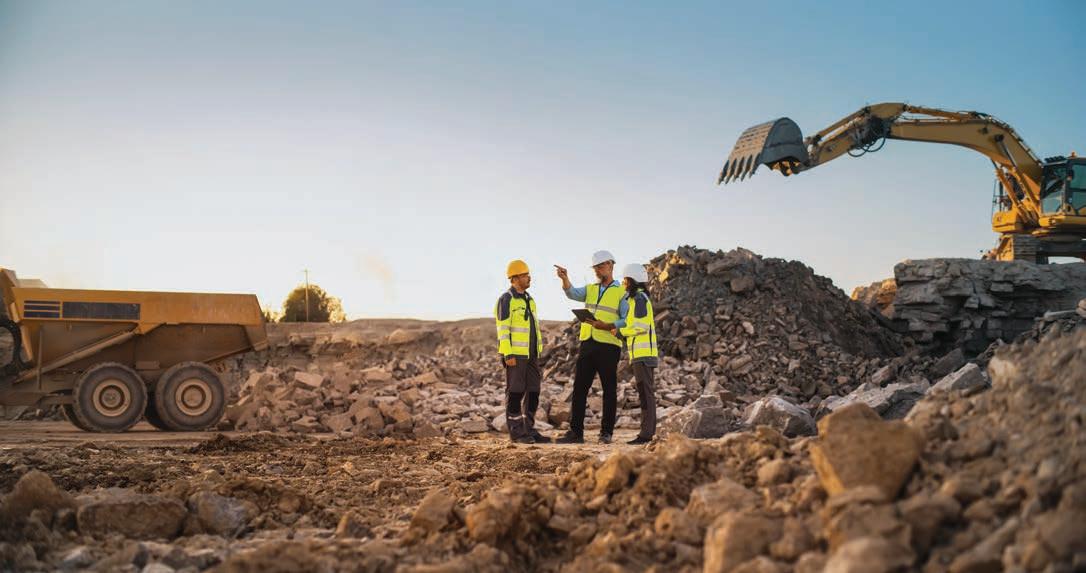
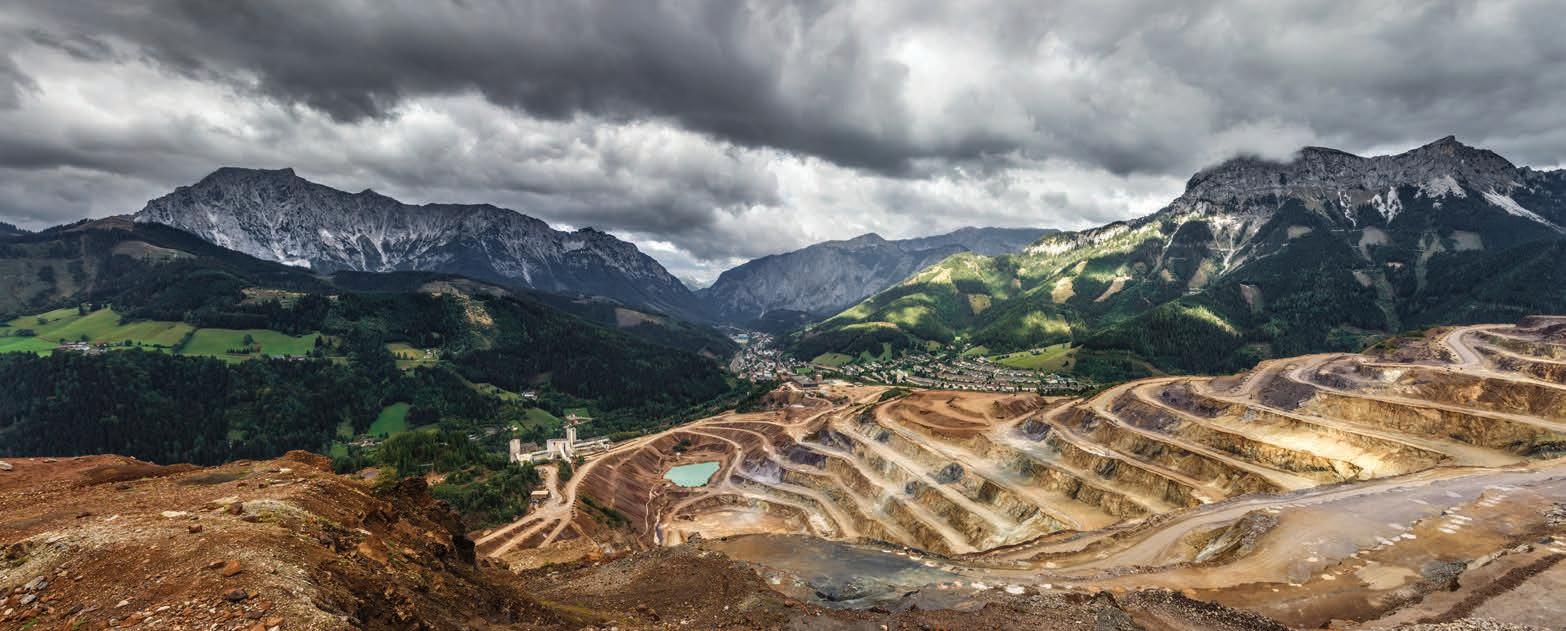
with the downward trend more pronounced from 2015 to 2023. The thin red dotted curve is a best-fit trend of rail loadings from 2007-23 to show loadings have decreased by 24.6% from an average of 1.3 million carloads per month in 2008 to an average in 2023 of 995,000 carloads per month, with the January 2024 count at 1.0 million carloads. Business volume has clearly decreased. A nearly

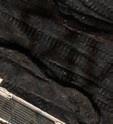
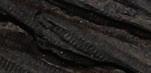

identical but subdued downward trend in railcar loadings is also underway in Canada with a decrease in volume of 12.5% from 2015 to 2022.
An explanation for the initial question of the sudden upward cost trajectory now favors rate or price increases as the cause for sharp increases in cost, as loading data show shipper volumes are eliminated as a cause.
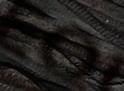

Other factors in rising rail costs



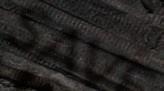
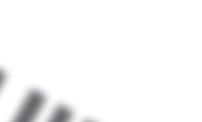
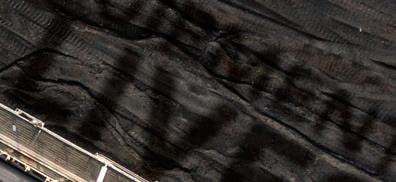
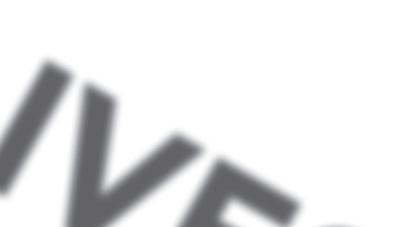
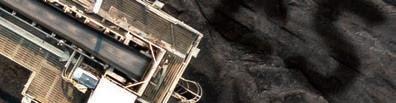

OF DOLLARS
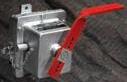
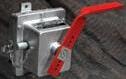
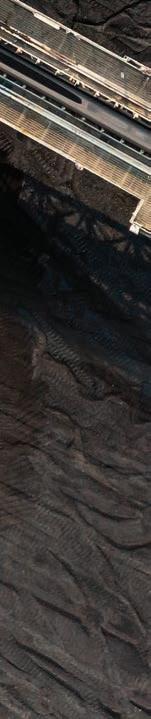
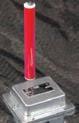
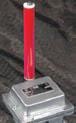
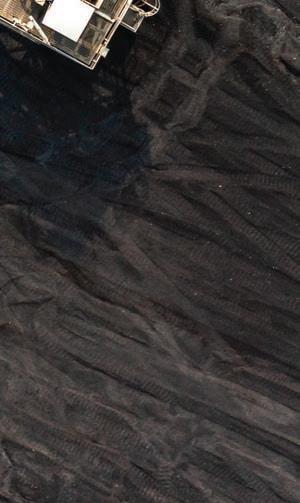


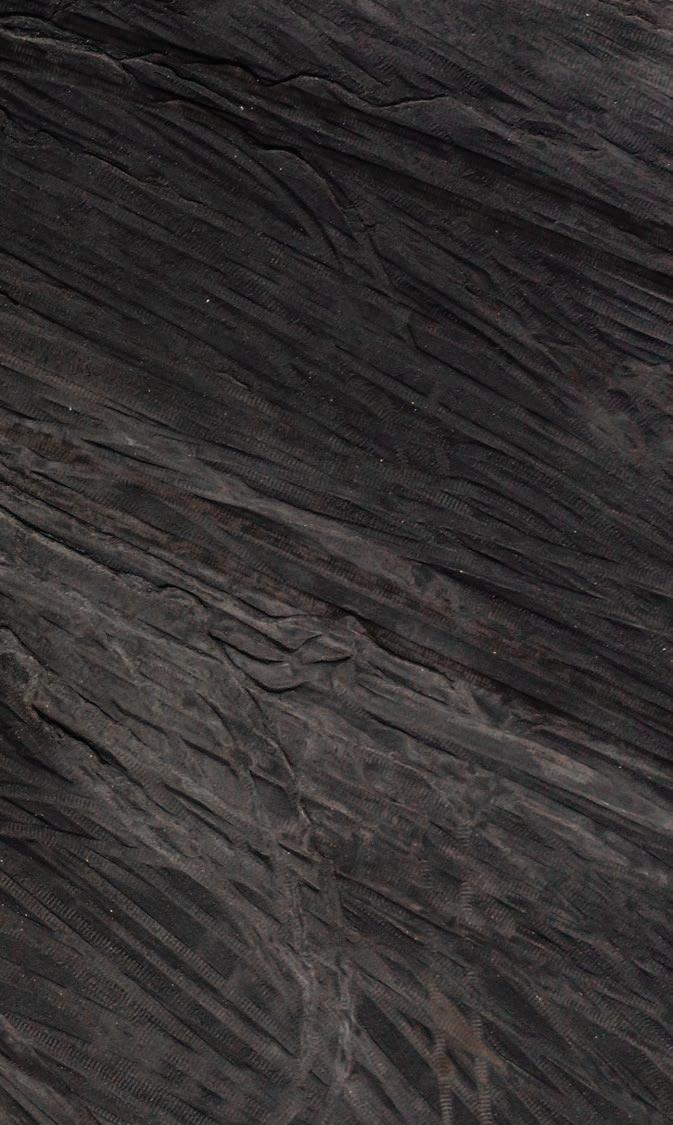
Is there more to the saga of high and increasing costs in railroading? The largest railroad companies earn revenue margins of 15%, and returns on capital invested are in the order of 12% to 14%. Data was not available on earnings of railroad employees, although employment in the industry (Fig. 4) has fallen from about 190,000 before 2016 to about 145,000 today. Class 1 railroad employment (not including warehousing) was 122,343 in December 2023. Freightwaves. com says the cost to build railcars has risen from US$50,000 in the past to US$150,000 today with about 100,000 more rail cars in service today at 1.6 million compared to 1.5 million in 2009. About 17% or 339,000 railcars remained in storage (not used or idled) of the total of nearly 2.0 million railcars (AAR Oct 2021). Perhaps the most significant factor is that railroads now must operate under the rule of precision scheduled railroading (PSR) to protect against high speed and to reduce accidents and increase profits or operating ratios. Costs of implementing PSR are borne by each railroad. Operating ratios have been sub-60% during the years-long period to implement PSR. Railroads continue to report that PSR provokes disruption at the six major U.S. and two major Canadian railroads and negatively affects service. To reach sub-25% ORs, chair Martin J. Oberman of the Surface Transportation Board says railroads must cut employment. This seems to be underway (Fig. 4), but the result translates to higher costs borne by rail shipping customers.
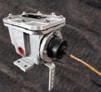

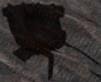




The reason for the upward trend to explain higher cost is complex and no one reason can be identified as a single cause, so the cause involves multiple factors. It is clear that increases in cost or rates best explain and translates to the much higher costs charged by railroads today.





More information to address the question of or to explain high cost is available for the 2023-24 period entitled 2023-2024 Update – Rail Industry and Freight Rates is provided in Appendix B-Transportation (TR) a chapter in Mining Cost Service of CostMine.com. CMJ
Dave Boleneus is a seasoned analyst with over 45 years of professional experience in major mining companies, oil corporations, and esteemed consulting organizations globally.
Sustainable mining finances: Exploring costs and liabilities
When done correctly, sustainable mining should save money and reduce emissions
The mining industry is changing, and mining professionals can spur progress on sustainability goals. After all, engineers play a vital role in achieving a sustainable vision. In addition to designing for safety and reliability, they can also include environmental, social, and governance (ESG) considerations. In doing so, engineers can integrate sustainable design elements into their daily work.
Focusing on sustainability gives companies a leg up on their competition. How? Sustainable decisions help a company meet its environmental goals, they comply with regulations, and they boost the bottom line thanks to cost savings from operational efficiencies. All this results in increased production. This is vital to meet the demand for critical minerals in clean energy technology.
Corporate leadership teams must drive goals focused on sustainability. It all starts with a future vision. Then, it builds with interim milestones and projects that will move the needle. But the goals must be supported with the investment and people to make it happen. Let us explore the finances behind sustainable mining below.
What is a carbon credit?
By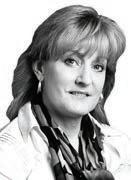
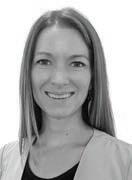
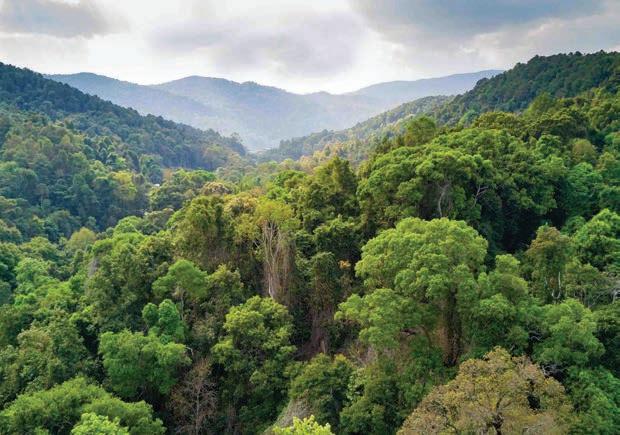
amount of emission reductions. The credits are then recorded and can be traded on the carbon markets.
We often refer to green credits as carbon credits or environmental certificates. They represent a reduction or removal of greenhouse gas (GHG) emissions. Mining companies can earn green credits by reducing carbon emissions. They can also earn them by sequestering carbon. Both actions contribute to sustainability.
Here is how carbon credits typically work:
1 | Emission reduction projects: Mining companies can invest in projects that reduce or offset their carbon footprint. This could mean using energy-efficient technologies. It could mean supporting reforestation projects. It could also mean capturing and storing methane emissions.
2 | Verification and certification: Next, the project undergoes a verification process. This helps confirm that the claimed emission reductions are valid. Independent third parties often certify these projects; they provide credibility to the achieved reductions.
3 | Issuance of credits: Once verified, the mining company receives carbon credits. The number of credits links to the
4 | Trading and compliance: Other entities looking to offset their own emissions can purchase the credits. In some cases, it is required that companies offset a portion of their emissions so they can use credits for compliance. Because of this, carbon credits can be sold in either the voluntary or compliance carbon market.
For a mining company, embracing green credit programs contributes to environmental sustainability, and it can also generate revenue. So, the company can make money from its decarbonization efforts. Then, it can invest in more sustainable mining practices. This financial incentive aligns with broader trends in corporate responsibility and sustainable development.
What about financial green premiums and brown penalties?
Green premiums and brown penalties are financial terms tied to environmental stewardship. Green premiums are incentives for environmentally friendly practices. Brown penalties are costs or fines associated with harmful practices. Green premiums and brown penalties both exist in the mining industry. Green premiums are a clear financial advantage. They benefit companies that adopt sustainable practices. This can include
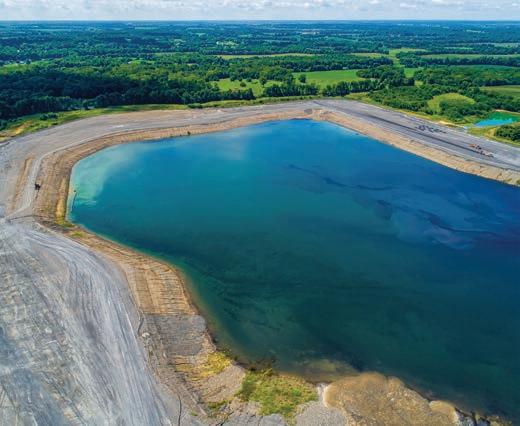
Mine
water management is a good opportunity for mining companies to showcase sustainable efforts and earn green premiums. For example, many sites are recycling or treating the water, showing water stewardship. CREDIT: ADOBE STOCK
using cleaner technologies, reducing carbon emissions, or applying eco-friendly processes. For example, mining companies that adopt sustainable practices might receive higher prices for their products. They could gain preferential access to markets, and they could attract environmentally conscious investors. These premiums reflect a market willingness to reward responsible actions.
Brown penalties are the costs that companies face if they engage in environmentally harmful practices. Think pollution, deforestation, or poor tailings management. Mining companies facing brown penalties might experience increased regulatory scrutiny or legal challenges. It could also lead to fines or less access to certain markets. Investors and consumers may shy away from companies with poor environmental records. This leads to a financial disadvantage.
Green premiums and brown penalties are economic outcomes, and they are linked to the practices of mining companies. It is key for miners to put positive practices in place; it is also important to limit harmful ones. These financial incentives reflect a broader shift towards responsible resource extraction.
Cost savings through recruitment and retention
It has been said before, but it bears repeating; Employees want to work for companies that are responsible. This is especially true when it comes to the environment. According to Gallup, Gen Z and millennials now make up nearly half (46%) of the full-time workforce in the U.S. These new generations care more about climate change and social equity than the workforce before them. Meaning? Companies that champion environmental and social efforts are more attractive to potential employees. They are more likely to get the top talent.
A culture of sustainability can also increase employee retention. This saves money and maintains a company’s intellectual capital. An employer of choice must prove how they are improving lives today and for generations to come. ESG-focused values are appealing for many employees — especially millennials —
who want their work connected to a higher purpose.
This is the ideal time for mining companies to tap into the new generation of workers. It is also a great time to further the ESG initiatives and achievements. This also means fostering a fresh view of the mining industry within society. Mining is changing its way of working. That is, being responsible and sustainable. It is an industry that is sourcing the critical minerals we need for green technologies, embraces workforce diversity, and engages with community. Mining is an industry that puts people first.
Making the cultural shift
One of the biggest obstacles to sustainability is a classic culprit: Money. Many people recognize the financial benefits of sustainability, but some still view it as an expensive undertaking or just a box-ticking exercise. Some may also think that these practices increase risk through downtime or less output.
However, it is important to measure the long-term view of the business, and to consider the liabilities from not operating sustainably. One example is increased costs for mine closure, or it could be something harder to measure, such as reputational damage or increased risks in the business.
Responsible miners have strong relationships with communities, their workforces, customers, suppliers, and governments. This yields a smoother business operation. Thus, it is a financial benefit as much as it is a social one.
An effective way to start a cultural shift is helping both leaders and employees recognize the financial and social upsides to sustainability. When done right, sustainable designs drive operational costs down. They also improve recovery rates. For example, a copper mine in Arizona completed a debottlenecking study to review their operation. During this exercise, they realized they could save energy costs by modifying their grinding and crushing circuit. How? The modifications helped reduce energy use while also increasing their recovery. Sharing success stories like this can teach others that sustainable solutions bring cost benefits to the business.
Everyone has a role to play in decarbonizing mining
Engineers can lead the charge by using innovative and sustainable solutions in their projects. The result is operations that deliver on environmental protection, decarbonization, safety, and the returns to stakeholders. The message is not hollow. The outcomes prove it.
Sustainability is not a target buried within an annual report. It is a moral obligation. It is a business imperative for corporations. It is the foundation of commitments, strategies, and metrics that are tracked and reported annually, and it is achievable, but only when supported with the funding and the people to make it happen. CMJ
Samantha Espley has over 30 years of experience, with a range of expertise encompassing mining operations, capital projects, mining, and mineral processing technical services. She serves on the Stantec mining leadership team as a senior advisor.
Lauren Meyer is a geotechnical engineer based out of Stantec’s Fort Collins office. She is passionate about including sustainability in her everyday work and is committed to enhancing her clients’ ESG goals.
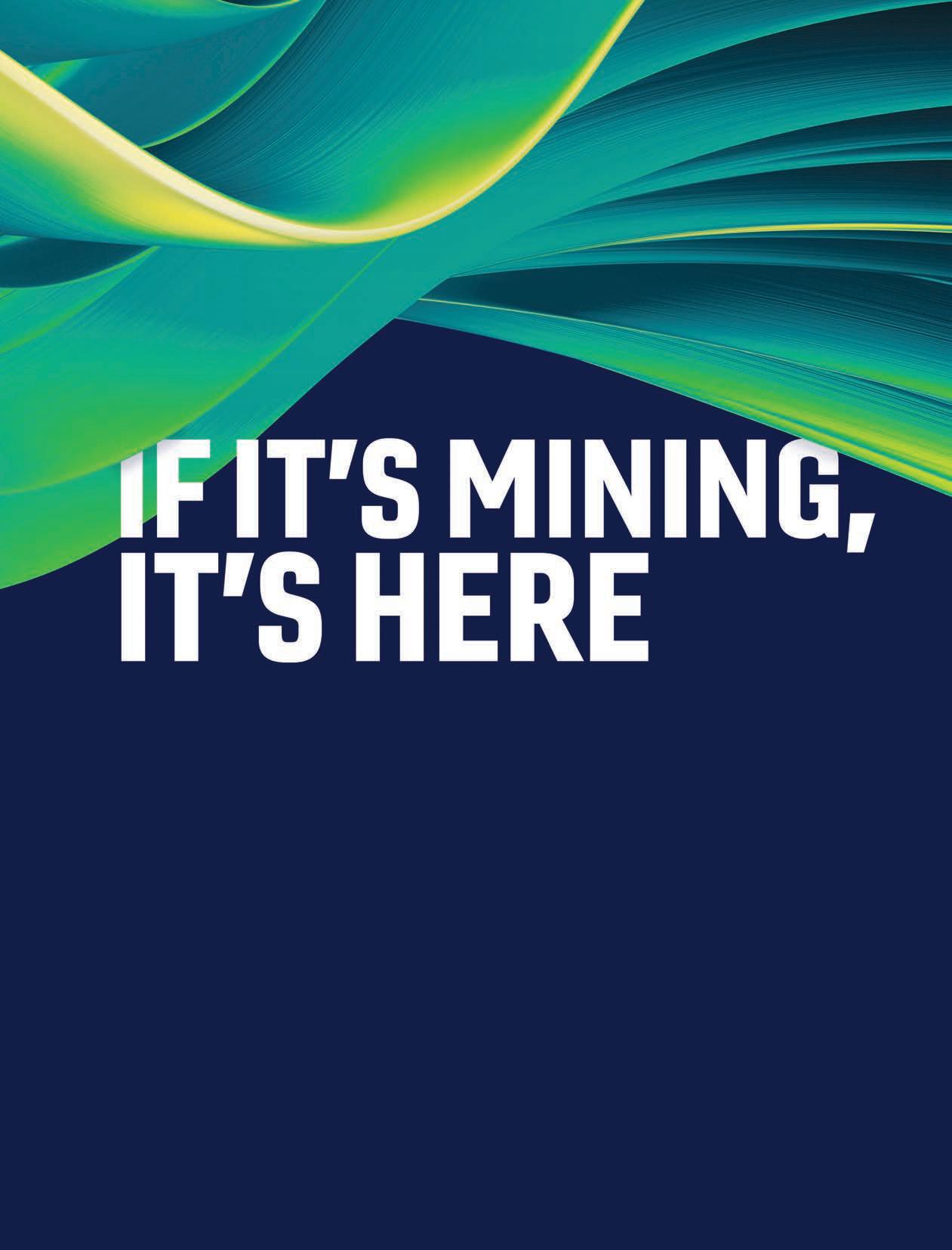
UNLOCKING BUSINESS POTENTIAL
By Jason Clifton and Karen D’Andrea
THE ROLE OF MINE ELECTRIFICATION IN A DIGITAL ERA
In envisioning the mines of the future, electrification emerges as a transformative cornerstone, heralding a paradigm shift in the mining industry’s operational landscape. Gone are the days when diesel-powered machinery dominated the extraction process. Instead, a new era of sustainability and efficiency is dawning, powered by electric technologies at the core. North American surface mines started testing out heavyduty electric equipment — mainly haul trucks attached to electric trolley lines — in the 1990s. Additionally, Canada was one of the first countries to introduce battery-powered electric vehicles (EVs) to underground mining in 2012.
Electrification promises not only to revolutionize the operational dynamics within mines but also to redefine their environmental footprint, aligning with global efforts towards decarbonization and sustainability. It is clear that electrification will serve as a primary component of the mines of tomorrow, signalling a new era of innovation, efficiency, and environmental stewardship by leveraging synergies between other technologies, connecting business and operational key performance indicators (KPIs) and aligning talent and capital.
Synergizing electrification with mining tech
When thoughtful electrification programs are combined with those addressing analytics, autonomous mining, software, and IoT, there is synergy driving needed disruption in today’s mining industry. Rather than addressing electrification in a vacuum, a holistic view of the entire ecosystem of technologies
being considered for use in current and future mine planning and operations scenarios is necessary to understand how the benefits of each can be optimized and accelerated. Assessing and planning for an electric mobile fleet transition without an outlook on the automation roadmap, or preparing for fleet management data and analytics software, is doing a disservice to the potential of your ultimate fleet.
Recognizing that the current vision of the fleet and its role in future mining operations will evolve over the next five years can provide planners with reassurance, understanding that market readiness may not always match their business readiness. In an industry traditionally reliant on proven technologies, adopting a mindset focused on progress rather than perfection is crucial for achieving tangible advancements.
By strategically integrating the technical and commercial dimensions of electrification with cutting-edge technologies and a firm commitment to meaningful impact, we can propel future outcomes, drive bottom-line growth, and foster genuine sustainability.
Connecting electrified operation KPIs to business metrics
The KPIs of electrified fleets and, in turn, operations hold significant relevance to overall business KPIs. For instance, understanding the energy consumption patterns during different phases of production can reveal opportunities for optimization. Aligning energy (i.e., vehicle usage) with production schedules is inherent to minimizing waste and reducing costs in any oper-
ation. Moreover, identifying areas of high energy consumption relative to production output can highlight inefficiencies that may require attention, such as vehicle malfunctions or suboptimal procedures.
However, beyond this, there is a notable gap in comprehending the full business value of an electrified fleet. There is great opportunity to translate conventional electric vehicle KPIs into pertinent metrics for the mining sector. This understanding underscores the necessity to adapt methodologies and operational approaches to maximize the value extraction in mining operations.
Decarbonization, talent, and capital alignment in electrified mines
Genuinely integrating environmental, social, and governance (ESG) principles into any business strategy is crucial. Companies with a clear sense of purpose are three times more likely to retain employees and outperform the S&P by ten times. However, merely having a purpose is not sufficient; it must be communicated effectively both internally and externally.
Incorporating actions that generate genuine long-term value and focusing on ESG factors like electrification into your talent narrative is essential. Engage your employees by offering opportunities to contribute to the discussions and innovate alongside leadership with appropriate change management and employee readiness programs. Foster a culture that actively promotes and celebrates open innovation daily, going beyond simply welcoming bottom-up ideas.
Expanding on the importance of people, we are navigating a landscape where consumers are increasingly thoughtful and
conscientious. Their preferences significantly influence the capital accessible to mines of every scale. As outlined in this year’s EY’s Top 10 Risks and Opportunities in Mining and Metals, capital rose to the number 2 spot as the mining sector grapples to fund the expansions required to meet increasing demand for minerals crucial to the energy transition. However, miners will need to balance continued economic returns with more investment in digital, decarbonization, and of course ESG.
In today’s rapidly evolving mining landscape, electrification emerges as a transformative force, synergizing with cutting-edge technologies to drive disruption. Yet, addressing electrification in isolation risks missing out on its full potential. A holistic approach, integrating electrification with analytics, autonomous mining, software, and IoT, is imperative for optimizing benefits across mining operations. This integration demands a forward-looking mindset, recognizing that the role of electrified fleets is evolving, necessitating alignment with both short term and long-term market and business readiness.
As electrification becomes increasingly central to mining operations, connecting electrified operations KPIs to broader business metrics becomes essential. Aligning electrification-enabled decarbonization efforts with talent retention and access to capital becomes critical for driving growth and fostering genuine sustainability for the industry and for future generations.
CMJEY Canada’s consulting practice includes Jason Clifton as a partner and Karen D’Andrea as a manager. To learn more about main electrification, visit: https://www.ey.com/en_ca/mining-metals
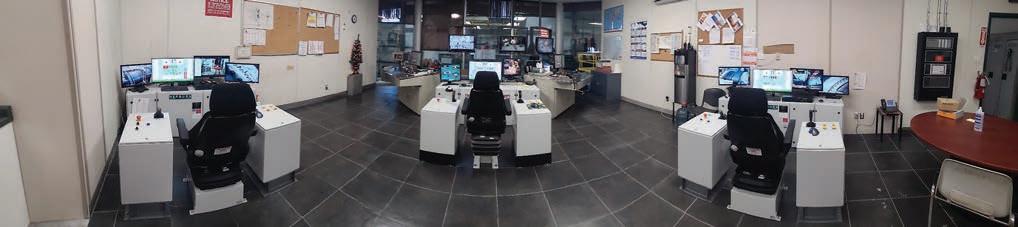

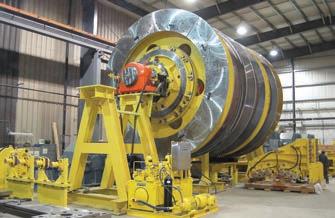

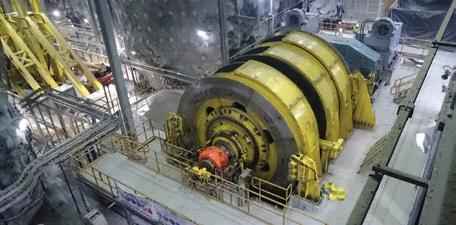


ENVIRONMENTAL TECHNOLOGIES CAN HELP MINING COMPANIES
NAVIGATE THE NEW GRI SUSTAINABILITY STANDARD
As we move towards net-zero, the vital role of the mining industry is becoming increasingly apparent. The sector must simultaneously increase production of minerals to sustain decarbonization and reduce its environmental impacts. Despite this difficult position, new biodiversity monitoring technologies are proving to be useful tools to tackle this challenge.
Mining plays a key role in the transition to net-zero because its products are central to the production of clean energy and technology. The International Energy Agency (IEA) has suggested that mineral inputs must increase by fourfold to meet the goals of the Paris Agreement. But the time from discovery to commercial extraction will still take some companies 16 years. Closing this gap will be vital to meet decarbonization goals.
Historically, some mining operations have contributed to environmental degradation through issues like contamination and pollution of local ecosystems. This is especially relevant given that 20% of existing mines are biodiversity hotspots, as tracked by the MSCI ACWI Investable Market Index (IMI). As a result, an accurate assessment of the impact of existing and future mines on the environment is crucial.
The Earth’s biodiversity remains our greatest asset, not only acting as “our strongest natural defence against climate change,” according to the U.N., but as a fundamental means to our global economy. More than 50% of global GDP is moderately or highly dependent on nature as estimated by the World Economic Forum. Thus, adopting sustainable practices is not only sensible for businesses from an environmental perspective, but also necessary from a profitability standpoint. Today, risking nature poses an economic risk, with four of the top five threats to business in the next 10 years being environment related.
In Canada, where half of the world’s publicly listed mining companies are based, the minerals and metals sector represents 4% of the country’s gross domestic product (GDP) with a value of $91 billion in 2021. Protecting this GDP from nature-related risk is vital, and initiatives led by the Canadian government such as the 2022 Critical Minerals Strategy reflect this need.
New standards within mining
Beyond governmental initiatives that aim to regulate the mining industry, there are other independent bodies that influence the sector. In early Feb. 2024, the Global Reporting Initiative (GRI) launched its landmark “Sustainability Standard for the Mining and Extractives Sectors.” This standard aims to guide mining organisations through their difficult positions of providing essential minerals for modern society while actively working to lessen the impact of their activities on the environ-
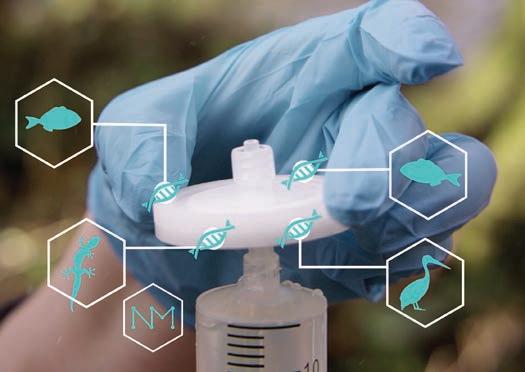
ment and local communities.
This is a pivotal moment for the industry and a welcome development for many stakeholders, offering a robust framework for reporting on ESG impacts that will elevate accountability and transparency practices. Successful navigation of the standards will aid companies in managing stakeholder relationships and building trust to make the industry more resilient to nature-related risk. As Carol Adams, chair of the GRI’s Global Sustainability Standards Board (GSSB), has said, “From a sustainability standpoint, the position of mining is complex, in that it is both part of the solution and the problem.”
The new GRI standard provides reporting guidance for the transparent sharing of certain material topics such as preserving biodiversity and engaging communities. However, to implement the sustainability reporting that the GRI standardizes, companies must establish a baseline for natural capital at a site level. Through this assessment, nature can be brought into the value chain, allowing mining companies to assess the impact of activity and ultimately limit nature-related risks.
However, because of the variety of nature data that can be collected and analyzed, it can be unclear which measurements are best placed to give an accurate picture of the state of biodiversity. The GRI standards aim to provide guidance and metrics to aid in the ability of mining companies to have a comprehensive understanding of reporting needs. Importantly, the GRI emphasizes the need for data to be reliable and reproducible if possible and provides examples to further support the industry.
In January, Rohitesh Dhawan, president and CEO of the International Council on Mining and Metals (ICMM) announced adherence to the biodiversity-preserving commitments set by
the Taskforce on Nature-related Financial Disclosures (TNFD) at a Nature Positive Initiative event in Davos. In this context, the announcement of the Global Sustainability Standards for the mining sector has not come as a surprise. It has simply reinforced the difficult position the mining industry is in to maintain regular activity whilst adhering to the latest biodiversity regulations required to halt and reverse nature loss by 2030.
Nature-based solutions
Currently, companies are held back by the lack of specialist knowledge, scalable solutions, and the data-gap in biodiversity monitoring. Fortunately, technologies, such as environmental DNA (eDNA) have enabled companies to measure nature in an accurate, cost-efficient manner, and on a large scale. While the technology is cutting edge in terms of its transformational impact on biodiversity monitoring, it has been used for over a decade, and is well-established and thoroughly vetted. In the GRI 101: Biodiversity 2024 guidance document, eDNA is listed as a primary data method for reporting on biodiversity.
Small traces of DNA left behind by living organisms can be captured from environmental samples and used to survey single species or whole communities. Surveyance of eDNA allows mining companies to identify at-risk, invasive, or protected species, along wider biological groups in the site of interest. These analyses of eDNA can also be utilized to set a baseline from which they can monitor nature restoration progress over time.
The simplicity of eDNA methodology is highlighted in one way by the ease of sample collection, which is frequently done as a citizen science project and aids in community engagement. This adheres to the new GRI standard that emphasizes community engagement as part of reporting. In many projects, com-
munity members or students in local schools can get involved, so this technology enables community engagement, one of the new requirements mining companies should take part in as per the latest GRI standard. This enables companies to not only contextualize biodiversity data to report back to stakeholders, but also to actively involve local communities, granting social licence to operate.
The combination of this eDNA technology and other nature intelligence technologies aimed at capturing nature’s complexity, such as geographic information systems (GIS), bioacoustics, and drones, is enabling businesses to gain a clear picture of biodiversity at any given time and location. Many companies, including Anglo American, Sínese, and Rio Tinto have already used these technologies to support their drive to nature-positivity through an understanding of the biological risks of their business’ activities.
It is hugely promising to see how these technological innovations can help the mining industry further its sustainability and nature goals. The adoption of the GRI Sustainability Standards will help the mining industry fulfill the environmental reporting valued by regulators, stakeholders, and the public. The rapid scaling and deployment of technologies such as eDNA will be the key to improve due diligence, producing transparent environmental assessments, and enable mining companies to engage with local communities, easing the pressure of regulators and the public on the sector. CMJ
Rachel Mador-House is an environmental geneticist with over 15 years of experience. She now utilizes her extensive molecular genetics knowledge to further biodiversity monitoring at NatureMetrics as the Head of Scientific Affairs for North America.
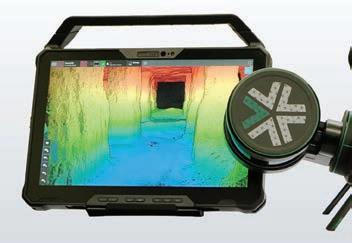
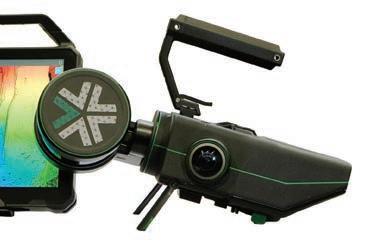
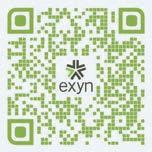

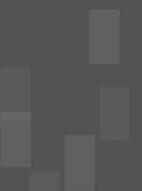

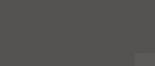
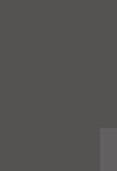

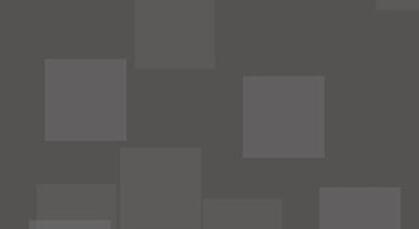


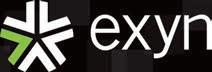
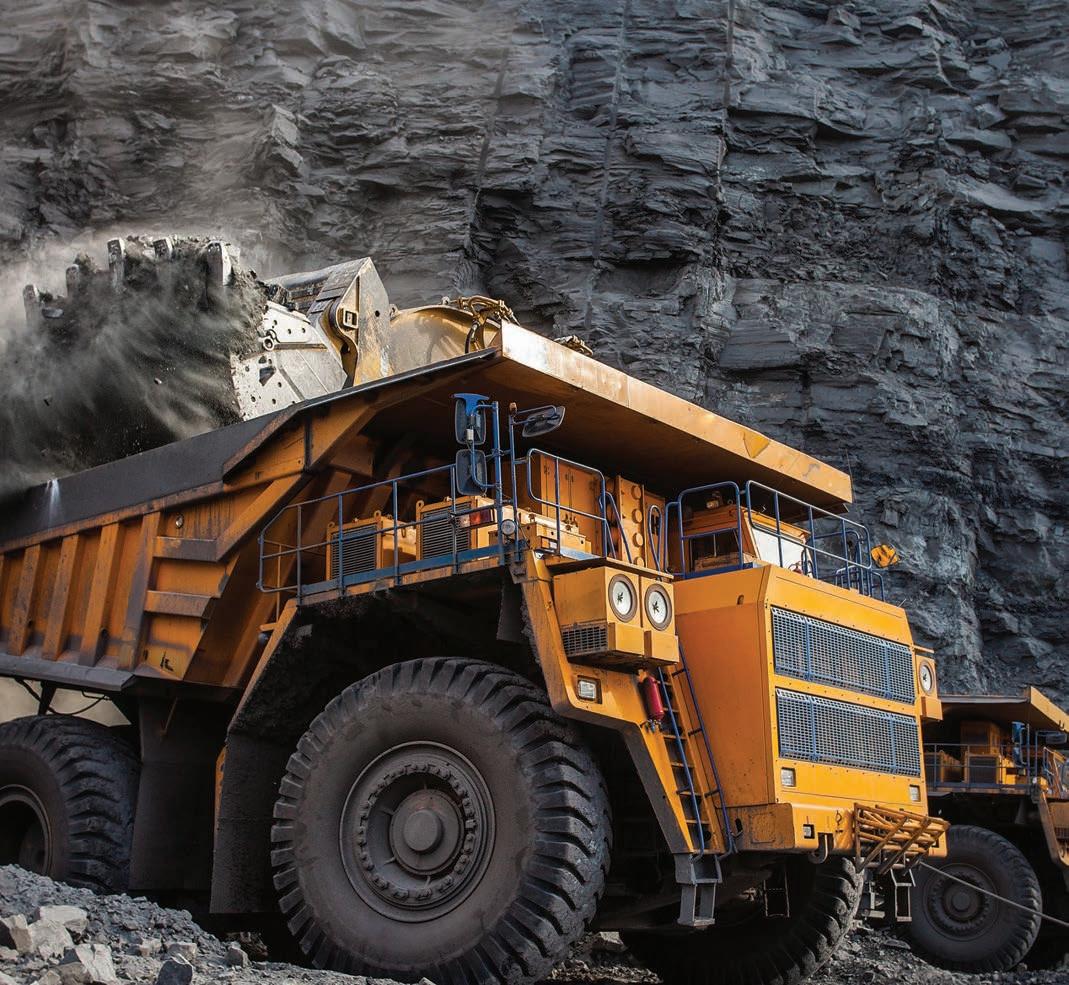
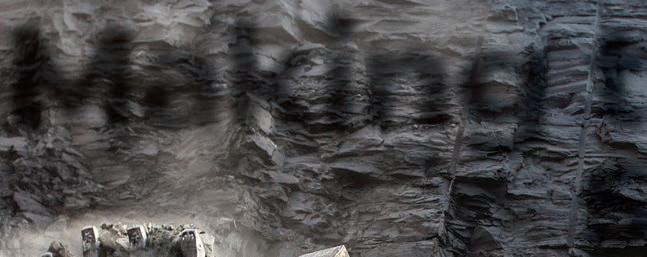
Making the seen



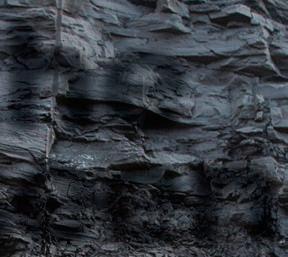
Artificial intelligence provides real-time visual insights into mining operations unseen
For the mining industry, continuous innovation is required to optimize production, lower costs, and improve the safety of workers. Artificial intelligence (AI) and machine learning (ML) technologies can help mining companies adapt to a changing landscape of unpredictable events. AI has many benefits for the industry; however, it is still very new and there is a lot of work that needs to be done while applying it, which requires a robust foundation of planning, research, communication, and change management.
In a previous article last year, we discussed how AI-enabled data analysis can assist in more efficient extraction of mineral deposits while minimizing environmental damage. AI is
increasingly being used to map more exploration data and streamline the process of discovery.
Additionally, AI-enabled mining innovation for other aspects of the mining supply chain continues to move forward. Eventually, AI will revolutionize the mining industry.
Moreover, extraction innovation is focusing on remote tunnel monitoring systems which allow monitoring of mining tunnel integrity. Remote monitoring system technology uses AI to determine the viability of digging the tunnels deeper to access additional mineral deposits. These technologies can help propel mining into the future by maximizing both the extraction of resources and safety in old and new mines.
A few examples of the various ways AI can help the mining industry include the following:
• Mineral exploration: Analyzing large datasets, including geological and geophysical data, to identify potential mineral deposits and expedite exploration efforts.
• Predictive maintenance: AI-powered sensors and ML algorithms can detect potential equipment failures, thus reducing downtime and increasing overall efficiency.
• Autonomous vehicles: Autonomous vehicles (powered by AI) can improve safety and efficiency in transportation and hauling operations.
• Process optimization: Optimizing mining processes, such as crushing and grinding, to reduce energy consumption and improve yields.
• Safety monitoring: Sensors and cameras can monitor mines for safety hazards and alert operators to potential risks.
• Environmental monitoring: Monitoring and mitigating environmental impacts, such as water pollution and land degradation.
• Supply chain optimization: Optimizing supply chain operations, including logistics and inventory management.
• Geomechanical analysis: Analyzing and predicting rock behavior to help reduce the risk of rockfalls and other geological hazards.
• Drilling and blasting: Improving accuracy and reducing waste by optimizing drilling and blasting operations.
• Data analytics: Providing insights and improving decisionmaking by analyzing large datasets.
During PDAC 2024, I caught up with Marty Beard, co-founder and CEO, and Justin Rich, director of cloud engineering and IT at alwaysAI, to discuss how mines can minimize downtime, maximize productivity, and enhance safety to improve top and bottom lines using computer vision to provide a detailed view of the entire mining lifecycle. This article is based on the conversation that took place during PDAC 2024.
The alwaysAI platform
The company employs computer vision for practical AI solutions across various sectors, from mining and manufacturing to retail and beyond, enhancing operational efficiencies while addressing privacy concerns.
The software (computer vision platform) is an extraordinary end-to-end vision AI platform, which means that they offer a comprehensive set of tools ― like advanced APIs, user-friendly dataset and model management, and convenient remote deployment ― that can eliminate the complexity of computer vision without sacrificing functionality, thus allowing companies to build computer vision applications, and there is a lot involved in that process. So, businesses can easily extract the data they need from existing cameras in real-time. The platform provides an end-to-end capability to build computer vision apps, run those apps 24/7 out in the real world, and then get all that data that people need to help them make better business decisions.
Computer vision enables existing cameras to quickly identify and interpret objects in the physical world allowing the realtime monitoring of everything happening in the mine, thus making more sustainable, safe, and profitable mining possible using practical artificial intelligence (AI) solutions.
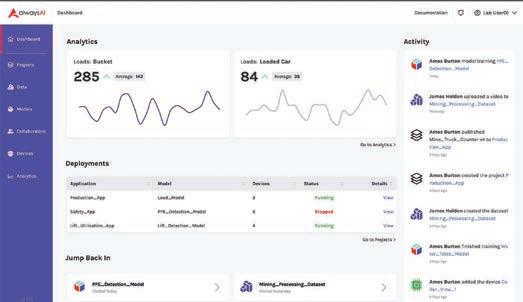
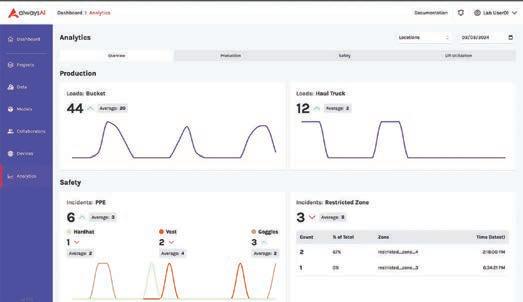

A game-changer for the computer vision industry
During the last quarter of 2023, alwaysAI announced the release of enhanced machine learning operations (MLOps) features to its comprehensive computer vision platform. These integrated capabilities solidify alwaysAI as a premier MLOps computer vision provider with a suite of powerful features and tools to streamline the entire computer vision lifecycle.
The release also complements alwaysAI’s existing Dataset Management and Remote Deployment features, making it easier for developers to create, deploy, and manage enterprise-grade computer vision models and applications.
“We are always enhancing our tools and functionality to provide practical AI solutions that can dramatically streamline operations and drive more revenue,” says Marty Beard. “These advanced model evaluation and management features are the latest upgrades to our comprehensive, end-to-end computer vision platform,” he added.
Key features of alwaysAI’s MLOps include the following:
> Enhanced user interface to streamline the model configuration process.
> Multiple GPU options for greater control of model training speeds.
> Forecasted model training duration based on your specific parameters for ultimate flexibility.
> Real-time session performance including metrics such as mAp, recall, and validation loss.
> Model evaluation with alwaysAI’s exclusive modelIQ tool that measures precision, recall, and F1 score, to facilitate successful model refinement.
The alwaysAI platform also features a comprehensive analytics dashboard to easily view operational insights and receive immediate alerts about potential issues or concerns. For mining operators, this could include PPE usage, movement in restricted zones, machine downtime, as well as precise data about the number of bucket loads and dumps.
Various ways for alwaysAI to help the mining industry
Computer vision provides a detailed view of the entire mining lifecycle to minimize downtime, maximize productivity, and enhance safety to improve top and bottom lines. Computer vision enables existing cameras to quickly identify and interpret objects in the physical world allowing miners to monitor everything happening in the mine in real-time. More sustainable, safe, and profitable mining is made possible with Vision AI.
“Vision AI can help in every critical mining process from extraction to processing, inventory management and transportation, and delivery. AI technology like alwaysAI Smart Mining solutions enable operators to quickly deploy computer vision applications onto cameras to accurately measure and count ore extraction, monitor cage and large machine utilization, detect PPE, and address a wide variety of other applications that will have a dramatic impact on profitability,” said Marty Beard.
When asked about examples of how the alwaysAI can help solve different problems in mining, Marty and Justin presented the following examples of problems and solutions offeredby the computer vision platform:
1. Collar and cage analytics
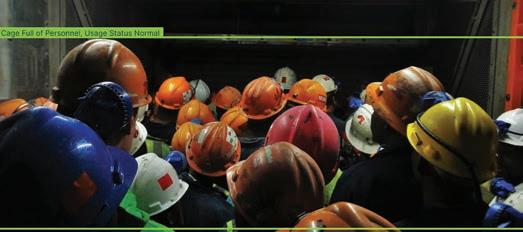
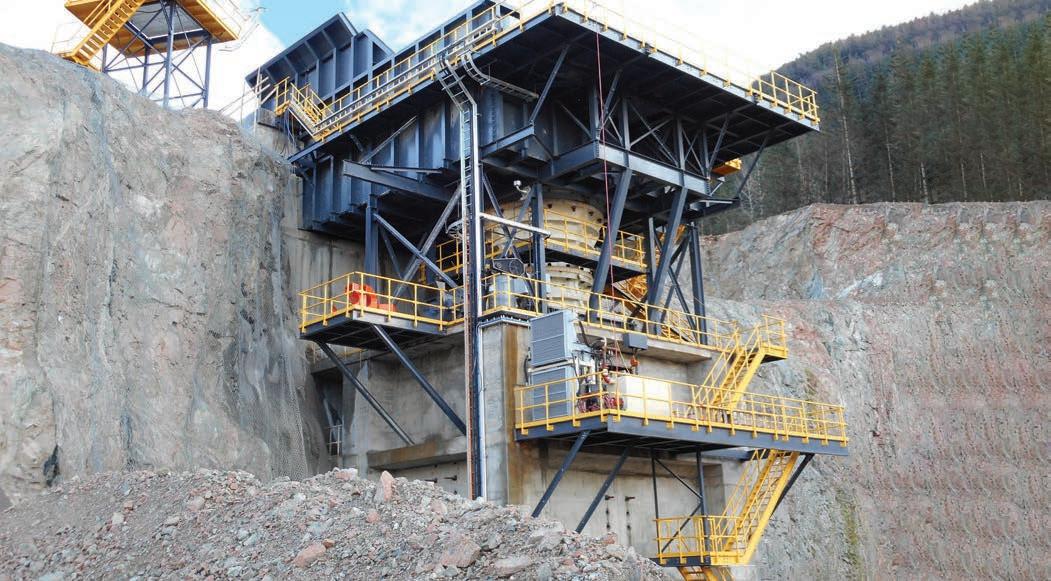
MINING
Problem: Lack of visibility in mines often leads to unplanned downtime and delays that can cost thousands of dollars a day. Solution: Monitoring and tracking all activities, including people, materials, and equipment in collar and cage feature with real-time visual data to improve efficiency and maximize tonnage production.

Problem: Inaccurate, outdated, or incomplete data about critical muck car and muck bucket activity makes improving processes difficult.
Solution: Use the feature for monitoring and tracking critical muck bucket and muck car activities to ensure debris is cleared efficiently to streamline processes and better manage resources.
3. Maximizing safety; PPE detection
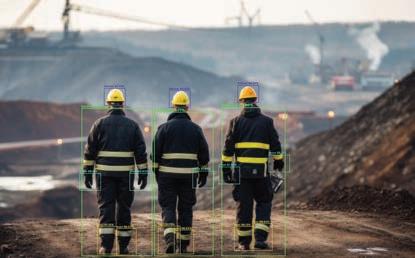
Problem: Because of the inherent dangers in mining operations, minimizing safety risks is essential. However, without visual insights into operations, injuries and accidents are inevitable.
Solution: Identify and track PPE usage including head, eye, ear, foot, and hand protection, and visibility apparel to ensure safety compliance, limit injuries and costly infractions, and prevent site downtime.
4. Labour productivity
Problem: Mining requires hundreds of workers in small spaces that are challenging to monitor, thus making shift variances difficult to reconcile.
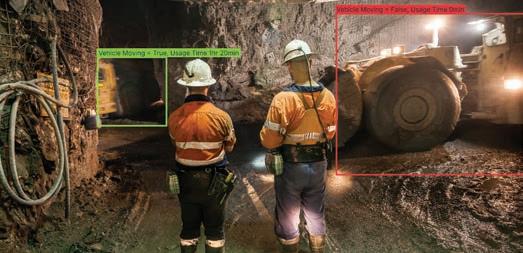
Solution: Real-time visual data about movement and dwell time throughout the mine will help to better manage human resources and maximize consistent productivity. For worker privacy, all data can be blurred and anonymized.
The future of AI in mining
“I think it is going to have a very powerful impact on improving productivity, safety, and the environment. So, it is going to become best practice. I think right now it is very early to start seeing that potential impact,” said Beard. He added, “I think companies like alwaysAI are starting to make the technology accessible. And once that happens and people see the actual impact of this technology, it will automatically become a best practice.”
“We are currently more focused on the operational part, but there are several companies that are using big data and starting to use AI to advance the exploration and make it a more efficient process. Ultimately, AI is perfectly positioned to help get more productivity out of the existing assets,” Marty Beard concluded. CMJ
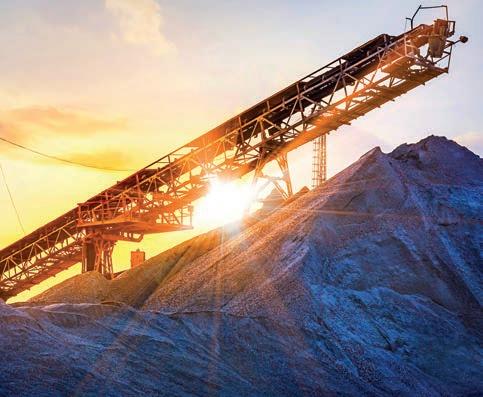



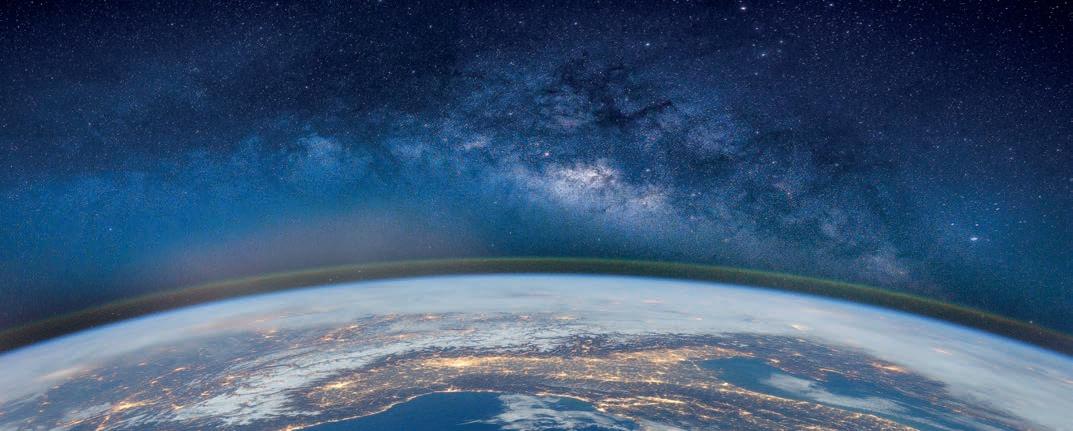
PRECISION BEYOND THE NOISE
Preparing for solar-triggered signal disruptions
Automated and autonomous operations are essential and expanding parts of mine operations worldwide. Technology is built into nearly every task — with a large majority dependent on global navigation satellite systems (GNSS) for precise positioning, safe navigation, and productivity gains. Mine sites include equipment that ranges from remote-controlled and robotic drilling machines to driverless haul trucks.
The Research and Market’s Global Mining Automation Market report recently noted that mining automation is on the rise, driven by technologies including robotics, machine learning and data analytics, which enable mining companies to automate processes, cut costs and improve safety. The report anticipates the global mining automation market size will grow from US$3.6 billion in 2024 to US$5.1 billion by 2029. And, nearly all these machines and workflows are reliant on accurate positioning delivered via GNSS satellites to hardware and software that processes these signals.
What happens when those GNSS signals go down, or perhaps even worse, deliver inaccurate data?
It is a very real challenge, particularly in high latitudes, such as in Canada, as the influences of Solar Cycle 25 grow. The current 11-year solar cycle began in 2019 and is anticipated to peak between 2024 and 2026, a time when ionospheric scintillation (signal noise) will be at its high-

est level — and GNSS signal reliability is
A measure of significance
Ionospheric scintillation is the rapid modification of radio waves in the ionosphere. It extends from about 80 to 966 km above earth’s surface. Severe scintillation conditions can prevent a GNSS receiver from locking on to the signal and make it very difficult to calculate a position.
By how much is dependent on several factors — though several metres of error are not uncommon. A 2014 study in Brazil evaluated the impact of scintillation on real-time kinematic (RTK) positioning using ionospheric scintillation data collected in the country during the
solar maximum year 2014. The report noted significant positioning errors when dynamic RTK processing strategies were used during strong scintillation events. In this case, the study found the maximum positioning deviations in the east, north and upper directions reaching 2.29 metres, 1.84 metres, and 1.37 metres, respectively.
Similar GNSS position deviations have been noted during the past three solar cycle peaks dating back to the early 1990s by mining customers in Canada, particularly in northern regions like Alberta.
For mine operators who have invested in autonomous machines as well as remote-controlled and automated precision applications, scintillation is already a concern. As occurrences increase in
frequency and severity as the solar maximum approaches, owners might see more downtime and shutdowns for mines that rely on precision GNSS applications. For instance, the level of positioning error noted above (e.g., 2.29 metres) can result in long-haul road truck accidents (with another truck or into a berm).
Perhaps the most challenging problem of scintillation is that loss of accuracy may not be immediately apparent. Autonomous vehicles could continue operating with inaccurate data, potentially leading them to wrong locations, causing productivity losses or even accidents. Automated systems are also at risk. For instance, GNSS position deviations could trigger false alarms or miss slope movement in slope stability monitored areas.
To make matters more challenging for owners and operators, the random and intermittent nature of scintillation events makes it difficult to predict and plan for this upcoming solar cycle peak. Scientists might estimate that ionospheric activity will occur at midday or dusk, for instance, but that will not always be the case. The disturbance can be random. As the solar cycle peak draws closer, the frequency will increase and the number of times where precision GNSS powered machines are not going to work predictably will rise.
The solar fix
Scintillation is not a new issue in the GNSS space, and leading manufacturers continue to improve receiver tracking and processing algorithms to minimize the disruption of signals during future cycles. Ionospheric mitigation features have been added and improved upon in GNSS receivers over the past three solar cycles, with frequency independence just one such adjustment. During ionospheric storms, there can be significant frequency-dependent differences in the phase and carrier delay through the ionosphere. Ensure your receivers are not dependent on any one frequency for operation.
To prepare for the current and future solar maximums, Trimble leveraged comprehensive data collection exercises to develop IonoGuard technology. This technology is designed to mitigate cycle slips and improve signal tracking of disrupted GNSS signals. It is an additional layer of protection that makes precise GNSS measurements possible under the most challenging atmospheric conditions, increasing the likelihood of unin-
terrupted and robust positioning data around the clock. During recent solar storm events in Brazil, Peru, and northern Sweden, the improvement in both horizontal and vertical positional accuracy using IonoGuard was significant. Bottom line, there are solutions available to minimize the risk of impact caused by scintillation in the coming years, but those strategies must be put in place in the near term.
One of the main challenges to resolv-
ing scintillation in mines is the lengthy validation process required for implementing new technology solutions — often taking six months or longer. While developing solutions to issues like GNSS signal losses, simply coming up with a hypothetical fix is not sufficient. That fix then needs to be thoroughly tested and validated to ensure it will work properly and safely without disrupting mine operations or other systems.
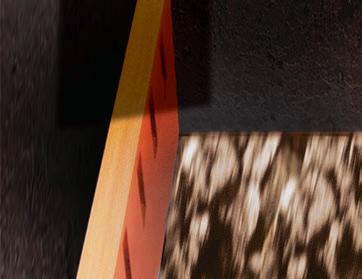
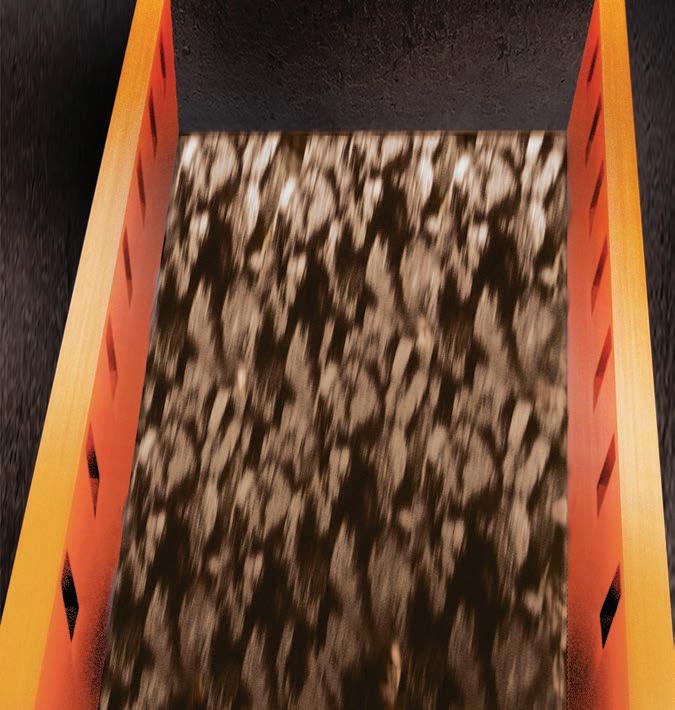
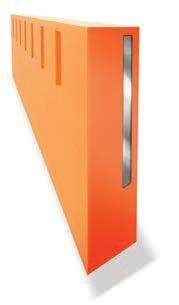
Martin® Manufactured
Liner has the backbone to stand strong while absorbing the impact and abrasion of punishing bulk handling environments. This proprietary design features impact-resistant urethane molded directly around a supporting steel plate. The rugged construction prevents the the urethane from separating from the plate which can subsequently damage belts and enclosures. Our canoe liners shield the sealing system and chute walls better, control more dust and spillage, and improve overall safety. All benefits contributing to reduced cost of operation.
PROcheck is our signature, expert analysis beginning with our diagnostic
Pulse Vibration Analysis examines the health of any brand of vibrating screen, while our Pulse Impact Test prevents your screen from operating in resonance.
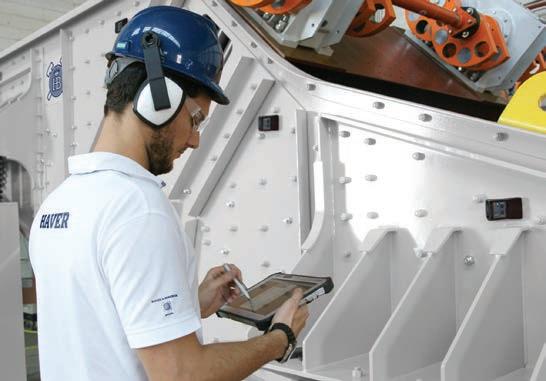
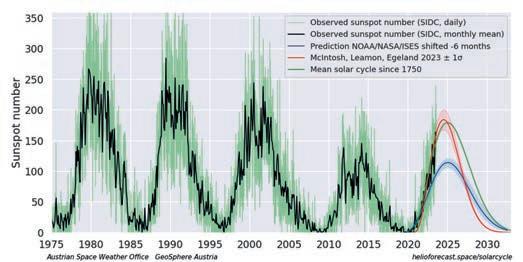
An NOAA model predicting the maximum magnitude of the solar cycle in 2025 would be similar to the previous 11-year cycle. However, new models and measurements indicate a cycle more like the cycle which peaked around 2002.
The intensive validation process for new technology involves testing in labs, with system integrators and on actual mine sites. The length of this validation means mines need to work with technology partners that already have identified problems and have solutions in place well in advance of when peak issues are set to occur.
Moving forward
There is no question that scintillation will directly affect the positioning accuracy of GNSS-enabled mine solutions in the future, but every owner can minimize those effects with the following steps to success:
> A mitigation strategy is essential, so be aware the peak season for GNSS issues in 2024 will be toward the end of the year, so strategies should be developed as an integral part of risk management plans and in place by then if not sooner.
> Work closely with a technology partner that has experience developing solutions to GNSS accuracy issues and can help validate and deploy solutions quickly before problems become critical. That technology partner should already have solutions that have been validated in real-world conditions. When evaluating solutions, consider automation that can detect errors in real-time and adapt accordingly to minimize downtime from accuracy losses and look for features like real-time ionospheric correction.
> Make sure to validate any new technology thoroughly by testing to avoid unintended disruptions, as validation takes significant time but is important for safety and productivity.
In equatorial and high latitude regions, like Canada, Brazil, and Chile, ionospheric disturbances are common, and will only intensify in the coming years. With Solar Cycle 25 on track to peak over the next two years, the time is now to implement a solution. CMJ
Kevin Andrews is director of land product at Trimble Applanix. Giri Baleri is director of product management and strategic marketing for Trimble OEM GNSS. Riley Smith is a marketing director for Trimble Geospatial.
QUANTUM TECHNOLOGIES IN MINING EXPLORATION
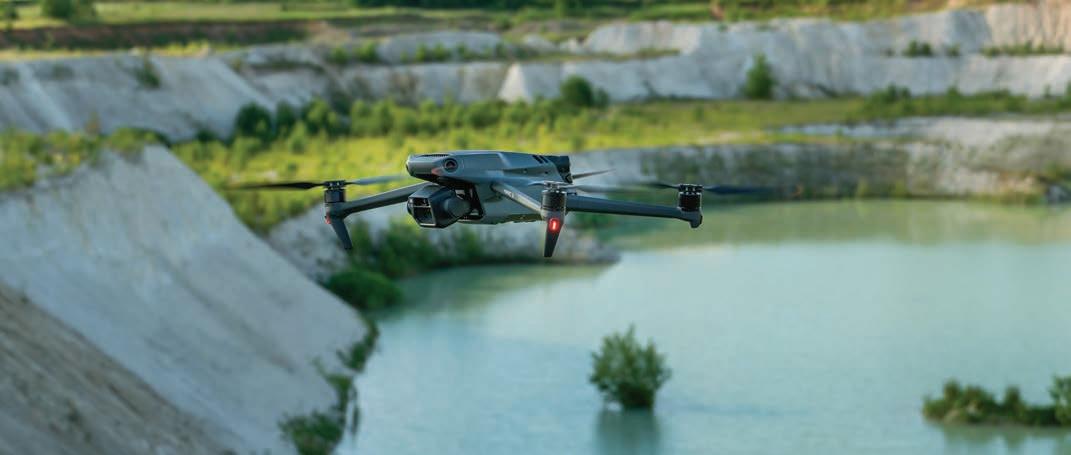

Embracing technology fusion and quantum sensing can accelerate mineral discovery
Mining has been a key industry across much of the world for centuries and has evolved a great deal over time. Now, as many of the world’s wealthiest economies begin to pivot away from fossil fuels and seek greener, more efficient sources of energy, the mining industry has taken on even more strategic importance than ever before. Control of key resources has become a vital geopolitical issue. Finding sufficient supplies of these minerals therefore not only determines who gets to extract them, but in some ways may also help to determine who will build the advanced economies of tomorrow first.
The ongoing transition toward electrification of multiple industries, along with the adoption of renewable sources of energy instead of fossil fuels, has created a massive gap between the supply and demand for many kinds of metals and critical minerals. An EY report in 2022 highlighted that demand estimates for the following year indicated a global deficit of 700,000 tonnes of lithium and 4.7 million tonnes of copper at that time. And many expect these numbers to trend upwards. Efficiency and increasing exploration along with high conversion rates from greenfield exploration to operating mines are therefore key to bridging this gap, both from a supply and a cost per unit perspective.
The good news is, there may be solutions available which can help address this problem. The use of multiple types of advanced sensors in combination to cross-correlate different sources of geophysical data can accelerate the identification of drilling targets. Conventional airborne methods such as gravimetry and magnetometry are combined with land-based electromagnetic methods, geological soil sampling methods, and others. Processing and correlating these huge datasets are a key challenge, and we can learn from other industries which have successfully adopted artificial intelligence (AI) and machine learning on a large scale to process the data. However, in most cases these approaches leverage historical datasets, in which data resolution and quality can vary drastically. Access to high-quality, high-resolution data is crucial for high depth dis-
coveries, particularly in the context where large, shallow deposits have already been found and developed.
Over the last decade, the advent of drone sensing technologies has provided high-speed, high-resolution data collection in a very efficient timeframe, turning weeks of ground surveys into days. Low altitude drone surveys also help exploration by revealing key data points which could not previously be identified in historical surveys.
As a next step towards this “data fusion” and accelerated exploration, SBQuantum is building a platform to deploy sensors measuring magnetics and gravity from a drone, accelerating the generation of these datasets while significantly improving cost efficiency. Conventional total magnetic field surveys are currently the industry benchmark, providing a single data quantity from which to infer the resource body from inversions. SBQuantum leverages the room-temperature, quantum-based vector readings using its diamond magnetometer technology to perform full tensor magnetic gradiometry, generating eight times more maps which can be fed into inversion or AI software. Combined with gravimetry, these juxtaposed airborne datasets will streamline both the collection of data and its interpretations.
A key consideration when inverting geophysical data is setting appropriate constraints for the inversion to reduce the possible degeneration of the potential solutions. By jointly inverting the gravity and full tensor magnetics data, solutions of this kind will provide enhanced 3D descriptions of the ore bodies, with greater resolution and confidence.
To demonstrate the readiness of our full tensor system, SBQuantum has built and deployed a backpack sized device over nickel ultrafamafic structures. By correlating the tensor magnetic maps, high resolution geologies were revealed and the dipping of the body could be inferred using only tensor data, in a way that cannot be done solely with total magnetic field data. Access to all tensor components also provides a means to highlight additional geologies. Ultimately, combining
SANDVIK SAVES ON DRILLER TRAINING
Learn anywhere, anytime with with cutting-edge simulators
Sandvik Mining and Rock Solutions leads the charge in revolutionizing operator training through the use of cutting-edge simulator technology.
This revolutionary tool, available for training purposes at Sandvik facilities and customer sites throughout Canada, aims to enhance the skills of operators and maintenance teams across a range of iSeries surface and underground equipment. With its advanced controls including automation capabilities, Sandvik’s operator training tools promise to revolutionize.
The simulators offer a comprehensive and realistic learning experience. Trainees familiarize themselves with equipment functions and operations before they encounter the actual machinery. In addition to enhancing operator skills, a Sandvik’s surface or underground simulator also contributes to improved environmental, health, and safety (EHS) practices.
By minimizing the risk of accidents and equipment damage, the simulator promotes a safer working environment for all personnel involved in mining operations. And an operator with better training will reap productivity gains as well.
“The introduction of the DS412i bolter and DL432i longhole drill training simulators at Sandvik’s facility in Sudbury, Ont., as well as the Seabee mine site has been a game-changer for our mining operations,” says Greg Scammell, mine manager for SSR Mining. “With the ability to practice in a safe environment alongside dedicated operator trainers before encountering new equipment, our operators have gained confidence and proficiency, leading to improved productivity and safety outcomes.
“Sandvik’s commitment to innovation has truly revolutionized our training
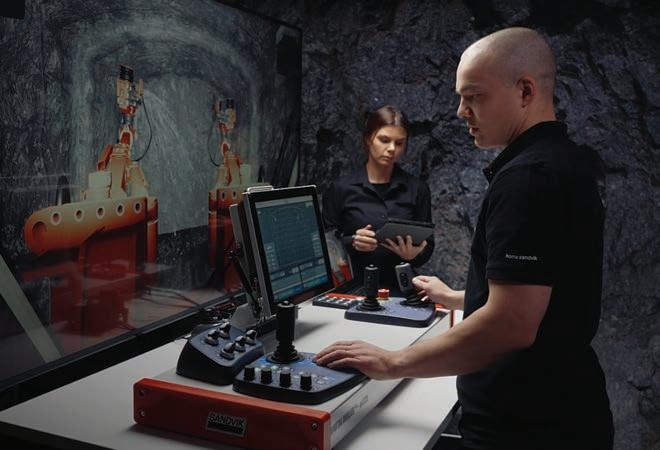
practices and elevated our operational performance, even before the newly purchased underground equipment was commissioned to site,” Scammell added.
By providing hands-on training in a controlled setting, Sandvik simulators significantly reduce the drill start-up period and improve overall equipment utilization. Trainees can practice various scenarios and learn to manage different operating conditions, optimizing productivity and minimizing downtime.
“Sandvik’s simulator training and tooling presentations have proven to be worth their weight in gold. Whether it was an operator’s introduction to Sandvik equipment, or just a refresher, Sandvik’s simulator training was an exceptional experience for our operators,” says Spencer Andriashek, project manager for Otokiak Corp. at B2Gold’s Goose project.
“The simulator provided a safe environment for a hands-on learning experience, enabling our indigenous
employees to focus on developing and advancing their skills, knowledge, and proficiencies on the equipment, while remaining free from the pressures and complexities associated with active job sites.
“Having an opportunity to learn the boundaries and limitations of Sandvik’s ground breaking technology proved extremely valuable to both our operators and our client(s). Mistakes that would normally be costly and risky can now be viewed from a learning perspective,” Andriashek added.
“I believe that the simulator is a game-changer in training operators. Our purpose-developed software offers a tailored approach with specific exercises to record and measure operator behavior accurately,” says Sebastien Roy, Sandvik’s national service manager for Canada.
“With the ability to simulate machine faults, incidents, and hazards, we ensure operators are provided advanced
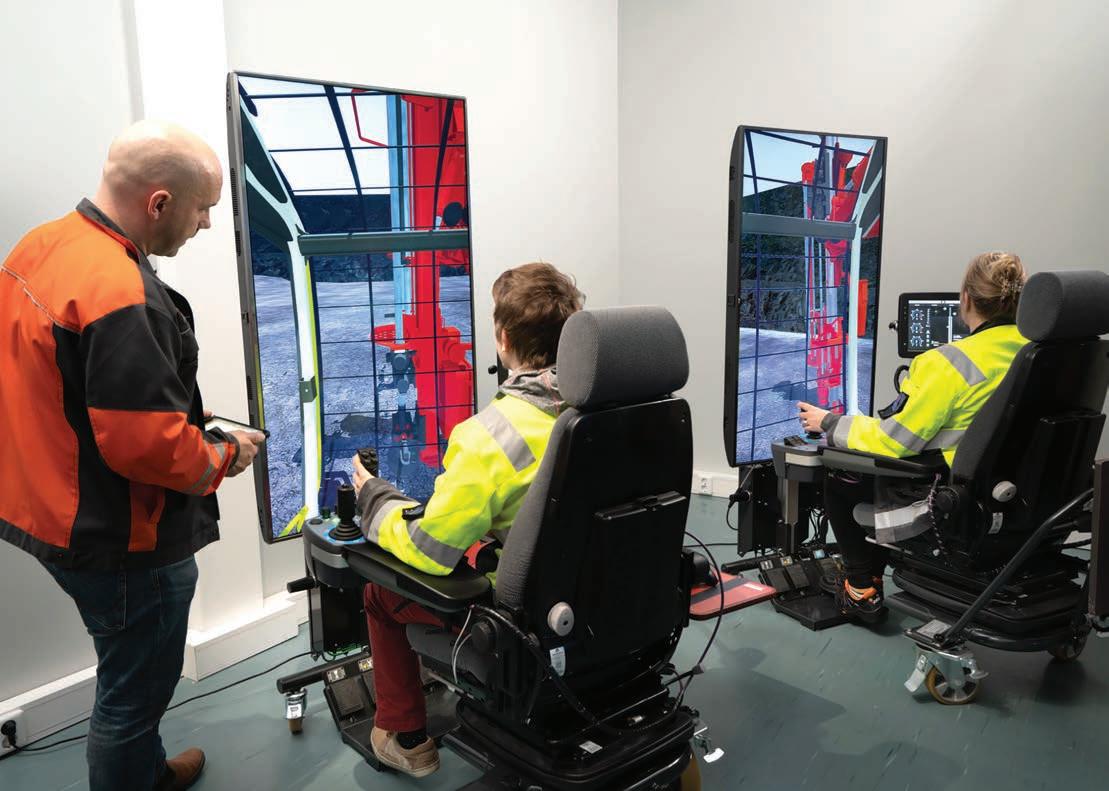
training by certified personnel to respond effectively to any scenario with utmost efficiency. Furthermore, our training programs support multiple participants simultaneously, fostering collaborative learning within a safe environment.”
Furthermore, the simulator’s compatibility with Sandvik’s advanced software tools, such as iSURE – a tunnel management tool – or AutoMine – which covers all aspects of automation, from remote and autonomous operation of a single piece of equipment, to multimachine control and full-fleet automation – further enhances its effectiveness in preparing operators for real-world challenges.
One of the standout features of the training simulator is its portability. Weighing less than 50kg and equipped with wheeled carrying cases, simulators can be easily transported to any location, enabling training sessions to be conducted anywhere, anytime.
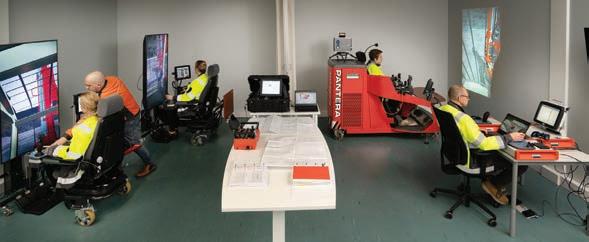
Sandvik simulators offer three levels of training: beginner, professional and drill master. Even the maintenance crew can benefit from beginner training. Drill masters, with the superior operating skills, are qualified to mentor others. A choice of languages is available.
Sandvik’s commitment to innovation continues to drive progress in the mining sector, setting new standards for excellence in operator training and equipment performance.
Take the opportunity to try out the
DL432i Digital Driller and the Leopard DI650i SimDriller on display at CIM Connect in Vancouver, British Columbia –Booth #1207.this with gravity data will further delineate the mineral body, so that drilling can be targeted more effectively, thereby improving drill hit rates. By deploying these geopotential survey techniques on a drone, the geological mapping of a site can be sped up an incredible 10 times, and costs can be cut in half.
Some key advantages quantum sensors provide in this instance include highly accurate measurements, combined with multiple sensing modalities from a single device which is highly efficient in size, weight, and power consumption. SBQuantum has miniaturized its quantum diamond vector magnetometer to a handheld sized device, weighing under one pound, and consuming less than four watts. The sensor can function accurately in conditions ranging from –50°C to +60°C. We have even shown that the sensor will work correctly for low earth orbit.
Though only five years in development, the device’s sensitivity and accuracy relative to DC magnetic fields were demonstrated to be comparable to classical vector fluxgate magnetometers, which unlike quantum sensors are prone to thermal drifts. By early 2025, this technology will surpass the sensitivity and accuracy of some commercially available classical vector magnetometers. Thus, making them an attractive alternative to deliver room-temperature full tensor magnetic gradiometry without deploying bulky cryogenic based platforms.
The capabilities of aerial exploration platforms are also being further developed by adding electromagnetics sensing. Through customizing quantum control pulse sequences, diamond quantum magnetometers can be used to provide electromagnetics mapping capabilities from a sensor 100 times more compact
than existing solutions, and therefore making airborne deployment possible. Adding this third non-invasive airborne mapping technique will further enhance the speed, savings and geologically relevant pre-drilling data.
This is only the beginning for quantum technologies in mining exploration. High-resolution multi sensor surveys will be the key to enhanced inversion models, AI-enriched correlations, and improved geological interpretations. This bespoke solution will optimize the yield of drilling campaigns, reduce the timelines for exploration programs, and increase the speed with which new mines can be commissioned. Hundreds of these new mines will be required worldwide to meet the needs of a society driven to achieve its net-zero objectives. We, along with our partners, are doing our part to unlock the potential quantum sensing can provide to the mining sector, enhancing the data quality and resolution to make this a reality near-term. While this technology is still being developed and will be fully deployed soon, exploration companies may be wise to begin to look at how it could eventually be integrated into their operations over the near- to medium-term. Not only does this technology present the opportunity to help them cut costs significantly as well as identify more deposits to develop, but it also has the potential to help determine who gets scarce resources needed for chips, batteries, electricity production, and other technologies vital to the ongoing digital transformation of every advanced economy. CMJ
ERIEZ_TrampMetal_1-2Pg_CMJ_3_23.qxp_Layout 1 2/17/23 9:40 AM Page 1
David Roy-Guay, CEO and Founder of SBQuantum.Stop DangerousTramp Metals
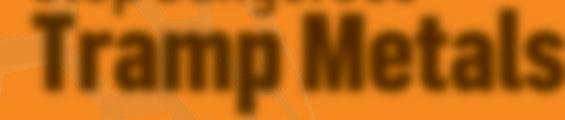
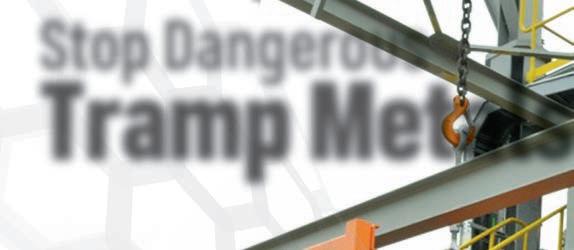
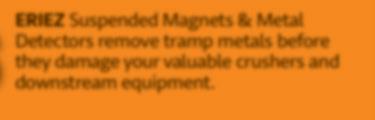

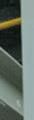





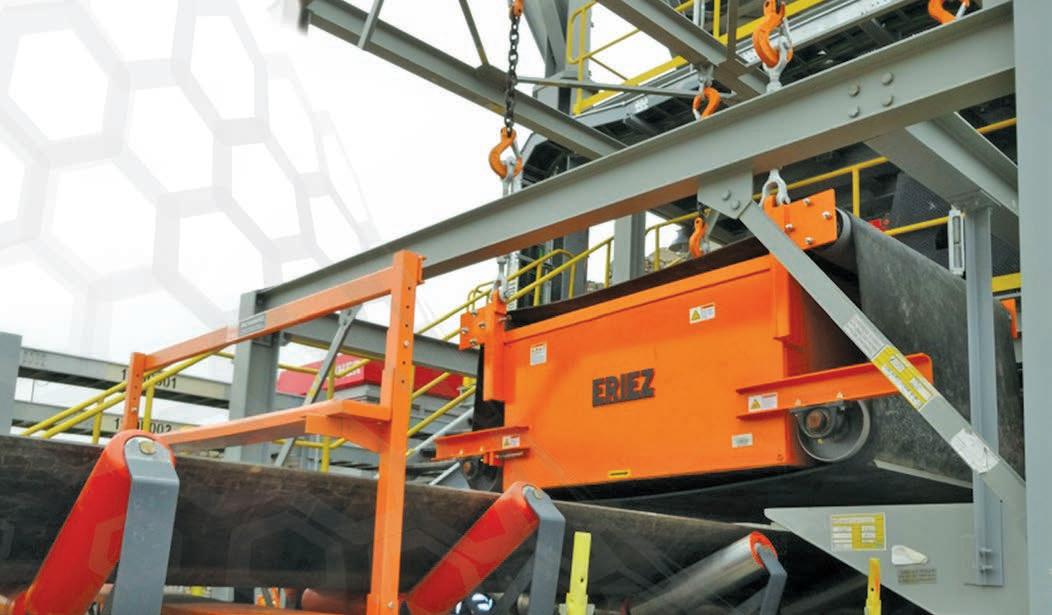
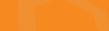

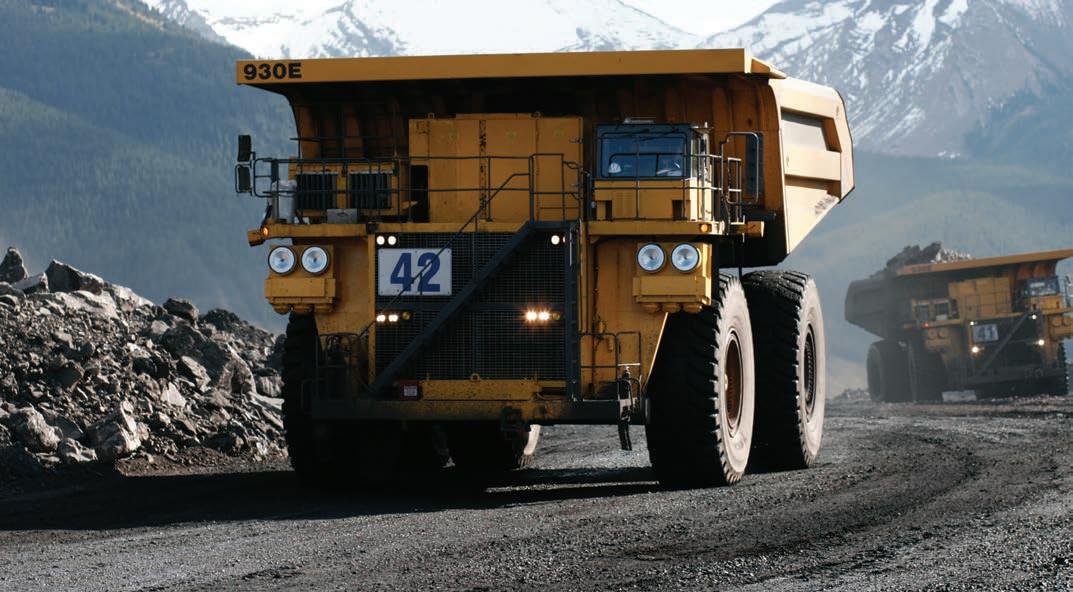
AUTONOMOUS TIRE INSPECTIONS AND ARTIFICIAL INTELLIGENCE CAN IMPROVE SAFETY, UPTIME, AND COMPLIANCE
The purpose of regular truck inspections in mining operations is to ensure trucks are safe for people to continue operating them to the next planned service and to address any findings with the least amount of unplanned downtime. Manual inspections, however, can present safety and productivity challenges that Kal Tire’s mining tire group was committed to solving. The result was TireSight, Kal Tire’s approach to autonomous tire inspections.
What is the difference between traditional manual inspections and the future of automated inspections?
Traditionally, manual tire inspections on mine sites take place perhaps every seven or 20 days. Once the earthmover vehicle comes to a stop and is locked out, the technician walks around it, looking at the ultra-class tires. Since the tires can span heights of nearly 4.3 metres, the technician can only inspect what he can see, about 50% of the tire.
“A human can only document findings for what they can observe when the truck is parked,” says Christian Erdelyi, manager, mining technology solutions, Kal Tire’s mining tire group. “The next time they might have a chance to see the other 50%
of the tire could be in seven days, at the next random inspection, or when the truck comes in for tire work in 25 days,” added Erdelyi.
Manual inspections can be both incomplete and infrequent — an issue exacerbated by industry-wide staffing shortages — and inconsistent. The priority or severity of the observation, and the recommended follow-up action, can vary widely. To a junior technician, what appears to be a serious condition requiring a stoppage could be a minor issue that an experienced technician would mark down to be addressed at the next scheduled maintenance.
For example, cut separations are a common sight on mining tires. To the untrained eye, a cut separation could look very concerning, but a more experienced technician would know those are not reparable, and we typically keep them running as long as it is safe to do so.
Mechanical separations — also known as “sealed separations” between the belt and tread, inside the rubber — can cause a range of findings and recommended actions.
Those are hidden from the human eye. Telltale signs do exist,
but if you overlook them, it could lead to catastrophic tire failure and pose a risk to humans on site. If we over-prioritize a condition, there is unplanned downtime. If we overlook or under-prioritize a condition, it could turn out to be critical.
Now, beyond the subjective nature of manual inspection findings is the potential time lag between notes being compiled and recommended action being taken. Sometimes, the journey of that piece of paper can take several days, making it challenging to ensure tasks like repairs are carried out when required.
What could happen during that gap of time?
“We now have the data to show that tire damage can progress far quicker than we used to think possible: from a manual inspection finding that a tire appears visibly safe to operate one day to there being a serious problem that needs a stoppage just a few days later,” says Erdelyi.
Lastly, mines are becoming increasingly autonomous and increasingly restricted to humans, making traditional manual inspections even more challenging.
Sites with autonomous vehicles often require any vendor vehicles entering restricted autonomous zones to be escorted by site vehicles outfitted with specialized equipment. Technicians undergo additional training to understand the signals and operation of machines driven autonomously, and people must carry emergency beacons. If a technician were to bend over to pick up a tool and accidentally activate the beacon, all autonomously operated vehicles within a certain radius would immediately stop, interrupting fleet productivity and requiring human intervention to restart vehicles. The more people there are in these zones, the more cautious we must be and the more chance there is for disturbance to productivity.
As the mining world began to shift toward autonomously driven vehicles several years ago, Kal Tire wondered, how could inspections complement a more autonomous operation and reduce risk for technicians — while also improving compliance frequency, findings consistency, and timely follow-up work?
Those questions led Kal Tire to integrate the thermal imaging camera and artificial intelligence (AI) software of Pitcrew.ai with Kal Tire’s proprietary tire and operations management system (TOMS), to offer TireSight: autonomous inspections that flag signs of potential tire damage in real time and inspire action.
Today, at a copper mine in Chile, the 198 tires of 33 haul trucks pass by a thermal imaging camera set up near a haul road fuel bullet. Without even needing to stop, images of front and rear tires are captured, and the Pitcrew.ai software scans the thermal imaging footage for anomalies such as hot spots and tread damage. Inspection anomalies are processed in TOMS and an off-site condition monitoring team confirms critical next steps. Now, depending on a customer’s goals, work orders are automatically released to plan and schedule tire work, such as tire replacements or repairs, at times when trucks might already be down for other work.
“What we are doing is summarizing everything, taking out the noise and condensing things down to the items that really require action. This allows our inspectors on site to focus their attention on tire issues that need their expertise, rather than inspecting every tire every week just because it is on a schedule. And we ensure critical items are added to the maintenance plan, so they are addressed proactively,” says Erdelyi.
How Kal Tire’s TireSight addresses some of the challenges of traditional manual inspections
At several mines already in Canada, Chile, and Colombia where TireSight is already in use, the frequency of autonomous inspections ranges from every 15 minutes to every six hours. Increased inspection frequency identifies potential issues earlier and allows for more proactive maintenance, which leads to better operational uptime.
For a tire progressing quickly from a normal to a critical condition, thanks to TireSight, we can scan that tire multiple times. If a mine site’s tires are more prone to rapid mechanical separation, the ability to see trucks more often, and talk to customers to determine the right frequency of scans, is very powerful in ensuring we identify issues proactively and can track issues as they develop.
Where technicians can only manually inspect about half of the tire, a truck passing by the TireSight station will give cameras between three and five full rotations of each tire, ensuring every area of the tire is inspected at every passing.
In addition to increased tire coverage area, inspection findings and recommended follow-up actions are consistent because standard “business rules” are used.
Equally important are consistent parameters and protocols for recommendation actions, such as how long to isolate a truck because a hot tire event, or the guidelines and timelines for reparable and non-reparable findings. When is a repair economical? When is the most convenient time for that work? If the condition is beyond repair and it is an aging tire, what are the removal parameters when it is no longer safe for use?
A Kal Tire reliability analyst supports those early conversations and questions with customers, while the condition monitoring team ensures priority work is addressed.
“We are working one-on-one with the customer to figure out which problems the customer wants to solve most, and develop rules and approaches to solving those problems, whether the priority is tire performance or fleet productivity,” says Erdelyi.
With TOMS as one of the data streams that feed into TireSight, customers have extended insight into how planned and aggregated tire work can increase truck availability.
Now we can take that data and the inputs we have from Pitcrew.ai to make important decisions about fleet use based on what is happening on that mine site. We want to manage the life cycle of the tire to its safe end of service life — and we can do that more effectively because we have the data, and we have this co-operation between our condition monitoring team, our reliability analyst, and our customer. We can use the info to create the most efficient plan and then put the plan into action.
With several years of TOMS capturing tire management data from nearly 150 mine sites served by Kal Tire across five continents, aggregated data allows teams to benchmark tire performance, downtime, haul fleet productivity, and more. Now, along with Pitcrew.ai data insights, it allows the study of the progression of damage on tires. Over time, we may be able to tell from initial inspection, how many days of safe, useful life a tire has left and bring that into our planning.
The ultimate goal of TireSight is to help operators achieve their goals. Our focus is to keep trucks running safely and productively, minimizing downtime while also getting the most tire performance out of their tires. CMJ
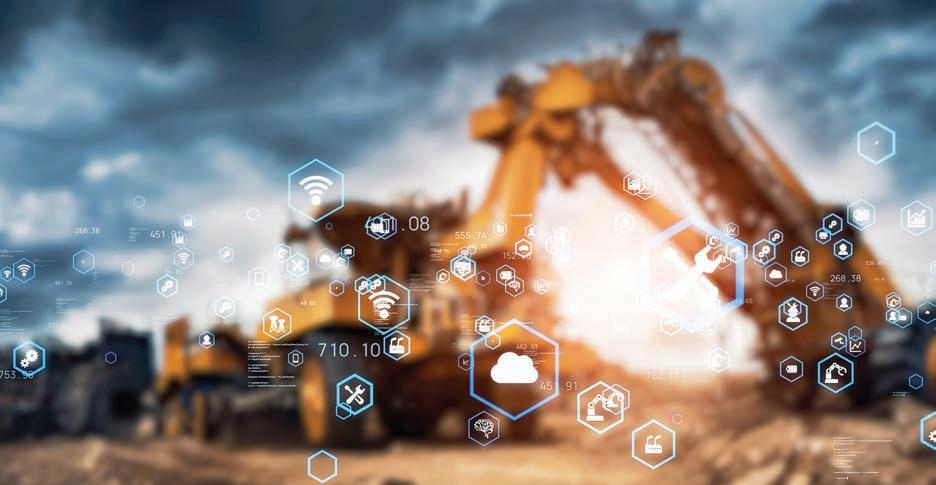
LACK OF TECH TALENT HOLDS MINING INNOVATION BACK
Technology is advancing at blinding speeds: Artificial intelligence (AI), block-chain, the metaverse, and self-driving vehicles. The list goes on. Keeping track of new developments can be downright impossible, and it does not help that every month a hoodie-wearing start-up founder proclaims from their ping-pong table filled office that they are developing the next big thing.
It is certainly difficult to parse out what is important from all the noise coming from the tech elite. But that should not stop miners from trying, because the benefits of new technology are likely to be substantial. In fact, McKinsey & Co. estimates that AI alone will be worth up to US$390 billion in annual savings for natural resource producers by 2035, and the market for AI services in the mining industry is forecasted be worth US$240 million this year, up from just US$76 million only five years ago.
It is thus no surprise, in an industry that has yet to embrace technology to its fullest extent, that EY’s 2024 survey of mining leaders counts “digital and innovation” as both a key risk and opportunity for the industry. A risk for those that do not get it right, and an opportunity for those that do.
The promise of automation, increased safety, and more efficient operations is a big enough carrot to encourage the mining industry to invest in innovation. Indeed, according to a recent study by PWC, 49% of mining CEOs say that digitalization and automation are part of their companies’ long-term strategy.
So, what is stopping mining leaders from embracing technology to its fullest extent? Well, the path to technology adoption is littered with rocks and stones (and not the kind miners like). High costs of implementation, institutional resistance to change, and a downright lack of understanding all impede even the most forward-thinking mining leaders from adopting new technologies. But in an industry plagued by labour challenges, perhaps one of the greatest impediments to the digital revolution in the mining industry is at its core (no pun intended) a talent challenge.
Miners lack tech talent from the C-suite to the mine site
Organizations rely on leaders to understand and champion the adoption of new technologies. Unfortunately, according to a survey by Egon Zehnder, only 18% of senior leaders in global mining come
from a digital background, and only 28% of top mining and metals companies have created or expanded roles focusing on digitalization.
It is no wonder that many mining companies struggle to implement new technologies when top leaderships teams lack technological understanding. One way mining companies may look to overcome these challenges is by bringing in experts from outside of the industry and by introducing leadership positions that ensure that technology strategies are aligned with the organization’s broader vision. For this reason, chief information and chief technology officer roles, leadership positions that ensure the C-suite has visibility on technological developments, are becoming more and more ubiquitous.
Though top-down leadership is important to help champion big ideas, many miners are also skeptical that their current talent pool is equipped to undertake large technological changes. Given a rapidly aging workforce (20% of Canadian mining professionals are over the age of 55), there is fear that the mining workforce may be resistant to change.
The mining industry is dealing with a
critical talent shortage that 71% of mining leaders say is holding them back from strategic objectives. While many mining leaders look to automation to combat workforce shortages, some fear that adding additional technical requirements to an already tight labour pool will only exasperate a talent problem that is not going anywhere anytime soon.
To combat this, mining HR leaders
need to the look at increasing the tech talent pool in two ways: By developing it and attracting it.
Upskilling needs to be a key component of any technological transformation, as it tends to be less costly, and helps ensure that mining expertise can be kept within the organization and enhanced rather then lost completely.
When it comes to recruiting tech savvy
talent, attraction strategies need to be rethought. In general, tech talent prefers to talk shop with likeminded individuals, so in the interview process, HR leaders should emphasize putting candidates into discussions with tech teams as early as possible.



















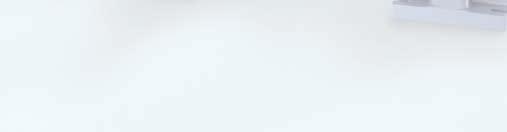
Reliable Automation Technology For The Mining Industry

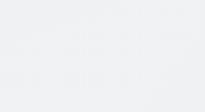


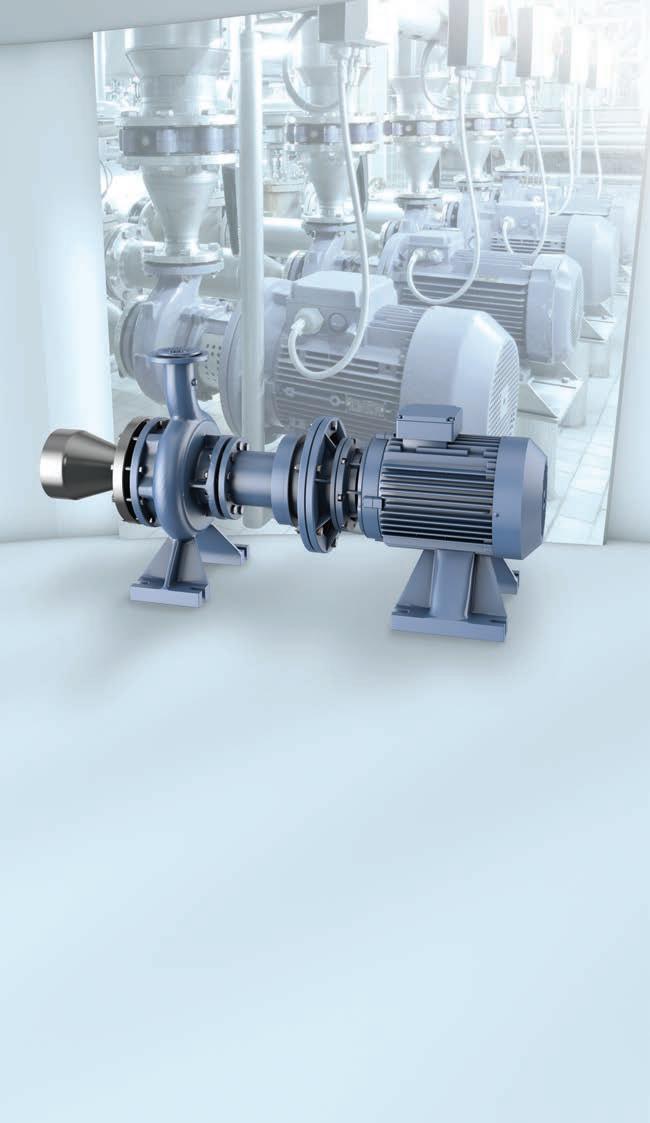
Speed is also the name of the game when it comes to moving through the interview process. In a digital world where everything is on demand, tech job seekers want to move quickly. In fact, 57% of tech job seekers are unhappy with the waiting times in interview processes, and 35% are unwilling to wait more than a week to hear back after an interview. To attract tech talent, moving fast in the hiring process is critical.
Finally, mining leaders need to be realistic about what new technology and digitalization will mean for their workforce. While some mining leaders may believe automation will get rid of their talent woes, miners should instead think of automation as a change to their labour requirements, not getting rid of them altogether.
For example, Nutrien recently implemented a tele-remote mining program, that has not eliminated any jobs, but instead moved operators away from the physical location, and into a more comfortable control room.
While overall headcount at a mine may decrease, to operate more digitalized equipment and software, the talent to do so will need to be hired. This means miners will not only need to compete for talent with each other, but also with the tech giants. Instead of headaches about how to get people to and from the mine, mining leaders may instead need to contend with high bean bag prices at their tech hubs.
The future of tech and how it could impact mining talent are not all negative. As mining embraces new technology, miners have an opportunity to rebrand themselves as a more forward-thinking industry, one that the most innovative young minds want to work in. As one mining professional put it, “Young people do not want to work at a mine, they want to work at Google.” As miners embrace technology, perhaps the next generation of miners can have it both ways: Being able to contribute to one of the most critical industries in the country while working with cutting edge technology. CMJ
Danny Parys is a senior consultant at Calross Consulting.
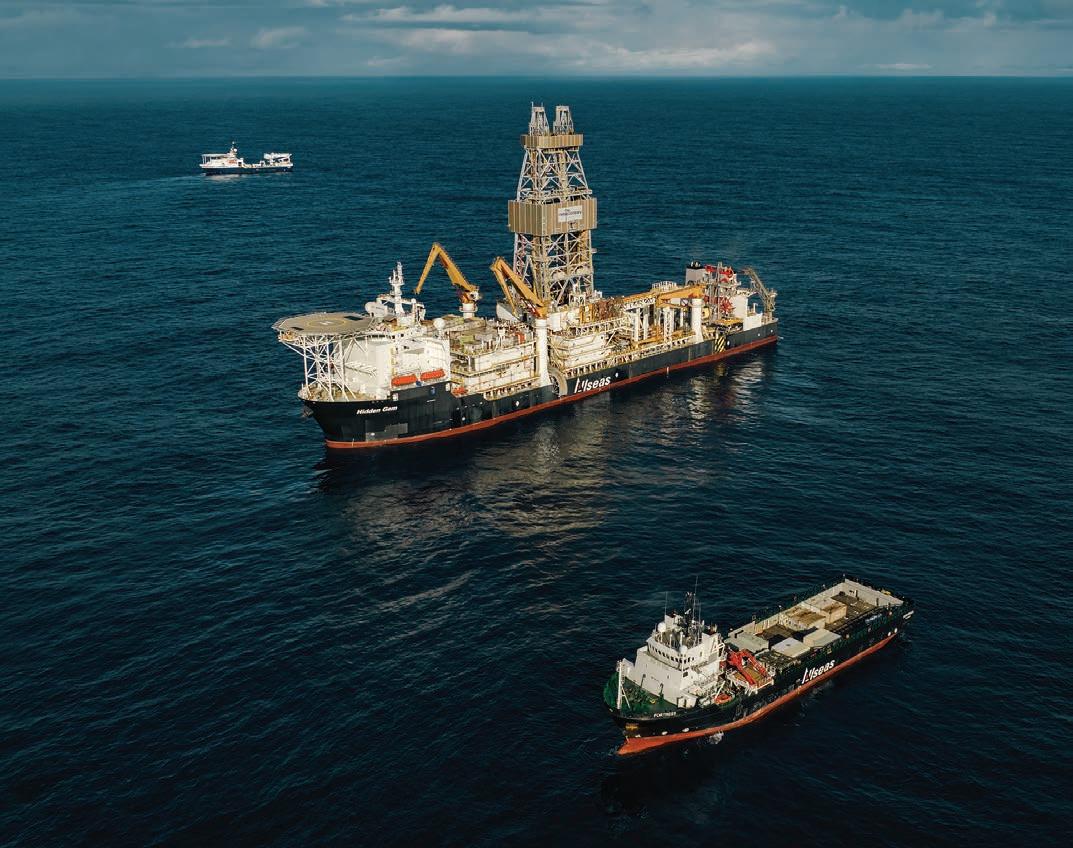
DEEP SEA MINING CAN PROVIDE METALS FOR THE GREEN TRANSITION
CMJ: As a conversation starter, could you please talk to us briefly about the history of deep sea mining and The Metals Company (TMC)? Also, how did you join TMC?
CS: To tell the history of TMC, I will share a little history on deep sea mining. There is an area that is considered a main resource of polymetallic nodules that sit unattached on top of the seafloor and within the Clarion Clipperton Zone (CCZ) of the Pacific Ocean between Mexico and Hawaii. This area has been known to have nodules in high abundance for an exceedingly long time going back to the 1870s when the British discovered that.
It is an industry that almost got started in the 1970s, when many companies, like Lockheed Martin, BP, Shell, and U.S. Steel, were out in the CCZ, collecting thousands of tonnes of these nodules. These companies started pilot mining to show that they could do it, but given that these nodules are in international waters, unlike Norway’s resources that exist in their territorial waters, there had to be a regulator set up to deal with assets like this in international waters. So, the United Nations stepped in and told them that they do not have clean legal title
to this asset. First, the countries of the world had to agree on the U.N. Convention on the Law of the Sea in 1982, and then from that establish the regulator, the International Seabed Authority (ISA), which was established in 1994.
DeepGreen, TMC’s predecessor, formed in 2011 and was the first private company to, alongside a sponsoring nation of developing states, have access to an exploration contract as granted by the ISA. The industry has come a long way, and TMC is now developing the world’s largest and second largest nickel projects. TMC has been around for 13 years, and we have spent more money and done more environmental research than any other company looking to pursue this resource.
I worked in the iron mines of Cleveland-Cliffs. I came to New York and worked for Morgan Stanley for two years, and then I spent 12 years at a $20 billion New York investment firm recommending investments in diversified miners across the com-
modity space. I heard about what DeepGreen, now TMC, back in 2019. I did about a year’s worth of diligence on deep sea mining and a bit of research on the regulatory process, which gave me confidence to first invest in the company in 2020, and then I joined full-time in 2021 taking on the role of CFO.
CMJ: Why do we need deep sea mining? And what are the difficulties it is facing?
CS: We need these metals because they are the critical driving force behind the clean energy transition. If we were going to fight climate change, and if we were going to slow the progress of global warming, one of the ways to do that is through renewable energy sources, many of which would have to be tied to energy storage systems and electric vehicles which require batteries. And what do batteries require? They require a lot of metals. In fact, the International Energy Agency estimates that to hit the Paris Agreement climate goals of 2050, we need to have four to five times more per year by 2040 of some base metals like nickel and cobalt.
It takes an average of 15 to 16 years to discover and then open a new nickel mine. However, the need for new, scalable sources of metals is immediate and urgent. A lot of people might say, do we need deep sea mining? Why not recycle? Why not do better on land-based mining? We would answer, of course, we need to do all those things. We need to do them urgently. And we needed to start yesterday, because this is not a climate change situation that is going to be solved through wishful thinking, and we have a known amount of these metals that need to be utilized for the clean transition.
We cannot get there by recycling the current stocks when expected needs are multiples higher than current supply. There is a need for a major new virgin source of these metals, and that is what deep sea polymetallic nodules represent. We think the clean energy transition is very urgent, and it needs to be solved through a scientific approach, comparing the impacts of getting these metals across all known sources. We think that deep sea nodules stack up extremely well on that basis.
The ISA’s mandate is to establish exploration rules which allow contractors to explore to estimate the size of the resource and do environmental baseline work. That is where we are now. The exploration regulations were put in place in 2001, but the ISA was also set up with another mandate to deliver rules of exploitation, in other words, to deliver a Mining Code which allows this industry to go forward. The ISA has been mandated legally, and this was an agreement that all countries who signed up to the U.N. Convention on the Law of the Sea agreed to deliver this Mining Code which allows exploitation to occur while protecting the environment from serious harm.
The target for the ISA is to finalize these rules over the next year and to adopt the rules to allow commercial production in 2025, and we are confident that they can meet that deadline.
CMJ: Why are the global plans for deep sea mining facing a lot of opposition? Why in your opinion did the Canadian government ban it? Do you think the federal government should lift the ban on deep sea mining?
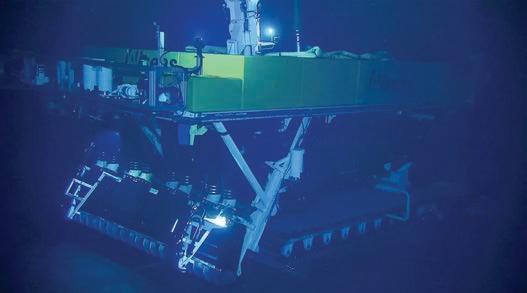
The Allseas-designed collector vehicle’s flow-lift system direct jets of seawater over the tops of the nodules to collect the rocks without touching them and then channel them inside the vehicle. CREDIT:
CS: The Canadian government did not ban it. The government’s position is that deep sea mining, whether it is in Canadian or international waters, should not take place until the environmental impacts are better understood and until regulations are in place. We think, to make those informed decisions, we must do the science and that is exactly what TMC and other companies have been doing. We spent over $150 million on our environmental research program over the past decade. There is a significant amount of pressure on some governments brought by NGO opposition groups like Greenpeace, for example, that have put a lot of pressure on governments to take a political stance.
The only country that pushed for a ban is France, and then France quickly walked back that call for a ban around the same time that they extended their own exploration contract for polymetallic nodules in the CCZ. You might hear a lot of things coming out of various capitals, and that might be good for short-term political wins, but what I would ask you to pay attention to is the behaviour of the countries at the ISA meetings. The contingents from many countries who have called for a pause continue to work constructively to deliver the final rules to regulate this industry, and to ensure that when deep sea mining does occur that it is done in a way that protects the environment from serious harm. That is their mandate by the ISA. That is the mandate that they all agreed to, and we are very encouraged that most of the small minority of countries that have taken a contrary stance do keep that mandate in mind. There are 168 member states of the ISA plus the European Union, and only 24 have called for a ban, a moratorium, or a pause, so the vast majority have not taken that type of extreme position. There is a lot of pressure from NGOs and a lot of NGO funding where they are focused on marketing for Northern European countries and others who have come out and made these political statements. We would say, “They are welcome to make those statements, but they still have the legal mandate to deliver a Mining Code that allows this industry to begin, and that is what we see happening. We expect to show the world that this can be done responsibly.”
CMJ: What is different from Canada in the case of Norway? Why did the Norwegian government/parliament approve it, and what are the other countries that are moving ahead with deep sea mining?
CS: Norway sees that oil and gas exploration may be under a bit of pressure in the coming decades as we move to decarbonize.
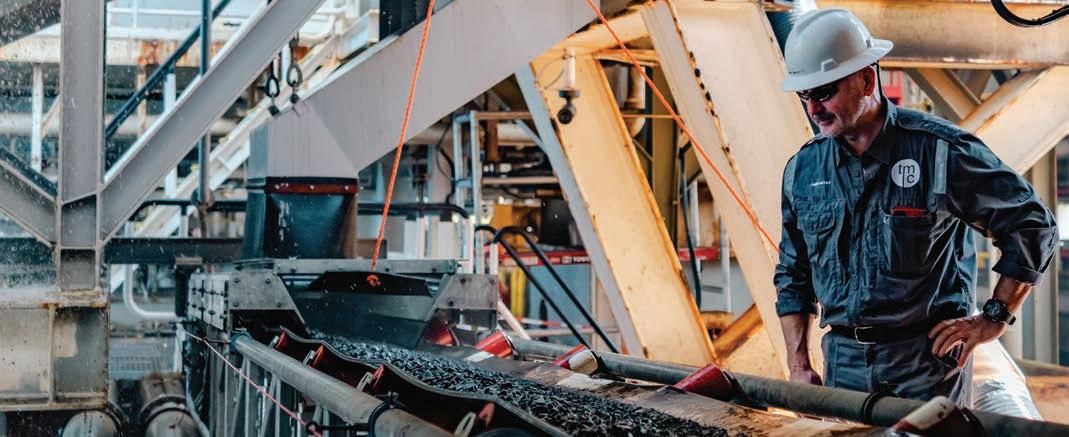
Norway has a very established industrial expertise when it comes to offshore exploration and extraction. This is an opportunity for that country to pivot from fossil fuels into metals to transition to a clean economy. Keep in mind that four out of every five cars sold in Norway are electric vehicles, and Norway knows that electric vehicle metals must come from somewhere, and they know that the appropriate way to assess the impacts are on a relative basis to the options for land-based mining. Norway also knows that you cannot magically recycle your way into material supply growth.
So, Norway announced their moves this year regarding deep sea metal resources, opening their territorial waters for exploration and, pending environmental work, potentially exploitation. Also, Japan has noted that they are going after rare earth metals in seafloor mud in their territorial waters. And of course, China is focused on this aggressively. This has led other countries, even the United States who is not a member of the ISA, to focus on the potential of seafloor polymetallic nodules. There is an increasing cadence of political support within the U.S. Congress for polymetallic nodules and now the U.S. Pentagon, the Department of Defense, is going to have to deliver a report to the House Armed Services Committee on their plans for the processing and refining of polymetallic nodules expected in March 2024.
It is worth mentioning that last year, the U.S. offshore company Transocean, made an investment in the Belgian contractor GSR, and they devoted a Samsung 10000 drillship to that contractor as well to do a collector test in a few years.
CMJ: What are polymetallic nodules? What are the metals/ minerals that could be mined from deep sea?
CS: People often think that deep sea mining is all the same. Just like on land, there is a wide spectrum of projects with a wide spectrum of impacts. It is the same thing in the deep ocean. TMC is only pursuing the collection of polymetallic nodules, and they are small potato-sized rocks that sit unattached on top of the seafloor in the abyssal zone. The ones we are focused on are in the abyssal zone of the Pacific Ocean in the CCZ.
These nodules form very slowly over time. They precipitate the metal from the sediment on which they sit, as well as the metals dissolved in the seawater. The nodules that we are focused on in the CCZ have high concentrations of nickel, copper, cobalt, and manganese. Because these nodules are polymetallic, multiple metals, it means our economics are incredibly attractive because the grade of the metals in nickel equivalent is over 3%, and that is much higher than almost any other undeveloped nickel project in the world. In fact, Mining.com for two years in a row, in 2022 and 2023, has ranked TMC’s NORI and TOML projects as number 1 and 2 when it comes to the world’s largest undeveloped nickel projects.
There are other types of deep sea metal resources, such as cobalt crusts and the seafloor massive sulfides. Those are resources that tend to be in shallower waters, the extraction process is different. Whereas nodules are just collected because they are unattached to the seafloor.
Benchmark Mineral Intelligence, a blue chip research firm in this space, has done a life-cycle analysis comparing the impacts of getting nickel, cobalt, and copper from polymetallic nodules versus getting them from typical land-based sources, and what they found is pretty striking: For nickel and copper, in every single impact category they measured, nodules from our first production area NORI-D were the lowest on the scale for every single impact category and that includes roughly a 94% reduction in CO2 per tonne emissions relative to Indonesian nickel laterite RKEF processing. For nickel, we believe this is about as low an impact as one can get, and we think it is important for the world to see this type of information to make an informed decision. Because we are going to need much bigger metal markets, and one option is to pick them up from this seafloor resource at a low touch, and the other option is deforestation and tailings issues. So, this is why polymetallic nodules are incredibly special, and at the end of the day, it all comes back to the grade. We can talk about technology, regulations, or economics, but what drives everything is the grade of the material, and the grade of these polymetallic nodules is extremely high, which means we can move less material to get the same amount of metal. That brings down our environmental impacts. It also brings down our cost of extraction.
We are seeing that there has been a lot of speculation about what the impacts might be, and now I think, as a society, we must move away from speculation and look at the observed
impacts from actual research and in-field observed data. Now, we are starting to see that come out, and in-field observed data contradicts a lot of that speculation.
There are some interesting organisms on the abyssal seafloor; there are a lot of interesting creatures. But over 70% of the biomass per square metre is bacteria. The abyssal zone is the ecosystem on the planet with the least life per square metre. Excluding microbial life, this is also the area that planet with one of the lowest levels of biodiversity. This is an abyssal zone that is quite common: covering over 60% of the Earth’s surface, this is the most common ecosystem on the planet and is remarkably similar over wide areas. That means it can effectively be protected through conservation. The ISA already set aside 43% of the CCZ for protection, allowing any of those species a place to live, thrive, and from which they can then re-colonize mined areas. These species will continue to be studied by science, so protecting them through conservation is what we are going to do.
TMC has also contributed more biological occurrences to the Ocean Biodiversity Information System than all other companies combined. Researchers can search this database, download the information, and continue to advance our knowledge on what species are down there.
CMJ: Can you talk to us about your exploration contracts in the Clarion Clipperton Zone? What makes the area so attractive?
CS: The CCZ is extremely attractive because of the types of metals that occur within these nodules. Nodules form in all the world’s oceans, for example, there are nodules west of Australia, but those nodules are iron focused, and they are not worth picking up. The CCZ is special in that the nodules have high concentrations of nickel and copper, both valuable metals, and that is what drives our project’s economics. The reason these nodules form and have high abundance in the CCZ is like the Goldilocks Zone, where all the conditions are right. They happen to form close to the Rockies and the Andes. Both of which have always historically been hotbeds for base metals.
As these nodules form, they precipitate the metal from the sediment and from the seawater, so they grow slowly much like the way a pearl forms. As I mentioned before, the nodules have high concentrations of nickel, copper, cobalt, and manganese, but they are also special because they have a consistent mix of those metals. You can tell how big your resource is because the nodules are sitting there on top of the seafloor. They are not buried underground. Those nodules are sitting on top of the seafloor which can be effectively imaged in addition to sampling.
Across two of our exploration contract areas, NORI and TOML, we have identified resources through technical reports that are compliant with Canadian National Instrument 43-101, and SEC S-K 1300 reporting standards. Across those two resource statements, we have identified 1.6 billion tonnes of these nodules, so the resource is massive. It is extremely scalable and importantly, we can use existing technology and existing offshore assets to collect this resource.
CMJ: Are there other companies that have been issued exploration contracts to mine in this area?
CS: There have been other countries and contractors that have been issued exploration contracts to explore, but none to mine to date. Nobody has been commercially mining in international waters. TMC expects to be the first contractor to begin production of seafloor resources in international waters, and we would expect to begin commercial production around the end of 2025. We estimate that would be a five-year head start on the next contractors who might move into exploitation. That would include GSR, a subsidiary of the DEME company out of Belgium. There are also two contracts in the CCZ held by Chinese contractors, Beijing Pioneering and China Minmetals. The Washington Post did a deep dive on Chinese intentions in international waters with respect to seafloor resources, and why China is pushing ahead to try to dominate this industry, as they have the processing and refining capabilities for metals on land.
CMJ: Can you describe the nodules mining process and some of the obstacles that you face in the field?
CS: The system consists of a ship on the surface connected to a riser pipe that is then connected near the seafloor to a robotic collector vehicle. Think of this like picking up golf balls on a driving range. The collector vehicle goes over the top of the nodules it shoots a jet of water, passing the curved collector head of the vehicle that creates negative pressure and a lift effect. The nodules are gently lifted into the hopper within the collector vehicle, and then they ride up on compressed air 4,200 metres (about half the height of Mount Everest) to the vessel waiting on the surface. From that point, the nodules are then offloaded to a bulk carrier, and that carrier can be brought anywhere to where the processing infrastructure already exists. We proved our processing flowsheet through pilot tests in 2021 which was developed with Canadian engineering firm: Hatch. We have announced a binding MoU to perform pre-feasibility work on processing nodules in Japan with Pacific Metals, or PAMCO. They have an existing rotary kiln electric arc furnace line, or RKEF, which is expected to require no capex from TMC and minimal modifications, that is ready to accept the nodules from the first production vessel provided by our partner and shareholder Allseas for our exclusive use. Thus, we can take advantage of existing assets to process the nodules.
CMJ: How does the future look like for deep mining and for TMC?
CS: The future for both deep mining and TMC looks very bright. We are at an interesting stage here, where perception takes a little bit longer to catch up. But the actual data, the reality of what nodule collection is, and what it can mean for the clean transition, is clear. We are already convinced that this is one of the key answers to how the world can decarbonize, and we are pleased to be at the forefront of this new industry. Taking a step back, this feels like the oil and gas industry in 1960, where 0% of production once came offshore and then very quickly, one third of production came offshore. We think it will be a comparable situation in terms of seafloor metal resources, and we are excited at the chance to be the first ones through the door. CMJ
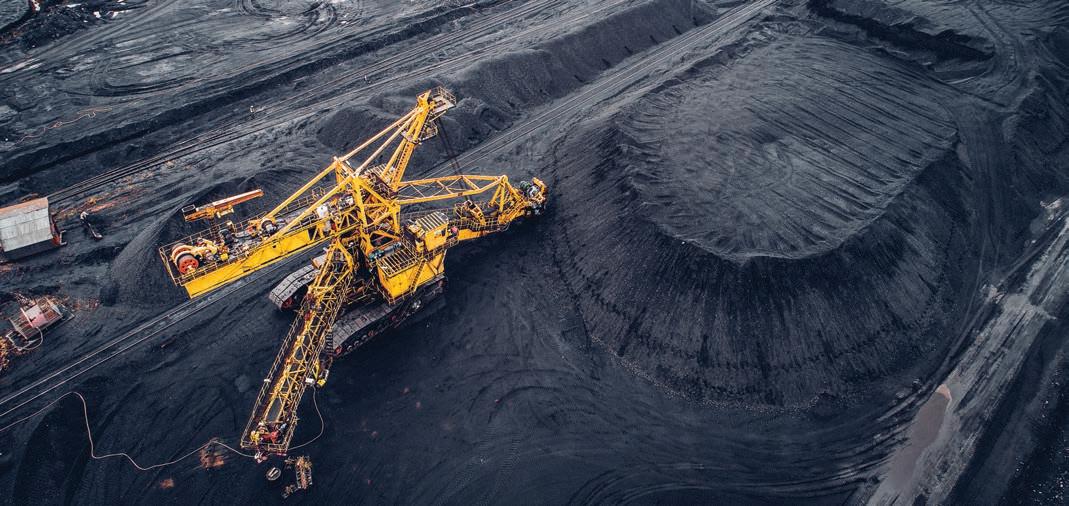
BENEFITS OF THE GRASSY MOUNTAIN COAL PROJECT IN ALBERTA
Even though Alberta has a moratorium on new coal mines, and the province’s coal-fired electricity generating plants have almost all been converted to natural gas, there is one mining company that has been working diligently for the past nine years trying to get its new coal mine project approved in this province.
Citing a need to extract high-quality metallurgical coal for steel-making purposes for the global market, in November 2015, Australia-based Northback Holdings applied to the Alberta Energy Regulator to construct and operate a coal mine.
If approved, Northback’s Grassy Mountain coal project (GMCP) will be located on legacy mining lands approximately 7 km north of Blairmore in the Crowsnest Pass region in southwestern Alberta.
The project description for the GMCP says the maximum production capacity of the coal mine would be 4.5 million tonnes of metallurgical coal per year, over a mine life of approximately 23 years. The project would include surface pits and waste rock disposal areas, a coal-handling and processing plant with
associated infrastructure, water management structures, an overland conveyor system, a rail loadout facility, and other facilities.
The project’s mining activities would be completed by blasting and truck-andshovel mining. Rock above the coal would be drilled, blasted, and hauled to waste rock disposal areas or used to backfill a portion of the mine pit. The pit would be approximately 1.8-km wide, 6-km long, and up to 430-metres deep. Once the mined coal has been removed, it would be transported by truck to the coal-handling and processing plant, where it would be cleaned to make a saleable product.
Waste rock and process fines from the coal-handling and processing plant would be disposed of in the waste rock disposal areas. After processing, the coal would be transported via overland conveyor to a rail loadout facility along an existing Canadian Pacific Railway track in Blairmore. The coal would then be loaded into rail cars and transported to marine facilities on British Columbia’s west coast.
Northback says it is committed to creat-
ing a better future through responsible and innovative resource development.
“The Grassy Mountain coal project sits on Category 4 land that was mined and abandoned, but never closed, over 60 years ago. Should our proposed high-quality, modern, steelmaking-coal mine be approved, the previously abandoned mine would be reclaimed during the lifetime of the project,” said Northback.
Not only would this coal project provide much needed high-quality, hard coking coal for the global market, the coal mine would provide much needed socio-economic benefits. Northback says, “Should the Grassy Mountain coal project become operational, it would create jobs, economic investment, growth, and improve the prosperity in the Crowsnest Pass region and Alberta.”
During the operations phase, the GMCP would employ approximately 400 workers directly. The project would pay tens of millions of dollars annually in royalty payments and individual and corporate income taxes to the provincial and federal governments and hundreds of thousands of dollars in municipal
taxes over the life of the project.
Northback says it is proud of the investments it has made in community organizations and social initiatives, including an important nutrition program. “Through Northback’s eight annual Australia Day events, we have raised more than $297,000 for schools, local groups, and the local health foundation,” added Northback.
There are many supporters of Northback’s GMCP application. The Coal Association of Canada (CAC) believes the coal mine would be important not only to the Crowsnest Pass region but to the entire industry and supply chain and would play a significant role in future investments in Canadian coal operations. The town of Pincher Creek believes the coal mine would be an economic driver for the Crowsnest Pass region. And the municipality of Crowsnest Pass believes the project would provide essential tax relief for the residents of Crowsnest Pass.
The CAC’s overall view of this coal project is positive. “We believe that Northback’s Grassy Mountain coal project will be positive for the region, a depressed area in southwestern Alberta, which is a long-standing coal mining area in the province. The residents of the area want their children to stay in the area after they finish school, but there are no good jobs for them there, other than good coal jobs,” says Robin Campbell, president of the Coal Association of Canada and a former Alberta Minister of Environment and Sustainable Resource Development.
The CAC believes the coal project would add real socio-economic benefits to the area. “For each coal job, there will be an additional three jobs in the trades, suppliers, and transportation, including the railway and ports in B.C.,” says Campbell. Northback says demand for metallurgical coal is expected to rise by more than 50% by 2050. “Combined imports from India and Southeast Asia are expected to grow from approxiamtely 90 million tonnes today to about 170 million tonnes in 2040, with additional growth expected from Latin America, Africa, and the Middle East, which combined will rise from approximately 20 million tonnes today to about 50 million tonnes in the late 2040s.”
Campbell says the world needs steel and the global demand for steel continues to increase. “Alberta and Canada
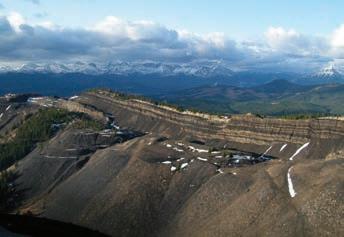
have high-quality coal, which makes good coking coal, and they should be part of global coal growth,” Added Campbell. Steel is necessary to achieve Canada’s net-zero emissions goals. Northback says the mining industry produces the primary products required for generating, distributing, and delivering renewable energy. “The first step in the supply chain to create solar panels, wind turbines, and electric vehicle batteries begins with mining companies like Northback,” they added.
However, in June 2021, the Alberta Energy Regulator (AER) denied Northback’s application under the Coal Conservation Act and related applications under the Environmental Protection and Enhancement Act, the Water Act, and the Public Lands Act, saying, “We find that the project is not in the public interest.” Some of the reasons cited as to why the application was denied were because the regulatory body believed the project was likely to cause significant adverse effects on surface water quality, fish, and trees.
Regarding the environmental concerns surrounding GMCP, the AER has mining legislation and regulations in place that Northback would have to follow if its application was approved.
Campbell says, “Northback will more than likely go above and beyond what the regulations require. Coal miners who work at the Grassy Mountain coal project would live in the area where the town’s water source is, so Northback is not going to engage in any risky operations that could contaminate the local water source. New coal mines, including the coal mine Northback would build, use closed systems, which means they are covered and use recycled water. As well, today’s coal mines use new technologies which reduce negative impacts on the environment.”
Northback’s water management plan includes limiting water use and ensuring
management and mitigation systems are in place for selenium and monitoring systems at and around the project site to grow its environmental baseline database and assist in planning future activities. The company is also conducting critical habitat studies and consultations with subject matter experts to inform its environmental programs.
Northback says, “As we live and work in the Pass, protecting and preserving the environment, including local wildlife, vegetation, air, and water, is a priority for Northback.”
In more recent developments, on Aug. 31, 2023, Northback submitted three new applications to the AER: one for authorization to run a coal exploration program, one for temporary water diversion, and one for a deep drilling permit (to drill 46 boreholes between 150- and 550-metres deep on a mix of crown land and its own private land to obtain raw coal samples/ acid rock drainage samples and model the structure of the coal seams).
On Feb. 13, 2024, a federal court threw out a decision from the federal environment minister denying a permit for Northback’s coal mine, which was in response to two First Nations, who said they never received a consultation opportunity they had been promised by the joint review panel that reviewed Northback’s application. Now, the federal government will be forced to revisit the issue after consulting with the bands on the economic benefits of the proposed coal mine.
On Feb. 23, 2024, the AER announced that Northback’s exploration drilling applications will be decided by a panel of hearing commissioners. A public hearing date has yet to be set. The AER also stated it had received confirmation that the GMCP has been classified as an advanced coal project and remains one regardless of previous application outcomes.
Canada is the world’s third largest exporter of steel-making coal. The strong demand for this type of coal is expected to continue well into the second half of this century. The coal mined from GMCP would be sold to companies based in Asia, including Japan and South Korea, which are leading the steel industry in reducing carbon emissions through carbon capture. CMJ
Diane L.M. Cook is a freelance mining writer.
CRITICAL MINING IN BRITISH COLUMBIA: $36 BILLION IN CRITICAL MINERALS INVESTMENT AT STAKE
Sixteen proposed critical mineral mines, representing $36 billion in near-term investment, 300,000 person-years of employment, and $11 billion in tax revenues, are at a key juncture, based on findings of a new independent economic impact analysis conducted for the Mining Association of British Columbia (MABC). The study evaluated the potential economic impact of proposed new critical mineral mines and extensions to existing critical mineral mines in B.C.
The study examined 14 potential critical mineral mines and two mine extensions and found the long-term economic impact of operating these mines over several decades could be nearly $800 billion.
Critical minerals can provide B.C. with a potential short and long-term economic boost and position the province to be a key player in the global market.
The mining industry in B.C. supports more than 35,000 jobs and over 3,700 small, medium, and First Nations businesses in every corner of the province through an annual spend of $3 billion.
Despite his busy schedule, Michael Goehring, president and CEO of MABC, spoke with the Canadian Mining Journal about the current state of B.C.’s and Canada’s mining industry.
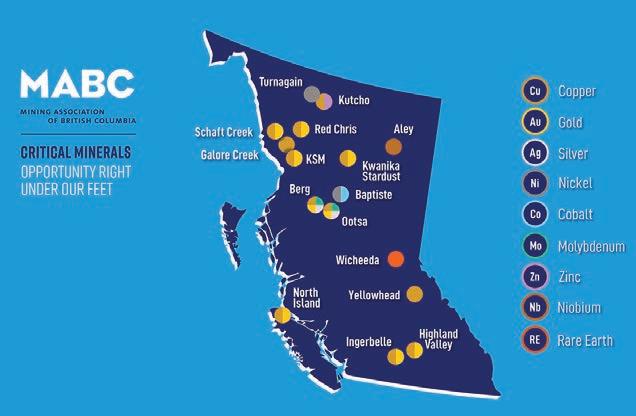

Q: Can you talk to us about your background? How did you benefit from your previous experience in your current role?
A: Prior to joining MABC, I was a partner in Canada’s largest public relations and public affairs agency where I specialized in the natural resource and mining sectors. Our clients brought us unique and complex challenges to solve, ranging from regulatory and policy obstacles to high-wire issues management. This experience has been beneficial in positioning me in my current
role. I joined MABC in 2019 and have not looked back! Mining is a great industry. There is an evolving understanding and recognition of how important mining is to everyday life; and of course, to the global energy transition.
Q: In your opinion, what are some of the major issues affecting the mining sector in B.C.?
A: There are four major issues in my opinion:
1. Continuing to sharpen the fiscal competitiveness of mining in B.C.
2. Fast-tracking permitting authorizations and project execution.
3. Enhancing Indigenous participation and advancing economic reconciliation.
4. Accelerating new and strategic investments in electrification infrastructure ― which drives emissions reduction and aligns with global net-zero commitments. There is an urgent need to meet the rising demand for critical minerals essential for electric vehicles, wind turbines, solar panels necessary to support the energy transition.
Q: What are some of the under-represented mining industry issues in general?
A: At MABC, we have made several recommendations to the government of B.C. and the government of Canada relating to the speed of permitting when it comes to new mining projects, of course without compromising environmental protection.
While we know that the federal government plans to reduce the time it takes to develop new critical mineral mines from 12-15 years to potentially five years, we need to see action and alignment between both governments to come together to make this happen now.
Enhancing Indigenous participation and advancing economic reconciliation is also critical. We have consistently made two recommendations to governments: First, we need to see coordinated assistance for Indigenous governing bodies to allow them to build their own governance, technical, and administrative capacity, on their terms, to participate in government-to-government processes and shared decision making. Second, provincial and federal governments need to cooperate to develop financial instruments that will enable Indigenous co-ownership and equity positions in critical mineral and other natural resource projects if they choose.
We were very pleased to see the government of B.C. announce details of a new First Nations equity financing framework in Budget 2024.
Finally, to unlock the full potential of B.C.’s critical mineral resources, we need to see strategic investments in new electric
DON’T GUESS. KNOW.
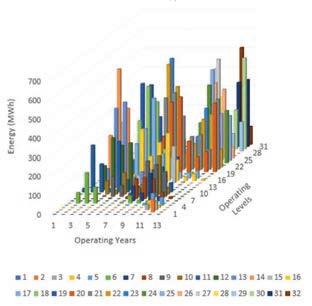
infrastructure as well as new value chain opportunities that can help drive industry growth through refining or processing. We have been recommending government expand B.C.’s electrical grid to support and electrify mine extensions and advance decarbonization at existing operations.
Q: MABC recently conducted an independent critical minerals economic impact analysis and released the findings in January 2024; can you please talk to us about some of those findings?
A: The finding clearly showed that critical minerals offer British Columbians a generational opportunity, while making a significant contribution to climate action. There are 16 proposed critical mineral mines in B.C., which could provide $36 billion in near-term investment. Other key highlights include the following:
> B.C. mining supports 35,000+ jobs.
> Over 3,900 small, medium, and First Nations businesses benefit from mining in B.C.
> The industry generated more than $18 billion in economic activity and almost 30% of the province’s goods exports in 2022.
> Several of B.C.’s critical minerals ― including aluminum, copper, and nickel ― are indispensable to clean technologies and the energy transition.
Q: What can the province do to realize the economic benefit that critical minerals provide?
A: We need to see government action in those four areas I mentioned earlier. We need continued focus by government to nar-
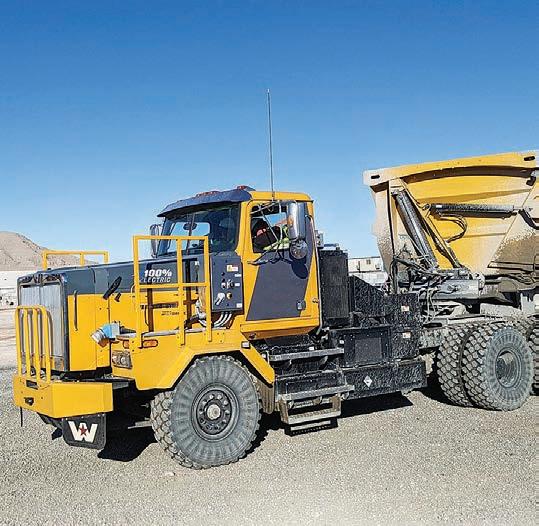
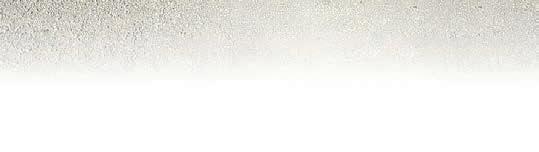

row the competitiveness gap between B.C. and other provinces, such as Quebec and Ontario. Government policies that support and accelerate permitting authorizations and project execution, as well as policies that support Indigenous participation and economic reconciliation, would immensely help our industry and Indigenous Peoples. Another point is targeted investment and funding for new electric infrastructure to power new mines and ensure that B.C.’s mines and smelters have the lowest greenhouse gas (GHG) emissions in the world. We would like to see the federal government take a strong focus on B.C. with respect to the Critical Minerals Investment Fund and the critical minerals opportunities that exist in the province, along with Canada Infrastructure Bank and existing federal budget commitments to critical minerals.
We can unlock the opportunity critical minerals offer B.C. if we have competitive fiscal policies that can attract and retain investment here in B.C. Workers in urban and regional centres, small towns, and First Nations communities deserve to benefit from the growth of our sector through high-paying, family-supporting jobs.
Q: In your opinion, how can the province build on the successful relationship with the Tahltan Nation and use it as a model for working with other First Nations?
A: It really comes down to listening, and early and genuine engagement. New mines are only permitted and authorized in B.C. with a very high level of partnership with the First Nation or Nations on whose lands the project is sited. That is why MABC, on behalf of its members, has been advocating and asking governments to ensure that First Nations have the governance, administrative, and technical capacity to participate in government-to-government negotiations and mining projects.
Q: The province recently released Phase One of its “Critical Minerals Strategy.” What are the positive points in the strategy and what is missing that MABC would like to see in the next phase?
A: MABC supports the direction that has been set out in Phase One of the strategy. However, I must make clear that the strategy was originally missing one fundamental component, which we diplomatically pointed out to the government: a competitive fiscal policy. That said, I am pleased that in Budget 2024, the government recognized this shortcoming and rectified it by making improvements to the Output Based Pricing System for critical minerals in B.C. It is a step in the right direction and will help narrow the province’s competitiveness gap with Ontario and Quebec. There is more work to be done.
Q: Finally, how do you see the future of mining in Canada?
A: I am concerned… Canada is poised to be a leading global supplier of critical minerals, needed for the energy transition and for new technologies for defence and national security. Many countries are looking to Canada as a reliable and responsible supplier of those critical minerals and metals. However, I am concerned that this potential could be lost owing to the fact that there are several competing priorities on the government’s agenda and that critical minerals might not receive the attention they deserve. We must move from aspiration to action. We need to show investors and allies that Canada can get things done. If we do not, capital will flow elsewhere. CMJ
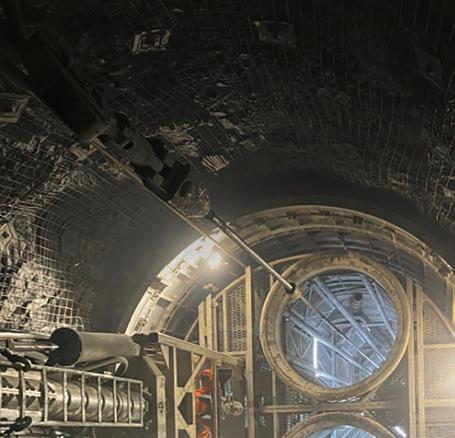
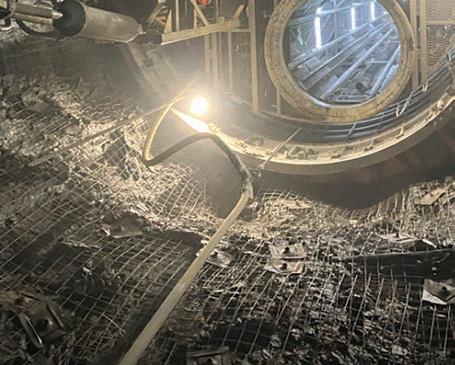
ARGENTINA’S ABUNDANT COPPER AND LITHIUM
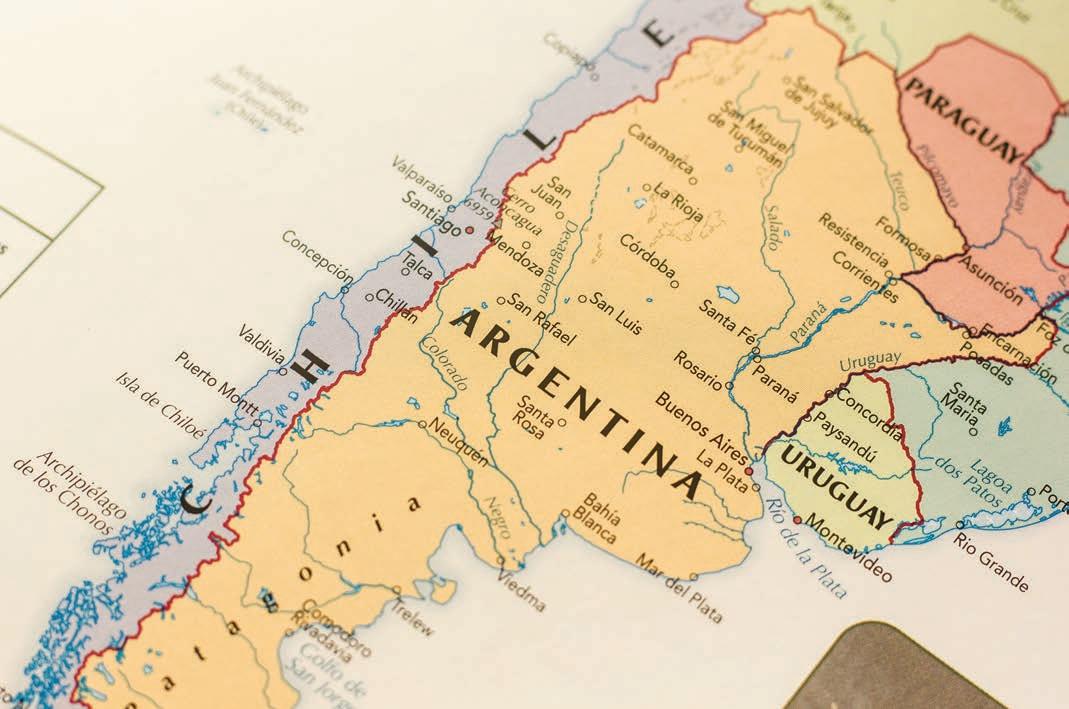
Argentina has a new president ― and an abundance of raw materials. The country is sitting on a trove of mineral wealth, particularly when it comes to copper and lithium. It is now widely discussed in Argentina that both are critical elements in the quest for a safer and greener energy transition.
Let us delve into the details of the business opportunities which these resources represent in Latin America’s third biggest economy. (Argentina’s GDP is an estimated US$1.2 trillion, surpassing Colombia’s US$1.09 trillion. Brazil and Mexico remain the top two players even under this metric):
Copper
Abundant reserves: Argentina boasts the world’s fourth largest copper reserves, estimated at 44 million tonnes. This potential is largely untapped, with only a handful of operating mines.
Strategic location: The country’s copper deposits are concentrated in the Andean belt, known for its high-grade ores and proximity to key markets like Asia and Europe.
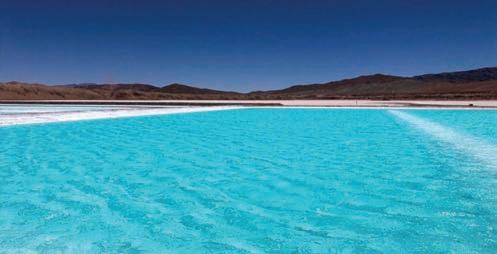
Growing demand: The global appetite for copper is surging, driven by the electrification boom, particularly in electric vehicles and renewable energy infrastructure. This trend is expected to continue for decades, presenting a lucrative opportunity for Argentina.
Major projects: Several large-scale copper projects are in the
pipeline, such as Mara in San Juan, expected to become one of the world’s largest copper mines. These projects have the potential to transform Argentina’s mining landscape and generate significant economic benefits.
Lithium
Abundant reserves: Argentina holds the world’s third largest lithium reserves, a key ingredient in lithium-ion batteries powering electric vehicles and electronics.
Strategic location: Argentina is one key part of the “Lithium Triangle” ― along with Chile and Bolivia. These three, taken together, contain over 70% of global lithium resources. This region is poised to play a dominant role in the global lithium supply chain.
Innovative extraction: New extraction technologies ― such as direct lithium extraction (DLE) ― do offer more environmentally friendly alternatives to traditional methods, addressing concerns about the environmental impact of lithium mining.
Major players: Argentina has witnessed a surge in lithium mining investments in recent years, with major players like Livent, Ganfeng Lithium, and Allkem developing projects. This rapid growth signifies the immense potential of the country’s lithium sector.
The challenges
Despite the immense potential in the minerals sector, both copper and lithium mining companies working in Argentina face challenges. Executives working in the key companies have been saying that environmental concerns, community engagement, and regulatory hurdles need to be addressed responsibly to ensure sustainable development.
However, with a new president having been elected in October 2023, the opportunities may now outweigh the challenges. Argentina clearly has the potential to become a major player in the global copper and lithium markets, attracting significant investments, creating jobs, and boosting its economy. By implementing sustainable practices and addressing stakeholder concerns, Argentina can harness its mineral wealth responsibly and contribute to a greener future.
> Argentina’s government is actively promoting the mining sector, offering attractive investment incentives and streamlining regulations.
> The country’s skilled workforce and well-developed infrastructure provide a solid foundation for the mining industry’s growth.
> Research and development in lithium extraction technologies like DLE can further enhance Argentina’s competitive edge in the sustainable lithium market.
Argentina has vast natural resources in energy and agriculture. Within its 2.8 million km2 of territory, Argentina is endowed with extraordinary fertile lands, gas, and lithium reserves, and has great potential for renewable energy. Argentina is a leading food producer with large-scale agricultural and livestock industries. In addition, Argentina has significant opportunities in some key manufacturing subsectors, and it has innovative service providers in various high-tech industries.
While Argentina’s economy expanded by 5% in 2022, the impact of a devastating drought is expected to result in a 2.5% negative growth in 2023. Growth is expected to accelerate in
2024, because of improved climatic conditions, continued historically high soybean prices and investments in the energy sector that will allow the country to reduce gas imports and improve external accounts.
The severe drought has deteriorated economic conditions and further amplified preexisting macro imbalances. Annual inflation accelerated in 2023, reaching 124% in August, affecting marginalized segments of the population. According to national statistics published in September 2023, poverty stands at 40.1% and extreme poverty stands at 9.1%.
Argentina is currently (since early 2022) under a 30-months Extended Fund Facility (EFF) with the International Monetary Fund (IMF). By August 2023, the IMF Executive Board completed the combined fifth and sixth review of the program, granting Argentina access to about US$7.5 billion. Key program targets were missed through the end of June 2023 on account of the historic drought. Modifications to the reserve accumulation target, as well as to the (nominal) primary fiscal balance and monetary financing of the deficit targets, were also approved ― alongside a commitment to implement a new policy package aimed at correcting policy setbacks, safeguarding stability, and securing core economic objectives.
Argentina stands at the crossroads of opportunity with its vast copper and lithium resources. By embracing responsible mining practices, addressing environmental concerns, and engaging with local communities, the country can unlock its mineral wealth. If and when the national government makes the right moves, it could pave the way for a more sustainable and prosperous future. CMJ
Gordon Feller is a freelance mining writer.
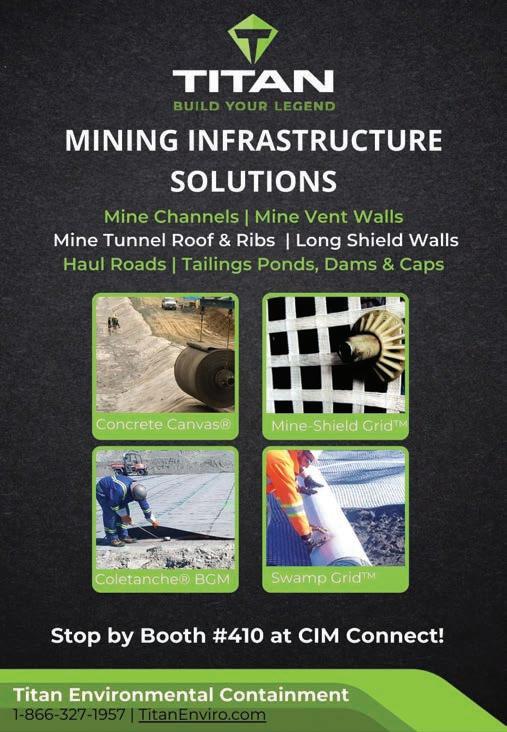
USING AUTOMATION TO CORRECT CONVEYOR BELT MIS-TRACKING
The friction heat from a mis-tracking belt that comes in contact with a conveyor structure can pose an extreme danger in any dusty environment, not just coal. The U.S. Mining Safety and Health Administration (MSHA) attributes approximately 30% of belt fires to friction caused by critical mis-tracking or belt slippage. Mis-tracking can happen so quickly, often a 24-hour inspection cycle is not enough to catch it and correct the belt path by adjusting idlers. Automated tracking devices monitor minor variations in the belt path and make immediate adjustments to avoid belt stoppage and unscheduled downtime.
With so many factors contributing to belt mis-tracking, achieving perfectly centered alignment may not be possible for most conveyor systems. Everything from ambient temperature to changes in material grade can impact belt alignment causing spillage and belt damage. But mis-tracking is as much a safety issue as it is an efficiency and spillage issue, so monitoring belt drift to avoid contact with the structure is critical.
Current CEMA/ISO standards
Conveyor Equipment Manufacturers Association’s (CEMA) Guide and the International Organization for Standardization (ISO) Standards 14890 and 15236-1 are very similar in their recommendations for normal belt deviation from the central path. The CEMA Guide is based on standard CEMA components and the ISO standards on the conveyor belt construction tolerances such as camber and troughability.
According to the ISO allowance, the conveyor belting, when running on a correctly aligned conveyor with centered loading, should not deviate from the central track by more than ±40 mm for a belt width up ≤800 mm, or by more than ±5% of the belt width for widths over >800 mm with a maximum of ±75 mm.
There are three categories into which mis-tracking can be graded: Allowable mis-tracking is the amount of design mis-tracking under normal conditions. Some deviation from perfect tracking is bound to happen on any system due to many operational and environmental factors.
> Actionable mis-tracking happens when operational or environmental factors influence belt tracking to the point where spillage or damage to the belt and/or structure occurs.
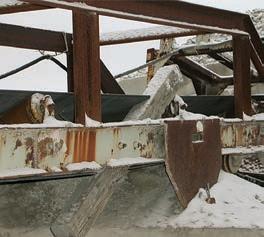
Attempt to control critical mis-tracking symptoms using a timber.
> Critical mis-tracking is a second-level fault that creates an immediate and serious risk of substantial damage and injury to personnel. Critical mis-tracking must be corrected immediately to avoid additional spillage, belt or structural damage and other safety incidents.
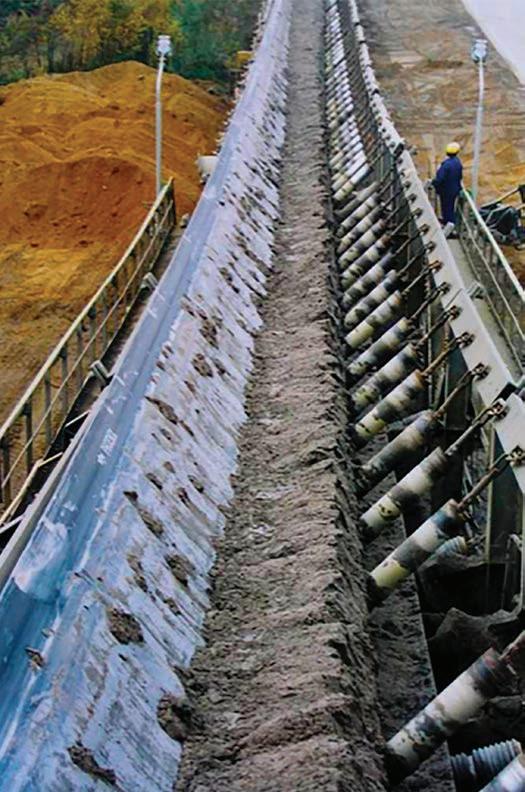
Consistent belt tracking is a system issue that must be addressed at every stage from specifications to the conveyor’s initial design, installation, operation and maintenance. The project specification should state the mis-tracking allowance as it affects the selection of the belting, structural clearances, and rotating components.
Conveyor installation and retrofits
Installation of the conveyor structure and alignment of the rotating components is the foundation of a system designed to track properly. Often when replacing a belt, components are moved out of the way and not reset in the proper position. Mixing idler brands to save a few dollars or in search of the “perfect” idler can affect belt-to-idler contact and loading point spillage.
CEMA installation tolerances should be followed in the fabrication, erection and mounting of the rotating components. Benchmarks should be established, especially for the main pulleys, so in the event of chronic mis-tracking, there is a reference for confirming the main pulleys are level and square as a starting point for correcting mis-tracking.
The same is true for resetting the idlers square to the centerline as they are often haphazardly knocked and shimmed in an attempt to treat symptoms rather than root causes of mis-tracking. There is a long-standing belief that the belt always tracks to the side of the idler or pulley that it contacts first, so many operators will adjust an idler by pivoting it slightly to move the belt tavel as a corrective action. However, when rolling components are misaligned both horizontally and from level, common corrective actions do not always apply.
When the components are misaligned both horizontally and vertically, the belt tries to flex and contact the component at both edges at the same time. Depending on the direction of travel, an out of level component creates a right hand (RH) or left hand (LH) screw thread effect and the belt may not respond intuitively depending upon which misalignment force dominates, making troubleshooting difficult.
Over time, several corrective actions along a system might cause the belt to develop a memory, making aligning a replacement belt difficult. Excessive adjustments of idlers to treat mis-tracking symptoms increases power consumption and bottom cover wear. When installing a new belt, it is best practice to reset the components within alignment tolerances.
ISO provides an overall allowance independent of the conveyor section or components. CEMA members realized that there was more to the question of misalignment than the free belt edge in the load zone and developed mis-tracking guidelines based on CEMA standard components. CEMA establishes mis-tracking allowances at three critical locations of the conveyors: main pulleys, the carrying side and return runs.
Return side mis-tracking is limited by the width of the CEMA 502 standard return rollers (Fig. 2). Usually, the structure for mounting the return rollers is based on the carry idler base dimensions. Serious injuries have resulted from failed brackets causing falling return idlers. Offset brackets are available but just treat the symptoms of mis-tracking rather than the root causes. Wide base carrying idlers can be specified which in turn would require using a return roll of the next wider belt side, but this comes at an additional capital cost.

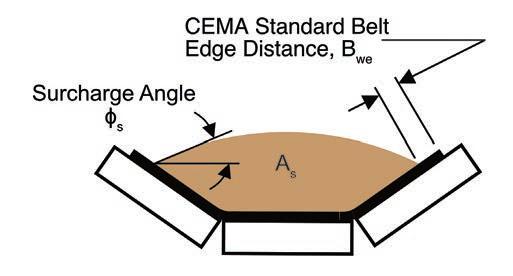
CEMA pulley misalignment tolerances are based on ANSI/ CEMA B105.1 standard pulley face widths (Fig. 3). When greater tracking variance is required, engineered pulleys are an option.
Proper belt loading
Operators and maintenance personnel should be trained on how overloading and off-center loading affects mis-tracking. Belt tracking is primarily through gravity (center loading) and friction (a minimum of 50% belt contact with the idlers). Spillage and carryback must be controlled for consistent tracking as buildup on idlers and pulleys changes the geometry of rolling components and can reduce belt-to-idler friction.
Skirting and mis-tracking allowances
The CEMA Guide started as a best practice for skirtboard sealing systems because spillage in the load zone due to mis-tracking is a common problem. There are many different sealing systems on the market. Depending on the spacing of the skirtboards and the thickness of the sealing system, there could be differences in the amount of free belt edge needed in the design for allowable mis-tracking in the load zone (Fig. 4). If there is a history of actionable or critical mis-tracking that cannot be mitigated, then an even wider free belt edge is warranted. Modern skirting designs are engineered to minimize spillage by creating a sealed environment within the loading zone. Depending on the type and allowable space of the belt, they can have a double seal that rides the belt offering greater sealing, but that can take up extra space on the belt edge. Skirtboards can lower maintenance costs by self-adjusting as they wear rather than having to be unbolted and adjusted manually when

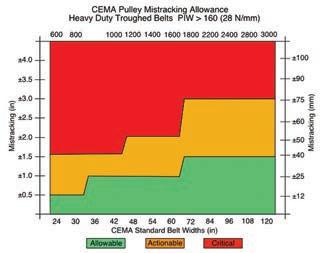

spillage becomes an issue. Once they have worn on one end, some models can be flipped to extend the equipment life.
Automated belt training
Accessories to deal with mis-tracking may come standard with conveyor systems. These are often “brute force” trainers that prevent the belt from coming in contact with the structure and are not actually training systems but merely protective barriers that lead to system issues and belt wear. When the belt drifts, the brute force trainers can cause the belt to fold into itself and fold back into the system. This can permanently damage the belt and lead to further mis-tracking and spillage.
Automated belt trainers use sensing arms to detect slight variations in the belt path. These arms are attached to a pivoting idler that reacts immediately to these variations and trains the belt back into alignment. If detected early enough, less force is needed to retrain the belt and ensure alignment throughout the belt path.
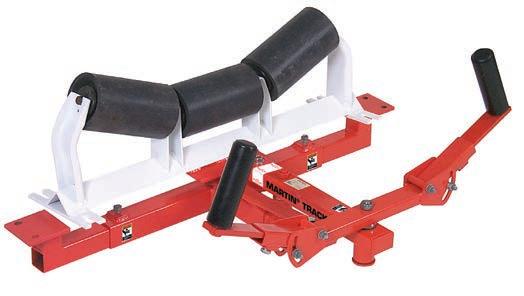
A belt can mis-track for various reasons at any time

Design options
The CEMA allowable mis-tracking recommendations do not apply to horizontal curves or specialty belts such as side wall belts. A good starting point for designing for misalignment is to examine current operating and maintenance practices either on site or in the mining industry.
Conveyors bought on 100% loading and price alone often experience tracking issues. Knowledgeable conveyor designers should consult the owner on the significance of design allowances, the costs and benefits associated with wider belts and less than 100% loading best practices. Training operators and maintenance personnel in techniques to reduce mis-tracking is an effective way to mitigate mis-tracking issues.
Laser alignment of components to CEMA installation standards is now a common technique for establishing conveyor alignment benchmarks. Positioning training idlers at critical locations is specified but commonly have limited ability to change the path of the belt when maintenance practices are poor, there are extreme environmental conditions or buildup on the rolling components.
Conclusion
Return trainers act in a very similar fashion but without a troughed roller. Training idlers are set slightly above the belt plane allowing the weight of the belt to offer some additional tension on the roller. As the sensing arm detects the belt drift, it turns the roller in the opposing direction to train the back into alignment. Since the low-tension belt return can easily become misaligned, a return tracker is especially effective when placed near the tail pulley to ensure the belt enters the loading zone aligned.
Autonomous belt mis-tracking makes sense from a production, labour, and safety perspective. A belt can mis-track for various reasons at any time, so installing economical equipment to mitigate potential belt fires is a capital investment in both the cost of operation and safety. Over the life of a conveyor, it is cost-effective to contact CEMA member companies for assistance in designing conveyors, specifying components, training, or troubleshooting to identify and prevent the causes of conveyor belt tracking issues. CMJ
R. Todd Swinderman is president emeritus of Martin Engineering
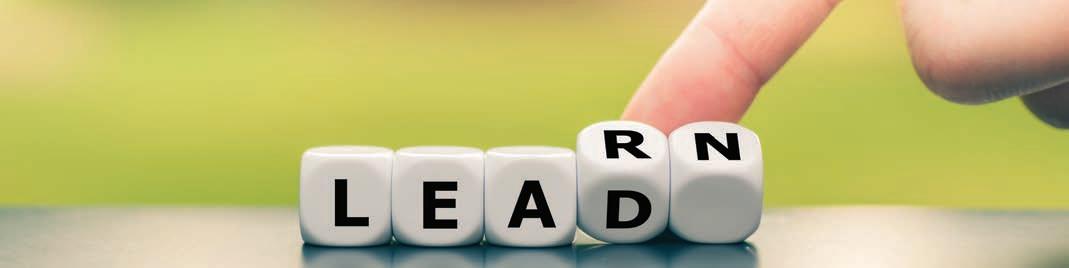
PART 2: WHAT IS THE CORRELATION BETWEEN TRANSFORMATIONAL LEADERSHIP AND THE PROFITABILITY OF ARIZONA COPPER MINING COMPANIES?
This article is the second of two articles: The previous article covered my hypothesis, and this article will discuss the findings from my research.
Demographics and Leadership Style
An interesting finding of this study was the correlation between demographic categories and leadership style. Most of leaders who have more than 16 years in the mining industry are more than 50 years old and have total top management team (TMT) tenure of more than 10 years. The comparison between organizational tenure of company leaders did reveal a significant difference.
When comparing the companies with the lowest copper price per pound and a “less transformational leadership (TFL) than the norm” group of leaders and the highest copper prices per pound and a “more TFL than the norm” group of leaders, there were several interesting findings. The company with the lowest cost per ton and a more transformational leadership (TFL) style had leaders with more than 16 years with their current organization, while the company with highest costs per ton but transactional leadership (TAL) style had few leaders with 16 or more years of organizational tenure. The higher cost, more TAL team had a lot of mining experience, more than 21 years on average, but less than five years of organization tenure.
The study showed evidence that a disadvantage of long-tenured TMT is isolation from outside information because they are no longer receptive to information that may threaten their perspective. From this, it can be anticipated that they will resist strategic change. I expanded on previous studies to look at tenure and its effects on the outcome in a sample of 100 organizations across different industries. I found that the tenure of the team did affect strategic choices, and long-tenured teams stayed within the norms of the industry. This finding was supported by other research. The less than five years of organization tenure mixed with the more than 21 years of average mining industry tenure may be the reason the company with the highest costs per tonne scored “more TFL than the norm” than the rest of the Arizona copper mining industry.
Another finding from this study was the relationship between
gender and TFL. In the review of literature, this relationship had a moderate or negative impact on effectiveness. Specifically, the female leaders in the Arizona mining industry scored above the 95th percentile in active management-by-exception. Overall, this shows that the female leaders in Arizona copper mining industry scored higher in both transactional areas. This would identify them as “more transactional than the Arizona copper mining norm.” All the transformational scores were in line with the Arizona copper mining industry’s mean scores. Another notable finding was that the company with the highest costs per tonne, a company that scored as “more transformational than the norm,” did not have any female members on its TMT.
Another finding from this study was the relationship between advanced education and TFL. In the review of literature, this relationship had mixed results. The study showed evidence that no relationship exists between growth and profitability and formal education. Having said this, other research showed evidence that companies with TMTs with little formal management education have more variation in their performance than companies with a highly educated team. Specifically, the leaders in the Arizona mining industry that possessed an advanced education scored above the 70th percentile in active management-by-exception. This score placed them 25% below the Arizona copper mining industry scale score in this leadership style. The research shows that leaders with an advanced education scored below the Arizona copper mining industry score in both transactional areas. This would identify them as “less transactional than the Arizona copper mining norm.” All the transformational scores were in line with the Arizona copper mining industry’s mean scores.
The company with the highest costs per tonne was the outlier and its leaders scored “more transformational than the Arizona mining industry norm.” Half of their leaders possess an advanced education, which was 25% of the total respondents. This compares to the Arizona mining industry’s mean that shows 18.34% possessing advanced degrees. The mean for the other five companies is 15.15%, which may be a contributing factor in this company’s resultant proclivity toward TFL styles
when compared to the rest of Arizona’s mining industry.
Conclusions
The investigation and data analysis bared the following findings: the data showed evidence that the managers employed more TAL styles compared to TFL; they quite often contemplated the moral and ethical consequences of their decisions and debated about what needed to be done but did not devote any time teaching and coaching; and managers with TAL styles concentrated on mistakes and deviations from standards frequently. In an industry that focuses on mining resources from the earth, this study showed evidence that the leaders employ leadership styles that mine their employees as well.
In the development of the constructs of TAL and TFL, there are two distinct schools of thought: dimensional and complementary. I investigated the dimensional school of thought by reviewing the literature, style, research, and my own observations. I felt that transformational and transactional leaders were distinct with TAL viewed as leaders that led by exchanging effort for something of value. On the opposite end of the continuum was TFL, who are leaders that engage others to rise to the occasion. This leadership style was not easily explained in traditional instrumental exchanges. I believe that all managers could be classified by leadership style according to their propensity for transactions versus transformation of subordinates.
Other researchers believe TAL and TFL styles are complementary constructs and not polar. These researchers felt that the achievement of goals and objectives required an integration of the two styles. They also felt that TFL would be ineffective without the inclusion of transactional styles. They also observed that every transformational leader must have transactional attributes or be supported by a leader with these attributes. In this school of thought, they branded transactional leaders as those who operate within the company systems and culture, avoid risks, keep time constraints, and prefer processes to maintain control. This type of manager is effective in predictable and stable environments where straightforward activities are measured against prior performance to determine success. This type of leadership is based on an exchange between the leader and follower for performance-meeting expectations.
Transformational leaders look for new approaches to getting tasks done, they seek appropriate risks, and look to extend beyond the status quo. I believe that these types of leaders are not reactionary but work to create and shape their environment. I propose that transformational leaders use transactional strategies when required while using symbolism and vision to increase effort. To accomplish this, leaders use intellectual awareness, possible outcomes, expand the individual needs, and ask their followers to look beyond self-interest to the health of the organization. I view followers as people with free will and the ability to exercise free choice behaviors. I further clarify that transactional leaders structure tasks with the “right way” to get them done and dependence on the leader for problem solutions. Transformational leaders provide vision and strategy that empowers employees to solve problems. Unlike TAL, no instrument was available to test the validity, limitation, or application of this theory. I developed an instrument that would measure both TFL and TAL behaviors and investigate the relationship between these styles and the effectiveness of the work group. This instrument is the Wright Leadership Multi-Factor Leadership
Questionnaire (WLMLQ), and it has been conceptually developed and empirically validated to reveal the complementary aspects of TAL and TFL with subscales to differentiate between leader behaviors.
Breaking down this study into the full range leadership model, the sampled population is identified as follows: Starting on the active and effective end of the model, the study found the leaders in this population sample to score weakest to strongest in the following order: individual consideration (1.70), when the leader acts as a coach, is below the fifth percentile on the WLMLQ scale; idealized influence attributes (1.85), relies on charismatic leaders, is below the fifth percentile on the WLMLQ scale; inspirational motivation (2.17) scored below the 10th percentile on the WLMLQ scale. This style offers challenge and meaning to the follower’s tasks, and it inspires the leader to convey a vision, which; idealized influence behavior (2.43), emphasizes a collective sense of values and mission, and scored below the 20th percentile on the WLMLQ scale; intellectual stimulation (2.77) scored just below the 50th percentile on the WLMLQ scale. This style fosters new approaches to task accomplishment. This behavior produces a stream of new ideas that challenge the employees and motivate them to rethink the way of leading people. All these leadership styles are transformational. Based on these findings, this group of leaders would be identified as “less transformational than the norm.” Moving closer to the middle of the full range leadership model, the next set of leadership styles are classified as transactional. Still on the active and effective end of the model, the next leadership style is contingent reward (2.92), which is just below the 50th percentile on the WLMLQ scale. This style has an incentive for the employee to attain the required level of performance; the final leadership style assessed in this study was active management by exception (2.96). Located in the middle of the full range leadership model, it is classified as not active or inactive and not effective or ineffective. This group of leaders scored just below the 95th percentile on the WLMLQ scale. This is when a manager acts when there is evidence that the task is not going according to the plan. Based on this study, this group of leaders are identified as “more transactional than the norm.”
Summary
By comparing the leadership styles and job performances of leaders, the results suggest that leadership styles could be linked to how the leaders act in their job performances. If a business plan with the concept of leadership developing programs expanding to all levels of an organization could be implemented and kept contemporary with new technology, the staff could be enhanced for future leadership.
In this study, it was concluded that TMTs in Arizona’s copper mining companies led with a predominantly TAL style, specifically, management-by-exception (active). While the WLMLQ was not designed to encourage the labeling of a leader as transformational or transactional, it is appropriate to identify this group of leaders as “more transactional than the norm.” However, not all the operating unit teams could be classified in this manner. CMJ
Dr. Nathan Wright is the founder and president of Transformational Performance Solutions LLC. He has a proven record of transforming organizations into revenue-producing powerhouses.
Fire
and the mining frontier
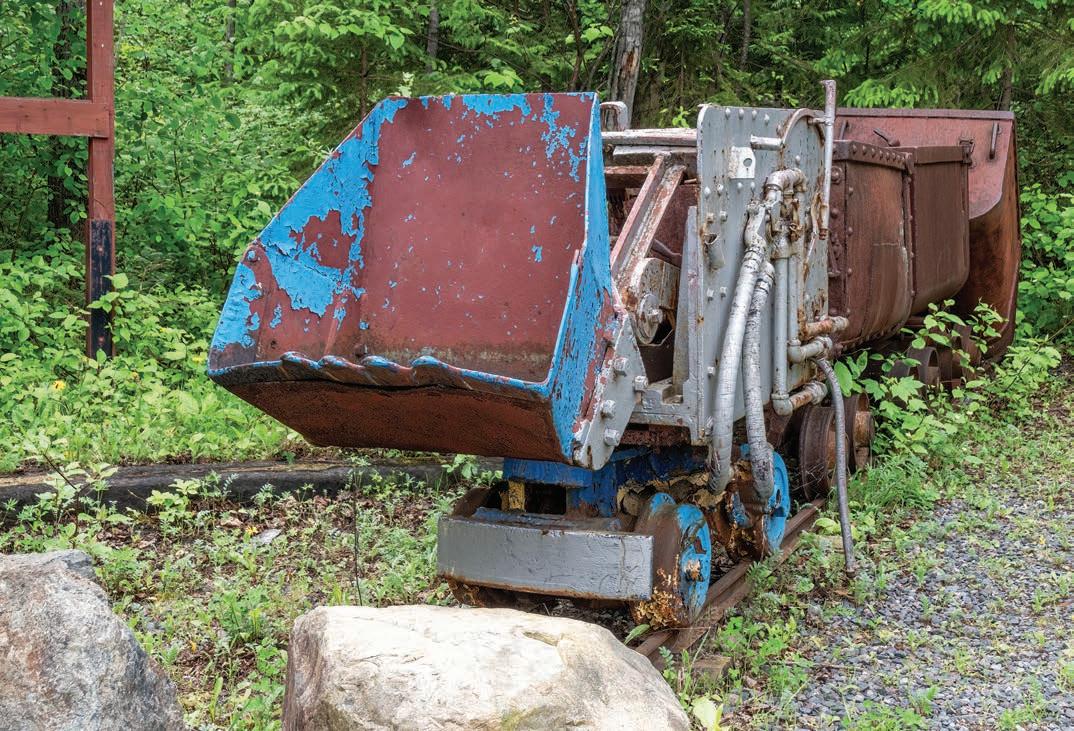
The massive expansion of Canada’s mining industry in the early twentieth century brought miners into close contact with one of the most fireprone ecosystems on the planet ― the great boreal forest. Although prospectors sometimes lit fires to clear land for exploration, the smell of smoke and the site of flames more often signaled a mortal threat to new mining communities in northern Canada. With their hastily constructed wooden buildings, rudimentary fire fighting capabilities, and lack of viable transportation infrastructure, mining communities had almost no defenses against fire. Some fires might start within a town or a mine (such as the July 1909 fire in Cobalt, Ont.), but large forest fires also spelled potential doom for anyone or anything in their pathway.
The Porcupine fire of 1911 stands out as a particularly destructive event amid the bustle and promise of a rich new mining region. The Porcupine gold rush began in 1909 after legendary figures in the history of Canadian mining ― Jack Wilson, Benny
Hollinger, Alec Gillies, Sandy McIntyre, and George Buttner ― discovered mineral deposits that became the foundation of Canada’s richest gold mining region. By 1911, there were a plethora of small communities and mining operations in the Porcupine, and the Timiskaming and Northern Ontario Railway completed a spur line to the region.
The summer of 1911 was a hot one, coming on the heels of a dry winter and spring that made the forests of northern Ontario more than ready to burn. Other changes to the local environment ― the creation of large slash piles because of logging for mining operations, fire suppression efforts in northern Ontario (which allows fuel loads to build up), and the discouragement of Indigenous burning ― may have exacerbated an already volatile situation. Fire was no stranger to the small mining camps and towns that made up the Porcupine (the town of Cochrane had burned the previous summer and the brand-new Hollinger surface plant burned in a forest fire in May
1911), but the wall of flame that ripped through the region in 1911 brought hardship and horror to residents.
On July 10, 1911, the temperature in the Porcupine regions was 41°C and several small fires were actively burning. The next day, increasing winds brought cooler air, but they also fanned the patchwork of fires, causing them to merge into a huge ribbon of flame over twenty miles in length and two miles wide in some sections. The heat from the growing fire also further whipped up the winds to tornado-like speeds of 110 to 160 km/h. Right in the path of the monster fire sat the fledgling town of South Porcupine, where residents mobilized every boat they could to evacuate further up Porcupine Lake to Golden City. Some remained behind to fight the fire or sought protection in the lake water. Many of these people, and many on the boats, drowned among huge waves that had developed on the lake.
At West Dome mine, the manager Bob Weiss organized crews to fight the fire
HISTORY OF MINING
with the company’s pumps and hoses, but they were quickly overwhelmed. Ten miners died battling the blaze, fifty survived by immersing themselves in the mine’s settling pond, while Weiss, his wife Jennie, his three-year old daughter Ariel, and seventeen other miners perished when they sought shelter in the mine workings, only to suffocate when the fire sucked out all the oxygen out from the underground. By the time it was all over, the fire had severely damaged or destroyed 10 mines, it had completely burned the communities of South Porcupine and Pottsville, and it had partially burned Golden city, Porquis Junction, and the town of Cochrane. While the official death toll was 73, local resident felt that many of the drowning victims or prospectors who died in remote bush areas went unaccounted for.
The fire became an international story, not only because of its destructiveness but because the Porcupine miners came from many different parts of the world. The
some for print,” but they printed them anyway, recounting how “one man was led through the town with both eyes burned out; another with his face and arms a mass of blisters. Harr Roche, a mining engineer, and A.S. Shields brought out a man who was so seriously burned his hand fell off when he was picked up.”
The Quebec Chronicle painted a similarly chilling scene of the fire’s aftermath: “The streets of South Porcupine were strewn with dead human beings, horses, dogs, and cattle, while along the mine roads charred corpses lie at intervals.”
The press also highlighted stories of heroism and foolhardiness in the face of the flames. Several newspapers recounted the actions of a Mrs. Gohr who, with baby in arms, refused to leave the lakeshore area while she waited in vain for her husband, who had returned to town to fetch valuables. Miraculously, Mrs. Gohr and her baby survived, but her husband was never seen again. Historian Stephen Pyne has recounted how a man, named Edward
family in South Porcupine. While attempting to flee, Meek’s family, having succumbed to the heat and smoke, simply lay down in the street and waited to die. Out of the din of the fire came Bell, who fought off the flames with water from nearby rain barrels, eventually saving the Meek family from certain death. Some incidents during the fire revealed the less savory aspects of human nature, such as several fights that broke out over access to boats (violence the Anaconda Standard blamed on “panicky foreigners,” likely a reflection of the ethnocentrism so prevalent during this period). As a counterpoint to these stories, the newspapers also highlighted the rapid fundraising and relief effort, with trains arriving in Cochrane just two days after the fire carrying material aid and crews to help with cleanup and the search for any survivors.
Mining towns and other communities in Canada’s northern forests remained vulnerable to the fatal effects until they had access to adequate means of escape by highway or airlift. In 1916, a large fire engulfed Cochrane and Matheson, taking the lives of 224 people. Six years later, a large fire levelled North Cobalt, Charlton, Haileybury, and other small northern Ontario communities. Haileybury was thriving town, home to many managers and owners of mines in the Cobalt and Porcupine area. The fire left 43 dead and 3,500 people homeless. The relief effort featured a donation of 80 streetcars from the City of Toronto, which were outfitted with stoves and rudimentary insulation, so people had some form of housing to get them through the winter.
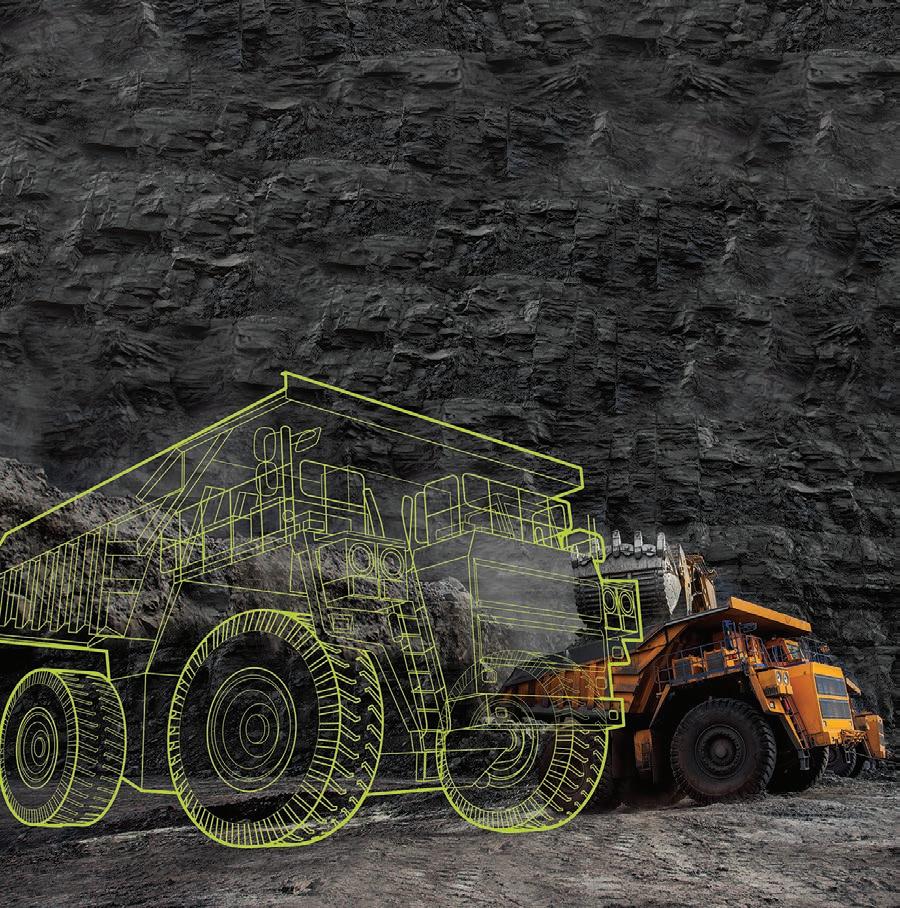
Better systems of fire control and evacuation have prevented the mass mortality events of the past (though not the property destruction), but wildfires still cause major problems for the industry, including costly shutdowns, damage to equipment, and displacement of workers. At the same time, today’s encounters with wildfire can hardly compare to those earlier mine workers, prospectors, and managers who were injured or killed by fires from which they could not so easily turn away. CMJ
John Sandlos is a professor in the History Department at Memorial University of Newfoundland and the co-author (with Arn Keeling) of “Mining Country: A History of Canada’s Mines and Miners,” published by James Lorimer and Co. in 2021.
ON THE MOVE
Executive, Management and Board Changes in Canada’s Mining Sector
TOP MOVES IN THIS ISSUE
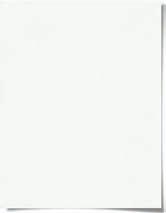
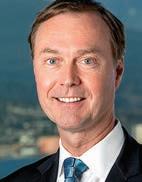
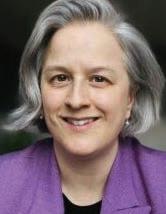
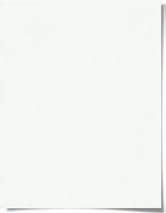
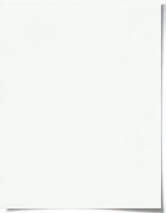
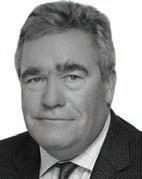
Don Lindsay
Don Lindsay is now on the board of BHP
The former CEO of Teck Resources is a graduate of Queen’s University and Harvard Business School. He has won numerous awards, including the Nature Trust of B.C. Conservation Champion Award, the CIM Distinguished Service Medal, and the Mining Association of B.C.’s Mining Person of the Year. He is also the recipient honorary doctorates from the University of Windsor and the B.C. Institute of Technology.
Sara Goodman is the new president and CEO of the B.C. Centre for Innovation and Clean Energy. She has an extensive background in advancing Canada’s climate change policies, plus over a decade of executive experience in the resource sector.
She joins CICE from the Boston Consulting Group, where she was a partner working with companies and governments around the world, and she previously served as the Prime Minister’s senior advisor on climate action and sustainable economy.
Ewan Mason is the new president and CEO of Star Diamond. He has extensive experience in corporate financing, restructuring and advisory work. He has worked as a contract geologist for a number of mining companies. Following receipt of his MBA, he was employed by Richardson Greenshields and then TD Securities to start up and head the re-launch of a mining investment banking team. Mason’s TD clients included Iamgold, Hudbay, Northgate, Equinox, BHP, Xstrata, Vale, and Eurozinc.

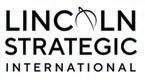
MANAGEMENT MOVES
» Andean Precious Metals added Marcos Holanda as its new COO.
» Industry veteran George J.Schuller, Jr. joined Arch Resources as SVP and COO.
» Armac Resources named Paul Johnston VP exploration, following the resignation of Roy Greig
» Atlas Lithium welcomed Brian Talbot as COO and a board member.
» The B.C. Centre for Innovation and Clean Energy appointed Sarah Goodman as president and CEO.
» Calibre Mining appointed Jason Cyr VP operations and Andre Morneau process manager for the Valentine gold mine.
» Canter Resources named Ainesh Mohan its CFO and Jan Urata as corporate secretary.
» Evolution Mining named Nancy Guay its chief technical officer.
» Founders Metals named Natalie Senger VP of resource development.
» The new CFO at Goldmoney is Sean Ty
» LiTHOS Group promoted Joe Fuqua to COO and corporate secretary. Michael Westlake became president, and Gabe Segal is VP strategy and finance.
» The new EVP of exploration at Montage Gold is Silvia Bottero
» Montage Gold named Constant Tia its new CFO.
» Perpetua Resources appointed John Cherry to succeed Laurel Sayer as president and CEO.
» Premier American Uranium named Colin Healey as CEO.
» Star Diamond named Ewan Mason as president and CEO.
» StrategX Elements named Ryan McEachern interim CFO upon the departure of Andrea Yuan
BOARD ANNOUNCEMENTS
» Adventus Mining named Maryse Belanger non-executive board member and chair.
» Aranjin Resources added David Wheeler to its board upon the resignation of Peter Trow.
» Argentum Silver announced the resignation of Albert Contardi from the board.
» Canadian Metals added Quentin Yarie to its board.
» Champion Iron appointed Ronnie Beevor to its board.
» Collective Mining announced the retirement of Ken Thomas from the board.
» Copper Fox appointed Manuel Gomez to the board.
» CopperEx Resources named Tom Yip to the board.
» Diamcor Mining named D. Wayne Howard, retired Tiffany & Co. executive, to its board.
» Euromax Resources said Nicolas Treand has resigned as executive director.
» Flying Nickel Mining said Jim Rondeau has stepped down from the board.
» Peter Coates will step down from the board of Glencore,to be replaced by John Wallington on June 1.
» Highrock Resources named James Pirie and Michael Power directors.
» International – Great Eagle Gold celebrated the
appointment of Patricia Kovacevic to the board of the International Green Gold Council.
» Pierre Clement became a director of Kobrea Exploitation
» A seat of the board of New Gold has been given to Richard O’Brien
» Chris Jennings retired from the board of North Arrow Minerals
» Orex Minerals named Adam Cegielski as chair.
» Prospector Metals offered Ian Parkinson a seat on its board.
» Quest Critical Metals (formerly Canadian Palladium Resources) has added Brian Kirwin and Percy Clark to its board.
» The newest director at Rare Earth Ridge is Sharyn Alexander
» Rover Critical Minerals named Gunnar Pedersen to the board.
» Sherritt International said Louise Blais and Steven H. Goldman joined the board.
» Silverstock Metals said Colin Little resigned his seat on the board.
» StrategX Elements named David Haig to the board.
» Tectonic Metals added John Armstrong to its board.
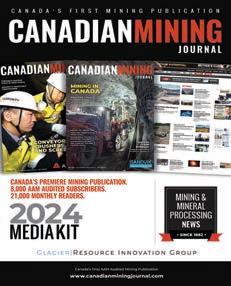
Contact Robert Seagraves at rseagraves@canadianminingjournal.com or George Agelopoulos at gagelopoulos@northernminer.com or call 1-416-510-6891 to request your copy.
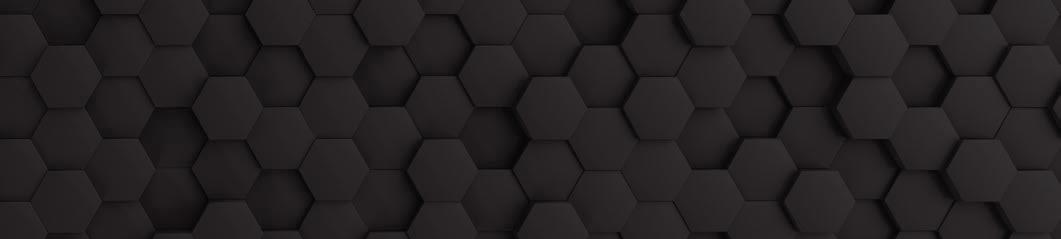


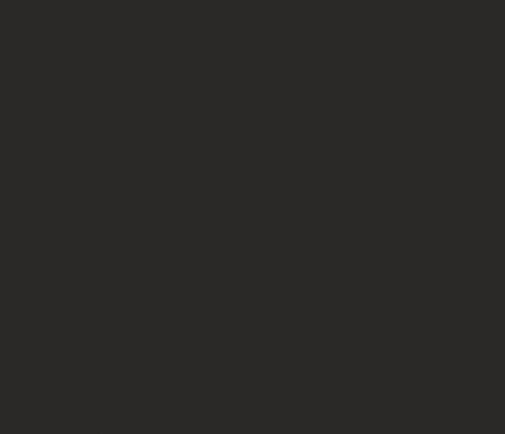
2.0
AI Powered Search
TNM Marco Polo’s integrated chatbot lets you quickly and easily search more than 2,600 global mining companies and 13,900+ properties by just asking a question.
5,000+ Site-level Contacts
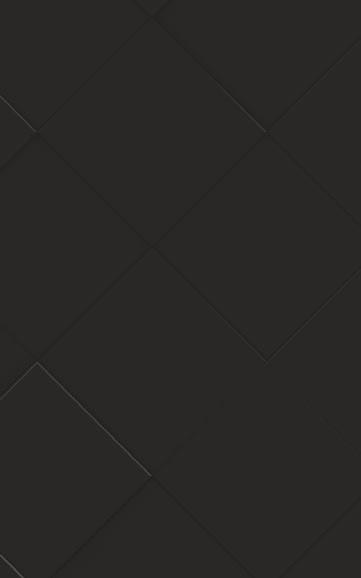
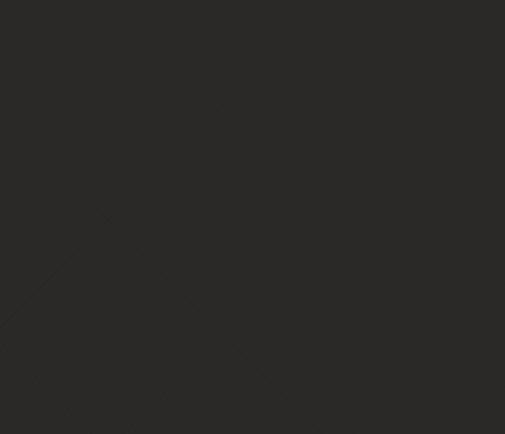
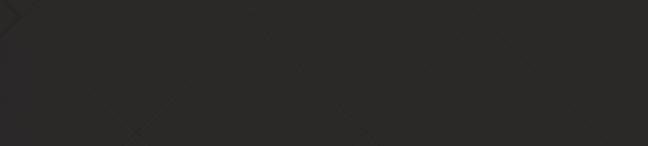

Search more than 13,900 global mining properties for the right contact and connect with them directly through a single click. Learn more at marcopolo.tnm.global
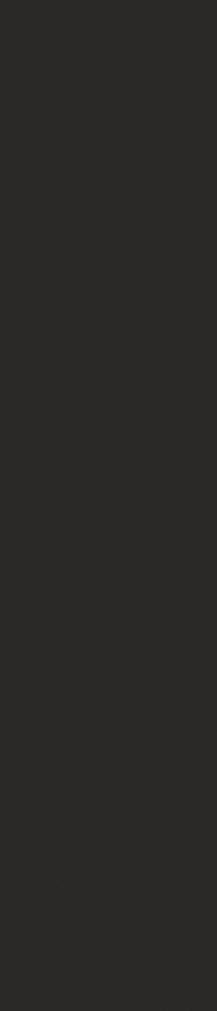

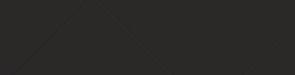




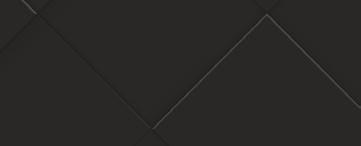
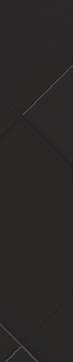
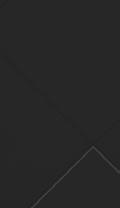

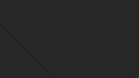
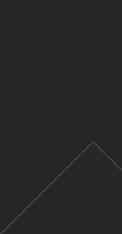
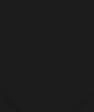
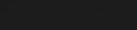
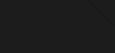
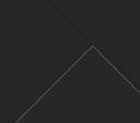
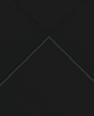

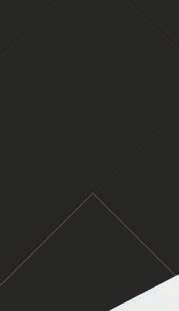
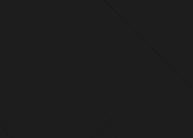

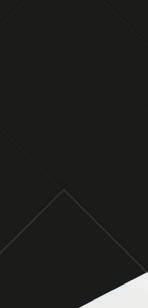
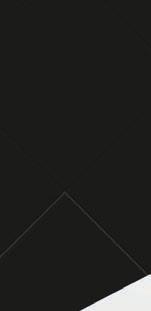
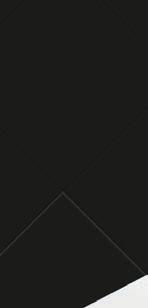

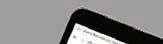
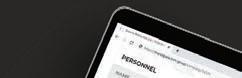


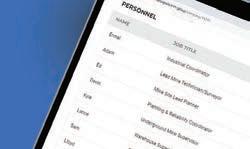
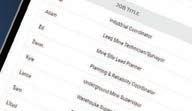
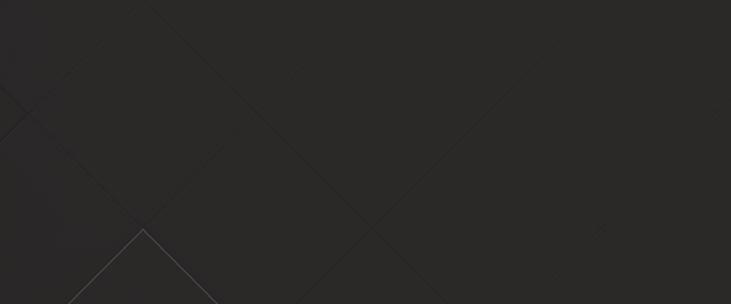
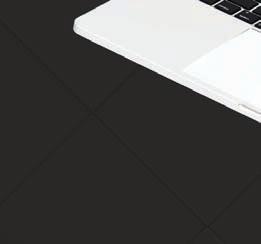

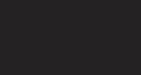
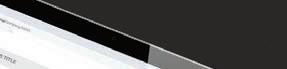
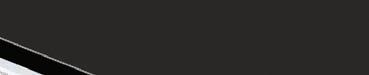
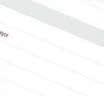
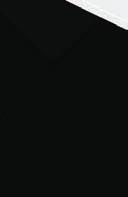
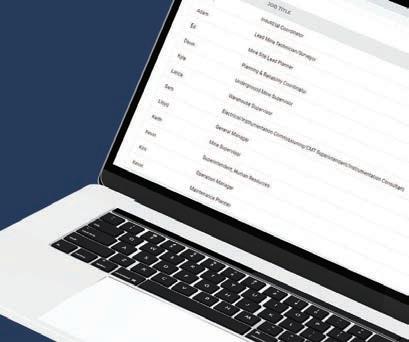


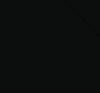

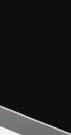
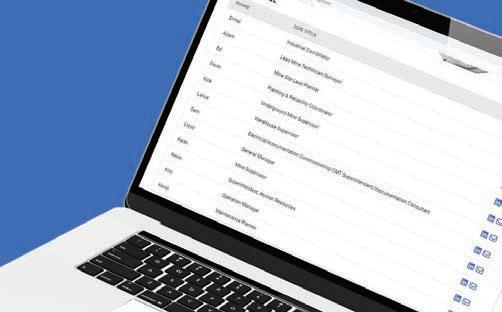

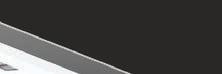
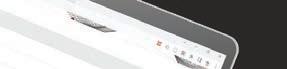
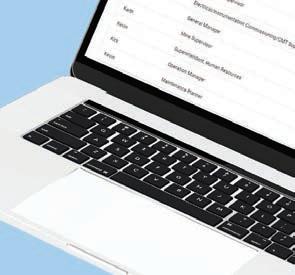
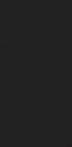
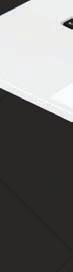
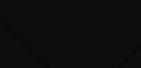

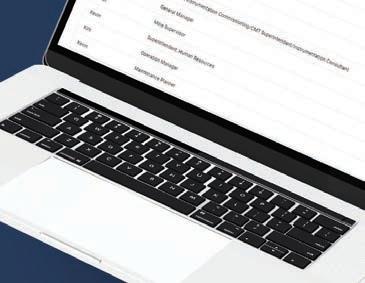

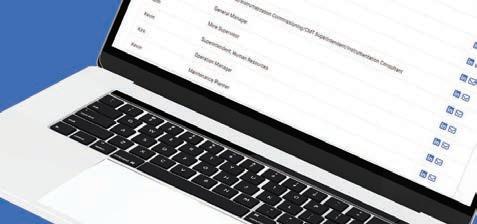
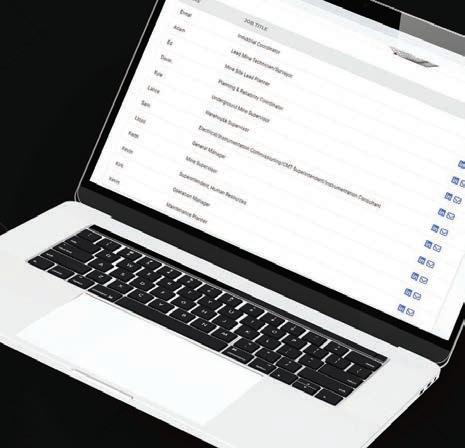
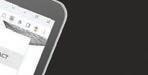
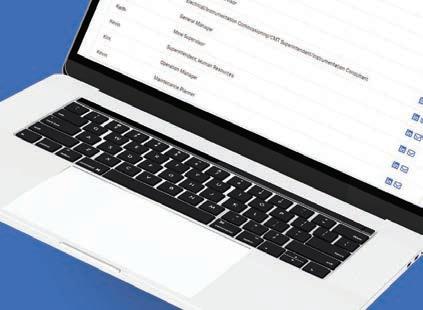

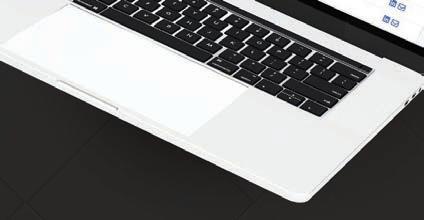
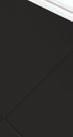

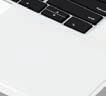
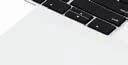


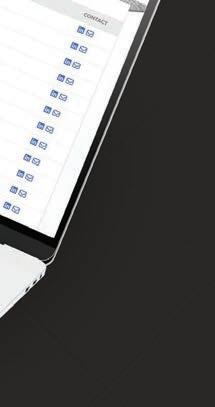




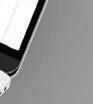
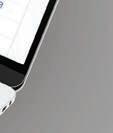
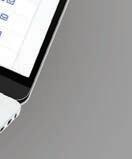


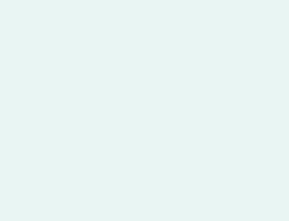

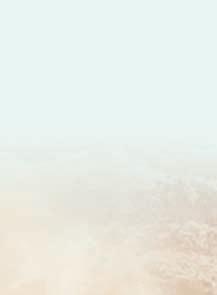
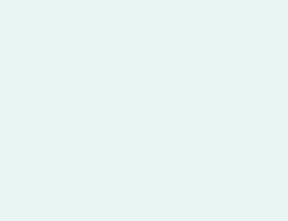
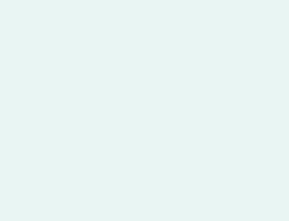
CONDITIONS?
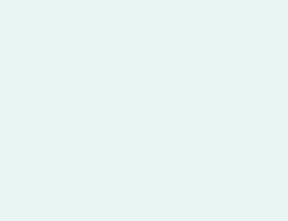
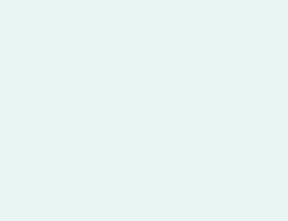
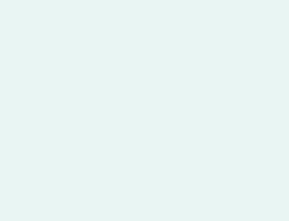


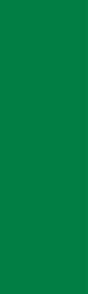

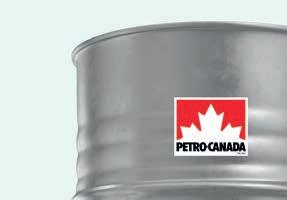




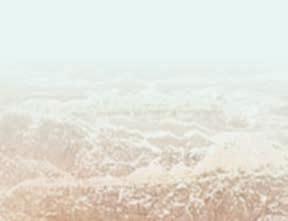
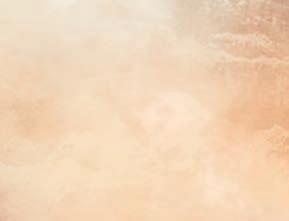
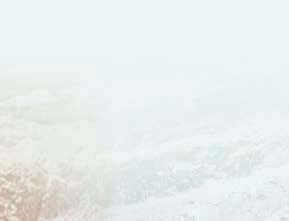

Premium multi-purpose synthetic all weather transmission, drive train, hydraulic and wet brake fluid for heavy-duty mobile equipment.


GAME CHANGING ASSET PROTECTION
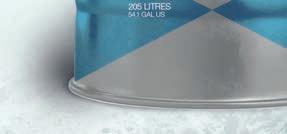

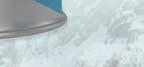
VISIT US AT CIM, BOOTH #504. VANCOUVER, MAY 12-15, 2024


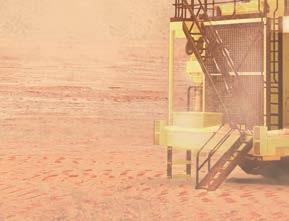
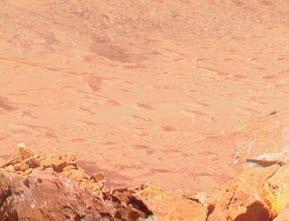
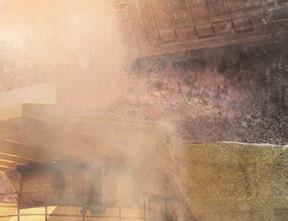
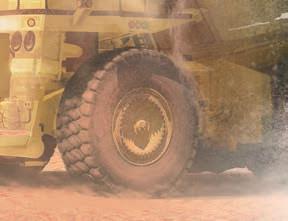
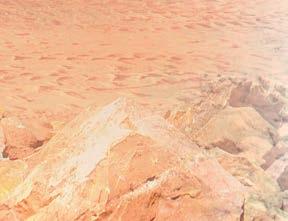
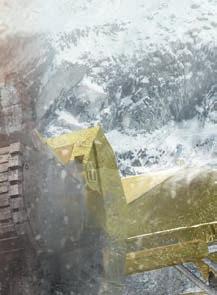
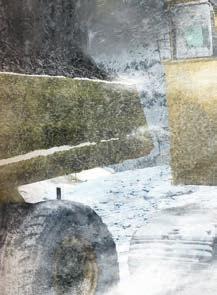
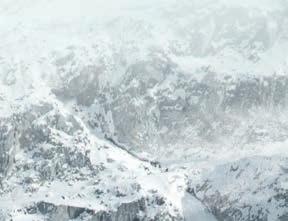
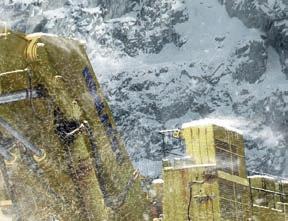
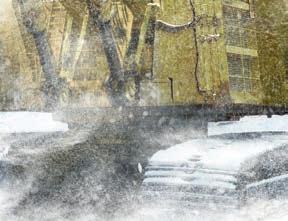
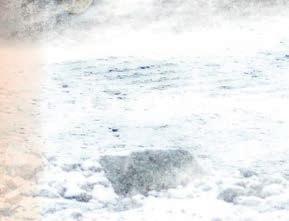
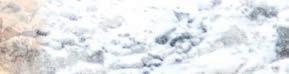
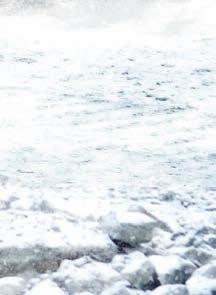
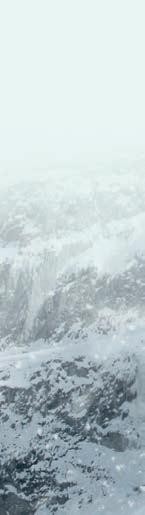
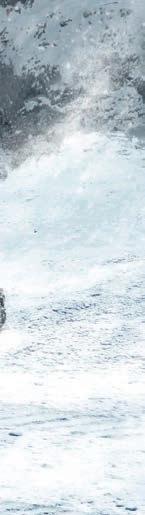
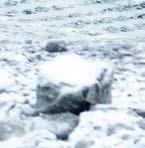