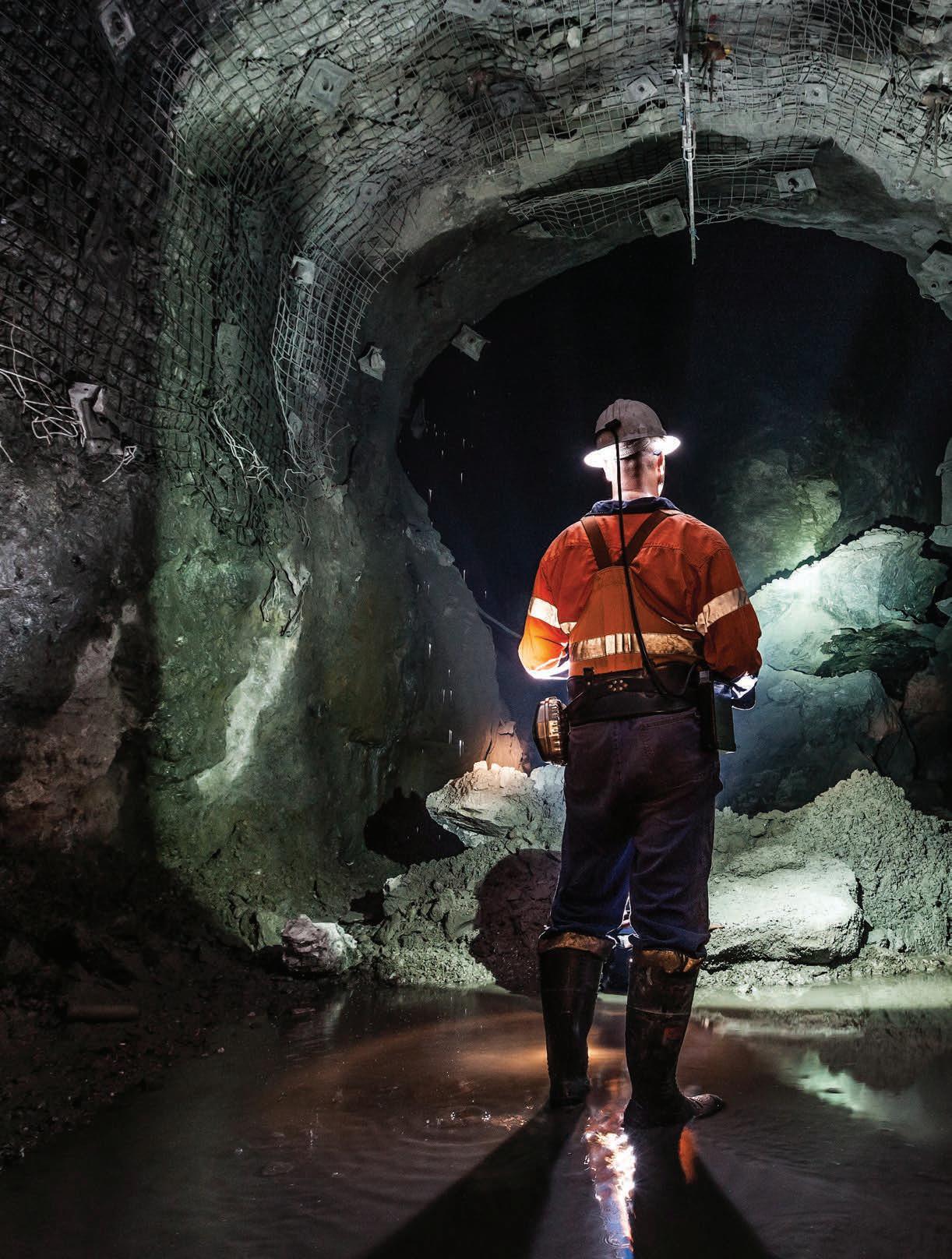
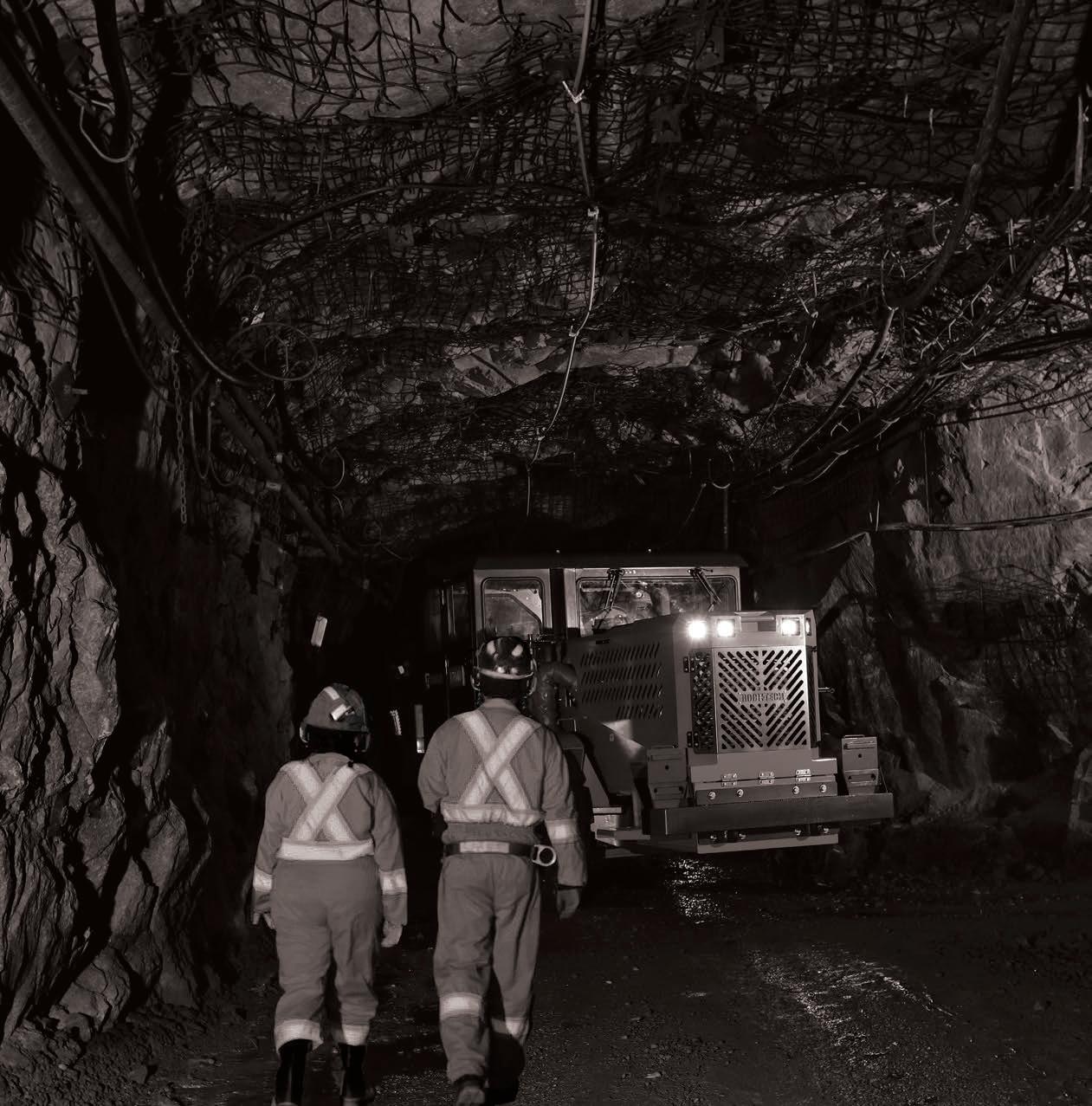
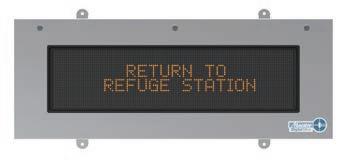

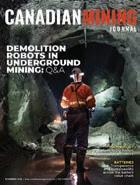
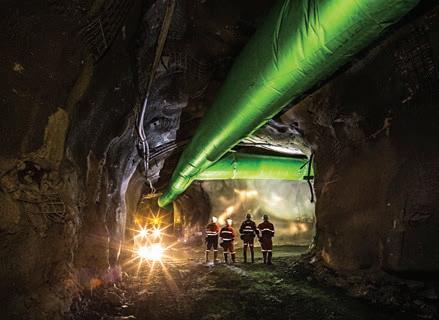
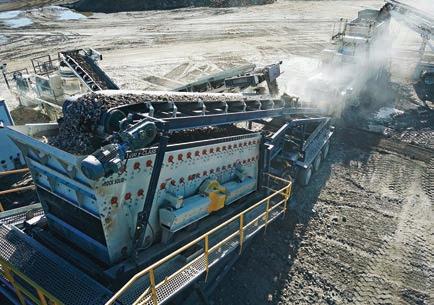
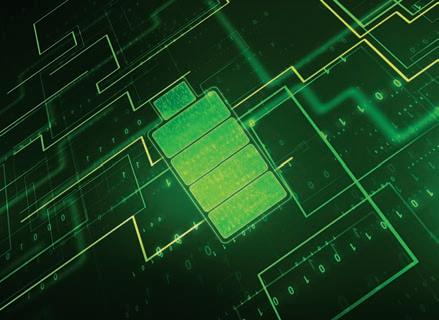
According to a recent draft discussion paper on Canada’s Critical Minerals Strategy, the strategy will address five core objectives: support economic growth and competitiveness, promote climate action and environmental pro tection, enhance global security and partnerships with allies, advance Indigenous reconciliation, and foster diverse and inclusive workforces and communities.
The value chain for critical minerals includes five segments: exploration, min ing, processing, manufacturing and advanced manufacturing, and recycling, and there is an opportunity for investors in every stage of that value chain. Therefore, the Canadian government has committed $4 billion in Budget 2022 to address the entire critical minerals value chain.
“Simply put, there is no energy transition without critical minerals, and this is why critical mineral supply chain resilience is an increasing priority for advanced economies,” Jonathan Wilkinson, Minister of Natural Resources.
Additionally, Deputy Prime Minister Chrystia Freeland signaled in a speech this week in Washington, D.C. that the federal government is prepared to address reg ulatory hurdles to economic development in Canada’s natural resource sector.
In this issue’s ESG column, Carolyn Burns reflects on critical minerals strategy, and how we can accelerate project development and advance reconciliation. Benedikt Sobotka argues on pages 42-43 that with battery demand set to explode over the coming decade, businesses, governments, and NGOs must renew their efforts to ensure the value chain is scaled up in a responsible, circular, and sustain able manner.
Also in this issue, we continue examining recent technologies that could maxi mize the production of critical minerals such as lithium on pages 32-35.
This issue also features several articles on underground construction, ventila tion, and communication, with a notable contribution from Cambrian College’s Centre for Smart Mining on pages 30-31, along with lawyers’ advice on invest ments in mining in case you are having trouble with international investments in foreign countries.
Our virtual symposium: “Reimagine Mining,” on Oct. 12, was an immense suc cess with almost 1,200 delegates registered. In case you missed it, we will have detailed coverage of the water management sessions in our January 2023 issue, including the answers to almost 40 questions that Dr. Chris Kennedy, Teck Resources’ water director, was asked by the audience.
On a personal note, I enjoyed my first visit to an underground mine during the “Mining Transformed 2022,” the world’s first technology exhibition in an under ground operating mine at the end of September. The NORCAT Underground Centre is a state-of-the-art operating mine. Mining Transformed 2022 provided a unique opportunity for more than 40 exhibitors and the visitors to connect underground amongst live demonstrations of emerging technologies that are poised to trans form the global mining industry. Kudos to Don Duval, CEO of NORCAT, and his team for organizing such a successful event. CMJ
NOVEMBER 2022 Vol. 143 – No . 9
225 Duncan Mill Rd. Suite 320, Toronto, Ontario M3B 3K9
Tel. (416) 510-6789 Fax (416) 510-5138 www.canadianminingjournal.com
Dr. Tamer Elbokl
TElbokl@CanadianMiningJournal.com
Marilyn Scales
mscales@canadianminingjournal.com editor@canadianaminingjournal.com
Jessica Jubb
jjubb@glacierbizinfo.com
David Brown (Golder Associates)
Michael Fox (Indigenous Community Engagement)
Scott Hayne (Redpath Canada)
Gary Poxleitner (SRK)
Allison Mein
403-209-3515 amein@glacierrig.com
Publisher & Sales Robert Seagraves 416-510-6891 rseagraves@canadianminingjournal.com
Sales, Western Canada
George Agelopoulos 416-510-5104 gagelopoulos@northernminer.com
Toll Free Canada & U.S.A.: 1-888-502-3456 ext 2 or 43734
Circulation Toll Free Canada & U.S.A.: 1-888-502-3456 ext 3
President, The Northern Miner Group Anthony Vaccaro
Established 1882
Canadian Mining Journal provides articles and information of practical use to those who work in the technical, administrative and supervisory aspects of exploration, mining and processing in the Canadian mineral exploration and mining industry. Canadian Mining Journal (ISSN 0008-4492) is published 10 times a year by Glacier Resource Innovation Group (GRIG). GRIG is located at 225 Duncan Mill Rd., Ste. 320, Toronto, ON, M3B 3K9 Phone (416) 510-6891.
Legal deposit: National Library, Ottawa. Printed in Canada. All rights reserved. The contents of this magazine are protected by copyright and may be used only for your personal non-commercial purposes. All other rights are reserved and commercial use is prohibited. To make use of any of this material you must first obtain the permission of the owner of the copyright. For further information please contact Robert Seagraves at 416-510-6891.
Subscriptions – Canada: $51.95 per year; $81.50 for two years.
USA: US$64.95 per year. Foreign: US$77.95 per year. Single copies: Canada $10; USA and foreign: US$10. Canadian subscribers must add HST and Provincial tax where necessary.
HST registration # 809744071RT001.
From time to time we make our subscription list available to select companies and organizations whose product or service may interest you. If you do not wish your contact information to be made available, please contact us via one of the following methods: Phone: 1-888-502-3456 ext 3; E-mail: amein@glacierrig.com
Mail to: Allison Mein, 225 Duncan Mill Rd., Ste 320, Toronto, ON M3B 3K9
We acknowledge the financial support of the Government of Canada.
Within underground mines, the primary horizontal trans portation openings are provided by drifts. A significant portion of overall development costs often account for their construction, and production costs may be noticeably affected by these excavations. To offer insight into the expense of excavating drifts and ramps, Costmine has designed an array of typical configurations and estimated the associated costs. These costs were estimated with the help of a software appli cation from Costmine’s suite of engineering-based mining cost estimating applications, Sherpa Underground. The following table summarizes the results of these estimates in U.S. dollars (2021) per metre of advance:
The assumed rock characteristics upon which the cost estimates are based.
Drift excavation Compressive Rock quality scenario strength (kpa)
Unsupported 190,000
Rock bolts 155,000
Shotcrete 130,000
In our designed configurations, blast holes for openings with face areas of less than 9.28 m2 are provided by airleg drills. Jumbos equipped with drifters drill the blastholes for the larger faces. In both the ramps and the untracked drifts, development muck is collected and transported using scoop trams. In tracked drifts, muck is collected and loaded into rail cars by overshot muckers. Diesel locomotives transport the cars away from the active face to the dump point. The costs of operating the neces sary ancillary machinery (such air compressors, auxiliary fans, and pumps) are also included in the estimates.
In our designs, high strength emulsion-based explosives are used for all blasting. Powder factors are tied to the face area of the opening and to the quality of the rock and vary from a low of 0.53 kg/t to a high of 1.67 kg/t. Under appropriate conditions, less expensive blasting agents (such as Anfo) can be used, which in most cases would result in a reduction in the costs of the blasting supplies. However, the use of bulk explosives is often accompanied by an increase in the required powder fac tor. Blasts are initiated with non-electric millisecond delay caps. Where rockbolts are used for support, our designs assume that
the bolts are placed 1.2 metres on center and one steel mat is used for every three bolts.
Rock bolts (1.2 to 2.4 metre long) $11.10 to $17.00/bolt Rock bolt mats $23.5 to $32.50/mat Shotcrete $512.72/cubic metre
Finally, the drift development cost estimates are summarized below in units of U.S. dollars per metre of advance.
Face dimensions (width x height in metres)
Unsupported Rock bolts Shotcrete
1.8 x 2.4 1,404 1,273 1,219 2.4 x 2.7 1,420 1,290 1,255 3.7 x 3.0 1,523 1,265 1,349
x 3.7 1,883 1,684 1,645
x 4.6 2,878 2,517 2,385
Costs are not included for items such as move-in and set-up, yard preparation, support equipment installation, camp facili ties, design and engineering, or contractor profit.
For all the drift excavation scenarios investigated, expenditures for labour far exceed those for any other cost category. Labour’s contribution fell within the range of 50% to 60% of the overall cost estimates, with supplies accounting for about 15% to 20% depending upon the drift excavation scenario.
The estimated development costs may strike some readers for lower-than-expected distribution of costs between support methods. This may be the result of decrease in quality rock characteristics that would require stronger rock support meth ods, which was accounted for in the reported estimates. As the quality of the rock decreases, the consumption rates for drilling and blasting supplies fall. The associated reduction in costs is offset, to a degree, by an increase in rock support costs. This bal ance is the primary influence on the cost distribution among the excavation scenarios described above. CMJ
Sam Blakely is asenior mining engineer with Costmine, a Division of The Northern Miner Group.
RIO TINTO is investing up to $515 million over the next eight years to decarbonize its Fer et Titane (RTFT) operations in Sorel-Tracy, Que. and to help diversify its critical minerals portfolio, while the federal government will contribute up to $222 million to the initiatives.
The partnership, worth up to $737 million will support innovations to reduce by up to 70% the greenhouse gas emis sions from RTFT’s titanium dioxide, steel and metal powders business.
The partnership will also support Rio Tinto’s BlueSmelting project, an ilmenite smelting technology for making highgrade titanium dioxide feedstock, steel and metal powders that could cut 95% of greenhouse gas emissions compared to RTFT’s current reduction processes.
A demonstration plant is under construction at RTFT to test the BlueSmelting technology and it is expected to be completed in the first half of 2023. Once operational, Rio Tinto said it could potentially reduce up to 70% of RTFT’s overall greenhouse gas emissions, or the equivalent of 670,000 tonnes of CO2.
Also enabled by the partnership will be an increase in the
production of the critical mineral scandium, of which Rio Tinto said it became the first North American producer in April this year at its Element North 21 demonstration plant.
The company plans to quadruple production capacity to reach up to 12 tonnes of scandium oxide per year, up from current capacity of 3.0 tonnes, by adding new modules to the existing plant that extracts high purity scandium oxide from the waste streams of titanium dioxide production.
The $30-35 million project is slated to begin producing scan dium oxide in 2024.
In addition, Rio Tinto will add titanium to its output portfo lio by joining with other titanium industry producers to advance a new process for extracting and refining titanium.
Rio Tinto will build a pilot plant at the RTFT metallurgical complex to validate the process which it said requires no harmful chemicals and doesn’t generate direct greenhouse gas emissions. The plant is expected to be completed by the end of 2023. CMJ
EMERGING AUSTRALIAN lithium miner Sayona Mining is closer to the re start of production at its North Ameri can Lithium (NAL) project in La Corne, Que., as it awarded a four-year, $200-mil lion contract to Quebec company L. Fournier et Fils for mining operations.
This is one of the largest such contracts ever signed in Quebec, and it is expected to create 120 new jobs to be
filled from the region of AbitibiTemiscamingue, Que., including the Pikogan and Lac Simon First Nations communities.
Fournier will be responsible for the supervision of all stripping and drilling, blasting, loading, and transportation of ore and waste rock. The contractor will also maintain the site roads and all other services. Drilling and blasting will
be conducted by another Quebec com pany, Dynamitage Castonguay.
Work is to begin this month with a fleet that includes 10 trucks of 100tonne capacity and two excavators.
First lithium production from NAL is to begin in the first quarter of 2023. The project will produce an estimated 115,000 tonnes of 6% lithium oxide in a spodu mene concentrate annually for 27 years.
AZIMUT EXPLORATION has won the Discovery of the Year award from the Mineral Exploration Association of Quebec (AEMQ) for the discovery of the Patwon gold zone on the com pany’s 100%-owned Elmer property.
The award is granted to highlight the importance of a new discovery that has a ripple effect on exploration activities both on the property and in the surrounding area. The Azimut team is understandably very honoured by this recognition.
Discovered in 2020, the Patwon zone has been delineated by 115 holes (48,381 metres). The zone is continuous from sur face to at least 800 metres, and it remains open at depth – and probably along strike, says Azimut. The strike length extends nearly 600 metres with an estimated true width of 35 metres. Drilling continues to expand and optimize a potential open pit.
Azimut’s wholly owned Elmer property is a gold-silver-cop per-zinc project located in the Eeyou-Istchee James Bay region of Quebec, about 5 km west of the James Bay Road and 100 km
from Newmont’s Eleonore gold mine. The property is also 60 km from the Cree community of Eastmain. CMJ
TECK RESOURCES is teaming up with SAAM Towage to deploy electric-pow ered tugboats at Neptune Terminal in Vancouver. These will be the first electric tugs operating in Canada, and their deployment supports Teck’s climate goals.
SAAM will supply two ElectRA 2300 SX tugs that will begin operation in the sec ond half of 2023. Their use will eliminate over 2,400 tonnes of greenhouse gas emissions each year. The electric tugs are much quieter than diesel-powered boats, a benefit for marine life in the harbour.
The ElectRA tugboats are designed by Vancouver-based Robert Allan Ltd. And will be built at Sanmar Shipyards in Tür kiye (Turkey).
Teck previously announced an agree ment with Oldendorff Carriers to employ energy efficient bulk carriers for ship ments of Teck steelmaking coal from the Port of Vancouver, reducing 45,000 tonnes of carbon dioxide per year, equiv
alent to removing nearly 10,000 passen ger vehicles from the road. Teck has also announced a pilot of a fully electric on-highway transport truck to haul cop
The deployment of electric tugs will remove 2,400 tonnes of GHG from the air each year and reduce noise.
per concentrate between the Highland Valley copper operations in south-central B.C. and a rail loading facility in Ashcroft, B.C. CMJ
Miners love to talk about “the markets,” but increasingly at industry conferences it is the carbon markets, and not just the stock markets, that has everyone’s attention. Pres sure is mounting on mining industry participants to make their operations “carbon neutral” or “net-zero.” But what does this mean, and what are the strategic and legal considerations that companies should be evaluating?
In response to the 2015 United Nations Paris Agreement, which formalized targets for lowering greenhouse gas (GHG) emis sions, countries and businesses alike have increased their pub lic commitments to reduce global emissions, with many coun tries announcing aggressive GHG emission reduction goals and pledging to be carbon-neutral or net-zero by 2050.
In Canada, building off regimes put in place by early adopt ing provinces like Alberta, the federal government has finalized the Canadian Greenhouse Gas Offset Credit System Regulations facilitating a national compliance carbon market. In the United Kingdom, the government has launched a comprehensive review of net-zero delivery by 2050 to ensure legally binding climate goals are pro-growth and pro-business, and that invest ment continues to boost economic growth. Similarly, securities regulators in Canada and the United States are actively examin ing expansive new disclosure regimes that will require detailed climate change related disclosures.
Carbon credits act as a complementary tool that can be used alongside broader decarbonization efforts. For example, car bon credits can compensate for unabated GHG emissions while a company pursues an emissions mitigation strategy in order to reach a balance between GHG emissions and removals (netzero).
The terms “carbon credit,” “carbon offset” or “carbon allow ance” are often used interchangeably but can mean different things depending on the particular carbon market in which they are deployed. Generally though, they refer to a transfer able instrument that represents one tonne of carbon dioxide (tCO2) or the carbon dioxide equivalent (tCO2e) of another GHG. Carbon credits are derived from activities that either avoid or reduce the release of GHGs into the atmosphere (such as the creation of biodiversity reserves), or that remove and use and/ or sequester GHGs from the atmosphere (such as carbon cap ture use and storage (CCUS) projects).
Carbon credits trade within carbon markets, of which there are generally two types: compliance and voluntary.
Compliance markets are created where governments pre scribe GHG emission reduction requirements within their juris dictions. Regulated entities within compliance markets either create or acquire compliance carbon credits as a means of com plying with legislatively prescribed GHG emissions reduction requirements.
Voluntary markets function outside of the compliance mar kets and allow participants to acquire carbon credits that may not satisfy the requirements of legislatively prescribed compli ance markets, but which demonstrate a participant’s efforts to satisfy GHG reduction required by an array of stakeholders. This includes customers, shareholders, and financing entities.
There are significant opportunities presented by the growth in the carbon markets where mining companies can take proactive steps and demonstrate leadership. These actions could include:
> creating market differentiation through voluntary enhanced corporate disclosure (for example, including discussion of Scope 1, 2 and 3 emissions) and preparation of focused sustain ability reports outlining corporate climate change vision;
> engaging consultants to determine the “carbon footprint” of business and associated activities;
> evaluating the purchase of voluntary carbon credits as a means of publicly positioning the company as “carbon neutral;”
> evaluating the possibility for adoption of “green” power sources, technology and equipment as part of exploration, development and mining planning and operations for both existing and future projects (and including detailed analysis as part of any NI 43-101 technical reports);
> setting sustainability targets or requirements for project partners and third-party service providers or suppliers; or
> evaluating the potential feasibility of any carbon credit gen erating projects on existing mineral lands or properties as an additional revenue source.
Investors are increasingly focusing investment decision-mak ing on a company’s carbon neutral or net-zero commitments. Unsurprisingly, the world’s largest mining companies already devote extensive disclosure to their voluntary climate change commitments, and even exploration and junior mining compa nies are now seeking to differentiate themselves from their peers through public commitment to net-zero.
CMJ
STEVAN D. BENNETT and THOMAS W. MCINERNEY are partners and co-heads of Climate Change, Power and Renewable Energy Practices at Bennett Jones LLP.
If we are going to transition to a low-carbon economy, we need to increase the production and use of critical minerals (e.g., cobalt, graphite, lithium, nickel, copper, and rare earth elements) by an alarming rate. Earlier this year, the Govern ment of Canada launched Canada’s Critical Minerals Strategy.
The objective of the strategy is to “… boost the supply of criti cal minerals to grow domestic and global value chains for the green and digital economy … and position Canada as a global leader in the responsible, inclusive, and sustainable produc tion of critical minerals and secure value chains from mines to manufacturing.” (Critical Minerals Center of Excellence, 2022) You can find the strategy on the Critical Minerals Center of Excellence website.
Two main pillars of the strategy are accelerating project development (i.e., streamlining and speeding up the permitting process) and advancing Indigenous reconciliation. On the sur face, these two objectives may seem to be at odds. But that does not have to be the case. Land use planning and Indigenous-led processes for consultation and consent can be the foundation of an accelerated permitting process that does not compromise reconciliation, and Indigenous rights.
As part of the government’s strategy implementation plan, there was a public consultation period this summer. Below are the excerpts from our submission to the Government of Canada that present some ways we can accelerate project development as well as advance reconciliation. To streamline permitting while advancing reconciliation and recognizing Indigenous rights, we can (i) incentivize and support Indigenous land use planning and (ii) support Indigenous-led consultation and con sent processes and decisions related to mineral development.
Land use planning can help Indigenous governments as well as regional and federal stake holders accelerate the responsible development and identification of preferred zones for critical minerals, cultural and social use, remining of waste, resto ration, and nature-based climate solutions. There are several useful benefits of effective local land use plans:
> They offer useful information to provincial and federal agen cies in their planning and permitting processes.
> They are an invaluable tool for private sector proponents –supporting early rightsholder and stakeholder engagement, consultation, and mineral development planning.
> They are more likely to consider cumulative impacts and could be a driver for community-led impact assessments on a regional scale.
Indigenous leadership in land use planning is essential to
uphold rights, Indigenous methods for land use, and reconcili ation. Local land use planning could take place within the con text of broader land use mapping efforts, and there are some excellent examples of community-led mapping that includes historical cultural and environmental information.
But to achieve this, there needs to be funding and resources available to Indigenous governments, municipal governments (or municipal coalitions), NGOs, land, and water organizations for voluntary land and natural resource use planning. This can take the form of grants, training workshops, and sharing skills and lessons learned with communities who have used land use planning to inform natural resource development. Land use plans must also be recognized in the decisions related to critical minerals, and where there are Indigenous rights to land use deci sions they must be protected. This means that local priorities for biodiversity, social, and cultural use and other economic oppor tunities may supersede critical mineral development.
Consultation and consent processes should be designed and led by Indigenous communities and governments. The process and outcome are more likely to be supported by the community, address community needs, and build off land use history, com munity mapping, nature-based assets, and critical minerals.
Support for Indigenous led consultation and consent pro cesses could be used to
> create opportunities to discuss and define expectations related to community protocols with a focus on critical minerals;
> develop Indigenous/community protocols that are aligned with regional, provincial, and federal permitting systems;
> increase training opportunities for government-band level land use managers, and funding opportunities to build the depth of Indigenous land use departments with a specific focus on research and data related to critical minerals and naturebased assets;
> create opportunities to learn from each other and share expe riences, including with international Indigenous groups; and
> create opportunities to co-design and participate in land scape-level programs designed to manage cumulative impacts (e.g., community safety specifically as it relates to gender based violence, changes to water quality and quantity, and biodiversity) and benefits (e.g., employment and procurement opportunities).
CMJ
CAROLYN BURNS is the director of sustainable resources at Resolve. Resolve is an NGO that forges sustainable solutions to critical social, health, and environmental challenges by creating innovative partnerships where they are least likely and most needed.
The mining sector is making progress.
The last year has seen many compa nies prioritize environment, social, and governance (ESG) factors, weav ing them into corporate strategies, deci sion-making and reporting, as the issues become a priority for all stakeholders and shareholders. With ESG now firmly integrated within business models, min ing companies must now consider how these issues will evolve and broaden their capabilities to manage them effec tively going forward.
This needs to be articulated through transparent, outcome-based measure ment and assurance. In fact, more rigor ous reporting will become critical if com panies are to meet growing expectations and avoid accusations of “greenwash ing.” Companies that go beyond policy and have a holistic approach to ESG can get an edge on competitors in many ways from accessing capital to securing licence to operate and attracting talent.
The EY Top 10 business risks and opportunities for mining and metals in 2023 report outlines some of the top ESG issues the sector expects to face the most scrutiny on and how to respond.
76% of survey respondents cited water stewardship as their top ESG risk, as climate change and water scarcity concerns esca late. As this will continue to be a critical issue for years to come, coordination between organizations and governments needs to be a priority.
The sector’s current trend of setting blanket targets around water usage often fails to acknowledge trade-offs, for example, water-saving technologies can be energy-intensive. Transpar ency around the water and energy nexus and a lifecycle ap proach can help companies assess and limit impact.
Improving diversity, equity and inclusion (DE&I)
DE&I remains a critical challenge for the sector. Unless mining companies can address these issues, they face significant risks in attracting the current next generations of talent, and in sustain ing their businesses into the future. Key DE&I issues include:
> Increasing participation of women: Companies still strug gle to attract, retain and promote women, depriving them of a huge talent pool as well as the proven benefits of a more gender diverse workforce. Rethinking traditional recruitment tactics, creating equitable career paths, and breaking down barriers on-site and in corporate headquarters are examples to help accelerate change.
> Safety and support on-site: Companies need to change how mining sites are built, operated and constructed to improve
safety and support for all workers. For example, on-site child care could attract more people while making a positive contri bution to the community.
> Building a purpose-led brand: Companies must do more to build a brand aligned with the purpose and values of the next generation of talent.
Increasing credibility of disclosures through data and communication
Around the world, regulation of carbon emissions, sustainabil ity and social governance is increasing, with companies subject to different regulatory and reporting frameworks across juris dictions. The new International Sustainability Standards Board (ISSB) aims to help meet the demand for high-quality, transpar ent, reliable and comparable reporting by companies on ESG, including climate data. Complying with new standards and expectations will require mining companies to improve the availability, rigor and reliability of data.
Accessing capital increasingly depends on meeting ESG tar gets, with investors expecting comprehensive, accurate non financial value included in company disclosures. Policymakers and companies need to work together to ensure the availability of better climate and other ESG data to create transparency and assurance of company actions or plans.
The circular economy offers opportunities for companies to take ownership of their products throughout their lifecycle, finding ways to unlock new value. For example, a company that mines battery minerals can also play a role in ensuring they are
retained and reused at the end of the battery’s life, opening up the opportunity of new commercial models for battery disposal.
Stewardship of minerals throughout their lifecycle can be an excellent differentiator for companies, particularly while recy cling continues to develop. While nearly 60% of survey respon dents said engaging in circular economy strategies is a differen tiator, only half of them plan to do so.
Developing long-term strategic vision for mine closure Mine closures impact a wide range of stakeholders, and expec tations are increasing around how miners mitigate these impacts, including the socioeconomic effects on communities.
A proactive approach to mine closure begins when a mine is first planned. Designing with closure in mind allows for effec tive ongoing engagement with traditional owners and commu nities, creates opportunities for progressive closure activities and ensures that decisions throughout the life of the mine con sider the impact of closure options. When companies take this strategic approach – while engaging with communities and supporting their socioeconomic longevity – they can leave a positive legacy long after mines have closed.
As we head toward 2023, new business models offer oppor tunities for mining companies to reposition for a changing future, with many considering the benefits of strategies to ratio nalize, grow and transform. Companies that scrutinize and shift business models now can get an edge on competitors as demand and expectations change. CMJ
THEO YAMENGO is EY Americas and Canada mining and metals leader. For more information visit http://www.ey.com/en_ca/mining-metals .
The alignment of global mining safety and CR’s Zero Harm values make us passionate about keeping people and the environment safe while using our innovative products. That’s why we’re always working with sustainability and safety experts to design solutions that are ready to meet the challenges of a modern mine. Mine smarter with CR.
Mine operators face mounting pres sure to produce and process ore at a lower cost per tonne and remain profitable in an increasingly compet itive landscape; all that while operat ing in some of the most complex and ever-changing industrial environments on the planet. A major task that these operators must overcome is successfully deploying a reliable and unfailing net work connectivity to all corners of the mine, especially the working face.
Underground mines and tunnels are some of the most challenging environ ments to deploy network systems. The corkscrew design of ramps, varying sized stopes, numerous crosscuts, and increas ing mine depths can severely limit the reach of wireless signals. In a setting with extensive connectivity and throughput demands, operators must consider all available options. The use of technology underground has increased drastically as operators seek enhanced productivity, semi and fully autonomous control, video feeds, energy cost savings, and improved employee safety.
Operators can achieve significant pro ductivity gains by unlocking full auton omy and mobility with a portable wire less infrastructure that voice-only leaky feeder cannot. However, many wireless networking options fall short of mining requirements due to their lack of
dynamic and fully mobile vehicle-to-ve hicle and vehicle to fixed node or worker communication.
Underground mines are mission-critical environments. They present a unique myriad of hurdles to deploying network systems. Connectivity and throughput demands are high, and mine layouts can limit how far wireless signals can travel.
The mining industry continues to invest in various technologies, like semiand fully autonomous scoops and trucks, remote fan and gas monitoring and con trol, video in the shafts and working areas, remote blasting over existing net works, decreasing post blast re-entry times, remote surveying with drones, real time telemetry from mobile and fixed equipment, and all call radio and phone communications during drills and emergencies.
The industrial internet of things (IIoT) is playing a significant role in reducing min ing accidents and downtime. The whole environment transforms when machin ery, equipment, and people are constantly interconnected. Onboard and fixed sen sors can monitor temperature and air quality to ensure adequate ventilation, while cameras can stream video in real time. Wearable devices in combination
with sensors can alert workers when entering an unsafe area and track their progression. They can also be used to alert operators to warnings from the numerous screens in today’s operator cabs.
New technology requires reliable net work connectivity that not only keeps operations running smoothly but seam lessly ensures staff, equipment, and applications remain functioning 24/7, 365 days a year. A solution that allows underground mines to quickly intercon nect existing infrastructures, introduce new technology, relocate, or remove network infrastructure all without caus ing network downtime is needed. As more and more devices get intercon nected, the transmitted data volume grows exponentially.
Underground mines are looking to lever age autonomy to meet increasingly strin gent safety and productivity mandates. The challenge is that autonomous appli cations are not only bandwidth-inten sive, but most require continuous, unin terrupted communication from surface to underground and vice versa.
Operators are utilizing remote technol ogy to help eliminate danger when per forming industrial tasks. Beginning at the working face of the mine and moving
outward, automated equipment enhanc es safety by keeping human personnel out of hazardous locations and streaming live data to enable real-time situational awareness. However, automation plat forms also require continuous connectiv ity to function effectively. If communica tions encounter interference, it may cause bandwidth-intensive autonomous applications to cease operating.
Many mines depend on fiber to achieve reliable underground communications. But installing fiber in active haulage drifts and ramps is challenging and can create operational and maintenance nightmares. In addition, development areas can rarely support any fiber infra structure. It is not uncommon for trucks to accidentally catch and rip down sec tions of fiber. When that happens, con nectivity across the entire underground mine can be lost. Therefore, operators must look towards a wireless solution that can limit the possibilities of down time and the risks it brings with it.
Another important cost factor is to use the existing fiber infrastructure up to a non-production area such as the station or an electrical substation and then go wireless from there.
However, traditional wireless net works cannot provide the unfailing con nectivity that is necessary underground. They depend on fixed transmission points, so they cannot be easily reconfig ured and expanded. In Wi-Fi, point-topulti-point (P2MP), or LTE network, a sin gle point of failure presents a real threat that is not tolerable in mines.
The ability to transmit dynamic video is also a prime requirement for mining as remote-controlled equipment and cameras provide visibility into under ground locations, so high bandwidth and multi-frequencies are a must. The ability to do remote mucking from sur face and continue to skip between shifts can lead to a large production gain.
As more and more devices are con nected, the need for bandwidth increases, so the network must be able to expand easily without interruption. Having a wireless infrastructure in key areas elimi nates the need for additional fiber runs from the surface. Underground, the net work must overcome uneven surfaces, numerous corners, changing back heights, vent tubing, air and water pipes, and power cables as well as be impervious to changing temperatures, depths, and dusty environments; all of which present vari
ous propagation challenges.
In a true wireless mesh network, there is no single point of failure, as each node acts independently, forming connections to other nodes. If one node becomes tem porarily unavailable or goes down, it should have no impact on the network.
The type of mesh required for mining should be self-healing, so that if one node
becomes unavailable, the next node self-optimizes to find another efficient path to transmit data. Uninterrupted, continuous routing is a must. Real min ing wireless mesh networks should be versatile, rugged, and flexible, moving with the mine, as new locations are opened to ensure uninterrupted cover age.
CMJ
Darrell Gillis is Rajant’s sales director in Canada.
Global demand for aggregates and mining materials is on the rise with the industry facing an expected growth of 4.2 bil lion tonnes over the next 15 years. That is a lot of material, which means producers need efficient equipment to meet spec ifications and turn a meaningful profit.
Every tonne of material must go over at least one vibrating screen, so ensuring the equipment’s efficiency is critical to an operation’s success. The good news is that there are technolo gies available today that can help increase or improve screen ing productivity. Integrating cutting-edge systems like eccentric screening technology, state-of-the-art screen media, and diag nostic tools can prevent blinding, pegging, carry-over, or con tamination, thus improving screening performance, productiv ity, and profits.
Vibrating screens that are engineered with a double eccen tric shaft assembly create a constant stroke to maintain g-force during material surging. The double eccentric shaft design forces the screen body to follow the movement of the shaft. While the shaft travels up, the counterbalance weights move in the opposite direction and create a force equal to what is gen erated by the body. As a result, the forces cancel each other out and maintain a consistent positive stroke that handles material volume spikes without losing momentum.
One producer in western Canada quickly saw the benefits of switching to double eccentric screening technology when they replaced two horizontal vibrating screens with one double eccentrically driven, four-bearing inclined vibrating screen. Changing their equipment helped to eliminate surging, blinding, pegging, and material contamination challenges while increas ing their production by 25%.
A vibrating screen’s operation can have a significant impact on a machine’s surroundings. The metal springs on a traditional concentric vibrating screen, for example, can be noisy to oper ate. This metal-to-metal, up-and-down or side-to-side move ment can cause excessive noise and vibration. To resolve this problem, double eccentric technology makes use of shear rub ber mounts that are strategically designed to minimize lateral movement. The rubber mounts reduce noise while maintaining smoother operation, even in extreme circumstances such as overloading, surging, and starting or stopping under load.
The use of eccentric technology virtually eliminates vibration in the structure – or chassis when used with portable equip ment – which protects the integrity of the machine. This means producers can potentially use multiple eccentric vibrating screens in one structure, boosting productivity. Attempting to operate multiple concentric machines in a structure, however, could create vibrations damaging enough to not only cause a negative effect on the quality of production but open the door to safety risks and downtime.
A leading phosphate producer in North America – producing 8.0 million tonnes per year – increased screening area by 60% by transitioning to double eccentric equipment. The mine incorporates a six-story screening plant to house multiple vibrating screens that run 24/7. Multi-storey screen houses are common in industry but can pose structural concerns due to the vibrating screens’ size, capacity, and force. Opting for dou ble eccentric technology eliminated those concerns.
Integrating eccentric screening technology, state-of-the-art screen media, and diagnostic tools.
Combining the use of advanced eccentric screening technology with the best screen media for the application is a recipe for success. Specifically, polyurethane screen media can be a bene ficial asset to any operation seeking to prevent blinding and pegging while improving material stratification and increasing wear life.
Polyurethane media offers the best combination of open area and wear life for both wet and dry applications. Polyurethane screen media that is poured open cast can result in 1.5 to 2 times longer wear life than injection-molded products. Opencast polyurethane permanently hardens when cured to main tain its chemical properties and improve wear life. Alternatively, injection-molded screen media can soften when temperatures rise, resulting in shorter wear life. Polyurethane screen media also features tapered openings to reduce the risk of blinding and pegging.
The solution to improving material stratification lies in find ing the ideal mix of screen media types to ensure all phases of screening work correctly. A screen media company that offers a variety of screen media types can help evaluate how material moves through the three phases of screening – from layered to basic to sharp – to give recommendations on the best screen media for an application. Producers can customize the screen deck by choosing screen media that maximizes productivity for each phase by blending the best combination of open area and wear life.
A vibrating screen needs regular checkups to run optimally. Vibration analysis and diagnostic systems designed specifically for vibrating screens by OEMs (original equipment manufac turers) are reliable tools for maintaining continued efficiency and longevity of screening machines. To ensure the best pro ductivity, operations can partner with an OEM that specializes not only in manufacturing equipment, but also offers addi tional diagnostic tools, product-specific knowledge, and years of engineering experience.
Utilizing vibration analysis software, for example, allows mining and aggregates operations to monitor a vibrating screen’s performance in real-time by detecting problems before they lead to diminished performance, decreased effi ciency, and increased operating costs. The most robust sys tems incorporate eight wireless sensors that magnetically fas ten to key areas of a vibrating screen and measure orbit, accel eration, deviations, and other important data points that indicate the condition of the machine. The sensors send realtime information wirelessly to be analyzed, ideally by an OEM-certified service technician who can provide a detailed summary and recommendations.
Some manufacturers use vibration analysis technology to offer impact testing – or a bump test – which ensures proper machine calibration and promotes efficient operation. Impact testing involves striking the machine at key points with a dead blow hammer while the machine is off. Vibration analysis sen sors are placed at key locations on the vibrating screen while a technician tests the natural frequency of a machine. Based on the results, engineers can adjust machine parameters to avoid operating in resonance, which can diminish productivity, dam age vibrating screens and pose safety risks. Natural frequency can shift over time as components are repaired or replaced, so the impact test should be conducted regularly. By incorporating impact testing into an operation’s regular maintenance routine,
producers can ensure optimum screening performance and equipment reliability.
Another advanced diagnostic tool is condition monitoring, which is designed to monitor the health of vibrating screens using modern algorithms and artificial intelligence. The system utilizes permanent sensors that monitor the equipment 24/7 to capture real-time information and provide alerts via e-mail immediately upon the first sign of a potential problem. By con stantly monitoring the accelerations of the vibrating screen, certain systems can even forecast the equipment’s dynamic condition in regular intervals of 48 hours, five days, and four weeks. With consistent use, condition monitoring software will accurately point out and predict critical issues and advise when to schedule maintenance, along with what to focus on during that planned downtime.
By using diagnostic programs to conduct regular analysis, and by engaging in predictive and preventative maintenance, operations will see minimized downtime through faster prob lem-solving, lower repair costs, and increased peace of mind.
The development of the double eccentric screen and other screening technology provides operations with innovative and cost-effective ways to increase their profits and efficiency. By integrating the right equipment, screen media, and vibration analysis systems, producers can see more uptime, higher qual ity results, increased productivity, and greater profits.
CMJ
Duncan High is the processing equipment technology manager at Haver & Boecker Niagara.
Ventilation is the greatest energy consuming system in most underground mines. Traditional operations, especially older ones, run their ventilation fans 24/7 to provide fresh air and to remove noxious gases and particulate matter.
It doesn’t have to be that way. Advances in ventilation on demand (VOD) offer real savings.
In the case of Newmont’s Éléonore gold mine, estimated energy savings thanks to VOD amounted to 43% on propane to heat underground air, 56% on electric power consumed by fans, and 73% on surface electric power demand.
The project is located in Eeyou Istchee or James Bay region of Quebec. The mine is 100%-owned by Newmont, and the 2022 guidance is 275,000 oz. of gold.
The Éléonore gold mine has a fresh air capacity of more than 425 m3/s. The principal ventilation system consists of two Howden Alphair 12300-AMF-6600 exhaust axial fans with a nom
inal power of 1,471 kWh each, configured in parallel. There is also an exploration shaft that has two Howden Alphair 11200AMF-6600 main intake fans with a nominal power of 551.6 kWh, again configured in parallel. The mine also has over 140 auxil iary and booster fans operated in conjunction with seven damp ers and air regulators, and a heating system fuelled by propane.
Newmont invited Howden to design and implement a venti lation control system that would optimize the supply of fresh air to underground workers while reducing energy consump tion and operating costs – all of which translated into the reduc tion of greenhouse gases.
Howden set out to create an automated system covering all the ventilation equipment in the Éléonore mine, including the main fans, underground auxiliary fans and airflow regulators. Thirty ventilation monitoring stations (VMS) were installed to determine the quantity and quality of fresh air at various
February
963
871
852
886
886
2,552,577
2,049,635
2,854,524
2,205,882
2,666,228
2,214,275
2,694,978
1,256,929
1,271,459
1,290,602
732,193
1,749,888 787,243
1,729,800 564,951
1,674,000 440,029
2,684,352 466,616
594,039
2,684,352 809,630
2,684,352 516,953
1,298,836
2,527,250 452,823
points underground. Each VMS includes one flow sensor and three gas sensors to detect carbon monoxide, nitrous oxides and propane. These VSM stations are an integral part of Howden’s Ventsim Control system.
The system communicates with all the hardware and instru mentation in the mine without the need of programming on the surface. The system automatically adjusts airflow according to real-time needs in the mine and allows easy point-and-click manual control as desired.
The Ventsim Control installation included a mine-wide track ing system to detect the presence of vehicles and personnel underground. Each of the 144 vehicles was fitted with a radio frequency identification (RFID) tag that indicates its position in the mine and whether the engine is operating. Everyone work ing underground was also given a unique RFID tag that con nects to one of 254 zone-based access points. As mine condi tions change, the system automatically recalculates and adjusts using the latest information.
The tracking data is transmitted from these access points to the control room on the surface through a hybrid fiber optic network. There is currently between 60% and 70% Wi-Fi cover age in the mine, with plans for 100% coverage during full pro duction. The data from the RFID tags provides enhanced safety and management of the movement of vehicles and personnel, as well as ventilation on demand.
The data from the tracking system allows ventilation require ments for each zone to be calculated by the VOD logic software. This information is then used to automatically modify the speed of each of 140 underground auxiliary fans, to ensure that
each zone of the mine receives enough fresh air.
The control system in the Éléonore mine can be easily expanded as the mine grows in size to maintain adequate, safe ventilation in every part of the workings as new areas and lev els are opened up.
The installation of the Ventsim Control system, with its mon itoring stations and automation of all ventilation equipment, means that the supply of fresh air to individual work zones is maintained with complete safety, ensuring all underground personnel have a comfortable working environment. At the same time, the waste associated with continual ventilation of the whole mine has been eliminated.
The results were verified by an energy audit caried out by Howden. The project could save almost 3.0 million litres of pro pane, 31 million kWh of underground electricity, and 19 mil lion kWh of surface electricity.
The Éléonore mine benefited from reduced air waste because Ventsim Control calibrates in real-time to actual air flow needs where people and machinery are active. This increased production because blast gases were cleared quickly, reducing downtime up to three hours per production blast. Safety is improved because personnel do not control the fans manually. Contaminants gases are monitored and reduced to comply with regulations. The strategic deployment of variable frequency drives reduces power use by 50% to 60%. And the system is expandable.
Newmont chose Howden’s VOD system for its promised ben efits in production, sustainability and safety – all of which were realized. CMJ
O P T I M I Z E Y O U R P R O J E C T SOPTIMIZE YOUR PROJECTS W I T H T H E M O S T E F F I C I E N TWITH THE MOST EFFICIENT V E N T I L A T I O N S Y S T E M
N T H E I N D U S T
ENERGY-SAVING SOLUTION
Capital-intensive projects in foreign countries and long-term agreements in the mining industry can be sub ject to political risk and change that can impact investment. The protections avail able through investment treaties and the importance of structuring investments at the outset can help mitigate risk and pro tect international interests.
One of the key tools available to those involved in international mining opera tions is investment structuring to seek protection (and rights) under interna tional investment treaties. Not only can investment structuring provide certain
protections, but it can result in a com pany being able to pursue its rights with assistance from disputes funders or to utilize disputes funding so that the dis pute is de-risked for subsequent corpo rate transactions.
Recently, CMJ met with a panel of three lawyers from Dentons to discuss invest ment protection of capital-intensive proj ects in foreign countries, and long-term agreements in the mining industry.
Dentons’ expertise and experience in mining and natural resources goes beyond the law and extends to a deep understanding of the industry and how
that should translate into legal matters. This article summarizes the key take aways from that discussion. A detailed version of the discussion is available through a podcast on the Northern Miner website.
What is investment protection? And what do investment treaties protect?
Investment protections are protections and benefits to foreign investors under international investment agreements. They are usually multilateral or bilateral investment treaties or free-trade agree ments that contain investment protec tions. The first investment treaties date back to the mid-fifties, but they became much more common in the 1980s.
RACHEL HOWIE is a partner at Dentons and the co-lead of the Litigation and Dispute Resolution group in Canada. She also co-leads the firm’s Canadian Alternative Dispute Resolution and Arbitration group. Her practice focuses on international and domestic arbitration and litigation, primarily in the energy, mining, and natural resources industries.
JAMES LANGLEY is a partner at Dentons in London, U.K. He focuses on international arbitration, including both commercial arbitration and investor state arbitration, as well as commercial litigation and alternative dispute resolution. He works within the natural resources, energy and infrastructure, retail, telecoms, shipping, and sports sectors.
JOHN HAY is a partner at Dentons and the head of the U.S. International Dispute Resolution group. He has more than 35 years of experience representing domestic and international clients in complex commercial and investment treaty disputes. He has arbitrated disputes in a wide variety of areas, including construction, energy and mining, joint ventures, financial services, real estate, and investments in foreign countries.
They are intended to attract private investment in developing countries. They provide fundamental protection for investments as an alternative to local law that is inadequate to protect the investor, and they provide rules for arbitration under the treaty as an alternative to local courts.
To put it in context, there are probably over 2,300 different investment treaties in force today in the world. In addition to the procedural protection of an arbitra tion clause, they also have some substan
tive protections, such as most favoured nation treatment and national treatment, which prevents discrimination in favour of local entities when a foreign investor is making an investment. Other key pro tections include an obligation to provide fair and equitable treatment and a guar antee against expropriation without compensation.
Freedom to transfer funds and capital into and out of the country is also an important aspect of these treaties. The treaties also provide full protection and security against possible actions by the government. They cover investments by an investor from one country in the terri tory of another country. The investment is usually generally defined to include virtually any asset.
Investment protection protects the inves tor against the risk of state interference with investments. This can be a concern in mining because mining projects are long-term. They could span multiple gov ernments and multiple elections in any given region. And even in states that are considered safer for investment, a gov ernment change because of an election or another regulatory shift that could see perhaps a new denial of a license for a
and political risk and change.
If those investment agreements give the right to arbitrate disputes, they ensure that the investor is not necessar ily required to act against the state in local courts where the outcome may be unpredictable or where the outcome might be political or where the courts might not be thought of as independent. Another important aspect is that these protections are additive to what can be obtained through political risk insurance from private providers or in contracts from governments or from the multilat eral investment guarantee agency. The protections and benefits are outside of national laws, which mean it is very diffi cult, if not impossible for one state to uni laterally change the law to deny them.
Investment protections also provide foreign investors with more expansive protections if they must pursue a claim for a loss; the amount that they could claim and could be entitled to under an investment arbitration could be far higher.
Unlike private insurance that might have premiums to be paid, there is no cost to these protections.
That is a relatively new thing and of course a massive advantage for an inves tor in mining, for example. Local courts do not necessarily have an expertise in mining, but arbitration tribunals do.
To allow negotiations that oftentimes come up with a resolution, investment agreements are structured where the party bringing the claim must give a notice, and then there is usually a cooling off period before the claim proceeds. The benefit of this structure is that it might be enough to bring the parties to the table to really get a commercially fair deal.
In most cases, you seek the benefit of those agreements in countries where the regimes are not democratic to protect your investment. So how do those gov ernments get into those agreements?
It is not an in an agreement between the individual company and the state, although that sometimes happens. It is a situation where one country has a treaty with another country where both coun tries are consenting to arbitration, and under that treaty, they agree that the investors from one of the countries into the other will have certain rights.
For example, Canada and Colombia
There are plenty of issues that can come up and motivate a government to change its policy.
have an investment treaty under which if a Canadian mining company invests in Colombia and the Colombian government does something that adversely impacts that investment, that investor has a right to bring an arbitration against Colombia. So, Colombia is bound to arbitrate.
These are bilateral investment treaties, but usually called investment protection and promotion agreements. States enter these treaties to incentivize investment from the other state. Despite exposing themselves potentially to claims from investors, they are also doing that in exchange for investment in the first place. Something that will be factored into the negotiations between the states is what protections one is prepared to offer to the other. The system can sud denly change, and one country might ter minate a treaty (as was the case during NAFTA renegotiations), but eventually they may reach another agreement that satisfies all parties.
Why is this particularly relevant to the mining industry?
There is an exponential demand for criti cal minerals and rare earth elements that is expected to quadruple by 2030 because of EV and other green technologies. These are still capital-intensive endeavors, and they still require substantial investment at the outset. They have high production
costs, they are long-term, and the investor might not see a profit for years after start ing a new operation. Also, at that intersec tion of competing regulatory and political issues for governments are things like water and land use plans, taxation, royal ties, mining permits, emissions targets, environmental areas of protection, and government interest and strategic and critical domestic supply. All of that could create a perfect storm where projects, in jurisdictions that might be politically unstable or even subject to just regular change through elections and change in government perspective, would be sub ject to impacts in a way that are detrimen tal to the investment.
Because miners doing business now need to make decisions on projects to meet demand in 2030 and beyond, it is difficult to predict where that political and regulatory perspective might be at that point in time. So, doing an invest ment agreement analysis and seeing what protections are or could be in place can help to protect them in the future.
You can expect all sorts of ways in which governments will seek to take a greater share of that investment. As an investor, you should never wait until something goes wrong to your invest ment to check whether you have treaty protection; you need to make sure you have that at the outset to avoid having to
restructure your investment to take advantage of a treaty, which you gener ally cannot do after a dispute has arisen.
There are plenty of issues that can come up and motivate a government to change its policy. If a mining company is investing in a country that does not pro vide a great deal of protection through treaties, they can at the early stages of the project partner with another com pany, that would be the actual investor, from a country that has a better invest ment treaty with the host state.
ESG has a more advanced regulatory regime in the more developed parts of the world. We are seeing provisions around ESG being introduced in trea ties. It is quite a new thing. ESG in the context of mining has several different strands. One of the obvious things would be the environmental impact of the min ing process itself. Then, the human rights related issues and the impact on local communities.
The G in ESG manifested itself in issues around corruption: we are seeing an increase in integrated companies operat ing projects out of subsidiaries or group companies. The parent company is a listed company in a jurisdiction where it is eas ier to bring claims. Also, when a country offers favourable benefits for investments in the renewable energy sector and then removes those or significantly reduces the benefits, the result can be a whole wave of claims against the state.
A relatively new phenomenon is the possibility that the treaty wording allows the state to bring a counterclaim against the investor in case of environmental issues for example.
So, there may be a situation where an investor has been successful in the pri mary claim against the state, but there is a counter claim that neutralizes the value of that. It is a growing area and will become more prominent as we see new treaties where it is easier to bring counterclaims. CMJ
In October 2022 issue, the title of the article on pages 16-17 should be “Updates on gold producers in the Maritimes and Atlantic Canada.”
Also, “and Atlantic Canada” should be added at the end of the first sentence.
As a leading provider of mining solutions, Hitachi offers high-performing equipment and services that help bolster your operational performance and overall productivity. From fleet management systems that render real-time visibility and establish control over mine operations, to highly engineered excavators and haul trucks, Hitachi is here to protect your operators, your site team and your bottom line.
New mining projects can positively transform the social, economic, and technological landscape of a region. But closure of a mining project often unin tentionally creates a stereotypical “boom and bust” cycle, creating economic, envi ronmental, and social challenges for stakeholders. Like many major drivers of economic growth, mining projects have the potential to mold multigenerational social architecture at the same time as modifying the surrounding environment, communities, and region to have a posi tive outcome.
With the increasing demand for criti cal minerals and the advancement of “green” technologies to slow the advance of climate change, mining operations will continue to be more prominent and widespread. Even with increased effort in recycling and reuse of metals, there is simply not enough material in circula tion to avoid a ramp up in the number of mining projects globally. This will chal lenge the industry to find solutions for a greater number of communities and regions. Local communities will face the challenge of departing human capital as mine cycles end, with trained, skilled workers leaving communities as mining operations wind down to find the next opportunity.
The wave of departing workers has real impacts on communities facing shrinking social benefits afforded by the influx creating economic activity and human capital. So, with briefer lifecycles, and more remote host communities, a more drastic effect is likely.
Despite these new or emerging para digms, planned reclamation and closure
is still one of the lowest priorities in min ing decision-making frameworks. Included in the Paris 2050 Agreement and UNDRIP, there is an ever-shifting regulatory landscape and new investor and consumer environmental, social –and governance (ESG) pressures. Yet a recent study from the Arabian Journal of Geoscience surveyed 60 mining experts on ranking what criteria is important to begin underground mining operations. The researchers found reclamation ranked as having the lowest importance in decision-making.
A study in early 2022, involving researchers from several Brazilian uni versities, found that mine closure in their country represented one of the top five greatest operational risks, and recom mended that planning for closure could help improve operational performance while lowering environmental, socioeco nomic, health, and safety impacts.
Likewise, inaccurate approaches to mine closure cost estimating carries sig nificant risk. An Australian study pre sented in the International Conference on Mine Closure found that rigorous clo sure estimates could be as high as double the initial budget in the Australian min ing space. This is further confirmed by a guide from the Intergovernmental Forum on Mining, Minerals, Metals and Sustainable Development, where “mine closure costs have been underestimated, partly due to a lack of understanding of the complexity of the task.”
Many international, national and com pany standards addressing mine closure and reclamation exist, providing exten sive resources that often exceed regula tory requirements. Best practices for
mine closure include Canada’s own Towards Sustainable Mining (TSM) mine closure framework which is frequently being adopted in other nations.
Resulting closure plans and strategies aim to mitigate socio-economic impacts and return mine sites to viable and diverse ecosystems that will serve the needs of post-mining use of the land. The principal objective has been to bring ‘planning for closure’ into the design phase, with progressive reclamation as the project progresses.
There has been progress to celebrate within the Canadian context. We can com pare the closure plans and approaches of the mines of today with those of the 1940s, the Giant mine in the Northwest Territories, and other “historic sites.”
Modern closure and remediation pro cesses take significant steps to ensure there is long-term chemical and physical stability to a closed mine site.
The Hollinger legacy project in Timmins is one example of community reclamation – a way to use the excava tion from gold mining to create recre ational value for the host community. The agreement between industry and community was signed before opera tions ended; an example of why good stakeholder engagement and putting a plan for closure in place long before it arrives can lead to positive outcomes.
The Hollinger legacy project demon strates both the risk of poor closure plan ning as well as how proper prioritization from industry and community can build a better future for mine sites.
Georgina Pearman’s 101 Things to Do with a Hole in the Ground lists popular examples from around the world where old mines have been converted into opportunities for socioeconomic develop
ment and growth. Examples include cre ating spaces for recreation, science, tech nology, medicine, and energy generation.
Despite having abundant available best practices and resources, why are the notable international examples not yet the new standard?
For all mining projects, exploration leads to evaluation which, in some cases, leads to development, construction, produc tion and then closure.
The trend for greater collaboration and stakeholder engagement when plan ning mine closure is a part of our new paradigm – as a report from CSA Group in 2020 highlights greater expectation around mine closure having social and economic benefit. This will necessitate greater multi-stakeholder engagement, earlier and better-informed consultation, and stronger collaboration between par ties in planning for the future.
One needs to consider the question: Is optimizing the current process alone going to solve the closure challenge for us and our stakeholders?
Some examples of key questions that lead to a different way of thinking about the closure challenge with more sustain able outcomes include:
1 To what extent have we gone past con sultation processes and co-designed a vision for the future that mining can enable with our host communities?
Impact benefit agreements are set up for those whose lives will be affected in all the stages of the mining process. If impacts of mining extend beyond this process, then how can we engage communities early to ensure we understand their visions for a future that a post-extraction use of the land and assets can enable?
2 To what extent are we being good neighbors during the project vs. being good citizens who are designing with the end in mind?
Because human, social, intellectual, and cultural capital extends far beyond the fence line of a site, why does closure focus on the impacts of mining in a region through a site-specific lens? Mining proj ects aren’t confined to development of a mine site, mining operations can impact the development of an entire region. If mine sites can be collaborative with local, regional, or national government agen das, mining can enable more economic and social possibilities. This can even be more effective through the inclusion and prioritization of Indigenous governments and voices of Indigenous leadership.
3 To what extent are we embracing the circular economy that many of our min erals and metals are increasingly becom ing a part of?
Cradle to cradle thinking reprioritizes our design for a circular economy – we should be designing for what the mine sites and assets become after extraction is complete. For example, how can mod ular units on sites be designed to build homes and facilities in local communi ties? How can mine sites be used to sup port new infrastructure projects to deliver lasting benefits for the region even after all the miners have left?
Some say, “the only certainty in min ing is closure.” A closed site is the legacy left behind for future generations. Looking at closure through the life-of-as set lens when designing and planning, as opposed to only the life-of-mine, mining companies have the potential to make good otherwise lost value for not just all their current stakeholders but for future generations.
CMJ Stephan Theben is managing principal and mining sector leader, SLR Consulting, Canada and Charlie Ursell is a consultant and managing partner at Coeuraj Consulting.
US AT
Demolition robots excel at under ground mining due to compact, emission-free power, and remote-op eration. Designed for demanding demoli tion applications, these machines easily stand up to the heat and pressure of ultradeep mining.
Demolition robots are used for a variety of tasks, including scaling, drilling, blasting, bolting, breaking, shaft maintenance, and stope retrievals. After a rock fall, for example, a demolition robot can be used to retrieve equipment like a loader. They tend to travel the uneven ground more quickly than traditional retrieval equip ment, and they can break up oversize and other obstacles to make extraction easier.
There are also models that are set on a pedestal rather than tracks. These sta tionary breaker boom systems are used for primary breaking tasks that feed mobile crushers, jaw crushers, gyratory crushers, and grizzlies. The power source and arm are integrated for a compact
breaking solution that has just a single power cable.
What are the main features of a demolition robot?
Demolition robots offer exceptional pow er-to-weight ratios – often on par with machines three times their size – and sig nificantly outclass even the most advanced jackleg drills. An advanced three-part arm provides unrivaled range of motion for drilling, scaling, breaking, and bolting in any direction. The use of hydraulics also eliminates the need for supplying compressed air, which in turn, minimizes the utility requirement at the face, while electric running guarantees zero-emission operation.
SmartConcept is a set of technological fea tures, developed by Brokk, that offer im provements in power management, reli ability, maintainability, and ergonomics.
The SmartConcept technology is split into three parts: SmartPower, SmartDesign, and SmartRemote.
How do SmartPower and SmartDesign technologies apply in the case of demolition robots?
The revolutionary SmartPower system was designed to withstand extremely tough day-to-day demolition forces. It helps the operator start the robot on a poor power supply while, at the same time, protecting it from harmful faulty power. The system senses when the power supply is poor or faulty and com pensates as much as possible to protect internal components. The technology has unparalleled reliability.
SmartDesign extends machine life and provides unprecedented ease of mainte nance. With 70% fewer cables and the addition of hardened exterior compo nents, Brokk robots are better equipped to withstand the rigors of machine vibra tions and heat generated during opera tion. The line features several elements to ease maintenance, including strategic, easy-to-access grease points and hydrau lic hoses; LED headlights with built-in protections; and steel machine covers. Through the technology, operators not
only get 360° rotation abilities, but they can operate “over the back,” which offers heightened flexibility in confined spaces.
What are the main reasons to choose underground demolition robot technology in the mining industry?
Everyone is aware of the dangers of un derground mining, so safety is a major reason to choose a robot. With remote-op eration, workers can strategically posi tion themselves to avoid the most dan gerous situations. We know that 80% of underground mining accidents and fatal ities occur at the face, so allowing work ers to perform drilling, blasting, bolting, and breaking remotely can make a huge difference.
Versatility and efficiency are other rea sons. With the right attachment, opera tors can move from scaling to drilling for bolting and then drilling for blasting with one tool change – that includes cleaning the lifters with a spade tool in the ham mer. These machines can also handle much larger attachments than similar
Opposite: Demolition robots are used for a variety of tasks, including scaling, drilling, blasting, bolting, breaking, shaft maintenance and stope retrievals
Right: The Brokk Pedestal Boom is a stationary breaker boom system used for primary breaking tasks that feed mobile crushers, jaw crushers, gyratory crushers and grizzlies.
sized equipment, allowing mines to bring powerful tools to new applications with out increasing tunnel size. It even opens the possibility of 100% remote drilling and bolting since there are several com pact demolition robots with ample power to operate carousel attachments. While the operator stands a safe distance away, the robot can drill, load a rock bolt, then torque it without any wasted movement for fast, efficient, safe bolting of the back.
Are the demolition robots batterypowered?
Currently, demolition robots are offered in electric and diesel models. The first re
mote-controlled demolition machine, in troduced in 1976, was electric, and the technology has continued to evolve ever since. The electric models feature zero emissions, which means they are ideal for underground mining. The Smart Power design ensures that faulty electric ity or power surges will not damage the machine while preserving unparalleled power consistency. Brokk (the demoli tion robot manufacturer) continues to monitor the development of battery-pow ered machines as technology continues to advance. It is conceivable that bat tery-powered models will be available in the future.
CMJ
Rajant
Industrial
Wireless communication got off to a slow start after James C. Maxwell, consolidating the work of others, created a theoretical description of electromagnetic waves in 1865. His elegant set of equations languished for over two decades until Heinrich R. Hertz developed hardware in 1887 capable of verifying Maxwell’s predic tions. These electromagnetic waves then remained a lab oratory curiosity for more than another decade until Guglielmo Marconi improved equipment to the point where by 1902 telegraphic messages could be sent over distances of more than 3,000 km.
Technological advancements in com munications like this ushered in a new era of interconnectivity which have echoed throughout industrial revolu tions, the age of information, and beyond. In the first half of the last century, radio communications were widely used by public organizations, such as the armed forces, emergency services, and other government entities. Over time, commu nication via radio waves was incorpo rated into other sectors, such as televi sion as well as industrial settings like fac tories and primary resource sectors.
Over the last 40 years, communication systems in mining have steadily evolved as new technologies and have become adopted across the sector. One of the research leads at Cambrian College’s Centre for Smart Mining, John Moon, wit
nessed the early history of underground wireless communications as he saw it unfolding in real time working in the sec tor and teaching at the College.
Moon moved to Sudbury in 1980 to teach courses in electronic communica tion in the Electronics Department at Cambrian College. Then, after many years teaching, he left the college, and eventually became one of six individuals
involved in starting a com pany called HLS Hard-Line Solutions that makes exten sive use of underground com munications.
Not long after being hired by Cambrian College, the department chair asked him to attend a conference on underground communica tions to be held across town at Laurentian University.
At the conference, several papers were presented. They primarily dealt with the use of very low frequency (VLF) communications using a large wire loop antennas buried in the ground for transmitting. While these systems have no infrastructure in the mine itself, the data rate is so low that only rudimen tary information can be sent, and in only one direction.
An exception to the VLF presentations was a paper given by an academic from England. He and a spin-off company had developed a system where relatively wide bandwidth communication could be supplied throughout a mine and would also connect to surface. It used what he called a VHF “leaky feeder” as both a radiating element and as a trans mission line. He passed around a section of leaky feeder, which looked like ordi nary RG-213 coaxial cable, only with the normal copper braid replaced by several wires running lengthwise along the out side of the cable.
He described in detail how the in-line bi-directional amplifiers were placed at
Not long ago, mining automation and operations management were limited by available communication systems.
regular intervals, how the transmit and receive frequencies were offset, and how appropriate amplifier gain was main tained using a sub-audible pilot tone. Moon recalled that the questions after the presentation were somewhat aggres sive, with objections mostly pointing out the susceptibility of the cable to damage in a mining environment, thus making the VLF system superior. He could see both sides of the argument and won dered if the systems could not be imple mented together. VLF for emergency alerts only, and VHF for voice communi cation. He remembers being impressed with this new solu tion, having no idea it would soon become a dominant technology in underground mines.
After the conference Moon encountered an interesting fellow who worked in the instrumentation department at Falconbridge mine (now Glencore). The man described a project for the radio-remote control of underground min ing equipment. He and Moon talked for a while and con cluded that the drift might serve as a crude waveguide. Conventional waveguides are hollow rectangular (or circu lar) metal tubes that can carry very short waves with low loss.
For waveguide transmis sion, however, there is a criti cal frequency, called the cut off frequency, below which the wave cannot propagate. We quickly calculated the cut off frequency of the drift and concluded that frequencies at the upper end of the VHF band should propagate.
Subsequent conversations revealed that multipath fading is a serious prob lem encountered by such point-to-point communication in a drift. Multipath con ditions occur when the transmitted sig nal follows several different paths to the receiver, due to reflections from the sides of the drift. If two paths differ in length by one-half wavelength, the two signals will destructively interfere with the receiver. At 150 MHz, one-half wave length is only one metre, so half-wave length path differences are common. Solutions include using multiple anten nas at the receiver, thus providing space diversity for the incoming signal.
There were now growing require
ments for three distinct types of commu nication. Mine-wide voice, which the leaky feeder system addressed, non-criti cal data transmission, such as the trans mission of environmental conditions to surface, and data used for the real-time control of equipment. Would it be possi ble to send data over leaky feeder as well as voice? Low speed, non-critical data can easily be sent over leaky feeder, but time-critical data is another matter.
Moon had occasion to work on such a leaky feeder application. The remote-con trol system worked very well most of the time. Unfortunately, “most of the time” is not good enough. The mystery was, what was causing the communication link to fail, unpredictably, “once in a while?” A spectrum analyzer revealed the reason.
Intermodulation distortion (IMD) results from having multiple strong sig nals passing simultaneously through an amplifier. This IMD can be divided into two groups, odd-order and even-order. The odd-order distortion products are by far the most troublesome, and this is what the spectrum analyzer showed was causing our problem. If two hand-held radios, operating on adjacent channels, were keyed at the same time, the IMD appeared and completely overwhelmed the digital data signal, even though we were on a dedicated channel. Once either
of the two radio users stopped transmit ting, the problem disappeared.
IMD can be troublesome, not just in leaky feeder repeaters, but in all commu nication equipment. Two ways of miti gating the effects of IMD are first, to reduce the amplitude of the signals caus ing the distortion, and second to mini mize the duration of the signals at any given frequency. In the 1990s, communi cation equipment using two types of spread spectrum modulation began to appear at reasonable cost. The first, known as direct sequence spread spec trum (DSSS), spreads the transmitted signal over a wide range of frequencies, while at the same time reduc ing its amplitude. The second, known as frequency hopping spread spectrum (FHSS), causes the transmitted signal to quickly jump from one fre quency to another. Either of these techniques not only reduces the problems caused by IMD, but also reduces mul tipath fading in point-to-point applications. Most spread spectrum devices, such as Bluetooth or IEEE 802.11 (WiFi), operate at frequencies above the capability of leaky feeder. Distributed antenna systems (DAS), capable of operating at higher frequen cies, are therefore used to extend range.
Not long ago, mining auto mation and operations man agement were limited by available communication sys tems. Thanks to significant improvements in wireless technology, this limitation is rapidly giv ing way, permitting increased levels of mine-wide monitoring of environmental conditions, equipment status, and even the health of personnel, in addition to the real time control of equipment and the coordination of autonomous operations. We have come a long way.
CMJ
John Moon is a former faculty member at Cambrian College in the electronics and instrumentation programs. He is responsible for training generations of electronics professionals in the Sudbury area and beyond. He is now the electrical engineering research lead for the Centre for Smart Mining at Cambrian.
Steve Gravel is the Manager of the Centre for Smart Mining at Cambrian College.
KMX Technologies, LLC is a company dedicated to solving critical environmental and energy challenges of the 21st century. Through its proprietary membrane distillation technology, the company sustainably sources critical minerals necessary for next generation supply chains and infrastructure, is advancing wastewater treatment, and is accelerating energy storage with its direct lithium recovery enhancement processes. KMX delivers zero-waste solutions using its proprietary tech nology spanning water, lithium, and critical minerals.
Lithium is an essential component of a sustainable future as it is a necessary element in EV batteries and grid storage solutions for renewable energy. KMX recently partnered with CanmetMINING of Natural Resources Canada (NRCan) to max imize sustainable and economical lithium production in Can ada. KMX will be using their membrane distillation technology in conjunction with CanmetMINING’s expertise in water treat
ment to optimize the concentration of lithium while maximiz ing water recovery of the highest quality.
This partnership will enhance lithium recovery across North America, making a sustainable future more possible. The part nership is timely, as it coincides with the Inflation Reduction Act recently passed by U.S. President Joe Biden. As part of that bill, American consumers receive tax credits for purchasing EVs with batteries whose materials were sourced in North America. This increased demand for North American lithium means that sustainable and economical production is essential to avoid supply chain issues and therefore maximize the posi tive impact on Canada’s economy.
Recently, I interviewed Zachary Sadow (ZS), CEO of KMX Technologies. Sadow explained how KMX has changed how critical minerals and lithium are secured, while providing next generation water treatment opportunities.
CMJ: Can you talk to us about the history of KMX Technologies? How long have you been with KMX Technologies, and how did KMX start providing zero-waste solutions to mining companies?
ZS: KMX was founded in 2020 as part of an IP and asset acqui sition, building on over 15 years of deep technology devel opment and vacuum membrane distillation leadership. We rolled the IP and assets into the newly formed KMX Technol ogies, began making critical enhancements to the technology, and soon after started focusing on lithium concentration as our core end-market.
The technology has gone through multiple generations of enhancements and successful demonstrations across vari ous fields. Since founding the new company in 2020, we have done a few things that built on the prior 15 years of technology
development. First, we have enhanced the technology signifi cantly by the introduction of our Generation III membranes. The performance and durability of the Generation III mem branes represent a significant improvement over the previous generation. Second, we have improved our supply chain and our ability to scale up by partnering with companies such as Sumitomo Electric.
The third significant thing is the emergence of lithium as a core focus since the founding of the company in 2020. With the global energy transition, lithium prices have taken off, and KMX has a unique application as a lithium concentrator.
CMJ: What makes the new membrane distillation technology of KMX unique, and are you collaborating with other companies to develop this technology?
ZS: What we do is unique and specific, but we are extraordi narily collaborative in our approach to the market. We have a great manufacturing and strategic partner of core elements, Sumitomo Electric Industries Ltd. In 2021, KMX and Sumitomo entered an MOU to commercialize KMX’s membrane distilla tion technology. Recently, we signed a global oil and gas tech nology licensing agreement with Tetra Technologies, which is a large oil service company that has an emerging focus on new energy. We also collaborate with our mining industry clients, which are really looking to develop various mining projects with our newest generation of technology.
CMJ: Can you briefly explain the separation technology and how it works?
ZS: KMX is solving three of the biggest environmental chal lenges with its proprietary technology: water, lithium, and critical minerals. We have a powerful crosscutting technol ogy that facilitates a separation of pure water, minerals, and other valuable constituents from brine and waste streams at low temperature and pressure. This technology has a broad set of applications across various industries and regions, spe cifically for industries that have a complicated waste stream but also need a high-quality water as an input, e.g., the mining industry. While the lithium, mining, and oil and gas industries represent obvious market opportunities for us, several other
industries, such as chip manufacturing, industrial manufac turing, inland desalination, and pharmaceuticals are also par ticularly attractive for our technology.
The process starts by feedwater entering the module and then it flows up through center core. When feedwater reaches top of module, it is distributed and flows downward through the fibers to the concentrate outlet, and then it is recircu lated in the same manner. The hydrophobic membrane acts as a barrier to the liquid and only vapor can pass through the membrane. Then, a vacuum is applied on the shell side (out side of the membrane). The combination of vacuum depth and heat creates phase transition from water to vapor on the membrane surface. Finally, water vapor passes through the membrane, is released from the modules, and it is condensed downstream.
ZS: Rare Earths and other critical minerals in waste present significant opportunity. Separation from tailings or waste ponds is estimated to represent 80% cost savings versus mining those critical minerals. For lithium production, our technology enables mining companies to maximize lithium concentration while also maximizing water recovery. The lithium market is our core focus currently, while Rare Earths represent a growth opportunity that we are not yet focused on.
There are three steps in recovering battery grade lithium from brine:
The first step is to extract the lithium, which is found in low concentrations alongside other salts and minerals like sodium chloride and magnesium, which need to be separated out. Today, that is done in evaporating ponds in South America; however, direct lithium extraction is an emerging technology which is an alternative to evaporating the water.
Once that step is done, lithium is still in very low concentra tions, and it needs to be concentrated up to a point where it can be converted from its natural state, which is lithium chlo ride, to battery grade lithium, which is lithium hydroxide or lithium carbonate. That is what we do; we concentrate the lithium chloride. We do this while achieving maximum high quality water recovery. And finally, step three is refining the lithium chloride to battery-grade lithium (lithium hydroxide or lithium carbonate).
CMJ: So, KMX’s separation technology only comes into that process at the second step, is that correct?
ZS: Yes. Step one: extract. Step two: concentrate, which is what we do. Step three: refining. We are a complimentary technol ogy to direct lithium extraction and to the refining processes. We are currently working with several mining companies that are using direct lithium extraction processes.
Importantly, a major criticism of the direct lithium extraction technology is that it utilizes a lot of water as part of the washing process. While it does not evaporate the water, like the evap oration ponds, it still needs a lot of fresh water. As part of our lithium concentration process, we recover water as part of the process. It is synergistic for a mining company to pair their
Far left: Critical minerals recovery process
Water recovery process.
direct extraction technology with our technology to maximize project economics, sustainability, and water recovery. We are trying to reach zero waste of water by recycling the water back into the process.
CMJ: KMX recently partnered with CanmetMINING; can you talk to us about this agreement and what you are hoping to achieve by this partnership?
ZS: We are hoping to maximize sustainable and economical lithium production in North America. KMX will be using our proprietary membrane distillation technology in conjunction with CanmetMINING’s expertise in water treatment to opti mize the concentration of lithium while maximizing water recovery of the highest quality.
We are very excited to work with CanmetMINING of NRCan through a task-shared agreement, as part of the Federal Research and Development component of the Canadian gov ernment’s $47.7 million Critical Minerals Research, Develop ment, and Demonstration Program announced under Budget 2021. We will be using the funding as CanmetMINING’s lith ium concentration technology partner to optimize the threestep process in bringing lithium from its natural state to battery grade lithium.
Natural Resources Canada is looking for the best available technologies and processes to optimize that process in the most economical and sustainable manner. We are extraordi narily proud that they have chosen KMX’s technology for the lithium concentration part of the process.
CMJ: Do you think your technology will play an important role in reducing the cost of lithium production to help attract more investments in the North American battery manufacturing sector?
ZS: North America has significant lithium resources read ily available to be extracted in a sustainable and economi cal manner. KMX’s work with the Canadian government will help ensure the coming North American lithium supply chain reshoring build-out is done with the highest environmental considerations. This partnership will highlight and optimize the steps that most efficiently, economically, and sustainably bring resources to the market for mining companies.
This will encourage more mining companies to develop lith ium resources in North America and will drive down the cost of production. It will also enhance the environmental and eco
logical considerations and the whole ESG component of the mining process, which is such a focus for investors, industry, and governments.
ZS: Building on our existing partnerships and execution for our existing customers is our focus for the immediate future. First, we have several exciting partnerships, and we are build ing on our recent licensing agreement with Tetra Technolo gies. We are excited about what is next in the global oil and gas markets, particularly as it relates to critical minerals that are found in mineral-rich produced water, which is a by-product of oil and gas production.
Second, we are also excited about our demonstrations and upcoming commercial development with our existing custom ers. We have two publicly announced LOIs with leading lith ium mining companies. The first is with CleanTech Lithium, an exploration and development company, advancing the next generation of sustainable lithium projects in Chile. Based in the U.K., CleanTech Lithium is a leading lithium project devel oper that harnesses solar power and advanced technologies to sustainably source and produce commercial scale lithium, with an initial focus on Chile. We are honoured to be the lith ium concentration partner of CleanTech Lithium, as they look to maximize lithium production efficiency and minimize its environmental footprint.
The second publicly announced letter of intent (LOI) that we have is with Cornish Lithium, which is a highly innovative private British mineral exploration company focused on the responsible extraction of lithium and other battery metals in the historically significant mining district of Cornwall, U.K.
Finally, I believe we have the leading membrane distillation laboratory in the world in Mississauga, Ont. KMX Technolo gies recently hosted a technology tour and opening ceremony of this new laboratory. The team was honoured to host govern ment officials and management from Sumitomo Electric Indus tries Ltd., KMX’s strategic partner of core elements. Our lab is led by our distinguished technical team comprised of leaders in this technology. Dr. Matt Narrol, senior research scientist, demonstrated KMX’s lab scale vacuum membrane distillation unit at the event. Dr. Sean Ghayeni, head of technology, gave an overview of KMX’s proprietary Generation III membrane bundle, manufactured by Sumitomo Electric. Mostafa Nosraty, P. Eng. (KMX’s technical sales manager) also presented a com mercial scale system rendering, currently planned for a lead ing lithium miner. CMJ
One of the biggest issues in mining is air pollution from both underground and above ground operations. During the mining process, numerous harmful aero sols are generated, such as quartz, silica, arsenic, diesel, and particulate matter.
Permissible exposure limits, which deter mine how much aerosol can be inhaled without adverse health effects, have been established. Aerosol size is the most important characteristic for health risk classification, as size determines where the particle is deposited in the lungs. Luckily, there are several technologies and automated systems that continuously monitor and provide real-time air qual ity data, so any issues can be immediately remedied.
One large air quality monitoring pro gram in Yellowknife at Giant mine pro vides information that protects miners, residents, and the environment. Giant mine is a former gold mine that stopped operating in 2004. The site is currently running a sitewide remediation pro gramme removing arsenic trioxide
PM refers to particulate matter. PM10 has a diameter of 10 microns or less, while PM2.5 is 2.5 microns or less and is nearly invisible.
caused by previous mining and asbestos materials in site buildings.
Continuous particulate matter moni tors are installed on the perimeter of the mine site to evaluate dust levels and com position. A second network, the activi ty-specific network, installs monitors at specific on-site work areas.
These stations measure airborne con taminants including arsenic, trioxide dust, asbestos, antimony, iron, lead, and nickel. They also measure airborne dust, including total suspended particulate (TSP), particulate matter 10 (PM10), and particulate matter 2.5 (PM2.5).
Real-time monitoring data is provided to construction managers so that workers and residents are not exposed to unac ceptable levels of contaminants and effec tive emission control measures can be implemented. If any air monitor detects an unusual spike in airborne dust levels, an alarm goes off, alerting site workers.
Total suspended particulate or TSP are particles in airborne dust which are 100 microns or less in diameter.
TSP indicates overall air quality and includes vehicle emissions, road dust, wood smoke, and pollen.
TSP also includes particulate matter. Larger particles are not considered a health risk as our body removes them. Smaller particles 10 microns or less (PM10) can be breathed deep into the throat and lungs. These are called “respirable dust”. Respirable dust can adversely affect human health, causing reduced heart or lung function. Particles 10 micrometers in diameter and below can reach the throat and lungs when inhaled.
When levels exceed Health Canada guidelines, which are 159 µg/m3 for PM10 or 333 µg/m3 for TPS over a 15-minute period, workers may water the affected area to reduce dust, shut the site down, or implement an emergency response plan.
Mine operators strive daily to keep their employees safe and complying with health regulations. Continuously moni toring the aerosols and dust emitting
from mines ensures compliance with Health Canada guidelines and keeps workers and local residents safe.
Instruments which monitor air quality can be installed both underground and above ground around the site perimeter, ensuring there are no dangerous levels of particulate matter within the mine or outside.
Ventilation in a mine provides ade quate airflow, diluting contaminants and ensuring air quality is safe to breathe. An automated system monitors the airflow throughout the mine and provides re al-time data. Signals from sensors like the flow meter or gas meter are analog and must be converted into a digital signal and sent to a server so that the informa tion can be accessed. Sensor data is com municated with fans, louvers, and other ventilation components. Using the data, the system’s fans and louvers can be adjusted to change the air flow. Approximately 50% of energy consumed by mining operations is used by ventila tion systems. An automated mine ventila tion system ensures a safe and cost-effi cient way of controlling the supply of fresh air underground. Optimizing the ventilation system lowers workers expo sure to noxious gases and reduces their
risk of injury. Monitoring gas concentra tions is also vital for workers safety.
Pressure is another important parame ter to monitor. Air naturally flows from an area of high pressure to an area of low pressure. Actively monitoring pressure throughout the ventilation automation system provides feedback on the air flow.
Products include airflow monitors, toxic gas detectors, temperature, pressure and humidity level sensors, and complete mine air quality stations (MAQS).
Advanced technology which measures particulates including aerosols and dust within a designated area includes gravi metric sampling, light scattering, beta attenuation, and TEOM (tapered element oscillating microbalance).
Mining sensors offer a complete pic ture of the mining site and surrounding environment and can be placed above and below ground.
Real-time, accurate coal mine dust mea surements are critical for providing data to the miner to minimize their exposure to coal dust. Personal dust monitors help ensure the respirable dust exposure does not exceed regulatory limits, which helps prevent black lung disease and other lung
diseases. Dust monitors utilize highly sen sitive light-scattering photometer (nephe lometer) technology and provide continu ous measurements of airborne particle concentrations. Portable, remote, and handheld air particle counters are de signed for routine environmental moni toring, and air filtration troubleshooting.
Automated air quality monitoring sys tems can measure air quality, low and high levels of criteria pollutants, as well as other gases and toxins, and helps ensure ambient air quality complies with local environmental regulations. The MAQS Mine air quality station is an affordable underground mine ventilation monitor ing station. MAQS monitors working envi ronments, integrates and communicates with remote devices, and automates the ventilation process. Its instrumentation functions with existing software and com munication infrastructure.
Several instrumentation and communi cation platforms are available for hosting SCADA (supervisory control and data acquisition) energy management systems (EMS), ventilation vimulation or ventila tion on demand (VOD) software. CMJ
Catherine Hercus is a freelance technical writer.
Highvec Canada Inc. provides a unique cleaning system for power distribution components. Our cleaning process cuts costs by eliminating expensive repairs, minimizing down-time, improving safety, and is environmentally friendly.
Launched in 1990, our crew members have years of experience, perfecting our cleaning process to serve a variety of industries, each with their own electrical contamination problems.
Underground Mining is possibly the worst environment for high voltage power distribution. In this environment, there are three major factors to take into account: High contamination from the dusty day-to-day workings and equipment diesel exhaust, high moisture content from the ground water and ventilation system, and damaged electrical components from concussion caused by long-hole blasting.
The contamination settles on all the electrical components inside the switchgear, which lowers the insulation values. Compounded by the moisture being trapped in the contaminant, this lowers the insulating values even more, increasing the electrical stress to the point of eventual flashover.
Prior to cleaning, Highvec inspects your switchgear and electrical equipment with infrared and ultraviolet cameras, looking for any hot spots, bad connections or thermal anomalies. Following this non-invasive inspection, we perform our environmentally-friendly cleaning process. Most of our work is done under live conditions, meaning you won’t need to power-down your
processes.
We’ve found that using ground corn cob at the proper grind has enormous abilities to clean fragile electrical components, attract and pick up contamination, and most of all, absorb moisture. We investigated the use of CO2/dry ice blast cleaning and found them less effective.
The dry ice creates moisture due to the change in temperature that it produces. O2/carbon dioxide does not contain moisture but the air around it does. With the addition of moisture, the situation becomes dangerous. And unlike with dry ice, the Highvec method can be performed while the equipment is energized. Also, CO2 displaces oxygen so cleaning switchgear underground without proper ventilation can create serious health issues and should never be allowed.
Xstrata Copper invited Highvec to an experiment to find out exactly which method is the best. There were
contractors on site for dry ice blasting, high pressure water blasting, and Highvec, for corn blast dry cleaning. The Highvec dry cleaning system proved to be the best.
One of our customers tried dry ice to clean some 15kv switchgear while de-energized. They hand-wiped all the insulators prior to energizing and it flashed over when energized because of condensation.
In conclusion, we believe the Highvec dry cleaning method is the most effective way to maintain the integrity of highvoltage power distribution components. It will prevent unscheduled outages and downtime, improve workplace safety, and is environmentally friendly. The dollar value pay-back is tenfold for our customers. n
For more information on how Highvec Canada Inc. can recharge your operations, please visit www.highvec.com or email Brianna@highvec.com.
Where are the engineers? My main goal of creating the Hub (Historical Canadian mines data hub and visu alization centre: https://www.cim.org/ the-hub/) was to continue taking the geo logical information that kickstarted it to build on the engineering information. But I have hit a roadblock. The hub has been in the public domain for several months, and the only updated mines information received to date was from a geologist. The new mine about to be added has been in operation for 36 years in Ontario, and it was not even in the database. I anxiously await the time that mining industry engi neers will become prolific about writing about their extraction methods as the users do in the Minecraft world.
In mining, the geologists take pride in transposing deposits into block models and those are published widely. In Minecraft, blocks are also the basic unit. Like mining engineers build mines, play ers in Minecraft construct creations with blocks found in the game’s worlds for commodities like iron, diamonds, gold, and coal. Gamers in Minecraft are more like the geologists in that many share their builds on platforms for others to download and enjoy. The procedural generation that makes every player’s Minecraft world unique is fantastic, but within the simplified simulation of the
game are engineering principles that are widely documented.
Like in real-world mining, Minecraft is a game constructed out of predictable systems that must be used to mine ores for crafting useful items for building. Water, lava, gravel, and more are all potentially dangerous hazards that a player is likely to encounter on their quest for useful blocks for crafting (mak ing items) or building (making struc tures). There are safety rules that must be followed. For example, users need to remember to never go straight down, or they may fall into lava. This can be equated to shaft sinking which is consid ered a specialized type of engineering since the hazards are higher. Digging at an angle is preferred, for game players to see what is in advance. In mining, ramps are at angles designed with grades for equipment travel. If a user encounters water in real life or in Minecraft, it must
be blocked off to avoid a flood. Gravel is one of the few blocks in Minecraft that is affected by gravity, meaning it could col lapse a mine the user creates, making digging directly above a risky endeavor. Small block sizes or unconsolidated materials in mining impose potential hazards too. Adequate lighting is a prior ity because there are monsters in the game that spawn in dark places. Based on the location of Canadian mines, light ing is important as more than one bear has gotten into a headframe. Safety is important to Minecrafters, just as it is to real-world miners.
The proof of the lack of input by engi neers is shown in the missing data of the Hub. There are only eight of over 14,000 entries that show a shaft depth. The min ing chain exists because of mines, and our industry has been content to over look sharing the critical first step in an easily accessible way, the extraction of the materials and easy access to where and how that is done. Minecraft, being the best-selling game of all time, clearly shows by the roughly 238,000,000 copies sold that if the mining industry could break the barrier between what engi neers do in real life, the public may per ceive what we could provide regarding the excavation of our mines as interest
ing information too.
Since 2015, I have been asking her engineering students to do research on a Canadian mine. I provide a checklist of basic information about the mines, and they mostly use the internet to find all that they can. And surprise, they often cannot find anything about equipment, mining method, and sometimes even the most basic information like depth of the shaft or open pit. There is no consistent information in annual reports except to publish on the financial statements and the social benefits of mining. National Instrument 43-101 documents are great but when reading, it is not always clear as to whether the engineering plan was followed. Only a couple of pages may be provided regarding the engineering of the mine.
Kudos to the Canadian Mining Journal (CMJ) for having published the engineer ing sourcebooks. Look at the tattered cover in the photo, worn out from all the use by students. Our 2007 and 2010 copy covers are now gone from wear. CMJ pub lished the things that matter to engineering students like type of deposit descriptions, mining costs, mining meth ods, drift-ramp-raise projects, existing shafts, stoping details, backfill methods, ground support, haulage methods and systems, crush ers, hoists, drainage pumps, main ventilation fans, drilling and blasting equipment, processing cir cuits, dewatering methods, water supply, tailings disposal, power sources, person nel requirements, and so on. My overar ching goal would be that this information is available for all current dots on the map. Maybe that would intrigue elemen tary and high school students to connect the dots, to realize that what they are doing in Minecraft is a gamified simula tion of a real engineering job. They may ask questions about equipment and dig ging methods and the different types of rock. I am also going to add interesting technical books like those of Keith Haddock of western Canada who has written several books about mining equipment.
Should investors be concerned? Dalhousie University has suspended their Mineral Resource Engineering pro gram, and it will close effective 2023-24.
Which program is next? How are we going to mine the rock in real life if there are no engineering students? When there is no one left to design the mines, where are they going to go to find the popular mining methods? Why are those methods popular? Have mining methods changed over time in this country? Does the improved safety sta tistics of mining have anything to do with mining methods? And even better yet, who is going to teach the next generation of students? I have been at the University of Saskatchewan for 10 years and there has only been one student in mineral processing that has done a PhD. And he is mostly self-funded because he could not find a mining company to support him.
How about teaching the public how digging is really done. What are the real benefits? How are deep holes dug in real rock. How wide do tunnels need to be? How big can rooms be before they col lapse? What drives the selection between electrical and diesel equipment? How are mine services like air, electricity, and water brought into a mine. There are so many interesting jobs in the mining industry.
As a final point about people, Minecraft is mining as it should be, demonstrating
another strength of the game. In an offi cially licensed comic, the cast of charac ters are diverse, featuring various gen ders and nationalities. Statistics in the real mining world show that there are only 17% females which is one example that highlights that the mining industry is lacking in this area. Perhaps it is time for our engineering community to take pride in what we do, and for corpora tions to require their engineers to pres ent what they do. All it takes to start is to fill in the basic columns of the database and that can be done by emailing mines database@cim.org for a Word document to complete. Then the really engaged mining companies can take the time to write more detailed documents describ ing their mines excavation and process ing methods as each mine can have a pdf attached. The more photos the better. Let us make real Canadian mining informa tion accessible to everyone by removing the publishing roadblock that currently exists regarding engineering details of our operations.
CMJ
Donna Beneteau, PEng, MASc is an assistant professor at the Department of Civil, Geological, and Environmental Engineering, University of Saskatchewan. The author acknowledges the valuable contributions of Patrick Ecobichon to this article.
Cover of the 2002 Mining Sourcebook.
CREDIT: D. BENETEAU
Statistics in the real mining world show that there are only 17% females which is one example that highlights that the mining industry is lacking in this area.
The 2015 Paris Agreement, negotiated by 169 parties at the U.N. Climate Change Conference, set the ambitious goal of keeping the rise in mean global temperatures to below 2°C. Seven years later, the need to take urgent and more intensive action to reach these goals is broadly recognized. One of the major near-term drivers to help achieve this in the transport and power sectors is the battery value chain. The International Energy Agency (IEA)’s World Energy Outlook 2021 argues that “batteries play a central part in the new energy economy.”
In fact, batteries could enable 30% of the required reductions in carbon emissions in the transport and power sectors, create 10 million sustainable jobs, and provide access to electricity for 600 million people that currently lack access. While this pres ents an incredible opportunity for the mining and metals indus try, with metals like cobalt and copper forming key compo nents of the lithium-ion batteries in EVs, we must ensure the sustainability of the sector does not suffer as a result.
The production of a rechargeable EV battery can pose signif icant social and environmental risks. At every stage of the pro cess, from the mine to the electric vehicle, issues such as child labour, unsafe working conditions, and carbon dioxide (CO2) emissions can significantly impact the overall sustainability of the product.
Mitigating these risks is the primary objective of the Global Battery Alliance (GBA), the largest multi-stakeholder coalition of its kind, which brings together leading international orga nizations, NGOs, industry actors, academics, and governments to drive systemic change along the entire value chain. It now comprises around 110 members, including the OECD, UNICEF, Eurasian Resources Group, Tesla, and BASF, who are commit ted to creating a sustainable battery value chain by 2030.
To achieve this, the GBA is working on several key initia tives: the battery passport, the critical minerals advisory group, and ongoing projects on energy access, lead-acid bat teries, and circularity.
One of the major difficulties with reducing the ESG impact of the battery supply chain is a lack of a standardized global reporting framework that covers the entire chain. Without establishing harmonized principles for digital traceability, access, and transparency, we cannot hold companies and nations accountable for their actions.
The GBA’s battery passport is a flagship initiative that aims to create a digital twin of the physical battery, giving consum ers technical data about the battery as well as applicable ESG
and lifecycle requirements, based on a comprehensive defini tion of a sustainable battery. Its role in underpinning a responsible battery value chain has been endorsed during global policy discussions, including the 2021 G7 leaders’ meet ing, by the Canadian and U.S. administrations and in the intro duction to the draft E.U. battery regulation.
By virtue of providing the critical raw materials for batteries, minerals such as cobalt, nickel, lithium, and graphite are essential to the green transition. The World Economic Forum projects that the production of materials like graphite, lith ium, and cobalt could increase by almost 500% by 2050 to meet rising demand for clean energy technologies. However, supplying these materials presents both challenges and oppor tunities.
In response to this, the GBA is launching the critical miner als advisory group (CMAG) in 2022, adopting a members-led and non-prescriptive approach to issue mapping. The CMAG will build on the success of the cobalt action partnership, a multi-stakeholder initiative convened under the GBA in 202021, dedicated to eliminating child and forced labour from the cobalt value chain. By working with members across the value chain, the CMAG will ensure that critical minerals are sourced, processed, transported, manufactured, and recycled in a responsible and just manner.
Batteries are crucial to helping the nearly 550 million people in Africa who lack access to electricity. As a source of clean and reliable energy, batteries can significantly support Africa’s energy access goals and as part of microgrids and off-grid solutions, especially in sub-Saharan Africa.
Alongside this, a GBA whitepaper on recycling found that access to information on battery usage and end-of-life metrics could lower the costs of repurposed batteries by around 20%, reduce hazardous waste accumulation, and create numerous job opportunities. The GBA is also working to maximize batteries’ end-use potential by promoting circular design improvements and ensuring stronger market incentives toward recycling.
Throughout its entire lifecycle – from the raw material to production processes, use, and recycling – the battery value chain has the potential for both harm and good. It cannot only support the fight against climate change, but also create new safe jobs, add economic value, and safeguard human rights in line with the U.N. sustainable development goals. With battery demand set to explode over the coming decade, businesses, governments, and NGOs must urgently renew their efforts to ensure the value chain is scaled up in a responsible, circular, and sustainable manner. CMJ
Benedikt Sobotka is the CEO of Eurasian Resources Group and co-chair of the Global Battery Alliance.
First Phosphate announced that Peter Kent has been appointed to lead the company as president. He brings more than four decades of experience as an international broadcast journalist. He was elected as the MP for Thornhill, Ont., in the 2008 federal election, and he served until 2021. As an MP, Kent served as Minister of State for the Americas (2008-11), and as Minister of the Environment (2011-13). In the environment portfolio, he oversaw changes to the assessment process for mining.
Aaron Puna is joining Newmont as EVP and chief technology officer. He most recently served as CEO of Anglo American’s copper business in Chile. In that country, Puna oversaw all company activities, including three operations and a joint venture, a workforce of over 16,500 and external stakeholder engagement. He led the implementation of Anglo American’s autonomous haulage fleet at high altitude operations and has driven the country’s copper production to over 600,000 tonnes per year.
Sigma Lithium appointed Dana Perlman as an independent director. Her expertise includes over 20 years in strategy, finance, investment banking, business development, acquisitions, risk management and investor communications. Perlman most recently served as chief strategy officer and treasurer at PVH Corp. Before that she held several positions at Barclays Capital after gaining banking experience with Lehman Brothers and Credit Suisse First Boston.
Director
+1 416.854.8468
erik.buckland@lincolnstrategic.com
www.lincolnstrategic.com
» A.I.S. Resources named Martyn Element president and CEO.
» Mike Struthers is the new CEO of Altaley Mining
» Josh Carron joined American Pacific Mining as VP exploration.
» Christopher Drysdale replaced Daniel Whittaker as CEO of Antler Gold
» Appia Rare Earths and Uranium appointed Irvine Annesley as VP exploration.
» Archer Exploration appointed Tom Meyer as president and CEO.
» Gary Lobb joined Argo Gold as VP finance and CFO.
» The Association for Mineral Exploration appointed Jonathan Buchanan as VP policy and advocacy.
» Auxico Resources Canada named Frederick Kozak as its president and CEO.
» Buscar Company appointed Jose Kreidler as president and Daniel McGill as COO.
» C2C Gold named Doris Tam as CFO.
» Caprock Mining named Amy Stephenson as the company’s new CFO.
» Paul Wright replaced Scott Perry as president and CEO of Centerra Gold
» Decklar Resources appointed Oluwasanmi Famuyide as CEO.
» Dundee Precious Metals EVP and CFO Hume Kyle will retire at the end of 2022.
» Jim Megann took over the interim CEO role at E-Tech Resources, replacing Daniel Whittaker
» Charlie Greig assumed the role of CEO at Evergold.
» GFG Resources appointed Natalie Pietrzak-Renaud as VP exploration.
» Grounded Lithium appointed Lawrence Fisher as VP, land and regulatory.
» Guanajuato Silver Company appointed Reynaldo Rivera as VP exploration.
» Current VP finance Maarten Theunissen will serve as interim CFO at Iamgold
» Ivanhoe Mines appointed Mark Farren as COO and Steve Amos as EVP projects.
» Lion One Metals appointed Jeffrey Edelen as its new VP corporate development.
» David King joined Magna Mining as SVP technical services.
» Mark Rodgers will transition to the role of SVP South America. Bernard Wessels will become SVP North America role at Newmont
» Guillaume Jacq is the new CFO of Northern Graphite
» Northern Lights Resources’ chief geologist Gary Artmont passed away.
» Sebastien Ah Fat resigned as VP exploration of Pacific Bay Minerals.
» Platinum Group Metals announced the appointment of Greg Blair as CFO.
» Nouveau Monde Graphite nominated Anoop Singh as VP mining projects; Josée Gagnon as VP legal affairs and corporate secretary; and Kelly LeBlanc as manager Indigenous relations.
» Rahul Paul stepped down as president and CEO of Radisson Mining Resources
» Nicholas Konkin replaced Tom Griffis as the president of Royal Coal
» Royal Road Minerals appointed Hugh Devlin as executive director sustainability.
» Paolo Lostritto replaced Cesar Gonzalez as CEO of Sailfish Royalty
» Tao Zhang resigned as VP sales of SouthGobi Resources
» Adventus Mining appointed Stephen Williams, Leif Nilsson and David Schettini to its board.
» Mike Struthers joined the board of Altaley Mining
» Anfield Energy appointed Kenneth Mushinski as non-executive chair.
» Daniel Whittaker will assume the position of executive chair at Antler Gold
» Archer Exploration named Tom Meyer as director.
» Arras Minerals appointed Christian Milau to its board.
» Frederick Kozak and Melissa Sanderson joined the board of Auxico Resources Canada
» Glen Zinn stepped down as a director of Bell Copper to be replaced by Eugene Schmidt
» Arif Merali was appointed to the board of Bessor Minerals
» Jose Kreidler became a board member at Buscar Company
» ColdBlock Technologies appointed Russ Calow to its board.
» Michael Waring and Matthew Rees replaced Gerald Riverin and Morgan Quinn on the board of Copper Road Resources
» Endeavour Mining appointed Sakhila Mirza as an independent director.
» ESGold welcomed Christopher Stewart to its board of directors.
» Charlie Greig joined the board of Evergold
» Ron Hochstein replaced Phil Brumit on the board of Filo Mining
» Jill Donaldson and Peter Hairsine joined the board of Fireweed Metals
» Foremost Lithium Resource & Technology welcomed Jason Barnard to the company’s board.
» John Herold, founder of Herold Supply as well as a founding board member of the Sudbury Area Mining Supply and Service Association, passed away.
» Mawson Gold appointed John Jentz as an independent director.
» Cyril Amadi and Daye Kaba joined Myriad Metals’ board of directors.
» Omai Gold Mines appointed John Jentz as an independent director.
» John Chisholm resigned from the board of Premium Nickel Resources
» Tom Griffis and Elia Crespo resigned as directors of Royal Coal, making way for Nicholas Konkin
» Royal Road Minerals announced Guy Wallis as its newest board addition.
» Rusoro Mining appointed Anthony Beruschi as a director.
» Paolo Lostritto became a director of Sailfish Royalty
» Anthony Taylor resigned as a director of Transforma Resources.
» Trevali Mining directors Richard Williams, Jill Gardiner and Jeane Hull resigned.
» West Red Lake Gold Mines appointed Susan Neale, Ryan Weymark and Robert van Egmond as independent directors.
SGS Canada 9 www.sgs.com Thermo-Tech Inc. 21 www.mag-heat.com Titan Environmental 17 www.titanenviro.com Westpro Machinery 46 www.westpromachinery.com