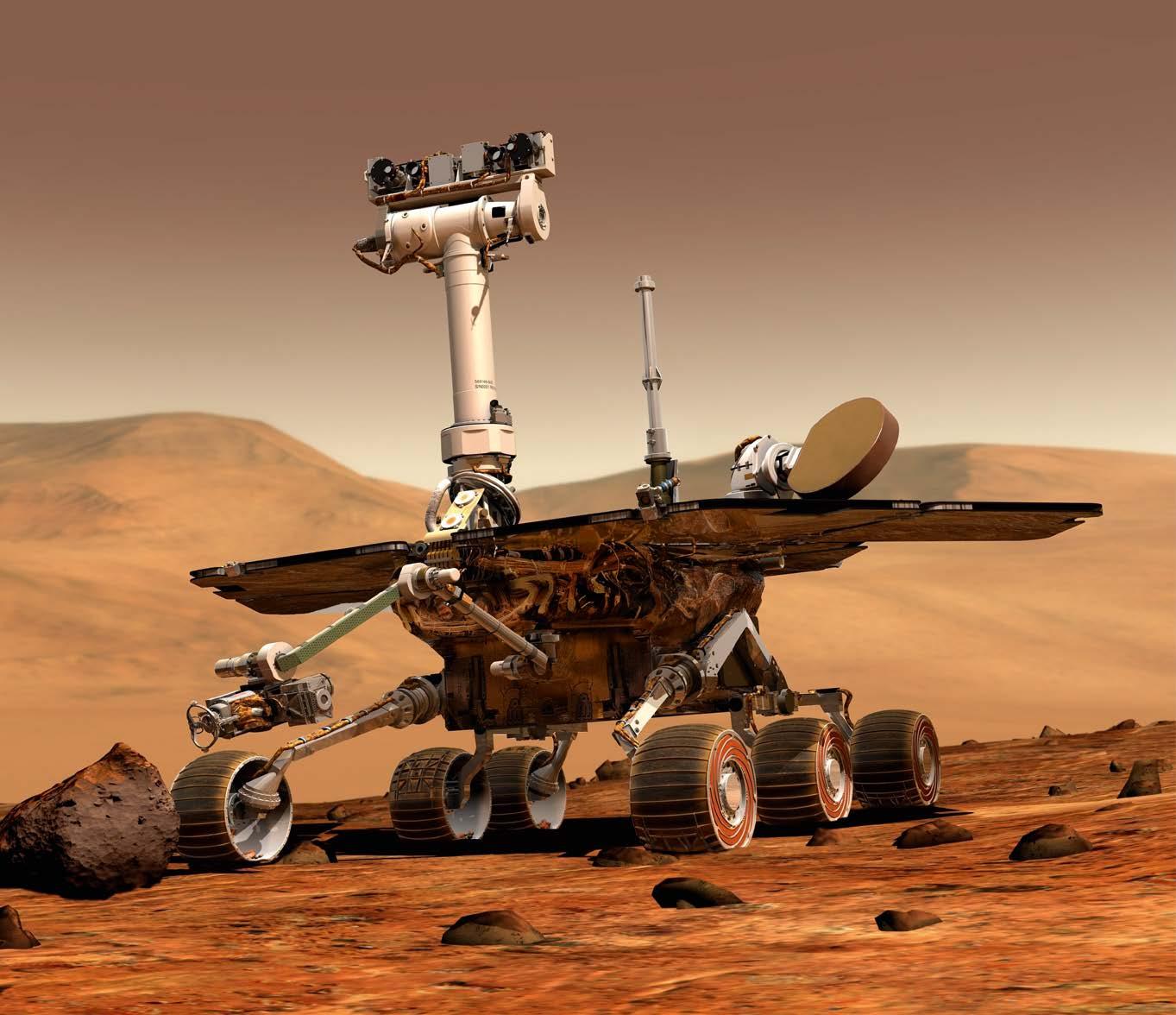
6 minute read
How to measure a planet
Angelo Hulshout has the ambition to bring the benefi ts of production agility to the market and set up a new business around that. His journey is taking a small detour.
Angelo Hulshout
Advertisement
In 1998, a not so obscure metal band from ’s-Hertogenbosch released an album called “How to measure a planet.” e band was called e Gathering, and this album was a break away from their previous albums, which were lled with rather bombastic heavy metal. Daring, but they did it – and they were successful.
With a startup, it’s no di erent. At some point, you may have to deviate from your original plan to become successful. I remember the story of an ex-colleague at Philips who started his own company in compiler optimization. He ended up doing completely di erent things, in the area of static code analysis. e core technology he used stayed the same, but he wound up in a completely di erent market.
You don’t make a switch like this from one day to the next. It requires a bit, or a lot, of trial and error to get there. is is what we’re facing with Shinchoku right now, shortly after we started and even before the rst version of our website is live.
Feet on the ground
My original idea is still alive: help small and medium-sized manufacturers optimize their production processes in a data-driven manner. Or in order words, make them part of Smart Industry, Industry 4.0. However, we now know that for this market, the world looks a little bit di erent than all the fancy Industry 4.0 videos show. ere are very few robots, there’s still a lot of manual labor and although we live in the age of digitization, a lot of factories have very little production management software running. at isn’t necessarily a bad thing, but it does require us to de ne which steps we want to take to realize our original goal. We’re not by default going in to install an internet gateway, hook it up to the PLCs of all production machines and then feed the data acquired to a dashboard. at was a bit of a short-circuited version of our story anyway – you can’t just collect random data and be successful, so we’d have to analyze with the customer what data to collect before taking o . at analysis has put us with our feet rmly on the ground now: in most factories we’ve seen so far, there’s very little data to collect initially. We have to work with the customer, with the operators in the factory, to identify which parts of the process are candidates for improvement. is has to be done based on anecdotal information and experience because there’s only limited automation and reporting support. Once identi ed, we need to establish what can be done to (semi)automatically collect and arrange data before we can start working on our actual goal.
Small steps
At one factory, for example, about 60-70 percent of the production process turned out to be based on manual labor. Not only are the machines operated by humans, but the metal parts produced by those machines are also polished by hand. e problem in this factory is that nobody at any point during the production has an overview of how many parts for a certain order are being processed and where they are.
In a place like this, going from manual labor to full automation in one big bang is nothing more than a dream. e reality is that we have to take small steps. e rst step, in this case, could very well be installing wireless foot pedals with certain workstations, which the operators can simply press every time they nish working on a
single part. Combined with tracking the trays transporting the metal parts through the factory (using RFID or similar), that would help us get a better view of how many parts are produced and in which production stage they are. Obviously, this is lightyears away from just installing a few network cables and a gateway and collecting data that’s already there.
We discussed our experiences with both customers and automation specialists from our side of the industry. ey all con rm that some important steps need to be taken rst if we want Industry 4.0 to come within reach of the smaller production companies as well. Not everybody is as big as L’Oreal or Volkswagen, where millions can be spent each year to improve automation and human labor in production has been largely eliminated long ago.
Process analysis
In keeping with the song from e Gathering, we need to nd out how to measure a planet before we can actually go ahead and measure it. at’s what we’re doing now. Realizing our Industry 4.0 vision requires some big steps, the rst of which need to be taken in our market of small and medium- sized manufacturing companies.
So, almost from the start, Shinchoku will not only be a data analysis company, but it will also have a lot of work to do in process analysis and automation – almost literally to be able to generate its own data.
Angelo Hulshout is an experienced independent software craftsman and a member of the Brainport High Tech Software Cluster.
Edited by Nieke Roos
CHILDREN IN UTRECHT SEEK SUPPORTING TECH COMPANIES
If you think about technology regions, you might not immediately think of Utrecht. Utrecht is famous for its beautiful city center. It’s also the central railroad hub in the Netherlands, which is why many major events are organized in the Jaarbeurs. And... from now on, Utrecht has a real “Hall of Discoveries,” to inspire children and youngsters to pursue a future in tech!
The tech situation: alarming
Employers in the construction and technology industries suffer a major shortage of workers. For realizing the climate goals alone, an extra capacity of 70,000 people in the Netherlands is needed in the short term. While the city of Utrecht has high ambitions in this area, its technical education outflow is extremely low: in 2019, only 17(!) VMBO students (preparatory secondary vocational education) chose technology as their major.
The solution: Hall of Discoveries
In response to this situation, leading companies (including BAM, Heijmans and Eneco), together with the municipality of Utrecht, have built the “Hall of Discoveries” (De Ontdekhal). With the proven concept of “The Inventors” as the cornerstone, children can discover if they have affinity and talent for technology and innovation. On top of the Inventors programs and workshops in the Hall, all schools (primary and secondary education) in Utrecht are offered ‘adventure programs’ for appealing tech education at their school locations.
The challenge: your company’s support
The responsible foundation, TEC Utrecht, already has a great partner network. However, for a sustainable continuation of the Hall of Discoveries and expansion of the activities, many more partners are needed. Only with the help of tech companies themselves, enough children will be inspired to choose for a future in their business area. Is your company one of those? Send an email to info@ontdekhal.nl and discover how this great initiative for all children will be beneficial for you as well!
The Inventors programs are there to inspire youngsters for a future in design and technology. Projects are supported by tech companies such as ASML, Brainport Industries, DAF Trucks, Frencken Europe, Hager, High Tech Campus Eindhoven, NTS Group, Philips, Prodrive, Stam en De Koning and VDL Group, and by Bits&Chips as the media partner.
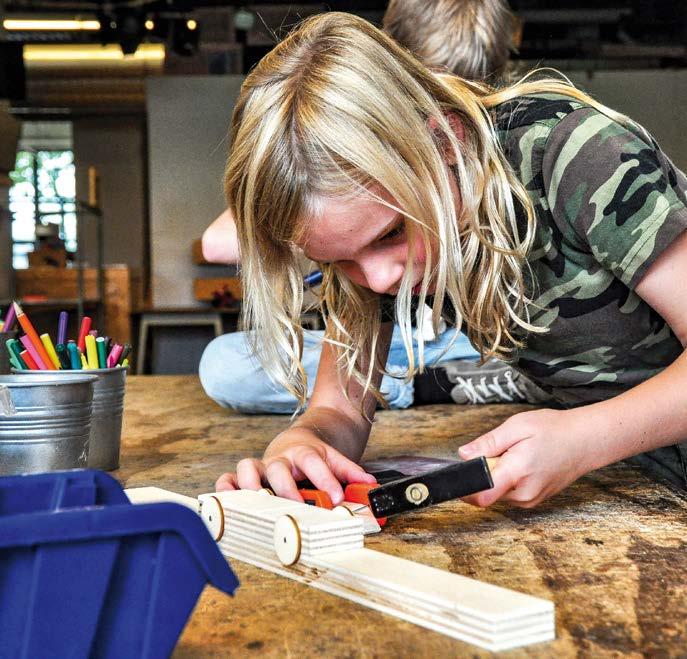

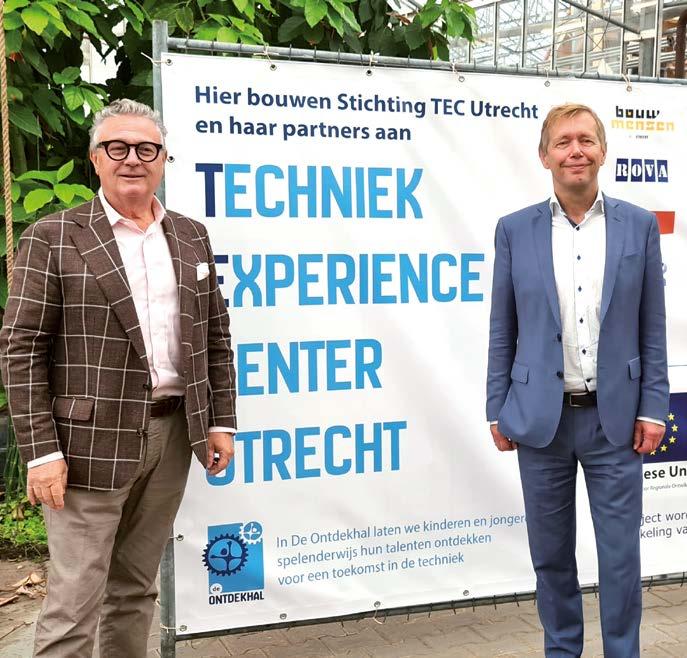