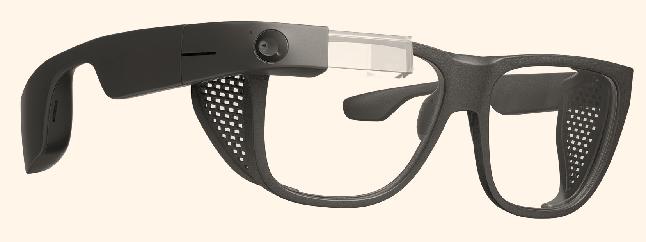
6 minute read
Envision sees clearer with Google Glass integration


Advertisement
After a year of discussions with Google, Yes!Delft startup Envision is ready to announce the integration of its AI-driven software for the visually impaired with the tech giant’s Google Glass solution. Now, the Hague-based company is looking to expand assistive technology to serve other impairments as well.
Collin Arocho
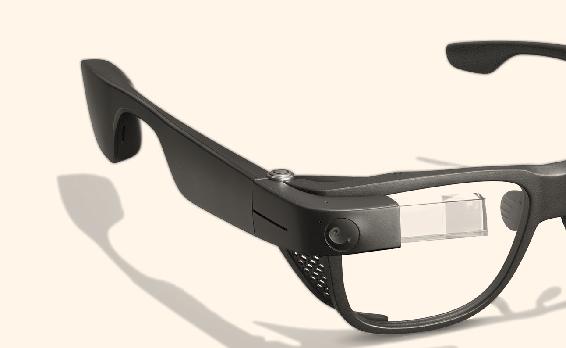
AI software company Envision’s assistive technology is now being supported on Google Glass, according to the Yes!Delft startup. Th e announcement comes roughly a year after the company started discussions with the tech giant to combine its AI solution with their smart glasses. Th e software, originally offered via the Envision app, was named the 2019 Best Accessiblity App by Google Play. Now, after a recent upgrade in hardware of the Google Glass Enterprise Edition 2, customers can preorder their Envisionenabled smart glasses.
Envision’s software utilizes in-house developed AI algorithms to extract diff erent kinds of information from images and surroundings and then speaks the images out loud to give its user a better understanding of the environment around them. Th e software was developed as a platform on Google Glass, which uses the same backend as the Android app. Depending on the function, the information can be processed onboard the glasses or online if needed. Th e glasses connect to a smartphone, via Bluetooth, to access the Envision app, which allows users to adjust settings and connect to the Internet via the phone.
Change of scope
Since last speaking with Bits&Chips, Envision has continued to develop and enhance its software solution, particularly its optical character recognition (OCR), which can read any type of text from any surface (ie food packaging, posters, display screens and handwritten text – to name a few) in addition to scene and facial recognition and object detection. Furthermore, the Haguebased startup has received some fi nancial support from EIT Headstart (50,000 euros) and MIT Haalbaarheid (20,000 euros) and has added two new members to its team.
With the news of this integration with Google Glass, Envision’s ongoing pilot proj
Credit: Google
ect with the municipality of Th e Hague has now expanded its scope to include smart glasses. Th e project, which started last year, was designed to help blind and visually impaired job-seekers in the city to increase their employment opportunities with the help of the Envision app. Th e project will now see the introduction of the Envisionenabled glasses to a select group of pilot participants, comprised of both employed and unemployed citizens. “Th e goal of the pilot is to determine the impact that the Envision app and glasses can have on the employment opportunities, workplace productivity and social integration among the visually impaired citizens,” describes Karthik Mahadevan, co-founder and CEO of Envision.
Product expansion
Going forward, Envision is looking to further develop its AI software to provide support for a broader audience and over additional platforms. “Th e way we see it, the Envision glasses are an addition to our off ering on a smartphone. In the long term, Envision aims to be a device-agnostic software that can function on any device with a camera,” explains Mahadevan. “Our next steps are to have a successful preorder while also determining supplier and distributor channel to scale our latest off ering. Next year, we also intend to extend our features to enable people with cognitive impairments like dyslexia and dementia.”
Han Schaminée is a product innovation consultant.
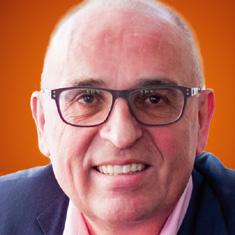
It’s all about cycle time and yield
Recently, I read in the newspaper 22,700 legal cases have been postponed because of capacity issues with judges and their staff. It reminded me of a discussion I had a few years ago. During a summer party, I had a chat with a judge who explained to me some of his challenges. At the time being involved with family-related conflicts, he mentioned a problem I was familiar with as an engineer: lead time. He told me that it took fourteen months on average to close a case in which one partner wanted to adjust the alimony.
Being trained in project management, Lean and QRM (Quick Response Manufacturing), I asked him two simple questions. Do you have one person in the organization responsible for the progress of the case? The answer was a resounding “no”. Then, I asked how much time it actually takes to resolve a case. His answer: about 32 hours. The rest of the time the case was sitting on the desk of some expert, waiting for his or her input.
I recognized the enormous opportunity to improve efficiency and suggested he should contact an expert in Lean and QRM I know. A few months later, I inquired whether any progress had been made. He replied there had been some consultations, but in the end, management decided there was no money available for a process consultant. You can imagine how I feel these days when I read about capacity problems at the Dutch courts.
Improving efficiency requires more than just a focus on cycle time, though. There are many examples where such a focus led to huge performance wins without raising customer satisfaction. One example I often encounter is when people diligently finish a task as fast as possible – even before they start a new one, but forget that real customer value is only created when the customer can use the feature and when all underly
ing tasks have been finished. Teams report impressive velocity figures, measured per task, but customers are unhappy, as they’re still waiting to use the full feature.
This way of working also leads to a higher risk of having to redo things, as the ultimate validation of a task is when the customer signs off on the entire feature. Studies show a positive correlation between cycle time and defect density. Reworking defects is avoidable waste. And late customer feedback results in even more waste.
A customer often doesn’t know in advance what he needs. This uncertainty is addressed by introducing buffers. Everybody knows time buffers, but few are aware that these buffers always fill up and don’t help. They create an illusion of certainty. The same holds for specifications: if there’s uncertainty about what’s required, customers will overspecify, suppliers will undercommit. The best way to overcome this is to implement short cycle times allowing for fast feedback and adaption.
I remember when I worked for an organization that had a huge annual meeting to plan next year’s activities. It was a terribly difficult, 3-day event. The CEO asked me how to improve and my answer shocked him: let’s do this every month! But it worked; we became far more efficient but also far more predictable: planning horizons became smaller and we needed fewer buffers to address uncertainty.
So, whenever you struggle to make a build or even product release once every quarter, try to do it every week. But also with the smaller increments, make sure to deliver full features that represent customer value and allow you to verify the quality. As I learned from an experienced manufacturing manager: it’s all about cycle time and yield! It’s far more effective than adding resources.
Back to our courts and their capacity problems. It’s easy to say that it’s all about cycle time and productivity, and that adding resources doesn’t help. But, of course, this is irrelevant when productivity is not the highest priority. No doubt, people in courts work very hard, but sometimes it takes something special to create a breakthrough. And that’s where leadership comes in.