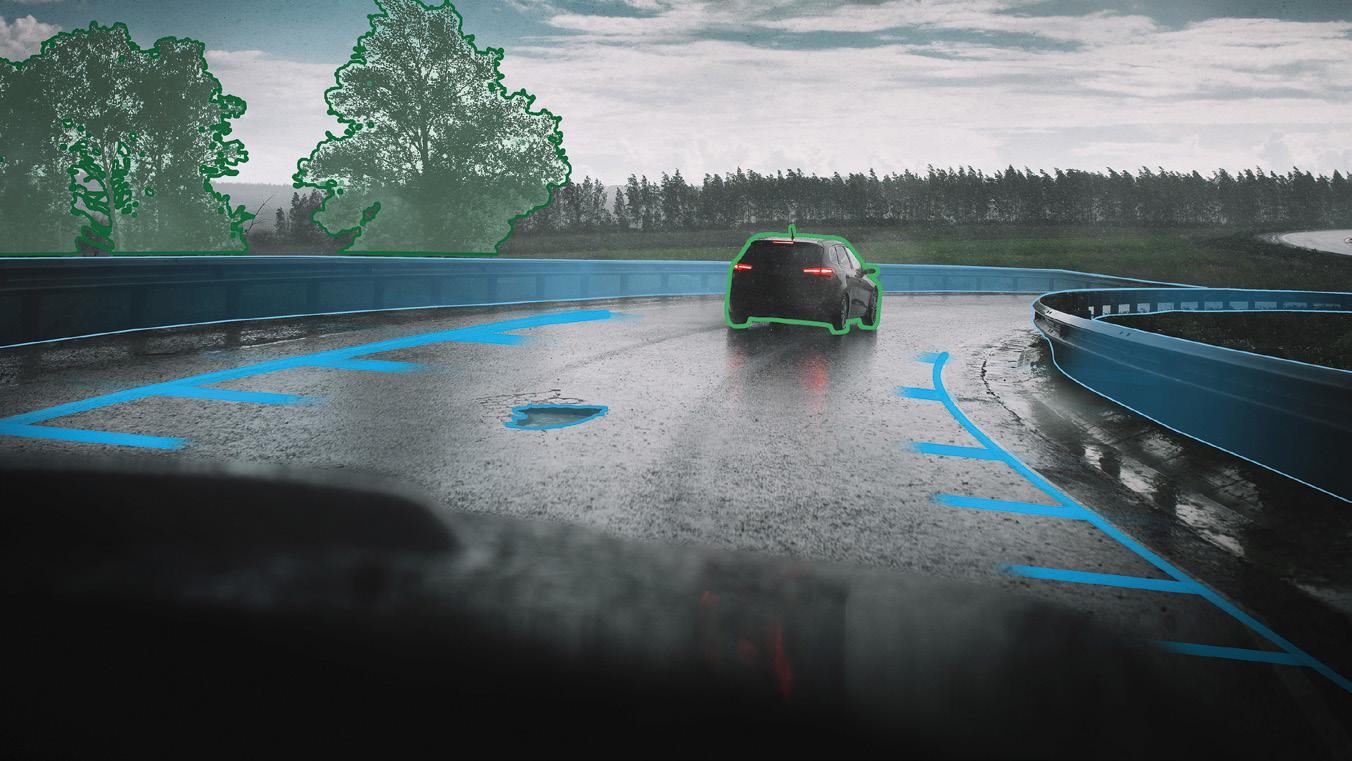
3 minute read
Thousands of beams light the way to the automotive big league
While most lidar companies focus on miniaturizing existing technologies, Belgium’s Xenomatix created a multi-beam system from scratch, with the automotive industry in mind. This culminated in the recent signing of a development agreement with Italian top-ten tier-1 company, Marelli.
Jessica Vermeer
Advertisement
Seeing Google’s self-driving vehicle in 2013, Xenomatix founders Johan Van den Bossche and Dirk Van Dyck knew this wasn’t the way to go. In their eyes, the sensor dome sitting on top of the car was unfit for mass production. “Designers are all-powerful in the automotive industry. Even when those Google cars were technologically sound, no one wants a giant sensor on their roof,” explains Filip Geuens, the current CEO of the Leuven-based company.
While competitors focused on miniaturizing existing technologies, Van den Bossche and Van Dyck decided to develop an alternative from scratch, with the specific needs of the automotive industry in mind: reliability, robustness, long lifespan – all for low cost. The result is a solid-state lidar module that’s small, consists of cheap components and easily integrates in a car. For sensing, Xenomatix has chosen multibeam technology, which has since been the company’s main differentiator.
The efforts are now starting to bear fruit. Recently, Xenomatix signed a technical and commercial development agreement with top-ten tier-1 automotive company, Marelli. The Leuven outfit is going to provide its solid-state lidar module to the Italian company’s Automotive Lighting division. According to Geuens, the deal didn’t originate spontaneously. “We’ve been working together for a while, visiting car manufacturers for example. That’s how they got to know and appreciate what we do.”
Lidar technology
The general principle behind lidar is sending out beams of light and measuring distance from the reflections. Usually, invisible light in the near-infrared spectrum is used. Essentially, distance can be measured in two ways: from the time difference between the light going out and the reflections coming in (direct time of flight, TOF) and from the phase shift between the outbound and inbound waves (indirect TOF). “Our approach is quite original,” states Geuens, without going into details. “It’s somewhere between the direct and indirect method.”
Most lidar systems only send out one laser beam, or a few at most, and combine this with a scanning mechanism to pick up the reflections that are used to digitize the surroundings. These scanning mechanisms, however, aren’t very robust and incur high costs, which makes them an unattractive option for automotive applications. Xenomatix’ Xenolidar system uses thousands of beams, rendering the scanning mechanism obsolete. “That effectively eliminates the weak spot of traditional lidar,” says Geuens. “We’re able to get high-res images with a much more compact module.”
At present, lidar is hard to find in mass-produced vehicles. Geuens: “No one has been able to get to that level of mass production.” Xenomatix hopes to change this. “We’re now running trials in test vehicles and real-life conditions.” A few weeks ago, Siemens’ Simrod electric vehicle took a test drive using Xenolidar, as part of an ongoing project to develop self-driving cars.
Performance and costs
Xenomatix’ current challenge lies in optimizing performance and cost. Integration is another key aspect. “We want esthetically attractive cars with well-integrated technology,” clarifies Geuens. For example, his company is now working on a cover to be placed over the lidar. This product may eventually be integrated in the headlights or windshield. “We need to make sure we can still achieve the required performance, even behind that cover.”
It will take a few years to get the Xenomatix technology verified and mass produced – Geuens is aiming for 2023. Eventually, he hopes to become a mature tier-2 company, delivering mass-produced components to tier-1 clients. After achieving success in the automotive market, the company could broaden its scope to other markets. “Robots, drones, shuttles – many types of autonomous vehicles will need these sensors.”