BREAST CANCER
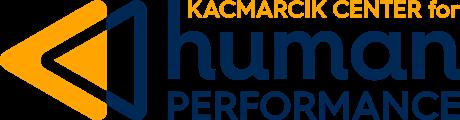
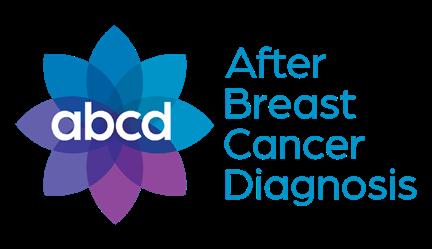
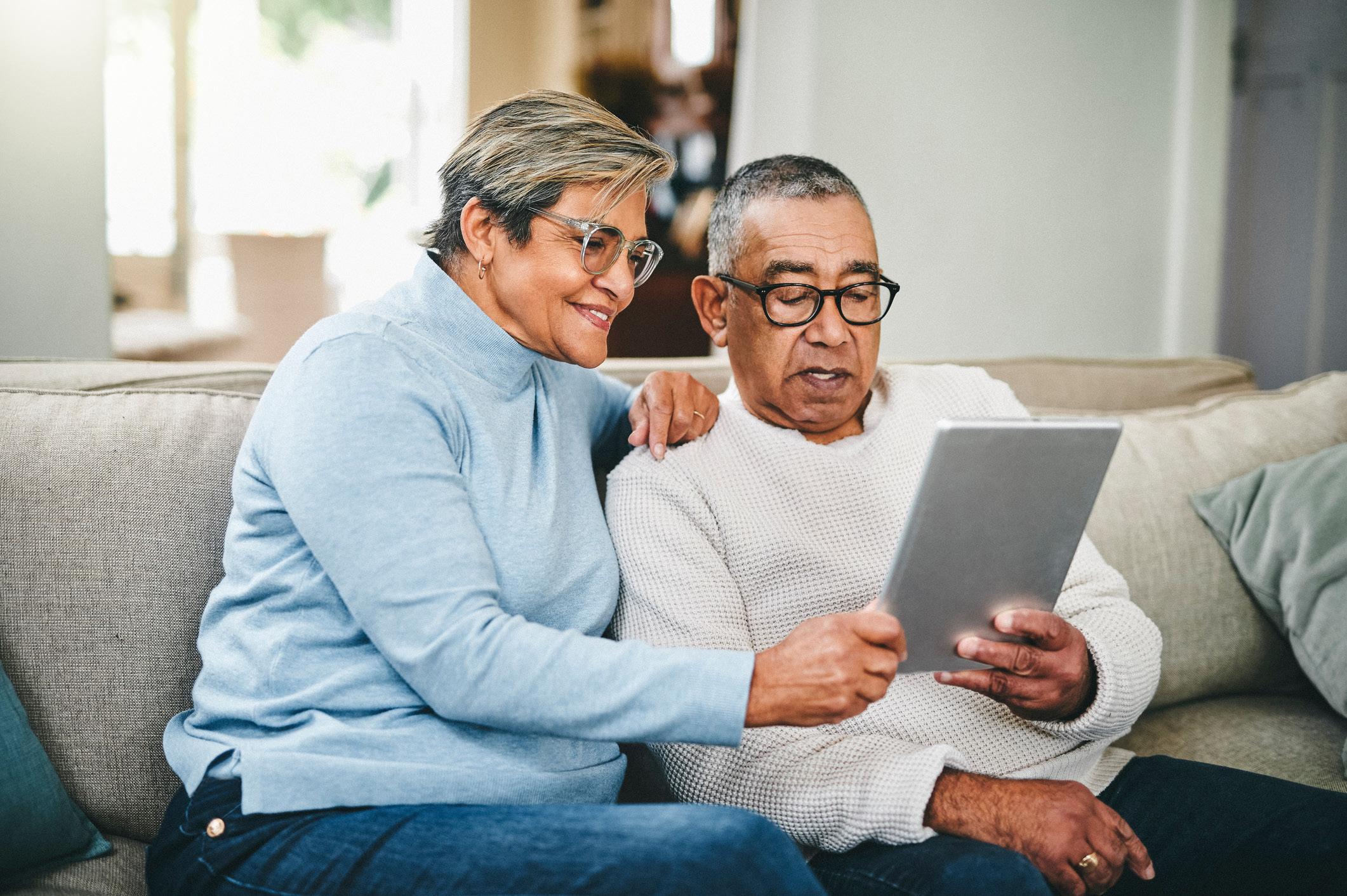
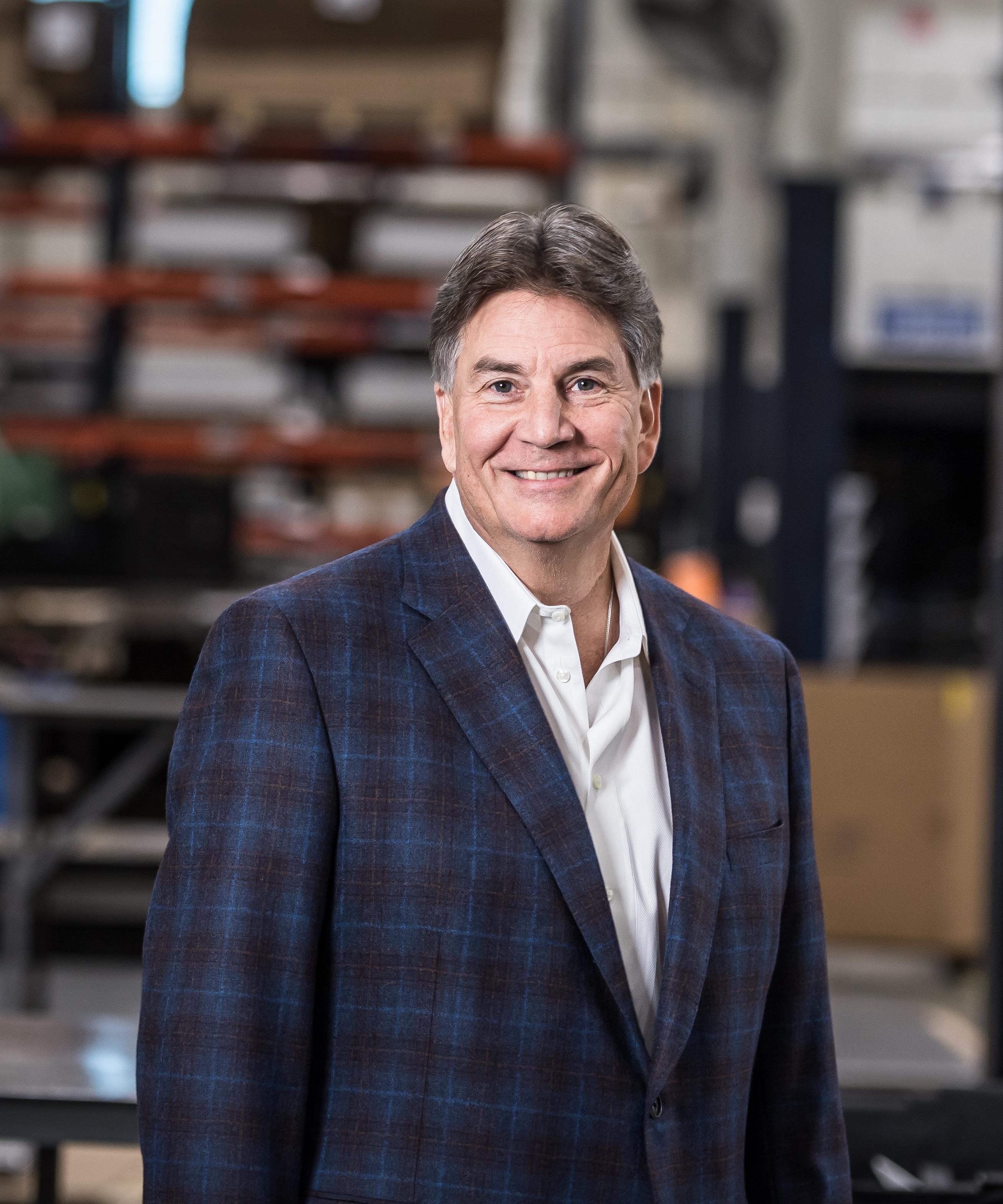
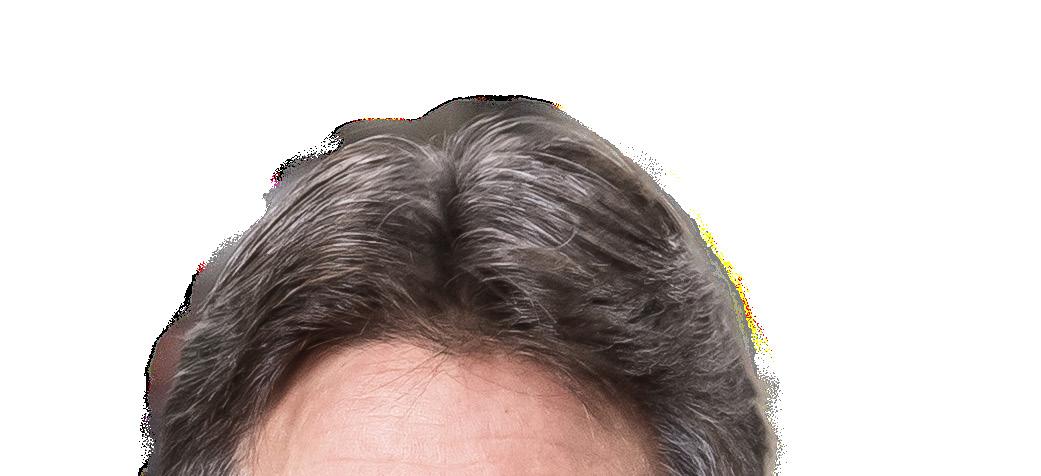
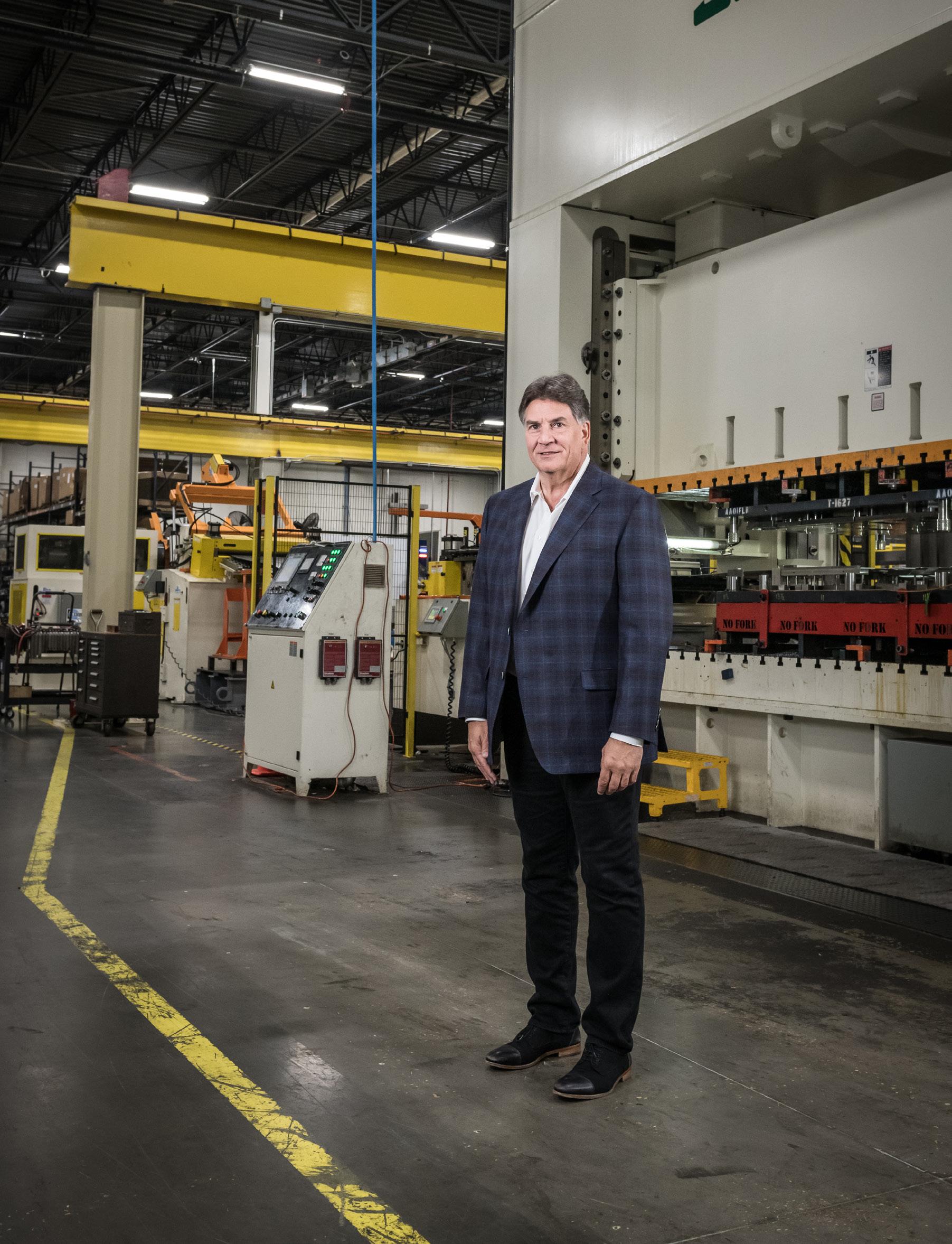
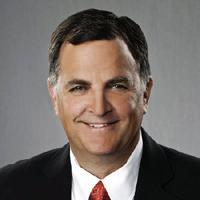
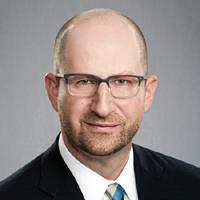
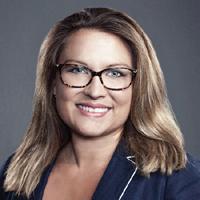
The Milwaukee Repertory Theater plans to build a new $75 million theater complex to replace its Patty & Jay Barker Theater Complex at 108 E. Wells St. in downtown Milwaukee. The Rep hopes to break ground on the
project in late 2023.
Like the Patty & Jay Bark er Theater Complex, the new complex will be attached to the 28-story Associated Bank River Center office tower. Associated Bank announced a 20-year, $10
million sponsorship of the Milwau kee Rep’s new theater complex, which will be named the Associat ed Bank Theater Center through 2042.
“Milwaukee Rep has been a cornerstone of Milwaukee’s cultur al heritage for nearly 70 years. We couldn’t be more proud to provide this enduring commitment to their mission and to making Milwaukee a more vibrant place to live and work,” said Andy Harmening, president and chief executive officer of Associated Bank.
complex with state-of-the-art the aters, abundant community gath ering spaces, an education center to expand student programming, and modern audience amenities.”
As part of the project, all three of The Rep’s theaters will be reno vated so they are compatible with theaters across the U.S., which will allow The Rep to tour productions.
BY THE NUMBERSThe number of electric and hybrid vehicles on Wisconsin roads make up less than of the vehicles in the state.
In February 2020, the Mil waukee Rep said it was planning a 30,000-square-foot expansion and renovation of the Patty & Jay Barker Theater Complex. A report analyzing the complex indicated that The Rep has outgrown the facility and that infrastructure upgrades were needed. The Rep moved into the complex, which includes a redeveloped former power generation plant, in 1987. The Rep’s complex houses three theaters: the Quadracci Power house, Stiemke Studio and the Stackner Cabaret, along with re hearsal facilities, production shops and administrative offices.
But now the Milwaukee Rep is planning to build a new complex in its place. According to a news release, its board of trustees have “unanimously approved plans to remain at its current location and build an entirely new, expanded
“Within the historic building it self, everything inside of the build ing will be basically completely redone,” said Chad Bauman, ex ecutive director of the Milwaukee Rep. “The four walls will remain standing, but everything else will be redone.”
The Rep will also build a new glass entryway structure along West Wells Street to welcome visitors into its main entrance.
Associated Bank is among “hundreds of community leaders, corporations and foundations” that have made pledges to sup port the project, according to the news release.
The Rep attracts more than 300,000 people annually to its performances.
“Theater has changed since we moved into our current home in the 1980s, and so has our community. While it has served us well for four decades, our aging and inefficient complex limits the productions we stage, the plays we develop and the kind of educational impact we create,” Bauman said. n
INSIDE AN OLD FACTORY building on Milwau kee’s south side, the hum of dozens of mid-cen tury industrial knitting machines is a constant sound – like it has been for decades.
Wisconsin Knitwear Inc. has produced cus tom knit hats, scarves and headwear out of the four-story, 30,000-square-foot facility at 1111 W. Lincoln Ave. since 1998, but the Milwau kee-based company has been in business for the past 43 years.
Today, its products are shipped around the world, largely to clients on the East Coast and Midwest, and have been worn as spiritwear for schools and sports teams; promotional merchan dise for businesses and bands, including big names like Dave Matthews Band, Wilco, The Lu mineers and Dr. Dog; and simply as a crucial ac cessory to the typical Midwest-winter wardrobe.
Wisconsin Knitwear produces about 200,000 to 250,000 hats in a typical year. In an industry increasingly driven by automation, mass pro duction and offshoring, what sets Wisconsin Knitwear apart is its “old-school” process, said Steven Arenzon, who took over ownership from his father, Mauricio, an Argentine immigrant who started the company in 1979.
“We’re the last knitting company in the U.S. that has the machines that make our knit hats, with names knitted directly into the hats,” said Arenzon. “(Other companies) have different ma chines, newer machines, new technology… and that doesn’t work for me. I like the old school.” n
— Maredithe MeyerWinemaking season is in full swing at the The Blind Horse Restaurant & Winery near Kohler. A shipment of approximately 30,000 pounds of freshly harvested grapes – including Grenache, Petite Sirah and Zinfandel varietals – arrived in mid-September from Lodi, Califor nia. It was the first of four or five shipments the winery will receive this season, for a total of 100,000 pounds of grapes, yielding 4,000 to 5,000 cases of wine.
“What makes us unique com pared to a lot of different wineries in the Midwest is our process,” said
By Maredithe Meyer, staff writer Tom Nye, general manager of The Blind Horse.Prior to fermentation, its red wine is “cold soaked” for five or six days – either manually using dry ice or inside two new tempera ture-controlled tanks that the win ery purchased last year. The wine later ages for two to three years in barrels.
“We’re really a hand-crafted small winery, we’re able to do things like this,” said Nye. “We’re able to really take our time and craft that wine the way we want to before we release it.” n
These grapes were harvested just three days prior to their arrival in Kohler.
Eric Escobar rakes the grapes on to a conveyor belt to be destemmed and crushed. Much of the wine production process is now automated.
A machine called a “crusher destemmer” crushes the grapes and removes the stems. Customers can see how wine used to be made at the winery’s annual Harvest Festival & Grape Stomp.
Once crushed, Grenache grapes are immediately pressed to make the winery’s 2022 Rose´, which will be ready to enjoy next summer.
Amid ongoing supply chain disruption, vineyards have struggled to find enough cardboard containers to ship their grapes, contributing to increased costs.
On a mid-September morn ing, assistant winemaker Patrick Regenwether, Eric Klemme, Luke Pennington and Eric Escobar kicked off production season.
WHAT IT DOES:
Sells meat and cheese products
FOUNDED: 2016 EMPLOYEES:
Ranges from five to 20-plus
GOAL:
Open a second brick-and-mortar location
FUNDING: $10,000 grant from the Village of Union
IT SHOULDN’T SURPRISE anyone that Wis consinites love their meat and cheese, espe cially if it’s from a local business. Add in the combination of a unique product offering and multi-pronged marketing approach, and you get Union Grove-based Two Creek Farms LLC, a fast-growing company specializing in premi um meats and cheeses.
Justin Miklaszewski, founder of Two Creek Farms, is only 22 years old but has run his business for six years while also earning a degree in general business and finance from UW-Whitewater. He grew up around animals while living at his family home, and farming has always been a part of his life through programs like 4-H.
In 2016, Miklaszewski and his family took two pigs to the Wisconsin State Fair in the hopes of selling them at the Governor’s Blue Ribbon Livestock Auction. However, the pigs
did not end up qualifying. To seek potential buyers, he made a Facebook post to gauge interest.
“Within about an hour, I had over 250 com ments on that post. That kind of was the start of (Two Creek Farms),” Miklaszewski said.
The next year, he raised a few extra pigs to sell. This process continued over the next several years, with Miklaszewski continually increasing the number of pigs and adding new animals, like steers. He also started attending the Racine County Farmers Market to broaden his audience.
“We had some customers come up to us one day and ask if we sold beef sticks or jerky or summer sausage. Right there, it kind of clicked in my head,” Miklaszewski said.
From there, Two Creek Farms continued to grow as customers sought out products rang ing from chicken and steak to brats. Miklasze wski began purchasing even larger volumes of animals to keep up with demand. Those animals are raised on a property in Franksville.
Two Creek Farms works with Rio, Wiscon sin-based processing company Johnson’s Sausage Shoppe to create recipes and make its line of approximately 250 products – including unique finds like cherry brats and Bloody Mary
beef sticks – all sold at its brick-and-mortar location at 1360 15th Ave. in Union Grove.
The company’s workforce ranges from five to more than 20, depending on the time of the year. Summer is Two Creek Farms’ busiest sea son as farmers markets wind up for the year.
“Basically, anything you would get at a meat market we now physically do,” Miklasze wski said. “It took off.”
Since its founding in 2016, Two Creek Farms has seen more than 300% growth, he said, attributing some of that growth to the decision to join an online farmers market, called Market Wagon, in 2019. This broadened the company’s reach to 18 counties in Wisconsin and Illinois and provided a constant flow of sales.
“… It was more of a safety net at first, and then it kind of kept growing and growing,” Miklaszewski said.
He wants to take advantage of the com pany’s continued growth and is working to identify a second storefront for Two Creek Farms. Whitefish Bay and Oak Creek are being considered as options for a new store, which could potentially open at the start of next year.
“For me, it’s always 100% about trying to promote and get the word out to different people,” Miklaszewski said. n
• Bunker was the chief financial officer at Potawatomi Hotel & Casino for seven years before joining The Bartolotta Restaurants in September. She has almost 40 years of leadership experience.
• She knew she wanted to join the Bartolotta team after having several people tell her they enjoyed working for the company. “The Bartolotta Restaurants has such a strong reputation of quality and a strong sense of community in the greater Milwaukee area, and with the recent announcements expanding the portfolio, I wanted to be a part of its future.”
• Bunker says her past position at Potawatomi was a good entryway into the world of hospitality. “Before working there, I had no exposure to the restaurant industry. But learning about and seeing the operations of a variety of restaurants there gave me the confidence I needed to take on this new role.”
• Outside of work, she enjoys golfing, seeing movies, dining out, and attending sporting events and concerts.
• Her favorite Bartolotta restaurant is one close to home: “Ristorante Bartolotta because it’s in my neighborhood, and it is a staple in the Wauwatosa community.”
UnitedHealthcare NexusACO® health plans bring together Advocate Aurora Health, Children’s Wisconsin, Froedtert and Medical College of Wisconsin to connect your employees to quality care.
Our network of Primary Care Physicians act as the nexus, or trusted single point of contact, to help guide members through their health care journey. And with access to so many quality, cost-efficient providers, your employees will likely be able to find care near where they live or work.
Collaboration Through providers working together, health outcomes for employees may be improved.
Designed to be simple and efficient PCPs aim to guide patients to the right care at the right time and setting.
Employers may save up to13% on medical premiums.¹
Contact your broker today
Spanish architect Santiago Calatrava recently visited Milwaukee to celebrate the 20th anniversary of the opening of his first U.S. project: the Milwaukee Art Museum’s Quadracci Pavilion. Best known for its wing-like Burke Brise Soleil, the 142,050-square-foot addition transformed the Milwaukee Art Museum into the city’s most iconic building. After being recognized by city and museum officials, Calatrava reflected on the project two decades later. n
“Entering the museum, it was for me like the opening day. It’s so well preserved, so beauti fully preserved, and so much care, you see, that is very important. It means respect to the work and respect to all the people working here.”
“I recognize myself in every curve. I remember when every curve, every small detail was done.”
“If I will cap some of the essence of this experi ence, it is a few times in your life that it happens to arrive at a place, recognize the extraordinary, human qualities of the people and then decide to change countries. We came to live in the Unit ed States immediately after the opening of the (Quadracci Pavilion). ... The consequence of that is we have four grandsons (who are) American.”
“I cannot forget David Kahler, who was with me co-architect of this building. He helped (enor mously). He has put his enormous experience as an architect, his whole life as an architect to elaborate and make sure the precision and the quality of all those details are there.”
“I asked myself many times, how can (the American people) be so welcoming? … I arrived at the conclusion that the reason is very simple, it’s not complicated: The majority of the people in this country are themselves newcomers or are sons, grandsons or great-grandsons of new comers. You have an art of welcoming people that is very rare to find some where else.”
Property values in Wisconsin jumped 13.8% in 2022 to $745 billion, the largest jump on record in data that goes back to 1985, according to data analyzed by the Wisconsin Policy Forum.
While residential properties account for a large portion of overall values at $538 billion and a significant portion of the increase, up 14.9%, other property classes are also part of the equation. Commercial proper ties, for instance, saw a 13.2% increase.
Manufacturing property values were up 4.8% statewide in 2022 and have seen a steady increase over the past decade. Here’s a closer look at how manufacturing property values have shifted in southeastern Wisconsin.
The total manufacturing property value in Waukesha County sur passed Milwaukee County in 2020. The gap narrowed this year, but Waukesha County retained its edge:
Manufacturing Equalized Property Value (in billions of dollars)
YEAR MILWAUKEE COUNTY WAUKESHA COUNTY
2012 $1.49 $1.35
2013 $1.48 $1.37
2014 $1.46 $1.40
2015 $1.48 $1.43
$1.52 $1.46
$1.52 $1.49
$1.52 $1.51
$1.56 $1.55
$1.61 $1.62
$1.65 $1.67
Wisconsin Policy Forum 2022 Property Values & Taxes DataTool
Manufacturing plays a different role in the economy of every county in southeastern Wisconsin. In Sheboygan County, which is home to sev eral global manufacturers, it accounts for 4.7% of total property value. In Walworth, which has a concentration of mansions in the Lake Geneva area, manufacturing accounts for just 1.9% of the county’s property value. But Walworth has seen the strongest growth in manufacturing property values over the past decade, up almost 77% since 2012 and more than 56% since 2017.
MANUFACTURING AS % OF TOTAL PROPERTY VALUE SINCE 2012 SINCE 2017
Has
Share
opinion!
biztimes.com/bizpoll
Sheboygan
Washington 2.9%
Racine 2.7%
23.4%
24.3%
34.4%
Kenosha 2.4% 42.7% 26.3%
Waukesha 2.3%
Ozaukee 2.1%
15.1%
24.0%
Milwaukee 2.0% 14.5% 12.7%
Walworth 1.9% 76.9% 56.6%
2.4% 41.1% 23.7%
Wisconsin Policy Forum
In its 6th year in Milwaukee, 7 local men will unite to fight breast cancer with the American Cancer Society through participation in the Real Men Wear Pink campaign. Throughout October, Real Men Wear Pink participants will encourage community members to take action in the fight against breast cancer.
“In addition to wearing pink and raising awareness about breast cancer, these men will be raising funds to help the American Cancer Society attack cancer from every angle and save more lives from breast cancer,” said Shannon Richards, Senior Development Manager, American Cancer Society. “Funds raised help us save lives from breast cancer through early detection and prevention, innovative breast cancer research, and patient support.”
Each Real Men Wear Pink participant accepts a fundraising challenge and will compete to be the top fundraiser among his peers by the end of the campaign.
Chris Ott’s is a 2022 Real Men Wear Pink participant. His wife Jennifer was diagnosed with breast cancer shortly after the birth of their son. “I had to realize a life without my wife and best friend was real...I did my best to be encouraging and to give her hope every day,” said Chris. Chris and Jennifer became passionate about the Society’s mission after the completion of her treatments and surgeries. “We needed to help in the fight to end cancer. We did not want one more person to have to deal with the fear of losing their life or a loved one’s.”
According to the American Cancer Society Cancer Facts & Figures 2022 an estimated 290,560 women in the United States will be diagnosed with breast cancer, and an estimated 43,780 will die from the disease this year. In Wisconsin, 5,380 women will be diagnosed this year, and 720 will die from the disease. Breast cancer is the second leading cause of cancer death in women, and it is the most common cancer diagnosed in women other than skin cancer.
“Our community can make a huge impact in the breast cancer cause,” said Richards. “We are grateful to our Real Men Wear Pink participants for lending their voices to this cause and fighting for everyone affected by breast cancer.”
For more information about breast cancer or the Real Men Wear Pink campaign in Milwaukee and for a complete listing of all the ambassadors, visit realmenwearpinkacs.org/milwaukeewi.
Our research program has played a role in many of the advances that save lives from breast cancer today from the efficacy of mammography to targeted therapies Today’s research investments are tomorrow’s breast cancer treatments
The American Cancer Society currently invests more than $71 million in breast cancer research. (as of December 2021)
We envision a future where our children no longer live with the threat of breast cancer and where everyone has a fair and just opportunity to prevent, find, treat, and survive this disease By supporting the Making Strides Against Breast Cancer movement, you help ensure the American Cancer Society can continue fighting Together, we can help fund the future of breast cancer research and programs for our loved ones today and for the next generation
We’re the primary private nonprofit funder of cancer research, investing more than $4 9 billion to date. Since 1989, death rates from breast cancer have declined by 40% resulting in more than 375,000 lives saved.
Cancer care is one of the vast inequities communities of color face. Example: Black women develop breast cancer at similar rates as white women yet have a 40% higher risk of dying from it Our commitment to health equity includes a $50 million investment in research to help understand these types of cancer inequities and create strategies for overcoming them.
Grantee: Paraic Kenny, PhD
Institution: University of Wisconsin School of Medicine and Public Health
Type of Research: Biochemistry and Immunology of Cancer
Some types of breast cancer are affected by hormones, like estrogen and progesterone. Those breast cancer cells have receptors that attach to estrogen and progesterone, which help them grow. Treatments that stop their attachment are called hormone therapy.
For instance, some drugs, including letrozole (Femara), keep estrogen from being made. Others, like tamoxifen (Nolvadex, Soltamox), keep estrogen from attaching to the receptors on the cancer cells.
Studies have shown that these drugs work in large part because they also suppress the effect of a substance called amphiregulin, which is found in normal, healthy cells. Amphiregulin helps normal cells grow, but it also helps hormone-positive cancer cells grow. Unfortunately, tumors can develop resistance to these successful hormone therapies, rendering them ineffective.
ACS grantee Paraic Kenny, PhD, recently published results of a mouse study showing that amphiregulin is closely linked to the growth of estrogen-receptor positive breast tumors. Importantly, these findings may provide a strategy to treat certain types of breast cancers.
Why does it matter? This could mean drugs that reduce the effect of amphiregulin in hormone positive cancers could also be used to treat hormone negative cancers. For example, drugs that target amphiregulin in the future may be used to treat triplenegative breast cancer, which has many fewer treatment options available today.
ACCORDING to the World Health Organization, cataracts are the leading cause of blindness and vi sual impairment worldwide. Fortu nately, the condition, defined as a clouding of the normally clear lens of the eye, is treatable through non-invasive surgical removal; the operation is one of the most common procedures performed in the U.S. today.
But it’s a much different story for developing countries, where 99% of the total 52 million people globally suffering from vision loss due to cataracts live. In places like India and Africa, cataracts treatment is neither accessible nor affordable, which is why the con dition is responsible for 50%-80% of blindness in India and 65% of blindness in Africa.
This is just one example of a global health disparity that Mil waukee-based medical technology contract manufacturer MPE (Mid west Products & Engineering) Inc. has worked to address through its “vertically integrated” business
model. The company specializes in medium-volume design and production for health care and high-tech original equipment manufacturers.
“A big part of our focus is tak ing various sophisticated technol ogies and simplifying how they’re used so that these technologies are available to global patients,” said Hank Kohl, president of MPE.
So, when a major OEM in the ophthalmology medical devices space wanted to create simpli fied technology that would allow organizations like Doctors Without Borders do high-volume cataract removal surgeries in developing communities, MPE brought that vison to life.
“What we were able to do was repurpose the sensors that we’ve identified and used in other surgical applications to be able to measure the pressure in the eye. It was a disposable sensor that was very low cost and readily available, and by using that, we were able to adapt the technology to automate
By Maredithe Meyer, staff writerthe eye pressure reading and hold that pressure in the procedure to take that off of the surgeon’s needs,” said Kohl.
The innovation significantly cut costs and reduced the surgery time by more than 70%, he said.
Located at 10597 W. Glen brook Court on Milwaukee’s far northwest side, MPE’s local foot print includes a 160,000-squarefoot manufacturing facility; a 40,000-square-foot receiving, quality and office facility; and a nearby 50,000-squre-foot distri bution facility. The company plans to add 30,000 square feet to its electronic and cable manufactur ing footprint next year. As a result of recent acquisitions, it also has a 75,000-sqaure-foot facility in Racine and a 25,000-square-foot location in Carlsbad, California.
Through its five business segments – MPE Design, MPE Prototype, MPE Components, MPE Mobility and MPE Systems – the company handles every step of a project’s development lifecycle,
from “concept to completion.” The result is an FDA-approved product that goes to market faster and at a much lower cost, ultimately increas ing revenue for the customer.
“For example, a major compa ny like Medtronic or GE Healthcare would typically take five to seven years to develop a new product in the market. … We’re doing that typically in 14 to 16 months today in our model,” said Kohl. “That’s the model that these companies are appreciating because we can get them the technology that the market is demanding much faster than they can on their own.”
MPE’s recent innovations cover a range of uses and areas, from neonatal to surgical navigation. To name a few, there’s the hospital bassinet that allows an infant to be next to its mother after a problem atic birth; a Cleveland Clinic device for thoracic surgical procedures that uses AI and sensors, rather than radiation, to create a live image of the patient’s heart; then there’s the self-guided CPR skills training platform, which is de signed to give health care staff an opportunity to practice their CPR skills frequently.
“I think we’re on seven surgical robotic platforms that are currently
in production in the market today, where there were none when we started this journey,” said Kohl.
This year, MPE is projecting 60% year-over-year growth. The company didn’t get to this point overnight. The company was founded in 1978, but its current mission and growth trajectory can be traced back to 2012, when it launched a plan to capitalize on a major shift within the medical device space. The Affordable Care Act introduced value-based, preventative health care into a market built on a foundation of reactionary practices. Medical device OEMs were forced to look differently at their product devel opment pipeline and technology they had on the market, said Kohl.
Over the next few years, MPE invested about $25 million in its manufacturing footprint and invested heavily in human capital, recruiting the state’s top engi
neers from medical device OEM customers and local universities, said Kohl. The business grew from 100 to now 300 employees at its Glenbrook Court facility.
In 2019, Chicago-based private equity firm Beecken Petty O’Keefe & Co. acquired a majority equity stake in MPE, accelerating the company’s growth objectives with access to a $550 million fund. BPOC is among the oldest private equity firms in the U.S. that spe cializes exclusively in health care.
“They knew our industry, they knew many of our customers, and they were able to put together a fund that could support the business plan that were acting on today,” said Kohl.
For BPOC, which has raised almost five funds and done almost 60 platform investments since 1996, MPE was a diamond in the rough.
“We see a lot of contract manufacturing businesses, it’s a
core vertical for us. We say ‘no’ to most of them,” said Adam Hentze, principal at BPOC.
MPE’s concept-to-completion model as well as its leadership team – and Kohl’s vision in partic ular – were the biggest attractors for BPOC, he said.
“The ability to start at the very early stage of design and devel opment and support a company all the way up to commercial scale manufacturing – that’s something we hear a lot but when you dig into the details, I think MPE is unique in its capability to truly do that,” said Hentze.
The strategic partnership enabled MPE in 2021 to acquire Yorkville-based Racine Metal-Fab, a fabricator of highly aesthetic and complex sheet metal components and sub-assemblies, and Califor nia-based MindFlow Design, a medical product development firm.
MPE has additional acquisi
tions in the works to continue to “fill the gaps” in its manufacturing capabilities, said Peter Georgi anna, vice president of corporate development at MPE.
“Right now, the capabilities that we have (in Milwaukee) are really around metals and bending and assembling this really hightech medical hardware. But some of the things that we don’t have is a tremendous depth in manufac turing plastics, for example,” said Georgianna.
Robotics and human-machine interface design are two other ca pabilities MPE is looking to bring in-house through acquisition.
“(Potential acquisitions) don’t have to be fully mature, they don’t have to have the quality systems or the high-level customer relationships that we have,” said Georgianna. “They just need to be able to do the thing that we want them to do.” n
IT’S OFTEN TRUE that the innovation behind creating new technologies is spurred due to the existence of some problem. For Deepak Arora, chief exec utive officer of Hartland-based startup Wearable Technologies Inc., the idea behind his wearable monitoring device came after he experienced every parent’s worst nightmare.
In 2020, a complete accident led to his two-year-old daughter, Mahi, wandering out of their family home and falling into a nearby retention pond.
“By the time we could find her, it was five minutes too late,” Arora said. “I couldn’t wrap my head around how something like this could happen, and our research showed that there’s nothing out there on the market that can protect against this.”
He immediately began thinking of ways a wearable device could be used to prevent similar accidents.
As part of his research, he found that more than 5.6 million kids worldwide do not make it to their fifth birthday due to accidents.
The statistics for elderly peo ple between the ages of 80 and 85 showed a similar trend.
“Think of it as driving a car without the airbags,” Arora said. “Those airbags are there to protect you if something were to happen. We believe our device and technology is the same way, it will act as a protective layer for your loved ones.”
and external temperature and humidity. There’s also a pressure sensor that could help indicate if the fall has happened on a hard surface or into water.
There are three key compo nents to the device. First, the detection component, which can let you know when the person being monitored has gone outside of designated boundaries. There is also a predictive modeling component, which allows users to mark possible hazards in the area, such as a busy roadway, and the device can provide a real-time esti mate as to when the person being monitored will reach that hazard. The last component provides an enhanced level of protection by sending out different levels of alerts. Up to five people can re ceive notifications from the device at a time.
“The bottom line is we’re trying to build awareness and educate others. People don’t realize that this can happen to them until it happens. We built our house in the most secured cul-de-sac that you could imagine, and even then, it happened,” Arora said.
He started building out a pro totype in late 2020 with the initial help of angel investors, including Jeff Horwath of Jeff Horwath Fam ily Builders. Horwath had built the Arora family home, and the two men regained contact after Mahi’s accident.
A Wearable Technologies device can allow a parent to keep tabs on their children through a series of different monitoring components. This photo shows the app component for smartphones.
Wearable Technologies has created a device – to be worn on the wrist like a watch or attached securely to different articles of clothing – that monitors several key pieces of information to help predict potential hazards or emer gency situations.
The current prototype monitors which direction the user is moving, whether they have fallen or flipped over, heart rate and oxygen levels,
“Our device has so many special functions including haz ard-mapping, geo-fencing and a variety of wearable options. But it’s the predictive capability and hands-free nature of our product that really sets us apart,” Horwath said.
He addressed one other common concern among parents of young children: data privacy. Any personal data stored on a Wearable Technologies device is secured. To prevent anyone from hacking into one of the devices, the Wearable Technologies team
chose to use a processor with a crypto-level security system built in at the hardware level.
The company’s official product launch is expected in the first half of 2023. While Arora and Horwath declined to comment on how much outside funding has been secured thus far, SEC filings show Wearable Technologies has raised at least $755,000. The company has also been named as a Qual ified New Business Venture by Wisconsin Economic Development Corp., meaning it’s eligible for a tax credit.
As the company continues to grow, Arora will focus on advanc ing the device to the beta stage. Eventually, second and third generations will be designed with additional features. Branching into other markets, such as hospital settings and senior living facilities, is also on the horizon. n
Several economic indicators show the economy may be heading into a recession and with the Federal Reserve raising interest rates to fight inflation, all while we try to adapt to a post-pandemic landscape, what is the outlook for the local commercial real estate market in 2023?
For some insight, join us at the 2022 BizTimes Commercial Real Estate & Development Conference to hear from industry professionals who will share their perspectives.
Keynote: Geoffrey Kasselman, Partner, Senior Vice President, Workplace Strategy, CRG Kasselman provides clients with “future-proofing” strategies for their real estate holdings and workplaces. He is also an innovation-minded business futurist and global speaker on topics like mobility, sustainability, e-commerce, supply chain and disruptive technologies. His remarks will focus on how big trends in the U.S. and global economies will shape commercial real estate in Milwaukee and the Upper Midwest.
Tony Lindsay, Principal, Asset Management, North Wells Capital, LLC (1)
• Thomas D’Arcy, Senior Managing Director, Hines (2)
• Lafayette Crump, Commissioner of City Development, City of Milwaukee (3)
• Andy Hunt, Vieth Director for the Center for Real Estate, Marquette University (4)
Phoenix Investors, which is developing 500,000 square feet of industrial space in Beloit, is just one of several institutional investors that are putting their money into industrial development projects in the Janesville-Beloit corridor.
FOR YEARS, Kenosha County has been a hot spot for distributors and manufacturers finding avail able land to move in and escape from Illinois taxes while still being close to the nation’s largest logis tics hub: Chicago.
Lately, however, another darling has emerged for industrial real estate developers and their would-be tenants: the Janes ville-Beloit corridor along I-39/90 in Rock County.
That’s especially true for devel opers who are now forced to push for 300,000- to 500,000-squarefeet buildings to make their proj ects feasible.
To Adam Matson, an industrial real estate broker and director in Newmark’s Milwaukee office, Be loit-Janesville could very well be the state’s next industrial hot spot.
“We call it ‘Little Kenosha,’” Matson said. “It’s sliding under the radar for some, but it is going to hop up really quick. Just in the last three years there has been two million square feet of industrial moves in that area. (There’s been
Situated on the northern edge of Walker’s Point, just south of the Menomonee River, in a longtime industrial neighborhood, the three-story, 134-year-old brick warehouse at 913 W. Bruce St. has been occupied by a num ber of different users over the years. Those have included woodworking compa nies and, most recently, metal coatings company Raphael Industries.
the building is owned by Milwaukee-based SUR Natural Health Brands
the maker of ZYN curcumin-infused beverages. Company founders Asim and Qasim
purchased the building in 2021. The brothers gained approv al from the Common Council
summer to rezone the building from heavy industrial
industrial commercial, allowing the business to operate out of the
activity there for a while), but it’s only been in the last two or three years that national, institutional investors have started to show interest. Now, (Milwaukee-based) Zilber Ltd. has holdings in Janesville, STAG Industrial has holdings in Janesville and (Mil waukee-based) Phoenix Investors is doing a speculative project in Beloit of 500,000 square feet.”
Part of the draw, says Matson, is not only the corridor’s access to I-39/90, but also the connections that freeway system provides. Trucks can reach metro Chicago via I-90, but the system also provides easier access to Iowa, the Dakotas, the Twin Cities and Denver.
The Janesville-Beloit corridor’s move from a tertiary to a primary market has also lowered cap rates, making it more attractive to inves tors looking for less risk, he said.
The large population of blue-collar workers near the state line has also made the corridor a place where companies want to locate.
“Ever since the Janesville (Gen eral Motors) plant closed (in 2008), that labor pool has been crossing into Illinois to work, or they have been commuting to Madison. That is a labor pool that is skilled and ready to work,” Matson said.
Jeff Hoffman, an industrial real estate broker and principal at Cushman & Wakefield | Boerke, agrees. But he’s also seen con tinued interest just up the road in Madison, where the supply of tech workers is the strongest.
“Madison going down to Beloit is most certainly a corridor to watch,” Hoffman said.
As for the Madison interest, Hoffman said his firm is very close to closing a “substantial deal” with a company that is currently located in the southwestern corner of the state.
“They are going to be locating in Middleton, and they are coming for the engineering talent coming out of UW-Madison,” he said.
NEAR NORTH, NEAR SOUTH
But with the Kenosha and
I-39/90 corridors increasingly designed for bigger users, compa nies –especially those that don’t need massive amounts of space –are looking just north and south of Milwaukee as the price of devel opment elsewhere has become increasingly expensive.
As far as the hottest industrial corridor to the north of Milwaukee, Hoffman and veteran broker Jim Barry say the Germantown-Richfield corridor at Holy Hill Road and I-41, which includes the nearly complete Germantown Gateway Corporate Park, is the one to watch.
“Just in the last three years, 11 buildings and over 2.5 million square feet of space delivered, and there is more coming,” Hoff man said. “It is a wide range of us ers, from manufacturers to service space, to distributors. It is a known quantity at this point.”
There’s also the proximity to workers on the northwest of Mil waukee and even the Fox Valley.
“A lot of people didn’t really expect it, but we are hearing about employers being about to recruit from that area,” Hoffman said.
As Germantown continues to grow its business parks, Barry said Richfield, just across I-41, is itself poised to grow.
He and Hoffman are also watching Racine County, especial ly those areas along the interstate that, up until now, really haven’t been as popular as those closer to Chicago in Kenosha County.
“There is going to be more go ing on at the interchanges, where there has been nothing up until this point,” Barry said. n
Racine-based Twin Disc Inc. announced in late September that it plans to lease 8,100 square feet at 222 E. Erie St. in Milwaukee’s Historic Third Ward for up to 25 employees. The company will move its “corpo rate team” there.
The manufacturer of power transmission equipment has not stated if the new office will be considered its corporate headquarters. In a press release announcing the transaction, the company described the pending office lease and tentative sale of its Racine headquarters facility as part of an “asset optimization strategy.”
An affiliate of Chicago-based R2 Companies bought the Erie Street building in 2019 for $9.65 million. Founders 3 Real Estate Services man ages the building. Twin Disc’s lease is expected to begin early next year. The 85,000-square-foot structure was built in 1891.
ADDRESS: 222 E. Erie St., Milwaukee
LESSEE: Twin Disc Inc.
SPACE: 8,100 square feet
OWNER: R2 Companies
WMEP Manufacturing Solutions is proud to be the Presenting Sponsor for the 2022 Next Generation Manufacturing Summit, an event that celebrates the vital role manufacturing plays in Wisconsin.
For over 25 years, WMEP has been helping manufacturers become more profitable and valuable.
WMEP is a specialized, not-for-profit organization that provides targeted consulting services for Wisconsin manufacturers.
Our team of manufacturing business experts work side-by-side with hundreds of manufacturers each year, helping them develop and implement effective solutions that address their biggest challenges.
We closely monitor trends and best practices in manufacturing, and proactively develop solutions that meet the existing and emerging needs of manufacturers. We’ve helped manufacturers reduce waste, improve efficiencies, automate
operations, grow their business, achieve certifications, find and develop talent, and increase profits.
We create results that count. On every client engagement, we are evaluated on both the results we produce together and our partner’s satisfaction with our services.
We are proud to excel on both metrics! Our average net promoter score is 9.1 out of 10 — and the vast majority of our clients experience a strong return on the projects for which they hire us.
In 2021, we recorded $300 Million in economic impact (cost savings, increased sales, etc.) from our project work with Wisconsin Manufacturers.
Go to WMEP.ORG to find out how WMEP Manufacturing Solutions can help your organization solve its biggest challenges.
BMO strongly supports the Wisconsin manufacturing community and we’re proud to sponsor the 2022 Next Generation Manufacturing Summit.
At BMO we understand the industry complexities that manufacturers face whether it’s managing a supply chain, procuring raw materials or planning for growth. Our teams of experienced, local relationship managers will work closely with you to understand the issues and opportunities unique to your business and will offer strategic advice and solutions to help keep your business moving forward.
To learn more, visit bmoharris.com/manufacturing or contact:
Dave Anderson
Managing Director
david.a.anderson@bmo.com (414) 765-7671
Banking products and services are subject to bank and credit approval. BMO Harris Bank N.A. Member FDIC.
In an era of skyrocketing inflation and costs, OSHA penalties are not exempt from the list of rising, uninsurable financial risks. These penalties add insult to injury and don’t correct the root issue that led to the incident or OSHA inspection.
Tim will lay the groundwork and provide historical context for inflation’s impact on penalties.
Tim and Dan will walk you through program priorities, strategies, and tactical elements of managing an effective safety program. The benefits of an effective program will ensure that you meet the primary objective of sending employees home safely to their families, reducing costs, reducing uninsurable risk and complying with minimum standards. Standard operating procedures, effective communication, observations, and continuous improvement are among the tactical elements that will be reviewed and discussed.
The discussion and interactive portion will include preventive strategies and tactics to mitigate and reduce the impact of an OSHA inspection.
As your business continues to grow and evolve, it deserves the capabilities of a global bank, while staying nimble, like a local one. So, no matter what your vision is, your Wisconsin-based commercial banking team brings deep industry expertise and strategic guidance to help uncover opportunities and take your business to new heights. That’s why we work here.
Visit bmoharris.com/commercial to learn more.
Wisconsin-based experts ready to help Wisconsin-based businesses. We work here.
alk in the lobby of Kapco Metal Stamp ing’s Grafton headquarters and there’s a decent chance you will hear the rhythmic pound ing of stamping presses. The drumbeat of one met al part after another being shaped into something new is at the heart of Kapco’s business.
The company has other capabilities, too, like laser cutting, machining, welding and painting. Founded in 1972, Kapco has grown to around 700 employees across nine facilities. Like many manu facturers, the company is part of the supply chain for its customers. It’s products – brackets found on home appliances, parts of ATVs and motorcycles and components used by the military, just to name a few – are found all over the world.
For many manufacturers, it’s easy to fall into routines. Shifts start at a set time. Standardized work processes ensure product quality and keep things moving across the shop floor. Continuous improvements are made to improve efficiency or reduce waste. It’s not that the industry never changes – dramatic shifts have taken place over the years in areas like robotics and automation, for example – but the industry trends toward a more traditional approach to work.
While Kapco’s profile may share similarities with so many other manufacturers in southeast ern Wisconsin, the other companies in Kacmarcik Enterprises’ portfolio cover a variety of industries. There’s Advanced Coatings Inc. and Steel Blue Logistics, which fit in the industrial realm. Then there’s Speedkore Performance Group, which builds custom carbon fiber cars worth hundreds of thousands of dollars; the House of Harley-David son motorcycle dealership; the Forward Madison FC pro soccer team; music and entertainment ven tures; and several nonprofit efforts.
Jim Kacmarcik, chairman and chief executive officer of Kacmarcik Enterprises, says managing all those entities starts with hiring “extraordinary team leaders in all of these phases that I feel can carry the torch.”
“I spend a little bit more time stitching the piec es together and trying to parlay things a little bit,”
he said. “It might, from a distance, seem like, ‘What in the world is this guy doing with all these unusu ally … disconnected types of businesses?’ There’s some pretty significant method to the madness.”
Some of the ways the businesses can work to gether include Speedkore clients contributing to nonprofit efforts, House of Harley benefiting from Speedkore’s customizing experience and access to carbon fiber parts, or Kapco marketing teams sup porting other businesses and new ventures.
And Kacmarcik also continues to push for ward, partnering with Kenosha-based Bear Devel opment on the Iron District, a $160 million sports and entertainment development planned in down town Milwaukee. The plans include bringing a professional soccer team to Milwaukee, something Kacmarcik said he has wanted to do for several years. The project also includes housing, a hotel, re tail and restaurants.
“I didn’t quite imagine it to be as potentially sig nificant as it is, but now we feel totally that it is, I don’t want to say game changing, but it is a very significant piece of Milwaukee’s future,” he said.
“I’m like, ‘Wow, who knew that this might be where I would be doing something?’” Kacmarcik added.
In many ways, there is a parallel between Kac marcik’s journey and what he wants to create with his latest major undertaking: the Kacmarcik Center for Human Performance.
Owning a soccer team didn’t seem to be in the cards when Kacmarcik was cut from high school sports teams. Speedkore’s high-end creations are a far cry from his first car, an American Motors Pac er. When his parents started Kapco in 1972, with Kacmarcik’s mother as the first shop floor employ ee, it would have been hard to predict the compa ny’s success.
The Kacmarcik Center for Human Perfor mance aims to open up a world of unimaginable possibilities for the Kacmarcik Enterprises em ployees and the wider community. It has a goal of touching 1 million lives annually.
“My 25-year-old worker who maybe thinks X,
Kapco owner Jim Kacmarcik says workers deserve a different approach, and his company is trying to deliver
who knows where he’s going to go or where she’s going to go and what they’re going to do,” Kacmar cik said. “We’re trying to unleash the mind and not have people be limited by their own thoughts of what they can do and where they can go.”
At its simplest, the KCHP (referred to as kaychip), is about learning and development for Kac marcik Enterprise employees. However, its ambi tions, both for employees and for the community are much grander. It is about helping people flour ish, allowing them to reach “the best possible pos sibility of their life,” said Gretchen Jameson, group president for human performance and social im pact at Kacmarcik Enterprises.
Employees will still learn the skills they need for new jobs, but the center is also offer ing classes on having a growth mindset, com munication, mindful ness exercises and much more. For the business, there are important measures like improved
productivity, employee satisfaction and engage ment, and even increased profitability. For the cen ter, a key metric is whether people are “flourishing.” That means measuring things like happiness and life satisfaction, mental and physical health, char acter and virtue, and close social relationships.
If it sounds different from how traditional manufacturers approach their people and human capital investments, it is meant to be.
“The work that a lot of teammates do in the factories is extremely difficult work, it’s hard work, I’ve done it. I’ve been there. Manipulating metal parts in machines and stuff like that is tiring, and they deserve a different kind of approach,” Kac marcik said.
The past two and a half years have also been far from the traditional way of doing business. There may have been lots of grief and turbulence, but Kacmarcik said it is important to learn from those experiences and assess how things might be different moving forward.
“Certainly, for us, this has been a time of great reflection and reimagining workers’ happiness and just what makes the difference,” Kacmarcik said.
When the COVID-19 pandemic hit, Kapco saw nearly every customer stop accepting shipments. Overnight, the company’s sales were sliced to less
than half of previous levels, Kacmarcik said.
Worrying about how to keep people employed, trying to work ahead and waiting out the storm soon gave way to a strong return in demand. Con sumers stuck at home with disposable income put that money to use.
“The manufacturing snapback that came shocked all of us,” Kacmarcik said.
Companies like Kapco quickly found them selves with almost too much work, and their cus tomers were struggling with certain finished goods as supply chain challenges began to emerge. There was plenty of demand, but Kapco’s customers were frequently changing their needs as they sought to produce what they could.
“We’d have semi loads of product ready on the dock to ship to a particular client or two, and they would say, ‘Sorry, don’t want it.’ We’d pull (the loads of product) back off, put them back in stock, grab a different subset of brackets and items. ... This kind of stuff was happening on a daily basis, literally, so planning and thinking ahead, I don’t want to say completely went out the window but, boy, it was never more strained,” Kacmarcik said.
The constant switching meant time lost to set ting up different parts, among other inefficiencies. The ongoing challenges of a tight labor market only
put into action, trust is earned.
knowledge and experience
Brown & Brown Insurance,
pride ourselves on building relationships
results-oriented
trust of Wisconsin’s
service
made things worse.
“All your lean manufacturing principles seem to fly out the window for a couple months as you’re just scrambling around trying to take care of what the customer is needing,” Kacmarcik said.
Going above and beyond for customers paid off with deeper relationships and comments like, “We never worried about you, you could always switch for us.”
Things may have begun to calm down, but the pandemic and its fallout have done a lot to reshape the workforce. Many people have re considered what they want from work and what they want from life, bringing new dynamics to every workplace.
“We, or others, can sit back I suppose and lament about it and say we have a worker shortage, we have issues ... and stick with your traditional ways, or you can reimagine what the new work force wants to be like,” Kacmarcik said.
For Kapco, reimaging its workforce starts with things like studying and understanding differenc es across generations of workers, developing a bet ter understanding of what each wants, needs and believes, and how each interacts with others.
In an era of low unemployment, changing at titudes and retiring baby boomers, manufacturers can’t afford to assume people will join their compa ny and have a 20- or 30-year career at one business.
“You’re not going to win, you’re not going to find the team, you’re not going to build the team,” Kac marcik said.
Kapco’s new approach requires an understand ing that the manufacturing world today is differ ent than what Kacmarcik grew up experiencing,
he added.
“Understanding that people are going to bless us with their time and talent for a period of time, might be a year, might be two, three, four years, might be a place where they need a job for awhile and their actual desire is to be a chef, or they want to be an auto mechanic,” Kacmarcik said. “We’re not afraid of someone who’d like to say, ‘I’d like to work for you for six months, and then I plan on do ing X.’ Great, come on in, and here’s how we get you working safe and letting people find their path.”
Kacmarcik acknowledged he previously would have been apprehensive of someone only planning to stay with the company for six months, just as many other business leaders might.
“You spend time training people and you’re looking like you want to get some investment back and you want them to stay with you for years and years,” he said. “I think that’s all changed.”
Just how is the Kacmarcik Center for Human Performance going about doing things different ly? Jameson said Kacmarcik is essentially asking KCHP to be “purveyors of an idea,” which she added “is inherently messy.”
“This sense that there is more that every hu man is uniquely designed to do and is worth the opportunity to develop. Every human is worth the opportunity of developing their potential,” she said.
The KCHP will have three primary focus areas. Its corporate learning and development work will help the businesses within Kacmarcik Enterprises. The center’s social impact work will seek to make its learning and development capabilities accessi ble to those who wouldn’t otherwise have access. Finally, Jameson and her team are tasked with ex
ploring what opportunities there are for a product or service related to the center’s work.
Jameson was quick to highlight the difference between training and learning. Pets are trained, she said, humans learn.
Training may help develop a skill or add some knowledge, “but that’s where a lot of training pro grams stop. Real learning changes my knowledge and my skills, but also three other things: It chang es my attitude, it changes my confidence, and it changes my commitment,” Jameson said.
Making changes in those additional areas mat ters because the intent is for KCHP to be centered on the person.
“When we think about the whole person and really helping them learn a job skill, I want more than just training them in ... how to run a press. I want to help them learn creative thinking and problem solving and (how to) expand their growth mindset and develop grit,” Jameson said. “That’s just going to give them what we would call a better flourishing, the best possible possibility of their life. And they’re worth it. They’re worth that.”
There are, of course, certain things a corporate learning and development program needs to ad dress. New hires have to be onboarded and in the manufacturing space that includes learning about safety and operating certain equipment.
Jameson said a new hire in the Kacmarcik En terprises industrial businesses will go through a 90-day learning experience to start. The program delivers knowledge and skills, but also includes check-ins every four or five days. Employees are surveyed on whether they find material interest ing, believe they can do the new tasks they are learning and how they feel about the material be ing useful on the job or in life.
Managing your inventory can be complicated if your inventory modules are not integrated with your general ledger. Did you receive inventory but no invoice to enter into your general ledger? Or maybe your inventory has shipped out but hasn’t been invoiced yet?
While this might not seem like a big issue at rst glance, it can cause signi cant problems during monthly reporting. Reconciling inventory to your general ledger must be synced, requiring an integrated system or manual intervention.
Reporting issues occur when inventory has been invoiced and is showing up in your expenses, but the warehouse hasn’t yet checked the inventory in. Or conversely, if the warehouse checks in the inventory, the invoice has not been entered in the accounts payable system. If this occurs over month-end, you will need to manually reconcile the inventory to the general ledger to ensure you have accurate reports. An integrated system will alleviate the need for manual adjustments.
When inventory reports are not synced, your nancial statements will be inaccurate if you don’t manually reconcile each month. This directly affects your margins and bottom-line net income. Why does it matter? You can’t measure your company's performance if you can’t rely on your nancial statement data.
Overestimating inventory may mean you have excess capital tied up in inventory that won’t be used timely, and you could risk buying too much at in ated prices, which will negatively impact your cost of goods. Underestimating inventory may lead to the inability to ll orders and meet customer demands.
A recession could create a de ationary period at some level when prices are lowered. During a recession, demand for products reduces and potentially drives costs down. As a result, a business carrying excess inventory could expose itself to additional nancial pain. The excess inventory acquired at a higher cost may need to be liquidated due to a lack of consumer interest. Be cautious about building excess inventory at higher prices. Monitor inventory levels and sales trends closely.
If you can’t align the systems, you should prepare a proof of inventory report from your inventory system. This report will be used to create a journal entry so that your ending inventory equals what’s in the inventory system. This creates a solid monthly process around inventory reconciliation until you can get an integrated system.
Consider a New or Updated System
Analyze your systems and work with an advisor to determine if you need a new system, or if there are add-ons to your existing system they can recommend.
Keep your support program current so that when issues like this arise, you can get support from your software company. They may have recommendations for add-on systems or modi cations to your current software package.
Robin“We intervene in a different way if we see those numbers dipping,” Jameson said.
Part of the experience for new hires is to meet with the KCHP’s learning experience design team.
“We learn from them what their past experiences have been with school and education because, by and large, I don’t think it’s an overstate ment to say that a lot of folks who are in this particular industry sector
have not necessarily had the most positive background with school,” Jameson said.
Beyond new hires, the vision is for the entire Kacmarcik Enterprise corporate family to have access to a life and career coaching experience that will help them figure out what their next steps will be.
The actual learning at the center
will not only include classes to help with upskilling or changing roles but will also range from developing and cultivating a growth mindset to com munication skills to wellbeing cours es in areas like yoga, breathwork or art therapy for stress management.
Other areas KCHP is working on include helping families with chil dren who have experienced trauma and opportunities for senior leaders to learn about systems thinking.
“Especially in manufacturing, if I’m going to make a choice A here, it impacts your choice B, C and D all the way over there, and if I’m not think ing about that, it actually makes prob lem solving harder (and) innovation trickier,” Jameson said.
On the surface, bringing a per son-centered approach – one that goes well beyond teaching the skills needed to do a job – to the manu facturing environment may seem challenging.
Kacmarcik said it is a seismic shift and the process involves a lot of change management, which can be tricky, “especially when you have a plethora of people in every different walk of life and a lot of historical, traditional, very appro priate and very effective ways to manufacture the product.”
“The big thing there is extraor dinary and repetitive communica tion, whereby you explain things to a much deeper level to some people,” he said. “There’s no memo or little shop meeting that’s going to explain all this stuff. It’s a core-value switch or an approach to different types of things that’s going to take an extend ed period of time to be fully living and breathing in every pocket and every corner of this company.”
Kacmarcik also said it will take time for the plans to reach every em ployee in the company and there will be pitfalls along the way.
“This isn’t all like rainbows type of thing, we try and sometimes we fall short,” he said.
For her part, Jameson said it has been fun to be the scholar on the shop floor as she works with her team to establish the center, adding she has not encountered much pushback from direct supervisors and opera tional employees. In fact, there’s been curiosity and questions about what objectives might be accomplished.
“It speaks to the old kind of mas ter-apprentice approach that has long been a part of manufacturing, which is the very best kind of educational model possible,” she said.
It may still be hard to see how es tablishing a new center and investing in a new learning and development approach translates to the business. Jameson said Kacmarcik’s view is there is “an ethical and moral imper ative” for the business to think about its people.
“When we put the person at the center, and we say, ‘Wow, how can we put you first?’ Guess what hap pens,” Jameson said. “All the produc tivity and profitability follow. So, it’s not won at the expense of the other by any stretch, but it’s actually a re ally strategic understanding of how investment in the people will deliver.”
“We manufacture metal parts and that’s kind of the endgame, and sometimes we say that’s the case,” Kacmarcik said. “But we really are working to affect people on a daily basis and trying to take care of their needs and wants along with ours, balance that all out as best we can.” n
SOMERVILLE, Massachusetts-based Formlabs, a 3D printing technology developer and manu facturer, opened a new regional headquarters in Milwaukee’s Third Ward last month.
The Milwaukee office, located at 220 E. Buf falo St., will add more than 100 jobs over the next three years and will play a key part in Formlabs’ efforts to address President Joe Biden’s Additive Manufacturing Forward initiative, which seeks to increase the use of additive manufacturing to improve supply chain resilience.
While 3D printing is not new, the idea that it should be implemented on a wide scale as a com plimentary technology to standard manufactur ing processes is, said Brian Nies, head of Ameri cas sales and Milwaukee office lead at Formlabs. Additive manufacturing can provide flexibility in how a part is designed, shorten lead times for certain parts and allow companies to increase the number of products they offer.
“Additive manufacturing as a whole and 3D printing really got a major boost with the pan demic because … when certain things weren’t able to be obtained anymore because of supply chain shortages, or if we needed to shift to make a different product because it was in high de mand, people who didn’t have flexibility in their
manufacturing process were at a disadvantage,” Nies said.
Formlabs offers its customers two primary 3D printing technologies: stereolithography (SLA) and a selective laser sintering (SLS) model. SLA models work well with several materials, provid ing users flexibility, while SLS models are target ed toward production-ready parts. A Formlabs setup can range from $5,000 to $50,000.
“The advantage with the size and the price point of what we offer is it isn’t restricted to only the biggest customers or biggest players. We see a lot of places bring in one or two (printers), like tool and die places, just to do jigs and fixtures. That just gives them another capability they didn’t have before,” Nies said.
As far as what kinds of manufacturers are using Formlabs’ printers, Nies said it’s “pretty broad across the spectrum” and both larger and smaller companies are moving into the space. Formlabs has seen success in the medical and dental industries and with manufacturers work ing with plastics.
It comes down to risk versus reward when looking at adopting 3D printing technology and while the benefits are numerous – supply chain flexibility, possible savings in production and add
ed independence – there are still several pitfalls.
Matthew Pearlson, founder of Wales-based PrintFoam, said while additive manufacturing is already being successfully used for rapid pro totyping and tooling, the industry is still several years out from 3D printing being used to make the “endgame” parts.
“The people who run big companies have been running those companies the same way for a long time, and they’re typically risk ad verse. Getting that step to the factory floor takes a super long time. So, what does that mean for additive technology? It means you have to wait a while,” Pearlson said.
There are few additive technologies that are currently able to solve the problems manufac turers are looking to address. Materials issues are a common example – there isn’t yet a ma terial that would allow a company to 3D print a product comparable to an athletic shoe or to replace a zinc part. Pearlson believes materials and throughput are the two main factors hold ing back the widespread adoption of 3D printing.
“There are very few products today that were designed from the ground up to be made in an additive way,” Pearlson said. “If you try to take a product or a part that is not designed for additive and make it in an additive process … you can physically do it, but economically it’s not go ing to make sense.”
Another factor holding back adoption of ad ditive manufacturing is simply a lack of educa tion in the area. Formlabs wants to address this issue through exposure to its products and com
engagement.
“By having (the new office) in this great, cen trally located place (near) downtown Milwau kee, it becomes much more accessible to people,” Nies said. “We want people to come to the office and try them out.”
The fact that there is an increasing number of younger engineers who are entering positions of leadership on manufacturing floors will also help the cause, as younger generations likely grew up having 3D printers in their labs and classrooms.
For Hartland-based Fathom Manufacturing, one of the country’s earliest adopters of additive manufacturing for metals and plastics, increased use of 3D printing means continued investment in new technologies.
The company’s Hartland headquarters has nearly 100 industrial 3D printers. Fathom has continued to make investments in new tech nology to address the manufacturing industry’s move to “Industry 4.0.” This new technology will also help manufacturers shift from primarily using additive manufacturing as a prototyping tool to using the technology as an actual means
of production.
“We’ve definitely seen from our customer base – not only here in Wisconsin, but also on a nation al level – a transition as the technology continues to mature and the material properties continue to mature,” said Ryan Martin, chief executive officer of Fathom Digital Manufacturing Corp.
Last year, Fathom invested over $1 million into a piece of 3D printing equipment used for metals. The equipment allows the company to make hundreds of aluminum components for customers. Fathom has also partnered with Minneapolis-based Evolve Additive Solutions, which has created a new 3D printing technolo gy, called STEP. The technology is almost like a photographic drum that allows users to create layers of material quicky. Evolve says its tech nology gives manufacturers the ability to reduce forecast estimates from one year to 90 days.
“You can make customizable parts – thou sands of them – with real material properties that are similar to injection molding at price points that make sense in the thousands,” Mar tin said.
He emphasized the fact that 3D printing technology is not meant to overtake standard processes like CNC machining or injection mold
ing. It should instead be used to drive efficiency in a way that is complimentary to those more traditional processes. Not every product should or can be 3D printed.
“I think you’re always going to see different applications where it makes sense. The number of applications where it does make sense is going to continue to grow exponentially,” Martin said.
He believes there will be more use cases for additive manufacturing and more widespread adoption in the next three to five years.
“If you’re not embracing some of these new manufacturing processes, you run the risk of be ing left behind,” Martin said. “It’s going to impact your competitiveness in the market.”
Pearlson echoed that sentiment, saying com panies need to realize the way things are made is changing and they need to start adjusting. He said PrintFoam has been “going gangbusters” and is adding new clients in the industrial sector who are looking to address energy and climate issues.
“I don’t know if COVID-19 accelerated things, I don’t know if President Biden’s program is ac celerating things, but my phone has been ring ing more and more every week as people realize they can’t keep doing business as usual for the next 50 years,” Pearlson said. n
IN AN IDEAL WORLD, manufacturing compa nies would see growth throughout the business. Revenues would grow, profits would increase and the organization would continue to move in a positive direction.
The real world, of course, is often far from ideal and the past few years have been full of ups and downs for manufacturers. Trade and tariff disputes in 2018 and 2019 gave way to pan demic-induced shutdowns. While some busi nesses made in-demand products or found ways to contribute in the early days of the pandemic, others saw their company’s existence threat ened. As shutdowns ended, demand from many consumers snapped back with travel limited and disposable income available.
While strong demand is certainly a welcome phenomenon for manufacturers, many quick ly found themselves facing new challenges as supply chains remained out of balance and it became difficult to get materials. Before long, businesses were passing along one price increase after another in an effort to remain profitable. Add in a tight labor market and rising wages and the picture only gets more complicated. A host of other factors, including government spending on pandemic relief and the war in Ukraine, have contributed to the inflationary environment pushing the Federal Reserve to raise interest rates and increase the risk of recession.
Much of what has shaped the economy in re cent years has been outside the control of man ufacturers, but business leaders still have plenty of levers to pull within their own company. At the BizTimes Media Next Generation Manufac turing Summit, a panel of executives from some of Wisconsin’s leading manufacturers will share lessons learned, best practices and other details from navigating, and growing, during the ups
and downs of the past few years.
The panel discussion will feature Tom Dan neker, president and chief executive officer of Menomonee Falls-based flexible packaging maker Glenroy Inc., Benjamin Gover, chief operating of ficer of West Allis-based architectural millwork firm Glenn Rieder LLC, Pat Koppa, president of Milwaukee-based vertical conveyor and lift mak er PFlow Industries, JP Moran, president and CEO of Pleasant Prairie-based label and lid maker LMI Packaging Solutions, and Sachin Shivaram, CEO of Manitowoc-based Wisconsin Aluminum Foundry.
Panel topics will dig deeper into the chal lenges facing manufactures, including:
» Tight labor markets: Beyond signing bonus es and rising wages, panelists will address how they are trying to take new approaches to finding their current and future work force. Shirvaram will discuss Wisconsin Aluminum Foundry’s new training center, which has helped cut new hire turnover from around 100% to 15% while helping the company attract a more diverse workforce. Moran will share insights on how LMI has tapped into work release programs from the Department of Corrections and a unique partnership with Carthage College to fill workforce needs, including the role of buyin from long-tenured employees to maintain company culture.
» Managing business ups and downs: Growing revenue is certainly a welcome thing for any business, but it can come with challenges. Koppa and PFlow, for ex ample, saw a dramatic increase in business from the e-commerce market in recent years, only to see a pullback in demand this year. He’ll address how the company tried to handle the increase in business
without over investing or taking on too much risk. Koppa will also discuss how PFlow is navigating the downswing in business by looking to some of the other markets it serves.
» Navigating supply chain and pricing cha os: Nearly every manufacturer has faced some sort of supply chain disruption over the past few years and while the worst may have passed, the recently averted railroad strike showed just how easily the system can be disrupted. Panelists will discuss how they handled issues by get ting more directly involved in sourcing and quoting to fostering and maintaining quality relationships with both suppliers and customers.
» Growing company culture: Every com pany has its own unique culture and ex ecutives have a unique ability to shape it through their actions. Danneker and Shivaram, for example, are leading fami ly-owned businesses as non-family CEOs, so both have worked to understand the val ues of the family owners while also driving the business forward. Moran is the third generation in his family to lead LMI, which comes with pro and cons to handle. Koppa is leading an employee-owned business while trying to manage through a difficult period. Each businesses’ experience offers lessons learned for other manufacturers.
Following the panel, there will be breakout sessions on leadership strategies for an effective safety program, improving a business with sus tainability, and taking a closer look at manufac turing in southeastern Wisconsin.
The Next Generation Manufacturing Sum mit will take place on Tuesday, Oct. 11, from 2-6:30 p.m. at the Brookfield Conference Center. Presented by BizTimes Media, the program is sponsored by WMEP Manufacturing Solutions, BMO Harris Bank, Brown & Brown and support ing sponsor Vistage. n
BizTimes Milwaukee is proud to present its second showcase of Notable Women in Manufacturing, spotlighting accomplished professionals throughout the region. The women profiled here all hold key leadership positions at manufacturers in southeastern Wisconsin. Their accomplishments set an example to shape a better future for the area.
METHODOLOGY: The honorees did not pay to be included. Their profiles were drawn from nomination materials. This list features only individuals for whom nominations were submitted and accepted after a review by our editorial team. To qualify for the list, nominees must be based in southeastern Wisconsin and work for a manufacturing company based in the region. They must currently serve in a senior level role at their firm (three levels or less from the company CEO).
Lesley Hill is following in the footsteps of her father and com pany founder, the late William Boles.
Hill joined Pewaukee-based Mixer Systems in 1992 as a new graduate from the Milwaukee Institute of Art & Design. She started by designing the company’s service manuals and as sumed more responsibility over the years in directing marketing. She was appointed to the board of directors in 2011 (the only female mem ber) and became a vice president in 2014 after the death of her father.
“Lesley’s father had such a positive impact on the industry. She’s dedicated to making products he would be proud of,” said Doug Du ley, president at Mixer Systems.
“During the (2007-09) recession, Lesley Hill strategically empha sized Mixer’s parts business to help customers maintain older equipment in lieu of purchasing new mixers,” said Neil Becker, pro prietor of Becker Design. “She also developed protocols to keep the Mixer workforce healthy and productive during the (COVID-19) pan demic and avoid a prolonged shutdown.”
Rachael Conrad leads a global team of 3,000 people, including the customer success team, in an area that is increasingly important to Milwau kee-based Rockwell Automation and the advanced manufacturing industry.
Under her leadership, the team has expanded Rockwell’s portfolio of data-driven services in areas such as sustainability, safety and productivity. Conrad also oversees cybersecurity services.
Conrad joined Rockwell’s leadership development program in 1997. She is an industrial engineer and was recognized as a 2017 STEP Ahead award recipient by the Manufacturing Institute. She is active in Rockwell’s Professional Women’s Council and the Society of Wom en Engineers.
“Rachael represents the leader that I, myself, and all who interact with her aspire to be,” said Angela Rapko, who reports to Conrad as North America vice president for lifecycle services. “She has driven significant change across a very mature organization by putting her people first, developing and communicating a clear strategy and empowering the organization to execute on it.”
Stacy Peterson started Connoils in 2007, and in 2019, she opened a new green technology certified processing facility in Big Bend.
“Her goal is to listen, learn and educate to im prove the health and vitality of peoples’ lives by creating, selling and growing a product line of nutritionally stable ingredients and bulk supplements for brands,” said Art Flater, owner and principal at Central Office Systems.
“Stacy has helped make Connoils known for internally stabilized or ganic oils, oil powders and a variety of specialty ingredients used in various wellness, nutraceuticals, pet nutrition, sports nutrition and beauty products,” Flater said. “Her manufacturing leadership means they have been able to achieve superior microencapsulation using cutting-edge equipment, which preserves the integrity of their prod ucts through advanced low-temperature drying techniques.”
“Connoils employs well over 50% female team members, breaking the mold of manufacturing as mostly a male-dominated field,” he added. “I remember meeting one of her team members for the first time. Her team member said to me quietly, out of Stacy’s earshot: ‘Stacy rocks!’”
Congratulations to Rachael Conrad, Rockwell Automation’s Vice President and General Manager of Customer Support and Maintenance, for being named one of Milwaukee’s Notable Women in Manufacturing.
At Rockwell Automation, we connect the imaginations of people with the potential of technology to expand what is humanly possible.
Cindy Lapidakis joined Darienbased Royal Basket Trucks Inc. in 2007. At that time, annual sales were less than $4 million. In her role, Lapidakis is directly responsible for over all sales growth. For fiscal 2022, the company expects sales of more than $38 million, a 16% annual growth rate over the 15-year period she has been on staff, said president Tom Carney.
The company started by selling vinyl and canvas laundry carts, largely through catalogs. Under Lapidakis’ sales leadership, the company has grown its product lines to include metal housekeeping carts, plastic rotationally molded carts, and carts made from PVC materials.
“Cindy has strengths when dealing with large accounts,” said Car ney. “She negotiates product placement in the various catalogs and other media as well as new product introductions and pricing. Whether it is a one-on-one meeting or a presentation to a large group, Cindy represents Royal as the company with ‘containers on wheels’ that provides all sorts of material handling solutions.”
Ronie Jaeger started her career at Town of Genesee-based Generac Power Systems in 2003, the day a major blackout hit the East Coast. An educator by training, she made the shift to customer satisfaction with Generac at a time when power outages were drawing the attention of homeowners across the country.
Jaeger leads Generac’s customer support team in her current role as director of customer experience. She collaborates with the quali ty team to provide real-time customer feedback on products.
Last year, Jaeger led an initiative to enhance Generac’s self-service customer support initiatives using an automated system, enabling customers to find answers to their problems without the need to contact a customer support specialist. This program has reduced the time that her team spends fielding basic questions.
“Over her nearly 20-year tenure at Generac, Ronie has shown a tre mendous drive and dedication to do right by our customers, leading the customer experience function with a people-first mentality,” said Carrie Toth, vice president of customer experience.
Heidi Balestrieri is not only a passionate and effective engineer at Oconomowoc-based Sentry Equip ment but within the larger community as well, colleagues say.
At Sentry Equipment, Balestrieri reviews operation and engineering metrics, identifies patterns in those metrics, and then uses the pat terns to identify opportunities for improvement.
“Her focus has supported the development of a long-term engineer ing vision and multiple product improvements, including BOM config urators, updates, and modifications to Low-E and Bulk Solid product lines,” said Kate Moreland, digital marketing manager at Sentry.
Outside of Sentry, Balestrieri is a supporter of children and women in STEM. She has partnered with STEM Forward, Girl Scouts of America and Society of Women Engineers.
“Under her leadership, Sentry Equipment has seen an improvement in focus on innovation and an increase in onboarded female engi neers at the full-time and internship level. We credit this increase to Heidi’s natural leadership style. She believes there is always an opportunity to learn something, regardless of the project,” Moreland said.
When Aly Ernst joined Town of Gene see-based Generac Power Systems seven years ago, it was the international business sector that captured her attention. Being bilingual in Spanish and English allowed her to work with Latin American and global audiences, including acquired companies that had notable differences with their U.S.-based coun terparts.
This perspective has helped shape her strategy for operations as well as her leadership style.
Today, Ernst is the director of business solutions for order to cash, a position developed to help drive enhancements in the OTC process. Colleagues say her solutions have helped streamline and strength en several areas of the buying process, taking a holistic view of sales, order management, planning, manufacturing, logistics, cus tomer care, analysis and post-sales procedures. The effects of her processes have made an impact on delivery and inventory metrics.
“No matter the task at hand, Aly always goes the extra mile, con tinuously showing care and dedication to every part of the OTC process,” said Tim Jones, vice president of global supply chain at Generac.
As Oconomowoc-based Sentry Equipment’s first female shop manager, Megan Patterson’s primary focus has been improving Sentry’s internal processes for on-time delivery and streamlining the customer experience.
“Her passion for process improvement resulted in successfully establishing Quick Response Manufacturing at Sentry Equipment,” said Kate Moreland, digital marketing manager at Sentry.
Patterson also led a project to help Sentry see demand in the system to order materials sooner to help with supply chain issues and lead times.
“The only constant in life is change. And Sentry believes in contin uous improvement,” said Patterson. “This allows people to explore their passions while improving overall operations. Be willing to learn and don’t define yourself on one single path. Do the thing that scares you for good outcomes – you miss out on so much when you run instead of embracing the challenge.”
Patterson followed her own philosophy and has been certified in production and inventory management and is Sentry’s resident QRM expert.
Von Rolon-Gonzalez, director of operations at Cedarburg-based PartsBadger, has a fundamental focus on support for all teams, knowing that building systems and providing training will lead to growth for individuals, colleagues say.
“I can say with confidence that PartsBadger’s continued success is a direct result of Von’s efforts and leadership,” said Alex Sparr, director of innovation deployment. “Since taking on the director of operations role, she has bridged the gap between all departments and continues to drive forward our vision of fundamentally trans forming manufacturing. She is extremely detail oriented and goes above and beyond all reasonable expectations to get objectives across the finish line.”
Rolon-Gonzalez was a participant in the ScaleUp Milwaukee program and has been part of PartsBadger’s recognitions from Inc. 5000, Fu ture 50 and Ozaukee County Business of the Year.
“She is integrated in all areas of PartsBadger and has shown ex ceptional ability to work with all groups and systems,” said Bran don Spenneberg, director of marketing. “Von has built out various sales-team verticals, improved shipping efficiencies, expanded the capability offering and designed a system to hold inventory for cus tomers.”
At companies across southeast Wisconsin, notable executives are running businesses, navigating company restructurings, serving on boards, running marketing departments, and investing in growth throughout the region. The notable individuals profiled in these categories are nominated by their peers at work and in the community.
Notable Heroes in Health Care salutes the accomplishments of people and organizations making a positive difference on the front lines of health care.
Nomination Deadline: November 4, 2022
Issue Date: December 12, 2022
Notable Leaders in Higher Education
Nomination deadline: December 16, 2022
Issue date: January 23, 2023
Notable BIPOC Executives Nomination deadline: January 13, 2023
Issue date: February 20, 2023
Notable Women in STEM
Nomination deadline: February 17, 2023
Issue date: March 27, 2023
Notable Women in Construction & Design Nomination deadline: March 10, 2023
Issue date: April 17, 2023
Notable Mortgage Brokers and Title Officers
Nomination deadline: April 7, 2023
Issue date: May 15, 2023
Notable Nonprofit Board Leaders Nomination deadline: April 28, 2023
Issue date: June 5, 2023
Notable Leaders in Accounting Nomination deadline: June 16, 2023
Issue date: July 24, 2023
Notable Alumni
Nomination deadline: July 14, 2023
Issue date: August 21, 2023
Rising Stars in Manufacturing
Nomination deadline: September 1, 2023
Issue date: October 9, 2023
Notable Women in Insurance
Nomination deadline: September 15, 2023
Issue date: October 23, 2023
Notable Veterans
Nomination deadline: September 29, 2023
Issue date: November 6, 2023
Notable Women in Hospitality
Nomination deadline: October 13, 2023
Issue date: November 20, 2023
Notable Health Care Leaders
Nomination deadline: November 3, 2023
Issue date: December 11, 2023
BUILDING A WORLD-CLASS culture is hard work.
As a business owner or CEO, you must be in tentional about it, then scratch and claw to keep it. In normal times, it’s difficult at best. Add remote or hybrid workforces into the mix, and you have a po tential for disaster.
In my work as a Vistage chair and executive coach, I speak to CEOs daily about their workplace culture. Every day, I hear a story about an employ ee trampling on the company’s core values. The reasons are too numerous to list. But a major one is that those words mean something different for everyone.
I’m not against core values if they truly speak to what the company stands for and practices. Re spect is a core value that many companies espouse. What does respect mean to you? Do you truly be lieve that everyone else in your organization de fines respect the same way you do?
I had the pleasure of bringing in David J. Fried man of CultureWise to speak to my Vistage group recently. I’ve been taught that you don’t have a real business if you don’t have core values, along with mission and vision statements.
Friedman, however, says you don’t need core values if you have clearly stated behaviors that are ritualized and instilled throughout the organi zation. The reason is that values are abstract ideas, but you can see behaviors.
Friedman has an eight-step formula for build ing a lasting world-class culture. The first two are where you win or lose with this.
Do the complex work of listing a set of behav iors that will help the organization succeed.
Ritz-Carlton Hotel Co. has 20 Ritz-Carlton Ba sics. For example: “Never lose a guest. Instant guest pacification is the responsibility of each employee. Whoever receives a complaint will own it, resolve it to the guest’s satisfaction and record it.”
I recommend you start your own list, then bring it to your team members to see what they think should be added or deleted.
Each behavior should include a sentence or two of explanation. Every description should answer the question: What do you want people to do?
Here’s one of my company behaviors: “Winwin, or I take my ball and go home. Make sure ev ery interaction is a win for all parties involved or we don’t do business.” This is in my vernacular and speaks to the culture of my practice.
A word of caution: Avoid lingo, acronyms and jargon.
You want to engrain the behaviors into the company culture. When watching a professional sporting event, do you ever have to guess if they will play the National Anthem? Of course not! That’s an example of a ritual. You know it’s coming, and it doesn’t take you by surprise.
Rituals help create consistency. They help you sustain your efforts around the desired behaviors when new initiatives inevitably begin to take pre cedence. Every day, at every scheduled meeting at every Ritz-Carlton around the globe, employees work on the same “basic” for that day.
Tomorrow, they will all work on the next one, and so on. When they complete the 20th basic, they will start all over again at Basic Number One and cycle through those. It’s no wonder that their service is world class. Everyone, from the CEO to the landscapers, knows the basics.
One great way to create a ritual is to start every
scheduled meeting with the ritual of the week (dai ly is probably too much for most companies). Then, spend only the first three or four minutes discuss ing the behavior before moving through the rest of the agenda.
The remaining steps Friedman lists for creating a world-class culture are:
» Select the right people
» Integrate (onboarding)
» Make your culture visible
» Coach
» Lead by example
» Create accountability
I’m convinced this works. On my one-page plans with my clients, I’m changing the “values” space to “behaviors.”
Good companies have good cultures by chance. World-class companies have great cultures by de sign. What kind of company do you want? The choice is yours. n
Offer opportunities for all to be heard and supported, while sharing credit
I AM VERY PROUD to introduce you to my son, Jonathan Waldbauer (known in some circles as Jon).
Jonathan works for a significant nonprofit in our community. He is also employed by Come dySportz Milwaukee, where comedy is played as a sport with two teams of improvisational perform ers competing in various improv games. If you have not had the experience, I encourage you to check it out!
Jonathan and I often talk about leadership and the current challenges for leaders in this world of chaos, divisiveness and uncertainty. In listening to him, I began to realize that there are lessons from improv that, when applied, enhance leadership ef fectiveness.
Jonathan agreed that he would be my partner in writing this article. I posed the following ques tions for his consideration:
WE KNOW THAT THERE ARE NO SCRIPTS FOR EFFECTIVE LEADERSHIP. WHAT DO YOU THINK LEADERS MIGHT LEARN FROM IMPROV?
“Improv stands on a foundation of listening and building together. That process begins with genuinely inviting others’ input and creating an environment in which folks feel safe and support ed when they share their ideas. People will engage more passionately when they know they’re actual ly being heard. Creating that space invites vulner
ability, so it’s important for leaders to actively show support for ideas that are offered.
“Improv thrives on a ‘yes-and’ philosophy, in which we validate an idea and develop it collabora tively. If someone shares an idea and it’s shot down without further discussion, you’ve said ‘no’ to the idea and also to the person. You’ve directly discour aged future creativity, collaboration and innova tion, and indirectly taught your teammates that their ideas will be scrutinized should they choose to participate.
“Alternately, embracing the offer, even if we’re only taking a piece of it, creates the seeds for the next idea. Not all of it may be gold or even usable. However, it’s valuable in advancing the process. You’re fostering an atmosphere in which people are celebrated and supported for what they bring to the table. Leaders need to take that next step, though –the ‘and’ of the ‘yes-and’ – because showing support for an idea without following it with action, will be experienced as performative and hollow.
“The hardest part of fostering an environment of creativity and support using the principles of improv requires continued work to dismantle the walls we’ve put up over the years as we’ve accumu lated experiences, responsibilities and traumas that teach us that it’s safer to say ‘no.’”
“Businesses are focused on deliverables and deadlines; we know what needs to get done by when, and there are consequences if goals are not met. Because improv isn’t driven by the same prin ciples, taking the time to practice – and play – can feel like it’s moving us laterally, if not away from the end goal within a business environment. Incor porating an additional creative thinking or brain storming-style session when an organization has already been operating within specific strategic pa rameters and timelines can feel like a burden, espe cially since there aren’t always tangible takeaways.
“However, when leaders take a step back from their processes to access the bigger picture, they’ll note that fostering the ‘yes-and’ environment can create an energy that ripples through the work, through the process and through solutions. Lead
ers are likely to see, that offering opportunities for all voices to be heard and supported, while sharing credit, can create a workplace in which people feel empowered to take ownership, celebrate innova tion and make bold decisions.
“Leaders who incorporate elements of improv into their workplaces may not see immediate change in the organizations’ output, yet they will be participating in a transformation of the work process itself with long term ramifications that po sition organizations for success.”
“I’ve been a fan of comedy since my dad first showed me tapes of his favorites from his youth, including Red Skelton, The Three Stooges and the Marx Brothers.
“Learning, performing and teaching improv has been transformative for me. Improv has of fered me an avenue to become a lot more comfort able in my own skin. I believe improv can be used in conjunction with other tools to help facilitate personal and professional growth. At the very least, I’m practiced in listening and collaborating, and those are wonderful tools to bring into any new challenge.” n
Karen Vernal is an executive coach and consultant with Vernal LLC, a Milwaukeebased leadership and organizational firm. She can be reached at Karen@ccvernal.com.
Editor’snote:Followingisanexcerptfromthebook
“Live As A Leader: Tools and Inspiration to Trans form Yourself, Your Team, and Your Life,” by Aleta Norris, Nancy Lewis and John Rutkiewicz.
IN OUR OWN LIVES, we recognize how a variety of complex factors shape our actions. We know if we showed up late for an appointment, it could be because the baby needed a diaper change right be fore we walked out the door, or we hit traffic when a car accident closed down the freeway.
But as we observe others, we only know what we see on the surface, and we make assumptions. If you were late, I might assume that it’s because you can’t stick to a schedule, you’re lazy, or you don’t view timeliness as a priority.
In psychology, this is called the fundamental attribution error. This means that for ourselves, we ascribe all the situations and environmental condi tions that we know went into shaping our actions. But in others, we only see the surface, so we don’t stop to think about everything they may be strug gling with, thinking about or facing. No one holds a sign around their neck that says, “I’m worried about my mother’s health while she gets medical tests today, and that’s why I seem distant at today’s meeting.” Or, “I have a special needs child, and that is what makes my schedule less predictable than others.”
Seeing someone check out at a meeting, we
may think they’re disengaged or just don’t care about this project. Or working with someone who requires more flexibility in their schedule may feel unfair unless you realize the unseen challenges.
It takes time and effort to get at the true moti vations of others. But like peeling an onion, there are always more layers than what you see on the surface.
One way to begin softening our very human tendency toward fundamental attribution error is a practice called sonder. You can practice right now, especially if you are in public. The idea of sonder refers to the profound feeling of realizing that ev eryone, including strangers you pass on the street, has a life as rich and complex as your own. Practice sonder on the street, the train, a coffee shop or any where people are around.
Right now, for instance, we’re in a coffee shop on a Saturday morning. An older man, perhaps in his late 70s, is sitting side-by-side with a man in his 20s with similar features, probably his grandson. The older man has close-cropped white hair, and the younger man has dark hair, tattoos, a trendy haircut, and new clothes. They come from differ ent generations. They likely have a different vocab ulary and value different things at distinct stages in their lives. But they are watching a soccer game together on a tablet in front of them. They both love soccer. Grandpa played professionally in Europe when he was younger, and some of his grandson’s fondest memories from his own childhood were the times when Grandpa played soccer with him in the backyard, teaching him how to dribble and pass. And Grandpa attended every game his grand son played in middle school and high school. Today, they’re coming together to watch Grandpa’s old team in the championship. Soccer has been their common passion for bridging a divide of maybe 40 or 50 years. They understand each other through it, and their bond runs deep.
Or at least that could be what we tell if we glimpse beneath the surface. Every person has a story.
Look at the people surrounding you right now or think about the people you saw on the street to day or in the restaurant at lunch. Realize that they all have lived rich and full lives just like you, full
of hardships and pain, hopes and dreams, love and heartbreak, with boring, mundane tasks and mo ments of pure joy. They all have perspectives on life and belief systems and goals for the future.
Now, you could pick any one of those people and, through sonder, imagine what their story is like, as we did with the two men in the coffee shop. Was the story we told ourselves about their lives and relationship correct? We’ll never know! But that’s not the point. The point is to open ourselves up to the realization that rich and complex possibil ities exist in the lives of everyone we meet.
The same is true for the people you lead.
Remember that we can see below the surface of our own actions, but we don’t automatically think about the backstories that drive and shape the lives and actions of other people, including our employ ees. It takes an extra effort to see what’s driving their attitudes, beliefs and actions. For leaders, it’s necessary to take an additional step and learn about the deeper motivations of your team. n
Aleta Norris is partner and co-founder of Brookfield-based Living As A Leader, a leadership training, coaching and consulting firm. She can be reached at ANorris@ LivingAsALeader.com. Learn more about her book at: livingasaleader.com/book.
Remember that everyone has a rich, complex life –like yours
The past two years has seen the de cay of the global supply chain as we know it.
A recent article by McKinsey & Co. warns that the immediate effects of supply chain disruption are only the tip of the
iceberg: “In fact, they may be overtaken in the long term by slower moving but more permanent ef fects on supply chains occurring beneath the sur face.”
As volatility persists, the authors argue that companies should prioritize “structural reform” over short-term solutions to restore supply chain resilience. They break down the process in three stages:
A reactive response to a supply chain snafu (think: expedited delivery service and emergen cy shipments) may provide a short-term fix, but won’t help much in the long run. The McKinsey article says CEOs should “consider implement ing cross-silo efforts that ensure an agile re sponse to fast-moving events.” Leaders should also encourage teams and suppliers to follow through on the more difficult long-term chang es put in place.
This phase involves establishing a “nerve cen ter” that coordinates and manages proactive re sponses to various issues that may arise; planning for extreme supply-and-demand disruptions by placing orders early, allowing extra time for deliv ery and accounting for higher costs; and reevalu ating “just-in-time strategies” by potentially finding new suppliers, redesigning networks, resetting inventory targets or sourcing locally or regionally.
As companies endure the often-difficult jour ney to supply chain resilience, put structural im provements to the test by creating “what-if scenar ios” that can be tested quickly, and then prioritize and mitigate the parts of the supply chain that fail most often, according to the article. Construct a digital twin – a virtual replica of a business’ opera tion – on which to test these scenarios before imple menting them in the real world. n
Trefoil Group, an integrated marketing agency, has promoted Jill Schroeder to President, a newly created position. In this role, Jill is responsible for managing the agency, while continuing to play a key role in the design and implementation of both longterm strategic and short-term operational plans. “Jill has been instrumental in accelerating our success, said Mary Scheibel, CEO. “She is an extremely talented and proven agency leader with a passion for building teams and creating sound marketing strategies that drive client growth and value.”
Wintrust Commercial Banking at Town Bank, N.A. welcomes new Senior Vice President
Wintrust Commercial Banking at Town Bank, N.A. is proud to welcome Senior Vice President of Middle Market Lending Dan Frazier. Dan is a financial services executive with over 30 years of experience in management, business development, client relationship development, structuring, and credit underwriting for middle market companies throughout the state of Wisconsin. He has developed strong and trusted relationships with business owners and management to bring a wide range of resources, ideas and solutions to meet their growth and efficiency goals.
Gimbel, Reilly, Guerin & Brown LLP Welcomes Attorney John D. McNally
The Milwaukee, Wisconsin based trial and litigation law firm of Gimbel, Reilly, Guerin & Brown LLP (GRGB) is pleased to announce the addition of Attorney John D. McNally to the firm’s civil and fiduciary litigation team.
Patricia Torres Nájera leads MATC community ed, Hispanic-Serving Institution work, engagement
Dr. Torres Nájera will ensure Hispanic-Serving Institution (HSI) standards for excellence collegewide, execute strategic initiatives, and forge strong bonds with community-based organizations, school districts and other partners.
Boldt promotes John Huggett to Vice President of Central Operations
Boldt, a 133-yearold national construction company has promoted John Huggett to Vice President of Central Operations. John will provide overall leadership for the Company’s Central Operations offices in the Milwaukee, Madison, and Chicago markets.
First Business Bank Promotes Chase Kostichka to Senior Vice President
First Business Bank announces the promotion of Chase Kostichka to Senior Vice President - Commercial Real Estate Banking. He has more than 15 years of experience in financial services helping clients grow their businesses and avoid financial risk.
CITY, COUNTY, STATE, AND ZIP+4): BizTimes Media LLC, 126 N Jefferson St, Suite 403, Milwaukee WI 53202-6120, Milwaukee County.
Person: Dan Meyer. Phone: 414-277-8181
MAILING ADDRESS OF HEADQUARTERS OR GENERAL BUSINESS OFFICE OF PUBLISHER: BizTimes Media LLC, 126 N Jefferson St, Suite 403, Milwaukee WI 53202-6120
NAMES AND COMPLETE MAILING ADDRESSES OF PUBLISHER, EDITOR, AND MANAGING EDITOR:
Dan Meyer - 126 N Jefferson St, Suite 403, Milwaukee WI 53202-6120
Editor: Andrew Weiland - 126 N Jefferson St, Suite 403, Milwaukee WI 53202-6120
OWNER: Dan Meyer - 126 N Jefferson St, Suite 403, Milwaukee WI 53202-6120
11. KNOWN BONDHOLDERS, MORTGAGEES, AND OTHER SECURITY HOLDERS OWNING OR HOLDING 1 PERCENT OR MORE OF TOTAL AMOUNT OF BONDS, MORTGAGES OR OTHER SECURITIES: None
TAX STATUS: Has not changed during preceding 12 months
PUBLICATION TITLE: BizTimes
Dan Meyer, Publisher, September 30, 2022
A little more than a year after unveiling plans for an $80 million multi-sport facility on Milwaukee’s north side, organizers behind The Opportunity Center project are getting a $5 million boost toward their fundraising goal from Bader Philanthropies Inc.
The Milwaukee-based nonprofit committed $5 million over five years to the development of the project, which is planned for 22 acres at 4206 N. Green Bay Ave., near the border of Milwaukee and Glendale.
Envisioned as the “first ur ban sports center of its kind,” the 300,000-square-foot facility would be designed to make sports and other wellness programming ac cessible to those with physical and developmental disabilities.
Project leaders Franklin Cum berbatch, vice president of engage ment for Bader Philanthropies, and Damian Buchman, founder of The Ability Center in Wauwatosa, did not disclose the amount of money raised for the project thus far. The original goal was to reach $9 million by the end of last year, followed by the rest of the $80 million to $100 million total by 2024. Leaders ex pect the facility to be built and open within three to five years.
The Opportunity Center also named past board chair David
Cooks as president and chief ex ecutive officer. Cooks has used a wheelchair since the age of 15, when he experienced a spinal an eurysm as a high school basketball player in Milwaukee. Cooks is now an author and motivational speak er, having built a successful career around finance, sports and educa tion, including 17 years as a teacher and coach at Marquette University High School.
The Opportunity Center’s lob by will include a community gather ing space, and the second floor will house spaces for education, men torship and community gatherings. Another highlight of the center will be a 300-meter track and field facil ity that is universally inclusive.
“We’re going to supplement what kids are involved in during the school year,” said Cooks. “The Opportunity Center will serve the whole person, not just serve to de velop athletes. Ideally, we’d love to see people of all abilities from Mil waukee and the surrounding mu nicipalities of Whitefish Bay, Shore wood and Glendale running around a 300-meter track. I see young children, disabled veterans and all races being active together, and having interactions you do not see anywhere else in our community.”
— Ashley Smart , staff writer
The Thiensville-Mequon Rotary Club will host its annual Fall into Comedy Night fundraiser on Thursday, Oct. 13, from 6 p.m. to 9 p.m. at the River Club of Mequon, 12400 N. Ville Du Parc Drive in Mequon.
Bloom360 Learning Community will host its major fundraiser and community event, The Bloom Social 2022, on Saturday, Oct. 15, from 7 p.m. to 10 p.m. at its facility in East Troy, N8921 Stone School Road. The event supports Bloom360’s educational programs for children with neurodiverse needs.
The Germantown Community Coalition will host a fundraiser on Sunday, Oct. 23, from noon to 3:30 p.m. at Bub’s Irish Pub, N116 W16218 Main Street in Germantown. The event supports GCC’s scholarship fund, which helps underserved students cover the cost of higher education, including trade schools, colleges and universities.
Phoenix Investors and the Crivello Family Foundation matched contributions up to $75,000 during a fundraiser for Kinship Community Food Center, helping the nonprofit reach its goal of $150,000. The event supported the center’s Mission Internship Program, a service-based initiative for young adults aged 21 through 26. | Acts Housing raised more than $450,000 from the annual Neighborhood Table fundraising event, which celebrates the more than 3,214 families it has helped purchase homes over the past 26 years.
Address: 223 Wisconsin Ave., Waukesha, WI 53186 1-844-WIS-HOPE | wishope.org Facebook: facebook.com/projectwishope
Year founded: 2016
Mission statement: Project WisHope is a 501(c)(3) nonprofit, peer-run recovery community organization located in the Milwaukee and Waukesha areas and serving the state of Wisconsin. Our mission is to provide resources, education, advocacy and peer support to Wisconsin’s recovery community members, including those directly impacted by addiction and mental health conditions and their family members, friends and allies.
Primary focus of your nonprofit organization: Substance abuse and mental health treatment.
Other focuses of your nonprofit organization: Recovery housing, recovery counseling, job and lifeskill training.
Number of employees at this location: 30
Key donors: Waukesha State Bank, Carroll University, Metal Tek,
Waukesha County Community Foundation
Executive leadership: Peter Brunzelle, executive director
Board of directors: Peter Brunzelle, Carrie Boisvert, Brian McQuestion and Ryan Rehak
Is your organization actively seeking board members for the upcoming term? No
Ways the business community can help your nonprofit: Donating to our Recovery Housing Capital Campaign; working with our Recovery Business Association to help those in recovery in the workplace; sharing our 24/7 hotline, 1-844-WIS-HOPE, with those in need.
Key fundraising events: BOOze Free Halloween Party, Oct. 15 at Inmoxicated sober bar in Racine; There’s No Place Like Home Gala, May 3 at Sixth Floor MKE in Milwaukee.
VOLUME 28, NUMBER 11 OCT 10, 2022
126 N. Jefferson St., Suite 403, Milwaukee, WI 53202-6120
PHONE: 414-277-8181
FAX: 414-277-8191
WEBSITE: www.biztimes.com
CIRCULATION: 414-336-7100 | circulation@biztimes.com
ADVERTISING: 414-336-7112 | advertising@biztimes.com
EDITORIAL: 414-336-7120 | andrew.weiland@biztimes.com
REPRINTS: 414-336-7100 | reprints@biztimes.com
PUBLISHER / OWNER
Dan Meyer dan.meyer@biztimes.com
DIRECTOR OF OPERATIONS
Mary Ernst mary.ernst@biztimes.com
COMMUNITY ENGAGEMENT / OWNER
Kate Meyer kate.meyer@biztimes.com
EDITORIAL
EDITOR Andrew Weiland andrew.weiland@biztimes.com
MANAGING EDITOR
Arthur Thomas arthur.thomas@biztimes.com
ASSOCIATE EDITOR
Maredithe Meyer maredithe.meyer@biztimes.com
REPORTER
Ashley Smart ashley.smart@biztimes.com
REPORTER
Cara Spoto cara.spoto@biztimes.com
This March 1947 scene shows large manufacturing equipment at Quirk Co. in Cudahy, with a worker observing equipment in the center left of the photo. The facility was located at 3364 E. Layton Ave., which today is the site of an NPS Holdings converting plant.
— Photo courtesy Historic Photo Collection / Milwaukee Public Library
THE WISCONSIN DEPARTMENT of Trans portation is working on a $300 million plan to rebuild portions of I-794 between Milwaukee Street in downtown Milwaukee and the Hoan Bridge.
WisDOT is seeking public comments on the project. Some, including environmental advocacy group 1,000 Friends of Wisconsin, say that instead of spending $300 million to rebuild part of I-794, a major portion of the freeway should be torn down, replacing it with a boulevard to eliminate the barrier it creates between downtown and the Third Ward and free up a large amount valuable real estate for new development.
That would be an extremely bold move with potential to drastically improve the southern edge of downtown and the northern edge of the Third Ward. But there would be a lot to consider and study, including cost and traffic impact.
I-794 is a key link between downtown
and the south shore, including the city’s Bay View neighborhood and suburbs St. Francis, Cudahy, South Milwaukee and Oak Creek. That connection would still exist via the Lake Parkway and the Hoan Bridge. But 794 is also used by drivers to get between the south shore and points beyond downtown. If the portion of 794 between downtown and the Third Ward was eliminated, that traffic would have to pass through the area on a slower boulevard.
The development potential of eliminating I-794 between downtown and the Third Ward is huge. It would be a tremendous opportunity to grow the city’s tax base.
However, it would take time to see that potential fulfilled. It took years for develop ment to occur in the former Park East freeway corridor, after that freeway spur was torn down in 2003. Although a lot of development eventu ally did occur there, significant portions of the corridor remain vacant. Also, a development site created in 2016 by a reconfiguration of the Lake Interchange (where I-794’s east-west and north-south portions meet) has yet to attract any development.
Because of investments made in other parts of I-794, including Hoan Bridge upgrades, some doubt that WisDOT would tear down part
Independent & Locally Owned Founded 1995 —
SALES & MARKETING
DIRECTOR OF SALES
Linda Crawford linda.crawford@biztimes.com
SENIOR ACCOUNT EXECUTIVE
Christie Ubl christie.ubl@biztimes.com
ACCOUNT EXECUTIVE
Paddy Kieckhefer paddy.kieckhefer@biztimes.com
ACCOUNT EXECUTIVE
Dylan Dobson dylan.dobson@biztimes.com
ACCOUNT EXECUTIVE
Christy Peterson christy.peterson@biztimes.com
SALES ADMIN Gracie Schneble gracie.schneble@biztimes.com
ADMINISTRATION
ADMINISTRATIVE COORDINATOR
Sue Herzog sue.herzog@biztimes.com
PRODUCTION & DESIGN
GRAPHIC DESIGNER
Alex Schneider alex.schneider@biztimes.com
of the freeway. That includes Bruce Westling, managing director of Newmark’s Milwaukee office and a veteran commercial real estate broker and advisor. Recently he’s been pushing a more modest, and what he sees as a more realistic, plan to change I-794. Westling says a couple of I-794 ramps should be removed. That would improve the pedestrian experience and connection between downtown and the Third Ward and help attract more development to the area along the freeway, which still includes several surface parking lots, he says.
However, that idea just seems too modest. Milwaukee needs big ideas and bold moves to boost its stagnant economy, and this is a big opportunity. While the devil is in the details, WisDOT needs to seriously consider eliminat ing the freeway between downtown and the Third Ward.
What it does: An online machine shop that offers custom CNC parts for entrepreneurs, engineers, product designers, manufacturers and makers.
Career: Dietsch co-founded PartsBadger after struggling to source machined parts for Rugged Video LLC, a helicopter video company he co-founded in 2014. He developed PartsBadger’s instant quoting technology.
“As a new company in the machining space, we were very successful in creating and deploying technology across quoting, order management and our partner management software but struggled with efficiency in actually making parts on our own shop floor. Our shop was far from profitable and was consuming a significant portion of our total profits, which we normally would allocate towards growth. After an expansion in 2020, our monthly losses of $20,000 turned into $100,000 monthly losses, and we desperately needed to turn things around.”
PartsBadger began working toward the goal of operating at the other level of “top shops” in the industry, which have some baseline financial met rics published through Modern Machine Shop.
“Over the next few months, things improved and our metrics began to approach that of top shops. However, we still were putting up big losses. It wasn’t enough to just be a good machine shop, we needed a different approach to keep our shop afloat.”
The company decided it shouldn’t try to copy what other shops were doing, but instead create its own vision. Dietsch and his team conducted a “bottom-up” analysis of the cost components of the machining process. They also invested heavily into not only purchasing new technology, but also creating it themselves.
“The results from this exercise were eye-opening. Not only did we find that some of the accepted industry norms were flat wrong, we found that the potential of a different approach wouldn’t just outperform other U.S. man ufactures, but we could actually become more cost effective than overseas production. Once we knew what was possible, we got to work.
“The first change was figuring out how to successfully staff 24/7 opera tions. We created a new ‘3x12’ shift schedule, where employees would work 12-hour shifts on three consecutive days, get paid for a full 40 hours and get four days off. These new shifts would give us the coverage we needed, allow us to pay our staff better and give our staff a better work-life balance.
“Next, we needed to start deploying automation on the major labor inputs to the machining process, including programming, material prep, machine tending, deburr and quality control.”
The changes Dietsch and his team made turned the shop component of PartsBader from a $1.2 million annual loss into a profitable asset.
Being true to the vision and values of the company was key to turning the shop component of PartsBadger into a success.
“When we approached the problem by trying to replicate other shops, it wasn’t aligned with our strengths and was inauthentic to who we are as a com pany. Once we were staring at a blank whiteboard where we could create with out barriers, you could feel the excitement and energy of the team transform.” n
Registration & Networking – 7:00-7:30am Breakfast & Program – 7:30-9:30am
Community Center
Join as we celebrate the region’s top nonprofits and corporate citizens at the 2022 Nonprofit Excellence Awards, including the Marcus family, this year’s lifetime achievement award recipients.
Before the awards, Jim Kacmarcik and Gretchen Jameson of Kacmarcik Enterprises will also share best practices for corporations looking to give back and discuss the vision for the Kacmarcik Center for Human Performance, a new organization aimed at helping everyone pursue their best life at home, at work and in their community.
Speakers:
• Jim Kacmarcik, Chairman and Chief Executive Officer, Kacmarcik Enterprises (1)
• Gretchen Jameson, Group President, Human Performance and Social Impact, Kacmarcik Enterprises (2)
Corporate Citizen of the Year: Catalyst Construction
• Ellenbecker Investment Group
• Northwestern Mutual
• Husco
Corporate Volunteer of the Year:
• Mary Burgoon, Rockwell Automation
• Brian O’Neill, Feeding America Eastern Wisconsin
In-Kind Supporter: Tarantino & Company
• SMART- Sheet Metal, Air, Rail, Transportation, Local 18
• Oldenburg Group
Next Generation Leadership:
• Danielle White, Rockwell Automation
• Matthew Wuest, Godfrey & Kahn, S.C. Maggie Pinnt, Pepper Construction of Wisconsin Lifetime Achievement
• The Marcus Family
Nonprofit Collaboration of the Year:
• Milwaukee Youth Arts Center: The Milwaukee Youth Arts Center, First Stage, Milwaukee Youth Symphony Orchestra
United for Waukesha Community Fund: United Way of Greater Milwaukee & Waukesha County and the Waukesha County Community Foundation
• Journey House Construction & Design Academy: Journey House Inc., All Hands Boatworks, Teens Grow Greens, Habitat for Humanity, Adams Garden Park FOR M: MKE Tech Hub Coalition, We Pivot, The Commons, Bader Philanthropies, WEDC
Nonprofit Executive of the Year:
• Marci Boucher, Independence First
• Stephanie Borowski, GPS Education Partners Lynnea Katz–Petted, Revitalize Milwaukee Mara Duckens, St. Francis Children’s Center
Small Nonprofit Organization of the Year: Kathy’s House Center for Urban Teaching ALIVE Inc. Milwaukee
• The Ability Center
Large Nonprofit Organization of the Year: Centers for Independence
• Seeds of Health, Inc.
• Junior Achievement of Wisconsin
• Goodwill Industries of Southeastern Wisconsin Inc.
Emcee:
• Chris Alexander, Scholar Advisor, All In Milwaukee; Weekend Host, Radio Milwaukee