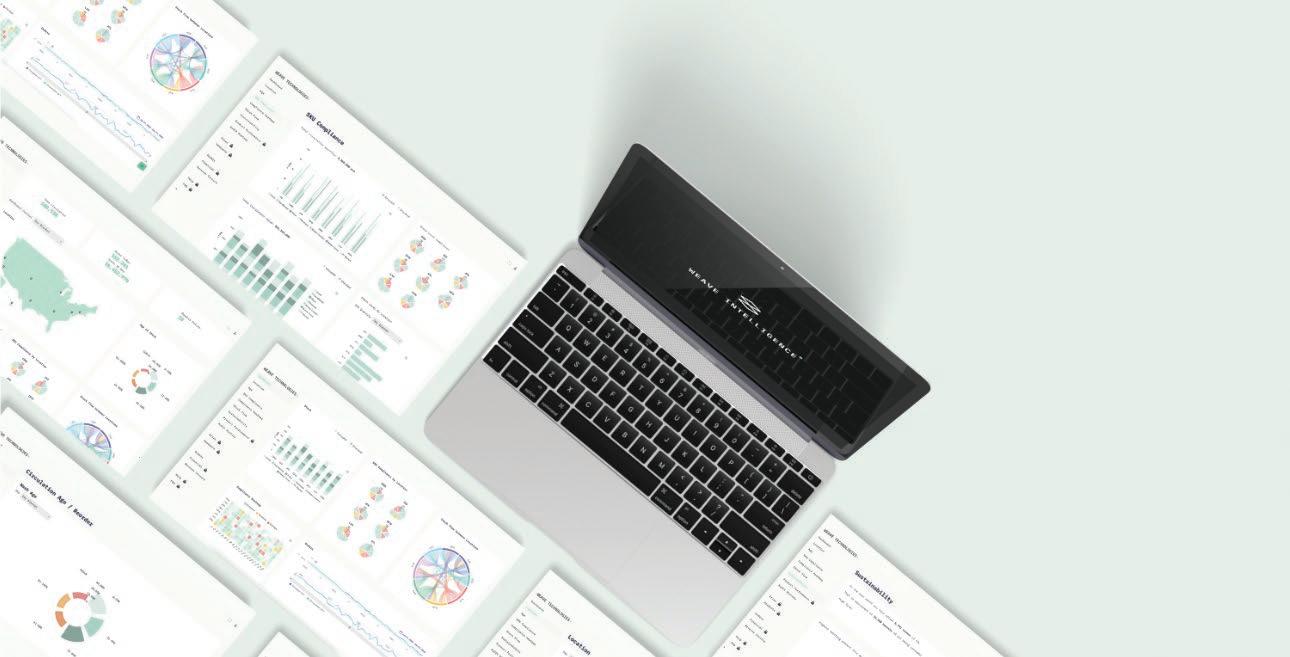
2 minute read
Weave Intelligence
Ian Linaker on how Weave Intelligence is changing aviation with Big Data and AI
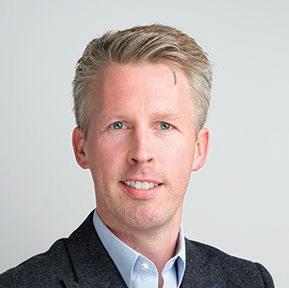
Weave Intelligence is a revolutionary software developed to meet a specific need within the aviation industry. It delivers fully connected product tracking to help customers make sense of their operations and find better ways to manage their complex procurement problems.
"Airlines are very good at procuring products, but the understanding of the product lifecycle can often stop there, once it's on the plane," says Ian Linaker, Founder of Weave Intelligence. "There are so many products where it then becomes extremely difficult to know what you have, how many you have, how old they are, and importantly, where all the product is at any one time."
"Airlines have huge, costly black holes where money is leaving the airline." These black holes are points all across the airline network but "the airline doesn't know where."
Inventory visibility
Weave saves product usage costs, autonomously tracks product locations and provides full global inventory visibility. "Our in-product and on-product chips give our customers powerful, insightful reporting that delivers savings and real, tangible change in their supply chains."
Weave Intelligence is built from the ground up using the very latest in Internet of Things (IoT) infrastructure and architecture, all connected through our cloud-based database and artificial intelligence (AI) platform.
"Weave humanises big data to deliver digestible, invaluable intelligence that our customers can use to achieve competitiveness, efficiency and a whole new level of accuracy."
The system makes it possible for clients to track and locate individual products wherever they are in the world, providing something that, as of yet, the airline industry has not had.
Digitisation in the food and beverage industry enables caterers to track their supply chain, stock levels, expiry dates and the movement of units. Until now, a comparable level of granular detail has not been available for textile products or other onboard items used by the airline industry.
"All airlines see is how many items they inject into the operation per year," Linaker says. Weave Intelligence solves this problem.
For example, for textiles, Weave uses a tracking technology to monitor the lifecycle of every textile product in circulation. Tags are sewn in at an airline's manufacturer and are not visible to passengers.
Weave Intelligence connects the dots across an entire network of provisioning centres and provides a full picture of the supply chain by analysing the traffic of millions of individually tagged assets.
"The moment you put a Weave tag into a blanket, you can track everything from the number of blankets you've got on hand to a product's age, its rotations, the overall equipment balance and location, as well as product performance." change their routes." to run out? Are they differentiate between all of the different every tag is unique."
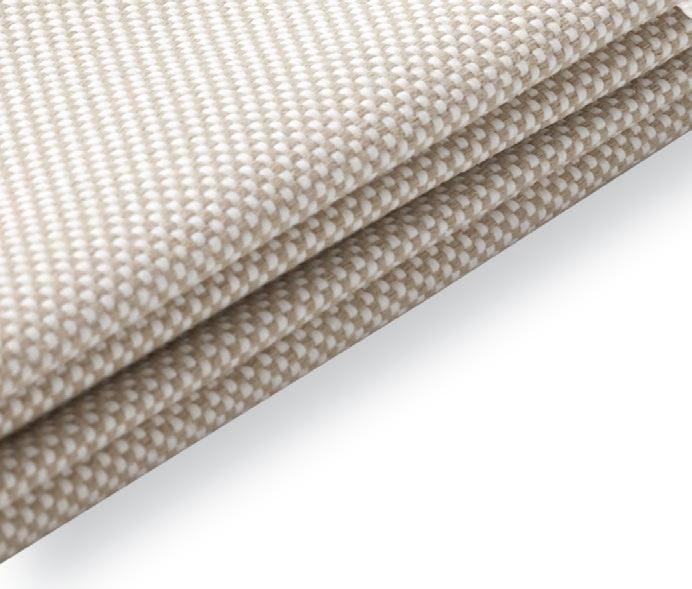
"For example, ‘Are there enough Business Class blankets in circulation? Where are they? Are we going to run out? Are they performing as expected?' Weave can answer all of these questions by tracking inventory automatically at a unit level. We can differentiate between all of the different stock keeping units (SKUs) because every tag is unique."
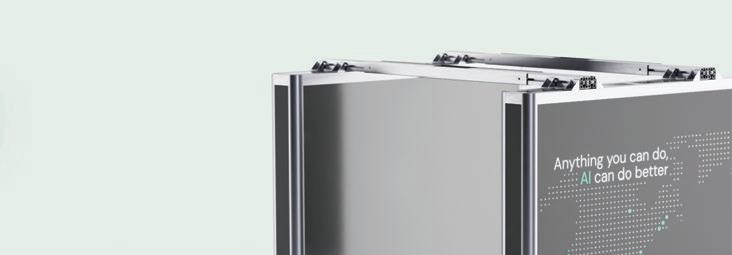
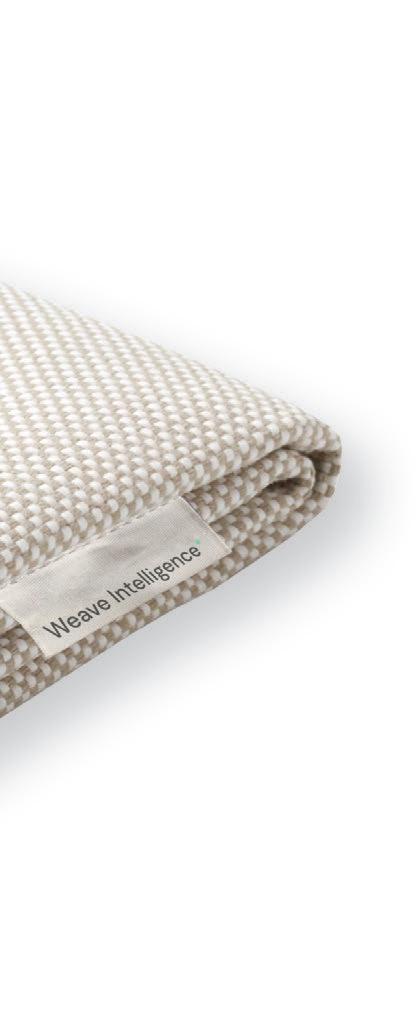
Before implementing Weave Intelligence, our team conducts comprehensive site assessments. "This ensures a seamless integration of Weave into existing systems and workflows, without requiring staff to
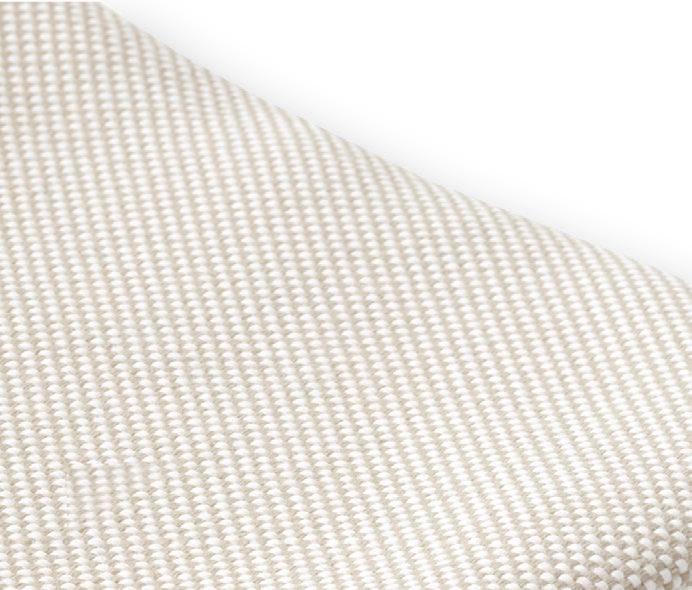
"This ensures a seamless integration to handheld readers. The transmitted to an encrypted, cloud-
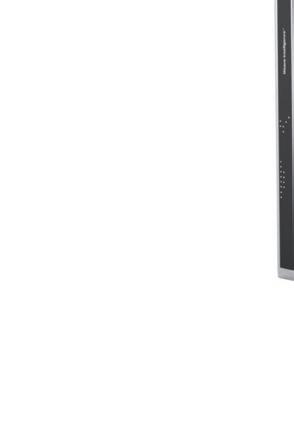
The terminals used to read the tags come in various sizes, ranging from full-size to handheld readers. The product data is then securely transmitted to an encrypted, cloudbased database. Access to this data is made available through Weave Intelligence's intuitive graphical user interface (GUI).
Weave's software then leverages this data to help its clients solve the underlying issues: “We have spent a considerable amount of time building a complex software along with an AI reporting platform that analyses huge volumes of data and tells our customers what is happening to the products.
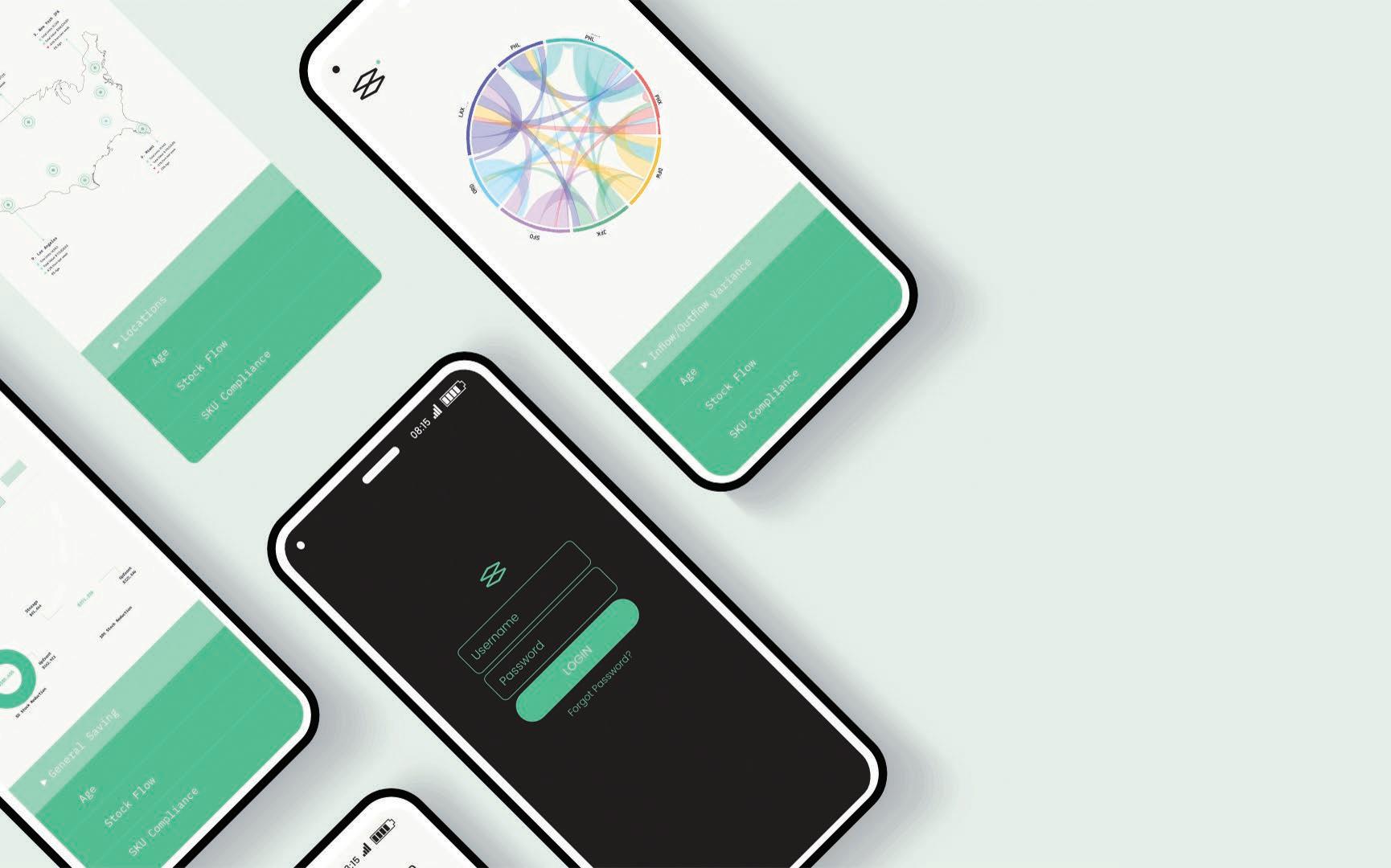
By the end of 2023, I believe we will be the largest global network of connected outstations in the world, providing our customers with one single source of real-time inventory data.” •
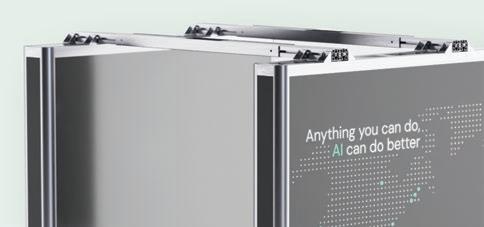
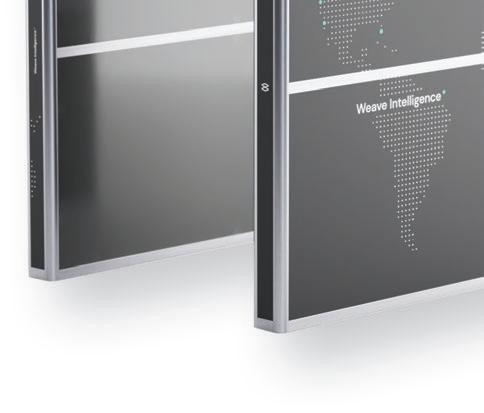