BOLIDT WHAT’S NEW Page 4 Custom floor for Mead Johnson Meeting the strictest food safety and hygiene standards Page 8 The cleaning aspect of a floor Artikel AGF Primeur Scelta & Bolidt Page 24 People Planet Profit Bolidt In the area of sustainability Bolidt innovates and inspires
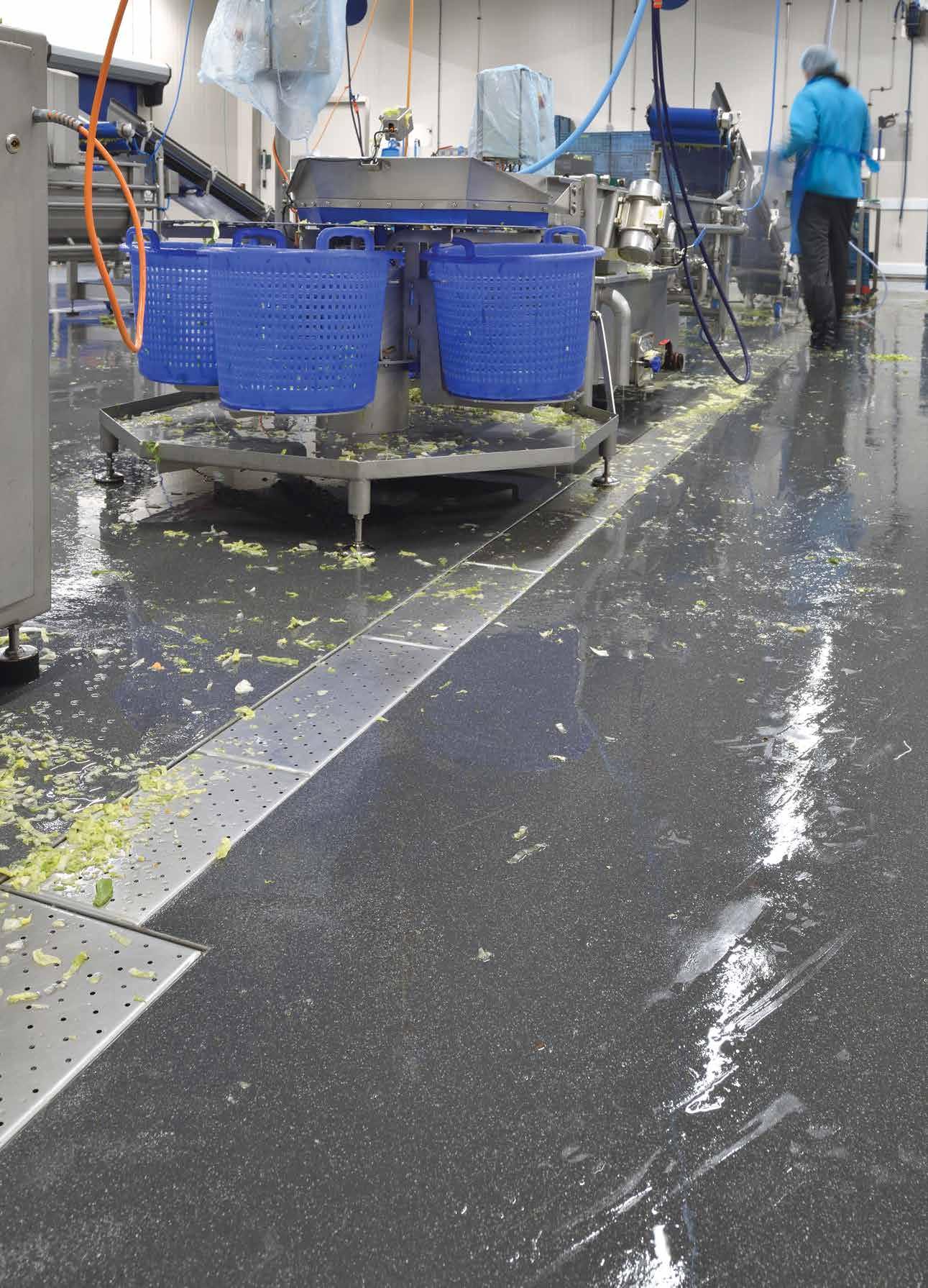
BOLIDT NO LIMITS
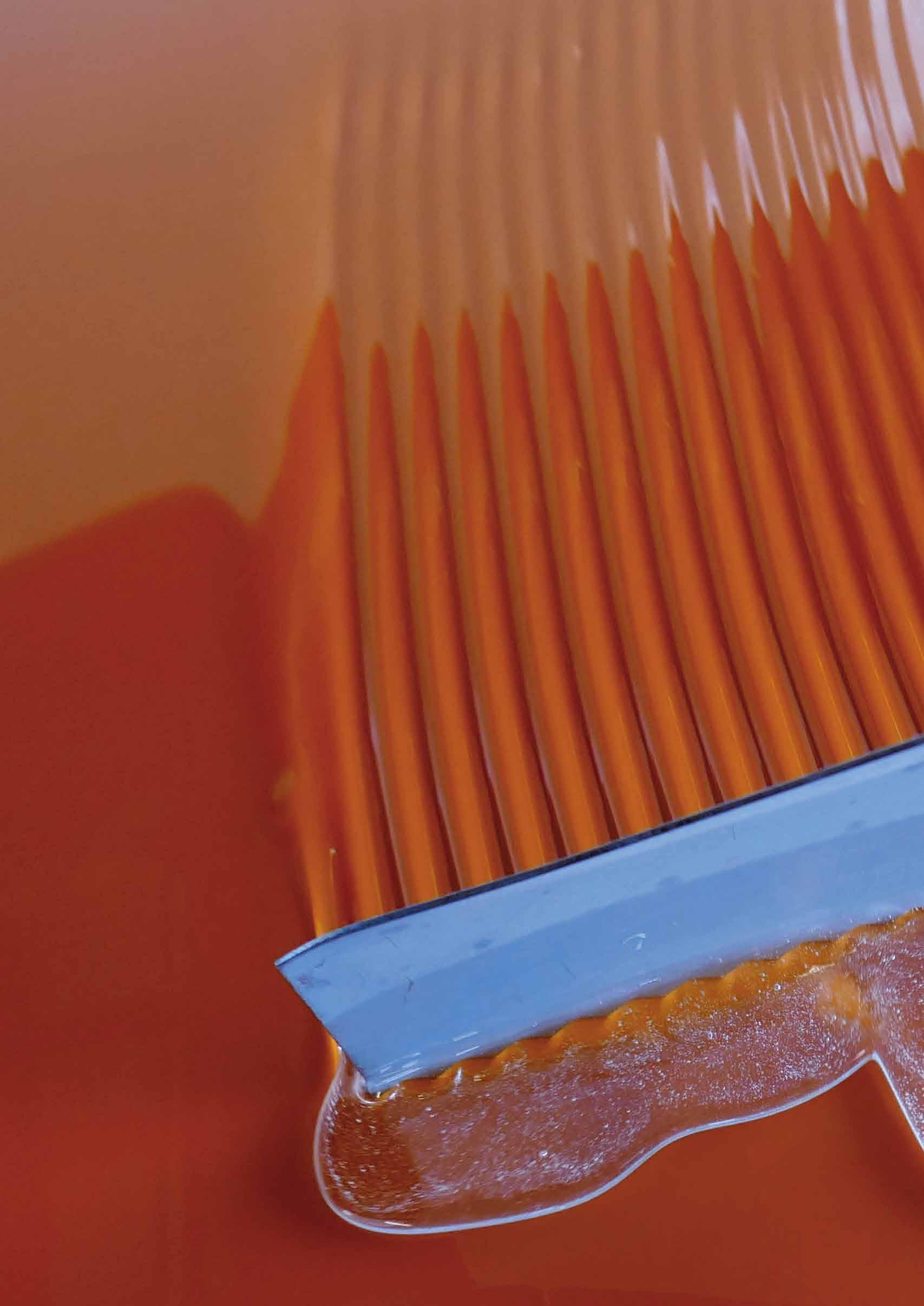
The question ‘What’s new?’ fits Bolidt so perfectly that we went ahead and named our news magazine that. In this magazine we show what our 27 specialisms are now dreaming up, what’s cooking in the Bolidt Innovation Center, and which brilliant projects we have recently completed. In this edition of What’s new? we talk to you about what’s so special about our floors for parking garages, how we continue to innovate in the field of colour, why People-Planet-Profit is our daily mantra, what we have done for renowned clients like SRON, Mead Johnson, Vedos and Tyson, and much So,more.what’s new? A lot! Enjoy reading. Team Bolidt
Ask one of our staff members and you are sure to get a fascinating reply. After all ‘What’s new?’ is what defines Bolidt. And innovation is our middle name. Whether it’s about our floor and wall systems, our way of working or the expertise of our people, we always strive for better. The constant urge for innovation has already resulted in so many wonderful things for Bolidt: innovative products, exciting cocreations, projects around the globe, happy employees and, perhaps most importantly, happy clients.
3
Dear ‘What’sReader,new?’
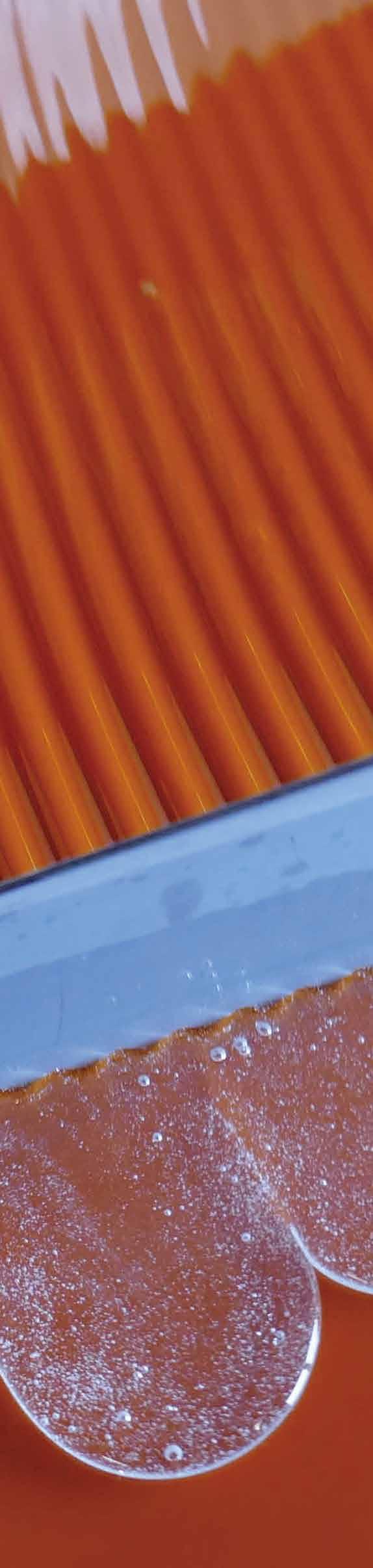
Inproblems.theNetherlands, Mead Johnson has had a manufacturing plant in Nijmegen since 1984, though a lot more than producing formula and such goes on here. The company also conducts research in Nijmegen and has its own R&D department where new products are developed. The main sales markets of the Nijmegen plant are Europe, Latin America and
Asia, with China being the largest buyer by far. Since 2021, the com pany has been part of Mead John son China and works closely with the Chinese manufacturing plant in MeadGuangzhou.Johnson has been experiencing strong growth in Nijmegen for years. To be able to handle the increasing demand for baby formula from Chi na, the manufacturing plant will be expanded further in the coming years. In the meantime, renovation work is also taking place. Take the existing tile floor for example, which was recently replaced. An audit revealed that this tile floor no longer met the interna tional requirements in the field of hygiene and food safety. The regula tions of the authorities who oversee food safety are extremely strict: if the floor did not comply, and comply very soon, production would have to be brought to a standstill.
Giving bacteria zero chance Bolidt has built an impressive track record in the food sector. So, there was no doubt on the part of Mead Johnson as to who would supply the new floor for the Nijmegen manufacturing plant. It marked the start of a complex project: the floor had to be replaced while production continued and the new synthetic floor system had to be installed over the existing tile floor. Natu rally, Mead Johnson wanted the number of production stops to be kept to a minimum. An there was yet one more challenge: to meet the standards as quickly as possible, the project had to be completed in three weeks. It was clear from the outset that Bolidt’s floors would meet the strict standards Mead Johnson was subject to. By working closely with clients and by continuously inno Bolidt designed and produced a new floor for Mead Johnston’s production location in Nijmegen in record time. A sleek, seamless synthetic floor system was installed over the existing, irregular substrate, producing a floor that meets the strictest standards in the field of hygiene and food safety. This producer of baby and infant food took full advantage of Bolidt’s ‘everything under one roof’ principle.
Imageforreference
For over 100 years, Mead Johnson has specialised in formulating and manufacturing nutrition for babies and infants. In fact, the company was one of the first manufacturers to conduct scientific research in this area. Today, Mead Johnson has some 3,000 employees worldwide and is active in more than 110 countries. This globally operating manufacturer has developed countless special prod ucts over the years, such as nutrition for infants with allergies and health
Baby and infant food producer meets strictest food safety and hygiene standards
Custom floor for Mead Johnson
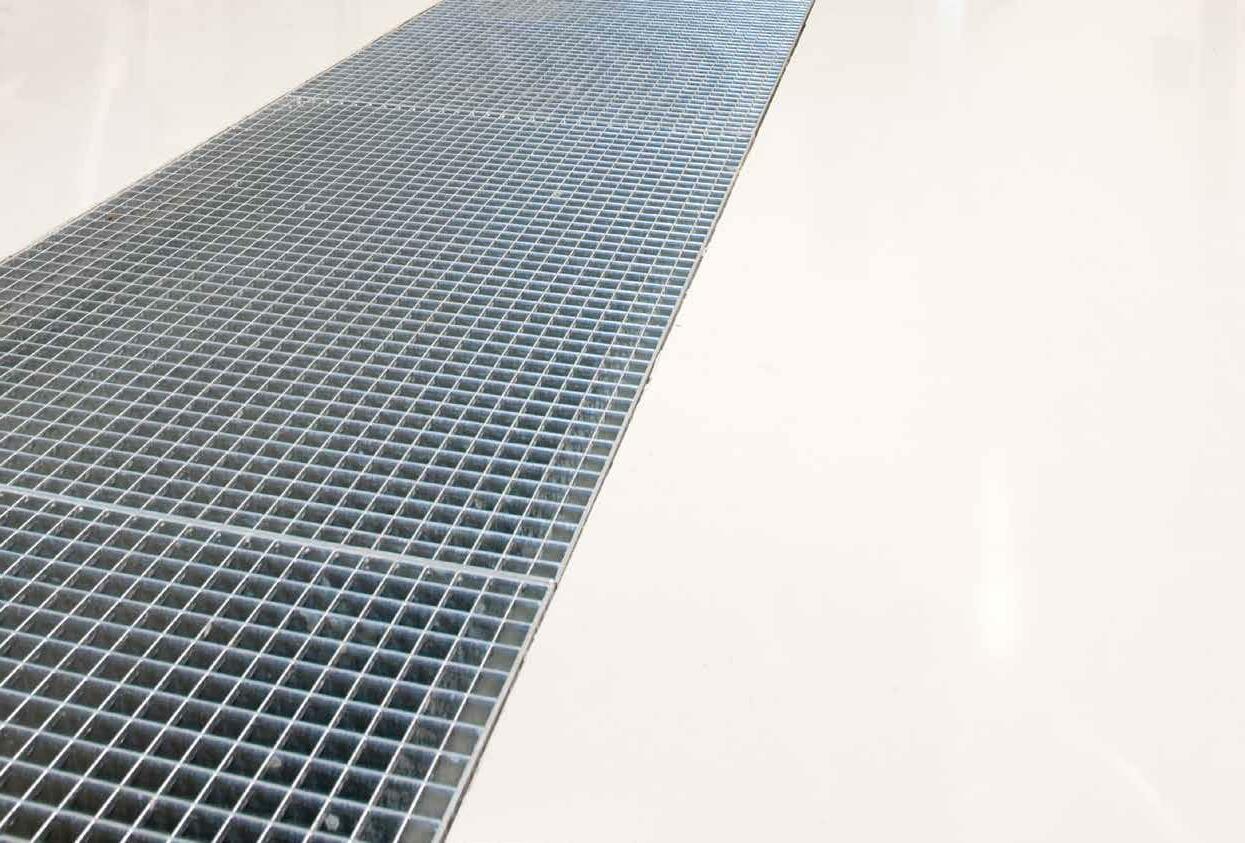
Aprerequisite.keyrequirement from Mead Johnson was that the floors must be easy for the staff to clean. Thanks to the sealed surface and the seamless finish, Bolidt floor systems can be cleaned quickly with a high-pressure hose. They have been extensively tested and can withstand the daily use of cleaning agents. The floor Bolidt installed at the Mead Johnson facility also has a non-slip finish to help ensure the safety of the people working there by preventing slipping or falling while working, even in wet conditions. With these features, Bolidt floors make an optimal con tribution to ensuring a safe working environment.
5 vating, Bolidt has developed floor systems that are extremely suitable for the food sector. The dirt-repel lent floors are pore-tight, meaning there’s no chance for bacteria to get a foothold and start growing. The risks of bacterial growth are reduced even further because Bolidt installs the systems seamlessly, including where the floor meets the walls, skirting, point and trench drains and grates. Thanks to the wear resis tance and durability of the synthetic systems, no holes, cracks or tears will appear in the floors, even when using heavy machinery and transport equipment. And given that any little crevice could allow dirt to accumu late and bacteria to grow, that is a
Everything under one roof It wasn’t just the quality of its floors that convinced Mead Johnson to go with Bolidt: the fact that Bolidt has everything under one roof in Hen drik-Ido-Ambacht was also a de ciding factor for the manufacturer. This distinguishes Bolidt from other suppliers, enabling the company to develop, test and produce floor systems and then install these with its own installation teams. Because Bolidt manages everything in house, Mead Johnson did not have to talk to several different parties and the floor could be completely custom ised, a major advantage for such a complex project that had to be delivered in record time. The biggest benefit of having everything under one roof became apparent when addressing a serious challenge, handling an irregular sur face like the existing tile floor. It was essential that the many irregularities in the original floor not show up in the new synthetic floor. With the proactive approach of Bolidt’s own R&D and production department, as well as Bolidt’s installation team, together with the client a solution was devised and the new floor was tailored exactly to Mead Johnson’s needs and wishes. The Bolidt team was able to create a solid surface by first installing expanded metal (metal mesh) onto the tile floors and applying mortar over this. They then installed a Bolidtop® 500 SAR floor over the now even surface. This system is not only heavy duty when it comes to handling chemicals and equipment, but also very wear-re sistant and durable. With this new floor, Mead Johnson will meet the strictest requirements in the area of hygiene and food safety for the next 30 years as well.
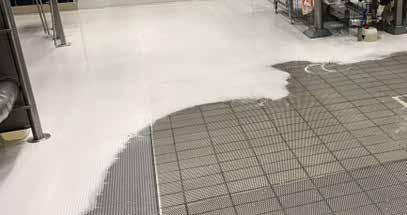
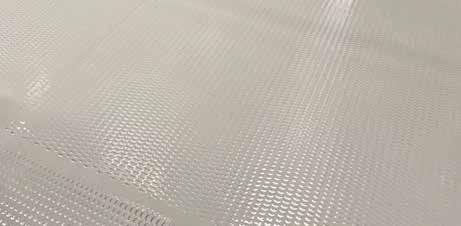
Multinational Orkla wanted a reliable floor for its new biscuit and wafer factory in Latvia. Because Bolidt manages everything in house, it was able to get right down to work and deliver the extremely hygienic Bolidtop® 700 system to Orkla on schedule.
Exactly the floor Orkla was looking for.
Listed on the Oslo Stock Exchange, Norwegian conglomerate Orkla has around 300 brands and more than 21,000 employees. And yet the name Orkla is barely known in the Netherlands. This is because the company is mainly active in the Nordics, as well as in the Baltics and in selected countries in Central Europe and in India. In these regions Orkla supplies a wide range of products: food, confectionery and snacks and food ingredients, care and health products, cleaning products, paint products and Theclothing.factthat Orkla does not limit its activities to the Nordics is apparent from the substantial investment the company is making in Latvia. In the city of Ādaži, Orkla is having an ultramodern factory built with 13 production lines and covering more than 30,000m2. Orkla’s new production unit specialises in the production of biscuits and wafers and should be operating at full capacity in 2023. Hygienic floor for new biscuit and wafer factory Orkla in Latvia
Develop–Produce–Apply–Repeat
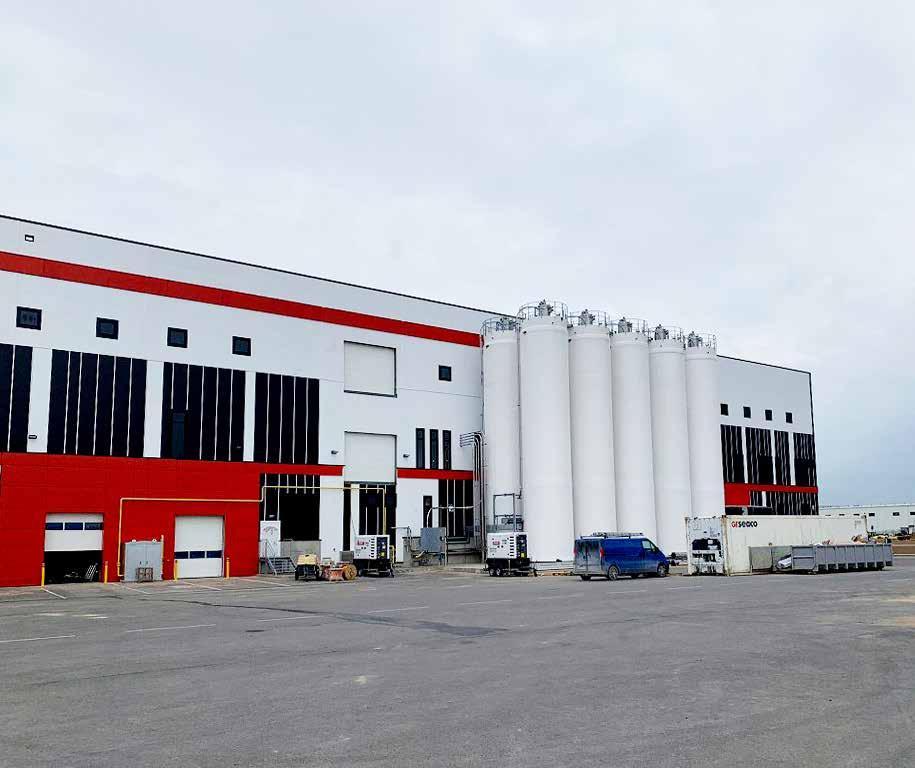
Full control When you say quality, sustainability and innovation, you say Bolidt. It’s hardly surprising then that Bolidt was commissioned to supply the flooring for Orkla’s new factory in Latvia. And that floor system was the Bolidtop® 700, an extremely wear-resistant and durable system that has already proven itself at many food companies. The reliable system is seamless, pore-tight and easy to clean, making it extremely hygienic. The non-slip top coat also makes the Bolidtop® 700 very safe. These are exactly the requirements Orkla set for the flooring in the new production unit.
7
The construction of the modern, efficient and above all sustainable factory aligns well with Orkla’s strategy, which is strongly centred on innovation. The company sees it as its mission to make customers’ lives ‘a little better every day’ by providing quality products. From Ādaži, Orkla wants to create new products and develop strong local brands further. According to Orkla, the new production unit will enable Orkla to continue building on innovations.
Recently, a special time capsule was laid in the foundations of Orkla Biscuit Production plant to leave a message for the generations to come.
Unlike the competition, Bolidt could assure Orkla that it could deliver the floor on schedule, the big advantage of handling the entire value chain in house. Not only does Bolidt develop and test floor systems, it also produces them. What’s more, Bolidt’s own staff handle the installation. This allowed Bolidt to respond agilely and quickly and offer Orkla security of supply. And there’s another advantage for Orkla in Bolidt having full control over all aspects: Bolidt can install the same floor system anywhere in the world. If the multinational decides to open new production units elsewhere, Bolidt can supply a synthetic system with exactly the same specifications as in Latvia. This also means considerable time savings and optimum security of supply.
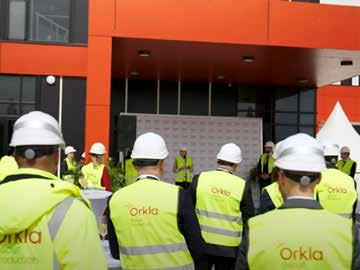
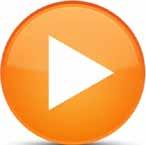

Article AGF Primeur - Text Martine van der Wekken
HygieneHYGIENEis another important aspect for Scelta Products, which holds BRC AA+ certification, Wilco adds. He explains that the company needed an antibacterial floor that was easy to clean in order to comply with the applicable NEN norm. Ton says the cleaning aspect is very important when choosing a floor. “Cleaning costs money, which is why it’s such a decisive factor when choosing a floor. In Scelta’s case, where the production process includes a wet process, the floor needs to be cleaned daily. If this can be done in under three hours, whereas other floors can easily take five hours to
“At Scelta we receive fresh raw materials daily, which are immediately washed and cut (wet process), after which they are prepared for the next (dry) process step: coating and breading. The products are then deepfried, frozen and packed, to be shipped and transported to the end customers”, says Wilco. “This means we have wet, warm, cold and dry flows. In all four of these phases, the floor - preferably one and the same floor type - must meet the safety requirements in terms of skid resistance, in addition to being thermally shockproof given the variable temperatures. Hygiene is important at every stage of the process. During the deep-frying phase, there is always the possible, incidental risk of hot oil leaks. The production facility is intensively cleaned, using chemicals. The floor must also be able to withstand this. In the dry, packaging phase, the floor must be able to able to withstand the use of transport equipment, such as a forklift and pump trucks, as well as footfall. We can offer a floor that matches the requirements in terms of hygiene and skid resistance for all three phases”, Ton adds.
when choosing a floor
Cleanability can be a dealbreaker
Ton cites the new floor of a newbuild project in Rilland for Scelta Products, which produces frozen vegetable snacks such as breaded mushrooms, onions rings and other vegetables, as an example of how intricate the process of choosing the right floor can be in fresh produce processing. “We are building a new, 14,000-sqm facility there, doubling our production capacity in the process. The new production facility will be up and running in Q4 of this year. The building must comply with the requirements of the BREEAM 2020 outstanding rating, which also sets requirements for floors. This production site will have the most modern production lines and fullyautomated production processes”, says Wilco Boone of Scelta Products.
“For many of us a floor is just a detail in a bigger picture. Nonetheless, an industrial floor is an important aspect of hygiene, especially in the fresh produce sector”, says Ton van Wijnen of Bolidt, which specialises in floors for companies in the fresh produce sector”. Technical characteristics, such as skid resistance, chemical resistance, resistance to intensive loads and hot liquids, and the aesthetic aspect all play a role when choosing a floor.
Ton explains that gutters and drains are necessary in the wet phase because of the production process. “This is a very important aspect of a floor. The details make all the difference, including for a gutter. Instead of sealed joints - which can come easily undone - we use detailing in the floor, in which stainless steel gutters can be integrated, ensuring a homogeneous connection between the floor and the stainless steel.” Wilco also indicates that the aesthetic aspect was a factor, in addition to the technical features. “We regularly receive customers, which is why we want our production facility to look spick and span.”
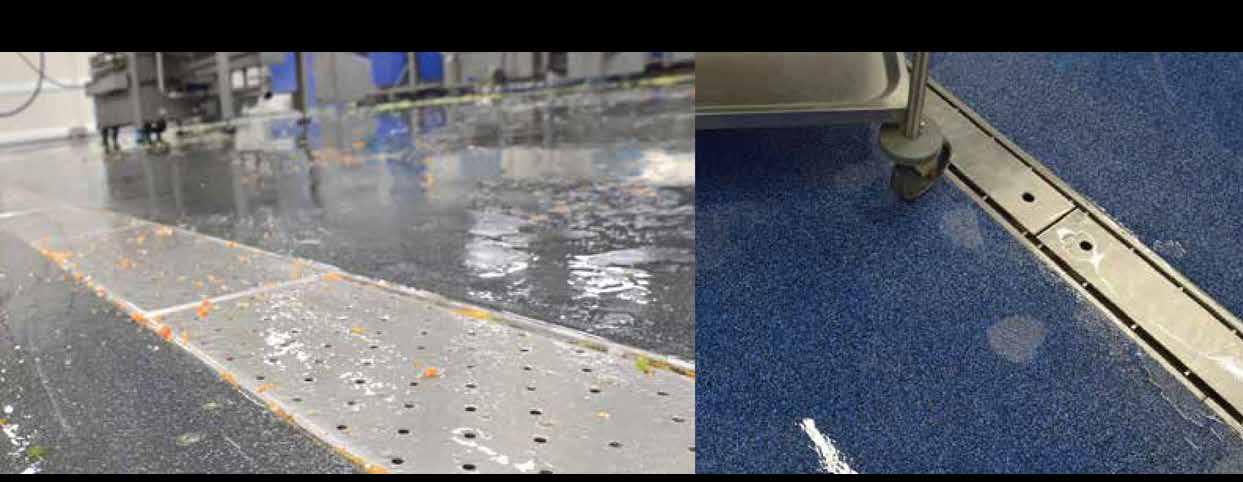
clean, this can be a dealbreaker.” This also explains why Bolidt oversees the cleaning process of the floors, with a cleaning consultant, who draws up a cleaning protocol. “Because cleanability can be a dealbreaker, we keep up with the latest developments”.
“Choosing an industrial floor means selecting a tailor-made solution, precisely because so many aspects play a role and each production process comes with different requirements”, Ton explains. “That is why we spend so much time on developing and giving advice on floors. We also take care of sales and installing the floor on site. Bolidt does everything in house. Another aspect that Wilco took into account when making his choice.
“Industrial floors can’t be too porous if you want to clean them quickly and properly”, Ton explains. “That is why we choose to use floors that are completely impermeable across their entire thickness, unlike many other floors where often the only guarantee for the floor’s impermeability is the sealant top coating. If this seal is damaged, however, penetration may give rise to mould in the floor, for example. A problem you won’t have with a fullysealed TIMINGfloor.AND PREPARATION
“The company runs like a well-oiled machine, e.g., for the communication of the planning schedule, but this also allows for flexibility throughout the process. The timing and preparation are crucial to the success on the construction site.”
Hygiene
The hard, sealed floor surface prevents dirt, dust, food residues, etc. from permeating the floor. Instead they remain on the surface (and are easier to spot), ensuring it can be optimally cleaned and remains clean. Good hygiene is vital in the prevention of infectious diseases such as flu, whooping cough, rubella, and so on. But a cleaner floor also benefits people who suffer from chronic asthma and bronchitis, for example. No wax or protective layers are applied, which are often marred by dirt. Another important aspect that also contributes to creating a healthier living, learning and working environment. Research has shown that absenteeism in education can be reduced by 20 to 30% by improving hygiene practices.
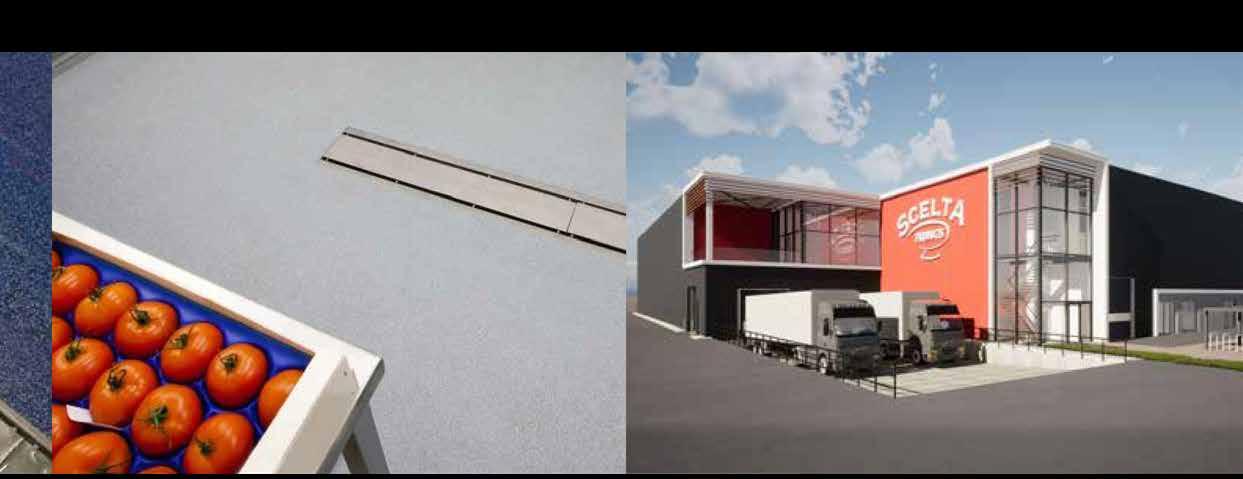
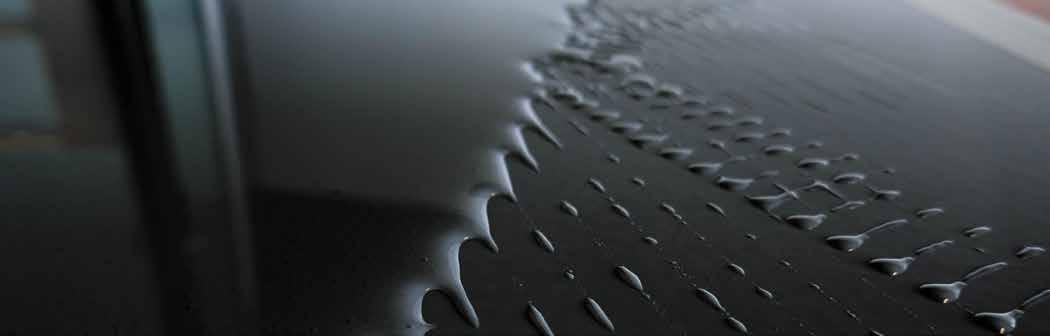
Innovation&colour
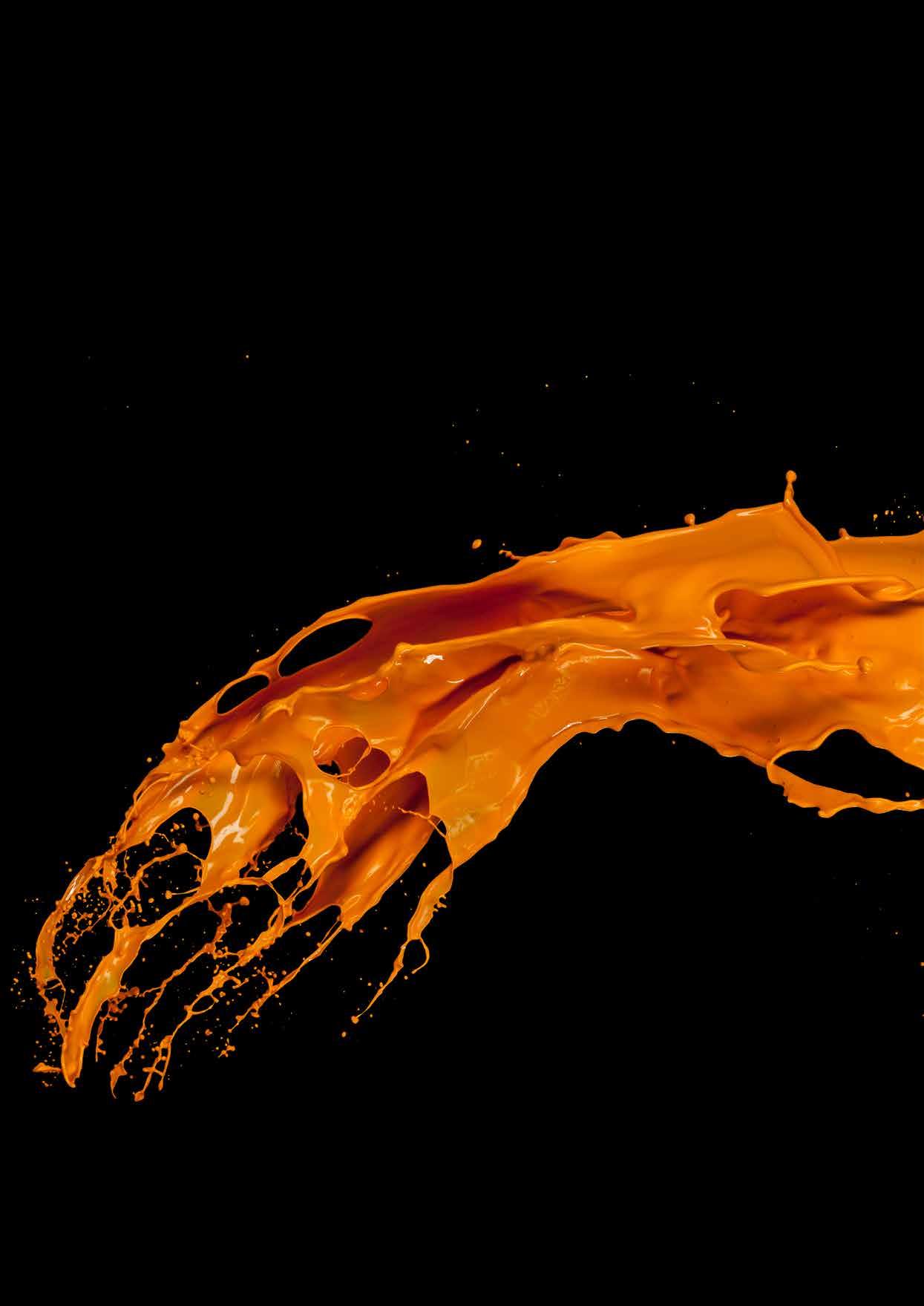
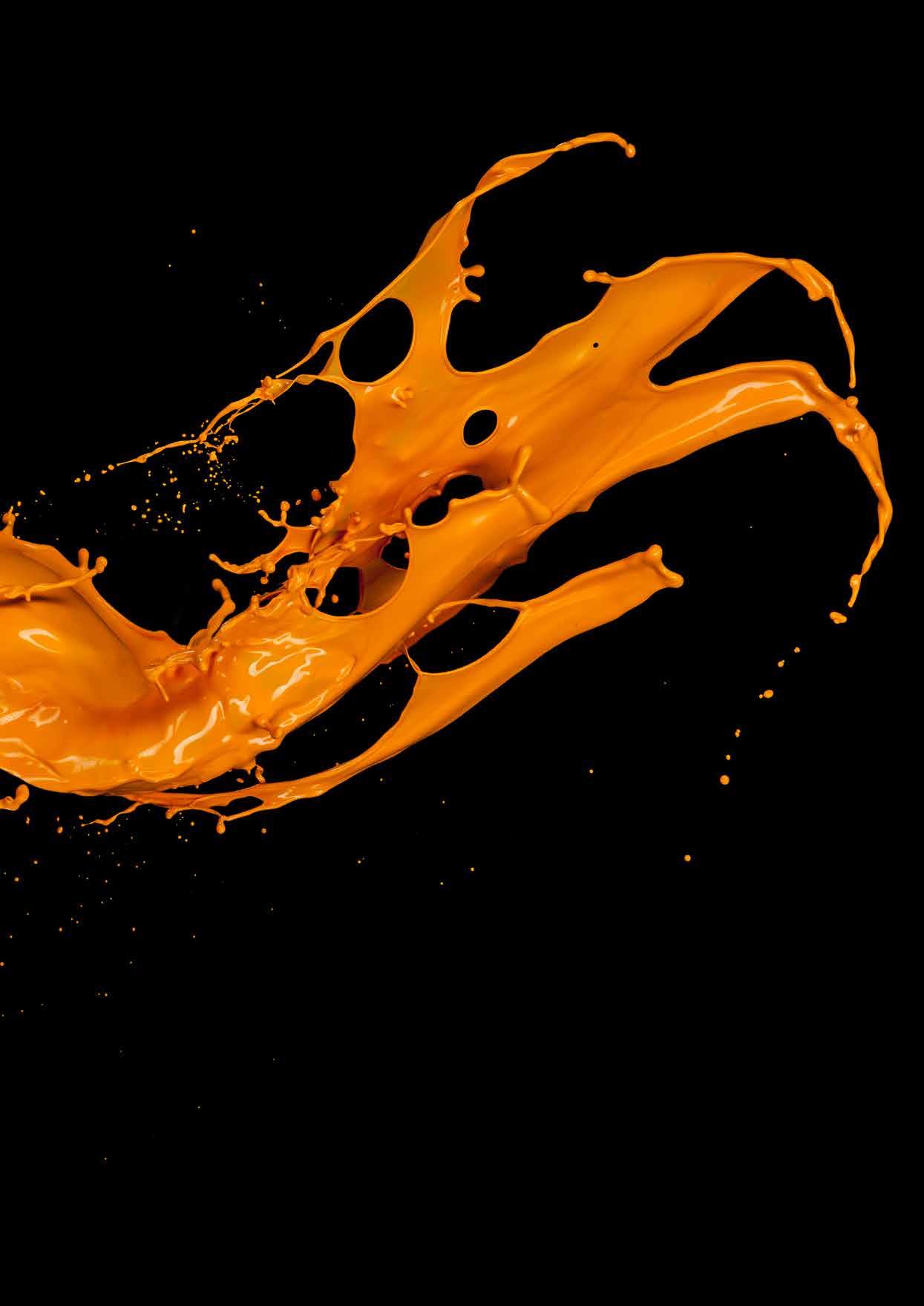
colours are used in all kinds of ways to make an impact. They can enhance the shape of a building, making it even more of an eyecatcher. Colours can give whole neighbourhoods a new identity, as happened, for example, in the favela in Rio de Janeiro with its brightly painted houses and colourful murals. Or closer to home in Almere-Stad, where various districts were given their own colour. Interior architects also use colour to create an effect and evoke emotion. We feel more at home when warm colours have been used indoors. Red makes us hungry, while blue stands for safety and green for harmony. Bolidt as innovator Bolidt, too, is aware of the functional and aesthetic impact of colour. Because the company has full control over the synthetic floors it produces, from development and production to installation, it can offer architects infinite design possibilities. Each client makes grateful use of this in their own way. Erasmus MC in Rotterdam chose Bolidt floor and wall systems Bolidt has elevated the development of colours to a science Clients dream in colour. To make their dreams come to life, Bolidt offers unparalleled design options – the result of years of innovation. What role does colour play in Bolidt’s projects? And what is involved in developing and producing all those special colours?
In12architecture,
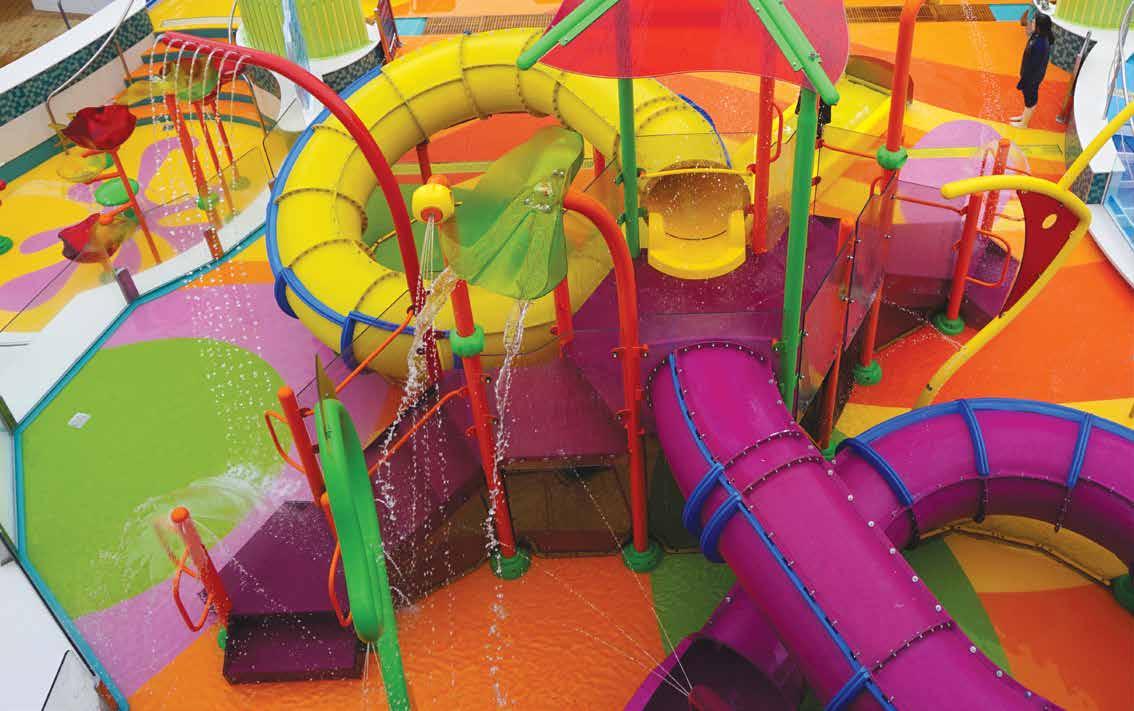
13 in timeless, calm colours that pair perfectly with this, the largest academic hospital in the Netherlands. The Nhow Hotel in Amsterdam, developed by OMA Architects, was given the aesthetic Bolidt design floor it deserved. The operators of Huis van Europa, the building that houses the European Parliament Liaison Office in The Hague, came to Bolidt with yet another wish: they wanted to bring the history of the EU and the European Parliament to life with an interactive map of Europe – on the floor. For this project Bolidt supplied its Bolidtop® Print flooring system that allows any drawing or other image to be turned into a beautifully finished, high quality floor. Finally, in the Vredenburg Hoog Catharijne car park in Utrecht Bolidt applied a range of colours, not only to clearly mark off parking spaces, lanes and pedestrian walkways, but also to enhance the sense of safety for visitors thanks to the bright colours that give the parking garage its fresh look. In the nearly 60 years of its existence, Bolidt has elevated the development of colours to a science. Bolidt has a mission to replace traditional materials with sustainable alternatives, and the company continuously strives for innovations in the areas of safety, sustainability, energy & data, hygiene, and in the field of design too. The upshot of this urge for innovation is that Bolidt can now supply virtually every colour imaginable and even offer synthetic floors and walls in fluorescent colours, with a motherof-pearl sheen or with 3D effects, or incorporate special patterns or prints into the finish.
For bringing the wishes of clients to life the Bolidt Innovation Center is the place to be. For larger projects, we invite clients to Hendrik-Ido-Ambacht where, at the Bolidt Innovation Center, they can experience what it’s like to work with synthetic materials and, together with our R&D department,
Calm in the classroom Innovation: it’s what Bolidt is all about. And the innovation in the area of colour is often customer-driven as well. Wouter Nugteren, team leader for domestic commerce, talks to clients every day about their colour needs and wishes. ‘Colour plays an important role in our projects. Clients often have the most extraordinary imaginings: they want a floor in a crazy colour or with a special effect. And on top of this the floor needs to meet various functional requirements. For example, schools want their pupils to be able to concentrate well and feel safe. A floor in the right colour ensures calm in the classroom, which boosts the children’s performance in class.

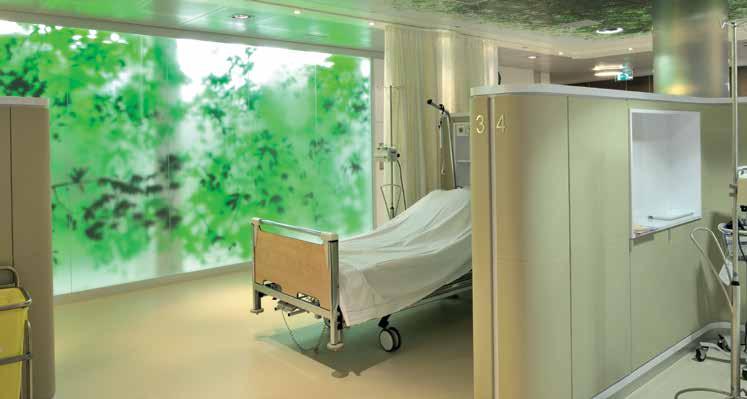
investigate how we can convert their designs into functional and aesthetic floors.’ One of Bolidt’s regular clients is Tillberg Design of Sweden, a renowned design agency that designs interiors mainly for luxury cruise ships. The design includes not only public spaces such as restaurants, lounges, bars, spas and swimming pools, but also luxurious private areas like suites and cabins. Tillberg devises a unique design for each client. ‘We take the time to get to know the client and their design wishes’, says Fredrik Johansson, partner and art director of Tillberg Design. His company regularly opts for Bolidt’s synthetic systems for its interior designs. Johansson: ‘Bolidt offers us countless colour and design options, which means that the systems can be perfectly customised. The passenger experience on board a cruise ship is becoming increasingly important. We can design Bolidt floors tailor made for our clients and this way create a truly unique atmosphere and experience.’ Design floor for Mercedes-Benz The actual development of colours is done at Bolidt’s R&D department. The design options have grown explosively over the years, says R&D chemist Pieter den Boer. ‘Some 50 years ago, the synthetic floor was
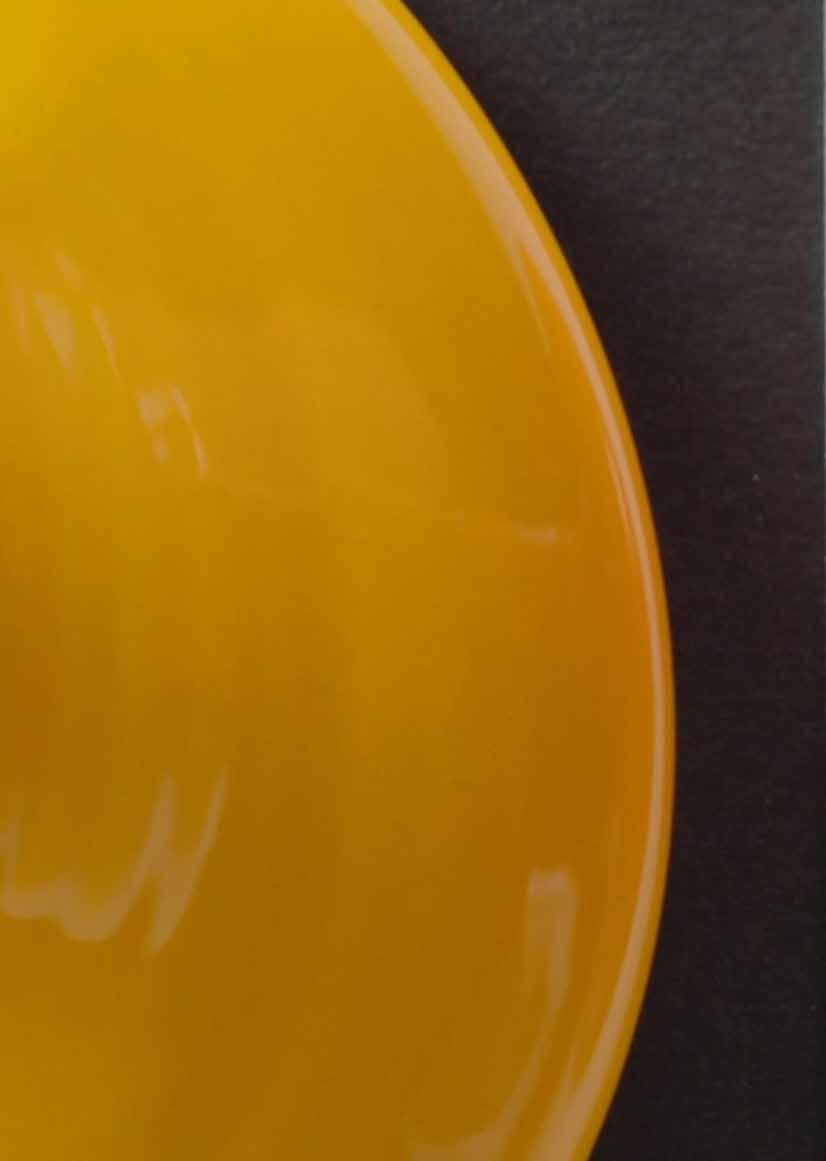

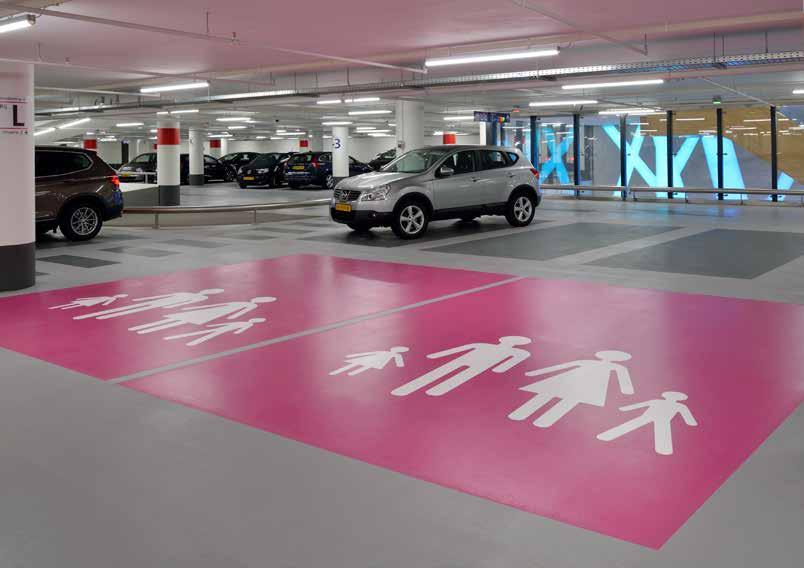
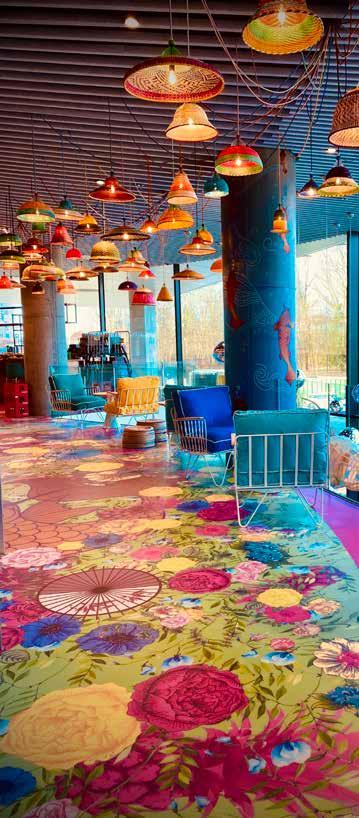
only available in grey. Design and the role of colour have become increasingly important. To serve our customers, we use sixteen pigments. We mix these powders in all different proportions to supply all 1,950 NCS standard colours.’
Producing the colours is the work of colour specialist Erthan Elbir. ‘Producing colours is often a matter of trial and error,’ he explains. ‘But we always arrive at the exact colour the client wants. The most difficult to make are the fluorescent colours, but we have developed special pigments for these too. I am most proud of our design floor for the Mercedes-Benz Museum. It was quite a challenge to develop all the specific colours for this exceptional building. I am also proud of the fact that we regularly produce colours for the buildings of leading architecture and design firm Zaha Hadid Architects.’ The employees of the R&D department all have their own specialism and special roles. Davey Baan, for example, is a ‘system impressionist’, or in simple terms a ‘sample maker’. He is responsible for small-scale system impressions made at the client’s request. As a ‘pigment specialist’, his colleague Yvonne van Blijswijk is responsible for testing colour pigments and developing the colour pastes needed to be able to supply the synthetic materials in the desired colours and with the desired properties. ‘Pigments are supplied in powder form. Consistently mixing a powder into our synthetics is an error-prone process. By continuing to innovate, we have been able to convert all pigment powders into sixteen stable pigment pastes. With these sixteen pastes we are now able to faultlessly produce any colour desired.’
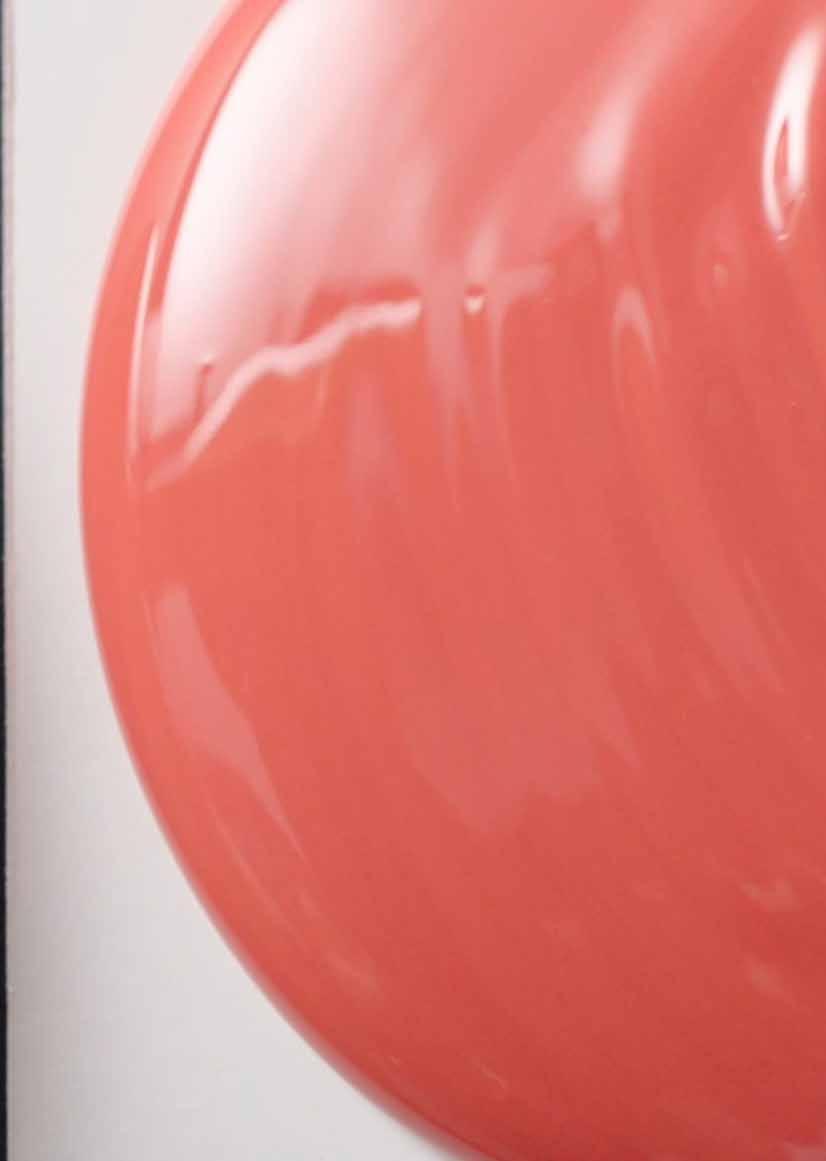

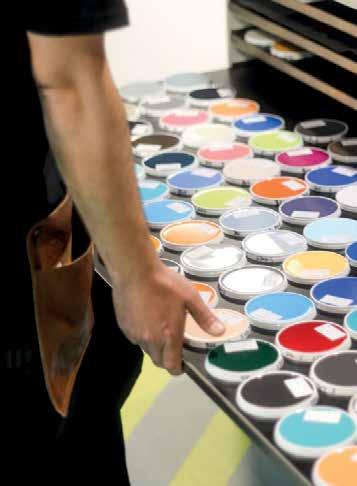
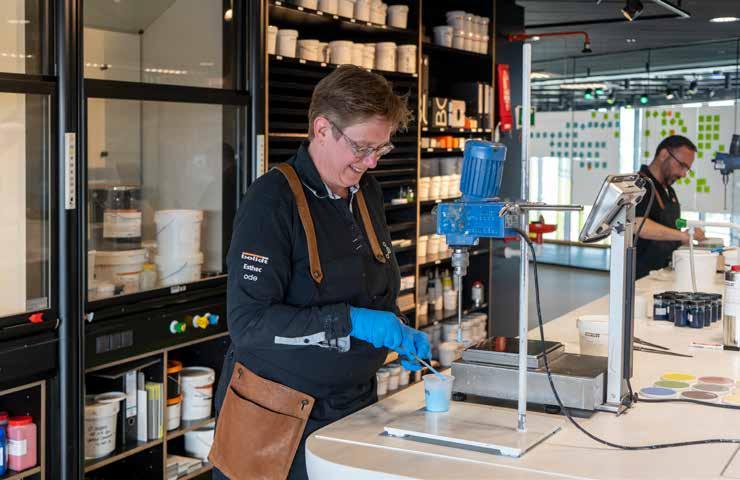
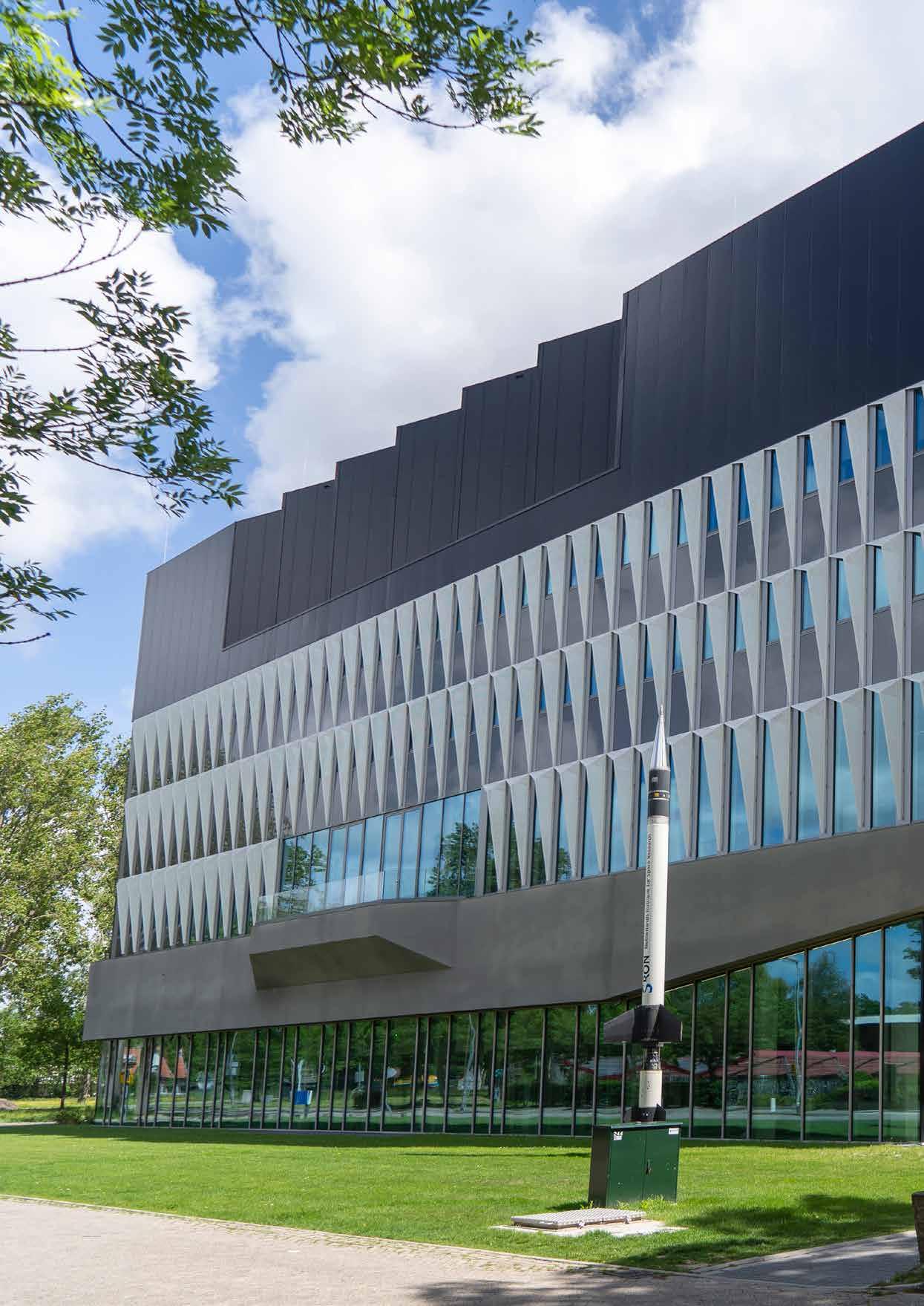
The InstituteNetherlandsfor Space Research SRON
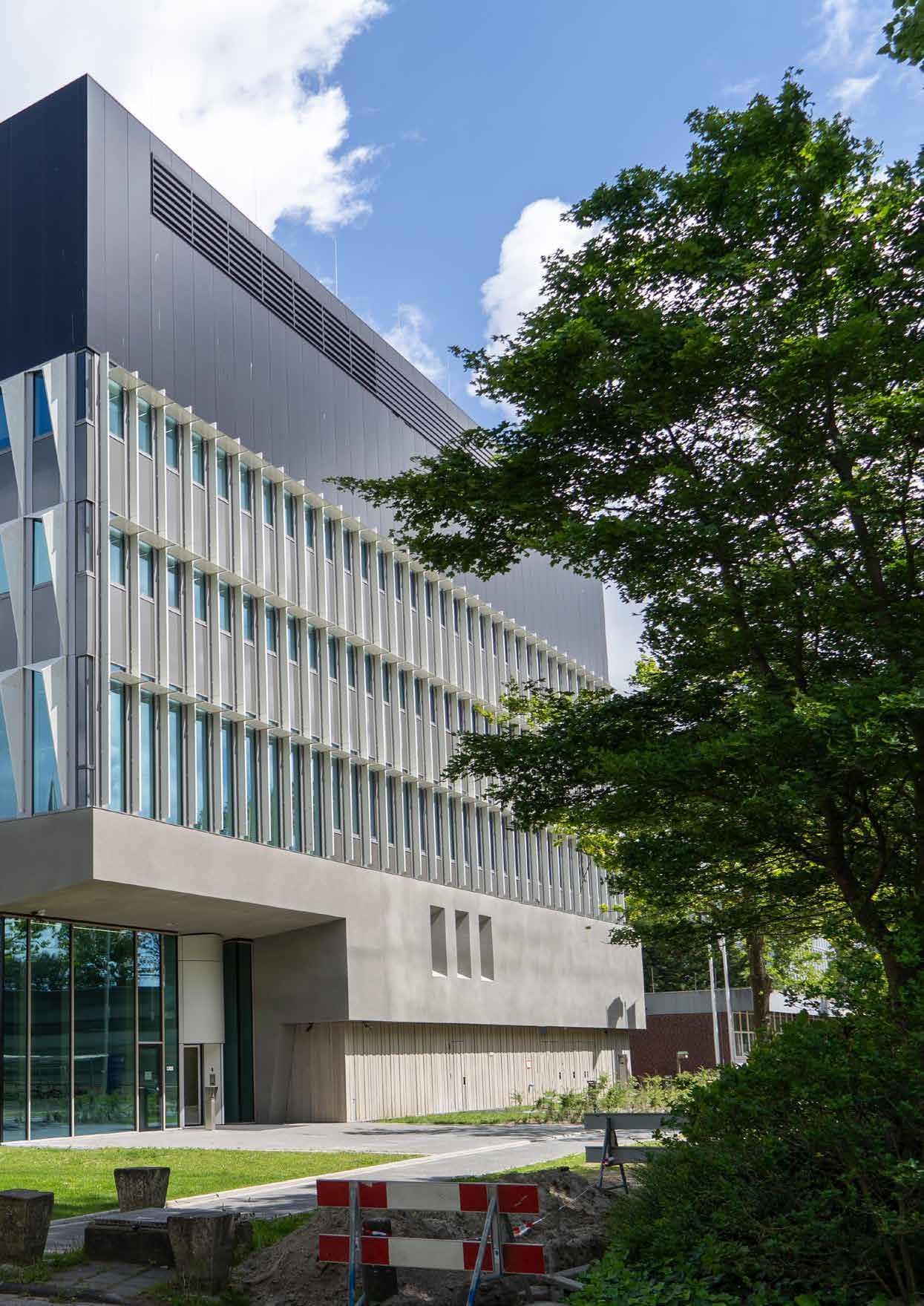
A prestigious institute should be housed according to it station.
SRON Netherlands Institute for Space Research recently had a new head office built in Leiden: aesthetically pleasing, but also technically complex. SRON set very strict requirements for the flooring in the new building. And that meant it was time to call in Bolidt. Floors were devel oped, tested and installed spe cially for this scientific institute.
Technically complex SRON recently had a new head office built at the Bio Science Park in Leiden. The spacious, transparent building consists of offices, cleanrooms, laboratories and workshops situated around a ‘connecting atrium’ intended to stimulate collaboration within the institute. The building, with total floor space of approximately 10,000m2, has emerged as a calling card that enables SRON to present itself in style internationally. The new ‘Earth base’ of the renowned institute is not only aesthetically pleasing, but also technically complex. SRON’s activities are very sensitive, so the institute sets extremely high standards for its accommodation. For example, the floors must be completely free of vibration, rooms must be free of dust, and there must be no electromagnetic radiation inside the building. To give an impression of the technical complexity of the new building, sterile areas such as cleanrooms and cryogenic facilities (cryolabs) are built on a lowvibration, solid concrete floor slab covering 5,000m3 and supported by a whopping 8 tonnes of rebar. Conditioned airlocks shield these spaces from radiation and dust. Working together MedicomZes – a Visser & Smit Bouw brand and part of VolkerWessels, one of the largest construction companies in the Netherlands – was responsible for the construction of the new SRON head office. As a specialist construction partner, MedicomZes has been delivering projects for healthcare, hospitals, laboratories and cleanrooms for more than 40 years. With its extensive knowledge and experience, the company was the right party to realise SRON’s new high-tech accommodation. To carry out the project, MedicomZes formed a construction consortium with technical installation company WhatKuijpers.applied to the building as a whole also applied to the floors of the new building: these also had to meet very specific technical requirements. Ed Lenting, project manager at MedicomZes, explains: ‘As construction partners, we sat down with SRON during the design phase. It was immediately clear to us that we also had to quickly involve Bolidt in the project. Bolidt distinguishes itself from other New high-tech building to house expertise centre for space research
It’s perhaps not what you expect to find in the Netherlands: SRON Netherlands Institute for Space Research (SRON). This globally renowned organisation conducts research in the fields of astrophysics, Earth observation and exoplanets – planets that orbit a star other than the sun. SRON analyses data from space telescopes and other sources and develops and builds parts, instruments and accessories for satellites of the European and American space organisations ESA and NASA, among others. SRON’s technology has contributed to many space missions over the years.
SRON, MedicomZes and Bolidt: a formidable team
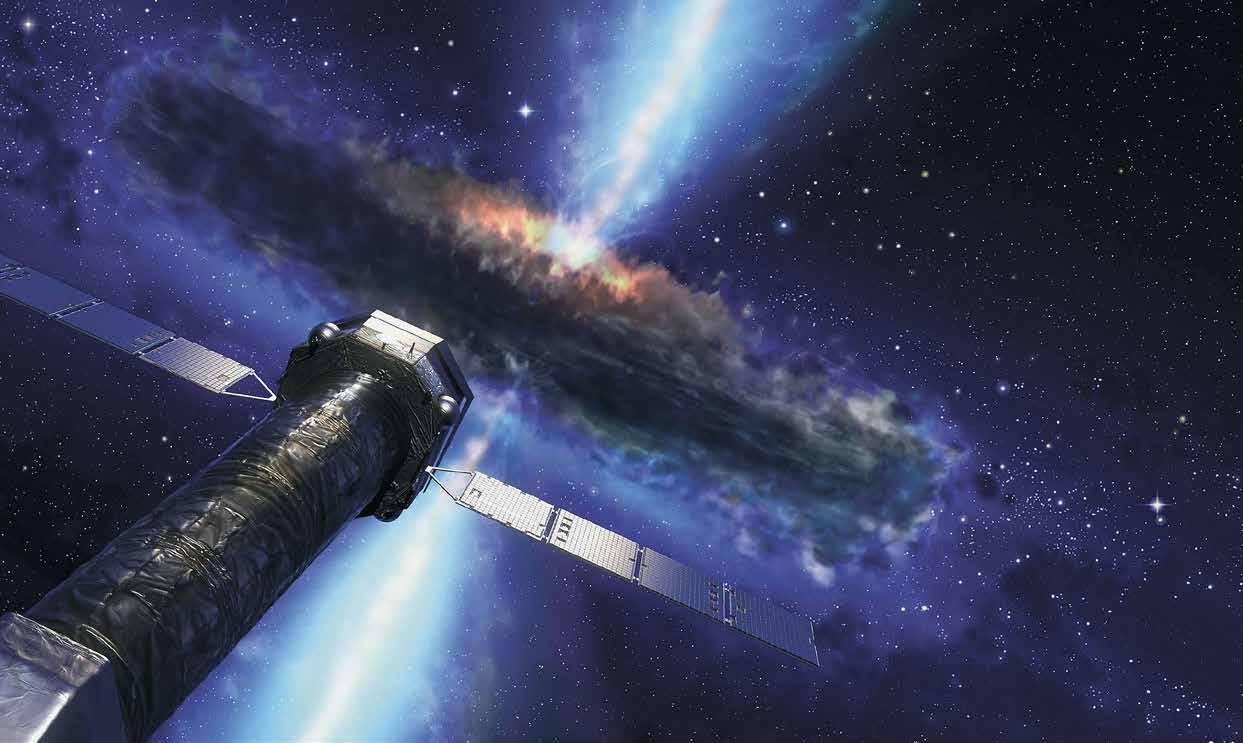
Nicole Tieman: ‘Because Bolidt developed the floors specially for SRON and also installed them, we were able to ensure that they could fully meet the requirements of the BREEAM Excellent certificate. When it came to sustainability, too, we had control over every aspect.’
Looking back, this really succeeded too: SRON, Bolidt and MedicomZes completed the project together.’
Ed Lenting: ‘The Bolidt Innovation Center was the perfect place to extensively test the flooring. We made a trial installation and then SRON performed measurements on the ESD flooring with its own calibrated equipment. Bolidt carried out its own measurements and these separate sets of measurements agreed. The Bolidt flooring offers sufficient protection against electrostatic charging: the “body walking voltage” of well under 100 Volts was achieved.’
Electrical discharge
At the initiative of Bolidt segment manager Nicole Tieman, the functional requirements for the floors were discussed at the Bolidt Innovation Center where SRON, together with its construction partners, held close consultations with the technical specialists of the Bolidt R&D centre. One of the requirements that SRON set for the floors in the cleanrooms and cryolabs was that they would have to perform optimally in the area of electrostatic discharge, or ESD. This means that the floors must discharge static electricity in a controlled manner so as to prevent static charge generation on people and equipment.
In addition to the requirements in the area of electrical discharge, it was also important for the client that the floors would perform well in use, says Nicole Tieman. She was also involved in the project from start to finish and was the single point of contact for SRON. ‘The Bolidtop® 700 College floor system, a seamless floor that is very wear-resistant and requires little maintenance, has been installed throughout a large part of the new building. To be really sure of the flooring, together with the people from SRON we visited various reference projects so that they could see with their own eyes – and hear from actual users – how the Bolidtop® 700 College performs in practice.
19 suppliers thanks to its specific knowledge of floors for cleanrooms and laboratories. Moreover, they also have their own R&D and production department, meaning we could also develop the floors of the new building together with Bolidt.
BREEAM Excellent The new SRON head office has also turned out to be a very sustainable building, good enough to earn a BREEAM Excellent certificate for sustainability. The new head office meets an extensive set of sustainability requirements, not only in terms of the end result, but also during design and construction.

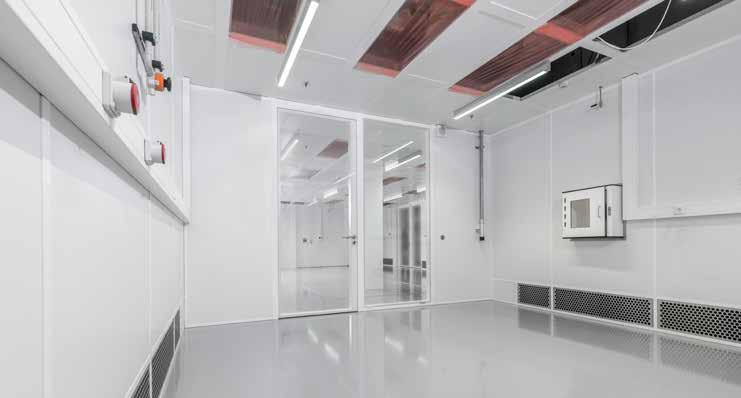
Perfect balance In Oosterwolde, Tyson recently laid a perfect foundation to realise this ambition: the company opted (once more) for a Bolidt floor. The existing watertight, wear-resistant Bolidtop® floor had served the company for the last 30 years, truly proving its worth. For the production plant, including the extension, Tyson chose the Bolidtop® 700 system to cover a total of 7,000 m2. Over the decades, Bolidt’s R&D department has further developed this floor system and now it aligns even better with all Tyson’s requirements: it’s durable and wearresistant, and it’s heavy duty when it comes to handling heavy equipment and chemicals. The new Bolidtop® 700 floor also meets Tyson’s requirements in the field of quality, health and safety (of employees and of food) – the key pillars of the company’s business operations. The synthetic floor system is seamless and pore tight, meaning extremely hygienic. The wear resistance prevents cracks from forming, which in turn prevents the growth of bacteria. For optimum hygiene, the skirting has also been produced by Bolidt. Thanks to the seamless design, bacteria have zero chance of getting a toehold here too. The new floor is also easy to clean on a daily basis, another important feature for the food company. And the non-slip surface ensures the safety of employees. On to the next 30 years.
Tyson20
Tyson Foods lays the foundation for sustainable ambitions
For the global meat giant Tyson Foods, having a good relationship with the local community is important. That’s why the company’s production plant in Oosterwolde is happy to contribute to social projects, which it does regularly. What’s more, Tyson has ambitious plans in the field of sustainability. The foundation for this was recently laid – literally – with a wear-resistant Bolidt floor.
Meat concern again goes with a Bolidt floor after 30 years
Foods is the second largest processor and marketer of chicken, pork, and beef worldwide. In Oosterwolde, in the province of Friesland, the company makes ready-to-use chicken products like chicken nuggets and cordon bleu for the catering and retail sector. Due to increasing demand, Tyson Foods recently expanded its annual production capacity in Oosterwolde by 38,000 tonnes, twice the current production capacity. That means more employment right off the bat. From the current staff of 200, the company expects to grow to 350 employees in the coming years. What’s special about the Frisian site of the meat giant is its strong bond with the region. Tyson Foods not only creates jobs, but also creates work for local businesses like logistics companies. Tyson also works with regional educational institutions and knowledge centres and invests in people with poor job prospects. In addition, the group regularly contributes to the community through various social projects, such as supporting a local Ronald McDonald house. Having a good relationship with the local community and society as a whole is important to the Frisian branch of the multinational, as is sustainability. Tyson Foods has the ambition to become one of the most sustainable companies in its industry in Europe. The multinational states that it wants to be at the forefront of the energy transition and so, over the coming years, will be setting up its production and logistics processes to run as efficiently and sustainably as possible. The company says it will allocate €50 million to facilitate this.
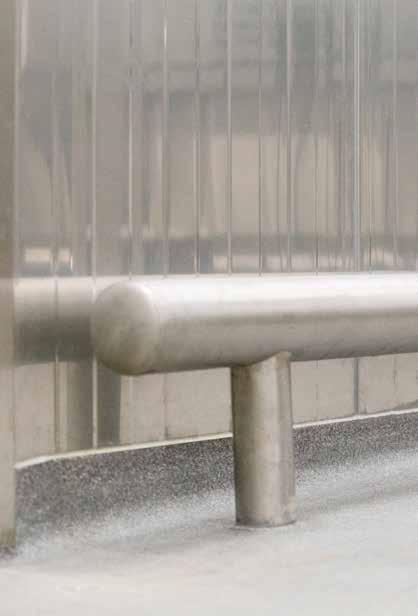
Sandstra Industry is part of the Sandstra Group, specialists in stainless steel drainage systems and collision barriers.
21 Sandstra For the Tyson Foods project, Bolidt (Dennis) introduced us to the contractor Dijkham Bouw.
The original plan included protective skirting with the intention that Bolidt would finish the exterior of this with the same product applied on the floors. In consultation, we offered an alternative in the form of full stainless steel from floor to wall so that Bolidt would not have to apply the product along the narrow edge at the top of the skirting. By using completely stainless steel skirting, this immediately addressed future maintenance, while a permanent, fully hygienic whole was guaranteed. On the underside, the skirting has a special shallow recess 4 to 5 mm deep that allowed Bolidt to coat the hollow skirting with a single coat. In addition, we supplied and installed around 1,300 meters of wall protection barriers. We installed these barriers both on the ground floor and the upper floors once Bolidt was finished so that the feet would not pose an obstacle when applying the various layers of the floor, and the floors could be installed smoothly and easily. On the ground floor, holes were drilled into the floor into which the fencing legs were sunk and secured with casting mortar. These holes were then finished by Bolidt as to ensure an even surface in terms of structure and colour.
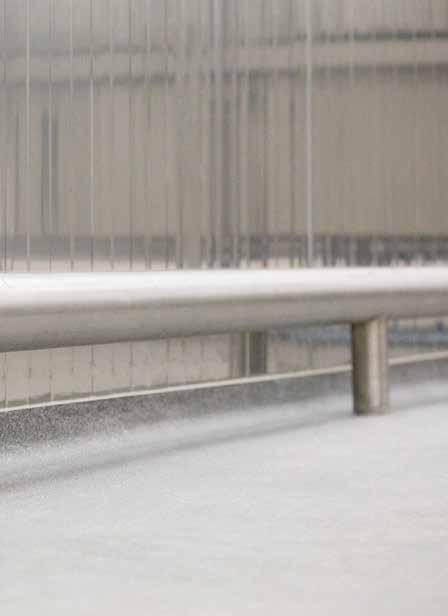
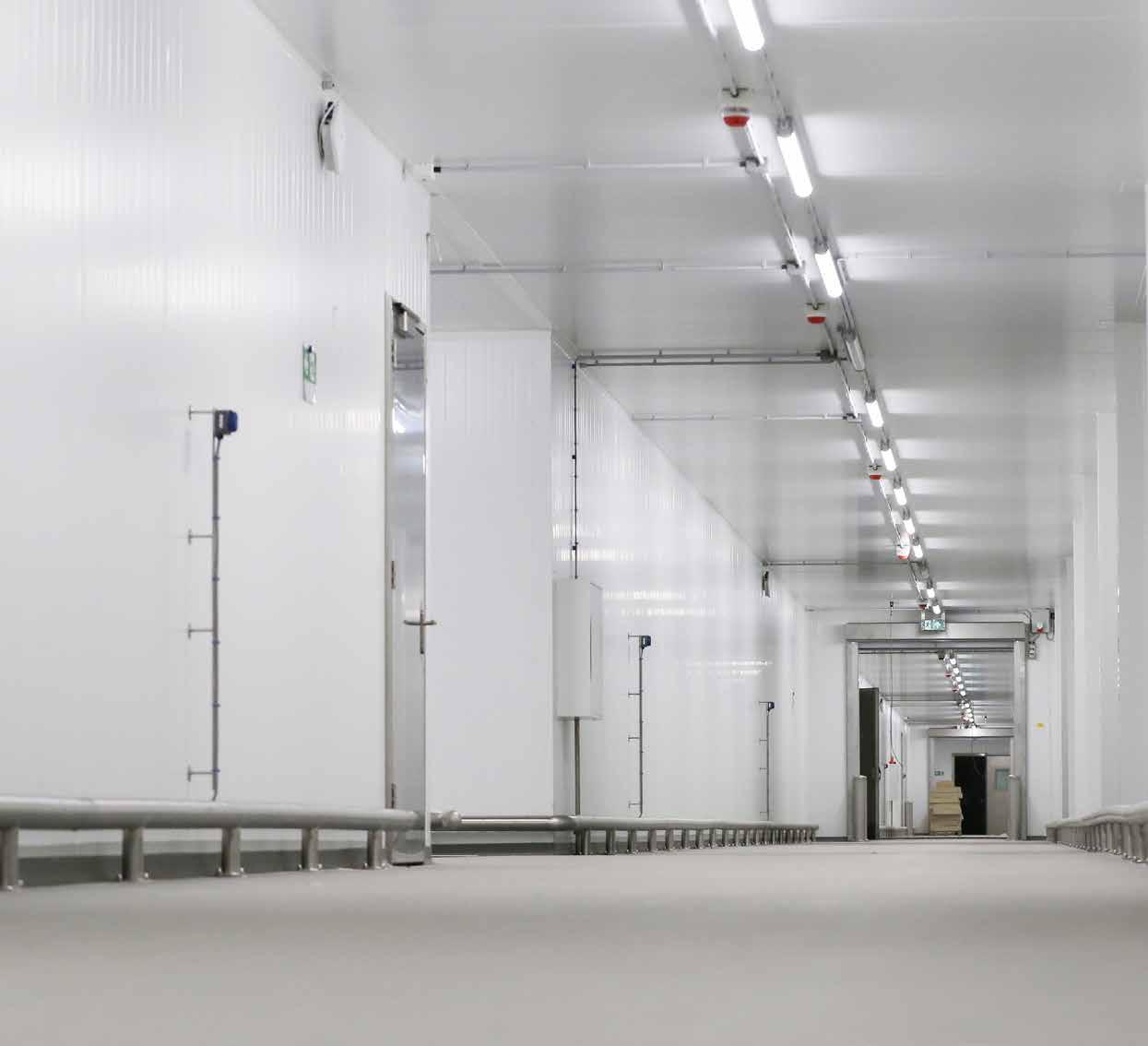
Work22 progressin
NORWEGIAN PRIMA Norwegian Prima is the first cruise ship with a go-kart track spread over three decks. Our application team say that they broke all speed records when applying the deck.
OSB For the Bijlmer Open School Community (OBS), the architect and the school worked together to create a design where connection between the spaces was the central focus. You could see the concept springing to life as the templates were being applied to the floor.
“Almost every day, the architect came by to see how her design was coming along“
‘But why’, you ask? Well, the track they needed to install was an impressive 420 metres in length!
On an annual basis, Bolidt covers around 2 million square metres with its floor and decking systems in various application areas, from floors in chicken hatcheries to wearing courses on roads and bridges and from hygienic floors in hospitals to sustainable decks in the maritime industry. Our application teams are flown in all over the world.
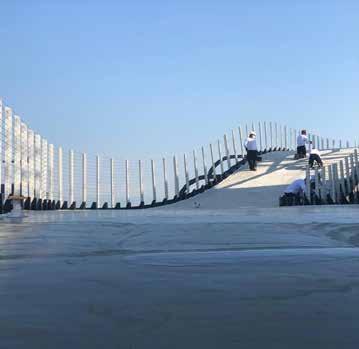
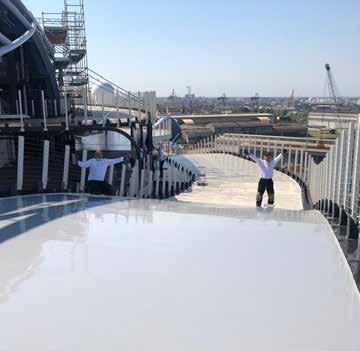
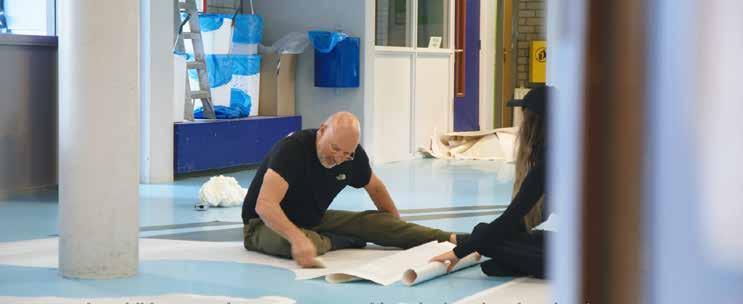
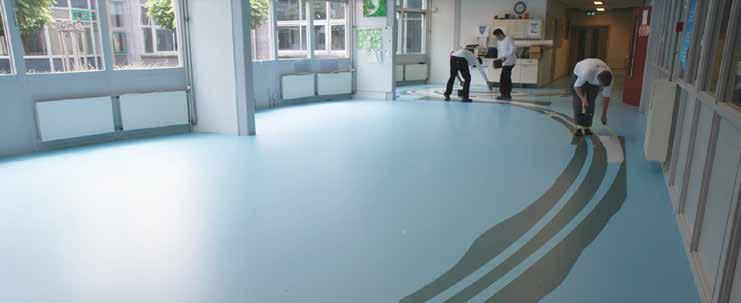
SLUISHUIS In Sluishuis you live in the city and yet in the midst of greenery and water. The residents of this highprofile building were curious about the progress of the works.
MAASTUNNEL Connecting the banks of the Nieuwe Maas in Rotterdam, the tunnel under this distributary is the oldest submerged tunnel in the Netherlands. The tunnel consists of four tubes: two for cars, one for cyclists and one for pedestrians.
Installing a new wearing course at the entrances and in the 565-metre-long bike tunnel.
23
“The tunnel had to remain open for cyclists while this floor was being created. This was a challenge,butitalso created a nice dynamic.’
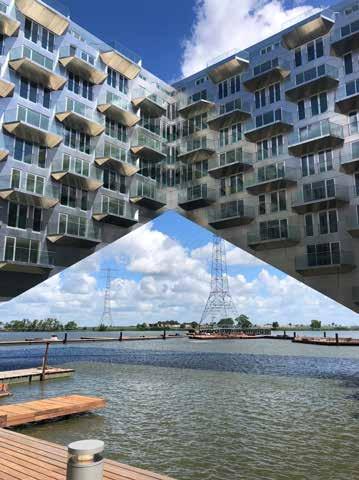
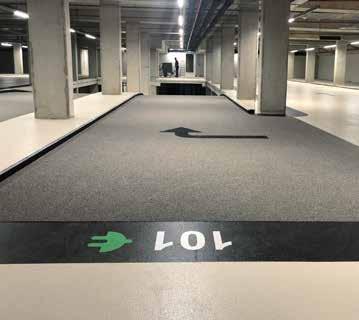
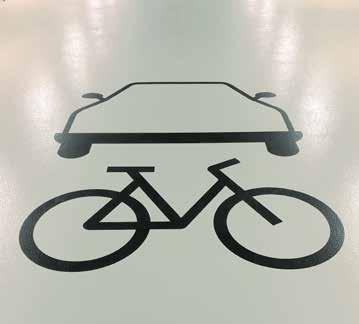

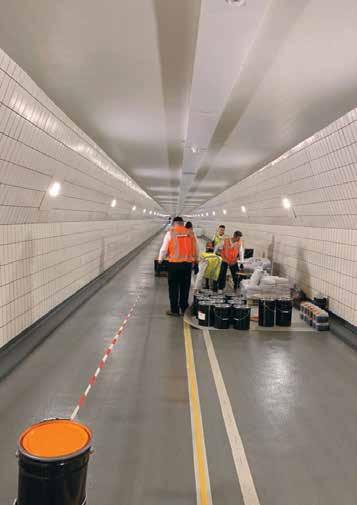
Ever since its establishment in 1964, Bolidt has been on a mission: the company aims to replace traditional materials with sustainable alternatives. The maritime industry is one of the areas where Bolidt has a string of sustainable innovations to its name. Bolidt continues to fulfil its mission in this sector, through innovations, sponsorship, partnerships and knowledge sharing.
PlanetPeople BolidtProfit
In the area of sustainability Bolidt innovates and inspires
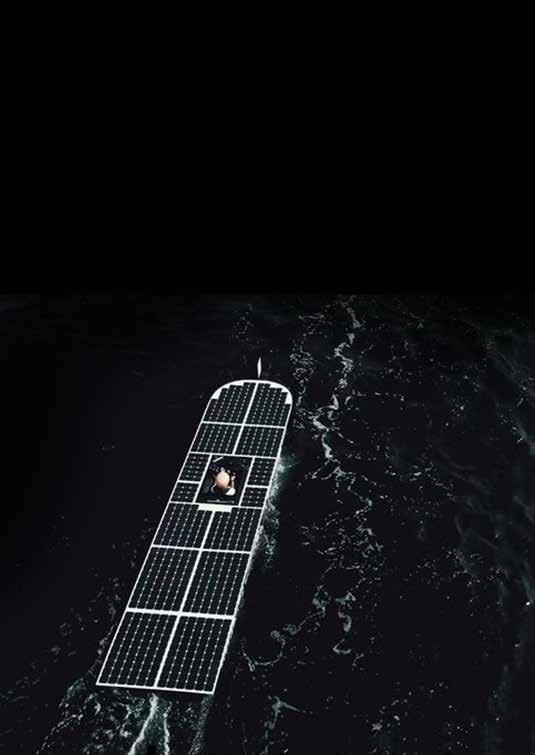
25
Talk about foresight: ‘People-PlanetProfit’ has been central to Bolidt’s business operations from the start. The mission of the founders in 1964 was to replace traditional materials with sustainable alternatives. What’s more, the company decided on a remarkable strategy: to have complete control. According to Bolidt, it was and still is the best way for a company to work as sustainably as possible. That’s why the company controls the entire production chain, from R&D to installation.
And because it has control over all aspects, Bolidt can optimally coordinate the entire process and always choose the most sustainable solutions. Bolidt also works using the LEAN methodology; with this management philosophy aimed at continuous improvement, Bolidt combats waste and eliminates elements that do not offer added value. To reduce the amount of waste, for example, parts of the production process are moved from the production site in the Netherlands to the various construction sites around the world. This saves on packaging material and unnecessary transport.
Flying hydrogen boat
One of the work areas where Bolidt is taking the lead in the field of sustainability is the maritime sector. Since its foundation, Bolidt has been involved in the design, development and production of sustainable ship decking. This has resulted in the innovative Bolideck systems that are not only functional, but also an inspiration in the industry. As far as Bolidt is concerned, it does not end here, either, as is apparent from the Maritime Sustainability Report, which focuses on the years 2021 to To2030.share its expertise and gain new knowledge, in 2022 Bolidt became a sponsor of the Solar Boat Twente team. Solar Boat Twente team, Solar Boat Twente encourages environmental awareness by applying renewable energy to the maritime sector through the design, development and optimi zationofareliablesolarboat.By pushing boundaries, the multidis ciplinary team embraces a major challenge: designing and building the powerboat of tomorrow. During the visit to the Bolidt In novation Center, knowledge was shared and ideas exchanged.
Bolidt not only develops raw materials – as natural as possible – for the synthetic systems, but also the equipment used to produce and process these.
Given such an outspoken mission, it goes without saying that Bolidt products are extremely sustainable. In fact, the durability of the synthetic systems has only increased thanks to ongoing innovations.
The Bolidt products retain their functionality, strength and colourfastness for virtually their entire service life. There’s no better way to reduce our carbon footprint (and that of our clients).

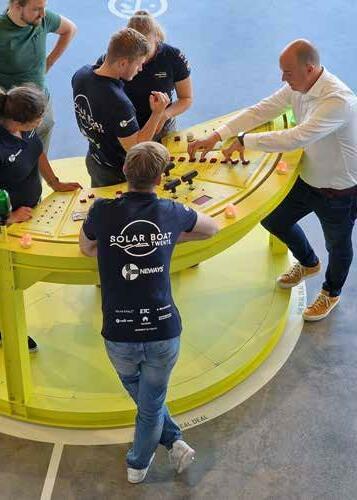
ALGAE LIFECYCLE FLOOR © Thorben Stubbe
26 are focused on creating an efficient solar-powered boat. You might wonder how this contributes to their aims of leading a movement towards sustainability?
Well, first some illustrative facts. Maritime transport alone is responsible for approximately 2.5% of global greenhouse gas emissions. However, contrary to what you would expect, ships were found to be (on average) less fuel-efficient in 2013 than they were in the 1990s. Moreover, while other sectors are successfully reducing their carbon emissions, it is estimated that the maritime sector can account for up to 10% of global greenhouse gas emissions in 2050. Our conclusion: the maritime sector really needs to step up its efforts to decrease its contribution to global greenhouse gas production.
The Solar Boat Twente team has set out to chart the possibilities for a sustainable maritime sector and inspire the industry to take steps towards a more sustainable future, a mission that aligns perfectly with that of Bolidt. Bolidt has also been investigating for some time now how a ship’s decking can be used to generate power. By sponsoring the Solar Boat Twente Team, Bolidt aims to share its knowledge and experience and, in return, gain inspiration from the students. The team has already visited the Bolidt Innovation Center this year to brainstorm on collaboration and possible sustainable innovations. Energy-generating dance floor In the maritime sector, Bolidt is the world market leader when it comes to decking for cruise ships. Bolidt has worked for years with many of the largest shipyards and shipping companies in the world. Innovative systems have emerged from these partnerships, as can be seen, for example, in the collaboration with Meyer Werft. This originally Dutch family business has been around for more than two centuries and is now one of the largest cruise ship builders worldwide. Like Bolidt, Meyer Werft is driven by knowledge and innovation. It is therefore not surprising that late last year Bolidt presented the first Design Challenge Award to Meyer Werft’s concept designer Thorben Stubbe, creator of the innovative concept ‘Algae Lifecycle Floor’ (ALF). This carbon-negative system for the cruise industry is now being further developed at the Bolidt Innovation Center and will hopefully be on board cruise ships in the near future.
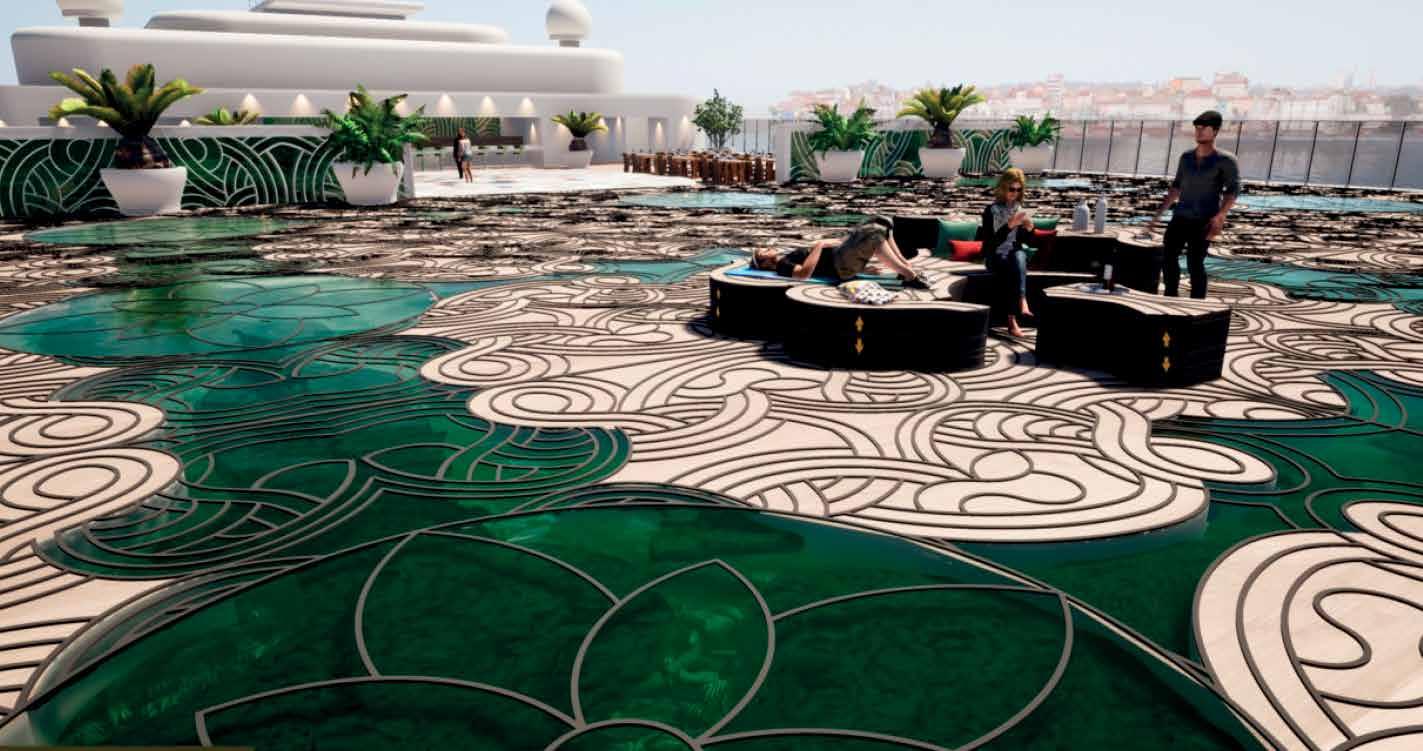
27
Who better to make recommendations about the future than the next generation? And that’s exactly why Bolidt has launched the project The Next Generation. A group of young Bolidt employees and children of Bolidt staff are thinking about the impact that Bolidt can make in the area of People-PlanetProfit. As ‘internal consultants’ they tackle issues from various departments. The United Nations Sustainable Development Goals (SDGs) are the standard against which Bolidt’s initiatives are measured. The Next Generation aims to ensure that Bolidt will continue to be a great place to work in the future too and continue to contribute to a world that is more sustainable.
ALF is a living, breathing system comprising lightweight, hardwearing, sustainable materials including soya resin, hemp fibre and bamboo. The system includes a bioplastic water tank containing live algae, which convert carbon dioxide into oxygen, and Pavegen tiles, which harness kinetic energy from footsteps to generate electricity. ALF can be used in both indoor and outdoor spaces in the form of flooring, partitioning, wind protection or wall decoration. In its inaugural concept, ALF has been presented as a dance floor where people generate electricity with their dance moves. This electricity is used, for one, to power the pumps needed to cultivate the algae. The award was presented to Stubbe thanks to his concept that allows floors and walls on cruise ships to convert carbon dioxide into oxygen while also generating energy, meaning this concept can make a valuable contribution towards reducing the cruise industry’s carbon footprint. And that’s exactly what Bolidt has in mind. For more information Download the Maritime Sustainability Report 2021–2030 at bolidt.nl.
The Next Generation
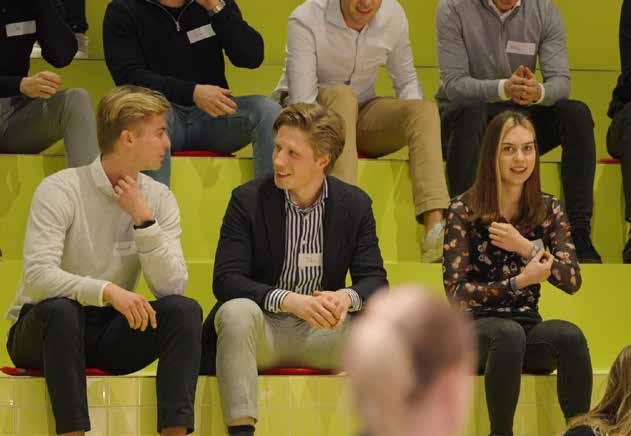
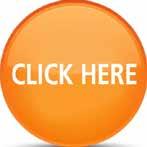
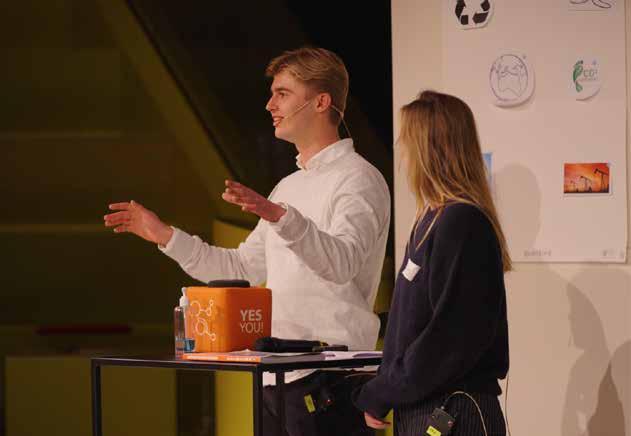
‘The basic ideal is that you use all the resources at your disposal. Your team is just one of those resources. It used to be that the Captain made all the decisions, and if he made the wrong decision, it could have dramatic consequences. As humans we are not flawless. We can be distracted by all kinds of things and also make miscalculations.
Theever.spot on the horizon
When the Wright brothers made the first-ever powered airplane flight on 17 December 1903, they didn’t have a single instrument in the cockpit. They were ‘flying blind’ so to speak. That was well over 100 years ago. On an Airbus, thanks to the vast array of instruments and systems, the pilots can now fly from point A to point B almost literally blind. As a result, flying has not only become safer, we also fly further than
‘In the beginning we also set our course purely based on what we heard and saw,’ explains Rientz Willem Bol, CEO and owner of Bolidt Group. ‘These days we measure all the key data, which enables us to look further ahead than ever and safeguard our social licence to operate in the future too. And I’m not talking about five or fifty years, but about 500 years from Togethernow.’ with the CEO and André van Geest, Boeing 737-800 Captain and instructor, we discussed the added value of a cockpit with all the bells and whistles. Rientz Willem also has his pilot’s license. He sets the course for Bolidt. ‘I love adventure and want to discover and push boundaries, but with one important stipulation: everything must be well prepared. This applies both in my private life and with the company. To ensure this I want to have something to hold on to; I need correct, up-to-date information, forecasts and a reliable team with commitment.’
And
‘Even if you’re flying with someone who hasn’t clocked up many hours yet, their opinion counts. After all, this person looks at situations from a different perspective than someone who perhaps by now largely relies on experience. We actually no longer talk about Captain and copilot, but rather a “Pilot Flying” and a “Pilot Monitoring”. Both have the same information and can make decisions based on this. If there is a difference of opinion, you discuss this so that you can ultimately make a well-considered decision. However, each pilot has their own area for which they are responsible.
Crew Resource Management André says that in aviation they talk about Crew Resource Management.
Setting a safe course based on standardisation and data
More and more in the world of business is being driven by data. KPIs are drawn up and monitored on every type of dashboard imaginable at every level and in every department. This flow of information allows you to make quicker and more targeted adjustments when a potential deviation from the course is detected.
Nowadays, though there is still a Captain and co-pilot (officially ‘first officer’), decisions are made together and in consultation, with the Captain having the last word.
For example, Pilot Monitoring is responsible for the radios and landing gear and Pilot Flying for all engine-related instruments.
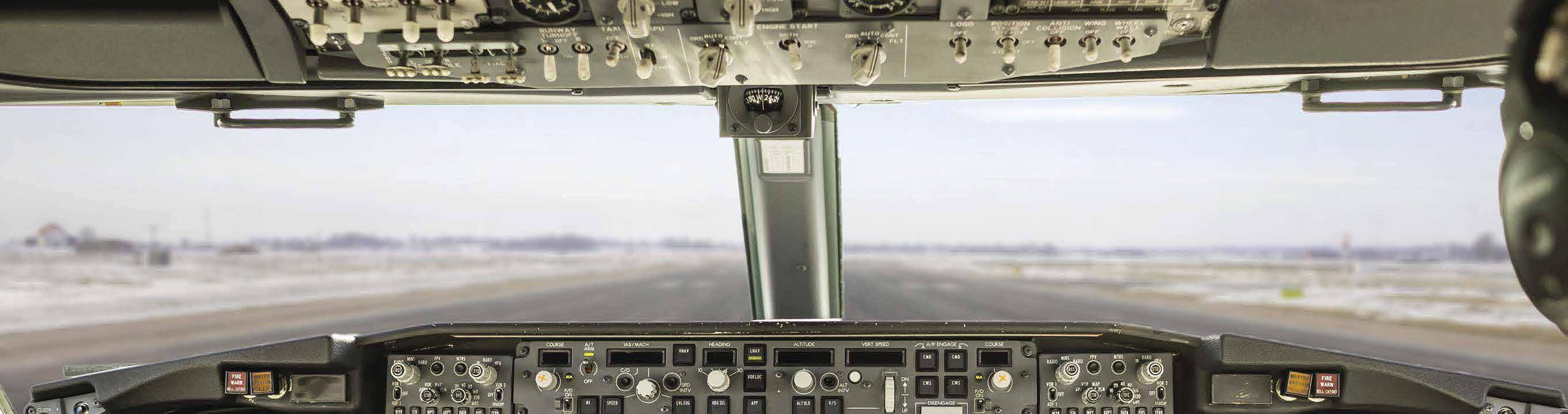
The more experienced you are, the better you can take corrective action independently. We escalate at specifically defined moments when business-critical issues arise. ‘With my team I communicate directly with the managers who, in turn, communicate with our people in the field; this way we know what’s going on each and every day. We also collect information from the market, such as feedback from our clients, laws and regulations, new government requirements regarding safety, the environment and sustainability, and other developments with a direct or indirect impact on our mission. This way, in the event of sudden changes you can make adjustments along the way. With the arrival of Covid-19, we saw a key market, the cruise industry, almost literally disappear. That was a real “Mayday moment” when we had to drastically adjust our course. And that’s why it’s so important to have a “diversion plan” that looks beyond the short term. If you know what your objective is in the long term, you can make more informed decisions at times like that.’
That’s how Rientz Willem sees it too. ‘I do set the course, but I rely on the people in my organisation while underway. Everyone at Bolidt knows our course. We all work the same way based on the same information. Each department has its own objectives and responsibilities. The teams know what information is needed, what we measure and how, and each team carries out their dayto-day operations on their own. At every level, we discuss the state of affairs every day and any departures from the norm that require action.
Dashboard and scripts ‘So a dashboard in your company is also a kind of cockpit?’ ‘Absolutely!’, says Rientz Willem. ‘And especially if you set it up in such a way that every team can quickly and easily understand the current status and the impact. At Bolidt we almost all work according to the same standards and use “A dashboard in your company is also a kind of cockpit”
‘In addition, of course, we also have to deal with the cabin crew and passengers. Before the flight there is always a crew meeting with an extensive briefing about all flight conditions. What weather can we expect? Will there be stops along the way? Is there anything we need to know about the passengers? During a standard flight, we communicate with the team in the cabin every twenty minutes about standard events like “unfasten seatbelts” and the start of the landing, as well as about any matters that need attention. For example, if a passenger falls ill we have to decide whether we need to make an emergency diversion. We also depend on outside information, from air traffic control at the departure and destination airports. What are the conditions on the strip and in the air? How busy is it? Can we take off or land? Or should we perform a go-around or even divert to another airport?’
and beyond they both have access to all the instruments if needed. Sometimes one of the pilots leaves the cockpit and then the other must be able to continue flying.
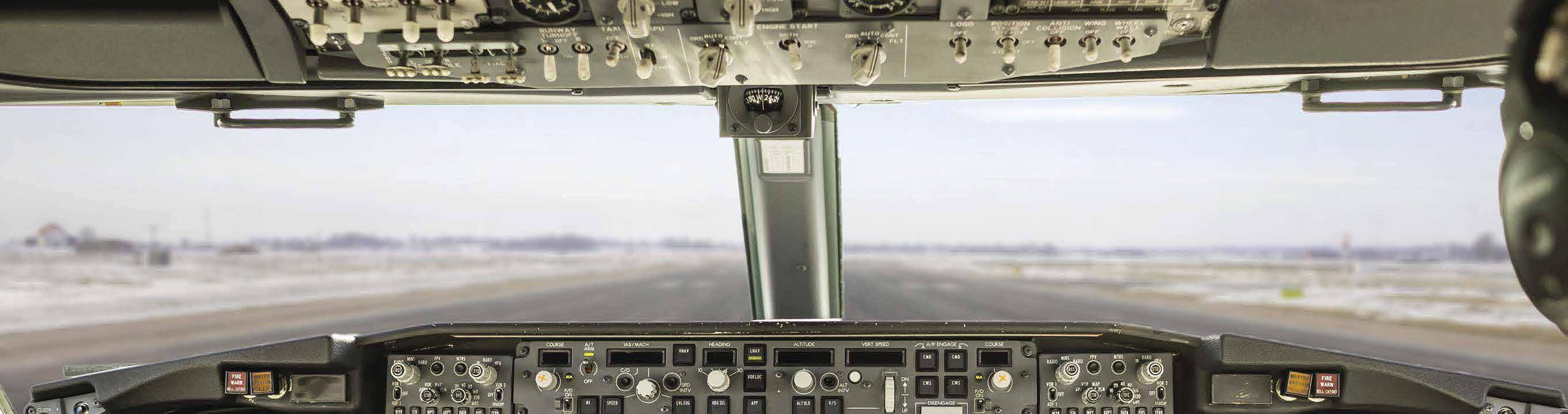
‘In principle, a cockpit always has the same six-pack of gauges: an airspeed indicator, altitude indicator or artificial horizon, altimeter for altitude above sea level, vertical speed indicator, heading indicator or compass, and a turn coordinator that indicates whether a turn is being made at the standard rate’, André explains. ‘In addition, each type of aircraft has its own specific systems and instruments for additional functions, such as communication with other aircraft. Furthermore, for 99.9 percent of the system deviations there are standardised checklists and procedures describing step by step what to do if a red light comes on somewhere. We always follow these when a situation like this arises, even when you think you already know how to handle the situation. In addition, as much of the critical information as possible is shown in a visual, easy-tounderstand manner. For example, the maximum temperature of the engine is not indicated with a number, but rather a red line that simply must not be exceeded. In emergency situations, you can see the critical situation at a glance and take action without having to think too hard or make calculations.
André van Geest
“At the end of the day, it’s executing as much as possible. Reality can never be simulated 100 percent.”
Bolidt also works using standard data throughout the company, supplemented with department or team-specific data. Rientz Willem takes the comparison a little further: ‘In addition, we have standardised an increasing number of activities so that employees can quickly and easily take over each other’s work. We also make use of visualisations, for example concerning the phase a project is in or the status of a task. Like in aviation we, too, work with scripts. Though we don’t have crew meetings, we do have concept. If there are any issues or major problems, these will be discussed and, based on impact,
the30same methodologies and instruments. Naturally, we don’t have two people in one cockpit. A company consists of various departments and teams. And actually, every department or team has its own dashboard showing the key data. We have also shaped a general dashboard in the form of a traffic light model in a central location where we monitor, at a higher level, all business activities across all teams, discuss the status and look ahead. This is possible because we have defined leading and lagging information.’
‘The two pilots continuously communicate aloud with each other about the status. You can only do that while you are flying if communication is standardised as well. Every pilot around the world basically communicates, in English, using the same standard messages and commands. There are, however, differences in laws and regulations between the United States and Europe, for example. And

Trainee pilots start their simulation training by looking outside and observing some of the gauges. It’s important that they first get the feeling of flying. Then the windows are blinded so they can learn to fly with instruments alone. After that, more and more non-standard situations are introduced during the training, as well as specific systems for each type of aircraft . You may only take your first flight once you know all the systems and procedures and common situations. Then you will apply them under the guidance of a trainer. And in the end it’s all about accumulating metres, or flight hours actually, initially on short, noncommercial flights. Reality can never be fully simulated though.
Rientz Willem Bol
André says in conclusion: ‘We could never go back to the situation the Wright brothers were in, flying blind, with no instruments at all. And especially not if you intend to fly a plane full of passengers safely over the ocean.’ ‘Or if you want to grow a company sustainably, without having to let people go if you suddenly have to deviate from your course’, adds Rientz Willem. Both agree on this: precisely because of all the tools and data we now have at our disposal – the automation and standardisation of actions based on years of experience and research –we are able to look beyond that spot on the horizon.
‘At Bolidt, the Lean & Learn philosophy and methodologies have been very helpful in getting us to where we are now. We expect everyone in our company to know and understand this,’ says Rientz Willem. ‘Many of our people at every level have followed training for this. New and less-experienced employees are also coached in this way of working in their day-to-day activities. You learn best by doing and by experiencing the benefits in practice. We also ensure that staff receive refresher training and hone their skills and knowledge on a regular basis. Through our Academy we organise several days a year to practice, share experiences and learn from each other and to reorient based on the insights gained.’
‘Based on their training, every pilot in the team can read the instruments and manage the flight on that basis. If something changes in a certain type of aircraft, if a new instrument is added or the philosophy behind a certain protocol changes and this requires different actions, then all pilots must be trained to deal with this change.’
31 insight and experience, will be either addressed and resolved immediately or escalated the same day so that a plan is drawn up.’
“I do set the course, but I rely on the people in my organisation while underway”
Training Training and continuous development are essential both in aviation and in a company that wants to continue to guarantee safety and agility. ‘Technology is constantly developing, and procedures, with regard to safety and security for example, are also constantly changing. In practice, pilots train and check their knowledge and skills twice a year. Every six months, every pilot undergoes retraining in the simulator to refresh their knowledge and experience. Once a year we are checked by the authority that issues our pilot’s licence. The training programme is designed such that all systems of an aircraft are covered over a three-year period.

The Bolidt Innovation Center Click here for a preview of the Bolidt Innovation Center
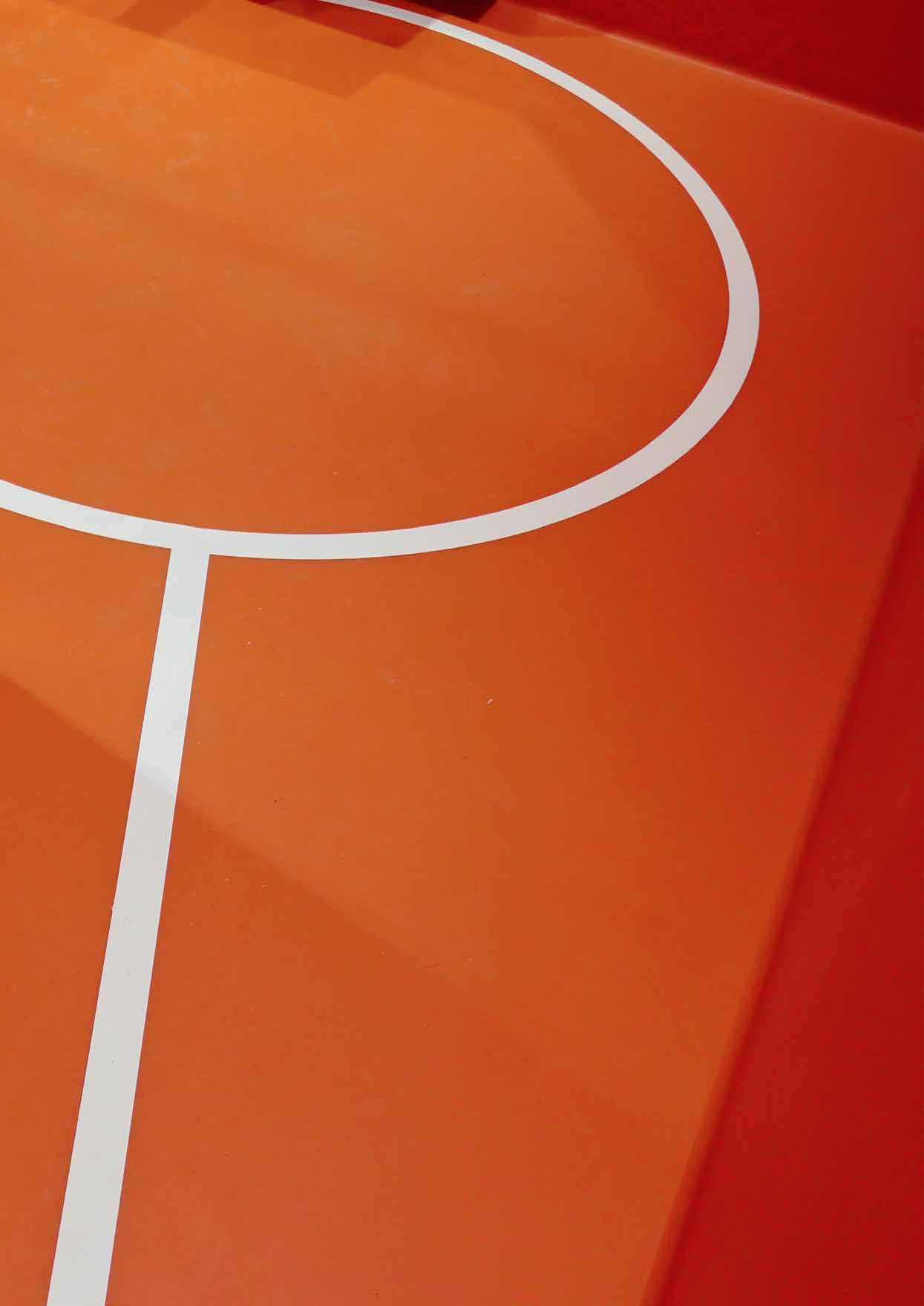
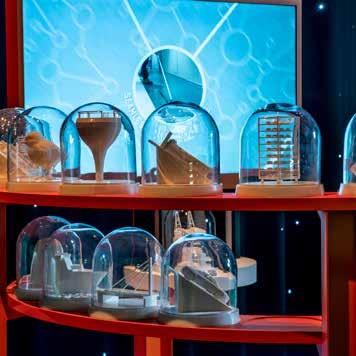
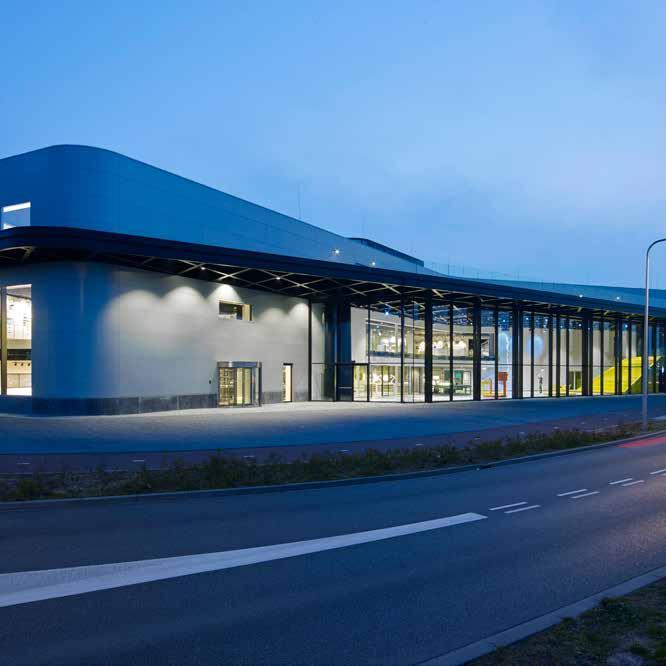
Bolidt is a pioneer in every sector in which it operates and focuses on innovation to enable its clients to excel in their profession. The drive to innovate has resulted in numerous groundbreaking, sustainable materials now used worldwide. Ours is a strong, enduring story, one that is too interesting to simply read about or hear told: you have to see it, feel it, experience it. And this is all possible at the Bolidt Innovation Center. Here we show how materials are made antibacterial at a microscopic level, how floors join up seamlessly with tiles, drains and skirting, and how materials are subjected to relentless mechanical testing, with the ‘Pounder’, for example, which is used to test the strength of the materials. But there’s much more too. You can put on VR glasses and virtually look over the shoulders of Bolidt staff working on projects around the globe. In the transparent R&D centre you can see Bolidt technicians at work; they are also ready to answer all your questions and explain everything in Ifdepth.youare not able to visit us, you can also sign up for a virtual tour. Our hostess will take you along a number of highlights in the centre, assisted by a ‘segment expert’.
During the tour we tell you all about the possibilities within your industry and answer any questions you may have. Your colleagues are also welcome to join the virtual tour.
33 Sign up here for the Virtual Tour
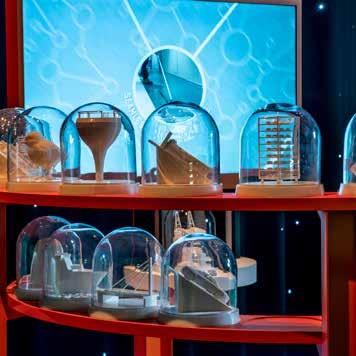

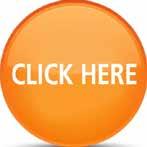
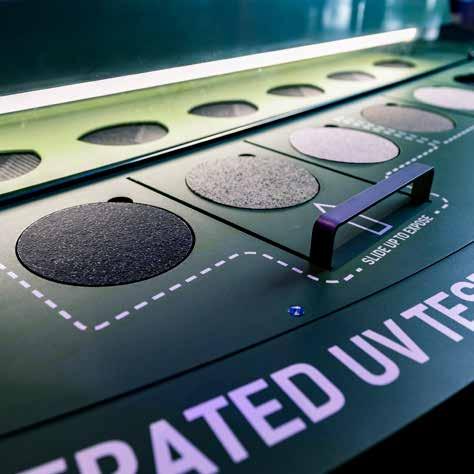
34 Bolidt Synthetic Products & Systems P.O. Box 131 3340 AC Hendrik-Ido-Ambacht The www.bolidt.comexport@bolidt.comNetherlands Bolidt Innovation Center Noordeinde 2 3341 LW Hendrik-Ido-Ambacht The Twww.bolidtinnovationcenter.comexperience@bolidt.comNetherlands+31786845444