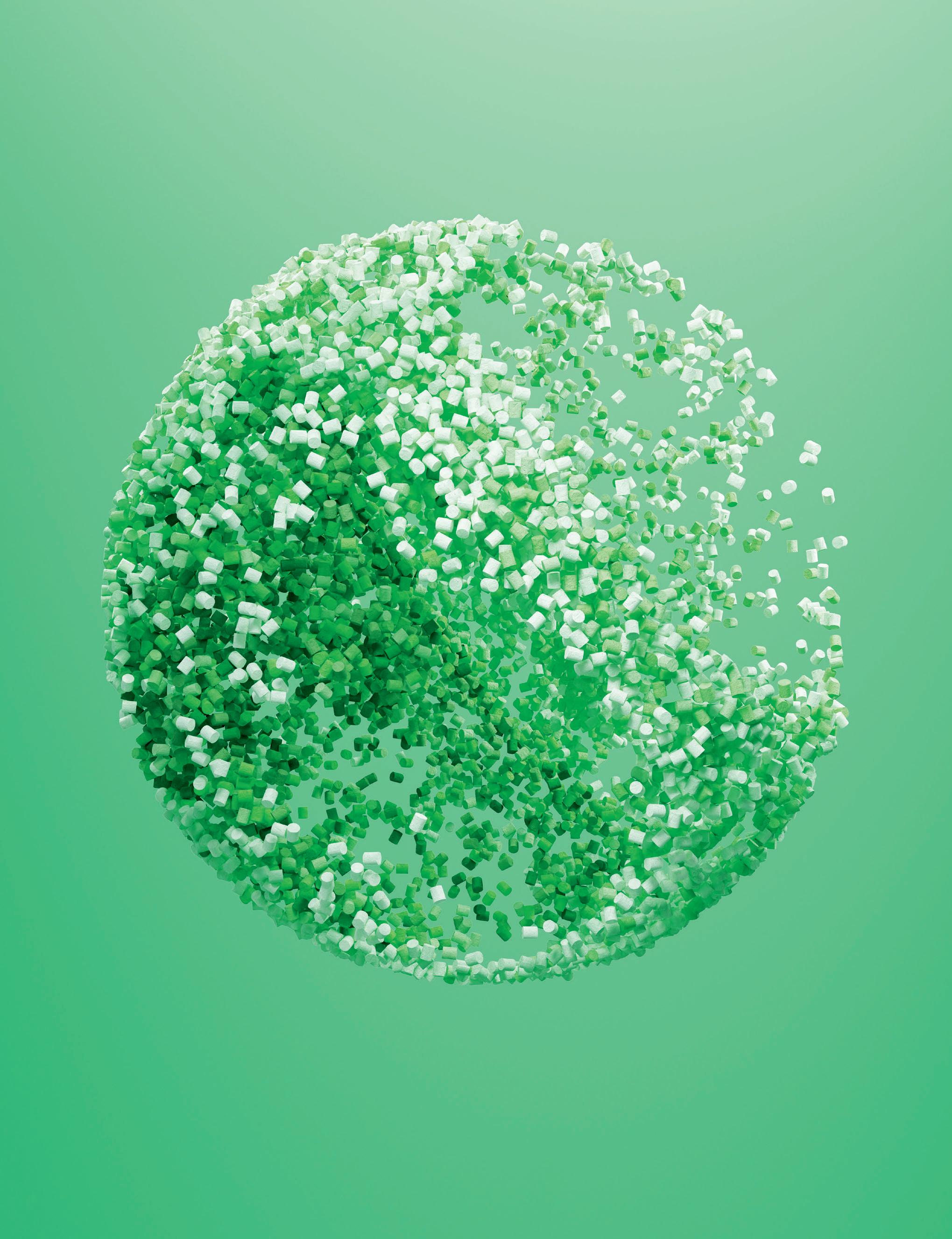
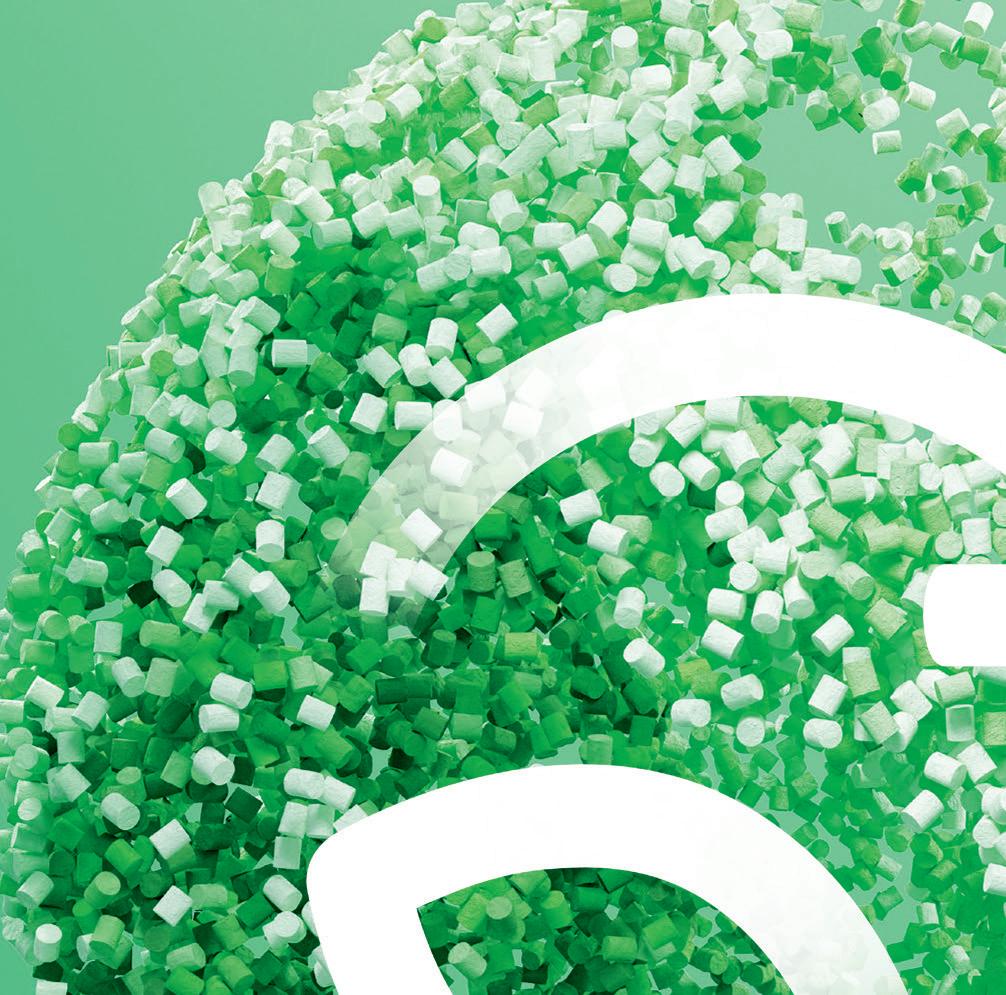
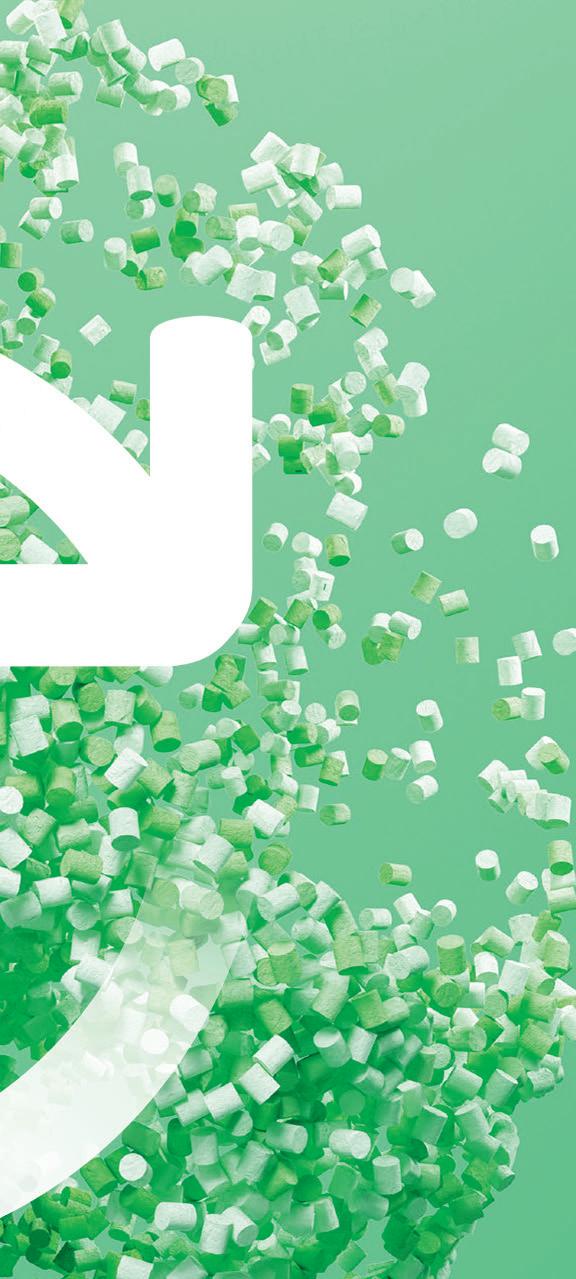
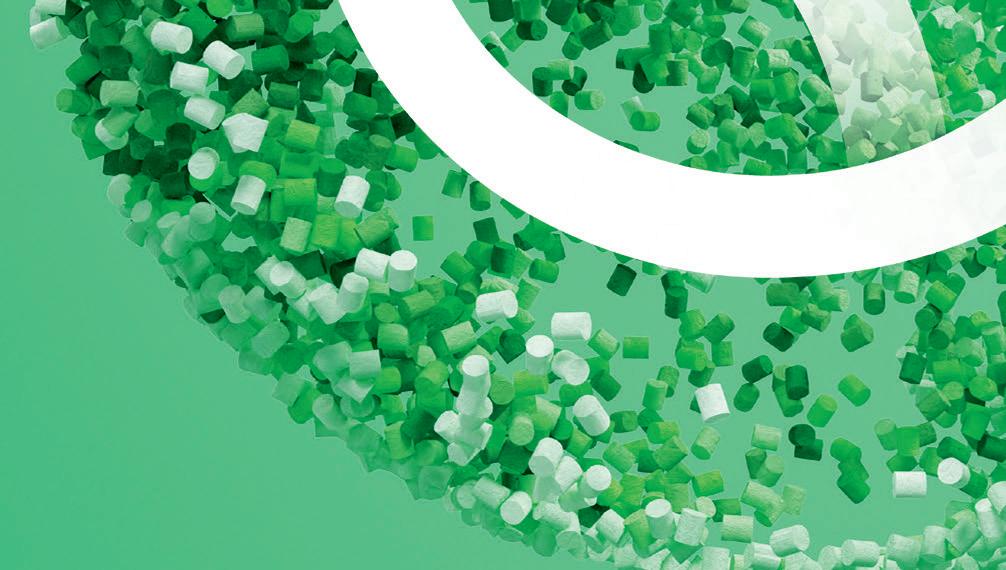
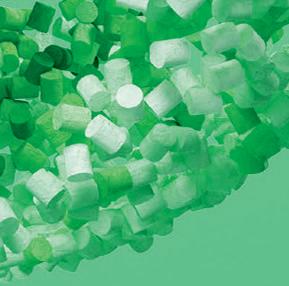
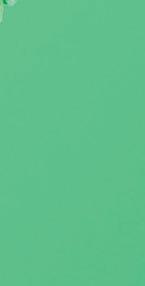

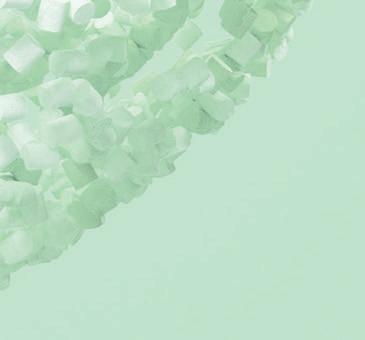
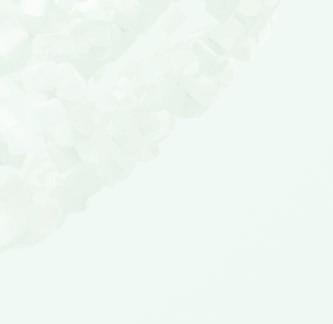

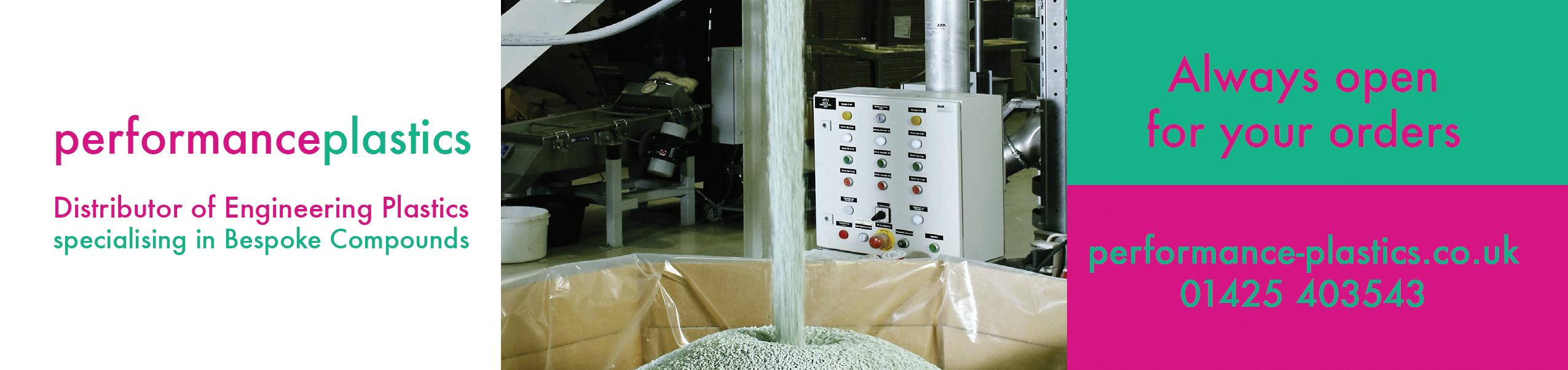
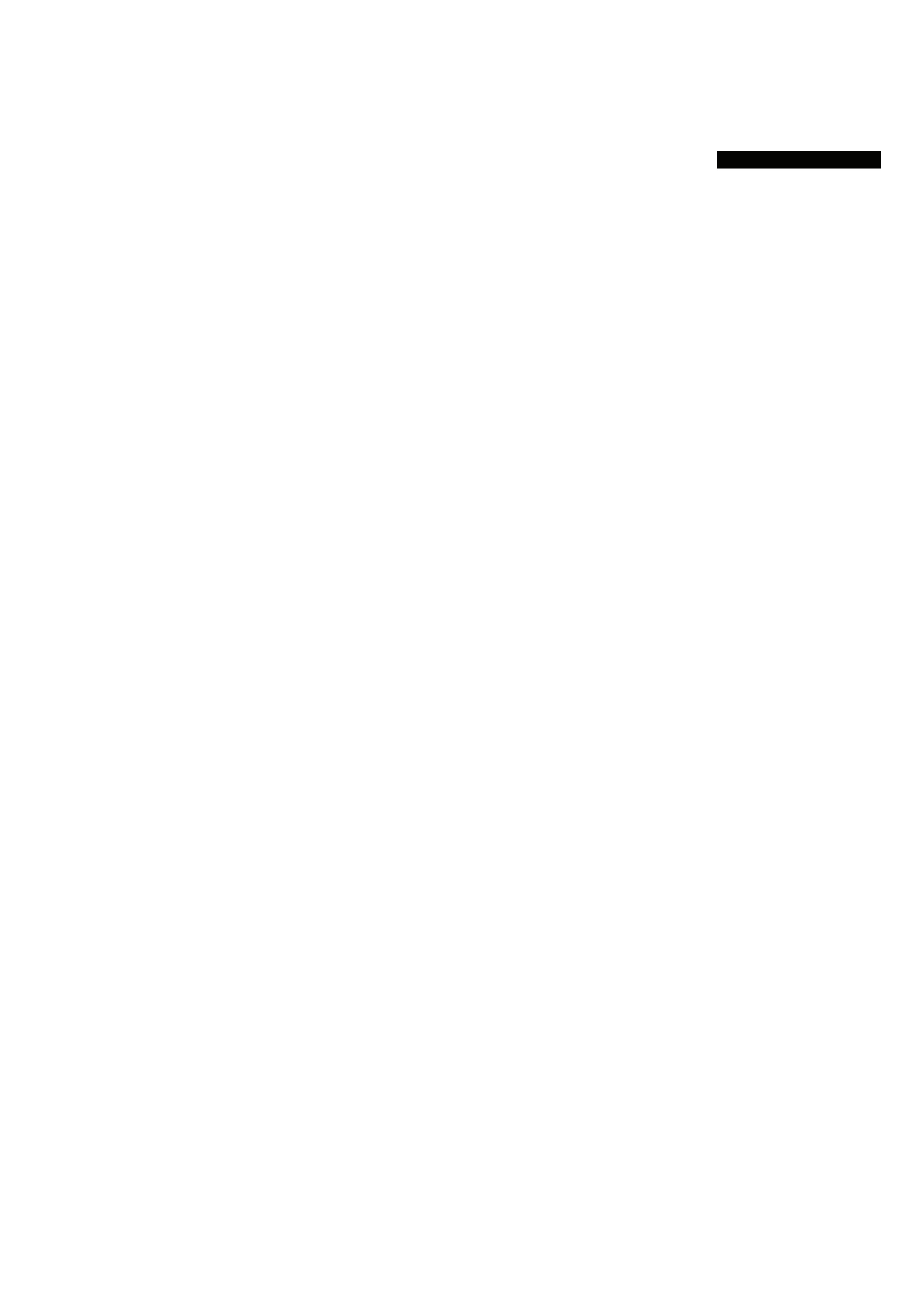
www.interplasinsights.com
head of content: dave gray
T: +44 (0) 1244 680 222
E: david.gray@rapidnews.com
Group portfolio sales manager: MANDY O’BRIEN
T: +44 (0) 01244 952 519
E: mandy.obrien@rapidnews.com
Advertising Manager: Gareth Jones
T: +44 (0) 1244 952 370
E: gareth.jones@rapidnews.com
Advertising Manager: Kelley Jo Gwatkin
T: +44 (0) 1244 952 375
E: KelleyJo.Gwatkin@rapidnews.com
Head of studio: SAM HAMLYN
T: +44 (0) 1244 680 222
E: sam.hamlyn@rapidnews.com
SUBSCRIPTIONS:
T: +44 (0) 1244 680 222
E: subscriptions@rapidnews.com
PUBLISHER: duncan wood
T: +44 (0) 1244 680 222
E: duncan.wood@rapidnews.com
Qualifying Criteria
UK – Free Europe – £249 ROW – £249 FREE digital issues available to view and download online
British Plastics & Rubber is published monthly (8 times/year) by Rapid Plastics Media Ltd, Carlton House, Sandpiper Way, Chester Business Park, CH4 9QE
T: +44 (0) 1244 680222
F: +44 (0) 1244 671074
© 2022 Rapid Plastics Media Ltd
While every attempt has been made to ensure that the information contained within this publication is accurate the publisher accepts no liability for information published in error, or for views expressed.
All rights for British Plastics & Rubber are reserved. Reproduction in whole or in part without prior written permission from the publisher is strictly prohibited.
ISSN 0307-6164
Incorporating Polymer Age and Rubber and Plastics Age.
There’s some comfort to be drawn from the volume and scale of the innovation we’re expecting to see at K Show this year. The energy crisis, the COVID hangover, supply chain disruption, inflation – and of course, the continuing atrocities in Ukraine – contribute to a sense of pessimism for the final quarter. And yet, suppliers are preparing for brighter times to come, with some major announcements due at K.
I’m particularly interested in the emergence of the chemical recycling partnerships that seem to be cropping up among the major materials suppliers. Driven by a demand for better quality post-consumer recyclate, this feels like one of those trends that could become genuinely disruptive. Then again, the energy required to execute chemical recycling is phenomenal. And given the fact that some countries and industries could be facing scheduled blackouts in the not-too-distant future, perhaps we’re still a way off.
Closer to home though, there’s still plenty to look forward to. The Plastics Industry Awards are nearly upon us, and what a perfect opportunity to get together with friends and colleagues after the frenzy of Dusseldorf. I had the pleasure of being asked to sit as a judge for the Unsung Hero category. I’ll keep my secrets, but I will say I was hugely impressed by the dedication shown by individuals in this space, particularly those who have risen to meet the unique challenges of our times.
“Thanks Dave, I’m glad you’re feeling so excited about going to K this year, but I simply don’t have the time – added to which, the hotels are charging criminal rates as usual” I hear you say. Fair enough – it’s not always an easy undertaking. And even if you do get there for a day or two, where do you start with something so vast? One option is to hang fire until September ’23. Interplas, historically, benefits from the UK launches of many of the major new products released at K, being less than a year after the show.
Speaking of, Interplas celebrates its 75th anniversary next year. Make sure you take a look at p.17, I’ve been through the BPF archives (thanks go out to the BPF for sharing with me their treasure trove of stuff), and have loved pouring over the minutes from 1945 onwards, when the first ever plastics exhibition in the UK was proposed as a mere agenda point. The rest, as they say, is history.
Finally, thanks go out to our regular contributors, Mike Boswell, who provides his resin pricing analysis, Philip Law, who gives his view from the BPF, and of course Richard Hird, former chairman of the PMMDA, who has handed the baton over to new chairman Dave Raine from this issue onwards.
CHASE PLASTICS, A UK MANUFACTURER OF RECYCLED POLYETHYLENE RAW MATERIALS (RPE), HAS ANNOUNCED SIGNIFICANT BUSINESS GROWTH. IN 2021 TURNOVER GREW BY 72%, AND THE COMPANY IS TARGETING SUSTAINED GROWTH IN 2022 BACKED BY SIGNIFICANT INVESTMENT.
TChe recycler, a recipient of £1m in UK Government funding under the Resource Action Fund, has increased plastic packaging recycling volumes with the installation of a new recycling line.
Chase Plastics’ success, underpinned by the demand for rPE generated by the Plastic Packaging Tax (PPT), has also been supported by the business improvement programme undertaken since acquisition in 2018.
In addition to increasing recycling capacity, the grant awarded by WRAP, which administers the fund on behalf of Defra, enables the further development of Chase Plastics’ Recothene rPE range.
Designed to incentivise manufacturers to use recycled content the PPT has fuelled the clamour for high quality recyclates that do not compromise the performance levels of plastic packaging.
Through the expansion of its Recothene range, Chase Plastics can better support customers redesigning high performance packaging to comply with the tax.
Claire Shrewsbury, Director WRAP, said: “The Resource Action Fund was developed to support resource efficiency initiatives such as this. Building a stronger recycling system is a core goal of the UK Plastics Pact led by WRAP. Our support of Chase Plastics’ recycling activities illustrates how business, NGOs and government can work together to divert waste from landfill or incineration and better manage resources.”
CEO David Harris said: “We are delighted with the progress being made by Chase Plastics, and view the future with confidence.
Increasingly, manufacturers are looking for rPE to meet their customers’ ESG requirements and respond to the Plastic Packaging Tax so demand for our high performance materials is strong.”
He continued: “Since acquiring the business in 2018 we have invested significantly in every aspect of the business which is now well positioned to provide the UK’s polyethylene film industry with the sustainable raw materials it needs.”
Now with 3 year warranty on parts and labour
Need to invest in Injection Moulding equipment, but concerned about the impact of the Pandemic?
be! You’ll be able
deduct 130% off your taxable profits when you
We have stock of machines between 100t – 650t from our EKS, FE and DK ranges which are backed up by our team of in house engineers and a 3 YEAR WARRANTY on ALL non-consumable parts that can be delivered within 5 days from order.
us to find out about our Part Exchange scheme.
The world has woken up to the urgent need to rethink how transit packaging is handled at the end of its life. The need to break the cycle of disposal via landfill or export is clear.
Such is the demand for the firm’s products, Chase Plastics is also making its K Show debut this year. The Circular Economy and Climate Protection are among the ‘hot topics’ being featured at K 2022 with plastic recycling and the processing of recyclates being key focus areas at the show.
“With the transition to a Circular Economy now underway, we see K 2022 as the ideal platform to demonstrate how Recothene rPE can help polythene film manufacturers contribute to the circular economy and reduce the carbon footprint of their products” Said Johnstone Smith, Managing Director at Chase Plastics in an earlier statement.
“The world has woken up to the urgent need to rethink how transit packaging is handled at the end of its life. The need to break the cycle of disposal via landfill or export is clear. Whether we use or manufacture transit packaging, we all have a part to play. Many businesses can support the transition to a circular economy through ensuring their used polythene is sent for recycling post-use whilst polythene film manufacturers can move from a linear model towards a circular model by reformulating their products to incorporate Recothene.”
Having invested significantly in personnel, processes and machinery over the last three years, Chase Plastics is now poised to expand its geographical reach. K 2022 will allow it to present its product range, recycling expertise and 50+ years of experience to a global marketplace. Chase Plastics will be located on Stand F06 in Hall 7.2.
BP&R caught up with David Harris, Chairman, Chase Plastics, to learn more about the group’s approach to recycling.
Can you tell us more about the new recycling line?
The new recycling line comes from Erema. We have been using Erema equipment for many decades and we value the continuity for our team being able to use familiar technology.
Tell us more about Recothene? What market needs does it meet?
The Recothene recycled polythene pellet range was designed to provide polythene
film producers with high quality recycled content that provides the highest levels of processability in the manufacture of transit packaging.
High quality recyclates, like Recothene, have fewer impurities and such purer recyclates run better throughout the manufacturing process and perform better within the finished product. Chase Plastics customers are achieving excellent results introducing Recothene into high performance packaging applications, at addition rates in excess of 30%.
Applications include collation shrink film for non-food primary packaging and secondary packaging in the food industry as well as heavy duty sacks for industrial packaging applications.
How long do you think it will be until the volume required for quality recycled resins are met in the UK?
We believe there are a number of challenges to meeting the demand for recycled content. The security of material supply is a key aspect of this and we must stop exporting material which should be recycled in the UK.
We have made a very significant investment in capacity to enable this material to be recycled in the UK.
MPS robotic tool changing systems from Stäubli unlock the maximum productivity in all automated manufacturing processes. The extensive MPS product range o ers optimum solutions for robots from all manufacturers and in all payload ranges. Benefit from Stäubli’s global experience and many years of expertise as a technology leader.
Highest process reliability through precise repeatability Full flexibility through high technological diversity
Optimum economic e ciency through minimised investment Outstanding productivity through full utilisation of the robot’s performance
MIKE BOSWELL LOOKS AT THE POSSIBLE IMPACT OF RESIN PRICE CHANGES - COULD THERE BE SOME POSITIVES?
Since Russia invaded Ukraine in February this year energy costs have skyrocketed, with a typical industrial user of electricity now paying 115% more than in January and without the recently announced UK Government price cap further increases would see the price exceed 250% of its original level. There has been understandable concern for the financial welfare of UK plastic processors where a combination of record high polymer prices and rapidly escalating energy costs which have been escalated by the falling value of the GBP against the USD are creating unprecedented input cost inflation which may be difficult to pass through the supply chain either in part or in full.
MHowever, the threat of a global economic slowdown, which is of itself largely a consequence of escalating global energy prices, is starting to apply downward pressure to polymer prices with PE, PP and PS already recording some significant reductions with other materials coming under increasing pressure as consumers divert from spending on durable goods towards increasing energy, food, and finance costs.
Whilst, of course, this type of correction is welcome it does not necessarily follow that a reduction in raw material cost will offset an increase in energy costs. However, with support from Doctor Robin Kent of Tangram Technology it has been possible to provide the following approximations of energy cost per tonne of polymer processed:
Who is ‘Polymerman’?
Mike Boswell is Managing Director of UK materials distributor, Plastribution, as well as the Chairman of the British Plastic Federation’s Polymer Compounders and Distributors Group and its ‘BREXIT Committee’.
‘Polymerman’ is the title used for announcements made via his Twitter account. This column is compiled using data from PIE (Plastics Information Europe) www.plastribution. co.uk | www.pieweb.com
Which can be calculated as the following in terms of incremental increase:
The threat of a global economic slowdown, which is of itself largely a consequence of escalating global energy prices, is starting to apply downward pressure to polymer prices with PE, PP and PS already recording some significant reductions
HOSTAFORM®,
Whilst the future price of polymers is yet to be determined, the historical analysis of the market does provide some grounds for optimism, based upon each material category hitting a low point in 2015 and a high point in 2022.
NB The costs are calculated at prevailing exchange rates, which will effectively deflate the 2015 values, the extent of the change is as follows: 2022 values are based upon the period from January to August.
The possible changes outlined above are in line with macro-economic expectations and along with support provided by the UK Government will to a greater or lesser extend will bring welcome relief to hard-pressed UK plastic converters, although it should be noted that polymer producers will also face the challenges of increased energy costs, and other inflationary pressures, within their own business activities and this will ultimately affect the extent of polymer price decreases.
AT ALBIS PROVIDE A NEED-TO-KNOW GUIDE TO THE LATEST LANGUAGE DOMINATING THE SUSTAINABLE PLASTICS SPACE.
MIt is fair to say that sustainability is one of the fastest moving and potentially complex topics our industry has faced in recent years. At the same time, it offers the opportunity to help address the great challenges of our time: the climate crisis and moving towards a circular economy, whilst remaining competitive. How then do we achieve the transition from fossilbased to more sustainable materials, when legislative and consumer demands keep adding to the pressure? A good start is by digging into some key buzzwords.
The market for sustainable plastics is undergoing upheaval. In years gone by, recycled plastic was considered an inexpensive, wide-specification product. Today, there are diverse waste streams, e.g. post-consumer electrical and electronic equipment or even household waste used to produce high quality recycled plastics, suitable for demanding applications. New products are also emerging where, for example used cooking oil or agricultural organic waste, are used as feedstocks to produce “bio-circular” polymers, and chemically recycled feedstocks are also beginning to deliver virgin quality plastics. Certification bodies such as ISCC and RedCert
operate audited systems which ensure the origin and quantity of sustainably-sourced feedstocks claimed by manufacturers are traceable and verifiable along the entire supply chain.
This relates to the natural carbon cycle i.e. the atmospheric CO2, captured during the growth of plants and trees, which is stored (or sequestered) in their leaves, stems and roots eventually returning back to the atmosphere through decomposition or burning. Over recent millennia, this natural carbon cycle has yielded a broadly steady state concentration of CO2. However, since the industrial revolution, this natural balance has been disturbed by the dramatic increase of CO2 being released into the atmosphere from the burning of fossil fuels. Essentially this is the source of the Climate Emergency; due to the increasing levels of greenhouse gases such as CO2 entering the atmosphere. The stored biogenic carbon used in bio-circular feedstocks to produce certain sustainable plastics delivers significant benefits in Life Cycle Assessments when compared to the use of fossil fuels. Companies such as LyondellBasell and Covestro are now offering portfolios with significant biogenic
carbon content. Specific examples include CirculenRenew® polyolefin products which have 100% renewable feedstock content and Makrolon® RE polycarbonate products with up to 72% bio-circular content.
The UK and EU are committed to becoming climate-neutral by 2050. Reducing greenhouse gas emissions (of all origins) should be our industry’s key priority according to Plastics Europe. One of the most beneficial aspects of sustainable plastics is their much lower GWP when compared with that of fossil-derived polymers. The measurement of “carbon dioxide equivalent” (in Kg of CO2eq / kg of polymer) is the relevant term here. In general, polyolefins compare favourably with many other bulk plastics. More durable, higher performance polymer types tend to be higher.
The re-use of waste plastics reduces the carbon-intensive manufacture of fossil-based plastics (of non-biogenic origin) which helps to significantly reduce the GWP and the carbon footprint of the polymer. Energy used to produce and compound polymers is also a major factor in GWP. Here, polymer producers and compounders are committed to increasing the use of renewable energy to further reduce the GWP of their products.
As already mentioned, typical chemical building blocks used in the production of plastics can now be produced from bio-circular resources. These renewably-sourced chemical building blocks are identical to their fossilbased equivalents and are co-fed into the polymerisation process. The resultant polymer is a mixture of fossil and renewable resources and is indistinguishable from its 100 % fossilbased counterpart.
This is similar to our electricity supply where it isn’t possible to determine whether the electricity supplied at a given moment in time is generated from renewable or fossil-based resources. However, our electricity suppliers record, document and attribute the energy mix of their electricity supply over a given period of time. This is the mass balance approach.
In the plastics world, producers strictly monitor and record the quantity of renewable resources used in the production of their polymers. This is documented and attributed to the polymer using Sustainability Declarations, supplied with the product. To avoid any potential claims of greenwashing, polymer producers must maintain a balance sheet, declaring what quantity of renewable resources they have used and what quantity of final product based on renewable resources they have sold. This mass balance approach is strictly controlled and audited by independent organisations such as ISCC and RedCert. ALBIS are the first UK “trader with storage” to be certified under the ISCC PLUS system. Brand owners and OEMs
are increasingly valuing the knowledge of feedstock sources to support their sustainability targets and convince consumers of the validity of their claims. A variety of products from COVESTRO, LyondellBasell, INEOS Styrolution, LANXESS and Tecnaro are ISCC PLUS certified.
The true environmental impact of a final product can only be assessed when the overall impact of the extraction, use and re-use of resources are holistically considered. The internationally recognised ISO 14040 and 14044 standards detail how the life cycle of a product is assessed. An LCA is a detailed process, but the main aspects which are considered are CO2 emissions generated during the extraction and conversion of raw materials, the total energy and water used, the use of land, the depletion of natural resources and the impact on fresh water. Due to their relatively low processing temperatures and lightweight transportation compared to other materials, plastics typically generate much lower CO2 emissions. Using recycled plastics or plastics based on biocircular resources further reduces their environmental impact, which is clearly visible in the LCA of these products.
Getting to grips with the terms explained above can really help converters and brand owners to move beyond discussions around mere recycled content. With a common understanding of the important terms, evidence-based choices can be reached. Engaging with a knowledgeable supplier helps drive this process and ensures that the best and most sustainable solution is selected for each application.
The standardised hot runner system from Meusburger has been expanded. Now the manifold type ‘H’ with four nozzles can also be selected and configured in the hot runner configurator.
Naturally balanced 4-drop system for optimal injection results
Individual selection of the gating position via parameters
Wide range of nozzle lengths and gate types
3D data immediately available
Completely-assembled and tested hot runner system
20th March, 1946
The group’s general manager reports that two directors from British newspaper The Daily Sketch are ‘anxious’ for there to be a UK plastics exhibition. The group agrees that this idea should be linked up with the BIF idea, which is still under discussion.
AS WE START TO SET THE STAGE FOR THE 75TH ANNIVERSARY EDITION OF INTERPLAS NEXT YEAR, I WAS LUCKY ENOUGH TO TAKE A LOOK THROUGH THE BRITISH PLASTICS FEDERATION’S ARCHIVES AT INTERPLAS IN YEARS GONE BY.
Talks of a showcase for the British plastics industry began at a BPF council meeting –just a couple of weeks after Japan surrendered, marking the official end of WW2.
The British Industries Fair was the subject of discussion. The purpose of the British Industries Fair, which began in 1915, had always been to encourage British manufacturers to help the country become more selfsufficient as global tensions escalated.
At the September BPF meeting, Charles Waghorne (later a chairman of the BPF) advised the group that the BIF was likely set to return in 1946, and that the organisers were encouraging participation from ‘any industries showing potential possibilities’…enter the plastics industry…
TAhanks go out to Stephen Hunt and Philip Law at the BPF for sharing this goldmine of memories with me. As well as the photos of the Federation’s memories of the show over the decades, I’ve also paraphrased some of the minutes from the planning meetings for the first ever UK plastics industry gathering – I hope you find this dive into history as fascinating as I did.
18th December, 1946
Plans are coming together. 21,000 square feet have been allocated for an inaugural plastics section at the 1947 BIF, at Earl’s Court in London. A panel of designers is appointed to plan the layout.
A change of plan… The committeevotes unanimously to postponethe plastics exhibition atthe BIF until 1948 ‘at theearliest’, as a result of‘the great dislocation of theindustry due to fuel cuts’.Sound familiar?
Getting back on track. May 1948 is agreed as the preferred timing for the plastics exhibition. Based on 1947’s BIF, some members felt it was important to note that the catering was not satisfactory!
Interplas is back in 2023, bringing with it the opportunity for you to experience the UK’s largest plastics industry exhibition showcasing the full spectrum of plastics processing machinery, materials, software, services and ancillaries in one place.
It’s also the only plastics event in the UK where visitors can see working machinery LIVE on the show floor and where they’ll come to compare, contrast and buy.
With an expected 12,000+ attendees across the three-day event, as well as new features and an expanded floorplan, now is the time to position yourself as a company that can offer solutions, showcase innovation and offer expertise to an audience known for its quality and purchasing power.
At this year's K-Show 2022 from 19 - 26 October 2022 in Düsseldorf, Swiss manufacturer Tool-Temp AG will present the first temperature control units of the new MATIC product line.
Temperature control has a great influence on product quality, productivity, energy efficiency and production costs. The product line MATIC with its control system IRIS has been specifically developed to provide users with optimum support in all these areas, claims Tool-Temp. The devices are characterised by their ease of operation and a predictive control system that adapts automatically to the circumstances, said the firm.
According to a statement from the group, “With the new IRIS controller, Tool-Temp offers a smart and intelligent solution for all types of process temperature control. The user can expect simple operation, at the same time a communication and interface solution that is geared towards the future.”
All data such as temperatures, pressures, flow rates, operating conditions, status messages, diagram and historical data are available to the user via the controller. IRIS continuously informs, reports and optimises the operation of the temperature control unit.
In addition to the touch screen operation, remote access is possible. Using a terminal device such as a phone, tablet or PC, users can access the web server integrated in the controller via a web browser. The connection is made via LAN cable or via the WLAN adapter integrated in the controller. The operation does not differ in any way from manual operation.
The model-based algorithms continuously summarise all available data and compare it with the current information. This constant adaptation enables the overall system to ensure optimal, uninterrupted and reliable temperature and flow control, as well as reliable monitoring of the process.
The MATIC unit line is divided into the following product groups:
- MATIC Duo
Water up to 90°C
Oil up to 150°C
- MATIC Water
Water up to 90°C
Pressurised water up to 160°C
- MATIC Oil Oil up to 360°C
The new MATIC temperature control units will be presented to the trade public for the first time at the stand H25 in Hall 11 at the K-Show 2022. The first models of the MATIC product range are scheduled to be available for ordering in the second half of 2023. The introduction of the new range will available to watch on www.tool-temp.net, or for live updates follow the Tool-Temp Ltd LinkedIn page.
RECYCLING PROCESS DEVELOPER SAPERATEC WILL DEBUT WHAT IT DESCRIBES AS A “FULLY CIRCULAR” FLEXIBLE PACKAGING PROTOTYPE BASED ON ITS MULTI-LAYER DELAMINATION TECHNIQUE AT K SHOW THIS YEAR.
RAt Hall 9, Stand D17, Saperatec will show a detergent package which, at 35% postconsumer recycled content (PCR), meets goals proposed for the pending EU Directive on Packaging & Packaging Waste.
The prototype was produced in collaboration with film supplier Wentus – which makes a monopolyethylene flexible packaging design that allows for easy recyclability – as well as adhesives group Henkel, which supplies the package’s recyclingoptimised adhesive.
Henkel made a significant investment in Saperatec in 2019, which has helped make a forthcoming plant for the technology a reality. Currently marketed by Wentus as Wentoplex Pure R, the marketing design recently received 18 of 20 points from Germanybased recycling alliance Interseroh.
The prototype is made using Saperatec’s extended mechanical recycling process for thin-layer composite materials, which results in virgin-similar recyclates. A two-layer design made entirely from polyethylene (PE), its inner sealing layer comprises
more than 50% PCR rLDPE from beverage carton waste. Its outer layer is printed with less than 50% surface coverage, and laminated with Henkel’s optimised adhesive for recyclability. Overall, the packaging will contain at least 35% PCR rLDPE – in line with the proposed recommendations for the EU Directive regarding non-food packaging.
Of the more than 140 million tons of plastics packaging waste produced globally each year, a significant portion comprises composite packaging, which consists of a combination of materials. Such packaging has posed sizable obstacles to recycling efforts, as separating composite packaging into its various origin materials has been technologically challenging and, even when successful, unsustainable due to the need for non-ecofriendly chemicals.
Saperatec says its approach results in recycled materials that can replace virgin raw materials in numerous applications, including film or foilbased packaging. Importantly, the process adds no contaminants to recycled polymers, and all chemicals used in the process comply with EU food contact regulations. Its technique is applicable for composite packaging comprised of various combinations of plastic, metal, and glass.
With the technology extensively tested in materials science labs and near-industrial pilot environments, Saperatec is currently building its first recycling plant for composite packaging in Dessau, Germany. In 2023, the facility will commence commercial operations with an initial goal of processing about 18,000 tons of packaging waste per year.
Saperatec’s composite packaging recycling brings the potential to separate and reintegrate a wide variety of substrates into the packaging stream. Initially, Saperatec will focus on composite flexible packaging materials and tube packaging with aluminum foil barriers, as well as plastics and aluminum from beverage cartons. Beyond that, Saperatec’s technology opens the door for future recyclability solutions in a wide range of composite packaging.
Of the more than 140 million tons of plastics packaging waste produced globally each year, a significant portion comprises composite packaging, which consists of a combination of materials.
The hot-wash separation fluids utilised are waterbased and solvent-free, and are reused more than 30 times in the process. Any and all materials employed during packaging recycling are listed for food contact materials without specific migration limit, per European regulations.
INJECTION MOULDER X2F HAS PARTNERED WITH MATERIALS PLAYER COVESTRO TO DEVELOP A THERMALLY CONDUCTIVE AUTOMOTIVE HEAT-SINK WITH IN-MOULD ELECTRONICS USING X2F’S CONTROLLED VISCOSITY MOULDING TECHNOLOGY.
Application samples will be displayed at Covestro’s stand (Hall 6, A75-1/A752), during K 2022.
The application presents an alternative to cast-aluminium heat-sinks for automotive OEMs and processors.
The new heat-sink moulded of Makrolon polycarbonate (PC) is approximately half as heavy as a comparable aluminium part.
It is part of an in-mould assembly that can be used to integrate LED modules directly into the headlamp housing – eliminating the need for brackets, screws,
thermal pastes, and adhesives. X2F technology has been demonstrated in high-volume series manufacturing for other applications.
Covestro’s Makrolon TC polycarbonate provides heat management and other suitable properties for in-mould electronics (IME).
“This new program involves using controlled viscosity moulding by X2F to attach the LED module directly onto the thermally conductive heat-sink without fundamentally changing the heat-sink adjuster module design. We are pleased with
the outcome so far of the X2F project where we have recently seen enhanced thermal management performance compared to traditional injection-moulded processes, and look forward to how the automotive industry will adopt the technology.,” said Paul Platte, senior marketing manager, Covestro LLC.
X2F’s process enables sensitive electronics to be insert moulded, thus providing functional integration, heat management, modularity, and miniaturisation.
“This innovative
technology enables the manufacture of previously impossible-to-mould thermoplastic parts that provide step-change improvements for our customers. In the case of heat-sinks, it dramatically streamlines production, reduces manufacturing times, eliminates fasteners and pastes, and increases product design flexibility,” said Reza Garaee, senior project manager for X2F. “This can be a game-changer for OEMs, and we’re thrilled to launch this new collaboration
This new program involves using controlled viscosity moulding by X2F to attach the LED module directly onto the thermally conductive heat-sink without fundamentally changing the heat-sink adjuster module design.
PLASTIC GRANULATION MACHINERY SPECIALIST HELLWEG MASCHINENBAU WILL BE PRESENTING EXTENDED OPTIONS AROUND THE SMART CONTROL SYSTEM FOR ITS ENTIRE GRANULATOR RANGE AT BOOTH C39 IN HALL 11 AT K 2022.
Also presented at the show will be a digital central lubrication unit with Bluetooth data transmission retrofittable to all central granulators together with a new edge trimming system for use in extrusion which is now servomotor-driven, so enabling optimum control.
Hellweg has added a hardware module to the Smart Control system that is capable of storing the power consumption of the machine it is fitted to over the long term, for example over a financial year, and providing it
for analysis. Together with the ability to display power peaks, it provides valuable data for optimising energy use.
The software itself now has the option of controlling granulator speed in increments of one, so giving the user even more flexibility in tailoring machine parameters exactly to requirements. The Secure+ package for the control system adds safety features. As soon as it detects imminent granulator overloads on the basis of motor current and torque values, it counteracts them so that rotor
blockages can virtually be avoided.
Hellweg says it can equip all central granulators from the 260 series upwards which are used for grinding sprues, sheets, moulded parts, sprue slugs and hollow items with a new central lubrication unit. Using a Bluetooth interface, the unit provides the operator with all relevant data, such as battery voltage, temperature, delivered lubricant volume as well as the time since the most recent pump stroke, operating time and number of pump strokes. The integrated, active reporting system enables the operator to detect irregularities at an early stage and nip them in the bud. Hellweg also offers the option of refilling empty cartridges as part of its exchange service.
The new R 200/20 Servo edge trimming system, a joint
Hellweg’s range of systems of this type, also known as guillotines or chippers. When trimming film webs, it pre-shreds one or two edge strips, which are then fed to a granulator for further processing. Its servo gear motor means that cutting cycle times can be freely specified. The operator can use the touch display to select the cutting frequency for the trimming and so specify the length of the chopped edge strips at a constant cutting speed.
That’s the view taken by Borealis, Oerlikon HRSflow and Engel, in a recent collaborative simulation, the results of which will be presented at K 2022.
Using a demanding mould, the three firms were able to show how injection moulding parameters can be optimised in the simulation and transferred directly to the machine as a proposed initial setting, provided that all relevant data of the injection moulding machine, the processed material as well as the hot runner system and other components are available.
The three firms say the end result was a highly effective and precise configuration –they will present the findings at K 2022.
The simulation was carried out on Moldflow, using a family mould with three cavities and a weight difference of 1:11 from the smallest to the largest component.
Engel provided a duo injection moulding machine, and supplied detailed technical
intelligence from the start. For example, the group shared details of the geometries of the nozzle used, as well as the sim link data interface for the direct connection of Moldflow to the CC300 control unit of the injection moulding machine.
Borealis provided comprehensive, precise data on the flow behaviour of the Daplen EE001AI polypropylene, and Oerlikon HRSflow contributed a servodriven 8-cavity hot runner system that allows the volume flow to be controlled, filling each cavity individually.
The three firms suggested that during mould configuration on projects with multiple stakeholders, the parties involved typically would not discuss possible causes of faults and remedial measures until after sampling has been completed.
By sharing as much data as possible up front, it was possible to optimise parameters like temperature control, injection characteristics and all other pressure and
time-related injection moulding parameters.
The parameters determined in several iteration steps were then transferred to the machine via sim link. The data exchange between simulation software and injection moulding machine can take place in both directions. It thus also enables the analysis of process data, which in turn provides potential for process optimisation. Access to sensitive design data is not necessary.
The first production run demonstrated the high precision of the settings achieved via Moldflow. The filling behaviour and the positioning of the weld lines matched the simulation 100%. The warpage behaviour of the largest part, the door trim measuring around 600 mm x 400 mm, was predicted to within ±2 mm, and the dimensions across the diagonal of over 650 mm were maintained with maximum deviations of only 0.04 %. After a few optimisation steps and without major manual readjustment, all three moulded parts met the quality requirements.
This joint project has not only shown that real production has run almost identically to the simulation, but the result also opens up potential for more sustainable production. For example, it is possible to see in the design phase whether a machine is suitable for the intended product or whether energy can be saved and production efficiency increased by using a smaller machine. In addition, the setting data suggestion developed in the simulation reduces the number of necessary setting cycles. This leads to fewer rejects and lower energy consumption during sampling.
Markus Kralicek, Business Development Manager at Borealis, Michael Fischer, Head of Business Development Automotive Technologies at Engel, and Stephan Berz, Vice President Sales at Oerlikon HRSflow and General Manager DACH, report on the project in a free webinar which is available to view here: https://www.hrsflow.com/ww/ en/events/borealis-engel-oerlikon-hrsflowwebinar.
In addition, all three will present the results during K 2022 at the Oerlikon HRSflow stand (Hall 1, Stand D10) on Thursday 20th October at 4.30 p.m. and on Tuesday 25th October at 4.00 p.m.
At this year’s K-Show 2022 from 19 - 26 October 2022 in Düsseldorf, the Swiss manufacturer Tool-Temp AG will present the first temperature control units of the new MATIC product line. Temperature control has a great influence on your product quality, productivity, energy efficiency and your production costs.
the new IRIS controller, Tool-Temp offers a smart and intelligent solution for all types of process temperature control. The user can expect simple operation,
the same time
interface solution
state-of-the-art communication
is geared towards the future.
Whether it is inhouse, postconsumer, bottle or chemical recycling: closing the loop in a precise and profitable way if machines are perfectly tuned for the respective application. Choose the number one technology from EREMA when doing so: over 6500 of our machines and systems produce around 14.5 million tonnes of high-quality pellets like this every year – in a highly efficient and energy-saving way.
The fruits of a new collaboration will be shown in hall 6 at stand A43 at this year’s K Show. Borealis and thin-wall packaging group ITC Packaging, have developed rigid packaging formats for food contact, which are based on chemically recycled feedstocks.
Borealis’ Borcycle C and Bornewables portfolios have now replaced pre-existing material for a variety of food packaging formats found on European supermarket shelves, primarily in the ice cream and ready-to-eat segments.
The grades use chemically recycled polypropylene (rPP) and renewable-based PP.
The innovation will likely be of interest to brand owners and converters at K who are looking to avoid various levies in place regarding the use of recycled plastics in packaging. Finding suitable solutions for foodcontact applications remains one of the major sticking points for many stakeholders.
Chemical recycling, though costly and still an emerging technology, may hold the key to many of these problems in the future. Grades in the Borcycle C portfolio are based on chemical recycling, while grades in the Bornewables portfolio are composed
of renewably-sourced feedstocks derived from residue and vegetable waste streams.
Both grades are produced using the mass balance method.
Borealis says that because they are “virgin-grade” resins offering “the same high purity and performance as polyolefins made using fossil fuel-based feedstocks”, they can be dropped in to existing processes without the need for grade revalidation.
“As packaging
pioneers, ITC has always been at the forefront of innovation. Our long-term strategic partnership with Borealis has enabled us to consolidate our position as sustainability trailblazers in the European rigid packaging industry,” said Jose Luis Olmedo, ITC Packaging Managing Director.
“Our ultimate aim is to maintain high food safety standards while implementing an added-value circular economy model that
meets market demands. This is what strengthens our relationships to both our customers and value chain partners.”
“Working together with ITC in the spirit of EverMinds has allowed us to identify and implement the ideal technologies and material solutions for making rigid PP packaging food-contact compliant yet more circular,” said Peter Voortmans, Borealis Global Commercial Director Consumer Products.
“Building on the success story with Bornewables and Borcycle C, Borealis and ITC are now exploring the use of mechanically recycled compounds from the Borcycle M portfolio to further reduce the carbon footprint of ITC’s nonfood packaging. This is how we advance value chain collaboration to close the loop on plastics circularity and at the same time underline how we manage to re-invent essentials for sustainable living.”
Chemical recycling, though costly and still an emerging technology, may hold the key to many of these problems in the future. Grades in the Borcycle C portfolio are based on chemical recycling, while grades in the Bornewables portfolio are composed of renewably-sourced feedstocks derived from residue and vegetable waste streams.
TTHE VECTOR EXTENSOMETER HAS BEEN HAILED AS A GAME-CHANGER IN ITS FIELD. WHAT CAPABILITIES DOES IT POSSESS TO HAVE EARNED THIS ACCOLADE?
THE VECTOR EXTENSOMETER HAS BEEN SENDING SHOCKWAVES THROUGH THE TESTING AND INSPECTION SECTOR. ROB COKER SPOKE WITH TINIUS OLSEN TECHNICAL MANAGER SHAWN BYRD AND IMETRUM COMMERCIAL MANAGER
MATTHEW PALFREY TO FIND OUT WHY.
SB: Because of its technology advancement, specifically the fact that it is stereoscopic and volumetric in its approach, distance to the target sample and out of plane movement issues are virtually eliminated. Because we believe not only is this a better non-contact extensometer, plainly stated, it’s just a better extensometer.
MP: It’s really a combination of factors. It offers all the benefits of advanced, non-contact extensometry, the versatility of multiple gauge lengths in a single unit, whilst being price comparable to a traditional clip-on sensor. We worked hard during the development of this to make what is simply a better extensometer, and with the help of those at TO we have succeeded. Once this goes on sale there won’t be any reason to buy a clip-on extensometer again.
SB: It has always been our approach to change how the society of testing can improve reliability and repeatability in day-to-day operations. with that in mind, the vector is positioned to be used by all the manufacturers of the testing frames, third party labs and captive labs will all see benefit from the use of Vector. More specifically, the fact that you can leave this measurement device in place through fracture will provide more repeatable and reproducible results. It will reduce human interaction and therefore human error.
MP: Really, anyone who uses extensometry of any kind will have an interest in Vector, from high throughput automation labs where zero touch systems are crucial, and R&D facilities where new materials are being examined for a myriad of different properties, to captive labs where a quick and reliable result is required.
SB: We definitely hope so. First indicators are that people are extremely excited for this product and, as we refine our approach over the next few years, I believe this to be a game-changer throughout the industry of material testing.
MP: This is just the beginning of our foray into Industry 4.0; we have a great deal more up our sleeve that really focuses on this and drives it even further. I wouldn’t call it saturation, however. There is a great deal more to change before we get even close to that point.
HOW SIMPLE IS IT FOR A MANUFACTURER TO PROCURE AND INSTALL THE VECTOR INTO THEIR OWN PLANT(S)?
SB: Simplicity was a major consideration because this is viewed as a plug-and-play system. We believe we have come up with a product that is easy to install with very little oversight needed.
MP: A big part of the project all the way through has been to offer something with universal appeal, removing as many barriers to sale as we possibly could along the way. As such, Vector offers a number of different hardware interface options designed to cope with a wide range of test machines and fixtures, as well as being able to connect via both analogue and digital methods to transfer data.
SB: The set-up is quick – less than five minutes –intuitive and easy to integrate into various systems and their software. Very easy.
We conducted a set-up exercise with various personnel within the company: some were engineers, some were office staff and some were from the shipping and receiving departments. They all found it rather easy to set up. In fact, I would say the non-engineers probably had a better time at it. They didn’t over think the room.
MP: When we started this project, our single most important goal was to make a commoditised product based on our previous generation systems, which were both incredibly powerful and very complex to use. By automating the key features and simplifying the product in order to tailor it for a single, specific application, Vector is incredibly simple and easy to use. Automatically switching between three simple modes: Scanning, Measuring and Validating, a clear status indicator light and a matching graphical interface provide immediate feedback.
SEEMS LIKE YOU’RE KEEN TO EXHIBIT THE VECTOR AT K 2022. WHICH INDUSTRY PROFESSIONALS ARE YOU HOPING WILL EXPRESS A SIMILAR INTEREST IN IT?
SB: That’s a good question. One of the benefits to going to a show is that you get questions from people wanting to utilise it in a way you’ve never thought of. With that in mind we know the target audience is uniaxial testing of various material. Both the static and dynamic platforms. This includes but is not limited to various engineers, R&D facilities, educational institutions and, of course, various types of testing labs.
MP: After spending the last three years developing this product, we’re understandably really excited about it. We had a great reception when we unveiled it at JEC and it has improved dramatically since then. I would like to think there should be something about Vector to appeal to anyone who works in the materials testing industry.
IS IT POSSIBLE THAT WE WILL SOON SEE A VECTOR 2.0? WHAT DO YOU FORESEE WILL BE THE CAPABILITIES OF THE NEXT ITERATION OF THIS BREAKTHROUGH?
SB: Absolutely, we are ever evolving the capabilities of the Vector platform and fully expect tier 2 to be released some time into the second or third quarter of 2023, with tier 3 to follow. Tier 2 will include both axial and transverse capabilities and tier 3 will include all of that and post processing for a true full spectrum DIC interaction.
MP: This is just the first of a family of products we are launching. The Vector T2 will go on sale in the first half of 2023, with an extended model, offering a much larger range of gauge lengths that will follow shortly afterwards. In terms of product succession, we are always looking to improve and optimise our products, and this is something that will continue into the future. The big improvements to the performance of Vector centre around AI and machine learning to try and implement further automation and the simplification or even total removal of the need to mark the specimen.
would like to think there should be something about Vector to appeal to anyone who works in the materials testing industry.
WEST LONDON BASED AQUAPURGE HEADS OUT TO THE K 2022 EXHIBITION THIS MONTH WITH NEARLY THIRTY YEARS OF PURGING COMPOUND EXPERIENCE UNDER ITS BELT. BP&R CAUGHT UP WITH THE TEAM TO FIND OUT ABOUT THEIR THREE DECADES OF SUCCESS.
Founding director John Steadman recalls that ‘in the first 20 years of our history we were busy with research developing over 160 purging compounds. With hindsight, such a painstaking R&D effort was necessary for us in order to finally settle on the key compounds capable of making a difference. In our book that meant eliminating process waste completely.’
Aquapurge directors, Steadman and Richard Brayne Nicholls realised that the company could continue being the test lab for the polymer sector in everything but name - or else it could fully develop and realise the full sales potential of its three purging compounds – Barrel Blitz Universal (BBU), Poly Clear Prime (PCP) products and PVC purge.
Aquapurge said its products strip out all carbon black deposits from plastics machinery, rendering the production equipment as new. “There’s really no point doing anything else,” said Steadman, “and the reason is simple – today’s pass/fail quality and production standards.”
“What sets us apart? I guess that it’s this total commitment to a complete and guaranteed purge for our customers. All our know-how leads us to that point: Not only is the physical nature of our leading two products different, one a hybrid purge the other a mechanical purge but we have the only products on the market that will remove carbon
Leading UK designer and injection moulder Agentdraw has won business, reduced costs and increased sales by using the BBU recipe.
When invited to pitch for a zero-defect contract involving the production of large expensive mouldings, Agentdraw MD Darren Parsons realised that a succession of previous contract moulders had been unable to match the quality standards required.
deposits effectively as opposed to help keeping them away.”
Any amount of residual carbon in a machine will mean that it is likely to fail the production changeover test– with very expensive
The contract involved producing a variety of large and expensive coloured parts and the cost of materials, additives and colourants alone represented well over 50% of the part price. Clearly any production waste at all would hurt the contractor considerably – making the job unviable.
However, says Parsons, ‘thanks to our complete confidence in BBU we were able to put aside our previous practices of
completely stripping down the machinery with every tool change. Instead, we relied on BBU to do its work.’
The process worked and Agentdraw was able to take on more work from the same client. Parsons said: ‘I sometimes compare BBU to the DAZ commercials of old. It really does wash ‘whiter than white’ - and all our machinery and systems at Agentdraw are much the better for it.’
consequences.
BBU is the Aquapurge’s proprietary scrubber concentrate and was selected as a finalist for best material in the pre-pandemic Plastics Industry Awards (2019). It is primarily designed for the total removal of carbon particles, purging fully degraded materials and plate-out from concentrated pigments or additives. BBU is a mechanical (non-chemical) purging compound and works most effectively from 160°C (320°F) to 340°C (644°F). It is easily cleaned out by any material – including clear ones – ensuring no milky mouldings and can also be used as a stripdown material. BBU thrives on problem materials or processes; high to low temperature changes, heat sensitive materials (PVC, POM, PBT, Flame retardant additives), metalizing ABS or PA, and it is also the world’s most effective transitional product to polycarbonate (PC).
Steadman says that “another of our purging compounds, Poly Clear Prime, has become by far the most impressive and easy-to-use Polyolefin Hybrid purging compound on the market today, with some cases only requiring 8% of what you would normally use to purge clean.”
Work with a recent client over a period of time involved the use of Poly Clear Prime when cleaning out a hot runner-based injection moulding system.
Aquapurge’s client was spending a huge amount of time when cleaning their Negri Bossi 250T from PP Blacks to PP White. This in turn was slowing down production and causing inefficiency and friction within the company.
On further inspection, Aquapurge noted that the time spent on the system purge clean sat at around eight hours each time - with 907kg of scrap produced at the end of process.
After the initial inspection, Aquapurge suggested the use of 10kg of Poly Clear Prime mixed with 10kg of PP.
After one single colour change, Aquapurge found that the time spent on the clean went from 8 hours per clean to 1.5 hours; the scrap went
down from 907kg to 23kg & there was a 100% maintenance cut, as the new process eliminated the need to involve human resources for manual cleaning.
Steadman said “When looking at the numbers we found that we saved 85% on time, 97% on material saved, 97% on reduction scraps and achieved 100% maintenance cuts.”
Steadman says that “After the first purge, the client was quickly made aware at how efficient our product range was; understanding that not only were they able to get time back, but they were able to reduce their waste dramatically.”
Twelve months later, and a sustained practice of Poly Clear Prime use has now delivered some more compelling figures.
12-month results with Poly Clear Prime: 78+ hours gained back. 11 tons of materials saved. 211000 scraps cut on start-up. 0 cleaning maintenance.
Richard Brayne-Nicholls preventative maintenance such as this is very rare within plastics processing. It often takes a near disaster – and a midnight run from Aquapurge – to remedy and mend what should have been better managed in the course of routine operations.
Richard said “The primary manufacturing mindset to be challenged is the one that sees or hears no evil and undertakes no pre-emptive maintenance. Our biggest issue is not competitor products but the plastics processor that believes in doing nothing at all….until it’s too late. Mistakes, breakdowns and interrupted production are many times more expensive to fix after the fact but, sadly, such situations frequently occur.
Richard added “The best way to use Aquapurge – and our purging compounds – is to engage with us before getting in expensive trouble. A regular programme of purging makes complete sense in every way – technical and financial.”
With customers embracing the Polymer, Purge and Project attitude. Dyna-Purge and Stoner Moulding Solutions offer a combined protection and production efficiency
Dyna-Purge is a commercial purging compound that is being used across all plastic manufacturing processes. If a company has a process with a hot melt screw and barrel, there is a grade of DynaPurge suitable for the application.
POLYMER DISTRIBUTOR CJP SALES SAYS IT IS SEEING A WIDESPREAD GROWTH IN THE USE OF COMMERCIAL PURGING COMPOUNDS (CPC), WHICH HAS BEEN DRIVEN BY A NECESSITY FOR EFFICIENCY AND COUNTERING THE EXPONENTIAL RISE IN MANUFACTURING AND RAW MATERIAL COSTS. HERE, THE FIRM EXPLAINS THE BASICS OF PURGING.
CPCs have been used for many years, by many industries as a solution to slow costly colour and material changes, transition for high to low temperature polymers, elimination of carbon build up in start up and shut down process and the longterm protection of machinery and costly injection moulding tools.
Lubricants are added to polymers to aid the flow and homogenisation. This process coats the screw and barrel with a layer of melted plastic. This allows plastic to flow over plastic, which often, after long term use, leaves a lubricant layer. This lubricant layer becomes the foundation for stubborn contamination and hang ups.
Dyna-Purge and other reputable CPCs have been specifically designed, after many years of development, to remove unwanted polymer and lubricants which cause carbon. Unlike highly lubricated polymers, they are designed not to coat the screw and barrel during the purging process, but to scrub away anything left in the barrel after the polymer is removed.
Often, processors use polymers to purge machines which isn’t always cost effective when calculating the amount needed and the effectiveness of this process. General Polymers are not designed to clean machines and the price per tonne shouldn’t be a reason to consider using them for this purpose.
Polymer is cheaper than a CPC, but they are designed to have a different function. The first question, is there an issue in your business with wasted time and polymer due to high scrap rates and lost production time? There are many ways that this issue can affect a company’s productivity and are symptomatic in some unseen waste issues.
It makes good business sense to diagnose these problems to prevent unnecessary energy and running scrap costs, paying staff to take the scrap and re grind it, using energy to regrind only to provide an in house reprocessed polymer.
Many companies have chosen to reduce waste and increase productivity by adopting a purging protocol that includes finding the right CPC, training staff on the benefits of purging and the behaviours of polymers on processing machinery. Establishing the best start up and shut down procedure for their manufacturing process.
One of the advantages of using Dyna-Purge as a choice of CPC is its ease of use. There is no mixing or blending required. Very few setting changes are needed, and it is also harmless to the equipment, which includes a gentle mechanical action that removes unwanted contamination or polymer without putting machinery at risk. CJP Sales also offer free onsite training to help customers find the right purging procedure.
See our illustration based on real trials using an 80te moulding machine. Customer X was experiencing black specs on start-up, which were caused by the shutdown procedure. The
figures are relative to machine size – the bigger the machine, the bigger the saving:
It makes good business sense to diagnose these problems to prevent unnecessary energy and running scrap costs, paying staff to take the scrap and re grind it, using energy to regrint only to provide an in house reprocessed polymer.
In addition to the purging compounds, CJP have introduced Stoner Moulding Solutions’ range of sprays including, mould release agents, to optimise production times, mould cleaners, which are essential protection, and rust preventatives for daily use with PVC tools or long-term use for storage of tools and dies. Plastic processors that are spending large amounts of money on state-of-theart machinery, hi-tech injection moulding tools and extrusion dies, need to take preventative action to protect and reduce costly preparation for resetting tools after storage.
ON STAND F23 IN HALL 12 AT K THIS YEAR, THE WITTMANN GROUP WILL SHOWCASE ITS CAPABILITIES IN AUTOMATION AND ROBOTICS – AND, TRUE TO PAST FORM, THE FIRM HAS FOUND EVER NEW CREATIVE WAYS TO DO THE JOB.
The Wittmann robots of the W818 / W918 series have been in use on injection moulding machines with clamping forces ranging from 80 to 200 t for a number of decades. More than 18,000 units of this type with various control systems have been manufactured so far.
Now, the group will use K to introduce the WX128, which benefits from the technology of the larger WX138 model already available on the market. It features newly developed compact control cabinet on the horizontal Z axis. To create this part, the rear structure has been shortened by 30%. This is useful for small injection moulding machines, as it makes for a compact protective housing, achieved by positioning the drive unit and connection cables on the inside.
The Wittmann WX128 relies on a belt drive concept on all linear main axes. Wittmann says the result is a high level of dynamism The vertical axis can accelerate at roughly four times the gravitational acceleration rate. The predecessor model of the WX128 was equipped with an external rack on the demoulding X axis.
Some main objectives of the development work were to create an easily accessible, lowmaintenance design and to meet the demand for flexible upgradeability. As a result, it has become possible to equip the WX128 with up to two additional rotational servo axes. This extension can be implemented either at once or as a retrofit later on without having to make any alterations to the control cabinet, which could involve having to modify the protective housing as well. At K 2022, Wittmann is presenting the WX128 robot with an A-C servo axis equipped with an illuminated gripper.
The new WX128 with a nominal load capacity of 6 kg, and offered exclusively with the current Wittmann R9 control system, will be available from the end of 2022. Based on the appliance exhibited at the K 2022, some further models will be added to the Wittmann range from 2023 onwards.
One of the new robot applications Wittmann will present at the K 2022 is the Wittmann palletising cell. This application handles automatic loading and unloading of transport systems.
In this application, stacks of trays [1 tray = 360 × 270 × 75 mm] will be transported by a horizontal servo axis from a buffer behind the palletising cell to the workspace of the top entry robot. A newly developed W938T robot with an upstream demoulding axis and a B servo rotation axis (rotating around the vertical axis) will take over the
trays. Before these are stacked on a Euro pallet [1,200 × 800 mm] or in a DB mesh box [1,240 × 835 × 970 mm] their orientation will be checked by visual inspection.
Then they are positioned on the transport container according to the instructions issued by the depositing program. This cell will also be used to demonstrate how two materials handling systems supplied by ErgoTek can move the full pallet or mesh box into and out of the protective housing. The outlets of the protective housing will be secured by light grids and muting.
All components supplied by ErgoTek are controlled exclusively via the robot’s Wittmann R9 control system. The concept shown can be used at the end of production lines with several injection moulding machines or as a stand-alone solution in warehouse logistics. The W938T robot shown in this configuration has a maximum load capacity of 15 kg. The interface connection to the materials
Wittmann automation at work at Linear Plastics, South Wales. Automation issues are key to Wittmann‘s success in the UK and Ireland.
handling system can be either – quite traditionally – a company employee with a pallet truck, or a semi or fully automatic solution (FTS). Depending on the requirements in each case, the Wittmann R9 control system can be equipped with the necessary interfaces.
Known for its creative displays of automation, Wittmann will illustrate the wide range of its robot series’ different functionalities, while also demonstrating the high performance of its latest R9 robot control system. One of these applications is the Sonic 143 robot, which is inviting visitors to a game of chess. While the chess world is rocked by accusations of cheating, Wittmann believes nothing will get past its robot.
This application makes use of the Sonic 143’s functionalities as a high-speed robot. Sonic robots are suited to short injection moulding cycles with mould-open times of one second and below. These robot models are designed for extra high electrical and mechanical acceleration and deceleration rates – and high volumes of axis movements per minute. All of these possibilities are used in the application shown, by reaching the shortest conceivable moving and manipulating times in handling the chess pieces.
are
While the chess world is rocked by accusations of cheating, Wittmann believes nothing will get past its robot at K
automation & robotics
The e-mobility trend is gaining momentum, particularly in view of issues such as resource preservation and climate protection. With our innovative materials, we are already contributing to the ongoing process of making motor vehicles more lightweight and therefore eco-friendly. Our high-tech Durethan® and Pocan® thermoplastics and Tepex® polyamide composite sheets open up new possibilities in structural engineering and design. With our flame-retardant product grades, we offer custom solutions speci fically for plugs, connectors, mounting elements and housings in electronic components. In this way, quality from LANXESS is helping to shape future mobility. new-mobility.lanxess.com
The chess board will be positioned vertically below the horizontal axis of the Sonic 143, to offer the human opponent and other onlookers the clearest possible view on the board and the development of the game. The robot is equipped with a combined A/C servo axis and an L-shaped gripper fitted with two individual magnetic gripping systems to handle the chess pieces. The second one of these two grippers comes into play whenever a chess piece is to be captured.
The chess pieces themselves were produced on a 3D printer and have a metal core, so that they can be moved by the metal grippers. The robot, the gripping systems and the chess software are all controlled by the latest Wittmann R9 robot control system. Thanks to its open program interface, this system allows the integration of an opensource chess software.
The Sonic 143 has the option of playing either against itself or against a challenger from among the trade fair visitors. At the Wittmann booth, all visitors will be offered the opportunity to compete against the Sonic 143 in a fast chess game with a three minute playing time, where they can enter their moves via a virtual chess board shown on the display of the Wittmann R9 TeachBox.
At the Wittmann booth, all visitors will be offered the opportunity to compete against the Sonic 143 in a fast chess game with a three minute playing time.
Ruplas Group Limited is Opulentia Capital’s new vehicle which has been established to acquire companies in the industry to build a group with cumulative sales in excess of 100m GBP. They are looking to acquire convertors that have at least 10 years’ experience and revenues between £4m and £30m.
Recycled plastics will form a large part of the group as Opulentia sees that this segment will have a significant growth in the near future; growth that maybe slowed through the pandemics but all the lost ground will surely be recovered as the march towards more sustainable consumption will continue with renewed vigour.
Plastic and rubber is a segment with annual revenues of £27bn and it employs 162k people in the UK. Despite being such a large segment, it is very much a fragmented segment comprising of 5,800 companies. Where there is fragmentation, Opulentia claims to be “a specialist of consolidation” with similar experience in both the leisure and
food space. Bruce Margetts has recently joined the Board of Directors for Ruplas Group Limited. Margetts is currently Managing Director of Bericap UK, a large plastics converter, with 26 production units around the world, providing caps and closures solutions to the largest players in multiple end markets. Previously, Bruce was President of The British Plastics Federation and also spent 18 years with the RPC Group a global design and engineering company specialising in polymer conversion. Bruce Margetts said “I look forward to offering my knowledge and experience to help build the group and grow the companies acquired.”
Bogdan Georgescu, Director of Ruplas Group Limited said “Our goal is to build a 100m revenue group in this space. Acquire and invest in Plastics, Rubbers and other related businesses. The model is to be involved with long established and well run companies, for which they can benefit from being part of a larger group and take business to the next level.”
The UK’s first free recycling programme for any brand of food storage containers and reusable plastic water bottles has launched, allowing households to recycle these hard-torecycle items.
Anyone can sign-up to the programme and be awarded points for each item they send in to be recycled. These points are redeemable as monetary donations to fund good causes including charities, community initiatives and schools.
The recycling programme has been set up by TerraCycle in collaboration with Sistema - manufacturer of food storage containers and reusable bottles. It has been designed to give wellused food storage containers and reusable plastic water bottles a second life after use.
These items are considered “hard-torecycle” due to the high quality food grade BPA free materials they are made of. Whilst some councils collect and
recycle some food storage containers, there are a number that don’t collect or recycle any. This means they are often destined for landfill or incineration.
As well as collecting these items from home, there’s an option to create a public dropoff location where the wider community can drop the items at one central point to be sent in together for larger volumes to be recycled. This allows programme members to become recycling champions for their communities, collecting more and raising more money for their chosen good cause.
Anyone can sign-up on the programme page on TerraCycle’s website to start collecting. It’s free to send the items to TerraCycle where they will be recycled into raw materials.
TerraCycle recycles these items by shredding, washing and sorting the materials by type. The material is then dried, compounded
and pelletized into hard-granulated plastic granules. These granules can then be incorporated into the production of different plastic products.
Julien Tremblin, General Manager for TerraCycle Europe said:
“This is a first-of-its-kind recycling programme for the UK so we’d urge everyone to get involved and start collecting as much as possible, either from home or from the community.
“It couldn’t be easier to collect and send us these items, and it’s a great way to help your home or community go greener.”
company has targeted 30 per cent circular plastic use across its fastmoving consumer goods packaging by 2030.
Berry Global’s Cambridgeshire-based recycling operation Plasgran is to be renamed as Berry Circular Polymers, alongside the company’s soon-to-beopened new recycling facility in Leamington Spa, Warwickshire.Berry Global
The new name is designed to reflect Berry’s leadership in recycling and the development and securing of circular polymers. This will support the move towards a circular and net zero economy, according to Berry, for which the
Established in 1999, Plasgran is one of the UK’s leading recyclers of rigid plastics. The company’s advanced technical facilities provide compounds and regrinds for customers across the UK and Europe, creating custom formulations, such as colour matching or improved impact strength, to meet specific requirements.
The Leamington Spa facility, which is due to open later this year, will utilise Berry’s CleanStream technology, the world’s first closed-loop system to mechanically process domestically recovered household waste polypropylene back into food-grade packaging. CleanStream has recently been granted a Letter of No Objection (LNO)
from the US Food & Drug Administration (FDA). This confirms that the post-consumer recycled (PCR) PP produced by the process can be used in levels up to 100 per cent recycled content for food contact applications.
MD Jeremy Blake said: “The launch of Berry Circular Polymers brings together our advanced rigid plastics recycling facilities. Our technical expertise and experience will enable us to deliver recycled material of high quality and consistency to support our customers’ drive for sustainable solutions.”
Together with its UK and European film recycling facilities in Dumfries, Heanor, Rhymney (UK) and Steinfeld (Germany), Berry counts itself among the largest plastics recyclers in Europe, with the ability to handle up to 200,000 tonnes of material annually.
IMAGE: The Berry Circular Polymers Leadership Team (from left): Matt Ayres, Plant Manager, Wimblington; Rosie Barber, Commercial Director; Stephen Allan, Finance Director; Toni Brook, Quality, Compliance, Environment and Safety Director; Jeremy Blake, Managing Director.
The group is introducing a variety of new products at K, including:
AS WE THANK RICHARD HIRD FOR HIS REGULAR COLUMN, WE WELCOME INCOMING PMMDA CHAIRMAN DAVID RAINEROBOSHOT SALES MANAGER AT FANUC, WHO OPENS HIS TENURE WITH A SOMBRE COLUMN FOLLOWING SAD NEWS FOR THE UK INDUSTRY.
preparations for, I guess, everyone, the formalities have yet to be done but I’m more than ready (I think)...!
My intention had been to use my first article to remind everyone what we do as an Association, and why it’s of such value being a member. However, that thought was quickly and sadly overtaken on hearing the very sad news that Simon Wrighton of Arburg UK had sadly passed away this week – for a full obituary, turn to the back of this issue.
First K for former Croda additives under Cargill ownership
For the fi rst time, the former Croda polymer additives business will exhibit at K Show as Cargill. Since the acquisition, Cargill is the new home for well-known polymer additives brands such as Crodamide, Incroslip, Atmer and Ionphase.
• New plasticizers in the range such as Cargill’s Biovero high performance bio-based phthalatefree plasticizers that o er permanence, e ciency, fast-fusing and thermal stability.
• Slip, anti-scratch, and processing aid data to improve the performance of biopolymers.
• New findings on how Incroslip C can improve HDPE recyclate by providing enhanced flow with improved MFR, whiter recyclate and no impact on mechanical properties.
The firm will also display a range of established products including:
• Crodamide slip and anti-block agents
• Incroslip high stability & performance additives for slip
• Atmer & Ionphase migrating and permanent static control additives
Cargill will be in Hall 7A, stand D05.
Here we have my first column as PMMDA Chairman, although technically I’m not actually Chairman until we hold our AGM at the beginning of November. We’ve had to delay this year due to K
Although Simon worked for a competitor in the same field as me, I always found him to be both friendly and excellent company socially, and he was both engaging and professional in his approach to his work, his colleagues, and most importantly, to those he did not need to be – Simon was the consummate professional, and I have to admit that K will be a different place without him this year.
In closing, I would like to take this opportunity to extend my condolences to Simon’s family and friends (of whom he had many) – he will be sadly missed.
Simon was the consummate professional, and I have to admit that k will be a different place without him
TPhis month has been tinged with sadness. Peter Davis OBE, my predecessor as BPF’s Director General, passed away on September 11th.I worked very closely with Peter for 18 years, from 1996 to 2014 and as well as a colleague he became a great friend. His passing had caused me to reflect on the debt the industry owes to its great figures Several have been lost in recent years. Springing to mind are Ron Jones (ICI and BPF), Dick Finnis (ICI and EVC), Jim Pugh (PAFA), David Williams (LinPac), George Copeland ( Blowmocan) and now Peter Davis (BPF). Over the years they provided the building blocks for the creation of the great edifice which we have today in the form of the UK plastics industry. The fact that we have this highly resilient structure capable of absorbing stresses and strains imposed from all directions owes to them and people like them at every level in the industry.
This month I would like to say a few words about Peter and his contribution. It follows closely the eulogy I gave at his funeral at the Danish Church in London.
Peter was born in 1949 of an English father and Danish mother. He married Anne, a Danish lady in 1985. His Danish heritage meant a great deal to him and he was able to use this to great effect in the BPF when, as Goodwill Ambassador for the city of Copenhagen, he organised a visit made by UK government officials to Denmark to study the potential for using energy from waste as a means of dealing with hard to recycle waste fractions in the UK. Issues have moved on since then and we now have a stronger focus on circularity but then it showed how and why energy from waste had been made acceptable in Denmark.
I was reminded when I recently passed through Heathrow last week how well known Peter was around the whole world of plastics and how he was on very good terms with its business leaders including, Mr Lau in China, Armin Mehta in India and the late Bill Carteaux in the USA.
He was a highly effective door opener for the industry, not just to export markets but to government, customer industries and to organisations like the Tidy Britain Group. The reason for this was that he was a very welcoming person who found something in common with everyone he encountered. His background
was very broad. His business career took in Metal Box and he was Director of INCPEN, the Industry Committee for Packaging and the Environment .He had also been a Director of The Royal Institute of British Architects He’d also spent a formative period in government, local and national, as a councillor in Lambeth and later as a Special Advisor to Lord Kenneth Baker a Cabinet Minister at the time, political service for which he was awarded an OBE.
Packaging was Peter’s speciality and he was proud of his role in brokering the famous percentage division of responsibilities along the supply chain while the Packaging Regulations were being drafted.
In my book one of the key attributes of a top-class operator is that they don’t always put themselves first. Peter had this quality in spades. It helped secure a very high level of co-operation His approach to the role of BPF Director General was that he was ‘primus inter pares’, the ‘first among equals’. Peter’s selflessness was evident throughout his whole career at the BPF. Although he was extremely busy he always made time for everyone, whether that person was a government minister or a member of our catering team.
He was also very far-sighted. He could see that plastics ending up in the seas would emerge as a major issue and as far back as 2008 was pressing our BPF’s Council to adopt Operation Clean Sweep to mitigate the loss of raw materials to the environment. He also saw the emerging importance of the Chinese market and at an early stage organised a visit of Chinese industrialists to the Interplas fair. This helped consolidate our own presence at the corresponding Chinaplas exhibition. He was quick to jump onto the Energy issue and warned of ‘brown outs’ when gas reserves were running close to the wind, advocating an expansion of gas storage facilities, a very prescient reading of the current situation.
Many in the plastics industry will not know that Peter had a keen interest in military history. He was a real expert on the Napoleonic wars. Indeed only within the last year he entered into a learned correspondence with Professor Jeremy Black of Exeter University on the very subject.
As one BPF member wrote ‘Peter was a truly lovely man and as perfect a gentleman as you could ever wish to meet’.
I was reminded when I recently passed through Heathrow last week how well known Peter was around the whole world of plastics and how he was on very good terms with its business leaders including, Mr Lau in China, Armin Mehta in India and the late Bill Carteaux in the USA.
InControl Ultrasonics Ltd
(FFR Ultrasonics Ltd)
PO Box 10380, Sileby, LE12 7ZX
T: 01509 621992
E: enquiries@ffr-ultrasonics. co.uk
W: www.ffr-ultrasonics.co.uk
W: www.incontrolultrasonics.co.uk
Telsonic UK Ltd
Unit 3 Vitrage Technical Park
27 Witney Road , Nuffield Industrial Estate, Poole, Dorset
BH17 0GL
T: 01202 697340
E: info.uk@telsonic.com
W: www.telsonic.com
Blog: telsoniccuk.wordpress.com
QUALITY MONITORING CONTROL
Kistler Instruments Ltd
T: 01256 741550
F: 01256 741551
E: sales.uk@kistler.com
W: www.kistler.com
Pressure transducers and associated monitoring/ control equipment for new and existing injection moulding applications.
PRINTERS OF PLASTIC MOULDINGS
Total Print Ltd
Specialist Pad Printers
Station Road, Gedney Hill, Lincolnshire PE12 0NP
T: 01406 330122
F: 01406 330123
E: info@totalprintltd.com
W: www.totalprintltd.com
Sub-Contract Pad Printers to the Plastics Industry
Looking To Outsource Your Branding? – We Can Help.
Specialist Sub-contract Pad, Screen, Digital and Laser Engraving Services.
Premier Impressions Ltd
Units 10-11, E.Plan Estate, New Road, Newhaven, East Sussex, BN9 0EX
T: 01273 512512
E: sales@premierimpressions.co.uk
W: www.premierimpressions.co.uk
TAMPO.SCREEN.FOIL
Contour Marking Co Ltd
Albert house, Gledrid Industrial Park, Chirk ,Wrexham, LL14 5DG
T: 01691 770093
F: 01691 770023
Sub Contract Tampo, Screen & Foil Printing to the plastic moulding industry
E: sales@contourmarking.com
W: www.contourmarking.com
On behalf of ARBURG LTD, British Plastics & Rubber is deeply saddened to announce the death of Simon Wrighton, Sales Director. Simon died from lung cancer at the age of 59.
Simon started his working career in the plastics industry in 1981 selling used blow moulding, extrusion, vacuum forming and injection moulding machinery before joining ARBURG in December 1997.
He worked for ARBURG for over twenty five years, joining in as Salesman for the Western area, progressing to Sales Manager and then in 2011 being appointed Sales Director at ARBURG Ltd looking after machine sales activities throughout the UK and Ireland.
Through his long career with ARBURG, Simon earned huge respect amongst colleagues, customers, suppliers and competitors alike. He was well known and trusted for his depth of knowledge on ARBURG technologies and applications.
He leaves Lesley, his wife of 38 years and two grown up sons, Rich and Will. He will be sorely missed.
Charity donations can be made in Simon’s name to Cancer Research UK. If you wish to contribute, please visit:
helps you gain the purest recyclates in a „like new“ quality that seemed unimaginable a few years ago. We imple ment your formulations in a way that costs little in terms of money, energy and CO2 emissions. Our groundbreaking technology in compounding and recycling gives you the critical edge in the competition for sustainability – for your company‘s figures and our children‘s future.