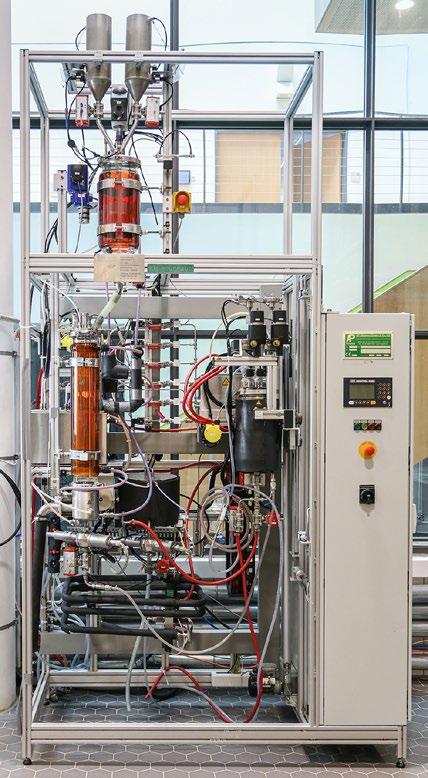
7 minute read
Assessment of brewing cereals and beverage recipes on a small-scale basis
VLB SERVICE
Dipl.-Braumeister Michel Werner, B.Sc. Florian Mischke, Dr. Ing. Roland Pahl, VLB Berlin, Research Institute for Beer and Beverage Production
The "nano brewery" has been situated in the Wilfried Rinke Technical Center at VLB Berlin since 2017. Roland Pahl and Werner Michel introduced the plant at the October Convention 2017 as one of the smallest fully automated brewing plants, which was acquired in 2014/2015 as part of a publicly funded research project. VLB now also offers a service related to the "nano brewery". Customers can have raw materials assessed on a 5-liter scale.
The processing properties of the brewery raw materials are subject to certain fluctuations. Influencing factors such as annual crop, provenance as well as growth and
Photos: ew
production conditions are relevant for almost all parameters in malting and brewing. The compositions of all brewery raw materials can be analyzed to a large extent. However, processing difficulties and undesired influences on wort and beer quality can usually only be demonstrated to an insufficient extent. For example, difficulties can occur during lautering, beer filtration, or gushing may arise, even though the analysis results were inconclusive. Although it is possible to judge the general processability of a raw material, it is not possible to predict process difficulties or adapt the process on the basis of the corresponding raw material.
Small quantities
An investigation on a very small scale can provide insight on important information such as the behaviour of of raw materials on an industrial scale if sample material is supplied in advance for analysis. In such a case, the economic expenditure is much lower. Processing on a very small scale is therefore the optimal tool for evaluating new raw materials, raw material mixtures, processes and recipes. Test equipmenthasa decisiveinfluence. It must be able to reproduce processing on an industrial scale in a reproducible and reliable manner. In light of the enormous potential of such plants, VLB Berlin has been dealing with the issue of down-scaling in the malting and brewing process for a long time. Consequently,

the institute has the know-how and plants designed for 4 l unfiltered beer. The entire process of malt and beer production from grain to bottle can be examined. Individual components, such as the micro malting plant (600–700 g malt)and the modified EBCfermentation test tubes (fermentation of 4 l wort) have been established for long time and are widely accepted in the brewing and malting industry [1]. With the development of the miniature brewhouse [2], the gap between malting and fermentation could be closed in 2017 [3]. Once all process steps required for beer production have been miniaturized, small quantities of malt, wort, and beer can be produced much more easily, flexibly, and economically.
High reproducibility
At VLB Berlin, a practical method was developed with which the raw material-related lautering behav- iour of malt can be assessed on a 5-l scale with only 720 g of malt. As the fermentation of the produced wort is possible, both the wort and beer can be evaluated analytically. At the very beginning of the method, the malt is ground by a convention- al 2-roller mill and mashed in within 6 minutes at 62 °C. The pH value of the mash is measured and adjusted to 5.5 if necessary. Then the mash is resting for 45 minutes at 62 °C and for 30 minutes at 72 °C before being mashed off at 76 °C. After the mash has been transferred to the lauter tun, a lautering rest of 10 minutes is taking place before the first wort is gained within 20 minutes at 60 ml per minute. After- wards, it is sparged twice. The hops are added at the beginning of boil- ing. With an α acid content of 9.2 %, the hop addition is 5 g. After the 60 minutes boiling time, the wort
3

concentration is adjusted to 11.3 °P. The wort is then transferred to the whirlpool. After a 15 minutes whirl- pool rest, the wort can either be filled uncooled into sampling bot- tles for analysis purposes or cooled into 5 l glass bottles for subsequent fermentation in the modified EBC test tubes. The brewing plant works automatically to eliminate all op- erator influences, which ensures a high reproducibility.
Lautering ability
A special feature of the miniature brewery is the fact that the wort kettle position is variable in height [4]. The lauter tun and the wort kettle are connected vessels. The speed. The course of the pressure differenceallowsconclusionsabout the condition and changes in the spent grains cake. As the course of the pressure difference is different for each malt, the lautering behav- iour of the respective raw material can be assessed. A malt that is re- sponsible for lautering problems causes a much greater increase of the pressure difference than a malt with very good lautering proper- ties. This behaviour is shown as an example in Fig. 1. For an objective evaluation of the lautering behav- iour, the curve is described math- ematically. A calculation of the areas under the curves has proven to be useful for this purpose and is

CHECK OUT OUR NEW VARIETIES
WWW.HOPSTEINER.COM
Fig. 1: Comparison of pressure differences of two malts with very good and bad lauterability
automatic lowering of the wort ket- tle increases the pressure differ- ence that is formed above and be- low the spent grains, which serves to maintain the required lautering
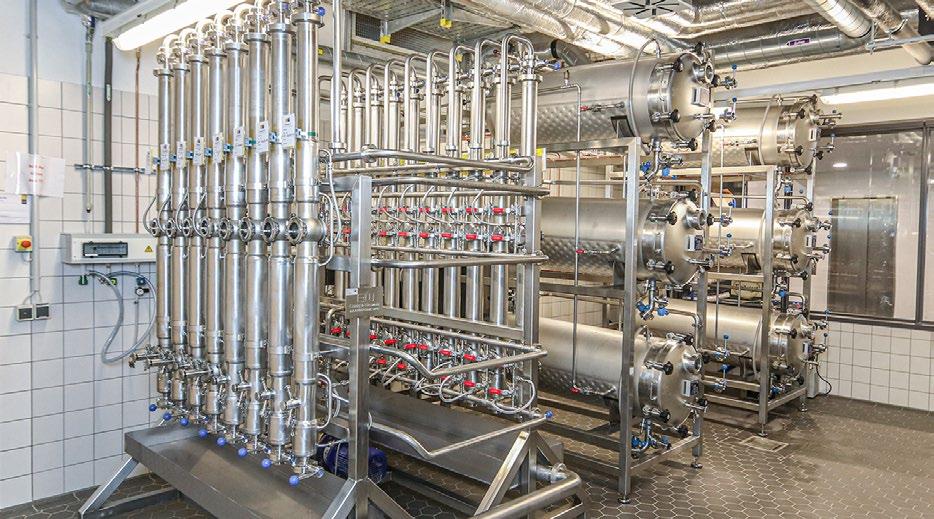
Photos: 1 – The 5-l brewhouse, fully automated 2 – Malting drums in the VLB malt house 3 – Lauter tun of "nano brewery" 4 – Fermentation and storage cellar 5 – Fermentation tubes
performed using the process data recorded by the process control system (Braumat ® , Siemens). The example in Fig. 1 shows clear differences between the two malt batches investigated. For the malt that causes a very small increase in pressure difference (refer to the grey curve), an area under the curve of 25700mm ∙ sec is calculated and is classified as malt with very good lautering ability. The other malt (black curve), with an area under the curve of 186000mm ∙ sec, was classified as having poor lautering ability.
Sample quantities
The plant can also be used to investigate the influence of different malts, water qualities or hop varieties on beer taste, gushing behaviour or product development in general. The plant has enormous scope, since a large number of parameters can be varied. For example, the energy input during wort boiling can be adjusted by adjusting the temperature of the heating medium, or the turbidity at the whirlpool outlet can be recorded. In the modified EBC fermentation test tubes, the wort can be fermented under standardized conditions. It is also possible to divide the wort of a 2 or 5 hl brew on up to 18 fermentation columns in order to test different yeast strains, enzymes or wort qualities. Due to the limitation of the preparation volume to up to 4 l, the quantity is also sufficientforvarious analytical tests and a sensory evaluation with 10 tasters. The economic advantage is particularly obvious when a large number of samples are processed. This advantage plays a major role,
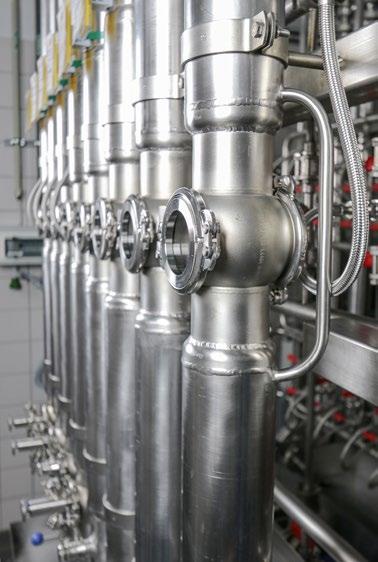
especially in the development of beverages. Due to the low use of rawmaterials, differentrecipes can be processed and analyzed against each other at low cost. Newer products such as hard seltzer and coldbrews deserve special mention here. The application possibilities of the miniature brewery and its individual components are extremely versatile. Working on a very small scale is particularly useful when very little sample material is available or when a broad screening is to be carried out. Although the plant volumeisverysmall,sufficientsample quantities can be obtained to carry out appropriate analysis and even tastings are possible. During the development of the individual components, the reproducibility of the results was always a priority, so that investigations on this scale have been used for research and services for years.
Contact: m.werner@vlb-berlin.org
[1] Tyrell, T., Exner, R., Folz, R., (2011), Further development of EBC Fermentation Test-tubes, Poster of 33 rd EBC Congress, Glasgow [2] Innokom MF140002 [3] Werner, M., Biering, J., Pahl, R., (2017): VLB Berlin forscht mit Miniaturbrauerei, Brauerei Forum (8/2017), p. 8–9 [4] Under licence of JBT GmbH, German patent DE102014202768B3